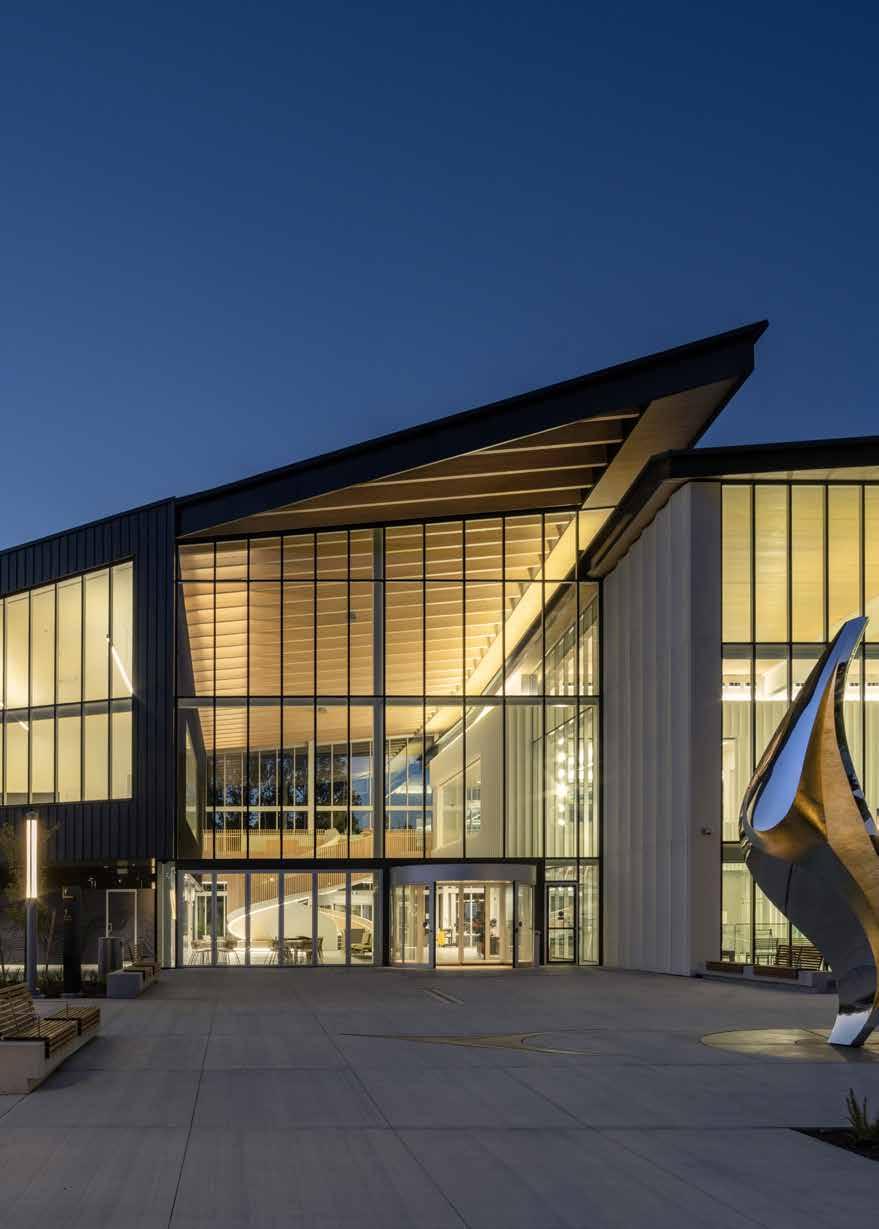
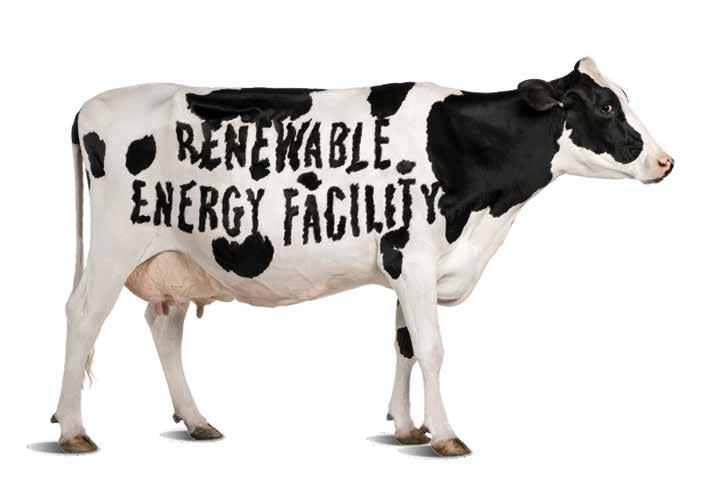
Like biogas captured from cow manure to create Renewable Natural Gas1 (RNG). It’s a low-carbon2 energy that can help reduce overall greenhouse gas emissions, with more RNG projects underway.
Customers can sign up for the voluntary RNG program to designate five, 10, 25, 50 or 100 per cent of the gas they use as RNG.
Find out more about RNG at fortisbc.com/rngbuild.
Vanessa Werden, partner at Jenkins Marzban Logan LLP, is the new chair of the B.C. Road Builders and Heavy Construction Association. She is the third female chair in the association’s 58-year history.
The New Westminster təməsewtxʷ Aquatic and Community Centre is an award winning facility that sets a new standard in design.
Is Payment Protection in B.C. Broken? Reducing Risk in the Face of U.S. Tariffs Cyber Insurance in Construction
Concrete: A Stronger and Greener Future Understanding Bias in Procurement The Importance of Bridge Rehabilitations
B.C. Transportation Consulting Engineers Awards Improving B.C.’s Transportation Corridors
Inquiries:
A significant project that recently completed was the new $39 million Canfor Leisure pool in Prince George. The city is also seeing strong residential development, which has increased significantly over the last few years. Earlier this year, the city reported 2022 saw record-high building permit values at a little over a quarter of a billion dollars.
“In Prince George, we don’t have as many capital projects but residential is very busy,” says Bryant.
IThe NRCA represents 211 members including general and trade contracting companies, manufacturers, suppliers and professional service providers. The association covers the largest geographical region in B.C., spanning from Williams Lake to the Yukon border and from the Alberta border to the West Coast.
t has been a volatile start to 2025 and the word of the year (only a few months in) is tariff. I would never have guessed how dominating the word tariff would become in everything we do and read.
“ We are a staff of three and being a small team, we have to work twice as hard to pull off what we need to do to serve our members,” says Bryant, who knows the region well.
When Scott Bone announced his retirement in 2022, he encouraged Bryant to put her hat in the ring. He was at the helm of the association as CEO for seven years.
“Given my combined knowledge of business development and the construction world, I thought the position was a good fit,” says Bryant, who just completed her bachelor’s degree in marketing at UNBC in April and is now working on a post-graduate certificate in non-profit management at SFU.
While Bryant juggles a range of industry priorities, the issue of prompt payment is a major focus for the association.
demand grows. The situation is particularly acute in northern B.C. with the large number of major projects and small population. Labour reports indicate B.C. will be short 23,000 skilled workers by 2029.
“ Our focus is filling that labour shortage and helping our members become employee of choice so that we can attract more people to the construction industry,” says Bryant.
The on-and-off tariff policies and exemptions from the Trump administration have raised massive concerns and uncertainty as prices are set to skyrocket. The inexplicable trade war attack on Canada has also unleashed a patriotic wave among Canadians, especially with Trump’s inflammatory comments about “annexing” our country.
Born and raised in Prince George, Bryant was exposed to the construction industry at an early age through her grandfather. He had an electrical contracting company called Bryant Electric which he founded in 1960.
job losses and potentially project delays or cancellations. These new policies are expected to disrupt already strained supply chains, and make projects more expensive on both sides of the border. The broader impact on the economy is a potential recession, which could have significant impacts on infrastructure investment and business confidence. All bad news.
“One of the top priorities province-wide is prompt payment,” she says. “It’s an important piece of legislation that’s been tabled time and time again. We are working to push that boulder uphill to see if we can get the attention of the provincial government. Construction is one of those industries where it can take up to 120 plus days to get paid. It’s time that changes.”
Inside this issue, several articles address the impacts of the tariffs and how to remain resilient and minimize risks in the face of the ongoing trade war turmoil.
