
24 minute read
2022 AWARD WINNER AND NOMINATIONS
COVER STORY: INNOVATION: TRAILBLAZERS FOR TOMORROW The bipolar battery AWARD WINNER 2022
Winner —2022 — Advanced Battery Concepts
Advanced Battery Concepts matched the strength of the bipolar battery it has developed with the need for emergency energy storage for households.
Advanced Battery Concepts has pioneered the development of a bipolar battery — commercialization of which had not been achieved since the bipolar battery was invented in the 1930s. Now, complete with a new filling technology, the firm has found a good use for its storage system for emergency back up in the home.
The ABC Home Emergency Energy Storage system relies on a foundation of critical technology built into the GreenSeal bipolar battery bank which holds the 18kWh of energy available to be delivered at up to 6.8kW continuous power for home energy supply in the absence of stable continuous grid power.
“Patent pending technology provides for easy integration of additional storage enclosures yielding up to 36kWh of total energy available. Licensees of GreenSeal technology now have access to a commercialized set of technologies that are demonstrating their reliability and performance in the high value emergency power market,” says the firm.
“Of note, is the newest ABC proprietary technology known as “RapidFill” and “RapidForm”. This is the first VRLA battery filling and formation process executed with acid flowing continuously through all cells in the battery from the start of formation to the end of it,” says the firm.
RapidFill results in a complete fill and saturation of all cells in the bipolar stack, regardless of the operating voltage of the monoblock, simultaneously and in under 60 seconds. Multiple 48V batteries are filled and ready for formation in less than one minute.
From there, formation can start immediately on the entire group of batteries at the same time, as acid begins flowing throughout each of the battery cells for the entire duration of formation.
Flowing acid allows for constant specific gravity acid during the entirety of the formation process as well as maintaining constant precise temperature of the battery during the formation execution regardless of the ambient temperature.
All this is done without the use of water baths or other forms of active cooling of the battery “This is a true innovation for the lead battery industry moving continually away from flooded batteries requiring maintenance and toward
moves into the home
AWARD WINNER 2022
maintenance-free VRLA batteries with the highest performance and lowest cost,” says the firm.
“This innovation is facilitated by the unique GreenSeal bipolar lead battery architecture invented and perfected by Advanced Battery Concepts.
“Integrating such unique and proprietary battery advances into a commercial product for home energy delivery is a true giant step forward for the industry.
“GreenSeal bipolar battery continues to represent best in class technology, lowest cost structure, best lifetime value and best battery performance within the lead battery industry.
The HEES system is attractive and functional in addition to providing seamless power transition in the event of a grid power disruption. Taking up minimal floorspace and fitting in almost any available area in the home, the HEES system can be placed in the garage, attic, basement, utility room or even in a living space.
Expanding on the HEES initial product capability, a daily cycling system is staged for commercialization in later 2022. This daily cycling system is built on a scientific and engineering platform of first principles resulting in GreenSeal bipolar battery design rules created and validated by ABC.
Those design rules govern the performance of the GreenSeal system under controlled cycling regimes predicting cycling lifetimes with astonishing accuracy.
ABC has internally developed the Home Emergency Energy Storage System from the ground up to integrate itself with the strength of the GreenSeal battery. MASTERS OF INVENTION
Edward Shaffer II Edward Shaffer II is CEO and Founder of Advanced Battery Concepts. He has spent the past 14 years focused on developing technologies to accelerate adoption of much needed alternative energy systems. In 2009, he established ABC to commercialize ground-breaking, large-format, rechargeable battery technology termed “GreenSeal”. Throughout his career, he has worked across a variety of advanced dielectrics for electronics, optical materials for displays, materials for energy storage and photovoltaics. He has held a variety of roles including new business development, global R&D manager and research scientist. He received his PhD in Materials Science from MIT.
Jon Joslin Jon Joslin has 30 years of experience in all aspects of financial management and business consulting. He has broad experience working for both an accounting firm and both small and large companies in a number of industries, from construction, manufacturing, wholesale and retail. In addition, he has started and run a number of companies. He has also served in his local government as a past mayor for the City of Mt Pleasant and a 15 year city commissioner.
Michael Everett Michael Everett brings over 30 years of experience in a variety of technology-based industries, most recently the senior. vice president of engineering for Trojan battery Company. His previous positions include CTO of Maxwell Technologies and senior director of engineering and research at 3D Systems Inc. While working with Trojan Battery, he was responsible for overseeing Trojan’s product development and research activities including all technical intellectual property innovation.
