Unit EX1.6: Operations, Quality and Supply Chain Management
Unit code: T/507/8102 RQF level: 7
Qualifi Level 7 Diploma in Executive Management
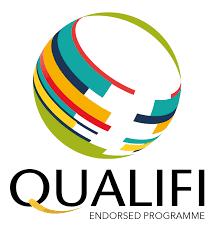
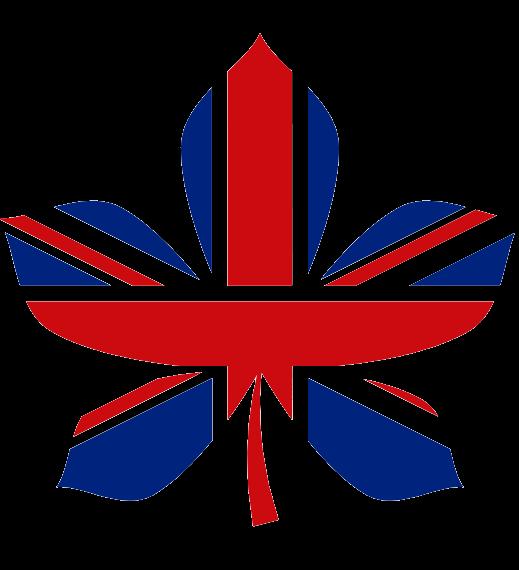
Unit EX1.6: Operations, Quality and Supply Chain Management
Unit code: T/507/8102 RQF level: 7
• Assess the contribution of operations management in organisations and how it supports business objectives.
• Evaluate the role and contribution of quality models, systems and standards to modern day business operations.
• Evaluate the contribution of suppliers and supply chains on effective operations .
• 1.1 Critically evaluate the business operations of a number of organisations in different industry sectors.
• 1.2 Critically analyse how process and lean techniques and methods can contribute to effective operations.
• 1.3 Explore the role of customer service in organisations and how this can impact operations
• 2.1 Critically evaluate a range of quality models, systems and standards.
• 2.2 Explore the use of quality models and systems in different companies across a range of industry sectors.
• 2.3 Identify the pros and cons, and the relevance of using quality models and systems in modern day business operations.
• 3.1 Critically evaluate supply chain theories and models and explore the use of supply chain management in different companies across a range of industry sectors.
• 3.2 Review how logistics impacts upon supply chain management.
• 3.3 Identify the main requirements of supplier contracts, the risks involved and mitigating strategies for organisations when securing effective contracts.
1.1 Critically evaluate the business operations of a number of organisations in different industry sectors.
• Commanding verb is critically evaluate which means As with evaluate, but considering the strengths and weaknesses, arguments for and against and/or similarities and differences.
• The writer should then judge the evidence from the different perspectives and make a valid conclusion or reasoned judgement.
• Apply current research or theories to support the evaluation when applicable.
• Critical evaluation not only considers the evidence above but also the strength of the evidence based on the validity of the method of evidence compilation.
• Conduct a comprehensive and thorough analysis of the business processes, strategies, and performance of several distinct organizations operating in diverse industry sectors.
• This evaluation should encompass a deep examination of their operational methods, competitive positioning, financial management, and overall effectiveness within their respective industries
analyse how process and lean techniques and methods can contribute to effective operations
• Commanding verb is Critically analyse which means -As with analyse, but questioning and testing the strength of a person and/or others’ analyses from different perspectives.
• Using the process of analysis to make an objective and reasoned argument. Criticality requires the consideration of the validity of sources used.
• Critical analysis not only considers the evidence above but also the strength of the evidence based on the validity of the method of evidence compilation.
• Please provide a critical analysis of how process improvement techniques such as Six Sigma and lean methods like Kanban can contribute to the overall effectiveness of business operations.
• Consider detailing specific examples of how these methodologies have been implemented and the resulting impact on operational efficiency, cost reduction, and quality improvement.
1.3 Explore the role of customer service in organisations and how this can impact operations
• Commanding verb is Explore which means - Go through the topic/issue thoroughly looking at all areas that affect the topic/issue.
• Customer service plays a crucial role within organizations as it directly impacts operational efficiency and customer satisfaction.
• Effective customer service can streamline operations, leading to improved efficiency and reduced costs.
• Additionally, providing excellent customer service can enhance customer satisfaction, leading to increased customer loyalty and positive word-of-mouth referrals.
• Commanding verb is critically evaluate which means As with evaluate, but considering the strengths and weaknesses, arguments for and against and/or similarities and differences.
• The writer should then judge the evidence from the different perspectives and make a valid conclusion or reasoned judgement.
• Apply current research or theories to support the evaluation when applicable.
• Critical evaluation not only considers the evidence above but also the strength of the evidence based on the validity of the method of evidence compilation.
• Please remember to thoroughly analyze and assess a variety of quality models, systems, and standards in order to gain a comprehensive understanding of their strengths and weaknesses.
• This evaluation should encompass a wide range of perspectives and criteria, such as effectiveness, efficiency, applicability, and relevance to the specific context.
2.2 Explore the use of quality models and systems in different companies across a range of industry sectors.
• Commanding verb is Explore which means - Go through the topic/issue thoroughly looking at all areas that affect the topic/issue.
• Examine how quality models and systems, such as Six Sigma, Total Quality Management, and ISO standards, are implemented and their impact on the operational efficiency, product quality, customer satisfaction, and overall performance of companies across diverse industry sectors such as manufacturing, healthcare, technology, and finance.
• Analyze the challenges and benefits associated with the adoption of these quality models and systems in different organizational contexts and explore best practices for successful implementation and sustained impact.
2.3 Identify the pros and cons, and the relevance of using quality models and systems in modern day business operations.
• Commanding verb is Identify which meansAscertain the origin, nature or definitive characteristics of something.
• In contemporary business operations, it's crucial to comprehensively understand the advantages, disadvantages, and significance of incorporating quality models and systems.
• Quality models and systems can bring about numerous benefits such as improved efficiency, higher customer satisfaction, and better decision-making processes.
• However, it's important to also be aware of the potential disadvantages, such as initial implementation costs and the need for continuous maintenance.
• Understanding the significance of these models and systems can provide valuable insights into how they can contribute to the overall success and sustainability of a business in today's competitive landscape..
3.1 Critically evaluate supply chain theories and models and explore the use of supply chain management in different companies across a range of industry sectors.
• Commanding verb is critically evaluate which means As with evaluate, but considering the strengths and weaknesses, arguments for and against and/or similarities and differences.
• The writer should then judge the evidence from the different perspectives and make a valid conclusion or reasoned judgement. Apply current research or theories to support the evaluation when applicable.
• Critical evaluation not only considers the evidence above but also the strength of the evidence based on the validity of the method of evidence compilation.
• The task involves conducting a thorough analysis of supply chain theories and models to evaluate their effectiveness and relevance.
• Additionally, it requires an in-depth exploration of the implementation and impact of supply chain management practices in diverse companies operating across various industry sectors.
• This comprehensive examination aims to uncover insights into how different organizations leverage supply chain strategies to optimize efficiency, reduce costs, and enhance overall operational performance.
