
3 minute read
MODULAR HOUSING AND PREFABRICATION REVOLUTIONIZE SUSTAINABLE CONSTRUCTION
Welcome to the forefront of sustainable construction, where innovative solutions are reshaping how we build our homes. The construction industry is undergoing a green transformation fueled by the need to minimize environmental impact and create a more sustainable future.
Building A Greener Future With Modular Housing
Advertisement
Picture this: a construction process that minimizes waste, optimizes energy use, and significantly reduces the carbon footprint. That’s what modular housing brings to the table. Gone are the days of outdated building practices that harm our environment. Modular homes are sustainability champions, offering a greener option for housing construction. By using materials efficiently and virtually eliminating waste, modular housing plays a vital role in reducing environmental damage caused by traditional methods. It’s not just a trend; it’s the future of sustainable housing.
THE POWER OF PREFABRICATION: A SUSTAINABLE SOLUTION
Let’s talk about prefabrication—a game-changer in the quest for sustainable construction. For over two decades, prefabricated office interiors have proven their worth, and now they’re taking center stage in transforming office buildings into sustainable residential spaces. How does it work? By manufacturing standardized modules off-site, prefabrication dramatically reduces construction waste and optimizes resource utilization. Imagine precise material calculations and efficient operations that minimize environmental impact. Prefabricated interiors offer the ideal solution for converting unused office space into eco-friendly homes while saving costs and promoting sustainability.
Say Goodbye To Onsite Waste And Hello To Efficiency
One of the significant advantages of prefabrication is its ability to minimize onsite labour and waste. Construction crews can focus on assembling pre-made components, saving time, and reducing resource-intensive processes. The streamlined approach leads to cost savings and faster project completion. But that’s not all—prefabricated interiors also help limit the environmental impact traditionally associated with construction projects. By embracing this approach, we’re consciously choosing to build with efficiency and sustainability. Furthermore, the controlled factory environment allows year-round construction, irrespective of weather conditions, accelerating project completion and delivery schedule.
PARTNERING FOR SUSTAINABILITY: Arthrotó AND DIRTT
In the quest for sustainable housing, two visionary companies, Arthrotó and DIRTT, have joined forces to revolutionize the industry. Arthrotó is on a mission to transform unused office spaces into innovative, eco-friendly living areas. And who better to team up with than DIRTT, a global leader in sustainable construction? Together, they drive the industry towards a greener and more efficient future. Through their strategic partnership, Arthrotó benefits from DIRTT’s technology utilization to optimize sustainable construction practices. The result? A streamlined, eco-friendly approach to housing development that meets the highest sustainability standards.
Meeting Esg Targets And Embracing Smart Building Integration
Environmental, Social, and Governance (ESG) targets have driven sustainability efforts in both public and private sectors. Prefabricated interiors play a crucial role in achieving and exceeding these targets. They provide a seamless platform for integrating sustainable features and cutting-edge technologies. From energy-efficient lighting systems to intelligent building automation, these interiors offer endless possibilities. By embracing these solutions, we can optimize energy consumption, reduce carbon footprints, and enhance overall building performance. It’s a winwin for residents, building owners, and the municipalities.
Transforming Vacant Offices Into Sustainable Communities
Imagine the possibilities of converting unused office buildings into thriving, sustainable communities. With prefabricated end-to-end solutions, we can turn this vision into reality. We breathe new life into our urban landscapes by embracing innovation and sustainable practices. These solutions save on labour costs, reduce onsite waste, and meet ESG targets. Moreover, integrating smart building systems ensures efficient energy management and operational cost reduction. Let’s reimagine our cities and create models of sustainability that inspire the world.