Electrical System Specifications
Battery Series Number of 48V Battery Units per battery box Usable Energy (kWh) Rated AC Power (kW) Max. Continuous DC Current (Charge or Discharge, A) Nominal Battery Bank Voltage (V) DC Discharge Round Trip Efficiency
Standard + 1 Standard + 2 Standard + 3
GS4830-1M
12 18 24
17.3 25.8 34.5
6.8
180
48
>88%
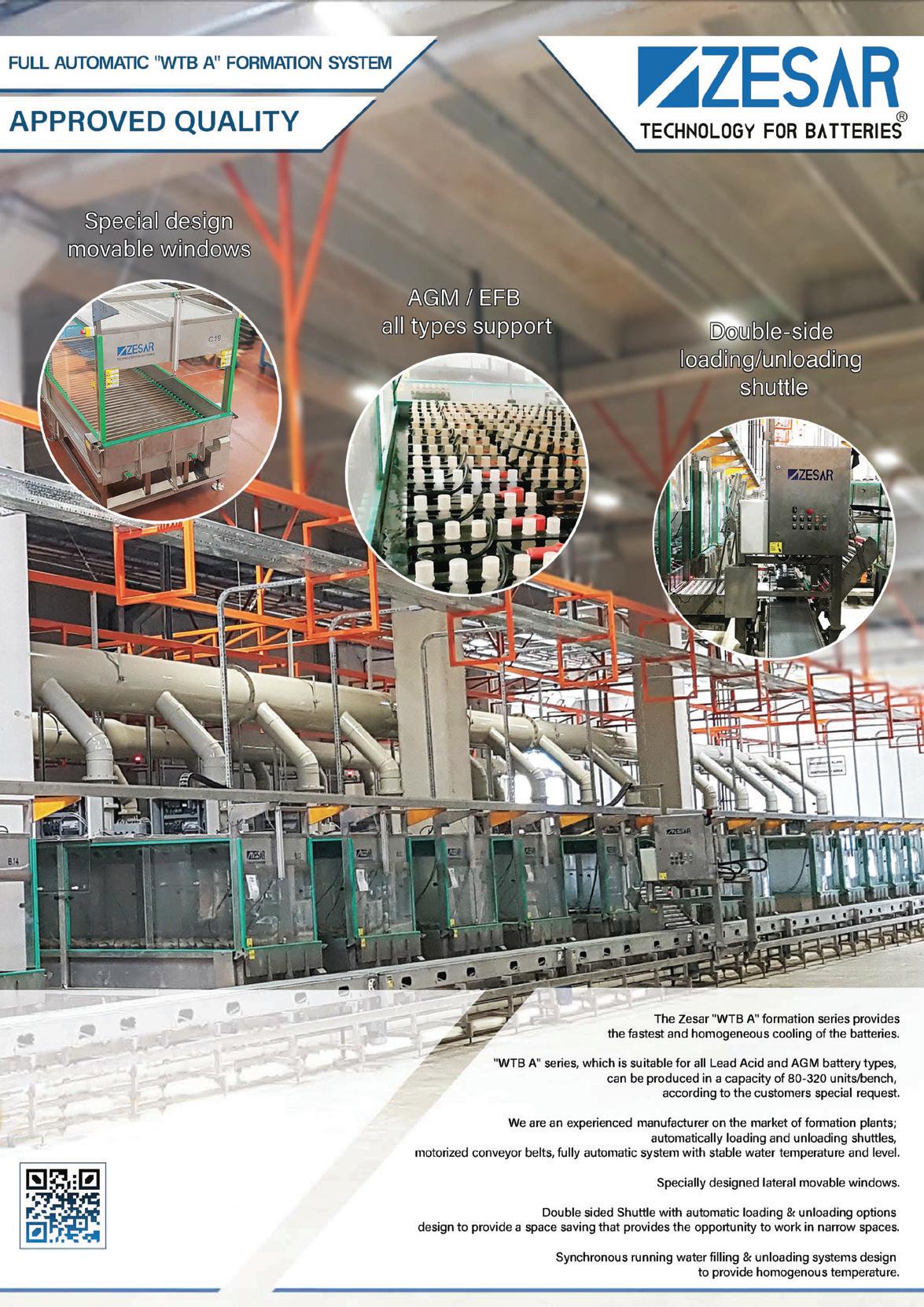
COVER STORY: INNOVATION: TRAILBLAZERS FOR TOMORROW AWARD NOMINEE 2022Abertax, the Maltese specialist battery product developer, has come up with a new filling process for gel batteries that promises improvements in battery quality, an environmentally sensitive process and requires low investment.
A better gel formation process
Abertax’s innovation award submission is based on a new patented gel circulation process that does away with standard filling processes for gel batteries. The firm says it needs less investment in machinery, reduced production time and labour cost.
