

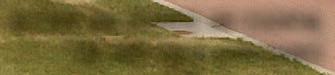
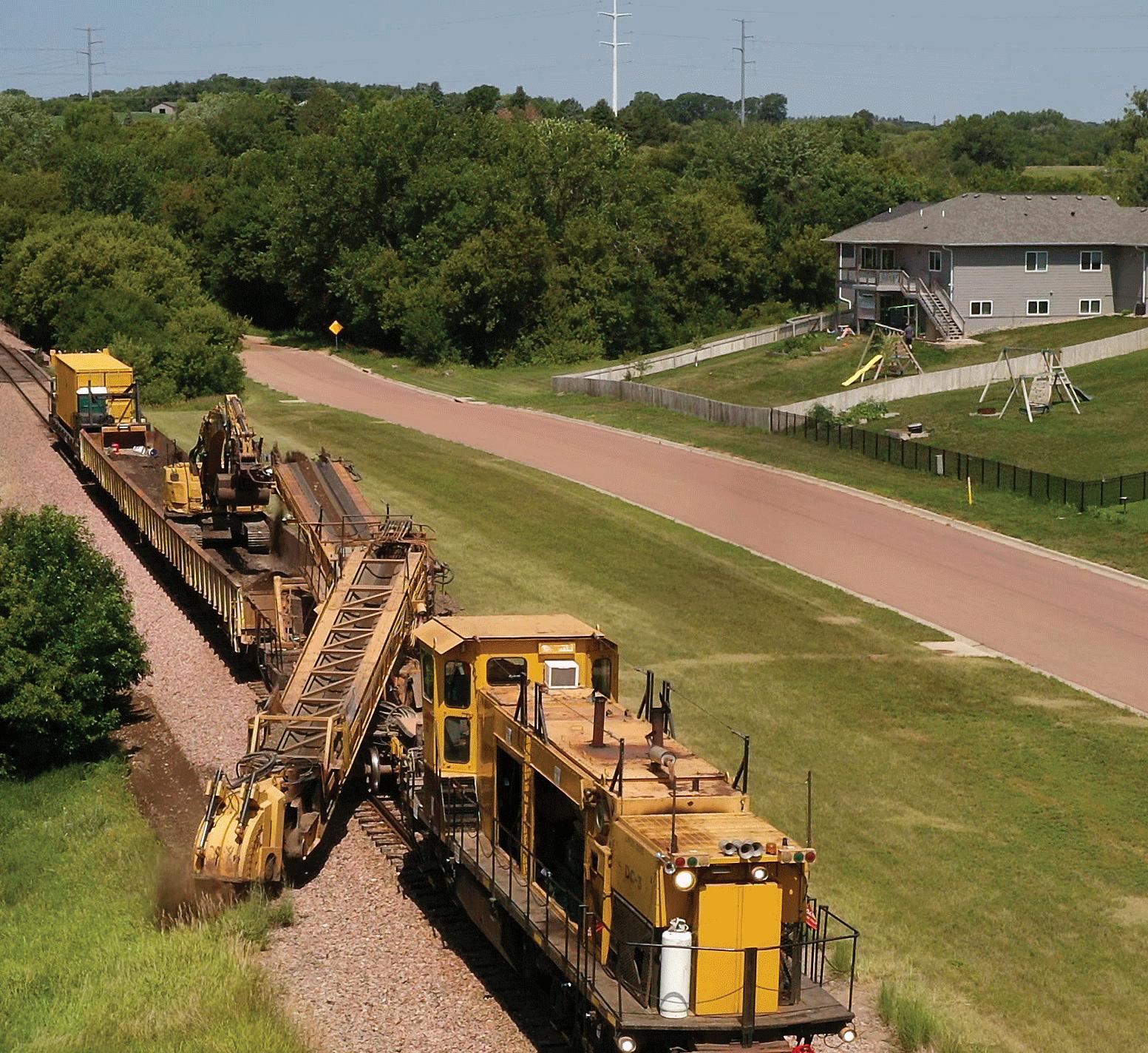
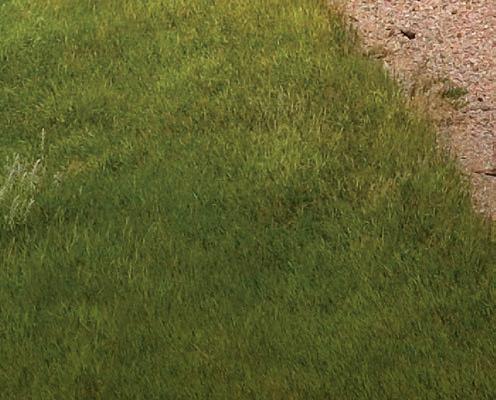
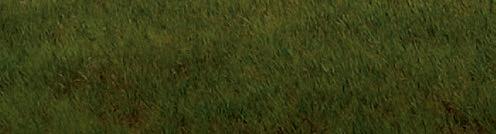

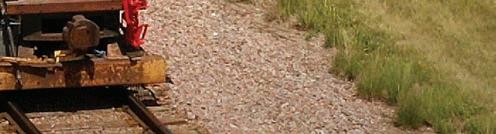
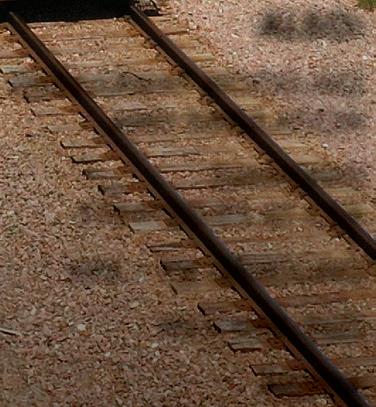


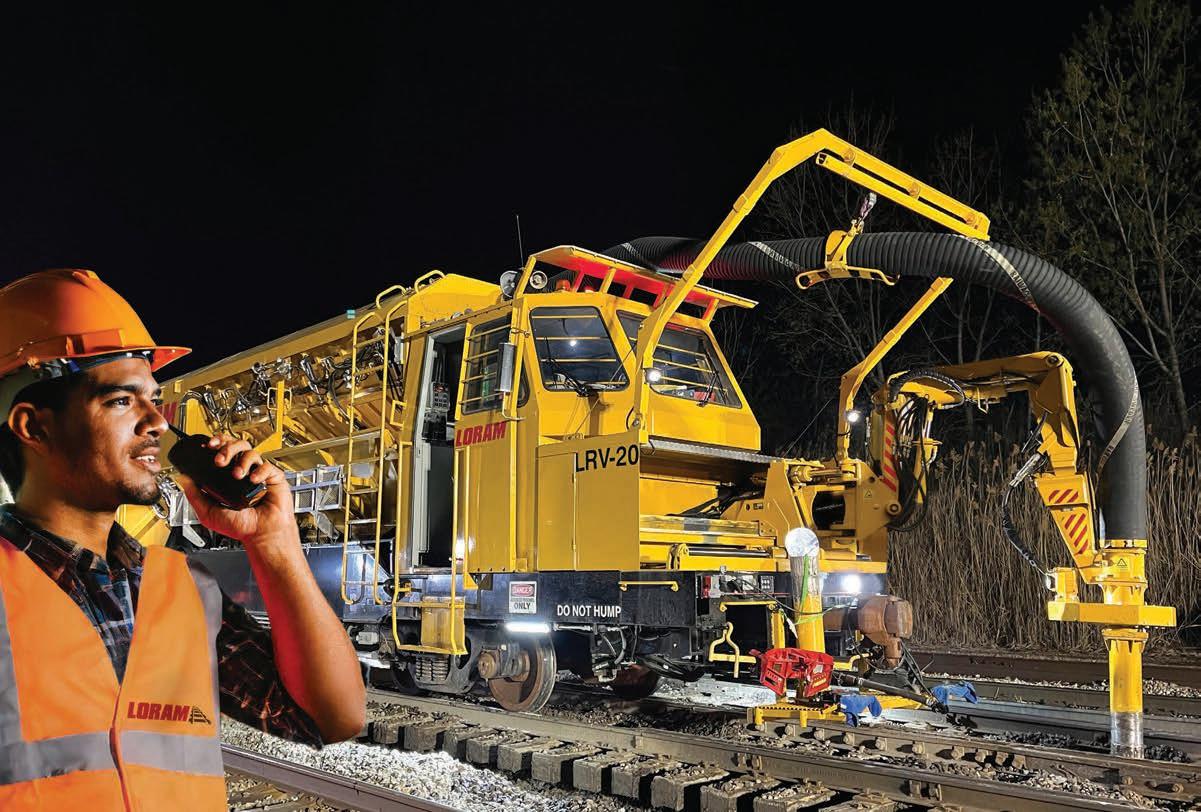
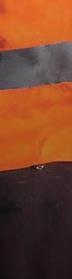

8 Derailment Modeling
Using Digital Twin Simulations of Automated In-Train & Vehicle/Track Dynamics to Reduce Derailment Risks 14
Grinding Strategies at CSX Mitigating Transverse Defects and Reducing Non-Testable Areas: Grinding Strategies at CSX
Vendor-Product Spotlight Ditching and Draining
Vendor-Product Spotlight Crossties
Key Features and Benets for these Products:
• Low Gross Weight - No CDL Needed for Transport
• Compact Size & Maneuverability
• Remote Controlled
• Each Functions as a Hydraulic Power Pack
focused equipment and technology solutions for the North and South American
Vol. 120, No. 10
Print ISSN # 0033-9016, Digital ISSN # 2160-2514
EDITORIAL OFFICES
1025 Rose Creek Drive Suite 620-121 Woodstock, GA 30189
Telephone (470) 865-0933 Website www.rtands.com
DAVID C. LESTER Editor-in-Chief dlester@sbpub.com
JENNIFER M c LAWHORN Managing Editor jmclawhorn@sbpub.com
EDITORIAL BOARD
David Clarke, University of Tennessee
Brad Kerchof, formerly Norfolk Southern William Riehl, Genesee & Wyoming/AREMA
Scott Sandoval, Genesee & Wyoming
Robert Tuzik, Talus Associates
Gary Wolf, Wolf Railway Consulting
CORPORATE OFFICES
1809 Capitol Avenue Omaha, NE 68102
Telephone (212) 620-7200 Fax (212) 633-1165
ARTHUR J. MCGINNIS, JR. President and Chairman
JONATHAN CHALON Publisher
MARY CONYERS Production Director
NICOLE D’ANTONA Art Director
HILLARY COLEMAN Graphic Designer
JO ANN BINZ Circulation Director
MICHELLE ZOLKOS Conference Director
CUSTOMER SERVICE: 847-559-7372
Reprints: PARS International Corp. 253 West 35th Street 7th Floor New York, NY 10001
212-221-9595; fax 212-221-9195 curt.ciesinski@parsintl.com
Automation
By David C. Lester, Editor-in-Chief
As I write this, I have just returned from the annual AREMA Conference in Louisville, Ky. While the conference was excellent, as usual, one session really caught my attention –– one on Emerging Technologies during the Monday morning general session. One of the themes of this discussion focused on automation and its impact on jobs. e traditional wisdom, which has proven to be the case on several occasions, is that jobs are lost when automated processes or some other new technology is introduced. Perhaps the most signi cant example in the history of the rail industry is the transfer from steam power to diesel and the resulting reduction of locomotive maintenance personnel. Most will recall that steam locomotives were complex machines, requiring a wide variety of attention, from keeping the coal and water tenders full to regular oiling of the valve gear during a run. When diesels came along, with their relatively simple daily maintenance needs, the number of railroad workers needed to keep the eet going dropped signi cantly.
Many of the technological changes in the rail industry today focus on the gathering and processing of data to provide information on the status of equipment and other elements of the infrastructure. For example, automated track inspection that utilizes equipment mounted to locomotives or in special freight cars are being tested and used. While this reduces the number of personnel needed to visually inspect the track, people are still needed to interpret the results. As one panel member put it, “Computer technology only presents facts and information. If it identi es a problem, it doesn’t tell you how the problem occurred or what needs to be done to x it. It takes the human brain to do that.”
Panelists also pointed out that they are being inundated with data of all kinds, and they are in the process of learning which data is most important to target speci c problems.
