Selfbuild
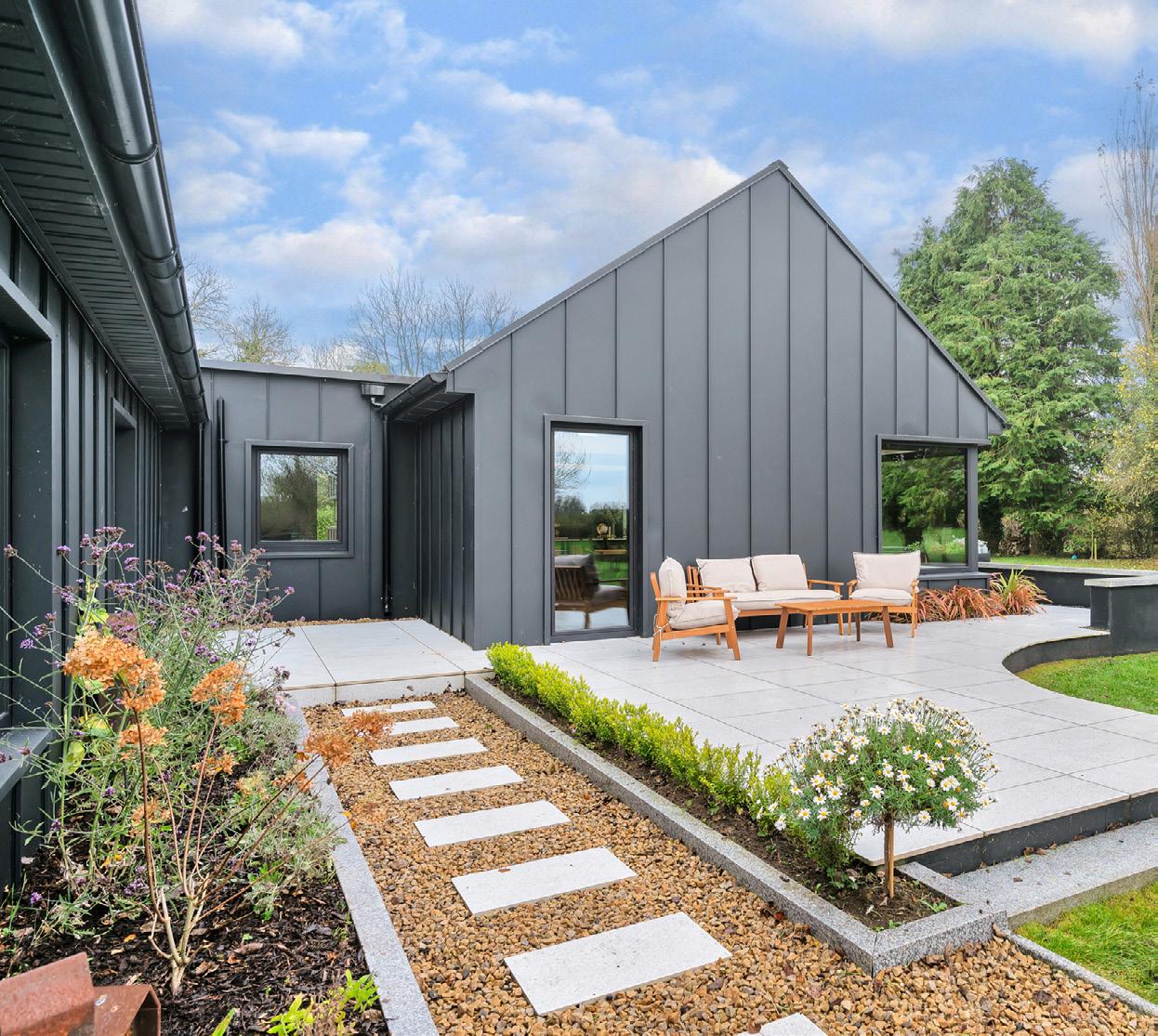

What’s included in your Selfbuild+ subscription?
- Build Cost Calculators
- House Plans Library
- Regular news updates
- Selfbuild Journey Guide
- Fully detailed Irish projects
- Advice pages
- Videos & Podcasts
- Inspiration galleries
- Quarterly magazine – exclusive to Selfbuild+ subscribers
- Plus… exclusive subscriber benefits
Europe’s leading, award-winning window brand for over 90 years. Innovative, high-performance architectural window and door systems for self-build, renovation and Passivhaus projects. Outstanding quality, bespoke design, and exceptional thermal performance. For further information, please visit uk.internorm.com.
Roadstone FlowPlus is the next generation self-levelling cementitious screed developed in conjunction with the ARDEX Group.
Roadstone FlowPlus is the next generation self-levelling cementitious screed developed in conjunction with the ARDEX Group.
• Provides a quick, smooth and level surface with minimal leveling
• Ease and speed of installation
• Provides a quick, smooth and level surface with minimal leveling
• Suitable for all domestic and commercial applications
• Ease and speed of installation
• Suitable for all domestic and commercial applications
“...the case for self-building when compared to buying an existing house remains strong.”
Despite the persistently high cost of building, for both labour and materials, the case for self-building when compared to buying an existing house remains strong.
To give you a full picture of where costs are at now, we have Keith Kelliher debating where material prices are heading on page 80 and a round up of what the experts had to say at Selfbuild Extend & Renovate Live about how much it costs to build a house in Ireland today on page 79.
Build costs tend to be quoted in per sqm or sqft but the reality is, your own house won’t hit whatever magic figure is bandied about. Cost experts are all at pains to warn self-builders that your house is bespoke, meaning sqm costs are little use to you - it’s not just the finishes you choose (the kitchen alone will have a big impact on final costings), but where you’re building and the availability of labour that can inflate costs very quickly.
Back to our comparison between building your own home or buying a house, and by now we’re all aware that we’re well past Celtic Tiger prices for homes.
Yes, that does ring alarm bells. Especially with potential trade wars on the horizon. But the reality is there’s a big shortfall in housing, and that’s propping up the market.
The latest leaked reports show ROI is currently short approximately 250,000 homes to meet market demand, a shortfall that’s expected
to grow by around 20,000 per year between 2025 and 2040 (see page 9).
Building your own home is a great way around this problem, if land is available (and despite what you might think, you don’t always have to inherit land either, see project page 26) and planning isn’t an issue (see project page 36 for how a set of homeowners got around planning hurdles).
But a home renovation project could equally be the solution; and pondering the pros and cons of each option is regular contributor Les O’Donnell on page 82.
This issue, we also look at green roofs (brace yourself for how much they cost from page 84), the very unsexy yet important topic of hot water systems and ensuring the pipe runs are kept short (page 87), the benefits of hiring an architect (page 89) and plenty of projects including my own bathroom reno (page 70).
Plus, the Selfbuild Journey pages have finally moved on to building the house, up to the point of being weathertight. It starts page 89.
Cosy up to a cuppa and enjoy!
Astrid
Madsen - Editor astrid.madsen@selfbuild.ie
The first stage of being On Site deals with getting your home weathertight, meaning the floors, walls, roof, and windows and doors are in. And so are the initial groundworks.
If you have a question, want to share some insights, or simply let us know how you’re getting on with your project, we’d love to hear from you for our Letters page. Email us at letters@selfbuild.ie 78
26 House of mighty oaks
How Laura and Peter Dillon found the perfect site to build their dream family home in Co Westmeath.
36 It’s a marathon, not a sprint
Niall and Rachel McAlinden had some planning hoops to jump through to build their home in Co Tyrone.
46 The cottage that grew with us
Darren Delahan explains how he built his extension out of Insulating Concrete Formwork (ICF) in Co Kildare.
56 Space reimagined
Emily and Matthew Morgan renovated their home in Co Down to completely transform their way of life.
64 Striving for perfection
Architectural designer Mark Davies relates how he went
about renovating his home in Co Dublin.
70 A slow start
Magazine editor Astrid Madsen relates how she’s getting on with her bathroom renovation project in Co Laois.
72 Rocky site for Co Galway garden
Anne Byrne shares her garden plans for a family home that has a large plot of land, and rocky site conditions.
09 News
Get up to date with the latest in home building and home improving, in both NI and ROI.
23 Company news
The latest products and services to hit the Irish market.
78 Letters
Build costs, the pros and cons of batteries, and more.
80 Cost of materials
Quantity surveyor Keith Kelliher brings us up to speed on the cost of building materials.
82 Build new or renovate?
Engineer and architectural designer Les O’Donnell weighs the pros and cons.
84 Green roofs
What it takes to build a garden in the sky. Hint: plenty of dosh.
87 Design tips for hot water systems
One of the biggest energy sappers, and contributors to overheating, is the humble pipe that leads from the tap to your hot water system. Here are ways to minimise losses.
88 Should you hire an architect?
The savings to be made, whether you do hire one or don’t.
90 Overview
An introduction to the first part of Stage 5 of your Selfbuild Journey: On site up to the point of being weathertight.
92 Construction timeline
An overview of the entire process, from start to finish.
95 Floor construction watchpoints
What to look out for when building your foundations, footings, subfloors and pouring your screeds.
98 Wall construction watchpoints
Top tips for making sure it’s built to spec.
102 Roof construction watchpoints
Common mistakes to avoid.
106 Project management tips
Louis Gunnigan explains how he went about managing the trades on his ICF build in Co Dublin.
108 Passive build tips
Patrick McMullen of Co Tyrone shares how he got to the point of being weathertight, with a special focus on insulation and airtightness.
114 DIY painting guide
Tips and tricks to get the perfect finish.
CONTACT info@selfbuild.ie
EDITOR
Astrid Madsen astrid.madsen@selfbuild.ie
DEPUTY EDITOR
Heather Campbell heather.campbell@selfbuild.ie
DESIGN
Myles McCann myles.mccann@selfbuild.ie
Shannon Quinn shannon.quinn@selfbuild.ie
Megan Buckley megan.buckley@selfbuild.ie
MARKETING Calum Lennon calum.lennon@selfbuild.ie
Victoria Hunter victoria.hunter@selfbuild.ie
Rebecca Ferris rebecca.ferris@selfbuild.ie
Erin Mason erin.mason@selfbuild.ie
SUBSCRIPTIONS
Becca Haslett becca.haslett@selfbuild.ie
ADVERTISING SALES
Emma Phillips emma.phillips@selfbuild.ie
Joanna McConvey joanna.mcconvey@selfbuild.ie
Lisa Killen lisa.killen@selfbuild.ie
Maria Toland maria.toland@selfbuild.ie
Nicola Delacour-Dunne nicola.delacour@selfbuild.ie
ACCOUNTS
Karen McLeigh karen.mcleigh@selfbuild.ie
Leanne Rodgers leanne.rodgers@selfbuild.ie
SALES DIRECTOR
Mark Duffin mark.duffin@selfbuild.ie
MANAGING DIRECTOR
Brian Corry brian.corry@selfbuild.ie
CHAIRMAN Clive Corry clive.corry@selfbuild.ie
DISTRIBUTION
EM News Distribution Ltd
Delivering windows and doors that are crafted to last generations.
Redefining quality and luxury for almost a century. Our windows and doors are not just built to last, but crafted to inspire.
For more information visit nordan.ie
NorDan’s Timber/Alu-Clad Windows combine the classic warmth and beauty of timber on the inside with a tough weather-resistant aluminium cladding on the outside.
Merging timeless elegance and enduring strength, NorDan’s Timber/Alu-Clad Doors are perfect for those seeking stylish yet practical modern living solutions.
The ideal solution for modern homes and commercial properties, offering a huge range of design possibilities, enhanced energy efficiency, and premium performance.
The perfect solution for the contemporary needs of residential and commercial properties that highlight energy efficiency, low maintenance, and versatile design options.
NorDan’s Entrance Doors have been designed with durability and energy efficiency at the core. With contemporary and traditional designs available, there is a perfect match available for your perfect welcome home.
Community rallies to help young Tipperary family complete their home after a life-altering diagnosis.
Afundraiser to help Declan O’Halloran (39) and his family complete their Tipperary self-build after a life-changing diagnosis has raised over €192,000 in just under six months.
Like many young Irish adults, Declan moved to Australia in 2008, where he met his wife, Joanne Kenneally, from Middleton, Co Cork. They got married in 2017 and have two children, Ava (3) and
Levi (3). Together, they always planned to return home to Ireland to live in Declan’s home village of Newcastle, Co Tipperary. In 2021, shortly after the birth of their son Levi, Declan began experiencing troubling symptoms that were initially suspected to be Multiple Sclerosis (MS). Despite his declining health, he and Joanne, a nurse, pressed ahead with their plans to move back to Ireland, secure planning permission and build their family home. But after their return in 2022, Declan’s symptoms worsened.
Eventually, in May 2024, he was diagnosed with Multiple System Atrophy (MSA), a rare and progressive neurological condition that affects movement, balance, speech and other bodily functions. There is
currently no cure, and the life expectancy is typically around 10 years from the onset of symptoms.
As a construction supervisor, Declan initially took on the self-build project with their savings and support from family, but the rapid progression of his illness has made it impossible for him to continue working. With no mortgage available due to his health status and costs rising, the family is facing an uphill battle to complete their home.
Friends and family launched a GoFundMe campaign to help Declan and Joanne finish building their house, with plans to adapt it for Declan’s future care. Time is critical, as they are currently renting accommodation that is no longer suitable for his needs. With support from the community, the family hopes to complete the project and create a safe, accessible home where Declan can be with his loved ones.
The fundraiser aims to cover construction costs, adapt the home to support Declan’s health needs and offset ongoing medical expenses.
If you’d like to donate to the fundraiser, go to the ‘Do It For Declan’ GoFundMe campaign page.
Not enough homes will be built to meet ROI’s housing demand until 2029 at the earliest, according to confidential Housing Department documents obtained by the Irish Daily Mail, as reported on extra.ie. The documents state that the 54,000 new builds it will take per year to outpace demand won’t be happen until 2029 at the earliest. Approximately 33,000 new builds were completed in 2023 (5,500 of those were self-builds) and the projection for 2024 is around 36,000.
The ROI government has pledged to build an average of 50,500 units per year until 2030. Ireland is currently short approximately 250,000 homes to meet market demand, a shortfall that’s expected to grow by around 20,000 per year between 2025 and 2040.
Noel McCarthy, incoming TD for Cork East, has officially marked the opening of farmer John Armstrong’s turf shed. The newly rebuilt shed no longer houses turf, not since the 1950s, but it continues to serve the purpose of storing firewood.
In an op-ed in The Echo, John Armstrong recounts how he asked his friend the newly elected TD to cut the ribbon on his humble steel frame shed.
Make the greener choice for your home, upgrade your existing central heating with an eco-friendly, low noise Midea Heat Pump. Air source heat pumps are the low-carbon future of home heating which integrates heating and domestic hot water into one system.
The future of heating, renewable energy is the greener, cleaner way to heat your home. Midea’s air source heat pumps are the costeffective way to lower your energy bills and switch to a low-carbon way of heating your home. Make yourself at home and start saving with Midea Heat Pumps.
OUR MIDEA MONOBLOC HEAT PUMP COMES WITH A MARKET LEADING 10 YEAR WARRANTY.
The High Court rejected a bid to block a couple’s home demolition.
A couple’s attempt to prevent the demolition of their family home – constructed without planning permission nearly 18 years ago – has been dismissed by the High Court as “frivolous and vexatious”, reports the Irish Times.
Chris Murray, a plumber, and his wife, Rose, brought fresh legal proceedings despite previously agreeing to vacate their 588sqm property in Co Meath, to allow for its demolition in September 2022.
The couple argued that new evidence had emerged, which they claimed warranted setting aside earlier court orders requiring them to leave the property. However, Mr Justice Conor Dignam rejected their case, agreeing
with Meath County Council that it constituted an abuse of process.
The court heard that the Murrays had been refused planning permission for a dormer bungalow in 2006, but proceeded to build a significantly larger house than was initially proposed.
In 2007, the council issued a notice regarding the unauthorised development, prompting the couple to seek retrospective permission.
Both the council and An Bord Pleanála rejected this, as well as a subsequent application to partially demolish and retain parts of the property, over fears it “would establish an undesirable precedent for further development of this kind.”
In 2017, the Supreme Court upheld High Court orders requiring the removal of unauthorised development and instructed the Murrays to vacate within a year, criticising the “deliberate breach of planning laws.” When the couple failed to comply, the council initiated contempt proceedings.
A settlement agreement was reached in 2020, where the couple consented to vacate the property within two years. However, three days before the deadline expired, they launched new proceedings seeking to pause the enforcement orders.
The Murrays claimed that fresh evidence regarding land sterilisation agreements by previous owners invalidated the original planning refusals.
They also referred to a recent High Court ruling that they believed supported their case.
Mr Justice Dignam dismissed these arguments, stating that judicial reviews of planning decisions must be brought within eight weeks of the decision unless exceptional circumstances, such as fraud or deliberate concealment, are proven. He said no such evidence was presented.
The judge confirmed that the couple’s claims were “vexatious and frivolous” and noted that Meath County Council had already rejected subsequent planning applications made by the Murrays.
A stone outbuilding that got planning permission for conversion saw the decision overruled by the ROI appeals board.
Laois County Council’s approval for a house in the backyard of a Mountmellick listed building has been overturned by An Bord Pleanála on the grounds that it amounted to ‘haphazard development’ that demolition work did not take into account nearby structures.
In overturning the planning permission, An Bord Pleanála stated that the proposed development would result in “haphazard backland development”, out of character with the area, and contrary to the sustainable development objectives for the locality.
The appeals board also expressed concerns regarding the demolition near protected structures, noting it was “not satisfied” that the impact on these structures had been adequately addressed, nor that the reuse of the outbuilding would conserve or enhance the built heritage.
The cottage is part of a row of Protected Structures.
As reported in the Leinster Express, neighbours raised significant concerns at the time of the initial planning
application.
Allistair Pim of Anngrove Stud Farm, who appealed to An Bord Pleanála, had initially objected to Laois County Council, arguing that the new house would be “wholly inappropriate” due to its close proximity to the stud farm’s yards and paddocks, which are used for bloodstock in thoroughbred racing. He also noted a previous agreement with the applicants’ late father, David Pim, which stipulated that no construction would take place on the property.
Anthony Booth, a neighbour residing in the bungalow next
door, also objected on the grounds of loss of privacy, light, right of way and parking issues.
Despite these objections, Laois County Council had granted approval, after the applicants, Martin and Bernadette Nolan, amended their plans significantly. The conversion of the stone outbuilding into a townhouse was agreed upon, with changes including a reduction in size, repositioned windows facing away from neighbours and additional rear parking to accommodate both the existing homes and the new one.
Political parties acknowledge the problem of building defects but the government still isn’t fully paying for them. This comes at a time when experts warn homes built with defective blocks require total demolition.
Political parties have mentioned building defects in their General Election 2025 manifestos. For example, Fine Gael wants to bring in an independent Building Standards Regulator to improve construction quality and safety. Sinn Féin, meanwhile, would also improve building controls, and supports 100 per
Redress for Defective Homes. This comes at a time when a TG4 investigation has revealed that full demolition is the only solution for the thousands of homes affected by defective blocks.
The government’s Housing Agency has downgraded many applications under the government’s enhanced Defective Concrete Blocks Grant Scheme, opting for cheaper, less comprehensive repair options instead of total demolition.
Under the terms of the government’s scheme, grant amounts vary and are subject to a €420,000 cap. Iniúchadh TG4 tracked down one of the first homeowners to avail of the new scheme, who was awarded €193,333 but after certain costs were deducted, she said she was left with €140,000 to build a new home and ended up spending €90,000 of her own money to bridge the cost.
The enhanced Grant Scheme, aimed at affected homeowners in Clare, Donegal, Limerick, and Mayo could apply to as many as 7,000 homes. However, defective block damage has been found in 13 counties, with fears every county in Ireland is affected.
Dr Andreas Leemann, a scientist from the Swiss
Federal Laboratories for Materials and Science Technology, explained to Iniúchadh TG4 that partial remediation, such as replacing the outer leaf of affected homes, fails to address the underlying damage caused by defective blocks.
According to Dr Leemann, who carried out forensic analysis on blocks from infected homes in Donegal and Mayo as part of international research being managed by Geological Survey Ireland, the mineral pyrrhotite, rather than mica or pyrite, is the true cause of the deterioration and eventual collapse.
Letterkenny campaigner Róise Ní Laifeartaigh from the Mica Action Group, whose own home is infected with defective blocks, told the programme she fears homeowners are being offered lower levels of remediation to save money.
The Housing Agency denied this, stating it engages chartered engineers, who
are members of Engineers Ireland, to provide appropriate remediation option recommendations in accordance with Irish Standard 465:2018 (IS 465).
IS 465 is a testing protocol developed at the request of the government to assess and categorise the damage to dwellings and aid in the selection of an appropriate remedial solution.
Pyrrhotite is not included in IS 465, which is currently under review, but the new enhanced compensation scheme states that the Housing Agency will “in their analysis and deliberations take into consideration the presence of pyrrhotite”.
Until pyrrhotite is formally included into a new revised standard for assessing damaged homes, director general of Engineers Ireland Damien Owens told TG4 that the Housing Agency should only proceed with recommendations for full demolition.
Fianna Fáil acknowledged the significant impact of the development levy waivers and the Uisce Éireann connection charge rebate, which together contributed to the commencement of 57,000 new homes in the past year.
Despite this, the Programme for Government, published as Selfbuild went to print, makes no mention of extending the waiver that expired at the end of 2024.
Sinn Féin says it would reform the waiver to target SME developers and urban projects with affordability challenges,
ensuring funding is effective in boosting supply and reducing costs.
Selfbuild has been campaigning to extend these waivers indefinitely for selfbuilders, as they can save cash-strapped families thousands of euros when building their home.
Sign the petition here
We gaze into our crystal ball to see what the political parties have in store for self-builders in 2025.
As Selfbuild went to print, the Programme for Government (PfG), the roadmap of what to expect from the new coalition government, stated the First Home Scheme would include secondhand homes, offering up to 30 per cent of the home’s cost.
Sinn Féin says it would end this scheme because it contributes to inflation. Labour would also phase out the First Home Scheme from 2026; it would instead introduce a new state agency to build homes.
The PfG is committed to the Help to Buy tax-back relief of €30,000 for those buying a new home or building their own. Fine Gael wanted to see an increase to €40k but this did not materialise.
The scheme sees first time buyers and self-builders avail of a tax back (you need to have paid that amount in tax over the past four years) to go towards their mortgage deposit.
Sinn Féin says it’s an inflationary measure and wants to wind down the scheme, cutting the amount in 2026 from €30,000 to €24,000, and continue cutting it by €6,000 annually to 2029. Labour also wants to phase out Help to Buy and replace it by an income-targeted Save to Buy scheme for the purchase of new homes with income limits on the tax refund available.
The PfG pledges to continue the Ready to Build Scheme, which provides serviced sites for individuals to build their own homes, and to further invest in rural water and wastewater infrastructure to support housing development in the countryside.
The PfG also supports the €70,000 derelict property grant (Croí Cónaithe Towns Fund – Vacant Homes Refurbishment Grant); including hiring more Vacant Property Officers, in part to expedite applications.
Fine Gael also wants to introduce the Town Centre Living Grant, a new €100,000 grant for converting “over-the-shop” premises for residential use. Labour supports a similar measure as well as making the Vacant Homes refurbishment grant available in instalments (as do Social
Democrats) along with zero-interest loans for retrofitting measures.