The association launched its Women in Construction committee last year to address barriers that prevent women from getting into and staying in the construction industry. One of the initiatives was to host a construction camp last summer to provide young women with practical hands-on skills and other training.
Construction Association — the third female chair in the association’s 58-year history. Finally, our feature project takes a look at an award winning aquatic facility in New Westminster that is setting a new standard in design.
“ We conducted a high school youth building program where women came together to build a shed — planning, project management and construction,” says Bryant. “We will auction the shed at the awards gala. It’s an opportunity for them to take pride in the project.”
For the construction industry, the sweeping U.S. tariffs along with Canada’s retaliatory tariffs on materials such as steel and aluminum will lead to price spikes,
“I grew up in the industry and was involved in estimating and project management in both construction and manufacturing,” she says.
Before joining NRCA, Bryant was an account executive at Bell Mobility. She knew many of the NRCA members by offering services and education through an affinity partnership with the association.
Procurement practices are another area of concern where the construction industry continues to call for accountability, transparency and fairness.
For our profile, I spoke with Vanessa Werden, a construction lawyer and partner at Jenkins Marzban Logan. She is the new chair of the B.C. Road Builders & Heavy
“Contractors are bidding on prices good for seven days and the tender doesn’t get decided on for nine days so by the time the contract is awarded, those prices are out of date. That’s how volatile it is,” says Bryant.
Of course, labour shortage remains a pressing challenge and will increase in severity as project
As the number of industry veterans hang up their hardhats over the next decade, recruitment and retention of skilled tradespeople from all underrepresented groups will be critical.
Cheryl Mah Managing Editor
“ We need to really empower our equityseeking groups, who are actively involved in construction or who want to be involved in construction, to see that it is a career choice. It’s not a boys’ club anymore. We’re looking at an equal and open environment,” says Bryant.
BY CHERYL MAH
Vanessa Werden is passionate about giving back. Through her volunteer leadership, she has devoted countless hours to the B.C. construction industry.
In December 2024, Werden was named the board chair of the BC Road Builders & Heavy Construction Association (BCRB). She is the third female chair in the association’s 58-year history.
“I am excited to continue my work with the association as chair and honoured to be asked to take on the role,” says Werden, who is a construction lawyer and partner at Jenkins Marzban Logan (JML). “Our members are an innovative and dedicated group of industry leaders. I’m always blown away by how committed they are to the work they do… and how they give back to communities in meaningful ways.”
BCRB represents more than 280 firms involved in the road building and maintenance industry as well as those providing service and support for the industry. Advocating for sustained and strategic investment in core infrastructure has been a strong mandate throughout the association’s history.
Werden got involved in the association as part of her efforts to better connect with her clients and the industry as a whole. She first joined BCRB as a board director in 2022 and then served as vice chair in 2024.
“ When I initially got involved with the board, I was the only woman on the board. Now there are three,” says Werden, noting her firm had several clients involved in the association. “I was looking for a new way to give back and it was a good fit for my skill sets and interest in policy and advocacy.”
An early ambition of hers was to form a committee to attract and retain women in the sector. She spearheaded the formation of the BCRB Women in Road Building Committee in 2023 and served as its first chair.
The committee promotes initiatives and hosts programs/events that focus on attracting and retaining a more diverse cross section of the population to the many jobs available in the road building, maintenance and infrastructure sectors.
“If we’re trying to attract a more diverse workforce into these sectors, we need to be showcasing
successful women already here and paving the way,” says Werden, who is an avid mentor and champion for women in the construction industry and legal profession.
The Ontario native attended UBC law school and graduated in 2011. She articled at a Vancou-
ver firm that specialized in construction and insurance during her studies and eventually practiced there for seven years.
“I had exceptional mentorship and discovered I really enjoyed construction law matters. It is high stress but also high reward,” she says.
In 2018, Werden joined JML as an associate and became an income partner in 2022. Werden provides a broad range of services across the construction industry during all phases of construction. Her experience includes advising on procurement, contracting, construction, dispute resolution and more. Arbitration is a particular interest for her. She is licensed to practice in B.C., Alberta and Northwest Territories and has a temporary practice permit in Ontario.
At 38 years old, Werden already has a distinguished legal career, having earned multiple accolades and awards for her leadership and achievements. She is a past chair of the Canadian Bar Association and committed to mentoring and training young legal professionals.
Most recently, she became the first female equity partner in the construction group at her firm. This is a significant achievement given that women are still underrepresented in leadership and partnership positions within law firms.
She explains that women have been entering the legal profession in numbers equal to or greater than men for more than a decade, but that number quickly dwindles at senior and partnership levels.
“When I started practicing, it was noticeable how few women held leadership positions in law. Then when I started serving the construction industry, I noticed a lot of parallels,” says Werden.
Prior to joining BCRB, she spent six years volunteering with Canadian Construction Women (CCW) including a two-year term as president. During that time, she mentored many women, spoke at conferences and was involved in awarding bursaries to women pursuing construction education and training.
“CCW was not only a way to connect with other women, but to see what the industry was doing to address diversity,” says Werden. “I’ve met so many brilliant, wonderful examples of women who are so resilient and ambitious. It’s been rewarding to be a small part of that.”
W ing underrepresented groups such as women to the construction indus
try is critical. The road builders are facing shortages in plow truck drivers, heavy equipment operators, and mechanics.
“ The membership wants to know how we can tap into this whole other half of the population to bolster the workforce, and understands the value of it,” she says. “There is ongoing concern around skilled workers and shortage of people to fill leadership roles.”
To tackle the labour shortage, BCRB launched The RoadShow trailer in 2024 — a mobile talent-attraction experience that puts people in the driver’s seat to learn about careers in road building and highway maintenance.
The 34-foot trailer with four state-of-the-art simulators has visited more than 25 communities across B.C. to connect with high schools and Indigenous groups.
“ We’re using that initiative to connect with people and give them a taste of what it’s like to operate heavy equipment and inspire them to pursue a career in the sector,” says Werden, adding the trailer will travel across B.C. until early 2026.
Another pressing issue is the U.S. tariff uncertainty and the looming impacts on construction and the economy. With retaliatory tariffs from Canada, the trade dispute threatens to disrupt established supply chains, increase project and material costs and create economic chaos for businesses on both sides of the border. Werden’s general advice is to examine contracts carefully and start conversations early to prepare.
“If the contract is silent on tariffs or changes in laws, the presumption is you’re not going to be entitled to any adjustments to material costs for example,” she says.
Werden is also a regular guest lecturer for the UBC Masters of Engineering Leadership Program, and has spoken at many industry conferences and associations, including Buildex Vancouver and the Vancouver Regional Construction Association.
“I have been super lucky to be so well supported throughout my career. I have great clients and I’m proud to serve as a model for young professionals
BY REBECCA MELNYK
The new $2.83 billion Broadway Subway project is a massive undertaking that will transform one of the most congested and critical transportation corridors in Metro Vancouver. Construction of the 5.7 km extension of the Millennium Line, from VCC-Clark Station to the Broadway and Arbutus intersection began in 2020. The project scope features a 700-metre elevated guideway section, five kilometres of tunnel and six new stations including an underground direct connection to the existing Canada Line.
The təməsew txʷ Aquatic and Community Centre in New Westminster, B.C., was named after the playful, curious nature of a sea otter and its family-
oriented personality, in turn, reflecting the kind of visitor experience the local community was hoping to create at the newly completed facility.
Weaving in this aspect of storytelling was integral for the city’s largest capital project to date. After a thoughtful naming process, meaning “Sea Otter House” in the hən q əmin əm language, təməsew tx ʷ encompasses a gathering place where social connection, inclusivity and participation thrive, and supports the city’s desire for reconciliation, which was a key element for HCMA Architecture + Design’s vision.
The firm took a multilayered approach in this respect, which included an Indigenous blessing ceremony at the grand opening and, beforehand,
the involvement of a naming advisory committee composed of representatives from Spirit of the Children Society, Qayqayt, q
(Kwantlen), x ʷməθkʷəy əm (Musqueam), and Sḵwx wú7mesh (Squamish) Nations, staff from School District 40 and city officials.
Throughout an Indigenous engagement process, designers also learned how the centre must be welcoming to Indigenous youth in a time of crisis or when one’s home is unsafe, says principal Paul Fast.