Additionally, automated inspection cars have enabled one railroad to go from inspecting around 50,000 miles of track per year with traditional crewed, rail-bound geometry cars to covering about 115,000 miles per year with automated equipment. Of course, inspecting this much additional track is going to increase the workload of those who need to interpret the data, so people who usually crewed geometry cars will have a lot more data to evaluate. Indeed, chances are that additional people will be needed to process and review all of the data in a timely fashion so any exceptions or major track problems can be addressed quickly.
ere was a story in the news recently about how fast-food industry had an unexpected result from the implementation of customeroperated kiosks used for ordering to reduce the number of employees needed to take orders. What they found, however, was that with the self-service kiosks, customers were able to place their orders faster, increasing the total number of orders to the point that the kitchen couldn’t keep up. So, the employees who used to take orders had to move to the kitchen, and overall sales for some restaurants grew signi cantly, and no jobs were lost.
Realistically, some jobs will indeed be lost due to automation. However, with management and labor members and leadership working together, chances are very good that many of those “lost” jobs can be replaced with openings created by directly or indirectly by automation. Losing one’s job for any reason is devastating and frightening. With smart thinking, though, railroad leadership can develop plans to ensure that automation is not a big reason for job loss.
DAVID C. LESTER Editor-in-Chief
An AAR-funded study where MxV Rail investigated the optimization of crossing diamond foundation designs.
Steve Wilk, Ph.D. – Principal Investigator, Engineering Services
Duane
Otter, Ph.D., PE – Scientist
Ben Bakkum, PE –
Principal Investigator I, Engineering Services
MxV Rail
Commonly found throughout North America, crossing diamonds are a special trackwork component that allows two rail lines to cross each other at-grade. Flangeway gaps are generally necessary for wheels to pass in both directions; however, this means the wheel tread must traverse gaps when crossing each rail, causing a wheel impact. ese wheel impacts 1) can produce loads that are two or three times the size of the static wheel load and 2) can signi cantly increase the rail and underlying component deterioration. In addition to the complexity of the diamond geometry, these impacts are why crossing diamonds present a continual maintenance challenge for North American railroads. To reduce the negative e ects of these impacts, crossing diamonds require stronger rail metallurgy and components. ere are many di erent types of crossing diamonds, each with di erent levels of complexity and customization. In addition to the general industry improvements from railroads and suppliers, in the past 30 years, MxV Rail has conducted multiple e orts that addressed crossing diamond and turnout deterioration from both a running surface and a foundation standpoint. e combined e orts from railroads, suppliers, and research institutions have resulted in the incremental improvement of crossing diamond life.1
Over the past 50 years, engineering pads have been used in various applications to
damp impacts and vibrations in the railroad industry. Di erent pads are needed for di erent applications that have resulted in a wide range of available pads from multiple vendors, with varying materials, thicknesses, stinesses, and damping properties. Within the past decade, many of these applications (e.g., under-tie pads, special trackwork pads) have been adopted by North American railroads to extend component life.
