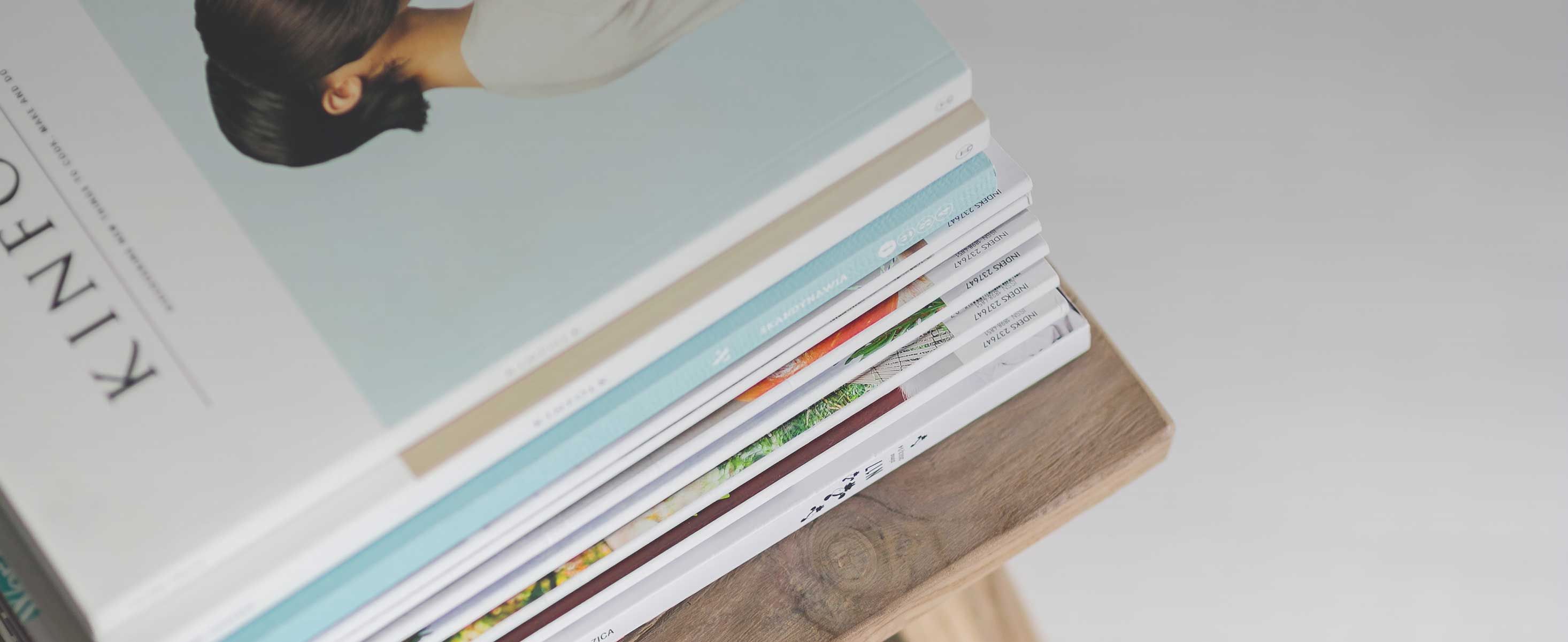
8 minute read
RECYCLING NEWS
Clarios expands recycling with acquisition of Spanish recycler Metalúrgica de Medina
Clarios has acquired Spanish battery recycler Metalúrgica de Medina, the international automotive battery company told Batteries International on March 23.
Metalúrgica, which recycles car batteries and other compounds to obtain pure ingots and other alloys, has an annual capacity of around 59,000 tonnes of recycled lead.
Clarios’ vice president of operations for Europe, Middle East and Africa (EMEA), Jose Domingo, said the acquisition gave the company “access to high-quality input materials and tolling in key regions where we operate.
“The acquisition further centralizes and vertically integrates our business to reduce supplier risks and lower costs.”
