
3 minute read
BUSHMANS – Australian Industrial Solutions
Bushmans is a family-owned and operated company with five manufacturing operations located in the eastern states of Australia – Queensland, New South Wales, Victoria, and South Australia. Bushmans commenced rotomoulding tanks in 1989 and were one of the early Australian manufacturers of very large capacity liquid storage tanks (up to 46,000L or 12,000USG) using biaxial hot air ovens. While commercial biaxial oven machines were able to swing up to 5m (200in) diameter parts, it was not until the 2000’s that carousels with 5.5m swing or shuttles with 6.0m swing became commercially available. Today moulders can purchase carousel or shuttle ovens which are >8.0m (>315”) in diameter.
Bushmans have been able to innovate, diversify, and grow business substantially since 1989. They now manufacture a range of polyethylene liquid storage tanks, including chemical tanks, heavy duty tanks, industrial tanks, for dewatering, agricultural fertiliser tanks, as well as traditional water tanks for domestic and agricultural use.
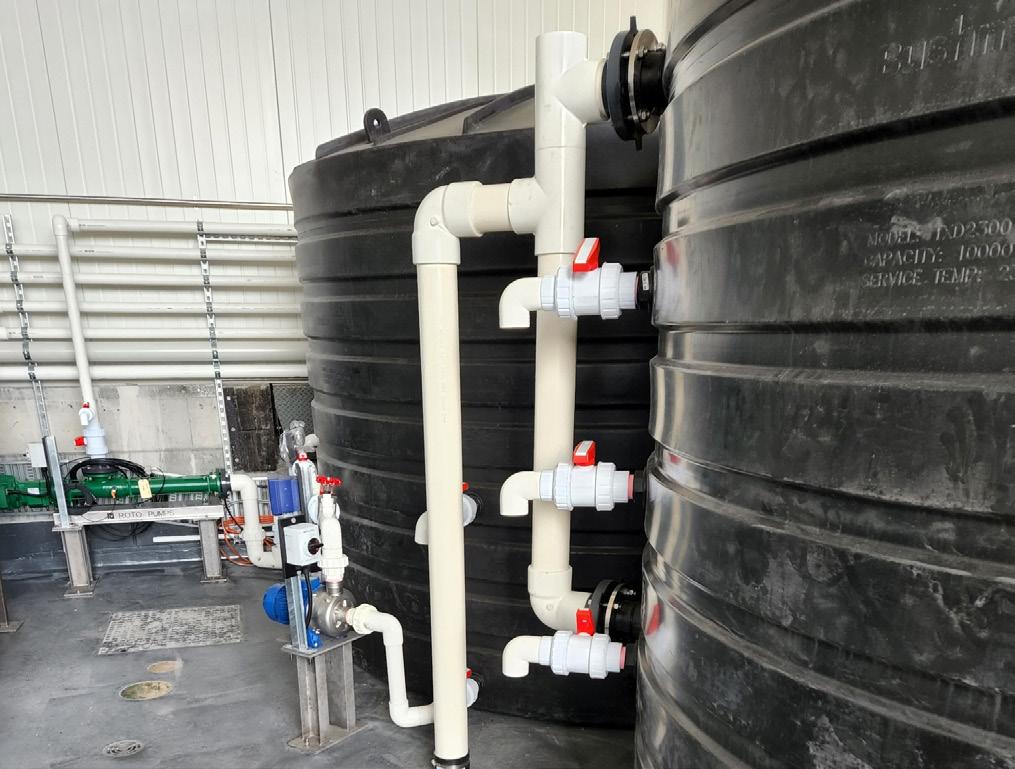

The business also values recognised standards of product performance. Bushmans are certified to the rigorous AS/NZS 4766 standard for water and chemical tanks. Bushmans has significantly expanded its scope over the past 33 years to provide a holistic approach to the delivery of its products to the agricultural, commercial, and industrial sectors.