One of the initial North American railroad crossing diamond pad tests was part of a jointly funded study by the Association of American Railroads (AAR) and the Federal Railroad Administration (FRA) that investigated crossing diamond life from di erent running surfaces, foundation strengths, and platework
pads at MxV Rail’s Facility for Accelerated Service Testing (FAST®).1 e importance of the pad type was emphasized as the rst pad iteration (so pads with high damping, intended for optimal sti ness) disintegrated overnight from the rst 100 train passes with 315-kip car loads. However, the potential bene ts of pads in crossing diamonds were shown in the second pad iteration (sti pads) with the crossing diamond signi cantly reducing vertical impact loads and extended life versus previous tests without pads.1 is study reinforced an industry push to start incorporating pads into crossing diamonds, however, questions remained regarding the optimal pad con guration (the number of pads and their placement).
is article summarizes a follow-up AAR-funded study where MxV Rail investigated the optimization of crossing diamond foundation designs by monitoring two Class 1 railroad diamonds over three years (2018–2021) with three di erent pad con gurations.2
Crossing Diamond Details and Measurements
e rst test location (Diamond #1) is a conventional 67-degree crossing diamond in Idaho. Installed in summer 2013, the rst diamond design evaluated had a two-layer pad con guration using under-tie pads (UTPs) and under-plate pads (UPPs) and a hot-mixedasphalt (HMA) underlayment. e second
diamond design, installed in April 2019, had a three-layer pad con guration (UTPs, UPPs, and casting pads) instead of the two-layer pad con guration. e study objective was to compare the performance of the two-layer ( rst design) and three-layer (second design) con gurations at the same location. A second no-pad 90-degree crossing diamond (Diamond #2) near Winnipeg, Manitoba was also monitored.
For all measurements, accelerometers were placed at three layers on the diamond: the casting, the platework, and the tie (see Figure 1). Generally speaking, accelerations can provide a useful measurement to assess vibration and impacts. e accelerometer records were analyzed by calculating the maximum
and minimum peaks from passing locomotive axles. To reduce the in uence of axle loads and other vehicle dynamics, only the locomotives were analyzed. e locomotive velocities were also recorded, but no signi cant in uence from velocity was observed with the available velocity ranges (20 to 40 mph).
e monitoring results showed that pad con guration and support conditions both in uence diamond accelerations.
Diamond #1: Pad Configuration
Figure 2 shows the accelerometer results of Diamond #1, emphasizing the in uence of pad con guration. To isolate the pad con guration
from the support conditions, only Diamond #1 measurements with well-supported conditions (no visible pumping greater than 0.5 inches) are presented. e black dots represent a peak from each locomotive axle while the various colored markers represent the median values.
As can be observed, while the newly installed three-layer pad con guration (July 2019) is similar to the in-service two-layer pad con guration (August 2018), the threelayer pad con guration shows deterioration and has much higher accelerations a er being in-service for two and a half years. ese higher accelerations agreed with visual observations of more broken bolts, loose elastic fasteners, moving platework, and churned ballast in the third observation trip (October 2021).
Accelerometer Results – Pad Configuration and Support Conditions
Figure 3 includes all results from both diamond crossings, both good and poor support conditions, and accelerations from both the plate and casting. e dot color represents the support condition (e.g., poorly supported in red) and whether the good support situations were newly installed (green) or in-service (blue). No newly installed diamond had poor support conditions. e results suggest the best performance (lowest casting and plate accelerations on the tested crossing diamond) occurs from a combination
of two-pad con guration (UTPs and UPPs) and good support conditions. Degradeded performance (i.e., higher accelerations) can be observed from the no-pad, three-pad, and poorly supported situations.
e crossing diamond eld test results show that pad con gurations and support conditions both in uence diamond performance. e deterioration of the three-layer pad con guration was also observed on other diamonds in revenue service, and the casting pad is believed to be the cause of increased maintenance on fastening systems, bolts, and platework. e increased platework vibration has been attributed anecdotally to the casting pads, and this study seems to agree with the observations. While the cause of the increased platework acceleration magnitude is not completely clear, suboptimal casting pad sti ness may be part of the problem. Casting pads with higher sti nesses have appeared to perform better both at FAST in Pueblo, CO, and at an in-service crossing diamond. Further study will be required before any casting pad recommendations can be made. However, for the monitored diamonds, it was noted that diamonds with either UTPs only or UTP and UPP combinations required less maintenance than diamonds with no pads or diamonds with casting pads (regardless of other pads).
Support conditions can also in uence the crossing diamond performance. Increased displacement and vibration can occur from both running surface and foundational issues. is study did not directly investigate foundational conditions other than making general observations; however, best practices have been determined based on previous studies. ese best practices include proper ballast maintenance (e.g., ensuring drainage), the use of premium, wear-resistant ballast, and additional foundational support methods, such as geosynthetics or hot-mixed asphalt, that can reduce the subgrade settlement in regions with poorer subgrade material.
e authors would like to thank Erik Frohberg (retired) from BNSF Railway for commentary and direction along with Edouard Valancogne from Getzner for advice and understanding of pad properties.
1. Davis, D. and R. Jimenez. 2016. “Next Generation Foundations for Special Trackwork – Phase III.” DOT/FRA/ORD-16-14.
2. Wilk, S., K. Morrison, D. Otter, and C. Johnson. 2022. “Crossing Diamond Performance: Pads and Foundations.” Technology Digest TD-22-013. AAR/MxV Rail: Pueblo, CO.
By Je Tuzik
Engineers predict things,” said Cory Hogan, Director of Vehicle Dynamics Studies at Ensco Rail Inc. As computing power and modelling have become more sophisticated, engineers have increasingly used digital-twins to model vehicle, track, and component behavior with incredible fidelity. Like engineers, digital twins can be great predictors. A digital twin is a virtual model of a component, process, or system that is designed to reflect its realworld counterpart (a physical twin) as accurately as possible. One of the most
common ways digital twin simulations are used is to predict potential problems or failure modes in a safe environment, and before the issue appears in the physical twin. “The predictive aspect of a digital twin is my focus: I don’t want to figure out how a derailment happened after the fact; I want to predict and avoid it,” Hogan told delegates at the 2024 Wheel/Rail Interaction conference.
A digital twin that faithfully represents its physical twin also allows for testing that may be impossible or unfeasible in-situ, such as modelling the effect of increased speed on vehicle dynamics
and derailment potential, for example.
In another example of how digital twins are used, Hogan and Ensco recently undertook a project that involved simulating vehicle and carbody dynamics of a train transporting very large wind turbine blades. These components are particularly sensitive to certain vibrational frequencies, Hogan said, so the team modeled several different support systems to find a configuration that would effectively isolate the component from carbody and wheel/rail vibration (figure 1).
Regardless of the specific end-goal, an
accurate digital twin requires accurate data on the physical twin.
“One thing I’ve found in derailment investigation is that often the data necessary to predict a derailment was available before the derailment happened,” Hogan said. This is often the result of underdeveloped data infrastructure; just as there are departmental silos that can prevent communication between teams, there are data silos that can prevent interaction between data streams. Much of the focus in this regard is on streamlining and automating collection
and correlation of data streams. “It is because we knock down the silos that we’re able to be predictive,” Hogan said.
Part of the challenge is that larger and more complex digital twins require more, and more frequent data collection. The digital twin for a single rail car operating over a small section of track, for example, is simple compared to the digital twin of an entire rail network; As a system, a rail network changes constantly, Hogan said. As a result, the digital twin and physical twin may differ significantly a short time after data collection. This means that frequent,
repeated measurements are necessary to ensure the digital and physical twins remain in sync. So, the creation of an accurate and useful digital twin for a network requires the combination of frequent geometry measurements and automated data transfer, processing, and reporting, he said.
From a practical standpoint, this type of digital twin is built by collecting geometry data from autonomous track geometry measurement systems (ATGMS) operating throughout the network (figure 2). These vehicles can be integrated into any freight consist
just like a standard box car and have their own redundant power supply. The ATGMS are also ballasted so that their weight and performance more accurately reflect that of a loaded boxcar.
