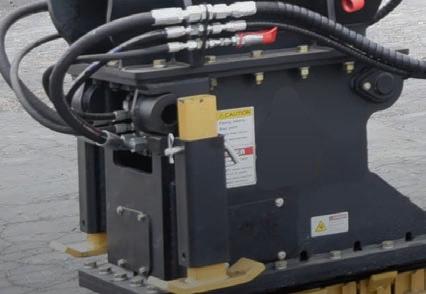
9 minute read
BALLAST
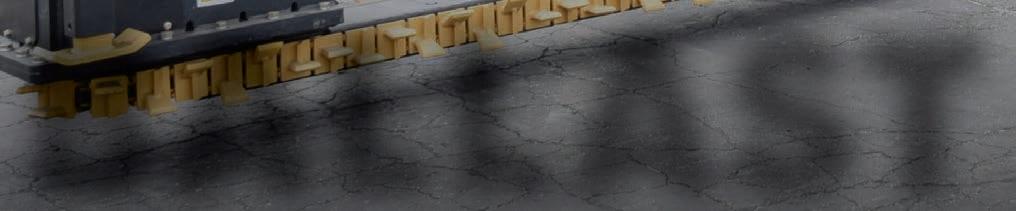
Ballast is indeed a topic we discuss o en, and so does just about everyone who is involved in railroad maintenance-of-way. Without proper ballast maintenance, the railroad would be a mess. Ballast is the only sector of maintenanceof-way to which Railway Track & Structures devotes two Vendor/Product spotlights each year. While the others are certainly critical, we only focus on those once per year. Here is what the ballast maintenance vendors that chose to participate are up to now.
Mitchell Rail Gear
Recently delivered two John Deere 210G track Excavators to Northeast Illinois Regional Commuter Railroad Corporation D/B/A METRA, specially con gured for track ballast maintenance. Mitchell installed their cab controlled Hydraulic Rail Gear for high-speed track travel. Mitchell’s hydraulic rail gear includes ride control with dual cobra rail brakes on each of its hardened forged rail wheels. Mitchell installed Tiltrotator’s on the excavators that quick attached a series of attachments that were con gured as plug and play attachments. Each attachment, such as the 12 . undercutter, plugs directly into the Tiltrotator without the operator having to perform any special machine monitor programing. e same goes for all the other attachments that include digging buckets, ditching buckets, clam buckets, brush cutters, buckets with thumbs, cold air blowers and magnets. Special machine tracks were installed that retained the full width of the machine for stability and allow