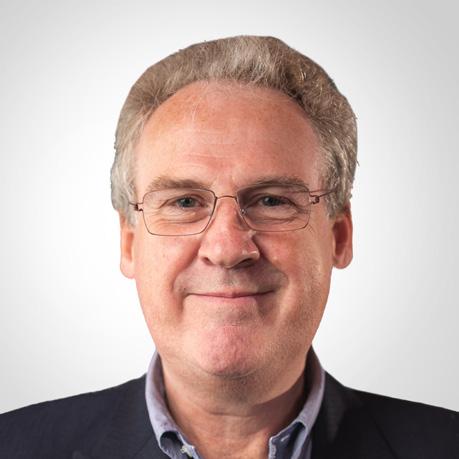
6 minute read
10 Tops Tips for Entrepreneurial Rotomoulders
Recently I was kindly asked to take part in an on-line Rotomoulding Leadership Discussion with Peram Prasada Rao and Martin Spencer of Tecnobiz. You can view the recording on YouTube if you are interested - RotoMoulding Leadership #9 : Conversation with Martin Coles, Group CEO, Matrix Polymers.
One of the questions I was asked was what are my top 10 tips for entrepreneurial rotomoulders. I thought you might be interested in my answers, which are in no particular order -
1. Good design – it’s fundamental to making good rotomoulded parts.
2. Excellent moulds – don’t skimp. It’s very difficult to make a good moulding from a poor mould. CNC moulds are much more accessible and cheaper these days and have enabled moulders to significantly improve their quality and consistency.
3. Measure and monitor internal air temperature to ensure good processing – this is especially important when moulding a new product.
4. Use the best material – work with your supplier to determine the right specification for the job. Different grades of material are like different golf clubs – designed to do different jobs. Use the right material for the application and don’t just use one club!
5. Use colour compounded material and not dry blend. The physical performance of the product is usually much better and so are the aesthetic appearance and consistency. People are often put off by the higher up-front cost, but you can get a lot fewer moulding problems and no pigment staining in your moulds.
6. Watch powder quality. It’s very important to have excellent dry flow and good particle size distribution (PSD).
7. Build up a network of other moulders for support – these can be local and overseas. There is so much help and support you can receive and it’s good to help others too.
8. Respect your suppliers and use their knowledge, experience and contacts.
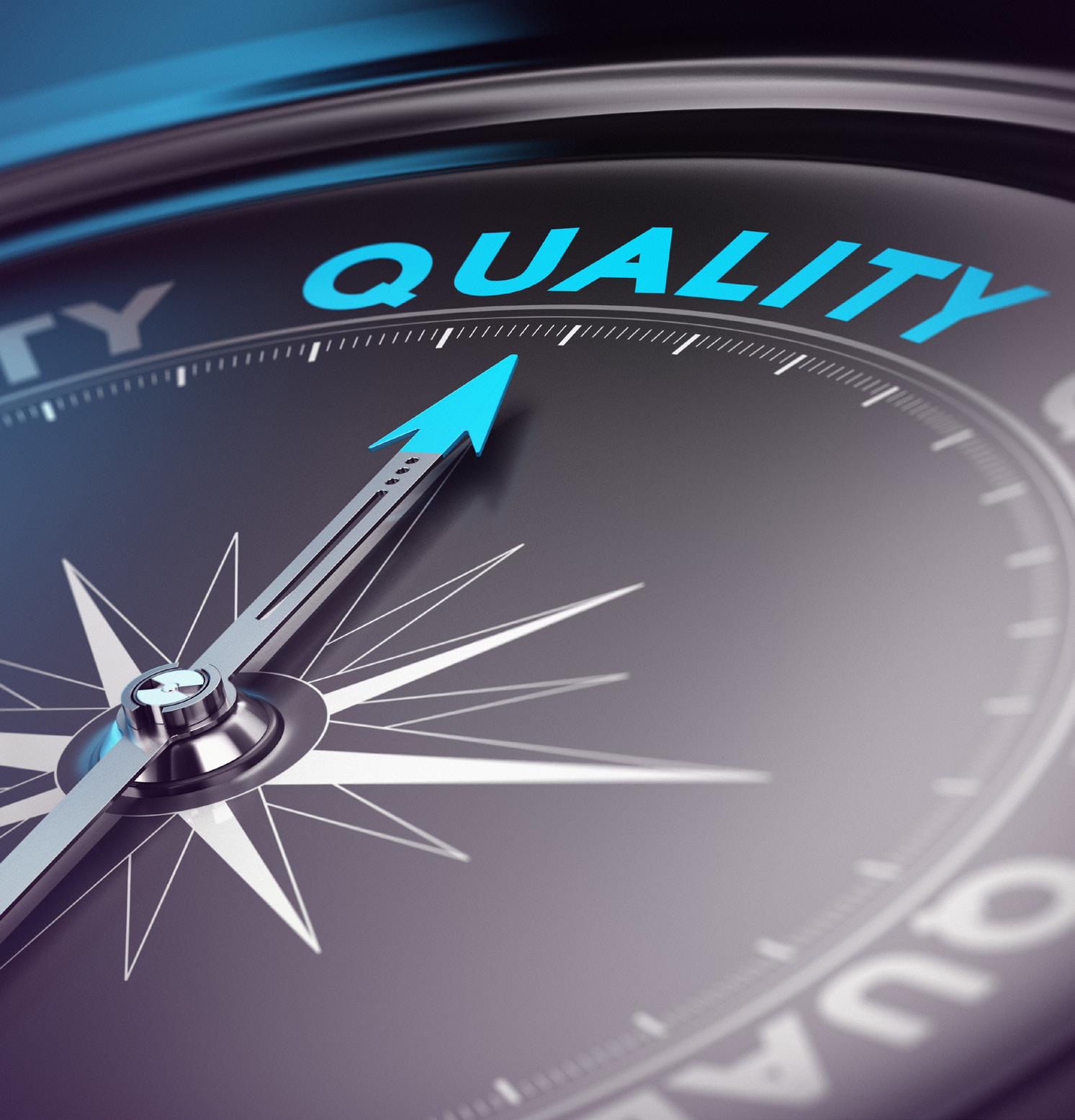