As a companion piece to təməsewtxʷ, Indigenous artist and master carver James Harry of Squamish Nation created a public art installation called Miyíwts (“Water’s Edge”) as a way to inspire collective pride. The mirror polished stainless steel sculp-
ture stands 16 feet high and reflects the strength and power of the site’s former Glenbrook Ravine.
“James Harry’s wish is that people sit with the piece and see themselves reflected in Miyíwts,” says Fast. “This permanent public art piece also affirms the vitality and presence of the Coast Salish on these lands. Harry hopes that, as the City of New Westminster’s largest public art installation, that Miyíwts serves to help future generations of Indigenous children and adults to feel proud of who they are and feel visible on their land.”
HCMA has been embedding Indigenous design principles in various projects over the past few years. The firm’s in-house Indigenous design studio led by Aiden Callison, continues to push the status quo by working with First Nations in the region to shift power and find opportunities to decolonize processes, systems and projects.
To further advance reconciliation efforts, the architects approached the design of the 114,571 square foot centre as an extension of the land, not separate from it.
“The centre is situated on the edge of a residential neighbourhood north of the Fraser River, which has long been a cultural and economic life source for Indigenous peoples,” explains Fast. “Located on the site of the former headwaters of Glenbrook Ravine, which was lost to development over the preceding decades, the project takes a strong stance toward reconciliation with the natural character of the landscape.”
The design prioritizes an east-to-west cardinal orientation over the colonial urban grid. The building sits along the natural topographic line of the former ravine, counter to the residential streets that surround it. The headwaters to the north have been reconnected with the remaining branch of the ravine to the south, establishing a major public green space and rain garden adjacent to the facility’s south plaza.
Completed in May 2024 and delivered at a cost of $114 million, the project has since won national and global accolades, including a Prix Versailles 2024 World Title Special Prize for an Interior in the Sports category. The facility is the third Canadian project to earn the recognition since the prize was established in 2015.
Before completion, the facility was also recognized with a World Architecture Festival award for Civic Facilities (Future Projects) in 2021, and this past November, təməsewtxʷ was awarded with a RHF Accessibility Certified Gold rating under the Rick Hansen Foundation Accessibility Certification program.
A two-year community engagement process brought accessibility to the forefront, along with the flexibility to future-proof the building, which features a four-pool aquatic centre with sauna and steam rooms, universal washrooms and change rooms, a fitness centre, gymnasia, community rooms, licensed
childcare, administrative offices, as well as new plazas and greenspaces.
According to Fast, inclusive design and physical accessibility were core aspects of the facility’s planning and detailing, with generous circulation space and additional handrails, high-contrast signage with braille and tactile directories, elevator access to level 2 programming and benches and accessible furnishings with backs and armrests.
Inside the fully universal washrooms are lift devices, with adult change tables in both wet and dry spaces.
For a more inclusive pool experience, the 50-metre lap pool features a moveable floor, which can be adjusted to different heights for people of all abilities,
including those in wheelchairs. It rises from a 2.5-metre depth to a 0 depth in less than a minute.
Pool change rooms have options for all genders and dedicated male and female spaces. There are ramps and bench entries into leisure and family hot pools, with transfer ledge entry and lift access in the adult hot pool. A provision for blocking visual access to pool areas accommodates all-body, women-only, neurodiverse or cultural-sensitive swims.
The aquatic spaces aren’t just accessible. Reducing energy use was also top of mind. The community centre is the first to use a gravity-fed InBlue filtration system, which uses a drum filter system with lower water consumption and energy requirements, says Fast.
“Based on monthly usage since its opening, the filtration system alone is on track to reduce energy costs annually by over $100,000,” he says. “The biggest benefit from this system is the reduced levels of required chlorine, leading to much better water and air quality for swimmers. Initial results show that the system produces air and water quality far exceeding the standards set out by the Health Act.”
Overall, the centre is aiming for a 92 per cent reduction in greenhouse gas emissions compared to the building it replaces. It also became Canada’s first completed all-electric facility to achieve the Canada Green Building Council’s (CAGBC) Zero Carbon Building-Design Standard, an ambitious feat that brought its own challenges.
“Pools are one of the most energy-intensive building types,” says Fast. “Pursuing the Zero Carbon
Building Design Standard required new ways of thinking and new design strategies in order to address the stringent requirements of the certification.”
The firm worked with the CAGBC to share knowledge about the unique issues and energy needs of aquatic facilities.
“ We collaborated to establish thresholds of performance that best reflect the energy demands of a natatorium, balanced with less energy intense spaces in the surrounding community centre,” says Fast. “Together with the CAGBC, we traced a path forward for similar energy-intensive projects to navigate and successfully achieve ZCB Standard requirements.”
Besides the gravity-fed pool filtration, pools separation for increased energy efficiency and an allelectric mechanical system for both heating and
cooling, minimizing energy use was achieved through a range of other strategies, such as compact massing and form factor, a highly-efficient envelope, shading on the south, east and west facades, natural ventilation, abundant daylight and heat recovery ventilators. The building orientation and program overlay were also optimized for energy efficiency.
“On a tactical level, to successfully minimize energy use, the design strategy for təməsew txʷ applies a passive approach first, considering not only how the architecture can respond to specific site conditions for efficiency and comfort, but how operational conditions, strategies, and expectations inform the design,” explains Fast.
To ensure a low-impact result meant reducing demand first, then optimizing active systems.
“ This means that insights from operators play an important role in the design process,” he further explains. “Pursuing certifications can seem abstract for those who are less familiar, but by ensuring involvement and making environmental performance feel more tangible in decisionmaking, we can all work together to achieve a high-performance result.
“There may be trade-offs, but rating systems like the Zero Carbon Building — Design Standard help to create a framework that can influence and inform sustainable design strategies.”
Rebecca Melnyk is editor of Canadian Facility Management & Design.
BY STEVE MCCONNELL
If you perform your work correctly and on time you should get paid. The majority of the time, both parties to a contract understand this with crystal clarity. Unlike verbal agreements and handshake deals, a written contract serves to provides evidence of the agreement, to avoid disputes and payment delays. So why are payment problems in the construction industry still so common? It is not so much that there is a misunderstanding of the agreed upon terms, but rather, interpreting the “true” meaning of the contract has become a tactic for delay and leverage. Which, ironically, directly opposes the intended purpose of the underlying agreement. This must be fixed.
In Canada and the U.S., government funded projects, and the occasional private project typically require performance bonds and labour and material payment bonds. The purpose of this is two-fold. Firstly, the owner or general contractor has the security of knowing that the parties they have contracted with have been financially and operationally prequalified by an independent bonding company and are therefore capable of completing the work at hand. Secondly, they know that funds advanced to the project will be available for sub-contractors and suppliers to complete it, even if the general contractor goes bankrupt. In the event of an insolvency, the bonding company provides these funds to project participants to complete the project, keeping it lien free for the owner. In theory, everybody wins. Unfortunately, in practice, many potential claimants are dissatisfied with the labour and payment product.
The problem with the labour and material payment bond is one of unmet expectation, rather than with the product itself. The product is designed to respond in the event of a clear default or insolvency. When a default is a black and white bankruptcy or failure to perform, the product works great. The labour and material payment bond is not designed or intended to respond to a contractual dispute. While all parties likely know when they have performed their work and are entitled to prompt payment, some bad actors will use the construction contract as a tool to renege on their original obligations. It has become well known in the industry that taking a construction dispute to a judge is a long, expensive, risky and arduous process. It is easy to dispute the contract terms and use the inefficiency of the court system to reduce or delay legitimate requests. Even when a claimant’s case is justified, the inherent complexity of construction and the vast amount of documentation required to convince a judge of a legitimate position in a twoweek trial is extremely challenging.
In the event of non-payment, a contractor will make a claim on a labour and material payment
bond. If they have completed their work accurately and on-time, they have a reasonable expectation that the bonding company will step in and pay them as promised. Often, after they have filed their claim, they find out it has been rejected, as the non-payer has denied liability by alleging a dispute. In this situation, while the bonding company does have an obligation to investigate the bond claim to determine the veracity of the non-payer’s position, their ability to determine the facts from the available evidence is often beyond their capacity. In most cases, this means that the product does not respond until the legal claims are resolved by the courts, a mediator or arbitration.
