Lessons from Boeing’s 737 MAX 8 crashes
Holistic safety
Integrating safety into the DNA of an organisation
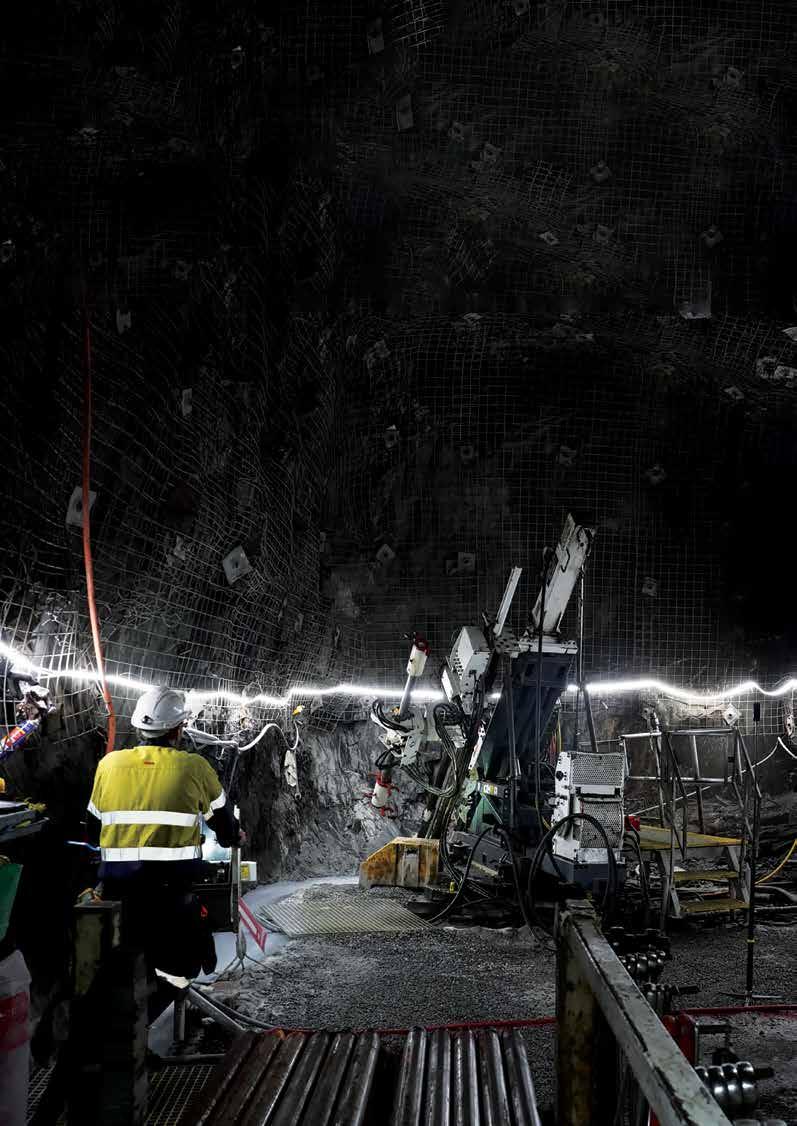
Inside Telstra’s return to work program
Rethinking contractor safety management
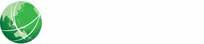
Our team provide a complete range of services through from audit and assurance, to building leadership to critical control management & improving wellbeing, we help to operationalise and create sustainable change. Scan below to learn how you can make a di erence.

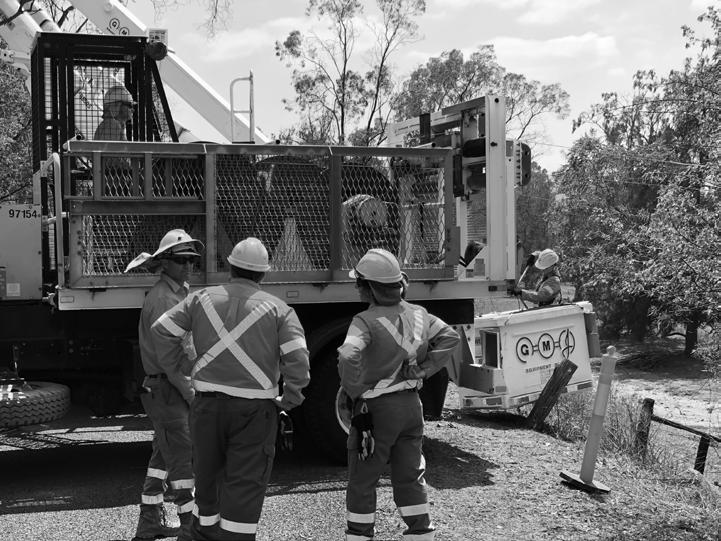

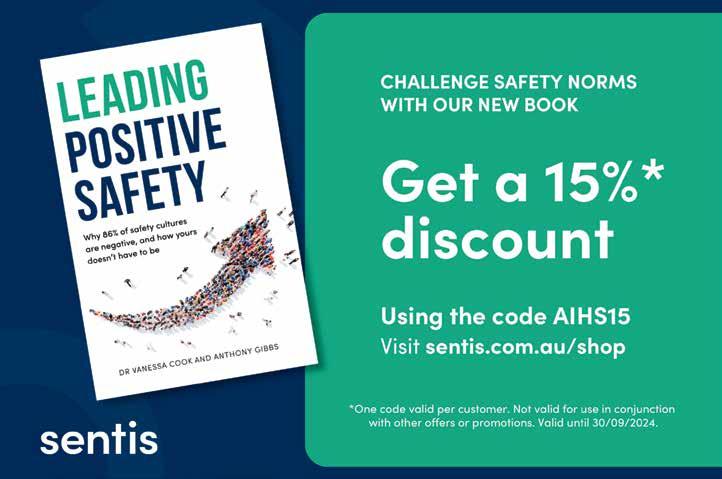
OHS Professional
Published by the Australian Institute of Health & Safety (AIHS) Ltd. ACN 151 339 329
The AIHS publishes OHS
Professional magazine, which is published quarterly and distributed to members of the AIHS. The AIHS is Australia’s professional body for health & safety professionals. With more than 70 years’ experience and a membership base of 4000, the AIHS aims to develop, maintain and promote a body of knowledge that defines professional practice in OHS.
Phone: (03) 8336 1995
Postal address
PO Box 1376
Kensington VIC 3031
Street address
3.02, 20 Bruce Street
Kensington VIC 3031
Membership enquiries
E: membership@aihs.org.au
Editorial
Craig Donaldson
E: ohsmagazine@aihs.org.au
Design/Production
Anthony Vandenberg
E: ant@featherbricktruck.com.au
Proofreader
Lorna Hudson
Printing
Printgraphics
Advertising enquiries
Advertising Manager
Natalie Hall
M: 0403 173 074
E: natalie@aihs.org.au
For the OHS Professional magazine media kit, visit www.aihs.org.au.
Disclaimer: The opinions expressed within are those of the authors and do not necessarily reflect AIHS opinion or policy. No part of this magazine may be reproduced in whole or in part without the permission of the publisher. Advertising material and inserts should not be seen as AIHS endorsement of products or services
Managing the risk of airborne contaminants: The rise of OHS risks such as silicosis and other airborne contaminants necessitates stringent safety measures
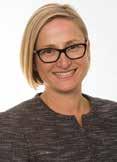

14
Leading the regulator: Head of SafeWork NSW, Trent Curtin, discusses trends, challenges and priorities for the regulator
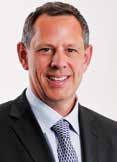
Inside Telstra’s return to work program: Telstra’s work transition program is an innovative and effective model for helping employees with the process of returning to work
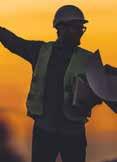
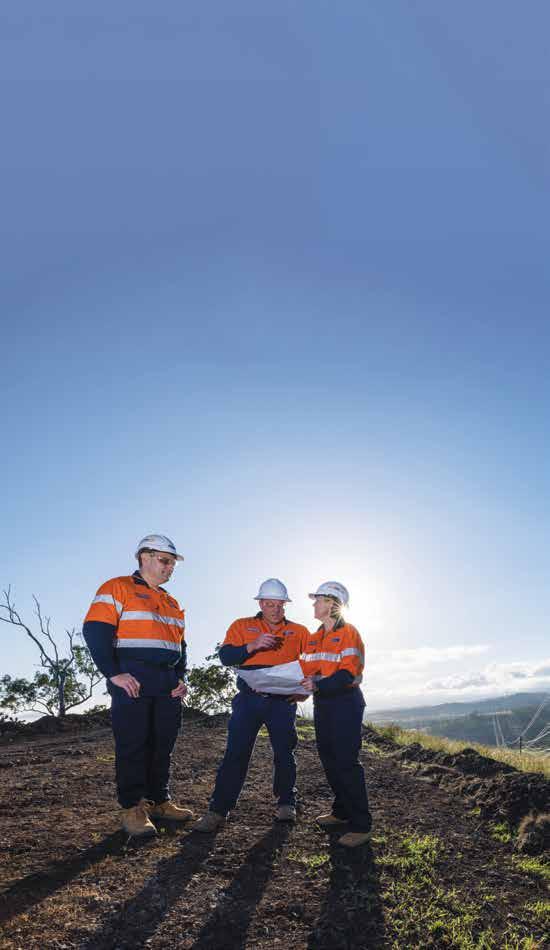
Holistic safety: integrating safety into the DNA of an organisation: A holistic approach to OHS, incorporating leadership, culture, processes, systems, and continual improvement, is critical to safety performance
Rethinking contractor safety management: changing perspective: The job of safety professionals is to ensure the safety of contractors at their
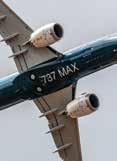
26 32
How complex systems complex systems fail: lessons from Boeing’s 737 MAX 8 crashes: A complex systems approach is more useful in analysing incidents such as Boeing’s 737 MAX 8 failures 16
Beyond compliance: building cultures of safety and resilience
In this issue, industry leaders share how they are going beyond compliance and taking a holistic approach to managing and improving OHS

When Mitchell Services won the Australian WHS Team of the Year in last year’s Australian Workplace Health & Safety Awards, the company’s WHS team was recognised for its initiative, determination, relationship-building skills, and drive to help achieve tangible business improvements. There has been a significant shift in how WHS in the business is perceived and managed, thanks largely to the efforts of Josh Bryant, Mitchell Services’ GM of people, risk and sustainability and his team, who have embedded philosophies
Corporate Members
SHARING OUR VISION – DIAMOND MEMBERS
Amazon
Avetta
CleanSpace Technology
Department of Agriculture, Fisheries, and Forestry
HSI Donesafe
Milwaukee Tools
GETTING CONNECTED – SILVER MEMBERS
Australian Bureau of Statistics
Australian Unity
Brisbane Catholic Education
Clough Projects
CM3
Codesafe
Compita Consulting
Convergint
Curtin University
Downer
Ecoportal
Fifo Focus
Fusion Safety
Guardian Angel Safety
Herbert Smith Freehills
Would
Pan Software
Programmed
SAI360
Sentis
Woolworths
Zenergy
Hitachi Rail
HOK Talent
Pilz
of Human and Organisation Performance (HOP) across the business. This has ensured a holistic approach to managing and improving WHS outcomes, which is the focus of the cover story (beginning page 16) of this issue.
Instilling a culture where safety is ingrained into every aspect of the organisational’s DNA requires a concerted effort at all levels, from leadership to frontline workers, as well as a commitment to transparency, communication, and collaboration. In addition to Mitchell Services’ Josh Bryant, Cumberland City Council’s manager audit, safety and risk, Belinda Doig, and Powerlink Queensland’s general manager of health, safety and environment, Ben Saal, explain how their organisations are taking a more holistic approach to safety that transcends compliance to build cultures of resilience, trust, and empowerment.
Also in this issue, Dr Sean Brady examines Boeing’s 737 MAX 8 crashes through the lens of a complex systems approach – namely the sand pile model. Rather than trying to string all the contributing factors together in a line, this model is a more useful way of viewing these types of incidents because it asks us to re-examine our more traditional views on
cause and effect, and instead look more closely at the sand piles we build in our own projects and organisations. For the full story, please turn to page 26.
The OHS Body of Knowledge feature for this edition also prompts readers to rethink contractor safety management, which will be the focus of a forthcoming OHS Body of Knowledge chapter. As Sue Bottrell and Jon Harper-Slade explain in this feature (page 32-33), WHS professionals are in a key position to change or influence contractor safety management for the better.
Professional development is another theme that runs through a number of articles in this issue, including our story on Michelle Price and her path to AIHS Fellowship. The College of Fellows was established in 2002 and comprises members who are Fellows and Honorary Fellows of the AIHS. As Price explains in this feature (page 8-9), becoming a fellow was personally important to her, as she wanted to give back to her chosen profession and share the learning and knowledge she had gained from others.
Lastly, the Australian Workplace Health & Safety Awards 2024 are fast approaching, with a gala evening slated for 29 August in Sydney. If you haven’t got your tickets yet, please see the ad on the back page for more information.
INVESTING IN HEALTH & SAFETY – GOLD MEMBERS
Alcolizer Area 9 Army
Aurecon
BGIS
Brisbane City Council
Coles
COLLAR®
Dangerous Goods Network
Everyday Massive
EY
Federation University
Pocketknife Group
Port Of Newcastle Risk Talk
Safesearch
Safetysure
Trainwest
Transurban
Uniting SA
University of QLD
Virgin Australia
Work Wear Direct
Zinfra
HSE Global
ICAM Australia
JLL
K&L Gates
Kitney
Liontown
Metcash
MinterEllison
Safety Champion
Soter Analytics
Teamcare
The Safe Step
BEING PART OF THE NETWORK – BRONZE MEMBERS
5 Sticks
Airbus
BWC Safety
Complete Security Protection
Employment Innovations
Employsure
Fefo Consulting
Flick
Health & Safety Advisory Service
Integrated Trolley Management
Isaac Regional Council
Kemira
Liberty Industrial
Modus Projects
National Storage
National Training Masters
Government of South Australia (Office of the Commissioner for Public Sector Employment)
Processworx
Safework SA
Scenic Rim
Services Australia
SIXP Consulting
Westside Christian College
Step-by-step solutions for tackling psychosocial risks in the workplace
With the right strategies, organisations can effectively manage the complex nature of psychosocial risks, writes Julia Whitford
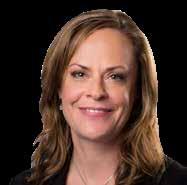
While psychosocial safety has been on the radar within the workplace health and safety (WHS) profession for some time now, many organisations still do not fare well when it comes to managing risks around this complex and nuanced issue. These risks require more than superficial solutions, such as awareness training. Instead, organisations must take a comprehensive approach that revisits work design, ensures consistency amongst departments, and is built on the foundations of trusting relationships with workers. The three case studies comprising this edition’s cover story (beginning page 16) all discuss the importance of psychosocial safety and why a holistic approach to managing WHS and mitigating psychosocial risks is essential.
One of the key areas for improvement is the design of work itself. Rather than taking a reactive approach that looks to mitigate illness once workers are struggling from mental ill-health and stress, organisations must realise that the work itself, when poorly designed, can be contributing to this
negative mental health. Simple data-gathering activities such as surveys, observations, and interviews allow you to understand not just what the psychosocial risks are, but who experiences which risks and when.
Building knowledge and capability within the organisation is vital. Sharing insights and best practices can help organisations develop effective strategies for managing psychosocial risks. Engaging workers in diagnosing and redesigning work processes can lead to healthier work environments and improved performance. By fostering a culture of continuous improvement and proactive risk management, organisations can better protect their employees’ mental health and wellbeing.
“As the management of psychosocial risk falls under WHS legislation, it is imperative to be across changes to legislation to ensure compliance”
Collaboration across departments – safety, HR, workers’ compensation, and operations – is essential. A key challenge in this process is the competing interests between HR and WHS, particularly around worker consultation. To overcome this, organisations should leverage existing HR metrics, such as staff turnover and sickness absence data, to gain insights into underlying issues. Additionally, aligning existing HR
The OHS Professional editorial board 2024





systems – such as recruitment, reward and recognition, learning and development, and performance management – with psychosocial safety objectives can enhance the overall effectiveness of these controls.
Once these steps have been implemented, a final hurdle to overcome is buy-in. You can ensure the design of work is conducive to happy and efficient workers, you can prioritise and streamline collaboration between departments, and you can ensure that they are aware of your initiatives and the risks involved. Still, if you are not able to meaningfully communicate with buy-in, then these processes will be ineffective. WHS professionals must clearly understand their goals or objectives in influencing buy-in, have a pre-planned and timed approach, and have built trusting relationships with the workers they are engaging with.
As the management of psychosocial risk falls under WHS legislation, it is imperative to be across changes to legislation to ensure compliance. From consultation with members, we learned that this is something that understandably is causing stress to our members, and so we have just announced the Psychological Safety Net. In collaboration with the Australian Psychological Service (APS), the Psychological Safety Net service allows members to access a free 15-minute discussion with the APS national team of workplace psychologists. The service will be used to allow WHS professionals to discuss ways to manage psychosocial risks and help ensure compliance. I am so pleased to offer this service to our members to ensure that those tasked with managing the psychosocial health of workers are not negatively affecting their own in doing so, and that we able to offer assistance to ensure they feel well-equipped and supported.