9. Attend conferences and webinars – knowledge is power and they are perfect forums to meet new people and get new ideas.
10. Don’t copy – innovate. The most successful in our industry are those that are keeping one step ahead.
If you have more “top tips” to share with our industry please contact me at martin.coles@matrixpolymers.com.
Arm Report
Serving the Rotational Molding Industry Worldwide for Over 40 Years
The mission of the Association of Rotational Molders is to promote, educate, and inspire the rotomolding industry. For more information, visit ARM’s website at www.rotomolding.org or contact the Association at 630-942-6589 or info@rotomolding.org.
Roto Recharge
With the annual ARM Executive Forum wrapped up, I look forward to the warmth of the summer months – particularly for us in the northern portion of the country! I truly enjoy the outdoor activities and camaraderie of family and friends the summer months allow. It is a time to refresh and recharge.
Over the past year, I have discovered a new way to refresh and recharge our inner Roto-selves: A day out of the office catching either the Intro to Roto or the Advanced Roto Seminar! A team of Plasticraft associates and me recently attended the two seminars. Both seminars provided invaluable tools for our team to recharge and improve our inner Roto-selves – individually and as a group. Bringing our team to these meetings was well worth our time. As a result of our group roto recharge, I have challenged our participants (and myself!) to review and share what we learned throughout our organization.
ARM is blessed with two great Roto educators for these seminars. Dru Laws and Dr. Nick Henwood have an unending passion for our process. Please take advantage of these opportunities to learn from the best. You can learn where the Intro program will be held next at bit.ly/Intro2Roto Both seminars will be part of our Annual Meeting in Kansas City September 26-29. There’s more information about the Annual Meeting in the pages that follow. We have a great meeting planned.