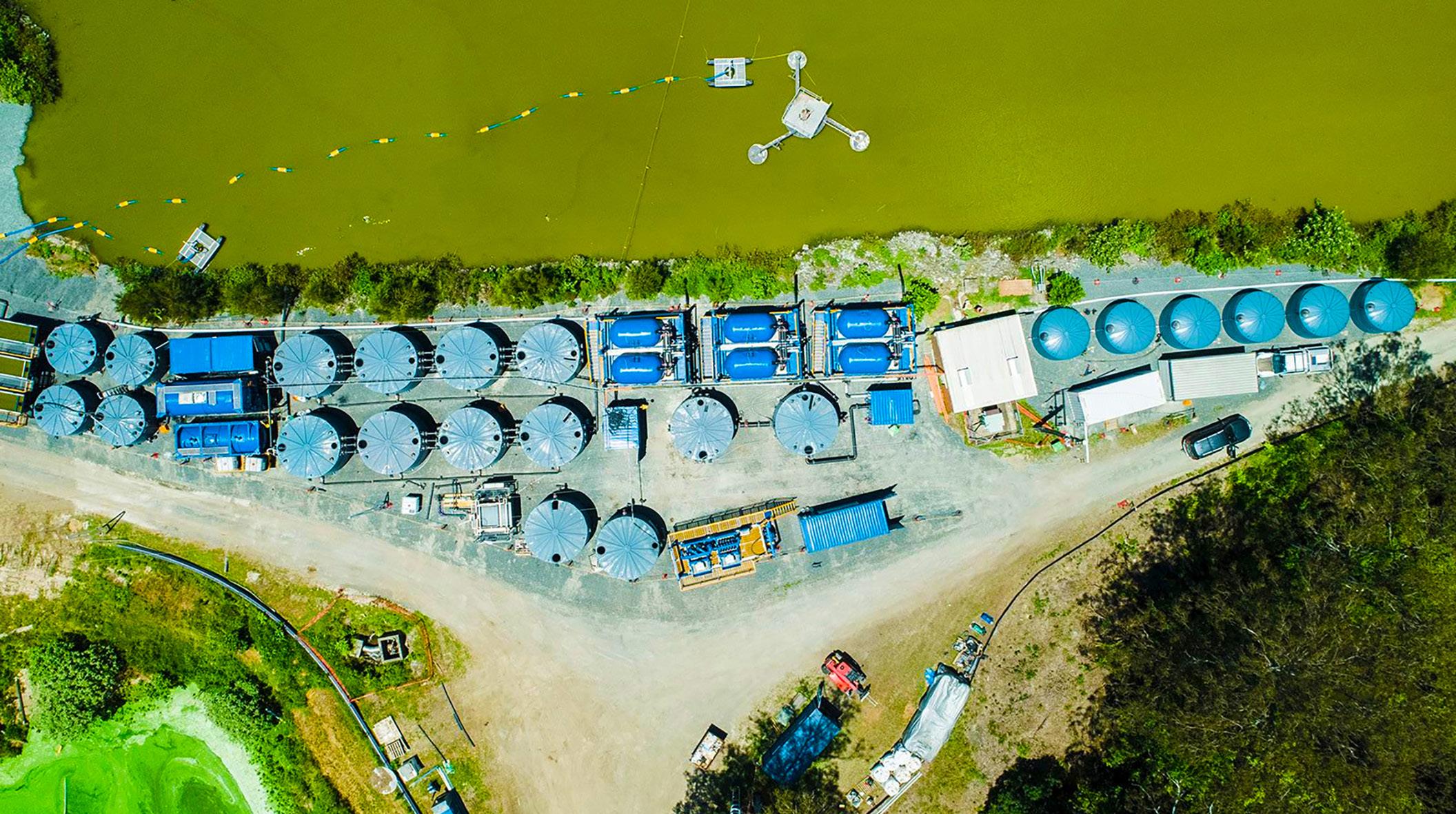
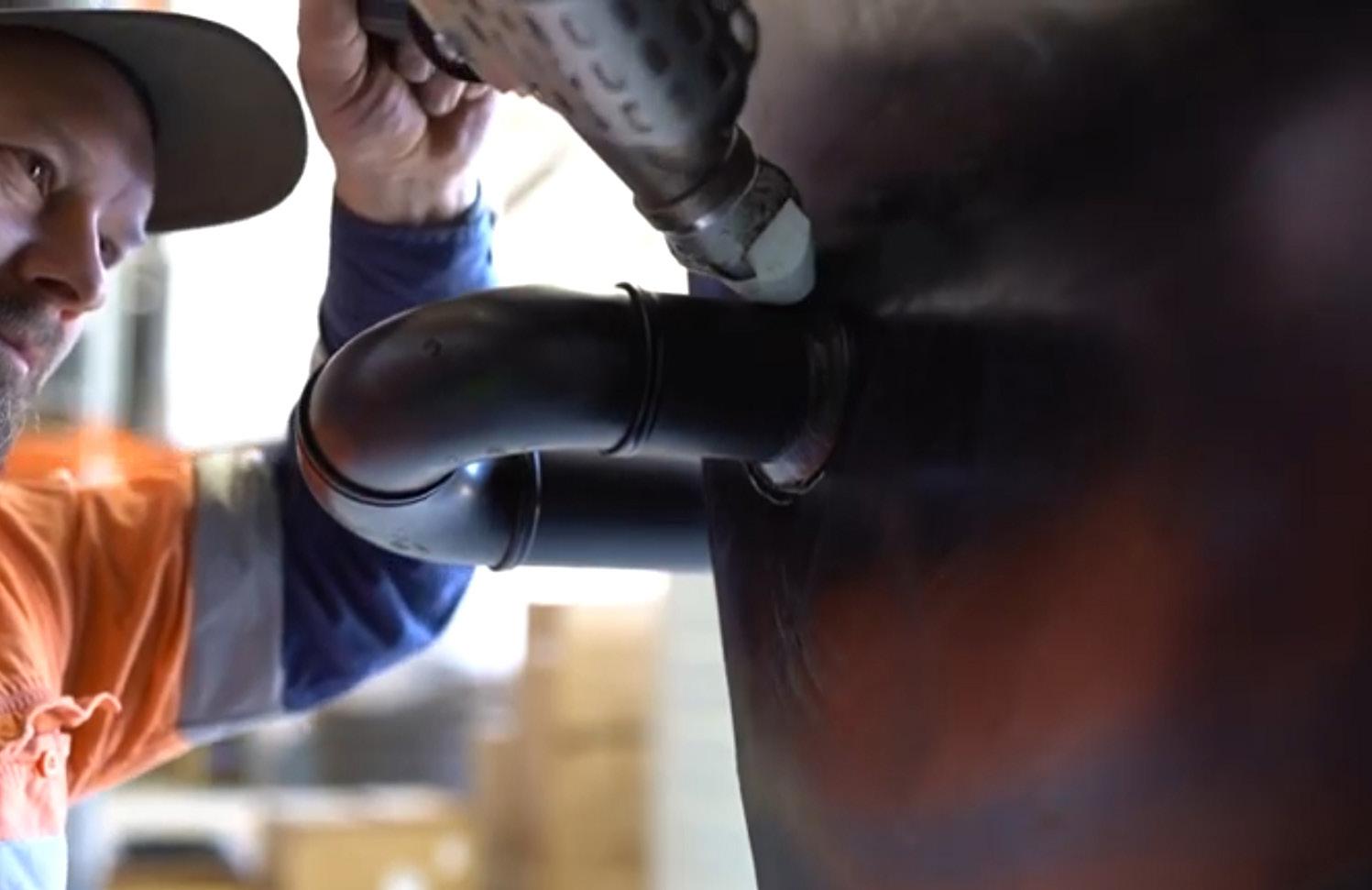
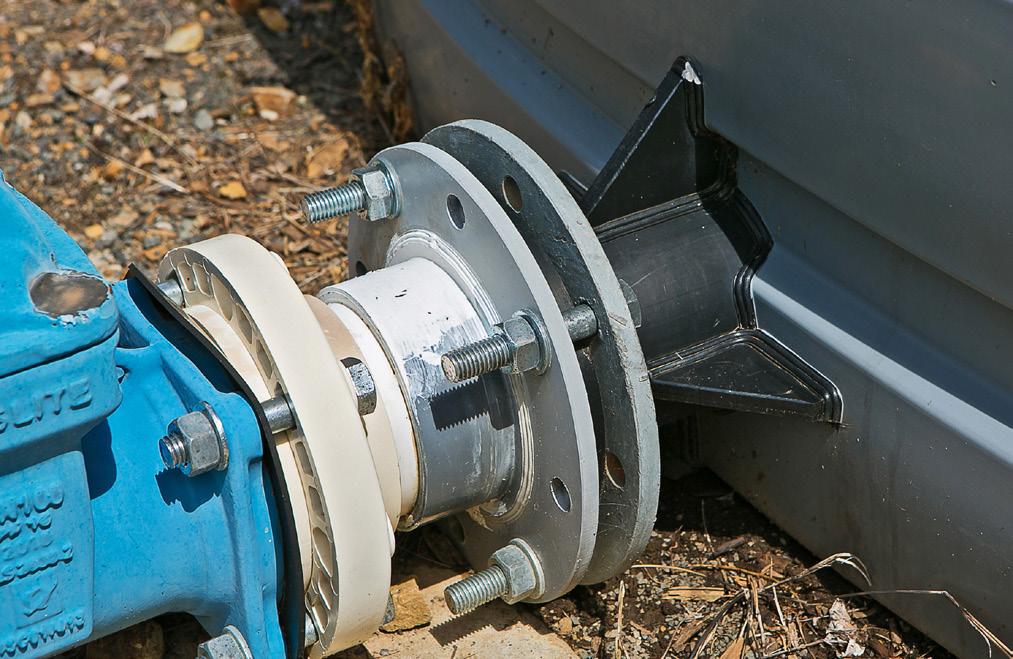
Water Treatment Applications
Long term use of land for industrial processes can lead to high concentrations of organic and inorganic chemicals which often pose a big threat to ecological health. This threat can be magnified when industrial sites are redeveloped, as this can initiate or accelerate the release of undesirable chemicals into water bodies.