It is an environmentally friendly process — there is no acid wastage and much better quality/performance of such manufactured batteries. From the results so far, it seems that this system will be adopted as the standard by major gel battery manufacturers
“As soon as KD Merz the inventor, came up with this brilliant idea, Abertax, being a company encouraging such type of innovation, and environmentally conscious, supported his idea,” says a company spokesperson.
“We immediately completed an agreement with a third party company to build and install such systems to undergo field tests at a battery company, while applying for patent protection.”
Below follows a description of the traditional ways of gel filling with the Abertax method.
Direct gel filling (formed batteries).
The oldest method to fill lead acid batteries with gel is the filling of the silica/acid mixture into the batteries or cells having already formed plates. The gel is pre-prepared by a homogenous mixing of fumed silica (SiO2) with sulfuric acid having a silica concentration of around 6% and filled by a vacuum filling machine.
With suitable machines and equipment, a good and uniform gel filling can be achieved. However, there is always a risk, and in particular at higher temperatures, that the gel is jellifying quite fast inside the cells and can inhibit a complete, homogeneous and consistent coverage of the electrodes.
Such dry areas on the positive and/ or negative plates results in a loss of capacity and can cause premature failure.
Gel formation process
A low cost process is direct gel formation. After filling the gel into unformed cells or batteries a formation program is started. It sounds easy with no high investment in equipment, but the formation time is quite protracted — seven days or longer and needs a number of different charge and discharge steps.
Beside the very long formation time, the quality and performance of the finished product is not very good and this is one of the most expensive processes.
Two shot gel filling process
The batteries are formed with sulfuric acid. After formation the batteries are discharged to a level of 80% to 90%. The batteries are then turned upside down to drain the remaining low density acid from the battery. Shortly after the drainage, the batteries are filled with a prepared silica/acid mixture in the same acid density as the drained acid. Afterwards, the batteries need to be recharged.
This method of gel filling is the mostly used technology today, however, it has several disadvantages, such as: • If the waiting period after drainage of the acid and gel filling takes too long, the electrodes, in particular the negative plates can dry out and may cause filling problems. • Another negative point is to achieve a good homogenous gel distribution inside the cells. • In particular in block batteries where the lid design causes acid to accumulate when the battery is turned upside down to drain the acid.
The Abertax gel circulation process
This new method introduced in the gel technology production of VRLA batteries follows the two shot gel filling process up to the formation step. The idea is to transform the liquid inside the cells into gel without the draining process.
This is done by a novel circulation process which circulates the liquid in the formed cells while adding the silica in the process in a gradual way until the perfect gel mixture is achieved in the cells.
After the formation, the cells are simply connected to the proposed gel circulation system and the controlled process is initiated until the right
KD MERZ
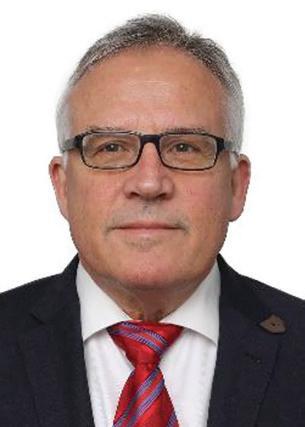
KD Merz is the vice-president for technology at Abertax Technologies and is also a council member, where, in parallel, he is also involved in research and development work on VRLA Battery improvements.

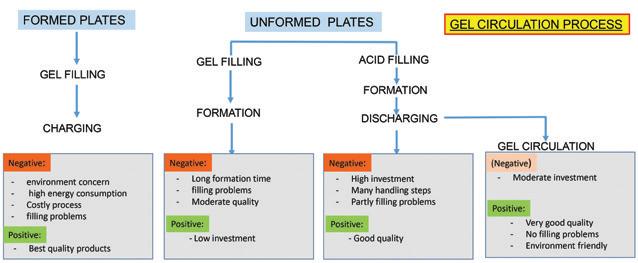
COVER STORY: INNOVATION: TRAILBLAZERS FOR TOMORROWAWARD NOMINEE 2022acid/silica concentration is reached.
The first step is the preparation of the gel/acid mixture in the mixing tank. The acid specific gravity and the silica content of this mixture depends on the conditions of the cells after the formation followed by an electrical discharge process to lower the acid specific gravity.
The specific gravity of the acid in the mixing tank is set to be the same level as the acid specific gravity in the discharged formed cells.
The silica content is calculated based on the electrolyte exchange volume and the required (final) silica content in the cells.
After the gel/acid tank mixture is completed (homogeneity can be tested with the syringe test), this thixotropic dispersion is ready for the circulation filling process.
The formed and discharged cells are connected to the gel circulation unit and the gel circulation is started by activating the pump in the mixing unit.
