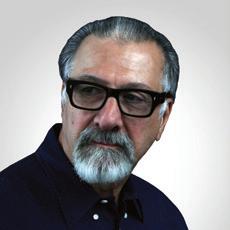
15 minute read
Design Comment
DESIGN
COMMENT
Michael Paloian, Integrated Design Systems, Inc.
Designing for the Long Term
Product design is very fulfilling as well as challenging. It feels great to be able to think of something, sketch it out on a piece of paper, maybe make a model, then translate your idea into an actual product! One of the most challenging responsibilities for a designer or engineer is designing a product for the long term. This process requires in-depth knowledge in materials science, manufacturing, physics, mechanics, aesthetics, human factors, and application. It would help if you had a crystal ball when designing a product to last for 5, 10, or 20 years. Unfortunately, none of us have a reliable means of looking into the future unless you subscribe to a fortuneteller. So how do you design a product to last for a specified minimum timeframe?
There are a few basic requirements for designing long-lasting products as listed below: • Know your material • Understand the product application • Manage stresses and loads • Always account for the environment • Never assume anything
Understanding Material Properties
Knowledge of material properties cannot be over-emphasized. Long-term performance is highly dependent on material properties, and how well matched they are to the applied loads, chemicals, radiation, and thermal conditions to which they are subjected. Engineers need to evaluate the extremes of these parameters based on the specified material and anticipated operating conditions. Although this may appear to be straightforward, it is quite the opposite. An engineer must carefully expect every possible use condition for a given product and evaluate its performance based on a combination of conditions. Unfortunately, most published material data is limited to immediate loads. This limitation requires product designers to conduct accelerated testing based on sound engineering principles.
Understand the Product Application
Although this may appear to be elementary, it is a critical and often overlooked step in product design. Understanding the application requires understanding the interrelationships between product use, misuse, use environments, maintenance, and safety. For example, a product exposed to sunlight for up to ten years requires excellent UV resistance. Specifying a UV 10 grade of polyethylene means that it will retain a minimum of 50% of its tensile strength and impact after this exposure period. Therefore your device should be designed to withstand a minimum of two times the loads from time zero.
Manage stresses and loads
Stresses and loads should also account for creep, which is time and temperature-dependent. For example, a water tank can be filled and perform well at room temperature and time zero. However, it could fail after two or five years under constant load and higher temperatures. This phenomenon is attributed to creep. Creep is a change in modulus over time under constant load.
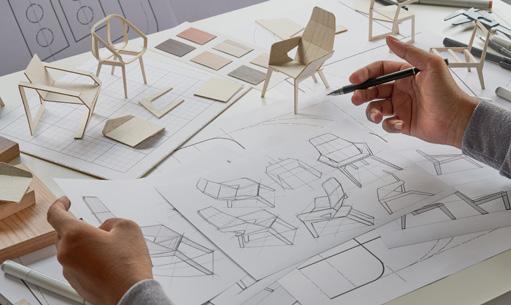
Always account for the environment
The environments of use are critical to assess when designing for the long term. Product environments could include harsh chemicals, which could rapidly degrade plastics. Environmental conditions also influence radiation such as UV, or X-rays, gamma rays, etc. Thermal conditions are another common environmental consideration. Electrical energy is also crucial since it will affect designs requiring insulation which is dependent upon dielectric strength.
Never assume anything
The last important consideration for designing for the long term is never to assume anything. Assumptions often lead to a false sense of security based on omissions of critical design considerations. Omissions lead to errors and premature product failures, which is why the US courts are backlogged with thousands of lawsuits every year based on “Errors and Omissions.” Critical due diligence is essential in any design methodology where long-term product performance is required.
I hope this brief editorial was informative and somewhat enlightening. It is intended to alert you to the challenges associated with designing products to last long periods. This topic would be an excellent subject for a book. If you have any comments or would like to reach me, please feel free to contact me at paloian@idsys.com.
Chemical Tanks: Knowledge is Power
Ian Hansen, Rota Consult
When it comes to chemical or industrial storage tanks, many rotomoulders use their existing water tank moulds to make tanks to store a variety of chemicals, usually with minor design changes. This article attempts to provide information and guidance primarily on the polymer properties which moulders should be aware of when designing a chemical tank fit for purpose.
