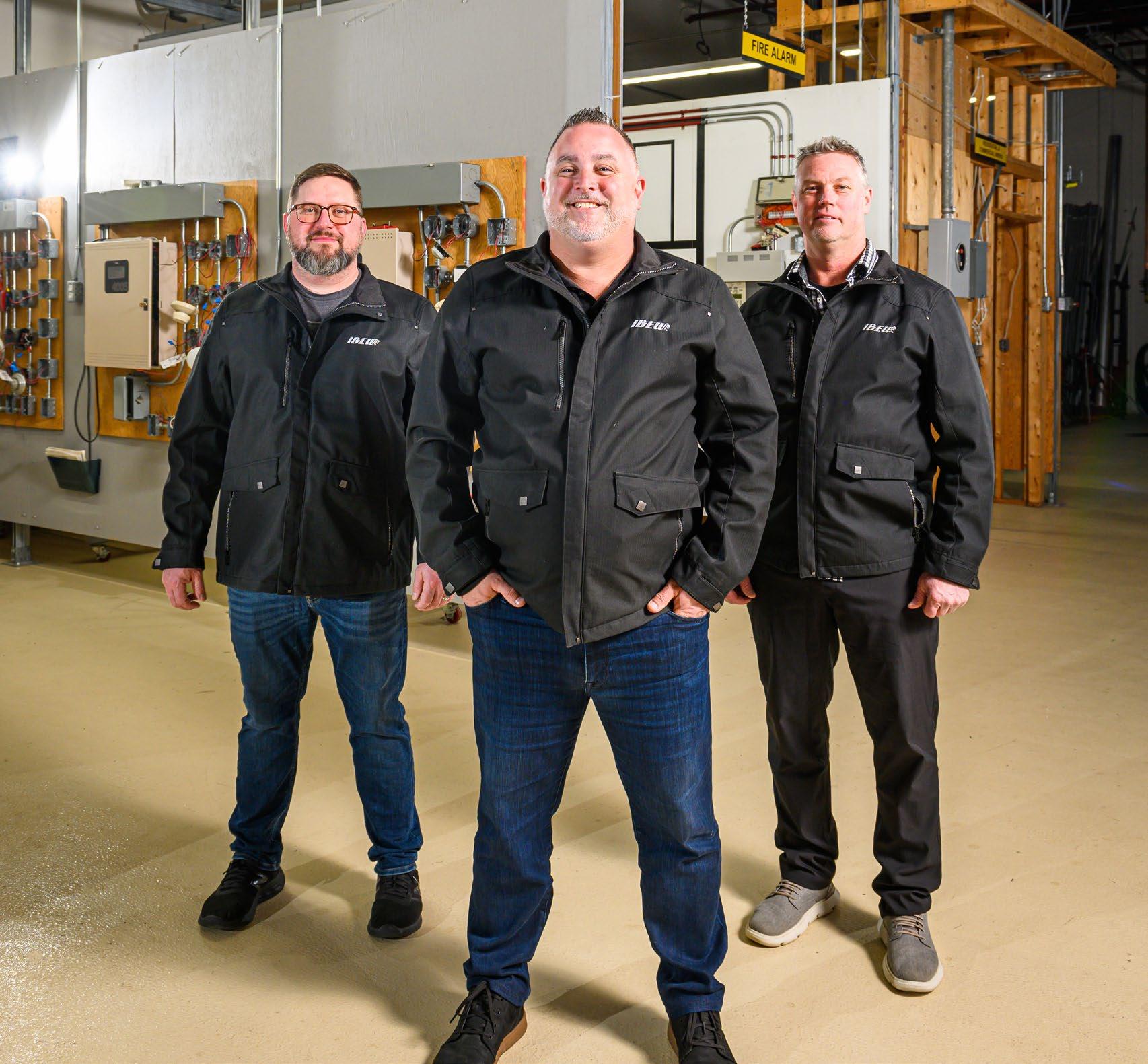
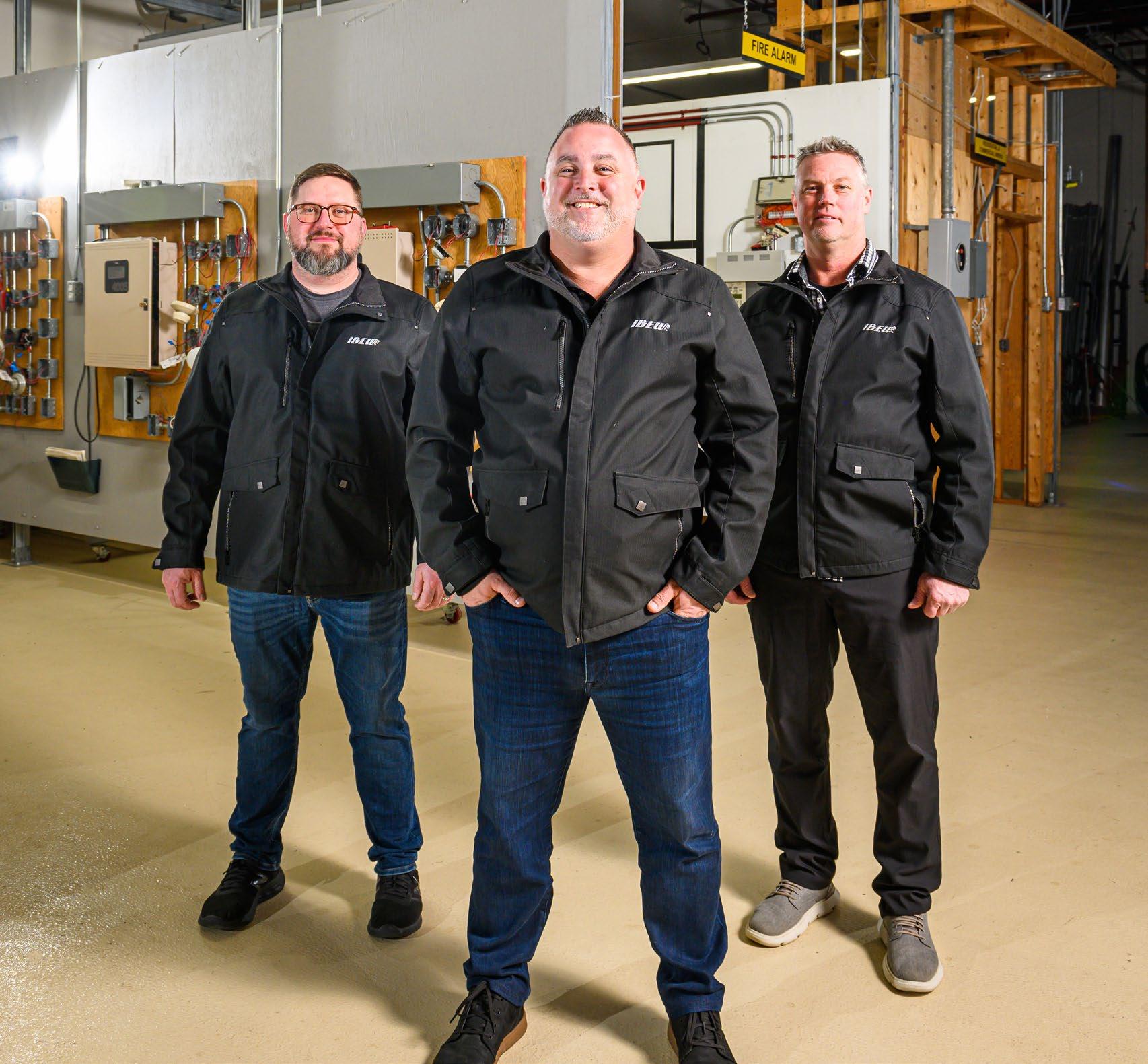
Engineering Tomorrow
Creating solutions as the automotive sector evolves
Working alongside industry to create solutions together for tomorrow.
These are just some of the ways #UWindsorEng is designing the future.
uwindsor.ca/engineering
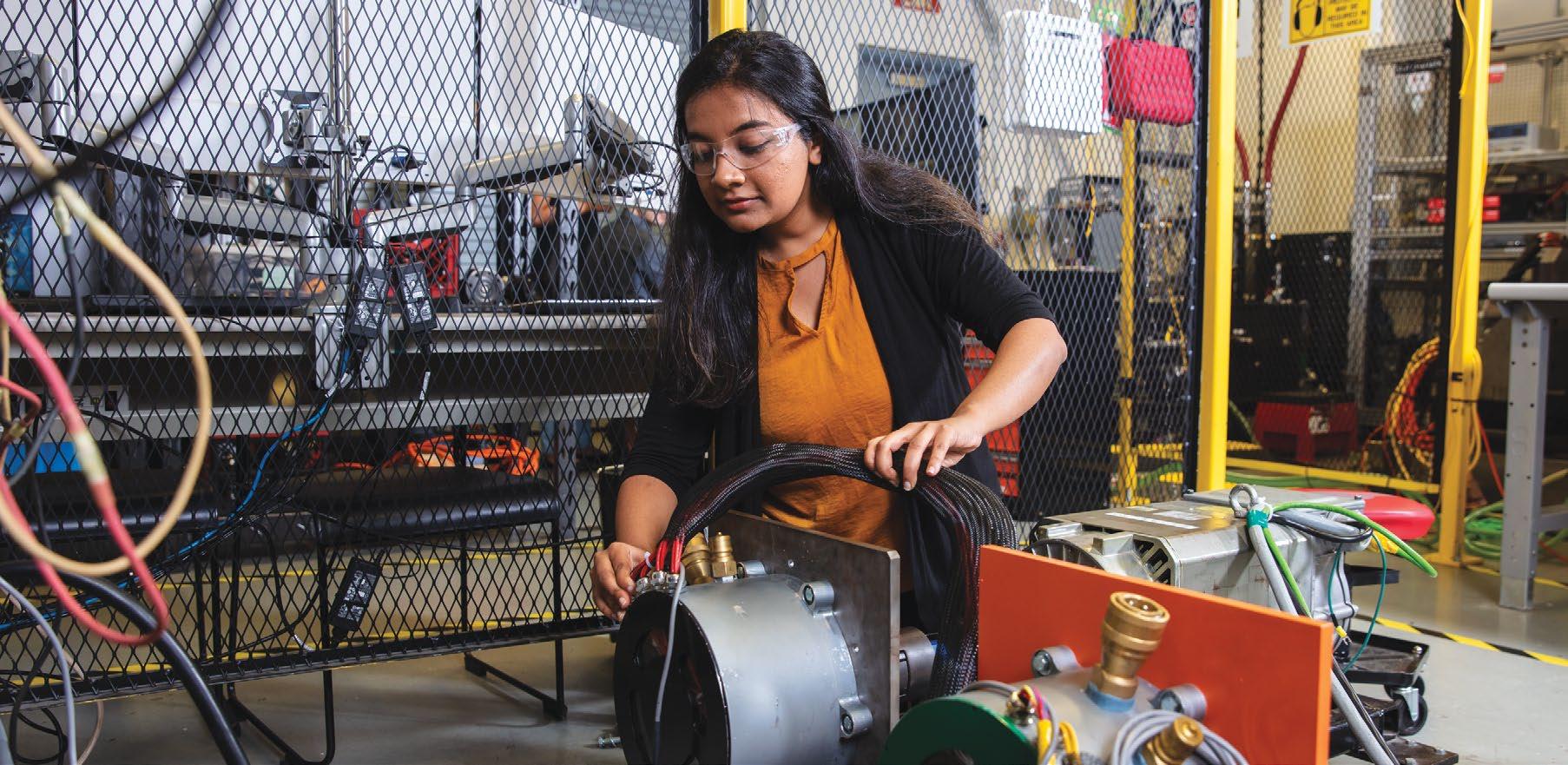
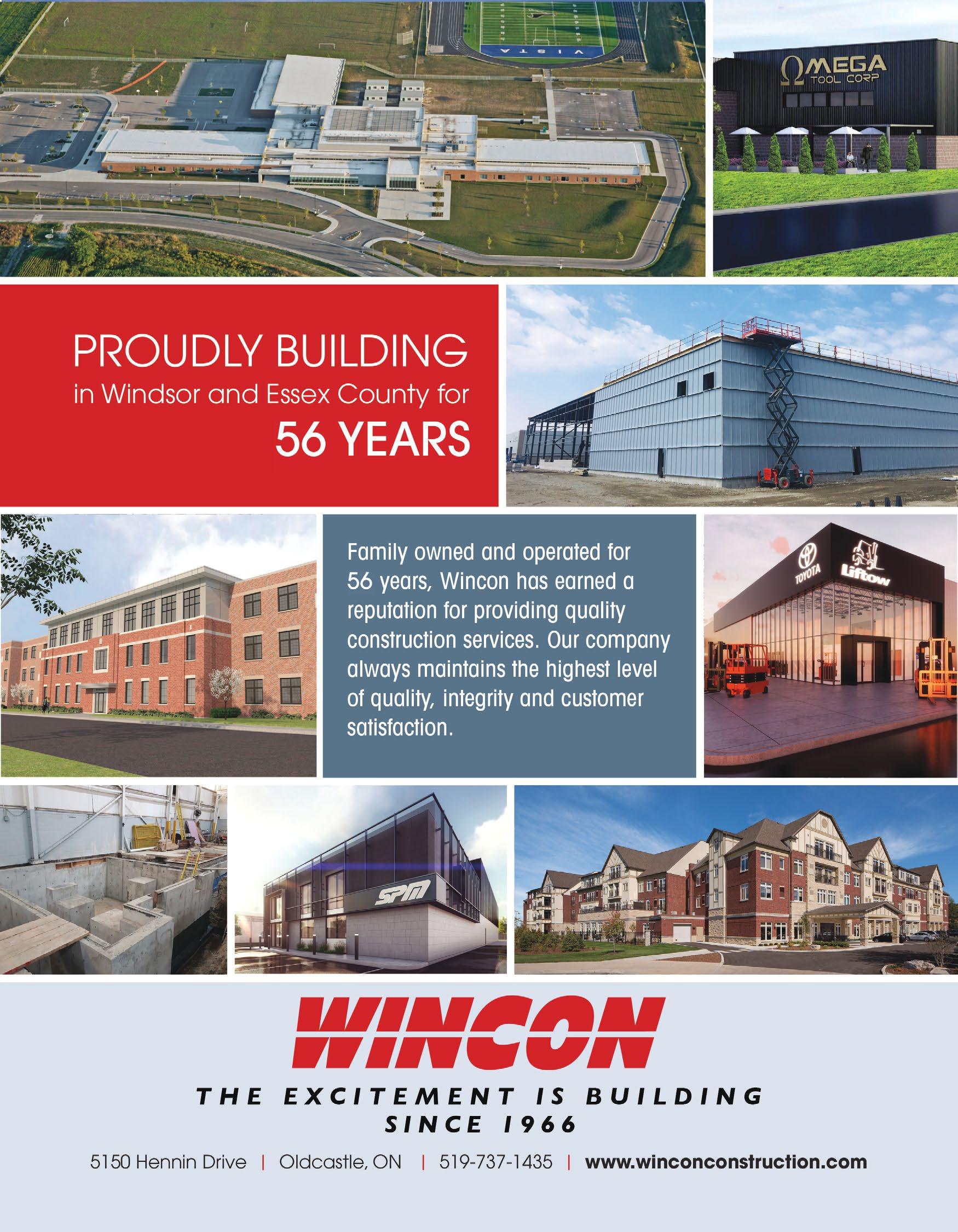
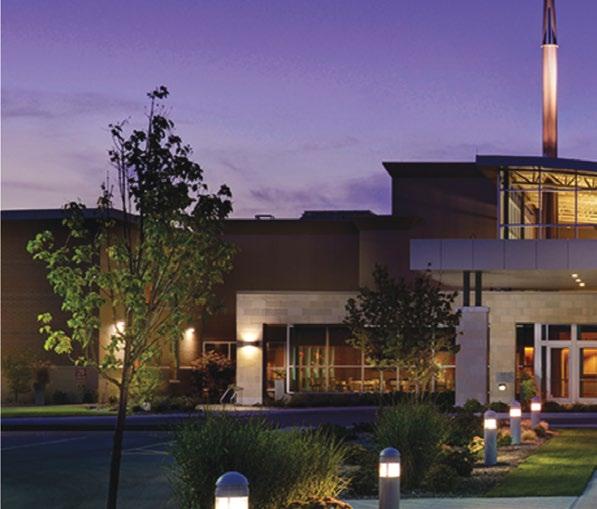
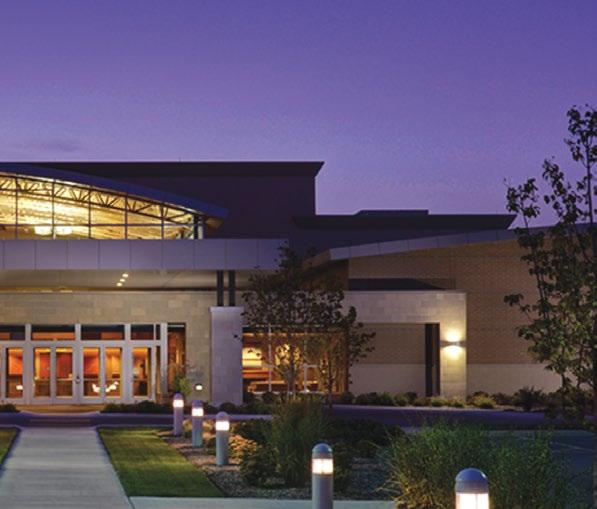

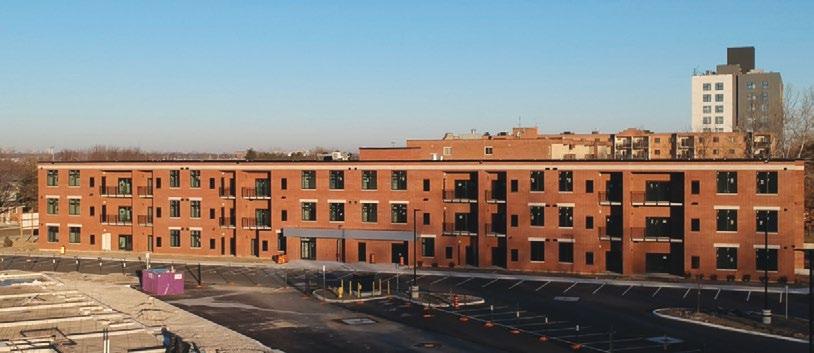

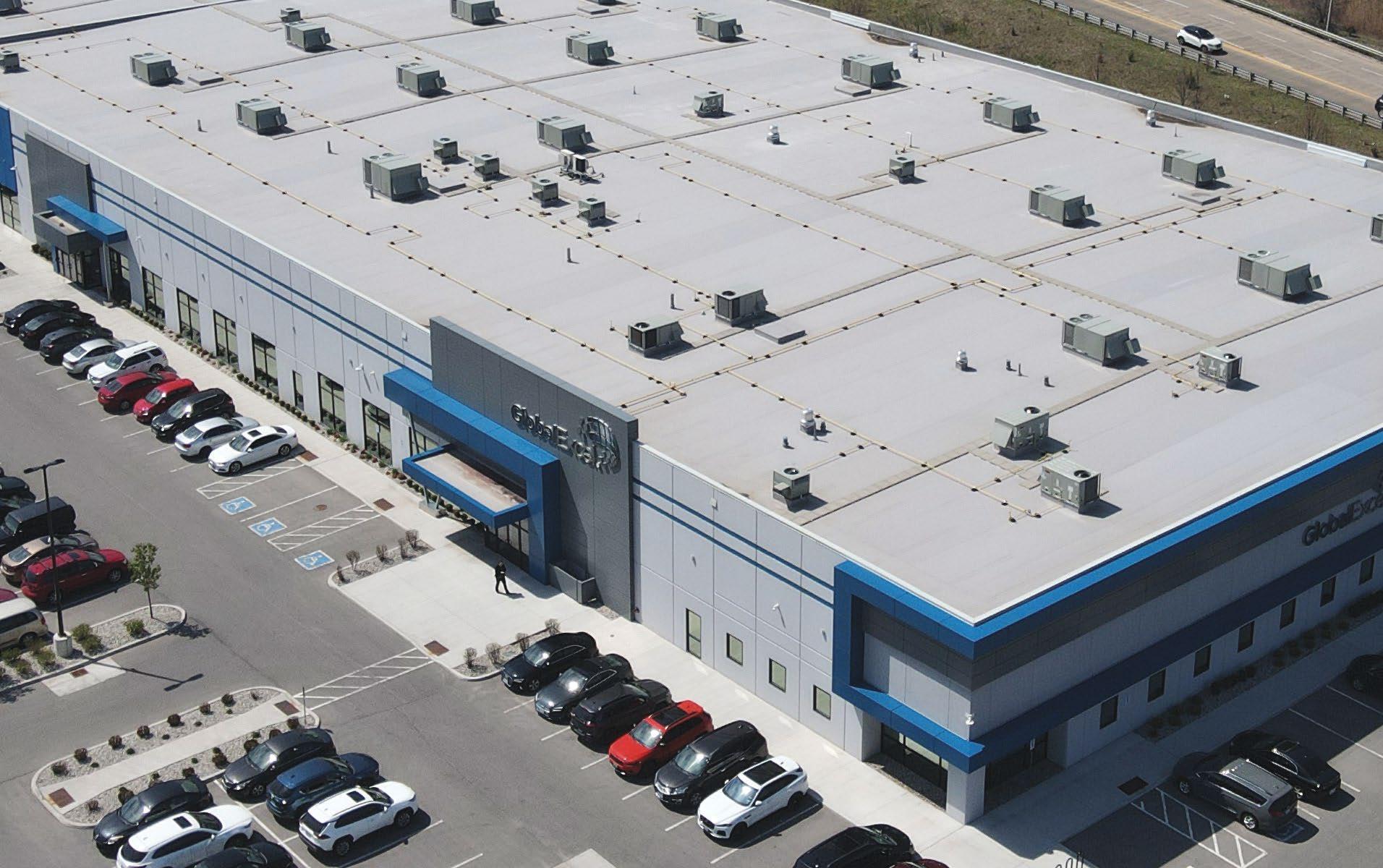

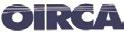

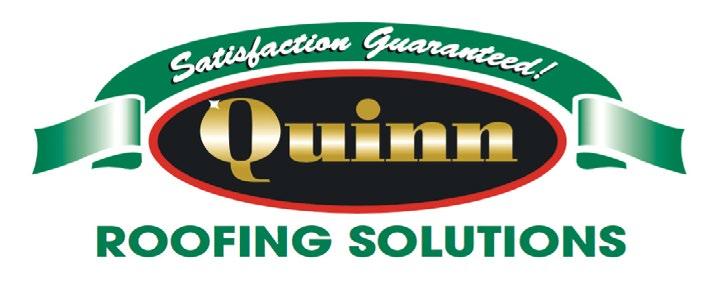
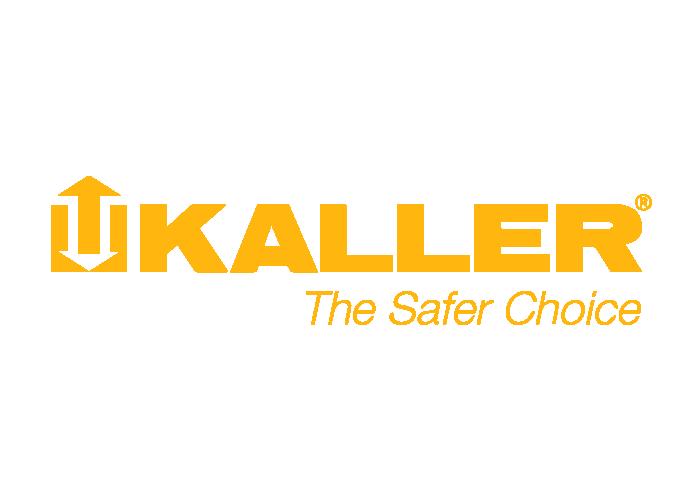
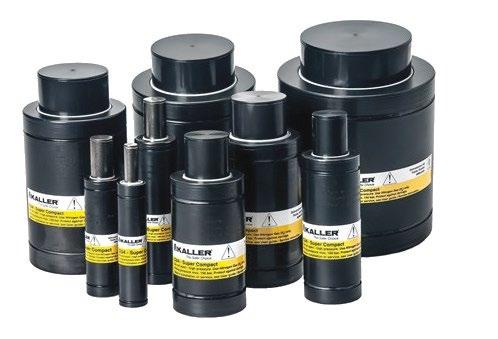


AV Gauge We Help People Grow
It is one thing for a company to state on its corporate website “We care about our people!” but it’s another thing entirely to live up to that. Oldcastle’s AV Gauge has been living up to its motto, “We Help People Grow” since its inception in 1985. AV Gauge knows about growth, having doubled in size six to seven times since the mid-1980s.
“In the history of the company, since starting in my dad’s garage in Essex County,” says Denis Levasseur, an original founder and now Vice Chair of the Board, “one of my passions has been helping my employees live a successful, balanced life. Now, seeing the second generation leading the team is very fulfilling.”
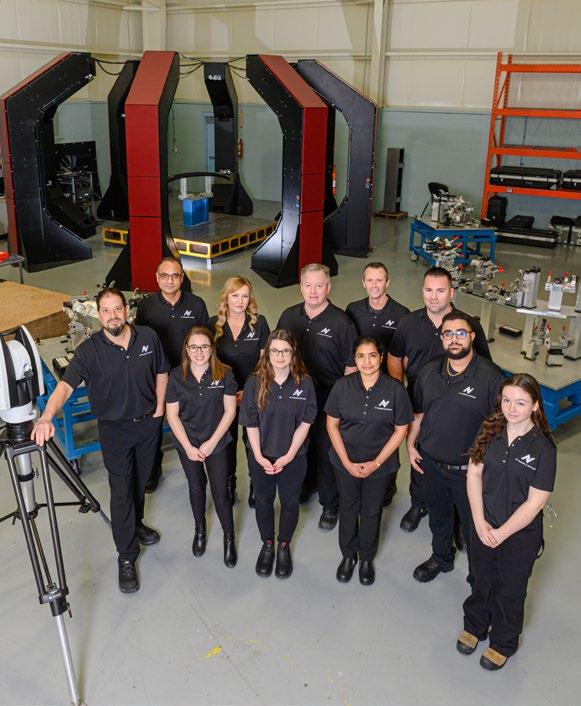
With the automotive sector’s tireless pursuit of improved quality of parts, AV Gauge rose to the challenge of providing exacting solutions for conformance, validation, and quality control verification.
By Matthew St. AmandThrough its relentless innovation and leveraging the latest in technology, AV Gauge has become the gold standard in the industry.
Tim Campeau, President of AV Gauge, explains: “We’ve expanded our products beyond the traditional check fixtures to related items on which we can apply our automation and quality expertise. We are always looking for new technology and good people to improve our products, services, and processes so that we can remain competitive on a global level.”
AV Gauge is among the select few companies chosen by Deloitte as one of Canada’s Best Managed Companies Gold Standard winners.
What kind of technology does AV Gauge use?
“Robots with CNC machines, custom software utilizing AI, photogrammetry, laser scanning, among others,” Tim says. “We hold patents from inhouse innovations that are technically superior. We developed proprietary fabricated bases, structures and carbon fiber solutions which are critical to create a solid foundation to build on. We are vertically integrated in all aspects of our business.”
In particular, AV Gauge’s Automation division is growing to meet the demands of their customers. Its core competencies include process integration focussed on inline inspection, validation, and assembly.
“Here’s an example of what our Automation Team has accomplished for one of our customers,” says Tim. “Our customer needed a machine for two different part variants. They specified that three separate stations, with one operator per station, were required. Through feasibility studies, AV Gauge combined all the tasks into a single cell requiring only one operator. This reduced floor consumption, labor and capital costs, cycle time, and increased productivity.”
As they continue to grow, AV Gauge is hiring. What are they looking for?
“A positive attitude, enthusiasm, creativity, pride, and a willingness to learn,” says Tim. “It helps if you’re mechanically inclined, but if you’re willing to learn, we’ll teach you.”
The company’s growth is tied to its employees. Being in a niche industry, AV Gauge has had to “grow its own” employees. They have done this by working with various high schools, colleges, and universities. They have been immersed in Co-Op, OYAP and other training programs for over 35 years. AV Gauge offers competitive wage packages and benefits that are fully funded by the company.
“Employees receive a semi-annual bonus based on company performance,” Tim continues, “even if you’re an apprentice who’s been here for six months. We have an RRSP program, and we’re always looking at people’s skills and helping them grow into their current and future roles.”
With plants in “Oldcastle, Kentucky, and Mexico, employing over 300 people, there is plenty of room for people to grow in AV Gauge.
For more information about the exciting services and technologies offered and created by AV Gauge, or to get in touch regarding a position with the company, visit avgauge.com. W.E.

One of Canada’s best managed companies is not only right here in Oldcastle, it’s looking for people to join its team.
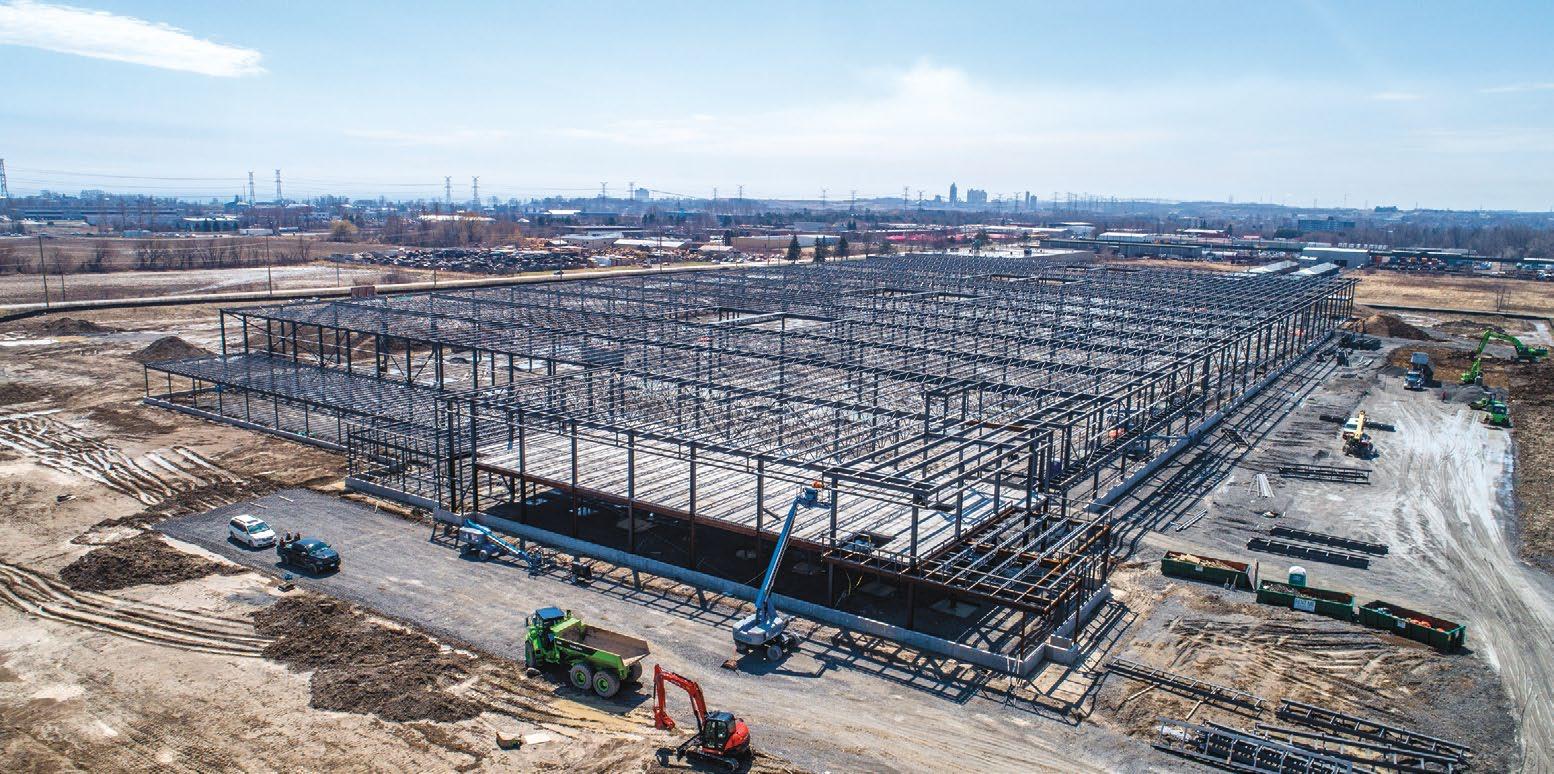
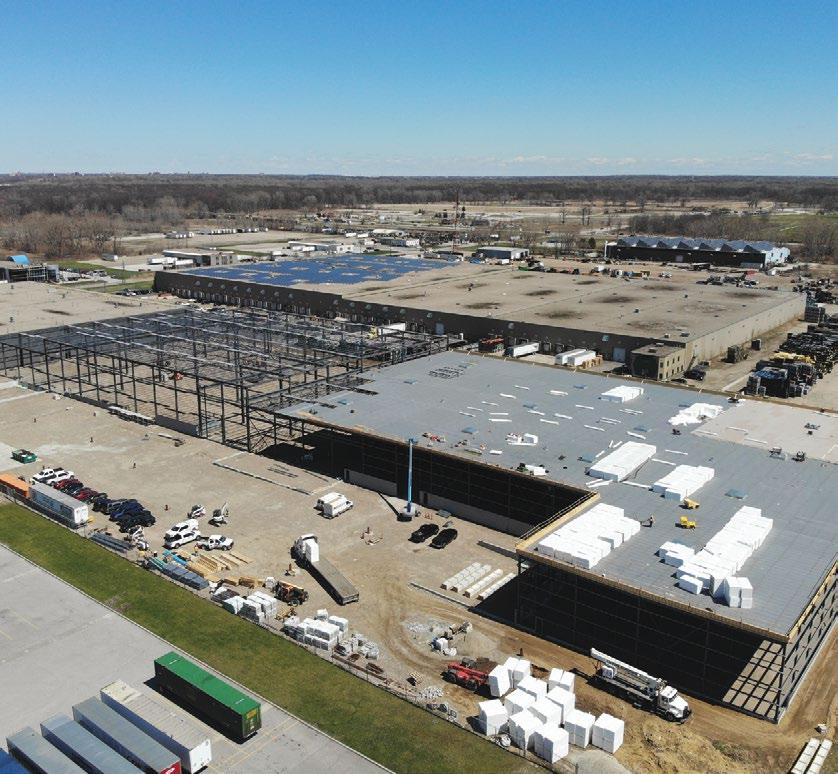

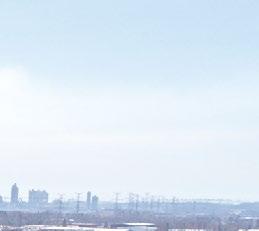
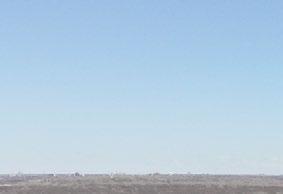

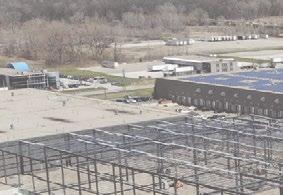

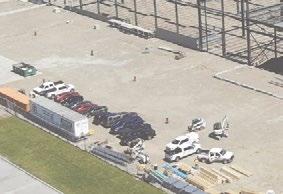
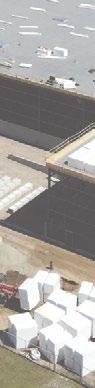
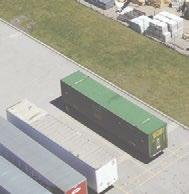
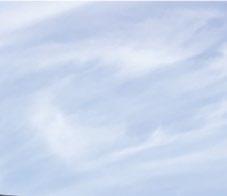
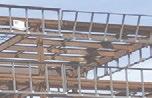

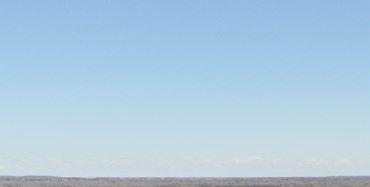

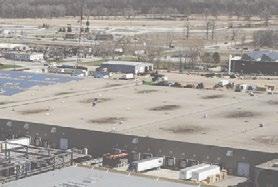


PAUL ST-PIERRE ................................................ Publisher
DAVE HUNTER .................................. Vice President, sales
BREANNE MCGINTY.................................................. Sales
MEL MONCZAK Sales
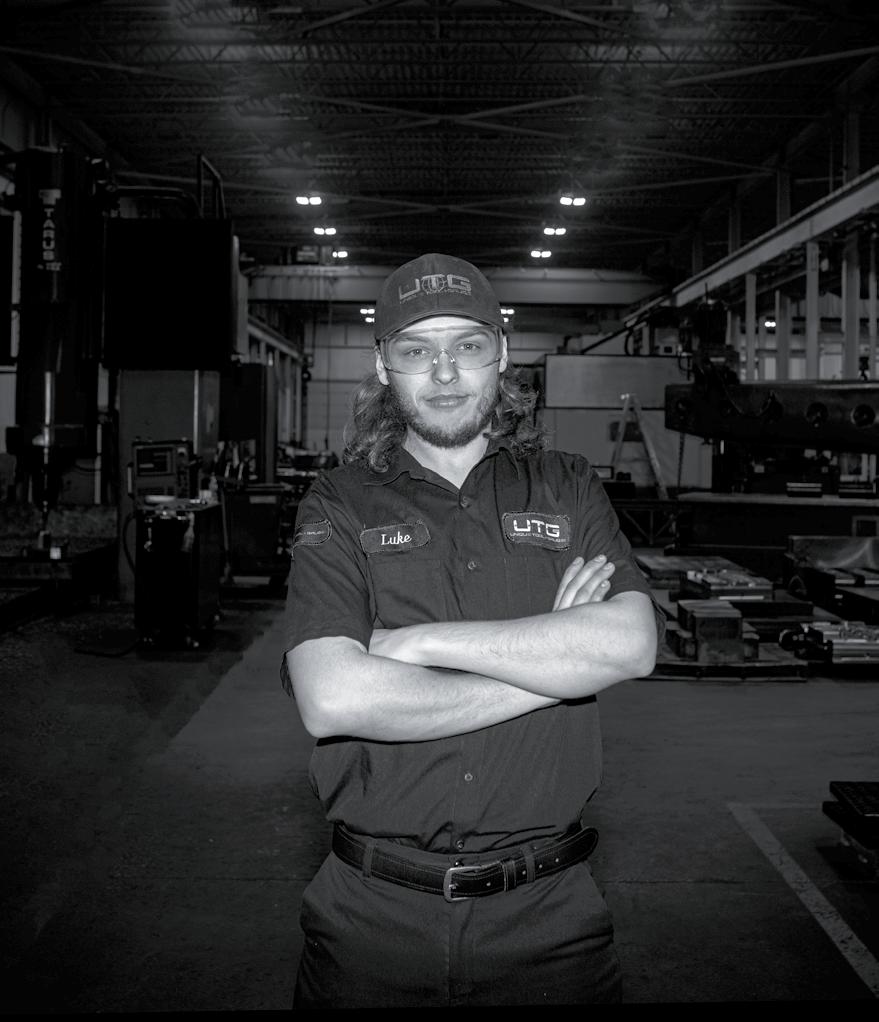
SHAWNA BEECROFT Graphic designer
GREG EDWARDS .................................... Graphic designer
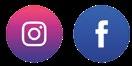
MARNIE ROBILLARD ............................ Director of design
CONTRIBUTORS
MATT ST. AMAND Writer
MAYOR DREW DILKENS ......................................... Writer
MPP CHRIS LEWIS ................................................. Writer
DEVAN MIGHTON Writer
SYX LANGEMANN Photographer
To advertise in W.E. Manufacture please contact:
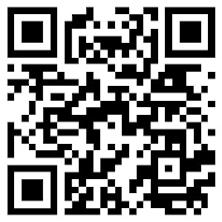
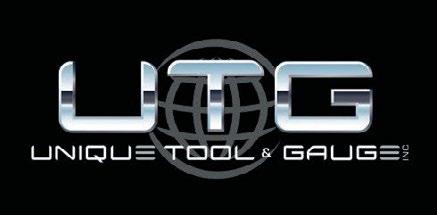
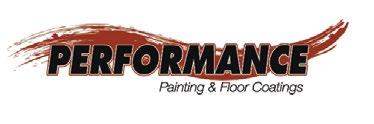
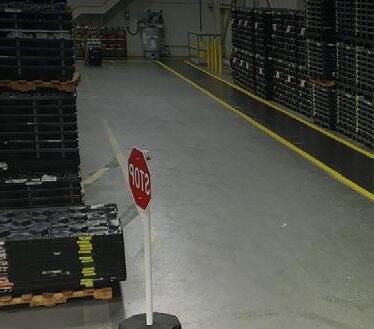