Removing pollution and contaminants in soil and wastewater is the key to protecting human health and maintaining a stable environment. Many municipalities, with strong environmental protection regulations, require companies to address wastewater clean-up. This typically requires installation of an industrial Water Treatment Plant (WTP) to purify the water to a level that is safe to be released into the environment.
While the elements of a WTP will vary depending on the industrial site needs, the increasing use of large capacity rotomoulded tanks, combined with advanced treatment technologies, has been making a significant difference to address the specific treatment requirements of different sites providing flexible and cost-effective clean-up solutions.
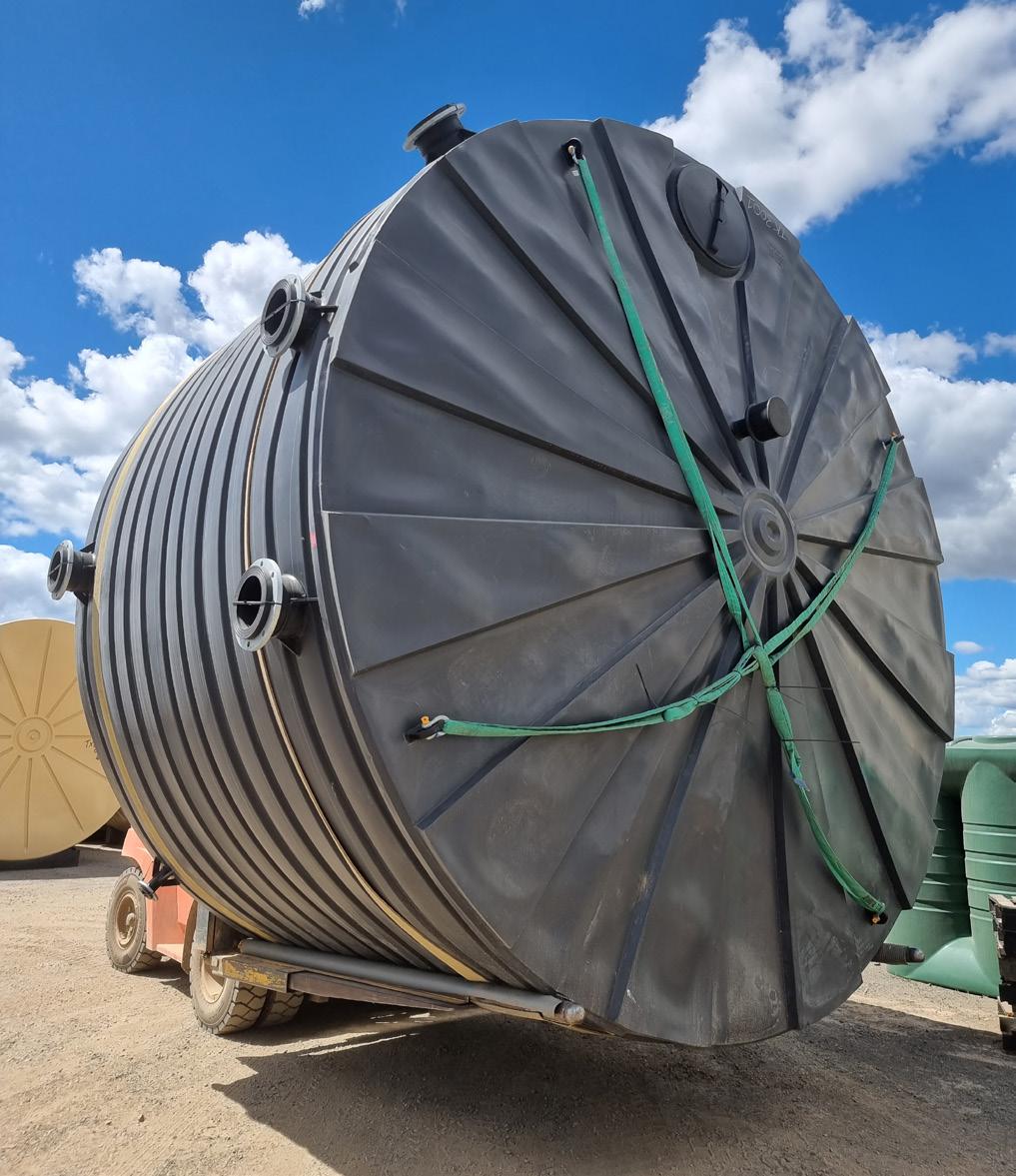
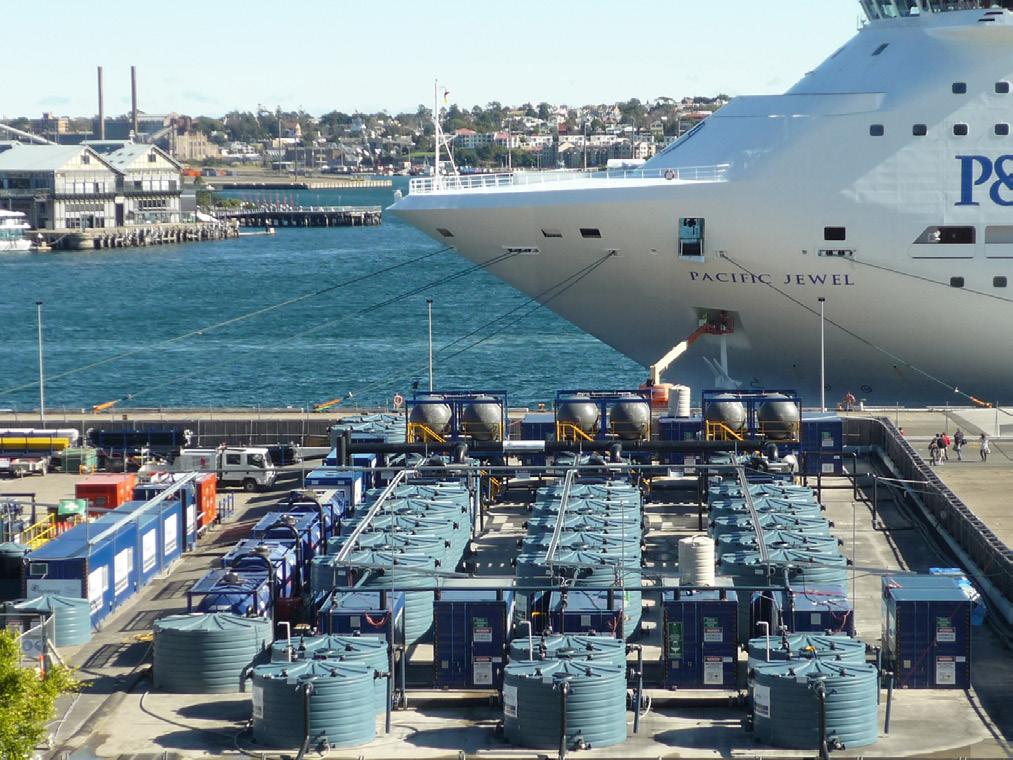
Bushmans have decades of experience manufacturing specialised liquid storage tanks for industry. A more recent application in the 21st century has been Bushmans’ development of customised industrial dewatering tanks (WTP) designed for high specific gravity (SG) liquids, different chemical combinations, and a wide range of custom welded plastic fittings which suit specific client needs.
The increasing demand to protect groundwater and surface water of individual sites by providing decentralized and small-scale process technologies has suited the flexibility and performance advantages of polyethylene tanks. However, a highly specialised part of the manufacturing process is the plastic extrusion welding process. This is quite different to butt welding or socket fusion welding, skills familiar to welders of HDPE pipelines.
