
5 minute read
Making Safety Proactive
Steps to Create Behavioral Safety Awareness on the Job
Don’t be an idiot.” It was a response that came when I asked a business owner of a specialized trade company if he had a safety manual. “Yes,” he said bluntly. “It’s one page and it says, ‘Don’t be an idiot.’”
On one hand, it was a remarkably simple edict — direct, easy to communicate, and not hard to understand. Unfortunately, as we know, it put the business totally out of compliance with federal and state law. All contractors — large and small — are required to have a safety manual and communicate its procedures and policies to all employees. It should also be stated that not being an “idiot,” while straightforward, is subjective and wide open to interpretation by the business owner, managers, and frontline workers. There’s a critical intersection where booksmart and street-smart meet on the jobsite.
Tucker Smith is an Area Manager for BBSI, a leading provider of organizational infrastructure solutions that bring peace of mind to specialized trade companies, including SEAA members. Reach him at Tucker.Smith@bbsi.com.
The company’s ability to serve as a crossing guard, so to speak, has a direct impact on its experience modifier rating used to help insurance carriers price workers’ compensation insurance. The key is more than having a detailed safety manual. It’s about addressing behaviors, and modifying them if needed, so employees have a more refined safety awareness.
Behavioral Safety is not Traditional Training
Behavioral Safety Awareness is a method of managing employee wellbeing by instituting a bottom-up approach that is actively supported by company management. It most often entails one-to-one and group feedback of employees performing routine work tasks, setting goals, monitoring progress, and often, rewarding safe behavior.
Critical to deepening one’s true understanding of behavioral safety awareness is to recognize that it is decidedly different than traditional safety training. The conventional approach to safety is reactionary and does not change the system; if a root cause analysis is conducted, the usual outcome is to blame the employee rather than reflect on the leading indicators that contributed to the incident. In contrast, behavioral safety focuses on influencing reactions to the environment by using scrutiny to assess job tasks, identify risky behaviors, and encourage safe ones.

Fortunately, creating a culture that values safety awareness isn’t as difficult as it sounds if there is honest buy-in from owners and senior management. One of the exercises we use with customers is a four-step ongoing improvement system called DO IT (Define, Observe, Intervene, Test).
Define
Define expected behavior by pinpointing problematic areas. The key here is to be precise about what people do and define the behaviors of employees, or the results produced by behaviors. You can get there by using an inter-rater reliability test in which two or more observers measure and record the event in complete agreement. Observations must be objective beliefs rather than subjective opinions, attitudes, or abstractions. For example, we might label someone as “lazy” because “they take too many breaks,” but the lack of specificity leaves “too many” open to interpretation.
In contrast, pinpointing would be, “They take eight breaks each shift which leads to a lack of consistent availability to co-workers to complete a task.”
The best way to define expected behaviors is to develop a checklist that can be used for performance feedback. Organize your checklist in way that makes it easy to define expectations as well as document observations and results.
• Group behaviors into like categories.
• Make items mutually exclusive of one another.
• Keep it brief.
• Include space to record observation notes.
Observe
Use the team to observe each other in situations where the target behavior is relevant.
Safe and at-risk behaviors are recorded and tracked daily, and the percentage of safe behaviors is calculated and charted each week. This becomes a form of coaching. For example, a supervisor observes the employee doing something unsafe. The best practice is to immediately stop, pull the employee aside, and review the checklist. A good way to begin would be, “I see that you’re working hard to complete the task but remember that ‘wet surface’ is on the checklist.” It’s respectful and clear, obviously designed to teach the employee how to avoid injury, help them practice safe behaviors, and conveys that the supervisor is observant.
Intervene
When observations indicate behavior is not improving (or not improving fast enough), management will need to develop an intervention to elicit change. Through group discussion, the situation should be analyzed to determine why at-risk behavior is occurring. The aim is not to find fault. Sometimes the factor motivating at-risk behavior can be removed or altered, or an activator or consequence can be added. It’s important to ensure feedback is specific, on time, appropriate, and sincere.
Test
Once intervention is implemented, management moves into the test phase to assess behavior changes. If a target behavior does not improve after several weeks, the situation is analyzed again, and another intervention strategy is developed and implemented.
