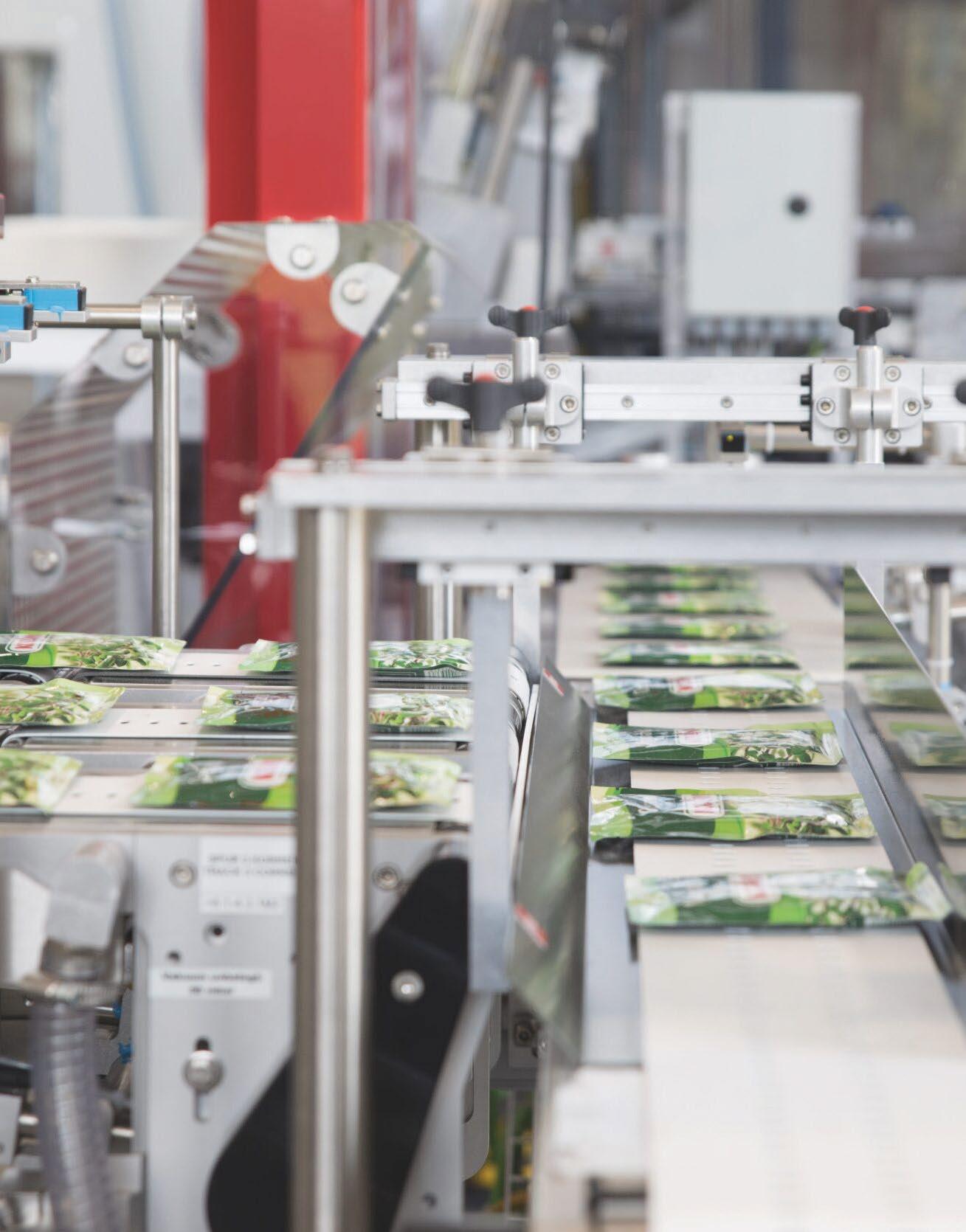
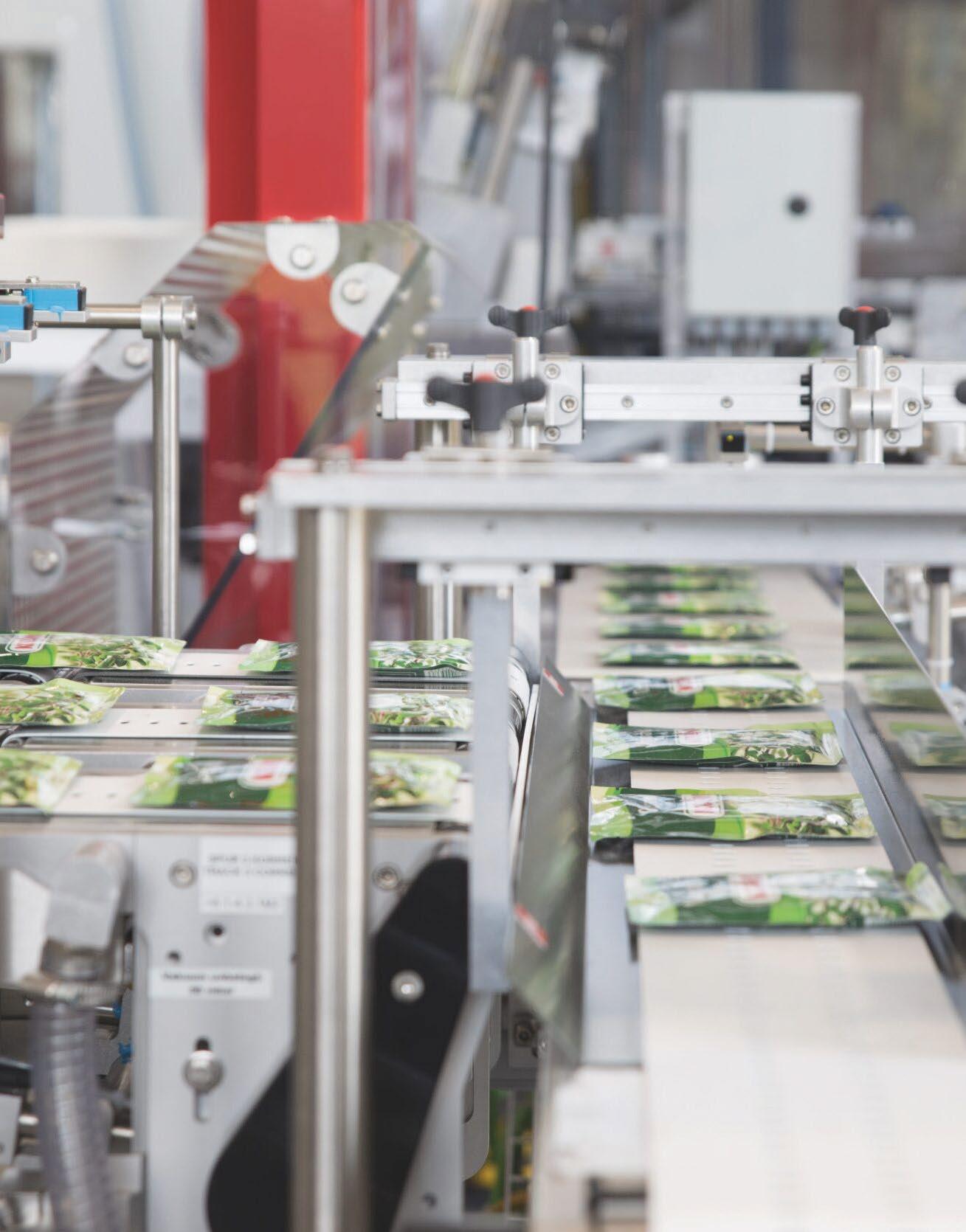
The edge of innovation
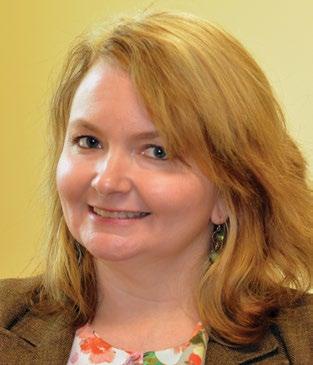
Melinda Waldrop Managing Editor
A common thread running through this issue of Produce Processing is innovation, and that concept is embodied by Nicole Glenn. Glenn, founder and CEO of Candor Expedite, created the transportation solution she saw a need for after decades in the industry deepened both her appreciation of and frustration with aspects of the business. Read about how her company’s innovation in packaging is poised to transform cold chain from shipper to supermarket — all while providing the increased transparency Glenn believes is as necessary as improved flexibility.
Glenn’s story starts on page 6.
Innovation is also the driving force behind SOMIC Packaging’s forward momentum. A decade into its expansion into North America, the end-of-line packaging solutions provider is preparing to ramp up production in a larger facility while launching the latest tailored technology in a line of the customized equipment that its customers have come to expect.
Read about how the company is striving to remain client-centric while managing exponential growth beginning on page 16.
A key feature of successful innovation is customer choice. A sales expert for a leading packaging equipment manufacturer takes a look at the newest options in wrapping, and the important role labeling plays in traceability and sustainability on page 22.
Automation is often synonymous with innovation. On page 28, PMMI, The Association for Packaging and Processing Technologies, explains why end-of-line can be the ideal place to start for processors looking to add automation — and the increased efficiency, flexibility and speed that it can bring — to their processes.
Successful companies display a responsive nimbleness to customers’ ever-changing needs, and the ability to craft workable solutions often depends on a willingness to think outside the box, coupled with the capability to implement cutting-edge solutions.
The ability to innovate gives the most adaptable businesses a leg up. The proof is in the processing.