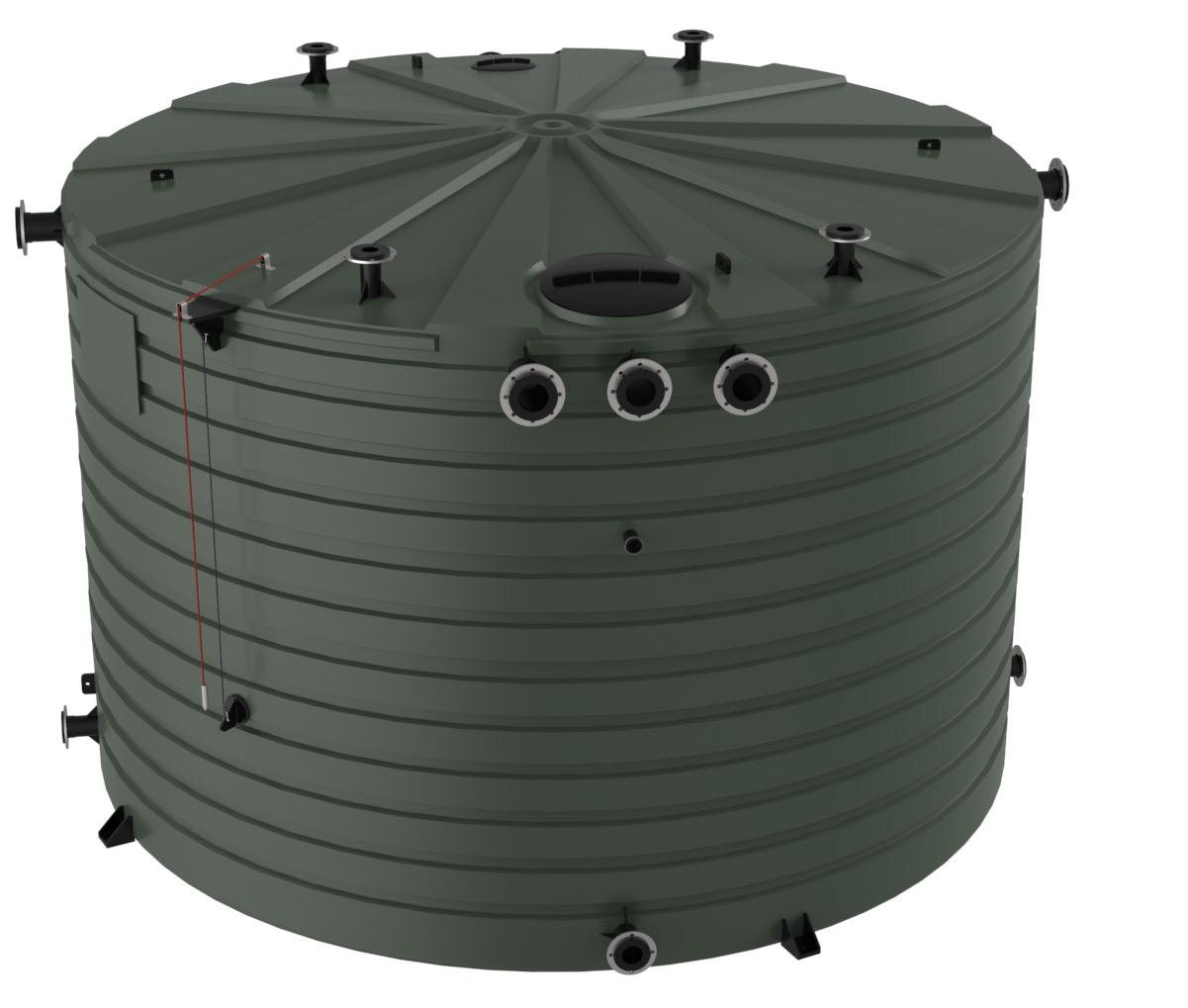
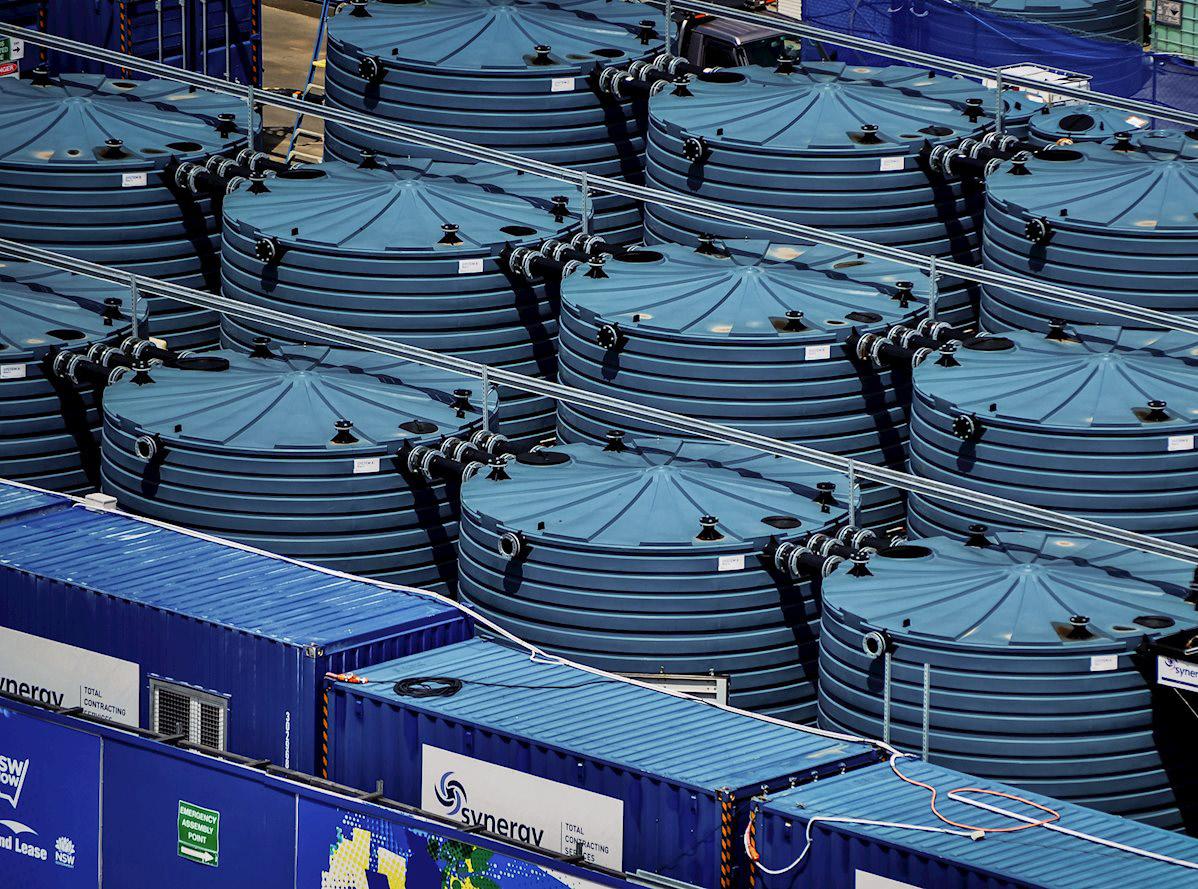
Skilled plastic welders are professionals who manually use a stream of heated air, which is directed towards the weld joint between the two plastic parts to be joined, where it softens or melts the polymer. Typically, there is a combination of hand welding with a hot air welder (often using a welding rod 3-4mm diameter) and an extrusion welder, where the welded joint is a thick section.
It is easier to make a poor quality weld than a good quality weld. Welding is a ‘special process’ which means that its quality cannot be easily verified and its successful application requires specialist management, personnel, and procedures. Without tight control you risk premature failure during service.
