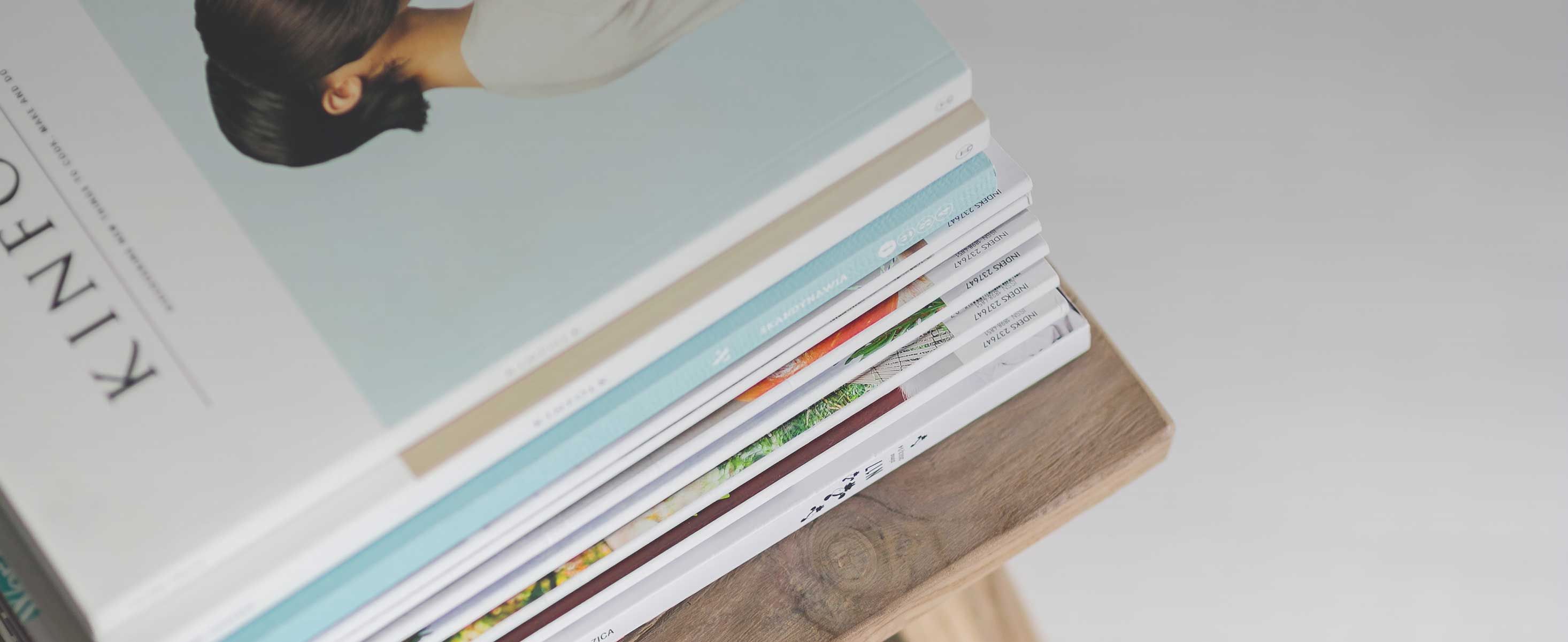
5 minute read
Chapter 5 COST-EFFECTIVE TECHNOLOGIES FOR COMMON MAN
from A Study of Cost-effective Building Materials and construction techniques for warm and humid climate
Chapter 5 Cost-Effective Technologies for the common man
Any house is made up of two parts: the foundation, or substructure, and the superstructure. The superstructure is divided into four sections: walling, roofing/flooring, finishing, and doors and windows. Our collection includes sections on numerous housing solutions. We are combining traditional, vernacular, and alternative systems. The alternative solutions shown here are not only costeffective, but also energy-efficient, environmentally friendly, and in harmony with nature. They also assist in the establishment of medium to small businesses that rely on locally available materials. (B.M.T.P.C., 2015) -Foundation -Walling -Roofing/ Intermediate Floors -Others
Advertisement
5.1 Arch foundation
This foundation was employed in the past when the spread foundation was replaced with an inverted arch. It can cut building costs by up to 40%. The benefit of this is that the depth of the foundation may be substantially lowered in soft soils; the downside is that the end piers must be carefully fortified by buttresses to avoid the push to arch action tending to tear the piers connection. (B.M.T.P.C., 2015)
5.2 Plinth
It is recommended that the plinth be 1 foot above ground level and built with a cement mortar of 1:6. The usual plinth slab of 4 to 6′′ can be eliminated, and in its stead, brick on edge can be utilized to save money. The cost of plinth foundation may be decreased by 35 to 50 percent by using this approach. (B.M.T.P.C., 2015)
5.3 Brickwork
Bricks made from black cotton and poor soil stabilized with fly ash were used in a 1:6 cement mortar. Rat-trap bond brickwork in a cement lime mortar/1:1.5:3 cement sand mortar ratio of 1:2:12. Masonry is made of hollow concrete blocks and cement mortar. Masonry is made of compressed mud bricks in mud mortar. Stabilized mud bricks in stabilized mud mortar (4 percent cement or lime). Sand lime brick walls with a cement mortar ratio of 1:6. Sand block FAL-G with cement mortar 1:6.(B.M.T.P.C., 2015) The bond is the manner in which bricks overlap when being laid. The rat-trap bond
is constructed by laying bricks on their sides with a cavity of 4 (100 mm) and an alternate course of stretchers and headers. To increase the strength of the walls, the headers and stretchers are staggered in consecutive levels. (B.M.T.P.C., 2015)
5.4 Rat Trap bonding
This method saves around 25% of the entire cost of a typical 9" constructed structure. With the help of brick columns, the construction has shown to be strong enough to hold three levels. This approach decreases the cost of the wall by 25% since a standard English bond (9"thick wall) requires 350 bricks per cu. m, but the Rat-trap bond only requires 280 bricks, and the reduced number of joints reduces mortar consumption.(B.M.T.P.C., 2015)
5.5.Soil cement block technology
This strategy saves around 25% of the total cost of a building "The typical 9" construction was built. The building has proven to be sturdy enough to support three stories thanks to the use of brick columns. Since standard English is used, this method reduces the cost of the wall by 25% "Bond (9"thick wall) takes 350 bricks per cu. m, but the Rat-trap bond requires only 280 bricks, and the fewer joints minimize mortar usage. (B.M.T.P.C., 2015)