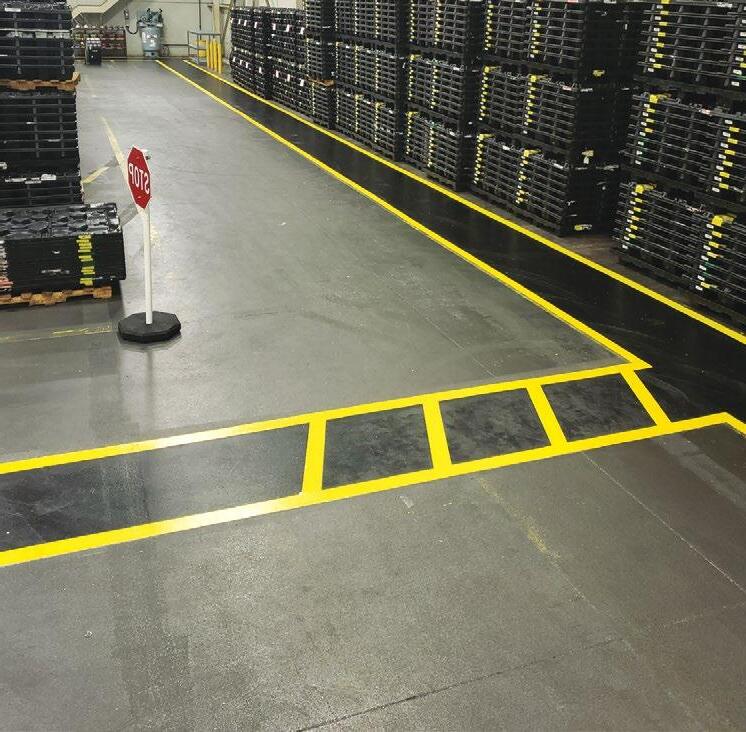
David Hunter – Vice President, Sales Cell - 519-816-0874
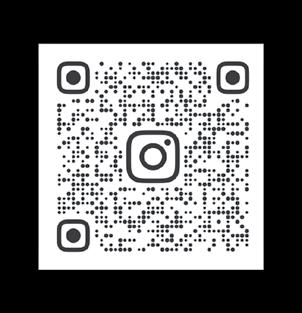
dhunter@thedrivemagazine.com
Breanne McGinty – Sales Cell - 519-819-4697
bmcginty@thedrivemagazine.com
Mel Monczak – Sales Cell - 519-903-1353
mel@thedrivemagazine.com
TREVOR BOOTH Photographer CANADA
ISSUE
By Devan Mighton
Photos by Dave Hunter
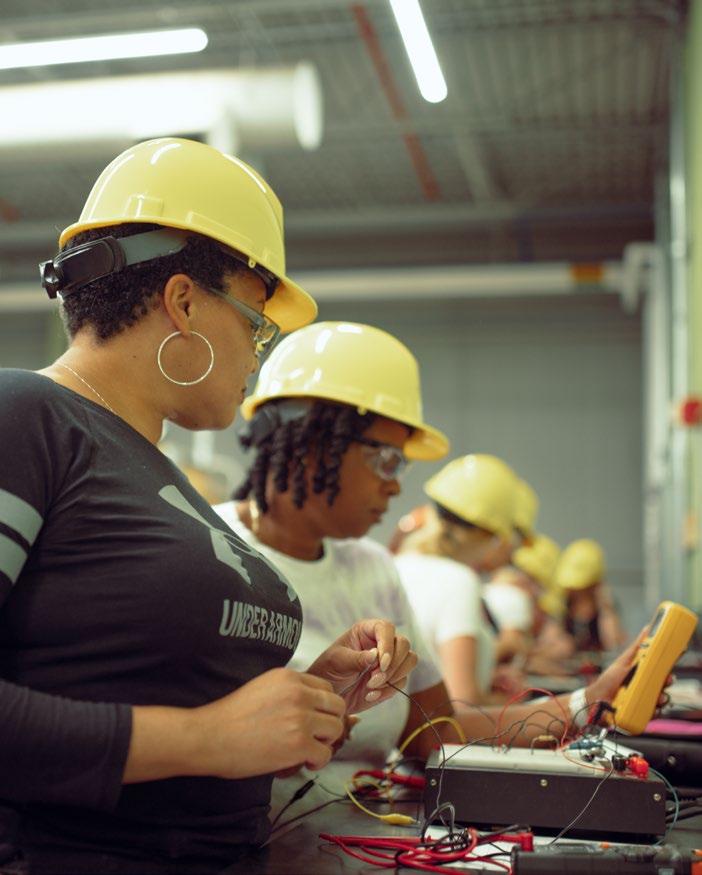
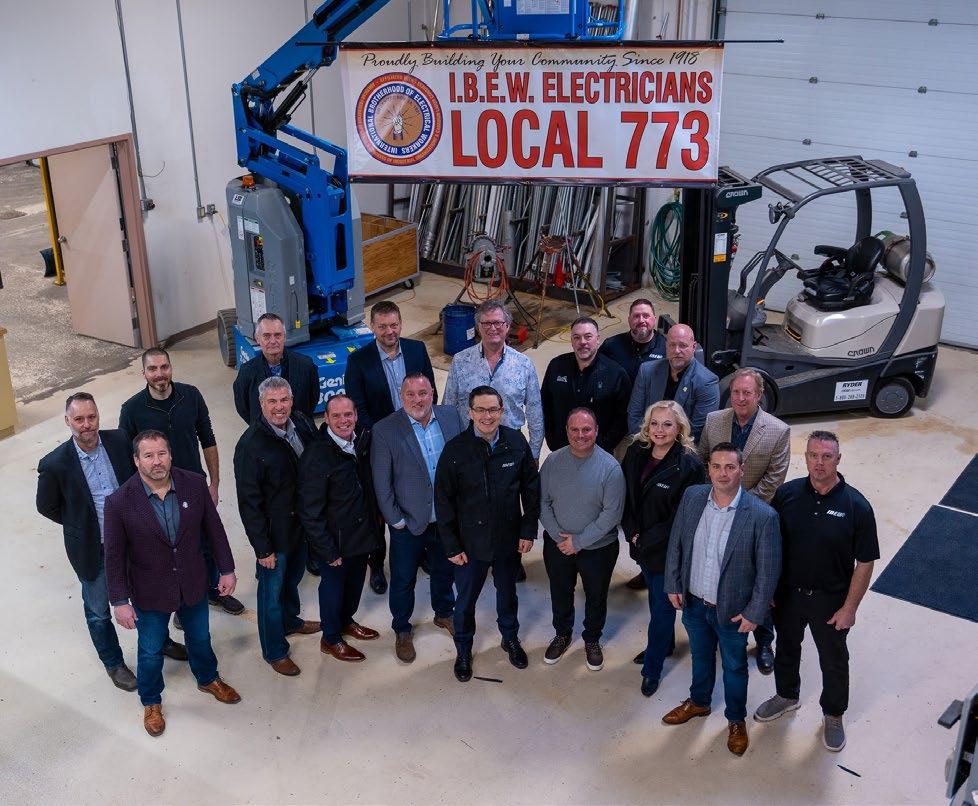
THE CITY OF WINDSOR
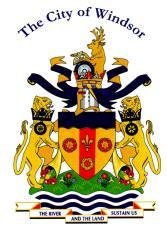
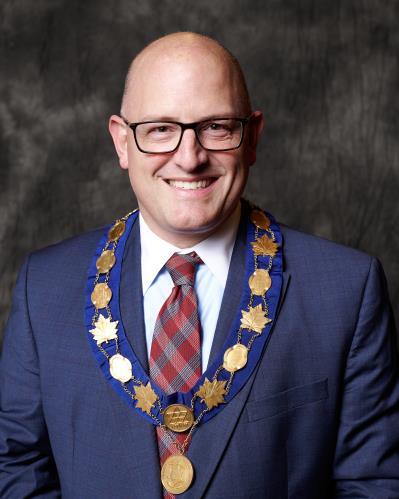
The City of Windsor is proud of its reputation in Canada and around the world for its work in design, construction, tool and die, research and development, automotive, and many other key sectors that form the broader manufacturing industry. Our strength as a manufacturing and automotive powerhouse have placed us on the world stage as a leader in the field of automation.
Our community is experiencing continued growth as a result of the game-changing announcement of the $5 billion NextStar Energy EV battery manufacturing facility. Work is underw ay to build this facility. Once operational, it will add over 3,000 new full-time positions to our community with significant additional spinoff jobs in supporting sectors. Of course, there’s a direct correlation between this kind of economic boost and the need for new housing options at a time of significant affordability challenges. Following a provincial Housing Summit, Premier Ford announced more than $45-million for a new Streamline Development Approval Fund. I was proud to be appointed as the Chair of Ontario’s Housing Supply Action Plan Implementation Team, which has been tasked with giving advice and proposing solutions to the province to tackle the housing affordability crisis. The Premier also announced a new plan to get housing built across Ontario, setting targets for 29 fast-growing municipalities to ensure the province achieves its overall goal of building 1.5 million new homes in a decade. Windsor is on that list, with a goal to see 13,000 new homes built by 2031.
As we continue the process to build our new regional acute care hospital, there is a need for our community to prepare the Sandwich South lands for future investment. This will mean new areas for industrial, commercial and residential growth Across the city, the Gordie Howe International Bridge continues its construction phase, with major impacts on our manufacturing sector. At the City of Windsor, we continue to support our rapidly changing global marketplace, positioning our region as a leader in the next industrial revolution. As the world pivots to EVs, Windsor -Essex has become the ‘Automobility Capital of Canada’
We are at a crucial point of unprecedented growth and opportunity, with more large -scale corporations, mid-size companies, small businesses, families and individuals looking at Windsor as the ideal place to invest, work, live, and lay down roots. Our manufacturers, our tradespeople, our innovators and dreamers are all at the heart of this exciting shift. I remain grateful for their continued support in building a strong and prosperous community.
Drew Dilkens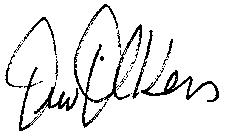
Custom Solutions That Last
More than twenty years in the business, and this local machine and tool shop remains on the cutting edge.
By Matthew St. AmandOff-the-shelf, cookie-cutter solutions might be easier to provide, but they are certainly not more interesting. Nor do they serve the needs of businesses in an increasingly competitive and technology-driven economy. At Trillium Machine, there is no interest in easy solutions.
“All of the work we do is custom,” says Trillium Machine co-founder Mike Hamelin. “Each customer has their own challenges, and Trillium continues to provide solutions.”
Founded in 2001, Trillium is a turnkey solutions company specializing in designing and building custom automated machines for a range of industries, including automotive, food processing, and consumer products.
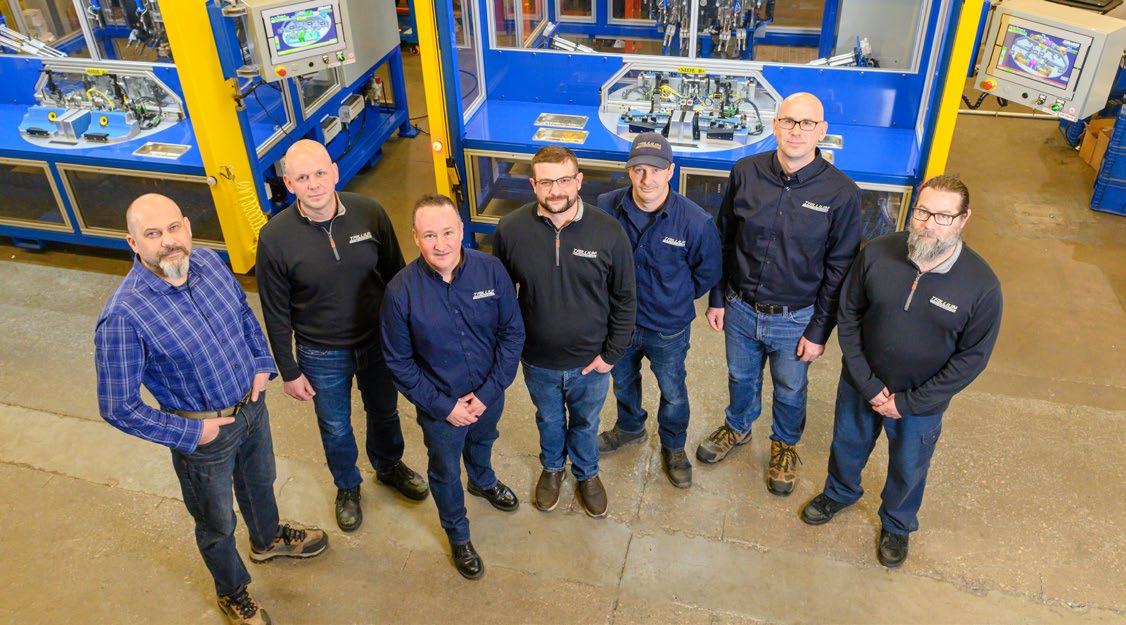
Because the challenges coming through the door are as singular as the customers who bring them, Trillium lives on the cutting edge of technology.
“Right now, we’re starting to work with ‘cobots,’” Mike explains, “which is short for ‘collaborative robots.’ These are robots that people can work safely with, side by side.”
Anyone who has been in the manufacturing environment is familiar with the myriad safety precautions taken to separate human beings from robots. Light curtains, area scanners, Safety interlock assembly cells, are but a couple of the safety measures to ensure a traditional robot ceases moving the moment a person is within its proximity.
“It took some getting used to,” Mike says, “but we’re finding that cobots are great for repetitive pick-and-pace tasks. They are reasonably new to the industrial field, but we are finding that they are safe, they’re very reliable. They can undertake the monotonous, repetitive tasks while the person working beside them can do the more intricate, complex tasks.”
six-axis robots found in most manufacturing settings. At the present time, they are working with a compostable materials company from British Columbia that is setting up shop in Windsor. This company produces compostable single-serve coffee pods, similar to K-cups.
“It all happens under one roof,” Mike says. “They roast the beans and fully package them at the end of the line. We’re in there at the ground level. This company is one hundred percent plant-based— everything they’re based on is plantbased. Once discarded, their coffee pods biodegrade in less than a month.”
One area that Trillium has gravitated toward is ultra sonic welding. Trillium has teamed up with industry leader, TELSONIC Canada Inc., and is quoting on building machines incorporating TELSONIC’s ultra sonic welding capabilities.
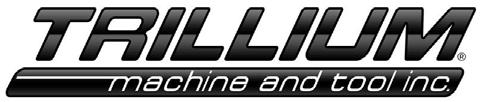
“They make the weld controllers and welding horns,” Mike explains, “and Trillium integrates them into our assembly machines. Right now, we are doing this mostly for the automotive and food and beverage products. We have made one-offs throughout the years, but this is
something we’re hoping to do more of. It’s opening doors to new customers and to new industries.”
He continues: “Each product, each different plastic is different. Every product we weld together has its own challenges. Telsonic has an office in Windsor and has excellent support.”
Trillium counts success one project at a time. One such successful project recently revisited them.
“The first machine Trillium designed and built was a stainless steel Tig welding machine that welds the top collar onto fire extinguishers,” Mike recalls. “We built the machine for a local company, Flag Fire Equipment, which was eventually purchased by Johnson Controls of Wisconsin. After twenty-one years of continuous use, the customer submitted a Request to Quote a duplicate machine. The original will continue being used, and they need another just like it because business has picked up.”
Not only does Trillium design and build custom solutions, but they deliver solutions that have staying power. -To learn more about what Trillium does, visit them online at trilliummachine.com.
Navacord is one of Canada’s largest commercial insurance brokers with over $1 Billion in premium and teams of industry specialized advisors. As a Navacord Broker Partner, one of Canada's largest commercial brokers, Ives Insurance offers increased Manufacturing sector expertise, expanded product offerings and stronger relationships with insurance companies.
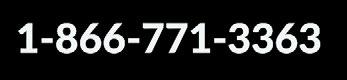


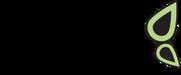
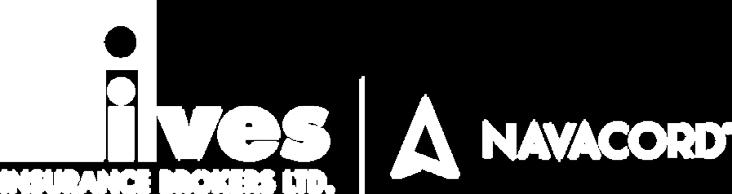
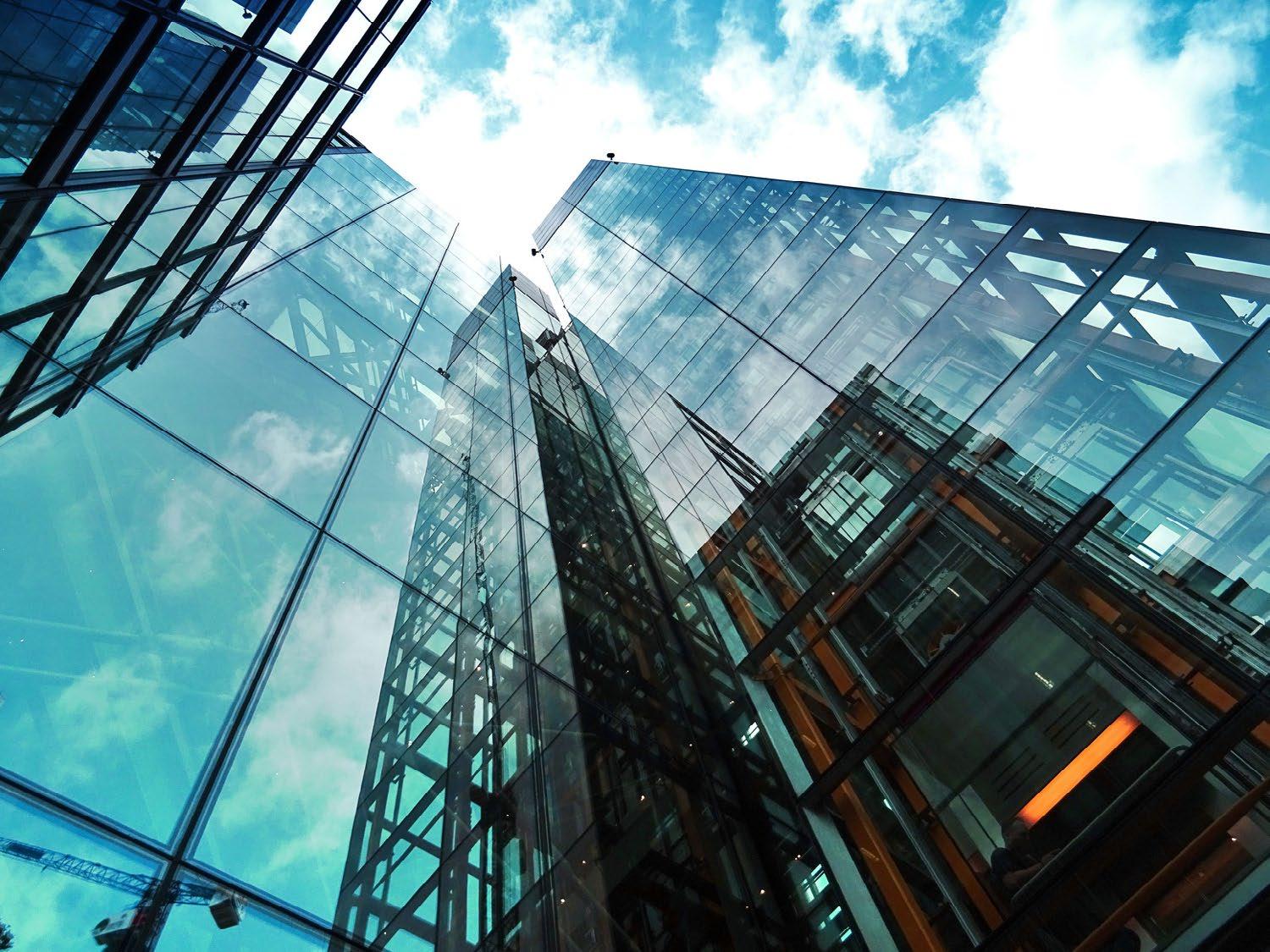
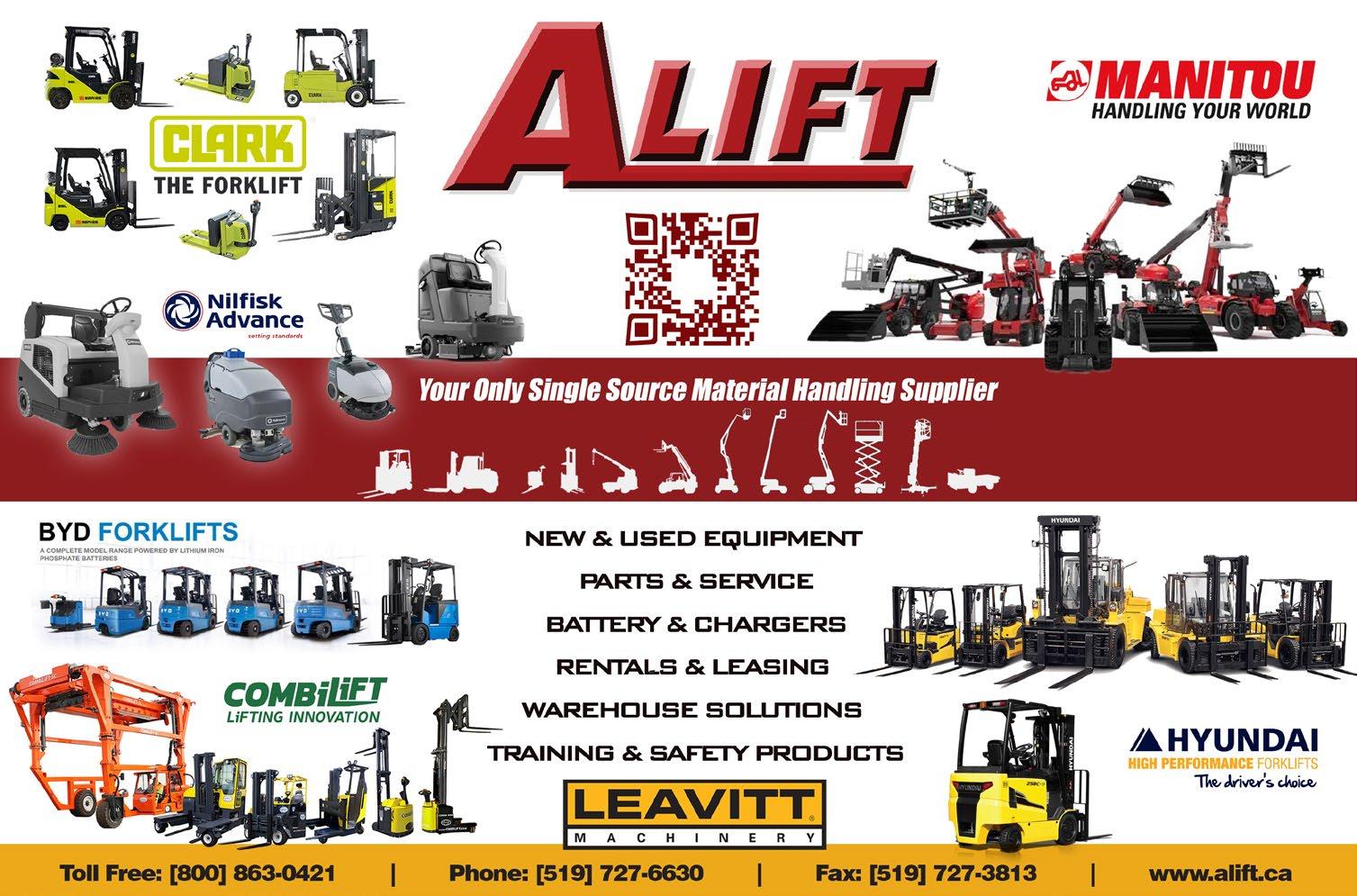
Chris Lewis , Member of Parliament for Essex Shadow Minister for Labour
I’m excited to represent Essex during this next chapter of growth . The future is bright. The new battery plant , the Gordie-Howe Bridge and all the investments they bring only build on the current tool and die and auto -manufacturing industries. These developments will need to be stewarded well. Of course, with this growth we must be prepared to gear up for a different set of jobs. Training new workers and re-training experienced workers to take on those new jobs , in a level of manufacturing we have never witnessed before, will be central to that stewardship This is vital, to guard against experienced workers losing their jobs in the changeover to electric vehicles.
I have always thought that skilled trades need to be taught right from a child’s early years. That is why I continue to encourage our future generations that a career in skilled trades and manufacturing is something in which they can be proud of and be paid well. These jobs are among the best in the country. The developments in electric vehicles, hydrogen power, auto -mobility and so many other advancements in technology will create a s teep learning curve, however the benefits will reap reward and our country will excel with fresh thinking and young minds to carry the torch into the next era of manufacturing.
In 2019 I was honoured to become the Member of Parliament for E ssex. Recently I have been tasked with the role of Shadow Minister for Labour. Further, I work with a group of MPs as Chair of the Conservative Auto -Caucus. This keep s me up to date with developments in my riding, the Labour world , and the auto-sector, to better plan for what Conservatives can do for our region and nation. It’s the perfect combination of responsibilities for me. As a member of the Transport, Infrastructur e and Communities Committee gives me the opportunity to speak to those decision s that are being made in areas like air, rail, roads and of course our international bridge and seaports. Ultimately, my greatest responsibil ity is to serve the people of the riding of Essex The decisions I make on a national level are always top of mind to the impacts they will have in our region.
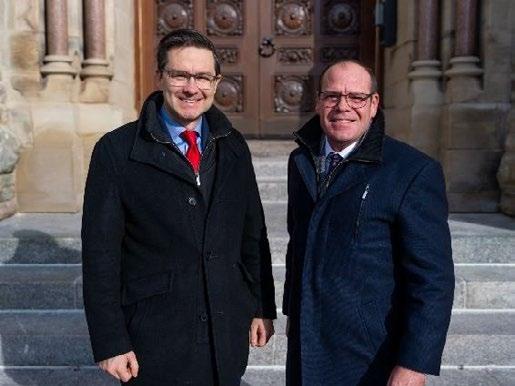
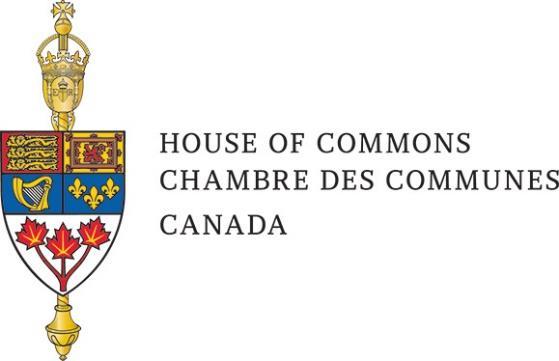
I have introduced a Private Members Bill (C-241) which would allow for a tax deduction for a tradesperson’s travel expenses, such as meals, lodging, mileage, or flights This is only the beginning of what can be done for our trades people in Canada. Supporting this bill along the way , with many organizations were Tomi Hulkkonen, the Coordinator of UBC Local 494 and Pierre Poilievre, our CPC Leader Pierre understands that we must support skilled trades, to which in turn supports our manufacturing industries. We continue to meet with both union and non -union skilled trades and manufacture rs across the country to further understand what is needed to support and build Canada in the future.
Looking forward, I am mindful that there are many areas of need in our country. Families and business es need relief from the pain of the current cost-of-living, inflation and supply issues that are impacting every single industry and worker My goal is to turn that pain into hope so manufacturing will be on solid ground and prepared for the developments ahead . I look forward to what the future holds and working together to make the world a better place than we found it! It is an honour to serve Essex.
Sincerely,
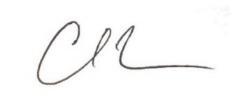
Longevity is not about doing the same thing over and over, and checking off the weeks, months, and years on one’s calendar. In fact, achieving longevity—particularly in business—means being most adaptable to change. The crew at Cunningham Sheet Metal (Windsor) Ltd., know something about this. With a history that goes back to 1908, they have not stayed in business by just doing the same thing over and over.
“You have to adapt with the changes of the times,” says Cunningham Sheet Metal co-owner, Justin Marchand. “We’ve always been known as a custom fabrication shop, but our actual trade is sheet metal, HVAC, and duct work— “tin knocking.” Things shifted over the years as we responded to customer demand, so we are doing more of that type of work.”
Justin, himself, is no stranger to change. He began with Cunningham in 2009 as a second-year apprentice and rose through the ranks where he is now a part-owner.
Nobody at Cunningham rests on the laurels of their 115 years in business. Just recently, the company decided to make a major capital investment, bringing in a state-of-the-art laser welder.
“This cutting-edge laser welder… there are only a handful this side of the

Cunningham Sheet Metal Stays on the Cutting Edge
By Matthew St. Amand Photo by Trevor BoothGTA,” Justin says. “This is not something you just buy off the shelf. It’s a significant investment that will increase efficiency and produce higher quality work.”
The two most common types of welding in Cunningham’s trade are Tig and Mig. Tig is very refined, and the welder has a lot of control, but it’s time-consuming. Mig requires less skill and is much more user friendly. It’s fast, but it’s less refined and used more in production-type welding.
“This laser welder combines the speed of Mig welding with the accuracy of Tig welding,” Justin explains. “It means more training for us because this is a Class Four laser, the most dangerous type of laser you can have. Manufacturer’s standards and Ministry guidelines require stringent safety measures for this machine. Most notably, it requires its own booth/lab, blocked off from the rest of the shop. It has special laser safe glass on all its windows. The door has an interlock that instantly kills power to the welder if it’s opened.”
Why bring in a laser welder that is expensive and requires extra training?
“This will create a better process inhouse for us,” Justin says. “It will cut our welding and cleaning time in half. It will also allow us to weld thinner material with less distortion. We anticipate
this could solve some of the problems that traditional welding produces, and the industry has just become accustomed to.”
Cunningham was purchased in 2012 by Justin’s partners, Carlo Cerroni and Rino Tedesco. In 2015, they moved from their historic Walkerville location to a more modern, spacious 10,000-squarefoot facility at 2060 Blackacre Drive in Oldcastle.
They serve customers in multiple sectors: commercial/industrial, pharmaceutical, and healthcare. Past projects include copper eavestroughs and downspouts at the legendary Low-Martin House in Walkerville, machine guarding for Hiram Walker and stainless-steel signage and statues for the University of Windsor. They also did the HVAC sheet metal for the Walkerville Collegiate Institute renovation.
Every industry is cyclical, but Cunningham is sufficiently diversified to weather the slow periods. And they’re always adapting to the changing economy.
“We fabricate and install commercial and industrial duct work,” Justin says. “That’s our trade. That’s what our guys are trained for.”
To learn more about the work going on at Cunningham Sheet Metal, visit them online at cunninghamsheetmetal.com. W.E.
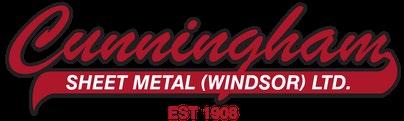
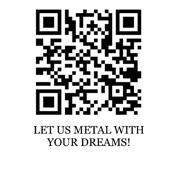
With a 115-year history in the business, this Windsor sheet metal shop continues to re-invent itself.
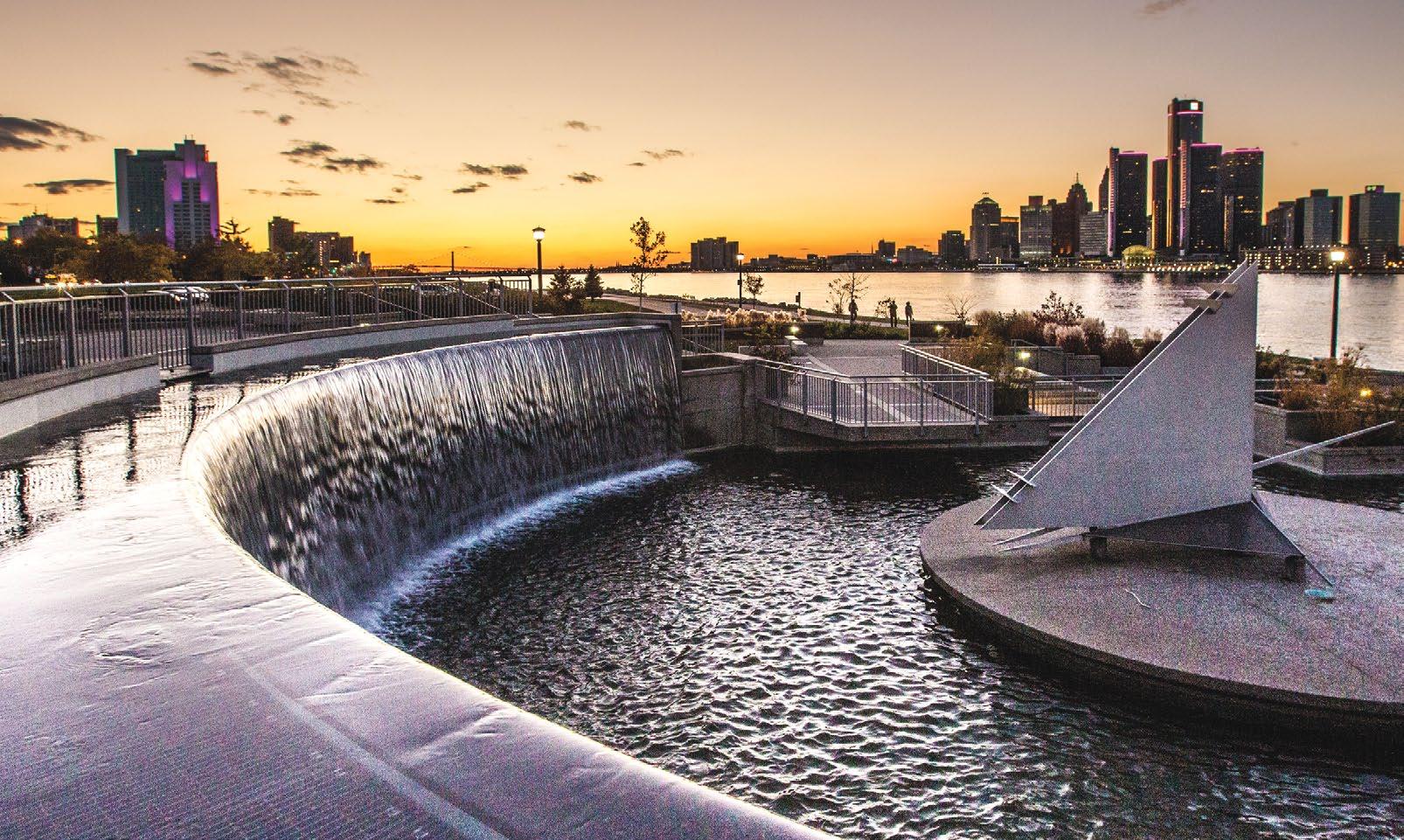
Our people go through four years of mandatory night school where we train them for what they’re going to learn at trade school, and then they go to St. Clair College, for instance, to learn their trade.”
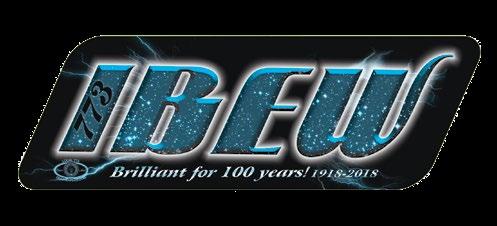
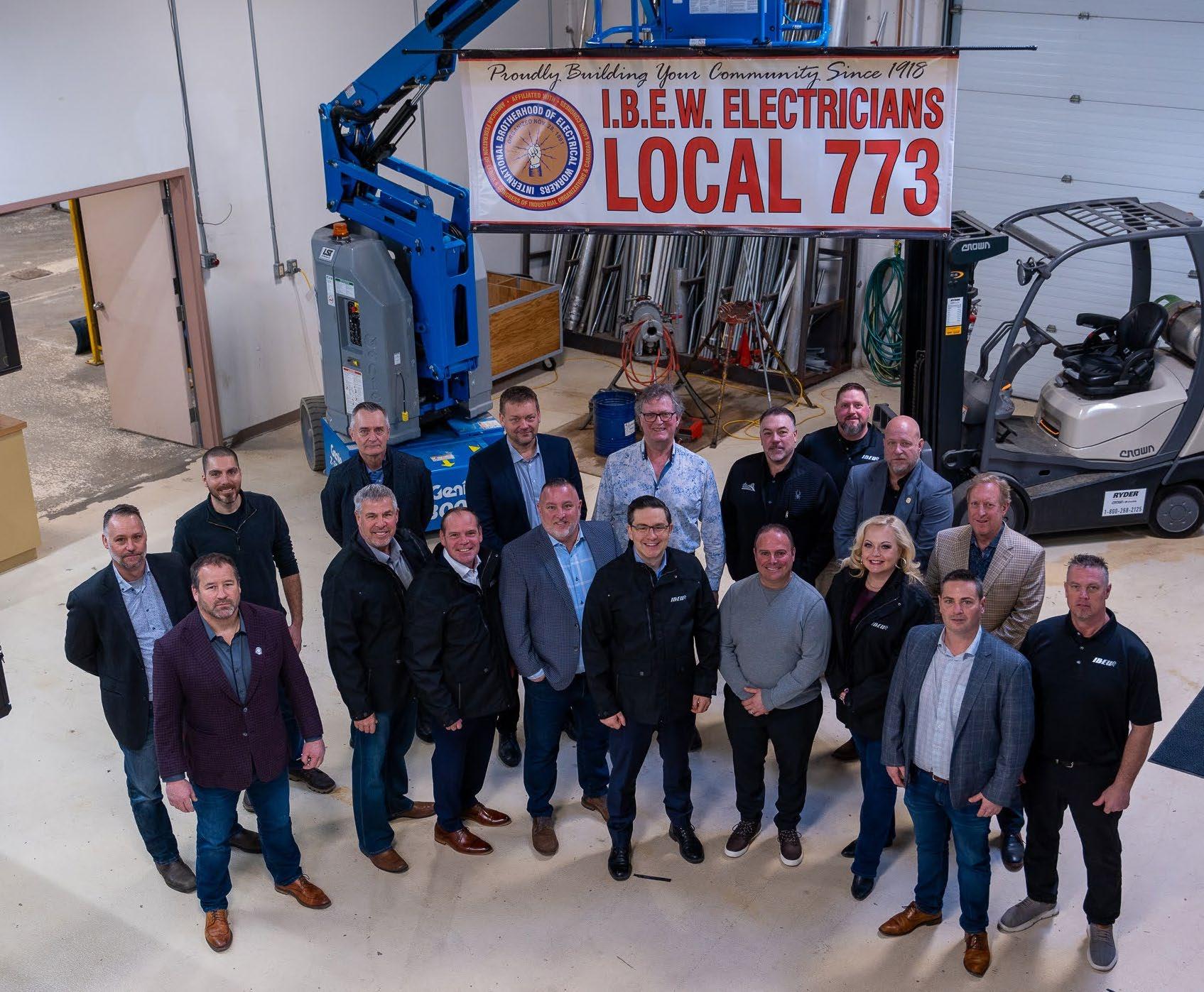
IBEW 773 Windsor Standing
Shoulder-to-Shoulder
By Matthew St. Amand Photos by Syx LangemannIn a sea of uncertainty, there are few beacons to guide job seekers along their way. For young people, particularly, just beginning to think about their futures, there have never been more choices for post-secondary education. It’s one thing to follow a dream, but it’s a universal certainty that, at some point, the future comes calling.
One of those beacons is the International Brotherhood of Electrical Workers (IBEW) Windsor Local 773. Unlike many employers who expect young people to come through the door already fully formed, inexperience is not a strike against applicants at the IBEW 773. All that is required is a desire to learn, a willingness to look at options they may not have considered before.
No origin story is complete without twists and turns. The IBEW 773 came into being on November 28, 1891, as the National Brotherhood of Electrical Workers (NBEW). It was founded in St. Louis, Missouri, and represented 286 members employed in the electrical industry. The brotherhood’s stated purpose was to look out for the people doing one of the toughest jobs in the country. The union came to Canada on December 20, 1899, setting down roots in Ottawa. At its sixth convention in 1899, the name was changed to the International Brotherhood of Electrical Workers (IBEW).
If this multi-trade service provider isn’t on your radar—it should be.
After more than 130 years, its core values remain the same: looking out for its members’ best interest.
So, how is the IBEW 773 a beacon to job seekers?
“We have people with masters degrees in bio chemistry, psychology, business degrees,” says IBEW 773 Business Manager, Karl Lovett. “People with all kinds of work experience. They have fields, elsewhere, but are not satisfied with the money they are earning or the challenges they face. They come to us for retraining. And once they’ve gone into the trades, some have come back and said to us: ‘Why didn’t I do this sooner?’”
He continues: “So, it only makes sense for young people who are looking to make their way into the workforce to come to the IBEW and do their apprenticeship.”