I look forward to seeing you there.
Matt Bushman President, Association of Rotational Molding President, Plasticraft Corporation
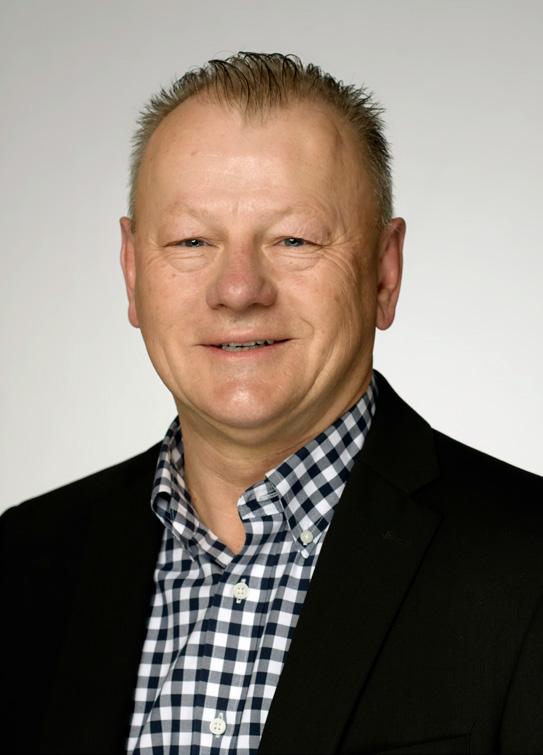
Annual Meeting
The Association of Rotational Molders brings hundreds of rotomolders and their suppliers together to learn from one another, troubleshoot, and network. This year we’ll be in Kansas City from September 26-29, 2023.
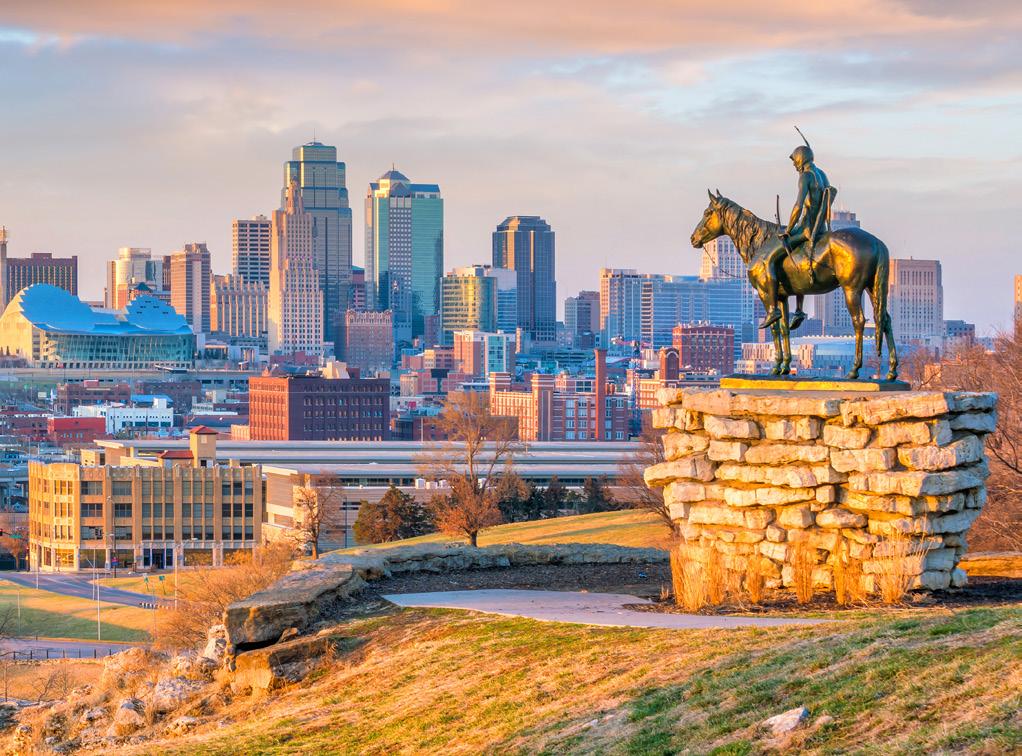
Molders call our Annual Meetings “the most informative conference” they have ever been to, and they report that solving one problem can pay for the meeting registration many times over. First-time attendees note they were “made to feel very welcome,” and the meeting is “exceptional for me in meeting key players in the industry.”
