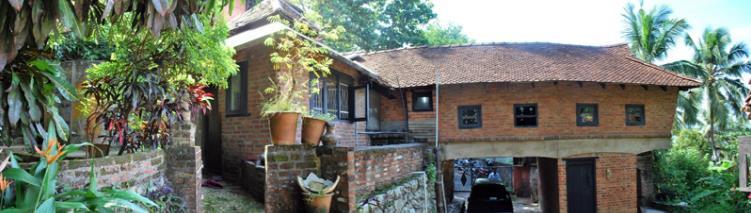
4 minute read
Chapter 6 CASE STUDY AND ANALYSIS
from A Study of Cost-effective Building Materials and construction techniques for warm and humid climate
Chapter 6 Case Study
The analysis is done by finding solutions to the cost-effective problems through case studies of projects carried out successfully by prominent architects and new construction techniques in metropolitan cities. In these case studies, emphasis has been put on the materials and techniques implied to make the building costeffective and affordable to the lower-income group. Both the case studies are taken in the region according to the climate-specific (warm and Humid climate)
Advertisement
Parameters for selecting the case study include the materials and techniques that should qualify the criteria of selection of building materials for cost-effective construction i.e Pollution prevention, Reducing Energy Consumption, Local material, non-toxic building materials, Longevity, durability, and maintenance of building material.
6.1 Case study based on vernacular materials and techniques - HAMLET (by Laurie Baker) Trivandrum
Fig 3 Bakers house (Tewari, S., 2015) Location: Trivandrum Architect: Laurie Baker Built-up Area: 3972 sqft Project type: Residence The way an architect designs his own home reflects his own nature. It embodies his personality, ideals, and architectural beliefs. The construction process exemplifies Baker's above-mentioned phrase, which emphasizes the traditional and Cumulus Mumbai 2015 5 natural approaches to habitation and development. The Hamlet - Bakers' Residence (Fig. 3) in Trivandrum is a live example of Baker's ideology. The home grew organically over time, from a multifunctional one-room hut to the initial construction on the summit and later expansions that followed the
slope downhill. The architectural shape allows for flexible linkages and access to each room. Over time, the majority of the construction materials came from unusual sources. Fish tiles from a castle, dormers and roofing timber from a ruined home, wood from a jetty, and fragments of stone or tile he picked up all complement one other (Tewari, S., 2015). The building shape appears to have grown from the earth.
Analysis:
Materials Used: mostly local and reused materials were used. Timber, Mud bricks, reused timber, reused metal pieces for grills, reused bottles which were inserted in walls to give stained glass effect, wall decorations from waste materials like pens, broken pottery, glass, roofs made of Mangalore tiles.
Construction Techniques Used for cost-effectiveness:
-Conservation of Resources and Energy, in Turn, Reducing the Cost -Using corbelling instead of a lintel above the frame reduces the cost of RCC lintel. -Using Rat-trap bonds less number of bricks to make a wall of the same thickness and provides cavities in between for insulation. -Use of Jaalis for ventilation lead to enough light, less material requirement. -Inbuilt furniture creates a permanent structure that is more durable than the Conventional furniture.
Fig 4 depicting materials (Tewari, S., 2015)
-Filler slabs to reduce reinforcement. - Curved walls instead of squares or rectangles. -Sewage materials, door, window frames.