Applications for apprenticeships through the IBEW 773 are accepted each March.
“We accept resumes,” Karl says, “but they must be accompanied by a completed application.” They’ll need a copy of their grade twelve diploma and have proof they were successful in a senior level math course. We get more than two hundred fifty applications a year. Last year we accepted thirty-eight applicants for the apprenticeship program.”
Applicants are encouraged to begin the process in early March because the processing of candidates only takes place during that month. If a candidate’s paperwork is not in order, they will want to have as much time as possible to secure the proper documents.
Is there anything applicants can do to increase their chances of being accepted into the IBEW 773 apprenticeship program?
“If they can, I’d recommend candidates take any construction-related course available to them,” Karl advises. “It doesn’t have to be electrical, alone. Welding or mechanical courses show mechanical ability. It’s helpful if can-
didates know what the tools are in advance.”
Licensed journeypersons can simply drop off their application at the IBEW 773.
The benefits of joining the union are many.
“The total package is great. Our pension is second to none, up to $10.17/ hour employer-driven contributions going into our pension,” says IBEW 773 field representative Joe Logan. “There are members who earn up to $71.71 an hour—journeyperson rate—with wage and benefits combined.”
IBEW 773 follows government-mandated rules, which dictate that firstyear apprentices earn forty percent of what a journeyperson earns. A second-year apprentice earns fifty percent. Third-year apprentice earns sixty percent, and a fourth-year apprentice earns eighty percent of a journey person’s wage.
More than wages, alone, the IBEW 773 looks out for members’ rights.
“It’s an unfortunate reality,” Joe continues, “but there are unscrupulous contractors who take advantage of workers. We negotiate collective agreements to ensure people are treated properly and paid what they are worth.”
The training workers receive at IBEW 773 is also second to none.
“Our people go through four years of mandatory night school where we train them for what they’re going to learn at trade school,” Karl explains. “And then they go to St. Clair College, for instance, to learn their trade.”
That’s right—the reason IBEW 773 members are so sought after and well-regarded is because they receive twice as much training as the government mandates: four years of IBEW 773 night school and then the government-certified school where they learn the trade.
“We want them to have that extra training,” Karl says.
Among other training the IBEW 773 offers: a communication course on telephone, fibre optic, internet lines, residential section, control wiring (electrical control, wiring through relays, control circuits, photo eyes, solenoids) courses about controlling electricity.
“We need hundreds of electricians at the NextStar Energy battery factory and at the new Gordie Howe International Bridge,” Karl says. “We also need them at the mega hospitals—approximately three hundred electricians for the duration of the hospital project. We’re looking for people for the future.”
That is where Joe Logan comes into the picture. As a field representative for IBEW 773, he oversees member recruitment.
“When we take in our apprentices in March,” Joe explains, “they go through a full week of training—construction-related—before working on a tool. That includes working at heights, workplace Hazardous Materials Information System (WHMIS), arc flash training, high
voltage splicing, aerial platform, hoisting and rigging.”
He continues: “Anyone who comes in is looking for longevity in their career. I’m the membership recruitment/regional organizer. This is the last time you’ll ever have to fill out an application or submit a resume when you join IBEW 773.”
It’s an experience so many people have in this economy: when they receive notice they are being laid off from their job, it’s up to them to pound the pavement and find the next job. It doesn’t work like that for IBEW 773 members.
“With IBEW 773, you come back into the union hall and we send you out to the next contractor who needs a person with those skills,” Joe says. “We negotiate provincially. Conditions don’t change from employer to employer. Wages and pension package stay the same within Ontario. The Electrical Contractors Association of Ontario (ECAO) and IBEW negotiate collectively. We secure the fairest deal because we work as partners. It’s not a combative relationship. Our members work for the contractors, so the contractors are our partners.”
Not only do people apply at the IBEW 773 to do their apprenticeships, the IBEW 773’s door is always open to people who are interested in joining the union and/or seeking to unionize their workplace.
“When I meet with people, especially a new journeyperson who is not in the union, often they’re working for an electrical contractor with whom they did their whole apprenticeship,” Joe explains. “The electrical worker feels loyal to them, and many times they don’t realize they are being underpaid. Sometimes they feel under-appreciated, so they come to see me. I just offer them information about IBEW 773: about what they could be paid if they joined the union. Meetings with me are one hundred percent confidential. At the end of the day, they choose
what they do with that information.” He adds: “I’ll meet with anyone any day of the week.”
The fact is, employees in Ontario and in Canada have the right to form a union. Employers are supposed to stand by, unbiased, neither encouraging nor discouraging. Many people don’t realize that’s how it’s supposed to work. And sometimes they’re right. Sometimes employees who are interested in unionizing a workplace suffer repercussions, they are disciplined or otherwise punished for their actions.
“And that’s illegal,” Joe says. “If an employee exercising their rights under the Labour Relations Act suffers repercussions, IBEW 773 covers the lawyers, and the lawyers handle the litigation.”
And when the IBEW 773 speaks, people listen. Recently Opposition Leader Pierre Poilievre was in Karl’s office along with all of Windsor’s construction building trade leaders. The union was doing what it does: looking out for workers.
“We asked Pierre Poilievre, if he becomes Prime Minister of Canada, what is he going to do for Windsor? What is he going to do to support the unions and trades in this city?”
Not only does the IBEW 773 look after its members, it’s involved with initiatives that make our community stronger, such as wiring homes built by Habitat For Humanity.
“During the pandemic,” Karl says, “we partnered with Filip Rocca and Darcy King at Mezzo Ristorante & Lounge to feed our nurses and hospital staff. We did six thousand meals.”
The members and leadership of the IBEW 773 take the idea of “brotherhood” to heart. Safe, well-paid workers lead to strong, stable communities. We’re all in this together.
Karl Lovett is proud to be hosting our 105-year Anniversary of Local 773 Gala at Caesars Windsor on June 24th. W.E.
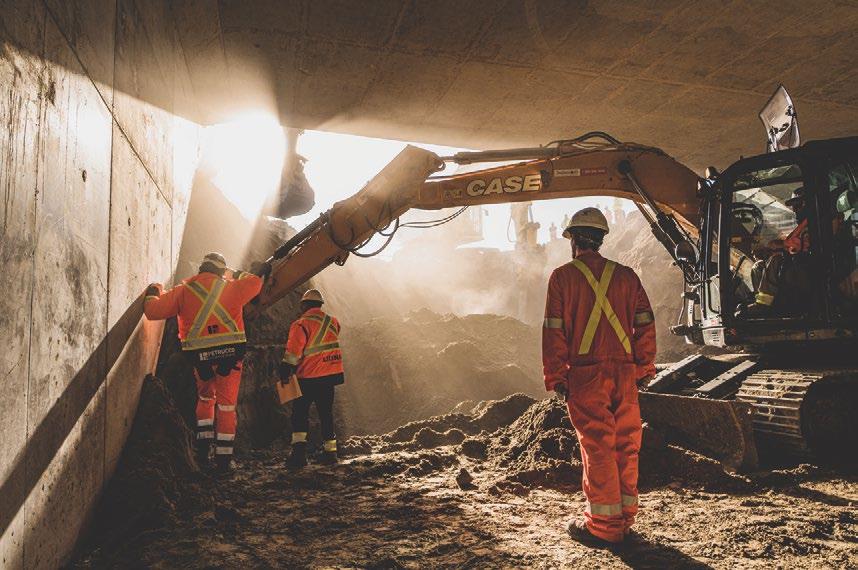
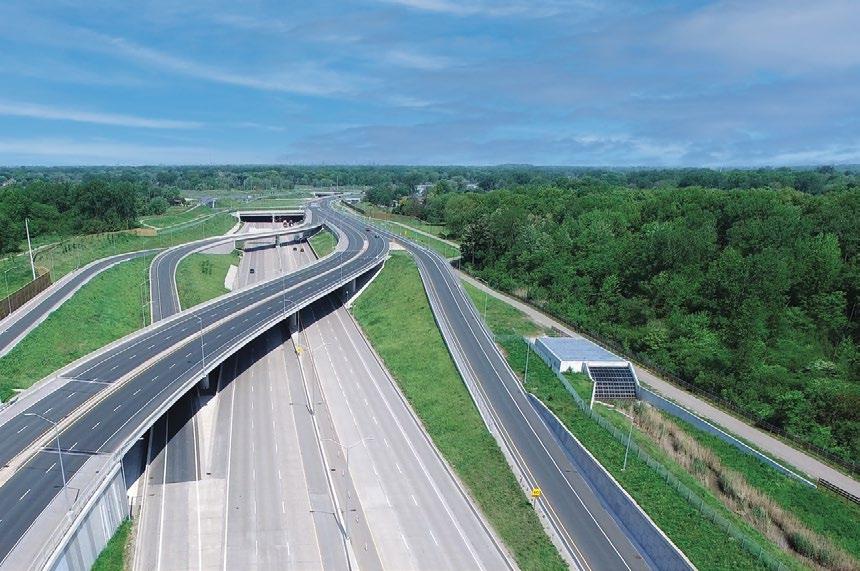
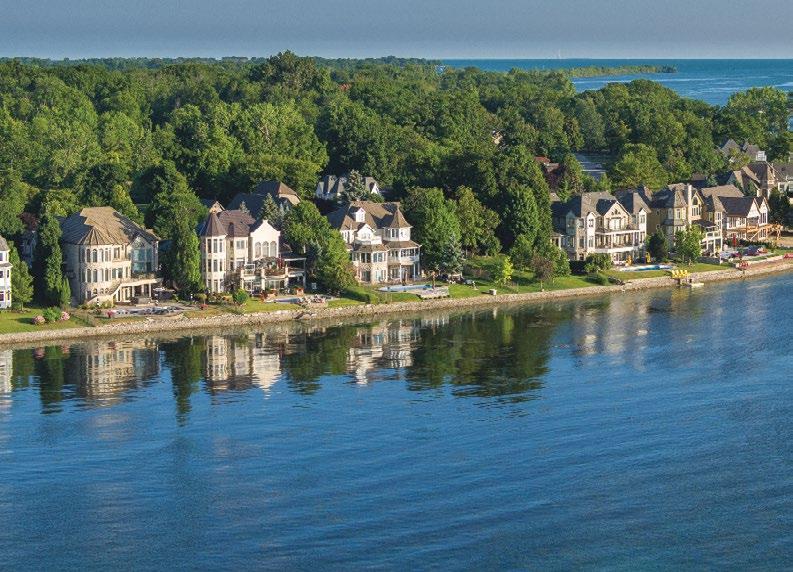
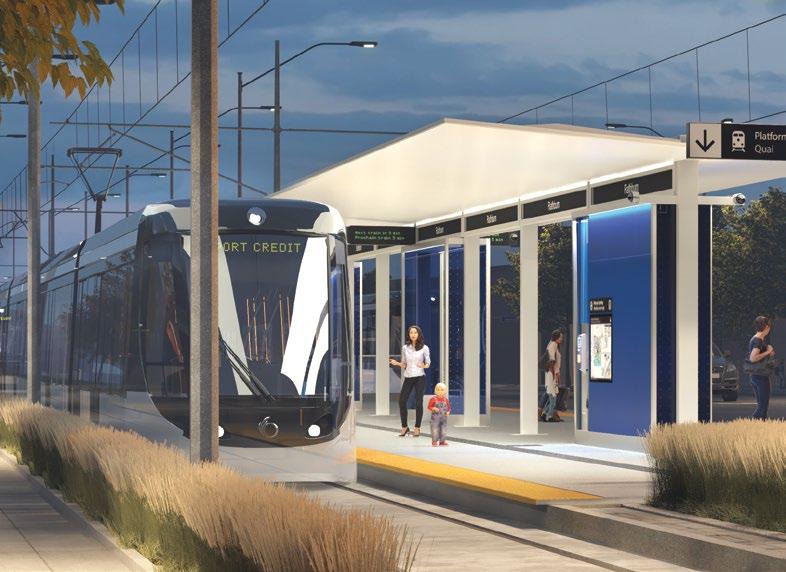
Strong
BUILDS
When we speak of Adaptive Synergies, we celebrate the extraordinary potential of our corporate diversity. Having in-house expertise across so many construction disciplines allows us to be more flexible, more responsive and more

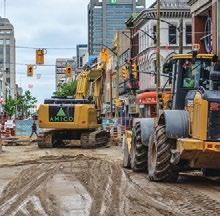
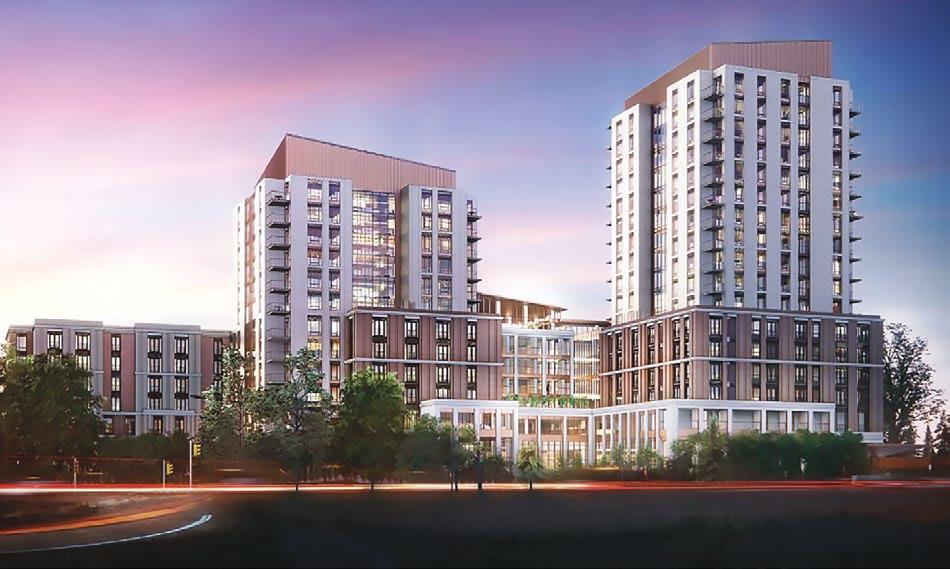
innovative. This highly productive structure is a key reason why we have been entrusted with so many of Ontario’s largest and most challenging undertakings. At Amico, the whole is greater than the sum of its parts.
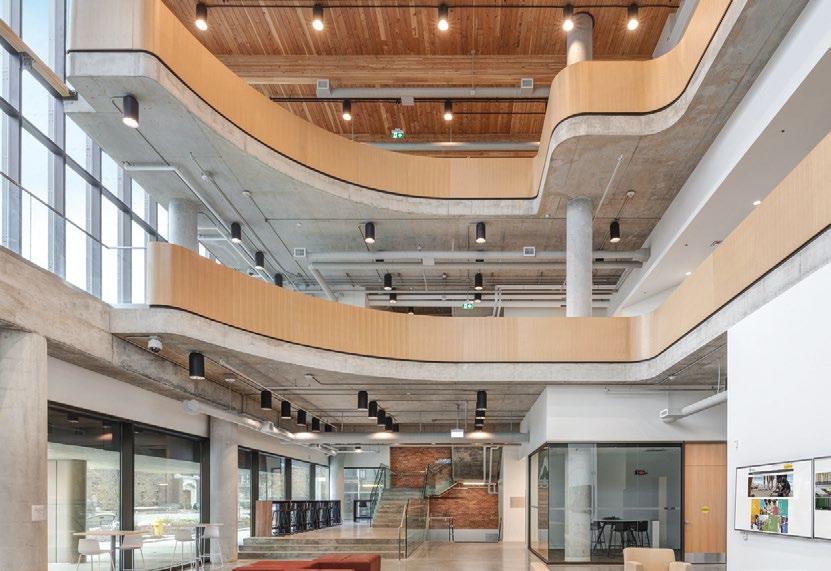
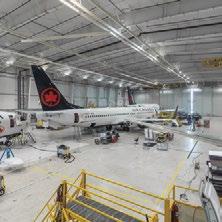
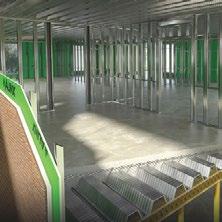
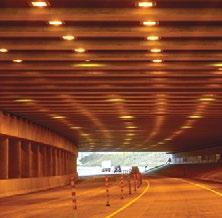

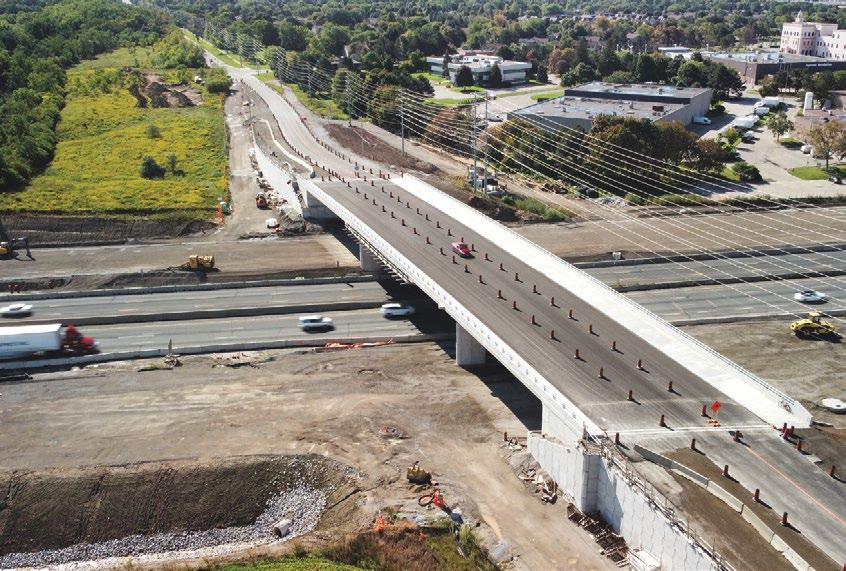
AMICO & ITS AFFILIATES BRING EXPERTISE ACROSS A WIDE VARIETY OF DISCIPLINES

Molding the Future of Industry with OYAP
There are great things happening in the Manufacturing room at North Star High School in Amherstburg.
and machining working on an Integrity component.”
By Matthew St. AmandA recent event showcased equipment provided to the school by Oldcastle’s tool and mold outfit, Integrity, the Canadian Tooling & Machining Association (CTMA), and investment by the Greater Essex County District School Board (GECDSB). It is all part of the Ontario Youth Apprentice Program (OYAP), that gives students an opportunity to explore and work in apprenticeship occupations through the Cooperative Education program. It also affords them the chance to become registered apprentices and work towards becoming certified journeypersons in a skilled trade while completing their secondary school diplomas.
North Star tech teacher, Glen Holden, conducted the tour of the Manufacturing room.
“A VF1 donated by Integrity, which is a computer numerical control (CNC) machine used for precision machining,” Glen explains. “It’s a three-axis, great quality machine… students are able to learn the basics of CNC programming
A series of Rousseau tool cabinets and toolboxes were also donated by Integrity, as well as two new milling machines and two new lathes.
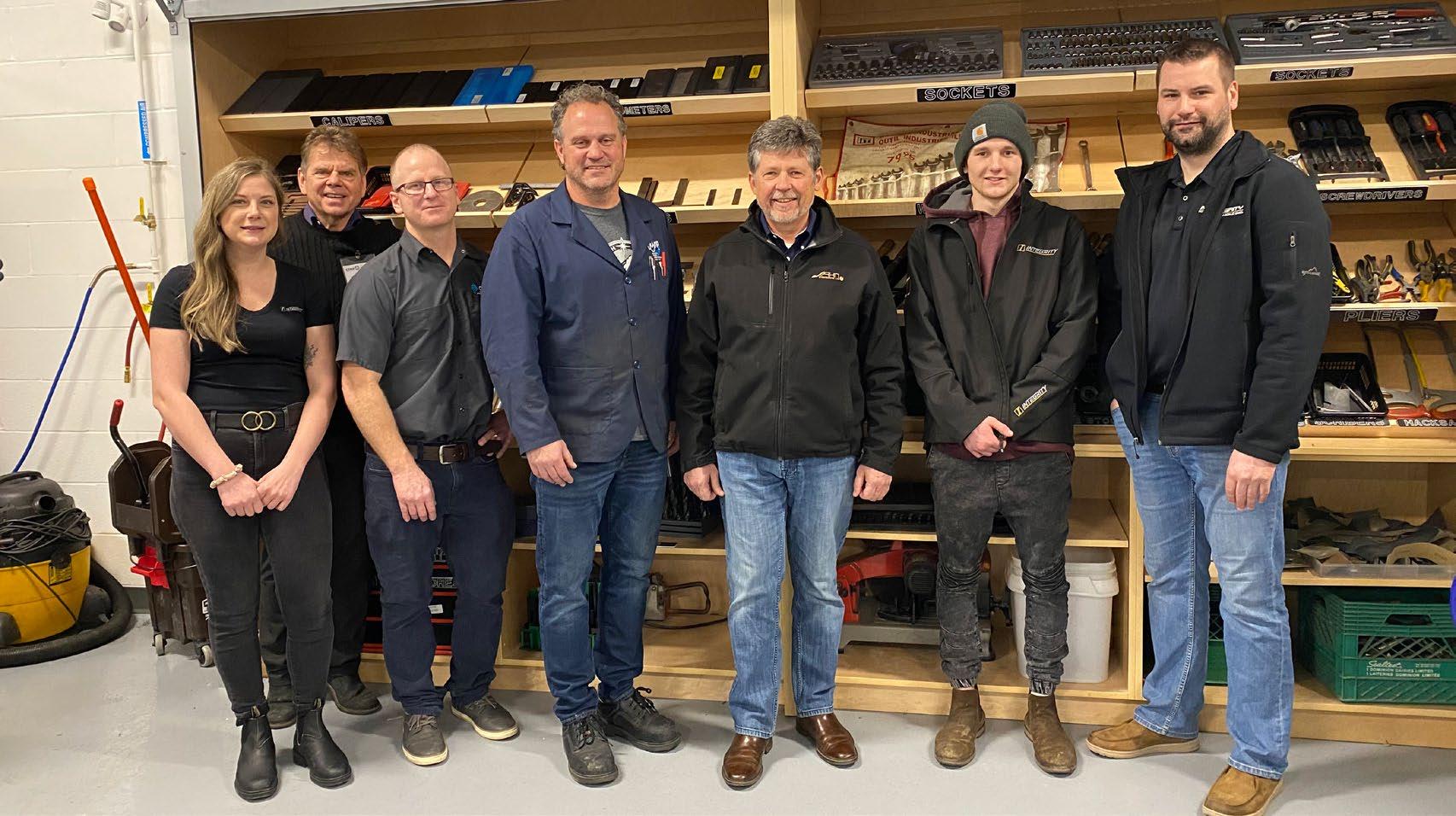
He moves onto another large machine and explains: “The TMI 1, through the original CTMA grant—it’s a $60,000, $70,000 dollar U.S. machine— three axis, great for training students in coding and basic CNC.”
The second part of the CTMA grant brought two desktop machines that students use for cutting and engraving metal and acrylic.
The third installment of the CTMA grant purchased carbide cutters used in the CNC machines, as well as two enormous new cabinets filled with tools: calipers, micrometers and a variety of hand tools. The GECDSB funded the acquisition of four remaining milling machines, four lathes, and a Lincoln Electric CNC plasma table.
“We’re lucky here,” Glen says, “basically all brand-new equipment, tooling
Industry and professional associations partner with Amherstburg’s North Star High School to train young people for the jobs of the future.Photos by Justin St. Pierre
and cutters to help train students for, potentially, a future in the trades. This is probably the best equipped manufacturing shop in the province at the high school level.”
These big dollar donations and grants were made for one reason: there is tremendous need in industry for new skilled workers to fill vacancies created by those moving into retirement. OYAP has played an integral role in preparing young people with skills that will provide them work for life. Industry embraces them.
“OYAP students are important to Integrity because they are our future team members,” says Lindsay Ken-
nedy, Human Resources Generalist with Integrity, “so there is no better way to learn our processes, the trade, the industry than by working and learning on the job. We really value the OYAP program.”
Lindsay goes on to say that one of the most valuable qualities a team member can bring with them to Integrity is a willingness to learn.
Louis Jahn, Vice President of the CTMA, commented: “Our involvement is to get people interested in the trades, especially the machining trades. So we have done something that’s completely unprecedented—we secured $5 million in funding and we’re going to high
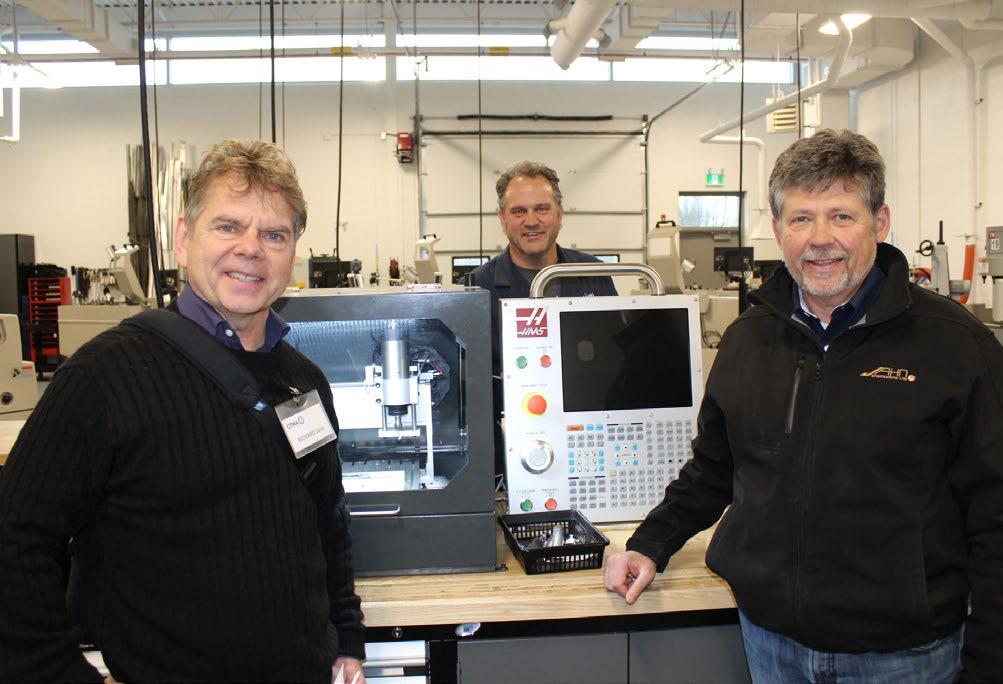
schools all over Ontario. We’re putting equipment into their shops so students have a good baseline when they enter the workforce.”
North Star student Evan Buratto has been involved with OYAP for two years and is working/training at Integrity. What drew him to the program?
“I was interested in something more hands-on, getting out of the school environment and trying something different and making money at the same time. I love it at Integrity, there are a lot of friendly people there. I like the work I do in the pre-inspection assembly mold group.”
OYAP students are also part of the Specialist High Skills Major (SHSM) program where they receive sector-related training, such as Forklift Operation and Working at Heights. SHSM students from all sectors receive First Aid and CPR certification which ensures they are an asset in the workplace from the moment they step through the door.
The training students receive goes beyond the job skills. Rod Levesque, Co-Op teacher at North Star explains: “The students come back to the school a few times a year for Integration Days. During those days, I bring in a financial planner because the students will make, by the end of the year, about $30,000. We encourage them to be sensible with their money, show them some scenarios—‘If you put away even $50 a week starting when you’re sixteen, you’ll eventually have this much.’ With money comes responsibility.”
The OYAP and SHSM programs have opened the door to good jobs for thousands of students. More information about it can be found at oyap.ca and ontario.ca/shsm. GECDSB students from all secondary schools are encouraged to contact their guidance counsellors for more information. Employers who are looking for Co-Op students in the Manufacturing sector, or beyond, can reach out to Jason Lepain jason.lepain@publicboard.ca or Justin St. Pierre justin.stpierre@publicboard.ca. W.E.

Sylvan Canada Ltd.
Quietly Walking the Walk
Donella H. Meadows once said: “As I travel on the path toward sustainability, I keep thinking of a motto I once heard: ‘Change is not sacrifice. It is learning, staying awake, being alive, moving to new places. It requires every part of us, our irrational minds and our loving spirits.’”
installing material handling systems throughout the automotive industry.

Originating in 1956 as a local residential plumbing company in Michigan, Sylvan has evolved into a leading multitrade services and solutions provider for Fortune-100 and government clients throughout North America. Sylvan Canada launched in 2009 under the leadership of CEO Robert Metz and President Sean Maine. Sylvan has expanded exponentially over the past fourteen years, doing approximately a billion dollars worth of work in that time. In 2021, Sylvan added a key strategic piece to the puzzle: a state-of-the-art Conveyor Division; designing, manufacturing and
“We recognized a gap in the marketplace for custom conveyor solutions,” explains Sean Maine. “Taking ownership of this key aspect of the process further cements our leadership position in the space.”
Sylvan will be providing all the conveyor solutions for the retool of the Windsor Assembly plant this fall.
Unlike other conveyor companies, Sylvan has its own installation company that performs all mechanical rigging and piping, (including wiring, in Canada) as Sylvan Vice President, Ernie Pandolfi, outlines.
Company-wide services include pipe and sheet metal fabrication and installation, CAD/BIM, service installation/ repair, turbine installation/mainte-
If this multi-trade service provider isn’t on your radar—it should be.
nance, millwright and rigging, electrical, general contracting, and complete turnkey conveyor systems. From engineering and design to project/program execution, Sylvan delivers comprehensive project management capabilities, built upon their vast experience, solid labor and industry relationships, and unbeatable record for safety. The scope of their services and complexity of their projects may have grown dramatically over the decades, but Sylvan’s success remains rooted in the fundamental principles of providing superior customer service and flawless delivery of work.
With an unmatched reputation for reliability, Sylvan is often found at the center of game-changing projects throughout North America.
“Just look at the NextStar lithium-ion battery plant being built on the Twin Oaks site,” Sean says. “It’s the largest private-sector investment in Ontario history and Sylvan has been brought on to perform all the low voltage electrical installations on the cell production facility, which will be nearly four million square feet in size.”
More than 200 acres of land has been cleared, 195,000 cubic metres of topsoil has been stripped and stockpiled, and 150,000 cubic metres of clay has been applied on-site. The campus has 10 structures totalling approx. 4.5 million square-feet, and Sylvan Canada plays a pivotal role in supporting the design, build and project optimization.
“Sylvan was picked to be a strategic partner on the battery plant from its inception,” Sean continues. “We are proud to serve along side the absolute best in the business on this incredibly important project. We look forward to leveraging our exceptional workmanship and stellar safety record on the new product launch at the Stellantis Windsor assembly plant. Since our inception, Sylvan has been part of more than fifteen product launches.”
In 2021, as the Detroit Assembly Complex – Jefferson North prepared to integrate the all new Jeep Grand Cherokee
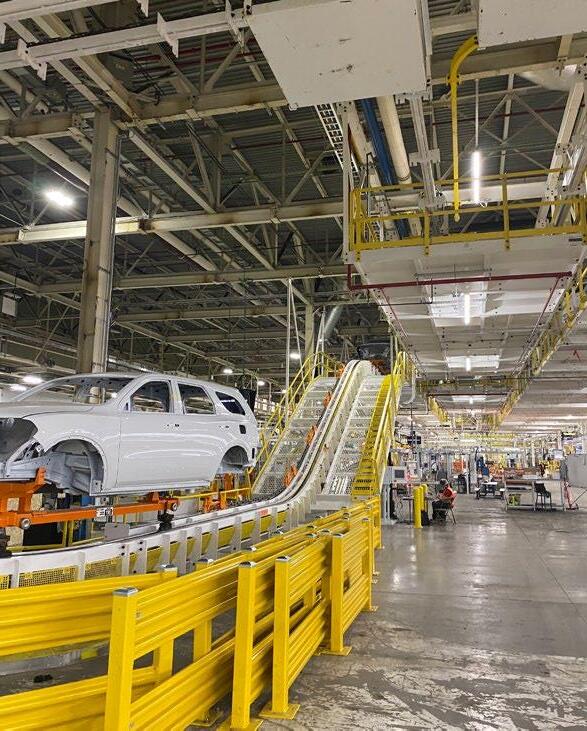
into existing production, Sylvan was brought in to design, build, and install pre-trim, chassis, engine, and final line conveyor systems necessary to handle the new and existing product. As the prime contractor, overseeing well over 200 workers and contractors, this required well-coordinated demolition of existing equipment, new concrete, wiring, piping, HVAC, fire protection, controls, and installation of new Sylvan-provided material and conveyors.
In support of its 2020 Explorer Program, Ford Motor Company required extensive facility renovations at its Chicago Assembly Plant. The challenge was to install nearly 2,000 feet of precision-welded stainless steel piping for a new Freon system. The complex piping infrastructure extended throughout the plant, including many areas that needed to remain fully operational throughout the project execution period.
With the support of over 150 skilled tradespeople, Sylvan met or exceeded all project milestones. Following the July 2018 production shutdown, Sylvan planned for the even more challenging task of completing this current contract in the Trim Shop, as well as two additional contracts in the Trim Shop and a large piping project in the Body Shop. These projects were scheduled during a four-week window in March 2019. Over 30,000 pipefitter hours were expended with no lost time to injuries.

