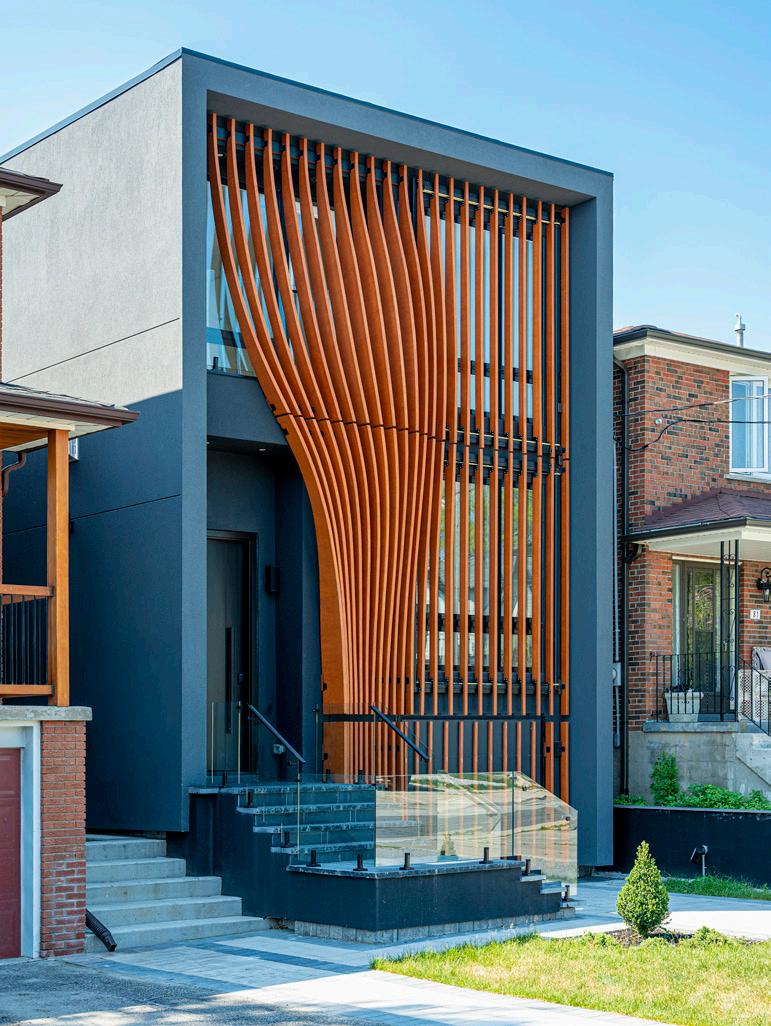
1 minute read
83 VIRGINIA SECOND SKIN
Constructed
Toronto, Canada | 2021 build these elements, we used standard exterior plywood and coated them with natural oil wood stain.
Advertisement
Role: Associate Designer and Fabricator (only the wooden second skin), Meanders Co.
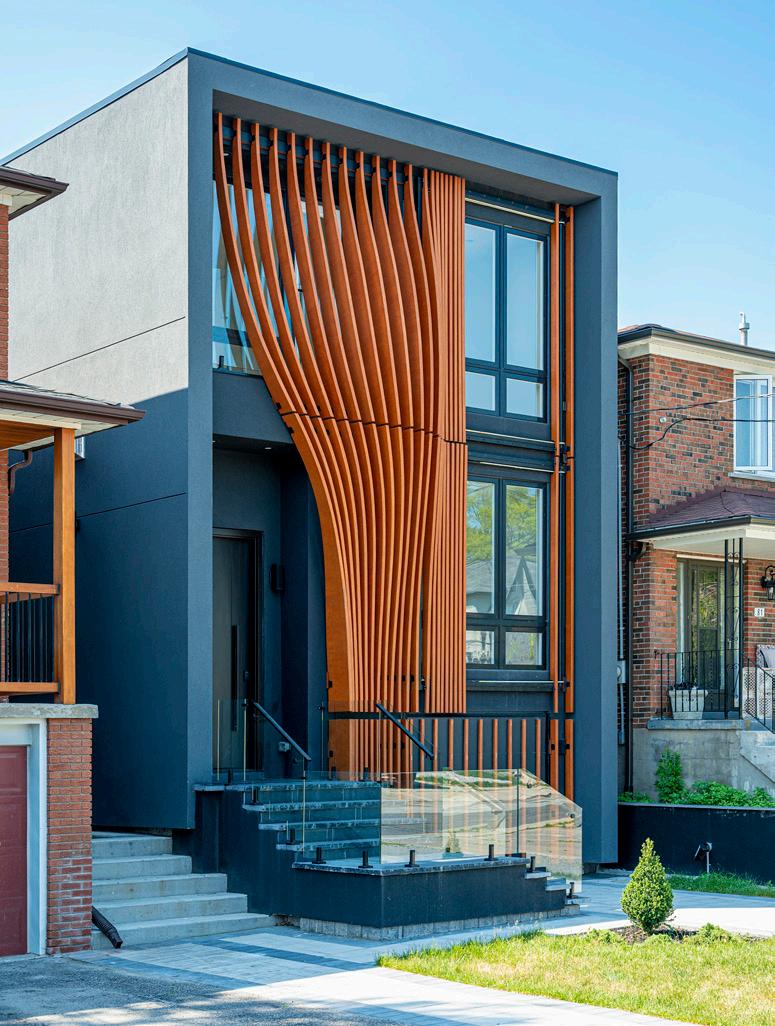
Credits: Photos by Meanders and diagrams by Hanie Omid.