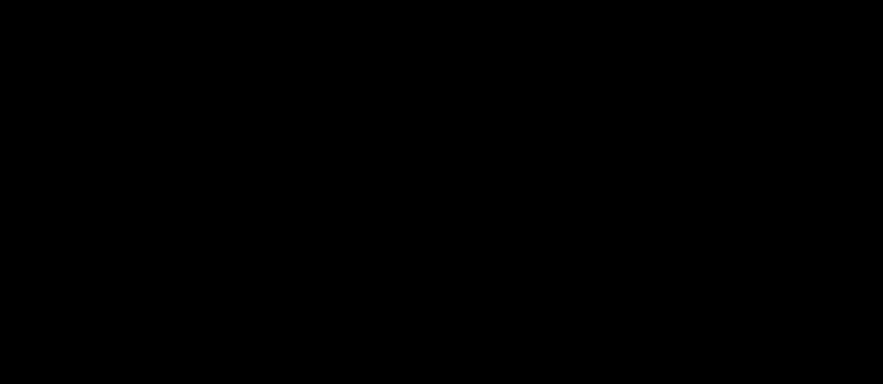
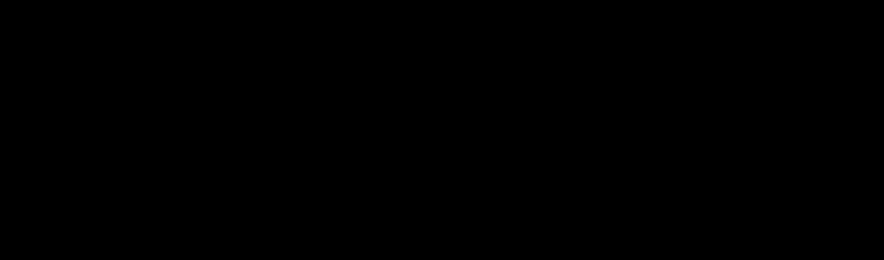
With decades of accumulated practical welding experience Bushmans are the industrial tank manufacturer of choice for many Australian suppliers of specialised WTP’s. Bushmans have been able to leverage their plastic welding knowledge, along with their rotomoulding experience, to tailor their tanks to suit the different liquid SG’s as well as weld a wide range of fittings all over the tanks. Some tanks have over a dozen inlet and outlet poly fittings of varying sizes welded into the tank shell. This is Australia, so customers can choose from over 20 different melt compounded colours.