• Commanding verb is review which means To examine, survey, reconsider a subject, theory or item
• Please review the ways in which logistics can affect various aspects of supply chain management, including transportation, inventory management, warehousing, and distribution.
3.3 Identify the main requirements of supplier contracts, the risks involved and mitigating strategies for organisations when securing effective contracts.
• Commanding verb is Identify which means-Ascertain the origin, nature or definitive characteristics of something.
• When securing effective contracts, organizations should carefully identify and outline the main requirements of supplier contracts, which may include specifics such as deliverables, payment terms, quality standards, and performance metrics.
• It's essential to understand the risks involved in supplier contracts, such as late deliveries, subpar quality, or breaches of contract.
• Mitigating strategies for these risks may involve thorough supplier vetting and due diligence, clear terms and conditions, performance incentives, and contingency plans to address potential disruptions.
• Operations management is the management of that part of an organization that is responsible for producing goods and/or services. There are examples of these goods and services all around you.
• Every book you read, every video you watch, every email you send, every telephone conversation you have, and every medical treatment you receive involves the operations function of one or more organizations. So does everything you wear, eat, travel in, sit on, and access the Internet with.
• However, in order to have a clear idea of Operations Management, one must have an idea of ‘Operating Systems’.
• An Operating System is defined as a configuration of resources combined for the provision of goods or services. Retail organizations, hospitals, bus and taxi services, tailors, hotels and dentists are all examples of operating systems.
• Any operating system converts inputs, using physical resources, to create outputs, the function of which is to satisfy customers wants.
• The creation of goods or services involves transforming or converting inputs into outputs. Various inputs such as capital, labour, and information are used to create goods or services using one or more transformation processes (e.g., storing, transporting, and cutting).
• To ensure that the desired output are obtained, an organization takes measurements at various points in the transformation process (feedback) and then compares with them with previously established standards to determine whether corrective action is needed (control). It is important to note that goods and services often occur jointly.
• For example, having the oil changed in your car is a service, but the oil that is delivered is a good. Similarly, house painting is a service, but the paint is a good.
• The goods-service combination is a continuum. It can range from primarily goods, with little service, to primarily service, with few goods.
• Because there are relatively few pure goods or pure services, companies usually sell product packages, which are a combination of goods and services.
• There are elements of both goods production and service delivery in these product packages. This makes managing operations more interesting, and also more challenging
• Objectives of operations management can be categorised into
• (i) Customer service and
• (ii) Resource utilisation.
• (i) Customer service
• The first objective is the customer service which means the service for the satisfaction of customer wants.
Customer service is therefore a key objective of operations management.
• The Operations Management must provide something to a specification which can satisfy the customer in terms of cost and timing.
• Thus, primary objective can be satisfied by providing the ‘right thing at the right price at the right time’.
• These three aspects of customer servicespecification, cost and timing - are described in a little more detail for the four functions in Table 1.
• They are the principal sources of customer satisfaction and must, therefore, be the principal dimension of the customer service objective for operation managers.
• Generally an organization will aim reliably and consistently to achieve certain standards, or levels, on these dimensions, and operations managers will be influential in attempting to achieve these standards.
• Hence, this objective will influence the operations manager’s decisions to achieve the required customer service
• Another major objective is to utilize resources for the satisfaction of customer wants effectively, i.e., customer service must be provided with the achievement of effective operations through efficient use of resources. Inefficient use of resources or inadequate customer service leads to commercial failure of an operating system.
• Operations management is concerned essentially with the utilization of resources, i.e., obtaining maximum effect from resources or minimizing their loss, under utilization or waste.
• The extent of the utilization of the resources’ potential might be expressed in terms of the proportion of available time used or occupied, space utilization, levels of activity, etc. Each measure indicates the extent to which the potential or capacity of such resources is utilized.
• This is referred as the objective of resource utilization. Operations management is also concerned with the achievement of both satisfactory customer service and resource utilization.
• An improvement in one will often give rise to deterioration in the other. Often both cannot be maximized, and hence a satisfactory performance must be achieved on both objectives.
• All the activities of operations management must be tackled with these two objectives in mind, and many of the problems will be faced by operations managers because of this conflict. Hence, operations managers must attempt to balance these basic objectives.
Below Table 2 summarizes the twin objectives of operations management. The type of balance established both between and within these basic objectives will be influenced by market considerations, competitions, the strengths and weaknesses of the organization, etc. Hence, the operations managers should make a contribution .
• Operations Management concerns with the conversion of inputs into outputs, using physical resources, so as to provide the desired utilities to the customer while meeting the other organizational objectives of effectiveness, efficiency and adoptability.
• It distinguishes itself from other functions such as personnel, marketing, finance, etc. by its primary concern for ‘conversion by using physical resources’..
• Following are the activities, which are listed under Production and Operations Management functions:
1. Location of facilities.
2. Plant layouts and Material Handling.
3. Product Design.
4. Process Design.
5. Production Planning and Control.
6. Quality Control.
7. Materials Management.
8. Maintenance Management
• There are two points of distinction between production management and operations management.
• First, the term production management is more used for a system where tangible goods are produced. Whereas, operations management is more frequently used where various inputs are transformed into intangible services.
• Viewed from this perspective, operations management will cover such service organisations as banks, airlines, utilities, pollution control agencies, super bazaars, educational institutions, libraries, consultancy firms and police departments, in addition, of course, to manufacturing enterprises.
• The second distinction relates to the evolution of the subject. Operations management is the term that is used nowadays. Production management precedes operations management in the historical growth of the subject.
• The production management of today presents certain characteristics which make it look totally different from what it was during the past. Specifically, today’s production system is characterised by at least four features.
• 1. Manufacturing as Competitive Advantage In the past production was considered to be like any other function in the organisation.
• When demand was high and production capacities were inadequate, the concern was to somehow muster all inputs and use them to produce goods which would be grabbed by market. But today’s scenario is contrasting.
• Plants have excess capacities, competition is mounting and firms look and gain competitive advantage to survive and succeed.
• Interestingly, production system offers vast scope to gain competitive edge and firms intend to exploit the potential.
• Total Quality Management (TQM), Time-Based Competition, Business Process Re-engineering (BPRE), Just-in-Time (JIT), Focused Factory, Flexible Manufacturing Systems (FMS), Computer Integrated Manufacturing (CIM), and The Virtual Corporation are but only some techniques which the companies are employing to gain competitive advantage.
• 2. Services Orientation As was stated earlier, service sector is gaining greater relevance these days. The production system, therefore, needs to be organised keeping in mind the peculiar requirements of the service component.
• The entire manufacturing needs to be geared to serve
• (i) intangible and perishable nature of the services,
• (ii) constant interaction with clients or customers,
• (iii) small volumes of production to serve local markets, and
• (iv) need to locate facilities to serve local markets. There is increased presence of professionals on the production, instead of technicians and engineers.
• 3. Disappearance of Smokestacks Protective labour legislation, environmental movement and gradual emergence of knowledge based organisations have brought total transformation in the production system.
• Today’s factories are aesthetically designed and built, environment friendly - in fact, they are homes away from homes.
