
4 minute read
Kaltfräsen im Großeinsatz
Im Rahmen der Sanierung des Flughafens Leipzig/Halle mussten innerhalb von 30 Tagen die 3 600 m lange Landebahn und die zugehörigen Rollbahnen vollständig abgetragen werden. 350 000 t sehr harter, durchgehend mit Stahlmatten bewehrter Beton (CRCP) wurden im schneidenden Verfahren ausgebaut. Um das Großprojekt zu bewältigen, hat das beauftragte Bauunternehmen leistungsstarke Wirtgen-Maschinen der Klasse W 250 Fi mit modifizierten Sonderfräswalzen eingesetzt.
50 %
Advertisement
Für die Baumaßnahme wurden die Großfräsen mit Eco-Fräswalzen und speziellen Meißeln ausgerüstet. Diese Fräswalzen sind mit bis zu 50 % weniger Fräsmeißeln in größeren Linienabständen als Standardfräswalzen bestückt.
Der Komplettausbau der nördlichen Start- und Landebahn war notwendig, weil der »Betonkrebs«, eine Alkali-Kieselsäure-Reaktion, wie sie auch auf älteren Autobahnen vorkommt, den Beton sukzessive von innen heraus irreparabel zerstört hatte (das bauMAGAZIN berichtete bereits in Heft 11/21, Seite 35).
Für ein Projekt dieser Größenordnung bedarf es leistungsstarker Maschinen und einer optimalen Schneidwerkzeug-Bestückung der Fräswalze. Die WirtgenKlasse W 250 Fi verspricht mit mehr als 1 000 PS zu jedem Zeit- punkt genügend Leistungsreserven. Um die Leistung optimal für den Schneidvorgang nutzen zu können, wurden die Großfräsen mit Zusatzgewichten ausgestattet. Das höhere Einsatzgewicht führt zu einer höheren Traktion an den Fahrwerken, um damit eine optimale Schneid- leistung an der Fräswalze zu garantieren. Für die Baumaßnahme auf dem Leipziger Flughafen wurden die Großfräsen zudem mit Eco-Fräswalzen und speziellen Meißeln ausgerüstet. Die Eco-Fräswalzen sind mit bis zu 50 % weniger Fräsmeißeln in größeren Linienabständen (LA) @c50 als Standardfräswalzen bestückt. Die geringere Anzahl der Schneidwerkzeuge verringert den Schneidwiderstand und macht damit auch das Fräsen harter Betonbeläge möglich.
Speziell für das harte Betonfräsen wurden die Wirtgen W 250 Fi mit Sonderfräswalzen und Zusatzgewichten ausgestattet.
Mehr als 1 100 t Beton pro Tag Innerhalb von 30 Tagen baute die leistungsstarke Fräsflotte
350 000 t Beton aus. Im Schnitt musste jede Maschine mehr als 1 100 t Beton pro Tag fräsen. Hierzu wurde zunächst die Betondecke schnellstmöglich in Schichten abgetragen. Für das Fräsen der Endlage wurden anschließend Maschinen mit einer präzisen 3D-Nivellierung genutzt, um eine optimale Basis für den Wiederaufbau herzustellen.
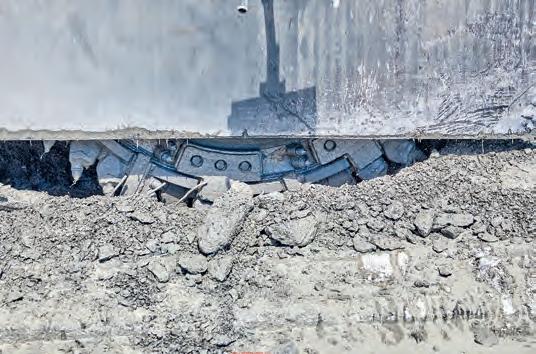
Vielfach angewendet
Betonfräsen ist eine weltweit etablierte Technologie, die Wirtgen in vielen Projekten erfolgreich eingesetzt hat. Auch der Rückbau von mit Ankern, Dübeln und Stahlmatten bewehrten Betonbelägen ist damit durchführbar.
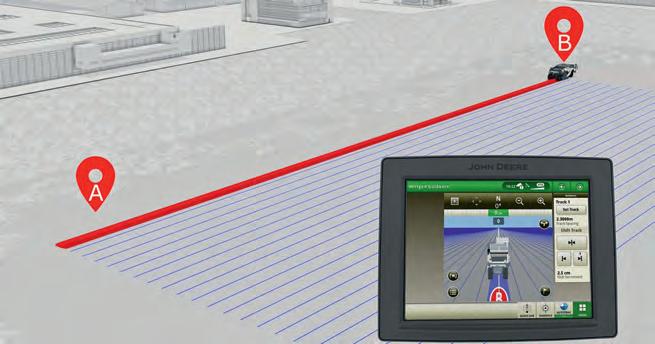
Automatisierungstechnologie AutoTrac für Kalt-Recycler und Bodenstabilisierer
Die Anforderungen an einen verantwortungsbewussten Umgang mit Ressourcen steigen angesichts der Notwendigkeit umweltverträglicher Prozesse auch bei der Bodenstabilisierung und dem Kalt-Recycling – nur bei effizienter Durchführung lassen sich diese Prozesse auch wirtschaftlich abbilden. Wirtgen hat für diese Problemstellung das AutoTrac-System für die WR-Baureihe entwickelt.
