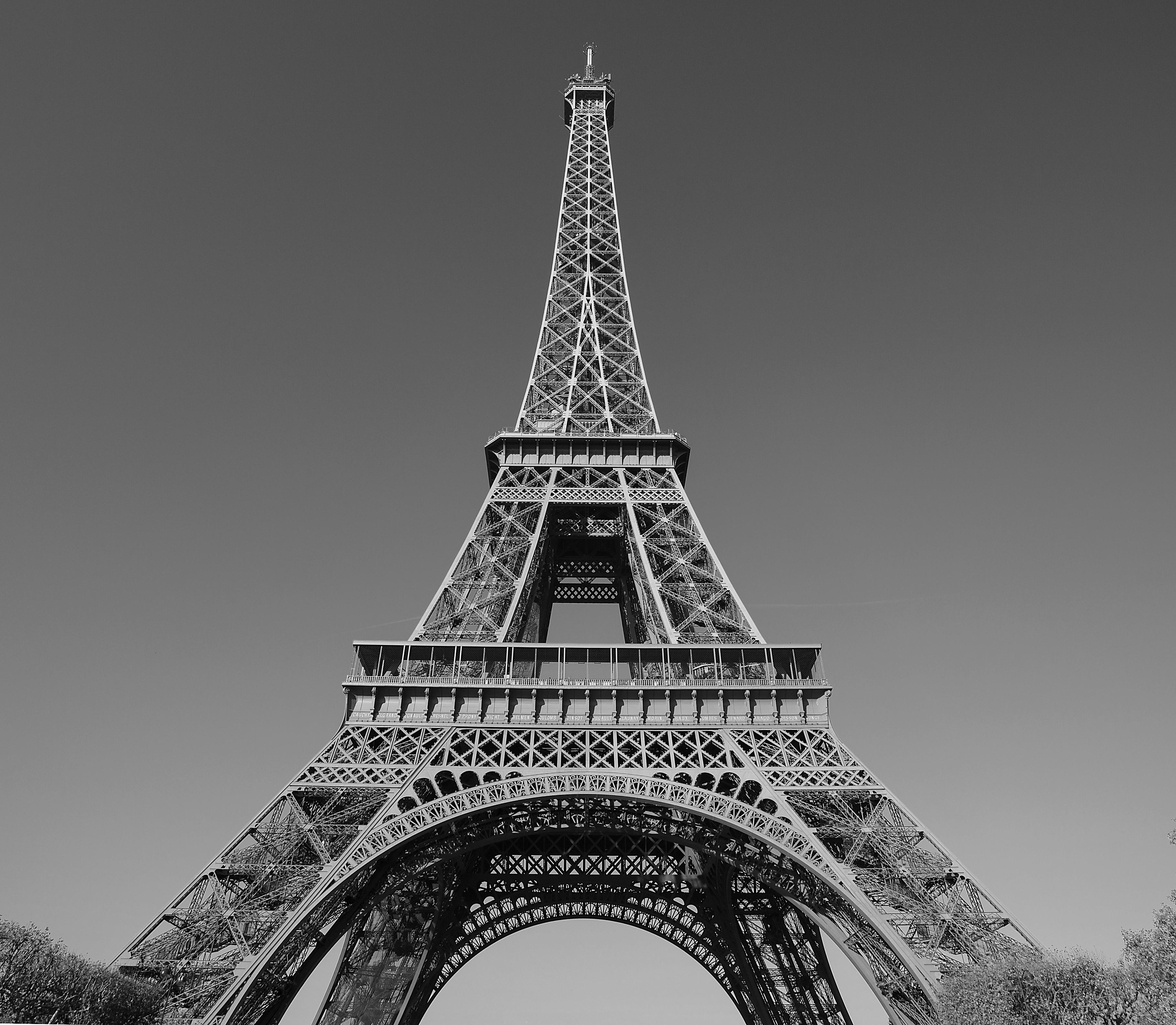
6 minute read
FROM THE EIFFEL TOWER TO THE FUTURE
THE EVOLUTION OF PREFABRICATED AND MODULAR CONSTRUCTION. A LESSON IN HUMAN INNOVATION
The pioneering vision of Gustave Eiffel back in 1889 sparked a revolution in construction methodology, proving that large structures like the Eiffel Tower could be efficiently and effectively constructed using prefabricated components. Architects like Moshe Safdie with Habitat 67 and Kisho Kurokawa later championed this construction approach with the Nakagin Capsule Tower, who further explored the potential of modular design in residential living spaces. Today, in the face of pressing global housing needs, the construction industry is again turning to prefabrication and modular techniques, integrating advanced technologies and smart building solutions for improved efficiency, sustainability, and affordability.