• Going to factory everyday is no more excruciating experience, it is like holidaying at a scenic spot.
• A visit to ABB, L & T or Smith Kline and Beecham should convince the reader about the transformation that has taken place in the wealth creation system.
• 4. Small has Become Beautiful It was E.F. Schumacher who, in his famous book Small is Beautiful, opposed giant organisations and increased specialisation.
• He advocated, instead, intermediate technology based on smaller working units, community ownership, and regional workplaces utilising local labour and resources.
• For him, small was beautiful. Businessmen, all over the world, did not believe in Schumacher’s philosophy. Inspired by economies of scale, industrialists went In for huge organisations and mass production systems.
• Recent trends in production/operations management relate to global competition and the impact it has on manufacturing firms. Some of the recent trends are :
• 01. Global Market Place : Globalisation of business has compelled many manufacturing firms to have operations in many countries where they have certain economic advantage.
• This has resulted in a steep increase in the level of competition among manufacturing firms throughout the world.
• 2. Production/Operations Strategy: More and more firms are recognising the importance of production/ operations strategy for the overall success of their business and the necessity for relating it to their overall business strategy.
• 3. Total Quality Management (TQM) : TQM approach has been adopted by many firms to achieve customer satisfaction by a never-ending quest for improving the quality of goods and services.
• Flexibility : The ability to adapt quickly to changes in volume of demand, in the product mix demanded, and in product design or in delivery schedules, has become a major competitive strategy and a competitive advantage to the firms. This is sometimes called as agile manufacturing.
• 5. Time Reduction : Reduction of manufacturing cycle time and speed to market for a new product provide competitive edge to a firm over other firms.
• When companies can provide products at the same price and quality, quicker delivery (short lead times) provide one firm competitive edge over the other.
• 6. Technology : Advances in technology have led to a vast array of new products, new processes and new materials and components.
• Automation, computerisation, information and communication technologies have revolutionised the way companies operate.
• Technological changes in products and processes can have great impact on competitiveness and quality, if the advanced technology is carefully integrated into the existing system.
• 7. Worker Involvement : The recent trend is to assign responsibility for decision making and problem solving to the lower levels in the organisation. This is known as employee involvement and empowerment. Examples of worker involvement are quality circles and use of work teams or quality improvement teams.
• 8. Re-engineering : This involves drastic measures or break-through improvements to improve the performance of a firm. It involves the concept of cleanslate approach or starting from scratch in redesigning the business processes.
• 9. Environmental Issues : Today’s production managers are concerned more and more with pollution control and waste disposal which are key issues in protection of environment and social responsibility. There is increasing emphasis on reducing waste, recycling waste, using less-toxic chemicals and using biodegradable materials for packaging.
• 10. Corporate Downsizing (or Right Sizing) : Downsizing or right sizing has been forced on firms to shed their obesity. This has become necessary due to competition, lowering productivity, need for improved profit and for higher dividend payment to shareholders.
• 11. Supply-Chain Management: Management of supply-chain, from suppliers to final customers reduces the cost of transportation, warehousing and distribution throughout the supply chain.
• 12. Lean Production: Production systems have become lean production systems which use minimal amounts of resources to produce a high volume of high quality goods with some variety. These systems use flexible manufacturing systems and multi-skilled workforce to have advantages of both mass production and job production (or craft production).
• Production or operations strategy is directly influenced by product design for the following reasons:
• (i) As products are designed, all the detailed characteristics of each product are established.
• (ii) Each product characteristic directly affects how the product can be made or produced (i.e., process technology and process design) and
• (iii) How the product is made determines the design of the production system (production design) which is the heart of production and operations strategy.
• Further, product design directly affects product quality, production costs and customer satisfaction. Hence, the design of product is crucial to success in today’s global competition.
• A good product design can improve the marketability of a product by making it easier to operate or use, upgrading its quality, improving its appearance, and/or reducing manufacturing costs.
• A distinctive design may be the only feature that significantly differentiates a product.
• An excellent design includes usability, aesthetics, reliability, functionality, innovation and appropriateness.
• An excellent design provides competitive advantage to the manufacturer, by ensuring appropriate quality, reasonable cost and the expected product features. Firms of tomorrow will definitely compete not on price and quality, but on product design.
• What Does Product Design Do? The activities and responsibilities of product design include the following:
• (i) Translating customer needs and wants into product and service requirements (marketing).
• (ii) Refining existing products (marketing).
• (iii) Developing new products (marketing, product design and production).
• (iv) Formulating quality goals (quality assurance, production).
• (v) Formulating cost targets (accounting).
• (vi) Constructing and testing prototype (marketing, production).
• Products, like men, are mortal. They flourish for a time, then decline and die. The life cycle of a product has many points of similarity with the human life cycle.
• A product is born, grows lustily, attains a dynamic maturity, then enters its declining years.
• Like a human being a product that has not built up its potential during its formative years is likely to be relatively unsuccessful on its maturity. But, there are critical differences between the product and the human life cycle.
• For instance, every person has an average life expectancy. But the life expected of a product varies widely. The concept of product failure is applicable both to new products and the existing ones.
• There may, however, be varying periods of life spans for each product: some failing immediately, other living for a longer period.
• The product, thus, has “life cycles” just as human beings have. From its birth, a product passes through various stages, until it is finally abandoned, i. e.. discontinued from the market. These stages taken together are referred, to as “the product life cycle”.
• This life cycle of the product comprises of four stages: Introduction, Growth, Maturity and Decline. It should be noted that it is purely a theoretical concept.
• This may graphically be represented as shown Fig. in below: The introduction stage is preceded by ‘production planning and development’. This period requires greater investment. This investment should be gradually recouped as the sales pick up.
• After testing, a product enters the introduction stage and the product will then become available in the national market. Sales would begin gradually as potential buyers come to know about the product through advertising and other seIIing techniques.
• But the profits will be low as part of the investment is to be recouped besides heavy expenditure on selling. In the growth stage, both sales and profits will begin to increase. It is here that similar other new products begin to appear in the market as substitutes and offer competition.
The management, therefore, should try to change its approach by changing its strategy from “buy my product” to “try my product”.
At the end of this stage, the distribution arrangement is likely to get completed and the prices, if necessary, are reduced a little. The third stage is the maturity stage.
• During this stage the manufacturers introduce new models or adopt methods such as trading-in, etc., to promote the sale of their brands with a view to retaining their position in the market.
• The number of buyers will continue to grow, but more slowly. In economic terms this is the stage where supply exceeds demand. Some of the promotional efforts may lengthen the span of this stage but they will not offer a permanent solution.
• At the final stage of decline, profit margins touch a low level, competition becomes severe and customers start using newer and better products. It is here that the story of a product ends-a natrural but hard end.
• The above discussion concentrates only on the life cycle of a product, beginning with its introduction into the market (i.e., post-marketing).
• But a series of processes are to be undertaken by the management prior to the introduction of a product.
• The diagram given above is presented in an enlarged form to incorporate the pre introduction (or pre-marketing) stages also.
• Product Iife cycle concept may be used as a managerial tool. Marketing strategies must change as the product goes through the life cycle.
