ORGANIC GROWTH, IMPRESSIVE RESULTS
Meteoric success story Once Upon a Farm aims for the next level with SOMIC equipment — pg. 8
SOMIC celebrates its Golden Anniversary pg. 4
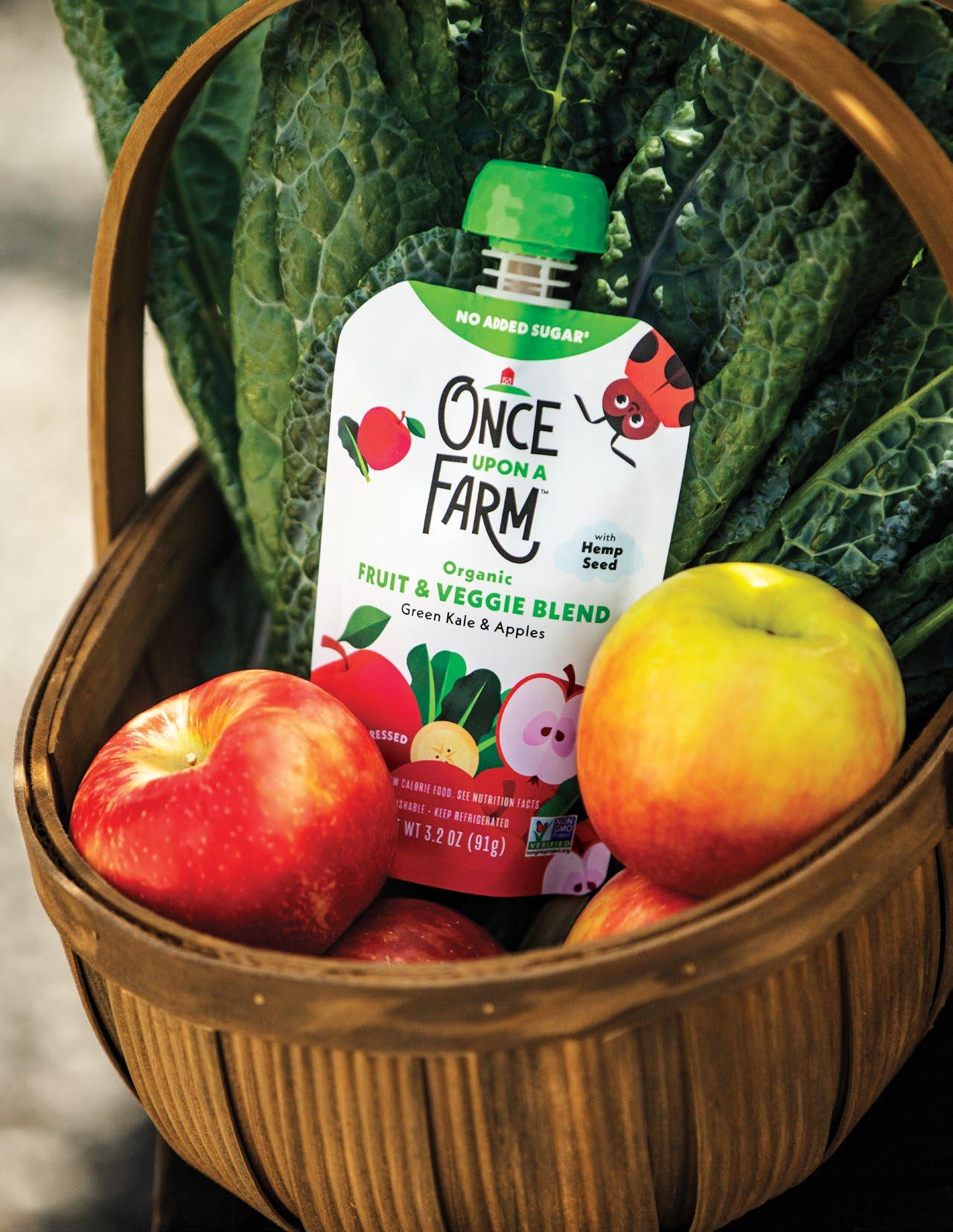
SOMIC Haag implements important changes prior to 5th anniversary pg. 14
Meteoric success story Once Upon a Farm aims for the next level with SOMIC equipment — pg. 8
SOMIC celebrates its Golden Anniversary pg. 4
SOMIC Haag implements important changes prior to 5th anniversary pg. 14
I have to admit I love this time of the year. Up here in Minnesota, summer changes over to fall almost overnight after Labor Day. For me, it goes beyond the seasonal aspects with the cooler weather. Football season is back, and so is PACK EXPO International 2024, our biggest trade show of the season.