Advertisement
Here we embark on a journey through the evolution of prefabricated construction, from the groundbreaking iron components of the Eiffel Tower to the smart, factory-built homes of today’s leading startups. Join us as we explore this transformative industry’s past, present, and future.
LET’S START WITH THE EIFFEL TOWER
When you think about innovative construction methods, the first thing that may come to mind isn’t the Eiffel Tower. Built in 1889, this French icon by Gustave Eiffel is one of the earliest and most iconic examples of prefabricated construction.
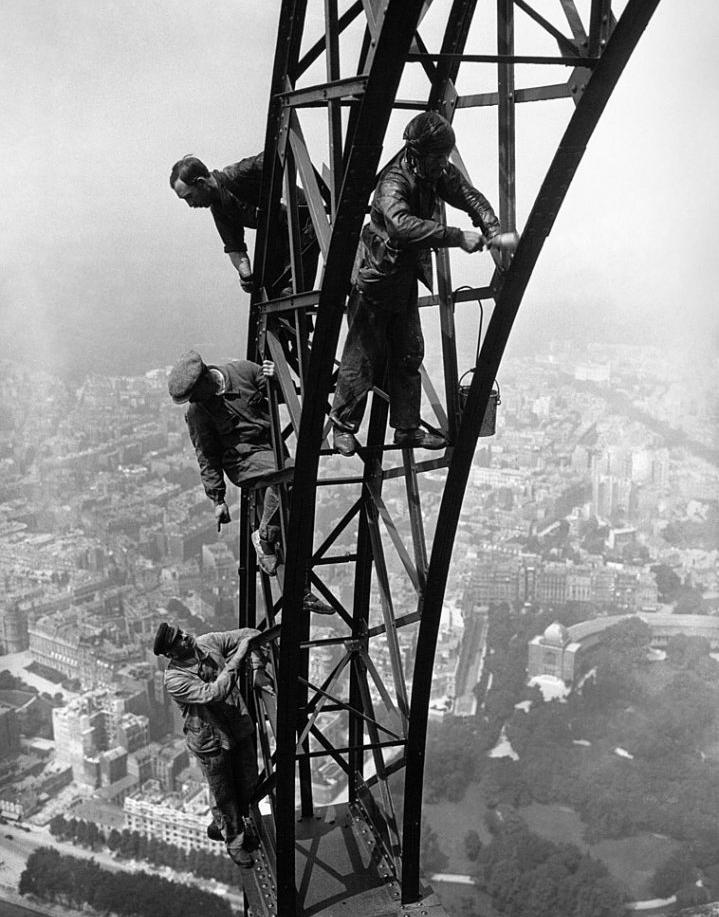

In 1889, Gustav Eiffel was already mastering the art of prefabrication. His iconic Parisian masterpiece, the Eiffel Tower, stood tall as a testament to innovative and effective prefabricated construction methods. Every part of this historic structure was carefully designed and produced off-site, then assembled on-site with extraordinary precision. This early example of the possibilities of prefabrication provided an efficient, cost-effective, and innovative construction solution that would set the stage for future developments in the industry.
When Gustave Eiffel unveiled his monumental tower in 1889, he showcased a marvel of design and a pioneering example of prefabricated construction. This engineering feat was achieved thanks to thousands of individual iron components fabricated off-site and meticulously assembled on-site, setting the stage for a revolution in construction methodology.
Eiffel utilized the precision of machine manufacturing to prefabricate over 18,000 individual iron components. These parts were designed and assembled with an accuracy of a tenth of a millimetre, allowing them to be fitted together seamlessly on-site without any extensive adjustments. It demonstrated that buildings could be constructed faster and more accurately with prefabricated components, forever altering the landscape of architectural engineering.
Eiffel’s genius lay in using pre-made iron components assembled with extreme precision. The entire structure was designed and fabricated in Eiffel’s factory in Levallois-Perret on the outskirts of Paris. The 18,000 individual iron pieces were precisely manufactured off-site and then transported for assembly, an approach that revolutionized the construction industry.
HABITAT 67: THE MANIFESTO OF MODERN MODULAR DESIGN AND WHERE MODERN PREFABRICATION BEGINS
Fast forward to the 1960s, Habitat 67, designed by Moshe Safdie for the Montreal World Expo, heralded a new era in modular design. His innovative design featured 354 prefabricated concrete forms arranged in various combinations, creating 146 residences of varying sizes and configurations.