• If managers understand the cycle concept they are in a better position to forecast the future sales activities and plan marketing strategies. The following points, however, may be kept in mind in using this concept.
• Productivity implies development of an attitude of mind and a constant urge to find better, cheaper, quicker, easier and safe ways of doing a job, which could be either manufacturing an article or providing a service.
• Since the beginning of the industrial era, the manufacturers or producers have been facing the problem of how to use the available resources and factors of production to the best of their ability and capacity so as to get the maximum output with the minimum cost of production.
• Industrial revolution, social, technological and scientific developments, changes in economic systems are the various efforts made in this direction and the process of development and changes is still on.
• New and new machines, methods and technology are being invented and used in the industrial field to minimise the wastage of men, materials and machines. It is all to increase the productivity.
• Productivity is the quality or state of being productive. It is some relationship of outputs to inputs. It is a concept that guides the management of a production system, and measures its success. It is the quality that indicates how well labour, capital, materials and energy are utilised.
• Productivity improvement is sought everywhere because it supports a higher standard of living, helps control inflation, and contributes towards a stronger national economy.
• Productivity is an indicator reflecting the changes in the performance of the enterprise and having some sort of inputoutput comparisons relating to various activities of an organisation.
• It also facilitates the management to control and plan the future operations of the enterprise.
• Productivity is the talk of the day and it is generally regarded as efficiency in industrial production to be measured by some relationship between outputs and inputs.
• The increase in productivity is looked upon as the key to prosperity at all levels. In its modern sense, it refers to the relationship between the result and the means employed or to be more specific between the product and the factors used for obtaining it.
• It is the quantitative relationship between what we produce and the resources which we use to obtain it. It can also be termed as the ratio of what is produced to what is required to produce it. The higher is the ratio, the greater is the productivity.
• Thus, it seeks to measure the economic soundness of the use of the means. It means productivity can be considered higher if the same amount of production is obtained with lesser means or it will be lower if the same quantity of production is obtained with larger quantity of means. It is higher when there is maximum production with the least expense of resources.
• A productivity index is a device of expressing the ratio between outputs and the inputs of the resources numerically. These indices are prepared by comparing the volume of output of goods with the labour employed on that job or the profits of the firm with the capital employed. If the comparison shows an upward trend in indices, it is a sign of improved or better productivity and vice-versa.
• The importance of the concept of productivity can be viewed from the following points:
• 1. To beat the competition: It is an age of cutthroat competition. There may be other commodities which can serve as the substitutes of the terms ‘product’ and can attract the consumers’ purchasing power. The firm whose productivity is higher can only beat the competition and can exist in the market for long.
• 2. Guide to Management: The productivity indices are very useful for the management and can be used for different purposes. These indices can serve as a valuable guide to the management for improving the performance of its enterprise..
The productivity measures can be used for the following purposes:
• (a) Strategic: With the help of productivity indices, the efficiency of different firms can be measured, analysed and compared. The necessary steps can be taken to improve the productiveness of the firm taking in view the productiveness of the other competitive firms.
• (b) Tactical: Different units or the sectors of the firm can also be compared as regards to their productivity and the productivity of the less productive units or sectors can be improved.
• (c) Planning: A firm uses different inputs in producing the goods. A comparison of relative benefits accruing from the use of different inputs can be had and the most beneficial input can be used in production. It helps the management to plan for the future.
• (d) Administration: Productivity indices indicate the progress of the firm over a period of years. The productivity of different inputs, including labour, can be measured individually.
• The individual productivity indices help the management in bargaining with the labour leaders, trade unions and the Government in case of labour disputes regarding welfare activities. Thus administration can be improved with the help of productivity indices
• An Indicator of Progress: In economically backward countries, productivity movement is basic aspect of progress.
• It implies the development of an attitude of mind and a constant urge to better, cheaper, quicker and safer ways of doing a job which could be either manufacturing a product or providing a service.
• In an urge to improve the productivity, new inventions take place. Thus productivity is an aspect of basic progress.
• 4. Maximum utilisation of Scarce Resources: In order to provide the articles or commodities to the consumers at the lowest possible cost, the productivity urges to utilise the available resources to the maximum possible extent to provide full satisfaction of customers.
• The productivity processes and techniques are designed to facilitate more efficient work involving less fatigue to workers by improvements in the layout of the plant and work, better working environment and simplification of works.
• 5. Key to National Prosperity: The productivity, in fact, has become the synonymous to progress. Higher productivity is an index of more production with the same inputs at lower cost. It enables industry to offer goods to the general public at cheaper rates and results in expansion of markets. The working conditions and wages of workers will improve and industrialists too will get larger profits. Thus higher productivity is the key to national prosperity.
The secrets of Japan and Western countries’ prosperity lie in increased productivity.
• 6. Prosperity to Labour:
The higher productivity is a boon to labour also. It brings improved working conditions, better wages and salaries to workers, better labour welfare activities to labourers. Thus their standard of living is improved.
• 7. Other Uses:
• (i) Higher productivity increases the profits and reserve funds of the industry that can be used for expansion and modernisation.
• (ii) It increases the goodwill of the firm due to cheaper goods to the public, well-off staff and more profits and better financial position.
• A philosophy that involves everyone in an organisation in a continual effort to improve quality and achieve customer satisfaction.
• 1. Top management commitment and support.
• 2. Focus on both internal and external customers.
• 3. Employee involvement and empowerment.
• 4. Continuous improvement (KAIZEN)
• 5. Partnership with suppliers
• 6. Establishing performance measures for processes.
• 1. Customer satisfaction
• 2. Leadership
• 3. Quality policy
• 4. Organisation structure
• 5. Employee involvement
• 6. Quality costs
• 7. Supplier selection and development
• 8. Recognition and reward.
• 1. Strive for quality in all things (Total Quality)
• 2. The customer is the creation of quality
• 3. Improve the process or systems by which products are produced
• 4. Quality improvement is continuous, never ending activity (continuous improvementKaizen)
• 5. Worker involvement is essential
• 6. Ground decisions and actions on knowledge
• 7. Encourage team work and cooperation.
1. An integrated organisational infrastructure
2. A set of management practices
3. A wide variety of tools and techniques.
TQM is Japanese approach to quality. The term TQM refers to a quest-for quality in an organization. TQM is a process that underlines three philosophies.
One is never-ending push to improve, which is referred to as continuous improvement; the second is the involvement of every employee in the organization and the third is the goal for customer satisfaction, which means meeting or exceeding customer expectations.
It often focuses on benchmarking world-class standards, product and service design and purchasing
• In addition, TQM involves a number of other elements such as:
➢ Team approach,
➢ Employee empowerment
➢ Decisions based on facts rather than opinions,
➢ Knowledge of quality tools [flow charts, check sheets, histograms, pareto analysis, scatter diagrams etc.]
➢ Quality at the source and
➢ Inclusion of suppliers as a part of quality improvement programme.
• TQM is a process of continuous improvement at every level of the organization-the centre of the entire process is customer satisfaction.
• TQM implies that the organization is doing everything it can to achieve quality at all stages of the process, from customer demands, to product design, to engineering.
