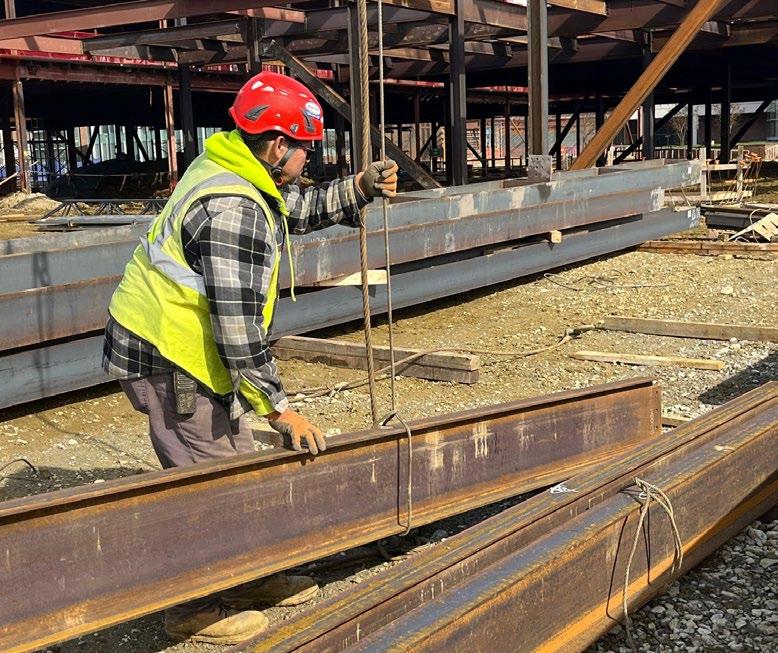
6 minute read
Every Sling, Every Lift
Sling inspection reminders for ironworkers
Rigging suppliers, steel erection operations directors, safety and training personnel agree. When it comes to sling inspections, ironworkers must stay vigilant for every lift, all day long.
Steel erection activities are highly repetitive, which means slings are used over and over again each day. “Users can’t rely on once-aday inspection. Because shock loads, severe angles, sharp edges, and excessive heat can quickly cause damage to a lifting sling, the user should inspect the sling prior to each lift,” says Nate Fisher, Account Manager for Mazzella Companies.
The goal of a sling inspection is to evaluate remaining strength in a previously used sling to determine its suitability for continued use.
“That means absolutely every time, prior to use, throughout the day,” said Mike Hurst, Erection Operations Manager for High Plains Steel Services, LLC, Windsor, Colo.
Wire rope is the most common type of sling used for lifting steel, followed by synthetic slings or chain slings. “The No. 1 most common slings in steel erection applications are wire rope used in a choker hitch configuration by riggers, because they can tighten and cinch down on themselves. Chain slings can also be used but aren’t preferred by ironworkers because they’re very heavy compared to equal size and equally rated wire rope slings,” said Fisher. In contrast, synthetic slings are lightweight but require the use of edge protection or to be rigged with other hardware.
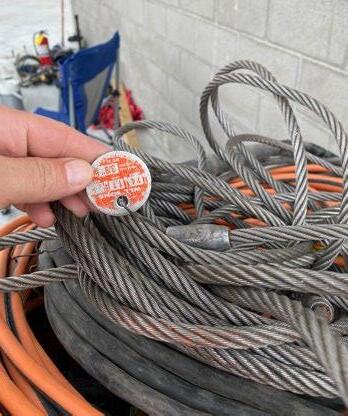
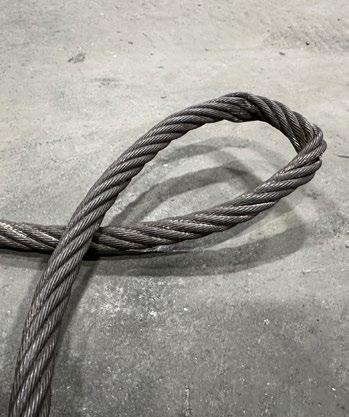

“There are times that chain slings may be utilized, but chains and wire mesh slings, do not hold their integrity in the application as well as wire rope or synthetic,” said Guy Callahan, Safety Director, GMF Steel Group, Lakeland, Fla.