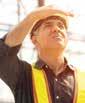
Warning over ‘cocktail’ of serious health hazards for workers
More than 70 per cent of the global workforce are likely to be exposed to climate change-related health hazards, and existing OHS protections are struggling to keep up with the resulting risks, according to an International Labour Organization (ILO) report. For example, the ILO estimates that more than 2.4 billion workers (out of a global workforce of 3.4 billion) are likely to be exposed to excessive heat at some point during their work. The report, Ensuring safety and health at work in a changing climate, estimated that 18,970 lives and 2.09 million disability-adjusted life years are lost annually due to the 22.87 million occupational injuries, which are attributable to excessive heat. This is in addition to an estimated 26.2 million people worldwide living with chronic kidney disease linked to workplace heat stress. “Comparing exposure estimates for 2020 with those for 2000, there was a 34.7 per cent increase in the number of workers exposed to excessive heat. This increase can be attributed to both rising temperatures and a growing labour force,” said the report.
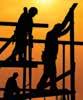
Five-day workweek boosts construction worker wellbeing
A five-day workweek for construction workers can reduce stress and improve worker wellbeing, with minimal perceived impact on productivity, according to a new report. Construction workers typically work six days a week, but research tracking a five-day workweek in the industry has demonstrated a number of significant benefits while reducing risks commonly associated with the industry. The interim report, led by RMIT University in collaboration with the Construction Industry Culture Taskforce (CICT), tracked five pilot infrastructure projects trialling a five-day workweek to address challenges such as the lack of time for life, poor health and wellbeing, and difficulty in attracting a diverse workforce. “We found the majority of workers, irrespective of gender, preferred a five-day workweek because it allowed them to spend more time with their family, see their friends, or play sports,” said project lead and RMIT distinguished professor Helen Lingard from RMIT’s School of Property Construction and Project Management.

Police officers drive up psychological injury claims payments
An increase in the volume of taxpayer-funded psychological claims is behind an estimated 50 to 66 per cent decline in return to work rates in recent years, according to a recent NSW report into workers’ compensation claims and state insurer iCare. Medical discharges of police officers who have been assessed as unable to return to the workforce have been the main source of increased psychological injury claims payments, the NSW Auditor-General’s performance audit report into workers’ compensation claims management found. Taxpayer-funded workers’ compensation payments also increased from $648 million in 2018-19 to more than $1 billion in 2022-23, according to the report. In response to a significant decline in the performance of workers’ compensation schemes, iCare is implementing major reforms to its approach to workers’ compensation claims management. However, the report noted that iCare is yet to demonstrate if these changes are the most effective or economical way to improve outcomes for the schemes.
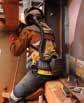
New workplace exposure limits for airborne contaminants
Work health and safety ministers have agreed to a new workplace exposure limit list for airborne contaminants and a harmonised transition period, which will end on 30 November 2026. The workplace exposure limits will replace the current workplace exposure standards, after the ministers agreed to rename them to make it clear that a limit should not be exceeded, and for Australia to align with terms used internationally. While most exposure limits remained unchanged, the workplace exposure standards review did result in some changes, including reductions and increases in limits for certain chemicals and the removal or introduction of new limits for others. Safe Work Australia’s workplace exposure limits for airborne contaminants list notes that some people may have health effects at levels below the exposure limit, either due to individual differences or due to existing health conditions (such as pregnancy, cancer treatment, or recovery from an illness, heart, or lung disease).

School principals highly stressed over workplace violence
Nearly 43 per cent of school principals triggered a ‘red flag’ email in 2023, indicating serious psychosocial risks, potential for self-harm, or serious impact on their quality of life, according to a recent research report. It also found that 54 per cent of principals reported being subjected to threats of violence (up from 49 per cent in 2022), 48 per cent reported being subjected to physical violence (up from 44 per cent in 2022), and bullying levels also rose to 38 per cent (up from 34 per cent in 2022). The most recent Australian Principal Occupational Health, Safety and Wellbeing Survey, which was conducted by the Australian Catholic University (ACU), also found that principals were concerned about the welfare of staff and students. ACU investigator and former principal, Dr Paul Kidson, said the numbers represented a substantial increase, which pointed to a worrying trend supported by the other findings. “It is a drastic increase when you look at the whole picture,” Kidson said.

How to improve RTW programs through early intervention
There are a number of early intervention strategies that are likely to improve return to work outcomes for workers, employers, and insurers, according to a new report. While there is a high level of understanding and belief in the importance of early intervention to improve work outcomes for injured and ill workers, the report found more can be done to improve the effectiveness of early intervention in return to work programs. The Early Intervention in the Workers’ Compensation Process report, compiled by Monash University for Safe Work Australia, emphasised the crucial need for stakeholders to systematically evaluate their existing projects involving early interventions. Ideally, the report said a national evidence-based framework or criteria could be co-developed to guide this. “This would enable a shared understanding of what works/does not work in the setting of Australian workers’ compensation schemes,” said the report, which also suggested creating more opportunities for open collaboration, partnership, and sharing around early intervention in return to work schemes.
Minimising misunderstandings: the role of OHS in risk management
In the recent Dr Eric Wigglesworth Memorial Lecture, Professor Tim Driscoll discussed the importance of clear and honest communication about workplace risks to help workers make informed decisions
It is important not to pretend that there is zero risk of an adverse outcome when it comes to managing and minimising risk, unless there is actually no exposure to the hazard that creates a risk, according to Dr Tim Driscoll, professor of epidemiology and occupational medicine in the faculty of medicine and health at the University of Sydney. Instead, he said it is much better to try to quantify the risk (even on a qualitative basis) and that this should then be communicated to the potentially affected people (such as workers or sometimes members of the general public) in clear, simple ways.
He recommended sitting down with those involved or exposed to a risk to find out what they are concerned about and answer their questions honestly. “If there is uncertainty about the size of a risk, say so,” said Driscoll, who recently presented the Dr Eric Wigglesworth Memorial Lecture as part of the AIHS National Health & Safety Conference in Melbourne. “Try to put the risks in perspective, so that others can make up their own minds as to whether that is something they should worry about. This is easier said than done, of course, especially when the absolute risk is very low.”
There are a couple of ways that WHS professionals can help in the process, according to Driscoll. The first is to provide guidance in terms of the absolute increase (or decrease) in risk arising from a hazard, even just in a qualitative way, and how to interpret this. Helping organisations and workers to understand the difference between absolute and relative risk can also be important, especially when there is concern about potential media articles reporting what seems to be a high relative risk, he said.
Help with advising organisations, or facilitating discussions between management and workers about exposures and the risks they might entail, is also important. This can be particularly helpful when the risk is very low, Driscoll said. “Words or phrases such as ‘negligible’, ‘minimal’, ‘essentially zero’, ‘not worth worrying about’… All of those might be used but all also have some problems – particularly the last one, because each of us have our own idea about what is worth worrying about,” he said.
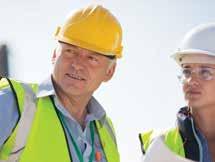
“I use a few different approaches, but the one I have settled on commonly is ‘no meaningful increase in risk’. That runs the risk of being interpreted as ‘not worth worrying about’, but when there is scope for discussion, most people find it helpful.” Of course, if the risk is not low, he said this needs to be made very clear and, wherever possible, the risk should be controlled so that it is low.
Challenges in understanding risk
Driscoll also said there are several challenges faced by organisations in terms of understanding risk and helping others (such as workers or the public) to understand risks they might face in the course of their work. Focussing particularly on illness, he said many organisations appear concerned that in admiting there is a ‘risk’ of harm, they might ‘unnecessarily’ worry their employees, or might open the organisation up to claims for compensation.
“In some situations, it can be hard to gain a good understanding of the risks. Many people don’t understand the difference between relative risk and absolute risk. Many don’t understand the difference between hazard and risk, or how risk varies with level of exposure. People understandably don’t want to face extra risk of something bad happening if they can avoid it; they commonly want to be reassured there is no extra risk arising from the particular work activity or exposure they might be concerned about,” he said.
So, Driscoll said there can be a tendency for organisations to downplay risks, or to say there is ‘zero’ risk. Instead, a key concept is that, in most situations, the only way to have no risk is to have no exposure. In contrast, he said organisations can sometimes
inadvertently create worry and anxiety in workers (or the public) by being overly cautious, or highlighting a hazard for which the risk of illness is extremely low.
“This runs the risk of creating ill health by making people anxious. The recent issue of asbestos contaminating garden mulch is a good example of that. For the general public who spent time in parks or gardens, essentially all of them would have had a very, very low risk of being exposed to airborne asbestos fibres, and so their risk of any asbestos-related disease as a result would be very, very low,” said Driscoll, who added that the risk was perhaps not zero, but very close to it.
Organisational shortcomings on risk
While most workplaces have hazardous exposures of one form or another, Driscoll said most organisations probably don’t have a good understanding of the true burden of ill health arising from these exposures. In terms of injury risks, he observed that organisations are generally pretty good in terms of communication with their workers. “Injuries and the hazardous circumstances leading to them are likely to be well recognised because they are easily observed and the connection to work easily seen (if a person falls from a ladder and breaks their wrist, for example) and easily explained,” he said.
However, he said this is much less likely when it comes to illness (for example, if a person is diagnosed with lung cancer 30 years after they started work as a tunneller). “These types of work-related disorders are much harder to appreciate for a range of reasons. There might be a long delay – many years in some cases – between the causative exposure and when the worker develops symptoms. The worker might have retired by then or moved to another workplace. The worker and their doctor might not suspect the connection between their past work and their illness,” he said.
It is also important to understand and communicate the difference between relative risk and absolute risk. Driscoll observed that many organisations are not experienced or skilled at recognising these problems and communicating with workers about them.
Michelle Price on the path to AIHS Fellowship
AIHS Fellow Michelle Price discusses her career path, contributions to the field of OHS, the benefits of Fellowship, and why it is important to give back to the profession
The College of Fellows was established in 2002 and comprises members who are Fellows and Honorary Fellows of the AIHS. As a senior network of the Institute, the College works to support the Institute’s vision, values, and strategy. Membership of the College recognises OHS professionals who are making a substantial ongoing contribution to and have a record of achievement in the field.
With this in mind, the AIHS encourages members to aspire to be Fellows. By highlighting volunteering opportunities and participation in the various activities of the College, they can gain greater peer recognition, personal satisfaction, and impact.
Michelle Price is one such member, who recently stepped up to become a Fellow of the AIHS.
The journey to Fellowship
Price commenced her professional career as the first in her graduating class with a three-year role as a hydrologist and water scientist with what was then the Department of Water Resources. Motivated to pursue health and safety, she then moved into the university sector. She spent a decade improving organisational health and safety, audit and risk governance, identifying deficiencies, and developing solutions to reduce risks and safeguard workers.
“I view my acceptance as an AIHS Fellow as the progression of my career and a learning curve”
In 2012, after the roll-out of the then new 2011 WHS model legislation in NSW, Price took up a new opportunity in NSW Health - first with Ambulance NSW as the Metropolitan WHS Coordinator and then with Sydney’s local health district in a variety of roles.