Vol. 10, No. 4
Office 616-887-9008
Editorial
Managing Editor Melinda Waldrop, 616-520-2158 mwaldrop@greatamericanpublish.com
Editorial Director Debbie Eisele, 616-520-2160 deisele@greatamericanpublish.com
Advertising Sales
Associate Publisher Andrea Schafer, 616-520-2139 prosales@produceprocessing.net
Account Specialist Kim Meyers, 616-520-2137 kmeyers@greatamericanpublish.com
Production
Senior Greg Ryan, 616-520-2145
Graphic Designer gryan@greatamericanpublish.com
Associate Amanda Mackey, 616-520-2157
Creative Director amackey@greatamericanpublish.com
Creative Director Allison McKenzie, 616-520-2142 amckenzie@greatamericanpublish.com
Circulation
Circulation Becky Stovall, 616-520-2138 circulation@produceprocessing.net
Corporate
CEO & Publisher Matt McCallum, 616-520-2133 publisher@produceprocessing.net
COO & CMO Kim Baker, 616-520-2135 kbaker@greatamericanpublish.com
CFO Deb Carnes, 616-520-2169 dcarnes@greatamericanpublish.com
Editorial Advisory Board
Adrienne Seiling, American Frozen Food Institute
Rudi Groppe, Heinzen Manufacturing International Lou Cooperhouse, Rutgers Food Innovation Center Sherrie Rosenblatt, Can Manufacturers Institute Leonard Batti, Taylor Farms, Salinas, California
ISSN 2375-3447
Editorial and advertising offices at Great American Media Services, a division of Great American Publishing, P.O. Box 128, Sparta, MI 49345 Phone: 616-887-9008
Printed six times a year in the U.S.A. Copyright 2024.
Produce Processing is $25 per year and $55 for three years if residing in the U.S.; $56 (U.S.) per year Canada; and $100 (U.S.) per year other foreign countries. Digital subscription: $9.95 per year. Single copy and back issues: $6.
The opinions and views expressed by authors, contributors and advertisers in Produce Processing do not necessarily reflect those of the editors and publisher. Appearance in Produce Processing does not constitute endorsement by Great American Media Services or Produce Processing of the advertiser, its products, or services. Great American Media Services and Produce Processing accepts no responsibility of liability for the validity or accuracy of information supplied by contributors, vendors, advertisers, or advertising agencies. Great American Media Services and Produce Processing do not make any claims or guarantees as to the accuracy or validity of information supplied by contributors, vendors, advertisers or advertising agencies.
Email me at: mwaldrop@greatamericanpublish.com
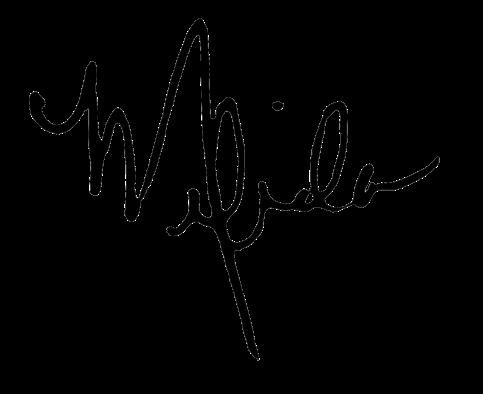
For subscription information, visit our website at www.produceprocessing.net. Permission is granted for reprinting material, except for commercial or advertising purposes, providing Produce Processing is given full credit.