the machine to straddle the track so it can sit on the railroad ties when situations required additional stability. e John Deere Excavators were con gured with high- ow and medium- ow hydraulic circuits with an additional dedicated return line to handle any attachment for track maintenance. e machine joysticks were programmed for easy operation with safety buttons to prevent accidental attachment operation. With the variety of buckets provided the machine operator can quickly prepare the ballast for undercutting and then return the ballast to its normal con guration for train travel. Included with the machines were 3000 hours of lubricants and lters for easy maintenance. e magnet attachment can pick up

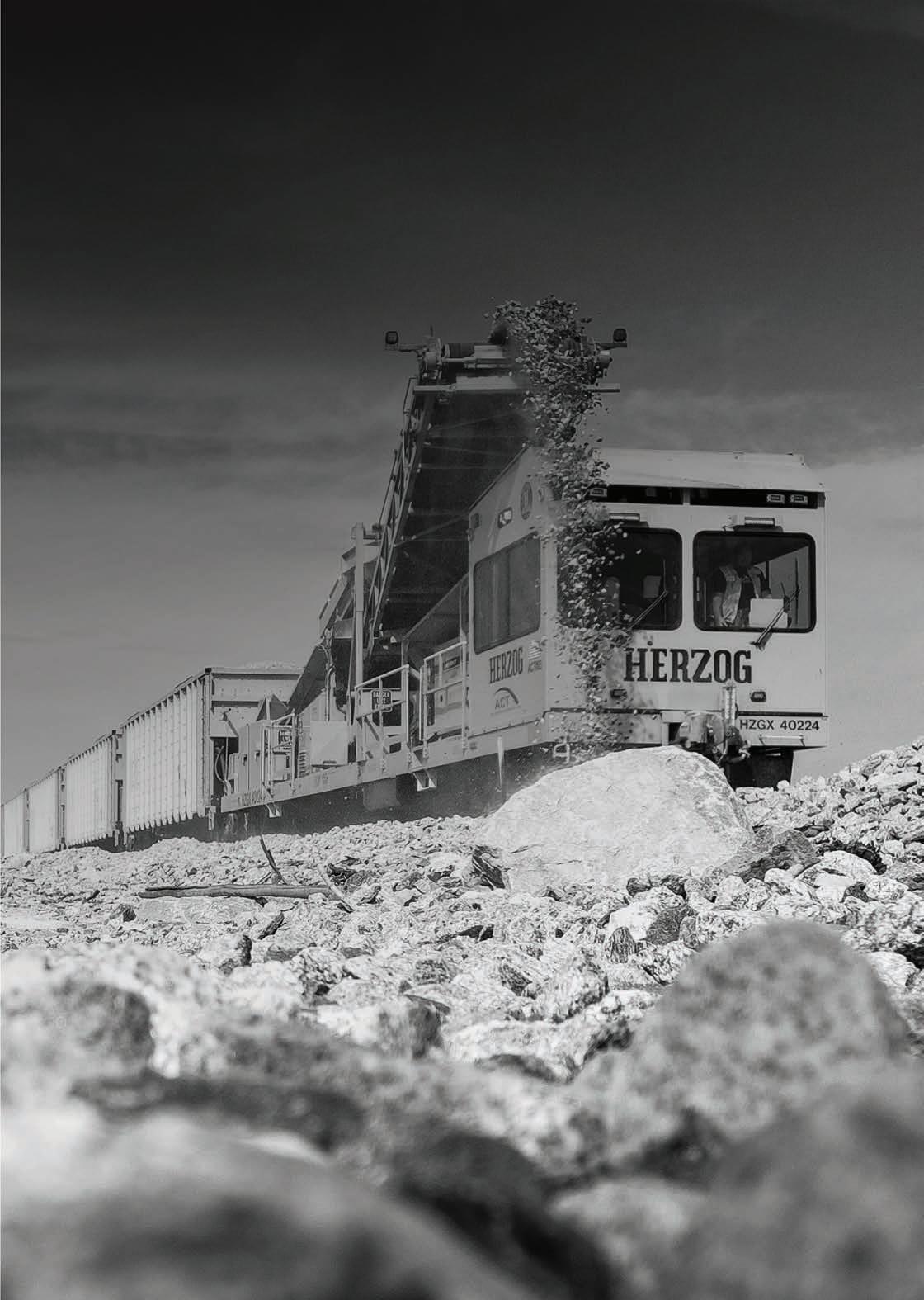

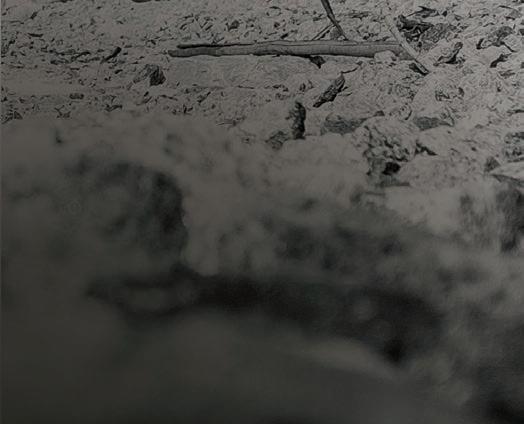

OTR along the right-a-way and extend the machine’s boom full reach for cutting and trimming trees. A multi-purpose machine such as this John Deere Excavator can easily switch attachments to perform jobs that were once only done with single purpose machines or easily add attachments in the future as the need arises.
Loram
In 2023 Loram started pairing the productivity of their Badger Ditcher with the versatility of their slot trains. is provides customers an equipment solution capable of managing any ditching and excavating needs with a single piece of equipment. is selfpowered machine is capable of track travel at speeds up to 45 miles per hour, excavating material from ditches at a rate of 1,000 tons per hour, and storing up to 250 tons of material on machine when necessary.