Price says that becoming a Fellow was personally important to her, as she wanted to give back to her chosen profession and share the learning and knowledge she had gained from others. “I see a Fellow as a professional who is integrated into a group of like-minded individuals, and who can astutely influence both government and business leaders at the highest professional level,” she said.
Price explained that Fellows possess peer-reviewed knowledge and skills to understand and help make smart, simple, but beneficial changes to public sector and business governance knowledge and policy changes. “Personally, I’ve always tried to simplify and communicate the benefits of a robust business-integrated safety system. I want to ensure that health and safety is a rewarding career path, no matter how you get into it. Most of us have moved sideways or ‘fallen into it’,” she said.
Stepping stones to Fellowship
Although Price had been an active member of the Institute since 2000, she decided to gain certification to demonstrate her knowledge and skills formally. She has always been a fearless supporter of what accrediting health and safety professionals brings to the profession.
As an active member of the NSW Branch of AIHS, Price contributes to policy and the AIHS mentoring program. Her mentoring has seen passionate staff like herself, who ‘fell’ into work health and safety, fall in love with it. She has also taken up opportunities to bring change to staff mentality regarding what safety is and what it means to make implementation a seamless workplace experience.
Price considers herself to have been “very lucky” in all of her roles on the journey to becoming a Fellow, in that she has been able to share the journey with
committed colleagues at all levels. “They have given me such valuable information and guidance that I never felt I could fail professionally. I also wanted to ensure that my knowledge was on par with the highest levels of our profession,” she said.
“While the AIHS (or SIA as it was when I first joined) has always been about networking, peer learning, and mentoring through events, webinars, and face-toface conferences, it has recently become more governance and strategy-focused,” she said. “What’s so vital for my skillset is attending state-based events or even interstate branch meetings and the AGM to further my development. Every single one of these activities has allowed me to meet and mix with my colleagues in the safety business and learn as I grow on personal and professional fronts.”
The benefits of becoming a Fellow
There is almost “no end” to the benefits gained on her personal journey to finally achieving her goal of being a FAIHS, according to Price. “I also think the journey to being admitted as a Fellow is as individual as our members are,” she said. “I view my acceptance as an AIHS Fellow as the progression of my career and a learning curve. In my journey, I’ve had the ability to mix with true visionaries and WHS leaders, especially since my Master of Safety, Health and Environment from UNSW (which sadly is no longer available). This cemented the knowledge I had gained as a health and safety representative and OHS committee member, when I first migrated from quality management systems auditing into a role implementing a new WHS management system.”
Other benefits include the ability to mix with like-minded professionals, not just within Australia but internationally, who hold her values, ethics, and passion for enabling all levels of staff to go home without harm. “Being a Fellow requires me to uphold a core set of work and education values that are my basic core values anyway,” Price said.
She gave the example of working during COVID, embedded as a WHS manager in a hospital under NSW Health. “I was the only person in the facility whose job it was to ensure that our staff were safe and protected from what was then an unknown and highly infectious pathogen,” she said.
“I was dedicated to looking after the physical and psychological aspects of every staff member, including doctors, nurses, back of house corporate and admin staff, as well as sub-contractors most likely employed by engineering to do specialised
work,” said Price. “I loved that 10-year role because I believed it was a privilege to be the contact point for staff advice, guidance, education, and support when they needed it, to ensure issues affecting them were resolved, minimised or, at best, eliminated.”
Workers’ compensation and psychological injuries
As a professional who works tirelessly in the preventive space, Price knows the workers’ compensation path is never ideal for workers to need or use. “If there is an injury at work, this means that some part of the preventative system of work safety that professionals like me implement has failed,” said Price, whose community commitments include Carers NSW, NSW Mental Health Carers Network, Physical Disability Council of NSW, and local government.
“I see a Fellow as a professional who is integrated into a group of like-minded individuals, and who can astutely influence both government and business leaders at the highest professional level”
Workers’ compensation is a challenging system to navigate or even be involved with, as Price said long-term injuries that are deemed not to be the worker’s fault are treated negatively by the public and media. “For example, in NSW, you can have an insurer-accepted injury incurred in the course of your work, but regardless of your fitness for work, the insurer and business can legally sack you after six months because you are unable to go back into your pre-injury duties fully,” she said.
Price also observed that psychological injuries are generally unlikely to heal in six months to the point where an injured worker can fully go back to their role. This creates an issue for good staff who might lose their job just because a psychological injury takes longer to heal – but Price noted
that workers’ compensation laws have not changed to reflect this. “Furthermore, if they don’t lose their job, workers’ compensation laws allow for workplace-injured workers to receive 70 per cent of their pre-injury salary, which is not remotely fair in what is supposed to be a ‘no blame’ system,” she said.
“For any leader wanting to be a WHS role model, I always suggest their best and most important work will be preventing the psychological injuries they are now responsible for managing, with kindness and respect to the home life people have – and then to the staff who may have incurred a compensable psych injury over COVID (for example, due to work burnout or fatigue, which was a huge staffing issue for hospitals),” said Price.
“I ask the leaders to walk in their staff’s shoes and show empathy, compassion and, most of all, kindness for their work. Hospital staff, especially those who might be public servants, simply care about their patients. I ask our leaders: if this was their relative, wouldn’t they want the staff in that facility to look after their patients as if they were their own family? I’ve never had a ‘no’ in response to that question.”
Advice for members aspiring to become Fellows
Price had some parting words of wisdom for those aspiring to become Fellows. “Just work towards being the best you can be,” she said. “Be curious and ask questions to give you a feel for what the actual issues are. Seek the truth. Be accountable for all of the information or instruction you give others. Always be ethical in dealing with all staff levels.”
Other necessary steps are to create meaningful WHS and ESG lead indicators, KPIs, and SMART goals for all staff performance appraisals, and to leave the lag indicators to HR and workers’ compensation to monitor. This is because innovative and human-focussed lead indicators enable real and meaningful business leadership and genuine WHS change.
“Be kind in all interactions until you get a real idea of the issues and the ‘how’ and ‘why’. And remember, every person in our workplaces has something that could hold them back from bringing their A game or just being all they can be in their role – whether it be having a disability, being a carer, being a parent, being new to their role, or not having English as a first language. Every person in a workplace is a person, so ask yourself how you can make your workplace one where you know every person goes home to their family at the end of every shift, each and every day,” she said.
Silicosis and beyond: managing the risk of airborne contaminants
The rise of OHS risks such as silicosis and other airborne contaminants necessitates stringent safety measures to protect workers and improve compliance
Airborne contaminants present significant challenges in occupational health and safety (OHS) across most Australian industries. These contaminants – dust, fumes, vapours, biological agents, and others – pose risks to workers’ overall wellbeing, potentially leading to acute and chronic health issues. Understanding and mitigating these risks is crucial for maintaining a safe workplace and ensuring compliance in accordance with Australian regulations.
Silicosis and black lung disease are prominent examples of the health risks associated with the chronic inhalation of airborne hazards at a large number of Australian worksites. Silicosis, caused by inhaling crystalline silica dust, is a significant concern in industries such as construction and mining. In particular, it has made headlines regarding its use in the manufacturing and installation of engineered stone. Emerging risks, such as exposure to welding fumes, are also gaining increased attention. Welding fumes contain a complex mixture of metallic oxides, silicates, and fluorides, which can lead to serious health issues, including respiratory diseases and lung cancer. These risks are faced by workers in sectors where welding processes are prevalent, including construction, automotive, and advanced manufacturing.
Engineered stone and silica dust
Addressing these risks is crucial due to the increasing regulatory pressure and compliance requirements set by Safe Work Australia and other state and territory bodies. Notably, Safe Work Australia has introduced stringent measures to control silica dust exposure, including the upcoming ban on uncontrolled dry cutting of engineered stone. This has been followed by the Workplace Exposure Standards for Airborne Contaminants update, which mandates stricter exposure limits and more rigorous control measures for harmful substances. Different industries need to be aware of the impact of these regulatory changes, such as the changes associated with crystalline silica dust and its potential impact on businesses, according to Peter Aspinall, principal
occupational hygienist for WSP (Australia & New Zealand). “If you can demonstrate that you are actively and effectively managing your risks on-site, then you should be able to continue your work. But with the recent focus on silicosis, the businesses out there that are not currently even complying with the older exposure standards are the ones that are now paying the penalty,” he said.
“It has pushed a lot of businesses to a point where it’s not viable for them to introduce all these controls and such, so these changes are kind of weeding out some of the cowboys. However, it is also impacting on some of those businesses that are trying to do the right thing, such as family businesses that have been in operation for a long time, who need support making those changes. So the past two years have been very interesting, particularly with regards to silicosis and the stone benchtop industry.”
Alex Virr is chief technology officer at CleanSpace Technology, an Australian owned manufacturer of advanced respiratory protection solutions in the form of powered air purifying respirators (PAPRs) He said the ban on engineered stone makes “plenty of sense” given the risks associated with silica dust. He also comments that there are many other forms of dust that contain silica that present a range of OHS risks. “We haven’t banned all sorts of materials that also have silica in them, and there are many sources of dust that contain silica. In somewhere like a mining tunnel, for example, you don’t know how much silica there is because you’re just boring through. I feel like it would be safer to have a more general focus on just excluding dust that may contain silica, for example, and not get too worried about exactly what the material is that’s the flavour of the month,” he said.
Diesel particulate and welding fumes
Apart from silicosis, Aspinall said diesel particulate is going to become “very much a concern” for a lot of workplaces in the near future. Diesel particulate has traditionally been seen as an issue for the mining industry where employees work in underground environments. However, the
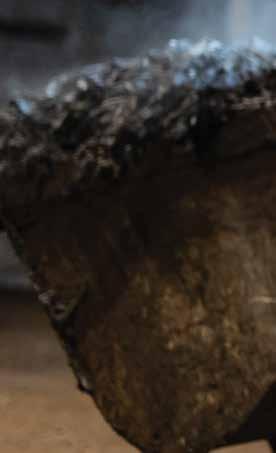
rising concern around diesel particulate is extending to other sectors that use diesel-powered machinery. “We have diesel forklifts going in and out of cold rooms, for example,” he said. “So there are some concerns around this, but my gut feeling is it’s probably not as bad as the underground application concerns. While there are some changes happening with the electrification of equipment and vehicles, with less diesel engines operating on the ground, it’s about quantifying that risk and whether higher order controls are required.”
“Welding fumes in particular are an issue for most industrial application workshops that do welding”
Another emerging and potentially significant risk involves exposure to welding fumes. Aspinall said this will be a “big one” for OHS: “Welding fumes in particular are going to become an issue for most industrial application workshops that do welding. There are a lot of them out there. Some places may only weld 15 to 20 minutes a day with certain tasks or patching up a job
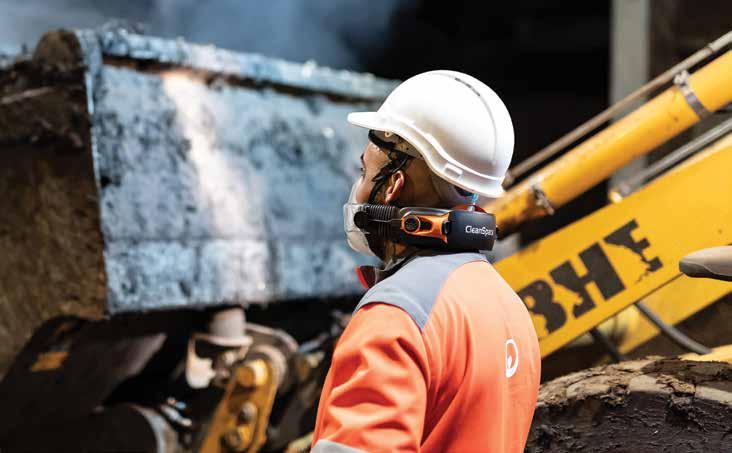
with a couple of fixing welds, but there are other workplaces out there that are consistently welding eight hours a day, all day, every day,”he said.
Safe Work Australia also released updated information regarding limits for airborne contaminants recently. For instance, workers must not be exposed to total levels of welding fumes greater than 1 mg/m3 over an eight-hour working day, based on a five-day working week. “One of our biggest markets is people welding galvanised steel. I don’t know if you’ve welded this steel, but it produces a cloud of what is actually very fine particles. There’s some gas mixed in there too, but it’s the fine particles that block up filters faster than almost anything else for our customers. It’s super fine material and it cannot be good for you,” said Virr, who added that the potential risks of airborne contaminants such as welding fumes can be amplified in enclosed spaces without adequate ventilation, such as in underground mining or the tunnelling industry, which are prone to a range of airborne contaminants.
According to Virr, there is an increased perception that legislation will be introduced and this in turn will require workers in the tunnelling industry to wear a PAPR. “We’ve had customers coming to us on the basis that they’ve been told they have to wear a PAPR, but they’ve never heard of one before. So things are changing, and they do
need a higher level of protection and a more reliable protection system than they’ve used in the past for whatever reason,” he said.
Steps for OHS professionals
In managing increasingly complex operational and compliance concerns about risks associated with airborne contaminants, Aspinall said it is important for OHS professionals to be confident with their skill sets, and understand where their strengths are and the point at which they need to ask for assistance. “In a lot of cases, we get OHS professionals who say they have got respirators and hearing protection for their workers, but how do you know they have the right one? How do you know that’s the right equipment? What was your risk assessment that said it is the appropriate product?” he asked.
Aspinall said it is critical for OHS and occupational hygienists to open the lines of communication, particularly when it comes to certain industry and organisation risks such as diesel particulate in underground mining. “OHS and occupational hygiene do need to be talking to each other. That needs to be coming from the top, and it might also involve legal and risk in terms of exposure. So it’s about getting the right kind of buy-in or stakeholder support to minimise the risks and make sure they’re taking a proactive approach in terms of compliance and looking after their workers,” he said.
It is also important to involve the right stakeholders, such as occupational hygienists, in determining appropriate products to minimise risks, Virr added. He gave the example of PAPRs and said that employers can underestimate the difference between going from an unpowered negative pressure system to a powered positive pressure system and the difference this can make in a dangerous environment (such as a tunnel) which may contain a lot of silica dust. “If you can pick any reputable PAPR, from an engineering point of view, the problem virtually disappears in this sense that when you have an unpowered system, you are completely dependent on the seal of the mask,” he said.
The seal and overall effectiveness of unpowered respirators are impacted by factors such as stubble, dirt, sweat, or changes in the shape of the face. However, Virr said that powered respirators (such as those manufactured by CleanSpace Technology which provide levels of protection up to 99.97 per cent) create a positive pressure, so this reduces the risks associated with such elements. “They just take all of the difficulty out of it. That’s the main point I would like to make to people who are looking at respiratory protection: that there is a big difference between powered and unpowered respirators,” he said.
CleanSpace Technology is a diamond member of the Australian Institute of Health & Safety.
Leading by example: the AIHS mentoring program
The AIHS mentoring program aims to facilitate knowledge sharing and personal growth among OHS professionals
The Australian Institute of Health and Safety (AIHS) mentoring program is a cornerstone initiative within the broader strategic framework of fostering excellence in WHS. At its core, the program aims to cultivate enhanced skills within the WHS workforce, expand career pathways, and drive demand for WHS expertise, according to Ben Kirkbride, Chair of the mentoring committee.
Since its inception, Kirkbride said the AIHS mentoring program – now into its seventh cohort – has seen remarkable success and achieved significant milestones. “Mentors and mentees alike have benefited from valuable insights, professional development opportunities, and networking connections. These interactions have not only contributed to individual growth but have also fostered a sense of community within the WHS profession,” he said.
Looking ahead, Kirkbride said the program is poised for further growth and evolution. As the AIHS continues to expand its education and training resources, he said the mentoring program will play a vital role in supporting this endeavour. “With a focus on fostering diversity and inclusion, the program also aims to showcase inspiring career pathways and promote new certification opportunities, ensuring that the WHS profession remains vibrant and accessible to those that hold current AIHS memberships,” he said.
For those considering participating in the program (whether as a mentor or mentee), Kirkbride offered some advice. Firstly, he suggested approaching mentoring as a two-way street, where both parties have valuable insights to share and learn from each other. Secondly, he said to embrace networking opportunities and actively engage with the broader WHS community to expand your professional horizons. “Lastly, be open to feedback and growth, as mentorship thrives on mutual respect and a willingness to learn,” he said.
“In recognition of the invaluable contributions of current mentors, the AIHS extends its sincere gratitude and appreciation.
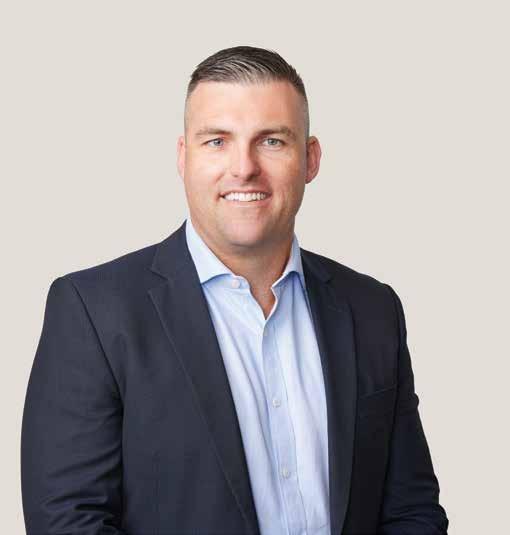
Their dedication to driving excellence in workplace health and safety exemplifies the spirit of collaboration and mentorship that lies at the heart of the AIHS mentoring program.”
A case study of mentoring in action
Peter Johnston is an AIHS mentor, Chartered Generalist OHS Professional and a Fellow of the Australian Institute of Health and Safety College of Fellows. With a wide range of experience in mechanical engineering, HR, occupational risk, workers’ compensation and injury management across sectors such as chemical, mining, automotive, and food manufacturing,
Johnston said there were a number of reasons he wanted to mentor others. “I enjoy assisting employees with their health and safety while ensuring that operational interface arrangements are safely implemented,” he said.
“Importantly though, my thoughts on mentoring fall back onto our Institute values and, in more recent times, my pledge as a member of the College of Fellows. Key for me is to ‘act ethically and with integrity’ and to ‘foster and encourage the Institute and its members to advance the knowledge and activity of the profession.’”
For many years, Johnston has also been lecturing in both the Certificate IV
and Diploma WHS programs and working with students from a number of tier one employer groups. “When the opportunity arose with the mentor program a couple of cohorts ago, I felt that this was a great opportunity to support the Institute and, specifically, people who are wanting support to progress within the profession,” he said.
In reflection, he said the program has allowed him to challenge himself and has provided enormous satisfaction through the positive progression of people within the profession. “As a mature person working within the profession since 1985, I have had significant experience in both national and international roles. Both the education and mentoring programs provide me the opportunity to give back, and have conversations that allow me to reflect on my experience and strategies that have been successful and those which provided challenges and learnings,” he said.
Johnston is currently mentoring Jemma Imanova, a WHS&E engineer who joined the AIHS mentoring program after relocating from overseas. There were two reasons Imanova joined the program. “First, I wanted to connect with a professional in the health and safety field. Communicating and being guided by a professional to ask industry-specific questions, share ideas, and gain insights from their experience just seemed invaluable,” said Imanova, who said the mentorship program offers a chance to learn from the best and accelerate her own health and safety knowledge and skills.
Second, she was eager to gain a broader perspective on the health and safety industry. “The program puts mentees in touch with a mentor who has navigated different career paths within health and safety,” she said.
Imanova said the mentorship program has definitely lived up to her expectations. “Having a dedicated mentor has been a fantastic resource,” she said. “For example, I was recently tackling a tricky project at work, and my mentor offered invaluable advice on best practices and potential solutions. It was a huge confidence booster to have his expertise in my corner.”
Beyond specific situations, she said the program has also helped her develop her overall professional network. Through events and interactions with other mentees, she has met some great people in the health and safety community. “These connections could prove valuable down the line, whether it’s for collaboration opportunities or simply expanding my professional circle,” she said.
In terms of her future focus, Imanova said the mentorship program is perfectly aligned with her goal of becoming a leading
health and safety professional. “The knowledge, skills, and network I’m gaining are all crucial building blocks for my future career. I’m confident this experience will give me a competitive edge in the job market and help me land my dream health and safety role,” she said.
“I’m confident this experience will give me a competitive edge in the job market and help me land wmy dream health and safety role”
“If you’re even remotely interested in health and safety, I can’t recommend the AIHS mentoring program enough. It’s a fantastic opportunity to learn from experienced professionals, develop your skills, and connect with others in the field.
Johnston said he was privileged to be
able to work with Imanova. “We did not use the online program on all occasions,” he said. “We both felt that we have a level of trust and confidence in being able to work at a personal level which considered elements such as family, workplace, and university. Through our conversations and document reviews, the bottom line is to enable Jemma to have a clear pathway for progression and her next steps. I observed Jemma learning from our communications, and saw a consolidation of her passion and determination to achieve and meet deadlines while maintaining a family.”
In recognition of this, Imanova recently received a letter of commendation from Professor SueAnne Ware, the Head of the School of Design and the Built Environment at Curtin University (where Imanova is currently studying a Masters in Environment and Climate Emergency). The letter commended Imanova on her academic performance, her personal commitment to her studies, and her contribution to the reputation of her degree.
For more information about the AIHS mentoring program and how to get involved, visit the AIHS website.
AIHS mentoring program: Recognition and thanks to mentors cohort 7
Annette Sommerville
Trent Yeo
Bryce Gregory
Veronica Cooper
Angelica Vecchio-Sadus
Andrew Sloan
Greg Stagbouer
Damian White
David Howard
Alissa Webster
Gerard Forrest
Sajan James
Gordon Smith
Eddie Bugajewski
Steve McNair
Ben Kirkbride
Kelvin Genn
Gregory Chrisfield
Bruce Vernon
Barbara Cooper
Tim Allred
Nan Austin
Michael Eather
Symone Mercer
Katie Watson
Anthony Bate
Harshal Jain
Danielle Stalker
Peta Mercieca
David Whitefield
David Trembearth
Peter Brian Johnston
Ryan Baldwin
Kenneth Charles Patterson
Daniel Grivicic
Abigail McPherson
Shona Backers
Michael Hagan
Sonia Correa
Paul Kozina
Owen Bevan
Kristine Cotter
Stephen Weber
Kim Schulz
Craig Ramadge
Abhijit Prasad
Katie Weber
John Christie
Mark Philippi
Kim Whale
Susan Allen
Jeremy Clay
Mark Devlin
Dean Matthews
Stuart Rawlins
Courtney Newman
Phil England
Philip Powh
David Clancy
Melita Caffery
Graham Campbell
Lisa-Marie Dembski
Peter David Hedger
Mary Kikas
Kevin Figueiredo
Louise Vella Jurd
Vlad Doguilev
Sanzid Alvi Ahmed
Glenn Jordan
Michael Hall
Robert Dunn
Braham Tindale
Catherine Jeffries
Michael Polito
Donella Redclift
Martyn Campbell
Mano Raghavan
James McGuire
Lois Frances Hutchinson
Justin Haddock
Robert Whiteside
Matthew Mark Gauthier
Marilyn Hubner
Leading the regulator: Trent Curtin, SafeWork NSW
Head of SafeWork NSW, Trent Curtin, speaks with OHS Professional about trends, challenges, and priorities for the regulator
Trent Curtin commenced the role of head of SafeWork NSW in October 2023. He is responsible for leading the WHS regulator’s operations, improving compliance, and leading the regulator’s transformation following an ongoing independent review of its operation by Robert McDougall KC. Curtin was formerly the acting deputy Commissioner for Fire and Rescue NSW and the national spokesperson on fire safety regulation and compliance.
What are the priorities that SafeWork NSW will be focusing on over the coming 12 months?
SafeWork sets its regulatory focus from various data and intelligence sources, as well as lived experience and inspector observations.
It has also been informed by recent reviews by McDougall KC and the NSW Audit Office. SafeWork, as a portfolio of the NSW Minister of Work Health and Safety, is currently in the process of finalising those priorities for 2024/2025 and will continue to focus on priority risk areas.
These priorities will align with high-risk harms and injury mechanisms identified in the Australian WHS Strategy 2023-33, such as falls, moving plant, psychosocial health and safety, dust diseases, and cancers.
These decisions are based on a range of criteria, including evidence from workers’ compensation injury claims and incident data, research on enduring and emerging high-risk harms, as well as alignment with the Australian Work Health and Safety Strategy’s identified harm priorities. We will continue to be informed via tripartite collaboration with the government, business, and unions.
How is the role of SafeWork NSW as a regulator currently evolving?
SafeWork has a multifaceted approach to interacting with government and employer organisations, unions, and injured workers, all of whom have a clear ability to influence safety culture. Larger and well-resourced organisations are not always prioritising
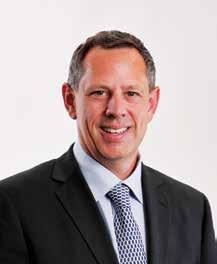
Head of SafeWork NSW, Trent Curtin, says WHS risks typically persist due to shortcomings in leadership and a lack of genuine consultation with workers on solutions to WHS risks
sufficient effort towards health and safety, particularly relating to psychological health and safety.
“Larger and well-resourced organisations are not always prioritising sufficient effort towards health and safety, particularly relating to psychological health and safety”
Our interactions include providing advice and education, inspections, investigations, and prosecution when necessary to achieve compliance with WHS laws.
WHS risks typically persist due to shortcomings in leadership and a lack of genuine consultation with workers on
solutions to WHS risks. Every worker has the fundamental right to come home safely from their working day. As a regulator, we look to work with employers to bring about improvements in workplace safety by raising awareness and encouraging leaders to embed good practice.
Working in partnership with government agencies and employer organisations and unions, we balance our efforts. Larger and well-resourced organisations can expect swifter, more robust regulatory actions and enforcement as there are obvious duty holders and accountable officers.
With a lift in the performance of major employers with influence, such as government and big businesses, SafeWork can focus more effort towards small and medium businesses and industries, businesses, and hazards that require more support.
How do you see this evolving and what are the major trends that will impact SafeWork NSW and employers?
Over the next three to five years, SafeWork will invest further in data and evidence-based risk reduction efforts to identify new and emerging WHS harms. By improving our systems and harnessing data analytics and insights, we will identify and address workplace hazards and high-risk industries more proactively and effectively.
We need to emphasise a preventative stance that enhances our capacity to anticipate and respond to newer and emerging risks, including gig work and other risks arising from contemporary research.
We will focus more attention on ensuring effective consultation mechanisms and supporting the important work of health and safety representatives.
We are also aligning with trends outlined in the National WHS Strategy 2023-33. These include the changing nature of work, new technologies, psychosocial harms, and the changing nature of workers and the workforce.
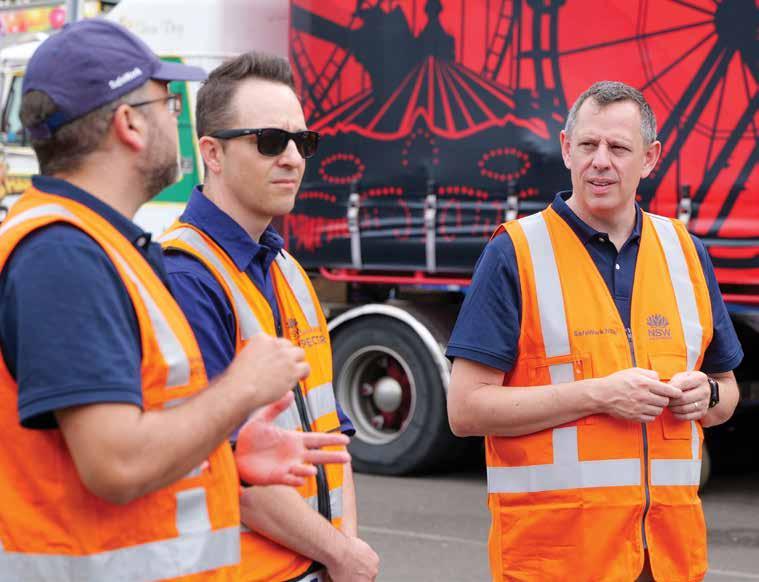
What do you notice among ‘best practice’ organisations that consistently have good OHS outcomes?
Organisations with good WHS outcomes are always led by strong leaders who are well-informed of issues in their workplaces and place safe work culture at the centre of their business. They invest in genuine consultation with workers and their relevant unions in finding innovative solutions to work health and safety issues.
When SafeWork inspectors visit worksites, they look out for well organised, clean, and tidy places, which show respect for their workers. This is most easily noticeable around amenities and other shared spaces.
We also look for appropriate safe work procedures, which are not complicated, in the workers’ language, and reflect how work is completed – not just an instruction manual.
What advice would you offer to organisations looking to improve their OHS outcomes?
When SafeWork is on-site, we want to see a culture where even the smallest risks are appropriately considered, and not just left to an administrative control or simple PPE. Strong WHS leaders invest in removing risks where possible and ensure employees are properly trained to handle any incidents that may occur.
This is especially important when working with employees who are young, new, and inexperienced or who are employed on a casual basis. There must be appropriate induction and education, along with proper supervision around hazardous tasks.
While SafeWork’s education can be focused on supporting smaller businesses, which make up a large percentage of Australian employers, we look for WHS leaders who support and work with health and safety representatives to ensure
effective solutions to WHS issues.
When looking at larger workplaces, inspectors will focus on understanding how the psychological health and safety of employees is being managed, as this can often be disregarded or overlooked. Businesses should have their key focus on systems that prevent the occurrence of incidents that could cause psychological harm. Whist systems to respond are always important, prevention is key and will save businesses significant time, effort, and money. Businesses should also keep up to date with relevant codes of practice and should never cut safety for the sake of productivity or profit.
As workplaces change and ways of working continue to evolve, there will be risks emerging that will need to be addressed and WHS professionals need to be agile in addressing these issues. This includes a greater awareness of psychosocial risks and the emergence of the gig economy.
Holistic safety: integrating safety into the DNA of an organisation
A
holistic approach to OHS, incorporating leadership, culture, processes, systems, and continual improvement, is critical to safety performance, writes
Craig Donaldson
Good OHS is more than a onedimensional functional pursuit, and is more about fostering a work environment where everyone feels empowered to identify hazards and make risk prevention a top priority. A holistic OHS approach transcends addressing physical hazards and focuses on the bigger picture. Leadership styles, the organisational culture, established processes, and existing systems all play a crucial role in workplace safety.
Imagine safety as a well-built house. Robust regulations and clear procedures form the foundation, providing a solid base. But a secure roof – supportive leadership that champions safety – and strong, well-maintained walls – a positive safety culture where everyone feels comfortable raising concerns – are equally vital for complete protection. A holistic approach allows for the building of this complete structure, ensuring long-term safety and wellbeing for all workers.
Instilling a culture where safety is ingrained into every aspect of the organisation’s DNA requires a concerted effort at all levels, from leadership to frontline workers, as well as a commitment to transparency, communication, and collaboration. From redefining safety strategies to practical implementation at the operational level, the following three organisations (Mitchell Services, Cumberland City Council, and Powerlink Queensland) are taking a more holistic approach to safety that transcends compliance to build cultures of resilience, trust, and empowerment.
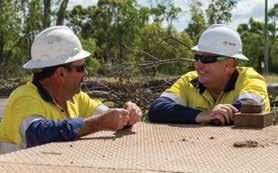
How Mitchell Services makes OHS business as usual
Mitchell Services is an Australian-based drilling company with more than 800 employees working across Australia, serving multiple clients in the surface and underground mining and exploration industries. The business faces significant challenges in managing the various systems and contractual requirements that must be met, all while managing high-risk activities.
There are a few standout challenges the business is currently facing, according to Josh Bryant, GM people, risk and sustainability for Mitchell Services. “It is a trend being experienced by businesses globally where some of our experienced people are leaving the business and it is showing that not only do our systems not necessarily capture their skills and knowledge (retention), but also that they were adapting in our system and covering for some its short falls. So, we need a way to really expose
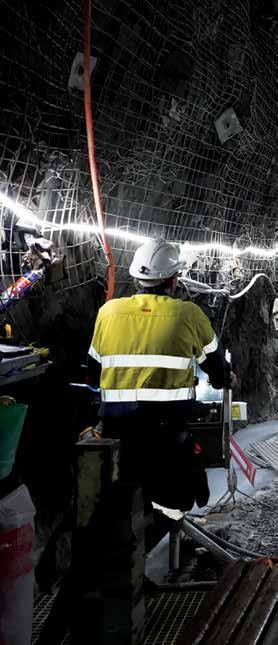
and learn from those system weaknesses now. Identifying and addressing these ‘weak signals’ is crucial,” he said.
The business is also introducing new equipment that has had a positive impact in decreasing the amount of manual handling that its personnel have do as part of their roles. No matter how many change management processes the business goes through, Bryant said manufacturers have not necessarily involved operations in equipment design and use. As a result, he said some changes have made the job more difficult for operations personnel, or that it does not make sense for them to now have to do things a certain way. “We must ensure that changes are practical and gather feedback to learn from necessary adaptations,” he said.
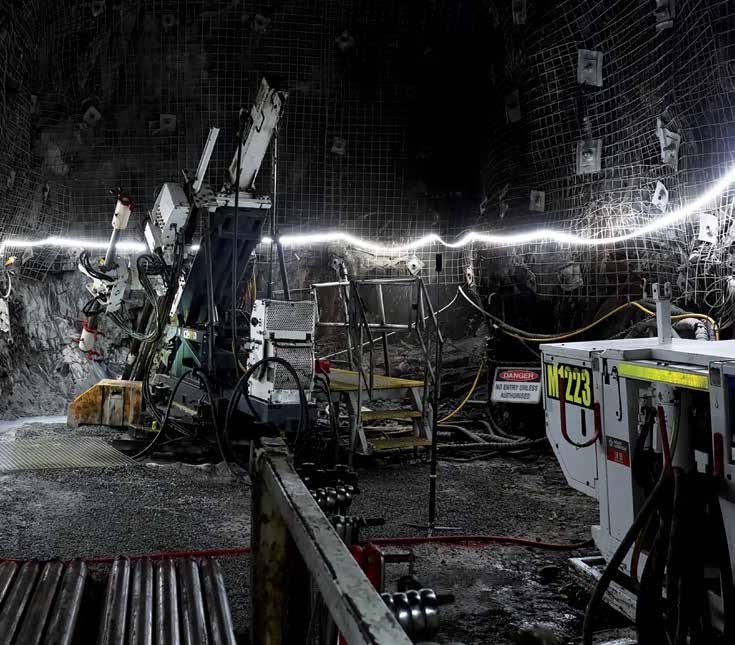
Psychosocial safety is also a priority, in terms of groups working in small teams and the business’ role as a contractor working for clients. “There is an expectation of safe operations whist delivering on client requirements, where that be production or quality goals. Our challenge lies not in the relationships between members of the teams, as we find our teams are quite social, cohesive, and welcoming. It’s us understanding the conditions they face, where they are having to make trade-offs, and what the interactions are with our clients. We strive for genuine partnerships rather than traditional contractor-client dynamics,” said Bryant, who explains that open dialogue with the workforce and transparency with clients are essential in addressing these issues.
The evolving role of HSE within the business has also presented challenges, said Bryant. “We really have moved away from the traditional role of being some sort of ‘compliance officer’ and our role as WHS to audit, check, and investigate. We are finding that we have transitioned to more operational improvement and being a conduit for information flow between groups,” he said.
This is not something people new to the business are used to in their roles, so Bryant said it is important to enable them to be able to interact and build trust with different stakeholders in the business in order to unlock operational learning and operational value. “We are actually improving the safety of work,” he said.
Key elements of Mitchell Services’ WHS strategy
The business’ WHS strategy, influenced by Forge Work’s Map (a free resource), marks a shift from compliance to enhancing resilience and genuinely improving workplace safety, according to Bryant, who also identified four primary areas the WHS team and organisation focuses on as part of its strategy: Systems of work and work management. This is about being proactive about improving and learning from frontline work that feeds into improving safety of work and risk management systems in support of the frontline. “This is reviewing the effectiveness of our systems and whether they are doing what they are meant to, rather than just seeing them as
a bunch of activities to be counted. This includes how we deliver our training, so that we achieve our ISO certification and that it adds value and is not just ticking a box, and doing reviews of our processes so they reflect the realities of their use in the field,” said Bryant.
Operational learning to build resilience and operational excellence. It is crucial that leaders understand the importance of their responses to events, which helps in building trust and facilitating learning from experiences by shifting focus from ‘who failed’ to ‘what failed’. “We prioritise practical engagement with work processes over mere safety paperwork and identify systemic issues as a key learning point from events,” said Bryant.
Management of critical risk. Reducing operational risks with controls that are not only present but effective and userfriendly is a priority for the business. “Our approach to critical control failures or improvement opportunities focuses on learning and enhancement rather than merely completing verifications,” said Bryant, who adds that WHS are involved in operational discussions regarding improvements in work design that can apply a human factors/error tolerance lens with controls.
Influencing stakeholders and inbound business support. Operational leaders in the business drive processes with a clear safety lens to understand and improve work-as-done (WAD). In the process, Bryant said information flows freely from the leadership team to supervisors to frontline workers and back. “The five principles of Human and Organisational Performance (HOP) form part of our foundation for leaders in Mitchell Services and Deepcore Drilling,” he said. “Is this easy to implement? We only have a small team with limited resources, so we believe we are working on the things that matter and the things that will make a difference.”
Operationalising WHS strategy on the frontline
Bryant recalls a comment from Greg Smith (a partner at Jackson MacDonald Lawyers), who recently stated at an industry conference: “Organisations use safety metrics that do not actually measure safety, but rather the volume of safety-related activities. Many businesses prioritise ticking boxes for legal compliance rather than focusing on the actual effectiveness of safety measures. This compliance-driven approach can result in safety processes that are superficial and do not genuinely protect workers.”
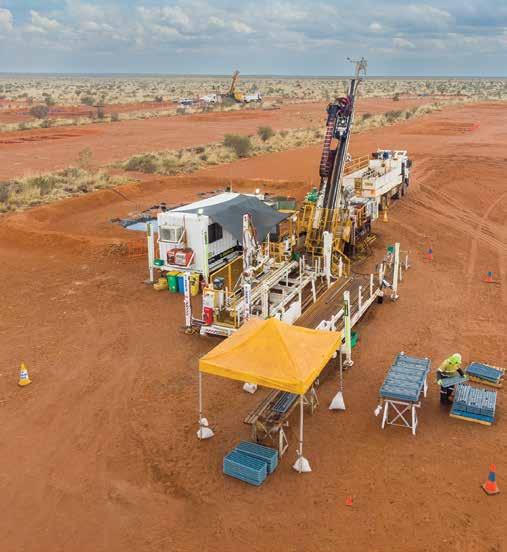
With this in mind, Bryant said a full review of Mitchell Services’ integrated management system was conducted with the leadership team to determine its continuing suitability, adequacy, and effectiveness, rather than chasing statistics and activity. “This has improved our understanding of the system’s use by operations in controlling our risks, and where the system needs to improve,” he said.
Learning is also vital in the business, given the spread of its operations and the variation in teams and working environments, Bryant said. “We have changed our field leadership or ‘time in field’ activities to incorporate the 4Ds into our workplace insights: what does not make sense, what is difficult, what is different, and what is dangerous. We have found that the use of the 4Ds is a quick way to build rapport between frontline workers and leaders, and it’s revealed many of those ‘weak signals’ in our business where people are having to adapt, where we do not have standardisation, or there are opportunities to learn and improve where we can,” he said.
“When the 4Ds uncover systemic issues, we can then conduct a learning team and
involve more of the business. This has led to changes in supply chains, stock availability, rig design, equipment design, onboarding, and process changes.”
“We are finding that we have transitioned to more operational improvement and being a conduit for information flow between groups”
Although the HOP principles are designed to be used together, Bryant said a standout element is the principle of ‘leader’s response matters’. This has changed the way that information is collected when there is an event, with subtle but important changes such as changing the ‘event statement’ form to an ‘event debrief’ form,


