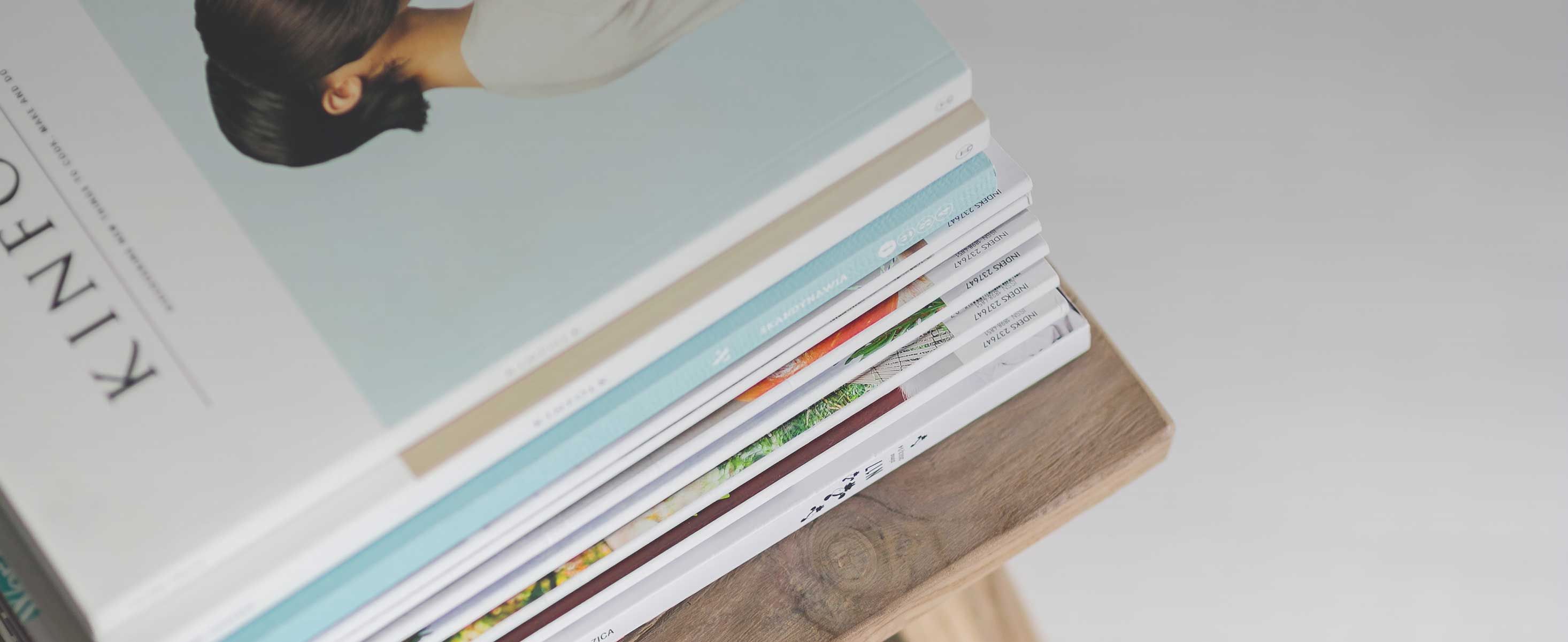
2 minute read
Electrifying the recycling process at room temperature
Complimentary Technologies
ACE Green says it is piloting several important new initiatives.
• Production of 99.99% pure e-lead
The firm says it can now directly obtain 99.99% high-purity e-lead from battery paste. This new process is also at room temperature, requires no external heating and can use the same commercial-scale electrolysis machines.
• In-process regeneration of desulfurization agent
ACE has developed a modified process to regenerate the desulfurizing agent, helping to further reduce costs. This improvement does not require any changes or modifications to the electrolysis process.
• Electric kettles for melting e-lead
By utilising a new electrically heated kettle, the firm say it is moving towards 100% electrification of the lead recycling process.
• Baghouse dust treatment
The firm has a room temperature technique to treat and recover lead from baghouse dust.
• Smelting furnace slag treatment
Fascinatingly, the firms says it has created a technology to treat and extract metals from slag generated during conventional smelting. Besides the recovery of lead and iron, there is also a reduction of more than 65% in the net solid waste for disposal in landfill.
US corporation ACE Green Recycling
Inc has developed a proprietary new technology that produces no waste products that require smelting and furnaces. The process, the firm says, operates at room temperature with no carbon or heavy metal emissions. It replaces the conventional smelting furnace with an oxygen-producing pH-basic electrochemical process. This modular process is also readily scalable to suit any production capacity needs.
“Our zero-emissions technology is a game-changer for the heavily regulated secondary lead industry,” says Farid Ahmed, business development manager for ACE Green. “Automated material handling enables plant operation with minimal operator intervention, further reducing exposure to health and safety risks. Higher lead recovery and lower waste generation contribute to our process having more favourable economics than traditional smelting.
The two streams of lead components from the battery breaker — battery paste and battery metallics — are treated separately.
Battery paste is treated with proprietary chemicals in the presence of sodium hydroxide, removing sulphur and preparing it for the next stage. This is then fed to the room temperature electrolysis process, producing ‘spongy’ lead of around 99.95% purity.
This lead sponge is then mechanically pressed into ‘e-lead’ briquettes, which are then transferred directly to normal melting kettles.
After minimal conventional refining and casting into ingots, the finished lead has a typical purity of better than 99.985%. The small quantity of drosses produced during refining can be treated by a separate proprietary electrochemical technique to recover the lead content or recycled through smelting.
Battery metallics such as grids, poles and connectors are first chemically cleaned with proprietary chemicals to remove any paste adhering to the solid lead surface. These clean metallics are then melted directly in normal process kettles. At this stage, the metal can be refined to produce pure lead or alloyed to obtain highvalue lead alloys. As these metallics haven’t been smelted, all the original alloys elements such as antimony are retained in the lead.
ACE Green has been operating a commercial-scale demonstration plant near Delhi through its Indian subsidiary but the process equipment was disassembled to accommodate ACE’s new commercial scale lithium ion battery recycling operation. Luminous India, part of the Schneider Electric group, was previously supplying scrap batteries as well as buying the lead produced at this facility.