Labour also wants to increase capital grants for the Built Heritage Investment and Historic Structures Fund to support maintenance and regeneration. It also wants to increase the maximum awards under the Housing Adaptation Grant to €60,000 and ensure when work is approved that it is aligned with the SEAI Warmer Homes scheme to deliver energy upgrades at the same time.
Labour also wants to increase the income limits and maximum award for the Housing Aid for Older People Grant in line with inflation so that more older people who require adaptations can remain in their own home.
safety and environmental guidelines, even where they need access to regional roads.
Sinn Féin would introduce a stamp duty exemption for first time buyers on properties valued at €450,000 or less.
Independent Ireland wants to cut VAT on building materials to make construction cheaper. It also suggests offering tax breaks to property owners who renovate and rent or sell vacant homes, or convert unused spaces into living accommodation.
Sinn Féin believes the main driver to building more homes is a quick and easy planning process. To get planning departments to process applications more quickly and fairly it proposes to increase staffing levels, stating that local authorities are short 500 planning staff and that An Bord Pleanála has a staff deficit of at least 50. It also wants to encourage development through ‘use it or lose it’ planning permission and ensure County Development Plans do not automatically rezone land as residential if no development has taken place.
Independent Ireland proposes easing rural planning rules to make it easier for families to get planning permission for one-off homes in the countryside. It also wants to encourage councils to meet with families in person at pre-planning meetings to help them build homes on their own land, as long as they meet
Independent Ireland also wants to help older people downsize by doubling the size of rear extensions that don’t require planning in areas without enough infrastructure or community housing so they can stay close to family while maintaining their independence.
Fine Gael says it wants easier regulations for dividing homes into flats, allowing older adults to continue living in familiar surroundings while adapting to changing needs. In general, Independent Ireland wants to speed up planning and make the planning process simpler and quicker to reduce delays and get homes built faster.
Sinn Féin also wants to update planning policies for rural, Gaeltacht and island communities, to encourage self-building.
Labour wants to reduce the validity of planning permission from five to three years, introduce a ‘use it or lose it’ clause, and implement a rule which would extinguish planning permission when selling land that has approval.
Fine Gael supports the uptake of efficient home heating (HVO and BIOLPG) for rural properties.
Meanwhile Independent Ireland wants more supports for modular, prefabricated and log cabin housing as a faster, more affordable option for creating new homes.
As Ireland’s housing market shows signs of recovery, homebuilding efforts are ramping up with ambitious targets for the coming years, but what role have self-builders played in 2024?
Stockbroker Davy’s research is estimating that 34,000 homes will be completed in Ireland in 2024, just a little more than the 32,695 finished in 2023, reports RTÉ.
But the stockbroker is looking ahead with optimism, predicting that we’ll see 42,000 new homes in 2025 and a huge jump to 50,000 in 2026.
This isn’t happening out of nowhere – there’s been a lot of action in housing starts, with over 59,000 homes getting underway in the year up to October 2024.
Many of these are apartments, which naturally take longer to complete, so we’ll likely see the full impact
of these starts in the next couple of years.
While big developers and social housing schemes often get the headlines, selfbuilders are quietly making a significant mark.
Showing that individual homeowners are playing a role in boosting housing supply is a recent report from the Central Bank of Ireland which revealed that one-off selfbuilds made up about 17 per cent of all housing completions in 2023, which adds up to roughly 5,500 homes.
These were mostly funded through €1.7 billion in private mortgages and savings.
To put that in perspective, private developments accounted for around 19,000 homes and required €5.9 billion in financing, while social housing contributed 8,000 units.
Even with these promising numbers, the housing market is still playing catch-up. The Construction Industry Federation says ROI needs more than 60,000 homes a year to keep up with growing demand, driven by population increases and a long backlog from years of underbuilding.
In 2024, a significant number of self-builds starts
could be attributed to the development levy waiver which is no longer available to self-builders now.
Ireland is leading Europe when it comes to housing completions per capita. According to EYEuroconstruct, Ireland is on track to build 5.9 homes per 1,000 people this year — 80 per cent higher than the European average. And it doesn’t stop there. EY predicts that completions will rise to 38,000 in 2025 and 40,000 in 2026, keeping Ireland well ahead of its peers.
UK grants scheme oversaw era of mould growth as lenders now refuse to insure homes with spray foam insulation, according to reports.
Homeowners in the UK have been unable to sell or remortgage their homes fitted with spray foam insulation, reports the BBC.
The BBC says a quarter of the UK’s biggest mortgage providers will not lend against homes with spray foam in the roof.
The BBC reports 250,000 homes in the UK have spray foam insulation, with much of it installed under the previous government’s Green Homes
Grant scheme.
Concerns have to do with botched installation: poor fitting leaving moisture trapped and roof timbers at risk of decay.
However, the Insulation Manufacturers Association told the BBC that spray foam can be beneficial if properly installed, and that it was worried homeowners could be needlessly driven to “cowboy” removals companies. Open cell spray foam,
when applied correctly, is considered low risk, according to a report by the Health and Safety Executive entitled ‘Spray foam insulation applied to timber sloped roofs in dwellings’. However it must not be applied directly to roof tiles.
Another report by the BBC from earlier this year shows that since 2008, more than three million homes have had cavity wall insulation fitted under green energy schemes
set up by the government. Energy suppliers were responsible for inspecting 5 per cent of them to check for installation quality, says the BBC report.
Figures compiled by energy watchdog Ofgem seen by the BBC suggest that insulation in hundreds of thousands of these homes could have failed because it was not installed properly. In total 15 million homes have had their cavities filled.
NI Housing Supply Strategy 2024 promises more land, easier planning and innovative construction methods for self-builders, but challenges like infrastructure issues and planning delays remain.
The Department for Communities has launched the Housing Supply Strategy, following approval from the Northern Ireland Executive.
With an ambitious target of 100,000 new homes by 2039, the strategy aims to address the region’s pressing housing issues.
The strategy sets several key goals, including increasing housing supply, improving quality and enhancing energy efficiency.
Despite the optimism
Irish building sector. About 19,000 homes are currently stalled because of these infrastructure constraints. However, the increased number of planning applications (up by 23 per cent in the first nine months of 2024) offers hope for recovery in the medium term.
For self-builders, the Housing Supply Strategy’s path to reach the 100,000 target
surrounding the strategy, NI’s building sector is facing substantial hurdles, including the continued restriction of new housing developments due to infrastructure limitations, such as wastewater capacity issues.
Ongoing issues have contributed to a forecasted drop in home completions for 2024, with only 5,100 new homes expected to be finished — the lowest in 65 years, according to Construction Information Services (CIS), which tracks activity in the
presents both opportunities and challenges.
• More land to build on: One of the key goals of the strategy is to make land more accessible, especially public land. For self-builders, this could mean more chances to find a good plot of land, particularly in areas where land has been hard to come by or too expensive in the past.
• Tackling infrastructure issues: Problems like limited water and wastewater capacity have held up development
in certain areas for years. The strategy aims to fix these issues, which could open up more places for self-builders to create their homes without running into these barriers.
• Making the process easier: The strategy’s focus on making policies and regulations clearer and simpler is good news for selfbuilders. Less red tape and clearer rules should make it easier to navigate the planning system and get your project off the ground.
• Better access to information: With more open data on housing, land and planning, self-builders will be able to make smarter decisions about where to build, what it’ll cost and whether their project is feasible. This could save time and help avoid costly mistakes.
• Building for the future: As climate change and sustainability become more of a focus, self-builders will need to consider low-carbon building standards in their designs. The strategy supports new, greener ways to build, which could help self-builders make their homes more energy-efficient and futureproof.
• New construction methods: With a push for innovation in construction, self-builders will have access to new materials and building techniques that can help reduce costs and build more efficiently. This could mean shorter timelines and fewer hurdles in getting your home built.
• Faster planning
decisions: The strategy includes improvements to the planning process, so self-builders could see quicker decisions on their applications. This means fewer delays and a smoother experience overall when trying to get your project approved.
• Energy efficiency grants: The strategy highlights the need to deliver a scheme to help cover the costs of adding sustainable features like solar panels or better insulation for people on lower incomes living in private accommodation.
The latest NI Planning Statistics highlight challenges that self-builders may face under the Housing Supply Strategy:
• Delays in processing applications: Local applications averaged 18.8 weeks to process, exceeding the 15-week target. Addressing these delays will be crucial for the strategy’s success.
• High approval rates: Encouragingly, 94.9 per cent of applications were approved, offering reassurance to self-builders about the likelihood of securing planning permission.
• Regional disparities: Some councils, such as Mid and East Antrim and Fermanagh and Omagh, are processing applications significantly faster than others, highlighting the need for system-wide consistency.
Water and wastewater capacity constraints in both NI and ROI threaten plans to build thousands of new homes.
Water shortages are now threatening the ROI government’s plans to build thousands of new homes, with Uisce Éireann warning that a lack of water capacity could halt construction.
The water utility also stated it needs an additional €1.7 billion in funding to meet its targets. Despite the Government’s pledge to deliver an average of 50,000 new homes annually, Uisce Éireann can currently only supply water to 35,000 new homes a year over the next five years, according to Niall Gleeson, CEO of Uisce Éireann.
The utility has developed a “capacity register” to track available water across the country.
It’s a register of all the towns and cities around the country and what their capacities are. Usice Éireann is encouraging people who want to build “to go into those areas where we’re ‘green’.”
“We have a colour-coding
system, green, amber and red, and where we’re red, we just don’t have capacity. We may have a plan in place. We might be upgrading the plant. It could be three to five years away from going green again.”
Gleeson noted that, despite these measures, Uisce Éireann has had to reject certain areas for development.
“We approved 38,000 units this year and rejected about 200 to 300 — it’s not a huge number,” he said.
According to Uisce Éireann’s capacity register, there are three counties with ‘red’ code settlements: Cork (Castletownbere and Whitechurch), Kerry (Kenmare) and Kilkenny with the largest number (12) of areas currently without capacity for new home connections
If you’re building or planning a home in a rural area not served by Uisce Éireann’s public water supply, the Multiannual Rural Water Programme could provide other ways to access water services (see p18).
In some areas, building a well could be an option but it needs to be well built and maintained to ensure the water is safe to drink.
A recent survey by the Construction Employers Federation (CEF) revealed that wastewater capacity issues are delaying about 8,450 homes, worth nearly £1bn in investment.
When you add in the plans from housing associations and other developers, around 19,000 homes are currently stalled. That number jumps to 37,000 if you include the housing enquiries NI Water has received.
CEF Chief Executive Mark Spence discussed these figures on BBC NI’s Sunday Politics programme in November 2024, saying the crisis in homebuilding stems from “decades of underfunding” of NI Water and the wider
economic impact that this is now having.
Meanwhile the Belfast Telegraph reports that housing completions in NI look set to continue to decline in 2024, or at best maintain pace with completions in 2023 which fell to a 60-year low last year, citing a CIS report.
“Plans for an estimated 19,000 homes are being held up due to restrictions from an underfunded water system. New investment in housing over a number of years, as measured by new developments getting underway, has been erratic,” read the report adding that the “pipeline for housing remains strong” and that “once infrastructural issues are addressed growth in this sector will follow”.
To tackle the issue, in December 2024 the NI government announced £19.5. in water and sewage infrastructure funding to 2,300 new homes across NI.
House price rises in NI were the highest in the UK, a report by Nationwide shows, as stamp duty relief is expiring in April.
NI was the best performing area for the second year running with prices up 7.1 per cent over the year, according to Nationwide Building Society. The NI average house price in 2024 was £197,696, ahead of just Scotland and the North region; the average UK wide was £268,518. The report also highlighted
detached homes have continued to have a slight edge over other property types, most likely due to the ‘race for space’ seen during the pandemic. Since the first quarter of 2020, the price of an average detached property increased by nearly 27 per cent, while flats have only risen around 15 per cent.
UK house prices in general ended 2024 on a strong footing, prices were still just below the all-time high recorded in summer 2022.
Stamp duty hikes for NI First time buyers will have to pay more stamp duty from April 2025 in NI. First time buyers currently benefit
from paying no stamp duty on house valuations up to £425,000.
From March 31, this threshold will shrink back to £300,000, the level it was at two years ago. The change is expected to have an impact on the property market with buyers keen to close sales before the hike kicks in.
Changes to mobility grants help self-builders create accessible homes from the start, instead of having to wait midway through the process to apply.
Qualifying self-builders can soon apply for a maximum €20,000 Housing Adaptation Grant once full planning permission is granted, instead of partway through construction. This revision is one of several being introduced by the government following recommendations from the Report on the Review of the Housing Adaptation Grants for Older People and People with a Disability. The new Regulations also provide for increases in the household income thresholds
by 25 per cent.
This change to the grant application timeline for self-builders aims to prevent costly delays in construction and allows accessible design features to be built in from the start, which is much more efficient and cost-effective than retrofitting later.
Originally intended for modifying existing homes, local authorities had offered a work-around for self-builders to apply for the Housing Adaptation Grant at ‘wall plate’ level – when the walls are built, but the roof isn’t in
place.
Some building contractors pause work once they reach wall plate level to wait for the grant decision, which can delay the process further and increase costs for applicants.
The revised grant has been increased from 48.33 per cent to 50 per cent of the cost, with a new maximum of €20,000 for newly built houses.
The grant can be used to improve access by adding: a ramp or other ways to access a home; grab rails; bathroom facilities like an accessible shower or a
downstairs toilet; a stair lift; space for wheelchair access; an extension (typically for a bedroom and/or bathroom to accommodate a person with a disability).
The revised scheme will take effect on December 1, 2024, and all applications submitted on or after this date will follow the new guidelines. Updated application forms will be available from local authorities starting 1st December.
Self-builders and homeowners to get better water access in rural Ireland, as the ROI government boosts investment in infrastructure where public supply doesn’t reach.
Self-builders in rural Ireland may have new opportunities to tap into water services with funding from the Multi-annual Rural Water Programme. If you’re building or planning a home in a rural area that’s not covered by Uisce Éireann’s public water supply, this could be a way to get a water connection.
The latest cycle of the programme, run by the Department of Housing, Local Government and Heritage, was launched in January 2024. It supports local group water schemes (GWS), which are communityowned and operated with the aim to improve water
infrastructure in rural areas so that communities have a more reliable and efficient water source.
Last year, local authorities teamed up with group water schemes and their main representative body, the National Federation of Group Water Schemes, to apply for funding for different projects.
After a detailed review by an independent Expert Panel, Minister Darragh O’Brien approved around €47.1 million for 256 projects across the country.
This funding will help group water schemes keep improving water quality, supply and reliability in rural
areas.
The programme’s Measure A5 is especially useful for self-builders. It’s all about expanding piped water to rural areas that aren’t covered by the public supply. This expansion helps support growth in the areas around rural towns and villages and can happen in two ways:
• the extension of existing group water scheme networks, and
• new standalone group water schemes.
By connecting with a group water scheme in your area, you could find ways to access water that weren’t possible before.
If you’re considering a rural self-build, your first step should be to reach out to the local GWS. They can let you know what’s possible under this programme – whether it’s an extension of existing water lines or a brand-new connection. The National Federation of Group Water Schemes has a distribution map of all existing GWS.
An overview of what local authority grants you can avail of if you own a historic building.
Grants to renovate older buildings used to be hard to get, the good news is that now they’re much more accessible and are worth applying for.
Historic home repair grants of up to €200,000 are available to restore and preserve historic properties in Ireland, and the deadline to apply for funding in 2025 was January 17, 2025.
The scheme provides homeowners of historic properties with grants between €50,000 and €200,000, with larger amounts available for exceptional projects. The HSF typically covers up to 50 per cent of costs, or up to 80 per cent in cases of exceptional need. There might also be tax relief available under Section 482.
Applications for 2025 closed in January but keep an eye out in the autumn for the next round of applications.
These repair grants support smaller conservation projects, offering grants of between €2,500 and €50,000. In 2025 the scheme incorporated streams for vernacular buildings and historic shopfronts, which were previously part of the Historic Structures Fund.
The ‘micro’ grant stream introduced in 2020 continues to be available for works of routine maintenance and
minor repairs. Applications for the BHIS 2025 closed in September 2024; keep an eye out this coming July for the next round of funding.
Under the Croí Cónaithe Towns Fund you can get a grant of €50k to renovate a vacant property or €70k for restoring a derelict one, whether you already own it or are in the process of buying it. The project can also be for renovating a property to rent out — you don’t have to live in it yourself.
The Traditional Farm Buildings Grant helps farmers in the Green Low-Carbon Agri-Environment Scheme (GLAS) with the conservation and repair of traditional farm buildings and related structures. You can get up to 75 per cent of the cost covered, with a maximum grant of
€30,000. For smaller projects, the grant can be as low as €4,000. Applications typically open in February. Information on how to apply through the Heritage Council.
There is a grant for renovating thatched roofs on owneroccupied houses. You can get two-thirds of the approved cost, up to a maximum of €5k, for homes built before 1970. Applications closed in January.
Older properties often have lead pipes and the €5k grant to replace them is no longer means tested. This funding aims to cover 100 per cent of the remediation costs and there is no closing date for applications.
Individual grants for various
home energy improvements to existing homes in ROI are available through the Sustainable Energy Authority of Ireland, from insulation (attic or cavity wall insulation ranging from €1.5k to €1.7k for detached houses, dry lining €4.5k, and external wall insulation €8k), to heating systems (heat pumps €6.5k, solar panels up to €2.4k for PV and €1.2k for thermal, and heating controls €700).
There are also deep retrofit grants, known as One Stop Shops, which include windows, doors and ventilation systems, but these require extensive work. For instance, SEAI provides an example of a detached house where homeowners spent €64.5k on the work with a €24.1k grant, leaving them with €40.4k in expenses.
Plus, there are fully funded energy upgrades available for families receiving government supports, including pensioners.
Fiona and Jonathan, finalists in the BBC NI’s House of the Year series, have clinched the prestigious award for Melmore House. The couple relocated to Holywood from London when they bought the 1855 detached house in 2020.
Originally from Northern Ireland, Fiona wanted to return home, and while Jonathan needed some persuasion to make the move, purchasing Melmore House helped seal the decision.
The house underwent a major renovation and extension to transform it into a modern family home. Blending traditional features with a contemporary style, it now reflects the family’s personality and taste, with hints of a Parisian apartment in its rich details and flair.
beautiful sea views weren’t lived in at all, so we thought we would bring the living area here because it’s all about the views” Fiona says.
The Holywood home overlooks views of Belfast Lough, which Fiona and Jonathan state was a key reason for buying the property.
“They [the previous owners] lived in the back of the house, and the rooms with all the
Some stand out features about the five-bedroom house include a former servants’ quarters that has been transformed into a kitchen and cinema room.
Five homes made it to the Grand Final of the BBC Northern Ireland series, see
page opposite, presented by design expert and television personality Laurence Llewelyn Bowen. Judges Patricia McGinnis, Jane Larmour and James Fairley had the difficult task of choosing an overall winner.
Patrica McGinnis said “I chose Melmore House because it’s an incredible and aspirational example of how a traditional home can be reimagined for modern family life.”
“The sensitive renovation and extension remain true to the integrity of the original building and maximise the natural light and jaw dropping views. It’s a building that could be intimidating but it’s been given a light-hearted touch with playful colours and lovely architectural details. It’s a dream home.”
Jane Larmour admired the homeowners’ commitment to the old house, retaining its existing character, and at the same time enhancing it with clever adaptations to make it a wonderful family home.
Jane said: ”The quality of
light and volume in both old and new is beautiful, and I enjoyed the personal touches in the organisation of the plan, and the details that very joyfully and colourfully brought the house to life.”
James Fairley described Melmore House as a worthy winner of House of the Year 2024.
James said: “I personally loved the bold interventions that the homeowners had implemented in its design, both in terms of its interiors and its architecture.”
“It demonstrates courage in tackling the issues associated with refurbishing a period property and how it can be done to suit modern family living.”
“The homeowners haven’t been afraid to express their love for good design and colour throughout the home. They have approached the interior sensitively and with great care and consideration but haven’t been afraid to implement their own tastes and ideas throughout the home.”
A 1920s farmhouse in Tyrone, this country home has been in the family since owner Scott’s great-uncle lived on the property. The two-storey house blends a modern interior design with its traditional structure – a deliberate choice to honour its original features. Memorabilia from Scott’s travels abroad line the shelves and walls throughout the home.
This historic 1860s mansion in east Belfast, once owned by the family of C.S. Lewis and designed by the renowned architect Thomas Jackson, is steeped in heritage. On the brink of collapse, the Grade II listed building was carefully restored to its former glory by Katie Coulter and her husband, Johnny.
Perched high on the hills east of the city, this black-clad home offers sweeping views of Belfast Lough. With a barnlike, understated design, the house is filled with light from wide bay windows and skylights installed by the owner, Heather. The transformation from its derelict state in 2010 took three architects and more than a decade to complete.
The red brick and white exterior fits right in with the other terraced houses, but inside, this home is full of character. For the last 10 years, Donna, a part-time interior designer, and her husband Alan have called this place home. With the support of their understanding landlord, they’ve been able to make the interior their own, filling it with art and vibrant colours.
Energy-efficient insulation solutions for renovation.
Your renovation project gives you one opportunity to get your insulation right, so it is important to consider it carefully.
At Unilin Insulation, our experts will help guide you to the best insulation solutions for your project – for a warmer, more energy-efficient home.
For free one-to-one advice, talk to our technical team on 046 906 6050.
The company behind K Rend, Kilwaughter Minerals Limited, is to become part of the Saint-Gobain group, which already owns many other manufacturing brands such as Gyproc, Weber and Isover.
The acquisition will close in the first half of 2025 when the Competition and Markets
Authority approves the sale.
Quarry and mineral processor Kilwaughter Minerals Limited was established in 1939. Headquartered on a 187-acre site in Larne, Co Antrim, its distribution centres are located in Glasgow, Cork and St Helens.
Known for leading brands K Rend, K Systems and Kilwaughter Lime, the company generated revenues of circa £50m in FY2024 and has over 200 employees. K Rend is the UK and Ireland’s largest independent silicone render manufacturer.
Saint-Gobain is a global leader in the design and manufacture of solutions for the construction industry and employs 160,000 people across 76 countries.
More about the companies on saint-gobain.com and kilwaughter.com
Concealed guttering offers the modern look many self-builders are after, but it can often be expensive and pose significant challenges for architects and builders alike. This is because the structure traditionally has to be designed and built to accommodate such systems.
Traditional concealed systems often rely on cumbersome designs, which often make the guttering difficult to access from the exterior. If a leak occurs, identifying and resolving the issue can be both complex and costly, as the structure prevents easy inspection.
Enter Litcore’s Niagara Concealed Guttering system, designed for external accessibility, making it possible to inspect, identify, and fix any issues without incurring a hefty repair bill.
Compared to other concealed systems, the cost is reasonable too; a standard threebedroom bungalow with two straight runs of guttering would cost approximately €1,350 euros plus VAT for the materials, including downpipes.
Both the Half-Round and Square Niagara guttering systems are now available with additional flashings, to provide that soughtafter hidden guttering solution.
The easy-to-install components simplify the process for builders and architects, saving time and effort. The new additional items include guttering fascia, corner covers, soffit panels,
brackets (for both wall plate fixing and roof mounting).
All components are designed for compatibility and ease of installation, ensuring a perfect fit for any project. The components also come with a 30-year warranty.
litcore.ie
Grant has announced the launch of its next-generation air source heat pump, which was designed in Ireland, specifically for the Irish and UK climate.