P OSTMASTER: Please send address changes and corrections to Great American Publishing, PO Box 318, Lincolnshire IL 60069


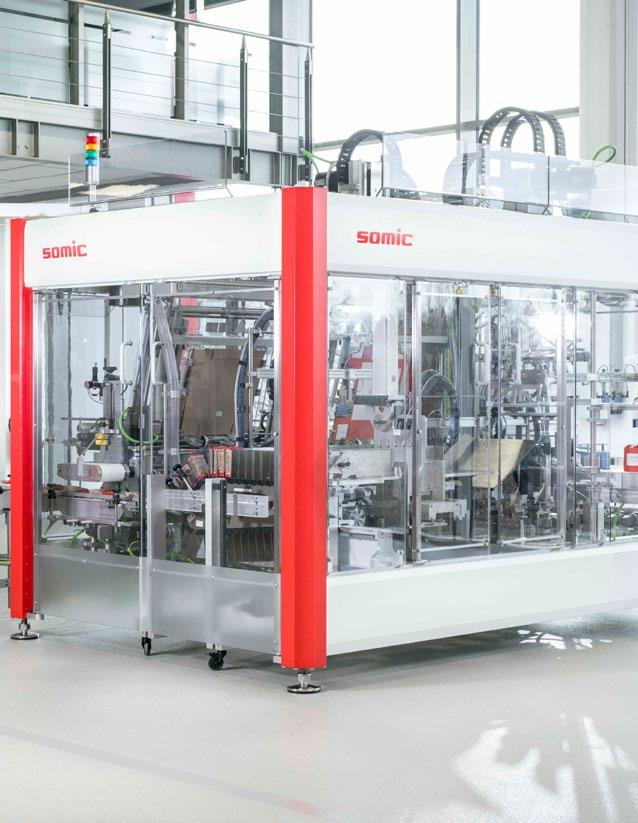
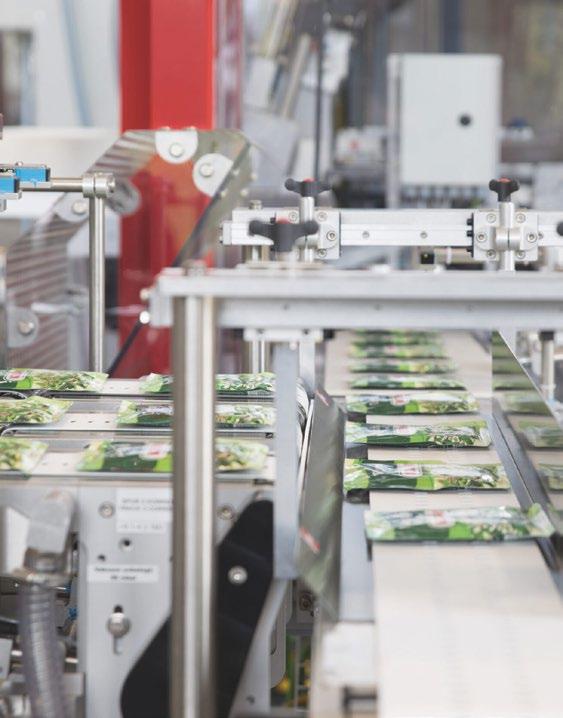
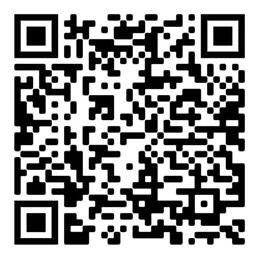
Success leads SOMIC to expand North American packaging operations
By Melinda Waldrop Managing Editor
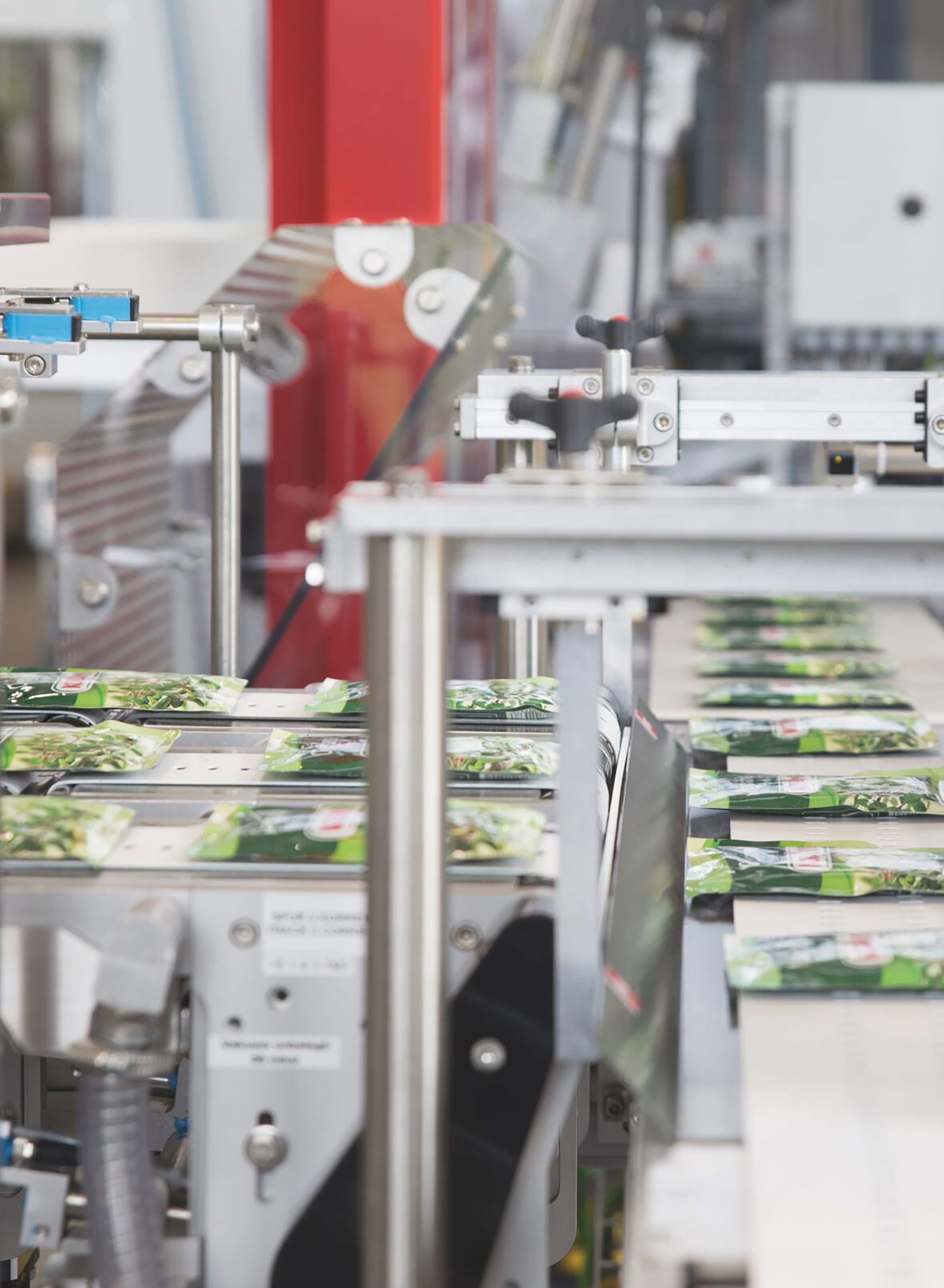
SOMIC’s solutions for single- and multi-component end-of-line packaging come equipped with customized tools tailored to customers, from open trays or wraparound cases to multi-component carton or corrugated packs. Photos courtesy of SOMIC Packaging.
