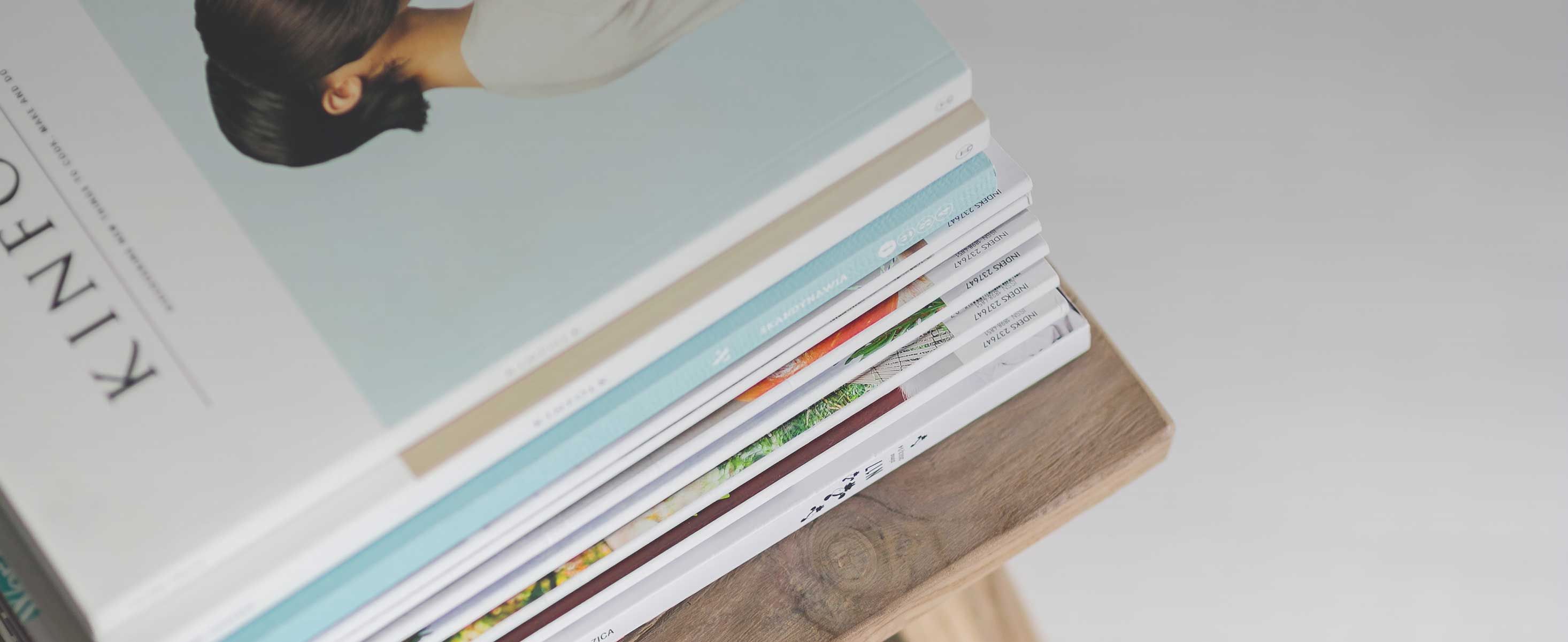
4 minute read
Getting the maximum value out of lead battery slag
Disposing of the slag from lead battery recycling has always been problematic — the end residue from smelting is toxic with a high lead content and traces, among other things, of antimony, arsenic, bismuth and cadmium. This slag, perforce, has to go into landfill.
Attempts to reuse it in, for example, paving blocks is just kicking the can further down the road. Finally, the paving will crack up and the poisons will leach out. Now perhaps a permanent solution is in sight.
Gopher Resource has developed a Slag Cleaning and Recovery of Useful Metals (SCRUM) process that is says can reduce its solid waste footprint by 99%.
The patent-pending approach, takes end slags that are typically landfilled as waste and economically recovers the tin and lead for reuse in the lead battery supply chain.
Each year the lead battery industry globally disposes of end slags that have approximately 100,000 tonnes of lead, and 30,000 tonnes of tin. This tin loss is equivalent to three quarters of US domestic tin consumption
This SCRUM process slag is a value-add product that avoids landfill for reuse in building construction and roadway aggregate industry sectors.
The SCRUM process uses furnace fuming technology to separate the tin and lead into a concentrated fume form with very high selectivity and efficiency, leaving behind a “cleaned” bulk iron sodium-silicate “SCRUM Slag”.
Previous fuming efforts have not been feasible due to poor selectivity and high partitioning of bulk slag components, in particular sodium, into the fume. “Our process leaves greater than 70% of the sodium in the slag, and recovers 99.9% of both tin and lead in the fume,” says Gopher Resource.
