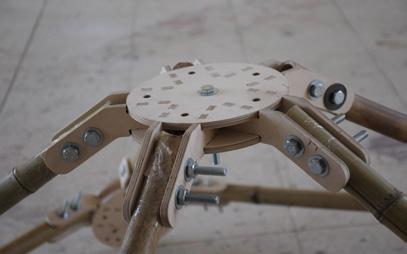
3 minute read
FSS#4
BAMBOO-BAM
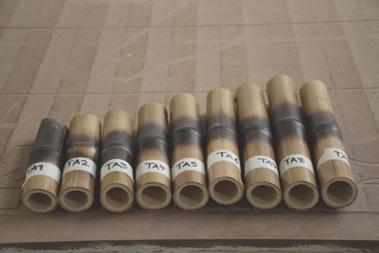
Advertisement
Yazd, Iran | Winter 2020
Role: Manager and Tutor
Credits: Photos and diagrams were created by the workshop students and instructors. https://issuu.com/ramtinhaghnazar/docs/bamboobam_-_a4_001113
Freeform Space Structure Workshops are held for research and practice of the two areas of “free form structures” and computer integrated “construction and design” methods. Each of these training programs deals with a specific way of constructing free form structures. This workshop was held with the participation of 42 students in 6 groups. 13 instructors helped them through the research and development process within four months.
During its process, the workshop tried to cover five major research areas: material studies, sustainability, computational design, form-finding, structural design, and digital fabrication. These disparate fields demand a diversified set of skills, abilities, and experiences. We had instructors and partners from various institutions and backgrounds who willingly offered to share their talents and expertise to ensure that we could cover the topics to the extent required for a workshop.
In the first chapter of this summer school, a team was tasked with researching bamboo as a natural, non-standard material, its qualities, applications, and construction possibilities. Following that, we conducted a market survey to determine the sorts of bamboo available. We identified four varieties and conducted a preliminary investigation, evaluating their quality, geometric and mechanical features, and workability, among other characteristics.
In the second chapter, in a series of brainstorming sessions, various systems were proposed until a handful of them were shortlisted. The shortlisted systems were then prototyped, with the fabrication method for each being investigated. We undertook an evaluation procedure based on several criteria to determine the benefits and drawbacks of each system. We chose the final of these four options and proceeded with it.
Evaluation Criteria:
- Visual elegance
- workability
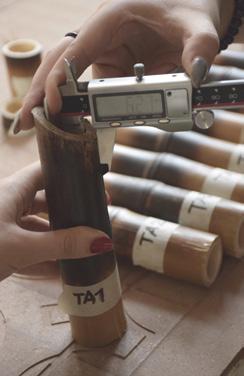
- Structural Performance
- Durability
- Cost
Images: we developed a “digital design workflow” in a parametric modeling platform known as “grasshopper”. This digital workflow fully automates the modeling process and delivers the required outputs in a timely manner. The workflow starts with getting two general inputs from the user: first, the wire mesh generated during the form design phase, and second, some numerical inputs about bamboo, CNC machine, Bolts and nuts, and node design preferences.
Left - Studying the accessible bamboo material (local species) and gathering its properties like thickness, dimensions, and strength. Additionally, researchers test the effect and functionality of digital fabrication tools such as laser cutters and CNC milling machines.
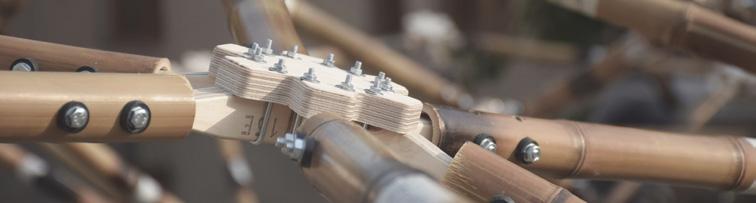
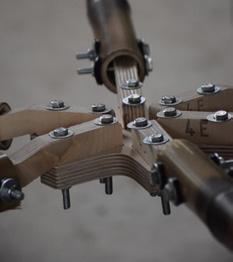
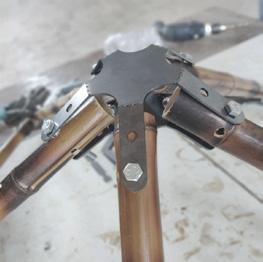
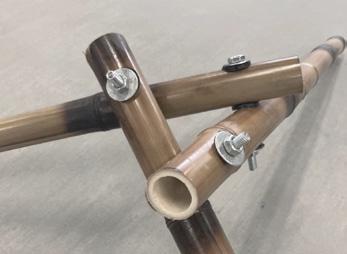

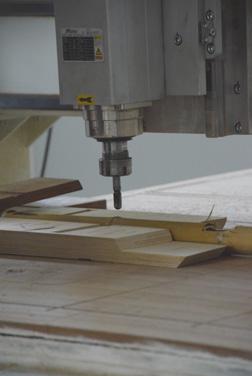
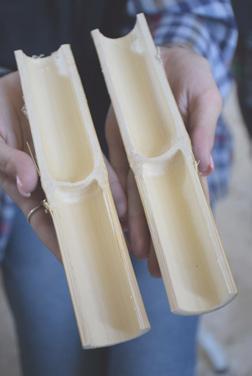
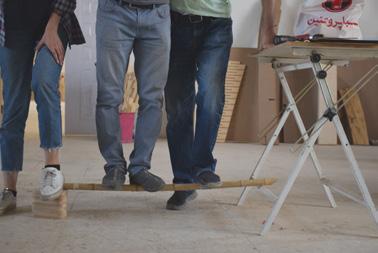
Right Top - Prototypes of the joint systems.
Right Bottom - Final joint.
After collecting and interpreting these data, it generates a completely comprehensive 3D model with labels for each element. As a result, it can be utilized as a coordination model during the assembly process.
For the bamboo poles, we understood they would need four bolts at each end and not alighned to one another to connect to their respective joints. Three-axis CNC milling machines already existed that could drill vertically through the bamboo poles. Our poles couldn’t be rolled due to the fact that the drilling was only going one way. A rotary axis that was not affordable and might not fit our CNC bed had to be purchased or we had to design a custom one. We decided to go for the latter solution.
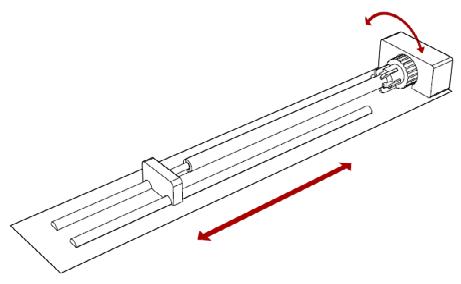