Innovative and aesthetically pleasing, the Grant Aerona R290 heat pump range is suitable for many types of homes and features five models, ranging from 4kW to 16kW, which are all available to order from Grant merchants now.
Built upon three core pillars –
design, performance and peace of mind – the A+++ energy rated Aerona R290 provides an even more environmentally friendly, low carbon heating solution, as it uses the energy-efficient and natural refrigerant R290, which has an incredibly low Global Warming Potential (GWP) of 3.
When compared to other refrigerants commonly used in heat pumps like R32, which has a GWP index of 657, the new Aerona R290 signals an important advancement in sustainable home heating for new build homes. grant.ie
Unrivalled performance WITH a spec that stands out:
Standard 1.2mm membrane (10% thicker than competitors)
Choice of 1.2mm or Premium 1.5mm thicknesses
High puncture resistance – won’t tear, split or crack
Excellent resistance to temperature extremes, UV & aging
Quick, clean installation
Maintenance-free and environmentally friendly
Ideal for refurbishments and new builds
Unmatched weatherability and flexibility
Belfast: +44 28 9038 0060
Omagh: +44 28 8224 6220
Dublin: +353 1 623 4541
Limerick: +353 61 531 381
Cork: +353 21 432 1868
www.sig.ie enquiries@sig.ie
Words: Heather Campbell
Photography: Damien Kelly
Overview
House size: 204 sqm
Bedrooms: 4
Plot size: 0.75 acres
Heating system: Air to water heat pump
Ventilation: Centralised mechanical with heat recovery Build method: Blockwork
Site cost: €80,000
Total build cost approx: €300,000
Cost of well drilling and associated equipment: €6,000
Kitchen and utility room (including quartz, appliances and boiling water tap): € 24,800
Laura and Peter Dillon set out to find their ideal home in Co Westmeath leading them to build a bespoke bungalow rooted in family tradition and designed for modern living.
aura and Peter’s decision to build their single storey home came down to a few key factors. “We wanted to stay near Athlone to be close to my family,” Laura explains. After months of searching and exploring various options, they finally stumbled upon a site that met their needs.
“The other reason was that building allowed us to create a home that fits our needs perfectly, rather than trying to make an existing property work,” she adds, reflecting on the flexibility and customisation that come with starting from scratch.
Their new home is tucked away in a quiet rural spot, just a quick 10 minute drive from the town. With fields and forests all around, it’s the peaceful retreat they were hoping for, yet still close enough to town for convenience. The location gave them exactly the kind of calm, natural setting they had imagined, making it the perfect place to start turning their vision into reality.
While they had some initial design ideas, they worked with a local architectural designer who was experienced with the Westmeath rural planning guidelines.
“This was a crucial step for us,” Laura says. “We felt confident choosing him because we knew he could successfully navigate the local requirements.”
“After he visited the site and talked through our ideas, he came back with a few design options and we picked the one
that felt closest to what we had in mind for the house.”
“We knew we wanted an open plan layout for the main living area, plenty of natural light, four bedrooms, a utility room and a separate sitting room. Vaulted ceilings in the living area were high up on our wish list also.”
“We also wanted a bungalow layout since that’s what we both grew up in, but we definitely didn’t want the usual dark, windowless hallway that comes with it.”
“He came up with an H-shaped design to let in as much natural light as possible. The bedrooms are in one ‘wing’ facing north, and the main living area is in the other ‘wing,’ with a hallway connecting the two.”
“We were aiming for a blend of traditional and modern styles. Externally, we wanted the house to nod
to the traditional Irish farmhouse style, especially with the small, cottage like windows at the front. But we also wanted large, modern windows at the back of the house to let in plenty of light.”
“Inside, we went for a modern farmhouse style, combining traditional materials like oak with contemporary touches, such as a shaker style kitchen.”
“We were inspired by other new builds we had seen, particularly the open plan living spaces. This was a key priority for us, we wanted that open, airy feel in the main living areas of the house.”
The couple opted to take the direct labour approach, with Peter project managing the build while still working full time. “This was challenging, but the pandemic helped in a way because Peter was able to be on site more often when he wasn’t working. He coordinated the tradespeople, many of whom were recommended by our family and friends.”
“He teaches construction at secondary school and is a trained carpenter, so he had the confidence and skills to be very hands-on with the build. He was able to handle carpentry work, ensure proper airtightness and fill in gaps between the different trades.”
“Being prepared to ‘roll up your sleeves’ and get involved is crucial when
you’re taking on a self-build project. Peter’s father, who lives near to the house also helped a lot, especially with letting tradespeople in and handling smaller tasks when Peter couldn’t be there.”
“Using direct labour and having Peter manage the build allowed us to keep more control over the process and save on costs.”
After receiving a quote of about €10,000 for a connection fee from Irish Water, they decided to drill their own well. “Peter grew up in a rural area with a well, so this didn’t faze us at all,” Laura says.
One of the standout features of the house is the glazing and windows. The open plan living area has a large, 4m wide lift and slide door that opens up to the outdoors. The kitchen has a distinctive long, narrow window that was strategically placed to capture morning light which would otherwise be shaded by the east facing treeline of the adjacent forest. “We really wanted to maximise natural light throughout the house, and the window placement reflects that.”
A unique element in the design is the oak trusses in the vaulted ceilings. “These were made from trees felled on Peter’s family land in Co Galway. We had them crafted by a specialist in Galway, so it’s lovely to have a piece of Peter’s family history in the house.”
The couple decided to install laminate flooring throughout the home instead of tile or concrete. This choice was a smart way to save on costs since Peter could handle the installation himself.
They installed an air to water heat pump with underfloor heating and a mechanical heat recovery ventilation (MVHR) system, both of which have kept the house energy efficient and comfortable. “We also opted for LED lights throughout, which has also helped keep our energy bills reasonable,” adds Laura.
“We spent a lot of time looking for style inspiration on social media during lockdown, especially for the kitchen,” says Laura.
They consulted with several different kitchen companies and had them provide kitchen designs. This allowed them to compare options and eventually settle on a design that they worked out with a local craftsman, who ended up building the kitchen for them.
“We eventually worked with a local
What is your favourite design feature?
My favourite part of the house is definitely the open plan living area. I love how much natural light floods the space through the large windows and skylights. It’s bright and welcoming no matter the season.
What would you change or do differently?
If I were to build again, I would make the bedrooms a bit bigger, especially the smaller guest rooms, as they feel a little tight. I’d also increase the size of the front facing windows, which are currently small, making the rooms a bit dark when the internal doors are closed. Additionally, I regret not consulting a lighting expert, as choosing where to locate the lights in the open plan layout with trusses and skylights was challenging.
What surprised you?
I was surprised by how long everything took. We initially thought the build would take about 1.5 years, but it ended up being closer to two years. Coordinating with tradespeople was also more challenging than expected.
What single piece of advice would you give a budding self-builder?
Spend a lot of time on detailed planning. Really take the time to think through every aspect of each room’s layout and how the furniture will fit before you finalise the plans. This kind of careful planning can make a huge difference, especially with practical details like the placement of electrical outlets. In short, planning is everything. It’s worth the extra effort upfront to avoid issues later on.
I wouldn’t say ‘definitely not’. Peter might be more hesitant, given the hard work and sacrifices involved, including living with family for five years in order to save up for it. We feel very lucky and rewarded by the end result, but we recognise it’s not something everyone can easily do.
craftsman who built our shaker style kitchen. He combined solid wood exteriors with MDF interiors to keep the costs down.”
“Sourcing the bathroom fixtures and fittings was one of the most challenging parts of the build,” admits Laura. “I managed to get some bathroom layouts done cheaply by a local draughtsman which I found very helpful in visualising the spaces.”
“A relative helped us source the fixtures and fittings from a local supplier at a good price,” she adds.
One thing the couple wish they’d done differently is to hire a lighting consultant. “The open plan layout made it difficult to plan the lighting, and there are some areas where we would have liked things placed differently.”
“The lighting design was a collaboration between the electrician and ourselves. We walked around the house with him one day and tried to figure out where things were going to go. Now, there are a few spots where I wish I had a socket or where a plug or light switch is in an inconvenient location. But these things happen; it’s tough to think of everything, especially when you have a hundred other things on your mind.”
“Still, we did incorporate energy efficient features, like LED lights and a motion sensor in the hallway, which our electrician suggested.”
“As for energy efficiency, we’ve wired the house for solar panels, but we haven’t installed them yet due to budget constraints. It’s something we might add down the line.”
During the construction process, the couple made a few changes to the original building plans.
“The architectural designer’s initial plans featured a different style of vaulted ceiling, but we decided to change this to incorporate the oak trusses.”
“Also, there was originally supposed to be a flat roof section connecting the open plan area to the bedroom section, but we changed this to a traditional pitched roof instead.”
Halfway through the internal construction, they realised they wanted to add a dressing room adjacent to the main bedroom, so they knocked down a half wall to create this additional space.
As for landscaping, it’s still a work in progress. “We’ve laid the lawns, but there’s no kerbing or tarmac yet. My father-in-law helped with some of the groundwork, but the landscaping is definitely on the ‘to do’ list. The area from the front door to the driveway entrance is
Shop around. It’s so important to hire a high quality architectural designer who knows the local area well.
Consider getting 3D plans done of the house and rooms, as this can help identify potential layout issues before finalising the design.
Don’t rush the planning process just to get the initial plans submitted. Taking the time upfront to get the details right is crucial.
“The couple decided to install laminate flooring throughout the home instead of tile or concrete. This choice was a smart way to save on costs since Peter could handle the installation himself.”
still pretty bumpy.”
“We weren’t allowed to place the driveway entrance where we had initially planned. Instead, we had to position it in a less ideal parallel location because of a dodgy corner on the road.”
Overall they are delighted with how the house is working for them after living in it for a good number of years.
“We love the open plan living area and
would definitely do something similar if we were to build again,” says Laura. “The open layout is a fantastic feature which works really well for our lifestyle.”
“We haven’t encountered any major issues with the heating system, as we’ve kept up with all necessary maintenance and servicing. We feel we’ve been able to make the home our own by adding personal touches, which is often harder to achieve when buying an existing house.”
“We are very, very happy and very proud of the end result of our self-build project. It’s been a very rewarding experience to see our hard work come to life in our finished home,” says Laura. “All in all, while the build took longer than we originally anticipated—about two years instead of 1.5—we’re really pleased with how the house turned out. It’s been quite a journey, but the blend of traditional and modern elements, along with personal touches like the oak trusses, have made this house feel like home.”
More photographs available at selfbuild.ie
Find out more about Laura and Peter’s project in Co Westmeath...
Architectural design
David Marshall, John Madden & Associates, Co Westmeath, tel. 044 9344347
Kitchen
David Conway Kitchens, Co Galway, mobile 087 221 0061
Electrician
Eamon Finlay Electrician, Co Westmeath, mobile 087 256 9868
Roofer
Richie Fallon, Co Westmeath, mobile 087 984 3009
Plasterer
David Rooney, Co Galway, mobile 087 412 4752
Blocklayers
David Kelly, Co Roscommon, mobile 086 736 8585
John Derwin, Co Roscommon, mobile 087 298 5822
Plumbing
Padraic Duignan Plumbing, Co Westmeath, mobile 086 087 7116
NI calling ROI prefix with 00353 and drop the first 0
Insulation: PIR for floor (150mm) and walls (120mm) and pitched roof on rafter (150mm). Spray foam insulation for apex roof with 150mm PIR on underside. Mineral woold insulation for intermediate floor.
Windows: Triple glazed uPVC argon filled windows, 4m aluclad slider double glazed argon filled, RAL colour 7016, overall U-value: 1.1W/sqmK.
Plot size: 0.8 acres
House size: 278sqm house
Bedrooms: 4
Heating system: Oil boiler
Ventilation: Positive input
ventilation
Build method: Blockwork cavity
walls
EPC: B
Niall and Rachel McAlinden’s self-build in Co Tyrone shows what it takes to create a personalised home. From overcoming planning restrictions to making crucial design choices, their journey highlights the rewards and challenges of building a space that reflects their family’s unique needs.
When Niall and Rachel decided to build their own home, they weren’t just looking for a roof over their heads. They wanted a place that reflected their unique style and met their specific needs.
For Niall, the idea of building from scratch was irresistible. “I was drawn to creating a house that was tailored to us,” he explains. “The freedom to choose everything, from the layout to the finishes, was a big selling point.”
Living in the countryside was also a major factor. “Having grown up in the countryside, I knew that’s where I wanted to settle. These days, it’s tough to find modern homes in rural areas, so building felt like the best way to get what we wanted. Plus, my dad had some land we could use.”
“I first brought it up with him about nine years ago, just to see if building on the land was a possibility. Then Rachel and I started thinking seriously about the process around 2018 – mainly about getting ownership transferred and planning for the build.”
“We were still living with our respective parents at that stage, but we were thinking about and planning to move in together, whether that meant moving into another place first before building our own home or moving into it when it was finished. There were a lot of unanswered questions at that point in terms of the timeline for the build and how long it would take, as there were
BATHROOM DESIGN
INTERIOR DESIGN CONSULTATIONS
D TAKE A VIRTUAL TOUR OF OUR SHOWROOMS
090 6424000 - info@tubstiles.ie - tubstiles.ie
many factors outside of our control. There was also the process of getting a mortgage and all the associated steps.”
“Then, obviously, Covid hit, which significantly changed our original plans. By that point, we were renting a house together but had not started the actual building process yet.”
“In 2020, we decided to move into a different rented house, as the one we
were living in was not suitable. We ended up moving twice. In late 2021, we moved into another, larger house in the town centre, as we had our first baby at that point and needed more space.”
From the start, Niall and Rachel had a clear vision. Their original plan was for a two storey home, but this was ultimately rejected by the local planning authorities
due to ridge height restrictions. “We are on high land here, and the houses around us are either bungalows or a storey and a half. So we had to change our plans to a one and a half storey. All the bedrooms had been on the first floor, which we had to work into the ground floor plan.”
“My sister, Lisa, is an architect, so I communicated with her extensively from an early stage. As someone who is not in the construction industry and had no prior experience building a house, I was massively out of my comfort zone, as was Rachel.”
The planning phase was tough. “When I first looked into building a house on the land I had in mind, I quickly realised it wouldn’t be straightforward. Initially, the planners viewed the land as a ‘random field’ that couldn’t be built on; it didn’t meet their criteria for development. It was right next to our family home, but I was told I couldn’t just build anywhere, and the land I wanted to use didn’t qualify.”
“However, a local farmer had recently received permission to build a house for his son in the field next to my site. Because of this, my land was now considered an ‘infill site’ – a piece of land that fills in a gap between established
properties.”
“This reclassification was essential. Without it, we wouldn’t have had a chance.”
Yet the challenges didn’t end there. Niall and Rachel faced logistical issues, such as needing to move overhead power lines underground. “That was a hassle,” Niall admits. Thankfully, Niall’s sister provided invaluable guidance during this time. “She was a huge help in navigating all the regulatory and logistical hurdles,” he says. “Without her, we might still be stuck in the planning phase.”
Niall brought in a contractor to handle the construction. “I thought that once I hired someone, I could take a step back. But I soon realised I had to stay involved,” he reflects. “It was our house, and I had to ensure everything matched what we both wanted.”
Niall had specific materials and features in mind that would make an individual statement. At the outset, he had a particular type of stone cladding in mind for the exterior. However, after consulting with others, Niall learned that his original choice was of poor quality. “That’s when I switched to Kilkenny limestone, which turned out to be a beautiful compromise,” he adds.
“These days, it’s tough to find modern homes in rural areas, so building felt like the best way to get what we wanted.”
Both Niall and Rachel shared a vision for good design. “We wanted an open plan, kitchen and living area with a sunroom,” he says. “And we also wanted to bring in as much natural light as possible and be able to enjoy the views of the surrounding landscape, so glazing was important also.”
They installed nearly floor to ceiling windows in the sunroom and a large window in the hallway that stretches from the ground floor up to the half storey. “Unfortunately, because of the pandemic, we weren’t able to finish the upstairs, so we had to block it off,” Niall
says. “That meant we couldn’t fully take advantage of the hallway window, which would have let a lot of natural light flow through the space.”
For the roof, they opted for tiles that combined good looks and functionality. “I originally wanted slate, but after researching and speaking to roof tile experts, we decided on an alternative that was a little bit more expensive but was more durable,” Niall explains.
When it came to decisions on heating and ventilation systems, the couple consulted with plumbers and friends who had experience in the field. At first, they planned to go with traditional radiators, but as construction progressed, Niall
had a change of heart and switched to underfloor heating powered by oil.
“I had considered a heat pump, but from what I understood at that time, it would involve installing solar panels to keep electricity costs down,” he says. “Ultimately, I weighed the pros and cons, looking at costs, long term performance and advice from industry contacts. It’s still an option for later down the line as the underfloor heating can be linked to a heat pump later on.”
For ventilation, Niall opted for positive input ventilation (PIV) units with two continual mechanical extract points.
As they moved into the interior design phase, Niall and Rachel took a hands on approach. They spent their time researching options for their kitchen,
bathrooms, lighting and flooring. “We knew we had to compromise on certain things, but we also wanted to make sure we enjoyed the process,” Niall reflects.
For flooring, they settled on laminate for the hallway, kitchen and bedrooms. The bathrooms were designed with a contemporary look in mind, featuring a cohesive design that included both an ensuite and a main bathroom. “We wanted everything to flow together nicely,” Niall explains.
The building process was not without its challenges, due to the amount of decisions the couple had to make. “There were days when I felt completely unqualified to make these choices,” he says. “I found myself thinking, ‘You’re making decisions all the time, and you have no idea what you’re doing.’”
The pandemic added an additional layer of stress to the build. “The changing costs and the trades going back on agreed prices made everything more complicated,” Niall explains.
Building their home proved to be one of the hardest experiences Niall had ever faced. “The constant decision making, my lack of preparedness and external factors like the pandemic made everything incredibly difficult,” he reflects.
As the build progressed, Niall and Rachel encountered unexpected changes. One major shift was the decision to forgo fitting out the upstairs level that they initially planned for additional bedrooms. “It was disappointing, but we realised we just couldn’t move forward with it at that time. We had to make compromises and adjustments along the way, but we still created the contemporary, open concept
What is your favourite design feature?
I love the open fireplace in the sunroom, framed with the same Kilkenny marble used on the exterior stonework.
What would you change or do differently?
We built a first floor, with plumbing for an ensuite bathroom, but didn’t put internal walls or a staircase to access it. If I were to do it again, I probably wouldn’t add the upstairs level at all. I’d also rethink where we positioned the house on the land; a different spot might have suited us better. I’d redesign the garden layout to make better use of the space – it doesn’t feel as efficient as it could be.
Looking back, I’d also choose different contractors for some of the work. Having the right people in place would have made the process clearer, easier and much less stressful. And finally, I wouldn’t build during Covid! With constantly changing costs and supply challenges, it made the whole experience a lot harder than it needed to be. But we had no choice about that.
surprised you?
What really caught me off guard during the building process was the sheer amount of detail, thought and time it demanded. I didn’t anticipate how much energy and decision making would be involved. Our first son was born in December 2021, and we started building just five months later. We had just moved into our second rented house. I was juggling my job, and we were deep in the building process, making endless choices and managing everything. To top it off, our second son was born in April 2023 – the same month we were moving into the house. Looking back, we definitely built at the wrong time.
you give a budding
Do your research thoroughly. Talk to as many people as you can – architects, contractors and others in the industry. Don’t rush into it or go in unprepared. Take the time to understand the entire process and make as many decisions as possible before the tender process even begins. This way, you’ll have fewer changes and less improvisation during the build, which will make everything go more smoothly.
View it as a collective effort. Don’t underestimate how much preparation is needed; getting advice from knowledgeable people beforehand is essential.
Communication is vital. Whether it’s with your partner, contractors or architects, keeping everyone on the same page can make a world of difference. It helps you navigate obstacles more easily.
Do your research before the build starts. One of the toughest parts of the build was the constant decision making. I was surprised by how much detail and thought went into every aspect of construction. I underestimated the energy and decision making involved, and it was an eye-opener for sure.
design we wanted,” Niall says. “That was really important to us.”
The open fire in the sunroom was another must-have for Niall. “It’s cosy, and I love the Kilkenny marble stone around it,” he says. “I first thought about installing a stove in the kitchen area but having that open fire in the sunroom turned out even better. It’s my go-to spot to unwind – whether I’m watching TV, reading or just relaxing.”
When it comes to the home overall, Niall is genuinely happy. “I love it,” he says. “Sure, if I were to do it again, there
October 2019
Outline planning permission application
January 2020
Build end and moved in Timeline
Outline planning permission granted
October 2020
Reserved matters application
February 2021
Reserved matters granted
April 2022
Build start
April 2023
are things I’d probably do differently, but this place truly feels like home. It really suits our family’s needs, and despite all the challenges we faced during the build, I’m satisfied with how it turned out.”
Because for Niall, building his own home wasn’t just about the house itself –it was also about the lessons he picked up along the way. “Building a home is more of a marathon than a sprint,” he says. “You’ve got to be ready for challenges and understand that things won’t always go as planned. Staying flexible is the key.”
Find out more about Niall and Rachel’s project in Co Tyrone... More photographs available at selfbuild.ie
Kitchen, utility and pantry
Dunlop Kitchens, tel. 6772 1919, dunlopkitchens.co.uk
Bathrooms, plumbing, heating and tiles
E&R Bennett, tel. 8952 2303, eandrbennett.co.uk
Stove
Maydown Stoves, mobile 07989 553597, maydownfireplaces.com
Sofas
BR Modern Interiors, tel. 8556 7364, br-modern-interiors.myshopify.com
Stones
Campbell Quarry, tel. 8954 1666, campbellcontracts.com
Blocks and concrete FP McCann, tel. 6772 1286, fpmccann.co.uk
Windows and doors
Clogher Valley Windows, tel. 8554 9764
Internal doors and handles Kildress Joinery, tel. 8675 1292, kildressjoinery.com
Building supplies
Creighton’s of Lisbellaw, tel. 6638 7207, creightonslisbellaw.co.uk
Solar panels
KB Electrical, tel. 6634 1093, kbelectrical.co.uk
Photography
Paul Lindsay, paullindsayphoto.co.uk
ROI calling NI prefix with 048, for mobile prefix with 0044 and drop the first 0
Walls: Render finish on 100mm blockwork outer leaf on 150mm cavity fully filled with blown bead insulation on 100mm blockwork inner leaf on 62.5mm insulated plasterboard with in-built vapour barrier on skim finish, U-value 0.21W/sqmK
Roof: Sloping roof covering fibre cement slate, on treated timber battens on breathable roofing membrane on 50mm ventilated air gap between rafters on 100mm rigid insulation between rafters on 62.5mm insulated plasterboard with in-built vapour barrier under rafters on skim finish, U-value 0.17W/sqmK
Floor: Damp proof membrane, 150mm concrete slab, 100mm rigid insulation, membrane, 75mm screed incorporating underfloor heating, floor finish, U-value 0.16W/sqmK
Windows: uPVC double glazed, overall U-value 1.40W/sqmK
Airtightness: 2.167m³(h.sqm)
Words: Heather Campbell
Photography: Damien Kelly
House size before extension:
90sqm
House size after extension: 220sqm
Bedrooms: 4
Plot size: 2 acres
Purchase price: €225k
Build cost: €130k
House value: €650k
BER before: G
BER after: B1
Heating system: Condensing
oil boiler
Ventilation: Centralised mechanical with heat recovery
Build method: ICF
Faced with a growing family in a two bedroom cottage in Co Kildare, Darren and Sinéad Delahan set out to create more space. Through determination, creative planning and DIY spirit, they transformed their home with a double extension without losing any of its original charm.
arren and Sinéad bought their two bedroom cottage in November 2015, a decision that felt right, even though the place wasn’t exactly in great shape. “We had been looking for a house for some time and stumbled upon this one while we were browsing online listings,” explains Darren.