and incorporating some of Investigations Differently’s event insight questions like ‘What surprised you?’, ‘What has to go well?’, and ‘What does management need to know about this task?’ “Our event learning communication contains information about what happened versus what we thought would happen, what surprised us, what worked well, and what we learned. This has led to workers being more open and has increased the flow of information across the business,” said Bryant, who explained that this kind of approach has also lifted the engagement of the business’ WHS team. “The WHS team enjoys their role. They aren’t stuck looking at whether first aid kits are in date and walking around auditing – they are engaged and feel that they are adding value and making a difference,” he said.
Leadership and integrating safety into organisational culture
In discussing the importance of leadership to OHS, Bryant cited a quote from Todd Conklin: “As leaders, the first thing that we need to do is to change our definition of ‘safety’. Safety is not the absence
of accidents. Safety is the presence of controls and the capacity for our people to adapt and to fail safely.”
Bryant said Mitchell Services has taken a proactive approach to shifting the focus of its leadership team. As a contracting business, many of its tenders still require the submission of measures such as the TRIFR (Total Recordable Injury Frequency Rate) and number of hazards reported in the past 12 months. However, Bryant said these numbers are not communicated internally “as it is not what matters most”. “We want leaders to have heightened awareness of risk and if our systems are working, the effectiveness of our controls, and also for them to be interested in work and how our people adapt,” he said.
Bryant explained that leaders can make an “enormous difference” simply by changing how they respond to failure, and that has led to an improvement in trust and openness with supervisors and the frontline. “We created our own Human and Organisational Performance (HOP) training program that uses our context and our examples, and therefore it has a lot more meaning to our leadership team and
supervisors,” he said.
“It is also how our leaders show up to a site. We have been purposeful in this - do we turn up, pull out our phone, and start doing a critical control verification? Or do we stop, and open with a 4Ds conversation by simply asking ‘Where have things been more difficult than you thought they would be?’ or asking a new starter ‘Tell me about all the dumb stuff we made you do with your onboarding, and where you suggest we can improve.’ It is not going in as the leader who thinks that they need to have all the answers; it is being a leader that is genuinely curious and interested in learning.”
Bryant and his team also work with the leadership team in transparency of information, as he said it is important to have a system that does not just count critical control verifications, but also provides detail of the failure and the observation of the control.
“And then leaders, including our Board, will do a deeper dive on any systemic failures to determine if a learning team needs to be conducted. Overall, the business has moved from purely quantitative measures to more qualitative measures. This has not been easy and has been a slow process of change,” he said.
Results, outcomes and benefits
Bryant said the first sign of success people will look for in a business is injury rates. “Ours have improved, particularly injury severity, but statistics have not been our driver,” he said. Critical risk management has improved through understanding the effectiveness of controls and, importantly, the human interface with these controls.
The 4Ds approach has also increased communication and flow of information across the business, particularly in understanding ‘weak signals’. “We are showing that it does not have to take an event for us to learn. The leadership team has maintained a close relationship with our supervisors as we are acting on the feedback and learnings we are gaining from the critical control verifications and 4D workplace insights,” he said.
“Both initiatives have resulted in changes to work design and conditions. This has made a genuine improvement to the safety of work, rather than some short-term campaign that focuses on ‘hand and finger injuries’ or ‘insert injury of the month here’. We have been genuine in making sure that our messaging is focused on critical risk and operational learning, and working closely with our leaders wanting to learn and improve. In the end we are not only a better business, but we are also a closer business. There has been one thing that has increased in this period – it is the level of trust.”
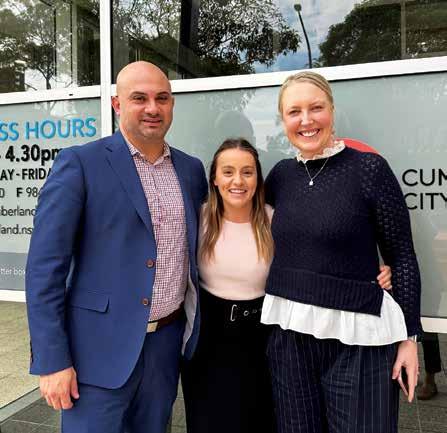
Integrating OHS into Cumberland City Council
Cumberland Council is a local government area located in the western suburbs of Sydney. Formed in 2016 from the merger of parts of the Cities of Auburn, Parramatta, and Holroyd, the council employs about 900 people and has a population of about 250,000 people.
Like many local governments, the council faces a number of significant WHS challenges.
A key element in the creation of a strong safety culture is that safety is “our number one priority” every day, according to Belinda Doig, manager audit, safety and risk for Cumberland City Council. This strategy is embedded in council’s culture, from the executive management team down through each layer of the organisation. “It is openly promoted in all staff communication, monthly WHS committee meetings, toolbox talks, and safety events,” said Doig.
The council’s WHS team works closely with the executive management team to ensure that safety is deeply embedded in the organisational culture, according to Doig. “Council’s executive team consistently emphasise that safety is our number one priority every day. By fostering a strong safety culture from the top down, we set the tone for all employees to prioritise safety in their daily activities,” she said. Every month, the council’s WHS
committee convenes to dive deep into discussions on safety culture, recent incidents, potential improvements, and strategies. “We’ve implemented a comprehensive WHS management system (compliant with ISO45001 standards) which is accessible to every member of our staff, to ensure strict adherence to safety protocols,” said Doig.
Communication, toolbox talks and risk assessments
Regular staff consultations also provide a platform to address any changes in plant equipment, work practices, or safety procedures. “We foster a proactive approach to incident prevention and improvement. Toolbox talks are a staple, offering an open forum for staff to voice safety concerns, share best practices, reflect on incidents, and propose solutions,” Doig added. Toolbox talks have a strong focus on raising safety hazards, safety improvements, and learning from incidents, near misses, and hazards. All teams across the council are required to hold a certain number of toolbox talks per month, and Doig said the agendas and frequency are monitored and reported to council’s monthly WHS committee and form part of management’s KPIs.
“Teams with high risk processes or tasks are required to hold more frequent toolbox talks to ensure that safety is their number one focus,” she said. “Initially there were challenges with implementing a high
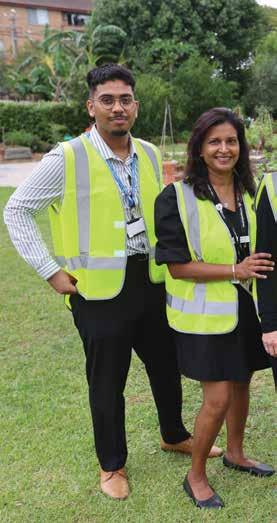
number of toolbox talks, but by creating a consultation and communication procedure and WHS roles and responsibilities procedure, as well as aligning management’s KPIs to toolbox talks, staff and management were provided with a strong awareness of the importance of safety.”
At an operational level, Doig said the council’s WHS strategy is implemented through various practices, procedures, and training that are integrated into day-to-day operations. All outdoor staff, for example, kick off their day with thorough pre-start assessments on all plant and vehicle equipment, ensuring everything runs smoothly from the get-go, said Doig. If any pre-start checks do not meet the requirement of the risk assessment, she said it is “down tools” until repairs take place or the site is safe to continue working. “This applies across the whole of council and there is a strong focus on situational awareness. If it is not safe, remove yourself from the site immediately,” she said.
Addressing psychosocial hazards
“One of the biggest challenges we’ve faced is helping our staff understand the importance of mental health and identifying psychosocial hazards in the workplace,” said Doig. “We have been on a journey to shift
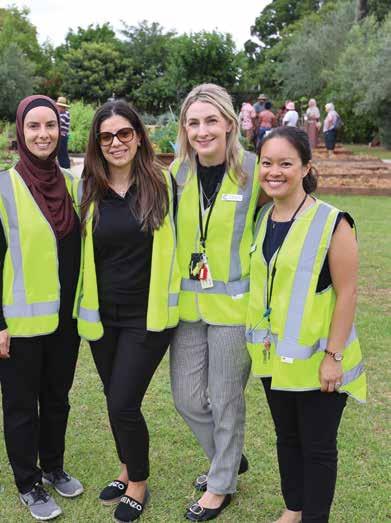
mindsets and recognise that our staff’s mental wellbeing is just as important as their physical safety. Previously, our focus has been primarily on physical safety, which, of course, is essential. But now, the lens has been widened to include mental wellbeing in the same spotlight.”
“Teams with high risk processes or tasks are required to hold more frequent toolbox talks to ensure that safety is their number one focus”
Given the nature of a council worker’s daily responsibilities, which entail close community interaction and the management of multiple tasks, Doig said there is an acute awareness of the potential toll on employees’ mental health. “Consequently, we’ve undertaken concerted efforts to normalise discussions surrounding mental health and to instil a culture where self-check-ins are