In the beginning
When tank capacities are small, the risks are relatively small. When the tank size increases in capacity, then any small deficiencies in design can become magnified. A tank designed to hold 3,000L (800USG) of water (or chemicals) will almost by accident rather than design, have a greater design factor of safety than a 30,000L (8,000USG) tank.
Polyethylene tanks are used around the world for the bulk storage of industrial chemicals, including dangerous and corrosive chemicals like hypochlorite solution (liquid ‘pool chlorine’) and hydrochloric acid. Bulk storage tanks for diesel, liquid fertilisers and molasses are commonly used by the agriculture industry. When storing chemicals, the damage (real cost) caused by failure (leak) can be significantly greater than for a leaking water tank. In countries that have robust rotomoulding tank standards for material, design, manufacture and postproduction testing of tanks, the suitability of the tank structure would be assessed using finite element analysis (FEA) to ensure the tank is fit for purpose (see Figure 1). AS/NZS4766 is an example of such a comprehensive tank standard.
Some standards provide general guidance about chemical tanks. Typically, the suitability of the polymer for chemical storage should be based on relevant chemical resistance data from polymer manufacturers. Moulders relatively new to chemical storage tanks need to be aware that ESCR (stress-cracking test) is not recommended to be used as an indicator of general chemical resistance of a polymer. The moulder should maintain relevant chemical resistance/performance data demonstrating the tank’s suitability for the intended application.
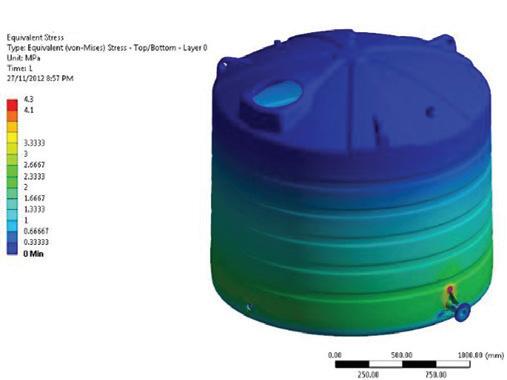
Responsibility
Generally speaking, the manufacturer of the storage tank is normally responsible for the evaluation of both the tank design and chemical resistance of the polymer material to ensure the tank can withstand chemical attack, with minimal change in appearance, dimensions, mechanical properties, and weight over a period of time. The degree of responsibility in the event of product failure will depend on the regulations and legal precedents of the region the tank is produced or sold into. To put this into perspective, there have been a couple of major court cases where moulders have unsuccessfully claimed the polyethylene supplied had:
• inadequate environmental stress cracking resistance. 2008 judgement, US$70M claim [1] • inadequate ultra-violet light (UV) resistance. 2012, US$50M [2]
These expensive disputes, involving combined claims of about US$120M, highlighted the primary importance of design, processing and quality control which the moulders were found responsible for, not the quality of material used. This article provides an introduction to the design changes to consider in managing the effects of storing bulk chemicals rather than water.
Chemical Effects
Chemical resistance encompasses the total effect a product would have on a storage tank. The 3 key factors that make up the overall compatibility of a chemical to a polyethylene tank are:
i. Chemical Attack - Oxidation ii. Stress Cracking - ESCR iii.Permeation – Plasticisation
(i) Chemical Attack
Oxidising agents undertake a chemical attack by chemically degrading the polyethylene. This can be a breaking of molecular chains and/or an addition of chemical groups to the molecule.
Oxidisation causes the eventual loss of properties with the plastic becoming brittle and the tank not fit for use. This would be similar to steel rusting/failing or wine turning into vinegar.
Chemical effects may be gradual and may not be measurable over the short term. Examples of strong oxidizers which potentially may be unsuitable for long term exposure to polyethylene include nitric acid & sulphuric acid.