“At first glance, it didn’t pique our interest at all. In fact, the initial photos of the cottage didn’t really sell it to us. It was painted in bright yellow and pink, which, to be honest, seemed a bit garish and off-putting. We weren’t drawn to it right away, but as often happens, our parents convinced us to take another look. They suggested that we go and check it out in person – ‘You never know,’ they said. So we gave it a shot.”
“Arriving at the cottage, it still looked a bit eccentric with its bold colours, but something about the location and the character of the place felt right to us.” Once they had a walk around inside, they could see the potential.
The land it sat on, the surrounding space and the overall feel of the property were enough to make them reconsider their first impressions. “It was quirky, yes, but we knew that with a bit of vision, it could be the home we wanted,” says Darren.
The timing of the purchase added a layer of urgency to the whole process. “Just one week after we closed on the cottage, our first daughter arrived.
Obviously, we were thrilled to welcome her, but we also felt the rush to make the house liveable. We had already planned to strip it down and renovate it completely, so we knew we had to get started right away.”
Their first goal was to tackle the most pressing issues – insulation and rewiring –so they could move in as soon as possible. “The existing insulation was almost nonexistent, and the wiring was outdated, not to mention unsafe in some areas,” explains Darren. “Luckily, we were offered a lot of help from family and friends. They pitched in and helped us get through those first critical weeks, making sure we could move in before things got too chaotic with the newborn.”
By March 2018, the family grew again with the birth of their second child. “At that point, the two bedroom cottage was feeling pretty tight. By June 2019, we had three kids and space was quickly becoming an issue.”
The cottage had an old 1960s extension at the back, but it was far from ideal. It was small, poorly insulated and not really
functional for a growing family. “We knew it would eventually need to come down, but we wanted to wait until we could afford to do it right,” says Darren.
“Rather than make small additions here and there over the years, we decided early on that we were going to do one big renovation – something that would serve
our family for the long term. We didn’t want to be constantly tinkering with the house and living in a perpetual state of construction. Instead, we chose to plan everything out thoroughly and tackle the renovation all at once. This was going to be our forever home, and we wanted to make sure it would work for us as our family grew and our needs evolved.”
The Delahans started by brainstorming what they really wanted
out of the space. “An architect friend offered to help, and while his ideas were good, they didn’t quite match what we envisioned. He was leaning more towards a modern, minimalist style whereas we wanted something that kept the cottage’s rustic charm but still offered the functionality and space we needed.”
After several back and forth discussions, the Delahans realised they had a clearer idea of what they wanted than anyone else. “In the end, I decided to draw up the plans myself. I had no formal training in architecture, but I sketched out our dream layout and sent the plans over to our architect, who then formalised them for submission.”
The design they settled on involved two main extensions. “The first was a large open plan kitchen and living area with a vaulted ceiling and mezzanine. This would be the heart of the home, a space where we could all gather, cook, eat and relax together. The second extension was at the back of the house, where we added two more bedrooms and an ensuite.”
They also added a first storey to the back extension. “I knew there was going to be a large ground floor space, so we decided to drop the floor down by about
“ICF offered the best combination of insulation, speed and cost effectiveness.”
What is your favourite design feature and your favourite room?
The vaulted ceiling in the kitchen and living area extension. The scale of the ceiling, combined with the lighting we chose –like the recessed lights and some more decorative fixtures – really works well. Surprisingly, my favourite room is the laundry room. With three kids, it’s become such a practical and useful space. It makes managing the day to day laundry so much easier, with a sink for soaking and plenty of space to fold clothes.
What would you change or do differently?
Originally, we had the playroom at the back of the kitchen, which was really convenient when the kids were younger because we could easily keep an eye on them from the kitchen. But now that they’re older, having the playroom right off the kitchen means we hear all the noise while we’re in the open plan living area. If I were to do it again, I might think about moving the playroom to another part of the house to keep the living and kitchen areas quieter.
What surprised you?
The biggest surprise during the build was how challenging it was to manage the project while living in the house with three young children. I hadn’t fully anticipated how tricky it would be to juggle everything. Sometimes deliveries or tradespeople wouldn’t arrive as planned, which made things more stressful. There weren’t any massive delays, but when you’re managing things yourself, it’s frustrating to have everything lined up for a Saturday only to get a text saying, “I’m not coming today”.
What single piece of advice would you give a budding renovator?
Don’t hesitate to spend the money on the fabric of the building. Make sure your insulation, airtightness and all that is up to scratch. It’s paid off for us. You can always redecorate a room, but you’re never going to get back into those walls or under that floor again. So, if you’re going to do it, do it right and let the other things come later.
eight inches. That gave us the potential headroom to add another room upstairs, keeping the roof level the same height as the original cottage roof.”
“The extensions gave us the space we desperately needed and made sure that each of our kids could eventually have their own room as they grew older.”
ICF extension
One of the biggest decisions the Delahans
made during the planning phase was the choice of construction method. After doing some research, they decided to go with insulating concrete formwork (ICF).
ICF is a modern building method that involves using hollow blocks made of rigid insulation, Expanded Polystyrene (EPS), which are then filled with reinforced concrete. The result is a highly insulated, energy efficient structure that is both durable and quick to build.
“I had first come across ICF on an episode of Grand Designs years before and was intrigued by its potential. I did a bit more research and eventually spoke
to a supplier at a Selfbuild Extend & Renovate Live show. We compared the costs and benefits of ICF against more traditional construction methods like blockwork and timber frame.”
“We found that, at that time, ICF offered the best combination of insulation, speed and cost effectiveness. The specialist contractor we hired was able to get the two extensions up in just a couple of weeks during the lockdown – a timeframe that would have been impossible with conventional block and plaster.”
The insulation provided by the ICF
system was one of the major selling points for them. “With traditional block construction, the insulation is often added as an afterthought, relying on external layers or cavity insulation. With ICF, the insulation is integral to the structure itself, wrapping the house in a continuous, airtight layer. This has paid off for us in terms of energy efficiency. The house stays warm in the winter and cool in the summer, and our energy bills have been significantly lower than they would have been with a less efficient build.”
For the interior, the Delahans wanted to balance functionality with a bit of style. “We used a flat pack kitchen as the base for our design, but we didn’t want it to feel like one. To make it look more individual, we splurged on high end countertops and added brass hardware.”
“The end result was a kitchen that felt bespoke but without the hefty price tag. We had previous experience with flat pack kitchens in a rental apartment we lived in before, and we knew how to make it work for our needs, adding a few custom touches to give it that luxury feel.”
The vaulted ceiling in the kitchen and living area gives the space a sense of openness and light, making it feel much larger than it actually is. “The mezzanine above adds an extra layer of versatility to the space, functioning as a quiet reading nook or a place for the kids to play while still being within sight,” adds Darren. Of course, the renovation wasn’t without its challenges. “During the early stages, when the back extension was being demolished, we were really tight on
Embrace modern methods. Take advantage of the speed and efficiency of modern methods like ICF.
Renovations are messy so, if you can, consider living elsewhere during construction work, especially if you have young children.
“We wanted something that kept the cottage’s rustic charm but still offered the functionality and space we needed.”
space. All three kids had to share one bedroom, with all their clothes and wardrobes crammed in there. It was far from ideal, but we managed.”
“At one point, the other bedroom was completely full of boxes and furniture we had to move out of the way while the work was being done.” For about seven to eight months, they lived in this cramped setup, juggling the needs of the renovation with the demands of everyday family life.
For heating and energy efficiency, they upgraded the boiler to the most efficient model they could source. “It’s been a worthwhile investment, as we’ve seen a noticeable difference in our energy usage. We also opted for mechanical ventilation, which complements the airtight nature of the ICF construction and ensures good air circulation throughout the house. We considered installing a heat pump system, but the cost of integrating it with the existing infrastructure of the old cottage was too high, so we decided against it.”
The decision to invest in the ‘fabric’ of the building – its insulation, airtightness and structural integrity – was one of the best choices they made, says Darren. “These aren’t the most glamorous aspects of a renovation, but they’ve had a huge impact on the comfort and efficiency of the home.”
“I wouldn’t hesitate to recommend ICF to anyone considering a new build or extension. It’s faster, more energy efficient, and, in our case, it allowed us to complete the project much more quickly than we would have with traditional methods.”
Now, several years on, they’re thrilled with the end result. “The house is not only more functional for our family, but it’s also a place that reflects our personality and meets our practical needs. The journey was challenging at times, but it was worth it to create a home that we can enjoy for many years to come.”
2019
granted
Find out more about Darren and Sinéad Delahan’s project in Co Kildare...
ICF system
Amvic Ireland
ICF installer
Daly Construction ICF Contractors
External metal cladding
Litcore Ltd
Electrics and light design
Energise Electrical Contractors
Roof insulation
Pro Sprayfoam
Ventilation system
Lindab Ireland
Kitchen/bathroom quartz
Atelier Stone
Windows
Vent Artic (imported from Poland); front door and sliding doors Reynears CP 155 (imported from Lithuania)
Walls: 350mm ICF system. U-value 0.16W/sqmK
Roof: traditional cut roof with 225mm spray foam insulation. U-value 0.17W/sqmK
Windows: triple glazed, aluclad, argon filled. Overall U-value: 0.75W/sqmK. Sliding doors and front door, all triple glazed, sliding doors 4500mm x 2500mm U-value 1.1W/sqmK, front door and side glazing 2400mm x 2500mm U-value 1.2W/sqmK, sliding doors 4500mm x 2500mm U-value 1.1W/sqmK, front door and side glazing 2400mm x 2500mm U-value 1.2W/sqmK.
Floor: 220mm EPS foam insulation with 60mm alpha hemi-hydrate screed covering.
Overview
House size: 160sqm
Bedrooms: 4
Heating system: Gas central heating
Build method: Blockwork
Cost Breakdown
House purchase price: £165,000
Build cost total: £115,000
(£73,000 build only)
Bathrooms: £6,000
Current house value approx.: £300,000
Emily and Matthew Morgan found the ideal location in Co Down, perfectly located for their work commutes. While the house itself wasn’t exactly what they were looking for, its huge south-facing garden inspired them to take on the challenge of extending and reconfiguring the space to create a home that worked for them.
mily and Matthew were on the hunt for a new home that fit both their work commutes and lifestyle.
With Emily working in Belfast and Matthew commuting to Omagh, they needed something ideally located, and they found it in a village in Co Down.
It struck the perfect balance – not too remote and close to the motorway, allowing both of them to commute to work with ease.
“At the time, there were a few houses for sale in the housing development we eventually moved into,” explains Emily. “One of them already had an extension, which provided an extra bedroom, an ensuite and a walk-in wardrobe. It was spacious inside, but the back garden was a let-down – it was quite small.”
“Then we viewed the house we ended up buying. It didn’t have an extension, but it had undergone a few internal alterations that opened up the space a bit more. The back garden, though, was huge and southfacing. We figured we could build the extension ourselves, in the style we wanted, for the same cost or even a little less than the other house.”
To get started, they enlisted the help of an architectural designer recommended by a friend. He was busy and tough to reach, but eventually, he came out to discuss their plans. The original idea was simply to extend the house, but they soon realised that the house layout had its own challenges, like the stairs coming directly out of the kitchen and the small living room space.
Emily had one major request: a U-shaped staircase. She wanted to create more of a hallway at the front in order to maximise the living space downstairs. Their architectural designer worked his magic and came back with a new design that addressed these concerns. “We looked at it and thought, ‘If we’re going to do the work, we might as well do it properly, all at once,’” says Emily.
However, the planning process wasn’t without delays. “There were no issues once the plans were actually submitted; it was just a matter of waiting for a planning meeting date. All our neighbours were notified, and I don’t recall there being any objections.”
“Once the planners finally met, approval was granted fairly quickly. The only delay was due to the meetings being held once every three months during lockdown. If you missed the
Take detailed measurements with you when you’re buying furniture so you know they will fit the space.
Consider living elsewhere during major renovations, if possible. This allows the work to be completed more efficiently.
submission deadline, you had to wait for the next one.”
When they spoke with their builder Mark, he advised them that living in the house during the renovation would be very difficult. Every internal wall was going to be either removed or moved, leaving the house essentially a shell. So, they packed up their belongings, stored them in the conservatory and moved in with Emily’s parents for a couple of months while the work was being done.
The decision to move out turned out to be a blessing. Mark was able to work efficiently without the need to constantly adjust for their living needs. As Emily puts it, “He just came in, disconnected everything and got to work.”
The renovation wasn’t just about adding space. The couple’s home underwent a complete reconfiguration. The downstairs bedroom, which had an ensuite and is now the gym, saw the least change.
“We moved the door and modified the front window; it was originally almost like a bay window, but we brought the wall forward and made it flat, then skimmed the inside,” says Emily.
“In the original layout, the kitchen had French doors to the left, leading into the conservatory and the kitchen window opened into the conservatory also. It felt quite closed off when cooking, with no natural air.”
“So, we relocated the kitchen window to the far side and blocked off the original French doors, moving them to the other end. This allowed us to create the U-shaped kitchen we have now. Before, it was more of a galley-style setup. Aside from the conservatory, everything else was taken back to the
timber frame.”
“The original upstairs layout of the house included a small double bedroom and two very small box rooms next to each other. When we moved in, we decided to knock down the partition wall between the two box rooms to create a larger space.”
“As part of the renovations, the small double bedroom was also expanded. Now, we have four generous doublesized rooms instead of the original setup, allowing us to maintain a four bedroom layout while significantly improving the size of each room.”
One of the standout features of the redesign was the U-shaped staircase that Emily insisted on. To accommodate the stairs, the internal walls had to be shifted slightly, which created a much more open and welcoming atmosphere. Thanks to Mark’s skills as a joiner, he was able to build a bespoke staircase that fit perfectly in the space.
The extension kept the same style as the original house. “All the houses in the development are timber framed with block and rendered exteriors, so we followed the same approach, obviously adding steel supports to handle the extra weight upstairs.”
“We kept the style consistent with other homes in the area, using pitched tiles and matching windows. The windows are double glazed and we also installed a triple glazed front door for better insulation.”
Throughout the process, the builder, Mark, proved to be a godsend. Despite
initial concerns about working with a self-employed contractor, Emily and her husband found him to be knowledgeable, flexible and reliable.
“Nothing seemed to be too much of a problem for him,” Emily recalls. A skilled joiner, Mark brought in subcontractors as needed but handled the timber framework himself, ensuring everything was done to spec.
When it came to the interior, Emily and Matthew knew exactly what they wanted. They envisioned a
sleek, minimal almost industrial look, particularly for the kitchen. Clean lines, a handle less design, and high tech, touchscreen appliances. They also chose an angled cooker hood with a touchscreen instead of a downdraft extractor.
For the living area, they bought an oversized L-shaped sofa. But it wasn’t all smooth sailing. One of the lessons Emily learned along the way was the importance of double checking measurements. They nearly bought a single chair to go with the new sofa, but after measuring the space in the house, they realised it wouldn’t fit. “Always bring your
What is your favourite design feature?
Our favourite design feature is our open plan kitchen living and dining as it allows us to host people and socialise whilst preparing the meals. The biggest splurge was the new kitchen with granite countertop at a cost of £17.5k.
What would you change or do differently?
The only thing we would change if we could go back would be to level the living room floor as the previous floor was glued to floorboards which left it uneven in places.
surprised you?
How little guidance or resource availability when starting the project, e.g. which architects are recommended, what the process would look like, timings and costing of everything outside the builder’s cost. We felt quite lost through some of the process but our builder really kept us right once he started.
What single piece of advice would you give someone who’s doing up their house?
Plan it well. Have an idea what style or materials you want to have. Honestly, parts of the decisions throughout the process are overwhelming, colour, shape, style, material, layout, what way for the doors to hang. Think it through and if you don’t know go to plenty of shops and look at what’s out there.
Would you do it again?
Do it again? Never, we are never ever moving now.
measurements with you,” she advises.
The renovation also included updates to the bathrooms. “We now have one family bathroom and two ensuites,” says Emily. “We didn’t change the ensuite downstairs, but we did extend the main family bathroom slightly by taking a bit of space from the main ensuite to fit a bath into a small alcove.
“Choosing the sanitaryware was tricky – there are so many options for toilets: rimless, narrow base, wide base, standard. At one point, I felt overwhelmed and didn’t know what to pick anymore.”
“Matthew suggested we go with a rimless toilet with a shallow cistern that sits closer to the wall. We also splurged on a slipper shaped bath and a freestanding tap for the main bathroom.”
“In the ensuite, we opted for a walk in shower, also with a shallow cistern, and countertop sinks. Finding the sinks was easy, but sourcing units that worked with countertop sinks was more of a challenge.”
“Eventually, we got everything in a sale. Altogether, I think the cost for the bathrooms was about £6,000.”
Lighting was another area where Emily had strong preferences. While they initially wanted a statement light in the living room, they ended up focusing more on functionality with LED spotlights in key areas. However, they did add a feature with a three pendant dropdown light over the U-shaped staircase, giving it a bit of character.
But not everything went according to plan. “One unexpected challenge was the need to relocate our underground NIE metre box, which we hadn’t anticipated. It wasn’t until near the end of the project that the builder mentioned, ‘To move your metre box, you’ll need to relocate your unit. Have you submitted the necessary paperwork for that?’ This delay set us back about eight weeks. We had to dig a trench to indicate the current location of the box and prepare the new site. Then, NIE had to come out to complete the move for us.”
“Also making decisions on fixtures, finishes and materials became overwhelming at times. “By the end, we were just frazzled,” Emily admits, especially when it came to things like picking out the flooring or wall colours.
Now that the renovation is complete, Emily and Matthew couldn’t be happier with the results. The house
flows much better, with a layout that makes sense for their lifestyle. The previously cramped landing upstairs has been replaced with a more open space, and the living areas downstairs feel much more spacious.
“Whenever anyone visits, they all comment on how inviting it is. You enter the house and can go straight upstairs to a small landing. Previously, when you went upstairs, you had to choose between going left or right, and there was no landing in front of you.”
“The usable space has definitely doubled,” Emily says. What started as a house with some awkward design elements has now become a home that reflects their style and needs.
As for the future, landscaping is next on the list, but they’re taking a break from major projects for now. With a quote of £13,500 for the garden, they’ve decided to wait a couple of years before tackling that.
October 2016
Purchased house
February 2019
First engaged with architectural designer
March 2021
Planning permission applied
April 2022
Planning permission approved
July 2022
Work started
November 2022
Work finished
Find out more about Emily and Matthew’s project in Co Down...
Architectural designer (John) Simpson Design NI, mobile 07845 588073
Contractor Mark McKibben, M.M. Construction, mobile 07743 816969
ROI calling NI prefix with 0044 and drop the first 0
New upper storey walls: U-value of 0.28W/sqmK
Roof (between rafters): 100mm PIR board between rafters, 50mm PIR under, U-value 0.18W/sqmK
Windows: uPVC with double glazed unit 16mm gap, argon filled and low e glass, U-value 1.6W/sqmK
House size before: 118sqm
House size after: 280sqm
Extension build method:
blockwork full fill insulation in cavity wall
Heating: air to water heat pump
Ventilation: centralised mechanical with heat recovery
BER after: A1
Build cost: €550,000 plus purchase of original house
When your job is to design dream homes, it’s difficult to come up with the perfect plan for your own. Mark Davies of Greystones, Co Wicklow chats about how he and his wife Elis managed to come out the other end a happy client.
Elis and I renovated and extended a 1905 house in the heart of Greystones, completed with the help of the Sustainable Energy Authority of Ireland (SEAI) Deep Retrofit pilot scheme.
We entirely gutted the house and kept two walls standing. It was a blank canvas, which in many ways turned out to be a curse as there were so many ways to configure the house. It was also a very busy time as we had a young child at the time we went for planning permission.
On the design team was myself, a quantity surveyor (QS) Russell Lincoln, and a friend and architectural designer, Garry Cohn. Elis and I both wanted to keep period features and stay true to the house’s original design. The question was more about what to do with the modern extension at the back, and
how to reconfigure the layout.
My previous house build was more straightforward than this one, in that there weren’t that many options in terms of design; it was a mews house on a small plot. I learned from the mistakes I’d made on that project, namely that the kitchen should have been bigger.
And in terms of finishes, we’d left a brick wall exposed but we should have plastered it for ease of maintenance. I have to say I was very conscious of getting everything
absolutely right on this house and I got myself caught up in it.
At this point I relied heavily on Garry’s advice. I brought him on board because I quickly realised that for our forever home, I couldn’t be both client and designer.
Garry brought clarity to the many different design variations running around in my mind, at a time when I was second guessing everything.
I was afraid to make a mistake I’d regret and I wasn’t enjoying the process so he helped a lot at that point, and thanks to his advice we were able to attain the design character I was after, on a budget.
At the start I worked very closely with the QS, before lodging the planning permission application. He did a full bill of quantities and the original costing he brought back was way too high. So we did a redesign based on his costing advice. It took two or three goes to get the design within a budget range I was happy with.
To get there we reduced the house size, removed a lot of the cantilevers I had originally included and reduced the amount of glazing in the extension, especially the corner glass units which are very dear.
The initial costings were just for the shell and core, meaning there were only basic finishes inside (we moved in without a kitchen), no landscaping done, no joinery items. We wanted a certain level of finish on the house and knew we couldn’t afford to do it all in the one go so we did it all over a period of a few years, and now it’s done.
In many ways it’s a more difficult way to go about it but it’s also more fulfilling.
The acers add colour
Don’t rush. Once you get on site, it all happens very quickly so spend the time to think of how you want everything to be finished. Our interior architect Garry helped a lot with the interiors which has knock on effects on the way you build and configure the house. Getting spaces right for furniture placement is important.
Let the builder take on the superstructure. I’m involved in the trade but it was still a big learning curve taking on subbies; my advice is to let the builder do the whole superstructure, leave it within his remit to hire the subbies. Especially considering you need to get the insulation and airtightness right, and it’s not that straightforward to do. You can take on finishing items like the kitchen, floor finishes, bathrooms. It’s not going to save that much to go direct labour for the main structure of the building; you might even be paying more if you don’t know the sequence of works.
Also as this is my home, it’s a great business card for my architectural business to future clients, so they can see what kind of design and finish they can attain.
Planning went very well. The problem we came across was more to do with the foundations. Because the plot is sandy, we had to engage with a ground investigation company to determine what to do. They drilled holes three metres deep, did impact tests, all so we could get the foundations poured.
The first two metres were too sandy but
further down the ground could take the weight for the extension so we filled the whole perimeter with concrete (trench fill) with a lean mix to a certain point then standard concrete foundations to take the walls of house. This swallowed up our contingency, it cost €15k more than what it should have been.
The old house is just sitting on stone on the sand and we left that as is.
I took on the role of the project manager. Because I knew who I wanted to build our house, using the same builder who’d built the mews, I waited a year for them to be free to work on this project.
The main contractor would normally take on the entire build but I took a lot from them. I organised the windows and subcontracted the plumbing, electrician and so forth. They had to tie in with them but I was here every day to keep things running smoothly.
Contractors wouldn’t usually allow this, and I did use most of their subbies, but as I had a working relationship with them, they were happy for me to organise the first fix trades – I just had to make sure it met with their programme of works.