Ten years into SOMIC Packaging’s foray into North America, the company faces an enviable conundrum: how to manage its gangbusters growth while maintaining the customer-specific solutions driving it.
The German-based company, with its North American subsidiary headquartered in Minnesota, is relocating to a larger facility and ramping up production on the heels of the launch of its next-generation 434 W-3 case packaging machine.
“We’ve built a facility that’s five times larger than what we’re currently in. We’ll be able to triple our output in terms of overall machine sales in the United States,” Peter Fox, CEO at SOMIC Packaging Inc., told Produce
Processing. “That’s a really big deal for us. We’re on a pretty steep growth trajectory, and it’s fun to watch the company grow.”
SOMIC’s solutions for single- and multi-component end-of-line packaging come equipped with customized tools tailored to customers, from open trays or wraparound cases to multi-component carton or corrugated packs.
The 434, which debuted at Interpack 2023 last May, builds on the company’s heritage 424 machine series and is the latest example of the flexibility and efficiency SOMIC strives to provide.
“It’s conceptually and functionally the same machine,” Fox said. “It’s just been updated and upgraded, with things
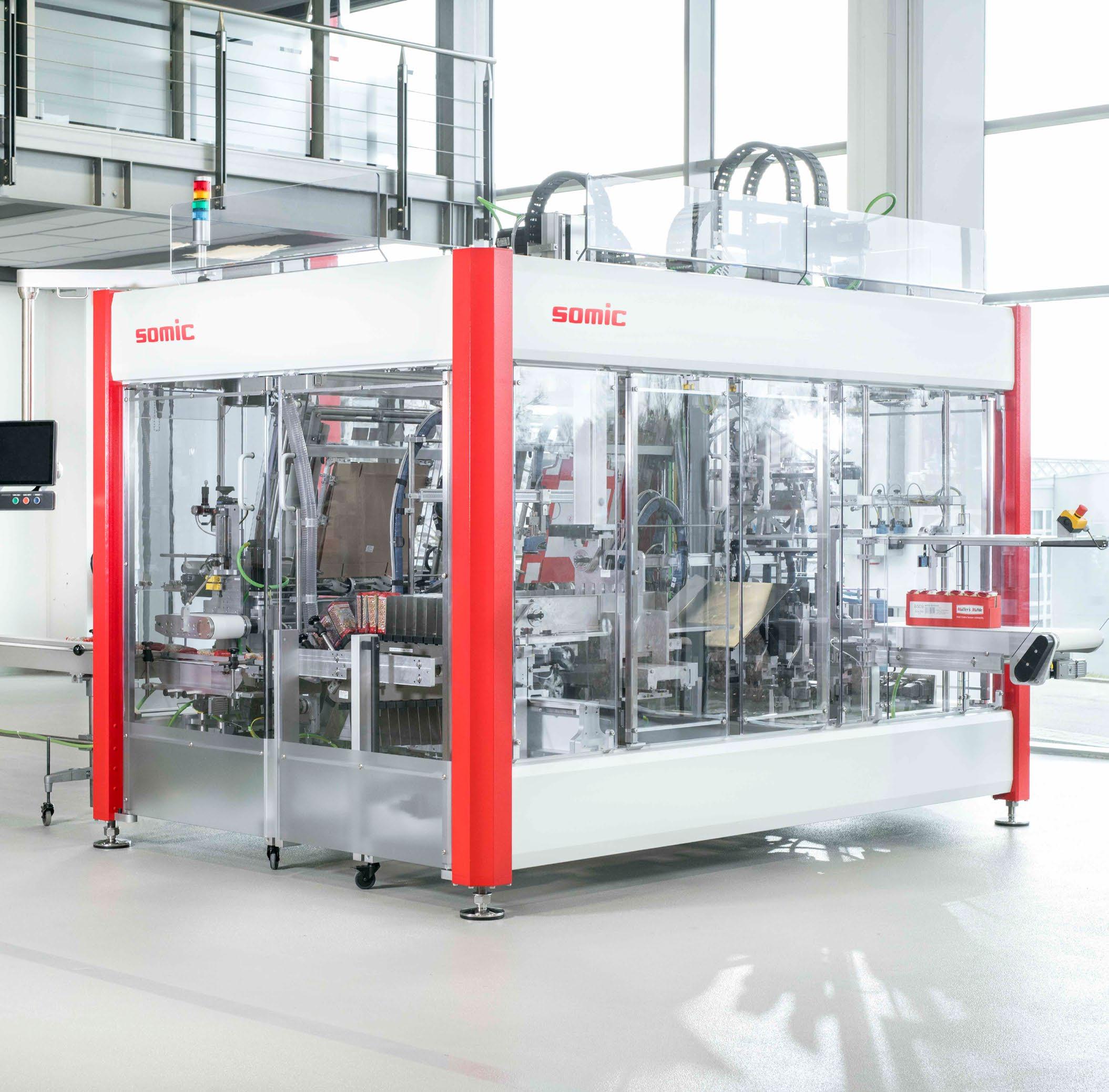

“Thebiggestchallengethatwehaveright nowismanagingourgrowthandjust makingsurewe’renotallowingthis growthtokeepusfromcontinuingto producethequalityproductthatwedoand satisfyasmanycustomersaspossible.”
—PETER FOX, SOMIC PACKAGING INC. CEO
that our customers wanted to see, such fewer barriers to getting in and out of the machine, whether it be a maintenance or a changeover situation.
FOCUS ON FUNCTIONALITY
American Pasteurization Co., the Milwaukee-based copacker for organic snack company Once Upon A Farm, turned to SOMIC to help keep up with booming business. Once Upon A Farm, founded in 2015 by a group of entrepreneurs including actress Jennifer Garner to provide nutritious baby food and snacks for children, needed to
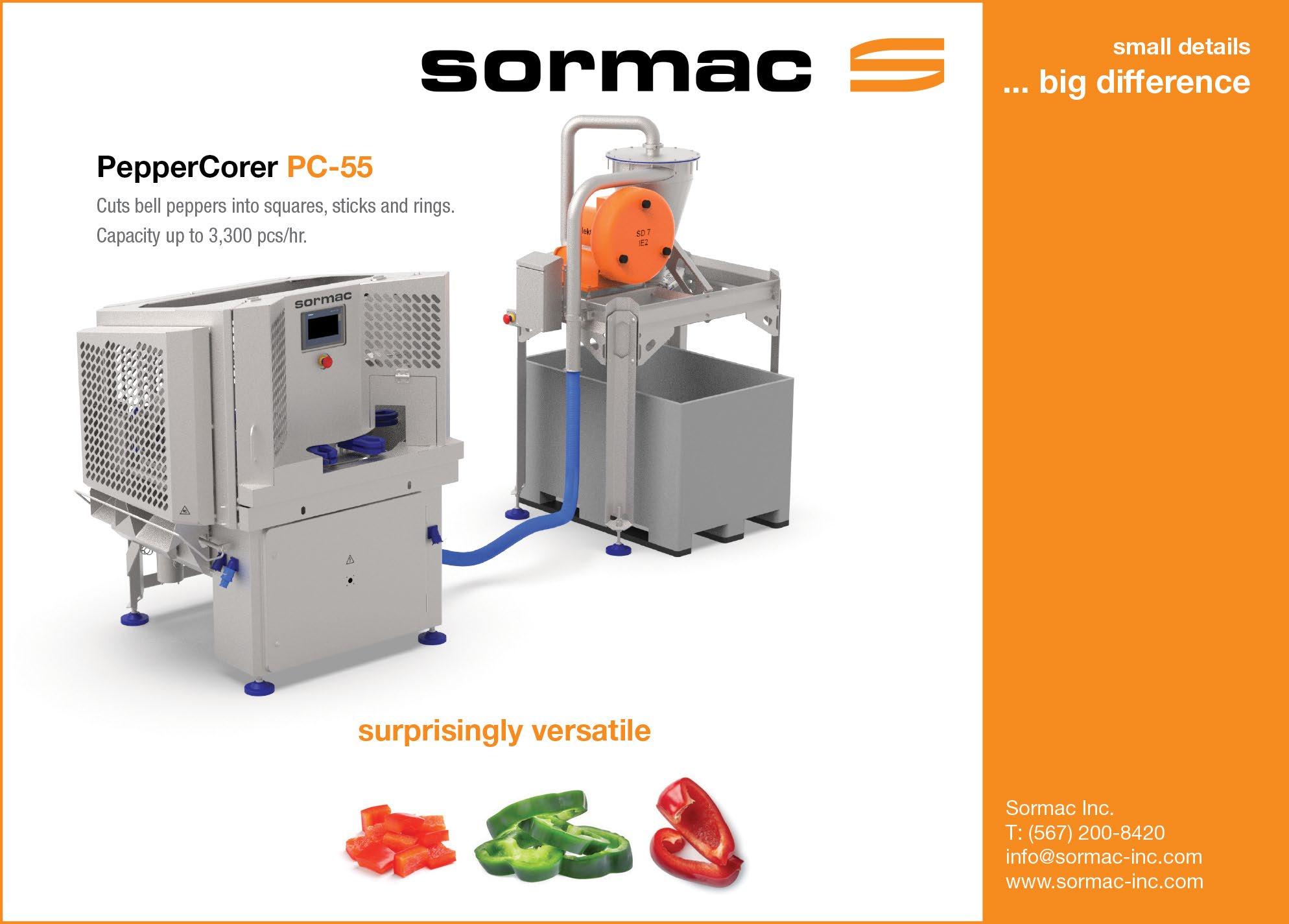