While the Labour and Material Payment bond may eventually pay after a multi-year legal battle, it is hardly a quick payment solution for unpaid subcontractors struggling to meet their own cash flow requirements. In addition, subcontractors may find their own legitimate Labour and Material payment bond claims denied due to a “dispute” while labour and material payment bonds claims made against them by their unpaid subcontractors and suppliers are paid out quickly by their own bonding company. If the alleged dispute is with the general contractor, there will be no financial response from the bonding company. On the same project, the subcontractor is still legally obligated to pay out its own subcontractors who have completed their work on the project on time. Obviously, this is unfair when the “dispute” may have been manufactured to
corner, delay and weaken a legitimate unpaid claimant.
Labour and material bonds have their place in the event of non-payment due to insolvency or cut-and-dry contractual default. They are not as effective when there is a contractual dispute, alleged or real. An unscrupulous contractor can easily exploit this product weakness by manufacturing a dispute, turning the Labour and Material payment bond from a useful tool designed to protect the subcontractor into a weapon of legal and financial leverage via false delay. While many may criticize the labour and material bond product as failing claimants, this comes from a misunderstanding of what a labour and material payment bond is designed to do. It was never intended to be the solution to contract disputes. This is best solved by mediation, arbitration, and/or Prompt Payment legislation. Prompt payment legislation should provide a legal mechanism to resolve disputes quickly. Labour and Material payment bonds can then provide the funds for clear defaults. In conjunction, both provide adequate payment for legitimate claimants. While more government regulation is not ideal, it is important to provide legal protection to good contractors from bad actors. If you do the work, you should get paid. Promptly.
Steve McConnell is president and owner of Nordcap Insurance Services, a niche bonding and insurance brokerage specializing in construction. www.nordcapinsurance.com
BY MORLY BISHOP
In general, insurance is about the transfer of risk; transfer of risk can be found in many forms, and it is our job as risk management and insurance providers to identify all forms of risk transfer for consideration. In addition to evaluating the strength of your insurance program, joining your local construction association could be the risk transfer solution your firm requires to make it through the current tariff threat. It’s clear that in the face of tariffs, the time to stand united has never been more apparent.
Tariffs coupled with a levy on Canadian energy products threaten to disrupt the deeply integrated North American construction industry. With Canada’s construction sector already navigating high costs, labour shortages, and a housing crisis, the added pressure of tariffs could push many projects to the brink of financial unviability. However, by standing united through collaboration with regional, provincial, and federal construction associations, contractors can mitigate risks, adapt to this new trade reality, and emerge stronger.
The U.S. tariffs target all Canadian imports with no exceptions beyond national security-related goods. For the construction industry, this means higher costs for materials like steel, aluminum, and lumber exported to the U.S., as well as retaliatory tariffs from Canada that could increase the price of Americansourced supplies such as appliances and machinery. The interdependence of the Canadian and U.S. construction markets means disruptions could ripple across borders, affecting project timelines, budgets, and supply chains.
For Canadian contractors, the risks are multifaceted. Rising material and insurance costs could erode profit margins, especially on fixed-price contracts. Supply chain delays may stall projects, triggering penalties or disputes. Smaller firms, less equipped to absorb these shocks, face the threat of insolvency. Yet, amidst this uncertainty, collaboration through construction associations offers a powerful strategy to reduce exposure and build resilience.
Canada’s construction industry is supported by a robust network of associations at the regional, provincial, and federal levels. These groups are uniquely positioned to advocate, educate, and facilitate collaboration; helping contractors navigate the tariff storm.
The CCA, representing more than 18,000 member firms nationwide, has already condemned the tariffs, emphasizing their potential to hinder housing affordability and critical infrastructure projects. Provincial bodies like the BCCA have issued alerts, urging members to review contracts and negotiate tariff-related provisions. Regional associations, embedded in local markets, provide tailored support
by connecting contractors with resources and peers facing similar challenges. By working together through these associations, contractors can pool their expertise, influence policy, and develop collective solutions.
The following are examples of how the construction associations and their member firms are working to reduce risk for all contractors.
1. Advocacy and Policy Influence
United, contractors can amplify their voice through associations to lobby federal and provincial governments. The construction associations’ call for a strong governmental response to the tariffs, alongside consultations with industry, demonstrates this potential. Contractors can push for measures like exempting construction materials from retaliatory tariffs. By presenting a unified front, the industry can pressure policymakers to prioritize housing and infrastructure amidst trade tensions, ensuring the sector’s concerns shape Canada’s response.
2. Contract Management and Risk Allocation Associations offer critical guidance on adapting contracts to tariff-related risks. The BCCA, for instance, advises members to ensure duty provisions are explicit in bid documents and to negotiate costrecovery mechanisms for unforeseen expenses. Collaborative workshops and legal resources provided by provincial associations can help contractors understand risk allocation — whether under fixedprice or cost-plus models — and adjust terms like notice periods or pricing validity. Sharing best practices through association networks ensures smaller firms aren’t left vulnerable.
3. Supply chain diversification and vertical integration
Tariffs underscore the danger of over-reliance on U.S. markets. Through the collaboration with association members firms you can reduce exposure to tariffs by acquiring or partnering with companies in alternative supply chains to gain more control over raw materials, production and distribution.
4. Knowledge Sharing and Training
The complexity of tariffs demands rapid adaptation. Federal and provincial associations can and have hosted webinars, forums, and training sessions to educate contractors on tariff impacts, procurement strategies, and economic trends. Regional groups can tailor this knowledge to local contexts, ensuring contractors have actionable insights in their specific regions. Peerto-peer collaboration within these networks fosters innovation as contractors share successes.
5. Collective Resilience Through Industry Standards Associations can spearhead the development of industry-wide standards to address tariff challenges.
For example, creating templates for escalation clauses allowing price adjustments for tariff-driven cost spikes could protect contractors across projects. By standardizing approaches to risk management, the industry can reduce disputes and maintain competitiveness, even as costs rise.
6. Review your Insurance Program
During extreme and unexpected events, the depth and quality of your insurance program will come to the forefront. It can be hard to plan for all possible situations without driving up the cost of your annual insurance spend. With that said, there are some simple additions that should be considered.
During this article, we have talked a lot about the possibility of contract disputes and how that presents additional risk to your bottom line. A contractual dispute based on added cost by itself doesn’t necessarily trigger coverage under most contractor policies. However, adding legal expense insurance to your annual insurance program could be a cost-effective viable option to assist in recovering any legal expenses associated to contract disputes over tariffs.
To maximize the benefits above, contractors should actively engage with their associations. Joining provincial or regional bodies provides access to resources and networks. Participating in CCA-led advocacy ensures national issues, like trade policy, reflect industry needs.
TheU.S.tariffs,whiledaunting,arenotinsurmountable. Canadian contractors have faced challenges before such as material shortages, pandemics, and inflation. Collaboration through construction associations offers a proven playbook: amplify advocacy, share knowledge, and adapt collectively. As Chris Atchison BCCA CEO, stated, “In times of uncertainty, the construction industry’s greatest strength lies in its unity. By collaborating across associations and working together, we can navigate these challenges, protect our projects, and continue to build the future of Canada.”
For contractors, that means standing together.
By leveraging the collective strength of associations, Canadian contractors can reduce their exposure to tariff risks, safeguard their projects, and contribute to a stronger industry. The path ahead requires agility and solidarity, but it’s one the construction sector is wellequipped to navigate — together.
Morly Bishop is a partner and senior risk management advisor with Acera Insurance Services located in Kamloops. He is an active director for both the Southern Interior Construction Association and the B.C. Construction Association.
BY NIKKI KEITH AND ROBYN WILSON
In 2025, cyber threats are more sophisticated than ever, and the construction industry is no exception. While firms focus on physical job sites, cybercriminals are exploiting digital vulnerabilities in project management software, IoT devices, and cloud-based tools. From ransomware attacks to financial fraud, businesses handling sensitive project data and high-value transactions are prime targets.
Many construction companies mistakenly believe they aren’t at risk, assuming cybercriminals prioritize industries like finance or healthcare. However, hackers recognize the value of construction firms due to the multiple access points to critical information. Phishing scams — where fraudsters send emails posing as trusted contacts — are increasingly tailored to trick employees into revealing credentials, transferring funds, or downloading malware. Ransomware attacks can lock down project files, with criminals demanding payment for data restoration, yet even when paid, recovery isn’t guaranteed. Third-party vendors with weaker security also create vulnerabilities, allowing cybercriminals to access confidential financial and project data. Invoice fraud is another growing threat, where attackers manipulate communications to divert large transactions to unauthorized accounts.