Taking on such complex and demanding projects, “Sylvan is an employer of destination,” says Sylvan Project Executive, Eric Farron. “We want top people applying. We build things the right way with the right people. Sylvan takes its culture very seriously. We believe in having highly engaged and enthusiastic teammates, supporting each other, and caring for customers. Continuing education is also a very important element to staying at the forefront.”
This culture of caring is manifested in Sylvan’s commitment to safety. It has established the Sylvan Safety Committee to ensure that all employees are empowered to identify ways to eliminate
or mitigate potential hazards. Sylvan accomplishes this through workplace training, awareness campaigns, experience/knowledge sharing, companywide standards, and incentive programs.
Rapid, unrelenting growth, an undying passion for safety, and an unparalleled record for reliability and innovation, Sylvan checks all the boxes for success. The most remarkable thing about Sylvan is that, with its stellar track record, more people haven’t heard of them.
“We go about our work quietly,” Sean says. “Our continued growth is a testament to our strong partnerships and commitment to execution.” W.E.
The Miracle at Twin Oaks Drive
Canada’s first lithium-ion battery plant is being constructed before all our eyes—at a pace that’s difficult to believe.
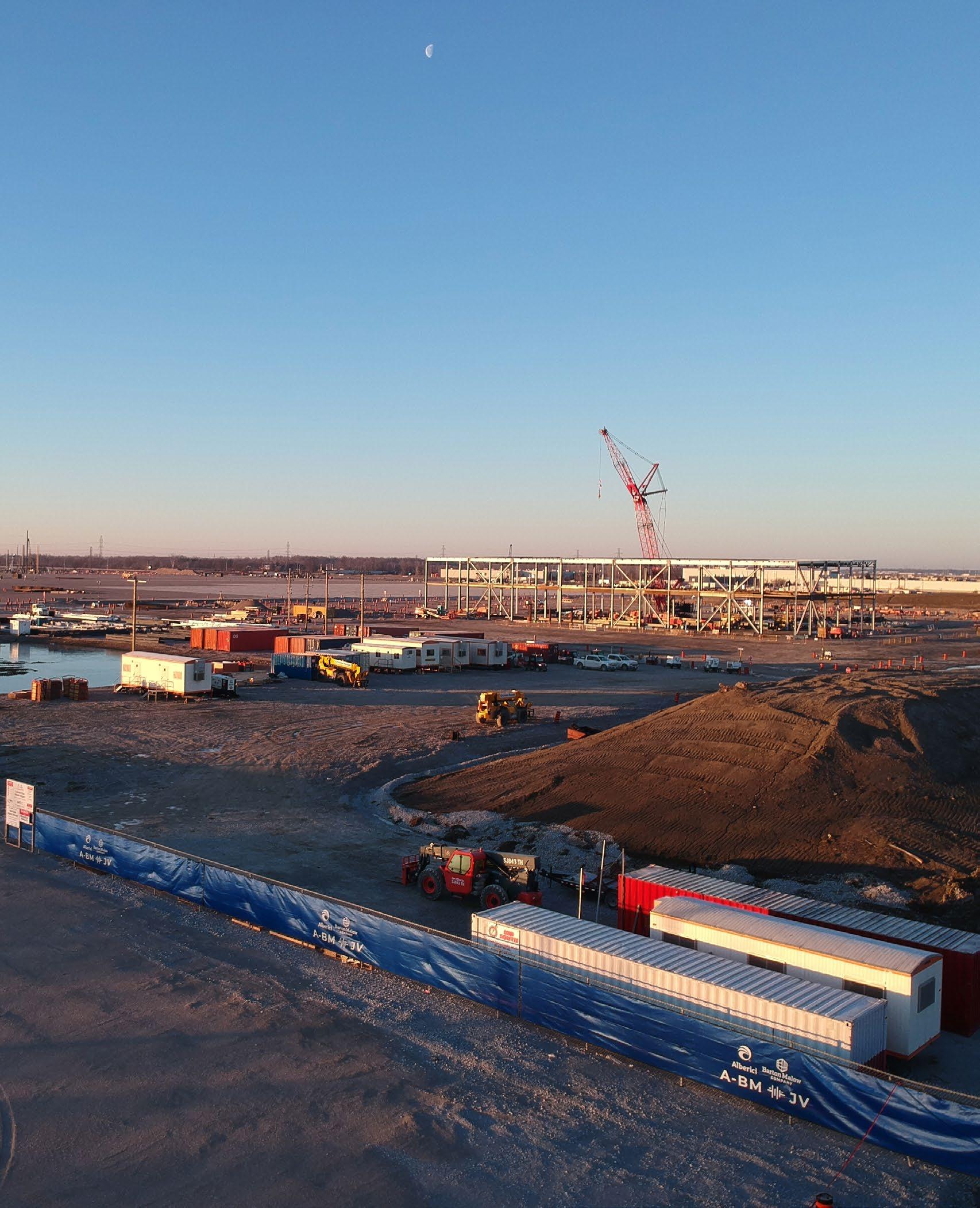
The NextStar lithium-ion battery manufacturing plant on Twin Oaks Drive is the largest private-sector investment in Ontario history. The construction work going on at the site is moving at a breathtaking pace. Most Essex County residents know about the battery plant, but one thing they may not know is that the NextStar Energy team is now here, in Windsor.
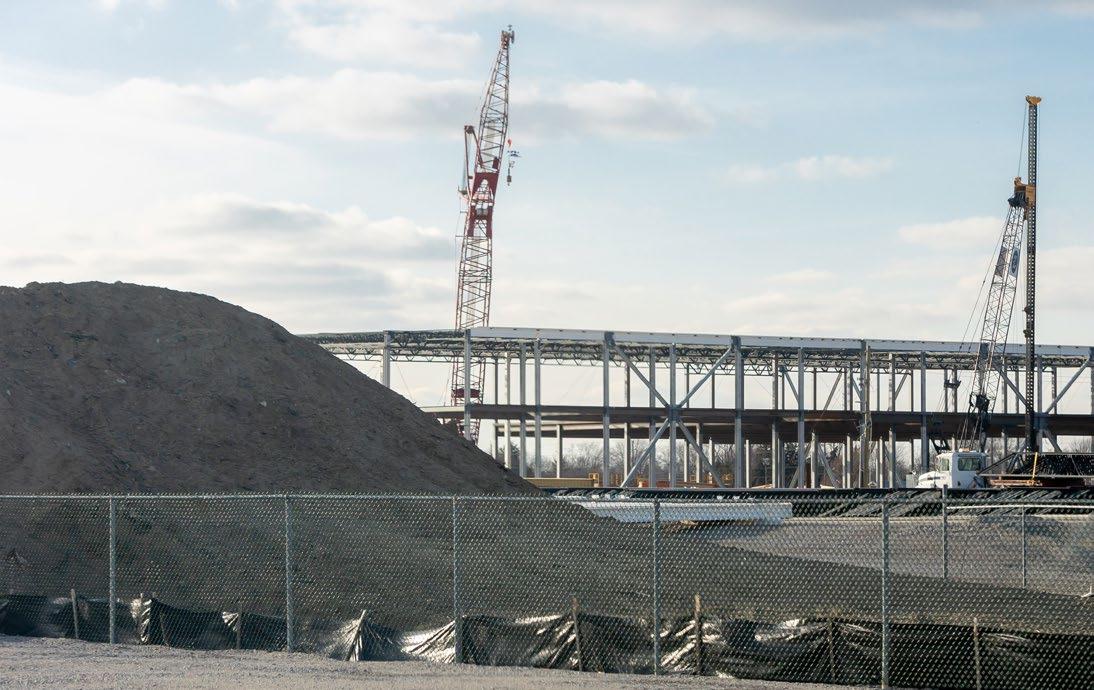
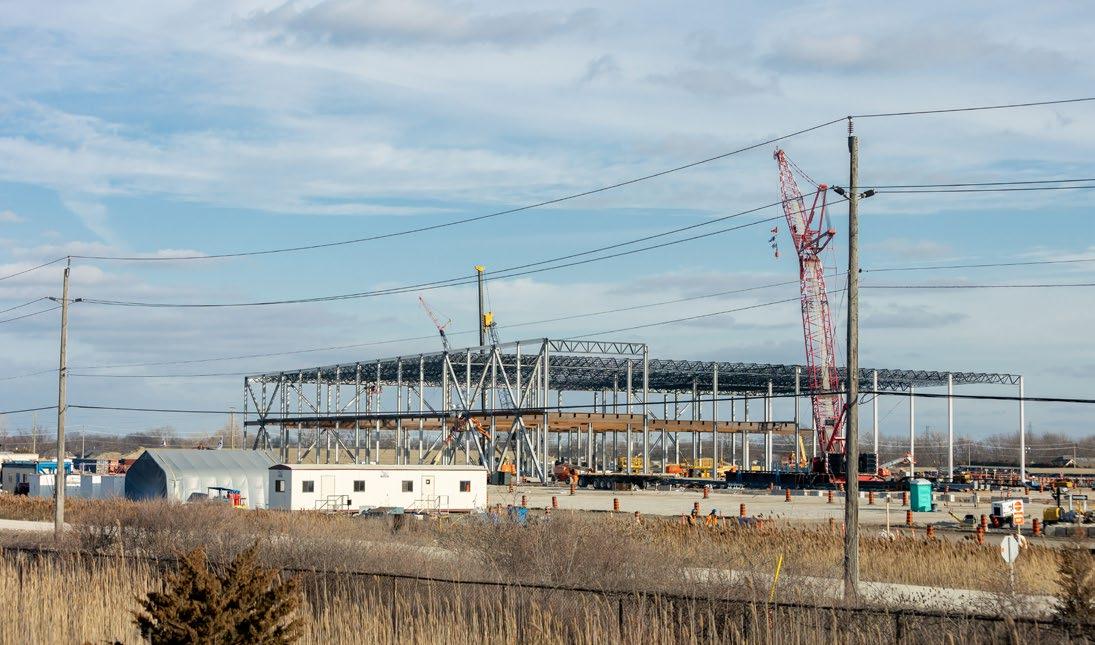
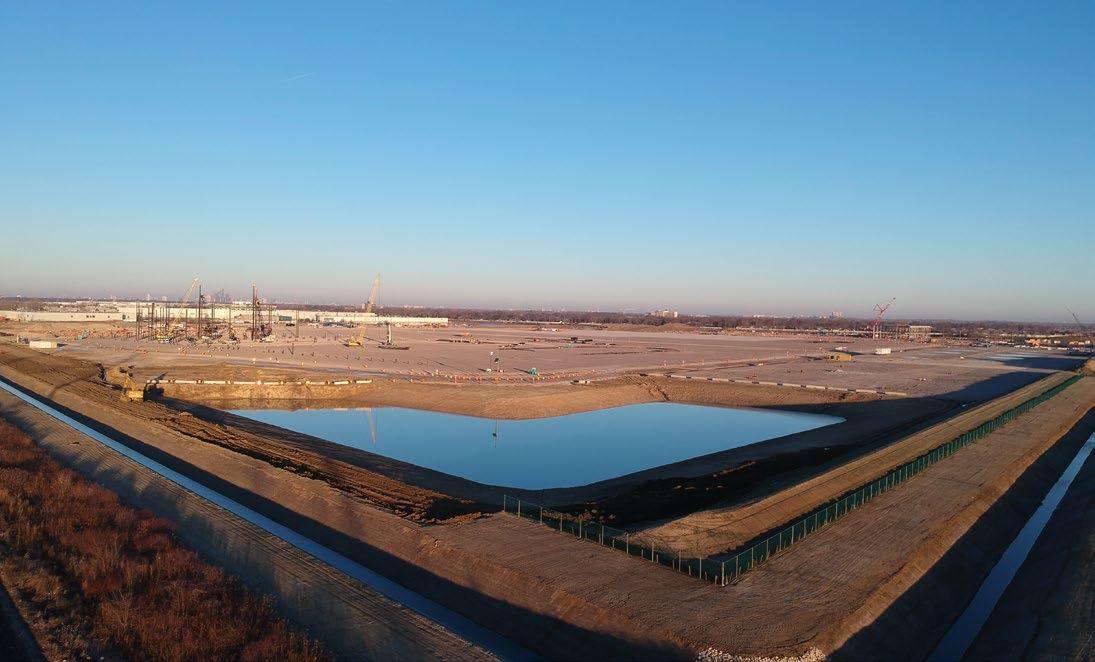
Those were the words of Sung Park, Planning Director of NextStar Energy, who took some time to speak to W.E. Manufacture Magazine on behalf of NextStar CEO, Danies Lee.
“I have been involved with this project since 2021,” Sung explains. “At that time, we were looking for the best site in North America to establish this lithium-ion battery plant. The southern United States had many different options. We wondered ‘Why don’t we include Canada, too?’ Once we began looking into Canada, we saw advantages over the United States.”
Among these advantages were support from all levels of government: municipal, provincial, and federal.
“Compared to United States, we found the best support here,” Sung continues, “in the form of incentives, infrastructure support, the Minister’s Zoning Orders (MZOs), which shortened the approval process. The city government provided us with a very good site at a very competitive price. The federal and provincial governments also provided many incentives.”
The NextStar site search group was also impressed by Windsor’s physical location, situated right next to Detroit.
“Windsor is the capital of automotive manufacturing in Canada,” Sung says. “We were looking for a place where the auto industry is strong. In the battery manufacturing industry, we need help from the auto industry.”
Sung continues: “As we looked deeper at Windsor as a possible site, we saw that the Canadian workforce is as strong as the American workforce, and
Canada was very competitive wage-wise. In Windsor, we will be hiring thousands of people. Everywhere we searched up to that time—in Ohio, Michigan—we knew we needed the right people, but there was not enough of them in those locations. In Windsor, we have very strong automotive engineers and operators. Also, the unemployment rate is higher in Windsor than elsewhere, which, for us, is good because we can hire more people than elsewhere.”
Regarding progress on the construction occurring at the battery plant site, Sung revealed the following: “The lithium-ion batteries are divided into two components: the cell and the module. The cell is the core technology of the batteries. The module is the outer portion around the cell. Our factory is being constructed in two phases. Modular is first, and then the cell.”
The cell buildings will require more time to be constructed than the module portion. To give some kind of scope, the module building will be a little over 300,000 square feet in size. The cell building, which will also serve as the main building will be almost four million square feet. The rest of the space will be taken up with parking for 1,500 employees.
“The module component can be started earlier,” Sung says. “We’re looking at the end of this year, 2023, for the building to be completed and we are planning to begin production in 2024. For the first few months, we will produce sample products. The real stuff will begin production in the middle of 2024. As for the cell component, we are looking at a 2025 completion date.”
What types of businesses does NextStar anticipate coming to this area once the battery plant is completed?
“Similar to the automotive industry, once the battery plant is completed and beginning production, a great many suppliers will come and support the plant,” Sung says. “The battery plant is huge. It needs hundreds of suppliers from Asia. The EV battery segment is
strong in Asia. That is where most of our suppliers are located right now. What we’re trying to do is, eventually, get those suppliers to come to Canada and be near the facility. It will be good for them and good for us. We are inviting more suppliers to the Windsor area. There is already one Korean module component supplier, near the airport. Similar to that, we will eventually get more.”
This is a reference to the Dongshin Motech facility, which has signed a lease agreement with the City of Windsor for a twelve-acre parcel of land off Wheelton Drive near the Windsor Airport. This is part of a $60-million investment, which may grow to as much as $90-million, creating 300 new jobs. The Dongshin Motech plant will manufacture battery casings for the lithium-ion batteries that will be produced at the NextStar battery plant.
“While they are being lured through the tremendous investment that [NextStar Energy] are making across town,” Windsor mayor, Drew Dilkens was quoted as saying in local media, “I know they have already started the process of securing additional investment and potential clients to expand their operations.”
Dongshin Motech already has a supply plant right next to LG Energy Solutions (one half of the joint venture that created NextStar Energy) battery plant in Poland. Choon Woo Lim, Chief Executive Officer of DongShin Motech Ltd., says that ever since the company’s experience in Poland, they have sought to continue their strong relationship with LG Energy Solutions and they wanted to continue that relationship in Windsor. He also noted the significant support they have received from the City of Windsor as one of the reasons for selecting this region for the company’s first North American facility.
Dongshin Motech is hopeful about completing construction of the Windsor factory by September 2023 with a goal of supplying battery cell casings to NextStar Energy by May or June of 2024.
So, what kind of technical skills will be in demand at the NextStar battery plant?
“Battery production is part of the automotive industry and requires mechanical engineers and operators,” says Sung. “The battery also involves chemical production, so chemical engineers will be needed. Our first priority is getting as many automotive engineers and operators as possible. On the chemical engineering side, we are working with local schools—St. Clair College and the University of Windsor—to incorporate the program that will foster the workforce.”
NextStar Energy is expected to directly employ an estimated 2,500 workers, locally.
CEO of Invest Windsor-Essex, Stephen MacKenzie, affirms much of what Sung says.
“One of the reasons our region was selected, we have St. Clair College and University of Windsor that will provide the education and training for potential employees,” Stephen explains. “This is a different automotive industry—the green industries—which involves a certain amount of transition to occur. But at the heart of it, there will still be manufacturing components, engineers, technicians, operators.”
Stephen continues: “We’ve been a leader in automotive manufacturing since 1904 when Henry Ford put his first factory here. We were the first plant of its kind outside of the United States. We’ve now turned toward the green industries. Windsor-Essex is constantly evolving. We’re now getting into EV. Securing this investment, and the follow-up investment, ensures our place, our status, for generations to come.”
All the while, the project between Twin Oaks Drive and Banwell Road continues apace. That is what it looks like when people from different countries, different levels of government, and even different political parties work together. W.E.
PAINTING THE TOWN IS WHAT WE DO!
AP Painting Solutions Ltd has years of experience in our industry. We are professional painters handling large industrial painting and commercial painting projects as well as epoxy floor coating throughout the Windsor Essex and Kent County. Above all, we make great efforts to provide unparalleled service and work with all clients.


We possess the full technical capabilities and skills to repaint, refinish, and restore your building interior & exterior, metal deck ceiling, wall, concrete floor, window & window frame extrusion, cladding, door, awning, column, office building, metal-clad commercial building, hall, warehouse, factory, or plant. Also, your arena, fitness centre, manufacturing facility, underground garage, apartment & condominium building, aluminum panels, galvanized corrugated steel siding, factory-painted finish & coating, storage tank and silo.
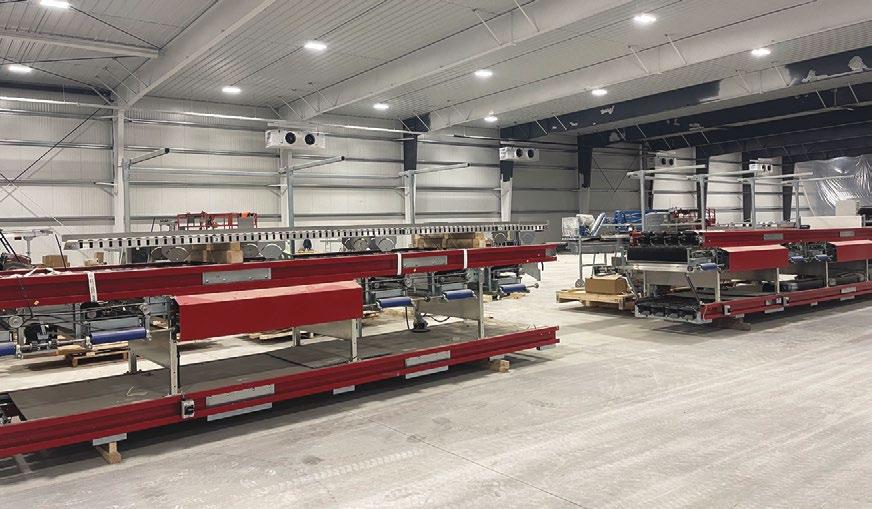
AP Painting uses the best paints and coating systems including the latest-technology oil and latex, dryfall, urethane, polyurethane, enamel and epoxy coatings and paints. Our success is based on our company’s motto: exceptional value, quality workmanship at reasonable rates.
Our paint and coating experts help with your project from initial conception to completed project. Choose us if you are looking for professional painters, the top big commercial painting companies, spray painters, recommended Ontario painting contractors, contract painters. We strive for customer satisfaction. Most importantly, we are bonded and insured, your ultimate protection as it is our priority.
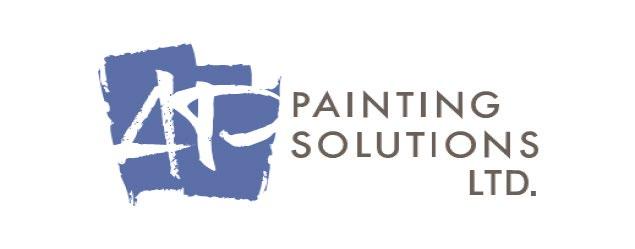
Stronger Together
Family owned and operated Sterling Ridge Group Inc, (the ‘Group”), is a group of eight construction-based companies which together create the synergies necessary to provide full services for construction-based client needs. The creation of the Group was its own project, borne of the vision of owners and brothers J. Randall Koop and Allan J. Koop. Forty plus years later, the Group has assembled a premiere collection of construction companies capable of providing all services necessary for a turnkey project. There was no quick or easy route to achieving success. Hard work, dedication, and excellent employees helped achieve the goal. These are the ingredients to Sterling Ridge Group’s success.
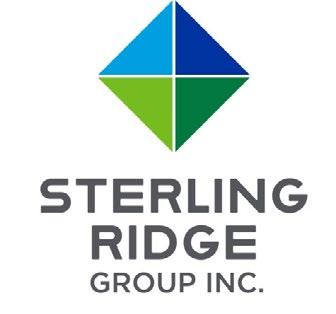
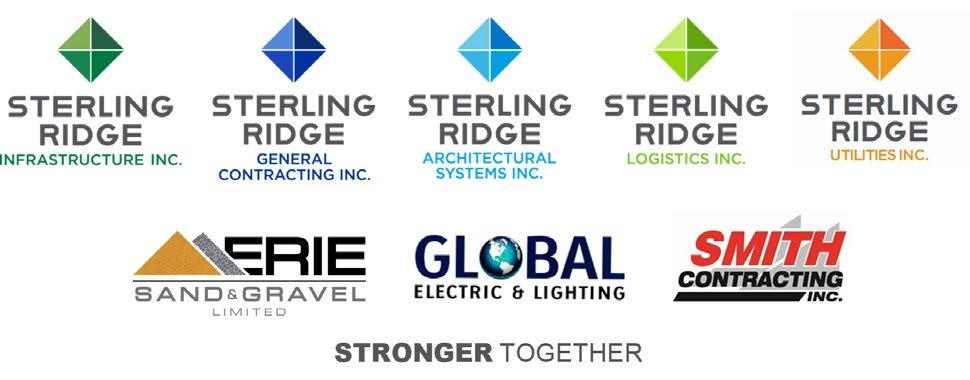
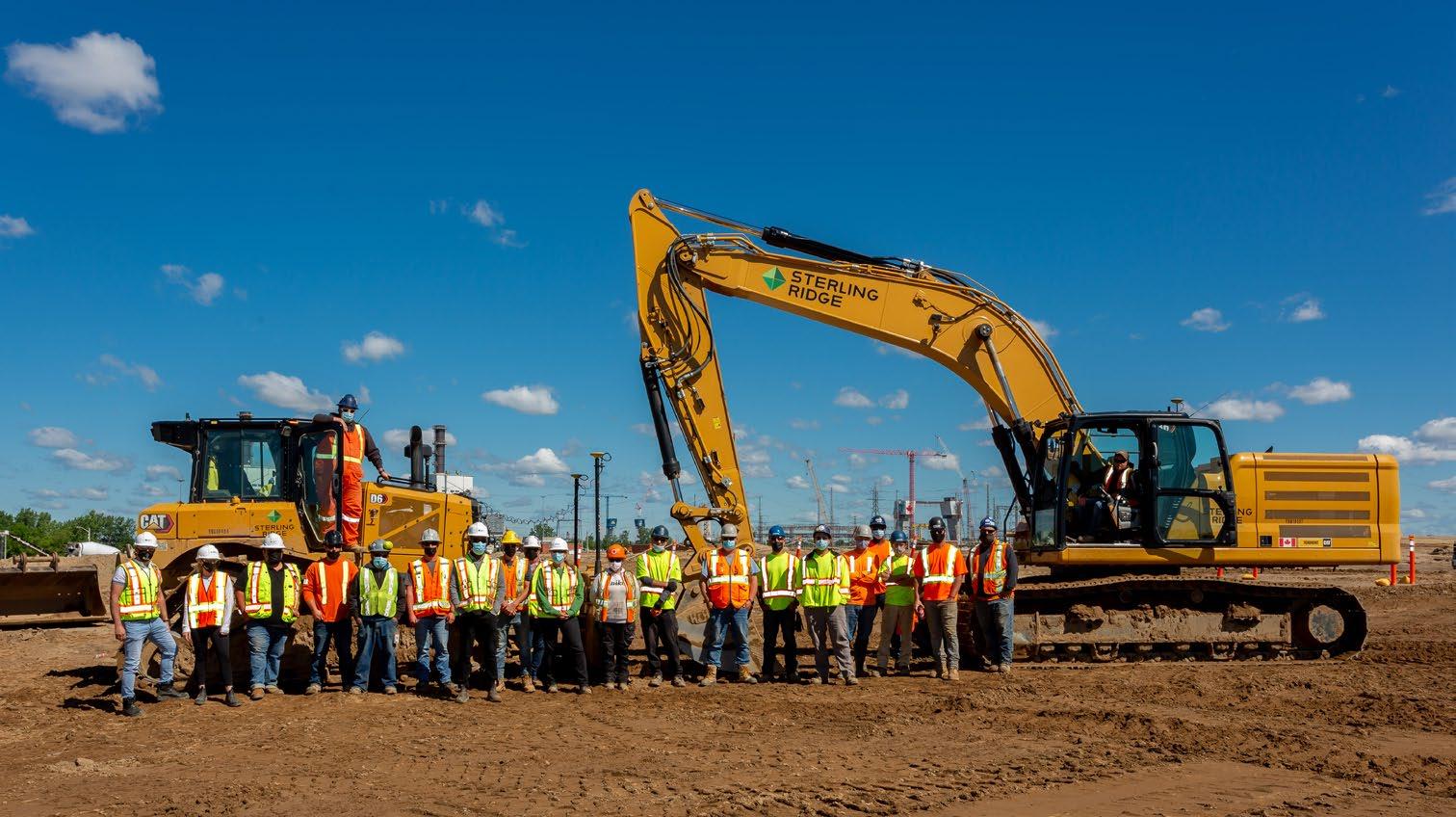
Matthew St. Amand
Photos by Trevor Booth
A Windsor contracting firm understands ‘If you want to go fast, go alone. If you want to go far, go together.’
Independently the companies are strong with solid reputations; when working together, the synergies and efficiencies which exist between them allow the Group to undertake large projects and complete them on time and on budget. It’s no wonder the Group’s motto is “Stronger Together”. “Sterling Ridge General Contracting Inc. (General Contracting), once Loaring Construction, a Division in the Group, has been in business for over seventy-five years,” Matt Soulliere, Vice President of General Contracting explains:
Each company in the Group has tremendous experience in their respective field. Sterling Ridge Infrastructure Inc. (Infrastructure) has experience working on roads and earthworks projects. General Contracting performs ICI work for, amongst other clients, both School Boards and the University of Windsor. Sterling Ridge Group’s Infrastructure -Industrial Division has done work at Hiram Walker and the Big Three Automotive Companies. Their motto is ‘Stronger Together’ because the Divisions work together on Projects which are often large in scope.
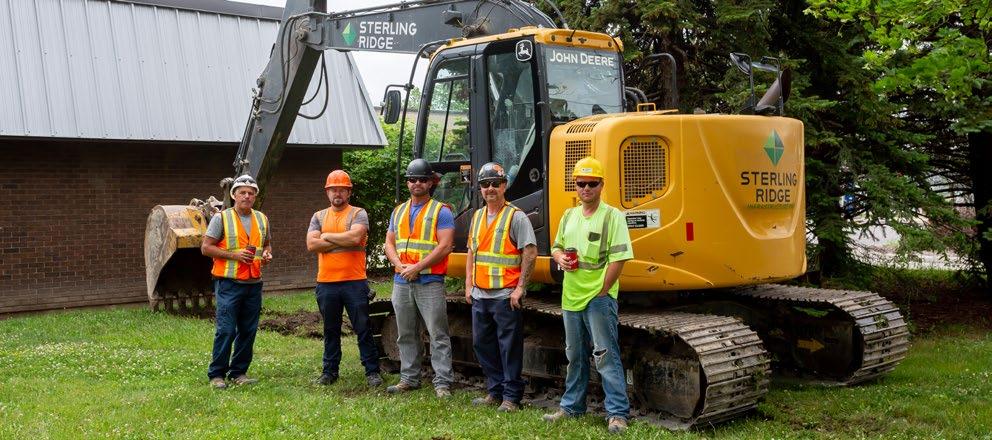
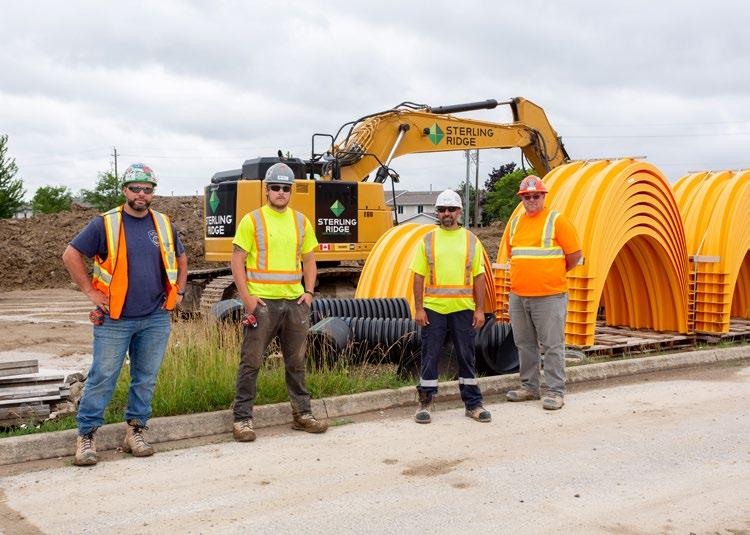
“Other significant Projects the Group has worked on include the Amherst Island Wind Farm near Kingston, and the Gordie Howe International Bridge Port of Entry, where the soil conditions dictated the need to place hundreds of thousands of tons of sand to surcharge the area.” Notable past projects by Sterling Ridge General Contracting and/or Infrastructure include the Herb Gray Parkway, the
new VIA Rail station, Windsor Fire Hall #6 on Provincial Road, and the James L. Dunn French Immersion School, once an old playing card factory.
Work at the NextStar Lithium-Ion Battery Plant construction site on Twin Oaks Drive is a Project that has captured the imagination of Windsor and Essex County. Infrastructure and General Contracting are two of the many contractors on the expansive site, who, together, are creating a 2.1 million square foot manufacturing plant. Currently General Contracting is working on the Footing and Foundation Contract for a Cell Building for the plant. “Sterling Ridge Infrastructure Inc. was the first major subcontractor to be at the Battery Plant Site,” says Matt. “The Lachance drain required locating around the new building structures on the 226-acre site.” He continues, “Sterling Ridge is a key player at the Battery Plant, Three Divisions of the Group are out there doing work: General Contracting is doing the formwork for foundations, and Sterling Ridge Logistics Inc. is providing trucking services in support
of Infrastructure which is completing the excavation and backfill for the foundation work.

Matt acknowledges this is a well-organized and sequenced site. “Footings for the module building will soon be finished,” Matt says. “The structural steel is visible from the expressway now. We’re working alongside other contractors as they drive H piles and helical piles, we follow, excavating around the driven piles. We then place a concrete mud mat to stabilize soil. Prior to starting the foundation formwork, another contractor comes in to cut the pile down to design grade. Other trades follow our work, performing underground services, slab on grade, and building envelope to close the building in. Manpower will increase once a significant portion of the building is erected.” This is a project that Sterling Ridge Group Inc. is proud to be a part of.
For more information about the Sterling Ridge Group visit them online at sterlingridgegroup.com. W.E.
We’re committed to better health for all.
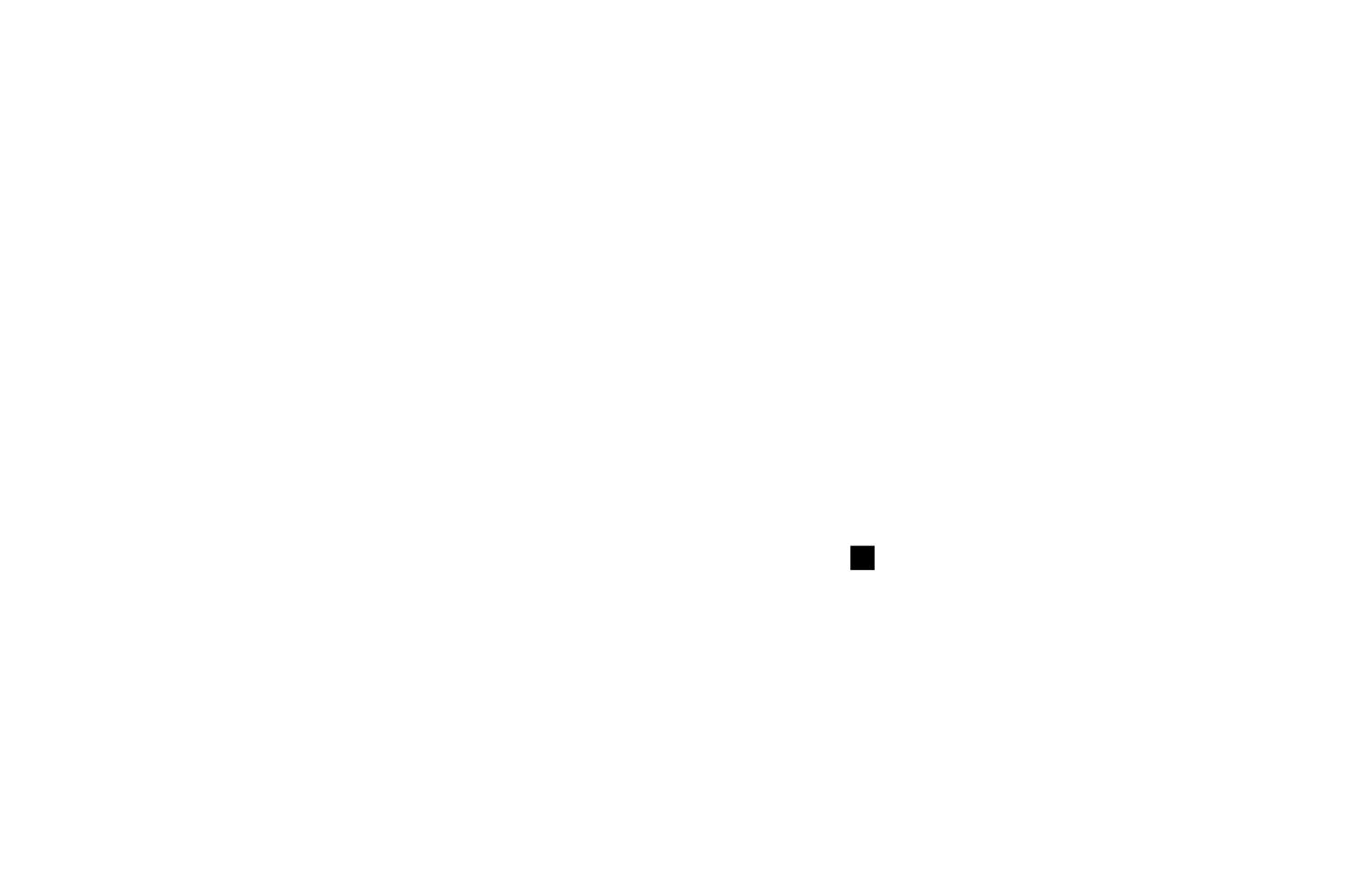
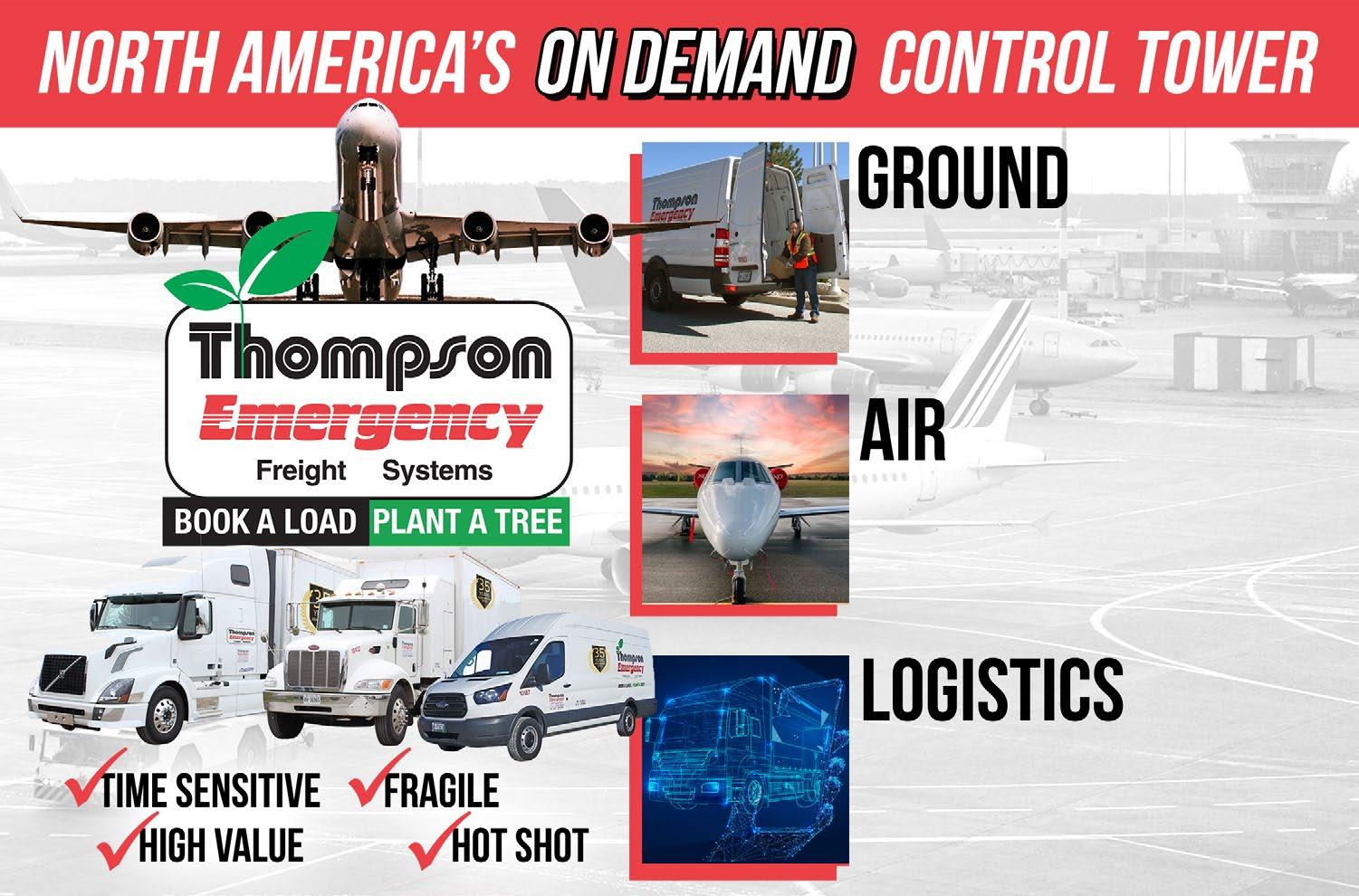
The Windsor/Essex community continues to be at the heart of who we are – thank you for your support.
To learn more about our new model of care, health services, and health insurance & benefits, visit greenshield.ca
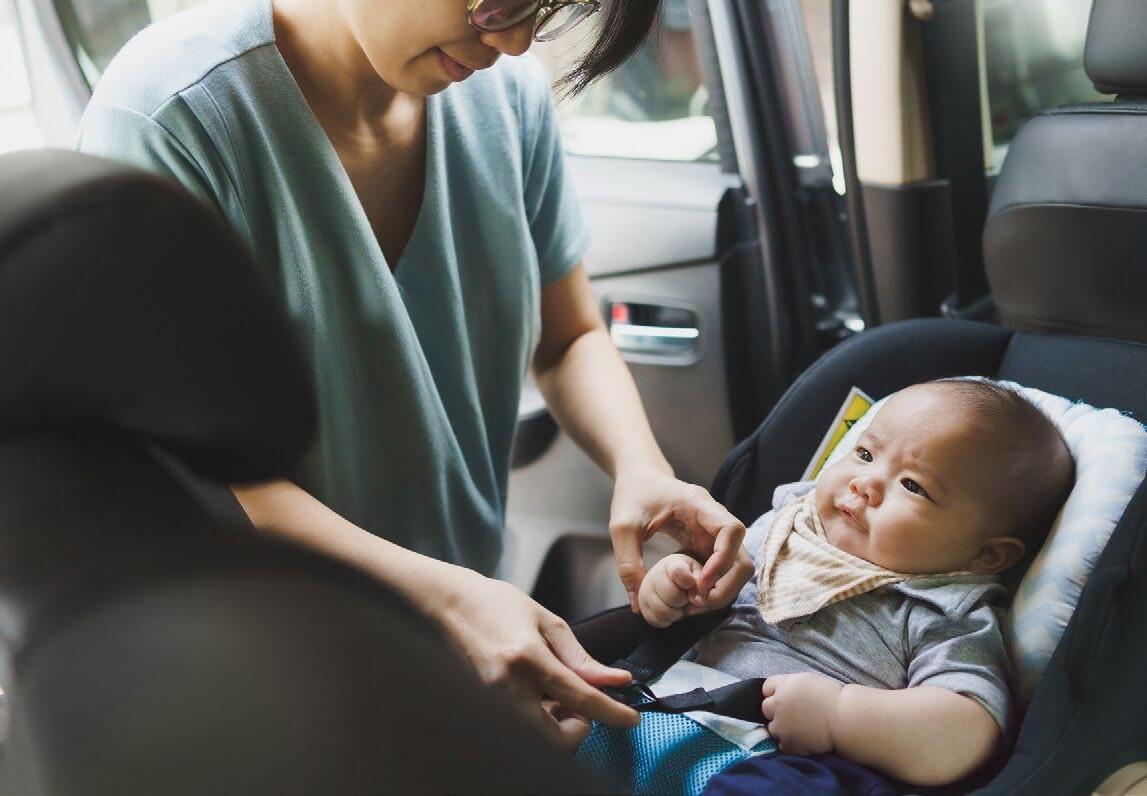
Has a Clear Vision of the Future
By Matthew St. AmandIt was twenty years ago this year that Dean Scarlett and Michael Sirizzotti got into the machine vision business.
“In 2003, this technology was very primitive, under-developed, compared to where it’s at today,” says Mike. “We had some experience in other businesses and thought there was an interesting opportunity in machine vision development and its integration. We didn’t want to build a product. We wanted to create a technology services business with expertise in that field.”
And they did.
“One of the things we liked about our idea for Vista was, coming from Windsor, the general perspective is that it’s an auto manufacturing universe,” Dean recalls. “For us, that would be a piece of it. Machine vision was slowly being adopted, but we felt there were opportunities for diversity into various other industry segments, such as medical devices, food, and beverage. The principles of imaging are transferable. It was our goal to do things outside of the automotive sphere.”
In 2006, Vista Solutions developed a best-in-class 3D inspection solution for the metal casting industry. This exposure to 3D imaging proved to be a pivotal moment.
Weathering the vicissitudes that affect the automotive industry— including the calamitous downturn
of 2008—Vista Solutions not only survived, but it also thrived.
“Between 2009-11, we experienced a critical moment that gave us some success,” Mike continues. “We got heavy into the food and beverage sector, doing work for General Mills, developing a custom 3D inspection for them, that in many ways, laid the groundwork for what we’re doing today. The project went very well. It allowed us to move from our first location to where we are now located on Kew Drive.”
Vista Solutions’ total footprint is now more than 20,000 square feet— between its Windsor location and offices in Detroit and Queretaro, Mexico. Its state-of-the-art vision laboratories enables the company to test and prove-out all prospective applications. Complete with the most current 2D and 3D machine vision technologies, high speed line scan systems and custom developmental tools (software and hardware). Vista can evaluate projects and conduct complete feasibility testing. Moreover, Vista Solutions owns a complete compliment of robotics, automation, and material handling devices to allow for simulation of production conditions.
Just when it appeared that Vista Solutions had reached its zenith, the company evolved in ways that surprised even Dean and Mike.
“We always ran the company as a smaller footprint organization,” Dean says. “By 2018-19, we knew that we wanted to scale and become more process driven. This new thinking has introduced new markets and opportunities, and ways to execute business.”
Vista Solutions now has a built-out organizational structure, which is primarily data driven. If data does not support a business idea, the company does not go with it. A leadership team has been established, that consists of VPs within both Engineering and Finance, as well as a Director of Sales to steer all business development. This leadership team drives cross-functional engagement between all departments.
“Our Machine Vision Engineers, the heart of our business, are truly world class,” says Mike. “This world class talent, combined with our new structure, has propelled our headcount from approximately thirty employees to over fifty, in only three years.”
Dean says he and Mike have never been more excited about the future of Vista Solutions than they are today. And just in time for their twentieth anniversary in business.
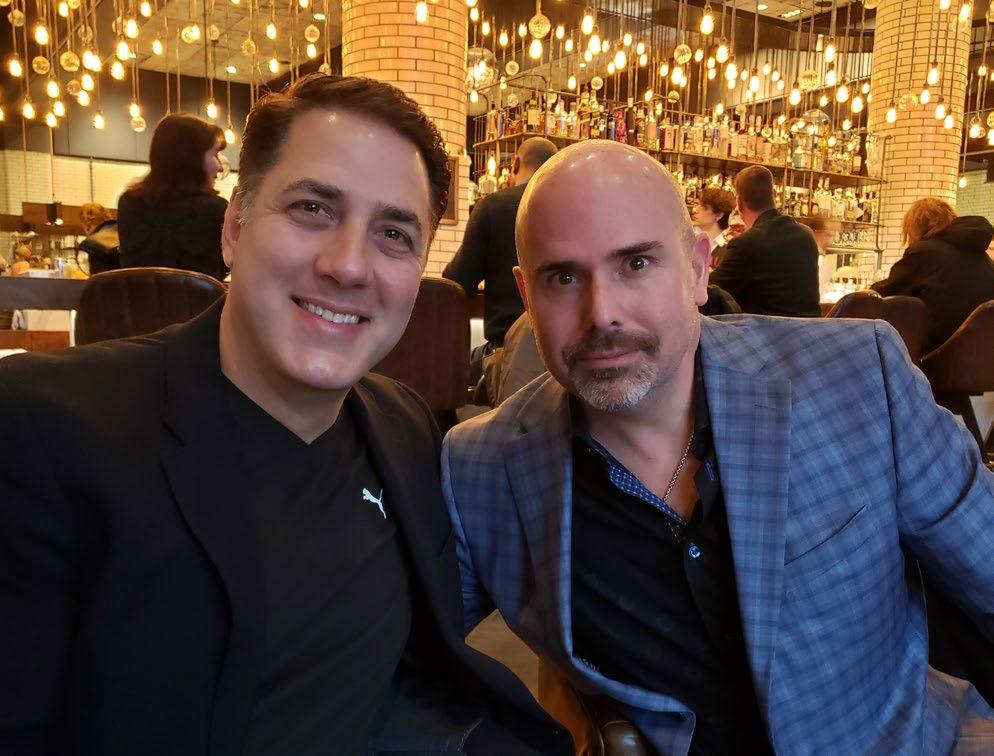
To learn more about the cutting-edge work going on a Vista Solutions, visit them online at vistasolutions.ca. W.E.
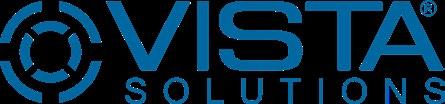
Local tech company finds new ways to evolve in a changing landscape.
EnerQuest: Where Innovation Never Rests