The process will stop when the silica mixture in the tank and cells ends up to be 12%.
The time of the whole circulation process depends on the overall volume of the acid which needs to be replaced in the cells. In an example of 150 litres it will take about 38 minutes.
Right after the completion of gel circulation, the cells/batteries are disconnected from the unit and prepared for a recharge. The charging regime should be of a regulated IU or IUI regime with a voltage limit during the U phase of 2.45 vpc.
From the numerous and regular quality checks done over the production lines in the past two years, it is evident that apart from an economic and cost efficient gel filling process, much better quality cells are produced using the Abertax gel mixing process.
Gel mixing and circulation system — actual installation
Gel filling processes (comparison)
Gel filling processes: investment and efficiency
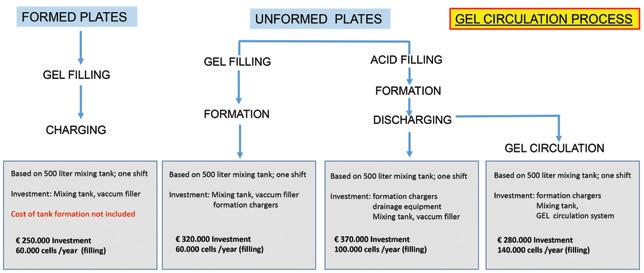
ADVANTAGES
Apart from offering excellent good performance and quality results, this new, patent-protected and innovative process for the filling of gel batteries, offers several remarkable advantages both financially and environmentally.
The avoidance of draining the cells in the commonly used two shot process has itself a huge impact. This offers a huge reduction in time on the overall process, no acid dumping with its risks and consequences, much less labour intensive, avoid exposure of the plates to air, and above all the elimination of possible air pockets while filling.
The battery lifetime is optimized hence reducing the recycling frequency and its related environmental impact and ensuring that guarantee claims due to filling problems is eliminated.
When considering a new gel filling system the capital investment using this method is cheaper and occupies less space when compared to the other methods especially the two-shot method as no drainage equipment and vacuum system are required.
COVER STORY: INNOVATION: TRAILBLAZERS FOR TOMORROWAWARD NOMINEE 2022Daramic has featured in the innovation awards since their inception in 2016 and has always been a strong contender to gain top ranking. This year it presents HD plus, another step change in separator performance.
The battle for the yet better separators
Daramic has a long history as a pioneer in the advancement of battery separators. So in one respect it’s perhaps fitting that the inventor of the polyethylene battery separator should unveil the next way forward in battery separator design and capabilities. The product known HD Plus is a step change in the development of deep cycle batteries and is an advancement of an early product, simply called Daramic HD.
One of the technological problems associated with the lead-acid battery is the self-discharge of the negative plate as a result of the deposition of antimony on to the sponge lead electrode, a process known as antimony poisoning. This results in gassing and water loss and eventually a shorter battery life. Antimony, however, is a useful additive for lead batteries in that it can increase conductivity of the grid enabling deeper and better cycling.
Daramic points to five features that the new HD Plus separator provides. These are: • Improved polyethylene formulation suppresses the effects of antimony poisoning, yielding longer life • New formulation provides lower internal resistance, improving charge acceptance and increasing capacity • Sealable for both envelope or sleeve automation provides protection from short circuits and higher manufacturing yields • High oxidation resistance • Optional glass mat for active material retention
The key benefits of HD Plus, according to Dawn Heng, vice president and managing director for global marketing and Northeast Asia, is that firstly, it exceeds battery life requirements by counteracting the negative effects of antimony poisoning including superior oxidation resistance and reduced water loss. And secondly, on average, HD Plus increases capacity by 9%13% versus standard separators, resulting in increased back-up time for users.
Daramic has always been a regular and strong contender in the BCI innovation awards.
In 2019, Daramic and Huff Technologies developed a way of

Daramic HD Plus at least doubles cycle life
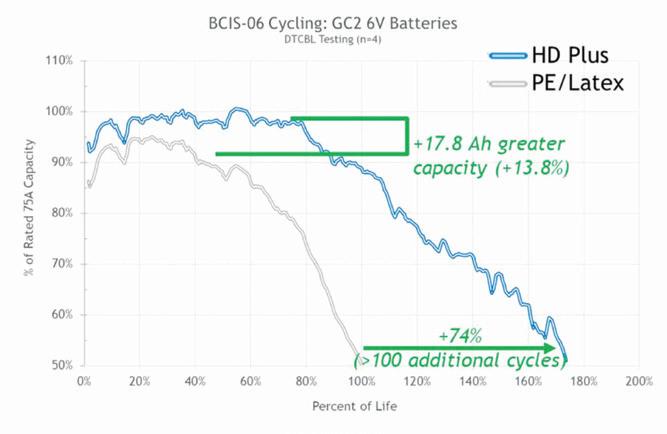
HD Plus gives more than 100 additional cycles compared to PE rubber/latex separators HD Plus also gives >17 Ah additional capacity
HD Plus gives longer life and more capacity than PE Hybrid separators
better simulating how batteries perform in the real world by simulating how they move around during everyday use. For this it received a distinguished mention.