The hitch configuration depends on the operation. In steel erection, the choker hitch is the most preferred style because it provides greater load control,” agreed Callahan. For long beams requiring more stability, often two slings are rigged in two-leg bridles. “But depending on the material being lifted, a basket hitch may become preferable given the size and dimensions of the material,” he said. Basket hitches are often used for low level lifts, such as unloading or shaking out material, but because they are less secure than a choker hitch, it’s important to have a plan to prevent the load from slipping from the rigging.
“We choke the iron when lifting. If we are unloading, we choke and basket, and sometimes we will straight pull columns if they are manufactured with a lifting eye on the top,” added Jonathan Mosebach, Safety Director, L.R. Willlson & Sons, Inc., Gambrills, Md.
“Small radii on structural steel shapes often contribute to damage of the sling. I-beams with sharp corners may cause damage as well,” said Sam Socolow, Director of Operations & Training, Ashley Sling, Inc., with locations in Georgia, North Carolina, Mississippi, and Tennessee.
What to Watch For
Warning signs vary depending on the type of sling being used and riggers must be trained to identify damage for each specific type.
“Normal wear and tear will affect all slings, no matter the type,” said Callahan. Damage can occur from improper usage, storage, or even improper selections for the application.
“When a sling is used that is not the correct choice for the lift, it allows for the sling to be pushed past its capacity and limitations,” said Callahan, who offers this brief list of common types of damage. In wire rope slings, frequent damage includes broken wires, distortion, kinks, doglegs, and arc strikes. Synthetic slings are susceptible to tears, cuts, and snags, abrasion, broken or worn stitching, and heat damage. And no matter the type of sling, missing or illegible identification tags is a problem requiring immediate removal from service.
It's a good idea to identify what is causing the damage. “If rigging is being damaged more often during a certain lifting operation, we evaluate to see if we need larger rigging, softeners, or a different lifting method,” said Mosebach. This is also a good time to revisit product options with your rigging supplier.
For example, Mazzella offers a patented 7-Part wire rope sling that is “more flexible and resistant to memory and permanent deformations in the wires and strands,” explains Fisher.
Preventing Damage
Slings are frequently abused. They are laid in the dirt, pulled out from under a load by the crane, used without softeners when lifting heavy loads, or straightened by an old-school choker straightener. “Improper storage, leaving slings out in the elements, over time will deteriorate the composition of the sling, no matter the type,” said Callahan. Regular cleaning and lubrication, if applicable to the type of sling, is a good best practice. To extend the life of slings, consider using rigging racks and storing them in a Conex trailer.
Softeners or edge protection are also a good idea. While often recommended for use with synthetic slings, don’t dismiss edge protection for other types. Mosebach of L.R. Willson is affiliated with a local fire service and so has access to old fire hose. “We always have this on hand to use as sling softeners,” he said.
“We offer a variety of sling protection products and sleeves that help with cutting and abrasion resistance. Lifting clamps are sometimes a good solution for helping with small radii,” said Socolow. The company’s TUFF-ASH product line includes products such as the Sling Armor sleeve made with Dyneema tubing. The sleeve is flexible and resistant to sharp edges and abrasion. Another option distributed by Ashley Sling is DICA’s LiftGuard Magnetic Sling Protector. Made from high-performance cast nylon, grooved sling protectors securely fit the flanges of an I-beam. Magnets allow for easy and secure placement.
When it comes to removing slings from service Callahan recommends: “When a sling is found to be damaged during the inspection process, it is best to remove it from service and tag it so that it is easily recognized as unsafe.” He also suggests reporting the damage to the supervisor or manager so that it can be further inspected. If necessary, the sling should be either destroyed in a manner that it cannot be used again or discarded properly, in accordance to the waste requirements.
“With no clear industry-wide rules on retiring or destroying damaged or failed slings, permanent disposal is typically left up to the owner or end-user,” said Fisher.
Ready to Inspect?
“A competent person shall perform a daily visual inspection of slings and all fastenings and attachments for damage, defects, or deformities,” cites Fisher. “The inspector should also make sure that the sling and hardware that was selected meets the specific job requirements it’s being used for,” he added. Employers should be familiar with OSHA’s definitions of “competent” and “qualified.”