Loram o ers a full line of material handling products to support delivering product where and when our customers need it. When industry leading material delivery is required, Loram’s DumpTrains can deliver 1,500 tons of material to washout locations, work sites, or stockpiles and unload a full consist in under an hour. O oading is done up to 45 feet from track centerline. e DumpTrain for Curves® o ers all the same features as the traditional DumpTrain and can operate while in curves or tangent track. e DumpTrain and DumpTrain for Curves® are the only belt trains in the market today that can deliver sub-ballast as well as ballast. e SlotMachine® eet continues to experience strong demand from customers that utilize the exibility of these machines to support almost any material handling demand. e SlotMachine® consists of overlapping gondola cars carrying an excavator that can traverse the full 378-foot length. is arrangement allows for quick and e cient loading & o oading of ties, ballast, rip rap, spoils, and almost anything in the right-ofway that is within reach of the excavator. e Self-Powered Slot (SPS) has the same features as the traditional SlotMachine® while also including a traction car so the entire consist is self-propelled to and from the worksite. e MHC60 material handling car continues to excel at storing spoils of excavating equipment and extending work windows in areas where discharging adjacent to the track is not an option. With bestin-class o oad rates and casting distances the MHC60 is a strong complement to undercutting, shoulder ballast cleaning, and vacuum excavation equipment.
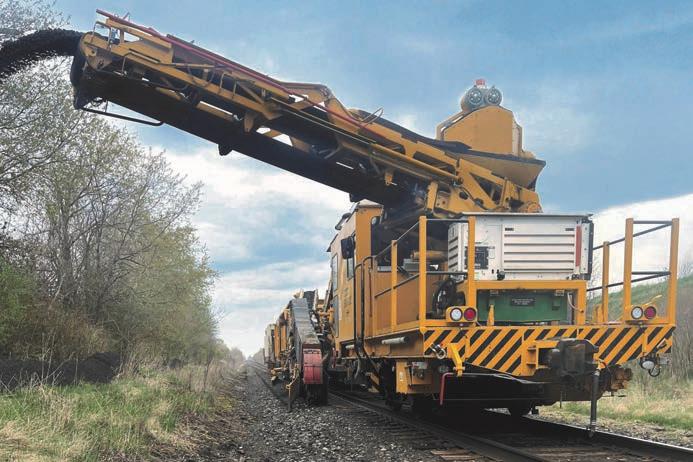
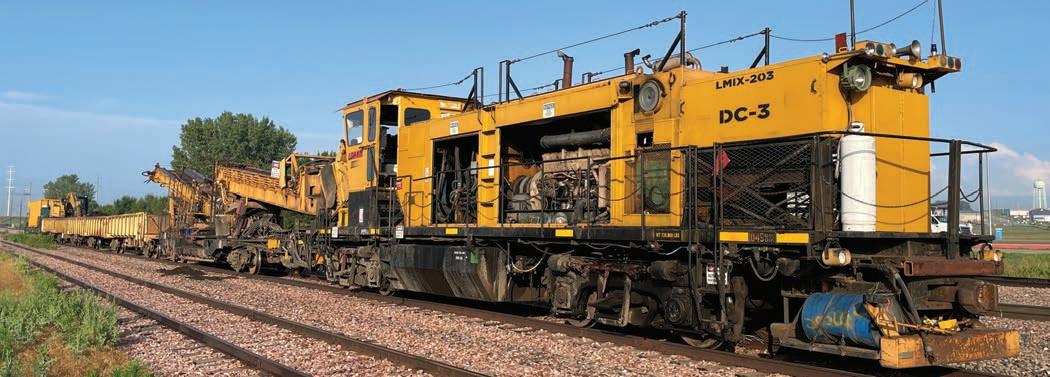
Plasser American e RM802, biggest undercutter in the U.S., is a high-production Ballast Undercutting/ Cleaning Machine especially designed to work on track with pre-dumped ballast. Production rates of up to 2,000 feet per hour are achievable. Shoulder Cleaning Machines like the FRM85F and FRM802 complement the portfolio, keep ballast shoulder free from ballast breakdown, ensure drainage, and stretched maintenance cycles. Both shoulder and ballast cleaning machines are equipped with one of two self-leveling shaker boxes that can recover a high amount of ballast in tough conditions. e BDS100/200 Ballast Distribution System is the ideal machine to accompany high-speed surfacing gangs or used alone to reposition existing ballast. e machines are equipped with a hopper unit for ballast storage, conveyors to distribute ballast and a fully adjustable x-type ballast plow, and unique shoulder plows to pro le the ballast. e BDS100/200 opens new possibilities to distribute the existing ballast in the network and saves money and important resources. e Plasser 09-2X DYNACAT is a heavyduty, high-speed, and continuous action switch and production track-tamping machine with an integrated dynamic track stabilizer. While the satellite tamps and indexes two ties at a time during the actual work process, the machine’s main frame, with stabilizer system, moves smoothly and continuously at a speed determined by the operator. is ensures a consistent quality throughout the whole tamping section.