The 1967 World Expo in Montreal showcased a unique project, Habitat 67, that sparked new ideas for residential design. Architect Moshe Safdie designed it as a housing complex that combined prefabricated and modular techniques. The project featured 354 identical, prefabricated concrete forms arranged in various combinations, creating 146 residences of varying sizes and configurations. Habitat 67 emerged as a revolutionary housing concept, pushing the boundaries of design and prefabrication and presenting a new approach to high-density urban living.

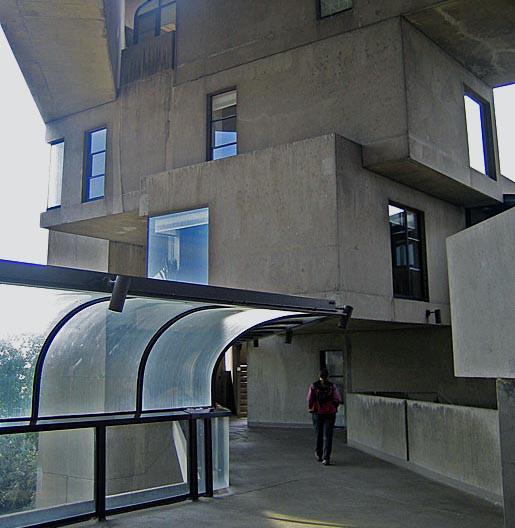
Designed by Moshe Safdie for the Montreal World Expo, it took the idea of prefabricated construction to another level. Safdie’s innovative design consisted of 354 identical, prefabricated concrete forms arranged in various combinations to create 146 residences. This assembly of prefabricated modules displayed the versatility and potential of this construction methodology in creating complex yet efficient residential structures.
This revolutionary housing complex demonstrated the potential of industrialized, prefabricated units. Despite its initial high cost, Habitat 67 represented a transformative vision of urban living, driving the evolution of modular construction.