“Our company does not allow anyone who is not a qualified rigger to rig. Technically a competent person could do the sling inspection with oversight of a master rigger,” said Mosebach.
Ultimately, it’s the responsibility of the employer to determine if an employee is competent, trained, or qualified to perform the job or task at hand,” said Fisher. There are a variety of resources available to train ironworkers for sling inspection. Both Ashley Sling and Mazzella offer training classes. Recently, SEAA partnered with Industrial Training International to launch the SteelPros Training Portal, where SEAA members have access to free and discounted online rigging inspection training courses. In addition, member companies seeking to integrate ironworker and rigger training and assessment as part of their business model, benefit from becoming SEAA/NCCER accredited and authorized. “Participation means your company can provide nationally recognized credentials to your employees. SEAA members can participate under NCCER’s sponsorship of SEAA, cutting your implementation costs and administrative requirements,” said Pete Gum, Executive Director of SEAA. •
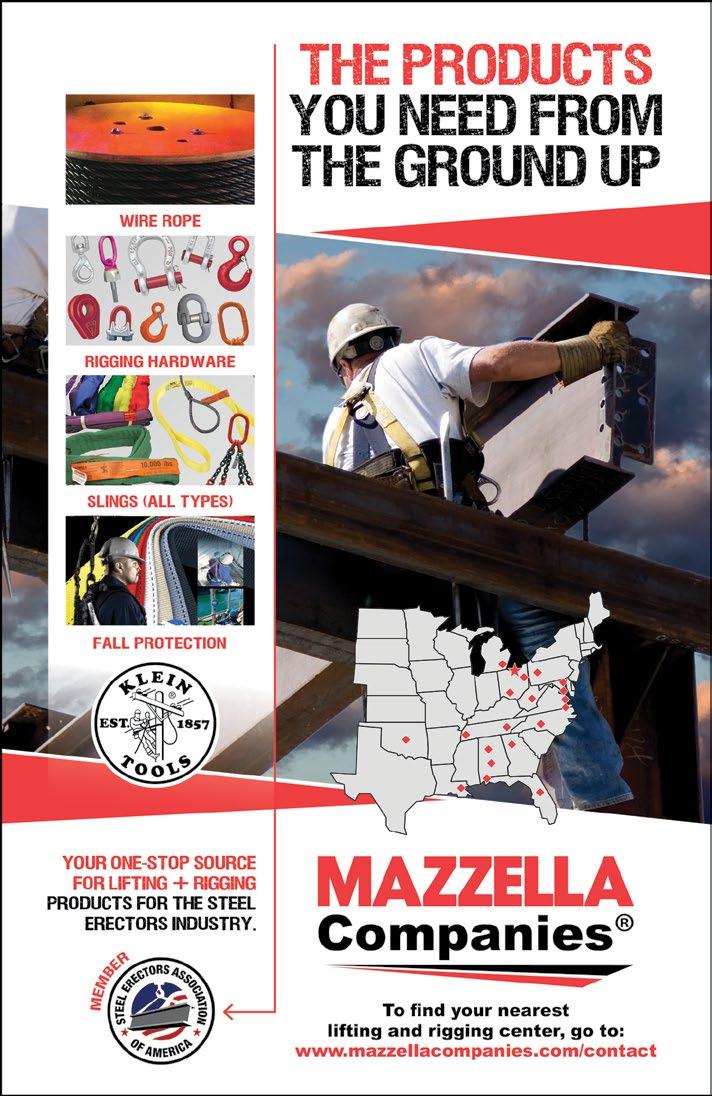
IRON WORKERS INTERNATIONAL SETS THE STANDARD HIGH WITH ACCREDITED RIGGER & SIGNAL PERSON CERTIFICATION
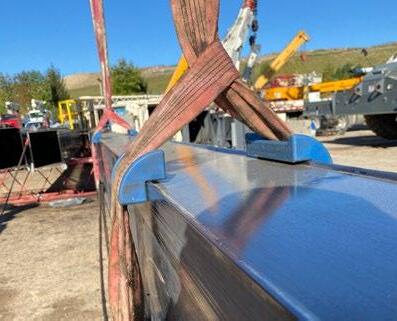
WHY IS IT IMPORTANT? WHAT IS IT?