Plasser American o ers a eet of machines that work together to improve track conditions and heighten e ciency during both regular operation and while performing regular maintenance. Ballast bed cleaning, ballast distribution, shoulder cleaning, stabilization, and tamping all work in concert to get track to its best performance.
Ballast cleaning machines with di erent performances ful ll the individual requirements in North America. Smaller Ballast Cleaning Machines, such as the RM80, are designed for plain track and turnouts with one excavating chain and one screening unit. e RM80’s 50 mph travel speed and short set-up and knock-down times allow maximum utilization of available track time.
Knox Kershaw Inc.
Knox Kershaw Inc. will introduce the HBR 2300, a hybrid model of its’ well known KBR925 Ballast Regulator, in the early months of 2024. It will have all the advantages of the standard KBR 925 Ballast Regulator with the added bene ts of hybrid technology, including fuel savings, battery powered operations to reduce emissions, improved engine e ciency, decreased demand on engine and pump components, and the use of environmentally friendly renewable energy.
From their recent experience converting straddle li cranes to hybrid technology,
KKI sees the immense advantages this innovation can have on current and future MOW equipment.
Benefits of the new Hybrid Ballast Regulator Model KHR 2300:
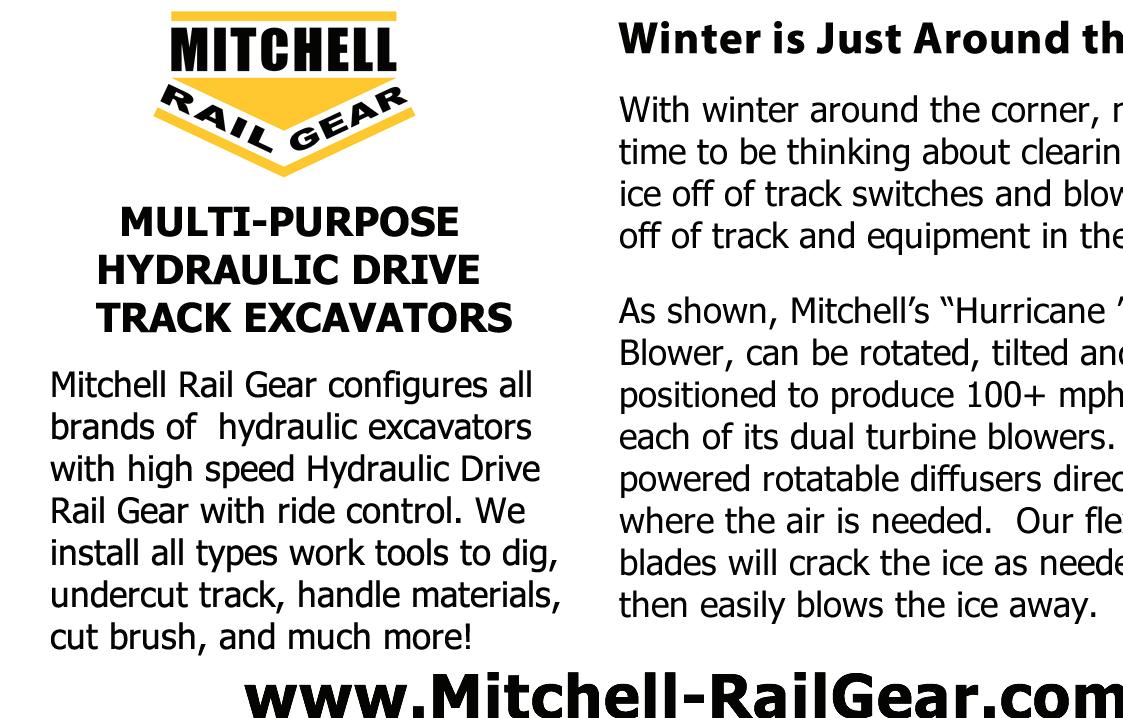
Engine Package: 3.8 L, 74 HP vs. 6.7 L, 260 HP:
• 7-9 gallon/per hour fuel savings
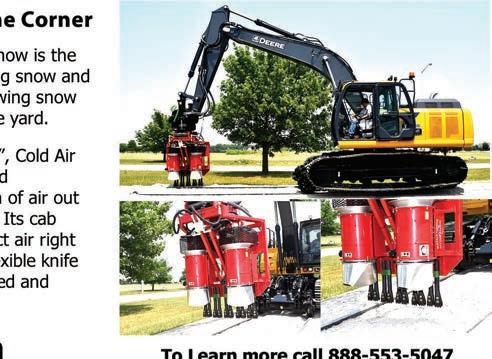
• NO DEF is required.