The only issue I came across was with the plasterer, as I hired my own even though the builder had his own. I should have used theirs as mine wasn’t meeting deadlines, and held up the schedule when it came to roofing and putting in the downpipes.
When it comes to designing your dream home, choosing the right heating solution is paramount. With sustainability, efficiency and comfort main priorities for self-builders, the new Grant Aerona R290 air to water, air source heat pump is set to be a standout choice for new builds this year.
We caught up with Barry Gorman, National Renewable Sales Manager at Grant to find out more about this next generation heat pump.
“The Grant Aerona R290 represents a major step forward in highly efficient, environmentally friendly home heating technology. The heat pump uses R290 refrigerant, a natural, energy efficient alternative which has a remarkably low Global Warming Potential (GWP) of just 3, compared to traditional refrigerants such as R32, which is being phased out of use in heat pumps. For eco-conscious self-builders, this aligns perfectly with the goal of reducing environmental impact while embracing renewable energy solutions.
Boasting an A+++ energy rating at 35°C water flow temperature, the Aerona R290 delivers exceptional performance and energy efficiency, with Seasonal Coefficient of Performance (SCOP) values of up to 5.02. This ensures maximum heat output for minimal energy input, which is vital for meeting today’s stringent energy standards under building regulations.
Barry continues, “At Grant we understand that no two homes are the same, and the Aerona R290 caters to this reality. With five single phase models offering heating outputs ranging from 4kW to 16kW, there’s a solution to fit the specific heating and hot water demands of any new build. Whether you’re building a compact starter home or a spacious family residence, our team of technical specialists can help ensure you have a correctly sized and specified heat pump. The Aerona R290 can also be carefully combined with other Grant technologies including hot water storage, underfloor heating and / or aluminium radiators and smart heating controls to deliver a fully tailored integrated heating solution to suit both you and your homes requirements. This process is done as part of our free home heating design service.
As well as high efficiency the Aerona R290 is aesthetically pleasing with modern, sleek, powder-coated black casing. All units within range are approved by Quiet Mark due to their impressive ultra-low noise levels, and for convenience they can also be managed and monitored remotely using the Aerona Smart Controller.
This controller also allows installers to offer diagnostic support remotely which provides additional peace of mind.
By installing a new Grant Aerona R290 heat pump, homeowners can not only ensure their home meets all required compliance under building regulations but also ensure that their home heating is prepared for the future”, added Barry. Designed in Ireland, specifically for the Irish and UK climate, the Grant Aerona R290 heat pump has already been recognised for its Outstanding Innovation at a recent industry awards ceremony. More than just a heating solution, the Grant Aerona R290 is a forward-thinking investment in sustainability, efficiency, and comfort, whether you’re focused on reducing your carbon footprint, cutting energy costs, or ensuring compliance with future standards.
Take advantage of Grant’s free home heating design service by sending house plans and choice of heat emitters (underfloor and/or radiators) to heatpump@grant.ie / heatpump@grantni.com
I learned a lot from our previous house, about the nitty gritty, the sequence of works like when the steel has to go in, and how much everything cost. It’s one thing to draw it on the plans but quite another for it to happen on site; the ceiling goes in before the floor, that kind of thing, thinking more like a builder than an architectural designer.
I organised everything from a building control point of view, filing the commencement notice. If I were building today I would have opted out of appointing an assigned certifier as that’s the way to go when self-building.
In terms of health and safety we had the inspectors come here, who issued instructions before we could continue on site. We had the scaffolding ticketed, but their concerns had more to do with producing the reports relating to Project Supervisor Design Stage (PSDS) and Construction Stage (PSCS).
Even Revenue showed up to make sure everyone was on the books; I think it’s because our site was so exposed, near the local supermarket, that we got so much attention.
We had to achieve a minimum building energy rating (BER) of A3 to get the grant; we got to A2. And with the solar panels we recently installed we’re now A1.
Like the One Stop Shop grant system that’s in place now, the deep retrofit grant paid for half the costs, so €60k in grants, but only on the original house. This included windows, heating system (heat pump with underfloor heating), insulation, ventilation.
It was the pilot scheme and this entailed using a registered energy company to compile the report and the application, and to monitor the build. We had to do external wall insulation on the existing house and could have done it on the extension but the cost was prohibitive so we went with cavity wall insulation there.
Overall it was a stressful process, mostly because we were one of the last ones to get in on the pilot scheme. This was the
February 2017
Bought house
August 2018
Planning applied
September 2018
Planning approved
October 2018
Planning approved and build start
December 2019
Moved in
February 2020
Kitchen installed
2021
Fit out finalised
time they cancelled it, and we’d started the works on the basis we’d get the grants. Fortunately, they brought the scheme back in for applications that were in.
We’d put all the requirements in to obtain the grants, which was costly and wouldn’t have been within budget without the grants. Because they only paid money out at the end, it was stressful enough from a cashflow point of view.
We should have done the solar panels then, as we would have gotten a subsidy,
but our budget didn’t stretch at the time. We put in 24 panels with 20kW battery storage since then, and our electricity bills have come down dramatically.
Elis had a big input into finishes; I also had my ideas, so instead of us fighting I asked Garry to act as a mediator. Since we moved in, we added a TV unit, floating stairs, renovated the attic with ensuite bedroom, got all the garden landscaped including mature planting, we also put in a walk in wardrobe for the master bedroom, got a headboard, repainted rooms, added furniture.
We also invested in decorative lighting and house furniture, which we got shipped
over from two stores in Madrid. We found a shipping company that collects from the store and brings it over by boat – we saved 40 per cent as compared to a high-end store we were looking at in Dublin, taking into account the shipping.
The fibreglass flat roof makes noise – when it heats up, it cracks so you get banging from it that’s quite loud. It settles down after a few years. But honestly, I can’t fault it; the design is delivering everything I wanted from the house and I really appreciate it all, especially after the effort that’s been put into it.
Walls: 150mm full fill cavity (PIR board), outer block 100mm, inner block 215mm
Floor: ground floor 150mm insulation on top of structural slab with 50mm liquid screed containing underfloor heating pipes, concrete precast first floor with underfloor heating pipes with 50mm liquid screed
Roof: timber warm flat roof with 150mm insulation board and fibreglass roof finish
Design
Arc Design, arcdesign.ie
Interior designer Garry Cohn, cohndesign.com
Structural engineer
Terry Sweeney, gnce.ie
Bathrooms
Villeroy and Boch sanitaryware, idealbathrooms.ie
Air to water heat pump Veissmann
Ventilation (MVHR) Brink, greenoakenergy.ie
PV panels
Solar Solutions Ltd
Astrid
Madsen outlines
the first phase
of renovating her bathroom,
with a special focus on the nightmare that was finding the right tiles.
When we first did up our house 10 years ago, we put in a brand new bathroom downstairs.
Complete with wall hung toilet and panelling. We also went with a polished lime plaster finish, our plasterer’s version of tadelakt, for the shower wall.
We did not, however, put in a shower curtain, which has led to inevitable water damage. The plaster finish wasn’t working at the junction between wall and mosaic tiles, meaning the time had come to reconfigure that section of the bathroom.
The floor tiles in the rest of the bathroom were slippery from the start, so their days were numbered too. We’ve had no falls but plenty of near misses.
While we were at it, we figured we might as well add underfloor heating – the space is small, so a timed, electric cable system would do us. My thinking is if the bathroom is warm and inviting, the kids will kick up less of a fuss to go have a shower.
When we originally did the bathroom, we put in a thick layer of clay bead insulation under a limecrete floor. This will be plenty to stop the heat from going into the floor instead of into the room.
My only concern here is having to level the floor for the new large format tiles. I’ll let you know how we get on with that in the next instalment.
We started off by gathering inspiration online, then visiting every showroom that was nearby. Not as easy as it sounds when your weekends, (well, the kids’ weekends), are filled with sports and playdates.
One idea we picked up was to include a high shelf with plants on it, over the basin. And incorporate gold brassware, dark
cabinets and timber effect wall tiles.
Unfortunately, we quickly realised that inspo images online are, more often than not, unattainable. Compared to when we last renovated, the situation doesn’t seem to have changed all that much.
There is a bit more choice but not that much. Yes, I know Ireland is an island
and it’s not easy to get things here. But it’s still a shame to realise anything that’s not standard is still very hard (read expensive) to get.
After all of that shopping around, we had a chat with a bathroom specialist, via video
link, to discuss our plans in detail. That was really helpful in determining what we could and couldn’t do. It also focused our minds on what kind of finishes we wanted and the overall aesthetic.
Even though there were quite a few follow up emails to clarify things, of my doing, I have to say this bit was by far the easiest. One reason was that I had the peace of mind that the finishes would be good quality and that everything we were getting would fit and work well.
We’d bought some stuff online before for the bathrooms, when we initially did up the house, and wouldn’t do it again. Getting expert advice and guidance really pays off. Plus we’ll be able to rely on our bathroom consultant’s expertise during fit-out, if any questions arise. I’m sure I’ll have a few.
It would have been great to hire a builder but cost was one issue. The other is not knowing any. And even if we did, I’m not sure they’d be available to take on such a small job.
Unfortunately, our bathroom specialist didn’t have the tiles we wanted, which was a warm timber wood slat effect for the walls. We felt that was the best way to tie in the concrete/grey finish of the existing bathroom with the new dark cabinets and gold fixtures.
We found a timber effect tile online that fit the bill and ordered in a sample, well worth the €20 courier fee (samples are free). It was fine but we kept going to showrooms and stumbled upon a tile that I fell in love with. However, the colour was too light for what we had in mind. We still got a sample.
I have to allow myself a rant here in that I found the exact same tile in Spain, in the right colour (it comes in multiple shades), for a fraction of the price we were being charged here (€30 per sqm versus €53 per sqm here). The glitch was the courier cost to get 10sqm of heavy tile shipped to Ireland (€280 excluding VAT).
When I enquired with the showroom where I found the light colour, I was told there was no way to get the darker shade. I suspect the way it works is that they have a certain stock they have to get rid of before they can start ordering anything else.
I rang every company that stocked that brand of tile in Ireland, both north and south of the border, and they all said they didn’t have it in stock. Some offered to bring them in but the courier cost of hundreds of euros was going to apply no matter what.
One quote was for £40/sqm plus £200 for shipping, making it more expensive than shipping directly from Spain. A place in Dublin quoted
€78/sqm plus €120 consignment charge for it being a small order, plus €80 delivery.
When you are shown a tile, the salesperson is unlikely to give you the make or model. Just ask for more images of the tile, pictures of it in an actual bathroom, and do a reverse image search online. This will give you the information you need (model and make) to shop around for the tile of your choice.
At this point we circled back to the light coloured tile and somehow the quote came back way more expensive (€830 including grout and adhesive).
Back to square one and we went with the initial wall panelling tile at half the cost, providing the warmth we need at the right price. And the people I dealt with there made me happy with my choice; it’s difficult dealing with salespeople who seem to only be concerned with extracting as much money out of you as they can.
Case in point is the fancy showroom in Dublin where we bought our floor tiles; light tiles with a warm marble effect which are lovely and certified slip-resistant. Unfortunately, the overly friendly salespeople ended up giving us too much product for the area we needed to cover.
So do check that you’re only getting an extra 10 per cent of tile (if a tile is accidently broken or cut the wrong way). I’m still fuming over my own mistake, which was not double checking the invoice for the amount of tiles being supplied.
In my defence it was all quite cryptic and I figured they knew what they were doing – so the lesson there is always query anything that isn’t crystal clear. And, as if I needed reminding, it never pays to rush. Quite the opposite.
The restocking fee, i.e. what we would be charged for them to take back the unused tiles, is 20 per cent.
Bathroom specialists: Bassetts Bathrooms, bassettsonline.com
How much will it cost?
A project of any magnitude begins with a budget.
And we gave ourselves a target of €5,000 including paying for the tiler and electrician, as well as buying the underfloor heating, new wall cabinet, vanity with tap, new basin and shower fixtures. Plus the tiles.
At the start, the world was our oyster and we toyed with the idea of installing a fluted glass partition with gold finish. But, because the space was so tight, it just wasn’t going to fit. And when we priced it, we realised it was completely outside of our budget anyway – at well over €1k.
To save on costs, the hubby and myself are doing the grunt work, as in rip out the existing units and floor, making good for the tiler and electrician to come in, and building the stud wall with niche in it.
The hubby will be plumbing the new shower valve too, and the tap.
In the end we spent about €3,000 on the fixtures and fittings, and about €500 for the wall tiles and trims (includes VAT and delivery), and €500 for the floor tiles including VAT. We have the electrician and tiler left to pay, plus bits of materials to buy like lengths of timber.
What we didn’t realise is that tilers charge quite a bit more for large format tiles; the reason is that it takes two tilers to do the job rather than the one.
This large
garden
in Co Galway had to deal with rocky site conditions; Anne Byrne explains how she turned what was an open field into a family garden.
When a new home has a very extensive outdoor space, it can feel overwhelming to turn it into a functional, manageable family garden.
You need to be able to think on a fairly large scale, and in practical terms, while paying attention to detail and making sure the home and garden sit well together.
It makes sense to divide a large garden into several areas. This can make the scale feel more human and make the space feel more inviting. In this case, the homeowners needed plenty of lawn for playing, seating areas, a kitchen garden and different kinds of trees. The design is broken up as follows:
Driveway: A long driveway connects the front gate with the house itself, so flowering cherry trees will be used to create an avenue of blossom and autumn leaf colour alongside.
Shelterbelts: Native willow, alder and silver birch will be planted closely together in strategic spots to help form shelterbelts and provide respite from strong westerly winds.
Wildflower meadow: An extensive area will be given over to a meadow of native Irish wildflowers, with a mown grass path leading through the meadow to a rustic seat. Not only will this reduce the amount of lawn mowing, it will also provide a much-needed habitat and larder for birds and insects of all kinds, whose presence in the garden will contribute to a healthier ecosystem and strong, healthy plants.
Lawn areas: In one of the lawn areas, some of the larger limestone boulders will be arranged into a circle for the children to play with, reminiscent of the ancient stone circles that can still be found throughout Ireland.
Seating area: The main seating area for outdoor dining is located to the rear of the house, accessed by glass sliding doors. As the front gets evening sun, a more informal area with bench or lounge style seating will allow the last rays to be enjoyed in comfort. A paved light grey sandstone circle will be surrounded by pebble to suggest a relaxed atmosphere, with carefully selected limestone rocks from the site placed here and there and interspersed with plants.
Firepit area: Continuing the circular theme, a firepit area will be located a little distance away from the main seating area, surrounded by a curved beech hedge for shelter. Here, an inner curve of plants in hot colours will wrap around the circle of Adirondack chairs, lighting up as they catch the setting sun. Sunny rudbeckia and flaming helenium combine with the blazing leaves of Berberis ‘Atropurpurea’ to bring visual warmth to the outdoor fireside.
Although located in Co Galway, this area forms part of the Burren lowlands
with an abundance of limestone rocks throughout the site, above and below ground, making it typical of the surrounding landscape.
Fairly close to the coast, the soil here tends to be sandy and free draining, providing an ideal home for plants that thrive in Mediterranean climates and rocky conditions.
Although the climate, sadly, could never be confused with a Mediterranean one, frost and snow are uncommon and harsh winters few and far between, so once these plants enjoy good drainage, they tend to be very happy.
Planting here includes shrubs euphorbia characias and cistus for structure, with spiky libertia grandiflora and softly waving stipa tenuissima providing contrast.
Aromatic salvias, members of the sage family, adore these conditions and bring brilliant crimson and violet colour all summer, along with the native wild oregano, which grows alongside hedgerows hereabouts.
Grey leaved stachys and artemisia offer interesting, sensory foliage and work very well alongside the grey tones of the limestone.
Keep the rocks. Removing large rocks from the site can be costly, but if you’re keeping them in the garden, plants will soften and greatly enhance their appearance, turning them into a feature rather than something you’re stuck with.
Zone the space. Extensive gardens can be made to feel more inviting by dividing the space into different zones, making each section feel more human in scale.
Think big. Remember to keep planted areas generously sized – most mixed planting is great for wildlife, and if you use the right plants, a large bed or border is as easy to care for as a small one and will make a much greater visual impact.
Planted borders and bench seat
Stepping stone path
Limestone rocks/planting/sundial
Grey sandstone circle
Beach pebble
This project on the Isle of Skye showcases what’s on offer from HebHomes, a high-end kit house supplier that’s recently launched in Ireland.
Tell us about the client’s brief and how HebHomes met it.
The clients wanted an open plan house that fitted the vernacular of the township, took advantage of the stunning views, was very energy efficient and cheap to run, but was also a practical family home.
This house was part of the HebHome’s range of architect designed houses. We amended the original design to suit the site and meet the client’s brief, such as making the downstairs bedroom larger. In this case we also removed the door from the hall into the kitchen to make the entrance more open plan, and removed the cupboard at the end of the corridor, creating a display for the clients’ art.
Having an architect designed kit house saves substantially on architect fees and overall costs. However, the result still feels like a bespoke architectdesigned house.
What was the building process like?
This was a HebHomes ‘turnkey’ service. This means our company obtained planning permission and building warrant, organised all the consultants, as well as supplying and erecting the kit.
We also used our local affiliated contractor to complete the build. The only consultant
we did not organise was the independent quantity surveyor, who also acted as the contract administrator during the build process.
How much did it cost? It was likely to have been over £350,000.
Spray foam insulation has been on the market for over 60 years and is the most effective form of insulation, providing a lifetime of insulation and airtightness for the comfort and longevity of your property.
However, spray foam insulation in the UK has received a lot of negative reviews in various media. In addition to this, some lenders have stopped lending on properties with spray foam installed due to a lack of understanding of the products used and a lack of availability of paperwork for the installation. Fortunately this situation is beginning to ease as surveyors and lenders learn the difference between open and closed cell foam, and paperwork and installation inspections are now
available
There is also now plenty of advice, information and support available from manufacturers, distributors and The Insulation Manufacturers’ Association (IMA).
The problems that arose with spray foam was as a result of shoddy operators applying non breathable closed cell foams directly to the underside of slates and tiles as a waterproofing and roof stabilisation solution.
The problem was that these roofs were already failing and were in no condition to receive spray foam and this resulted in the trapping of moisture which expediated the failure of the roof. Unfortunately the media, lenders and a number of property
“Our product range is a superior insulation delivering up to 50 per cent more energy efficiency...”
GMS Insulations Ltd is also the distributors of SprayCork by CorkSol, the sprayed cork coating that’s an ideal solution for traditional renovation systems.
• Spray breathable, flexible, weather resistant, CorkSol’s SprayCork is an insulating coating for commercial and domestic buildings.
• SprayCork comes in 28 different colours and provides a fresh new look to your property in addition to providing a weatherproof coating.
• Solving cracked renders, it also adds insulation value to your building and can also be installed internally to eliminate mould, mildew and dampness issues.
• SprayCork is also a suitable product for companies who use industrial coatings and recover old asbestos sites.
• SprayCork has tremendous benefits, but it does require a professional installation. GMS Insulations Ltd is assisting painters, plasterers and renderers with advice and training, to achieve CorkSol certification.
associations has taken a blanket approach to spray foam in general and have ignored the huge numbers of foams properly applied to roof membranes and felts the majority of which is open cell.
Do note that this issue of applying closed cell foams to failing roofs is only applicable in mainland UK as these applications have not taken place in Ireland or Northern Ireland, where the vast majority of applications are open cell foams safely applied to roof membranes and felts.
GMS Insulations Ltd
+353 87 2394962 / +353 49 4335057 / 1800 98 98 90 info@elastochem.ie / elastochem.ie
“Since 2004, GMS Insulations Ltd has completed around 150,000 spray foam applications in the UK and Ireland with almost no issues.”
Your checklist to ensuring your spray foam installation is a successful one:
• Only use a well-recognised brand like Elastochem, avoid generic spray foams
• Make sure the product has full Agrement certification like KIWA, BBA or NSAI to the applicable building regulations
• Check that the installer is registered and approved by the manufacturer or distributor and is fully trained
• Make sure the installer has a full quality management system in place in accordance with the manufacturer or distributor
• Make sure the installer is part of a third-party approval and monitoring scheme
• Insist on a full homeowner pack which will include but not limited to pre-installation survey, information on the product used, product certification, U-value and condensation risk analysis, before and after photos, attic notice, product warranty
Formed in 2004 GMS Insulations Ltd, a family-owned business, has a long successful history in the distribution of spray foam insulation products. GMS Insulations Ltd is now sole distributor for the Elastochem range of products from Canada (elastochem.ie and elastochem.co.uk).
Like Elastochem, being a family-run business means trust and integrity are at the heart of everything GMS Insulations Ltd does. “We’re not just here to provide products; we’re here to build lasting relationships with our customers,” says managing director Gerry Sheridan.
“Count on us for personalised support and service every step of the way. With over 150,000 applications you are in safe hands with GMS. Elastochem has been making, distributing and selling quality products to their worldwide customer base and beyond since 1987.”
The GMS Insulations Ltd product range includes open cell spray foam insulation which was specifically developed for residential properties and this breathable product allows all your building materials, including timber, to breathe naturally.
“Our product range is a superior insulation delivering up to 50 per cent more energy efficiency due to its ability to fit all shapes and sizes and its excellent air sealing properties,” adds Gerry.
The open cell product which is fully KIWA BDA Agrement certified to building regulations is suitable for wall drylining, sloping and flat roofs and raised timber floors and comes with a 25 year guarantee.
In addition to spray foam, GMS also distributes a range of polyurea and silicone waterproof coating products for roofs, and wall waterproofing including asbestos encapsulation.
I enjoyed the article on PV batteries in the latest magazine.
We installed solar panels a few years back in our current
home, with a battery, and I’m currently seeking quotations for a system in our new build. I was surprised to see mention of lead acid technology but no reference to LFP, the technology most installers provide. A figure of €13,500
for a 5kWh battery seems very wide of what’s on offer in the market. I also wonder why there was no discussion of the concept of using off peak electricity to charge the battery which is then used to run the house at peak hours. Perhaps consideration could be given to revisiting this battery topic again in the future. Wishing you all the best.
To address the queries, the scope of the article was batteries for solar PV rather than for domestic use in general, and LFP is a type of Li-ion battery which was mentioned in the piece. Also, the costs used are from recent published sources.
This was an op-ed and is my opinion on the current situation – that may change in time due to reductions in equipment costs and, perhaps, increases in electricity tariff rates.
I did mention that costs
would vary according to whether the batteries were being newly installed and also what type and capacity and that people should do their own cost benefit analysis based on their own particular situation.
Lastly, connecting the batteries to the grid would require additional signal conditioning and grid synchronisation equipment, which would increase capital costs.
Patrick Waterfield Independent energy consultant
Get
Building is very expensive at the moment; what are your tips to reduce
Different experts that were at Selfbuild Extend & Renovate Live Munster are probably best equipped to answer that question.
We had mortgage providers saying that as a rule of thumb they won’t lend to self-build projects that are coming in at under €1,600 per sqm for a builder’s finish (€154 per sqft for direct labour or €179 per sqft for a contractor led build for one lender), meaning to a finish where the house is weathertight (no kitchen or finishes). We heard many figures bandied about for the cost of building a finished house and this brought the figure closer to €2,000 to €3,000 per sqm, which in large part seems driven by a lack of builders. DJ Rasdale of DJ Build Estimations says that you can expect to pay trades €30 to €40 per hour, and he’s seen blocklayers charging a whopping €3 per block.