Quality Certification Many international businesses recognize the importance of quality certification. The EU, in 1987, established ISO [International Organisation for Standardisation] 9000 certification.
Two of the most well known of these are ISO 9000 and ISO 14,000.
ISO 9000 pertains to quality management. It concerns what an organization does to ensure that its products or services are suitable to customers expectations. ISO 14,000 concerns minimization of harmful effects to the environment caused by its operations.
• Both ISO 9000 and ISO 14000 are related to an organization processes rather than its products and services and they stress continual improvement. ISO 9000 is composed of the national standard bodies of 91 countries.
• About 90 countries have adopted ISO 9000 as national standards. This certification is intended to promote the idea of quality at every level in the organisation. ISO certification is an elaborate and expensive process.
• Any firm seeking this certification needs to document how its workers perform every function that affects quality and install mechanisms to ensure that, they follow on expected lines.
• ISO 9000 certification entails a complex analysis of management systems and procedures. Rather than judging the quality of a particular product, ISO 9000 evaluates the management of the entire manufacturing process, from purchasing, to design, to training.
A firm that seeks this certification must fill out a report and then be certified by a team of independent auditors.
With certification comes registration in an ISO directory, that firms seeking suppliers can refer to, for a list of certified companies. They are generally given preference over unregistered companies.
There are essentially five standards associated with the ISO 9000 series. The series, if we place them on a continuum, would range from design and development through procurement, production, installation and servicing. Whereas, ISO 9004 only establishes guidelines for operation, ISO 9001, 9002 and 9003 are well-defined standards.
• 9001 Model for Quality Assurance in Design, Production, Installation and Servicing. (To be used when conformance to specified requirements is to be assured by the supplier during several stages that may include design/ development, production, installation and servicing).
• 9002 Model for Quality Assurance in Production and Installation.
• (To be used when conformance to specified requirements is to be assured by the supplier during production and installation).
• 9003 Model for Quality Assurance in Final Inspection Test.
• (To be used when conformance to specified requirements is to be assured by the supplier solely at final inspection and test).
• Guidelines for Use 9000 Quality Management and Quality Assurance Standards - Guidelines for Selection and Use.
9004 Quality Management and Quality System Elements - Guidelines
• ISO certification is a must for doing business with any member of the EU.
• In addition to the benefits of accessing the EU, ISO 9000 certification and registration is particularly helpful for companies that do not currently have a quality management system, as it provides guidelines for establishing the system and making it effective.
The latest version of ISO 9000 forms the basis of eight quality management principles.
• 1. A system approach to management
• 2. Continual improvement
• 3. Factual approach to decision making
• 4. Mutually beneficial supplier relationships
• 5. Customer focus
• 6. Leadership
• 7. People involvement
• 8. Process approach.
• ISO standards are reviewed every five years and revised if needed. This helps ensure they remain useful tools for market place.
• The challenges faced by business and organisations today are very different from few decades ago and ISO 9001 has been updated to take this new environment into account.
• The last version was ISO 9001:2008 and has been replaced by further updated version ISO 9001:2015 on and from September 2018.
• The Magic Supply Chain and the Best Operations Manager Santa Claus is one of the best supply chain (SC) and opera-tions managers in the world. He achieves incredible perfor-mance: he always delivers the right products, at the right place and at the right time.
• And this is despite highly uncertain de-mand and a very complex SC with more than two billion cus-tomers. His strategy and organization is customer-centred and strives to provide maximal children satisfaction.
•
• The organization of the operations and supply chain management is structured as follows. The customer department is responsible for pro-cessing all the letters from children from all over the world.
• This demand data is then given to the supply department. The supply department is responsible for buying the desired items from suppliers worldwide.
• The core of the supply de-partment is the global purchasing team which is responsible for coordinating all the global purchasing activities.
• Since many of the children’s wishes are countryspecific, the regional purchasing departments (socalled lead buyers) are distributed worldwide and build optimal SC design.
• In some cases, the desired items are so specific that no supplier can be found.
• For such cases, Santa Claus has established some production facilities and located them globally to minimize total transportation costs and to ensure ontime delivery of all the gifts for Christmas
The customer department regularly analyses children's' wishes. It was noticed that there are lots of items which are asked for each year.
In order to reduce purchasing fixed costs and use scale effects, Santa Claus organized a network of warehouses worldwide.
Standard items are purchased in large batches and stored. If the actual demand in the current year is lower than forecasted demand, this is not a problem – these items can be used again in the following year.
Since there are millions of different items in each warehouse, Santa Claus created optimal layouts and pick-up processes in order to find the necessary items quickly and efficiently.
• The SC and operations planning happens as follows. In January, Santa Claus and the customer department start to analyse the previous year’s demand.
• During the first six months of the year, they create a projection of future demand. The basis for such a forecast is statistical analysis of the past and identification of future trends (e.g., new books, films, toys, etc.).
• After that, the supply department replen-ishes the items and distributes them to different warehouses. The production department schedules the manufacturing processes.
• From October, the first letters from children start to arrive. The busy period begins. From October to December, Santa Claus needs lots of assistants and enlarges the workforce.
The operations and supply chain execution is now responsible for bringing all the desired items to children.
It comprises many activities: transportation, purchasing and manufacturing. Children are waiting impatiently to start the incoming goods inspection.
No wrong pick-ups and bundles are admissible and no shortage is al-lowed. More and more, children’s wishes are not about items but rather about some events which they want to happen (e.g., holidays, etc.).
• Service operations are also in the competence of Santa Claus. In addition, Santa Claus has established the most sustainable SC in the world based on transportation by sledges.
• Some-times, the letters with very unusual wishes come in the very last moment but Santa Claus’s SC is prepared for the unpredictable .
• Planning, implementing, and controlling the effective flow of goods, services, and related information from the point of origin to the point of consumption in order to satisfy customer needs is the definition of logistics.
• It entails the coordination of all tasks involved in moving goods from one location to another. This covers delivery, storage, inventory control, packaging, and other associated tasks.
• Logistics is concerned with the financial and practical aspects of moving goods from one location to another.
• The definition of supply chain management (SCM) is the integration of activities across various organizations to maximize the flow ofgoods, data, and services from suppliers to clients.
• It entails overseeing the entire supply chain, starting with raw materials and ending with finished goods. S
• CM encompasses tasks like ordering supplies, scheduling production, keeping track of inventory, managing distribution channels, and more.
• It also entails managing interactions with customers and suppliers to guarantee that products are delivered on schedule and within budget.
• The primary distinction between supply chain management and logistics is that supply chain management focuses on managing relationships with suppliers and customers in order to optimize the flow of materials and services while logistics focuses on the actual physical movement of goods from one location to another.
• While SCM is concerned with managing relationships with suppliers and customers to guarantee that goods are delivered on time and at the appropriate cost, logistics is focused on the actual transportation of goods.
• Additionally, SCM concentrates on customer satisfaction while logistics concentrates on cost reduction.
• While SCM includes tasks like procurement, production planning, inventory management, transportation, warehousing, distribution, customer service, etc.,
• logistics also involves tasks like inventory management, packaging, warehousing, and transportation.