• Smaller engine package for increased visibility
• Lower Noise Emissions
Battery Capacity and Pump Power Unit:
• Fuel savings by using batteries to power operations such as the A/C and motors
• Electric HVAC for operator comfort
• Increased engine air lter life due to reduction in engine use
• Increased engine life (only runs when charging is needed)
• Less wear-and-tear on pumps
• Lower Noise Emissions (when engine is not running)
KKI is focused on product line expansion, especially in the eld of renewable energy. e company continues to improve upon existing models of its machines to make them safer, more e cient, and easier to operate. We could not do this without the guidance and support of our customers. rough them we learn how to make our products better with each model.
Knox Kershaw Inc. is a top manufacturer of ballast regulator machines. With 5 di erent models to choose from, each one customizable with a variety of options, there is a Knox Kershaw Inc. Ballast Regulator to suit every job, large or small.
Rhomberg Sersa North America e MHDT is designed to operate with the company’s eet of RM80 high output ballast undercutters to provide the ability to collect track spoil in areas where casting of material from the undercutter is either impractical, environmentally unacceptable, or both. e MHDT con guration is highly adaptable and can also serve as a ballast feeder to the ballast cleaner during the undercutting process, optimizing production and reducing overall ballast maintenance cost. e recent introduction of our new material handling train in North America o ers an environmentally friendly method for the delivery and distribution of ballast and handling of track spoil material. e system allows maintenance to be performed in challenging but highly critical infrastructure which includes highly populated areas, environmentally sensitive locations, and “traditionally di cult” locations such as tunnels.
Rhomberg Sersa North America (RNSA) provides ballast maintenance solutions and technologies o ering public and private railroads new and innovative approaches to ballast and trackbed management.
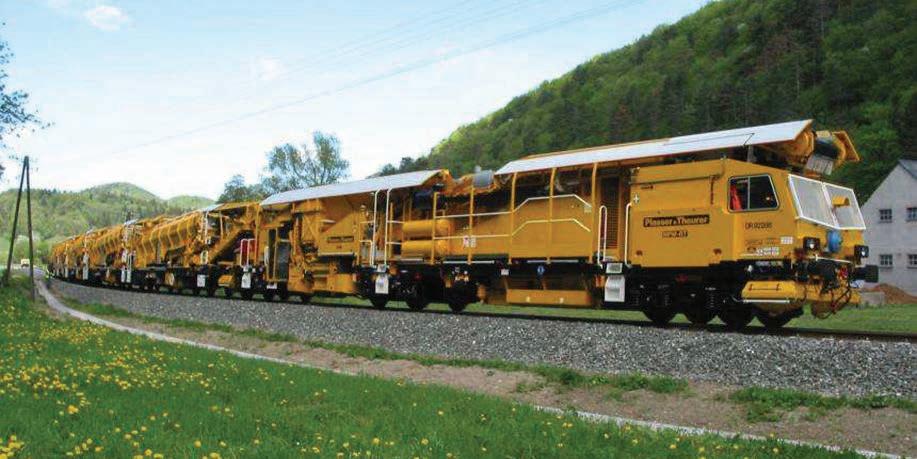
As part of its ballast management strategy and end-to-end service o ering, RSNA has recently added a Material Handling and Distribution Train (MHDT) which consists of MFS Cars and Power Wagons that collectively enable ballast to be loaded, stored, transported, and unloaded and distributed at site.