routine. Council have run effective awareness campaigns, provided resources for mental health support, and fostered a culture where it’s okay to not be okay.”
Across every council directorate, key staff (45 to date) undergo specialised mental health first aid training, which Doig said equips them to respond effectively to mental health challenges. Additionally, she said mental health awareness training empowers staff with the tools and strategies to manage their own mental health and recognise signs of distress in their colleagues. Council’s recent 2023 safety events also focused on mental health and CEO of the Mental Health Movement, Dan Hunt, provided staff with tools to manage their own mental health and to recognise the changes in those around them.
The council also has an employee assistance program, which extends support to staff and immediate family members. “Our recognition programs celebrate and commend employees who demonstrate an unwavering commitment to safety, fostering a culture where safety is deeply valued. These efforts culminate in our annual council safety day, where we celebrate the council’s dedication to safety, showcasing the work of our safety champions,” she said.
The benefits of a holistic approach to OHS
Creating a strong culture of safety within the council has yielded several significant outcomes and benefits. By prioritising safety at every level of council, Doig said there has been an overall decline in incidents and injuries (council has reduced its time lost by 7 per cent and average claims costs by 72 per cent compared to industry standards).
Staff are also more aware of potential hazards and take proactive measures to mitigate risks, which Doig said has resulted in a safer work environment. Fewer workplace incidents and injuries has also led to a reduction in workers’ compensation claims and insurance premiums (workers’ compensation claims were reduced by $127,000 in the past financial year).
“Building a strong safety culture provides staff a supportive environment and encourages ongoing feedback and collaboration to identify areas for improvement. Council staff are empowered to suggest safety enhancements and participate in initiatives to continuously enhance the safety culture,” she said.
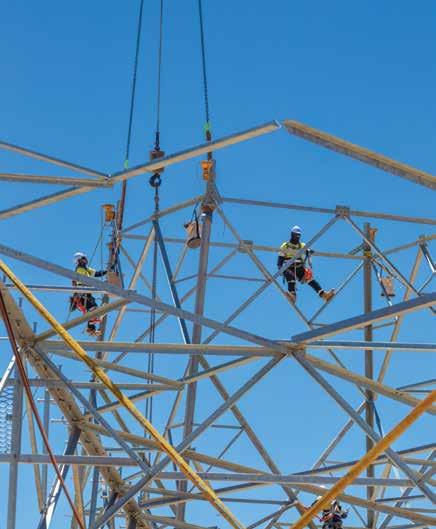
Powerlink Queensland: scaling up OHS for mega projects
Powerlink Queensland is a government-owned corporation that owns, develops, operates, and maintains the high voltage electricity transmission network in Queensland. Its network extends 1700 kilometres from Cairns to the New South Wales border, and comprises 15,345 circuit kilometres of transmission lines and 147 substations. With about 1300 employees, safety is a critical consideration for the business, given the high-risk nature of some of its operations for workers in the field.
Ben Saal, general manager of health, safety and environment at Powerlink Queensland, said that there are a number of significant WHS challenges in the organisation. “I think one of the challenges for most organisations, including ours, is understanding the true and detailed picture of how controls are performing day to day - understanding the small variations and contextual differences in the things you think are keeping people safe,” he said.
Powerlink’s workforce is also growing to help provide the necessary skills and capacity to deliver the mega projects detailed in the Queensland Energy and
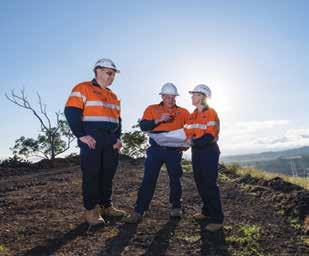

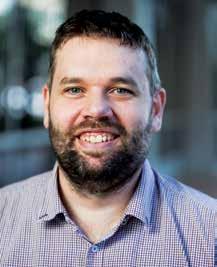
Ben
Saal, general manager of health, safety and environment at Powerlink Queensland
Jobs Plan. There was a 23 per cent increase in the number of full-time employees last financial year. “We are also growing in regard to geographical footprint, new technology, and new people, so the challenge of understanding how your safety controls are performing in that context is another challenge,” said Saal
Human and organisational performance at Powerlink Queensland
The organisation’s strategy integrates the key elements of Human and Organisational Performance with critical control management and contemporary safety theory and practice, according to Saal. “So far, this has involved applying a range of techniques to understand and improve control performance. This means creating a foundation of psychological safety, then integrating that into tools for learning from the people who do the work both proactively and reactively in order to make controls more robust,” he said.
For example, investigation practices have been replaced with more adaptable event learning methods, which range from larger learning teams to simpler control review conversations.
“We are working on doing the same with assurance, and adding to traditional audits with other methods for understanding control performance from the workers and engineering functions,” he said.
In practice, Saal said having scalable options for event learning has been well received. “People were sick of ticking boxes to satisfy investigation structures for simple