The consequences of cyber incidents are severe: project delays, financial losses, regulatory fines, and reputational damage. A phishing attack compro-
mising a firm’s email system could allow fraudsters to alter invoice details, redirecting funds away from subcontractors. A ransomware attack could halt operations, forcing costly downtime and legal repercussions. A data breach via a vendor could expose sensitive project blueprints or employee records, leading to regulatory scrutiny and potential lawsuits. These risks highlight the need for both proactive security measures and cyber insurance.
A strong cybersecurity strategy involves proactive risk management, employee training, and comprehensive insurance coverage. Firms must regularly assess their vulnerabilities, monitor emerging threats, and implement security best practices. Multi-factor authentication (MFA) strengthens defenses by requiring multiple verification steps, while regular data backups ensure critical information is secure and retrievable in the event of an attack. Robust endpoint and network security —such as firewalls, antivirus software, and encryption —prevents unauthorized access.
Human error remains one of the biggest cybersecurity risks. Educating employees on identifying phishing attempts and fraudulent emails significantly reduces exposure to cyberattacks. As threats become more sophisticated, employee training should be an ongoing effort rather than a one-time initiative.
Even with strong security measures, no system is immune to cyber incidents —making cyber insurance a crucial safety net. A well-structured policy covers legal fees, regulatory fines, forensic investigations, business interruption costs, and crisis management expenses. It ensures companies can recover quickly, minimizing operational disruption and financial fallout.
Cyberattacks are becoming more advanced, leveraging artificial intelligence (AI) to craft highly convincing phishing emails, deepfake videos, and fraud schemes that are increasingly difficult to detect. The widespread use of mobile devices on job sites presents additional risks, as compromised phones and tablets can provide attackers with direct access to project data. Meanwhile, the rise of Ransomwareas-a-Service (RaaS) has made cybercrime more accessible, allowing even inexperienced hackers to launch attacks.
Despite these escalating threats, some construction firms hesitate to invest in cyber insurance due to misconceptions. Many assume only large corporations are targeted, but in reality, small and mid-sized firms are frequent victims due to weaker defenses. Cybercriminals prioritize easy targets, not just high-profile ones. Another common belief is that cyber insurance policies rarely pay out, but in 2025, insurers continue to provide reliable coverage for data breaches, ransomware attacks, and fraud-related losses. Additionally, some firms mistakenly assume their general liability policies cover cyber incidents, but traditional policies typically exclude cyber risks, making dedicated cyber insurance essential.
Beyond financial protection, cyber insurance strengthens client trust and contract security. Many project owners and investors now require proof of cyber insurance before engaging with vendors, making it a valuable asset in securing contracts.
As cyber threats continue to evolve, construction firms must integrate cybersecurity into their overall risk management strategy. Predicting threats, preventing incidents, and insuring against losses are key steps to safeguarding operations and ensuring business continuity. Investing in cybersecurity and cyber insurance is no longer optional — it’s a necessity for resilience in an increasingly digital world.
Nikki Keith is principal at Wilson M. Beck Insurance Services, and Robyn Wilson is vice president at the company. For more information about cyber exposures or cyber insurance solutions, visit www.wmbeck.com.
BY KEVIN YUERS
Concrete is among the most durable building materials. Many have marveled at ancient Roman structures built from concrete that have lasted through millennia. Their durability is an inspiration to modern builders, and one might rightly ask, “Why don’t modern concrete structures last as long as these ancient ones?”
The short and simple answer is that modern concrete is different in two critical aspects: modern concrete must deliver vastly increased performance, and it must at the same time remain economical. Modern concrete elements must be thinner, narrower and span greater distances, while at the same time carrying greater loads and resisting earthquakes. These demands necessitate the inclusion of steel reinforcement and so today nearly all structural concrete is reinforced with steel rebars. Unfortunately, including steel will also introduce the potential for corrosion, cracking and deterioration.
Concrete has a natural porosity, which allows water and waterborne salts to penetrate and cause corrosion of the reinforcement. Corroding steel will expand, causing cracks and these cracks will allow even more water to penetrate — accelerating the deterioration process. If the concrete contains cracks to begin with, this process will initiate even sooner and more rapidly.
Climate change is a relatively recent and increasing threat to the durability of concrete structures. We are seeing more extreme weather systems, such as tropical storms and hurricanes in ever increasing strength and frequency. Coastal areas are often inundated with salt water. In the future, we can expect to see higher
sea levels and even greater temperature extremes. Deterioration mechanisms are bound to accelerate. Modern, reinforced concrete will require greater protection than ever before.
Concrete is made from rock and sand that is “glued” together by cement. One way to make concrete stronger and more durable is to add more cement, but this presents a new problem. The manufacturing of ordinary cement releases large amounts of CO2 into the atmosphere. For every ton of cement manufactured, the process will release between 0.6 and 0.9 tons of CO2. This adds about 1.5 billion tons of carbon to the atmosphere each year — about 8 per cent of global carbon emissions. We can see that increasing the portion of cement in concrete can actually have an unintended negative effect as adding carbon contributes to more global warming and climate change.
The global community’s response to this selfinducing cycle has been drastic, calling for massive reductions in the carbon output from manufacturing cement and concrete. More efficient manufacturing has helped and employing carbon capture technologies is gaining some traction. Replacing at least a portion of the cement in concrete with alternative cementing materials is a proven strategy and has become commonplace.
Incorporating more advanced formulation technologies for concrete must also be part of the solution. Innovations in the use of specialized admixtures are increasingly transforming the construction industry, giving builders a more sustainable concrete material for building modern
structures while reducing the need and cost for unexpected maintenance and repairs. Utilizing these technologies in the initial stages of construction can save owners 50-70 per cent on repair costs, according to the American Concrete Institute.
One of the most effective technologies has been permeability-reducing admixtures (PRAs), such as crystalline waterproofing admixtures. These admixtures react to form crystals that block pores and fill cracks in concrete to protect it from water penetration, even against extreme hydrostatic pressure. The first crystalline waterproofing admixture was invented in 1980 by our company but has only become widely used worldwide in the past 30 years.
Another specialized admixture pioneered by Kryton is a unique abrasion-resisting admixture called Hard-Cem. This admixture can reduce abrasive or erosive wear in concrete exposed to harsh environments and extend the service life of the concrete by double.
Over the years, concrete admixtures have gained popularity for their ability to resist corrosion, reduce carbon emissions, avoid unnecessary maintenance or repairs, and improve the performance, durability and lifespan of infrastructure. In the past, decision-makers may have prioritized short-term savings over long-term durability, but this mindset is shifting. Builders now recognize that using concrete admixtures can reduce the amount of cement needed, shorten construction timelines, and lower labour costs, making it a financially viable option for creating more sustainable, durable structures. For example, Kryton has helped its government sector clients achieve greater durability for large infrastructure such as hydroelectric dams and to address leakage issues in drinking water systems by incorporating these advanced admixtures into their concrete.
To be truly sustainable, concrete must not only minimize its environmental footprint, but also deliver long-term durability and service life. Fortunately, the challenges faced by concrete structures from the effects of climate change can be addressed through improved technologies. The construction industry can realize both environmental and economic benefits by simply using a more durable version of concrete that lasts much longer and doesn’t have to be repaired as much — reducing the demand for so much additional concrete, cement and other materials.
Kevin Yuers is Kryton International’s vice president for product development and acquisitions. His 40 years of industry experience allows him to bring real-world solutions and value to the company’s many customers and associates spread around the globe. He is the author of numerous articles and is the named inventor on patents related to the concrete industry. www.kryton.com.
BY KATY FAIRLEY
With the rise of construction management as a widely used project delivery method, Requests for Proposals (RFPs) have become increasingly important in the construction industry. As the procurement process evolves, it is essential for both owners and contractors to navigate the complexities of RFPs effectively.
In traditional design-bid-build projects, the selection process is rightfully straightforward: the lowest price typically wins. However, for more complex procurement used for construction management, design-build, or alliance delivery methods, the procurement process becomes more nuanced. In these cases, it is essential to take steps to reduce subjectivity and ensure that decisions are based on objective facts rather than personal biases, whether conscious or unconscious. This article will explore how bias can affect procurement decisions, particularly in the RFP process, and provide methods for mitigating its impact. These principles equally apply to Requests for Qualifications (RFQs), where the same need for clear, unbiased evaluation criteria and well-crafted submissions ensures a fair and transparent selection process.