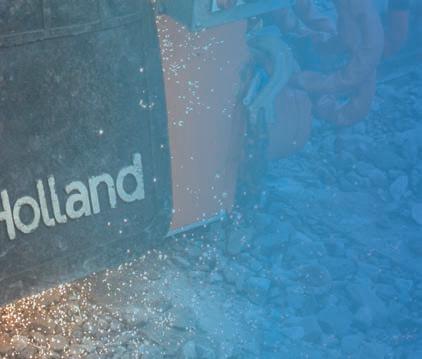
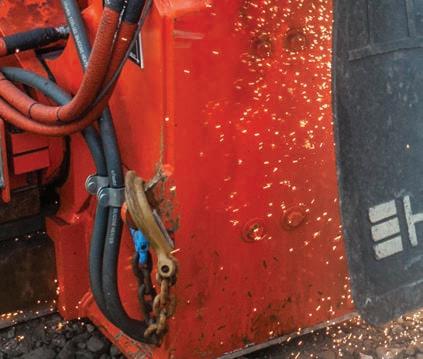

With each MFS car having its own internal conveyor system that connects to each adjacent car, single line ballast cleaning is possible and removes the need and costly expense of taking adjacent track out of service to accommodate support equipment.
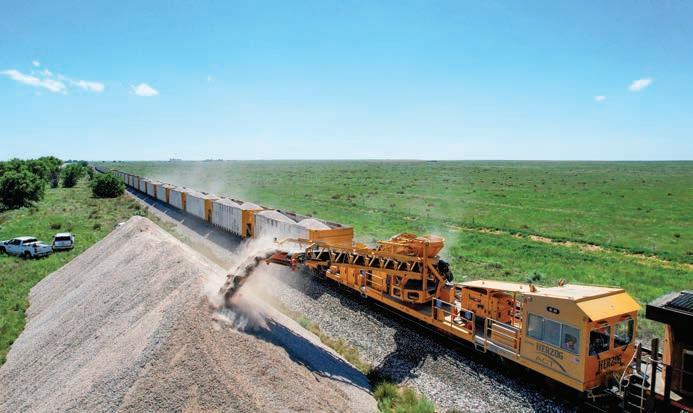
Herzog
Herzog just raised the bar again on the newest model of its Automated Conveyor TrainSM (ACT), designed and manufactured by Herzog railroad maintenanceof-way equipment experts. “Herzog has a culture of continuous improvement. We want each new product to be better than the last,” says Jake Herzog, Vice President of Engineering, Research, and Development. A er a re-design of the equipment’s gate system, the ACT now provides an increased production ow rate of 28% and further addresses railroad customers’ needs for versatile material unloading. e newest model can handle cohesive materials, such as base rock, that typically would not unload from a hopper of this type. “ e increased ow rate allows for less track time and more production,” says Ryan e ACT’s conveyor belt system excels at safely and e ciently distributing ballast, even in curves and S-curves with angles of up to 13 degrees. It unloads material 50 feet from the track center, 15 feet directly in front of the cab, and is accompanied by an automated plow to strike ballast away from the center of the track. e ACT signicantly improves delivery e ciency to the right-of-way and eliminates the need for additional truck transport. e machine o ers numerous advantages, starting with its one-person operation from a climate-controlled cab, eliminating the need for ground personnel and ensuring operator safety by avoiding exposure to silica dust and adverse weather conditions. e locking mechanism on its 35’ conveyor arm enables safe working conditions on the eld side while train movement occurs on an adjacent track. Moreover, the ACT provides around-theclock support, with 24/7 unloading availability and eld support.
Crawford, Vice President of Ballast Operations and Railcar Leasing. Its performance is evident as it can unload a 30-car consist of 2,900+ tons using just one generator car and one discharge car. Other enhancements include wireless tablet control from outside of the cab, simpli ed controls architecture, and an increased generator size for future consist expansion.
Custom Truck One Source
Custom Truck One Source’s rotary dump body proves a reliable solution for the transportation of ballast and other materials, up and down the rail.
e Load King 14 , 12-14 cu. yd. elliptical dump body has proportional hydraulics, joystick control, hinged drop ladder (street side), as well as rail dogs.
Rail gear included in this build includes hydraulic actuation, front brakes, front rail sweeps, slotted rear links, a heavyduty rear bracket and manual rear pins. Each unit is track-tested and includes FRA annual rail gear inspection. Custom Truck One Source’s railroad division has a full catalog from hi-rail pickups to tandem axle material handlers.
Ballast Tools Equipment (BTE)
Ballast Tools Equipment (BTE) has developed a new attachment for clearing fouled cribs between ties. e BTE Cribber was developed by the engineers at Ballast Tools Equipment, to make quick work of clearing ballast and debris that traditionally called for the use of a Cribbing Bucket. is new attachment, when teamed with a BTE Hi-Rail Excavator, makes short work of clearing out a run of ties.