• While SCM is concerned with managing relationships with suppliers and customers in order to optimize the flow of materials and services, logistics is concerned with the actual movement of goods from one location to another.
• For businesses to guarantee that their goods and services are delivered to customers on time and efficiently, logistics and supply chain strategies are crucial.
• The flow of goods and services from the point of origin to the point of consumption can be optimized using a variety of logistics and supply chain strategies.
• The various types of logistics and supply chain strategies, their benefits and drawbacks, and how they can be implemented in an organization will all be covered in this subsection.
• Push and pull strategies are the two primary categories of logistics and supply chain strategies.
• Pull strategies entail customers pulling products from the supplier, whereas push strategies involve pushing products out to customers.
• Pull strategies are typically used when there is a low demand for a good or service, whereas push strategies are typically used when there is.
• Push strategies entail anticipating consumer demand and producing or stocking products in response.
• In markets where there is a high demand for a good or service, like electronics or fashion, this kind of strategy is frequently employed.
• The benefit of using this kind of strategy is that it enables companies to foresee customer needs and make sure they have enough inventory on hand to satisfy customer demand.
• The drawback is that it might result in overstocking, which would raise inventory costs.
• Pull strategies involve only manufacturing or keeping products on hand when there is a genuine demand from customers.
• In markets where there is little demand for a good or service, like those for pharmaceuticals or medical supplies, this kind of strategy is frequently employed.
• This kind of strategy has the benefit of assisting businesses in lowering inventory costs by only manufacturing or stocking products when there is a genuine demand for them from customers.
• The drawback is that if the supplier does not have enough inventory on hand to meet customer demand, it may cause delays in processing customer orders.
• Instead of anticipating customer demand and producing or stocking products accordingly, just-intime (JIT) strategies produce or stock products only when they are required. In markets where there is little demand for a good or service, like those for pharmaceuticals or medical supplies, this kind of strategy is frequently employed.
• This kind of strategy has the benefit of assisting businesses in lowering inventory costs by only producing or stocking goods as needed.
• The drawback is that if the supplier does not have enough inventory on hand to meet customer demand, it may cause delays in processing customer orders
• Vendor managed inventory (VMI) strategies entail having suppliers control the stock levels of the goods that belong to their clients.
• In markets where there is a high demand for a good or service, like electronics or fashion, this kind of strategy is frequently employed. This kind of strategy has the benefit of enabling suppliers to more accurately predict customer needs and guarantee that they have enough inventory on hand to meet customer demand.
• The drawback is that it might result in overstocking, which would raise inventory costs.
• Cross-docking strategies involve moving items from one truck to another without storing them in between shipments.
• In markets where there is a high demand for a good or service, like electronics or fashion, this kind of strategy is frequently employed.
• By removing the need for storage space in between shipments, this kind of strategy has the advantage of assisting businesses in lowering the cost of their inventory.
• The drawback is that if the supplier does not have enough inventory on hand to meet customer demand, it may cause delays in processing customer orders.
• In third-party logistics (3PL) strategies, third-party providers are used to handle logistics tasks like warehousing, shipping, and order fulfillment. In markets where there is a high demand for a good or service, like electronics or fashion, this kind of strategy is frequently employed.
• This kind of strategy has the benefit of letting businesses concentrate on their core competencies while outsourcing noncore activities to third-party service providers who are experts in those areas.
• The drawback is that because third-party providers charge fees, it might result in higher costs.
• The flow of goods and services from the point of origin to the point of consumption can be optimized by businesses using a variety oflogistics and supply chain strategies.
• Before implementing any logistics and supply chain strategies, businesses should carefully consider which type best meets their needs. Each type has its own benefits and drawbacks.
• By lowering the cost of transportation and warehousing, logistics and supply chain management can be used to enhance business operations.
• Businesses can lower their costs by reducing the number of unneeded steps in their supply chain by optimizing the flow of materials from suppliers to customers.
• Additionally, by ensuring that orders are delivered on time and within budget, businesses can use logistics and SCM to enhance customer service.
• Businesses can enhance their inventory management by combining SCM and logistics to make sure they always have enough inventory without overstocking or understocking.
• This can ensure that customers receive their orders quickly while also assisting businesses in lowering their inventory management costs.
• Although they are closely related and frequently used interchangeably, supply chain management and logistics have different purposes.
• While supply chain management (SCM) focuses on managing relationships with suppliers and customers to optimize the flow of materials and services, logistics focuses on the actual movement of goods from one location to another.
• By lowering the costs of transportation and warehousing as well as by ensuring that orders are delivered on time and at the right price, both logistics and SCM can be used to enhance business operations.
• For any business to succeed, logistics and supply chain management are two concepts that are closely related.
• Planning, organizing, and controlling the flow of goods and services from the point of origin to the point of consumption is the process of logistics.
• The goal of supply chain management is to coordinate activities between various organizations so that products and services are delivered on time and efficiently.
• Both supply chain management and logistics involve a variety of elements that need to be managed for success.
• The various elements of logistics and supply chain management, such as inventory management, transportation, warehousing, customer service, and information technology, will be covered in this section.
• Management Logistics and supply chain management both depend on effective inventory management. From the point of origin to the point of consumption, the flow of goods must be managed.
• This entails keeping track of inventory levels, placing orders for additional stock Logistics and Supply Chain Management: Fundamentals and Strategies as needed, and guaranteeing that there is always enough stock on hand.
• In addition to managing inventory levels to satisfy customer needs, inventory management also entails forecasting demand for goods and services.
• Another crucial element of logistics and supply chain management is transportation. It entails efficiently and affordably transporting goods from one place to another.
• Choosing the most effective mode of transportation—such as an air, rail, truck, or ship—as well as the most economical route and guaranteeing that goods arrive at their destination on time are all included in this.
• Managing freight costs, including those for fuel, insurance, and other related expenses, is another aspect of transportation.
• Supply chain management and logistics both heavily rely on warehousing. It entails keeping items safe and secure until they are required.
• This involves choosing an appropriate warehouse location, controlling inventory levels, making sure that goods are stored securely, and allowing access to them when needed.
• In addition to managing inventory levels to satisfy customer needs, warehousing also involves making sure that goods are shipped promptly.
• Customer Service Customer service plays a key role in supply chain management and logistics. It entails timely delivery of order-related information to customers as well as prompt responses to their queries.
• Customer service also includes promptly and effectively resolving customer complaints. Giving customers accurate information about goods and services, as well as helping them return or exchange items, are additional components of customer service.
• Logistics and supply chain management both depend on information technology. It entails managing the flow of goods from the point of origin to the point of consumption through the use of technology.
• This includes using software to manage orders, track shipments, track inventory levels, and give customers up-to-the-minute updates on their orders.
• Additionally, processes like order processing, invoicing, payment processing, and customer service can all be automated using information technology. The success of logistics and supply chain management depends on the management of a number of different components.
• These elements include customer service, information technology, transportation, and warehousing. To guarantee that goods are delivered in a timely and economical manner, each component is crucial.
• Businesses can make sure that their supply chain and logistics operations run smoothly by comprehending these components and managing them successfully.