Lenders tend to revise the
cut-off below which they won’t lend every six months; 10 years ago, the cut-off figure lenders had in mind was €900 per sqm.
Even though material prices are still high, they seem to have stabilised, according to DJ. However, he says, labour costs continue to rise, simply because there’s a shortage of skilled labour. For this reason, there’s a shift to modular construction whereby you have sections of walls already made craned into place.
We heard from the likes of iDomus (mass timber building method) and EcoCocon (straw bale modular building method) who confirmed this, saying that on some projects they were coming in more cost effectively than blockwork.
Back to DJ and he was saying that going direct labour, that is managing the
tradesmen and build yourself, is likely to save you on average 20 per cent of the build cost. That’s where most contractors seem to be nowadays, some will charge more, others less. Contractors will also charge more if there’s anything unusal or complicated about either the site or your design. He did say that this comes with a health warning; do factor in the time it will take you to manage the project (unlikely to be feasible if you have a full time job) and the cost of making mistakes - a good builder will know what they’re at. They’re also likely to deliver the project more quickly, which could be a saving for you too.
In general, savings can often be made by sticking to your budget; for example, it’s very common to start with a reasonable kitchen budget and end up paying double that amount because you decide you want a nicer finish.
In terms of house size, DJ made the point that you need to shave off quite a bit of sqm to see a reduction in the total build cost - a few sqm might not make a lot of difference to the bottom line yet could negatively affect the design.
Do you profile projects that are happening now?
I recently 3D printed my house design to get an idea of the layout and shape of the house. This helped us in our decision making, so I thought I’d share the images as it’s something that might interest other new homeowners designing their home.
Conor Traynor
I read through the Laois Build on a Budget and it was built before Covid. Absolutely irrelevant to the times we are living in now. I would like to see a build completed this year “on a budget”! Does one even exist? Probably not.
We feature different types of projects and the one you refer to was professionally photographed and featured in Selfbuild magazine; these tend to be older because we wait for the homeowners to have lived in the house for at least a year to share their insights on how it’s worked out. Many homeowners also prefer to wait for landscaping to do be done before we photograph so this can delay things further. For current projects, which include costings where homeowners have shared them, see our Homeowner Diaries series (scan the QR code) for current house builds. These tend to be on a budget also, but as you point out costs have risen since Covid.
Keith Kelliher Quantity surveyor, adjudicator.ie
Q: What way are material prices these days? Will they ever come back down?
The Society of Chartered Surveyors Ireland’s latest construction tender price data at the time of going to print was for the first half of 2024. In that report the SCSI outlines that tender prices increased by 1.5 per cent.
Whilst many seek to highlight material prices dropping, what is clear on the ground in construction is that whilst prices are generally not running at the high increases that they once were, there is no evidence that they are dropping and are at best just levelling off.
In some respects, they continue to rise with increases still occurring in plasterboard, concrete and stone products. In the 12 months between June 2023 and June 2024, the Central Statistics Office wholesale
price index, which measures movements in materials costs, shows plasterboard increasing by 3 per cent, insulation by 2 per cent, concrete by 11 per cent and blocks by 11 per cent.
We do see costs falling in timber products, including plywood, and in steel but given the heights those products reached in the period post-Covid, it is not surprising that we see downward movement there. But the magnitude of the decrease is not coming close to the increases of the past.
Many in the market question why materials costs have not gone down at the counter in the various builder’s merchants. Very often shipping and transport costs are given as the reason. Both are still high in relative terms to what they once were
but at the same time we see the highest recorded profits across the majority of the builder’s merchants in Ireland which would raise questions as to the real reasons behind the slow pace of material cost reductions. It should be noted that the picture in Ireland very much appears to mirror that in international markets with costs in construction continuing to rise. The question around if we will ever see material costs reduce is one akin to having the power to guess the lottery numbers, but the reality is that there is no sign that they will in the medium term. Sadly,without a reduction, constructing one’s dream home will for many, not become a reality.
There is no evidence that material prices are dropping, they are at best just levelling off...
Introducing the Litcore Nordic Niagara Guttering System –now enhanced with a unique hidden system option! The strongest guttering system on the market just got a stunning upgrade. With our sleek gutter fascia and soffit covering, your property will not only be protected but also transformed with a clean, modern aesthetic. Perfectly tailored for domestic and commercial projects, the Litcore Niagara system combines exceptional durability with unmatched style – the ultimate choice for those who demand both performance and elegance. Experience the difference today!
Ideal for today’s, low energy homes, MVHR provides effective ventilation, without compromising efficiency. As a ventilation specialist, Brink knows a thing or two about effective, efficient ventilation. That’s why Brink offers:
• A choice of machines certified by the experts at the Passive House Institute (PHI);
• Industry-leading levels of efficiency;
• European design, engineering and manufacturing;
• Integrated Sound Dampeners to virtually eliminate noise transfer;
• Standard Pre-Heater and Summer Bypass functions for maximum comfort all year long;
• A range of filter choices to suit any application.
To discover five essential considerations when choosing an MVHR system for your build, visit www.brinkhrv.com/fivetips.
Leslie O’Donnell Architectural technologist and structural engineer
Extending or converting can be the more economical option, but only if common sense and restraint is applied to prevent the project from costing more than it needs to. Here’s what to consider, and where to save the most on your renovation project.
With self-build costs coming in at around 1,500 euros or pounds per sqm at the very least, renovating can prove appealing. A small renovation, at a much lesser cost, may be able to give you the space and comfort you need.
As there are economies of scale when building new, the cost per sqm for a renovation will be higher but the overall square footage is much less.
As each project is unique, you’ll find that to make a real comparison you’ll need a quantity surveyor to give you costings based on two sets of plans. House hunting with a builder you trust, your architectural designer or a building surveyor could help in making decisions but their opinions are no guarantee unless they provide a written report.
If an upper storey is to be built or converted, for example, you should calculate whether the space gained upstairs compensates for the total space lost to the stairs. Existing garage stairs may not comply with the stair regulations for habitable use.
Unless an upper storey was originally designed for use as domestic habitable space, the floor may need to be strengthened. Inserting a steel beam into a floor or roof to support rafters or joists will reduce their required sizes and this can be a less expensive option than erecting heavier timbers over longer spans.
All that to say, nothing beats a real comparison. Remember that new build costs can balloon too, when site factors are taken into account.
The case in favour of a new build is that they benefit from zero VAT in NI. In ROI, first time buyers get €30k in tax back under the Help to Buy scheme and other supports like the First Home Scheme which sees the government take an equity share in the property.
In ROI the grant to do up old buildings can
amount to €70k but the application process is cumbersome. It’s still a great support if you qualify, and there are other types of heritage grants to avail of through local authorities.
ROI has better grants for energy upgrades, from the Sustainable Energy Authority of Ireland, than in NI where most grants are targeted at low income households.
Here are ways to make savings on your renovation project.
Set your budget on finishes: The cost of internal and external finishes is where many self-build budgets take a real hammering. Floor tiles can range in price from £10 per sqm to £150 per sqm or more. Will the expensive ones do the job 15 times better than the cheaper ones? Depending
For more about your budget and financing
With self-build costs coming in at around 1,500 euros or pounds per sqm at the very least, renovating can prove appealing. A small renovation, at a much lesser cost, may be able to give you the space and comfort you need.
on the specification, kitchen and bathroom prices can differ massively too. Ask yourself before committing to a deal in a bright and shiny sales emporium: “Do I need it or just want it, what are the real benefits of buying this instead of an alternative; and have I checked prices elsewhere?”
Re-examine the drawings, specifications and schedules of work, apply this mantra to everything and be prepared to make compromises.
Keep your heating system: The heating and domestic hot water may only be sufficient to supply the dwelling as it is, yet may not require replacement for some time to come. In that case, a high efficiency combi boiler could be used as a separate system for the new space.
Extend services: In a similar vein, think about whether services such as plumbing, electrical and telecoms are to be separated between the dwelling and the new space. If the conversion simply extends the use of the existing dwelling, services can be extended from the dwelling into the converted space. This approach may prove to be cost effective but a lot depends on the layout, service routes and entry points. If keeping services separate, new connections may be required, which will incur additional costs.
Reuse or repair where possible: A fire-resisting door between a garage and a dwelling might no longer serve its original purpose, but it can be a useful acoustic door. Do you need to replaster or render the walls or would it look just as good to patch in any new work?
Savings on insulation: If the space is available, insulation such as polystyrene products, quilts or blown fibre (preferably mineral wool) will work out cheaper than top-end polyiso (PIR) insulation boards, even though they will need to be thicker to achieve a comparable U-value. Fire regs may influence the choice, so make sure to get professional advice.
Renovate, don’t extend: Building a new external wall will need foundations and footings so will be costlier than adapting an existing one. Internal walls of timber stud or lightweight block construction can be built on top of an existing floor, as long as the floor can carry the extra loads. Similarly, a new insulated internal wall leaf could be built on the inside of an external solid wall, with an air cavity between them.
Keep the roof: If the roof structure is sound and weather resistant and does not need to be altered to achieve the design objectives, leave it as it is. If essential, replace or repair rainwater goods, external fascias, soffits and barge boards.
Skip the skimming: Plasterboard doesn’t necessarily need to be skimmed. On the ‘decorate only’ face, you can use a jointing compound and scrim tape to fill joints and gaps. Then apply the finishes directly over it all, referring to the instructions supplied by the manufacturers of all the materials being used.
Limit glazing: Designs for contemporary extensions or alterations can incorporate large areas of glazing in the walls and measures for controlling solar gain may be required. Building an external wall without any opening costs less than forming openings in it and the windows or doors in the openings will also lose more heat energy than the wall surrounding them.
You will obviously need windows and doors and whilst it may be desirable to have large ones, they are often unnecessary. Much the same doctrine can apply to roof windows. Stick on an external glass box porch and you could add anything from 10,000 to 50,000 euros or pounds more to your costs. If you do want a large window or glazed wall, try to make use of the existing garage door opening. If you intend to replace other existing windows and doors, it will cost less if the wall openings are altered as little as possible.
The first thing to do is set your budget. For a new build, the cost must not exceed the final house value. This must include all fees paid to buy the site and build the house and also the fees due to the authorities and your consultants. You also need to factor in the cost of lanscaping; at a very minimum there will be site clearance and access to pay.
Similarly, for a renovation make sure the cost will not leave you in negative equity if you were to put the property on the market.
Whether new build or renovation, it’s well known that building costs can easily escalate – even on small building projects. The good news is, if the working drawings and specifications can be sufficiently detailed before the tendering process, the total project cost can be established with reasonable accuracy.
More legwork at the pre-tender stage to make firm decisions on materials and products will pay off in allowing the designer to prepare a detailed schedule of works and in avoiding unforeseen extra costs at the end.
Also, make sure you have enough funding in place. In the case of a renovation, in ROI if you’re availing of the one stop shop grants for energy upgrade from the Sustainable Energy Authority of Ireland (SEAI), or the vacant property grant from your local authority (up to €70k), your lender will not see that as ‘money in the bank’. You will need to borrow the full amount of what it will take to renovate and prove you can fund those repayments. This is because the grant amounts are paid by the government upon completion of the build.
Installing a rooftop garden is a costly endeavour but if you have limited square footage outdoors, your roof could offer a good solution for extra garden space.
1. Roof structure (base layer):
The roof must be structurally sound and able to support the entire garden system without risk of damage or collapse. A structural engineer will be involved to assess the roof’s load-bearing capacity at the design stage, well before any work begins.
2. Waterproofing membrane:
Typically made from rubberised asphalt, EPDM (ethylene propylene diene monomer) rubber, or PVC, the waterproofing membrane should be installed seamlessly to cover the entire surface of the roof.
3. Root barrier: Made of puncture resistant materials such as polyethylene or other specialised root-resistant fabrics, this layer stops plant roots from breaking into the waterproofing layer and thus damaging the roof.
4. Thermal insulation: Often made from rigid foam boards or mineral wool, it helps to minimise temperature fluctuations that could stress plants or the building structure.
5. Drainage: Made of a variety of materials, it is essential to prevent water from pooling.
6. Filter fabric (geotextile
membrane): Made from non-woven synthetic fabrics, this layer is porous enough to allow water flow but fine enough to prevent soil from clogging the drainage system and allow water to flow freely through the soil while preventing erosion.
7. Growing medium (soil):
Lightweight, specialised soil mixes, often containing expanded clay aggregates,
Source: Information from Raaft, compiled by Selfbuild.
perlite, or volcanic rock, are used to reduce weight and improve drainage. The growing medium is typically less dense than traditional garden soil.
8. Vegetation: May include sedums, grasses, small shrubs, or even small trees, depending on the depth of the growing medium and the climate conditions.
Finishing (protective layer):
Some roof gardens will require a finishing layer consisting of an organic mulch, gravel, tiles or decorative stones to help with moisture retention, erosion and to enhance the aesthetics.
Here’s what you need to know to add a green roof to your new build plans, or to retrofit one on your existing home.
You will need planning permission to add a roof garden. For a new build project, this will be taken into account at the design stage and the design will form part of the overall planning application for the house.
Whether building new or renovating, both a structural engineer and preferably a specialised company should be involved at the design stage.
Note that a design that will allow you to see into the neighbour’s garden (or upper storey windows) will lead to issues securing planning permission in both NI and ROI.
As with any project that requires planning permission, make sure to let your neighbours or local resident’s association know of your plans before lodging your application.
In addition to securing planning permission, you will need to comply with building regulations and health and safety regulations in both NI and ROI.
This will involve an application to building control in NI; they will carry out inspections of the work. In ROI you must also comply with building regulations and may need to file a commencement notice, depending on the scope of work.
An architect or a structural engineer will ensure the design complies with building regulations. Crucially, their report will calculate the roof’s structural tolerance and determine whether structural changes must be made to support the roof. The report will also specify the waterproofing layers.
Garden design firms can help map out the building work to be done too. “We primarily build roof gardens on pedestal and frame or tray systems that [lift] the main body of weight off the waterproof layer or allow for additional insulation beneath,” garden designer Tony Woods says, explaining that “this also allows space for running pipes [and] cables”, used for rooftop lighting and irrigation, underneath the garden.
“It’s all about the research and figuring out what is possible first,” says garden designer Damien Keane. He says that hiring landscaping professionals is advisable as they can oversee every aspect of the design and installation.
Manoeuvring machinery and materials onto the rooftop is no mean feat. Tony says: “Access to the roof is one of the most challenging aspects. In an urban environment, if a crane cannot be used, then the design will need to consider what size of materials can be transported through the building to the roof.” If passage to the roof is narrow, “materials such as decking boards will have to be cut off site”, he says.
Damien says the landscapers involved may require harnessing, and that safety and logistics are the two big things you really have to worry about.
The drainage layer is essential to prevent water from pooling, according to Ashton Lewis of Raaft, as it will allow excess water to flow freely from the soil, avoiding waterlogging, root rot, structural damage, and erosion.
There are three ways to drain the roof: specialised mats or boards that allow water to pass through and be directed to the outlets while providing air pockets to keep the roots oxygenated; gravel or crushed stone in
How much does a roof garden cost?
Small balcony garden with paving, decking and electrics already in place: from €2,500 (£2,100) to €3,500 (£2,900)
Small roof garden with paving, decking and electrics already in place: anywhere between €25,000 (£20,800) and €50,000 (£41,600)
Roof terrace built from scratch: from €120,000 (£100,000)
combination with a perforated drainage pipe system; or geotextile fabrics that prevent soil from clogging the drainage system, ensuring effective water flow.
All that takes root on your roof must be hardy enough to withstand the sweeping gales and scorching sunshine that a rooftop faces. “Everything is magnified massively up there,” Damien says.
Strategically placed slatted screens and hedges can “break the force of the wind”, Damien explains. Solid windbreaks, however, are counterproductive because the wind will flow up and over them, hitting the garden with full force.
For cover, he recommends planting Elaeagnus, an evergreen coastal hedge. “That does very, very well in windy spots,’” he says.
Consider sowing a theme through your planting. Minimalist zen gardens, also known as Japanese rock gardens, are popular, as are Mediterranean gardens, replete with terracotta accents, tiles and perfumed herbs.
This will inform the garden furniture you choose; whatever it is, make sure it is securely fixed so it doesn’t become a risk in strong winds. Note that fibreglass pots are an alternative to the heavier stone or terracotta variety, but they need to be heavy enough to avoid wind lift. Also remember to include a lighting plan for your rooftop.
A final step is figuring out the aftercare your garden will require. “We would probably go back to a roof garden three or four times a year, just to tweak it and make sure everything is okay,” says Damien.
Plant selection is important for many reasons: temperature regulation, water retention and providing shade. Also some plants, especially trees and large shrubs, have aggressive root systems that could compromise the integrity of the waterproofing. Damien recommends sourcing dwarf mountain pine such as Pinus mugo or a large bonsai pruned pine.
Low-maintenance grasses and Alpine plants will flourish on Irish rooftops. Damien says: “As a general rule, anything with a glassy or hairy leaf will usually do well up on an exposed site.” Stipa arundinacea, Miscanthus grasses, Carex, Libertia, Cordyline palms, Trachycarpus, Phormium, Agapanthus, Vinca, Arbutus and ferns are among the other plants he recommends.
As for flowers, choose red hot pokers, named for their pronged shape and flame-like colouring, for summer colour and fuschia or tangerine crocosmias for vibrant autumn colour. Nepeta
lavender,
hues.
Those hoping to pluck fresh cooking ingredients from their garden can plant rosemary plants and a bounty of herbs, while vegetables can be grown in troughs.
What doesn’t work? “I would steer clear of any soft plant,” Damien says. Large herbaceous perennials can be blighted by windburn. No-nos include Japanese maple trees, tree ferns and any plant that requires protection in the wind, he says.
Barry McCarron Vice Chairperson of the Passive House Association of Ireland
In a typical Irish dwelling, more than half the energy used for hot water can be attributed to significant heat losses within the building. Here are ways to maximise efficiency and reduce overheating.
The average domestic hot water (DHW) system contributes to both overheating and inefficiencies. This is particularly true in multi-residential buildings where there can be long lengths of hot water pipes.
To reduce heat loss from your hot water system, the following strategies should be employed:
Flow temperatures should be kept at the minimum you require, i.e. do not distribute at high temperatures and mix down at point of use. For example, oil or gas boilers will heat water to a high temperature which will then need to be cooled down if your heat emitter is underfloor heating. Heating water to cool it down leads to inefficiencies. Take advice from your plumber. Minimise pipe runs. The length and complexity of pipe runs should be minimised by coordinated and intelligent room layouts. This is best achieved by reviewing the design at concept stage to ensure the most effective layout and distribution pathways.
This is often achieved with vertical distribution (but is dependent on building geometry) with outlets close to risers. Where hot water or communal heating is circulating year-round, reducing flow and return temperatures is very beneficial.
In particular, the distance between the primary heat source and the hot water storage vessel (if present) should be minimised as these pipes will need to be large.
In non-circulating systems, pipe diameters can be reduced to small bores (outside diameter of approx. 10mm) by use of a radial distribution system whilst still maintaining satisfactory levels of flow and pressure. It is important that these
systems are designed appropriately to address pressure drops.
The volume of stored hot water should be optimal (not oversized) and the storage temperature should be as low as is practicable whilst ensuring there is an appropriate periodic (weekly, or even monthly) sanitisation cycle to deal with legionella. A storage temperature of around 50degC is sufficient to provide for hot showers.
Match the heat source to the hot water storage volume, and the associated hysteresis setting should be optimised to avoid rapid cycling. Secondary circulation systems should be avoided (again achieved by efficient layouts). Where they are required, the return pipework should be small bore, and the circulation times minimised in line with the building’s usage patterns.
Many appliances and devices (dryers, refrigerators, freezers, dehumidifiers, ovens, computers, etc.) within a building generate heat, which can significantly impact the risk of overheating. These devices are often added after construction and may not be part of the building’s fixed services, making them difficult to model. When in doubt, assume the worst-case scenario in the PHPP (the PassivHaus methodology used to design buildings to comply with the passive house standard, see passiv.de) model. Appliances that are always on, even at a low load, can have a disproportionate impact on heat gain.
The average domestic hot water (DHW) system contributes to both overheating and inefficiencies. This is particularly true where there can be long lengths of hot water pipes.
Andrew Stanway Author of Managing Your Build
Q: My partner and I have already done one self-build before and don’t think we really need an architect for our second one. What do you think?
A: Unless you are going the turnkey, kit-house route I think you’d be crazy not to use an architect, even given your previous experience.
Having done one build successfully doesn’t bring you anywhere close to the experience and clout of an architect. It will be money very well spent.
I don’t know what you used your architect for on the previous build but experience shows they can offer all kinds of services and knowledge that would be impossible for you to match after even as many as five self-builds. They also have professional indemnity cover that you will not have.
If in any doubt about what an architect or any other professional designer can offer, have a look at the list below. As with so many complex undertakings in life, when things go well one can often manage without a professional. When things go pear-shaped, though, they earn their money many times over. And in the world of house building so many things can, and do, go wrong.
You’ll be making a huge personal investment of time, energy, money and emotion in your build and, as a result, may be unable to make good decisions. In contrast, your architect will simply see it as another job that has to
be done well. This dispassionate approach will pay dividends for you time and again. A good architect will:
• Look at your site and asses its viability
• Prepare design options for your consideration
• Design your house and, maybe, even your landscaping
• Prevent you from making silly mistakes that you’ll later regret and that could be costly to remedy
• Guide you through ecological/ sustainably options that could affect your long-term finances
• Help you decide on materials they know will be acceptable to the local planners
• Make a digital 3D representation of your home so you and others can express their views
• Send suitable drawings to the planning department and negotiate with the planners on your behalf; some of these officials will be well known to your architect who may then be able to effect all kinds of solutions you would find impossible
• Negotiate planning appeals
• Ensure your build will conform to the requirements of local and
national regulations
• Help find other professionals you may need, such as engineers/ surveyors/experts on geology/ ecology advisors/interior designers/mechanical and electrical experts and so on
• Oversee the tendering process and advise on which quotation to accept
• Create a detailed specification document
• Work with a quantity surveyor to get your costing accurate before you start building anything
• Use his/her local knowledge of suppliers and other building contacts on your behalf
• Do the drawing and detailing required to satisfy the planners and building control officials
• Do all the necessary construction drawings so the builder can price and then build the whole thing But, most important of all, your architect will be a listening ear and informed intermediary between the mass of officialdom and other self-interested parties who’ll appear to be getting in the way of you having what you want. This takes a lot of skill and a knowledge of how to ‘play the game’.
In a construction project, site works follow on from the design phase; here’s a bird’s eye view of the process up to the point of getting weathertight.
Frank Lloyd Wright is widely quoted as having said: “You can use an eraser on the drafting table or a sledgehammer on the construction site.” We all know which is going to be more expensive. But the reality is, changes are still routinely made on site.
Before doing anything on site, check the drawings and if a detail cannot be found, ask your designer. Inspections are then required during site works in order to ensure that the building work achieves the design objectives.
The most important thing at this stage is quality control; getting your inspections done and having a qualified professional to call upon for any changes to the plans. This is likely going to be your structural engineer, as most changes will have structural implications and potential knock-on effects, but for more minor changes it could be your architectural designer.
Communication on site is key; many self-builders create WhatsApp groups to keep everyone in the loop but ensure there is no overloading of messages either. You can limit the group for only admins to post, to just include the latest plans on that channel for example.
Whatever way you organise it, make sure you are available and the channels are open so that any questions go through you – it’s common for builders to assume what you want or go with the way they normally do things. In many cases that’s fine but make it clear you want to be involved if the plans aren’t clear or if a decision has to be made that’s not specified on the plans.