PSYCHOLOGY AND PROCUREMENT
Bias is an inherent part of being human, including both conscious and unconscious biases, but acknowledging and understanding them can significantly mitigate their impact on the procurement process. An easy example of conscious bias in procurement is drafting an RFP with such narrow criteria that only a preferred firm would be capable of meeting the requirements, undermining fairness in the process. However, the sneaky part of bias lies in the unconscious types, which can subtly influence decision-making without awareness.
One of the most significant unconscious biases in procurement is decision fatigue. Decision fatigue occurs when the quality of decisions deteriorates after prolonged decision-making, leading to rushed or incomplete choices. For instance, studies have shown that judges’ decisions, for either granting parole or dismissing charges, can be influenced by the timing of their decision-making sessions, with favourable rulings decreasing throughout the day.
In procurement, this fatigue can impair the ability to evaluate proposals thoroughly, especially during long evaluation sessions. When evaluating multiple proposals, evaluators may rush through the final ones at the end of a long day, leading to hasty judgments based on initial impressions rather than the content of the proposal. This is often evident in the diminishing quality of comments as the evaluation progresses, highlighting the importance of reviewing proposals in a random order.
To minimize its impact, it is crucial to schedule breaks and conduct evaluations in the morning when decision-making ability is typically at its peak.
Anchoring bias occurs when evaluators rely too heavily on the first piece of information they encounter, setting the tone for subsequent decisions. For instance, when the first proposal is reviewed, evaluators may unconsciously adjust their expectations and scores for the following proposals. This can lead to unfair comparisons, as subsequent proposals may be assessed not on their merits, but in relation to the initial proposal.
To mitigate this, it is essential to randomize the order in which proposals are reviewed by each evaluator. This approach minimizes the influence of the first proposal, as the first proposal will vary for each evaluator, reducing the risk of bias.
Another example of anchoring bias is why it is critical for evaluators to withhold reviewing fees until all technical submissions have been evaluated. This ensures that financial considerations do not unduly influence the technical assessment.
Confirmation bias occurs when evaluators favour proposals that align with their pre-existing beliefs. For example, an evaluator has worked with a contractor previously and had a positive experience. If the contractor’s proposal aligns with the evaluator’s expectations, they might give it a higher score, disregarding any areas where the proposal falls short of the criteria. Another example is evaluating proposals more favourably if the contractor has a strong reputation within the industry, even if their proposal does not fully meet the criteria. To counter this, involving multiple evaluators with diverse perspectives can challenge assumptions. Evaluators must also document both positive and negative reasons for their scores.
Finally, for contractors, optimism bias can lead to unrealistic expectations of success and ability.
Contractors may overestimate their capacity to execute the project, even when their experience on paper does not align with the requirements needed to win the RFP process. This bias can cause them to misjudge how well their proposal aligns with the project’s actual needs and the RFP’s evaluation criteria. Contractors should ensure their proposals align with the specified criteria, accurately reflect on their experience, and seek unbiased feedback before submission. Conversely, an owner or evaluator may assume a contractor will perform well based on their success in a past project for that owner, believing the outcome will be the same. This can lead to overly optimistic expectations and inflated scoring, even if the proposal does not fully align with the RFP requirements.
Effectively navigating the complexities of the procurement process, particularly in RFPs, requires both owners and contractors to be mindful of the biases that can influence decision-making. By recognizing the natural presence of bias — whether conscious or unconscious — parties can take proactive steps to mitigate its impact and ensure a fair, transparent, and objective evaluation. Owners should focus on clear, unbiased RFP drafting, while contractors should submit proposals that align with the specified criteria, providing clear evidence to support their claims. Recognizing that bias is a natural part of human decision-making is key—it is not about eliminating bias entirely, but rather about acknowledging and managing it to ensure fairness and transparency in the procurement process.
Katy Fairley is principal of Fairley Strategies. She is an expert and adviser on topics related to project delivery, construction contracts and procurement best practices.
BY MARK BOWEN
That bridge you crossed on your morning commute was designed to last up to a century. But for Canada’s bridges to achieve their 75- to 100-year lifespans, rehabilitation is an essential investment.
Bridge rehabilitation, by definition, is the partial replacement of a bridge to maximize its lifecycle and maintain safety. With everyday foot and vehicle traffic well in the thousands on many aging bridges, ensuring that infrastructure is maintained to support expected loads is essential for public confidence and more importantly, community safety.
When it comes to local bridge infrastructure, municipalities bear responsibility for the inspection and maintenance of their structures. As soon as a new bridge is built, it’s added to the municipality’s inventory. From there, inspections are programmed every two to three years. This involves on-site visits to review the bridge structure’s condition, identify elements that are deteriorating or simply not performing well, and reflect updates in an asset management database.
By the time a bridge turns 25- to 40-yearsold, municipalities identify elements that have
deteriorated sufficiently to need repair. Water and de-icing salts that seep through joints at either end of a bridge are common culprits that start to degrade the critical steel and concrete structure below. Not surprisingly, early maintenance and rehabilitation of expansion joints can protect the underlying structure and defer more substantial repairs to later in the bridge’s lifecycle.
Adding to pressures from water and salts are thermal changes. With temperature swings from -40° C winters to +30°C summers, Canada’s harsh climate adds stress to bridge components. Large thermal movements are typically accommodated in the expansion joints and bridge bearings. However, uneven geometry or loading can cause degradation of these elements. One rehabilitation strategy gaining favour is to consider removing joints altogether by revising bridge articulation to a semi-integral configuration which can eliminate one of the primary sources of structural deterioration.
Once a municipality is aware of deterioration, it has two options: major or minor rehabilitation. For either avenue, the municipality starts the process by sourcing consultants to map out the critical issues and present the optimum rehabilitation solutions based on each bridge’s unique characteristics. Everything we do is essentially an intervention to help our client’s bridge reach its desired lifespan, while working with the limits of available funding.
As the name suggests, minor rehabilitation means smaller upgrades — replacing the less robust elements of a bridge that tend to fail earlier. This could mean swapping a bridge’s expansion joints to restart that lifecycle, for example. Here, a design phase will take roughly four-six months, followed by a similar timeline for the construction phase.
W hen a bridge nears five decades in service, however, major repairs become more likely. There are many reasons for this. Since the year a bridge is built, salt is used on its travel surface to remove ice for safer driving conditions. Over time, this salt seeps into the structure, going through the asphalt road surface. Although there’s often a membrane under the bridge’s asphalt layer, it eventually deteriorates under traffic loads, allowing the salt-laden water to seep into more robust concrete elements. As the salt goes in, it initiates corrosion of steel rebar that causes concrete to delaminate and separate — leading to localized failures of material. The result is a deteriorating road surface and potential hazards for drivers.
When challenges are overcome and all the right stakeholders are engaged, bridge rehabilitations are prime opportunities to champion accessibility.
At this point, the municipality will recognize a need for substantial action. This entails more significant work like taking up the road pavement, repairing concrete underneath, and then placing a brand-new road pavement on top. A major repair’s design phase will take around a year, followed by 12-18 months of construction. These construction timelines depend on the project’s magnitude, frequency of traffic, and how that traffic flow can be managed. To illustrate, if there’s a six-lane bridge but only one lane can be closed each way, only a third of that bridge can be worked on at a time. The complexity of cycling through lane closures ultimately extends the project’s duration.
All bridge rehabilitations have a host of challenges in common; working around traffic, whether it’s from vehicles, pedestrians and/or cyclists, is paramount. Adding to this, engineers must be cognizant of emergency routes. For example, most municipalities have designated fire or transit routes. If a bridge happens to be close to a fire station or bus stop, this may impact how the project can be phased.
Surrounding site features become another case-by-case consideration. Most bridges cross over roads, railways or water. Water is the most complex to access for construction work. Meanwhile, working over railways demands communications with another stakeholder group to fully understand all site restrictions related to railway operations.
When challenges are overcome and all the right stakeholders are engaged, bridge rehabilitations are prime opportunities to champion accessibility. On top of fixing deterioration, engineers look at options for levelling up. Additional upgrades such as wider sidewalks or reduced ramp slopes can make travel more convenient for all users, particularly those with reduced mobility. More than aesthetics, these projects prolong critical pieces of infrastructure that often double up as destination spots for the community.