But before we travel to Chicago for this year’s show, everyone here at SOMIC Packaging is in overdrive and burning the midnight oil in preparation for the move into our new production facility. A month before PACK EXPO, we intend to make the trek a few miles down the road to Inver Grove Heights where we will increase our workspace by five times compared to our current footprint.
As we recognize our tenth anniversary as a company, I remember the days when we first began operations in a small office in
Bensenville, Illinois. It was so close to Chicago’s O’Hare International Airport, you could hear the airplanes overhead on their landing approach. Great times they were, serving as the first vital steps and putting us on the path to future success.
Ten years have gone by pretty quickly with the many equipment installations we’ve made. From the first installations with cheese manufacturers in the Midwest and across the border in Canada, to the most recent, we’ve crisscrossed the United States with our equipment. It runs at the facilities of manufacturers and companies representing many different industries. To everyone who has purchased a SOMIC machine, we thank you.
If you think our first 10 years were productive, wait until you see what we have planned for the future. The investment in our larger headquarters will enable us to facilitate the assembly of all new North American machines, and increase warehousing capabilities to provide a larger inventory of critical parts and consumables.
Interested in scheduling a booth appointment or attending PACK EXPO? Register for free with code: 75P22. Go to packexpointernational.com
In anticipation of these developments, and to better serve our growing customer base, we have implemented many new procedures. We have also committed resources to accommodate this growth phase by hiring additional staff in every department. From the assembly line, parts and service, to sales support and HR, we are moving forward with a larger team to better serve you and other customers.
If you did not attend PACK EXPO in Las Vegas but are planning to visit us in Chicago, I think you will be impressed when we demonstrate the new 434 generation wraparound case packing machine in booth N-6148. It represents our commitment to the future by producing the highest quality and best performing packaging systems.
Our newest modular machine concept is based on fixed function groups, consisting of proven, tested and standardized mechatronic systems. The decentralized servo technology is particularly suitable for the machine’s modular design. The functional units can be individually adapted to the desired format ranges, therefore giving this machine a customized, future-proof design.
We continue to listen and learn from our customers so some new features have also been implemented. The stainless-steel frame with an integrated electrical installation is spilt between the product infeed, which handles the collection and grouping stages, and case forming.
Machine height safety doors with a 180-degree opening have been added to allow full use of the space around the machine. The new frame construction also provides ideal ergonomic conditions for any format adjustments, as well as for cleaning and maintenance work.
You will also see the machine’s supply unit, a combination of control cabinet and supply cabinet, now contains all noise-intensive components. With the noise level dramatically reduced, this makes the machine more user-friendly for your operators. It also now offers an automatic SOMIC QuickChange adjustment system. This prevents incorrect operation and allows for a faster and easier format changeover.
I mentioned earlier about our tenth anniversary, which coincides with SOMIC’s golden anniversary in Germany. In this issue of Retail Ready Magazine, you can read all about the many innovations and successes since the company began operations 50 years ago in a converted farmhouse. It is amazing to realize all of the steps the Bonetsmuller family and others have taken for SOMIC to become the company it is today.
We manufacture advanced mechatronic case-packing systems that collate, unitize and load cartons, trays, retail-ready packages, and wraparound cases.
See how SOMIC can bring new efficiencies to your packaging line.