While the rotomoulding world is dominated by water tank moulders, there are still great opportunities for rotomoulding businesses to diversify beyond the basic water tank shell. While water tanks are big business in every part of the world they are in a highly competitive market often driven by consumers who purchase only on price.
Diversification into the industrial tank market will take time and resources above the simple water tank market. If you can make a quality tank you have the potential to enter a niche market which offers significantly better margins and less competition. The cost of failure (ie leaking welded fitting) can be expensive. Significantly greater than a domestic or agriculture water tank failure. While there are greater risks, there can be substantially greater rewards manufacturing specialised industrial tanks.
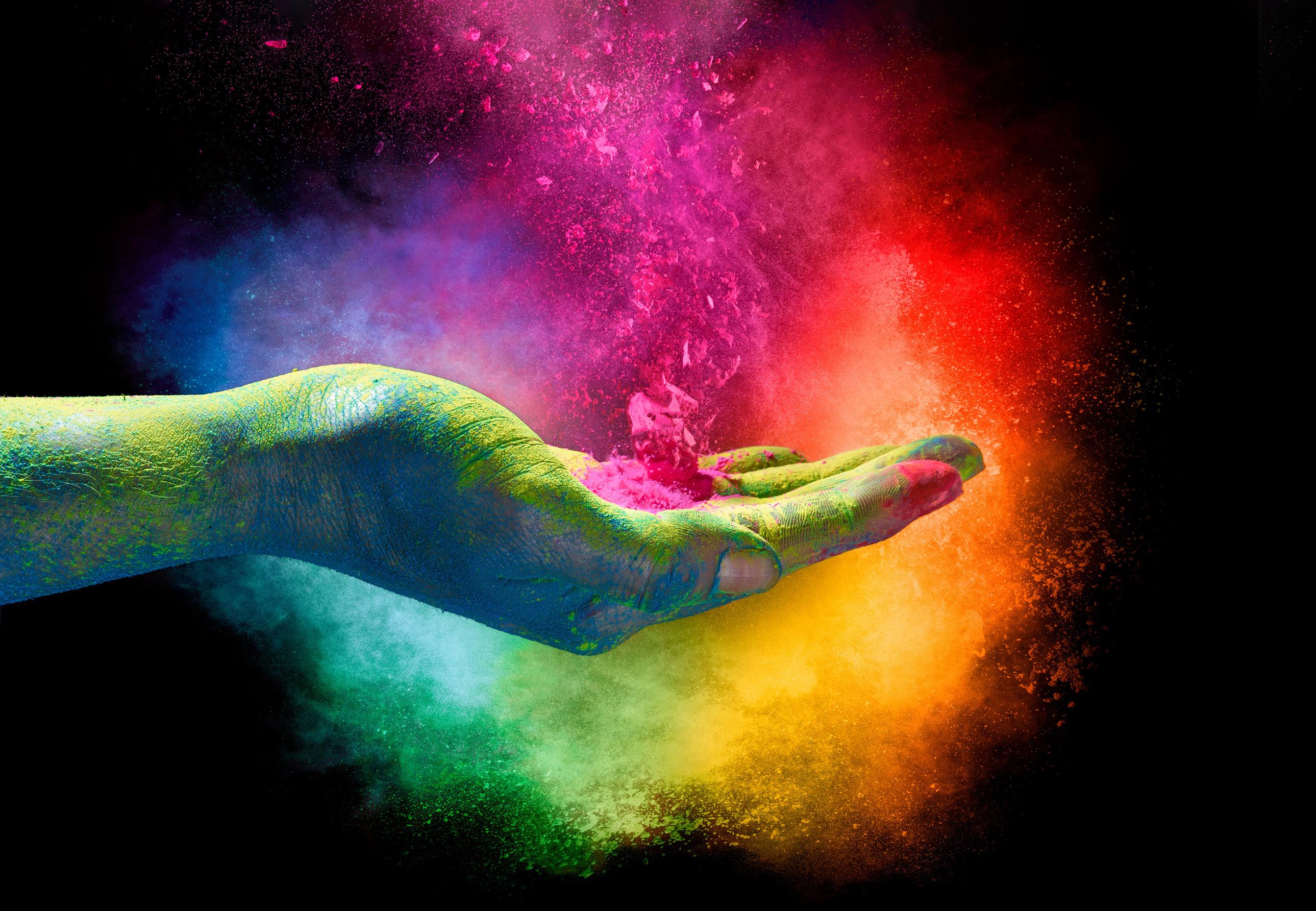