Here are a few of the first education sessions announced for the meeting. Find updated information at www.rotomolding.org
• Introduction to Rotomolding Seminar
• Advanced Rotomolding Seminar
• Design Seminar
• 2022 Product of the Year Case Study
• Beyond Polyethylene: Challenges and Opportunities
• Curing of Mold Release and Controlling Warpage
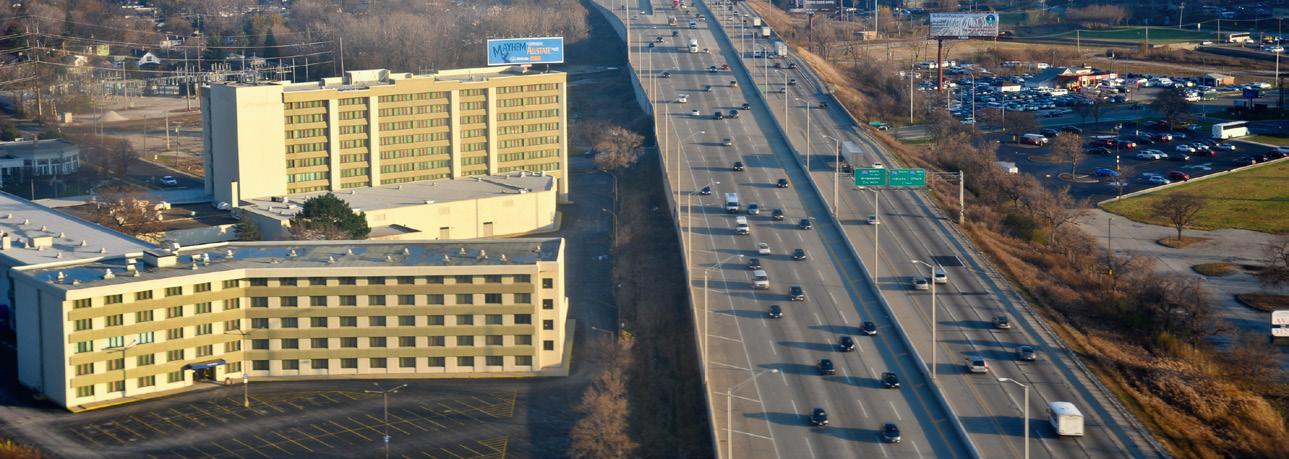
• Cyber Security
• Enhance Competitive Advantage through Smart Product Design
• Hydrogen Liners
• Problem Solving in Rotational Molding Manufacturing
Executive Forum Wrap Up
More than 75 attendees joined in Carlsbad, California this spring to discuss high-level topics concerning managing rotomolding organizations. Although the rain kept us inside, the networking and shared knowledge were worth the trip. The meeting highlights included a great panel of members discussing cyber security for rotomolders and manufacturers, a panel discussion on HR issues, and speaker Ram Charan on managing in times of inflation. Multiple ARM members said Ram was one of our best speakers ever. His insight into economic forecasting and market knowledge captivated the audience. The 2024 Executive Forum will take place in Northern Italy in June 2024. We will be visiting factories and joining IT-RO to learn from each other. Stay tuned for details on this meeting.
• Product Track and Trace
• Recycling of Crosslinked Polyethylene
• Scientific Approaches to Improving Part Quality
• Understanding Success with Recycled Solutions in Rotomolding
• Utilizing Resin Automation
• What’s Your Problem?