Amazing aptly describes Once Upon a Farm, and this issue’s cover story. This customer began business one year after we opened the doors at SOMIC Packaging, and what a run they are experiencing. Learn more about the meteoric rise of this organic snack food company, and how one of its SOMIC 424 W3 wraparound case packing systems is performing at a co-packer’s facility in Milwaukee.
We also have a story about two important developments at SOMIC Haag in Germany, as they celebrate their five year anniversary. And as part of our ongoing series, you can read more about one of our new employees, Brad Nelson. As the After Sales and Service Coordinator, you may have already spoken with him.
On behalf of our team, I hope to see you in our booth at PACK EXPO, which runs from November 3-6 at McCormick Place in Chicago.
Respectfully,
Peter Fox, Chief Executive Officer
“If you think our first 10 years were productive, wait until you see what we have planned for the future.”
+1.651.419.6050 somic.us info@somic.us
Follow us on Linkedin for updated material and conversations.
SOMIC celebrates 50 Years of Success
In 1974 the world experienced some monumental events.
Richard Nixon became the first United States president to resign after the Watergate scandal. Baseball’s Hank Aaron broke Babe Ruth’s longstanding career home run record. Blazing Saddles was the top grossing movie at the box office when people actually had to visit a theatre when a film came out. And the Rubik’s Cube was invented and would soon become one of the bestselling novelty products.
It was a simpler time when Manfred and Hildegard Bonetsmuller began a small machine engineering company the same year with two other employees in Upper Bavaria. They created SOMIC and worked from a converted farmhouse to develop transport and handling systems for cheese dairies in the region.
The decision to concentrate more so on the range of secondary packaging machines and not its cheese counterparts took place in 1994. Today, these machines serve as the foundation for market presence.
Fifty years later, the minienterprise in Vogtareuth would become a leading, world renowned manufacturer of secondary packaging machines. Now led by Manfred’s eldest son, Patrick, SOMIC’s bright and spacious headquarters in Amerang is home to 550 employees. Others diligently work at subsidiaries in the United States and Thailand. From stacking machines for cheese to fully automatic packaging machines, SOMIC equipment now operates in 45 countries.
Let’s celebrate by taking a look at the groundbreaking achievements through the years that led to SOMIC becoming the company it is today.
From the start and until 1986, the machine portfolio was systematically expanded for the entire cheese industry. Including a cheese packaging line, the first step was to introduce the SOMIC VA 60, a wrapping machine for Reblochon, at the Salon d’Emballage in Paris in 1977.
The KA-20 carton erector soon followed. Able to erect and automatically glue the flat carton blanks, it formed the basis for our company’s focus on food and nonfood carton packaging.
As early as 1981, the SOMIC team designed a tray erector with folding and gluing positions and an output of up to 1,200 trays per hour. The focal point in the machine portfolio, it would really take off 20 years later in 1994 when management bundled things together and said goodbye to the majority of cheese-making machines. These were the first steps into the secondary packaging machine business. But first, there were other breakthrough events.
The dairy industry marked the starting point for SOMIC’s success. By 1986, design engineers had gradually developed all the individual processes involved in cheese production. The team quickly realized applications worked for other product groups.
Equipment for peanut cans and tins of cocoa powder were introduced in 1988. SOMIC packaging machines would handle a 3-row grouping of 200 gram peanut cans in two layers with a processing capacity of 350 cans per minute. The range of applications expanded to include:
• Potato chip cans
• Coffee capsules
• Bags of baked batter pearls and tea bags
• Granola packets
• Frozen products
• Leaf gelatine sachets
• Toothbrushes
• Tube feeds for the pharmaceutical industry
• Baby food
• Bath fragrances
• Kitchen herb and lettuce pots
A year later, sales quickly expanded to new markets including the Benelux countries of Belgium, Luxembourg, The Netherlands, and in Poland. The first order was received for muesli packs that were packaged in a wraparound carton. The flexible fan collector was also developed during this time, serving as the basis for the upright packaging of pouch packs. While the classic infeed conveyor is suitable for packaging products horizontally, a different grouping method is required for the upright presentation of products in the carton.