Top: The second skin form generation.
Bottom: Open and closed form.
The mold and fabrication process of each element. Each element needed a unique mold, and the molds were built two-sided to save material consumption. It takes a day for the glue activation process, and we could only fabricate two elements per day.
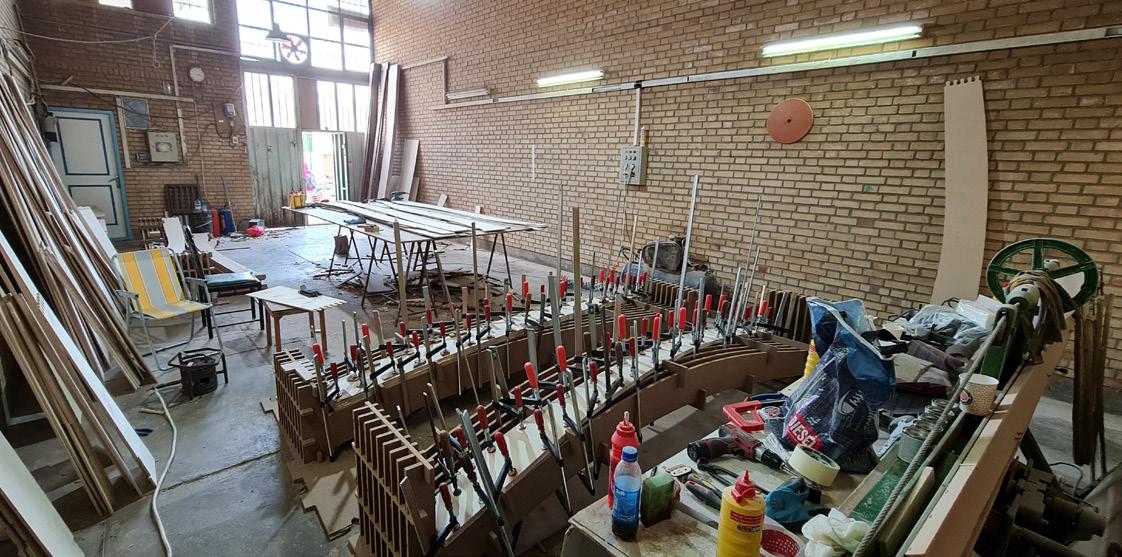
This project is a second skin for a residential facade in Toronto that covers the windows to control daylight. The elements are fabricated from 5 layers of 9mm thick plywood glued together in a mold’s curved shape. Due to the parametric form of the facade, each element had its unique mold made by MDF using a CNC milling machine.
Each element had a specific shape, and each layer of the elements was different from the others and unrolled with Grasshopper 3D and made by a CNC machine. Two parts of the facade had retractable elements that could open the view of the user according to user needs.

All elements were fabricated in Iran and shipped to Canada by a container. The mechanical components of the retractable parts are assembled on stainless steel in Iran, while the windows’ sizes are larger than the container’s width. Thus, the customized container was built with angled racks to handle and grab the oversized frames.
