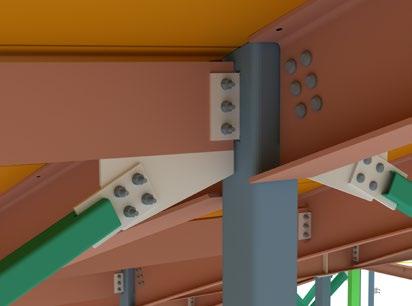
8 minute read
6 Technologies to Take You from Planning to Execution
Detailing Steel Connections
KMA Steel, a steel detailer in Iowa, and Jeffords Steel and Engineering, a steel fabricator in Pennsylvania, used SDS2 Detailing software for planning the steel connections for two winter sports facilities in Lake Placid, N.Y. The first was the Mt. Van Hoevenberg Mountain Pass Lodger. The three-story, mountainside structure encompasses the United States’ only indoor push-start facility for bobsled and skeleton sled competitions. The second was a reconstruction of an Olympic ski jump, now the only facility in North America equipped for both summer and winter training and competitions. The projects required dedicated teamwork, elite connection design, and breakneck speed. Here is how KMA and Jeffords Steel worked together before the 2022 Winter Olympics. SDS2 provides BIM software for steel projects, with solutions for detailing, fabrication, material handling, and site planning. Their flagship product for steel detailing comes with built-in connection design intelligence, providing automated connections with a
Lift Planning, Site Planning
360-degree analysis to ensure designs will hold up through fabrication and field fit-up.
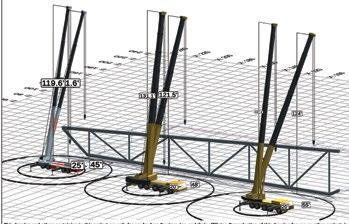
A key feature is SDS2 Cloud, which allows multiple users to do live modeling at the same time without fear of data conflicts or lag times. KMA has built its business around this versatile functionality, enabling them to assemble a dream team from around the country. On these projects the team included Brian Thompson, detailing manager, Josh Hawley, head detailer, and Sonny Schroeder, an owner of KMA and project manager— each working from different locations.
To accurately detail the irregular geometry and highly rated axial and compression loads of the steel connections, the detailing and fab teams worked closely with engineering. SDS2 automatically generates connection designs from most engineering calculations, and presents both the graphical and numerical calculations together.
“Jeffords Steel trusts the connections in SDS2 and tries to get the model to do as much as it can,” said Schroeder. Despite the extreme load requirements and irregular framing situations, KMA provided SDS2-generated calculations for around 95 percent of the connections on the lodge project. This was a huge time-saver for Jeffords Steel. Delays were not an option on the project. While construction was underway, high-profile Olympic competitions were already on the schedule. “The contractor and the state of New York were demanding steel on site while we were getting final design drawings,” said Jesse Ringer, Jeffords Steel’s president and connection engineer on the project. “KMA did a very good job of getting details and updated drawings and implementing those the same day or the next.”
Supply chain constraints, escalating materials costs, and labor shortages are just three factors influencing the adoption of new technologies by contractors. According to the 2023 Engineering & Construction Industry Outlook report by the Deloitte Research Center for Energy and Industrials, most companies in the construction market are utilizing digital technologies “to expand business opportunities and boost profits by reducing costs.”
The industry is just beginning to explore newer tech—like autonomous equipment, robotics, and simulation—and heavily relies on software for construction design, labor tracking, and project management. But even those applications are continuously evolving with expanding applications in construction.
Driving the adoption of new technology is funding managed by the Federal Highway Administration for two initiatives: Advanced Digital Construction Management Systems (ADCMS) and Technology and Innovation Deployment Program (TIDP). More than half of the Deloitte survey respondents agreed they would likely invest in digital technologies such as artificial intelligence (AI), and contractors are interested in combining digital tech with physical technology that has direct application on the jobsite. Examples include visual intelligence, sensors and Internet of Things (IoT) devices, robotics, immersive collaboration, and drones.