(ii) Stress Cracking
Environmental stress cracking is the cracking of a polyethylene part under stress when in contact with a medium, e.g. kerosene, in the absence of which surface initiated micro cracks or fractures do not occur under the same conditions of stress. The polymer’s resistance to such failures is called environmental stress crack resistance (ESCR). A diluted chemical (10%) will normally have a greater effect than a full strength (100%) chemical. Consider diluted detergents such as dish washing liquid.
This stress cracking can often be accelerated when combined with elevated operating temperatures. Figure 2 illustrates an example of a stress crack failure. Examples of known stress cracking agents which may be unsuitable for long term exposure to polyethylene include detergents, surfactants and vegetable oils.
Remember, these stress cracking agents do not chemically attack the polymer. Stress on the polyethylene comes from applied forces (hydrostatic stress), part design (tight radii) and residue stress (warpage or deformation).
(iii) Permeation
Permeation involves the physical absorption of the chemical into the polyethylene, causing the plastic part to lose stiffness or rigidity. Additional effects include swelling, weight gain, reduction in tensile strength and loss of long-term creep resistance. Normally, absorption does not prohibit the storage of the chemical. The property losses due to permeation can usually be offset by increasing the design wall thickness of the tank or changing the type of polymer for the application.
Hydrocarbon fuels such as diesel are well known to permeate into, and pass through, polyethylene over time. Even polyethylene grades approved for storage of diesel (ECE-R34) still require the moulder to consider design and wall thickness changes to manage the softening of the polyethylene. Figure 3 illustrates a diesel approved grade of polyethylene after more than 5 years of service. Examples of plasticising chemicals which may be unsuitable for long term exposure to PE include petroleum, gasoline, benzene or other aromatic hydrocarbons.
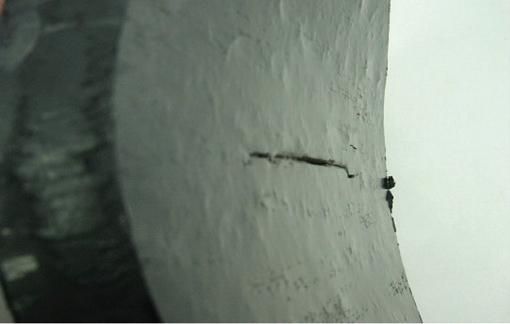
Figure 2: Stress crack failure [3] Figure 3: Diesel fuel permeation (brown) in a 10,000L (2,640 USG) tank
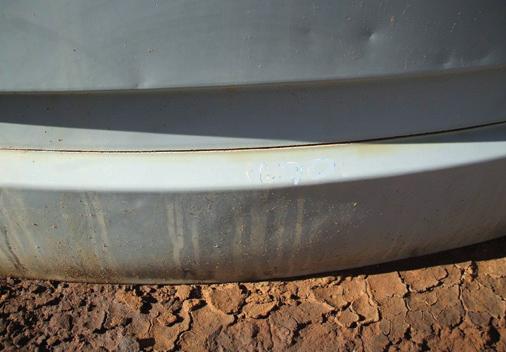
Environmental Effects
Extreme temperatures can also have a negative effect on tank performance, especially hot ambient temperatures. This can be a result of external heat from the sun, or it can be internal from hot liquids entering the tank. Polyethylene, which is a flexible material, becomes even more flexible when heated. Figure 4 illustrates the bulging effect that can occur when a tank is subjected to elevated temperatures, instead of room temperature (23°C or 73°F).

The rigidity or stiffness of polyethylene is measured at a standardised temperature of 23°C. Figure 5 shows that the rigidity of polyethylene will decrease by 35% when the temperature of the material is increased from 23°C to 40°C. If a storage tank is to operate in elevated ambient temperatures, or with a liquid operating at elevated temperature, then consideration should be given to increasing the wall thickness of the product to compensate for the reduction in rigidity.
Material selection
The basic parameters for material selection are:
i. Density (crystallinity) ii. Melt index (molecular weight) iii.Comonomer type (octene, hexene, butene)
Large capacity tanks using higher density and lower melt flow polyethylene will normally have enhanced chemical resistance, while IBC’s using lower density and higher melt flow PE will have enhanced stress crack resistance. Figure 6 illustrates the two different tank applications. It is important to be aware of the advantages and disadvantages of different grades of material.