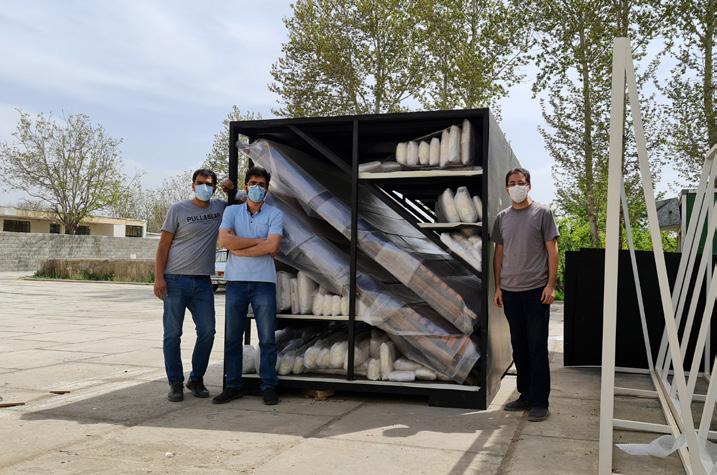
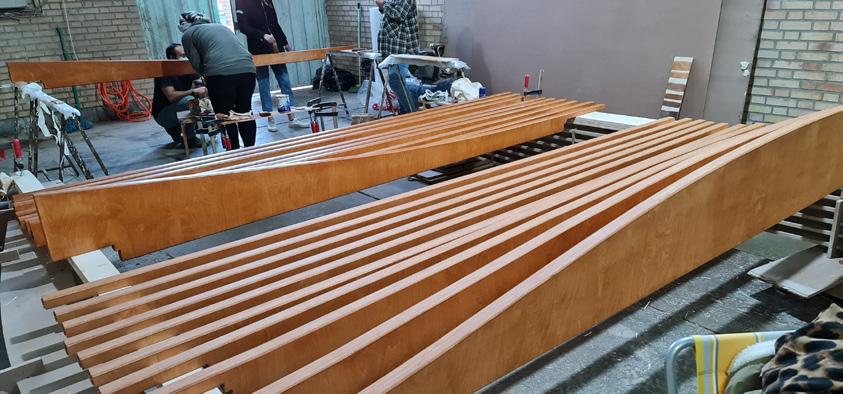
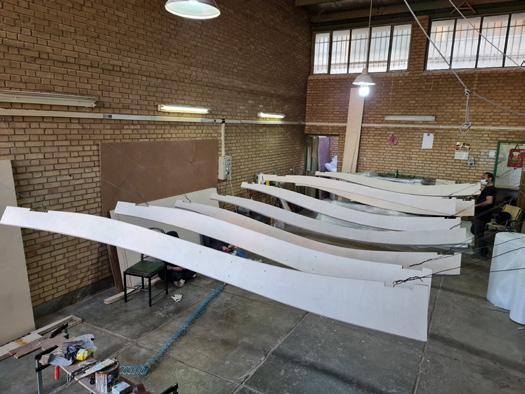
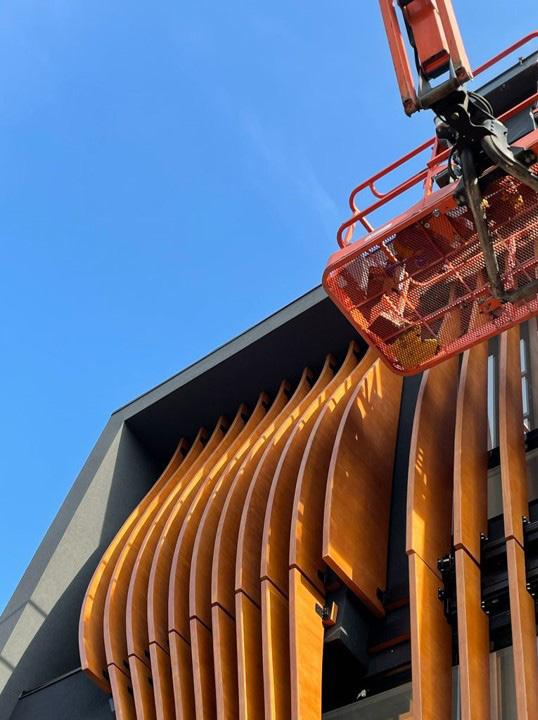
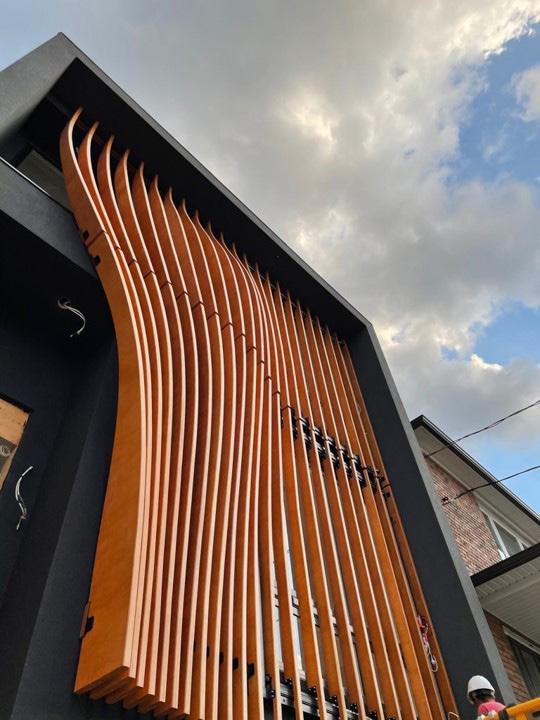