The product was the Daramic Shuttle Table which was designed to mimic real world scenarios during testing. It was developed because the companies acknowledged that in all types of environments, vehicles and the lead acid batteries they use are constantly moving. The system allows for a direct comparison between batteries based on different working patterns and battery environments. It will enable the testing and validation of a variety of passive acid mixing devices, the company said, as well as many standard industry tests performed while the batteries are in motion. This includes the testing of tall motive power and deep cycle batteries, while providing a safer battery testing environment.
In 2018 the firm showcased its latest product using Carbon Coated Separator Technology. Developed to support operations in partial state of charge, utilizing the separator as a carbon carrier, dynamic charge acceptance is improved. It does this by reducing sulfation crystal growth, delivering a more active surface area on the plates for improved conductance of the electrode.
In 2017, using advanced computational fluid dynamics, Daramic developed two new separator solutions — Daramic EFS and Daramic RipTide. Daramic EFS is specifically designed to support startstop vehicle batteries by reducing the battery’s internal resistance and improving voltage drop and CCA. Daramic RipTide combines the latest innovations of Daramic with novel separator profile designs using advanced computational fluid dynamics computer modelling to enhance EFB durability by reducing acid stratification in a partial state of charge environment, which is more typical in start-stop applications.
Daramic’s first entry to the BCI Innovation Awards in 2016 was for a product innovation invented three years ago with research continuing on further refinements. Called DuraLife, this helps protect and maintain the quality and performance in battery designs that use less lead content — a technique that many battery producers have adopted as a way of reducing the overall cost of their products.
Attribute
Backweb thickness (mm) Electrical resistance (mΩ-cm2) Porosity (%) CMD elongation (%)
*Daramic Internal Testing
Typical value*
Rubber HD Plus™
0.400 0.300
450 165
38 55
78 200
AWARD NOMINEE 2022
The key benefits of HD Plus are that firstly, it exceeds battery life requirements by counteracting the negative effects of antimony poisoning including superior oxidation resistance and reduced water loss. And secondly, on average, HD Plus increases capacity by 9%-13% versus standard separators, resulting in increased back-up time
for users. — Dawn Heng, Daramic
WHY DEEP CYCLE BATTERIES MATTER
In North America, the lead acid battery industry delivers around 20 million deep cycle batteries, annually, they are used in a variety of applications and golf carts, floor scrubbers and general utility vehicles rely on lead acid batteries to deliver higher capacities for extended life on the golf course, the showroom floor and out in the field,
Alternative battery technologies, especially lithium ion are pushing the boundaries regarding what is expected of deep cycle battery performance.
As a result, lead acid batteries are facing unprecedented challenges in deep cycle markets. to close the gap on cycle life capacity and operations and partial state of charge users of lead acid. The Daramic HD Plus separator will be yet another tool challenging the in-roads of lithium into traditional lead markets.
Deep cycle batteries are pushing for longer battery life that far exceeds the warranty periods offered today. Lowering warranty return rates through a more robust battery design allows battery manufacturers to increase cost savings while meeting these shifting market needs.
In addition to longer battery life extended run times are also becoming a priority to meet this need users need higher capacity lead asset batteries to power these deep cycle vehicles.
Lead acid batteries are facing unprecedented challenges in deep cycle markets to close the gap on cycle life capacity and operations and partial state of charge users of lead acid. The Daramic HD Plus separator will be yet another tool challenging the inroads of lithium into traditional lead markets.
COVER STORY: INNOVATION: TRAILBLAZERS FOR TOMORROWAWARD NOMINEE 2022Hollingsworth & Vose has nominated PowerFill for the innovation which it says is an improved and faster acid fill that can include a 12% increase in battery capacity and cycle life.
Better acid filling, better battery performance
One challenge many customers encounter during AGM battery assembly is the slow and uneven filling of acid electrolyte. Slow filling reduces the battery assembly speed while uneven acid distribution in the AGM separator and plates potentially cause dry spots and black spots on the plates during battery formation. Furthermore, uneven acid distribution can degrade battery performance.