(i) Density
Higher density materials tend to have lower stress crack resistance but are more notch sensitive than medium density materials. That is, they are typically less able to deform or yield upon impact and cannot resist crack propagation once it is initiated.
(ii) Melt Index
The influence of viscosity and melt index on material selection has been outlined in a RotoWorld® article by Alvin Spence [5]. Lower melt index materials will typically have improved stress crack resistance and chemical resistance.
(iii) Comonomer
The influence of comonomer type on material performance has also been previously outlined in another RotoWorld article by Nick Henwood [6]. When using low melt index material (<3.5MI) increasing from butene to hexene or butene to octene will make a significant improvement in long-term performance like stress crack resistance. When selecting a material consider the best combination of stiffness (hydrostatic load), melt index (processibility) as well as commoner (chemical resistance) to meet the functional needs of the application.
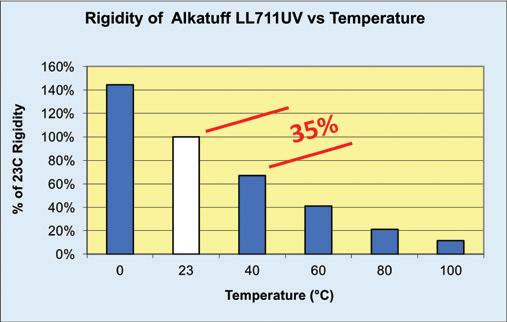
Figure 5: Effect of temperature on rigidity [4]
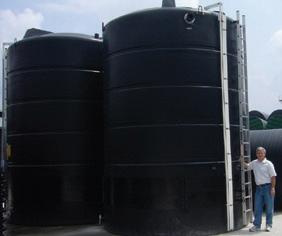
Figure 6: Different tanks usually require different performance characteristics
Questions to ask the customer
When designing any product, it is critical to have a fundamental understanding of the product’s functional requirements for the chemical tank and the customer’s intended use.
• What is the chemical being stored in the tank? • What is the % concentration of the chemical? • What is the Specific Gravity of the liquid? • What is the service temperature range? • What regulatory standards apply? • What capacity is required?
While these appear to be basic questions, overlooking any one of them may result in a catastrophic failure. Therefore, it is critical to have a complete understanding of the end use application and functional requirements in order to determine the best design and optimal material/wall thickness for the application. Be aware that the moulder will normally be deemed the chemical tank manufacturing expert, not the customer.
Chemical Concentration
It is important to have access to chemical resistance tables which list chemicals and concentrations. Identification of multiple sources of information is also important as there may well be conflicting data and/or various concentration levels of chemicals listed. Liquid fertilizers are commonly made with nitric acid (HNO3) and are stored in bulk for agricultural use. Chemical resistance tables usually indicate nitric acid is satisfactory to be stored at lower concentrations, but not satisfactory at higher concentrations. The concentration of liquid nitrogen fertilizer, in the form of nitrate, ammonium and urea will be written on the SDS/MSDS (Safety Data Sheet/Material Safety Data Sheet).
Chemical resistance tables provide general advice for polyethylene. However, not all grades of polyethylene perform the same. TOTAL compared elongation after 3 weeks of exposure to HN03, at 55% concentration, at 40°C (104°F). The polyethylene grades compared were M3421UV = mPE, XLPE = crosslinked PE, ZN-LLDPE = conventional PE. Figure 7 illustrates the performance
difference between polyethylene grades. The metallocene polyethylene (MPE) outperformed the crosslinked and standard polyethylene grades by a significant amount. This is an example of why it is important to get your polymer supplier to provide their advice on the suitability and performance of their material for your customers application. If you have a written record of this, you also have supporting evidence about the suitability of the material for a specific application. Always ensure the material supplier has all of the pertinent information relating to the application.