Harrow’s EnerQuest Technologies Solutions Inc. turns 20 this year,but it’s been a lifetime of innovation and finding solutions to customer quandaries.
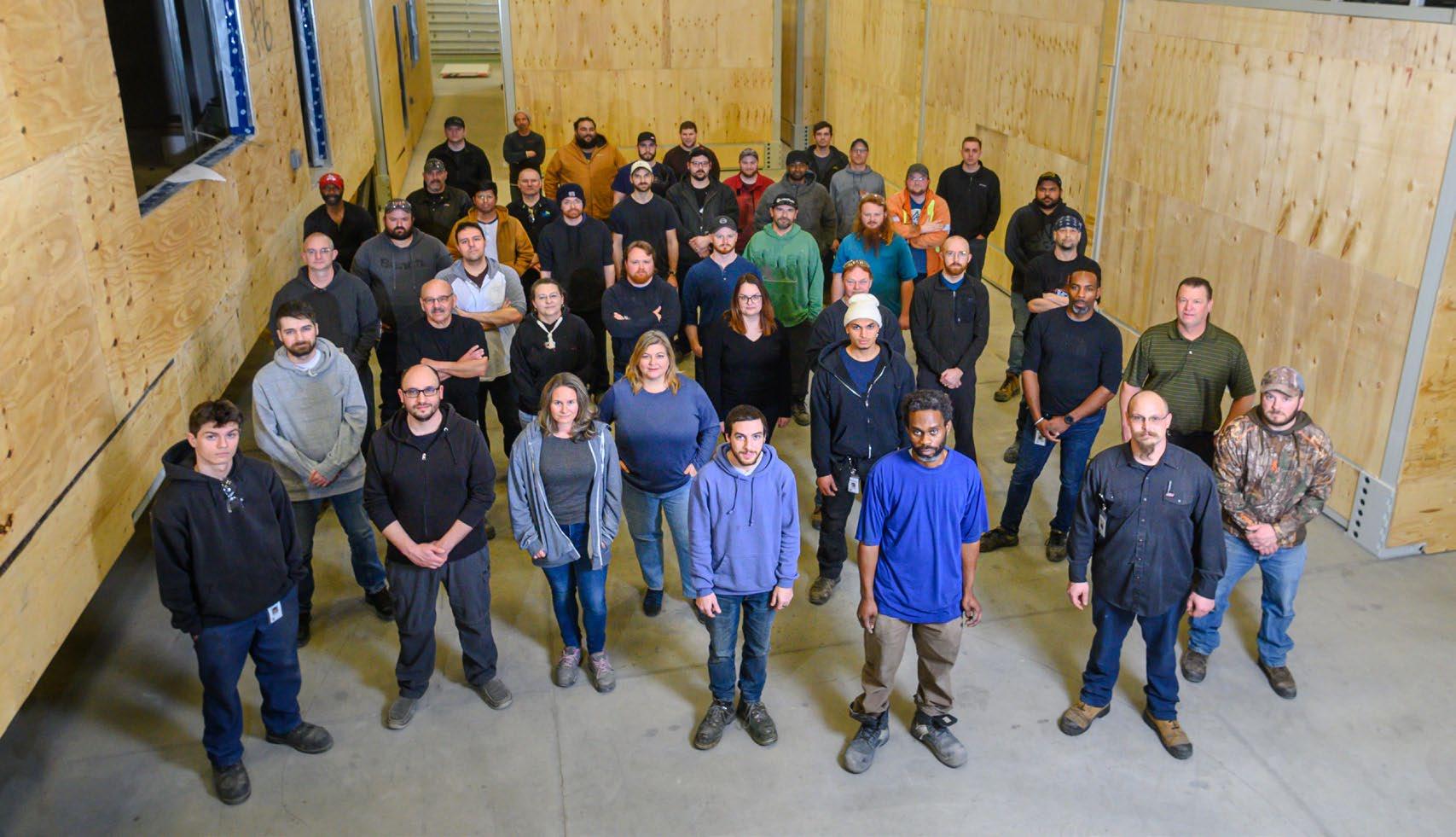
It sometimes takes a wrestling match with misfortune to get us onto the path we’re supposed to follow. That happened twenty years ago to Bill Parr, president, and co-owner of EnerQuest Technologies Solutions Inc., when his job as an electrical service technician with a global company was phased out due to company restructuring. Nine days later he incorporated EnerQuest and began working out of his garage. Among his first jobs was doing some retrofitting with circuit breakers.
“I knew it was time to move out of my garage when a tractor trailer pulled into the cul-de-sac to make a delivery,” Bill remembers. “I needed some copper bus bar that comes in twelve-foot lengths. There was no way to get it off the truck, so we opened the crates and took them off by hand.”
EnerQuest’s first facility was on Point Pelee Drive.
“We’ve been in thirteen buildings in the first thirteen years we operated,” Bill says. “We just continually grew. It’s been mind boggling.”
The game-changer that took EnerQuest to the next level came in 2006. EQ landed the job of providing all the electrical equipment for Casino Windsor’s expansion into Caesars Windsor.
“Every electron that comes off the street from Windsor utilities moves through our equipment,” Bill says.
This year—having weathered the automotive downturn of 2008, the downturn in oil, gas, and renewables in 2015, and the lockdowns of COVID-19—EnerQuest Technologies Solutions celebrates its twentieth anniversary.
The only thing EnerQuest does better than providing power solutions is re-inventing itself.
“Our first solutions were similar in nature, but for different market sectors,” Bill recalls. “There was a lot of automotive previous to 2008, then we migrated to mining, and then renewables, wind and solar projects. Then oil and gas started to pick up. After that, we re-in-
vented ourselves and moved into light rail transit and providing co-generation packages for greenhouses.”
The transformation of EnerQuest continues to this day.
“Today is very exciting,” Bill continues. “We brought in some new investors last year: Integra Mission Critical out of Dallas and Beswick Group out of the GTA. They have a solid history in data centers, but the missing piece for them was having an electrical group. That’s the space we fill. EQ manufacturers its integrated systems, which fit perfectly into their modular mission critical data center construction.”
vided switch gear for multiple generator backup on a hospital project. The solutions were designed with a customized narrow low profile so that they fit through doorways.
“We put them on castors and pushed them through the halls so that construction stayed on schedule,” Bill says.
A tour of the plant revealed a multiplicity of projects: solutions for the mining industry, stackable modules for a data center, and even housing. It seems that EnerQuest always finds time to be of service to the community.
“We’re building two four-plexes for the Bridge Youth Resource Centre project in Leamington,” Bill explains. He points out one full living quarter and says: “They’ll interlock together onsite to do a back-to-back quad, and it’ll be assembled in a week. We’re shipping this fully furnished, all the exterior, everything complete so there is very little to do on the receiving site.”
The one detail that hasn’t changed at EnerQuest is Bill’s ability to make the stupendous sound like the ordinary. That said, EnerQuest’s growth even has the ability to impress Bill.
EnerQuest’s solutions have always been modular. They are built, tested, certified all in the factory, so that all that remains when they are shipped to a site is installation. Now, EQ’s modular solutions are stacked six units high to save floor space on customer sites. Instead of the generator building, chiller, fuel supply systems for the generator, UPS (uninterrupted power supply) systems, and cooling, all standing shoulder to shoulder on the same skid, they are now stacked one on top of the other. EQ builds these solutions, so they are optimized for shipping.
“These are all high voltage equipment in modules that you can ship conveniently and economically by transport truck, rail, air, and sea,” Bill says.
An example of building solutions to a practical scale occurred when EQ pro-
“As part of our growth, especially having new investors in… the amount of work they have brought into this facility is amazing,” he says. “We’ll soon be purchasing the longest fourteen-inch tube laser in the world, with a sixty-five foot infeed and a sixty-five foot outfeed for all the length of tube that we use.”
As a matter of course, EnerQuest cannot stop innovating. Most recently it created with their paint supplier an antistatic anti-slip paint for IT spaces. Wherever a need arises, EQ creates a solution.
Bill concludes the tour of the EnerQuest’s facility saying: “The great thing about this facility is that it’s allowed us to become vertically integrated, so we do our own structural design, sheet metal design, we have our weld shop, sheet metal shop, our electrical department, our automation department, final assembly testing area, and then out the door. All under one roof.” W.E.
We’ve been in thirteen buildings in the first thirteen years we operated,” Bill says. “We just continually grew. It’s been mind boggling.”
Women Can Do It Too. They’re Already Doing It!
WEST continues to grow their women in skilled trades programs.
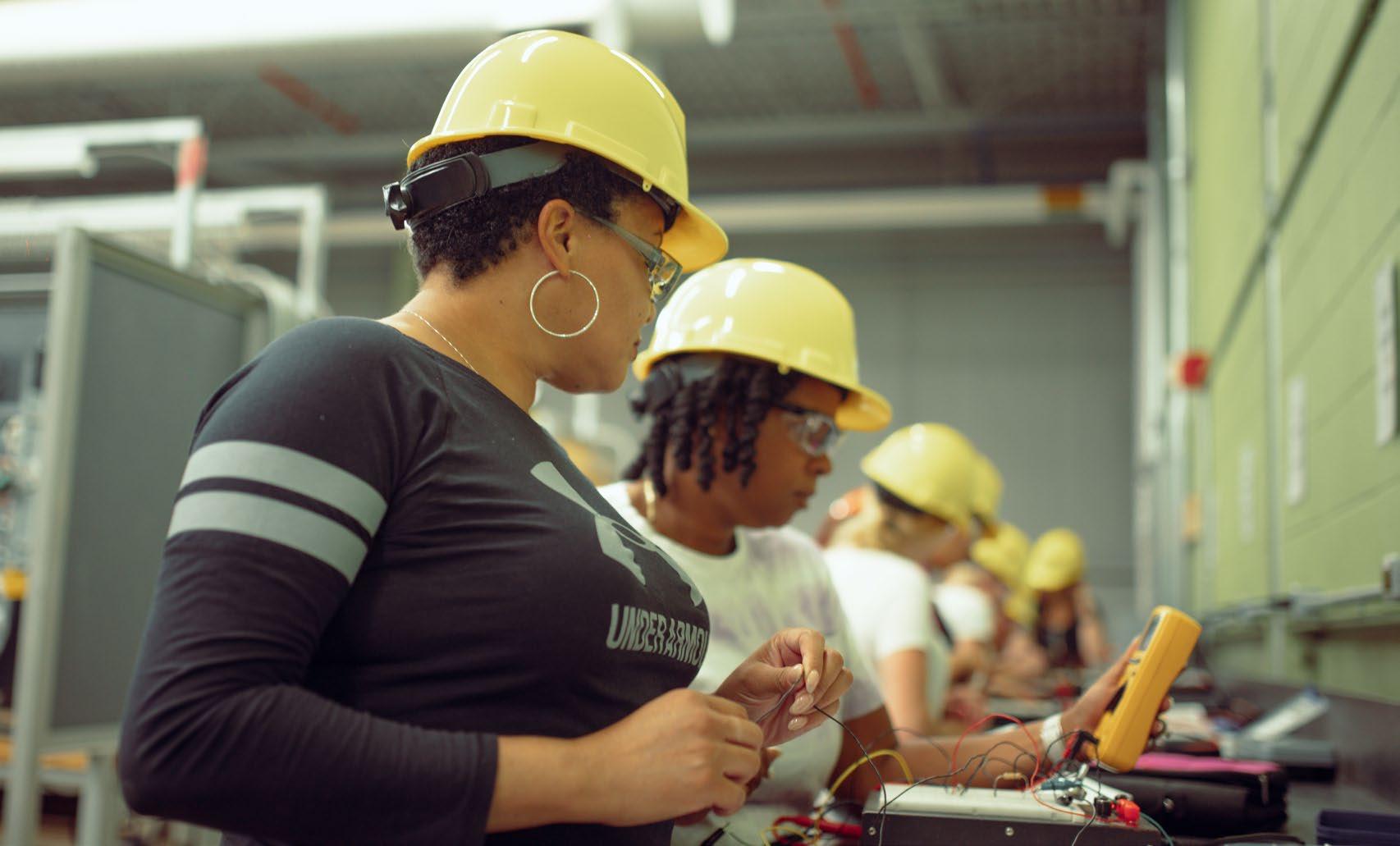
Since time immemorial, men have dominated the skilled trades—not with ability, but by social contract. Only a couple decades ago, to see a woman working a “dirty job” in a shop was like searching for an albino elephant—they might be out there, but good luck finding one. Old sexist tropes flew freely in the wind, while half the potential workforce was left out in the cold.
It wasn’t always this way. People like their action dramas and documentaries about World War II, don’t they? Epic films like Saving Private Ryan and Full Metal Jacket, classic shows like Band of Brothers and The Pacific. That may have been life in the European and Pacific Theatres, but the engine that kept the war machine running at home was skilled trades. With the men off at war, who worked the trades? A lot of women. Ever heard of Rosie the Riveter?
Those jobs, worked by thousands of women, disappeared after the war effort ended. However, slowly, over the past couple decades, women have progressively made their way back into the skilled trades.
In 1987, Women’s Enterprise Skills Training of Windsor Inc. (WEST), a non-profit, community-based organization serving women in Windsor and Essex County, entered the local business scene. Their goal: to help women find work and develop and learn new skills. Also, to provide support to women new to the community, such as immigrants, with settlement and orientation in the region.
Making alliances with local businesses, community organizations, and individuals, WEST’s programs and services have grown exponentially over the years. Currently, they offer a wide range of specialized training programs to support women and their community, helping to fill gaps in the local labour market. One way they help is through their Women In Skilled Trades (WIST) programs.
“Participants have described our WIST programs as life-changing,” states WEST of Windsor Inc. executive director Rose Anguiano-Hurst. “Building on our strategic partnerships and organizational strengths, WEST has become a leader in offering WIST programs. [We have] helped 260 women gain training and skills to pursue careers in various skilled trades sectors.”
Recognizing shortages in the skilled trades labour pool, WEST sought an innovative way to empower women through training and skill enhancement, while also looking to fill the needs of local employers. With Windsor-Essex being a key manufacturing hub and considering the aging workforce, WEST has put a heavy focus on the skilled trades through their WIST programs. Partnering with industry leaders, labour leaders, and educators, WEST now offers programs to further the careers of women with
apprenticeship opportunities leading to Red Seal designations.
“I recommend to any women out there who are looking to change their lives for the better and have the determination and motivation to see it through to go forward with this program,” said one participant in the WIST program. “It’s the best decision I have ever made.”
For the past nine years, WEST has provided their CNC Mechanical Millwright Pre-Apprenticeship Program, which is funded by the Province of Ontario, and in partnership with St. Clair College and Unifor Local 444. The program works to prepare and support women on their journey to find employment in this underrepresented field, while addressing economic issues women will face and help them enhance their skills to what is required to take the next step in their careers. In nine intake sessions for this WIST program, 200 women have received training so far.
Similarly, WEST also offers an Introduction to Craft Trades for Women program, funded by the provincial government and in partnership with LiUNA 625. In four intakes, 40 women have so far received training in this field.

Also, WEST recently delivered their first intake for their Electrical Pre-Ap-
prenticeship Program. The program was a success as it helped train 20 women in its inaugural run. These women are now seeking careers in the electrical trade. WEST’s electrical program was offered in partnership with St. Clair College and Unifor Local 444.
“Acceptance into the WEST Electrical Pre-Apprenticeship Program provided me with the tools and experience necessary to succeed in gaining employment as an electrical apprentice,” said another WIST participant. “The WEST Program provided the financial and educational resources I wouldn’t have been able to obtain otherwise.
“Gaining a career in the skilled trades offers guaranteed employment in a high demand field. It teaches you humility and builds confidence. The impact of the WEST program provided a solid foundation which I now stand on to build a beautiful life.”
Having empowered 260 women with the skills to succeed in various skilled trade career routes, WEST continues to strive for innovative ways to break down gender barriers, while supporting local labour needs, and paving a path to success for the often-underrepresented women in the manufacturing and skilled trades sectors. W.E.

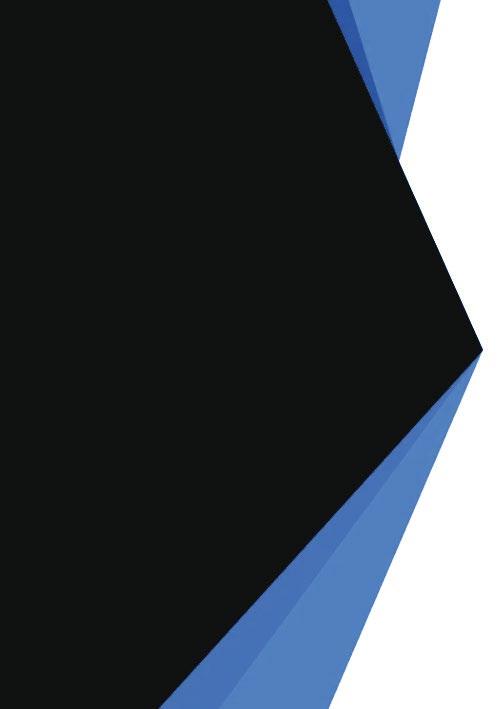
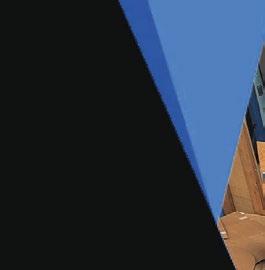
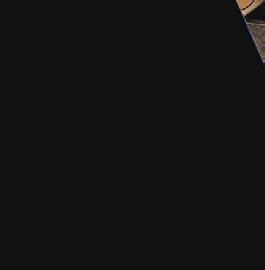
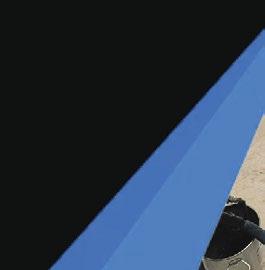

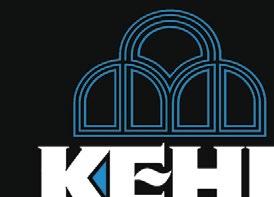


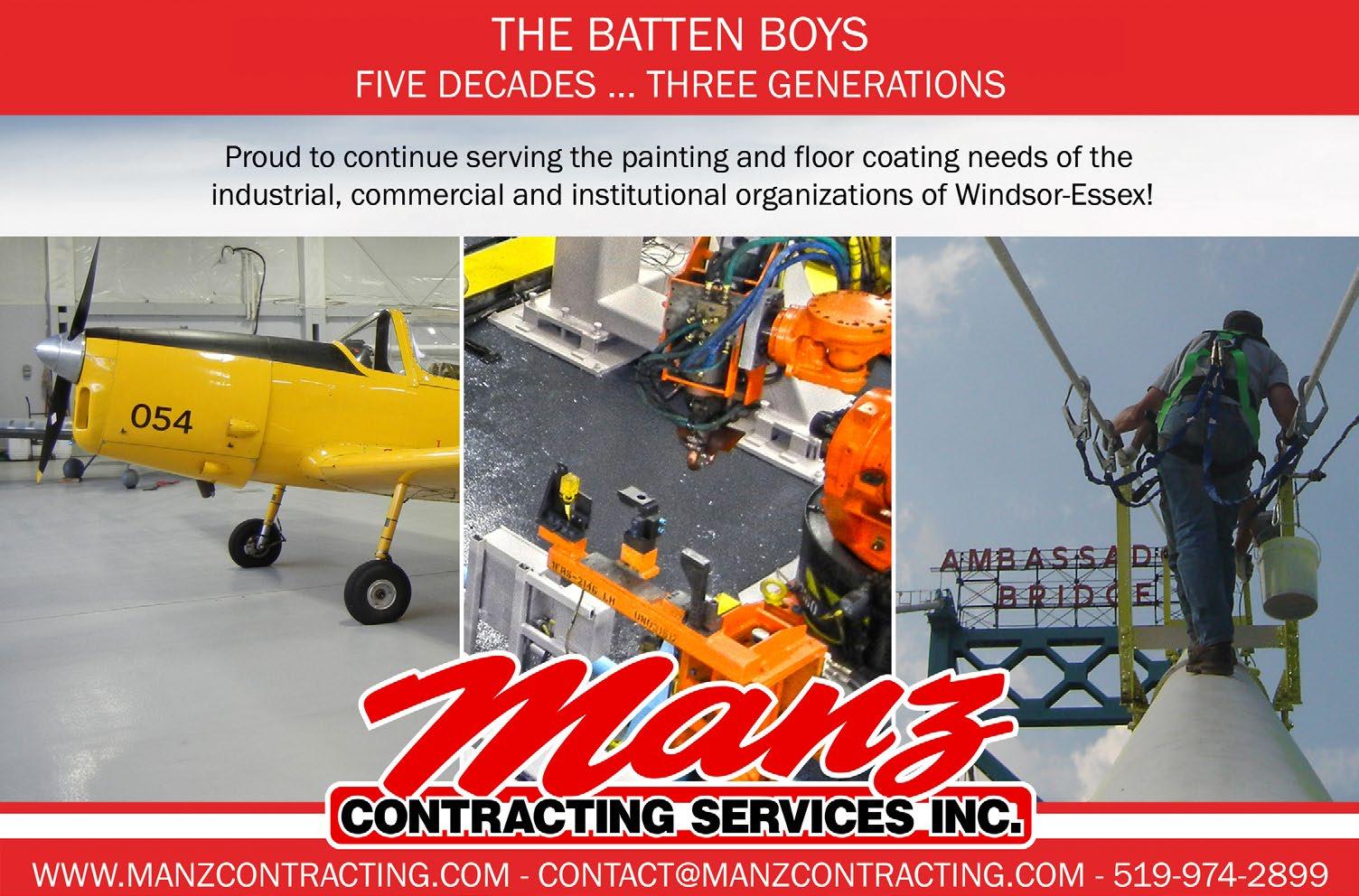
Post Packaging Customer Focused Solutions
The packaging industry continues to evolve as customer needs and expectations grow. Post Packaging leverages the power of its people and technology to provide a wide range of packaging solutions. To achieve this, the company has added horse power, innovation and continuous improvement to its operations.
“To support our customers’ needs, we continuously re-invest in our people and overall operations,” explains owner Paul Giberson. “We have added more team members, purchased additional manufacturing and logistical equipment, as well as added new processes and systems to ensure we’re able to provide best-inclass customer service.”
Recently, Post Packaging added key leadership talent: Director of Operations, Rocco Moceri.
typing. This improves our response time to customers.”
Last year, Post Packaging partnered with Conestoga College, the leading packaging program in Canada, to bring in students for internships on an ongoing basis.
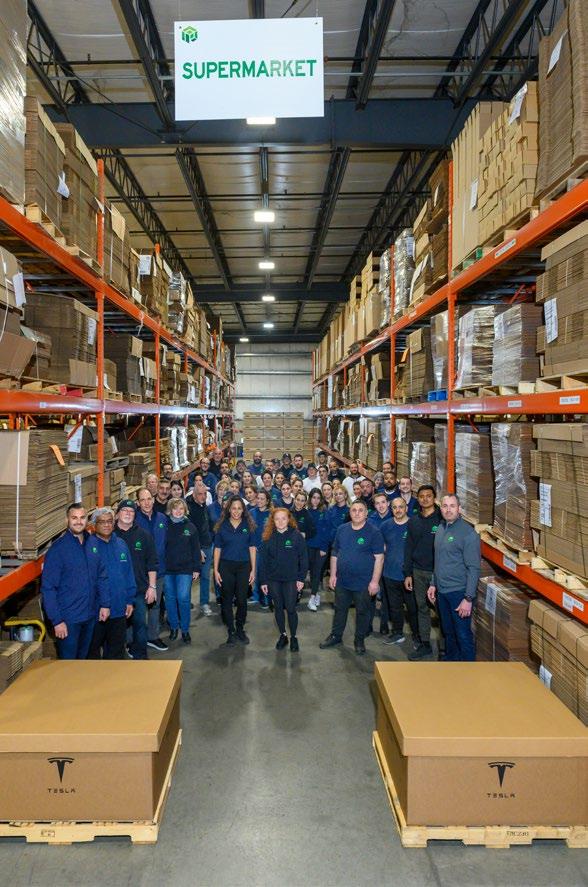
“This is an investment in our future and to attract the next generation of packaging talent to the Windsor/Essex area,” Paul says. “This area has so many exciting things happening, we need people to know about it.”
By Matthew St. Amand by Syx Langemann“I was born and raised in Essex County,” Rocco says. “I was a plant manager prior to joining, and was actually a customer of Post Packaging. I watched the company evolve. When I saw this opportunity advertised at Post, I thought it could be a new challenge and a good move for me and my family. We’ve got a great team at Post Packaging, which really feels like a family. My team and I are now developing ways to improve our organizational processes and efficiencies.”
This mindset extends to its customers, whose needs are as unique as the solutions Post Packaging designs to meet them.
“We create unique and intricate packaging for customers,” Paul says. “We design, manufacture and assemble the packaging in-house so, as the parts come off our customers’ production lines, they go right into the packaging solution.”
Vice President, Rob Michie—with more than thirty years in the company— leads the engineering and customer experience team. Rob’s department boasts more than seventy-five years of packaging engineering experience which they make available to all their customers day-in and day-out.
“We recently invested in new packaging design software to support 3D design work,” Rob explains, “which gives customers a clearer idea of the solutions we create for them before building a sample. We have also purchased an automated packaging design table for rapid proto-
As a long-time solutions provider to the auto industry, Post Packaging now looks to the EV battery segment. With NextStar Energy bringing Canada’s first large-scale lithium-ion battery production plant to Windsor, Post Packaging has devoted significant R&D resources to developing innovative solutions for use in that sector and are excited to showcase these soon.
What does the process involve when new customers choose Post Packaging for a solution?
“Getting started with us is a seamless process,” says Paul. “We are industry agnostic and can help with anyone’s packaging needs. This makes us unique. We also have the capabilities here, locally— and a network of partners—to provide our current and future customers with unique, cost-conscious solutions.”
Post Packaging is a responsible corporate citizen, focused on providing sustainable products.
“We are now an FSC certified company,” Paul says.
The Forestry Stewardship Council (FSC) is the corrugated packaging industry’s most trusted certification body.
Post Packaging believes that sustainability is vitally important and buying raw material from companies that have responsible labour and forestry policies is a great start.
“As we look toward the future, we focus on growth, innovation, high quality manufacturing and unparalleled customer service!” Paul says.
To learn more about Post Packaging, the industries it serves and the solutions it offers, visit them online at postpack.ca W.E.

For more than half a century, Post Packaging has been a part of the Windsor/ Essex community.
FULL-SERVICE PLASTIC DESIGN & FABRICATION IN LAKESHORE
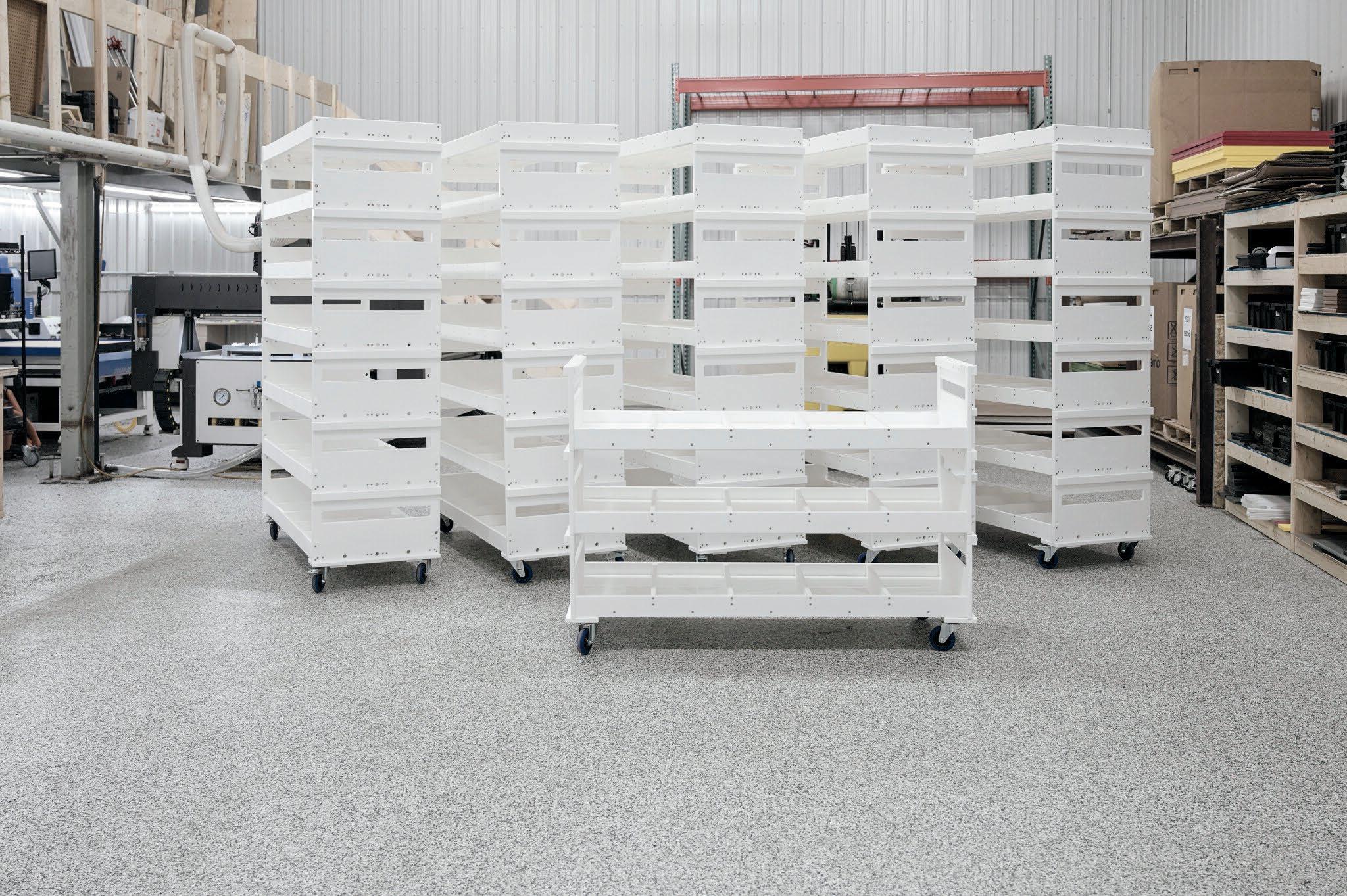
LET OUR EXPERTISE WORK FOR YOUR NEXT CUSTOM APPLICATION


CHECK OUT SOME OF THE COOL STUFF WE MAKE HERE
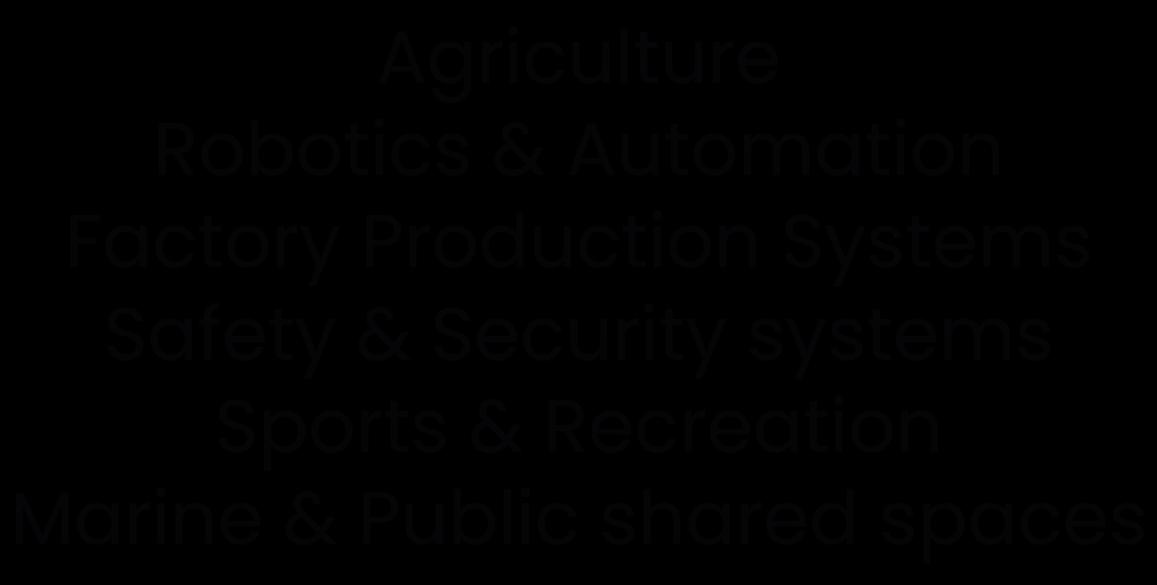
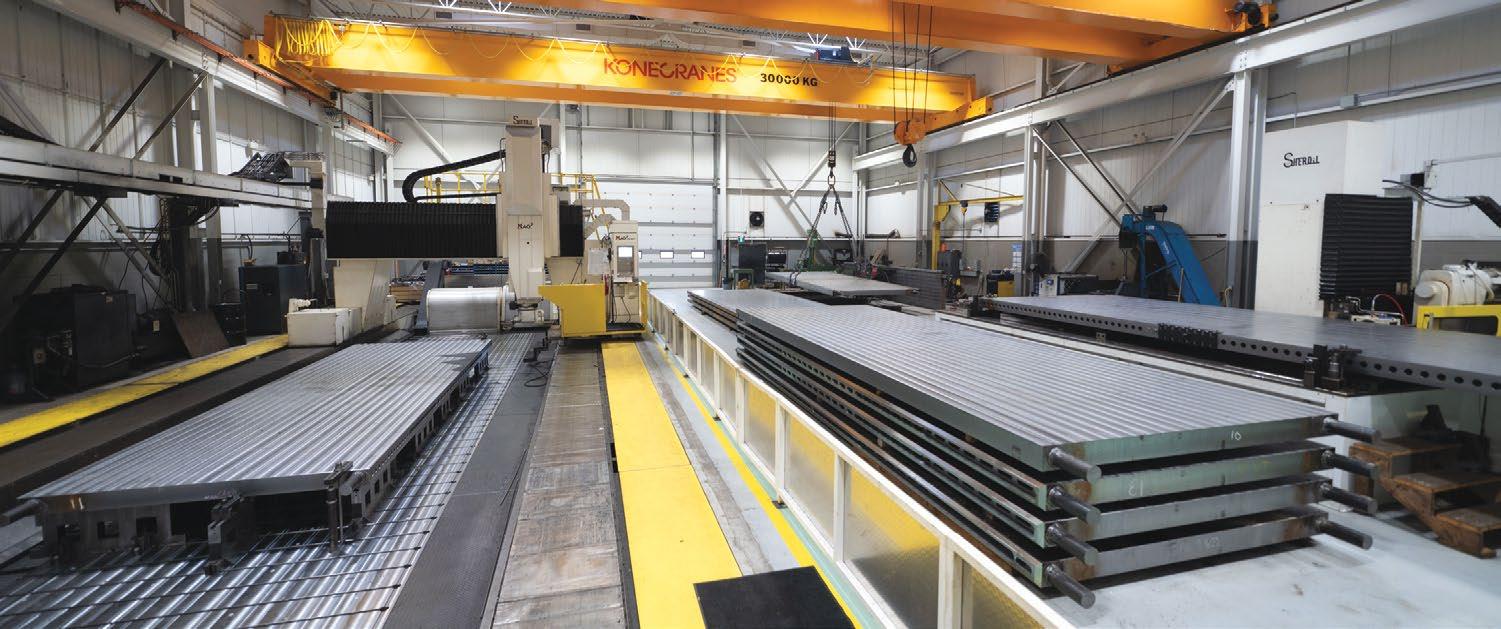