The goal is to increase efficiency, which is critical for meeting project demand while facing ongoing labor shortages. “Technology adoption and innovation could help attract employees with new skills and roles such as data scientists and retain workers by encouraging them to work with cutting-edge tools,” reported Deloitte.
“Our customers are going to be changing mentalities,” said William Nassauer, manager of product strategy for Komatsu America’s autonomous systems, mining technology solutions, in an article from the Association of Equipment Manufacturers.
“They’ve got to maintain their site in a different way, use workers in different ways and transition operators into supervisory roles. There’s a lot of learning involved.”
When evaluating new technologies for your company, Rossouw Nel, Product Marketer for software company ITONICS advises to first assess the costs and workload required to implement it. The expected benefits need to compensate for the costs.
He also acknowledges that new technologies come with risks, or the benefit may not be great enough to warrant the investment. Does the new technology give you a competitive advantage? You should also consider the likelihood of adoption by your employees, business partners, or customers.
The following short case studies represent just a few of the possibilities for applying technology from the planning stages to the execution of construction. These companies will exhibit at ConExpo-Con/Agg in March and/or at NASCC: The Steel Conference in April. It’s a chance to explore in person the latest technologies with applications in steel fabrication and steel construction.
Illinois steel erector Area Erectors, Inc. regularly uses A1A Software’s 3D Lift Plan for planning and executing lifting tasks on its projects. Last year, the company created more than 20 3D Lift Plans for their role on the Pritzker Military Archives Center in Somers, Wis. In all, the company used seven cranes to lift two 40 ft. x 250 ft. long trusses that made up the walls and two 40 ft. x 80 ft. cantilever trusses that became the entrance. Brent Genseke, Project Manager for Area Erectors, shares how their team used 3D Lift Plan from the start of the bidding process through the completion of the project.
“3D Lift Plan was a perfect tool for the job because it’s so versatile. During the bidding process 3D Lift Plan was necessary to convince the General Contractors that our plan to build structural pieces on the ground and then use multi-crane lifts to place, was safer and more efficient than erecting individual steel members,” he said.
“When presenting a plan of this nature it’s much easier to follow when you have that visual support. In the end, the Lift Plan document for lifting one of the trusses was 56 pages long,” he said.
Once the wall trusses were tied into the core of the structure and detailed, it was then time to erect the cantilever trusses to create the entrance. During this phase, space constraints presented a challenge for crane placement. “With 3D Lift Plan we could easily show contractors the best placement for the cranes in order to maximize available space on the ground,” said Genseke. “We were able to provide detailed printouts that showed dimensions, crane assembly areas, and crane mats for the machines,” he said.
Area Erectors also utilized 3D Lift Plan to complete smaller scopes of work to show how those lifts would impact other trades working in a tight area. And, in the final phase Genseke was able to reduce time and eliminate the need for crane access roads when placing bridge structures. Instead, he proposed a plan that would mobilize and demobilize a 550t Liebherr LTM1450 in a shorter time frame than it would have taken to build the crane roads, tear them out when finished, and rework the site to get the final desired result.