The data generated by ATGMS is automatically transferred via cellular signal to a cloud-based reservoir where it is automatically processed and prepared for simulation by modified VAMPIRE (Vehicle Analysis Modeling Package In the Railroad Environment) software. VAMPIRE is a multi-body dynamics modeling package often used to model forces imparted from
track to vehicle, forces transmitted into vehicle components, and derailment risk. VAMPIRE is widely used in the railroad industry and by researchers and academics; its origins are in the late 1980s with Delta Rail, AEA Technology and British Rail Research.
“Getting VAMPIRE to work in a cloud environment is something we’ve been working on since 2008, and there’s still work to be done,” Hogan said, “so none of this is an easy process.” The benefit is that simulations are supported by cloud-based parallel processing, so they are completed very quickly. Automated
reports from these simulations are then made accessible to the relevant personnel.
As is the case with any simulation, the veracity of the output must be validated, which is done by comparing simulated output data with measured data. This was done by running an ATGMS equipped with several accelerometers and an inertial measurement unit over a section of track, and then modeling ATGMS vehicle dynamics for the same track section. Figure 3 shows the close agreement between simulation and measurement. “If you can accurately
model mass and inertia, stiffness, damping, and excitation source, you’ve got a useful model,” Hogan said. “This validation test gives us confidence that we’re accurately modeling accelerations and wheel/rail excitation.”
Following the development and validation of the ATGMS / cloud-based VAMPIRE system, Ensco first deployed the system on the Canadian Pacific Kansas City Limited (CPKC) network. At the time of deployment, the CPKC network was roughly 14,000 track miles. With three ATGMS units each averaging 100 miles of track measurement per day, this gave Ensco 300 miles of track geometry a day to process and simulate. CPKC requested simulations for 11 vehicle models moving both directions (up- and down-milepost) at the maximum posted speed. This added up to 22 total simulations per mile of track. VAMPIRE can run a single simulation of a mile of track (including filtering, simulation, and data export) in roughly 1 minute. This all adds up to 6,600 minutes of processing per day — an impossible task without parallel processing.
To keep pace with all the data, Ensco created a 4-core VAMPIRE cloud instance for each ATGMS (figure 4). Under this processing regime, the required processing time went from 6,600 minutes to 600 minutes (per day). “At this rate, we were able to not just keep up, but to stay ahead of the incoming data,” Hogan said.
One of the ways Ensco sought to further leverage the data they were collecting was to investigate and simulate the e ect of coupler angles and forces, as well as in-train longitudinal (bu and dra ) forces on L/V derailment risk thresholds. “Longitudinal forces and coupler angles have a big e ect on L/Vs at the wheel/rail interface, and we wanted to pull that data into the automated system we built,” he said.
Ensco partnered with Union Pacific and PS Technology to develop a proofof-concept for adding this data to their existing VAMPIRE software package. Coupler angles for a given route were calculated based on consist makeup and car type, and existing curvature data from the track geometry system (figure 5), and then correlated to ATGMS in the cloud.
The proof-of-concept simulation was based on a 121-car mixed-load consist with head-end and rear-end power. Ensco focused their analysis specifically
on a 90-foot bi-level autorack, 23rd from the head end. This car was bracketed by two shorter cars (a 68-foot reefer and a 50-foot boxcar) — an arrangement known to generate severe coupler angles and high coupler forces, Hogan said.
The simulation did indeed predict high coupler forces at several locations on the simulated track. “We were particularly interested in how the integration of simulated coupler forces would affect vehicle dynamics,” he said. Figure 6 shows the simulated vertical loads for the lead axle of the car of interest in green, and the same car with the addition of simulated coupler forces in red. At this location, the simulated train is traveling at 11 mph through a 6-degree right-hand curve with 5 inches of superelevation, under 145 kips of draft. Both the red and green graphs predict vertical unloading of the lead axle on the high rail as expected for a vehicle traveling at underbalance through the curve, he said. However, the red graph, which takes into account coupler forces, indicates a much more significant unloading. As shown in figure 7, a similar
effect can be seen on the low rail as well; dynamic lateral loading peaks 30% higher with the inclusion of coupler forces than without.
This proof-of-concept highlights the value of integrating multiple data streams to create a more robust and flexible simulation. And although the project only simulated a single car, the ease of incorporating parallel processing to cloud-based solutions means that processing power doesn’t represent a major bottleneck, Hogan said. In fact, part of what makes the cloud VAMPIRE system so adaptable is that simulations considering many different types of data including train handling, speed, topography, and power distribution can be integrated with VAMPIRE data without disrupting or interfering with ongoing ATGMS-based simulations.
Hogan sees many potential improvements and expansions of the cloud VAMPIRE/in-train force modeling package. One potential feature is a vehicle dynamics risk-lookup table based on VAMPIRE simulation data that automatically runs against other simulations
in parallel, he said. For example, a coupler-force simulation of a single car could be applied to system-wide data relating to multiple speeds, conditions, and locations to determine whether any combination of factors could present an elevated derailment risk.
Future plans for the project also include the integration of rail and wheel profile measurements so simulations
can model wheel/rail interaction with high granular accuracy and output data points like base-over-height (B/H) ratios, conicity plots, and critical L/V ratios for individual wheel/rail combinations. Wheel and rail profile data will also improve the ability to model vehicle/track interactions that are heavily influenced by wheel/rail interaction, such as hunting and steering
characteristics. “At this point we’re focused on completing the picture — of building a more complete digital twin,” Hogan said.
Jeff Tuzik is Managing Editor of Interface Journal.
This article is based on a presentation made at the 2024 Wheel/Rail Interaction Heavy Haul Conference.
By Je Tuzik
Transverse defects are among the most costly and dangerous rail defects that freight railroads contend with. Across all Class 1 railroads, transverse defects are responsible for roughly 31 percent of broken rails system-wide; so mitigating the growth of transverse defects and detecting their presence via internal aw detection is of critical importance. To that end, CSX has recently made signi cant improvements to its rail grinding program that have both reduced the number of TDs and TD-caused rail breaks on their system and improved their ability to detect them.
Transverse defects can be initiated in two ways: surface-initiated and subsurfaceinitiated. In both cases, standard ultrasonic
rail aw detection tools can detect the defect before it reaches a critical point and potentially causes a rail break. However, poor rail surface conditions due to shelled, spalled, corrugated (SSCs) rail or rolling contact fatigue (RCF) can re ect and distort ultrasonic signals, preventing detection by conventional Ultrasonic Testing (UT) inspection systems, and making the section “non-testable”. is combination of factors makes transverse defects a particularly vexing problem, Dan Hampton, CSX Director of Contract Services, told delegates at the 2024 Wheel/Rail Interaction Conference.
“In 2016, we had a combined total length of 30 miles of non-testable locations. By 2023, there were less than 1000 feet in 21,000 track miles; a 98% reduction,” said Dan Hampton,
CSX Director of Contract Services.
Surface-initiated TDs, which are typically initiated by cracks formed by RCF, are typically controlled through rail grinding. Le unaddressed, RCF-generated cracks will propagate. A combination of thermal and mechanical stresses can drive the cracks deeper into the rail, potentially initiating a transverse defect (and broken rail) of the type seen in Figure 1. Surface-initiated TDs can be particularly dangerous because RCF and SSCs on the rail surface can interfere with ultrasonic detection, e ectively occluding the transverse defect (or any other defect beneath the RCF).
Rail grinding does double duty by removing the damaged layer of the rail surface: It arrests the development of RCF-generated
cracks before they propagate deeper into the rail and allows for e ective UT testing. Rail pro le grinding is done to bring the rail into a desired pro le shape that mitigates excessive contact stresses on the gauge corner; in the case of TD mitigation, the target is typically a light 2-point contact pro le that works well with a variety of wheel pro les. “Since freight railroads don’t control wheel maintenance on freight cars, rail pro les have to accommodate a wide range of wheel pro les and conditions,” said Frank Stillman, Vice President of Service Excellence at Sperry Rail Service, and Hampton’s co-presenter.