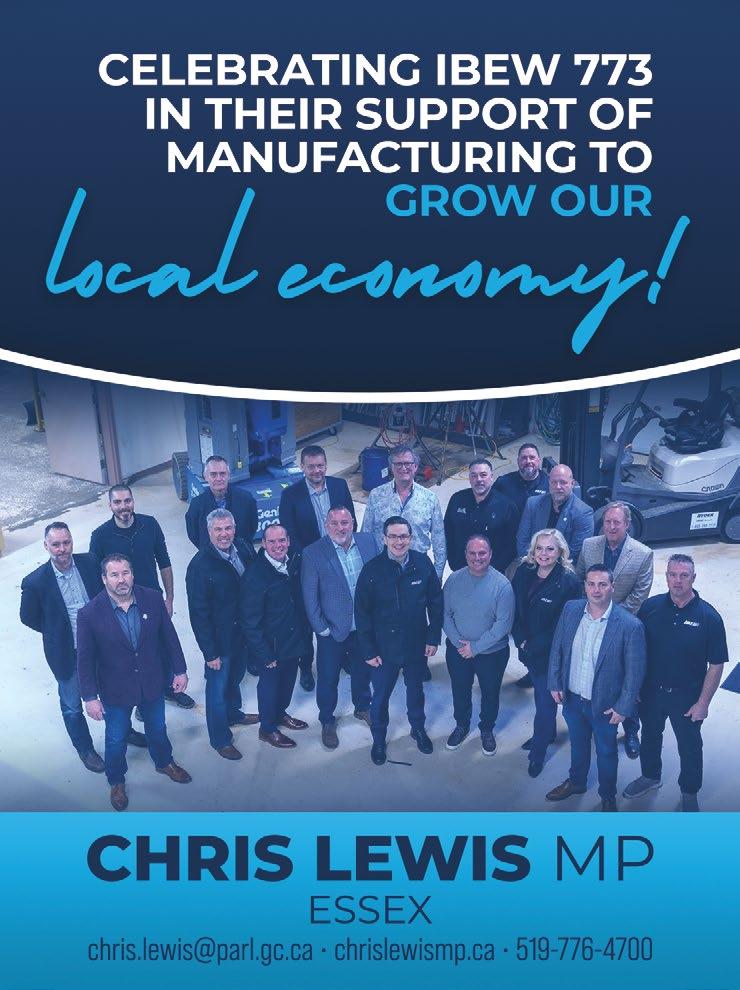
KMJ Industrial Contractors
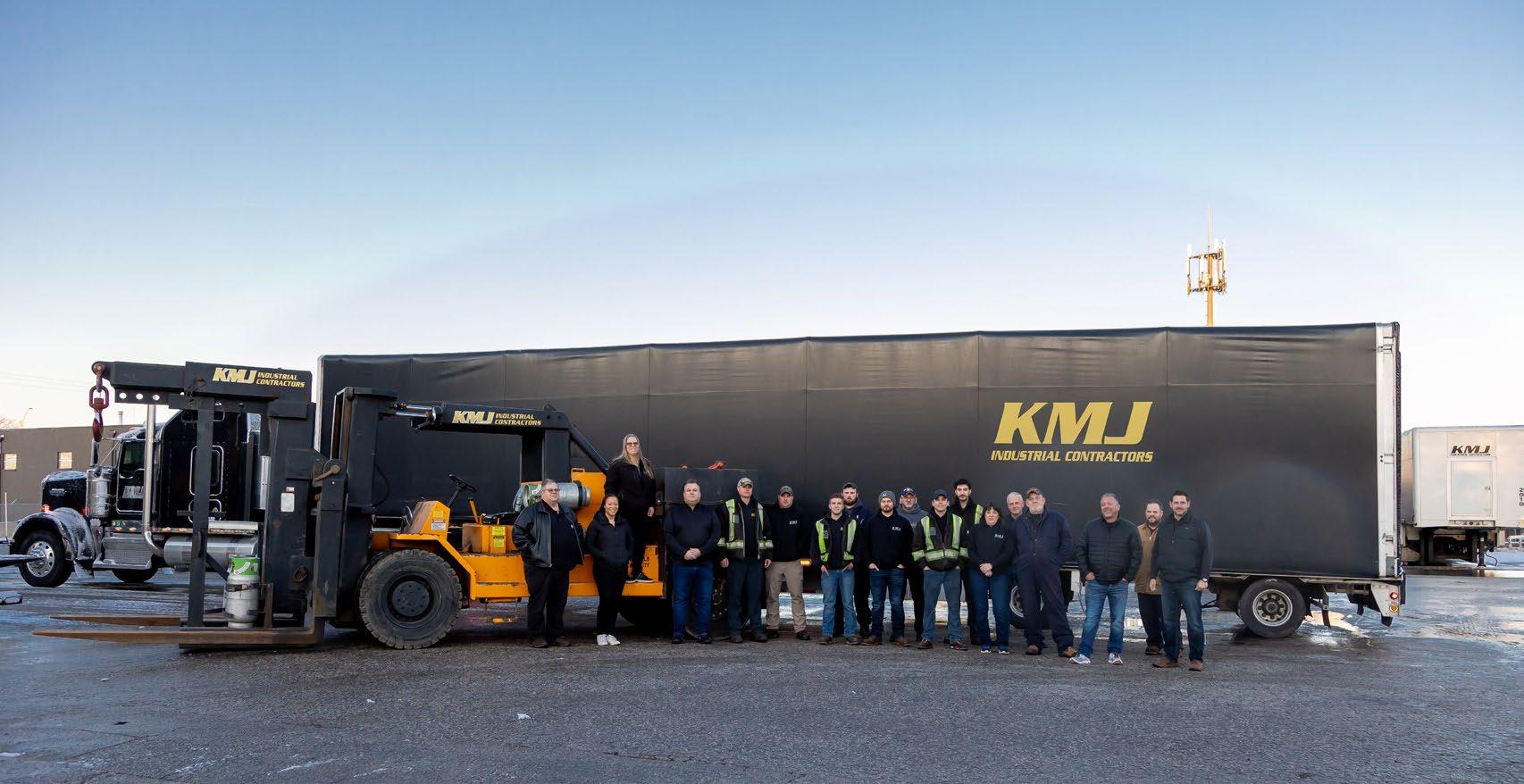
“We’re Only As Good As Our Crew!”
A new vision guides an industrial contractor that has paid its dues over the last twenty-five years.
By Matthew St. Amand Photo by Trevor BoothFor some people, moving an industrial machine the size of a battleship is just another day at the office. That’s how it is for the crew at KMJ Industrial Contractors.
There is always risk getting into the crowded industrial contracting business, but partners Rob Simard, Sean McIvor, and John Crease had two things in their favour: unmatched experience in the field and a vision for the future.
“We’ll travel anywhere in the U.S. and Mexico,” says co-owner John Crease. “We’re very diversified with what we do and can take on any project.”
This allows the team to serve a variety of industries which include automotive, manufacturing, heavy industry, plastics, machine tooling, energy and power, healthcare, food and beverage, and industrial construction.
KMJ has an arsenal of equipment to meet all job requirements. From forklifts that are rated up to 100,000 lbs. to hydraulic gantry systems, mobile cranes, and industrial cranes, KMJ has the tools to get the job done.
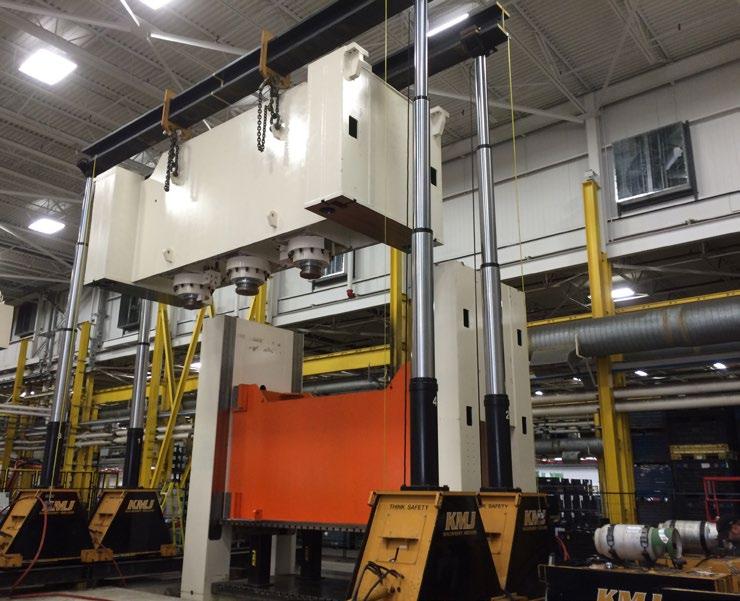
“We have specialized transportation, from single axle trucks to modular float systems that can accommodate any load,” Rob says. “This diverse fleet allows us to haul standard, heavy, oversized, and over-dimensional loads. We’ve even handled delicate laboratory and electronic equipment.”
Customer service is the number one priority on every project. “Our motto is: ‘We’re only as good as our crew,’” Rob says. “The crews take pride in doing a good job and keeping our customers happy.”
In addition, the safety of our workforce and job sites is KMJ’s top priority. The company maintains a zero-tolerance safety culture that actively works to identify and control any potential hazards. A dedicated safety officer is on staff to ensure compliance across every project.
“We’re a unionized shop,” Rob explains. “We have forty to fifty full time employees between the Windsor and Brampton location. If a bigger project requires more employees, we work with local union halls to supply additional manpower.”
KMJ has yet to face a challenge it could not meet. Whether it is moving and installing an MRI machine into a medical facility, or relocating a complete manufacturing plant, KMJ has the horsepower to handle the job. They have completed multiple plant relocations over the years, with minimum plant disruption and maximum cost efficiency.
“We are the complete package,” Rob continues. “We can offer all phases of a project including engineering and design, transportation, civil, electrical, mechanical, sheet metal, startup, troubleshooting and total project management.”
KMJ partners with the best electrical and piping contractors around. Their team is comprised of certified electricians, pipefitters, plumbers, welders, and sheet metal fabricators, each bringing experience in all industrial aspects.
The team does not limit itself to projects just in Canada.
“Our employees know what safety is all about,” Rob says. “We all contribute to making sure everyone goes home safe at the end of each day.”
Learn more about KMJ’s multitude of capabilities by visiting them online at kmjindustrialcontractors.com. W.E.
We are the complete package, we can offer all phases of a project including engineering and design, transportation, civil, electrical, mechanical, sheet metal, startup, troubleshooting and total project management.”
A Day For Our Future
Workforce WindsorEssex’ Manufacturing Day is opening students’ eyes.
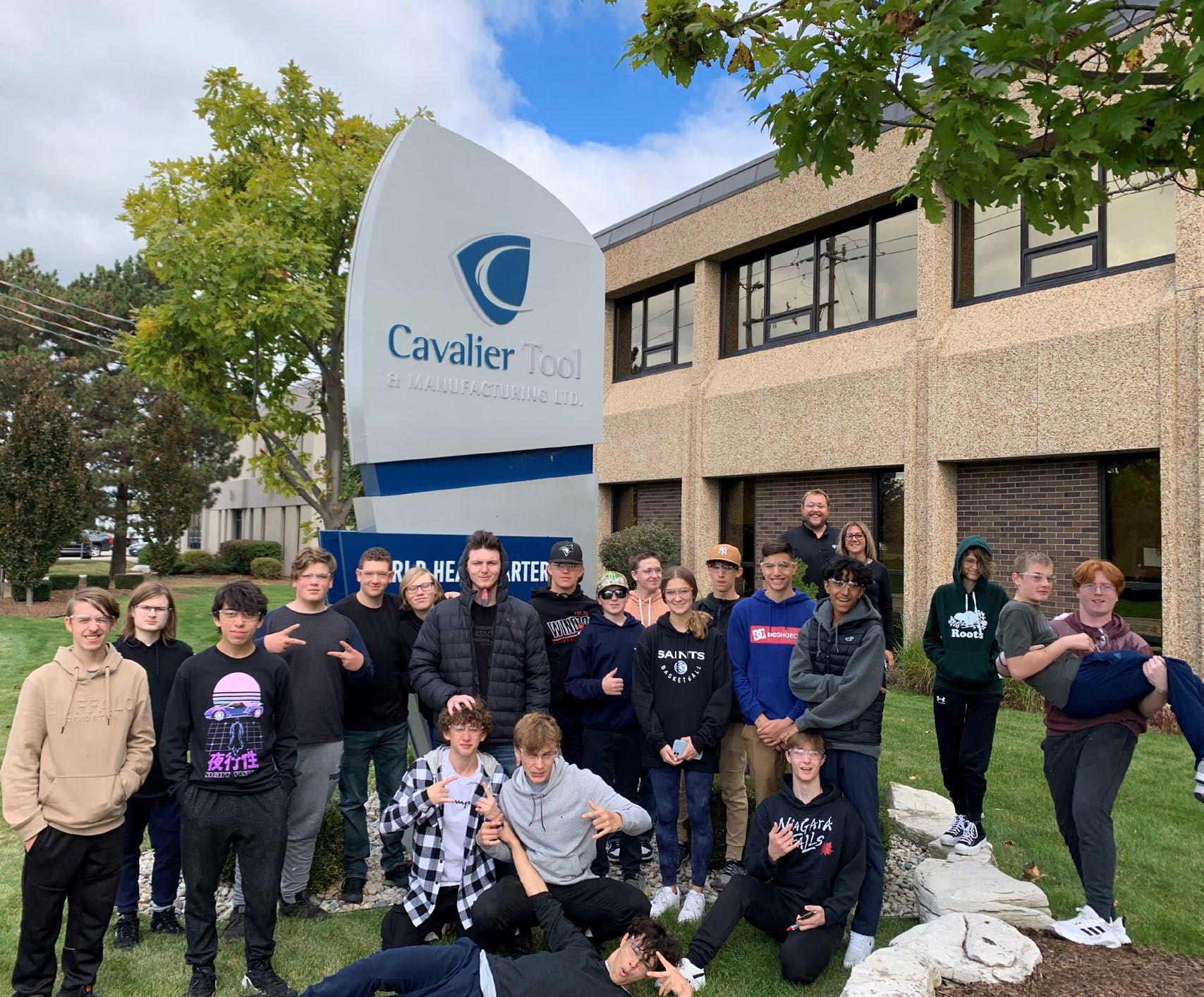
Manufacturing Day is all about setting up the future. For years, local nonfor-profit Workforce WindsorEssex has been working with business and educational leaders in the Windsor-Essex County region to open the eyes of young people and make them realize their potential in a manufacturing field.
“The purpose of Manufacturing Day is to showcase the benefits of working within the manufacturing industry, a sector that accounts for 19 per cent of our workforce but continues to face persistent labour gaps,” explains Workforce WindsorEssex manager of research projects Tashlyn Teskey. “Touring clean and technologically advanced facilities unravels the misconception that jobs within the manufacturing industry are somehow worse than other jobs and inaccessible for jobseekers who don’t fit the stereotype of what somebody in the field should look like.”
Students are afforded a chance to see how far the industry has come in recent years, how complex manufacturing jobs can be, and that there are also supports for people who thought a job in the industry because of their gender or physical capabilities was out of reach.
Every October, students from across the region are invited to meet local industry leaders, tour factories, and learn about the benefits of jobs in the skilled trades and related fields. The event, which locally operates in partnership with Invest Windsor-Essex, originated in the United States, but grew to Windsor-Essex in 2016—the first Canadian region to host the event.
“A big benefit of Manufacturing Day is the opportunity for students who are interested in the industry to form real connections with employers,” states Teskey. “In last year’s Manufacturing Day, students were able to secure co-op placements with the businesses they were visiting. It’s a great way for the students to ask questions about skill and education requirements and potentially hear from younger employees just starting their career in the sector.”
She adds that the event has grown every year since its inception. Last year’s event, which took place on Oct. 7, 2022, featured 19 companies participating in 22 locations. Teskey says that the hope is that the event will grow further in 2023 and adds that the event has recently also been opened up to newcomers and jobseekers working with local employment services.
“Manufacturing Day is a great example of the importance of education and industry partners working together to provide our students with opportunities to explore skilled trades and careers that are in demand in our community,” states E.J. Lajeunesse Catholic Secondary School principal Natalie Julien-MacAdam.
Ryan states that Manufacturing Day has done a great job of exposing students, who may be interested, to co-op programs and the Ontario Youth Apprenticeship Program (OYAP). Last year, over 100 students from Lajeunesse, from Gr. 8 to Gr. 12, were able to visit over 10 different local companies.
“Manufacturing Day is a great opportunity for high school students all over the county to get introduced to all the different careers and options for work in the world of manufacturing,” says Cavalier Tool & Manufacturing Ltd. manager of employee relations and talent Tal Czudner. As a company, Cavalier has been a major employer in the region since 1975 and currently boasts 250 employees.
“Cavalier has long been a big supporter of Manufacturing Day,” states Czudner. “We really roll out the red carpet—we get every one of our managers involved—to get the kids excited about the opportunities. As an industry, we don’t do a great job of explaining what we do and Manufacturing Day gives students the opportunity to see modern, clean, and safe facilities—and you can do a bunch of cool stuff and make some good cash.”
He says that past events have resulted in a great influx of interested co-op students that, in time, have made for beneficial OYAP students and are boon for local industry.
Lajeunesse Business teacher Shelley Ryan, who is also the school’s coordinator for the Specialist High Skills Majors program, says that Manufacturing Day has been highly beneficial for their students.
“Windsor-Essex has so much opportunity in the skilled trades and there’s a lot of myths and stigmas that we’re trying to break,” she says. “We need women, we need diversity, we need all different kinds of skills and talents that are university-bound, that are college-bound, apprenticeship-bound, and I think it’s all about opening up kids’ eyes.”
“Reko has been participating in Manufacturing Day every year since its inception,” says Reko International Group director of corporate human resources Lauren Beaudoin. “It’s always such an amazing day, seeing all the bright, young faces walking through our buildings, and watching our employees engaged with them.”
Founded in 1976 by the late Steve Reko, the company is headquartered in Lakeshore and employs hundreds of local tradesman from across the region.
“This is such a great community event that allows employers in Windsor-Essex County to showcase their
Manufacturing Day is a great opportunity for high school students all over the county to get introduced to all the different careers and options for work in the world of manufacturing.”
businesses,” she states. “It is crucial for the younger generation to know and understand the potential manufacturing and skilled trades pathways that are available to them during and after high school. It allows companies like Reko to really show off the talent and innovative, modern manufacturing that we have here today.”
At last year’s Manufacturing Day event, Valiant Machine & Tool opened three of its facilities to students, with three busloads attending each spot.
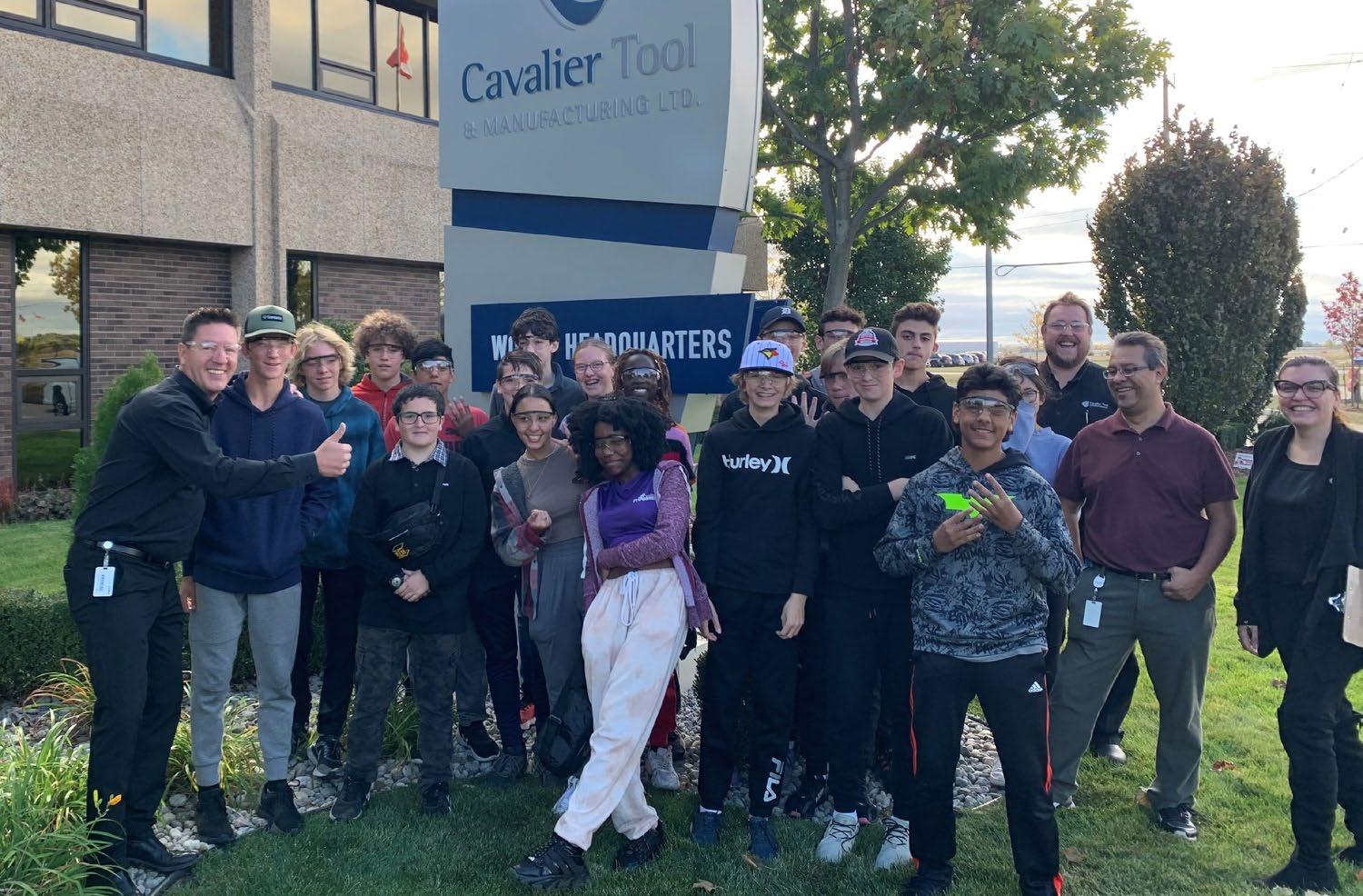
“For us, it’s an opportunity to give high school students exposure to the automation business,” states Valiant senior human resources manager Mike Van Nie. “We go into their schools and we talk to them, we can show a video or two, but they don’t really get the true picture unless they get out in person and see. When we bring them out on the shop floor, we’ve got 50 robots out there that are two feet tall and they’re moving. You can see their jaws drop. It’s something that you have to see
in person to get an understanding of what’s involved.”
Founded in 1959 as Avco Tool & Die, Valiant has long been a local leader in manufacturing. Today, they’ve grown to boast over 1,500 employees at 20 locations in 11 different countries.
“With a company like we are, there are pretty much options for every career path they would want to take,” explains Van Nie. “If you are good with your hands and are interested in the skilled trades, then we have apprenticeship opportunities right out of high school. Your schooling costs are all covered and you’re working during the day and going to school at night. After three or four years, you can be a skilled trades person.
“If the college route is something you’re looking at, that’s where most of our PLC programmers come from. St. Clair College, here, I would say has the top program in Canada for that.
“If you are more focussed on a university path, then we need people to
come up with the concepts, engineer, and design all of our equipment—and there’s engineering and business school opportunities for purchasing, estimating, or sales.”
He says that Valiant has done a great job of recruiting co-op students through the event, and now take about 10 of them per school term.
“[Manufacturing Day] gives them exposure,” states Van Nie. “It’s an eye-opening experience for them. With manufacturing, people think of dirty environments; that they’re labour intensive. For them to see how that’s changed with all of the automation, updated machinery, robots— part of it is changing that mindset of manufacturing.”
Manufacturing Day 2023 will take place on Friday, October 6. For more information, please visit Workforce WindsorEssex’ Manufacturing Day web site at workforcewindsoressex.com/ manufacturing-day. W.E.

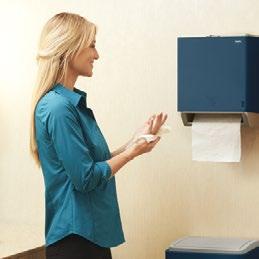
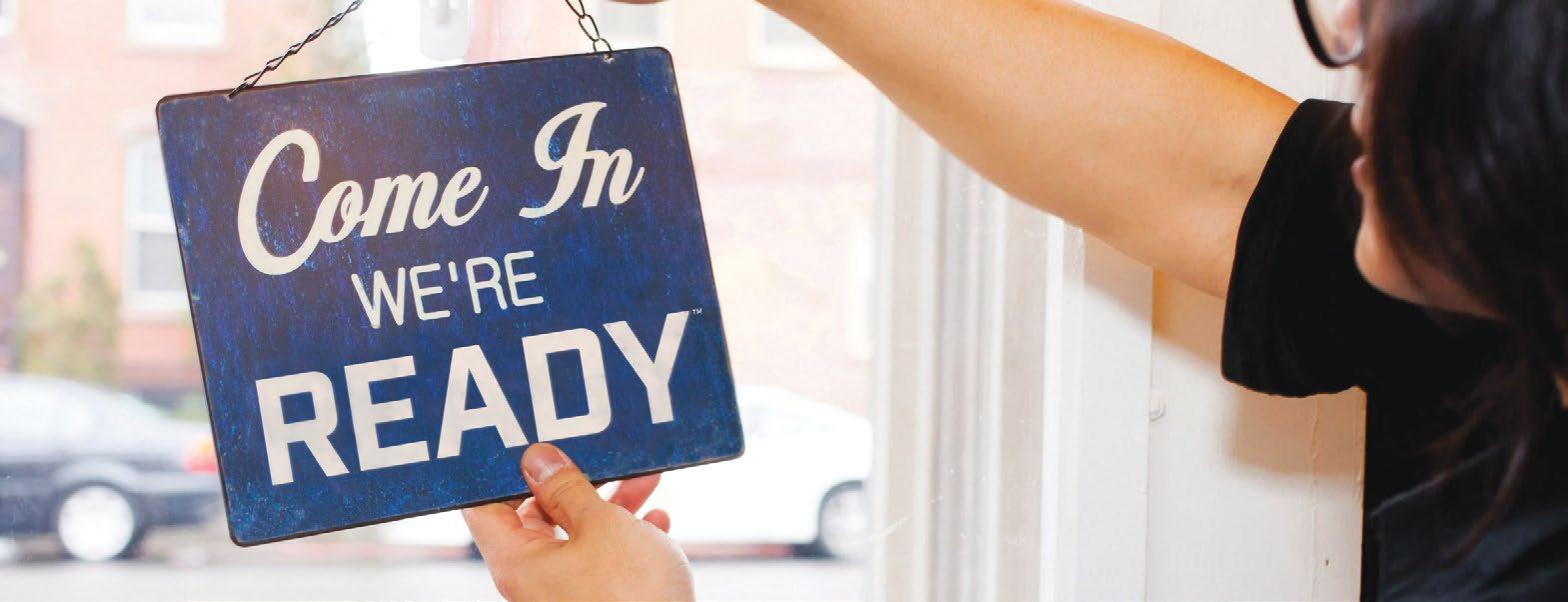

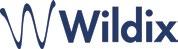
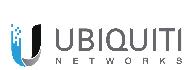
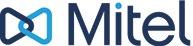


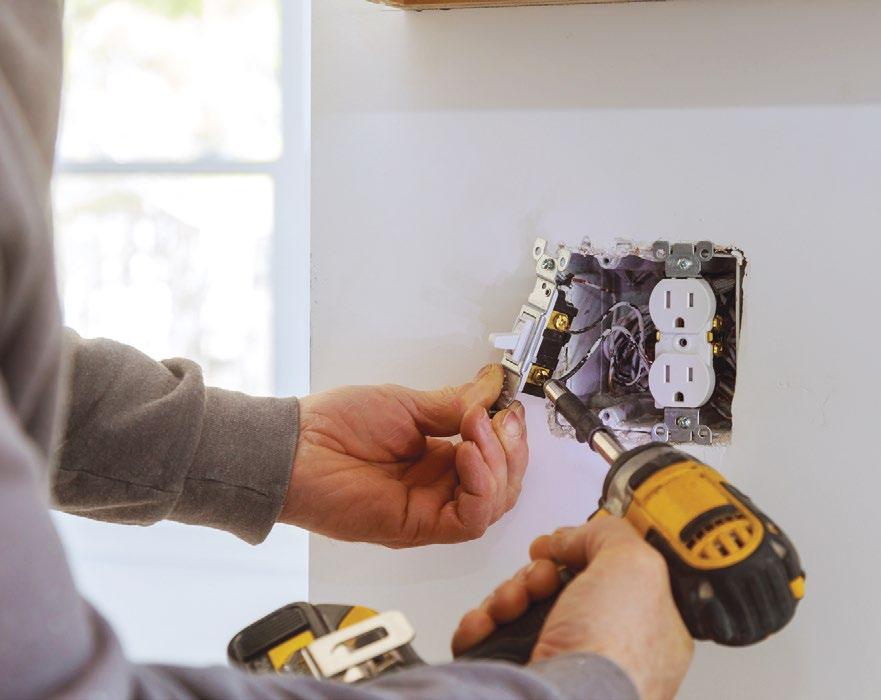
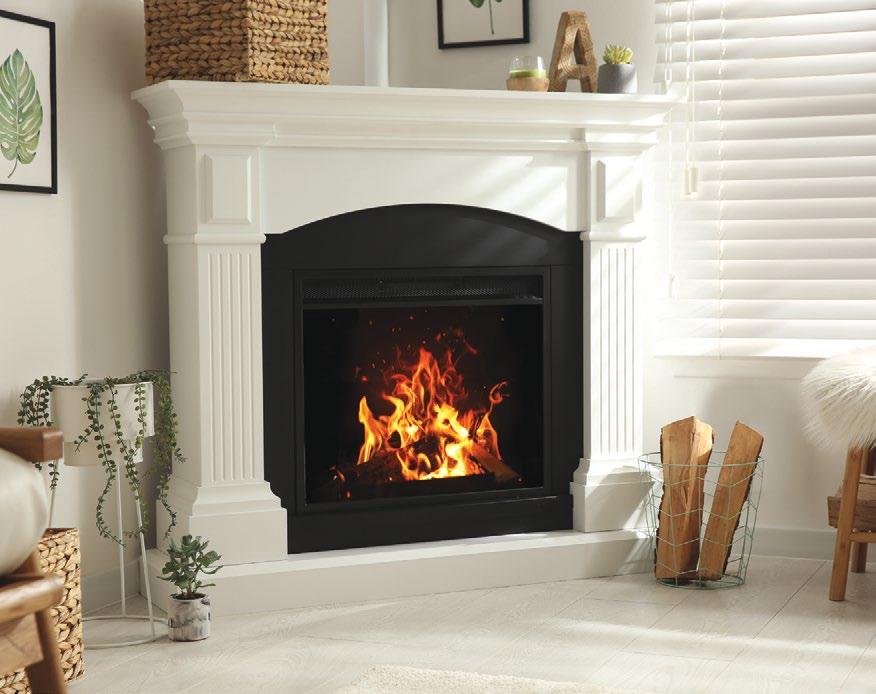
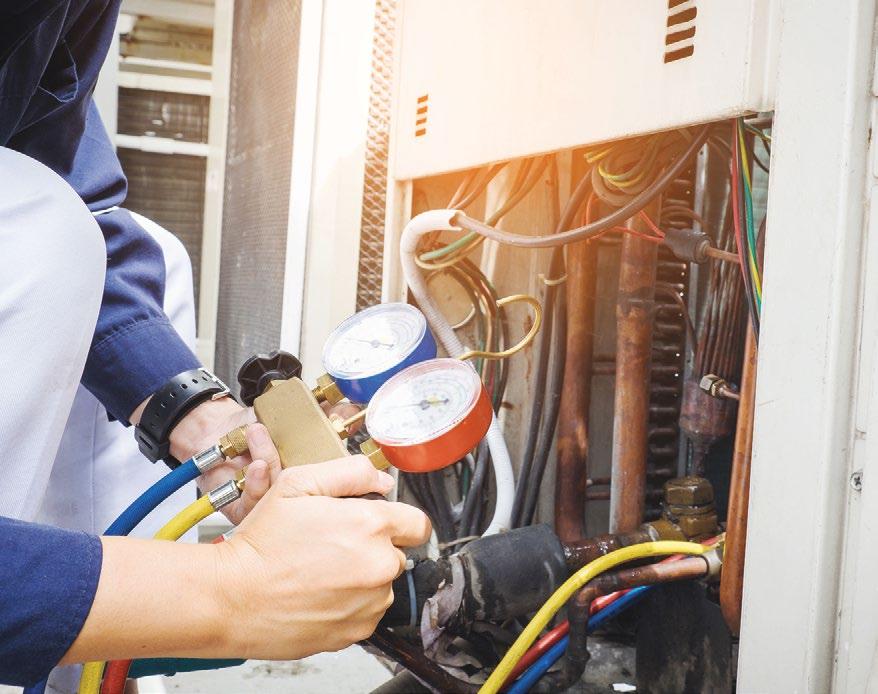
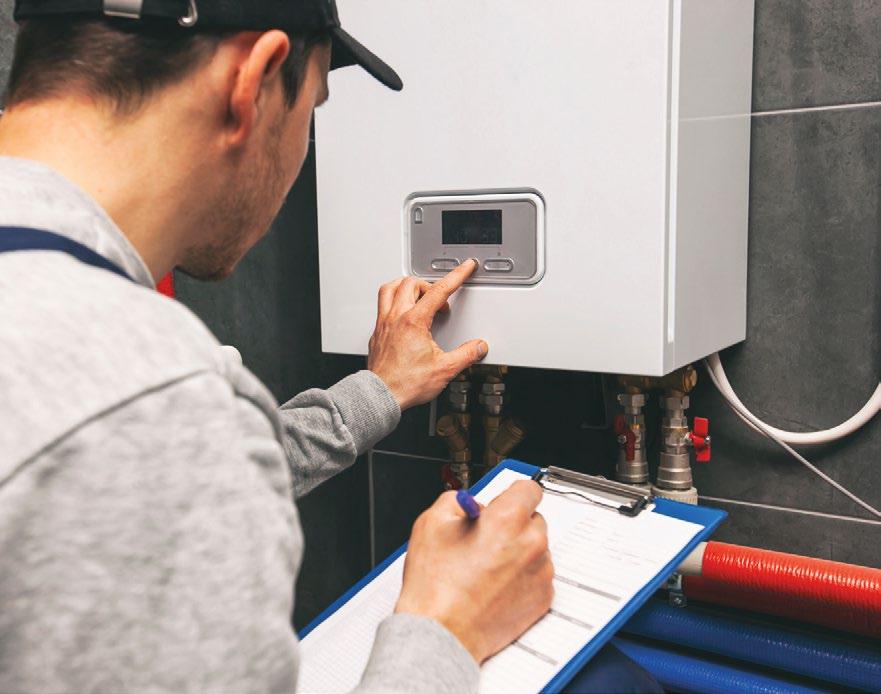
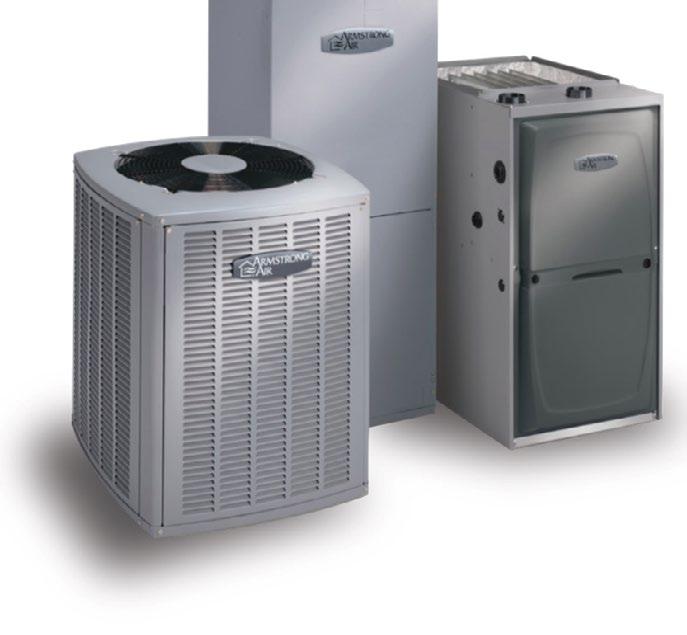
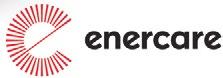
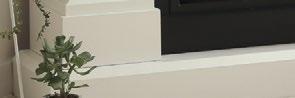
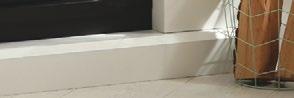
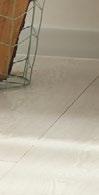
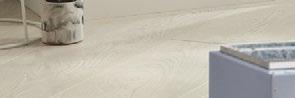
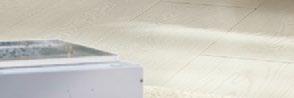
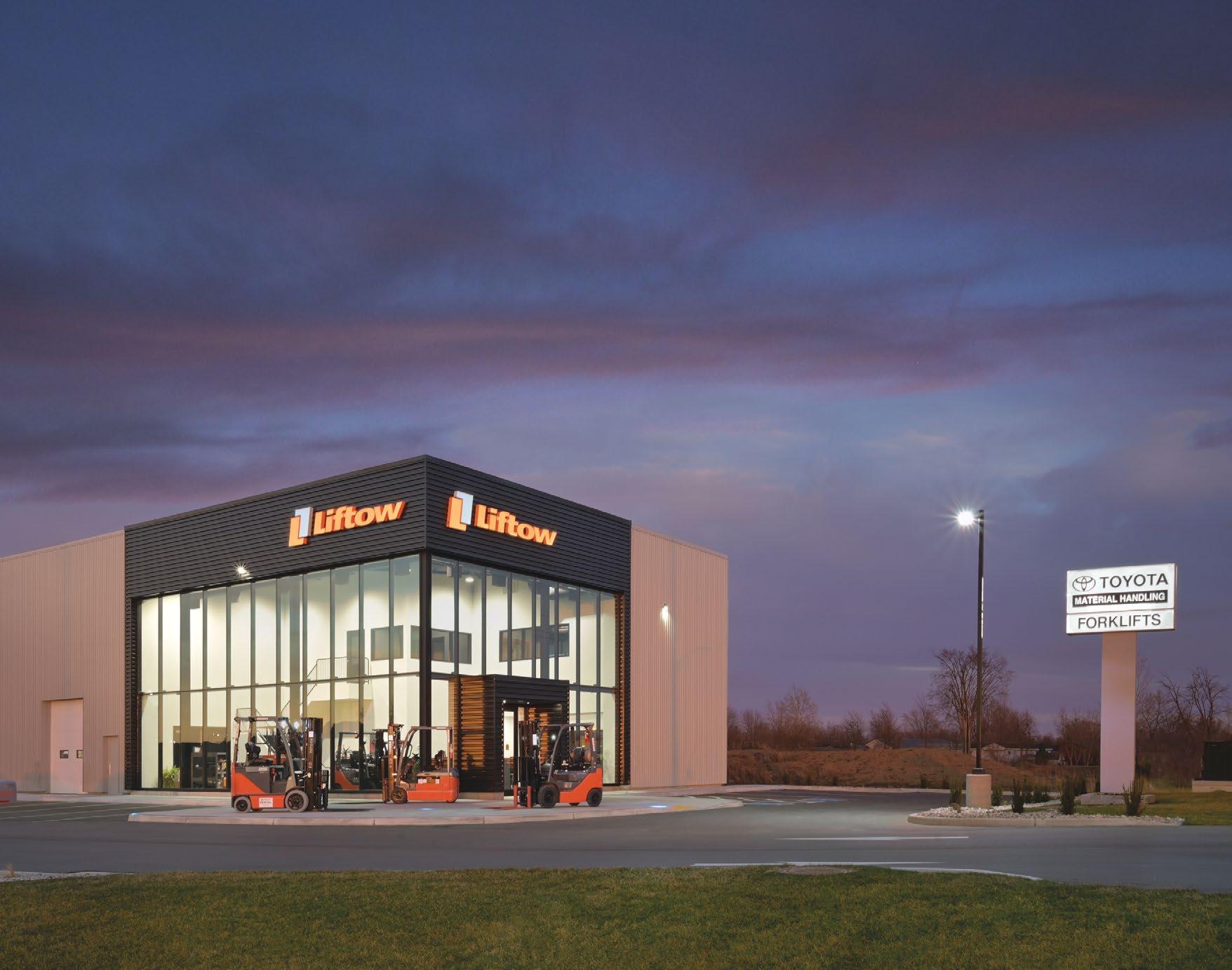
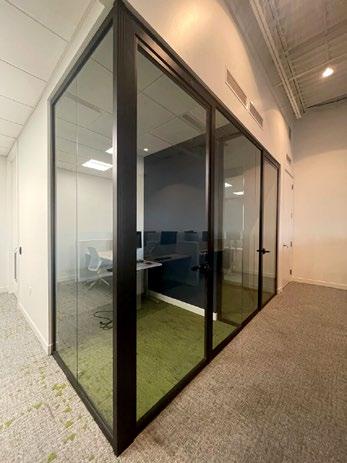
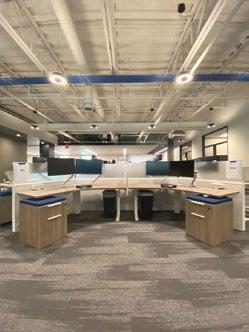
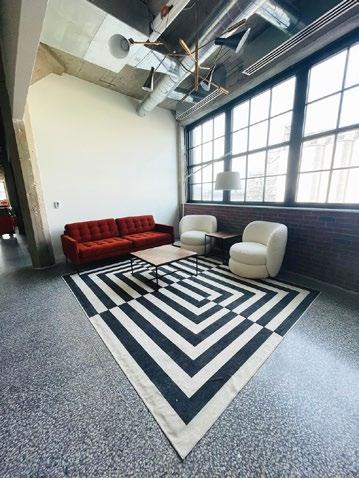
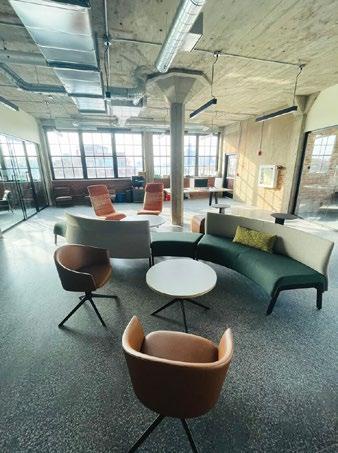
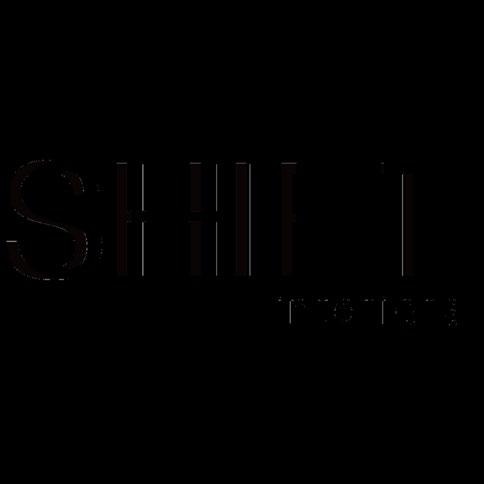
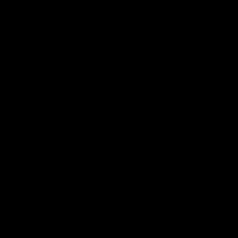
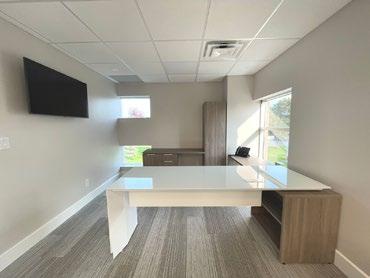
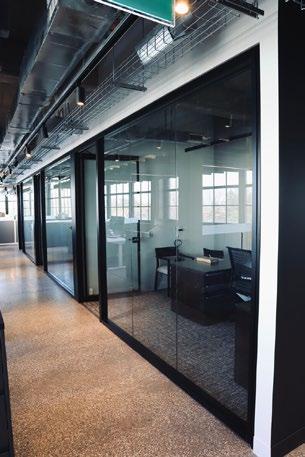

