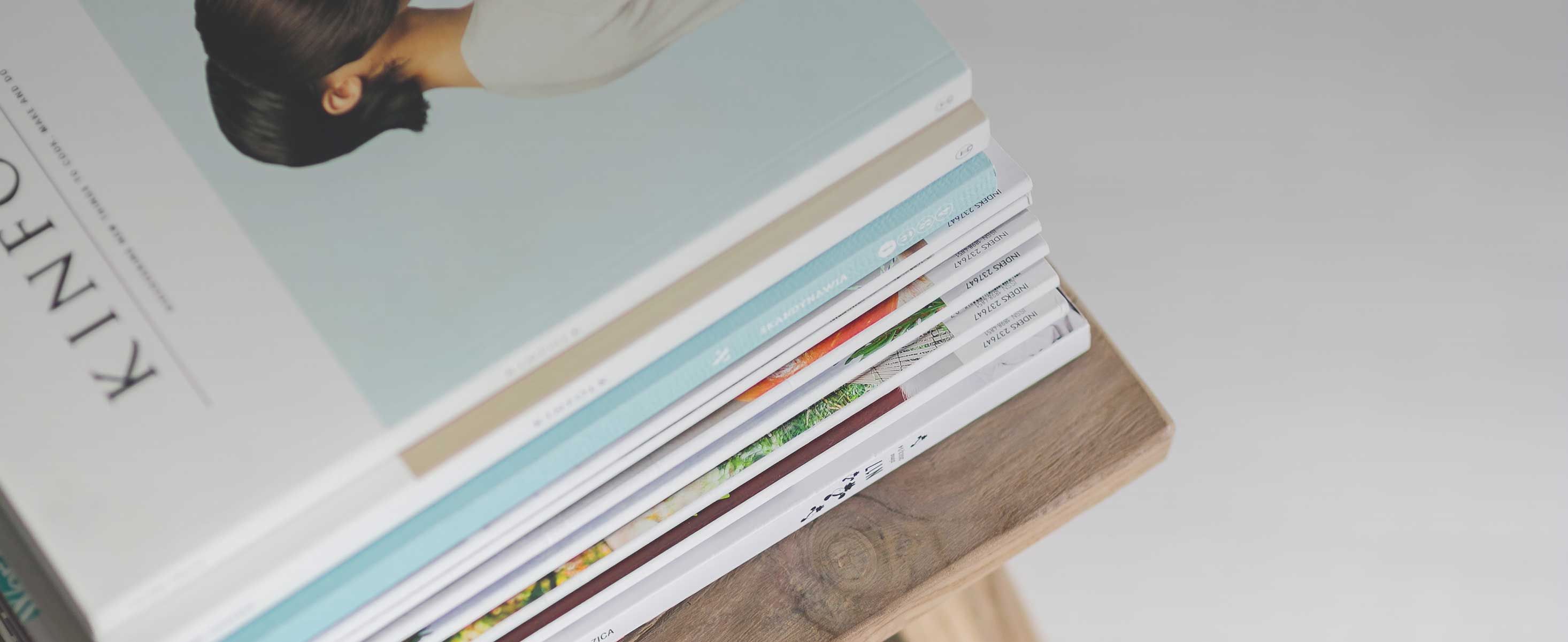
1 minute read
CADF96
COMPUTER AIDED DESIGN AND FABRICATION Tehran, Iran | Fall 2018
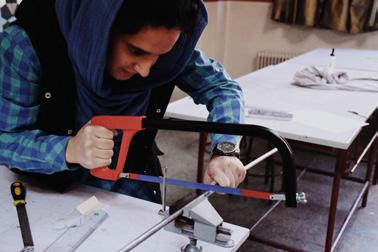
Advertisement

Role: Lecturer at the University of Tehran Credits: Photos were created by the workshop students and instructors.
Like the previous CADF program, in this course, students tried to experience another type of fabrication. This year, students wanted to work on a spacial lattice structure using 3D printed joints.

Dahi Design Studio and Kade 3D printing lab were the commercial sponsors of the projects, providing 3D printers freely. The final installation was a 4-meter height column.
At first, students studied the basics of computational design, and after that, students started to make proposals for an installation. In the second phase of the class, five groups prepared a proposal for the final product. Proposals contained various techniques and generated a digitally fabricated model. All of them, which are presented in the pictures, demonstrate the technique of the fabrication. Finally, students voted, and the first technique was selected for the final project.
In the final sector, students finalized the design and selected PLA as the final material; then, they developed the code which was able to generate all the details and shop drawings. All the joints were 3D printed and assembled by students.

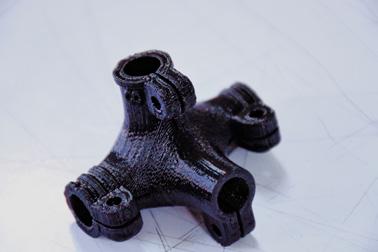
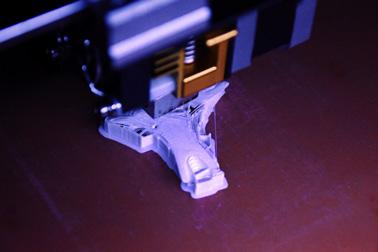
All of the linear elements are 1cm diameter steel pipes. The thickness of the pips is 0.1cm, and the joints are the rigid type made by PLA. Therefore the weight of the structure is less than 50kg, although it can carry loads much more than its weight because of the space frame feature.
Wires ended to a joint | Sphere as the basic geometry to calculate intersection | Basic mesh, containing convex hall of the points from intersection plus sleeve of the elements | Relaxed mesh | Final Model