• Any business needs logistics and supply chain management to function. They are in charge of ensuring that products are transported effectively from the point of production to the point of consumption.
• Numerous tasks are involved in logistics and supply chain management, such as inventory control, shipping are housing, and customer support.
• The advantages of logistics and supply chain management, such as cost savings, enhanced customer service, and increased effectiveness, will be covered in this subsection.
• Cost savings are one of the main advantages of logistics and supply chain management. Businesses can lower their costs for inventory management, transportation, warehousing, and customer service by optimizing the flow of goods and services.
• For instance, by utilizing just-in-time inventory systems that enable them to order only what they require at the precise moment they require it, businesses can lower their inventory costs.
• Additionally, by utilizing effective routing strategies that reduce the distance that goods and services must travel, businesses can lower their transportation costs.
• Using automated systems that enable them to store goods in a more effective way allows businesses to lower their warehousing costs. Improved
• Enhanced customer service is a further advantage of logistics and supply chain management. Businesses can guarantee that customers receive their orders on time and in good condition by optimizing the flow of goods and services.
• CRM (customer relationship management) systems can also be used by businesses to keep track of customer orders and deliver individualized customer service.
• This enables companies to strengthen their bonds with clients and boost client loyalty. Increased Efficiency Finally, supply chain management and logistics can help businesses become more productive.
• Businesses can cut waste and increase overall efficiency by optimizing the flow of goods and services.
• Businesses can also automate some processes to increase their efficiency by using cutting-edge technologies like artificial intelligence (AI) and machine learning (ML).
• This enables companies to provide their customers with high-quality goods and services while saving time and money.
• Any business needs logistics and supply chain management to function. To make sure that goods and services are delivered to customers on time and efficiently, they entail the coordination of resources, materials, and services. However, controlling supply chains and logistics can be a difficult task.
• Various logistical and supply chain management challenges, such as cost control, customer satisfaction, inventory management, and sustainability, will be covered in this section.
• Controlling costs is one of the biggest challenges in logistics and supply chain management. Transportation, warehousing, inventory management, customer service, and other activities are all part of logistics and supply chain management. Resources are needed for each of these tasks, and they can add up quickly.
• Companies need to figure out how to cut expenses without sacrificing service quality. This can be accomplished by streamlining routes, negotiating lower prices with suppliers, and automating procedures using technology.
• Customer Service Providing top-notch customer service is a challenge that logistics and supply chain management must overcome.
• Customers anticipate receiving their orders promptly and undamaged. To meet customer expectations, businesses must make sure that their supply chain and logistics operations are effective enough.
• This includes putting in place an efficient tracking system that makes it simple for customers to follow their orders. Having a trustworthy network of suppliers who can deliver high-quality goods on schedule is also necessary.
• Another difficulty in logistics and supply chain management is inventory control. Businesses need to make sure they have enough inventory on hand to satisfy customer demand without going Logistics and Supply Chain Management: Fundamentals and Strategies overstock or out of stock.
• In order to make sure that the appropriate amount of inventory is available at the appropriate time, careful planning and forecasting are needed.
• Businesses also need a reliable system for monitoring inventory levels so they can modify orders as necessary.
• Sustainability In logistics and supply chain management, sustainability is becoming more and more crucial.
• Businesses need to figure out how to have a smaller negative impact on the environment without sacrificing service standards.
• This entails lowering emissions from transportation, utilizing renewable energy sources, and putting waste management techniques into practice.
• In order to maintain their competitive edge in the market, businesses must also ensure that their suppliers adopt sustainable practices.
• Various tasks that are involved in logistics and supply chain management call for careful planning and coordination.
• Businesses need to figure out how to keep costs under control while still offering customers high-quality services.
• Additionally, they must make sure that their inventory levels are effectively managed and that sustainable business practices are being used.
• Companies can make sure that their supply chain and logistics processes are effective and economical by addressing these issues.
• A supply chain (SC) is a network of organizations and processes wherein a number of various enterprises (suppliers, manufacturers, distributors and retailers) collaborate (cooperate and coordinate) along the entire value chain to acquire raw materi-als, to convert these raw materials into specified final products, and to deliver these final products to customers (see Fig. 1.4).
• Supply chain management (SCM) is a cross-department and cross-enterprise integration and coordination of material, information and financial flows to transform and use the supply chain resources in the most rational way along the entire value chain, from raw material suppliers to customers.
• SCM is one of the key compo-nents of any organization and is responsible for balancing demand and supply along the entire valueadding chain (see Fig. 1.5).
• SCM integrates production and logistics processes. In practice, the production, lo-gistics and SCM problems interact with each other and are tightly interlinked.
• On-ly two decades have passed since enterprise management and organizational struc-ture have been considered from the functional perspective: marketing, research and development, procurement, warehousing, manufacturing, sales, and finance.
• The development of SCM was driven in the 1990s by three main trends: customer orientation, markets globalization and establishing an information society.
• SCM, as the term implies, is primarily directed to the inter-organizational level. Another successful application of SCM depends to a very large extent on the intraorganizational changes.
• Even the collaborative processes with an extended infor-mation systems application are managed by people who work in different depart-ments: marketing, procurement, sales, production, etc.
• The interests of these de-partments are usually in conflict with each other. Hence, not only outbound synchronizations but also internal organizational synchronization are encompassed by SC organization
• The main management task is to make decisions. Chocolate SC can be used as an illustrative example to depict basic decisions in SC and operations management (SCOM).
• What happens between the cocoa pods harvest and placing chocolate on the shelves in a supermarket? A complex SC should be built between raw material suppliers and end customers (see Fig. 1.6).
• To produce chocolate, cocoa pods are first harvested from cocoa trees, e.g. in Côte D'ivoire.
• Cocoa pods are then moved by donkeys to a processing station where they are packed into special carrier bags to avoid damages during transportation by container ship.
• At harbor, the bags are packed into special containers and moved to a container ship that will bring them, e.g., to Hamburg (see Fig. 1.7).
• Simultaneously, from harbors in Guatemala and Madagascar container ships with vanilla starts. Along with sugar and milk powder, vanilla belongs to the compo-nents needed for chocolate production.
• Sugar and milk powder are typically sourced locally to avoid long transportation ways. Simultaneously, from harbors in Guatemala and Madagascar container ships with vanilla starts
• First, cocoa pods are delivered to preliminary processing plant to produce cocoa butter and cocoa mass which are then moved in trucks by road to chocolate manu-facturers.
• After getting all the components, multi-stage manufacturing process can be started, the final result of which is chocolate.
• Chocolate is then packed and delivered in large batches at pallets to distribution centers from which small batches are finally delivered to supermarket.
• It can be observed from the chocolate SC as well as from the introductory example of the Santa Claus’s SC that the responsibilities of SCOM managers can be divided into sourcing, production, distribution, transportation and SCM (see Fig. 1.8).
• Fig. 1.8. House of SCOM The responsibilities of SCOM managers are really multi-faceted (see Fig. 1.9). The decision-making area in SCOM ranges from strategic to tactical and operative levels. Strategic issues include, for example, determination of the size and location of manufacturing plants or distribution centres, decisions on the structure of ser-vice networks, factory planning, and designing the SC.