The solution was the fan-type collator. The highly dynamic compartment collector module is variable in design, and also bundles several product packs in one compartment. To date, more than two-thirds of SOMIC machines have integrated compartment collections.
Three main steps characterize our secondary packaging process. It includes the collection and grouping of the products, folding the carton blank around the product grouping, and closing the carton.
In 1996, the modular SOMIC 404 machine generation was introduced. It combines all aspects of today’s machines and completes format changeovers without tools.
Continues on next page.
While simpler products such as folding cartons could be brought together into the desired product grouping via a classic infeed conveyor, a new collection option had to be implemented for products in flexible pouches or products with a soft consistency, such as grated cheese or baking mixes.
The solution was the lamella chain. Highly dynamic, this module is variable in design and allows for several product packs to be bundled in one compartment. To date, this method is the preferred product collating technology in over 90% of SOMIC machines.
Until the early 2000’s, packaging machines were based on a drive concept with a vertical shaft and cam discs. The integration of servo drive technology into the machine assemblies paved the way for further progress. This meant all functional movements could be individually controlled electronically and programmed using an industrial PC.
For the company in 2001, this was the start of the SOMIC 414 machine generation. With an increase in speed and precision for all individual movements within the packaging process, the advantages of the new drive technology were immediately apparent. Servo technology made it possible to achieve performance levels of 500 horizontal or vertical chocolate bars, and 360 bags of instant powder per minute.
It also linked to a wide variety of formats. Theoretically, an infinite number of carton formats can be realized on one machine and always within the maximum format range. In reality, a machine is supplied with over 40 different formats.
It didn’t take long for word to spread. In 2005, the first customer in Nigeria presented SOMIC with a challenging project. A packaging machine was required for approximately 35 cm-long chain bags filled with powder. Requiring an output of 120 bag strands per minute, the product was not stable and needed a special packaging solution. The customer was satisfied with the result and four years later, they ordered a line combination on a manipulator basis.
The new SOMIC QuickChange technology invented in 2006 made format changeovers quick and easy. Since then, this has guaranteed a very convenient changeover process. Format parts can now be changed 100% without needing tools, and changeover times have been reduced by more than 50%, producing more machine uptime and greater productivity.
When an order from South America arrived in 2008, SOMIC was able to impress with a fast, double-cycle tray packer. The packaging of small, round cans with meat content on the 414 series required some special functions, resulting in a high output of 400 aluminum cans per minute.
In 2009, SOMIC’s 424 generation machines continued the modular concept. It formed functional assemblies, including cartons, as a tray or wraparound solution, grouping the products and producing the lid for a two-part packaging variant. Adorned with the stylish and distinguishable red color of the corner pillars, it achieved maximum flexibility in the design process with a customized solution combining mechanics, electric and software.
As a result, food industry customers benefit from increased performance, flexibility and user-friendliness thanks to the 15-inch touch panel and improved accessibility of the machine.
By 2010, SOMIC was already using a wide network of partners and its own sales staff. It enabled the company to advise and support
markets worldwide, so the 2014 founding of SOMIC Packaging, Inc. in the United States was a logical step towards further development of the company’s global presence.
In just four years, the SOMIC Packaging sales team installed 120 packaging machines in North America. Since then, regular appearances each year at the PACK EXPO trade shows in Chicago and Las Vegas that attract international visitors have expanded SOMIC's exposure. Our presence at Interpack in Dusseldorf and FACHPACK in Nuremberg led to trade show appearances throughout Europe and has since expanded to the United Arab Emirates, Korea and Thailand.
SOMIC once again is taking packaging machines to a higher level with the introduction of the 434 machine. It offers a completely new design utilizing the platform concept in machine design. This concept changes the layout of the individual modules, from a combined square to a linear arrangement of the stations, and complete from the carton forming stage to the sealing modules.