A key factor affecting the acid filling speed is the gas pocket trapped toward the center of the plates and AGM separator. The gaseous species in the pocket is air and possibly CO2 generated by the reaction of the acid with carbonate species in the plates. The gaseous species have the tendency to hinder the flow of the acid into the center area, unless removed from the battery.
H&V has recently developed PowerFill AGM to solve these challenges by enhancing the surface of the separator to create open channels. With the open channels on the PowerFill AGM separator, the gaseous species in the pocket can escape more easily from the battery during the acid filling process, thereby allowing acid to flow quickly and evenly into the center of the plates/AGM. The PowerFill patented technology can be applied to various types of AGM, and the resultant separators still retain the same strength and compression retention behaviour of the base AGM. PowerFill has demonstrated it can increase production throughput and battery performance for a wide-range of applications.
“H&V is a global leader in filtration and energy storage solutions. Our advanced materials are used in nearly every industry and touch every aspect of modern life. Wherever you work, live or travel, chances are an H&V solution is close by, contributing to a cleaner, healthier, more sustainable world,” says the firm.
“H&V is the lead battery industry’s only vertically integrated Absorbent Glass Mat (AGM) producer.”
POWERFILL — ADDS VALUE TO BATTERY PRODUCERS AND END-USERS IN THREE WAYS.

First, it increases battery assembly speed and throughput. PowerFill has demonstrated electrolyte acid filling time can be reduced over 50% allowing battery producers to reduce cost.
Second, PowerFill improves the quality of lead batteries since acid filling is uniform across the AGM separator and plate/electrode. Better batteries means improved battery assembly yield.
Finally, PowerFill has demonstrated battery performance improvements to include 12% increase in battery capacity and cycle life.
Zhiping Jiang holds a PhD in Chemistry from Rensselaer Polytechnic Institute (1990) and MBA from University of Massachusetts at Lowell (2005). He began his industrial career in 1992 after a two-year’s post-doctoral study at Materials Processing Center/Massachusetts Institute of Technology. Over the years, he has worked on product and technology development in various areas including batteries, battery materials and separators. In 2012 he joined Hollingsworth & Vose Company as the chief scientist in the Battery Division. He has been awarded with 32 US patents, and received R&D Magazine’s Year 2000 R&D 100 Award for technology innovation.
ZHIPING JIANG
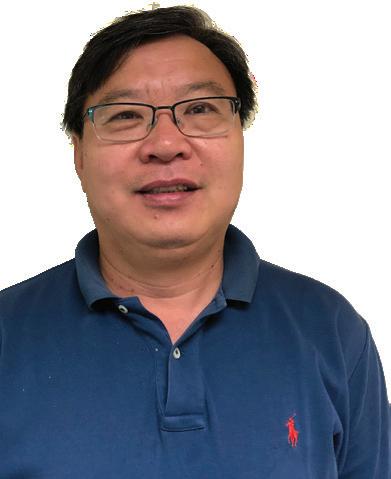
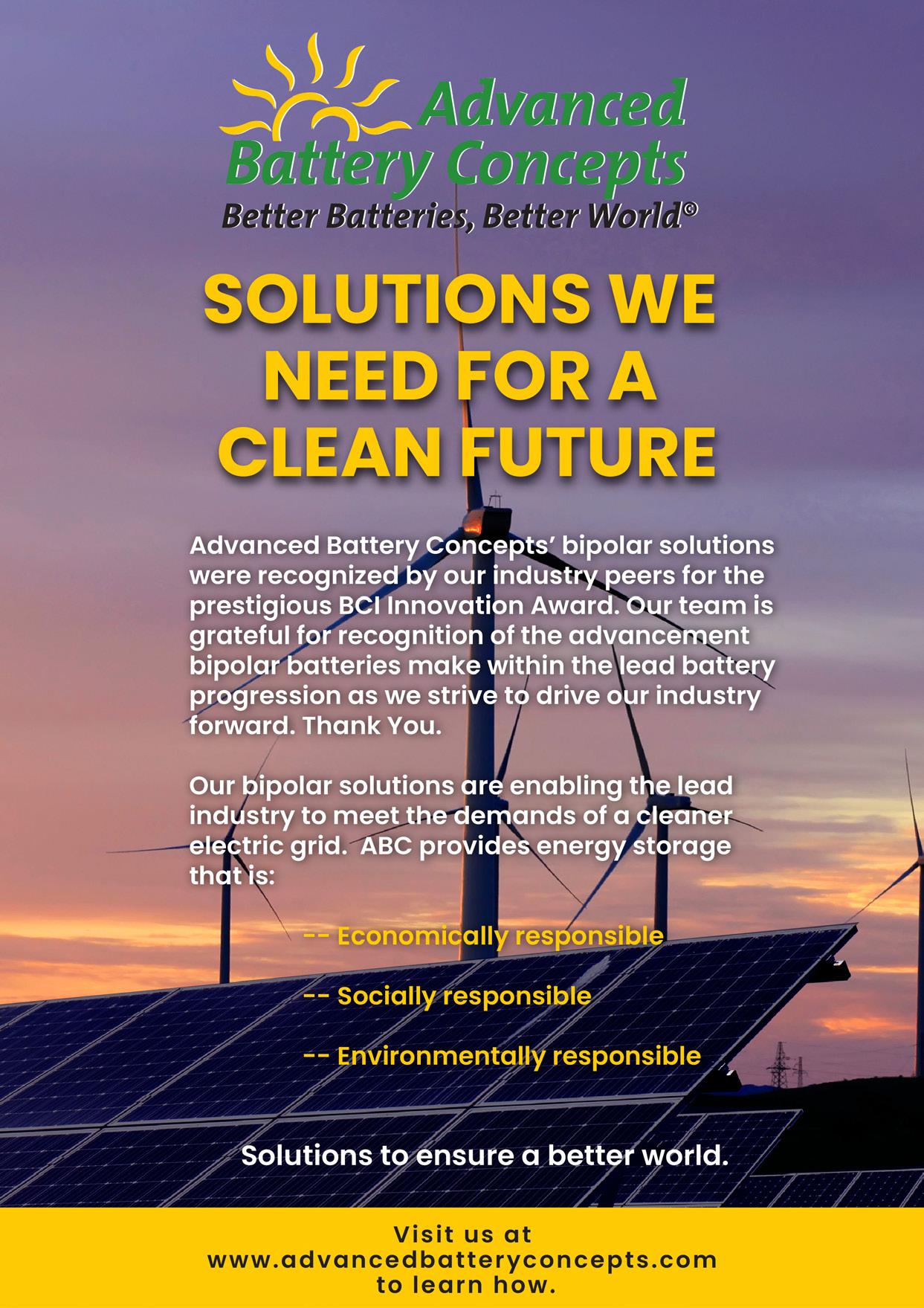
COVER STORY: INNOVATION: TRAILBLAZERS FOR TOMORROWAWARD NOMINEE 2022This year Meszaros Tamas submitted an entry suggesting that a radical new grid design using ultrafine fibres could dramatically improve battery performance.