NAKAGIN CAPSULE TOWER: A SYMBOL OF JAPANESE METABOLISM

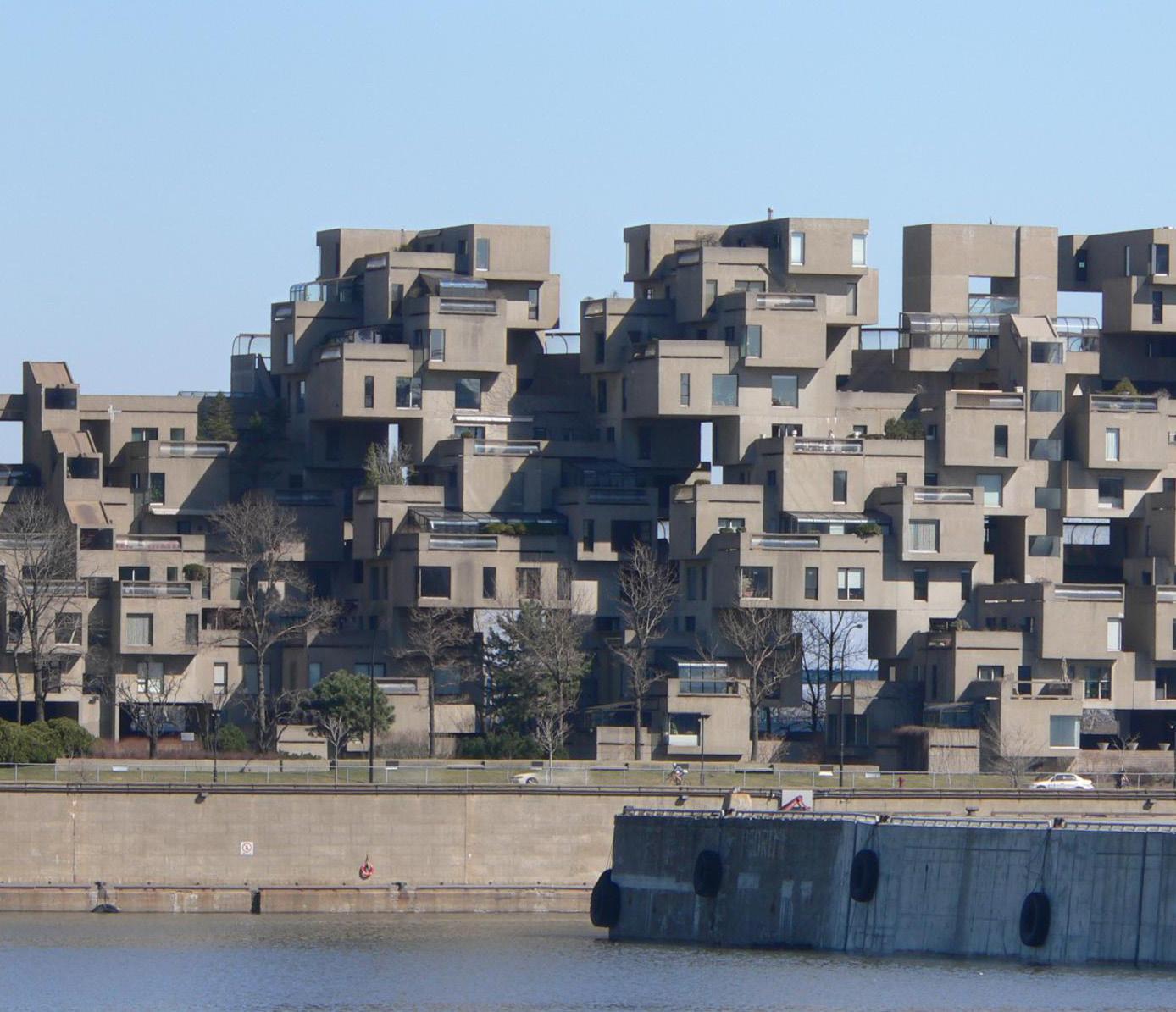
Kisho Kurokawa’s Nakagin Capsule Tower, built in Tokyo in 1972, further advanced the modular construction concept. The tower consists of 140 prefabricated modules, or “capsules,” intended to represent the dynamism of the post-war economic boom in Japan. Although it faces demolition threats, it remains a symbol of the Japanese Metabolism architectural movement and its aspiration to adapt and grow with changing societal needs.
Further embracing the modular approach, Japan’s Nakagin Capsule Tower, designed by Kisho Kurokawa in 1972, incorporated compact, interchangeable capsules to provide flexible living and working spaces. This served as a testament to the adaptability and sustainability of prefabricated construction, echoing its time’s societal and technological changes.
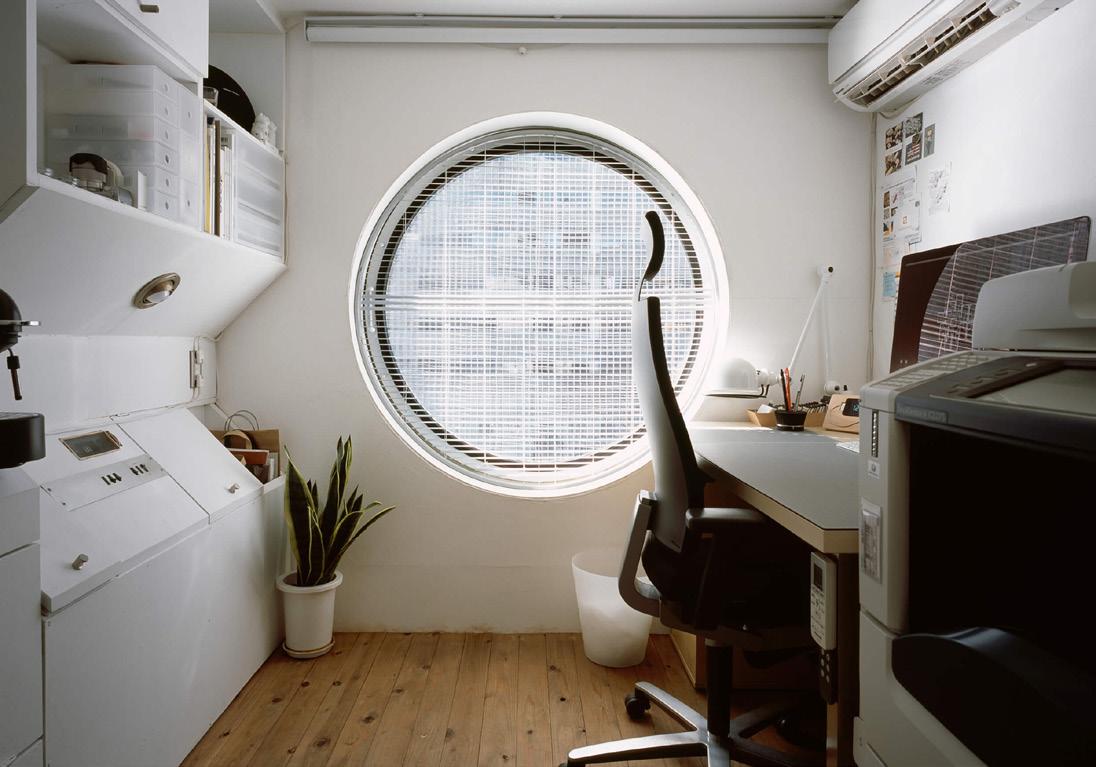
This iconic residential and office tower in Tokyo, designed by architect Kisho Kurokawa, embraced a unique form of modular construction. Completed in 1972, the tower consists of 140 independent capsules, each prefabricated and equipped with all the necessities for living or working. They can be individually replaced or reconfigured, showcasing modular architecture’s extreme flexibility and adaptability.