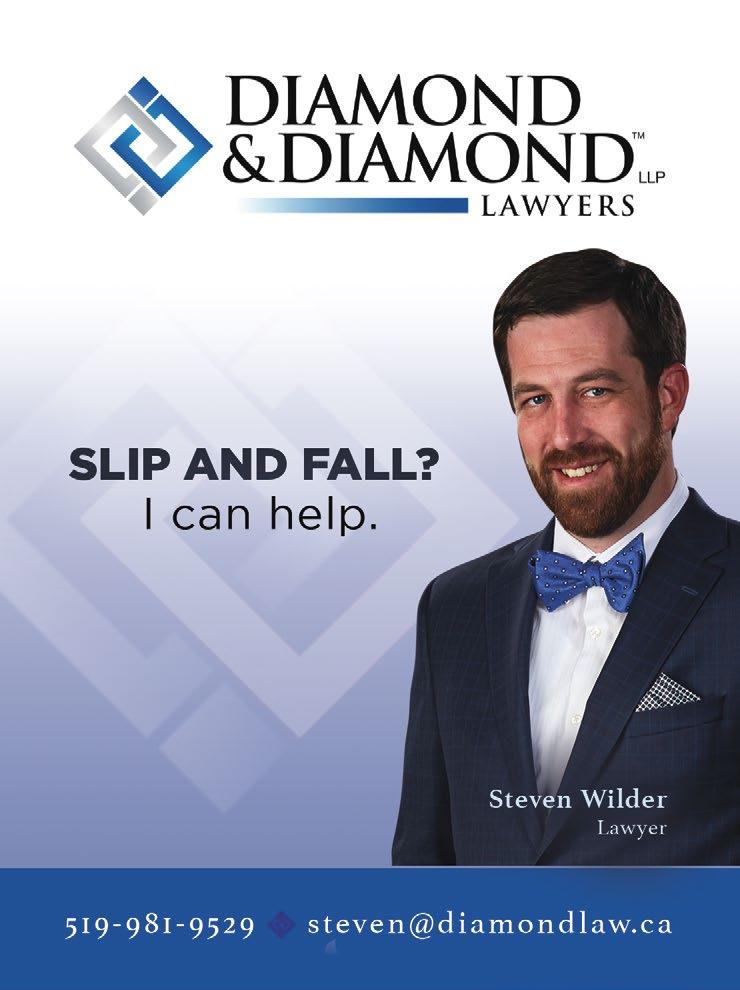
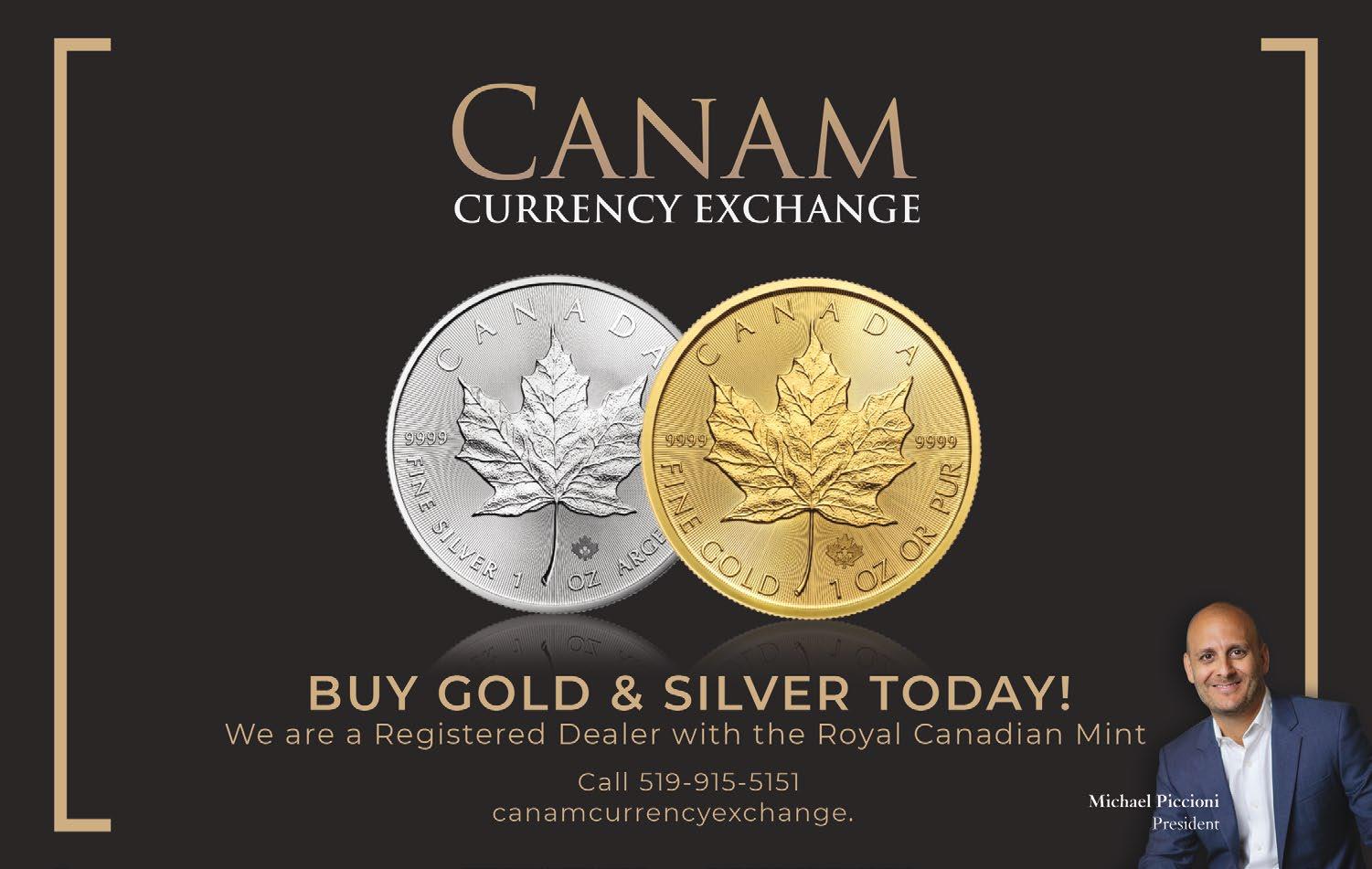

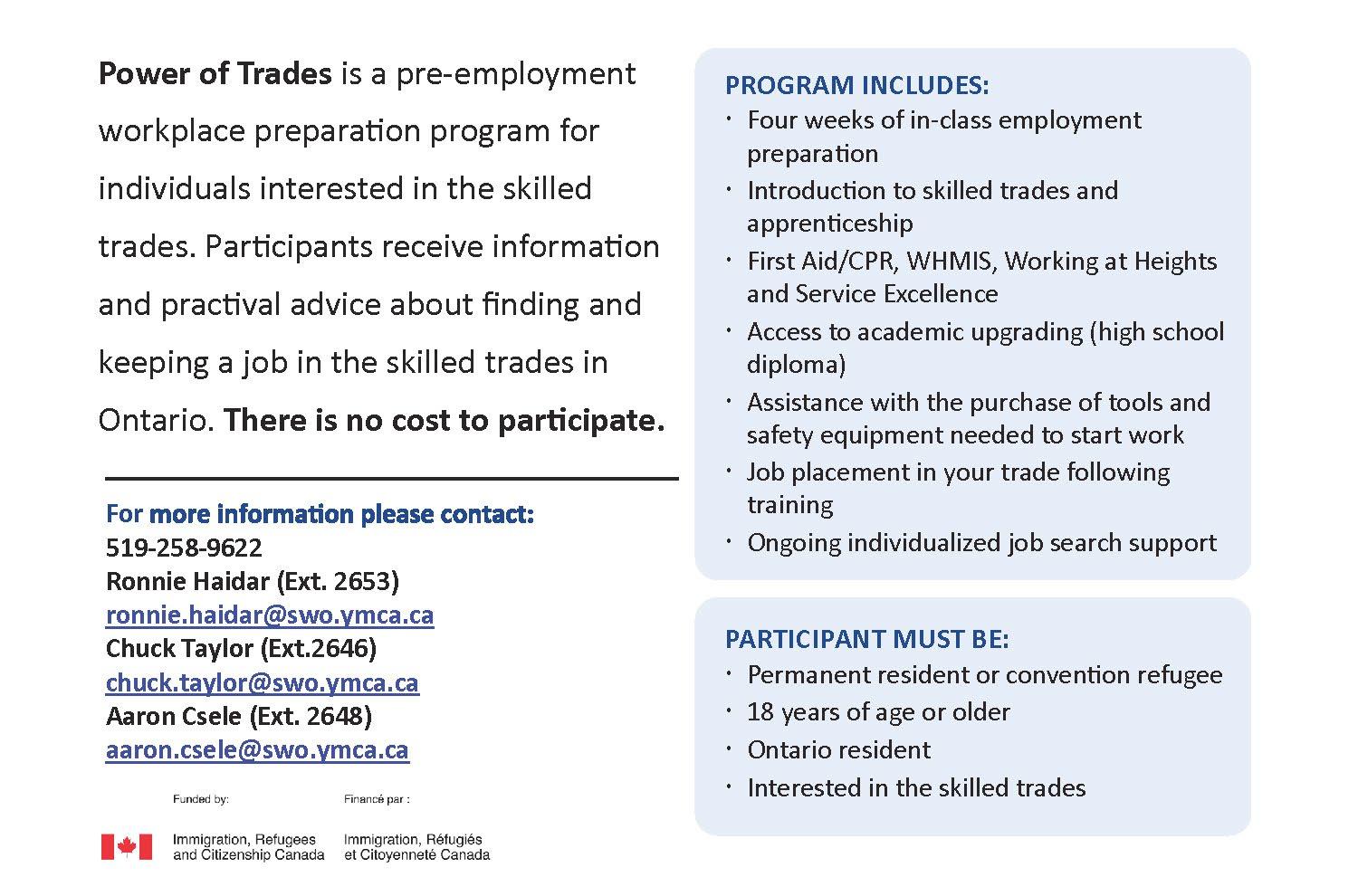
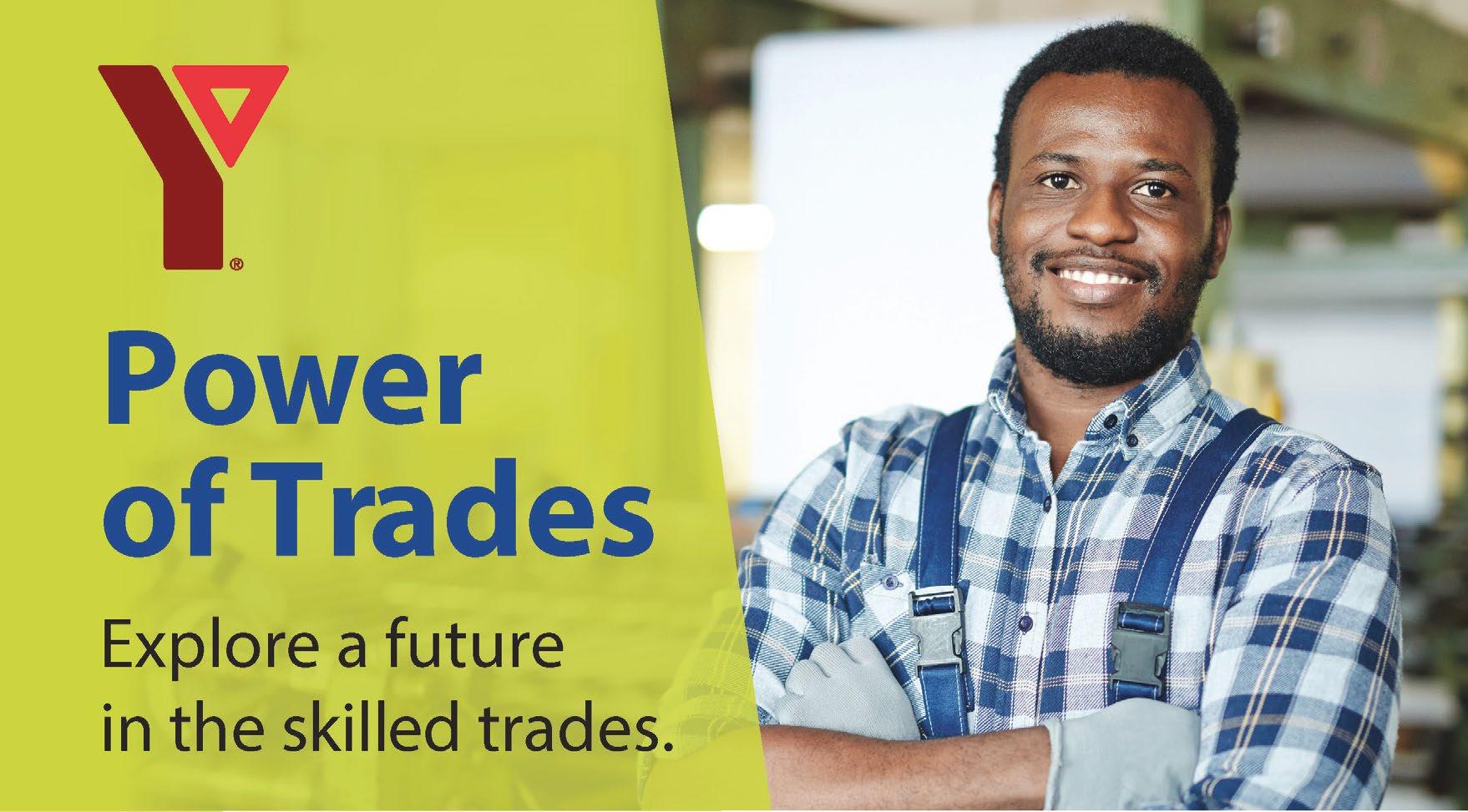
Framing in the Future at the Carpenters Local 494

Enhanced Construction students learn from industry professionals at Local 494.
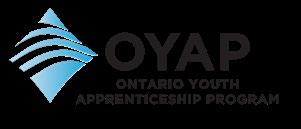

Some of the students who come here are from schools that have no tech. They are here for one semester and during that time we teach them as many applicable skills as we can.”
For the past three years, the Carpenters Local 494 in Oldcastle has been a training center for high school students enrolled in the Enhanced Construction Program through the Ontario Youth Apprentice Program (OYAP).
“This semester we have seventeen students,” says Logan Kane, Training Coordinator for Carpenters Local 494. “Last year we had thirty-four. In total, we’ve had one hundred and five students come through the program in the three years since it’s inception.”
This course is unique because students learn directly from the construction industry. Being housed in Local 494, the program is always up to date on what is new in industry—whether that is tools, methods, safety—because Local 494 has earned such a good reputation among its contractors.
“Some of the students who come here are from schools that have no tech,” Logan continues. “They are here for one semester and during that time we teach them as many applicable skills as we can.”
Entry into the program involves an interview process, which goes through the course’s teacher Mr. Trent Durocher who has been a teacher with the GECDSB for fifteen years. Students’ grades are looked at, as well as their attendance.
“The most important quality students bring with them is their attitude,” Logan says.
Not all of the students aspire to be carpenters. Some of them train at Local 494 just because it is a tech course. They receive safety training and see the course as a good way to enhance their resume.
“The contractors have been really supportive,” Logan explains. “They are responding to the students very well. Some call and ask specifically for co-op students. The kids are eager to
learn and haven’t picked up any bad habits yet. The contractors see this as an opportunity to train them the way they want. The students enjoy the co-op placements because they’re doing actual work and adding to their skill sets.”
The only issue the program has had is with parents not understanding the apprenticeship process. Nobody is saying to the kids “Don’t go to college or university,” but it is important that students know there is another route toward a satisfying career: namely, through apprenticeship.
“After many years of people looking down on the trades, we’re finding that the attitude toward them is changing,” says teacher Trent Durocher. “We were recently at a Pathways Night at Massey high school and we had parents asking if they could submit resumes at Local 494.”
The OYAP program is particularly beneficial because it gives students a chance to try out some trades without being locked in. If they choose one direction, but decide it is not for them, they can simply choose another.
“This program started at Local 494 because we didn’t want kids going out to co-op placements and just pushing a broom,” Trent explains. “With this program the students go out to contractors with tools lent to them from the school board, so they are productive.”
He continues: “There is a big advantage to being here. If there is new tech in industry, we know about it the next day. We can teach it the next month. Our students are very current with what is happening in the industry.”
There is also room for students to make mistakes. Many who enroll may not know much about tools or building.
“We all make mistakes,” Trent says. “As long as you’re working safely, mistakes are learning opportunities.”
Kyle Côté is a student who has gone through the program at Local 494 and is now working in the field. A friend of the family recommended the program to him.
“I started in grade ten,” Kyle says. “The course was challenging and interesting enough. I felt welcome in the training program and with the contractor where I was placed.”
He continues: “Today we were putting up concrete footings. I helped with pouring concrete and forming it with two-by-tens, then reinforcing it with rebar. I was cutting a lot of the wood, helping wherever I could help. It looked good when it was all finished.”
Kyle also gained experience working with a cabinet maker during his time in the program.
“The program is amazing! I would take it again,” he says. “You learn a lot. The teachers are awesome there. The training we get really helps you with your future. I have eleven certificates: first aid, scaffold, hoisting and rigging, forklift, elevated platform, and others. I’d recommend this program to anybody who is interested in the trades. Even if you’re not interested in carpentry, but maybe an electrician or plumbing. You learn these skills and make connections that can help down the road.”
And it is never too early to have a look at the trades as a career option.
“This past semester, we started a seventh-grade outreach,” Trent says. “We showed students some skilled trade activities, like framing in a wall using hot glue, cosmetology, changing a tire, and even a chef’s challenge. We tried exposing them to skilled trades. We had seventeen grade schools here —approximately thirty-five students per school—and we’re not done. The kids loved it.” W.E.
One Woman. One Step. One Movement.
What’s more bad ass than a woman knowing what she wants? A woman getting what she wants, that’s what! Society often tells stories of the women who came before us, those trailblazers who have paved the way for others, well like it or not Shanna Hodgins is one of those women. Intrigued with the opportunity to become a mobile crane operator, she thought about it, for a minute, then went right after it!
By Devan MightonJust a few short years ago, Shanna was working as a sales representative for Moir Crane, travelling from job site to job site. For Shanna to sell, she needed to understand more about the product. Understanding this, the crane operators offered their help, allowing her to understand more about the machines. What happened instead was not what she was
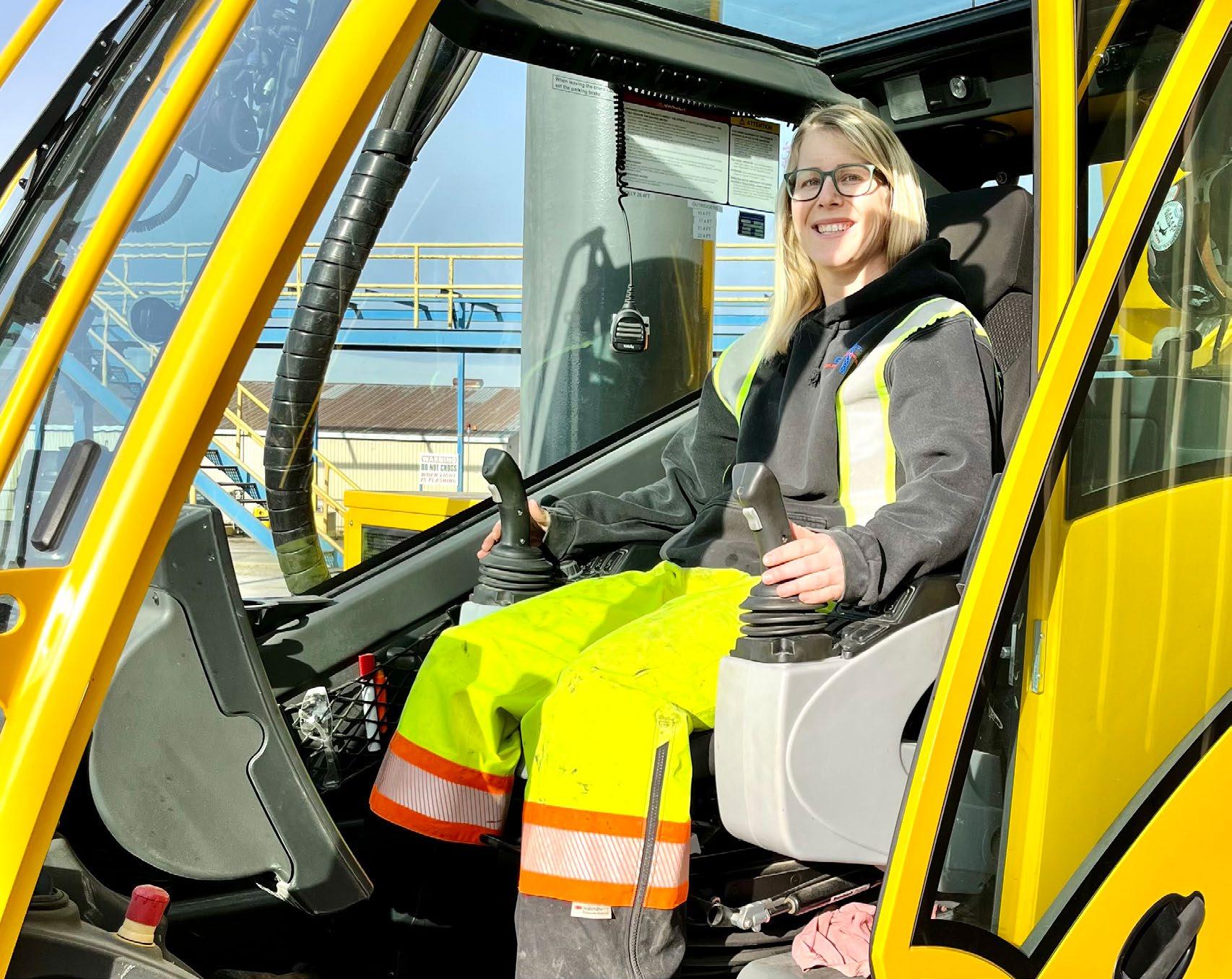
Every time a woman steps into a skilled trade, its another step forward for all of us.
A positive story of one woman’s curiosity.
expecting. The more Shanna learned about the cranes and how they operated, the more questions she had about the job. She learned that like most skilled trades, crane operators make a good liveable wage, good benefits and a pension. She started to believe maybe this was something she could do for herself. In her 30s, with a family to consider, she wanted to know more. So where does someone wanting to be a crane operator begin?
There are a few options when looking for an apprenticeship in any skilled trade. You can go directly to the union or you can find an employer in your field willing to take you on as an apprentice. There, they will train you and sign off on your hours. You learn by working under a licenced tradesperson and while you’re working you are earning a good wage. If you play your cards right, a young person straight out of high school can finish an apprenticeship before the age of 25. For Shanna’s particular skilled trade, it takes 3 years or 6000 hours of working under a licensed crane operator, along with 12 weeks total of schooling. Once completed, the apprentice is responsible to write a test in order to receive their licence. Sounds great, right? So why aren’t more women taking advantage of these opportunities? What does it take, as a woman, to be in this industry?
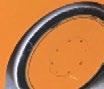













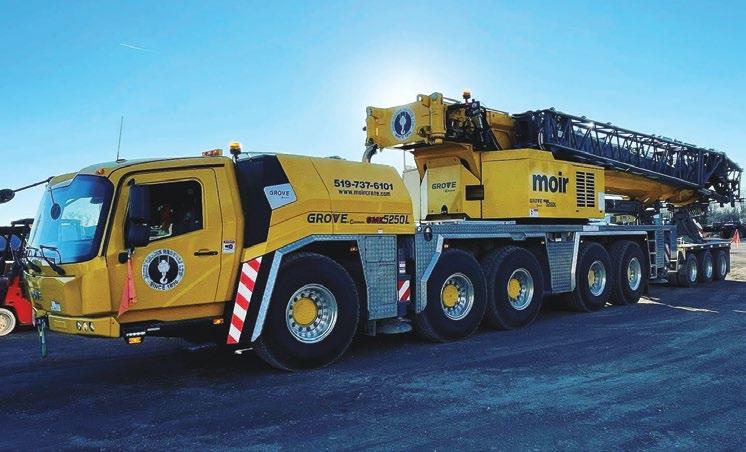
“A strong mindset and a healthy dose of problem-solving skills,” says Shanna, “the job itself is teachable.” She believes that being a woman in a male dominated industry can be an advantage. “I may be physically weaker, but I bring more to the table as a multi-tasker and problem solver.” Shanna knows that having a “good mentorship, someone who really takes you under their wing and teaches you,” makes all the difference in a person’s experience as an apprentice.





Shanna says “100%,” she would encourage young women to explore their options in the skilled trades. There are countless opportunities. Welders, boiler makers, millwrights, electricians, mechanics, woodworkers, heavy machine operators and let’s not forget the secondary jobs that are related to skilled trades. These jobs are readily available, most with 6-figure incomes, pensions and benefits, all giving someone, including women, a secure future.
Shanna wants young women to “try a little bit of everything,” until you find what you’re interested in. “At first it might be hard, but be strong and focus on the work, if I can do it anyone can.” In the future, she hopes high schools will start offering more workshops and opportunities for young people to explore their options in trades. “Offer a 1 week program in different trades, to give kids choices.” This could certainly give young people a leg up when deciding their future. There are, after all, 140 different trades to offer in Ontario alone. Shanna is a year and a half into her three year apprenticeship and she enjoys every minute of it. Her coworkers at Moir Crane are patient, kind and encouraging. The opportunities are endless. W.E.

ENWIN Self-Healing Grid Automated Feeder Ring Project.
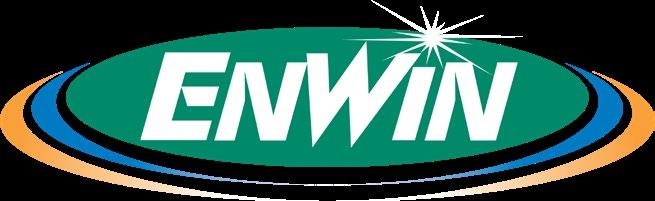
Mitigating the inconveniences of power outages to Windsor’s customers.
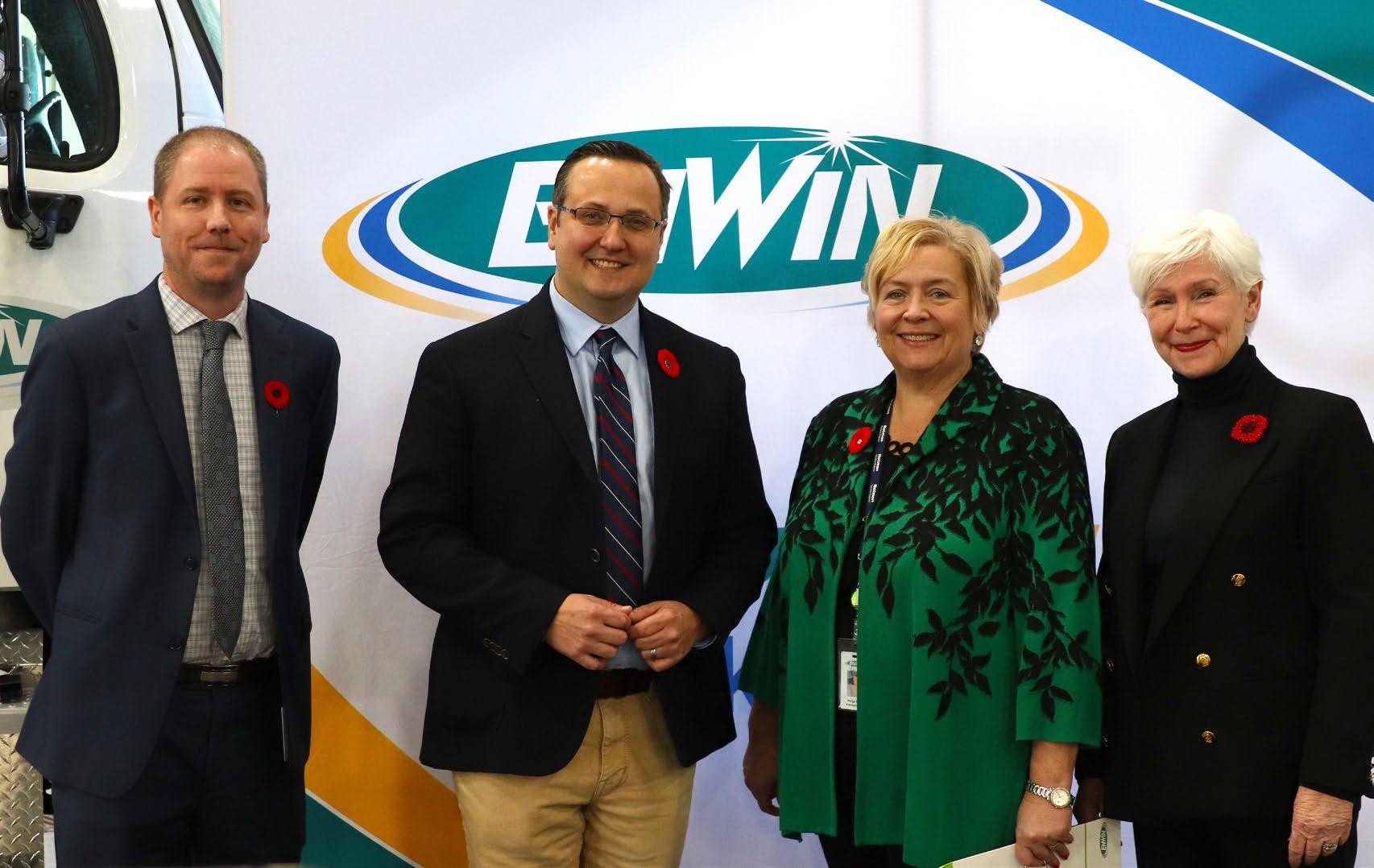
Story and photos by ENWIN
Extreme weather conditions can often lead to power outages. Whether they are caused by an ice storm, windstorm, or thunderstorm, it’s no secret that power outages are a major inconvenience for many of ENWIN Utilities Ltd.’s (ENWIN) customers. This ongoing issue has sparked ENWIN towards the investment and development of a Self-Healing Grid Automated Feeder Ring Project, a solution that will help mitigate the negative impacts of power outages on the community.
A feeder ring is a special configuration of the electrical distribution system where the high-voltage feeders start and finish at the same point, thereby forming a ring, instead of a conventional linear configuration. This ring configuration enables an automated isolation of a faulted section of the ring while allowing the other parts of the ring to remain in power.
The ENWIN Self-Healing Grid Project is focused on implementing two automated feeder ring systems within the City of Windsor. When a fault occurs, smaller feeder sections will be automatically isolated by protective devices on the grid and only customers within the faulted section will be impacted. In other words, outages that normally affected thousands may only affect hundreds.

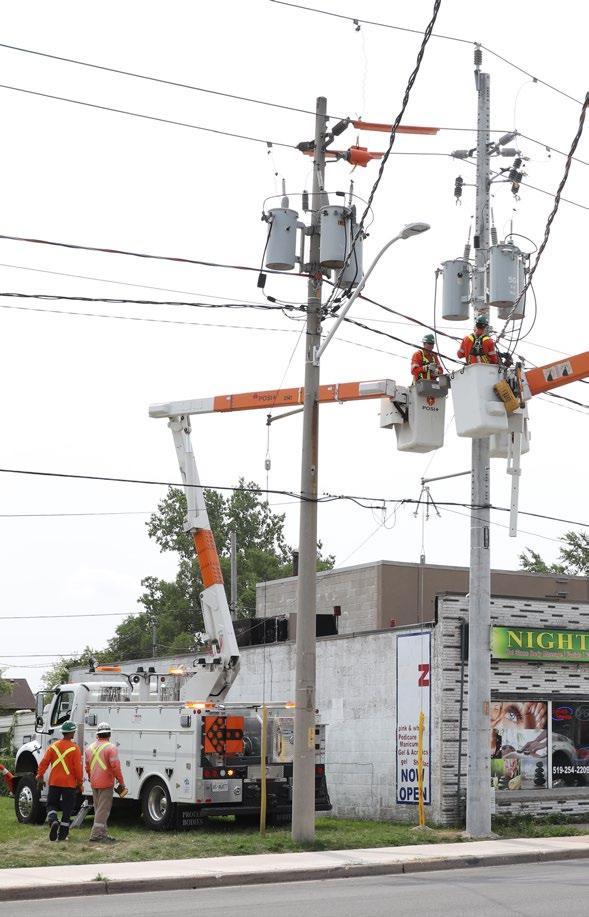
In November of 2022, it was announced that ENWIN would receive funding for this project in the amount of $800,000 from the Federal Government through Natural Resource Canada’s Smart Renewables and Electrification Pathways Program.
According to the Honourable Jonathan Wilkinson, Minister of Natural Resources, “By investing in the modernization of our grid infrastructure, the Government of Canada is supporting Canadians in reducing emissions, accessing reliable clean energy and strengthening the energy security of our electricity system. This project will strengthen the resiliency of Windsor’s grid while creating sustainable jobs.”
Including contributions from ENWIN Utilities, the total investment in this project is estimated at $1.6 million. The self-healing grid will provide service with no incremental cost to customers served by the self-healing grid and allow them to further benefit by avoiding other costs associated with long power outages such as indoor lower-level flooding, loss of perishable foods, loss of potential business, and general inconvenience. Additionally, not only will the system allow for the continuation of power for people served in unfaulted sections, but it also allows any solar generation connected to those sections to continue to produce renewable power.
The self-healing grid will also improve the reliability of the two automated feeder ring systems as the number of outage hours will lower for areas where the ring sections are unaffected by the cause of the outage.
The successful completion of this project will benefit nearly 5,000 residential and commercial customers within Windsor-Essex. This innovative system can also be leveraged in other regions to create similar self-healing grids.
“Investing in grid modernization technologies is a key part of securing a prosperous net-zero future for Canadians,” says Irek Kusmierczyk, Parliamentary Secretary to the Minister of Employment, Workforce Development and Disability Inclusion and Member of Parliament for Windsor-Tecumseh. “The Self-Healing Grid project will reduce greenhouse-gas emissions, improve renewable -energy capacity, and keep electricity reliable and affordable for Windsorites. This is another investment in Windsor–Tecumseh that creates sustainable jobs, tackles climate change, and makes life more affordable.”
With plans to be implemented by 2025, the Self-Healing Grid Automated Feeder Ring Project will provide immediate benefits to customers and is also part of ENWIN’s larger plan to create a “smart” grid. As part of ENWIN’s vision, this grid upgrade will include additional features such as remote sensing of grid conditions and rapid system reconfiguration. This new technology will also reduce customer outage times for customers served by unfaulted sections, from a few minutes to a few seconds, allowing for an overall decrease in the inconveniences that power outages cause.
According to ENWIN President and CEO Garry Rossi, “ENWIN’s goal is to provide the community with safe, reliable electricity, especially in times of need. With this project, we are confident that this is one of the first steps in the development of solutions to further strengthen our system and prepare it for the future, including further electrification, all for the benefit of the City of Windsor and its residents.” W.E.
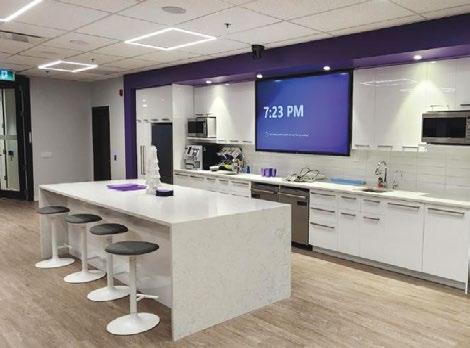
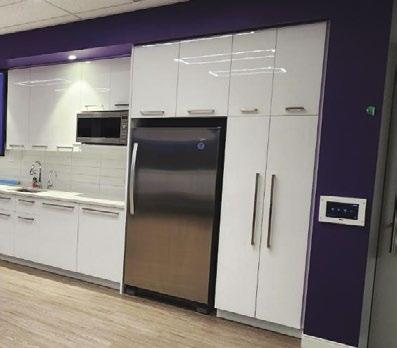
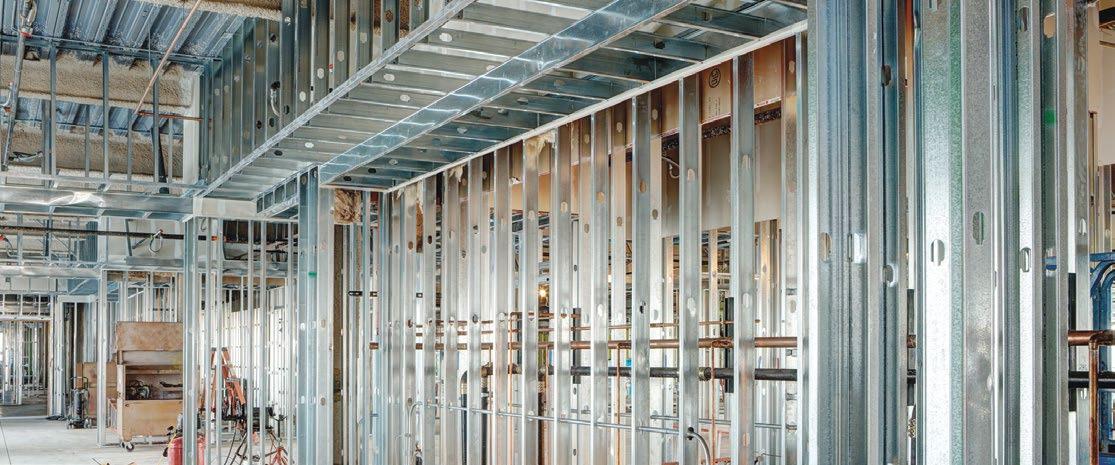
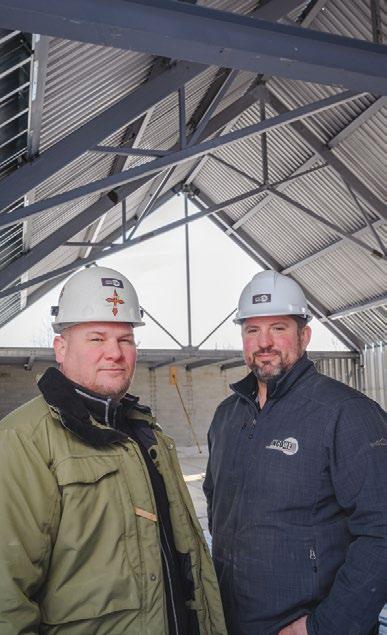



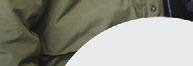

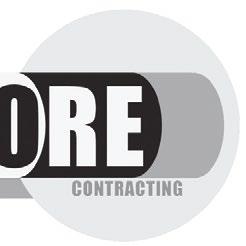
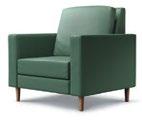
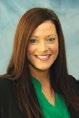
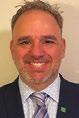
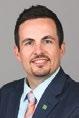

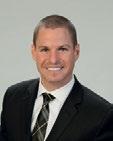
Think globally, act locally.
Creating new solutions as the automotive industry evolves.
Working alongside the auto sector to revolutionize the future of the automotive industry by improving how cars are produced.
These are just some of the ways UWindsor Engineering is designing the future.
uwindsor.ca/engineering
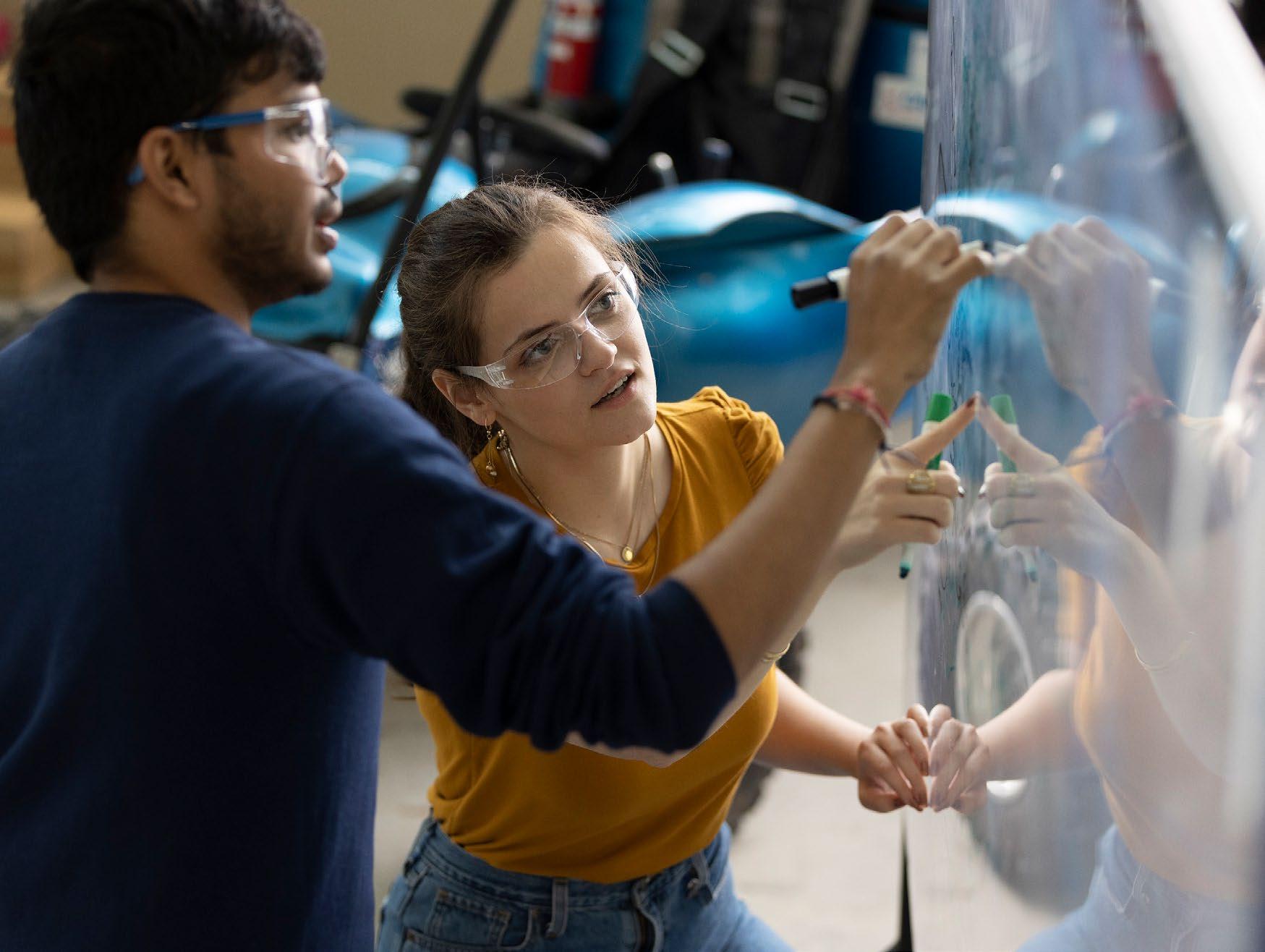
Get it Built by SHIFT
By Devan MightonHow do you expect to get work done if your workspace doesn’t inspire your headspace? Do you need a collaborative work environment, or maybe a quiet one built for introspection? Will your workspace meet the needs of your company’s future?
Steven Pressacco along with his wife and business partner, Wendy Furtado-Pressacco, want you to maximize your business’s potential with their contract-furniture and architectural interiors dealership— SHIFT Interiors.