• Tactical issues include such decisions as production or transportation planning as well as inventory plan-ning. Operative issues involves with production scheduling and control, inventory control, quality control and inspection, vehicle routing, traffic and materials han-dling, and equipment maintenance policies.
• Fig. 1.9. Decision matrix in supply chain and operations management This description holds true for many different organizations like global brand manufacturer such as Apple or Toyota, major retailers such as Tesco or WalMart, nonprofit organizations such as International Red Cross, local petrol stations or hospitals. Purchasing, assembly, shipping, stocking and even communicating are just a few examples of the many different actions unfolding within these organiza-tions, united by a single purpose: to create value for a customer.
• management SCOM is everywhere! SCOM specialists should obtain different qualifications since SCOM is multi-disciplinary in its nature (see Fig. 1.10).
• There are many skills and attributes which are important for SC and operations managers to suc-ceed in the operations environment.
➢ systems and engineering knowledge
➢leadership an d strong communication skills
➢ general multidisciplinary business knowledge
➢ strong analytical problem solving abilities and quantitative skills
➢negotiation and presentation skill
• To become an SC or operations manager, it is important to be able to communicate well with people from all departments.
• There is a strong relationship between the SCOM function and other core and support functions of the organization, such as accounting and finance, product development, human resources, information systems and marketing functions. Another important skill is time management.
• Some of the job responsibilities common to SCOM are as follows:
➢ coordinating business processes concerned with the production, pricing, sales and distribution of products and services
➢managing workforce, preparing schedules and assigning specific duties;
➢reviewing performance data to measure productivity and other performance indicators
➢ coordinating activities directly related to making products / providing services
➢planning goods and services to be sold based on forecasts of customer demand;
➢ managing the movement of goods into and out of production facilities
➢locating, selecting, and procuring merchandise for resale, representing man-agement in purchase negotiations managing inventory and collaborating with suppliers
➢planning warehouse and store layouts and designing production processes
➢process selection: design and implement the transformation processes that best meet the needs of the customers and firms demand forecasting and capacity planning
➢logistics: managing the movement of goods throughout the SC
➢risk manager: pro-active SC design, risk monitoring, and real-time coordination in the case of disruptions SC and operations managers have strategic responsibility but also control many of the everyday functions of a business or organization.
• They oversee and manage goods used at the facility such as sales merchandise, inventory or production materials.
• SC and operations managers also authorize and approve vendors and con-tract services at different locations worldwide.
• Starting positions for SCOM typically comprise operative responsibilities in procurement or sales departments and work as for example a consultant, customer service man-ager or a supply chain analyst.
• With five–ten years of practical experience, such positions as purchasing manager, transportation manager, international logistics manager, warehouse op-erations manager or SC software manager can be achieved.
• With ten or more years of experience, vice president for SCOM is a realistic position.
• SCOM positions may include jobs in production planning, inventory control, ma-terials control, work scheduling, quality control, and operations analysis.
There are a wide variety of career options in the field of SCOM.
Some key opportunity areas are as follows
➢ Operations manager Business analyst Production planner
➢ Operations analyst Materials manager
➢Quality control specialist Consider some of these and other possible careers in SCOM more detailed.
➢ Plant managers supervise and organize the daily operations of manufacturing plants.
➢For this position, expertise in activities such as production planning, purchasing and inventory management is needed.
➢ Quality managers aim to ensure that the product or service an organization provides is fit for purpose, is consistent and meets both external and internal requirements. This includes legal compliance and customer expectations.
➢ A quality manager, sometimes called a quality assurance manager, coordinates the activities required to meet quality standards. Use of statistical tools is required to monitor all aspects of services, timeliness and workload management.
➢Process improvement consultants take over activities which include designing and implementing such activities as lean production, six sigma and cycle time reduction plans in both service and manufacturing processes.
➢ Analyst is a key member of the operations team supporting data management, client reporting, trade processes, and problem resolution. They use analytical and quantitative methods to understand, predict and improve SC processes.
➢ Production managers are involved with the planning, coordination and control of manufacturing processes.
➢ They ensure that goods and services are produced at the right cost and level of quality.
➢Service manager plans and directs customer service teams to meet the needs of customers and support company operations.
➢ Sourcing managers are involved with commercial and supplier aspects of product development and sourcing projects.
➢ They conduct supplier analysis, evaluate potential suppliers, and manage the overall supplier qualification process, develop and create sourcing plans, request for proposals and other sourc-ing documents, evaluate and recommend purchasing and sourcing decisions.
➢ International logistics manager works closely with manufacturing, marketing and purchasing to create efficient and effective global supply chains.
➢ Transportation manager is responsible for the execution, direction and coordi-nation of transportation.
➢ They ensure timely and cost effective transportation of all incoming and outgoing shipments.
➢ warehouse manager is responsible for managing inventory, avoiding stock-outs and ensuring material replenishment at minimal costs.
➢ Risk manager analyses possible risks, develops proactive operations and SC design, monitors risks and coordinates activities for stabilization and recovery in the case of disruptions.
• Bowersox DJ (1969) Physical Distribution Development, Current Status, and Potential. J Mar-keting 33:63–70
• Bowersox DJ, Closs DJ, Copper MB (2012) Supply Chain Logistics Management. 4th edn.
• McGraw-Hill, Boston et al. Chopra S, Meindl P (2012) Supply Chain Management. Strategy, Planning and Operation. 5th edn.
• Pearson, Harlow Christopher M (2011) Logistics and Supply Chain Management. Creating Value-Adding Net-works. 4th edn. FT Press, New Jersey
• Dolgui A, Proth J-M (2010) Supply Chain Engineering: Useful Methods and Techniques.
• Springer, Berlin Forrester JW (1961) Industrial dynamics. MIT Press, Cambridge Francis M, Fisher R, Thomas A, Rowland H (2014) The meaning of ‘value’ in purchasing, logis-tics and operations management. Int J Prod Res 52(22):6576-6589
• Geoffrion AM, Graves GW (1974) Multicommodity Distribution System Design by Benders De-composition. Manage Sci 29(5):822–844
• Greasly A (2013) Operations Management. 3rd edn. Wiley, New York Heizer J, Render B (2013) Operations Management: Sustainability and Supply Chain Manage-ment. 11th edn.
• Pearson, Harlow http://careersinsupplychain.org http://www.apics.org Ivanov D, Sokolov B (2010) Adaptive Supply Chain Management. Springer, London Oliver RK, Webber MD (1992) Supply Chain Management: Logistics catches up with strategy. In: Christopher M (ed) Logistics: the strategic issues, Chapman & Hall, London.
• Simchi-Levi D, Kaminsky P, Simchi-Levi E (2007) Designing and Managing the Supply Chain: Concepts, Strategies and Case Studies. 3rd edn.
• McGraw-Hill, Boston et al. Slack N, Brandon-Jones A, Johnston R (2013) Operations Management. 7th edn.
• Pearson, Har-low Stadtler H, Kilger C (2008) Supply Chain Management and Advanced Planning. 4th edn. Spring-er, Berlin et al.
THANK YOU