Customers can now benefit from being able to easily integrate the packaging machine into complete and narrow line layouts. The next generation machine offers further progress for user-friendliness. When changing formats, folding tools, gluing positions, and blank magazines are automatically controlled from a panel using servomotors and adjusted to formats without manual intervention. Only a few format parts are changed in the new machine using the SOMIC QuickChange system.
Leading companies like Kroger, Hartz and Goya use SOMIC equipment. See their stories at somic.us or scan the QR Code.
As a company, we continue to grow in many dimensions and one key developmental area is our team. We plan to keep you updated in future issues by introducing new associates.
Given Brad Nelson’s background and experience, he could be considered the perfect candidate for one of our most demanding jobs: After Sales and Service Coordinator. Perhaps successfully dealing with the public as a service advisor for a BMW dealership, and as an account coordinator for a local lumber company for five years, is why a phone call changed his professional direction and led him to joining the company.
“I was contacted by a recruiter regarding the opening at SOMIC. The description sounded like a job that would challenge me and allow for growth within the organization,” he recalled.
communication between them and our customers. I also check in on a regular basis with our Shipping and Receiving department to understand their current capacity levels.”
As you can tell, communicating with others is one of Brad’s strengths.
“The toughest part of my job is the distance between us and Germany. Communication across such different time zones only allows us a couple of hours of shared office time a day,” he shared.
“Having to communicate so much technical information through email can be a very meticulous task, but that’s where team chats and phone calls help. The topics we mostly discuss involve parts availability, pricing, lead times and logistics.”
“We currently stock over 1,800 unique parts and plan to increase our inventory significantly over the next year.”
“My greatest accomplishment at Lyman Lumber was advocating for my customers. I drove Lyman’s production capabilities to their limits and sometimes beyond so I could serve the customers’ needs and building schedules. I also did research to find the shortest lead times and best pricing for any special order building material needs.”
Those lessons have prepared him for his role here. Reporting to After Sales and Service Manager, Brian Neill, Brad’s main responsibilities start with creating price quotes for customers. His duties also include responding to their inquiries, in addition to placing orders with our corporate office in Germany.
“I process all of the orders that need to come from our German warehouse.
“I monitor which parts should be kept or added to our inventory, and regularly spot check our pricing and lead times for parts deliveries. I also confer with the engineering team because I find myself as the line of
Brad is one of the many employees looking forward to the company moving soon into new headquarters in Inver Grove Heights. The extra space will certainly help with the on-site inventory situation.
“We currently stock over 1,800 unique parts and plan to increase our inventory significantly over the next year.”
When he does get time away from the office, Brad enjoys exploring bike trails and running around the Twin Cities and the many lakes Minnesota is home to. Earlier this year he became an uncle and godfather to his first nephew, Archie, whom he enjoys spending his time with.
“My goal for the rest of the year is to continue learning and growing in this role. The parts department needs to be a completely autonomous function that is not reliant on inventories outside of our own facilities. Autonomy will drive down our lead times and that is a major goal of ours. I learn every day, and I feel proud to be in this position at SOMIC.”
Last February, the company implemented a new packaging plan to accelerate its growth. Things took off fast.
Organic snack food company Once Upon a Farm, has come a long way in a very short time to establish its brand and prosper. In only nine years, the privately owned California company has achieved one ambitious milestone after another and is busy preparing for its next phase of success.
Since 2018, Once Upon a Farm has nearly doubled the number of outlets that sell its nutritious baby food and snacks for children. In just five years, revenues reached $20 million in 2020. Looking ahead to satisfy future demand, the company in February 2024 installed automated SOMIC Packaging 424 W3 wraparound case packing systems at two of its co-packing providers’ facilities in Milwaukee and Orange County, Calif.
Douglas Blake, Once Upon a Farm’s senior manager, Co-Packer Engineering, said he is impressed with the early results of the SOMIC machines and is looking to finish the year on a high note.