Subsurface TDs typically begin with the development of a subsurface shell at the gage corner due to high contact forces between the gauge corner and wheel ange.
Nov. 5 & 6, 2024 Chicago, IL
We’re returning to Chicago with an expanded event!
Railway Age and RT&S are proud to recognize the growth in leadership roles for women in the railway industry. Our second annual Women in Rail Conference is now a two-day event, filled with instructive panels, an awards luncheon, and a local transit tour.
Join a diverse group of railroaders with a shared commitment to our industry’s future.
PROGRAM HIGHLIGHTS:
•Furthering industry inclusivity and showing allyship
• Advancing your career—from asking for a raise to developing new skills
•Understanding the latest regulatory and legislative happenings
•New tech innovations and the latest applications
SUPPORTING ORGANIZATIONS
•How mentorship can change your journey
•Building a safety culture
•Railway Age’s Women in Rail / RT&S’ Women in Railroad Engineering awards luncheon
•Tour of Metra’s rebuild shop and training center
4. CSX’s overhauled program e ectively reduced the surface-initiated and subsurface-initiated transverse defect population.
Over time, continued high stress causes the subsurface rail material to crack and collapse along a shear line thus forming a shell. Once a subsurface shell has begun to develop, it can quickly (invisibly) propagate deeper into the rail. e mechanism of propagation in most such cases is the repeated bending and thermal stress of the rail under load, Stillman said. As rail steel quality and metallurgy/micro-cleanliness has improved over time, manufacturing defects and internal aws are responsible for a shrinking portion of rail breaks, while those initiated by TDs (both surface and sub-surface-initiated) have grown in proportion.
A shell that has already formed can’t be ground out of the rail; it must be cut out and replaced with a plug rail, said CSX’s Dan Hampton. But rail grinding does play an important role in alleviating the high-stress contact conditions that caused or contributed to the previous shell formation.
Mitigating the risk of TD development and controlling RCF so that rail surface condition doesn’t interfere with ultrasonic testing requires a grinding program that takes into account varying crack growth and wear rates
throughout the system, Hampton said.
CSX began to overhaul its rail grinding program in 2016, initiating a process that both curtailed transverse defect development, and improved the accuracy of ultrasonic rail aw detection. For example, most tangent sections typically only need to be ground every 50 to 70 MGT, while sharp curves may need to be ground every 15 MGT, he said. In CSX’s case, 90% of the network has 3-degrees of curvature or less. As such, their preventive grinding cycle is based on RCF crack growth rate on 3-dregree curves. For the small population of sharper curves on the network, CSX allocates the resources for additional grinder passes but adheres to the same MGT-based cycle.
In 2016, CSX introduced a second grinding team to its network. Based on historical data on RCF development, wear rates, and MGT, Hampton’s team developed and implemented optimized grinding cycles and routes and focused on targeting RCF at the gage corner. Under this new regime, the occurrence of transverse defects fell by ~19% (see gure 3). Additionally, their TD-caused broken rail incidence fell from ~20% to ~13% (of all broken rail causes). ere are plans to further re ne the metrics used to calculate these grind cycles. “ e MGT-based RCF crack growth gures we’re currently using are an average, but with a surface evaluation system like an eddy current device, we could know the exact crack growth of any given location,” Hampton said.
Another aspect of the grinding program that CSX continues to optimize is the target depth of cut, or metal removal, for a given
Figure 5. The number and size of non-testable locations fell dramatically after CSX implemented an optimized grinding program.
track segment. Based on data collected from broken rails with transverse defects indicating gage-corner cracking as the defect initiation point, CSX modi ed their grinding protocol to increase depth of cut if gagecorner RCF is present at any severity level. Gage-corner RCF is typically found on high rails in curves, and these rails’ service life is typically limited by lateral rather than vertical wear; “so the additional ‘wear’ due to metal removal has a negligible e ect on rail life,” Hampton said. Additionally, CSX now grinds the entire curve body based on the worst-case gage-face RCF found in the curve. e combined e ects of ensuring that preventive grinding cycles are met, and of aggressively targeting gage-corner RCF have yielded impressive results. Since these protocols were implemented in 2020, CSX has seen the TDD population fall by 37%. Over this same period; TDDs as a
percentage of all rail service failures fell from 20% to 13%.
In addition to improving rail condition by mitigating RCF and reducing transverse defect formation, CSXs grinding improvements have also improved the accuracy of ultrasonic aw detection, which requires a smooth, clean surface for optimal signal transmission between the ultrasonic transducer and the rail. In addition to blocking or otherwise interfering with ultrasonic transmission and e ectively hiding potential internal defects, poor surface conditions due to SSCs or RCF can interfere with ultrasonic testing results in other ways, too. “Sometimes a surface defect looks just like a transverse defect and sometimes a transverse defect looks just like a surface defect,” Sperry’s Frank Stillman said. “Surface conditions also a ect the repeatability of inspections, and these variations make it
impossible to accurately track the progression of internal defects over time.”
Since CSX began to overhaul its grinding program with respect to transverse defect mitigation, their e orts have also signi cantly reduced the number and size of non-testable locations throughout their network. In 2015, prior to the improvements Hampton detailed, there were 692 nontestable locations measuring a combined 142,704 feet on the network. By 2023, there were only 58 non-testable locations measuring a combined 799 feet (see Figure D).
Hampton noted that the small spike in non-testable locations in 2019 corresponds with the increased depth of cut implemented that year which resulted in the grinders covering less of the network overall. “Once we caught up to our new grinding cycle, we got over that hump and the SSCs continued to trend downward,” he said.
Frank Stillman, Vice President of Service Excellence at Sperry Rail Service.
track.Over1500termsfromantiquatedforgottenslangto today'sjargon.Clearlyillustratedlineartenhancesthetext.
Another part of the e ort to reduce non-testable locations was to catalogue these locations by type. Figure 6 shows the number of non-testable track feet by category from 2014 to 2018.
The categories are:
• Specialty assets
• Curves
• Rail surface quality and fatigue
• Bridges
• Tangents within 200 feet of a spiral
• Sidings
• Steep grades and absolute signals
“Switches and road crosses made up the majority of [non-testable] locations, and we found that we just weren’t grinding them with adequate frequency,” Hampton said. Before the grinding began in 2016, CSX had access to only one specialty grinder for six months out of the year to address these locations. CSX has since devoted more resources to specialty grinding and to better leveraging the exibility of their mainline grinders. is includes signi cantly more combined operations in which a mainline grinder
Reprintedbypopulardemand,thisbookisavaluablereference forroadmasters,tracksupervisors,trackforeman,surveyors andothersinvolvedintheplanningandexecution oftrackmaintenanceandconstructionwork. Fold-outdiagrams.Softcover.301pages.
Railgrindingsavesmillionsofdollarseveryyear!TheArt andScienceofRailGrindingisthefirstbookdedicated exclusivelytothesubject.
Thisneweditionencompassescurrentdesignmethodsusedfor steelrailwaybridgesinbothSIandImperial(USCustomary)units. Itdiscussestheplanningofrailwaybridgesandtheappropriate typesofbridgesbasedonplanningconsiderations.
BasicPrinciplesofTrackMaintenance progressesfroman overviewofthebasictrackstructuretoexaminationsofits componentsandendswithacomprehensivelookat turnoutsandright-of-way.
works alongside a specialty grinder for added exibility. ese modi cations to the grinding program have proved particularly e ective; as Figure 6 indicates, virtually all categories of non-testable locations were drastically reduced or eliminated by 2018. e optimization of CSX’s rail grinding program is an ongoing project. Rail grinding itself is a balancing act; defect removal and pro le shape must be balanced against metal removal. e allocation of grinding resources must be balanced against other operational and logistical constraints. In reducing both the number of non-testable locations and the population of transverse defects in their rail, CSX has struck a balance between the theoretical and practical aspects of rail grinding to develop a program that has yielded tangible — remarkable, in fact — results.