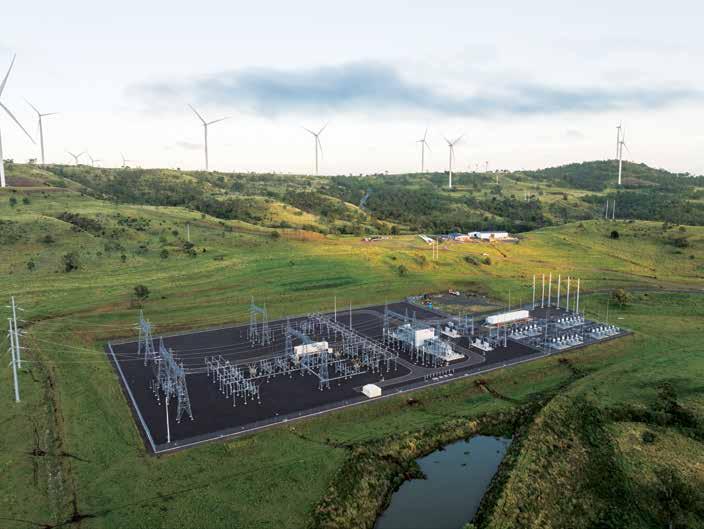
events and not getting enough good information on complex ones. Getting the time with operational people can be challenging, so we have done what we can to equip our safety team with the access and resources needed to increase contact with our operational staff. Building trust in what are trying to achieve will take time when you have people used to the safety function traditionally just coming to check things.”
“People were sick of ticking boxes to satisfy investigation structures for simple events and not getting enough good information on complex ones”
Powerlink’s HSE strategy focuses on building on its safety learning methodologies and improving psychological safety, with a continued focus on control improvement. Its maturing HSE approach has been supported
in 2022/23 by piloting the introduction of control performance intelligence tools to enable analysis and actionable insights.
Last financial year, the organisation also matured its measurement of HSE performance towards proactive learning by implementing a program of HSE risk inspections focused on understanding how its controls are performing. This also focused on improvements to controls for hazardous manual tasks, seeking to take a preventative approach to injuries.
Leading and measuring safety at Powerlink Queensland
In working with Powerlink Queensland’s leadership team to integrate safety into the culture of the organisation, Saal said the first step was to build an understanding of contemporary safety theory and research. Safety is one of the disciplines where certain approaches have been so heavily drummed into people that there is some work to be done to undo certain assumptions, he explained. “We provided leadership teams with some reading material and videos to begin challenging some old methods for doing safety to start the change process,” he said.
The next step was to provide updated tools and systems to guide more
contemporary practice, as he said an understanding of what can be better derived from some contemporary information needs to be coupled with methods to do it. “The benefit of being able to fix people’s bug bears while updating your methods also helped with the change,” he said.
A key change for Powerlink has been how it measures safety performance, with a focus on lead indicators rather than lag indicators such as total recordable injury frequency rate (TRIFR). Lead indicators include injury reduction, control review, and lessons learnt, for example. “We worked to do away with meaningless old metrics, but putting something in their place is always a challenge. For our first step, we opted to start talking about learning effort and qualitatively describe the control improvement arising from it as our indicator of performance,” he said.
One of the main benefits of these approaches has been a shift in discussions to control improvement. While there is still work to do to shift the majority of effort to control validation and improvement (as opposed to other safety work that doesn’t derive the same benefit), Saal said that “once people can start to describe controls and how they are performing and improving, we’ll know we are starting to see the outcomes we are after.”
Inside Telstra’s return to work program
Telstra’s
work transition program is an innovative and effective model
for helping employees with the process of returning to work, writes Craig Donaldson
Telstra is Australia’s leading telecommunications and technology provider with a market capitalisation of approximately $49 billion and more than 31,000 employees. The company operates in a sector where the safety and security of its teams are often placed at risk. Employees and contractors, for example, are involved in major construction works, working at significant heights and other similarly dangerous situations.
As well as physical safety risks, Telstra actively monitors a diverse range of other health, safety, and wellbeing outcomes. These include the security of its workplaces and premises, the mental health and wellbeing of employees, and the potential for harm to the environment and the communities in which employees work.
Telstra employs an SSW (safe system of work) risk governance framework (see box) which governs the way the company manages and report these risks. This framework aligns with rigorous ISO standards. There has been an improvement in key performance metrics that measure safety and security and maintain a constant focus on relevant risks. The company promotes a range of health and wellbeing services to increase awareness and understanding of the services available to employees and contractors, including mental health and wellbeing services.
Returning to work
Telstra’s work transition program is a bespoke workplace rehabilitation service that provides the complex support people need to return to suitable employment following an injury or illness. This has resulted in a significant increase and improvement in successful rehabilitation outcomes for many employees in need of assistance, some of whom had been out of the workforce for extended periods of time.
Nancy Abdelnour, principal, support and recovery for Telstra, who is tasked with
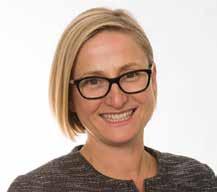
Nancy Abdelnour, principal, support and recovery for Telstra, says people need to be empowered and engaged in their own return to work journey
leading the company’s work transition program, explained the broader thinking behind the program. “We want people to have long and rewarding careers here at Telstra, which is why we consistently review aspects of our employees’ career experience to see where we can improve,” she said.
“Before we introduced the work transition program, we reviewed existing program offerings and found that there was more we could do for employees returning to work after a work-related injury. We knew we could do better to support them to make a meaningful and sustainable return to work.”
From a vocational rehabilitation standpoint, it was found that previous return to work programs were often time limited, prescriptive, and compliance driven. Abdelnour said there was an opportunity to consider people more holistically, including their cultural and social beliefs, their level of engagement, and what their realistic career aspirations were. “As an organisation, we wanted to do better for our people,” she said.
Key aspects of the work transition program
Abdelnour explained that injured workers who are unable to return to their
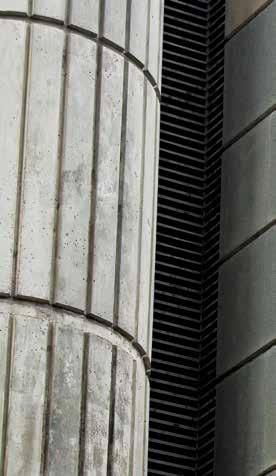
pre-injury role often find navigating the process around sourcing new roles within Telstra or external employment daunting.
“The work transition program aims to support and partner with injured workers, whether they are a current or former Telstra employee, to help them navigate the complex path of a career change,” said Abdelnour. “This bespoke rehabilitation offering is a people-centric program that changes the way we engage, motivate, and support our job seekers to find and secure new meaningful employment.”
The work transition program is made up of three key pillars: exploration, work readiness, and active job seeking. Through partnerships with Telstra’s workplace rehabilitation provider panel, the business, and ongoing feedback from job seekers, Abdelnour said several tailorable modules and training programs were developed to comprehensively support people to obtain and/or sustain new employment. “Typically, a person going through work transition program would be involved in vocational coaching discussions along with tailored training programs which complement their existing skillset, with the goal being better alignment with actual employment opportunities,” she said.
Keys to success
There have been a number of elements that have been key to the program’s
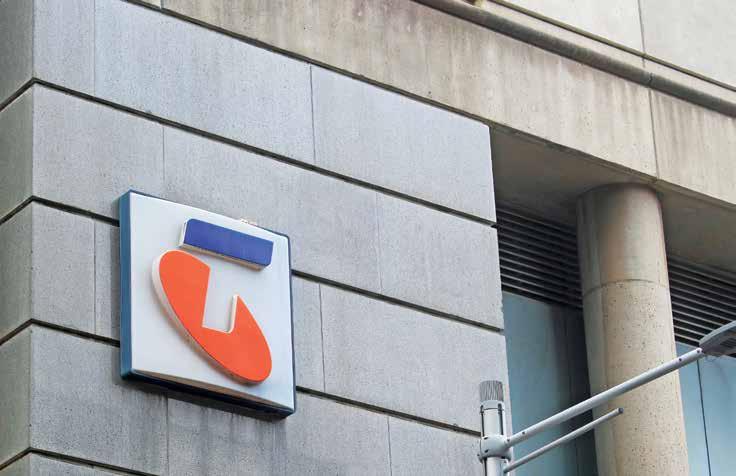
success, according to Abdelnour. “We removed the rigid and prescriptive single service assessments and compliance-focussed tasks of conventional job seeking programs, and developed a system that truly partners with our people, their health and social network, representatives, and our business,” said Abdelnour, who explained that this process has helped unlock people’s true potential to become the most employable candidate they can be.
“We’ve also focused on ideal career pathways, their future, and what they could achieve, to help drive motivation and engagement in the program”
The program focuses on the whole person and understanding their unique circumstances, which Abdelnour said is necessary to create the most successful path forward for a career transition. Modules
with specific learning objectives have been created to help people become as employable as possible. This includes embedding ‘soft skills’ into the rehabilitation program, such as phone call and interview techniques, verbal and non-verbal communication skills, and computer literacy. “We’ve also focused on ideal career pathways, their future, and what they could achieve, to help drive motivation and engagement in the program,” she said.
Results of the program
Abdelnour said the results of the program have been “overwhelmingly positive”, with a dramatic increase in successful rehabilitation outcomes. More than 70 current and former employees have now participated or are currently engaged in the work transition program. Feedback from participants, business stakeholders, medical practitioners, union representatives, and rehabilitation providers has also been very positive. “All stakeholders have found the program to be comprehensive, with a suite of tools and resources that empower our people to look at their career development and job seeking progression,” she said. Compared to the three years prior to the introduction of the work transition program, there has been an increase in the success rate of rehabilitation outcomes of 750 per cent for current employees and 800 per cent for ex-employees. These results
Developing an effective return to work program
For other WHS and related professionals looking to develop an effective return to work program, Abdelnour said that one step that has made a measurable difference has been to ensure that people are empowered and engaged in their own return to work journey. “Developing people-centric, evidence-based programs is critical to optimising the results of any return to work program,” she said. “The key to our work transition program and its success lies in our laser focus on ensuring our people know that they are the key in developing a realistic, achievable, and enjoyable redeployment goal that not only supports their immediate recovery, but also serves as an important milestone in their career journey.”
have only resulted in a marginal increase in the rehabilitation costs required to service the needs of the work transition program. “We couldn’t be prouder of the significant human and financial impact for our people and our business,” said Abdelnour.
Rethinking contractor safety management: changing perspective
The job of safety professionals is not to manage contractor safety on behalf of contractors, but to ensure the safety of contractors at their sites, write
Sue Bottrell and Jon Harper-SladeContractor safety management is a critical function for many organisations. There has been a discernible shift in contractor management in recent years, with a more collaborative approach between organisations and contractors at all levels of work and down through supply chains being adopted.
There have also been some significant shifts in the legislation and regulation of safety and governance priorities through supply chains (incorporating contractor relationships), which have clarified the relationship between contractors and those who hire them. However, this clarification does not seem to have had the desired impact on processes designed and implemented to manage contractor safety.
Often, activities undertaken in the name of contractor safety management are focused on managing safety on behalf of contractors, which is looking in the wrong direction. The result of this is that almost all our time is spent staring obsessively at contractor safety management systems as opposed to our own.
For principal contractors, the inclusion of contractors as workers under safety legislation creates a primary duty of care to ensure the safety of contractors, and a secondary duty to ensure a contractor is working safely so as to not harm workers and others at the workplace. It does not create a duty to manage safety on behalf of a contractor in respect of the contractor’s own work or workers. The duty is also limited by reasonable practicability, with the High Court finding that it is not reasonably practicable, due to issues of knowledge, suitability, and cost, for a principal contractor to direct or supervise contractors in their method of work.
The general interpretation of this duty to contractors is that it creates a duty of the principal contractor to ensure that contractors’ methods of work are safe in a general sense, including approving and even directing them in their work and then supervising that they are working safely.
This results in contractor safety management systems that are almost exclusively designed to focus on how contractors are
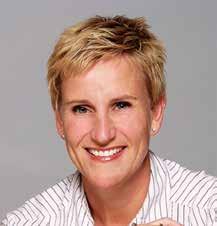
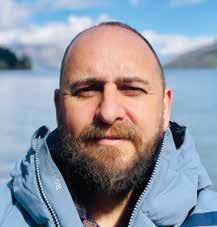
managing safety, whereas the focus should be primarily on ensuring a principal contractor does not pose a risk to contractors working in their workplace. As a result of this mistakened focus, most organisations fare pretty poorly when it comes to contractor safety management and are often implementing complex systems that do very little to improve safety.
A paradigm shift is needed, which requires a change in mindset to a perspective where the client (or buyer of services) is intrinsically linked to the success of contractors (or suppliers of services) through the management of both parties’ operational risks.
However, on a positive note, there has been a shift over the past decade towards the recognition of the independence of contractors in managing their own safety. There has also been a significant amount of focus placed on strengthening partnerships between organisations and contractors, resulting in greater cooperation and discussion about safety and its management by both contractors and principal contractors.
Common contractor management challenges
Organisations face a number of common issues when it comes to contractor safety management, with the most common being:
1. A misunderstanding of the duty of care owed to contractors.
2. The implementation of complex systems to manage contractor safety.
3. Failure to recognise contractors as experts whose primary role is to deliver their specialist work safely.
Another observation is that there is way too much focus and weight given to health and safety prequalification, which generally relies on assessing documented safety systems to confirm contractor operational safety management. There is not enough focus on ensuring contractors are selected based on their demonstrated capabilities and capacities to deliver safe work outcomes. Organisations and their WHS professionals need to question the relevance of documented safety management systems and redirect their efforts towards consultation and communication versus management.
This also has unintended impacts on smaller businesses that are overlooked because they do not have extensive written safety management systems. A decluttering of the bureaucratic load downstream urgently needs to be addressed.
The reality is most safety management systems prepared by contractors do little to improve safety, and they often result in enough paperwork to keep the most diligent safety professional chained to their desk. The obsession with collecting and reviewing documented contractor safety management systems prevents time and