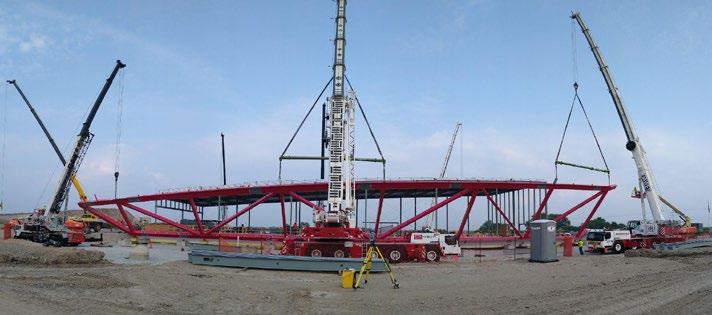
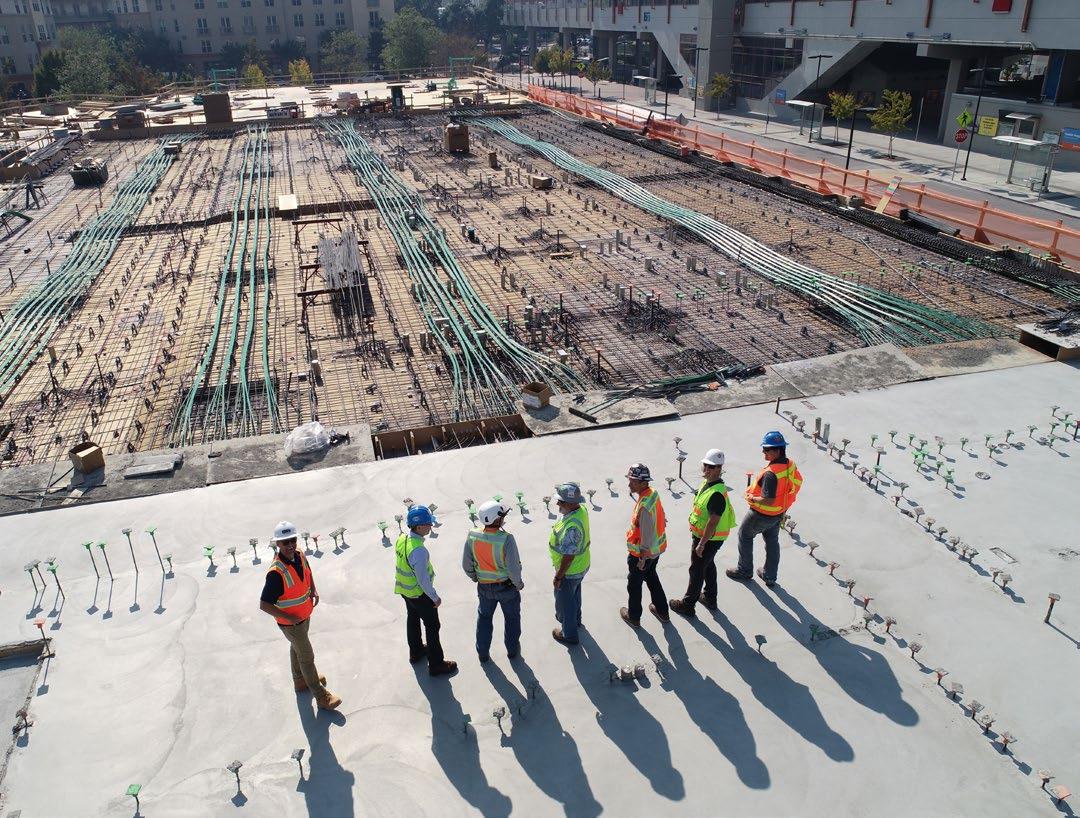
Equipment Operator Training
Steel erectors often employ their own crane operators for lifting during construction. This includes using RT and AT mobile cranes, crawler cranes, and even tower cranes. “Contractors must address ongoing training, recruitment, and various levels of operator experience. They also are dealing with inclement weather, multi-site management, and remote locations. Crane simulators can be used to address these factors as well as ongoing recertification, recruitment assessment, employee benchmarking, maintaining skills, and working on advanced training,” said Alan Limoges, CM Labs product manager.
CM Labs Simulations features Smart Training Technology in its crane simulators, which accurately replicates machine stability—providing real-world training opportunities. The simulated machine behavior helps operators gain a better feel for controls, throttle, inertia, boom flex, and other real-world scenarios that affect cycle times or precision placement.
Lifting steel structures is just one of many training exercises built into CM Labs Simulations crane training models. The exercises are designed to help the operator practice techniques for handling long loads, including beams, columns, joists, and sheet bundles. Among the techniques the operator must master is efficient lifting, tilting up and positioning steel beams. Other skills that can be practiced include:
• Maintaining a vertical hoist line while tilting up the load by hoisting and swinging at the same time. Operators can observe the pendulum swing of the load when they do not use proper lifting techniques.
• Placing beams in challenging positions with precision and avoiding any collision.