meet growing production needs faster using less labor. Packing with SOMIC’s 424 W-3 case packer began in Milwaukee in mid-February.
“This machine replaced quite a few extra sets of hands we needed to have on the line,” Greg Zaja, vice president of business development for American Pasteurization Co., said. “We also had an older piece of equipment that we were getting by with but it wasn’t intended to handle the volume we now do. The SOMIC machine allows for greater hourly throughput with a far-reduced risk of human error.”
Less error means less downtime, which increases efficiency and profitability.
“Keeping costs in check helps us offer our customers the most competitive pricing in the industry,” Zaja said. “Reducing the risk of delays or cost overruns helps our customers meet all their objectives, which is our No. 1 priority.
“The functionality of the machine itself was key.”
All the updates found in the 434 — including automatic changeover adjustments to components including the glue nozzle and magazine — are designed to increase that basic goal, Fox said.
“It (the 434) incorporates what I believe to be the biggest strength of the SOMIC case packer, and that is the ultimate
simplicity in the functionality of the machine,” Fox said. “Whether it be a flexible film product or a bottle or virtually any type of package, our ability to organize, collect and then manipulate the product is pretty significant. That makes so many of our packages perfect for the world of retail-ready, because we can present that product exactly how the customer wants it to appear when that case is opened.”
SOMIC’s flexibility and functionality also helped a cheese packaging company overcome a challenge, Fox said. The company was struggling to meet club store packaging requirements for stacking strength and shelf positioning, running a separate product line with complicated, handformed casing that ate into profitability.
Different functional groups allowed SOMIC machines to run a standard wraparound case, then switch to a run with specific requirements, Fox said. The company developed a tray concept with flaps folded into a corner post.