“Since we put the equipment into production, we have tripled our efficiency while using the same number of people. Currently, our goal is to pack up to 1.2 million pouches weekly on the SOMIC machines at each facility to accommodate demand for our growing business.”
A flexible solution to help improve the process and satisfy demand
As the story goes, Once Upon a Farm was founded in 2015 by Cassandra Curtis and a group of entrepreneurs looking to modernize the standards of organic baby food. They answered the call from a generation of socially conscious newer parents asking for healthier food options by using cold pressure, High Pressure Processing (HPP) technology. It preserves original nutrients without using additives or heat.
Continues on next page.
Up to 1.2 million pouches
Once Upon a Farm’s goal to pack weekly on both of SOMIC’s 424 W3 machines.
“The SOMIC case packer allows for greater throughput with a far reduced risk of human error.”
Greg Zaja, APC’s vice president of Business Development
"Keeping costs in check helps us offer our customers the most competitive pricing in the industry."
Greg Zaja, APC’s vice president of Business Development
With CEO John Foraker and actress, philanthropist, and entrepreneur Jennifer Garner on board as cofounder and chief brand officer, the company grew distribution rapidly across most sales channels and developed multiple experimental product lines to accelerate growth. Today, they employ over 100 fulltime people and rely on several co-packers throughout the United States to service their national retail partners and consumer base.
“Once Upon a Farm has grown exponentially since our inception,” noted Mr. Blake. “In 2018, we expanded and reached more than 8,500 retail outlets at the time. We are now in over 16,000 retail operations and growing every day.”
Prior to purchasing the pair of SOMIC case packing systems, Once Upon a Farm’s co-packers used manual labor to handle the products. They currently use several workers on the assembly line for each shift, but the change to a faster and more consistent method began with a visit to a packaging trade show in late 2022.
“We heard about SOMIC and the 424 machine at PACK EXPO, and I had prior interaction with Stacy Schmeiser, their west coast sales manager,” recalled Blake about the preeminent packaging event which usually attracts over 50,000 professionals.
“We were impressed by the machine’s capabilities and knew there was an opportunity to streamline our production process. We considered two other companies,” said Blake, “but SOMIC was the clear winner because of its accuracy, capabilities with different boxes, and overall customer service. Stacy’s persistence and tactful style of communication is a large reason why SOMIC earned our business. He was patient, strategic, straightforward, and knew SOMIC would deliver what we needed.”
SOMIC Packaging CEO Peter Fox said having the ability to configure the 424 machine platform to Once Upon a Farm’s unique requirements made a huge difference.
“Everything we do is based on efficiency. Our machines are flexible and adaptable, and having options to provide a customer or plant with more operational flexibility is huge. From the space-saving compact design of the machine to the formats they run and the type of box they use, it all adds up and can have a powerful impact on the bottom line.”
Co-Packing Partner experiences Productivity improvements
The American Pasteurization Company (APC) in Milwaukee is one of the co-packers that runs the 424 W3 machines. Greg Zaja, APC’s vice president of Business Development, said they first heard of SOMIC through contacts in the food industry.
“The decision to invest in the machinery was ultimately made by Once Upon a Farm, and the functionality of the machine itself was key. SOMIC’s specifications were a good match for the production needs, and the responses from companies already using their equipment were all positive,” said Zaja, a 20-year veteran at APC.
He further explained there have been several advantages since the 424 W3 was installed last February.
“Our machine replaced quite a few extra sets of hands we needed to have on the assembly line. We also had to replace an older piece of equipment that we were getting by with, but wasn’t intended to handle the volume level we currently do,” he acknowledged. “The SOMIC case packer allows for greater throughput with a far reduced risk of human error.”
Each shift, Once Upon a Farm product is placed on the assembly conveyor belt by two or three workers who feed the compact, end-of-line packaging machine. An operator stands ready and monitors the line in the 44-degree production area, and another individual stacks each boxed finished product on a skid. The speed and reliability of the high performance machine, Zaja says, is boosting output and resulting in a positive, across-the-board outcome.