The main thing is to have
printed versions of the construction drawings on site for everyone to refer to. A usable scale is 1:50 to show enough detail; use clear sticky back plastic (or a laminator) to protect them from wear and tear. Only have the latest plans available to avoid confusion.
The trades will have questions for you and even if you are not managing the build yourself, you will need to make
a million decisions. So to avoid delays on site, which will cost money directly or indirectly, you will need to be readily available. You will also need to have your research ready for every element, from choice of door handles to skirting boards. Otherwise you’re likely to end up with whatever your local builder’s merchant stocks.
The most important thing at this stage is quality control; getting your inspections done and having a qualified professional to call upon for any changes to the plans.
Futureproof your house and have all the downpipes meet at one soak pit location, to enable the addition of a rainwater harvesting tank later down the line.
The Institute of Geologists of Ireland has guidance on what to look out for when drilling your well.
Location. Water wells must be drilled in locations which minimise the likelihood that the well will be polluted by, for example, septic tanks, farmyard runoff or slurry spreading.
Construction. Wellheads should be constructed so as to ensure that surface water and shallow groundwater, which are likely to be polluted, cannot enter the well. Wells must be cased and grouted to an adequate depth, the casing and grout must meet certain minimum standards, and the placing of the casing and grout must meet a certain specification. Water well drillers and their equipment and methods should meet certain minimum standards. The equipment should be clean, and drilling should not introduce any polluting matter into the ground. Cleaning. Water wells should be cleaned and disinfected before being brought into use. The methods and materials should meet certain minimum standards. Testing. Water wells should be tested for yield and quality. A mandatory list of tested chemical and bacteriological parameters should be specified. Grants. In ROI you can apply to your local authority to rehabilitate your well, covering 85 per cent of approved costs (min €750, max €3,000 grant). If you need a new well, the maximum grant is €5,000. Filtration and ultraviolet (UV) treatment may qualifty for 100 per cent funding up to a maximum of €1,000. This can be claimed on its own or in addition to either the grant for rehabilitation works or the grant for a new well.
In NI, consult with the Northern Ireland Environment Agency (NIEA), daera-ni.gov.uk; your local authority is also available for advice and help with testing water quality. In ROI refer to the IGI guidelines for building a well, igi.ie, also see protectyourwell.ie and epa.ie.
In NI, building works may be commenced following building control (BC) approval of the drawings and specifications, or may at the discretion of the local authority, commence soon after the BC application has been submitted, albeit at the applicant’s ‘own risk’.
In ROI, the system of providing commencement certificates and notices is to be found online by looking for the National Building Control Management Project (NBCMP) or by visiting the National Building Control and Market Surveillance Office website, on nbco.localgov.ie. Be aware that the ‘FAQs’ document currently
Get started with the On Site stage of your Selfbuild Journey here
Graphic from the Environmental Protection Agency, epa.ie
runs to 134 pages. Notification should be regarded as a ‘pre-construction’ activity. Also, if it has not been previously done, verify ownership or control on the ground, including boundaries, rights of way, easements or wayleaves and any other features or restrictions which relate to the proposed development.
If any site investigations determine that a site is ‘hazardous’, the proper authorities should be notified in advance of the commencement of works. These might include environmental agencies, health and safety agencies, local councils and any warranty bodies such as NHBC, who require eight weeks advance warning.
Before installing your onsite wastewater treatment system, here’s what to check for.
Found on Site Characterisation form submitted with planning: In ROI once the onsite percolation test is completed, a site characterisation form is completed and sent as part of the planning application. This report dictates the type of percolation area required, i.e. trenches, low pressure networks, raised beds, etc. It’s also determining whether you’re installing a septic tank or packaged treatment plant and the Population equivalent (PE) of the treatment plant among other details.
Access: The tank is a big piece of kit, which means access will be required to install the system. In some cases this will require a temporary roadway installed to lower the tank into the ground directly from the delivery truck. Other tanks can be put in by digger.
Check the levels of sewer pipes from the house, as this will determine if pumps or risers for the systems are required.
Electrical requirements for the system being installed; this needs to be sorted in advance.
Know what backfill is required: concrete or stone. Have it ready on site.
Cathal Keane, Graf managing director
Les O’Donnell Landmark Designs landmarkdesigns.org.uk
A bird’s eye view of the schedule of works and key moments in the inspection schedule.
The construction timeline presented here is a suggested sequence of events for a typical house construction project. The first item in the timeline can be regarded as pre-construction activities, but will usually require some input from the contractor. For
2. Foundation test holes or trenches dug and inspected if not already done.
instance, if an archaeological report is required, the survey may require soil removal under the archaeologist’s guidance; or sight splays may need to be excavated and fenced and the new entrance properly provided in accordance with the planning conditions.
5. Foundation concrete poured and levelled or piles installed if required.
4. Excavations completed for foundations and reinforcement provided if required
3. Access including sight splays, hardstandings provided and site cleared and fenced.
1. Completion of pre-construction environmental measures and fulfilment of any planning conditions required to be completed ‘before work commences’.
7. Install all pipes, ducts and cables which penetrate the ground floor and walls.
6. Substructure works completed before backfilling.
Environmental protection measures might include the removal or treatment of invasive species, the provision of hedgehog safe routes, the erection of bat boxes or the construction of earthen barriers to protect waterways, etc.
Certificates of compliance
11. Superstructure constructed up to first floor level (or up to wallplates if single-storey).
8. Backfill around bases and fill underfloor hardcore up to sub-floor level. 9. Radon membrane and fittings installed.
Subfloors provided or install precast concrete flooring for any suspended ground floors.
with standards may be requested by building control (BC) for certain structural components, e.g. roof trusses, precast concrete slabs before they are erected or installed on site.
The remainder should be kept on file for checking as
14. Roof structure and support works complete.
13. Superstructure walls complete with all flashings, DPCs, aprons and preformed cavity trays installed. DPC trays within cavities should remain uncovered for inspection.
18. All ventilation and ductwork installed.
17. All insulation correctly installed.
19. Underground services trenches excavated. Inspection chambers, manholes, septic tank and soakaways all installed. All pipes, ducts or cables laid. All to be left uncovered for inspection.
12. First floor construction completed. Prop if required.
15. Dwelling weathertight and secure (roof covered, external doors & windows fitted, etc.)
16. First fix M&E and non-structural joinery.
20. Internal ‘wet’ finishes such as floor screeds, plastering and tiling, etc.
21. Second fix M&E including heating installation.
part of the final inspection. Certificates should be obtained at the earliest opportunity from manufacturers, suppliers, installers, subcontractors or others as appropriate. Failure to keep on top of this will create a huge amount of extra time and frustration at the end of the build.
During the course of the building works, site inspections will be carried out at various stages (top portion of the timeline below), not only by a surveyor from the local Building Control (BC) office, but also by a suitably qualified person who provides
certificates for the satisfactory completion of each stage.
The Certifier is usually, but not necessarily always, the designer; and could be an architect, a chartered architectural technologist or the structural engineer. The contractor might be registered with a warranty body such as NHBC or Homebond and their representatives will also carry out routine inspections.
The different inspectors will not necessarily visit the site at the same time, nor will they always be checking exactly the same things. Sometimes a number of stages might be covered by one inspection.
To get a bird’s eye view of the construction phase:
Experience indicates that the Certifier will usually appear more often than the BC surveyor. The warranty surveyor will have their own inspection schedule as instructed by their employers.
All inspections will include checks that the building is being carried out in compliance with the building regulations and the effluent discharge consent (if it was required); however the BC inspections are only one part of the story.
The Certifier will additionally be checking that planning conditions are being met, including any environmental measures which might have
been stipulated, together with any requirements by other public bodies such as the roads authority, water service, rivers agency or the historic buildings department, etc.
Some other aspects of the works might not need to be formally certified but neither should they be ignored, such as temporary works and health and safety measures. It is the responsibility of any competent professional visiting the site to make a note of any safety related matter which may be noticed and to immediately
27. Completion of external construction works such as paths, steps, ramps, walls, etc. All retaining walls or free-standing walls must be designed by a structural engineer.
33. Snagging inspections and remedial work.
37. Rectify defects. Undertake seasonal commissioning.
23. Kitchen (including appliances) and sanitary ware all installed and tested (including drainage).
22. Install and connect renewable energy equipment.
25. Underground services trenches covered.
24. Drying out period followed by second fix joinery.
28. Groundworks completed. Postconstruction environmental measures completed. Tree and hedge planting. Lawn and/or wildflower sowing, etc.
26. External finishes completed to the house.
30. Confirm that windows, doors and means of escape are all fitted correctly and operate as required.
29. Testing and commissioning of systems for heating, chimneys (if any), ventilation, electrical, plumbing, security equipment, all fire safety measures, telecoms, renewables, etc.
32. Obtain as-built SAPs or DEAP calculations if required.
31. Obtain a thermal imaging report. Complete air-tightness tests. Correct defects as required.
35. Compile the Building Manual including the Health and Safety File and Fire Safety points.
34. Practical completion: All specialist certificates and warranties obtained. Defects list issued.
38. Undertake project performance review and postoccupancy evaluation.
40. Update the Building Manual, Health and Safety File and Fire Safety information. Note: Additional
36. House ready for occupation. Aftercare initiated.
Conclusion of construction contract.
39. Issue Final Certificate. Verify project outcomes including sustainability and building performance.
bring it to the attention of the contractor and the employer (the employer being yourself as the property owner).
Contractors and employers are legally obligated to notify the health and safety authority (HSENI, hseni.gov.uk, or HSA, hsa.ie, depending on where you are) of any reportable injuries, diseases and dangerous (‘near miss’) occurrences.
By doing so, you will assist the enforcing authority in identifying where and how risks arise and whether they need to be investigated or when they need to provide advice about how to avoid work-related deaths, injuries, ill-health and accidental loss.
It is essential that any items which may later be covered up, remain uncovered (but kept safe) until they are inspected. The construction contract will usually stipulate that if the contractors close or cover work before it is inspected, then it may be requested to be uncovered for inspection at the contractor’s expense. Works should not proceed to another stage before an inspection of the current stage is carried out.
The project certificates file should include certification of products such as insulation, radon barriers and associated fittings and sealants, fire retardant paints, cladding, glazing, sheeting materials, wall ties, bolts and
other structural components. Evidence of compliance is also necessary for fabricated structural components including timber frame and ICF structures, roof trusses, space joists, lintel systems, precast concrete (including bricks, blocks, beams, flooring planks, etc.), metal assemblies, welding and connections, etc. Product certificates should match the markings on the products or their packaging and stamps, labels or similar markings must be clearly visible, legible and indelible.
“... if the contractors cover work before it is inspected, then it may be requested to be uncovered for inspection at the contractor’s expense.”
What to look out for at this potentially budget-busting stage of your build.
Here’s what to look out for when building your foundations.
Foundation depth usually should be at a minimum of 450mm below ground level to avoid frost damage. In reality, this depth is usually exceeded. The depth may differ, for example, if the soil is mainly clay and perhaps with trees in the vicinity.
The depth should be taken from the existing, not finished, ground level, even if the finished ground level will be above the existing ground level. If strip or trench fill foundations need to go deeper than 2.5m, consult a structural engineer.
Foundation excavations must be square (i.e. not rounded) at the bottom and must be excavated down to subsoil which is of consistent load-bearing quality throughout the extent of the foundations under the building. These rules apply equally to strip, raft and mass concrete types of foundations.
Any large boulders or soft pockets of sand, subsoil, fill material or organic material found at the bottoms of foundation trenches must be removed and the space filled up to the underside of the
proposed foundation level with lean mix concrete.
In less favourable soil conditions, engineered fill or ground improvement schemes may be necessary. These procedures must be undertaken by a specialist contractor and tested by an engineer.
If the water table could rise to within 250mm of the lowest damp proof membrane (DPM) of the building, or where surface water could enter or adversely affect the building, the ground to be covered by the building should be properly drained.
If the route of an existing active subsoil drain is discovered passing under the building it should be relaid in pipes with sealed joints and have access points before and after it passes under the building, or be rerouted around the building or connected to another outfall.
and investigative work should have been carried out at a very early stage, preferably before submitting the planning application.
Where it is suspected that the site is potentially contaminated (brownfield site), a combined geotechnical and geo-environmental investigation should be considered. On a brownfield site some form of unfavourable ground conditions such as contaminated soil, buried waste or organic fill material might be expected
Adverse soil conditions may be discovered on greenfield sites too. Deep pockets of underlying organic soils are not uncommon and although most may be fine for growing crops, are unfortunately not very good at carrying building loads without some degree of settlement. Because of this and also owing to the fact that some organic soils, such as peat, may produce gases such as carbon dioxide and methane, they may need to be removed if under or near to the building; or the ground ventilated or otherwise treated by a specialist contractor.
The detailed soil analysis in the geotechnical report will
allow your structural engineer to design suitable foundations and the geo-environmental report will recommend suitable actions for dealing with contaminated or deep organic soil.
Before pouring the concrete foundations, the excavations should be tidied up to remove any debris that may have fallen into the trench. All excavations must be kept free from water, and if left open for a long period of time, further excavation down to a non-weathered strata may be required. Double check that all dimensions are correct for trench lengths, widths, depths and diagonals across the opposite corners of the house. If the soil shows signs of
Foundations support buildings by transferring their loads to the ground. The performance of the foundation depends on the load bearing capacities and settlement characteristics of the layers of rock or soil on which they are placed.
Most of us usually think of them as the continuous strip foundation consisting of concrete cast in trenches directly under the line of each wall to be supported. In fact, the type chosen for your site by your designer will generally be this type of shallow strip foundation, a choice usually based on preliminary assumptions about the soil conditions.
If the ground conditions are found to be unsuitable for strip foundations, then a solution will need to be designed by a structural engineer.
There are two main types of foundations.
SHALLOW FOUNDATIONS: Strip types are the most common form of shallow foundations, whereas trench fill foundations are a variation of strip foundations which are usually used where the depth of the trench is deeper than normal, or where it is intended to almost completely fill the trench to take the place of blockwork footings.
A raft foundation consisting of a layer of reinforced concrete over the footprint of the building can be a good solution where ground conditions are inconsistent across the building area or where strip foundations would be impractical, for example where there are individual loads positioned closely together.
Rafts may be locally strengthened where loads are higher.
slipping into the trenches, do not excavate more soil to create sloping sides. Even if there was the available horizontal space to do this, a foundation profile could be created which may be unstable.
Instead, provide shuttering to create vertical sides to the trenches. Such trenches may in any case need to be shored and propped in order to comply with health and safety measures.
Regardless of the anticipated depth, a risk assessment should have been carried out by a competent person before carrying out any excavation and should aim to minimise the requirements for operatives to enter an excavation. If this cannot be avoided then shoring and propping would usually be required.
Tragically, fatalities have occurred in trenches as shallow as 1m, so there is no standard minimum depth at which shoring must be provided and its installation is all down to the risk assessment which may vary from site to site.
Fence or tape off exclusion zones on the surface adjacent to trenches for plant, machinery and stored materials. When not being worked at, cover all open holes, including any small diameter ones.
If steel reinforcement has been specified, it must be laid in accordance with the structural engineer’s design and bar schedules and then checked
Pad foundations are used for separate point loads, for instance under columns supporting parts of the building at higher levels.
These are typically formed using a version of piled foundations, upon which are cast reinforced concrete beams to carry the walls above. If a suitable load bearing layer of subsoil cannot be found at relatively shallow depths, the only option is to dig deeper. However, the practical limit of depth for normal foundation trench excavations is, as a general rule of thumb, 2.5 metres.
Below this depth, pile foundations should prove more economical. Driven piles can be steel or precast concrete which are hammered or vibrated down by a piling machine until sufficient resistance is found. These can be end-bearing piles which rely on finding a load bearing stratum at their lower ends, or friction piles which depend on the effects of shear stresses in the soil along their sides when hard layers are too deep.
Pile foundations under houses and extensions are quite often mini- or micro-piles, which can be placed when space is restricted or when loads are not too great. On a site where the vibrations and noise from driven piles would be unacceptable or where the soil is primarily cohesive (e.g. soft clay), screwed or bored piles can be a good option. Screw piles, like their name suggests, are screwed into the soil until sufficient resistance is encountered Bored piles are created by boring vertical holes into which concrete is poured.
Continuous-flight auger (CFA) piles are formed using a simultaneous boring and poring process. Other types of deep foundation such as contiguous piled walls, interlocking secant piled walls, sheet piled walls, diaphragm walls or caissons, would usually only be needed for larger buildings.
by the structural engineer. Check that the concrete is supplied in accordance with the specification in terms of strength and slump class.
Do not allow the concrete delivery operative to wash out his lorry into the foundations and if washing machinery must be done elsewhere on site, make sure that approved environmental protection measures are in place to take care of it.
After concreting work is complete, prevent water from collecting and weakening the concrete and always allow sufficient time for the concrete to cure properly before
proceeding with building the footings.
If the water in the concrete mix freezes, the concrete will need to be removed, so provide frost protection if the temperature is likely to fall below 5degC.
Firstly, the term ‘footings’ can mean different things depending on where you come from. For some, the footing is the support for the foundations, for others it is the foundation itself and for yet others it is the part of the base of the wall constructed on top of the foundation and reaching up to about ground level or subfloor level. It is the latter
“The subfloor is a means of protection for the underfloor void against burrowing pests or vegetation growth, etc.”
definition which we tend to use in Ireland.
All footings from foundation level up to a point 225mm below the lowest damp proof course (DPC) will typically consist of dense concrete blockwork without any cavities. Unless designed otherwise, the footings for all walls should be located centrally on the foundations and if any variance in dimensions is found on site, it should be reported right away to the designer or structural engineer.
Footings should be at least as wide as the thickness of the walls above them and it is good practice to construct 215mm wide blockwork footings for 100mm or 140mm thick internal walls. External cavity walls of 400mm in width, would require footings built at 440mm in width to suit the next available standard width of blockwork.
After the footings are constructed, fix in position all pipes, ducts and cables which will penetrate the ground floor and the bases of the walls. This should include radon sumps and their discharge pipes if they have been specified for your site. Check all components for compliance with standards.
Ensure that backfilling avoids displacement of the ducts and drains from their lines and levels. Mechanical compaction equipment should not be used over underground services until there is a minimum of 450mm material above the top of the duct or pipe. Away from these locations, fill should be mechanically compacted in 150mm layers.
Where a drain is liable to surcharge, protective measures such as wrapping it in polythene, bedding and surrounding it in concrete and
the provision of movement joints will be required. In some cases, underground services may have to be supported on piles.
Where groups of pipes have to pass through the footings together, the opening should be bridged using precast reinforced concrete lintels, although it is best to avoid wide openings in wall bases.
The subfloor, placed at or near ground level, is a structural element of the building. In cases where the ground floors are suspended, the subfloor is a means of protection for the underfloor void against burrowing pests or vegetation growth, etc.
In a basement, it may form part of a barrier against groundwater and horizontal restraint for the bases of retaining walls.
Insulated concrete rafts combine the requirements served by foundations and subfloors together, so cost savings on time and materials can be made. The raft may incorporate underfloor heating and it provides a method for maintaining a continuous thermally insulated envelope around and under the building.
address this at the design stage.
The radon barrier membrane will usually also serve as the damp proof membrane (DPM) and is preferably fitted under the subfloor over a layer of sand blinding on top of the hardcore fill, the top 200mm of which should be gas permeable.
The membrane must extend out past the external faces of the external walls, above finished ground level, but it is quite common to find radon barriers which don’t extend out far enough. This is usually due to under-estimating the area of membrane needed to account for rises and dips across the base and the effect of shrinkage when concrete is poured over it.
Radon sumps need to be piped out to the external air and vented above ground level, with the potential for later adding mechanical extract equipment if radon levels are very high.
The external ends of the pipes must not permit groundwater or rainwater to pass back into the sump.
The radon barrier / DPM should be at least 300 µm thick (1,200 gauge), CE or UKNI marked as such and with properly sealed joints. All pipes, ducts or similar services which pass through the membrane must be properly sealed using proprietary ‘top hat’ collars.
These insulated raft structures rely on parts of the insulation to act as loadbearing elements, so skill and experience is needed to get it all prepared and installed correctly. If you are tackling one yourself, take advantage of the manufacturer’s on-site supervision and training.
In certain cases, the subfloor may be the only constructed floor element that you need and floor screeds can be avoided altogether, but it is essential to
Needless to say, the membrane and its seals, taped joints and fittings must be gas tight throughout. Failing to repair a puncture is likely to concentrate radon into one point of the dwelling, which is not good, particularly if that point is under a habitable room.
Les O’Donnell Landmark Designs landmarkdesigns.org.uk
What to watch out for when the walls are going up.
The best tip for installing products in wall cavities, under floors or in roof voids, is to remember that you are not likely to want to go back in there any time soon to fix deteriorating products. So buy the best quality to suit the purpose.
Things like cracking or crumbling plastics or composites, slumping or decaying insulation, corroding metal components and badly fitting pipe joints are a nightmare to remedy if they are in inaccessible or hard to reach places.
No one likes to be given unpleasant or odoriferous repair work (think foul water drains), but whoever does it will charge accordingly.
Walls should be built in stages to avoid premature collapse and no portion of the work should be built more than 1.2m above another at any time. Additionally, do not carry up one
leaf more than 1.5m high in any one day. Bring both leaves of cavity walls to the same level at every course containing rigid wall ties and any rigid rod type ties left protruding must be capped to avoid injury.
Masonry cavity walls should be protected whenever work stops overnight or for inclement weather by securing plastic sheeting over the tops of both leaves, the cavity and any insulation.
The courses of bricks or blocks should be carefully planned to match the storey heights and the heads of wall openings. All courses should be level and all vertical joints should be in line and plumb. A gauge rod is handy to check the heights of windows, doors and floors.
If using different products in the inner and outer leaves of cavity walls, carefully plan the positions of courses, mortar
joints and wall ties. Avoid the use of dissimilar materials in any one wall, such as a clay brick course in a blockwork wall. Copings on walls will require damp proof courses (DPCs) and if near a roof line (such as at parapet gables), will also require flashings and soakers to be fitted. Copings, whether stone, concrete or composite products, need to be securely fixed to the wall head. Allow for differential movement where the inner and outer faces of the walls are of different materials. Check the drawing details.
The DPC in the external cavity wall should be at least 150mm above finished ground level and the bottoms of the cavities should start at least 225mm below the level of the lowest damp proof course.
If the wall is built directly off a raft foundation, ground beam or similar supporting structure and it is impractical to continue the cavity down 225mm, preformed cavity trays should be built in along with external weep holes.
If an exposed radon barrier membrane crosses through
walls at the bottoms of door openings, the radon barrier must be permanently protected against damage from the frequent movement of workers and their equipment passing through.
Check that DPCs and flashings are properly fitted at any junctions between them.
Cavity wall ties must be fit for purpose and fitted at the correct vertical and horizontal cross-centres. There are some unapproved ties, especially some of the wire types, on the market, so double check the certification.
Alternatives, such as basalt fibre and resin wall ties, will permit significantly less heat transfer out through the walls than the metal types.
Additional numbers of wall ties are installed at the sides of openings, vertical unreturned edges, sloping unreturned edges (e.g. roof verges) and adjacent to vertical movement joints.
Check tie installation for orientation, fall to the outer leaf, embedment depth in each leaf and that they are clear of mortar
“Some site workers seem to have been taught that the humble shovel is an excellent tool for measuring volumes or weights of different materials, whereas sadly, the opposite is true...”