According to BTE Sales Engineer Matt Weyand, “the BTE Cribber is an extremely powerful trencher-style undercutter for spot maintenance and cleaning out the cribs between the ties. Its continuous action allows for a faster, more e cient clean-out of debris compared to using a traditional cribbing bucket.” He went on to say, “We understand that durability is crucial in demanding work environments. at’s why the BTE Cribber is built to withstand even the toughest conditions. Its robust construction ensures longlasting performance, reducing downtime and maintenance costs.”
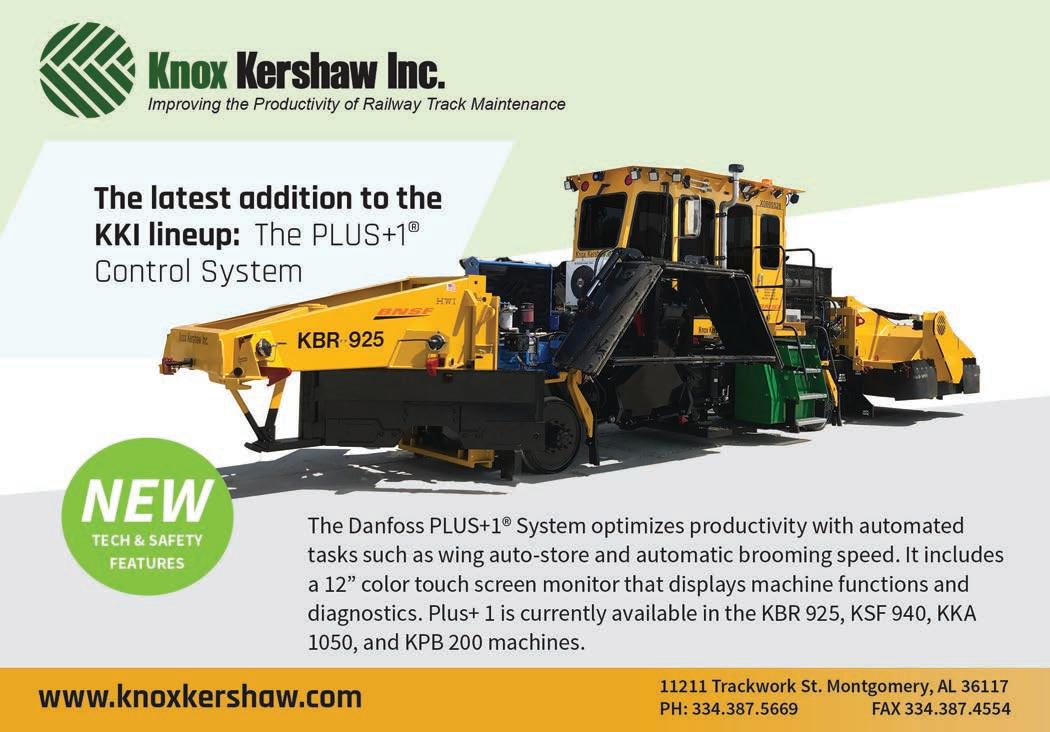
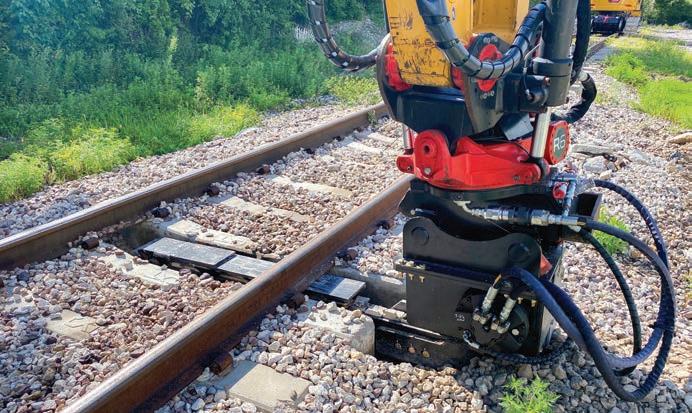
Utilizing additional chain guarding, the BTE Cribber can protect against damage to the rails and ties while in use. e proprietary Tungsten Carbide protected cutter chain can withstand extreme wear during operation. is is the most e ective crib cleaning system on the market today. For more information go to https://BTEquip.com