Meet Requirements
OSHA’s Subpart CC requires signal person qualification by a third-party qualifier.
Meet Demand
While an OSHA letter of interpretation recognizes apprenticeship programs that train and assess riggers and signal persons as third-party qualified evaluators, many contractors, states and municipalities require a Qualified Rigger and Signal Person Certification.
Reduce Cost
Third party certification comes with a hefty price tag without input on testing from subject matter experts, ironworkers and their contractors. The Iron Workers’ certification eleminates the recertification cost of $500 per person.
Improve Safety
Ensuring that only trained, skilled and competent ironworkers complete rigging and signaling tasks elevates workplace safety standards and reduces risk.
Iron Workers International Certification Board’s (I.I.C.B.) Rigging & Signalperson Certification Program is accredited by the National Commission for Certifying Agencies (NCCA), the accrediting body of the Institute for Credentialing Excellence. The I.I.C.B. joins an elite group of more than 130 organizations representing over 315 programs that have obtained NCCA accreditation.
HOW IS IT DONE?
6,000 HOURS OF HANDS ON EXPERIENCE
3-PART EXAM
TESTING & RECERTIFICATION EVERY 5 YEARS
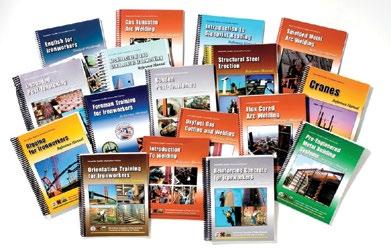
IRON WORKERS RIGGING & CRANE COURSE
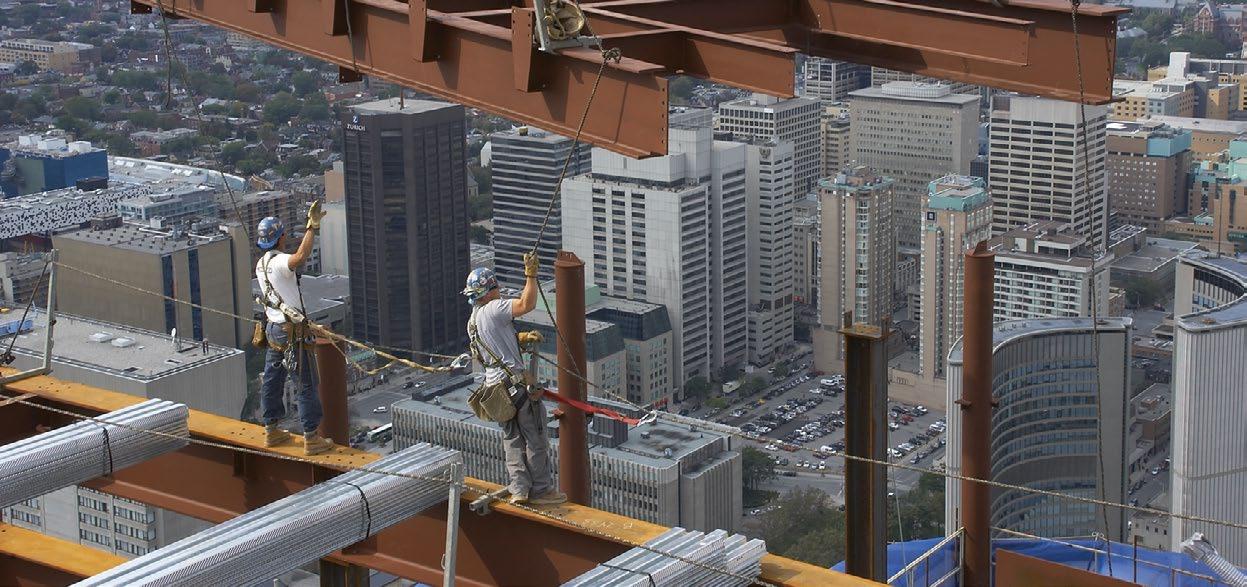