“We form these corner posts on the tray and then we erect the trays around the product inside of a forming mandrel,” Fox said. “It creates a tremendously strong box that, if you compare it to what they were doing before with their hand erecting, uses about 45% less material. Not only are you getting a stronger box, you’re
LABELING MADE SIMPLE
Unlock the future of labeling efficiency with Ossid’s NextGen Weigh Price Labeler (WPL). Domestically designed and built, this cutting-edge machine is engineered to elevate your packaging operations to new heights.

your labeling process? Connect with us today
with the user in mind, the intuitive interface streamlines operations, making label creation and SKU changeovers a breeze.
“We also had an older piece of equipment that we were getting by with but it wasn’t intended to handle the volume we now do. The SOMIC machine allows for greater hourly throughput with a far-reduced risk of human error.”
—GREG ZAJA, AMERICAN PASTEURIZATION CO.
automating the entire process and eliminating 40% of the material.
“It gave the plant much more operational flexibility, (and) it’s a pretty common story that we have with a lot of the projects that we do.”
SUCCESS IN ALL SIZES
Another appeal of SOMIC’s equipment is its small footprint, Fox said.
“We use the minimum amount of space necessary to complete a lot of different functions in that very small space,” he said.
That proved the deciding factor for a small, family-owned sausage company in Kentucky which chose SOMIC for its first automated case packer.
“The primary driver was they had so little space available for a traditional case packer, where you have case forming, case loading and case closing,” Fox said. “We do that all in one very small frame.”
That compactness helps SOMIC address another core company focus: sustainability. Its wraparound cases, formed around the product, use less material, while SOMIC reduces energy consumption at its plants by using vacuum material handling systems instead of energy-inefficient compressed air, Fox said.
