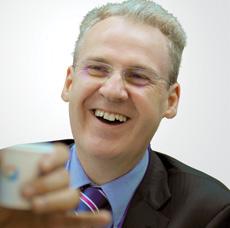
5 minute read
At Issue
Martin Coles, Matrix Polymers
Reducing Gas Dependency in Rotomoulding – What Are Our Options?

Image courtesy of AMS Belgium
In the previous edition of RotoWorld® I raised the alarm that rotomoulding as we know it is under long-term threat, due to our industry’s reliance on cheap, efficient, and readily available natural gas.
The world is rapidly turning away from fossil fuels and country after country is announcing new measures to reduce carbon emissions and promote greener forms of energy. A good example is New Zealand’s proposed total ban on all new installations using natural gas.
What is our industry going to do?
In my last article, I talked about the possibility of converting conventional rotomoulding machines from gas to electrically heated ovens. This is happening on a limited scale, but the ovens are more expensive to buy and to run and there can be practical difficulties relating to the very high electrical load requirements at start-up.
There are some novel solutions being created to overcome some of these issues. Dhanu Patell at Reinhardt Teknik in India is developing a hybrid machine, which uses diesel or gas for the ramp-up, to avoid the connected load problem with electricity, and then the machine switches to run on electricity which is sometimes generated ‘in-house’ from solar.
Another option to consider is bio-gas. This is a growing renewable source of fuel that is produced from the breaking down of organic matter, such as food scraps and animal waste. There is much talk in places like New Zealand about replacing natural gas with biogas, but clearly the infrastructure to produce this is considerable and not within the control of the rotomoulder. Biogas is also just a stepping stone to a zero-carbon world as burning this energy source still produces CO2.
Are there other creative solutions?
Oven-less rotomoulding?
If you take away the need for the oven and you directly heat the mould then you are going to need to use less energy. Is this the solution?
AT ISSUE
Heating moulds using jacketed hot oil has been done for many years and more recently electrically heated moulds have become increasingly popular. Pioneers of this technology have been Persico in Italy with their SMART machine and AMS in Belgium with their Robomould concept and other companies are working on similar concepts.
These non-conventional machines are becoming more commonly used across Europe and I’m starting to see them in other parts of the world too, particularly for the production of really top-end, high value, and smaller-sized rotomoulded parts. There are many advantages, as you can have much more accurate control of temperatures which opens up the use of many more materials, and have various temperature zones across a mould which allows you to have variable wall-thicknesses in different sections. These technologies help moulders make parts with tighter tolerances and can deliver sizeable reductions in cycle times. And of course, they use much less energy.
Could electrically heated mould technology be the solution to our industry’s potential energy crisis?
As things stand my view is that electrically heated mould technology will continue to grow rapidly, however, the relatively high capital expenditure of the machinery, and perhaps even more importantly, the higher cost of moulds will mean that this type of process will remain niche. Currently, there are also limitations on the size of products that are being produced and there isn’t the degree of flexibility to produce short runs of products that you get with conventional equipment. For it to become more mainstream the costs would have to come down considerably and the process is simplified.
Perhaps this is an opportunity for someone to develop?
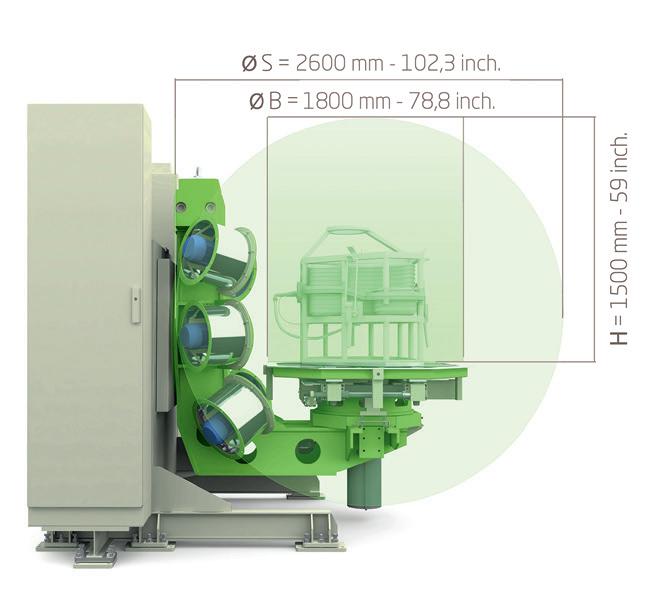
Improve efficiency and use less gas?
Image courtesy of Persico
Now, we don’t have a “silver bullet”, one solution that solves all our future problems. Whilst electrically heated moulds might be of growing importance moving forwards, what about now? I think most rotomoulders would accept that the conventional gas oven machine is energy inefficient and most open flame machines are even more wasteful. It’s been estimated that the overall efficiency of our industry (amount of energy used to process vs. kilograms of the finished product) is in the 3-8% range. So, there must be plenty of scope to improve the efficiency and waste less gas.
There are many things rotomoulders can do to improve energy efficiency, such as reduce heat loss in ovens by having better seals; use more efficient burners; reuse the energy from the oven exhaust; use air movers or transvectors to concentrate heat on certain parts of the mould to increase wall-thickness and use less material overall; have better air circulation within the oven; use faster sintering powder; and heat the powder before moulding.
In the past, I think people were not particularly motivated to look at these kinds of things as the cost of gas has been cheap and minimising its use has not been a priority. Certainly, I’ve seen profligate wastage including witnessing a Production Manager firing up an idle rotomoulding oven so that he could heat up his pie!
Perhaps attitudes will now start to change as we all become much more aware of our CO2 footprint and our responsibility
to not squander precious finite resources and to minimise our harming of the environment. As an industry, we need to face up to the fact that we have a long way to go as far as energy efficiency is concerned – and this is going to become a much bigger issue very soon.
Whilst energy efficiency is currently a “D minus” and “must do better”, rotomoulding is making many positive contributions to the environment and improving people’s lives. In the next edition of RotoWorld®, I will be examining some of these and discussing how important it is for us to promote the benefits of our industry to our customers, colleagues, and the wider world.