effort being spent where it matters, such as on identifying what we are doing to make our contractors’ jobs harder and less safe, and discussing with contractors the work they are doing to understand their hazards and safety arrangements in real-time.
Addressing contractor management challenges
There are a number of important steps organisations can take to address these common contractor safety management challenges, with the most critical being looking at your own safety management arrangements first and considering if they adequately control risks that can harm your contractors.
Then, consult with contractors about their work, the risks that may be imported into your workplace, and how you will cooperate and communicate to identify what each party needs to do to control those risks. Finally, let them get on with their job.
Referring to ‘contractor management’ also creates the wrong impression and leads us to think clients need to be managing the work of their contractors, which is not useful. Perhaps it should be titled ‘contractor safety engagement’, which will lead us to think about whether we adequately support their contractors in the execution of safer work.
Organisations are as diverse as the people who work in them, so there are
no ‘cookie cutter’ solutions. There are, however, some general principles that can help guide what we do. In the forthcoming OHS Body of Knowledge chapter, we detail the four pillars of modern contractor safety management:
1. Effective and efficient prequalification that limits the collection of documentation, but confirms the roles of both contractors and principal contractors in safety management and obtains assurance of safety arrangements.
2. Informed onboarding to ensure contractors know where they are working and the risks posed by the workplace they are working in, to enable them to be safe and design safe work.
3. Meaningful assurance of both contractor and principal contractor performance in the achievement of safe workplaces.
4. Diligent performance reviews to inform continued relationships with contractors.
Improving contractor management
WHS professionals are in a key position to change or influence contractor safety management for the better. The advice for safety professionals is to change your point of view. Your job is not to manage contractor safety, but to ensure the safety of contractors at your sites.
Primarily consider your own workplace and safety arrangements. Spend 90 per cent
Collaborating with contractors on safety
A more collaborative approach to contractor safety management is gaining traction. This new model emphasises partnership and open communication between organisations and their contractors. The benefits of such an approach are significant: Shared safety goals: Collaboration fosters a culture of shared responsibility, where both parties prioritise safety throughout the project lifecycle. This leads to the improved identification and mitigation of risks.
Focus on capabilities: While prequalification processes can be a helpful starting point when engaging a contractor, a documented safety system may not always reflect a contractor’s actual ability to deliver safe work. A collaborative approach encourages a focus on demonstrated safety practices and capabilities. Streamlined efficiencies: The excessive bureaucracy associated with prequalification and oversight can hinder both organisations and contractors. Collaborative approaches aim to streamline processes, freeing up resources for open communication and improved risk management.
of your time working with your contractors to ensure they understand your workplace and how your risks can impact them and their work.
Also, respect their skill and ability. If you don’t think they can do the job and manage their own safety, you should question why you hired them. If you do need to ‘work’ with contractors because you think they aren’t managing safety, ask lots of questions, but don’t assume that a lack of written safety documentation equals poor safety.
Focus on doing the basic things well and maintain empathy for what it’s like for the smaller businesses providing services either directly or indirectly through sub-supply chains. Think more about what your organisation is doing and how your approach will enhance the ability for your suppliers to execute their best work. Use their perspectives and expertise to build your own systems.
Sue Bottrell is a chartered safety professional and lawyer with ContractorSAFE, and Jon Harper-Slade is GM health and safety innovation for Construction Health and Safety New Zealand (CHASNZ). Bottrell and Harper-Slade are co-authoring a new chapter on contractor management in the OHS Body of Knowledge.
How complex systems fail: lessons from Boeing’s 737 MAX 8 crashes
A complex systems approach is a more useful way of analysing incidents such as Boeing’s 737 MAX 8 failures, writes Dr Sean Brady
On the morning of 29 October 2018, Lion Air Flight 610 – a Boeing 737 MAX 8 aircraft – is preparing for take-off at Soekarno-Hatta International Airport, Jakarta. In command is 31-year-old Bhavye Suneja, who has more than 6000 hours of flight time, most of which were in previous versions of the 737. His co-pilot, Harvino, is ten years older, with more than 5000 flight hours.
At 6:20 am, they take off. But only minutes into the flight, Suneja’s control column starts shaking. This indicates the plane is nearing a stall, a situation where the angle of the plane’s wings – the plane’s so-called angle of attack – is too steep, which results in a loss of aerodynamic lift. At the same time, two alerts go off in the cabin: bad altitude and air speed. Harvino asks the Captain if he wants to turn around, but Suneja says no. He asks Harvino to get clearance for a holding point to buy them some time. Harvino gets on the radio: “Flight control problem.”
Then the nose of the plane suddenly dips forward. Suneja has no idea why it’s happened. He presses the trim switch on his control column, which changes the angle of the small wing on the rear of the aircraft – the horizontal stabiliser. The nose of the plane comes back up. But then it suddenly dips forward again. It’s like the aircraft has a mind of its own.
Beside Suneja, Harvino is working through Boeing’s quick reference handbook, looking for an emergency checklist to work out what’s wrong. But the handbook is no help – it says nothing about the nose repeatedly pitching downwards.
Over the next eight minutes, Suneja continues to fight with the controls. The plane repeatedly pitches forward, filling
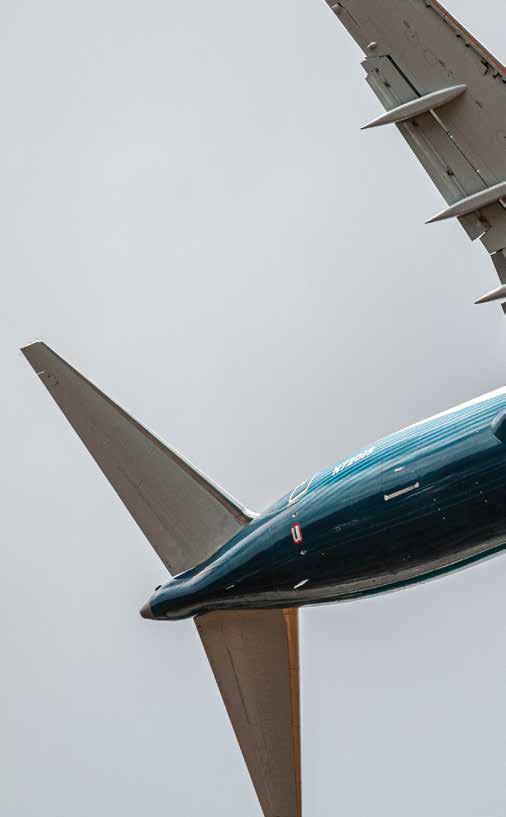
the pilots’ view with the blue expanse of Jakarta Bay. And each time, Suneja flicks the trim switch, and the nose comes back up. Then it pitches downwards again. It does this 21 times, and although they are cleared for an altitude of 27,000 feet, they are still less than 6,000 feet in the air and dangerously close to the water.
Suneja asks the co-pilot to take the controls. But as Harvino takes over, the plane
pitches downward again. Harvino presses the trim switch, but not as hard as Suneja had. The plane pitches further forward, then further forward again. Harvino tells the Captain they’re pointing downwards. Distracted, Suneja says, “It’s okay.”
They plummet at 10,000 feet per minute. Harvino pulls desperately on the control column, but it has no effect. Alarms blare in the cabin: “Sink rate, sink
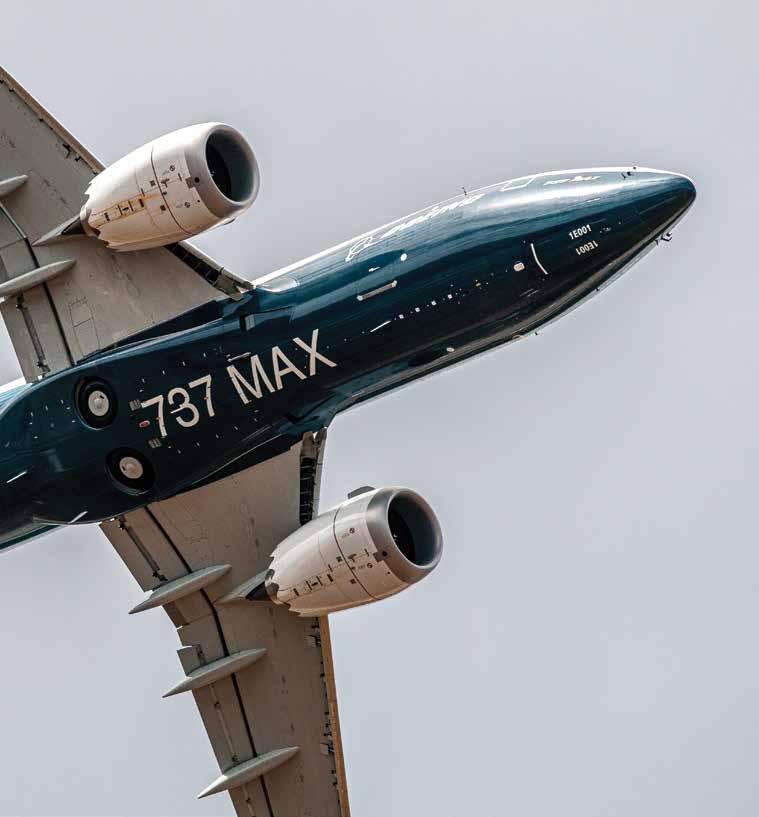
rate.” Blue water fills their view. Harvino starts to pray. Suneja is silent. The alarms continue: “Terrain, terrain.” They hit the water at an almost vertical angle, travelling at 800km/h. All 189 people on board are killed.
Over the months that followed, two narratives played out. The public narrative was driven by Boeing’s CEO and top engineers, as well as by the airline regulator
in the United States, the Federal Aviation Administration (FAA). As far as they were concerned, there was no fundamental issue with the 737 MAX 8. They claimed the cause of the crash was Lion Air’s fault, saying that the Indonesian airline was poorly managed.
In time, the technical cause of the failure would be identified as an issue with one of the plane’s angle of attack sensors.
As its name suggests, this sensor measures the plane’s angle of attack, which is the angle of the wing relative to the airflow. It was found to be reading an erroneously high angle, which incorrectly suggested that the aircraft was nearing a stall. But we know that aircraft are designed and built with multiple layers of redundancy, so how could an incorrect reading from a single sensor crash a plane?
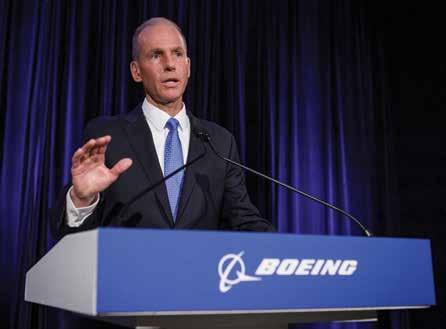
Complex systems
When we think about cause and effect, it would be very easy to conclude that this issue with the angle of attack sensor ‘caused’ the crash. In other words, the crash could have been avoided if the sensor had been working correctly. But when we examine systems as complex as the 737 MAX 8, we need to think about failure differently. We need to take a complex systems approach.
“In March 2019, Boeing’s CEO, Dennis Muilenburg, got the highest paycheque of his career: US$31 million, including a US$13 million bonus for performance”
Many of us think in Newtonian terms, meaning that when we examine systems, we tend to believe there is a direct link between cause and effect – everything that happens has a definite, identifiable cause and effect. Furthermore, we expect symmetry. The seriousness of the effect is related to the seriousness of the cause, significant failures happen because of significant causes, and vice versa.
However, this is different for complex systems, which are systems made up of
agents or components that interact with one another and produce feedback. While we often think of systems as ‘the sum of their parts’, complex systems are better thought of as ‘the sum of their parts and interactions’.
An analogy is a sports team. The overall performance of a sports team is so much more than the sum of the abilities of the individual players. A good team is one where the interactions between those players produce a performance that transcends the abilities of the individuals. Further, attempting to understand the overall performance of the team by studying each player in isolation will not provide much insight into the behaviour of the team as a whole.
Just as a team is the sum of its players and their interactions, in complex systems, it is these interactions that result in complex systems having a disproportionate relationship between cause and effect. This means that relatively small causes can produce very large effects. For example, the assassination of Archduke Franz Ferdinand in 1914 in Sarajevo sparked the First World War and led to millions of deaths. How could a single assassination lead to a world war?
The sand pile model
There is a different way to think about system failures, to help us on this journey: a model of a sand pile. This model, which started as a thought experiment, was developed by physicist Per Bak. As described in Mark Buchanan’s Ubiquity: Why Catastrophes Happen, Bak and his colleagues created what physicists often
describe as a ‘toy model’ – a model that allows you to think about complex phenomena in a simple way. Considerable research has been done on this model, and we will only examine a few key concepts here.
The model is as simple as it is profound. Bak asks us to imagine the following situation: we have a tabletop and drop grains of sand onto it at random locations, one grain at a time. As more and more grains fall, they build up into small hills. The formation of these hills is random because the grains of sand fall at random locations. As the hills grow taller, they become steeper. Eventually, one becomes so steep that an avalanche results when the next grain of sand lands on it. This avalanche could be localised, or it could trigger further avalanches as it strikes neighbouring hills.
Now, consider what is causing these avalanches. On one hand, we could say that the cause of the avalanche is the single grain of sand that fell and struck the hill (as the avalanche only occurred because this specific grain fell at this precise location). But blaming the single sand grain alone doesn’t fully explain why the avalanche occurred.
Firstly, most sand grains that fall on the table do not result in avalanches. Secondly, a single grain of sand can start a small or large avalanche. The initiating event for each is the same, but the magnitude of the effect is independent of the initiating sand grain. In other words, the single grain of sand doesn’t help us explain why the magnitude of some avalanches is then greater than others.
Instead, we can attribute the cause of the avalanche to the hill itself. If the hill weren’t shaped as it was, the grain of sand would not have initiated the avalanche. Shifting our thinking about the cause of the avalanche, from the grain of sand to the shape of the hill, has several profound implications for understanding failure in complex systems.
If we accept that the shape of the hill –and not the sand grain – dictates the risk of an avalanche, then understanding how the hill came to be that shape is critical. We, therefore, need to know its history –how it was produced as each grain fell on it. In complex systems, we cannot take a snapshot in time, but we must consider the culmination of steps that brought us to this point.
Further, it introduces the concept of the ‘critical state’. As more and more sand falls on the table and the hills get taller, the system is becoming more and more at risk of an avalanche. Bak described this process of reaching a critical state as ‘self-organised criticality’ because no one is
organising the sand pile and increasing the risk of an avalanche. Instead, it is doing this naturally because of the interactions between the individual sand particles. As Miller & Page state in Complex Adaptive Systems: An Introduction to Computational Models of Social Life: “The key driving force behind self-organised criticality is that micro-level agent behaviour tends to cause the system to self-organise and converge to critical points at which small events can have significant global impacts.” The sand pile model, therefore, is a helpful way to understand why simple causes can produce significant failures in complex systems.
“A single grain of sand can start a small or large avalanche. The initiating event for each is the same, but the magnitude of the effect is independent of the initiating sand grain”
For example, we can use it to re-examine the cause of the First World War. Serbian nationalist Gavrilo Princip assassinated Archduke Franz Ferdinand in Sarajevo in 1914, setting in motion a series of events that led to a world war. But when we look at this through the lens of the sand pile model, as Mark Buchanan does in his book, Ubiquity, he suggests that we should think of the assassination as a grain of sand and Europe as a hill in the sand pile. This hill was in a critical state due to interlocking treaties between multiple countries – a state ripe for a single grain of sand, Gavrilo Princip, to fall and start an avalanche. Once this grain landed, the interactions between the European parties cascaded and resulted in the war, just like the cascade of grains in the sand pile. If it hadn’t been for Princip and the assassination, there probably would have been another initiating event. It was the critical state that mattered, not the specific grain of sand. With this in mind, let’s go back and examine the story of the Boeing 737 MAX.
Boeing, Airbus and the A320neo
The story of the MAX begins not with Boeing but with its rival, Airbus - a
European consortium that received its first order in the US in 1978 and who, in 1984, launched the Airbus A320 in direct competition to Boeing’s existing 737. In 2010, it repeated the move with the A320neo, a plane designed to take more market share from the 737. This aircraft was larger than the previous A320 and was more fuel efficient, with the ‘neo’ standing for ‘new engine option’. By the Paris Air Show in June 2011, Airbus had secured more than a thousand orders.
Boeing had to respond – more than a third of their profits came from the 737 –but they didn’t have an aircraft that could compete with the fuel efficiency of these new planes. Then in July that year, they got word of a potential deal between American Airlines and Airbus. It looked like the airline was about to order the neo. Boeing stepped in to try and secure its own deal, convincing American Airlines to split the order: the airline would buy 260 A320neos, with the remaining 200 planes being a more fuel-efficient aircraft from Boeing. This plane, which was entirely hypothetical at this point, would come to be named the 737 MAX 8.
Developing the 737 MAX 8
The original Boeing 737 was launched in January 1967. By 1988, it was flown by over 137 operators worldwide and described as the ‘unsung prodigy’ of the Boeing family. It would also form the basis of the 737 MAX 8. Boeing planned to take the existing plane, replace the engines with more fuel-efficient ones, and bring them forward on the wings.
A critical decision made early in the MAX’s development was that Boeing wanted pilots already trained on the existing 737 to be able to fly the MAX with no additional simulator training. Training is a significant cost for airlines: simulators cost around US$15 million each, pilots have to be taken out of service, and the training itself costs hundreds of dollars per hour. In fact, training, wages, and maintenance costs amount to 20 per cent of the overall costs of running an airline – more than they spend on fuel. If Boeing could put a new plane on the market without requiring pilots to undertake additional simulator training, it would give them a massive advantage. But to achieve this, they had to ensure they could modify the existing 737 and not add any new functionality that would change the handling or operation of the aircraft.
To understand the environment in which the development of this aircraft occurred, we need to look at Boeing’s history and the dramatic changes it went through from 1997 onwards. The company was founded
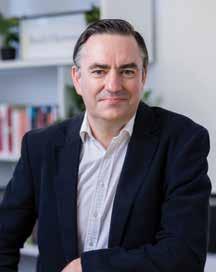
Dr Sean Brady says the sand pile model is a helpful way to understand why simple causes can produce significant failures in complex systems
in 1916. By 1944, it had a workforce of 50,000 people, and by the 1960s, this had jumped to 142,400. They were all about producing high-quality, safe planes and had a saying: “We hire engineers and other people”. At meetings, designers were encouraged to fight loudly for what they wanted on the planes to make them safer.
But in 1997, they merged with McDonnell Douglas – a company much more cut-throat when it came to cost-cutting. As the McDonnell Douglas executives spread throughout the organisation, their approach to building planes began to dominate how Boeing operated. The infiltration was described as ‘hunter killer assassins’ being let loose on a room full of engineers. The organisation started to change – in many ways, a microcosm of the Jack Welchinspired culture of the times. Cost-cutting and a return on shareholder investment seemed more important than producing quality aircraft. Engineering views took a back seat. The ‘other people’ were now firmly in charge.
Against this backdrop, the design of the 737 MAX 8 got underway, with a focus on ‘more for less’. A countdown clock was set up in the conference room where program meetings took place to remind people there was no time to waste. Overshadowing every decision was the drive to ensure no new functionality was added to the aircraft, which would have required additional pilot training.
The Manoeuvring Characteristics Augmentation System
A big problem with Boeing’s design approach for the MAX emerged during wind tunnel tests on a scale model of the
aircraft. The model pitched up during tight, high-speed turns due to the new engines being placed further forward on the wings. This behaviour was a genuine concern: if the plane pitched up too far, its angle of attack would become too steep and it would stall, which could lead to a crash.
The 737 chief pilot, Ray Craig, examined the problem and discovered it only happened in the part of the flight envelope that commercial pilots rarely go. But pilots could enter this zone if they were dealing with high turbulence or responding to some upset. And if they did, the nose of the plane could pitch up and they could stall.
This issue had to be addressed and several mechanical solutions were proposed. They explored putting tiny vanes on the wing, but they didn’t think that would work. The only real mechanical solution was redesigning the tail and removing the pitch-up risk. But this was a costly solution that could delay the plane’s release.
So they agreed upon a software, not mechanical, solution. This software system went by the cumbersome name ‘Manoeuvring Characteristics Augmentation System’, or MCAS for short. The software would detect when the plane was pitching up too far while in this edge-of-the-envelope zone, and it would rotate the horizontal stabiliser at the back of the aircraft and push the plane’s nose back down. This would manage the stall risk. Not only was this solution cheap, but it would ensure the plane handled like the previous 737s – simulator training would not be required.
To detect when the plane was pitching upwards, the software would rely on measurements from two sensors: an accelerometer measuring the plane’s acceleration, and one angle of attack vane mounted on the front of the aircraft, measuring the plane’s angle of attack. While there are two angle of attack vanes on the 737 MAX 8, the software would use only one. Critically, the software would rely on input from two sensors, not one, to control the plane in this edge-of-the-envelope zone. The chief pilot of the project, however, wanted a hardware solution, but was overruled because the software was cheaper.
But adopting this solution did raise a concerning problem. Boeing engineers were worried about what they should call this software and who they should tell about it. There was a real danger that the regulator, the FAA, might view this software as ‘new functionality’. And if they did, it was something that pilots would need to be trained on in the simulator. This was the last thing Boeing wanted: they had publicly announced that existing 737 pilots could
migrate to the MAX by undertaking a short training session on an iPad.
The extension of MCAS
The design and development of the aircraft continued, with the first test flight of the 737 MAX taking place in January 2016. But there was more bad news only a few months into these tests. The pitch-up problem, which the scale model showed only happened near the edge of the envelope, was now also evident at slower speeds. This meant that an edge-of-the-envelope concern could now occur during routine operations. To make matters worse, this stall risk at slower speeds could occur during take-off and landing - the most vulnerable part of the flight, and when the pilots are at their busiest. There was now a genuine concern within Boeing that the FAA would not certify the plane.
“Pilots could now take the plane up without additional simulator training, with a system on board that was not discussed in the manual, which could override their control”
To solve this problem, Boeing extended the software solution to cover these low-speed stall risks. If the aircraft was at risk of pitching up at these slow speeds, MCAS would detect it and activate the horizontal stabiliser on the tail so the plane would pitch down again. This stabiliser, which MCAS could move by 0.6 of a degree previously, could now move 2.5 degrees at slower speeds. But at these slower speeds, the software could no longer use the accelerometer as an input. MCAS now relied on only one sensor: an angle of attack vane. Boeing, who had previously put so much focus on engineering and safety, were now relying on a system with no redundancy if anything was to happen to this sensor. And Boeing had another problem. They’d picked an unproven supplier to deliver the simulator. While Boeing wanted no simulator training for existing pilots, they still needed a simulator for new pilots who had never flown a 737. But simulator development was falling behind. This not only proved a worry for training new pilots,
but it also meant that if the FAA declared that training was required for the MAX, even for pilots who had flown the 737 before, there was nowhere for this training to take place. That would prohibit planes from flying. Now the necessity of convincing the FAA there was no new functionality, specifically around the role that MCAS would play, was crucial.
MCAS was first loaded onto the 737 MAX 8 computer on 15 August 2016 – it was now ready for production. In November of that year, Boeing engineers sent their system safety assessment of MCAS to the FAA. The latest version, revision E, had all the details of how the system would operate at lower speeds and move 2.5 degrees. But revision E was not the version submitted to the FAA. Instead, revision C was submitted, covering only MCAS’s more limited role. Not only did the FAA approve MCAS, but they also approved no reference being made to it in the manual.
Pilots could now take the plane up without additional simulator training, with a system on board that was not discussed in the manual, which could override their control. Most MAX pilots didn’t even know MCAS existed.
The first crash
The grain of sand that would initiate the Lion Air 610 crash was a misaligned angle of attack sensor that erroneously told MCAS that the plane’s angle of attack was too steep. MCAS engaged, activated the horizontal stabiliser, and pushed the nose of the aircraft down. While Captain Suneja could activate the trim switch and pull the nose back up, each time he did, the software would continue receiving data from the misaligned sensor, reactivate, and push the nose back down again. Even when Harvino pulled back on the control column to pull the nose up, this had no effect – MCAS was designed to override it. As Suneja and Harvino continued to battle the aircraft’s behaviour, neither was aware of the software, what it was doing, or what was required to deactivate it. They were entirely at its mercy.
In November 2018, one month after the Lion Air crash – with planes still flying – Boeing met with pilots and trainers. The pilots and trainers were shocked when they heard about MCAS and the fact that they had not been told it was on the plane. Boeing also explained what was required to disable MCAS in the event of a malfunctioning angle of attack sensor. This sequence would turn out to be very difficult to execute in the real world.
Also that month, the Indonesian investigators released their report on the Lion
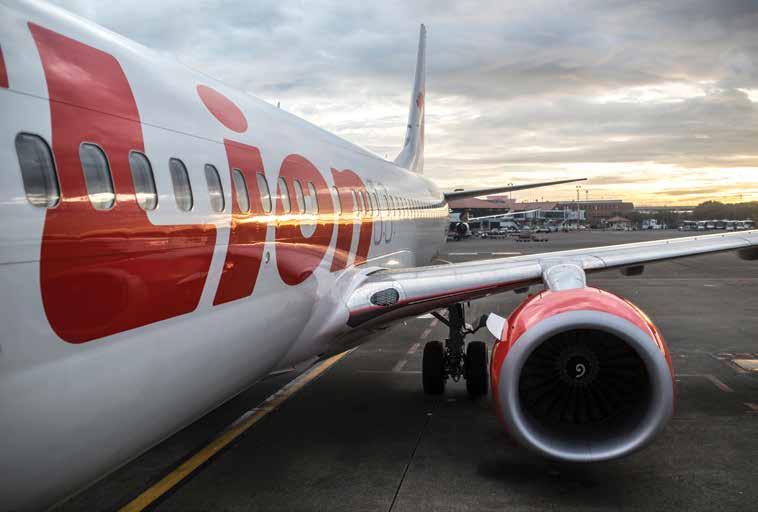
Air crash, primarily blaming the pilots and maintenance staff. The MAX continued to fly, Boeing’s stock price rose over the following months, and the FAA gave them ten months to fix the software, even when the FAA’s own analysis concluded that the MAX posed a serious risk. In March 2019, Boeing’s CEO, Dennis Muilenburg, got the highest paycheque of his career: US$31 million, including a US$13 million bonus for performance.
The second crash
And then, on 10 March 2019, only five months after the Lion Air crash, Boeing received news of a second incident. Ethiopian Airlines flight 302, a 737 MAX 8, had taken off from Addis Ababa Bole Airport. At the time, Ethiopia Airways were considered one of the best-run airlines in Africa. But shortly after take-off, MCAS activated because the angle of attack sensor developed an electrical issue. It was sending incorrect data to the software. The pilots fought against MCAS, trying to execute the sequence Boeing had prescribed for disabling the software. But this was a complex and ill-explained sequence that proved very difficult to execute in flight. The aircraft crashed, tearing itself apart and killing all 157 onboard.
By now, there had been two crashes and 346 people had been killed, yet Boeing still publicly argued the MAX 8 was okay – and the FAA agreed. China moved first and grounded the plane. They were followed by the European Union, India, Australia, Singapore, and Canada. The US grounded it on 13 March 2019.
Seeking closure
A traditional approach to understanding Boeing’s 737 MAX 8 failures would result in us attempting to draw a line between cause and effect, beginning with the issues with the angle of attack sensors. After all, if it weren’t for these faulty sensors, the crashes would have been avoided. But taking a complex systems approach, especially through the lens of the sand pile model, provides a more useful way of viewing these types of incidents.
Rather than trying to string all the contributing factors together in a line, the sand pile model asks us to consider how each of them interacted with one another and layered upon one another to build a hill. It asks us to examine the change in culture at Boeing from engineering excellence to cost cutting; the need to get a new aircraft out quickly and cheaply in order to compete with Airbus; the decision on no simulator
training for existing 737 pilots; the use of MCAS, and then the extension of that use; the software’s reliance on a single sensor; the fear the FAA wouldn’t certify the aircraft if MCAS was deemed new functionality; and the decision not to tell the trainers and pilots about the software, nor provide details of it in the manual. It asks us to treat the issues with the angle of attack sensors as the initiating event, with the failure being the result of the shape of the hill we’ve built, not the grain of sand we’ve dropped.
It asks us to re-examine our more traditional views on cause and effect, and instead look more closely at the sand piles we build in our own projects and organisations. It requires us to ask ourselves if the systems we’ve built are tending towards a critical state, just waiting for that single, innocuous grain of sand to bring them tumbling down.
Dr Sean Brady is a forensic engineer and the managing director of Brady Heywood, where he works with businesses, governments, and the legal sector to investigate and resolve complex issues that typically require a systems approach. He has acted as an expert witness in numerous proceedings involving a wide range of constructed facilities, and authored the Brady Review into mining fatalities that was tabled in the Queensland Parliament in 2020.