Why Does This Matter?
A September 2022 survey conducted by Microsoft found that 87% of workers feel they are being productive while at work, but only 12% of leaders agree. That’s a remarkable 75-point spread. The primary reason for the disconnect? A lack of clear, easy-to-digest communication in which expectations are set and reviewed. Fortunately, filling the void isn’t difficult to achieve if you have genuine interest, the right leaders in place, and processes to follow. And given the high cost of injury (see sidebar), instilling the behaviors needed to get your employees home safely at night is not only culturally critical but financially savvy as well. So, as they say, just do it. •
How Much Does an Injury Really Cost?
The Experience Modification Rate (EMR) is a rating factor applied to workers’ compensation policies. It compares your claims against those with similar business operations and can have a great impact on the premium an employer pays. Companies can also be financially rewarded for having a good rating, but it goes beyond insurance costs, as an EMR may impact a company’s ability to bid on certain projects. Here is an overview of some direct and indirect costs associated with having an accident.
Direct Costs
Workers’ compensation insurance covers the cost of treating an injured employee, but the insured could see higher premiums for several years to come in addition to the following factors.
• Medical bills
• Lost-time wages
• Case management expenses
• Disability settlement
Indirect Costs
While not often considered, the man-hours lost when a worker gets injured can have significant ripple effect through the rest of the organization. Consider losing one employee on a 10-person crew.
• Lost productivity: You immediately lose 10% of your output.
• Overtime: The other nine must pick up the slack, and that usually means paying overtime.
• Training: If you find someone to fill in, the new person usually needs to be trained/mentored, and that slows everyone down.
• Hiring: If the injured worker is out for a while, you need to find and recruit new talent.
• Production delays: Unless things go flawlessly, a reduced crew usually results in a delayed delivery, impacting contract language, pricing, and renewals.
• Coworker morale: Seeing or knowing someone got hurt usually has an emotional effect on other employees, resulting in even more lost productivity.
• Incident investigation: Every incident should have a root cause analysis that yields corrective measures; serious incidents usually require state and federal paperwork as well.
• Administrative: To stay in compliance, there’s a sea of paperwork every step of the way.
• Legal: You may be exposed to a negligence liability lawsuit if the injured employee caused an accident and that accident caused damage to other parties.
• Damaged property: If property or equipment were damaged during the injury incident, you will likely have to pay.
• Damaged reputation: Others — customers, general contractors, etc. — almost always hear about injuries, which can cause a perception that you operate an unsafe place to work.
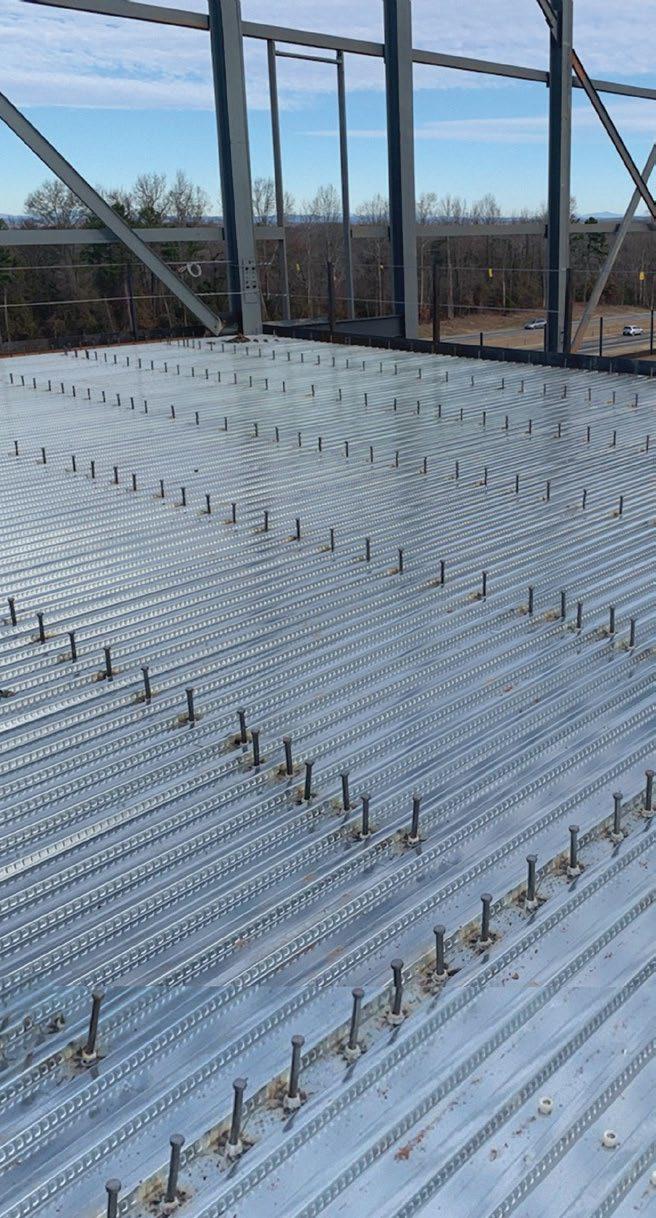
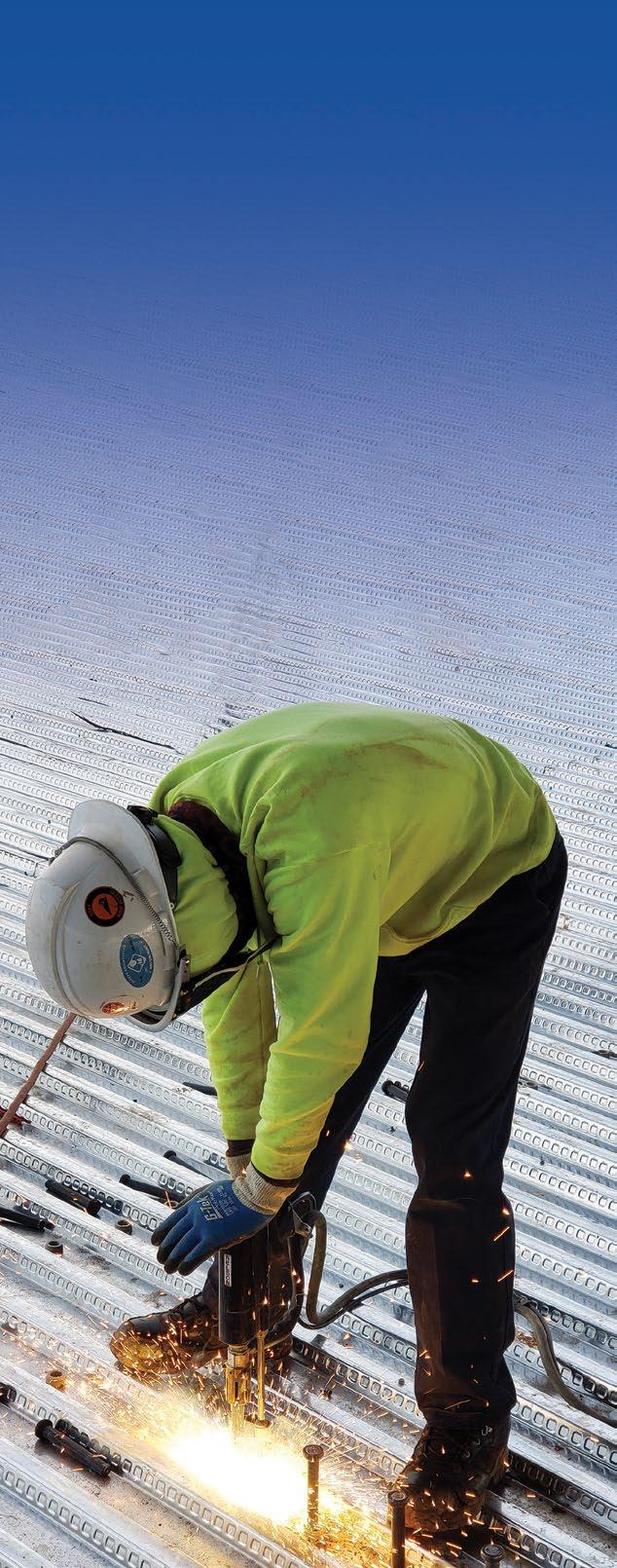