Mark Bowen, MEng, P.Eng., CEng, MIStructE, is a principal at RJC Engineers. He is a leader in the design, assessment and rehabilitation of bridges and related transportation structures.
WSP Canada Inc.
The Narcosli Creek Bridge project is a testament to engineering adaptability and resilience. Following significant flooding in 2018, the existing West Fraser Road and Narcosli Creek Bridge suffered severe damage. A new route was developed to bypass unstable zones, calling for a robust, climate-resilient bridge spanning the creek’s floodplain.
WSP Canada successfully designed the bridge to accommodate increased flood flows and future climate change impacts. Innovative design choices, such as extended steel pipe piles and low-carbon reinforcing steel, prioritize long-term sustainability and reduced maintenance costs.
Environmental considerations were integral to the project schedule, resulting in a deliberately innovative construction approach that minimized impact while ensuring exceptional results. By prioritizing environmental preservation and exceptional engineering foresight, the Narcosli Creek Bridge project sets a high standard for resilient infrastructure development.
The Peers Creek Frontage Road Recovery project in Hope is a model of collaborative infrastructure restoration. This project stemmed from severe flooding of the Coquihalla River during the 2021 atmospheric river event, which disrupted Peers Creek Frontage Road near Hope, cutting off access for residents and the Trans Mountain Pipeline Expansion Project.
McElhanney and BGC Engineering provided swift and innovative solutions. McElhanney’s interim road design minimized waste for the future permanent solution and expedited access restoration, while BGC’s hydrotechnical assessment addressed future climate impacts and environmental concerns. This collaborative effort not only restored vital access quickly, but also enhanced the corridor’s resilience in the final design.
This project exemplifies a commitment to sustainability and climate resilience by addressing extreme weather impacts and ensuring long-term stability. It also demonstrated how collaboration can accelerate project timelines and deliver resilient, permanent infrastructure, benefiting the people who rely on this critical transportation corridor.
Glacier
The Quartz Creek Bridge Replacement and Four-Laning Project, was successfully executed under Glacier’s skilled supervision. This ambitious project included replacing the Quartz Creek Bridge with a 184-meter-long, three-span, four-lane structure and completing extensive highway upgrades, wildlife underpasses, and culvert replacements. The project was especially challenging due to its remote location and harsh climate.
Glacier’s team provided expert guidance and mentorship to a contractor new to B.C. highway construction work, ensuring the project’s timely completion and adherence to high quality standards.
Their collaborative approach, combined with effective issue resolution and cost management, resulted in a project delivered within budget and on schedule. Glacier’s investment in future leadership through mentorship fosters succession planning for the next generation of professionals.
Associated Engineering (AE) excels in emergency bridge response and their ability to rapidly mobilize skilled teams to address critical issues, like the Oliver Underpass Impact, Ladner Underpass Impact and Red Bridge fire. Their innovative approaches, exemplified by custom designs and advanced technologies, ensure efficient and cost-effective repairs. Their ability to coordinate effectively with all parties involved guarantees that they can respond to emergencies with the urgency and precision required, providing timely and effective solutions that restore normalcy and safety.
R.F. Binnie & Associates
Project: Highway 1 – Chase Creek Road to Chase West
R.F. Binnie & Associates’ Highway 1 Chase West four-laning project prioritizes safety and accessibility for the Neskonlith Community and the Village of Chase. The project involved widening a 3.3-kilometer section of highway and constructing two at-grade protected T-intersections, all while enhancing active transportation options.
By engaging with First Nations, the municipal government, businesses, and residents, the project team developed a comprehensive active transportation network, including a grade-separated tunnel, multi-use paths, crosswalks, and paved shoulders. The project also considered the needs of the local farming community by incorporating a livestock underpass. With strong community support and a commitment to safety and sustainability, R.F. Binnie’s innovative approach encourages sustainable travel options in a rural environment.
Project:
Rehabilitation
PBX Engineering’s exceptional work on the George Massey Tunnel Reversible Lane Control System Rehabilitation Project showcases their innovative problem-solving and commitment to safety and efficiency. Highway 99 is a vital trade route and commuter connection across the Fraser River. The George Massey Tunnel relies on a Reversible Lane Control System to manage traffic flow and maximize capacity during peak times.
Project: Highway 37/37A Corridor Planning Study
McElhanney’s Highway 37/37A Corridor Planning Study evaluated nearly 800 kilometers of vital routes in northern BC, connecting communities, businesses, and natural resource industrial sites. Their study assessed highway performance, identified improvement opportunities, and guided long-term investment decisions. Extensive public consultation was key, engaging over 700 participants and collecting more than 10,000 data points through surveys, in-person sessions, and virtual meetings. By engaging with First Nations and local communities, McElhanney identified opportunities to overcome existing corridor challenges with a comprehensive strategy that highlighted the corridor’s economic and community value. This innovative approach ensured safety, mobility, and long-term prosperity for all users of this important corridor.
BY CHERYL MAH
Engineers play an important role in designing the critical transportation infrastructure that connects communities throughout B.C. From highways and bridges to transit systems, well-designed and planned transportation systems are essential for economic development and connectivity.
B.C.’s leading engineering firms are helping to deliver several mega infrastructure projects which will improve the province’s most critical transportation corridors. Three projects were highlighted during a session at the 2025 ACEC-BC Transportation Conference.
Major construction is underway on the first rapidtransit project south of the Fraser River in 30 years. The $6 billion Surrey Langley SkyTrain project will extend rapid transit 16 kilometres, primarily along Fraser Highway on an elevated guideway from King George Station in Surrey to 203 Street in Langley City. It includes eight stations and three transit exchanges at the Bakerview-166 Street, Willowbrook and Langley City Centre stations.
Significant progress was made in 2024, with 90 per cent of right-of-ways cleared and drilling and piling at the 152 Street, 166 Street and 184 Street
station sites with 15 foundation piles completed, according to Gilles Assier, executive project director for the Surrey-Langley SkyTrain Project Transportation Investment Corporation.
The complex project is being delivered by three contractors: Skylink Guideway Parnters (guideway), South Fraser Station Partners (stations) and Transit Integrators BC (systems and trackwork).
Casting of guideway segments will begin in April at a pre-cast concrete facility in Campbell Heights with 40 per cent of all segments expected to be completed by the end of 2025.
Foundation construction has also started for three stations: Green Timbers, Fleetwood, Clayton and Langley City Centre.
“Looking ahead, it’s going to be a very busy year. We have the majority of utility work done and will start construction of guideway spans and the installation of 200 guideway piers and columns,” he said, noting more than 30 engineering firms are involved with the project. “The province is excited to deliver such a transformative infrastructure project…that will reshape transit in the region.”
Another significant project is the $4 billion Fraser River Tunnel Project, which will replace the George Massey Tunnel.
The new crossing will be a toll-free, eight-lane immersed tube tunnel that includes three generalpurpose travel lanes and a dedicated public transit lane in each direction. The new tunnel will also feature a separate multi-use path to support walking, biking and other active transportation options.
The Fraser River Tunnel project will be the fifth widest tunnel in the world, said Donald Trapp, executive project director, Transportation Investment Corporation.
The new tunnel will be made of six tunnel elements. Each element will weigh approximately 60,000 tonnes and will be 130 x 45 metres or about the size of a football field.
Trapp explained the tunnel elements will be made on Deas Island to promote efficiency and reduce construction traffic in the region.
Cross Fraser Partnership, collaborating with the province through the development phase, is comprised of Bouygues Construction Canada Inc., Fomento de Construcciones y Contratas Canada Ltd., Pomerleau BC Inc. and Arcadis Canada Inc.
The project will be delivered through a collaborative Progressive Design-Build. The construction contract is expected to be awarded in 2025 with work beginning in 2026. When completed in 2030, the tunnel will reduce traffic congestion and improve reliability.
Traffic congestion is also being addressed with the Fraser Valley Hwy 1 Corridor Improvement Program, a large-scale highway widening initiative between Metro Vancouver and the Fraser Valley.
Sarah Gaib, engineering director, BC Ministry of Transportation and Transit, provided an overview and an update on current work. The project is in phase 2 with highway widening between 216th and 264th streets and the replacement of the 232nd interchange. The existing cloverleaf interchange at 264th Street is also being replaced.