Bodenstabilisierer werden für die ressourcenschonende Aufbereitung des Unterbaus von Verkehrsflächen eingesetzt. Ungenügend tragfähiger Untergrund wird mit ihnen in belastbaren, tragfähigen Boden verwandelt. Bei diesem Verfahren wird das vorhandene Bodenmaterial genutzt, lediglich Bindemittel wie Zement und/oder Kalk werden beigemischt. Beim Kalt-Recycling mit Maschinen der WR-Reihe werden beschädigte Asphaltschichten in einem Arbeitsgang ausgefräst und granuliert, durch die Zugabe von Bindemitteln und Wasser neu gebunden und wieder eingebaut. Die an Ort und Stelle hergestellten, neuen Tragschichten zeichnen sich daraufhin durch eine sehr hohe Tragfähigkeit aus.
Der selektive Ausbau ermöglicht zudem die Trennung unterschiedlicher Betonschichten und damit auch die Reduzierung von schadstoffbelastetem Material. Weiterer Vorteil: Betonfräsgut lässt sich in der Regel ohne weitere Nachbehandlung wiederverwerten.
Günstige CO²-Bilanz Auch beim Flughafenprojekt in Leipzig wurde der granulierte Beton als wertvoller Recycling-Baustoff zu 100 % genutzt. Nach der baustellennahen Zwischenlagerung wurde er in darauffolgenden Projektabschnitten für den Unterbau der neuen Landebahn verwendet. Kurze Lkw-Transportwege bei gleich-
Lenksystem für optimale Überlappungen
Das AutoTrac-System soll den radmobilen Recyclern von Wirtgen durch eine präzise, automatische Lenkung zu einer gesteigerten Prozesseffizienz und damit zu einer hohen Umweltverträglichkeit verhelfen. Es steuert die Maschine mit einer Genauigkeit im Zentimeterbereich anhand einer zuvor erstellten Referenzspur und einer definierten Überlappung der nebeneinander liegenden Spuren. So lässt sich immer die ideale Arbeitsbreite der Maschine nutzen. Zur exakten Standortbestimmung setzt AutoTrac u. a. auf verschiedene GNSS-Systeme. Die Bedienung erfolgt über ein weiteres Display, das zudem Informationen zur Position der Maschine und den gefahrenen Bahnen bereithält.
Einsparpotenziale ausschöpfen
Addiere man die im manuellen Betrieb oft großen, vermeidbaren Überlappungen der benachbarten Bahnen und damit die Verschwendung von Ressourcen, zeige sich laut Wirtgen schnell das Einsparpotenzial des Systems. Der Verbrauch von Bindemitteln, Betriebsmitteln und Kraftstoff lässt sich durch die Einhaltung der eingestellten Überlappung reduzieren, der Carbon Footprint wird verkleinert und die Bauzeit verkürzt. Als Ergebnis steigt die Effizienz des Prozesses und dadurch die Wirtschaftlichkeit sowie die Umweltverträglichkeit. Bei manueller Steuerung einer Maschine erfordert es stets viel Aufwand, um unbearbeitete Stellen im Boden zu vermeiden. Auch hier unterstützt und entlastet das automatische Lenksystem den Bediener. Bei Einhaltung der gewünschten Überlappung können Fehlstellen vermieden werden. t zeitig geringem Bedarf an Neumaterial dienten einer sehr guten CO₂-Bilanz.
Zudem bieten die WirtgenKaltfräsen selbst ein breites Spektrum umweltgerechter Maschinentechnologien. Verbrauchsoptimierte Drehzahlbereiche im Fräsbetrieb, gesteuert vom »Wirtgen Mill Assist«, und motortemperaturgeregelte Lüfterdrehzahlen beispielsweise schonen Umwelt und Ressourcen. Das automatische Zu- und Abschalten der Wassereinsprühanlage sowie die fräsleistungsabhängige Wasserdosierung reduzieren den spezifischen Wasserverbrauch laut Anbieter erheblich.