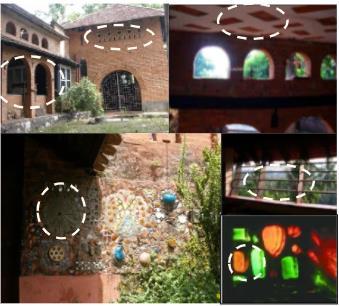
6.2 Case Study based on Modern materials and techniques - GFRG Demonstration Building, IIT Madras, Chennai
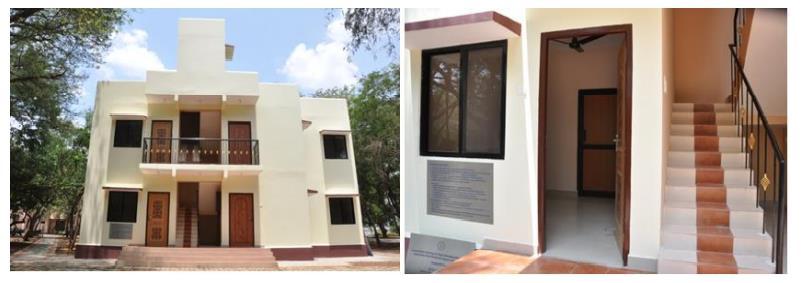
Fig 5 GFRG Demonstration Building (T E R I., 2014)
Location: Chennai Architect: Civil engineering department IITMadras Buil up Area: 1981 sqft Project type: Demo building This project comprises a single two-story structure developed on the campus of IIT Madras by the civil engineering department.IIT Madras researchers developed a design and construction method that makes use of Glass Fiber Reinforced Gypsum (GFRG) panels, with R&D assistance from India's Department of Science and Technology (DST) and industry support from Australia's Rapid wall building systems. The IIT-Madras research team extended the product's use to the entire building system – including floors, roofs, and staircases – significantly lowering the consumption of reinforced cement concrete (RCC). The team also collaborated on the creation of a good waterproofing material in-house, which is crucial for the longterm lifespan of GFRG panels, notably on roofs and toilets. The property has a total built-up area of 1981sft, which includes two EWS apartments (269 sft) and two LIG flats (497sft). (T E R I., 2014) Key features include the ability to create at a faster rate. The twostory prototype building with four units was constructed in two months. Fig 6 GFRG Panel (T E R I., 2014)
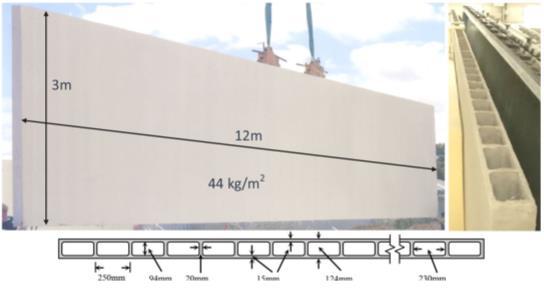
The GFRG panels substantially minimize the consumption of RCC, water, cement, steel, and sand, lowering the building's energy and carbon footprint. This material savings translates into decreased building costs. Because GFRG is a lightweight material, it adds to foundation cost savings. Load bearing systems may be used to construct 8-10 story structures without the need for beams and columns. The demo building is aimed at low-income and low-income households. This project's cost per square foot was only INR 1250.
Analysis
-Rapid construction: In one month, GFRG produced a demo building with four flats on two levels (total 1981 sq.ft.). -Wall panels are just 124mm thick, requiring less built-up space per carpet area. -Lower embodied energy and carbon footprint: significant reduction in Use of cement, sand, steel, and water;
Gypsum recycling from industrial trash Fig 7 GFRG Panel construction (T E R I., 2014) -Lower construction costs: material savings; no plastering. -Decreased building weight (panels weigh only 43 kg/m2), which helps to foundation savings and reduced earthquake design, especially in multi-story construction. -This load-bearing technology may be used to create buildings up to 8-10 stories tall, eliminating the requirement for beams and columns. -Excellent prefabricated GFRG panel finishes were used for all walls, floors, and staircases, with minimum embedded concrete: no further plastering was necessary. -Reduce the use of rich agricultural land and energy-intensive burned clay bricks. -It is concluded that GFRG buildings are more durable than similar conventional buildings, as the concrete and steel are encased by the GFRG shell.
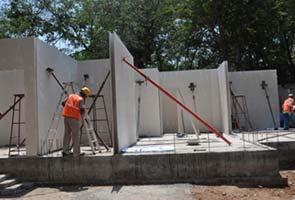