“Speed and downtime are always important consideration. Production efficiency, reducing delays – these issues are always at the forefront,” he admitted.
“The machine’s reliability and prompt service from SOMIC when there is an issue has minimized downtime, allowing us to maintain a consistent production schedule. Keeping costs in check helps us offer our customers the most competitive pricing in the industry. Reducing the risk of delays or cost overruns helps our customers meet all their objectives, which is our number one priority.”
Under the leadership of CEO Justin Segel, APC is doing brisk business in Milwaukee. The company employs approximately 300 people at a 200,000 square-foot plant located about seven miles west of downtown. Demand for Once Upon a Farm product was so strong by the end of August, the company added a third shift that runs at least five days a week.
Continues on next page.
"Box type, design and size, and labor reduction all played a part in the decision-making process.”
Douglas Blake, Once Upon a Farm’s senior manager of Co-Packer Engineering, explains why the SOMIC 424 W3 was the best choice.
Once Upon a Farm’s refrigerated pouches and frozen plant-rich meals are prepared at the APC facility in Milwaukee. Two very different products, Blake said only the spouted pouches are run on the SOMIC machine. Since they are processed with HPP technology, the combination of speed and efficiency is of the utmost importance.
“Our product has a short shelf life because we deliver a fresh, nutritious product to our consumers. Getting everything through the system quickly and safely is extremely important,” said Blake, who is happy with how everything has proceeded.
“SOMIC’s ability to run the type of box we wanted for our product was a key factor. Their team was more than willing to work with us to create a solution type that answered all our needs. They also had prior experience with chipboard in a size and similar thickness we were looking to implement,” he said, indicating the size varies from 3.2 to 4 ounces and the product is packed eight to a box.
“This gave us the confidence they would be able to execute the project successfully,” summed up Blake.
“The chipboard itself was critical to getting the cost reductions we needed to make the project viable. Box type, design and size, and labor reduction all played a part in the decision-making process.”
Throughout the years SOMIC Packaging and our parent corporation, SOMIC Verpackungsmaschinen GmbH & Co. KG in Germany, have been at the forefront of designing and manufacturing the most adaptable and sophisticated automated case packaging systems in the world.
To stay ahead of the global demand for the newest packaging developments to meet today’s business needs, we adopted our mantra of More, Better, Faster! for everything we do.
This mission statement is reflected in every capacity, from the original engineering design of a machine, through our world class customer and technical support and service.
So it is with great pride that we recognize our team in Minnesota for their achievement this summer;
they completed 365 consecutive days without one incident, with no accidents or lost time.
Congratulations everyone!
It speaks volumes to their dedication and efforts to work safely using the latest in cutting-edge technology and deliver innovative packaging solutions to our customers.
With the move to a new production facility that will increase our physical footprint to nearly 50,000 square-feet, for the first time we will soon begin the manufacturing of all new North American machines, including the 434 platform.
Adding these responsibilities to already conducting Fully Automated Testing serves as another challenge to working safely, one that our team looks forward to completing.
Five years ago in August 2019, SOMIC completed the acquisition of a small mechanical manufacturing company located in the Bavarian town of Haag in Oberbayern, Germany. All 35 employees were retained and continued working for the new company known as SOMIC Haag.
At the time, SOMIC Packaging CEO Peter Fox said the acquisition provided the company with additional machining capacity to support the company’s overall increasing volume of business throughout Europe, North America and other parts of the world. In the last five years, the DIN ISO 9001 certified division has manufactured precision parts for SOMIC machines.
Two important events implemented within the last two years are continuing to have wide reaching impacts on performance and productivity.
An investment was made in a new Hedelius CNC machine. It has made day-to-day work easier and resulted in significant improvements in the production of manufacturing parts. Delivery took eight months and it was operational after a two week installation period.
SOMIC Haag employees use the 5-axis machining center to expand the range of possible manufactured parts. All long profiles are machined completely in one clamping
operation. Complex parts are produced with the rotary table (C-axis) and the swiveling spindle axis (B-axis) in a single operation.