Financial details of the deal were not disclosed, but Clarios said the acquisition was “a natural extension” of its existing partnership with Metalúrgica. More than 90% of Metalúrgica’s offtake goes to Clarios.
Metalúrgica is Clarios’ largest tolling partner in the EMEA region and provides tolling — the financial arrangement whereby scrap metal collected by the battery manufacturer is returned and a fee paid for the lead to be recycled, ready to be reused in batteries — for all production scrap and customer cores collected from Clarios’ Spanish plants.
In the EMEA region, Clarios already has nine production sites, five logistics centres, 12 sales offices and one recycling centre.
Neil Hawkes, base metals principal analyst at CRU in the UK told Batteries International that companies such as Clarios have been have been pushing for a long time to secure more lead supplies via tolling agreements for their battery manufacturing plants.
Hawkes said: “Now that they have acquired the smelter, is this a tacit admission that it is easier to buy a smelter rather than toll with it on a third-party basis?
“The hugely fragmented nature of scrap collection across Europe, with lots of small-to-mid-sized players along the chain, makes it difficult for big battery makers like Clarios to make inroads in lifting lead volumes through tolling arrangements.”
Work starts on UAE lead battery plant and processing operations
Ground has been broken for a combined lead acid battery manufacturing plant and recycling facility in the United Arab Emirates (UAE), Italian group Seri Industrial announced on March 22.
The company behind the Dubai Industrial City project — Dubatt Battery Recycling — is a joint venture between Dubai-based Regency Group and Seashore Group. Dubatt is investing AED110 million (about $30 million) in the project.
Meanwhile, Dubatt is discussing a potential technology partnership with Seri group company, Faam Italia, to also produce advanced lithium ion batteries for electric vehicles and other applications.
The 154,000 square-feet recycling plant is to be operational by January 2023, while the advanced lead acid battery plant is set to start operating within the next two years.
Regency Group corporate management chairman, Shamsudheen Bin Mohideen, said the battery plant would be commissioned over the next two years and would produce a “made in the UAE battery brand”. The battery plant will be built on a 70,000 square-feet site.
Dubatt director Hasique Pandikadavath said the small to medium sized recycling plant would start with a 10-tonne-hour battery crusher, a four-cubic-meter fuser and four refining kettles.
The initial recycling capacity would be up to 25,000 tonnes of used lead acid batteries annually, producing 14,000 tonnes of lead ingots and 1,750 tonnes of plastic chips to be sold to battery manufacturers, the medical sector, fisheries and other industrial sectors.
There was no indication provided by the firm as how the slag from the smelting would be disposed of — an issue that has troubled permitting in the region in the past.
Pandikadavath said this represented the recycling of about 35% of the scrap lead acid batteries generated in the UAE each year. “We are planning to double our recycling capacity within a year of commercial production and our plant is built with this arrangement to expand.”
ABR highlights role US recyclers should play in powering energy storage future
The Association of Battery Recyclers (ABR) highlighted the key role played by lead battery recycling in underpinning an expansion of energy storage in the US in new data published on March 16.
ABR, the trade association for North American lead battery recyclers, gave details of the high standards deployed by the industry on a new website launched in the run-up to Global Recycling Day on March 18.
ABR president Rick Leiby said: “Our country’s well established lead battery recycling system has become the standard for creating a circular economy for all battery recycling.
“As demand for battery energy storage continues to rise, the success of lead battery recycling is the benchmark for other technologies.
“Batteries are critical for meeting demand growth in energy storage, for vital industries such as security, data centres, electrified transportation and renewable energy.”
According to the ABR, around 130 million lead batteries are typically diverted from US landfill sites annually, giving the country a 99% recycling rate. In turn, a new lead battery typically consists of about 80% recycled material from used lead batteries.
Today, 62% of the lead needed for a new lead battery made in the US is supplied by US lead battery recyclers.
Leiby said: “These statistics are especially relevant in this time of supply chain disruption. The US must continue to become more self-sufficient by domestically providing the raw materials needed to maintain advanced lead battery manufacturing in the US.”