“The 264th interchange is a showcase project for the corridor and is being delivered through design build procurement. It will be B.C.’s first ever divergent diamond interchange and on the third in Canada,” said Gaib.
B.C.’s leading engineering firms are helping to deliver several mega infrastructure projects which will improve the province’s most critical transportation corridors.
BY REBECCA CLEARY
Managing risk on a construction project starts and often ends with the wording contained in the contracts. Whether facing unprecedented challenges such as a pandemic, economic uncertainties arising from geopolitics, or day-to-day challenges on any project, the language used in your contracts will have a significant impact on who will be holding the bag for unanticipated costs at the end of a project. One way to address unanticipated project risks is by using a price escalation clause to identify how these risks will be addressed should they arise during the course of a project.
A price escalation clause allows a contractor to make adjustments to originally agreed upon contract pricing when certain conditions are met. When dealing with a subcontract, attention should always be paid to the prime contract to determine how price fluctuation risks are passed through and allocated to the parties. From there, a comprehensive price escalation clause will identify the event or circumstance which triggers the application of an escalation clause; set a level of magnitude whereby the triggering event becomes compensable; provide a formula for calculating the value of the event to fairly compensate the contractor; and provide a method whereby by which the claim is made, adjusted and paid out.
Triggering events are characterized as events outside of the control of the parties that will impact the ability of the contractor to perform the work for the originally agreed upon price. A triggering event could be identified as a material increase in the price of labour, materials, equipment or energy. It could include unanticipated delays in the availability of materials or the unanticipated interruption of labour for the project. Or, it could include new, or increase to existing, taxes, levies, duties and tariffs which were unknown or uncertain at the time the contract was executed.
Once the triggering events are defined, consideration should be given to the magnitude of the event — by how much the contract price or schedule will be impacted before the triggering event gives rise to a claim for price adjustment. In other words, the contract should specify not only that a triggering event gives rise to a price adjustment — but should specify a materiality threshold. A materiality threshold could include the use of a percentage to indicate increase in material costs — for example it could be defined as an “increase in the market price of lumber by x% or more”. Market price could be identified with reference to a consumer price index or simply to the cost locked in by a contractor with its own suppliers. When the triggering event results in a delay to the project schedule arising from supplier delays, the contract may identify the number of days of delay to a project required before the contractor
is entitled to a price adjustment. However, if the triggering event is a new or increased tax or tariff, the parties may agree that any increase triggers a pass through of the cost to the owner.
Some triggering events are by nature are easier to identify than others. For example, the imposition of a new tax or tariff would be clear. However, whether cost increases arising from labour or labour shortages amount to an unanticipated triggering event could be more difficult for the parties to assess. Consideration should be given to defining the circumstances under which labour cost increases and shortages ought to be quantified. A clause may include a requirement that a contractor has taken reasonable steps to mitigate against labour cost increases or labour shortages before being able to seek price escalation. Contractors will then have to carefully document what steps it took to mitigate against such circumstances and demonstrate how it reasonably addressed the issues that arose.
Care should also be taken to consider circumstances where more than one triggering event occurs either concurrently or consecutively. The imposition of a tariff may result in an initial pass through cost to the owners, but it also could result in reduced supply leading to delays, or the use of new suppliers impacting pricing. Consideration of the
method upon which these concurrent costs might be assessed will assist in clarifying expectations and quantifying and claims.
Parties should consider a clear method for determining the amount of any resulting price escalation. Will the owner take on the full risk of escalation or will the contractor? Will it be shared among the parties? Will the contract include a clause permitting the owner to claw back the price escalation adjustment if market conditions stabilize and return to pre-escalation levels? Finally, the contract should clearly identify a method by which price escalation adjustments will be treated under the contract. The clauses could be tied into existing change order provisions in the contract. Alternatively, a separate process could be outlined to address specific information needed to establish requests for price adjustment.
Effective risk management in construction projects is largely shaped by the language in the contracts. While price escalation clauses are not new, they can be an effective tool in mitigating risks associated with unanticipated changes in the market.
Rebecca Cleary is associate counsel and member of the construction and engineering practice at Alexander Holburn Beaudin & Lang LLP.
BY JOSH FRIEDMAN
In response to the tariffs and other trade policies of the Trump Administration, which the provincial government of British Columbia projects could result in $1.7 billion to $3.4 billion of lost revenue per year in the province, the B.C. government has announced a strategy for strengthening economic resilience and fostering development.
Under their three-pronged approach, the provincial government will be (1) responding to U.S. tariffs with counter-actions and outreach to American decision-makers; (2) strengthening B.C.’s economy by expediting major projects and supporting workers; and (3) diversifying trade in products away from U.S. markets and customers. This is in addition to the measures implemented by the Canadian federal government, such as countertariffs.
As part of its response, the B.C. government is assessing private-sector natural resource projects worth approximately $20 billion (and supporting roughly 8,000 jobs) with the intention of streamlining regulatory reviews and decreasing the amount of time required to issue permits. Towards this end, the B.C. government introduced Bill 7 — Economic Stabilization (Tariff Response) Act (Bill 7) to, among other things, make it easier for the provincial government to cut red tape as it sees fit.
Premier David Eby has confirmed his government’s intention to accelerate renewable energ y projects
in B.C. by creating a single window permitting process under the B.C. Energy Regulator. Affected projects are anticipated to include the nine wind energy projects awarded electricity purchase agreements with BC Hydro under the recent BC Hydro Call for Power, which were already subject to condensed timelines under the Call for Power, as well as the North Coast Transmission Line and other high-voltage electricity transmission projects in B.C. Bill 7, if passed in the legislature, would also allow the B. C. government to charge certain fees for use of provincial infrastructure by nonCanadian commercial operators and direct B.C. Crown corporations and agencies to prioritize buying products and services from Canadian or non-U.S. suppliers.
The development and construction of the new clean energy projects under the Call for Power are anticipated to attract between $2.3 billion to $3.6 billion in private capital spending to British Columbia, creating an average of 800 to 1,500 jobs annually. BC Hydro’s strategic calls for power, coupled with the initiatives proposed in BC Hydro’s 10-year capital plan released in January 2024, are projected to stimulate around $40 billion in public and private capital investments, creating an estimated 11,300 to 14,000 construction jobs in total each year.
These measures are in addition to the stated intention of the B.C. government to exempt all currently contemplated and future wind energy
projects in B.C. from the statutory environmental assessment process.
In their budget and fiscal plan for 2025/2026 — 2027/2028 (Budget 2025), the B.C. government also outlined a plan to significantly increase capital spending above the levels set in previous years. As set out in Budget 2025, the B.C. government plans to spend $45.9 billion in taxpayer-supported capital expenditures over the next three years, supporting an estimated 180,000 direct and indirect jobs. This includes roughly $4.6 billion on K-12 schools (including upgrades, replacements and expansions), $4.7 billion on post-secondary institutions and research centers, $15.5 billion on healthcare infrastructure (including new and redeveloped hospitals, long term care facilities and cancer treatment centers), $15.9 billion on transportation projects (including bridges, tunnels, rapid transit and highways projects), $2.8 billion on housing developments, $1,9 billion on government ministries (including maintaining, upgrading and expanding infrastructure such as park amenities, wildfire stations, and judicial and correctional facilities), and $109 million on stadium capital upgrades in connection with the 2026 FIFA World Cup.
In addition to this taxpayer-supported capital spending, Budget 2025 also outlines more than $14 billion in self-supported capital spending from B.C. Crown agencies over the next three years, including $13.2 billion in capital spending by BC Hydro (as discussed above), $340 million for ICBC projects (including the relocation of its head office and facility maintenance and upgrades), $310 million for BC Lottery Corporation projects, and $92 for Liquid Distribution Branch projects (including upgrades to liquor stores).
It is not yet clear the effect such measures will have on the development of projects under the Call for Power or the projects for which capital funds were allocated in Budget 2025, but preliminary assessments indicate the potential for positive outcomes in the provincial job market. While much still remains to be seen as these policies are iterated, capital expenditures filter through the economy and new projects come online, it is clear that infrastructure development will continue to be a key avenue in B.C. towards stimulating economic growth and building resilience.
Josh Friedman is an associate at McCarthy Tétrault LLP in the firm’s financial services group in Vancouver. He maintains a corporate, commercial, and debt-finance practice with a focus on clean energy and infrastructure projects.