Dr John Downer is associate professor in science and technology studies at the University of Bristol. His 2011 article in the American Journal of Sociology and chapter in the 2019 book, Safety Science Research, argued for a new category of ‘epistemic accidents’. In 2023, he changed the label to ‘rational accidents’, in part to pay “homage” (p10) to Charles Perrow and his 1984 book, Normal Accidents: Living with High-Risk Technologies, and in part because ‘epistemic’ “can be an onerous word” (p96). Perrow commented on many drafts of Rational Accidents, but Downer’s book takes a different route and logic to reach conclusions about the dangers of ‘catastrophic’ technologies such as nuclear power and weapons. He employs a ‘finitist cosmology’ version of constructivism, criticising a ‘positivist’ “pervasive cosmology of technoscientific knowledge” (pp14-15).
Downer states that “safety is always a holistic accomplishment requiring constant work on a wide range of fronts: as much a function of organisation and culture as of engineering epistemology” (p18). But “most safety scholarship frames technological failure as a problem to be solved rather than an inevitability to be confronted” (p22). His book “explores only a narrow, albeit vital, dimension of technological safety: the question of how it is even possible for experts to know complex systems well enough to achieve and verify of them extreme reliabilities” (pp18-19).
Rational Accidents: Reckoning with Catastrophic Technologies
Book: Rational Accidents: Reckoning with Catastrophic Technologies
Authors: John Downer
Publisher: The MIT Press, 2024
RRP: $100
ISBN: 9780262546997
Reviewed by: Kym Bills, FAIHS (Life)
He defines rational accidents as “accidents that occur because a technological understanding proves to be unsound, even though there were rational reasons to hold that understanding before (although not after) the event … rational accidents can arise from uncertainties embedded in a single element” (pp96-97). A key argument is that because models and tests simplify knowledge about reality, their use to reduce technological risk and error involves underdetermination, circularity, and a knowledge gap that can lead to a rational accident. While his citation of the Quine-Duhem problem (that points to implicit background hypotheses) is overly simplistic, the gap can be important.
Downer states that an ‘aviation paradox’ (p16) drives his argument - namely how passenger jet travel can be ‘ultrasafe’ and uniquely avoid most rational accidents (pp216-217). His answer includes conservatism in design/changes, a high volume of operational data, and incentive structures not found, for example, in nuclear power or offshore petroleum extraction.
Downer uses the 1988 Aloha Airlines B737 delamination accident as an exemplar of his new unavoidable rational accidents category. While it was an unexpected accident, I wasn’t convinced that it was unforeseeable that the aircraft’s age and usage cycle fatigue could combine with saltwater corrosion in Hawaii’s warm conditions. Downer sometimes used old data (e.g. pp31-32) or
loosely cited accident reports – for example, AirAsia 8501 did not crash in 2014 primarily because of flight computer malfunction. Rather, a cracked solder joint impacted both rudder and computer operation, flight crew response was implicated, and the rudder limiter system had had 23 maintenance reports within the prior year. However, I agree with Downer that Boeing’s 737 MAX accidents illustrate the dangers of prioritising profit and downplaying design changes and risks - but this weakens his aviation uniqueness thesis.
“Downer’s book takes a different route and logic to reach conclusions about the dangers of ‘catastrophic’ technologies such as nuclear power and weapons”
In a 2023 article, Barry Turner: The Under-Acknowledged Safety Pioneer, I summarised Perrow’s focus on a small number of technologically deterministic (hence ‘normal’) but unpredictable/ unpreventable emergent ‘system’ accidents - particularly rare catastrophes with multiple causative factors, involving high ‘interactive complexity’, ‘tight coupling’, and the ‘catastrophic potential’ that
Downer distinguishes from rational accidents. Downer (p103) briefly cites Turner’s landmark 1978 book, Man-made Disasters. However, in many ways, Downer’s rational accident thesis is seen in Turner’s concern with model and information inadequacy (p132-133) or lack of visibility and discussion of warnings and learning when information is completely unknown and unsuspected; known but not fully appreciated; known by someone, but not brought together with other information so as to be acted upon; or available to be known, but not appreciated because there was no place for it within prevailing modes of understanding (pp194-195). Turner was not a naïve positivist, concluding that while “we can continue to try to improve... we are in a contingent universe, in which ultimately there are limits on our ability to reduce uncertainty, to master all of the open-ended and perverse qualities of our environment, and upon our ability to prevent disaster… We may come to realise that, even when our strategies are successful, they are still dependent upon the munificence of the environment and upon the mutability of fortune” (p201).
Having purchased this book, I wanted to like and recommend it but sadly found that despite some strengths, its long gestation had not worked in its favour.
Kym Bills, FAIHS (Life), is a PhD candidate at Edith Cowan University & visiting research Fellow at the University of Adelaide

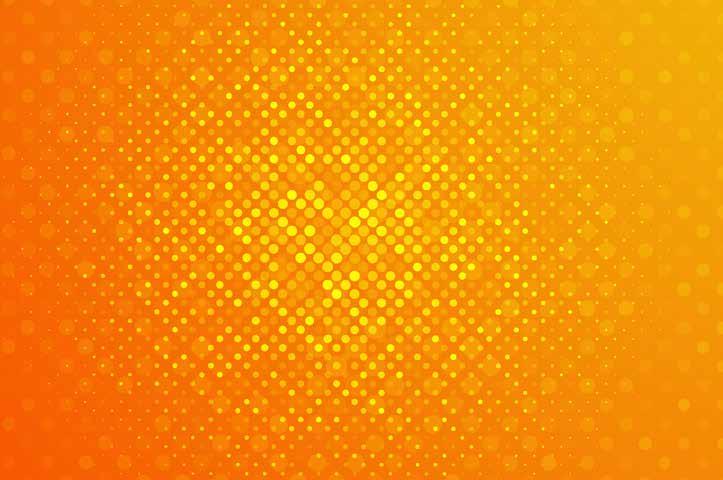
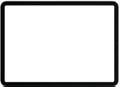



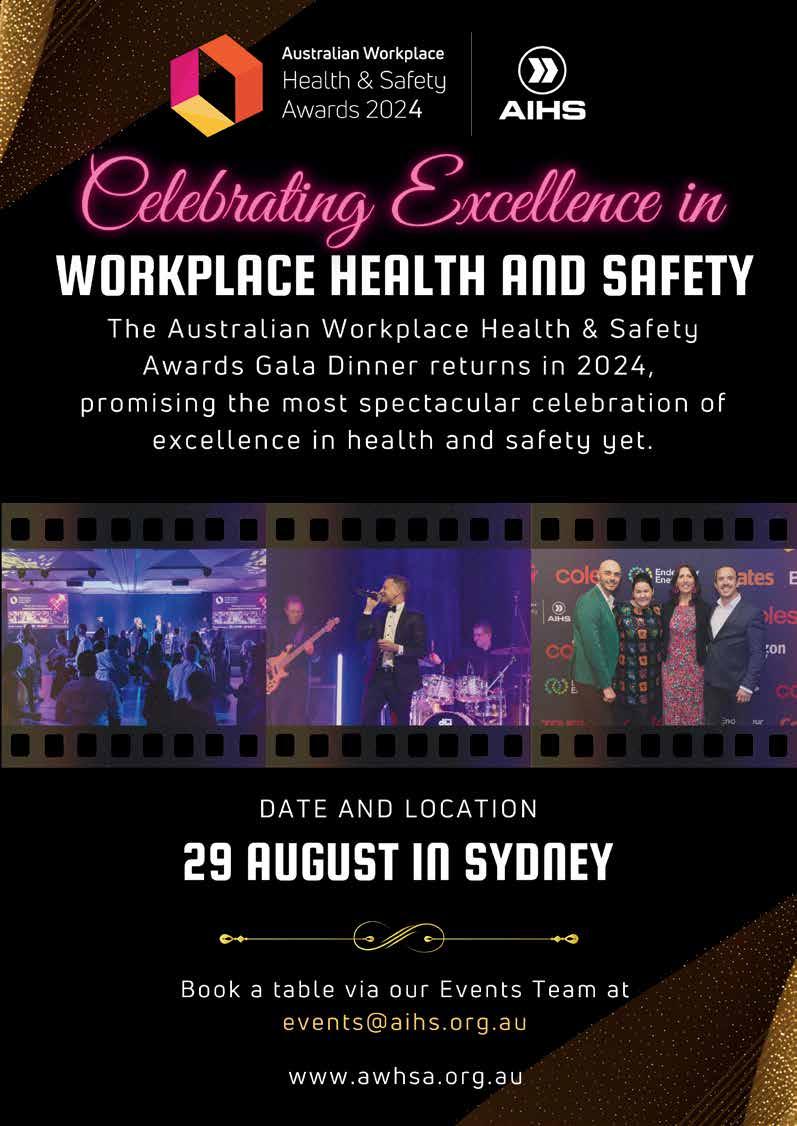