Breaking through the 100Wh/kg power barrier
An unusual entry from retired Hungarian academic Meszaros Tamas looked at what he named Uff (ultrafine fibre) technology tied with a manufacturing process he called the Blewin System — the intellectual property of both of which are his.
The Uff solution keeps the geometry of the grids unchanged with the already known in-plane arrangement, but in the third dimension it transforms the now-usual convex quadrilateral and the already improved triangle cross-sections into concave polygons.
Figures 1 and 2 above: note the extended electrochemical active surface ratio and there is a 40% raw material saving in lead, there is also lower internal resistance allowing for more rapid charging
Research on these grids — which had even achieved a specific power of around 80Wh/kg at the turn of the 21st century — was halted. At this level r, the system resulted in 30% lead savings / batteries, as well as a reduction in internal resistance that reduced the previous charging time to less than a third, eliminating unnecessary heating and acid vapor emissions.
“Optimized current paths and extremely low internal resistance have made it suitable for handling extreme power fluctuations and much more, making the four variants capable of performing virtually any energy storage task for a quarter of the price of a Li-base of the same power (capacity),” says Tamas.
The internal elasticity of the Blewin system is important because it can accommodate parameters that are not uniform but fit in an internal structure.
Figure 3 above illustrates the size and design of the smallest (moped) battery grid and the magnified detail of the microporous surface waiting for the paste.
“The grid manufacturing system is capable of producing any shape that is suitable for an acid lead-acid battery grid and produces better results than current products,” Tamas says.
“It can be seen that the grid is still built of ubiquitous convex cross-section elements, so the ratio of the electrochemical surface area to the fiber cross-section (mass) is still not optimal.
The cross-sections in figures 1 and 2 improve the crosssection-to-surface area ratio by more than 25%. The effect of this can be demonstrated by mathematical modelling, any solution will bring the value of the specific power above the value of 100Wh/kg (102~105).
Mathematical modelling also offers additional curiosities, as the use of grids with such a cross-section results in a lead saving of over 40% (with the same performance), e.g. it results in a weight loss of over 4kg for a normal (60Ah) starter battery, which costs ~ $8 in lead.
The extremely high electrochemically active surface results in extreme load-bearing capacity and a significantly shorter charge (also) with a higher current. This presupposes, for example, an outstanding recuperation capacity for urban cycle vehicles and the ability to withstand extreme current changes in wind turbines, says Tamas.