The Future Is Factory Built
Fast forward to today, prefabrication and modular construction have evolved dramatically, spurred by the pressing need for affordable, efficient, and sustainable housing. Beyond time and cost savings, these methods offer significant benefits, including reduced waste, enhanced quality control, and minimal weather-related delays.
Key technologies have been instrumental in driving this evolution. Augmented reality, AutoCAD, and Building Information Modeling (BIM) have transformed the design and planning stage, enabling seamless collaboration and accurate visualizations. Meanwhile, robotics and new material science advancements have streamlined the manufacturing process, enhancing efficiency and precision.
The Rise Of Modern Prefabrication
Today, the benefits of prefabrication and modular construction are more evident than ever. Prefabrication offers significant savings in terms of time and cost. It simplifies construction, reduces material waste, and ensures better quality control.
With the world’s housing crisis, off-site and manufactured housing solutions have become critical. Prefabricated homes are affordable and efficient to build and meet high standards of quality, sustainability, and design. Prefabricated structures can be produced in a controlled factory setting, eliminating the impact of weather delays and minimizing labour costs. The predictability of this process also allows for precise budgeting and scheduling, offering significant cost and time savings compared to traditional construction.
Smart Building Solutions And Manufactured Housing
Smart building solutions are increasingly integrated into manufactured homes, ensuring energy efficiency and user comfort. Furthermore, state-of-the-art manufacturing facilities are crucial in meeting global housing demand. These factories employ highly controlled production lines to create precise, high-quality building components, which can be quickly assembled on-site.
A Technological Revolution In Construction
The construction industry is experiencing a technological revolution, with innovations like AutoCAD, BIM (Building Information Modeling), augmented reality, robotics, smart building solutions, and state-of-theart manufacturing processes are pivotal in advancing prefabricated and modular construction.
Emerging technologies are propelling the evolution of prefabrication and modular construction. Augmented reality, AutoCAD, Building Information Modeling (BIM), robotics, advanced materials, and smart building solutions play crucial roles.
Augmented reality and BIM allow for precise planning and visualization of construction projects, while AutoCAD facilitates the design of accurate and detailed components. Robotics and advanced manufacturing techniques enhance precision, reduce waste, and speed up production.

AutoCAD and BIM allow precise planning, designing, and managing building constructions. They enable the virtual creation of parts and modules, facilitating a seamless and error-free production process. Robotics and advanced manufacturing techniques enhance efficiency and accuracy in producing prefabricated components. They also contribute to safer working conditions by reducing the need for human involvement in potentially hazardous tasks.
WALL STREET AND SILICON VALLEY: AN UNLIKELY ALLIANCE SEE THE FUTURE OF HOUSING
A new wave of startups, such as Veev, S2A Modular, and Plant Prefab, are capitalizing on these advancements, building state-of-the-art manufacturing facilities to produce factory-built homes and buildings. They are attracting significant investments from Wall Street and Silicon Valley, spotlighting the potential of this industry. Recognizing the immense potential, Wall Street and private investors are heavily investing in this space. Startups like Veev, S2A Modular, and Plantprefab lead the charge, utilizing cutting-edge technology and constructing sophisticated facilities for factory-built homes and buildings.
The potential of prefabricated construction has caught the eye of Wall Street. Investment is pouring into innovative startups like Veev, S2A Modular, and Plant Prefab that employ cutting-edge technologies and establish advanced manufacturing facilities. These firms are not just building homes; they’re redefining the future of the housing industry.
The surge in investment reflects a growing recognition of the transformative potential of prefabricated and modular construction. The sector promises to reshape the future of the construction industry, delivering housing solutions that are efficient, sustainable, and affordable.
These companies represent the construction industry’s future, proving that we can create high-quality, sustainable buildings quickly and affordably. They are leveraging prefabrication and modular construction to redefine how we approach housing, transforming how we live, work, and play.
The journey of prefabricated and modular construction, from the Eiffel Tower to today’s high-tech housing solutions, showcases the industry’s evolution and adaptability. These methods present a compelling solution as we grapple with the urgent need for affordable, sustainable housing. Embracing new technologies and innovative approaches, the construction industry stands at the brink of a revolution – and the future looks modular.