… and more to be announced
Email Newsletter
If your company is an ARM member, you should receive our email newsletter twice weekly. The email includes practical educational videos, industry news, curated links relevant to your business, customer inquiries, and occasionally actual fun.
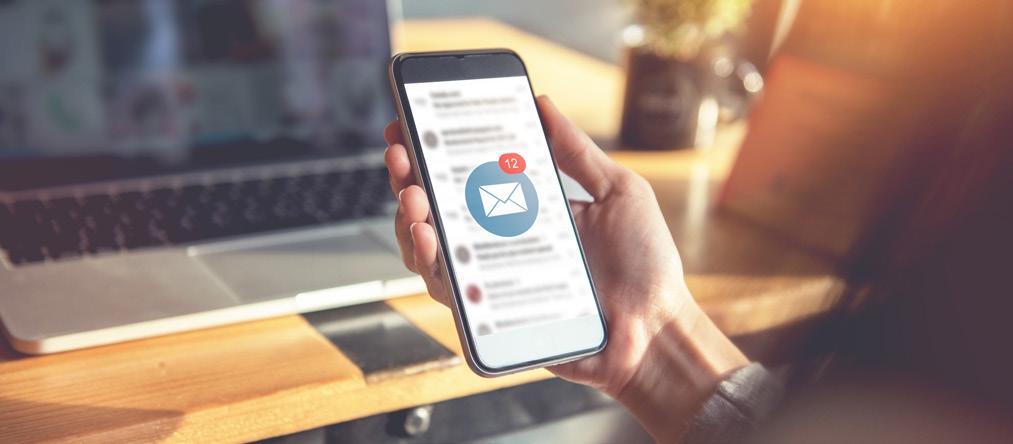
If you’re a member and you’re not getting our email, it’s worth your time to contact ARM at 630-942-6589 or info@rotomolding. org so we can get you on the list. If your company is a member, you’re a member. And we’re happy to add as many employees to our list as you’d like.
Ask Dr. Nick: Are There Guidelines for Vent Sizes?
SIZE - 2
During a recent “What’s Your Problem?” session, we were asked whether any guidelines existed for the sizing vents for rotomolding tools. This subject is covered in the ARM webinar series on “Operator Training.”
There is a “rule of thumb” that has been cited for venting by several sources: 0.01 in2 of ID / ft3 mold volume.
VENTING SIZE - 1
• What SIZE of vents should you use?
• Many different opinions...
• One “rule of thumb” states: 0.01 in2 of ID / ft3 mold volume
• What does this mean in practice?
If you have an approximate number for the volume of your mold, you can use this to calculate the cross-sectional area required to be provided by your vent, or vents.
The volume should be available directly if you have a CAD file for the mold. Otherwise, you can calculate an estimated volume by splitting the mold up into a series of standard shapes like rectangles, triangles, and trapezoids. Or you could fill a molded part with water and weigh it; the density of water is approx. 62 lb/ft3
The Table shows the kind of results you will obtain from this type of calculation. It’s generally safer to provide several vents for large molds if you can. That way, if one blocks, you still have some venting available.
It’s important to stress that I’m not aware of any research that has gone into proving this rule, so apply it with discretion and use your own experience to complement the calculations. Actually, it’s unclear whether the rule applies to open vents or vents that have packing.
These calculations will give you vent size recommendations larger than what I’ve generally observed in the field. Considering the frequent incidence of vent-related problems (especially blowholes in parting lines), I suspect many vents are significantly under-sized. When sizing vents, I would advise erring on the generous side if the layout permits.
Another important point is that, ultimately, the rotomolder is responsible for vent sizing. Your mold maker will, understandably, be reluctant to size the vents for you.
I would like to get feedback from any of my readers about whether you consider these recommendations realistic and practical. I hope this is a useful starting point.
Happy rotomolding!
Dr. Nick Henwood