The rotary consisted of three main parts. A gripper to grab the pole firmly in place while drilling and meanwhile align its center to the rotary axis. A rail and an adjustable wagon for different pole lengths. And a rotator to orient the pole at the right angle.
We decided to buy a low-cost 3-jaw concentric gripper for one end and 3D print a cone-shaped piece for the other end that would attach to a plywood wagon. It was built to go easily along the Y-axis on a rail, making it flexible to the length of the bamboo pole.
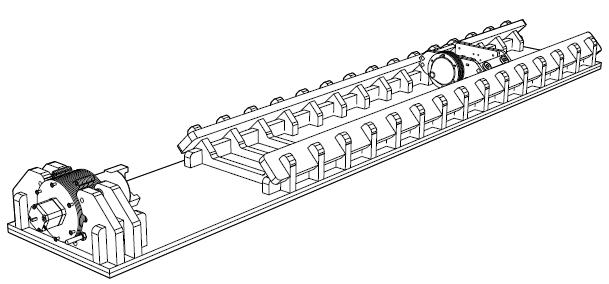
Images:
For the rotator, we built a harmonic drive, also known as a strain wave gear, using 3d printed and laser cut parts, ball bearings and a stepper motor along with An Arduino board.
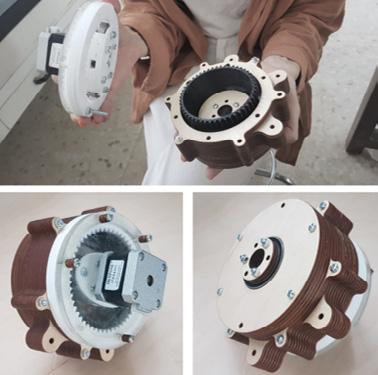
With the rotary axis in place, We only needed the precise toolpath to drill the poles with our CNC milling machine and the correct angle to rotate the poles after drilling the first two holes after the rotary axis was in place. The rotation angles of each pole are collected from the grasshopper BIM model and used to construct the Arduino program for each rotation.
Images: Fabrication and assembly process.

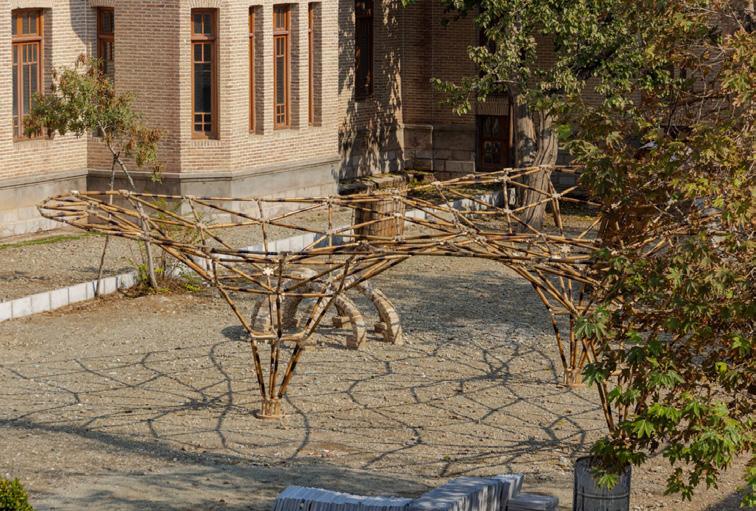
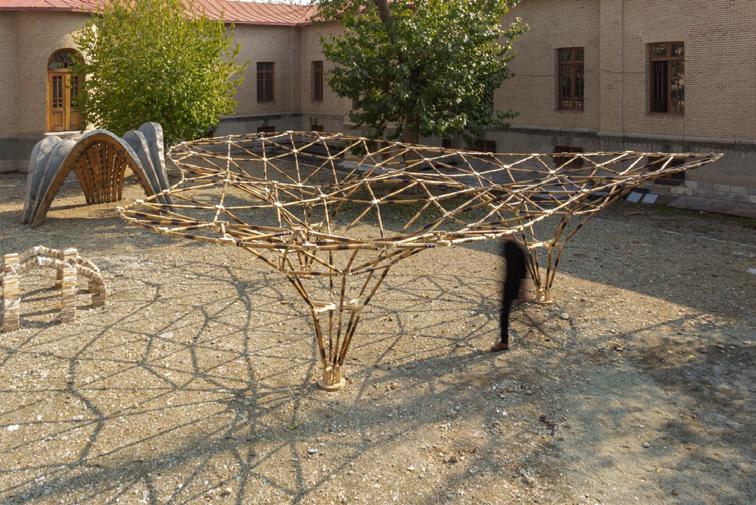