Effective utilization of the machine in two-shift operation was achieved after just a few months. The use of zero-point clamping systems enables a reduction in set-up times and flexible use of the entire work area.
With the use of new deburring tools and simultaneous processing, profiles no longer need to be laboriously deburred by hand. By saving the manual work step, it has reduced throughput times and improved quality because the machine does not miss any edges. Overall, it has made production work much more economical.
All aluminum profiles are now completely manufactured and deburred on this machine. Profiles and components that are shorter than 1200 mm have been produced with double clamping, which means even more unmanned machine running time and potential savings. Expectations regarding the possibilities of this machine have already been clearly exceeded.
Since the COVID-19 pandemic, manufacturing has become more sophisticated. Labor, supply chain and logistics issues all impacted the production landscape. Smart manufacturers began adopting the latest business process optimization strategies, and that’s how SOMIC Haag successfully introduced a Shop Floor Management (SFM) program in 2022.
In essence, SFM helps make things happen. It is comprised of processes, methods and systems to ensure the most efficient production possible, including all equipment, machines and inventory. The main components of SOMIC Haag’s SFM include:
• On-site leadership which involves employees
• Improved Communication from the bottom-up and top-down
• Visualization at the board with key figures
• Structured problem-solving Managers and production employees meet daily to carefully analyze the equipment, inventory, storage and manufacturing processes. They do so to identify any deviations in the value-added processes and initiate corrective countermeasures where necessary to keep operations moving forward.
The consistent assumption and implementation of leadership responsibility is one of the basic principles of a functioning SFM. The constant changes and process improvements require an understanding and a leadership system that supports employees in their daily work, recognizing the need for action and in setting priorities. Managers act as coaches in a learning environment.
“We started a pilot program with the first training courses on SMED (to minimize set-up times) and basic principles for the introduction of SFM,” recalls Alexander Gaier, director and initiator of the SFM project.
“After the expected initial difficulties, the Group manager and the director continued to develop the system. All employees now appreciate the daily, open and clear communication. The positive error culture helps to improve quality and implement our CIP (Continuous Improvement Process) and Kaizen measures. Our greatest success is the sustainability in delivery reliability. We were able to improve our machine hours by 18.5% compared
to two years ago. Productivity was increased by more than 11%, without worsening our complaint rate.”
“Shop Floor Management is one of the best communication and leadership tools par excellence,” noted Kai Lassig, head of technical who explained some of the benefits.
“It not only offers each individual employee the opportunity to participate in at least one meeting a day directly at the point of value creation, but also provides a cross-departmental exchange between managers at the value stream and management level. They communicate the information received, tasks and decisions back to the groups. This ensures constant communication of important information, escalation and decisions in the entire parts production process. Another important benefit is the sensitization of managers in the role of supervisor and decision-maker. This has resulted in an effective and positive leadership culture.”
Fabian Schmeisl, group manager for milling, said the SFM has significantly improved the general floor of information.
“In the employee meetings, I am repeatedly given positive feedback. We discuss our standard topics of man, machine, orders and information with the early and late shifts. In the beginning, we often needed 20-30 minutes. Now, everyone prepares accordingly and we are often through in five minutes.”
Tobias Schubert, head of mechanical installation, perfectly summarized the success of the program. “SFM is the tool that hits the nail on the head. Employees and the company benefit equally.”
“SFM not only offers each individual employee the opportunity to participate in at least one meeting a day directly at the point of value creation, but also provides a cross-departmental exchange between managers at the value stream and management level.”
8270 Courthouse Bvld.
Inver Grove Heights, MN 55077
1.651.419.6050
somic.us
Over the years, the SOMIC team has enjoyed the opportunity to bring our innovative equipment to PACK EXPO in Chicago. As leaders in Retail-Ready packaging, we’ve helped our customers stay ahead of new demands in the marketplace with highperformance equipment. The flexibility and adaptability keeps customers efficient and productive today, and future-ready for whatever comes tomorrow.