The future of sustainable construction is here, and it’s time to embrace it with open arms. Modular housing and prefabrication are leading the charge toward a greener tomorrow, where waste is minimized, resources are optimized, and our carbon footprint is significantly reduced. Through partnerships like Arthrotó and DIRTT, we see the transformative power of collaboration, innovation, and sustainability. Together, we can create thriving communities, repurpose vacant office spaces, and build homes that embody the values of a brighter future. Get ready to step into the modular housing and prefabrication world—it’s a sustainable revolution you won’t want to miss.
Modular construction is 50% more efficient in energy usage compared to traditional construction methods. It also reduces waste usage by 30% and raw material usage by 40%
Prefabrication in construction has the potential to result in higher-quality buildings delivered in a shorter time frame, with more predictable costs
Modular construction minimizes inconvenience to local residents by reducing noise, dust, and construction traffic. It also allows for smaller construction sites and less transport movement, leading to significant reductions in CO2 emissions.
Raw materials are used more efficiently in modular housing, with an efficiency increase of at least 40% during manufacturing.
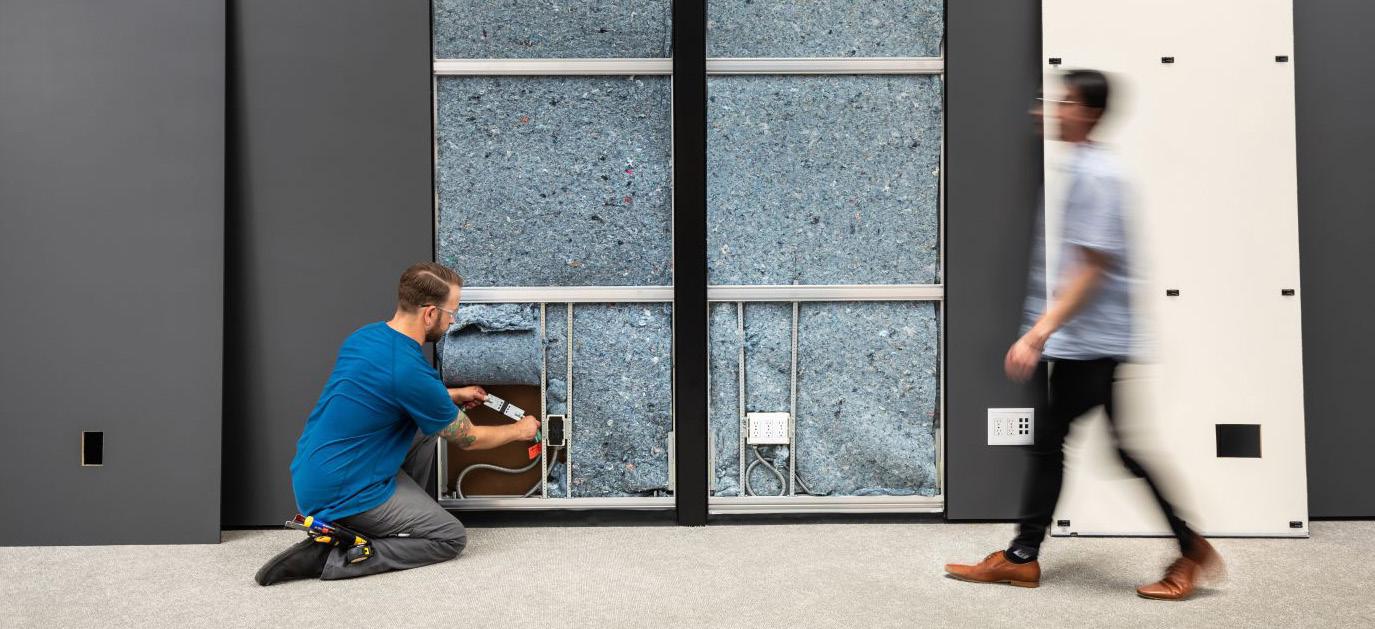
Prefabrication allows for a more efficient use of resources and materials, contributing to the overall sustainability of the construction process.
Incorporating prefabricated elements can make housing construction more affordable and accessible, addressing equity in access to housing.