The material of the grids is pure lead, but it can be hardened with an alloy that does not cause internal damage (Na), any Ca alloy should be avoided due to its tendency to form gypsum.
The production of Uff solution grids requires the transformation of a previous machine system operating on a similar principle, primarily by entrusting process control to more precise artificial intelligence and transforming it into an automated process, he says.
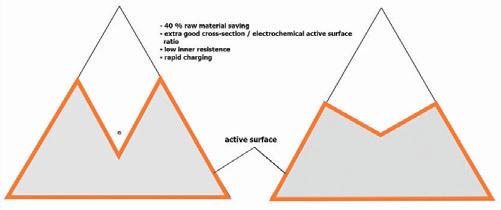
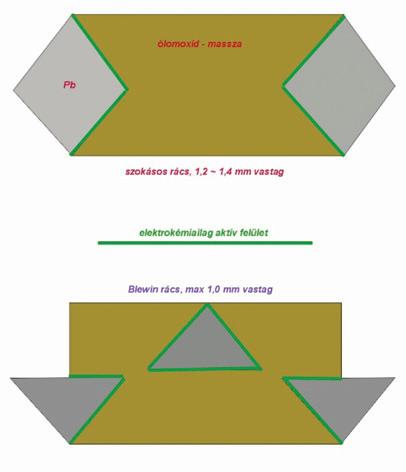

COVER STORY: INNOVATION: TRAILBLAZERS FOR TOMORROWAWARD NOMINEE 2022Michigan-based manufacturing technology developer Vivet has designed a novel manufacturing process that it says can be applied to a number of industries, including for the production of lead acid batteries.
Where repetition leads: costs decrease, profits rise
Vivet co-founder and director of R&D, Amjad Hashem, is leading R&D engineering efforts to find, develop, and build unique projects that aim to disrupt manufacturing industries.
In its innovation award submission, Vivet says its ‘Repeating Layer Process’ (RLP) manufacturing system reduces costs as equipment is scaled up.
RLP is suitable for products that have a multiple of sub-components or operations, which repeat for a defined number.
The system design is scalable, enabling companies to add more machines to expand production at any time, while keeping downtime to a minimum and with no changes to the existing equipment being used.
In a case study prepared by Vivet, the company shows the build of a single system to build a battery module. The system is later scaled to seven times the initial capacity for four times the initial cost.
According to the study, the first build of the assembly system could produce more than 40 battery modules an hour and a total of 205,000 in the course of a year. This is for an initial estimated investment of $1.5 million.
The second layer would increase the capacity by 1.9x (390,000 modules a year) for a total of 1.3x the initial cost (an estimated $2 million).
The third layer would increase to 3x the capacity (615,000 modules a year) for a total of 1.7x the initial cost.
As the system is scaled further, total costs and the final manufacturing cost per unit “will fall to levels the market has never seen before”, Vivet says.
RLP systems are configured to continually perform operations until a specified number of layers is completed and then remove the product from the system. The repeating layer may include one or multiple parts.
“The process is an alternative to the linear method of manufacturing and offers a totally different level of manufacturing efficiency.” Says the firm.
“Our process not only improves production, but also quality, efficiency, scalability, modularity and more.”
The company says its process also introduces the concept of ‘zero system downtime’, with production able to ‘bypass’ any individual machine that is out of operation such as for repair or maintenance.
This in turn eliminates bottlenecks and increases utilization of equipment.
Vivet says its process is the first to give companies the option of increasing investment incrementally in line with its production requirements — providing an ability to build a lowcapacity system for low investment, without existing equipment becoming obsolete.

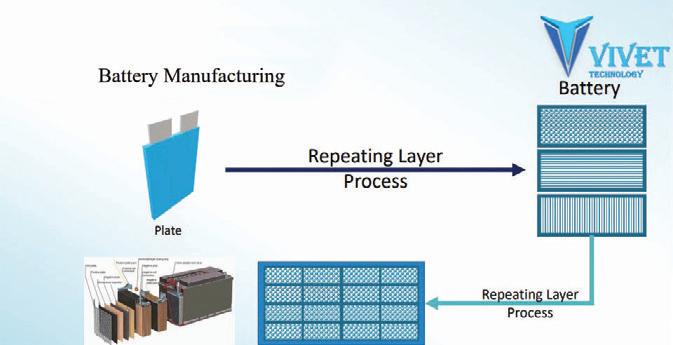
The capacity of the production system can be scaled to over 5x the initial capacity. Vivet says it can provide several options of manufacturing operation capabilities through its manufacturing branch and partners.