Je Tuzik is Managing Editor of Interface Journal. https://interfacejournal.com/ is article is based on a presentation made at the 2024 Wheel/Rail Interaction Heavy Haul Conference. https://wheel-railseminars.com/
To prevent flooding and misalignment of the track, ditching work is a necessary area of track maintenance.
By Jennifer McLawhorn, Managing Editor
To allow rainwater to better flow through and away from the track structure, railroads need specialized track equipment to maintain the ballast and prevent flooding. Loram Maintenance of Way told RT&S about its suite of products that are created to “maintain ditches to keep water flowing away from the ballast section of track.” Depending on the situation, there is a variety of equipment available in the industry for railroads to choose from. What follows is a breakdown of Loram Maintenance of Way’s offerings in this area of track maintenance.
For smaller ditching tasks, and work around near track obstructions, the SelfPowered Slot (SPS) is the ideal solution. For high performance out of face ditching the Badger Ditcher is the product of
choice. For projects requiring high speed excavation and work around obstacles the Ditcher Max can meet all ditching needs. All Loram’s ditching solutions are self-propelled and can travel at speeds up to 45 miles per hour.
The SPS is capable removing, and placing, almost any type of material within the reach of the excavator. The SPS can excavate to create/clean ditches at up to 250 tons of material per hour and work around, or remove, any obstacles that may be present to create a clean ditch line. Up to 550 tons of excavated material can be stored on the consist for offload at an appropriate location.
The Ditcher is the highest performance machine in the market for creating consistent ditches along track. The Ditcher can excavate up to 1,000 tons
of material per hour and discharge excavated material up to 35 feet from track centerline. The ditcher is ideal for cutting new ditches, terracing slopes, and cleaning eroded material out of existing ditches.
e DC Max combines the excavating speed of the Ditcher with the exibility of a SPS for a premium ditching solution. Utilizing a DC Max the excavator can remove obstructions from the planned work location for the Ditcher so consistent and smooth graded cuts can be made regardless of the starting condition of the work area. While excavating, the ditcher can discharge material up to 35 feet from track centerline or into the gondola cars that are in consist. Up to 225 tons of excavated material can be stored on the consist for o oad at an appropriate location.
No matter its composition, creating and maintaining ties are necessary.
By Jennifer McLawhorn, Managing Editor
If you were to view a segment of track as a spine, you could argue railroad ties are similar to vertebrae. ey give the railroad a backbone, a structure that allows rails to be fastened into alignment. With the amount of track maintenance needed to produce, maintain, replace, and reuse ties, RT&S has gathered a selection of what the industry currently o ers.
Stella-Jones supplies up to 10 million pressure-treated wooden crossties per year. It o ers not only railway ties and timbers for Class I, short line and commercial railroad operators, but also industrial products—including wood for railway bridges and crossings, marine and foundation pilings, and construction timbers—and customized services. Preservatives for mixed hardwood and oak include creosote, borate and copper naphthenate. With facilities located across the United States and Canada, Stella-Jones’ extensive network o ers economical coverage using rail, truck and maritime transport. StellaJones’ combined production capacity and long-term relationships with wood suppliers
ensure a constants ample supply of raw material, particularly in times of emergency need. Lastly, its continental network of treating facilities and distribution yards carry a large inventory to ensure its customers get the materials they need.
Using data scans from Aurora to identify which ties are most in need of replacement, Loram Technologies works with customers to build a replacement plan based on current tie condition and budget allocation. With this nalized plan, an automated tie marking system marks each tie planned for replacement and the Tie Set Out team places new ties at the point of use by the marked tie. is eliminates the need for someone to walk the track and physically mark where to set out ties ahead of a tie distribution team.
e Tie Set Out So ware allows users to know exactly where to set out ties and how many are required for each drop as the team travels along the track. As well as making any edits needed to the tie count. e result is ties that ere much closer to where they need to be installed and allows for increased productivity
for the tie replacement teams as less time is spent moving ties around and along the track to the appropriate install locations.
Loram Technologies collects data on thousands of miles annually. is information and the use of the so ware e ectively and safely helps increase tie life and reduce fouling conditions.
Koppers tells RT&S its North Little Rock, Arkansas, facility has been updated and upgraded to o er peak e ciency, now capable of processing and treating more than 2.5 million crossties annually. Fully automated, the plant handles larger volumes of ties per treating cycle, with less need for direct employee contact, and in a cleaner, more environmentally friendly work ow. Bundles of ties enter the facility and are moved automatically into transport bays, then into cylinders for treatment. Following treatment, the ties are moved automatically from the cylinder into a drying area, where following a speci ed time, they are moved out for distribution to customers. And this entire process happens with the push of a button.
Koppers’ North Little Rock, Arkansas facility has been updated and upgraded to o er peak e ciency.
TiEnergy LLC has provided responsible and innovative tie disposal and track maintenance solutions for Class 1, shortline and private railroads for decades. It has received and recycled hundreds of thousands of old ties and turned them into an in-demand,
marketable product that supports railroads, land lls, and the community. Expired ties create storage issues, disposal headaches, and safety hazards for railroads, and TiEnergy has systems in place to turn the ties into an aggregate substitute called TIEROC, which
helps land lls operate more e ciently. In turn, the responsible disposal method helps railroads meet sustainability goals. Each recycled tie saves 3.06 pounds of carbon from entering the atmosphere. Once ties are transported in cars, they can cause car capacity issues. ey leave behind small debris such as stone, grit, dirt, and slivers of wood, and over time, accumulated debris reduces the volume available for tie loading. TiEnergy has built its business on recognizing issues and creating solutions, and has developed an as-needed car cleaning service as part of tie unloading/ disposal. is service helps customers maximize their individual car volume and reduce their overall tie disposal cost.
For Nisus, its QNAP® copper naphthenate is an American-made, general use preservative for pressure treating crossties and bridge ties. QNAP-treated ties are safe, long-lasting, and sustainable. Testing conducted by the USDA Forest Product Laboratory on ties treated with copper naphthenate demonstrated an estimated service life of over 65 years. QNAP-treated ties also have the most options for their further use at the end of
life, from fencing and residential landscaping to serving as fuel for permitted boilers. Under the EPA’s Nonhazardous Secondary Material rule, only QNAP-treated ties can be used in any boiler covered by the rule, and only QNAP-treated ties are allowed as boiler fuel with creosote-treated ties. In addition, QNAP is not a skin-sensitizer, and its cleaner handling characteristics mean that crews face less risk of skin irritation when handling treated ties. A non-conductive and non-corrosive formula, QNAP results in less drippage in use, a particularly important aspect for environmentally sensitive bridges over pedestrian walkways, roads, and waterways.
Omaha Track facilitates the removal, processing, and distribution of over 3 million ties annually, and its business continues to grow and evolve as its operations expand. It starts by acquiring second-hand ties from a variety of locations, where it uses a meticulous sorting process to ensure the highest-quality ties are resold for landscaping products. Ties of lower quality are designated as a crosstie fuel source for power plants and other industries. Omaha
Track tells RT&S it is currently working on making the operation more energy-e cient and sustainable, with the goal of reducing its carbon footprint. It partners with Class 1 railroads to safely repurpose crossties, including those treated with creosote.
TrackSafetyStandards Subparts A-F
TrackSafetyStandards, containstheTrackSafety Standards,SubpartsA-F,forClassesoftrack1-5.The standardscovergeneralinformation,Roadbed,Track Geometry,TrackStructure,TrackAppliancesand Track-RelatedDevices,andInspection.IncludesDefectCodes. Updated December28,2023.
BKTSSAF TrackSafetyStandards,SubpartsA-F $12.95 Only$11.65forordersof50ormore!