“Office design is more than just desks and chairs,” explains Wendy. “We’re able to provide tailored solutions to each client to fit their needs and goals now—but we’re also thinking about the future. How are our recommendations today going to work if a client needs to reconfigure their space, or hire more people or move offices in the future?”
Growing up in Windsor, Steven long held a passion for the hospitality industry, working in some of the city’s most beloved establishments. Steven attended St. Clair College for mechanical engineering, completing his degree at Saginaw Valley State University. He then took a job at Chrysler, before jumping to a technical sales job in Michigan selling valves, controls, and regulators. After moving to New York City, he discovered the world of contract-furniture and was inspired by the need to create functional spaces in the ever-changing work environment. Steven met Wendy, originally from the San Francisco Bay Area, in New York, where she had just left her online marketing position at LVMH to pursue a career in special education.
Steven was going places. He was promoted to sales and upper management for a Canadian-based contract-furniture and architectural interiors manufacturer called Teknion. As he rose through the company, Steven and Wendy travelled the world, including spending prolonged periods in Malaysia, Singapore, and Northern California.
“What’s different about Teknion is that they make 90 per cent of their products,” states Steven. “Not a lot of manufacturers can actually say that. A lot of manufacturers just assemble their products, but Teknion manufactures it themselves.”
In 2020, the couple moved from California to Windsor, bringing Steven home for the first time in 13 years.
“Why wouldn’t you want to live in Windsor?” asks Steven. “The peo-
ple are nice, the weather is mild, there are always events going on. We have a major city, Detroit, right next door— there’s a lot of opportunity here. No matter where I’ve lived, I’ve always been proud to call Windsor my home.”
A year later, Steven and Wendy launched SHIFT Interiors—a Windsor-based contract-furniture dealer that distributes Teknion solutions, as well as products from dozens of other contract-furniture lines. Since launching, they have installed glass and demountable walls as well as furniture in offices, schools, and hospitals across Windsor-Essex and Southwestern Ontario, and have partnered on several large-scale projects in the United States. By collaborating closely with their clients, they have been able to achieve their goal of creating beautiful, functional, and dynamic spaces.
Having outfitted hundreds of offices around the globe and recognizing the potential of the Windsor-Essex market, it was only fitting that Steven found himself back in the contract-furniture world, this time, in the form of owning and operating a Teknion dealership with Wendy.
“I truly believe that Windsor is one of the best places to start a business,” states Steven. “We have such a supportive community and the response to our entry to the local market has been overwhelming. Amazing things are happening in Windsor: the new bridge, the new battery plant, the new hospital. As a border city, more international companies are recognizing the benefit of doing business in Windsor.”
Wendy, who, during her downtime, volunteers with the Windsor Public Library and is on the board of Art Windsor-Essex, says that every project they encounter is different. “We’re coming in at different points along the process, so we meet clients where we need to,” she says.
Wendy says its important to meet with the client in their space, to fully understand their needs. “Every client is different, every project is different, and everybody using the space has different needs and goals,” she explains. “We want to understand what a clients business outcome desires are and help them to achieve that with their space. Steven and I compile all the information that we’ve gathered from those conversations and meetings and work through the space planning and designing with our technical designers. A lot of times, there’s some back-and-forth with our clients to make sure we’re tailoring the perfect solution. It’s important that our clients have a space that functions for them.”
SHIFT Interiors comes along for the entire process, from design to installation, and plans for your workspace’s future.
“Companies are always shifting and changing,” says Steven. “So, when we are prescribing these solutions, the idea is that they can grow and shift and change with our clients. We’re there on Day 2 if a client wants to add a space or if walls and furniture have to be reconfigured to accommodate their changing business needs.”
Steven says SHIFT Interiors is here to help your company grow.
“Regardless of how many people are in the office at a time, business and corporations need a place to call home and employees need a place to come together to work and collaborate and build brand identity. It’s more important now than ever to create spaces where people want to gather,” states Steven. “Companies need to invest in spaces that can attract and retain talent. There’s an appeal to working for a company that invests in the ergonomics, aesthetics, and functionality of their offices. Ultimately, it’s an investment in the well-being of their employees.” W.E.
builtbyshift.ca @builtbyshift
Tirecraft brings the experience and care so you can keep it local.
Owner Erik Smith talks coming up in tire industry, growth, and doing it right.
By Devan MightonWhen Erik Smith says he has experience in the tire industry, he isn’t joking, and after a lifetime of learning the game from the ground up, at Windsor Tirecraft at 3800 Webster Dr. in Windsor, he has the location, the services, and the staff it takes to give you the automotive and commercial tire experience you need.
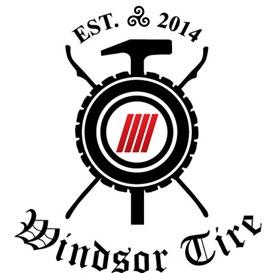
Smith started changing transport truck tires at 16 years old while he was still going to school. “I was changing tires on the side of the road for a lot of years—and did emergency night calls,” he recalls. Eventually, the company he worked for was sold and he was given the opportunity to join the sales staff. After six years, he walked away and partnered at Windsor Tire, Inc. and, in 2018, bought out his partner.
“Tirecraft is a group of independent tire dealers that joined together to make a group to combat against the big corporation stores,” explains Smith.
“Everyone who is involved in Tirecraft owns their location, but because we’re heavy into the commercial trucking industry, if there is a truck driver coming from North Bay to Windsor with a blown tire, there’s a Tirecraft here he can deal with just like there’s a Tirecraft in North Bay.”
Windsor Tirecraft offers a wide variety of services for their customers. On the commercial side, they offer 24-hour service for transport truck companies, on-site mobile service for construction companies and farmers, and tire pressing services for forklifts in factories. When it comes to mechanical work, Tirecraft provides full engine diagnostics, brakes, suspensions, alignments, tires, and oil changes. They are also a leader in aftermarket accessories, offering wheel and lift kit packages that have become quite popular.
Smith says that what sets his company apart from his competitors is the level of experience and amount of caring among his staff.
“With our commercial division, everyone that is in a leadership position has done the job of changing tires before,” he states. “Whether it was the giant earthmover tires, forklift tires, Bobcats, backhoes, farm equipment, everyone in a management or sales
position has done the job before. We have tons of experience, and the management team isn’t afraid of jumping in and getting dirty when we are slammed with business.
“With our service technicians, I have the most amount of service trucks on the road. I have double of what my two main competitors have combined. In our commercial division, we’re extremely service oriented—which is everything nowadays.”
He says that on the retail side, his mechanics have roughly 50 plus years of experience between them, and that his service advisors have grown in the business from the shop floor to the front desk. Why shop for tires at a big box store whose staff are typically shuffled from one department to another with no continuity, and minimal knowledge? Tirecraft invests heavily in continuous training for all departments of the business and believes in long term relationships with its customers.
Smith explains that they are a company that cares—both about their customers and their employees. He says that before going out on his own, he experienced a boss that was stingy and treated his employees terribly, and he has learned from that. Service guys on mobile service get to bring home
their work trucks, phones, uniforms, and boots are paid, employees on night call get paid 50 per cent of the labour charge, while Tirecraft’s competitors only pay 30. Then there are the small details, like the staff receiving cash bonuses, Under Armour hoodies, and personal cars fixed at cost.
Smith grew up changing tires for almost 20 years, he gets it. He knows what it’s like to work for a living and just scrape by. “I spent a lot of years working days and nights to provide for my family. It has given me a unique perspective as a business owner to understand what my employees go through. It also gave me a special understanding of what customers truly value. Which is service, dependability and affordability.”
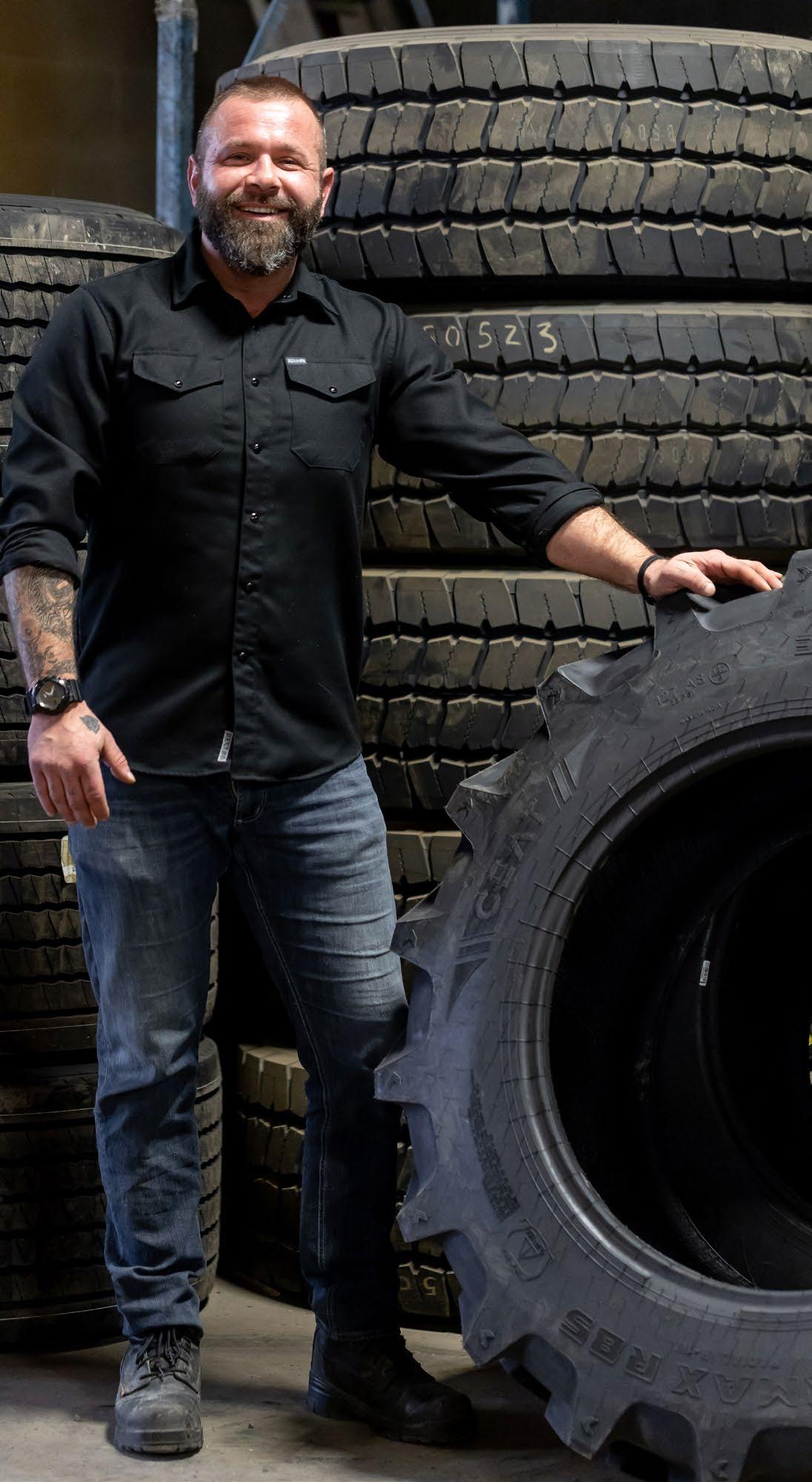
His loyalty to his employees has paid off for him. With steady annual growth, he has expanded his business from 18 to 31 employees since the start of the pandemic.
“They see how I treat them and they know what else is out there in this industry for them—they watch my back quite a bit,” says Smith, and he admits that after years of pounding the pavement and working long hours and as an active single father of three, taking night school classes, all while running Tirecraft, it is nice to have peace of mind when it comes to his staff and business.
Smith continues to look toward the future, adding more apprentices, another licensed technician, more hoists, newer equipment, a new alignment machine, as well as a touchless tire machine for high-end and after-market rims. He says that he is always looking to expand and is currently looking into adding to their fleet of commercial service trucks and maybe a mobile heavy mechanical truck.
“We’re looking to grow,” states Smith. “I’m at the point now, with having my management team around me, I can step back from working in the business and start working on it and figure out where our growth opportunities are.” W.E.
Keeping It Local, Because It’s Worth It
Why entrepreneurs are sticking with Windsor-Essex.
By Devan Mighton Photos by Dave HunterNaturally, businesses need to branch out. Whether it be to find affordable locations, skilled labour, or better access to investors and materials, companies, as they grow, need to find what works best for them to thrive in the modern global marketplace.
However, there is a growing demand for businesses to support their local communities—through jobs, through feeder industries, and supplying local product to local consumers.
These three entrepreneurs, representing Windsor-Essex County have done what it takes to not only grow, but to thrive in their markets and, most importantly, keep it local!
Ameen Fadel, Cedar Valley Selections
While attending Belle River District High School, Ameen Fadel, a Gr. 10 student at the time, heard over the announcements that the government was giving away $3,000 to 30 business-oriented students to start their own company. He was excited about the idea, but what he didn’t have was an idea.
The next day, as he sat with a guidance counsellor, she suggested an idea. Her son played minor hockey with Fadel and reminded him that whenever they held a team party, everyone would always beg Fadel’s mother, Surria, to bring her fattoush salad. She suggested that maybe Fadel should consider bottling his mother’s dressing as a business. At first, Fadel thought the idea was funny, but, suddenly, it struck him that it wasn’t such a bad idea. “I said, ‘There’s no bottled fattoush dressing in Canada, so maybe I’ll partner with my mom and see how it goes.’”
And, a business was born.
In 2017, Cedar Valley’s product started hitting the local farmer’s markets, but since fattoush salad is traditionally served with pita chips, the Fadels started getting asked if they would soon make those too. They acquiesced and another popular product line was born. The next year, their products were in Sobey’s and Whole Foods, but with the whole production still just a mother and son team, with an ever-expanding product line, they outsourced their dressings to a company in London.
“With the chips, we couldn’t find anyone across North America ... to make them, so we decided to take the risk and open up a facility in Windsor and see what happens,” explains Fadel. “In mid2020, we signed a lease for a 5,000 sq. ft. facility in Oldcastle and we turned it into a pita chip manufacturing facility.”
Today, Cedar Valley Selections is available in 750 retail outlets across Canada and will soon be expanding
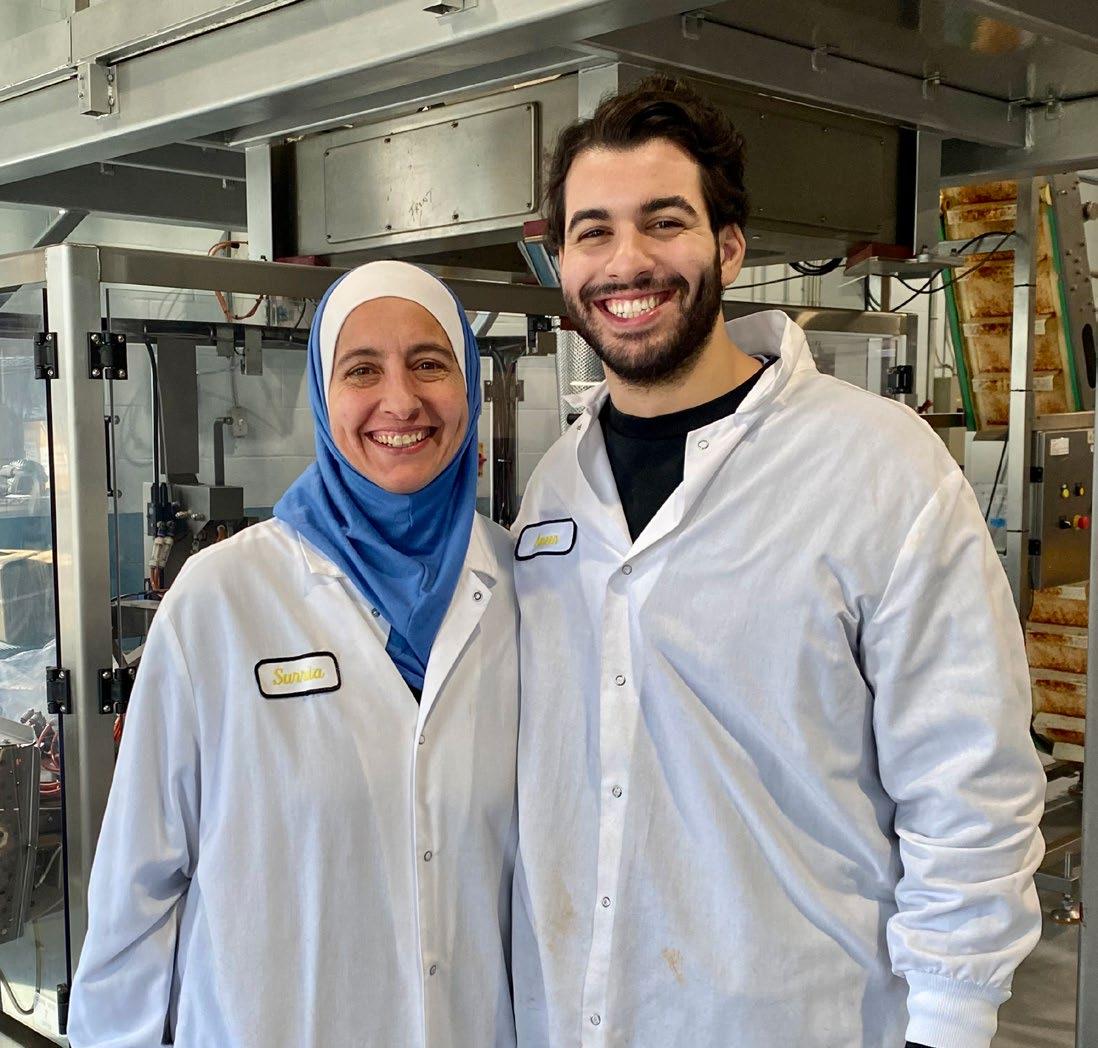
fine balance of ventilation, lighting, and humidity. His goal was for his flora and fauna to thrive, as well, to feel like they were living in their native jungle. For his dart frogs to reproduce, Krol knew that he needed to provide small bursts of fine mist at certain times throughout the day—while he was still at work.
Krol used a mixture of his IT training and biology courses he took in university and fabricated an automated system to keep the dart frog situation in check. As word of his creation grew, he used his business acumen to craft his own business—MistKing.
“Once the news came out that some frog-obsessed guy was making automated misting systems, I started getting contacted by different hobbyists, collectors, universities, zoos, and botanical gardens,” explains Krol. Eventually, he was able to make his hobby his day job. “My then seemingly perpetual and somewhat aimless UofW education of business, IT, and interest in biology fit my business like a glove. I could do my own websites, run my own business, and understand a lot of the biology concepts my customers were talking about.”
further with a few new yet-unannounced partners.
“We have a team of 12 employees working for us in the facility, making all of the product day-in and day-out,” states Fadel. “Now, me and my mom are more in management roles now, working on the growth and the vision of the company—and where we’re going to go next.”
Cedar Valley is just as focussed on staying local as they are going national.
“For us, it’s important because, you see the trend of the market, you’re seeing that consumers want to buy more local and they are supporting more local,” explains Fadel. “There’s not a lot of food manufacturing here in Windsor and we want to be one of the leaders
here and grow our business to show that it’s possible, and encourage other local entrepreneurs to do the same.”
Marty
Krol, MistKing by Jungle Hobbies Ltd.
Marty Krol never saw making misting systems for amphibians as a profession. After picking up business and computer science degrees at the University of Windsor and finishing his Master’s in business IT overseas, Krol was happily working IT at Wayne State University. However, his self-described obsession with tropical environments, orchids, insects, and amphibians like poison dart frogs dominated his personal life. Late into the night, Krol would build intricate terrariums with mosses and orchids as homes for his prized frogs, requiring a
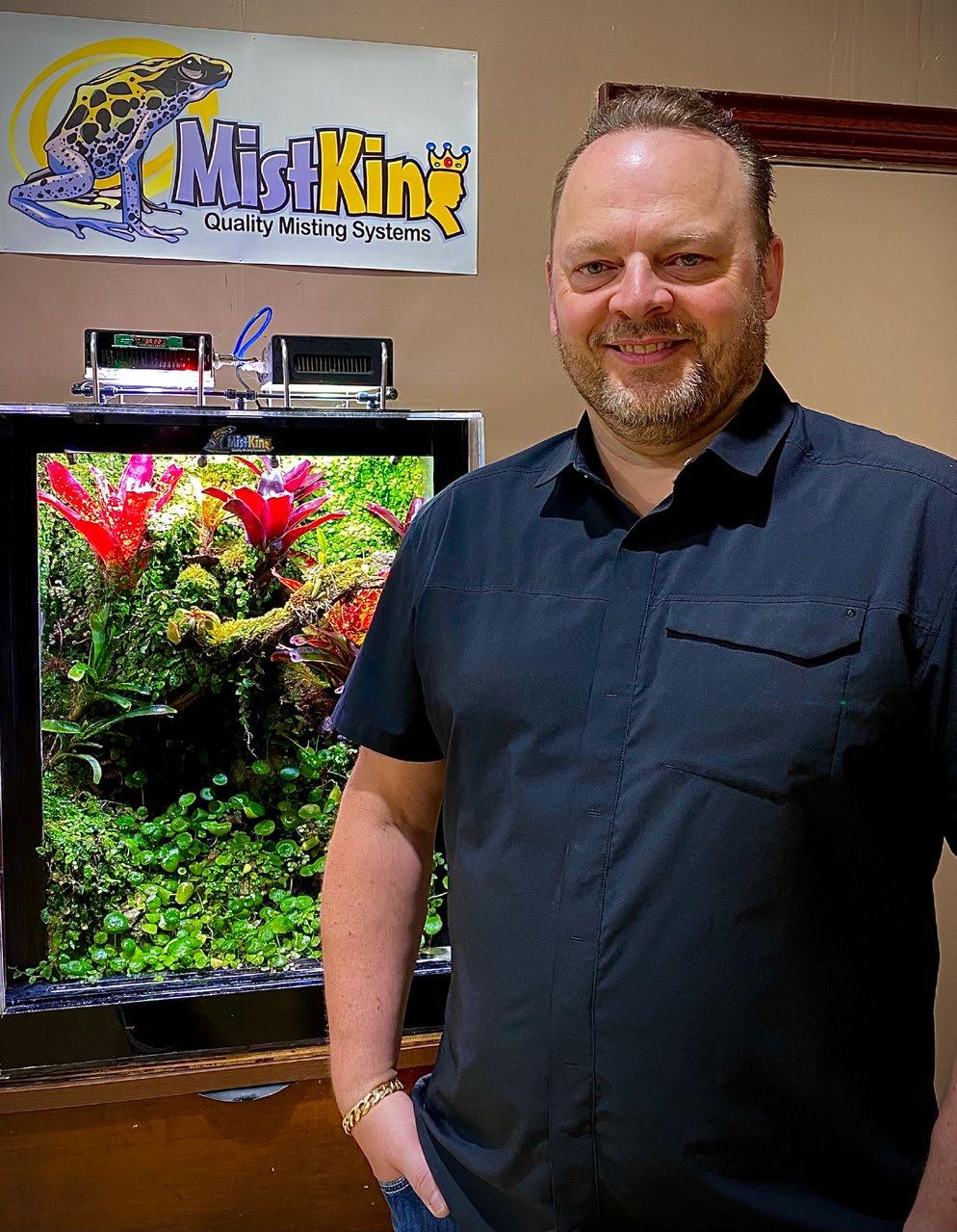
Krol has an extensive list of worldwide clients, like the San Diego Zoo, Bronx Zoo, Smithsonian, Harvard, Stanford, a few museums of natural history, London’s Royal Botanical Gardens, Atlanta Botanical Gardens, the Vancouver Aquariam, and has distributors in the US, Canada, United Kingdom, Australia, and across Asia. Also, MistKing has aided in helping organizations like the Bronx Zoo keep the virtually extinct Kihansi spray toad alive. Now, thanks to MistKing, these near-extinct toads are multiplying and are being bred in multiple zoos.
Through all of this, Krol has kept MistKing local because of his strong personal connection to the area and its place as a manufacturing and eCommerce hub.
“I’m a first generation immigrant and came to join my family in Windsor when I was 14,” states Krol. “A few decades
later, my parents passed away and my brothers moved back, so I’m essentially here by myself with my own family.
“While Windsor may not be a Canadian crown jewel, it is very conveniently located. We are essentially an eCommerce company and rely heavily on courier shipping daily. Having good rates to the USA is vital. Overnight ground shipping all the way up to Ottawa is also a major bonus. I’ve lived in Essex County most of my life, so having a business here works. I don’t know if there is a more strategic location in Canada for an
eCommerce company that does a lot of its business with the USA.”
James Gibb, Affinity Outdoor Living Products
When the COVID-19 pandemic hit in 2020, James Gibb was already 18 years deep into a career in plastics manufacturing. Gibb had spent time in injection molding, thermal-forming plastics, and fabrication—servicing automotive, recreational, and marine applications—and was well-versed in both the manufacturing process and manufacturing systems for plastics.
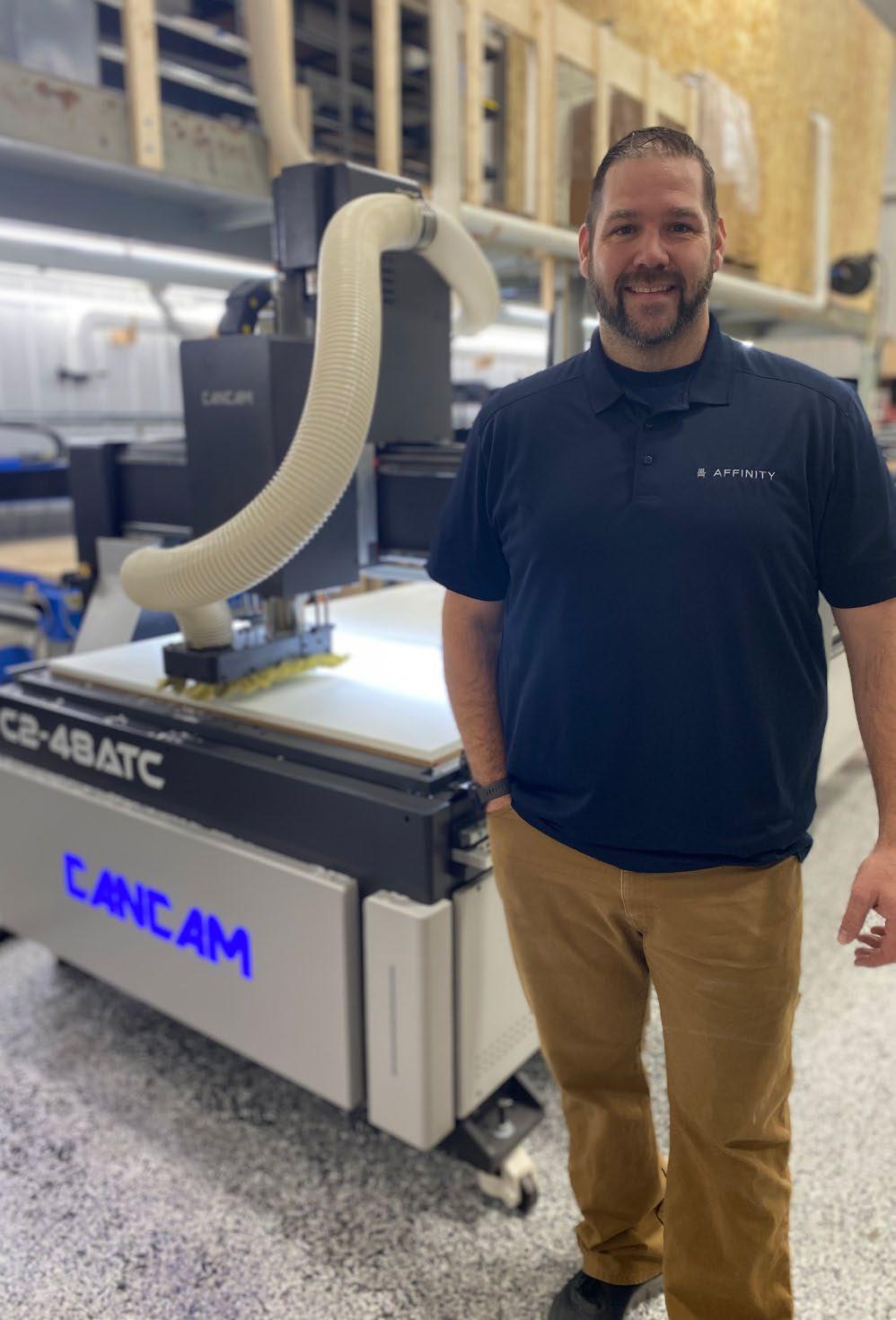
“When COVID started, I had a number of friends and families who owned businesses and restaurants who were reaching out to me looking for COVID plexiglass and lexan barriers,” explains Gibb. “They did not know where to go, where to source these ... and I had a couple people reach out because of my experience and my industry contacts and asked if I could start building something for them.”
Finding his new calling, on Feb. 13, 2021, Gibb quit his day job and pursued Affinity Outdoor Living Products fulltime. His company is predominantly focussed on outdoor living products for both home and business. Twenty per cent of their business is other industries like agriculture and sports and recreation.
“Our success story is our brand recognition,” states Gibb. “Over the past two and a half years of growing the outdoor living products division, we’ve grown our catalog. I started with a custom consignment of a park bench for a client and that park bench is really what started the process of building a catalog of outdoor living products.
“In the past 30 months, I’ve grown the catalog to over 30 products that are designed, ready-built for sale that we sell-direct, as well as through a network of dealers and resellers throughout Ontario and expanding into the US now.”
Gibb explains that keeping the business local has aided in their success.
“We have the skills, the knowledge, and we’re a manufacturing hub of Canada and, honestly, North America,” says Gibb. “We have the people, we have the brains, we have the know-how to do a lot of stuff in this area. This area, from a manufacturing standpoint, has a very deep, strong history of people with capabilities. When I look at Windsor-Essex, for me, growing the business here, it’s very vital to be able to supply throughout Canada and, as well, into the US.” W.E.
Are you looking for a dynamic career that is in high demand? Look no further than St. Clair College. Our exceptional faculty provide top-notch, in-class and hands-on learning to ensure you have the skills and knowledge needed to succeed in the manufacturing industry. Our programs offer apprenticeships and earn-while-you-learn options for added hands-on experience. Let St. Clair College be your launching pad for a successful career in manufacturing.
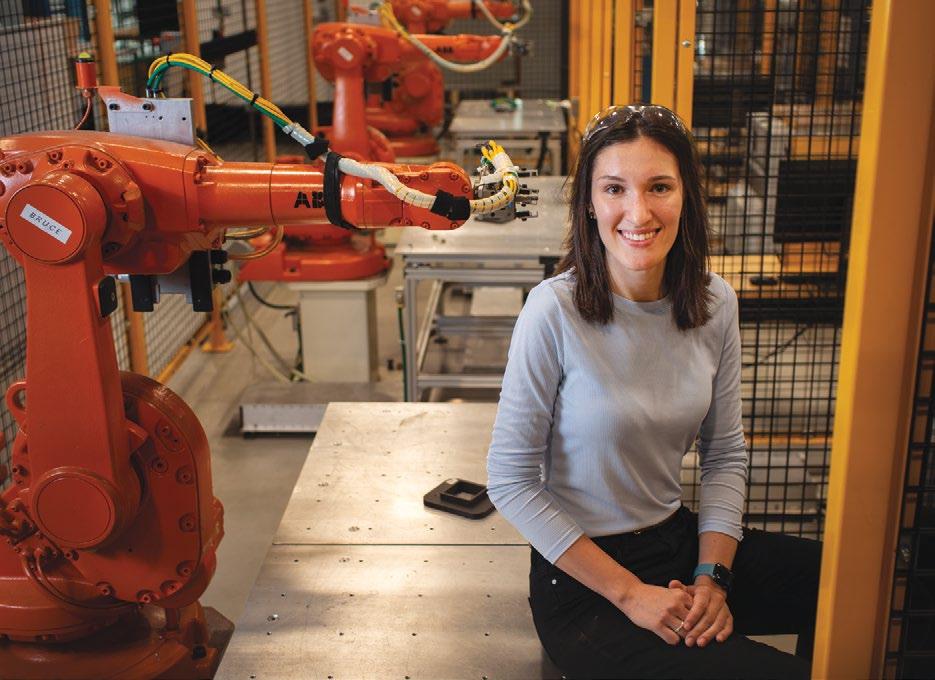

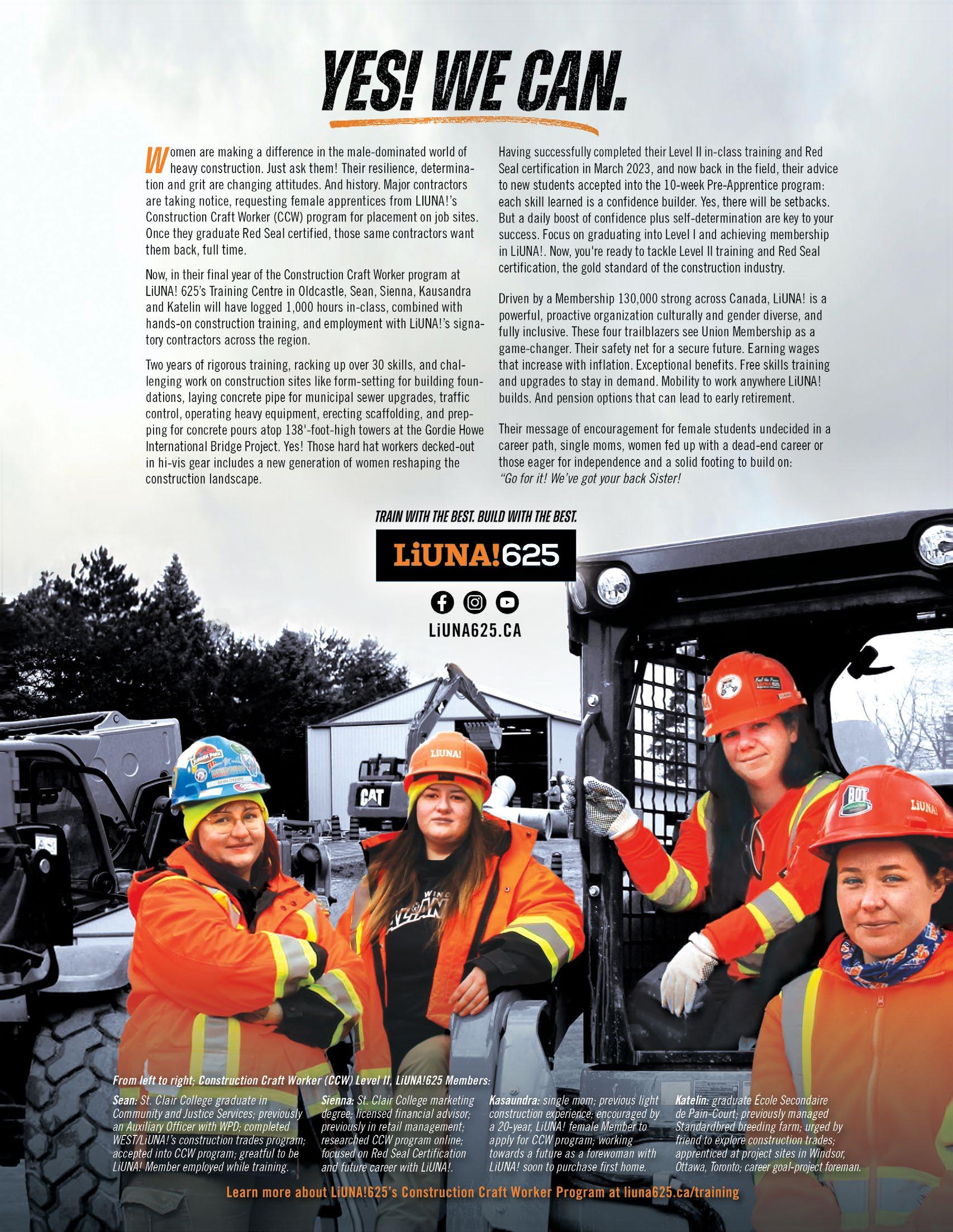