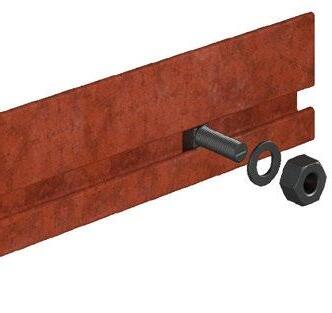
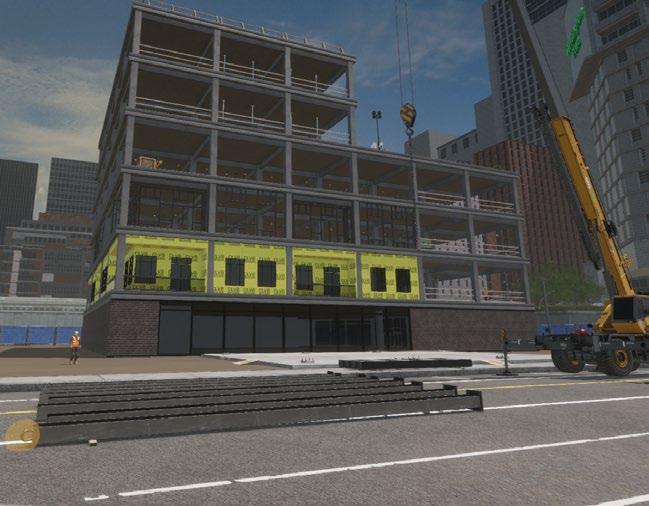
“Today’s simulators are data- and analytics-driven. This means that training techniques can target specific skills deficiencies for cross-training or advanced skill development. In addition, simulators can present trainees with a variety of increasingly challenging scenarios and conditions (lighting, terrain, weather, exercises) that are not always practical or possible with traditional training methods,” said Limoges. They can also be used for advanced crew training exercises for team learning. This might include a scenario with multiple crane operators for tandem lifts, or signal person and crane operator communications. For example, the International Union of Operating Engineers Local 14 in New York City successfully implemented CM Labs’ Vortex simulator to replicate a complex procedure for erecting and laying down a 300-foot boom or luffing jib in order to provide training that is not practical without a simulator. According to their training director: “Experiencing the controls, forces, inertia, twisting, and movement of a crane, are critical to understanding the reaction differences between a 200-foot and 300foot boom.”
Job Cost Accounting, Project Management and Payroll
Deltek ComputerEase is the leading construction software provider of job cost accounting, project management and payroll services. The construction-specific solution keeps everything in one location, reducing the use of multiple spreadsheets and the number of human error inputs while also allowing companies to manage their paperless journey through crucial aspects of the business.
Bridge rebar contractor Shelby Erectors has been using Deltek ComputerEase for more than 15 years to track labor hours through the Time Entry app, distribute payroll stubs and W-2s digitally through the EmployeeHub, and manage and track daily credit card expenses with ExpenseEase. They also are able to give their superintendents additional oversight with payroll balancing and project management through FieldEase.
“Deltek ComputerEase makes our work much more efficient. You can do more with less people. It also helps us stay in tune with where the jobs are and really helps us manage our business—it gives us a full view of everything,” said Jack Nix, COO of Shelby Erectors. Ultimately, the software helped Shelby Erectors accomplish its goal of becoming a paperless company.
Deltek ComputerEase also helps companies manage the growth of their business. Rizzo Brothers, a commercial painting contractor, transitioned to cloud services and modernized their company to improve efficiencies and access to information. They went from printing and scanning every document, losing invoices, and having stacks and stacks of folders and papers to creating a paperless culture. Routine tasks were automated. Ultimately, Deltek ComputerEase helped Rizzo Brothers break down silos and improve communication, creating a positive change throughout the organization as a whole.
Contractors choose Deltek ComputerEase because it helps them stay in control from any location, offering affordable tools for managing jobs, inventory, finances, and people. In addition, access to executive dashboards, WIP reporting, drag & drop workflows, and permission-based logic—customizable for each employee— helps contractors proactively plan project profitability.