“Everything that we do is really based on efficiency,” he said. “There’s a lot of restrictions and regulations in
Europe when it comes to energy consumption and packaged material usage. Because of our European heritage, we tend to minimize, minimize, minimize.”
When he spearheaded SOMIC’s launch in North America a decade ago, Fox expected larger consumer packaged goods operations would make up the bulk of the company’s customer base, but he has found that businesses of all sizes have benefited.
“We’re not the most inexpensive machine out there, so I thought we’re going to be hard-pressed to justify this to smaller companies,” he said. “Actually, we’ve really kind of found a sweet spot mostly in the mid-sized companies, for companies that are producing a large number of formats.
“They have really been a huge part of our success, and some very small companies.”
That across-the-board success will soon see SOMIC relocate from its Eagan, Minnesota, facility to its larger plant in Grove Heights, where the company will make all machines for the North American market, in October. Fox also expects the North American arm of the company to add around 20 employees by 2025.
“We’re growing fast,” he said. “The biggest challenge that we have right now is managing our growth and just making sure we’re not allowing this growth to keep us from continuing to produce the quality product that we do and satisfy as many customers as possible.”
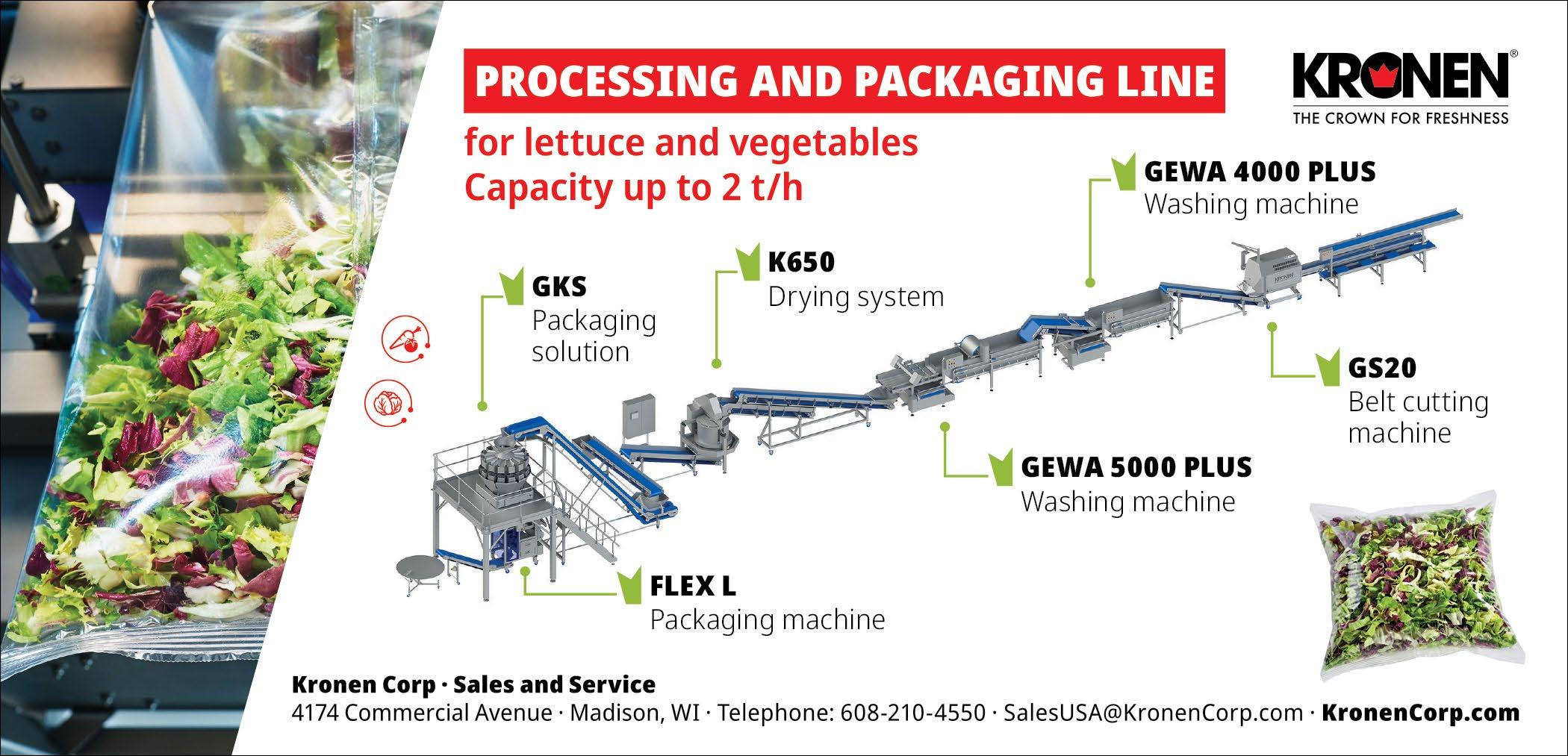