Ford, Volvo back Redwood Materials’ California collection and recycling push
Nevada-based Redwood Materials announced on February 17 it had launched an EV batteries collection and recycling project in California backed by Ford and Volvo.
Redwood said the car firms are the first to directly support the program — but all lithium ion and nickel metal hydride batteries in the state will be welcomed into the scheme and other car makers are invited to support the scheme.
A spokesperson told Batteries International the program was “focused solely on lithium ion and nickel metal hydride batteries, working directly with auto dismantlers and dealers to find them”.
“The pathways for lead acid are quite mature with 99%+ already being recycled.”
Redwood announced last September it was expanding its operations to produce battery materials for the US market.
The company said it would “safely package, transport, and recycle” these batteries at its facilities in neighbouring Northern Nevada — returning “high quality, recycled materials back into domestic cell production”.
Annually, 6GWh of lithium ion batteries or the equivalent of 60,000 EVs, pass through Redwood. The company said this represents “most of the recycled lithium ion batteries in North America today”.
Ford invested $50 million in Redwood in 2021 for a partnership to create a circular materials supply chain for production of EV batteries in the US. Europe faces major shortages of the key materials needed to make the batteries to power the bloc’s clean energy transition, according to a study published on April 25.
Eurometaux, which represents non-ferrous metals producers and recyclers in Europe, said the independent study by Belgium’s KU Leuven research university showed the bloc could face problems around 2030 from global supply shortages for five metals — especially lithium, cobalt, nickel, rare earths, and copper.
Meanwhile, the study said coal-powered Chinese and Indonesian metal production will dominate global refining capacity growth for battery metals and rare earths — while Europe continues to rely on Russia for its supply of aluminium, nickel and copper.
The study says Europe faces “critical shortfalls” in the next 15 years without more mined and refined metals to supply batteries needed for electric vehicles, energy storage systems and renewable power infrastructure.
Study lead author Liesbet Gregoir said: “Europe needs to decide urgently how it will bridge its looming supply gap for primary metals. Without a decisive strategy, it risks new dependencies on unsustainable suppliers.”
The study recommends that Europe link up with “proven responsible suppliers” to manage environmental and social risks and asks why the bloc has not yet followed other global powers, such as China, in investing in mines to ensure environmental, social and governance standards.
Recycling metals in Europe could produce three quarters of Europe-made battery cathodes by 2050 if it “invests heavily now and fixes bottlenecks”, according to the study.
However, recycling “will not provide a major EU supply source to Europe’s electric vehicle batteries and renewable energy technologies until after 2040”, the study says.
Meeting the European Union’s so-called green deal goal of climate neutrality by 2050 will require 35 times more lithium and seven to 26 times the amount of increasingly scarce rare earth metals, “compared to Europe’s limited use today”, the study says.
Li-Cycle signs recycling, investment deals with LG Chem and LG Energy Solution
Li-Cycle has completed various commercial arrangements to become the preferred lithium ion battery recycling partner in North America for LG Chem and LG Energy Solution (LES), the companies announced on April 21.
The signing of an agreement with LES for the supply of manufacturing scrap for recycling and deals with both LES and LG for the sale of nickel sulphate from Li-Cycle’s recycling Rochester hub, in the state of New York, paves the way for the Korean group’s companies to finalize a $50 million investment in LiCycle.
All three companies said the agreements would support increasing demand for lithium ion batteries and their critical materials for the energy storage and electric vehicle batteries markets — and the partners would continue to explore additional opportunities globally.
Li-Cycle co-founder and CEO Ajay Kochhar said: “We’re thrilled to advance our collaboration… Together, we are driving sustainable global electrification through the creation of this milestone closed-loop ecosystem in the lithium ion battery supply chain.”
The recycling company announced in September that Koch Strategic Platforms (KSP), a subsidiary of Koch Investments Group, was making a $100 million investment in LiCycle through the purchase of a convertible note.
Li-Cycle said then that the incremental capital being raised from KSP would be directed towards the accelerated expansion of the battery recycling footprint, both in North America and internationally.