FRAPart237establishesFederalsafetyrequirements forrailroadbridges.Thisrulerequirestrackownersto implementbridgemanagementprograms,whichinclude annualinspectionsofrailroadbridges,andtoauditthe programs. Part237 alsorequirestrackownerstoknow thesafeloadcapacityofbridgesandtoconductspecialinspectionsif theweatherorotherconditionswarrantsuchinspections. Updated December28,2023
BKBRIDGE BridgeSafetyStandards $10.95
Only$9.85forordersof50ormore!
Its facilities in LaCrosse and Superior, Wisconsin; Pueblo, Colorado; Hazen, Nevada; and Chicago Heights, Illinois specialize in processing scrap railroad ties and other wooden railroad materials into chips suitable for co-generation fuel.
ThisreprintincludestheFRA's RailroadWorkplaceSafety Standards addressingroadwayworkersandtheirwork environments.Theselawscoversuchthingsas:personal protectiveequipment,fallprotection,andscaffoldingfor bridgeworkers;andtrainingissues.Alsoincludessafetystandardsfor on-trackroadwayvehicles. UpdatedDecember28,2023.
BKWRK RailroadWorkplaceSafety $12.95
Only$11.65forordersof50ormore!
The TrackSafetyStandardsCalculator isamustfor anyonewhoworksontrack.Thisslideruletype calculatorcontainsmanyofthedetailsforClassesof track1-5.Deviationfromuniformprofileandfromzero crosslevel.Differenceincrosslevel.Compliantwithpart213.
BKTCAL
TrackCalculator $11.50
Only$10.75forordersof50ormore!
UpdatesfromtheFederalRegistermaybesuppliedin supplementform.
U.S.A.CAN
Join Railway Age and RT&S at a premier event: Light Rail 2024, our annual conference on light rail transit.
13 & 14
The Westgate Hotel San Diego, CA
LRT, North America’s fastest-growing passenger rail mode, employs a full range of technologies and operating practices. Light Rail 2024, developed for transportation professionals in planning, operations, civil engineering, signaling and vehicle engineering—as well as students at the undergraduate and graduate level—will o er a comprehensive review of the specialized technical, operational, environmental and socio-economic issues associated with LRT in an urban environment.
The conference concludes with a special tour of the San Diego Trolley, the first modern LRT system in the United States.
Key Sessions
•Engineering for Operations
•Capital Program Management
•Dealing with Extreme Weather Events
•Project Updates on Major New-Builds and Expansions
•Alternative Propulsion Technologies
•Customer Interfaces – Fare Collection, Communications, Security
•Funding Challenges
Sharon Cooney CEO
San Diego Metropolitan Transit System
John Mardente Civil Engineer, Passenger Rail Div. FRA
Alfred E. Fazio, P.E. BRT Rail Services
Brian Riley COO – Rail
San Diego Metropolitan Transit System
Rachel J. Burckardt, P.E. SVP / Sr. Project Mgr. WSP USA
Wayne Terry Retired COO – Rail
San Diego Metropolitan Transit System
Sr. Project Dir., Purple Line MDOT MTA
Ken Luebeck, P.E. Project Mgr., Systems Engineering Benesch
Stephen Cusick, P.E. Cabinet Chief of Sta –Capital Delivery Sound Transit
Get PDHs At Your Own Pace With Arema’s On Demand Education
Access to important professional development content is just a few clicks away with AREMA Education. Our On Demand content spans many disciplines of PDH accredited courses that allow you to get your PDHs by learning from experts online without leaving your office.
BENEFITS OF LEARNING ONLINE
1. LEARN MORE
Studies show that participants learn more while taking On Demand courses as you can skim through the material you understand and take more time in the more challenging areas.
2. GET INSTANT ACCESS
With AREMA On Demand courses, you don’t have to wait to learn and get your PDHs as they’re available instantly after purchase.
3. CONVENIENT AND FLEXIBLE
Above all things, On Demand education is meant to take at your own pace and on your time. Study from anywhere in the world, whether from your office or the convenience of your sofa.
4. COURSE VARIETY
AREMA On Demand education offers a wide variety of topics for all studies of the railway engineering community.
Register and Start Learning today at www.arema.org.
BECOME A MEMBER AND SAVE
Not an AREMA member? Join today at www.arema.org and get discounts on all AREMA Educational Offerings, from Virtual Conferences to our Webinars.
BILL RIEHL AREMA President 2024
Last month, I touched on AREMA’s Updated Strategic Plan that was unveiled at the Annual Conference & Expo. is Plan was last updated in 2018 and revised in 2019. While it served the association well over the last six years, it was time for an update.
In 2022, President Hudak appointed the Strategic Planning Committee. As background, the Strategic Planning Committee is a Standing Committee of AREMA and reports to the Board of Governors. It is chaired by the current President and is charged with ensuring AREMA’s governing documents remain relevant for the needs of the Association in an ever-changing landscape. e governing documents include the AREMA Constitution, Bylaws, Technical Committee Regulations and Procedures, Technical Committee Supplemental Operating Procedures, and the Strategic Plan.
In addition to the President, the other members of the committee are the Past President, Senior Vice President and Treasurer. Also, four other Past Presidents served on the Committee and included Jim Kessler, Mike Freeman, Ed Sparks, and Vic Babin. rough this committee, discussions began on the development of the next iteration of the Strategic Plan. is was driven in large part by wanting a Plan that was a Dashboard or document that could easily tell AREMA’s story and direction. For the Strategic Plan Dashboard project, the Strategic Planning Committee met frequently, and additional input was solicited from each of the Functional Groups, Members, active young professionals, and AREMA Sta . Additionally, responses from
past member surveys were also reviewed.
A er many discussions and iterations, President Verrelle moved the Plan over the nish line for Board of Governor approval in February and an unveiling of the Plan in Louisville.
As you would expect, a Strategic Plan drives the long-term direction and ensures investments in resources, time and talent t that direction. is update to the AREMA Strategic Plan will be no di erent. What is new to this version is the concept of four pillars or focus areas. ey are Knowledge Delivery, Industry Networking, Technical Expertise, and Workforce Support. Each of the pillars has its core tenants that de ne the goals of the pillar.
Amassing the greatest source of practical knowledge and innovation is pointless if we do not e ciently share that knowledge with those who need it to be e ective in solving their current challenges. Obviously, AREMA knows how to put on a great Conference and Expo like the one just held in Louisville, where we were able to present to over 3,000 attendees. But is that enough? at’s just half of our own membership. What about all the other railroaders ghting their own challenges? How do we make sure our collective lessons learned get in their hands so they can move on to the next problem? is will be our focus as we grow how AREMA delivers content to a wider audience.
Recently, Committee 15 teamed with the American Institute of Steel Construction’s National Steel Bridge Alliance to create the “Guidelines for the Design of Steel Railroad Bridges for Constructability and Fabrication.” is is the rst manual of its kind, and it directly links the needs of modern steel railroad bridges with the capabilities of the steel manufacturing and fabrication industries. As AREMA grows the foundation of its recommended practices, we need to partner with the other associations that touch our space to ensure our manuals re ect the best knowledge available.
When it comes to railroad engineering, there is no greater source of knowledge than within our membership. Sure, there are smart people all over the world driving new
technology. However, there is no greater body of knowledge in railroad engineering innovation beyond our almost 6,000 members. We just need to unlock our collective potential. First, we need to reduce barriers that impede member engagement. Next, we need to focus on streamlining our recommended practices so that they re ect the best railroad speci c information available. is can be achieved by ensuring the Functional Groups work together in a systems approach to reduce duplication of e orts.
For AREMA to increase its membership, we must meet the needs of future members. Some programs are well established such as the network of student
chapters and the student and young professional programs at the Annual Conference & Expo. However, other programs are still in their infancy. We remain a heavily Civil Engineering based membership and continue to struggle to capture the front-line supervisor along with the other disciplines in the industry. The majority of our content remains technical in nature. However, I would argue that leading in our environment, where one poor decision can snarl a network for days, is different from other industries. In addition to sharing the best engineering practices, we need to expand our content offering to cover those soft skills that are unique to railroading.