5.6.Concrete block walling
Given the high energy consumption of burnt brick, it is advised that a concrete block (block hollow and solid) be used instead, which uses around one-third the energy of burnt brick in its manufacture. Concrete block masonry reduces mortar consumption, allows for faster wall building, results in greater worker productivity, and eliminates the need for plastering, resulting in an overall savings of 10 to 25%.(B.M.T.P.C., 2015)
5.7.Domes and vaults
Using suitable mortar in brick or stabilized mud block Upgraded thatch roof on the suitable structure. RCC "L" panel precast M15 concrete precast RCC cored units M15 concrete precast RCC channel units Precast M15 concrete waffle units Vaultstyle burnt clay tube roofing. (B.M.T.P.C., 2015)
5.8 Filler slabs
M15 concrete precast RCC boards and joists. RCC joists and brick panels that were partially prefabricated RCC in a hollow concrete block that has been partially prefabricated. Thin ribbed RCC slabs Channels for Ferro cement On the outer beam is a brick funicular shell. Concrete with bamboo reinforcement RCC edge
beams on brick funicular shells RCC joists is supported by brick jack arches. M15 concrete precast RCC cored units M15 concrete precast RCC channel units. Cost reductions ranging from 15% to 25% are possible. However, the spacing between the reinforcing bars in a filler slab must be determined by a structural engineer. Insulation against heat The air pocket created by the tile shapes serves as an efficient thermal insulation layer. A filler slab's design integrity requires careful planning that takes into consideration the negative zones and reinforcing regions. (B.M.T.P.C., 2015)
5.9 Open prefab systems Based on an acceptable production level and tiny, easily handled pieces with rationalized production techniques, housing experts have identified this as a key solution for halting the fast-growing escalation in material and labor costs. Building Centers in various parts of India have played an important role in spreading several of these prefabricated solutions at the grassroots level. Partial prefabrication can be used for almost any feature of a structure, including foundations, walling systems, doors and windows, roofing systems, lintels, and staircase parts. Roof costs being one of the key components of any building project's construction expenditure, one of the focus areas has been the prefabrication of roofing elements. (B.M.T.P.C., 2015)
5.10 GFRG Panel Building System
GFRG is especially important in India, where there is a pressing demand for costeffective building technology. The product is both environmentally friendly and fireresistant. Rapid wall and gypcrete are other names for GFRG panel systems. Used in load-bearing and non-load-bearing structures alike. Having modular cavities that may be used for both interior and exterior walls. RCC may also be utilized for roof and floor slabs. Advantages include a 50% decrease in dead load, an increase in carpet area, a 15%–20% reduction in building costs, resistance to corrosion and termites, material savings, and a reduction in CO2 emissions. The disadvantage is that in low seismic zones, only 10 stories may be constructed. (Cherian et al., 2017)