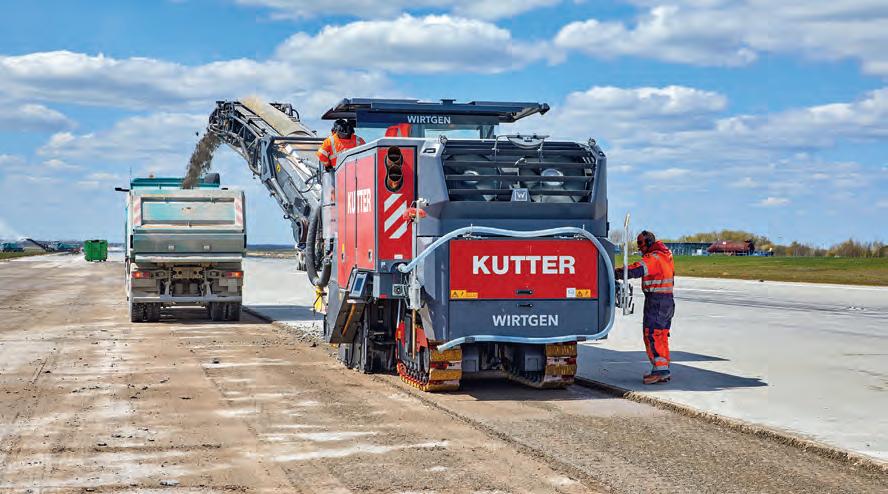
Vorausschauend geplant
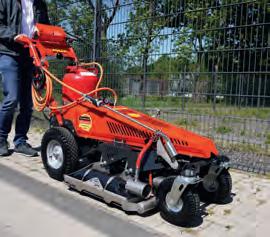
Um einen reibungslosen Ablauf sicherzustellen, wurden die Planungen frühzeitig aufgenommen. Bereits acht Monate vor Baustellenbeginn starteten praxisbezogene Einsatztests. So ließen sich auch präzise Verbrauchsprognosen für Meißel und weitere Verschleißteile erstellen, die vor Ort bevorratet wurden. Stillstandszeiten durch Meißelwechsel und Wartungen konnten so minimiert und die Produktivität maximiert werden.
Zufrieden mit dem Ergebnis
Am Ende konnte das Großprojekt um die Start-Landebahn auf dem Flughafen Leipzig/Halle innerhalb des vorgegebenen Zeitplans abgeschlossen werden. Den Grundstein hierfür legte die pünktliche Fertigstellung des Betonausbaus inklusive optimalem Fräsergebnis.
Bernhard Fischer, Projektleiter und Niederlassungsleiter vom bauausführenden Unternehmen Kutter, zeigte sich über die erfolgreiche Projektabwicklung zufrieden: »Die enorme Härte des Betons bringt, im Vergleich zum Fräsen von Asphalt, etwas niedrigere Fräsgeschwindigkeiten mit sich. Außerdem ist der Verschleiß an den Fräswerkzeugen deutlich höher. Die Mehrkosten durch den erhöhten Materialverschleiß werden durch den schnellen Baufortschritt und die
Präzision mehr als kompensiert. Der Ausbau mittels Kaltfräsen war die ideale Methode für dieses Projekt.«
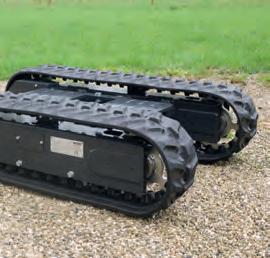
Komfortkabine für F-Serie
Abseits des erfolgreichen Einsatzes der Maschinen der Klasse W 250 Fi am Flughafen Leipzig/ Halle hat Wirtgen kürzlich verkündet, dass erstmalig Maschinen der Kompaktklasse mit einer Komfortkabine ausgestattet werden. Die Fahrerkabine für die Modelle W 100 Fi bis W 130 Fi will dem Fahrer einen komfortablen, körperschonenden und effektiv vor Geräuschemissionen schützenden Arbeitsplatz bieten. Zudem schützt die Kabine den Bediener vor der Witterung – ob Wind, Regen, Sonne oder Hitze.
Die Kabinenluft wird durch ein Filtersystem gereinigt und mittels automatischer Klimatisierung temperiert. Die Kabine ist außerdem als Überdrucksystem ausgelegt, wodurch das Eindringen von Schmutz, Staub und Gefahrstoffen in den Innenraum verhindert wird.
Den Geräuschpegel verringern
Auch bei der Kommunikation will die Komfortkabine für Kompaktfräsen ein Ausrufezeichen setzen. Der Geräuschpegel ist laut Wirtgen so niedrig, dass der Bediener bequem über eine Freisprecheinrichtung tele- fonieren kann. Für die Kommunikation auf der Baustelle kann er entweder auf Funkkopfhörer zurückgreifen oder er öffnet das Seitenfenster zur Kommunikation mit dem Bodenpersonal. Der Fahrerstand und alle Bedienelemente sind bei ver- schlossener Kabine vor Vandalismus geschützt. Das Abnehmen und Verstauen von Schutzabdeckungen sowie das Ausklappen versenkter BedienDisplays bei Arbeitsbeginn und die umgekehrten Vorgänge bei Arbeitsende entfallen. t