“This tin and lead concentrated fume can be combined with other byproducts for refining into lead, and LME tin. The ability to recover these metals from lead battery recycling slag in a safe, economically feasible way is an industry first.
“Waste minimization is a key goal of ours in developing this process. To reach that goal our SCRUM Slag has trace ppm levels of RCRA elements enabling its use in a variety of value added applications.”
This cleaned slag is applicable for use in commercialized products such as cements and roadway aggregates. SCRUM Slag valorization improves process economics, minimizes our environmental footprint, and is an embodiment of the circular economy.
How it developed
Gopher Resource has supported SCRUM process development efforts for over five years with hundreds of person hours and over $1 million spent in external and internal funding.
Internal R&D resources were committed in 2016 when desk studies began to develop a process to recover metals from the blast slag and render a “cleaned” slag available for value-addded applications.
As part of these investments, from 2017-2019 various process technologies were evaluated and tested at the lab scale, including hydrometallurgical and mineral processing technologies. These technologies were found not viable, and pyrometallurgical process routes were then tested.
Gopher said it initially investigated pyrometallurgical lab scale work on “extreme” methane reduction which was promising but ultimately unsuccessful, and the research results were published at the Pb/Zn (LeadZinc) 2020 conference.
Pyrometallurgical fuming
Pyrometallurgical fuming was then evaluated, which has been demonstrated in zinc and other industries but not successfully in the lead battery recycling industry. There was some reluctance to strongly pursuing pyrometallurgical fuming processing routes as every single expert Gopher conferred with discouraged this as being practical.
Conventional wisdom argues selective fuming in high sodium slags doesn’t work as there isn’t sufficient selectivity in the separation. “We persisted and after repeated lab scale tests and advanced thermodynamic calculations, we generated some initial results that were promising enough to proceed to the next stage,” says the firm.
Gopher Resource continued to support this work through piloting efforts through 2020-2022 where various components of the SCRUM process were tested at larger scales. The firm worked with multiple partners to test various process parameters and equipment configurations, and eventually discovered a set of process conditions that separated 99.9% of the tin and lead to the fume, keeping >72% of the sodium in the slag.
To date, SCRUM has been successfully piloted at scales of 100lb through repeated tests by multiple independent parties, with 1000s of lbs of material having been processed.
“These pilots used equipment and process parameters that are realistic, scalable, and economic. In parallel to the SCRUM process development work,” says the firm.
“The SCRUM process successfully demonstrated pilot results on metal fuming, impurities management, and metal conversion and refining.
“SCRUM slag has also been demonstrated to be sufficiently clean for a variety of applications. Process information collected in our pilot tests provide engineering information for equipment sizing, labour, utilities, consumables, etc., to generate CAPEX and OPEX estimates.”
The firm says that product streams with required specifications have been demonstrated to provide realistic cashflow forecasts for lead bullion, >99.9% tin, and SCRUM Slag.
“Cashflows are resistant to low tin prices and NPV (net present value) analysis has shown favourable results. We’re evaluating next steps and appropriate strategies to bring SCRUM to market,” says the firm.
The future
Gopher Resource continues to have multiple external projects funded looking at value add applications for its slag past 2025. These include road aggregates, cement paving stones, and advanced manufacturing applications such as 3D printing.
Development of this technology has been a global undertaking with test work conducted at Gopher Resource facilities and partner facilities in six countries across North America, Europe, Australia and Africa.
This cleaned slag is applicable for use in commercialized products such as cements and roadway aggregates. SCRUM Slag valorization improves process economics, minimizes our environmental footprint, and is an embodiment of the circular economy
WHAT’S LEFT OF THE SCRUM SLAG
The SCRUM Slag byproduct is also applicable for use in building materials such as concretes and dense or porous monoliths. Slag is granulated using air or water and made into a slurry mortar via a binder/activator [such as Metakaolin (MK; Al-Si), limestone (LS; CaCO³), Alkali salts (mainly Na) (Na2CO3 (Nc), Na2SO4 (N$), NaOH (NH), Na-silicate (NS)],
Controlling the TBRC slag to retain the high concentrations of sodium, provides benefits of a natural binder/ activator in the slurry. This reduces the amount of additives needed to meet specifications for use. This mortar has multiple uses in structural applications or design applications and uses 5x less cement than typical mortars resulting in approximately 80% less CO2 production. The strength of the mortar projections matches that of current commercial produced mortars.
These mortar products allow for efficient construction customization and complexity in building systems, while reducing CO2 footprint.
Leaching results from column tests have shown non-hazardous solids. The mortar can be 3D printed or cast into different types of monolithic construction materials (dense or porous).
Daramic has featured in the innovation awards since their inception in 2016, receiving an Honorable Mention for its HD Plus separator in 2022. This year, the company presents its latest innovation — the HiCharge advanced separator.