These are exciting times in AREMA
engineering association for North American and International railways and
as we look to the future. Our financial position has moved from one of survival to stability. This means we are now able to invest in the organization unlike any time in the past. From an update to our member management system and website refresh expected in 2025, to enhancement of our learning management system, we are now positioned to make strategic investments in the association infrastructure. Each new project and offering will be measured against the Strategic Plan and those projects that deliver the most value to the Plan will be considered first.
If you have any thoughts or ideas on future projects, raise your hand and get involved. This is your association. Help shape its future.
On September 18, 2024, during the closing General Session of the AREMA 2024 Annual Conference & Expo in Louisville, Kentucky, new leaders for AREMA’s Technical Committees and Boards were officially installed. We welcome the railway industry’s latest volunteer leaders! For
Connected
volunteer opportunities, please email info@arema.org.
Leadership Roles Overview:
• AREMA Board of Governors: is governing body sets the strategic direction and policy for the Association.
• Functional Group Board of Directors: Responsible for overseeing Technical
Committee operations, monitoring committees, and approving their structure and assignments.
• Technical Committees: AREMA has 30 committees that develop technical content, including recommended practices, plans, specifications, and educational resources for the railway industry.
Thank you for attending the AREMA 2024 Annual Conference & Expo in Louisville; we hope you had an excellent experience. If you registered as a full Conference Attendee, you will get access to the On Demand AREMA sessions recorded during the event. Stay tuned for details.
Unlock the essential resource for designing steel railroad bridges with the AREMA/NSBA Guidelines for the Design of Steel Railroad Bridges for Constructability and Fabrication. This comprehensive guide offers insights on cross-section types, corrosion protection, and construction techniques to enhance constructability, all while complementing the Manual for Railway Engineering. Download it for free at www.arema.org to streamline your design process and improve project outcomes.
Registration opens in October for the AREMA 2025 Railroad Bridge Symposium, taking place February 4-6 in Fort Worth, TX. Get involved today by exploring
sponsorship opportunities that will help support supervisors and engineers as they share the latest advancements in railroad bridge structures. For more details, visit www.rbs25.arema.org.
Did you know we offer a wide variety of on demand education for learning on your time? Browse our most popular webinars, seminars, and Annual Conferences to earn your PDH credits on the go. Visit www. arema.org to start your On Demand education today.
Download the AREMA 365 App for essential rail resources and networking opportunities. Easy access to news, events, and educational materials lets you stay informed and connected to the industry. Download it today by searching for AREMA in your phone’s app store.
Don’t miss out on the conversation in AREMA’s Member Forum. The Member Forum connects you with other Members, allowing you to send messages, start
conversations, and more. See what everyone is talking about today: https:// community.arema.org/home.
If you’re looking for a podcast to binge, listen to AREMA’s Platform Chats. It features guests from every aspect of the railway industry. Catch up on all four seasons available on all your favorite listening services today.
Leverage the power of your trusted association’s Railway Careers Network to tap into a talent pool of job candidates with the training and education needed for long-term success. Visit www.arema. org/careers to post your job today.
JANUARY 23-24
Committee 8 - Concrete Structures & Foundations
Las Vegas, NV
Join a technical committee
FEBRUARY 3-4
Committee 15 - Steel Structures
Fort Worth, TX
MAY 22-23
Committee 8 - Concrete Structures & Foundations Tucson, AZ
Joining a technical committee is the starting point for involvement in the Association and an opportunity for lifelong growth in the industry. AREMA has 30 technical committees covering a broad spectrum of railway engineering specialties. Build your network of contacts, sharpen your leadership skills, learn from other members and maximize your membership investment. If you’re interested in joining a technical committee or sitting in on a meeting as a guest, please contact Alayne Bell at abell@arema.org. For a complete list of all committee meetings, visit www.arema.org
ERIC J. FROSTESTAD, PE | 2024-2027
Sr Railroad Project Engineer, HDR Committee 1 – Roadway & Ballast
LARIZA STEWART | 2024-2027
Director of Data Management and Digital Solutions, ENSCO, Inc. Committee 2 – Track Measurement and Assessment Systems
W. BRIAN MULLINS | 2024-2027
Mgr Rail Welding, Norfolk Southern Railway Committee 4 – Rail
ALOIS J. KOSTELNIK, PE | 2024-2027
Principal Engineer, ARCADIS Committee 6 – Rail Facilities, Utilities and Buildings
PAUL B. MICHIELS, PE | 2024-2027
Structural Practice Leader - Rail/Industrial, Wilson & Company, Inc.
Committee 8 – Concrete Structures & Foundations
SEAN COONEY, PE | 2024-2027
Senior Project Manager - Rail and Movable Bridge, HNTB Committee 9 – Seismic Design for Railway Structures
WILLIAM S. RIEHL, III, PE, F.SAME | 2024-2025
Chief Engineer Structures, Genesee & Wyoming Inc. Board Role - President
RAYMOND G. VERRELLE, JR., PE | 2024-2025
Vice President/Sr Project Director - East Region, HNTB Board Role - Past President
KATE O’CONNOR, PE | 2024-2027
Chief Engineer, Bridges & Buildings, SEPTA Board Role - Governor
JERRY W. SPECHT, EIT | 2024-2025
Asst. GM - South S&C Operations, CPKC Board Role - Senior Vice President
CASSANDRA M. GOUGER, PE | 2024-2027
Sr. Director Design, Union Pacific Board Role - Functional Group Vice President, Engineering Services/Re-elected
JARED HOPEWELL | 2024-2025
AVP Communications and Signals, Norfolk Southern Corporation Board Role - Functional Group Vice President, Communications, Signals & Information Technology
PETER T. MASSON | 2024-2027
Principal, TRC Companies Committee 13 - Environmental
SKYLAR M. LEACH | 2024-2027
Manager: Work Planning & Major Outages, Amtrak Committee 17 - High Speed Rail Systems
CARLOS AGUILERA | 2024-2027
Signal R&D - Engineer Signals III, BNSF Railway Committee 39 – Positive Train Control
JOSEPH PRZYBYLOWICZ | 2024-2027
Director Telecom., BNSF Railway Board Role - Director, Communications, Signals & Information Technology
KRISTA L. KEENE, EIT, MSE, MBA, PMP | 2024-2027
Director Real Estate – Utility Occupancies, Amtrak Board Role - Director, Passenger & Transit/Re-elected
JASON HALE, PE | 2024-2027
Asst Director Bridge Inspection & Maintenance, BNSF Railway Board Role - Director, Structures
CHRISTOPHER S. MOALE, PE | 2024-2027
Director Engineering Testing, Genesee & Wyoming Inc. Board Role - Director, Track
COMPANY
AREMA
Brandt Road Rail
DavRail
Light Rail
Loram Maintenance of Way NRC
Railway Educational Bureau
Stella-Jones Corp
Women In Rail
WVCO Railroad Solutions
PHONE #
301-459-3200
306-791-7541
817-201-0157
212-620-7200
763-478-2627
402-346-4300
800-272-8437
203-791-4507
212-620-7200
E-MAIL ADDRESS
marketing@arema.org MHaliwyz@brandt.ca jalopez@davmarketing.com www.railwayage.com/lightrail alexis.b.nubbe@loram.com www.nrcma.org bbrundige@sb-reb.com kdulski@stella-jones.com ww.railwayage.com/womeninrail wvcorailroadsolutions@wilvaco.com
Reader Referral Service
This section has been created solely for the convenience of our readers to facilitate immediate contact with the RAILWAY TRACK & STRUCTURES advertisers in this issue. The Advertisers Index is an editorial feature maintained for the convenience of readers. It is not part of the advertiser contract and RTS assumes no responsibility for the correctness.