Summary
Chemical effects on polyethylene that you need to understand can be divided into three categories:
i. Oxidation ii. Stress cracking iii.Plasticisation
Tank design and processing (optimal moulding) are interacting factors which influence chemical resistance & stress cracking resistance. Experienced moulders should already understand that some of the many factors which must be controlled for successful production of chemical storage tanks include chemical compatibility, chemical concentration, stress crack resistance, regulatory standards, operating temperature, impact resistance, vacuum or pressure conditions, duration and type (intermittent versus continuous) of operation, weatherability, design features of tank, customer installation, recyclability, overall cost, etc. This article provides a guide to some of the complex and technical issues which moulders need to consider when undertaking the risk/benefit equation presented by the storage of chemicals in tanks. For information on material selection, I would recommend you contact your material supplier for their advice on each new chemical storage application. When designing high performance chemical tanks versus water storage tanks, always design in adequate safety margins to ensure the product is fit for the application.
Specific Gravity (SG)
Another critical factor is the weight of the liquid chemical to be stored in the tank. Many chemicals increase in weight as the concentration of chemical increases. Some, like diesel, decrease in weight. The specific gravity of chemical concentrations should be
written on the SDS/MSDS. Sodium hypochlorite (NaCIO), known as chlorine or bleach, is a chemical commonly stored around the world in many different concentrations.
• 8% has SG of about 1.12 • 10% has SG of about 1.16 • 15% has SG of about 1.25
In simple terms, if your tank design required a wall thickness of 6.5mm (0.26 inch) to store water, you would need to increase it to 8mm (0.32 inch), a 25% increase, to store sodium hypochlorite at 15% concentration. This design change is just to manage the increase in weight. Note that NaCIO is also an oxidizing agent.
Figure 7: TOTAL Petrochemicals, ARMA Rotomould Conference 2008 [7]
References
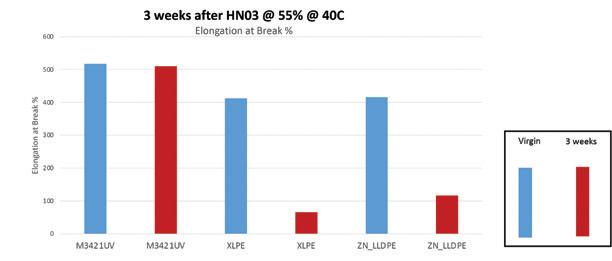
Service Temperature
A simple method most moulders use to manage the elevated temperature is to make a small increase in the wall thickness to offset the negative effect of elevated temperatures. Increasing wall thickness 25%, say from 8mm to 10mm, (0.32 inch to 0.39 inch) will yield approximately a 100% increase in rigidity (as rigidity is proportional to wall thickness cubed). Having access to performance data at elevated temperatures for the polyethylene being used, will help to correctly determine the increase in wall thickness. The material properties published by polymer suppliers are normally generated at 23°C (73°F). The good news is that most polymer suppliers will have short term tensile properties at 23°C (73°F) and 40C (104°F). Some polymer suppliers also have longterm tensile creep properties at 23°C and 40°C. Moulders need to request this information to better predict performance at elevated temperatures.
1. Balmoral Group Ltd V Borealis (UK) Ltd & ORS, England and Wales High Court, 2006, 1900 (Comm) (25 July 2006) 2. Kingspan Environmental Ltd & Ors V Borealis A/S & Ors,
England and Wales High Court, 2012, 1147 (Comm) (01 May 2012) 3. Mercieca, Tony, QENOS, The importance of Slow Crack Growth in the Failure of Rotomoulded Products, ARMA Rotomoulding conference 2004 4. Whitehand, Garry QENOS, Polyethylene - Essential Knowledge for Rotational Moulding, ARMA Rotomoulding Conference 2012 5. Spence, Alvin, How Viscosity and Melt Index Influence
Material Selection, RotoWorld®, Volume XVI, Issue 4 (2020) 6. Henwood, Nick, What Rotomolders Need to Know about
Polymer Chemistry – Part 1, RotoWorld®, Volume XVI,
Issue 5 (2020) 7. Maziers, Eric, TOTAL Petrochemicals, Rotomoulded Products for Biodiesel Applications, ARMA Rotomoulding conference 2008.