Differential movement cracks in walls are very often found where the ends of lintels and sills meet the adjacent blockwork, so it is good practice to install bedjoint reinforcement at these positions.
The drawings should have identified all other concentrated load points such as under girder trusses or at sides of wide openings, etc. and given suitable solutions for spreading or supporting the loads.
When the air temperature on site falls, or is likely to fall, below 5degC, then the use of mortar, plaster or render should cease and all work should be protected. Overdosing the mix with admixtures will be very likely to have a detrimental effect. droppings.
The stainless steel mesh or rods should be provided in the first and second courses above and below all openings, out to no less than 600mm either side of the opening. Bed joint reinforcement can also be used to provide additional strength in parapet walls.
Joist hangers are often used in order to avoid joists penetrating wall cavities and allowing air leakage. External walls will require lateral restraint from upper floors and the roof structure. Where restraint straps are installed, ensure that they are fitted in accordance with the drawing details.
Timber wallplates will also be tied down to the walls using steel straps. Some council areas will also permit the use of flexible steel straps to act as diagonal wind bracing between roof trusses.
With any straps, ensure that they are not damaged or distorted and that they are fixed with the correct number and type of nails or screws.
Steel wind posts are used in external walls to stiffen the wall against horizontal loads. Where needed, they must be designed by a structural engineer. Wind posts should be made from austenitic stainless steel if they are to come in contact with the external leaf of an external cavity wall or if they are used in aggressive environments such as coastal locations. Check before using any other type.
Use only steel plate for shims if they are needed for height adjustment where steel beams bear on concrete padstones in walls.
Cavity fire barriers may have been specified and should be clearly detailed on your drawings as a means of interrupting fire spread in cavities. They are typically fitted at the edges of cavities including around openings or where the wall cavity abuts compartment walls and floors (i.e. if the house is not a fully detached single dwelling).
The dimensions of barriers which are manufactured to stay in position under compression must exactly match the width of cavity for which they are designed and vice versa. Also check for the protection of concealed spaces around and behind external wall cladding. Compartment walls, such as the dividing wall between two semi detached houses, should stop 25mm below the top of the roof framing and a soft fire-stopping material inserted in the gap.
Fire stopping is required above and below the roof underlay and at the eaves. Check the details on the drawings.
Mortar, plaster and render should be mixed in accordance with the specifications, or bought in wet or dry premixed forms from an approved supplier. Keep an eye on site mixed mortar to make sure that all mixes are consistent and that each mix ratio is correct for each batch.
Check your drawings to find the recommended mixes for each part of the building. To obtain accurate ratios, it is best
to gauge the dry materials by weight-batching them, but if you choose to gauge them by volume, then gauge boxes should be used. Some site workers seem to have been taught that the humble shovel is an excellent tool for measuring volumes or weights of different materials, whereas sadly, the opposite is true.
Chemical admixtures can be used in small quantities to modify the properties of the mortar and can also be pigmented to the correct colour for facing brick. Air entraining admixtures may be introduced to reduce the risk of frost damage, however the mix ratio will need to be adjusted to allow for any resulting reduction in strength.
Check the quality of all precast concrete products including bricks and blocks. Delivery should be accompanied by a Declaration of Performance (DoP) and comply with the relevant standards. The thickness, density and compressive strength of blocks may differ in different parts of the building to account not only for strength but also acoustic and thermal performance in certain areas.
Wall insulation
Insulation is expensive stuff, so install it right. Insulation boards will be fitted as the blockwork rises, but although relatively easy to monitor, is not so easy to remedy, especially if beyond easy reach.
Injected bonded bead insulation products will need voids and wall penetrations sealed before installation, so the cavities can usually only be checked by the installer using an endoscope or borescope camera during installation.
Any doubts about the insulation can be double checked by a thermal imaging survey after the house is sealed and the heating system is functioning. The use of soft insulation such as quilts or blown fibres in a cavity is not recommended due to the risk of settlement over time.
Examine the insulation at junctions where floors and ceilings meet walls, or where the internal leaf of a cavity wall meets the external leaf around wall openings. These areas will also require airtight seals to achieve the as-designed air permeability rate in the building.
Check that board type insulation in cavities is fitted snugly against the inner leaf of the wall, that all joints are accurately cut and properly taped. Cold air looping between the boards and the inner surface of the wall cavity will severely reduce the efficiency of the insulation. It is imperative that the wall ties and the cavity side faces of the wall are all kept entirely free of mortar and droppings. If insulation boards are to fully fill the cavity, seek evidence that they have been manufactured to do this.
It is all too easy to damage strips of board type insulation as they are built in around openings. Insulation should be
fitted under the sloping DPCs between lintels and over wall openings.
When windows and doors are installed, these areas can easily be missed, which will be very difficult to remedy. Take care that soft insulation such as glass fibre quilt is not stuffed into these voids. Any compressed insulation will be less efficient so use cutto-shape insulation batts or boards.
Tracks or chases are cut into the surfaces of walls in order to install cables and small diameter services, but if badly done will weaken a wall. Watch out for:
• All chases should be neat, precise and not be cut with impact power tools.
• Vertical chases should be not deeper than one third of the thickness of the wall, or of the leaf if it is a cavity wall.
• Horizontal chases should be not deeper than one sixth of the thickness of the leaf or wall.
• Chases should be positioned so as not to impair the stability of the wall.
• Consult the block manufacturer before cutting chases in hollow blocks.
• Do not make chases back-toback on the opposing faces of any wall.
• Only cut chases that are straight and true, vertical or horizontal; not at angles or curves.
New walls should be ‘toothedin’ to existing walls at every alternate course of blocks when the new wall is built as a continuation of the existing one, on or near the same plane. A good quality of mortar
bond between old and new work is essential. Where the new wall is perpendicular to the existing one and meets it a sufficient distance away from a corner, it can be connected using an approved stainless steel wall tie starter system. When trying to create continuity of insulation between new and existing cavities, take care that the structural integrity of the existing wall is not compromised. Consult your designer if in doubt.
Your windows and doors should come with certification including datasheets, operations and maintenance manual and confirmation of CE marking. Ensure that your datasheet includes the U-value of the window, along with the solar transmittance. This will ensure that your building energy rating (BER) reflects the true benefit of your new energy efficient windows and doors.
The timber frame elements of the construction should be manufactured to BS or Eurocode standards by a registered Structural Timber Association (STA) or Irish Timber Frame Manufacturers’ Association (ITFMA) member. Many timber frame buildings are erected by contractors, so check those works which may be beyond the direct control of
the manufacturer. A checklist may include:
• Evidence of the installer’s conformance with a suitable
quality assurance scheme.
• The moisture content of solid timber members and woodbased panels for internal use, after delivery and after erection when protected from the weather.
• Proper handling and storage on site and protection from inclement weather.
• All dimensions should match the drawings.
• Perpend vents of the correct size and spacing in the external blockwork at the top and bottom of each storey in all external walls.
• Wall ties of correct quality, at the correct spacings and positions.
• All wall ties should be fixed to studs, not sheathing.
• Vapour Control Layer (VCL) fitted on the warm side of external wall panels.
• Services cavity of sufficient width, if specified.
• Measures for differential movement, including at openings, services penetrations and flues.
• Ensure that any sealant has been manufactured to meet movement gap requirements.
• Breather membranes on the outside faces of the timberframe wall panels.
• Suitability of spandrel panels in terms of structural stability, fire resistance and acoustics.
Aine Finlay, Architectural Project Manager at KORE Retrofit
In both new construction and retrofit projects, airtightness at the openings prevents thermal bridging, which in turn reduces heat loss and improves comfort. Here’s what to keep track of for the window and door installation.
Detailing at reveals:
If you are getting external wall insulation (EWI) fitted, a common detail is to move out the new window to the edge of the existing masonry structure. This leaves a smaller reveal at the outside edge to let more light in and has the added benefit of reducing thermal bridging.
This detail also gives an opportunity to allow for airtightness tape to be fitted internally. Airtightness around windows and doors typically involves applying an airtightness tape that bridges 50 per cent of the frame and the adjacent substrate, whether timber or masonry.
This tape provides a consistent, continuous barrier that eliminates air leaks.
While airtightness paints are increasingly popular, they should be considered supplementary in these highstress areas, with the primary airtight layer established through tapes.
Thresholds: Thermal bridging around doors and windows is often most pronounced at thresholds. One effective approach is to minimise the threshold length by opting for a sub-wall rather than floor-toceiling glass, reducing the exposed area and thus the potential heat loss. Incorporating structural insulation materials, or in some cases aerated concrete blocks, beneath thresholds can also help.
Sealing the external face of windows: If caulking and weatherstripping are not properly applied around the window during installation, it can lead to gaps that cause draughts or water penetration.
Remove guides: A window that is difficult to open or close may have a damaged or
misaligned mechanism, or the track may be dirty or obstructed. Often, window companies use guides during transit to prevent damage. If these are not removed, it can cause an obstruction during opening and closing.
Servicing: It is common for windows to require a service after installation: the hinges may need tightening, along with the alignment made good.
Safety catches: These are an important fitting on any new window.
Building Regulations state they are required on all openings over 1.4m from the ground level outside, no matter the size or type of window.
Safety catches on windows are devices designed to prevent windows from opening too far, often for the purpose of preventing accidents, especially in homes with children or pets. They have the added benefit of improved security by preventing the windows from being opened from the outside.
in windows can affect their performance, appearance and longevity. There are several common types of imperfections to be aware of. These issues can arise during manufacturing, installation, or even during transit. Surface scratches can occur during handling or installation. Scratches can be superficial or deep, affecting the aesthetics of the window. While they may not always impact function, they can make the glass and/ or frames look damaged and degrade the overall appearance of the window.
Weep holes: While not every window has them, they are an important part of your new window. They exist to allow any water ingress to ‘weep’ out, ensuring that water is not held within the window to cause swelling or a leak internally.
Check delivery times: These can vary wildly between window companies. Some can be as quick as three to four weeks, while others take up to 20 weeks for bespoke designs. This can have a huge effect on your construction programme.
Underlays below slates and tiles will be delivered in rolls. In roofs of buildings in areas of severe exposure, boards or rigid sheets may support the flexible underlay. Check that:
• The underlay and any support boards are all of the correct specification.
• It is undamaged and the manufacturer’s instructions are being followed.
• Laps are of the correct size and the underlay continues over hips.
• It is cut neatly and not torn, around service penetrations in the roof covering.
• It is fixed over rafters at vertical laps and secured by battens over horizontal laps.
• Support is provided at the eaves, e.g. by using support trays, to prevent sagging.
• The underlay is UV resistant at the eaves and over gutters or a proprietary eaves guard is used.
• It is dressed correctly under ventilated ridge systems.
• It is turned up at abutments, usually a minimum of 100mm.
• It will allow any water to pass behind the slating or tiling battens.
Cold roofs require ventilation between the timber members
and over the insulation, with an unbroken airflow between the lowest and highest external points of the roof on each slope. VCLs are usually polythene or polyethylene of a minimum thickness of 125 µm (500 gauge).
• Common ventilation problems are encountered at lean-to roofs at wall abutments, roof slopes meeting at valleys, above and below roof windows or other obstructions and where a flat roof meets a pitched roof. Ventilation failure is very likely to lead to condensation within the structure and decay of the roof timbers.
• Attention needs to be paid to the junctions of wall and roof insulation to provide continuity of the thermal envelope. Ventilation routes can be maintained by inserting rigid insulation boards snugly between rafters to prevent the ceiling insulation quilt from blocking the airflow. Preformed plastic trays can also be used.
• To prevent birds, small animals and larger insects from entering the building through ventilation gaps, they should be covered with fine mesh of maximum 4mm apertures.
• Minimum permitted vent sizes at eaves and ridges will differ according to the roof shape, pitch, span, air permeability of the roof covering and type of underlay used.
• VCLs should be fitted only after the building is
weathertight and the moisture content of the structural or framing timber is 20% or below.
• VCLs should be fixed at maximum 250mm centres, sealed at all penetrations and jointed with minimum 100mm laps which should be fixed to timber members.
• Lap and seal VCLs in around openings in roofs and walls.
• Check that all recesses in ceilings, such as downlights, are correctly sealed.
• Repair any tears in VCLs before they are covered over.
• Ensure that a VCL is always fitted on the warm side of any insulated element.
• If using ballast, the roof structure must have been designed to support it and it must prevent wind uplift of the layers below.
• Insulation on warm roofs should wrap the structural timbers within the thermal envelope.
• Counterbattens running in the direction of the slope are required on warm pitched roofs to avoid any moisture from building up behind the horizontal battens.
Insulation for warm roofs should be bonded or mechanically fixed to resist wind uplift in accordance with the manufacturer’s recommendations. Insulation of warm flat roofs can be laid ‘loose’ and ballasted to resist wind uplift.
• All insulation on warm flat roofs should be kept dry to avoid trapping moisture.
• Care should be taken to prevent condensation buildup in ducts or pipes passing through insulation layers. Such ducts or pipes should be rigid with the correct CE or BS markings and laid to fall to the exterior of the building. Some commonly available types of flexible ducts are of very inferior quality, so avoid.
• Attic decking for walkways or light storage, or platforms for water tanks or MVHR units, etc. must be supported on legs to be at least 50mm above the height of the uncompressed ceiling insulation.
• Ceiling insulation in attics should go around and over, but
not under, water storage tanks.
• All water pipes and overflows on the cold side of the ceiling insulation must be insulated.
• Loft hatches must be insulated and fitted with air seals and holding-down catches.
A flat roof which is intended to also act as a terrace, deck or roof garden should have design details for access and perimeter guarding. The roof design should account for any permanent service equipment to be installed on it and temporary construction loads.
Timber is not a suitable material for any element of the guarding around a roof, terrace or balcony and also should not be used as a structural support for a terrace or balcony.
• For green roofs, make sure that the guidance in the GRO fire risk guidance document and Building Regulations is being followed.
• Any surface protection provided to the waterproofing layer must satisfy the fire
protection requirements in the Building Regulations.
• Pay attention to the waterproofing details at abutments, joints between the roof waterproofing and the wall cavity trays or DPCs and the heights of waterproofing to be dressed up walls. Noncombustible trays may be required in external walls.
• Flat roofs may be used for emergency egress, with a protected route leading to a safe place on the ground. Guarding will almost certainly be required.
• Emergency egress can be provided from dormers and rooflight windows.
Gutters are not water storage vessels, but are intended to get rainwater off your roof structure. Some gutter installers lay them flat but they should have a slight fall towards the outlet, as should built-in gutters in flat roofs and in level valleys between two adjoining roof slopes.
• Rainwater outlets in flat roofs must be recessed into the waterproofing layer.
• Check that the installer is using the correct sizes of gutters and downpipes, as specified.
• Check the fall towards gutters and rainwater outlets in flat roofs.
• A blue roof should have a slow run-off to attenuate the rate of water flow into stormwater drainage systems. Blue roofs should be constructed as warm roofs, with flow restrictor outlets and with overflows which are visible when in use.
• Drainage outlets in built-up roofs (green, brown, biodiverse, etc.) should have inspection hatches fitted at surface level.
• Green or biodiverse roofs may require automatic irrigation systems.
• Check gutter and downpipe joints and supports for strength, spacing and fixing.
For more about roofing watchpoints
As with all other structural elements, a new or renovated roof will have resulted from a design process that conforms with the building regulations, planning guidance, client preferences, the physical shapes required, external finishes and the structure needed to support it.
Most roofs with a timber support structure will consist of a weather resistant roof covering on battens or decking, supported by rafters or joists. In terms of insulation configuration, there are two principal types, warm roofs and cold roofs. Essentially, a warm roof has its insulation between and over the rafters or joists and a cold roof has the insulation between and under the rafters or joists.
Flat, or sloping roofs of up to a 10 degree pitch, may also be constructed as green, biodiverse or brown roofs. Blue roofs need to be flat. These non traditional roof types tend to be heavier so generally require a stronger supporting framework; and they should be constructed by members of the appropriate trade bodies, such as the National Federation of Roofing Contractors (NFRC) or the Green Roof Organisation (GRO), etc.
As alternatives to the ubiquitous slates or tiles, roof coverings can be lead sheet, zinc and zinc alloys, copper, stainless steel, aluminium, shingles, composite products and thatch. Advice is available for the correct use and fitting of each of these alternatives, for instance the Thatching Advisory Services (TAS), the Federation of Traditional Metal Roofing Contractors (FTMRC) and the Lead Contractors Association (LCA) are just some of the bodies which supply extensive guidance.
For slates and tiles, there is a huge range of natural and man-made products available, so know what you are buying and study the manufacturer’s written technical guidance carefully.
Fascias, soffits and barge boards may be timber, composite, PVCu or a metal product maybe matching the roof covering. If timber, they should all be preservative treated or be naturally durable and the first coat of stain or primer should be applied to all surfaces before fixing.
Prefabricated roof cassette systems may be supplied, similar to timber frame construction, in which case the requirements are: certification for the structure and its installation, durability, moisture protection, structural, thermal and acoustic performance, fire resistance, ventilation and condensation control.
Installers of solar roof panels must liaise with the roof covering manufacturer before work commences, in order to ensure compatibility, stability, weather-tightness and any special requirement for flashings and fixings. At coastal locations, grade 316 stainless steel fixings and brackets are usually recommended.
• Internal downpipes must be insulated.
• Where gutters are positioned behind parapet walls, overflows must be provided.
• Smaller surfaces should be drained, such as balconies, terraces and small roofs.
• Where roofs have upstands on all sides, there should be a minimum of two rainwater outlets provided to two separate downpipes.
• Firring pieces should not taper to zero, but should be a minimum of 38mm high at their lowest ends. It is vital that these are accurately cut.
• Any structural timber which may be exposed to the weather or which may be subject to wetting and all timber used in flat roofs, should be kiln dried and vacuum treated with preservatives. Any cut edges of structural timber should be re-treated.
• Check all structural timber to confirm that it is as specified on the drawings.
• All timber, including solid and engineered joists, should be checked on delivery and any which are excessively wet, distorted or damaged should
be rejected. All timber products should be stored under cover to prevent wetting or sweating until they are going to be used.
• Check that metal web ‘space’ joists or ‘I’ joists are being installed in accordance with the manufacturer’s design layout and technical instructions.
• Cross-laminated timber (CLT) is generally not acceptable for use in flat roofs.
• Structural insulated panels (SIPs) are not acceptable for use in warm flat roof construction.
• Check that the decking material has been supplied according to the specifications.
• For metal roof coverings, there are certain species of timber which should not be used with certain metals.
• Plywood or OSB decking boards should have movement gaps at rigid upstands. Square edge boards require an additional movement gap between boards.
• Roof decking boards are usually tongued and grooved (t&g). Square edge boards should be used for metal roof coverings.
• OSB decking should have arrows denoting the direction of fixing in relation to the joists or firrings.
• Timber nogging pieces are needed under any edges of
decking which do not have direct support from joists or firrings.
• Decking should be fixed at 100mm centres using the correct sizes of ring shank nails.
• Timber decking should never be allowed to get wet.
• All metal fixing components and fastenings should be of the correct size, corrosion resistance and strength.
• Metal components must be fixed strictly in accordance with the manufacturer’s details.
Prefabricated roof trusses are designed and manufactured specifically for each roof and should never be adapted. Check for:
• Condition of all timber and the joint plates upon delivery to the site.
• Handling, stacking, ventilation and weather protection when stored on site.
• Dimensions, including overhangs, angle of pitch and spacings when erected.
• Stamps and markings of compliance with standards.
• Bearing lengths on truss shoes.
• All bracing is provided at the correct locations.
• Straps at wallplates and lateral restraint points.
• Multiple or ‘girder’ trusses should be factory-fixed together.
• Trimming and supports around openings such as chimneys, hatches and roof windows.
• Support platforms or decking on the ceiling joists.
• Intersections between truss roofs and cut roofs.
• Strutting where the bottom chord of a truss acts as a floor joist.
Cut roofs will be specified on the drawings; check for:
• If different strength grades of timber are being used in
different parts of the roof, make sure that the right grade of member is in its proper place.
• The structural frame must be fully completed before any roof coverings are fitted.
• Purlins and binders should be built in to supporting walls.
• Valley boards and hip rafters must be wide enough to accept the full cut of the rafters.
• Valley rafters will be larger than the main rafters.
• Purlins should be mitred at hips and jointed to take the bottoms of the hip rafters.
• Check that any joints, holes and notches in the timber members comply with the building regulations and the working drawings.
Wallplates are common to both trussed and cut types of roof. They should be:
• Jointed using half-lap joints, including at corners.
• Bedded straight and level and strapped down to the walls.
• Tied across at corners using angle ties and tied to hip rafters using dragon ties.
• At least 3m long or extend over at least 3 joists, rafters or trusses.
Timber slating or tiling battens should be sized to suit the roof covering and the rafter spacing, be at least 3m long and be fitted to avoid joints occurring over the same rafter. Zinc-coated annular ring-shank nails of the correct dimensions should be used to fix battens, but use hot-dip galvanised steel nails or aluminium nails on roofs in coastal areas.
Follow the manufacturer’s written technical instructions if using metal batten and clip systems for slating and tiling. Nails for fixing slates or tiles can be silicon bronze, phosphor bronze, aluminium, stainless steel or copper; but not
galvanised steel. They should be at least 38mm long and penetrate at least 15mm into battens. Additionally, hooks and clips may be used. Check the slate or tile manufacturer’s fixing schedule.
Slates or tiles on mansard roofs, dormers and dormer cheeks will require additional fixings, so check this. Cut tiles or slates on dormer cheeks close to the main roof surface. Follow the verge construction details on your drawings.
Flashings can be formed using lead, aluminium, aluminium alloys, zinc alloy and copper. Other proprietary lead alternatives and GRP products are also available. Follow the details on the drawings and guidance literature such as the Lead Training Academy’s manual.
The job of forming, welding and fitting lead flashings is skilled and quite complex. Ensure that lead is the correct code for the exposure rating and watch out for things like protection of lead against reaction with mortar, the heights of upstands, lap lengths, strip lengths, methods of support and fixing. Saddle flashing should be fitted at the tops of valleys.
installer on site. Confirm that adhesives are compatible with any additives in the concrete.
• The installer of any bonded waterproofing layer to be laid on concrete or screeds should carry out adhesive bond tests before commencing.
• Some precast decks require a screed to achieve their intended strength and these can be sloped to create falls.
Warm flat roofs can be built up on profiled metal deck sheeting. There are a number of methods used for the make-up of these roofs, so check yours. Any insulation board used to span across the troughs of profiled metal deck sheeting should have adequate compressive strength or be laid on support boards across the profiles.
Insulated metal roof cladding can be used on a steel framed construction to create roofs which can range in pitch upwards from as low as 1.50 (after deflection).
to outlets, before handing it over to the waterproof covering installer.
• Provide walkways to protect the membrane until all works are complete.
• After the covering is laid, it should be checked by an independent testing company using electronic leak detection equipment to prove the integrity of the waterproofing layer.
• Re-test any defects which have been repaired.
• Get the test report and a written warranty for the materials and installation on completion.
Proper access to roof voids will allow for inspection, maintenance and possibly removal of equipment including ventilation units, water tanks, roof-mounted services (e.g. solar panels), TV and telecoms cables and connection boxes and other plumbing and electrical components.
Openings need to be made for dormer windows, rooflights, and chimneys. The details for doing this should be shown on the drawings. Wider openings such as stairwells require design input by a structural engineer. Multiple trusses will be installed to each side of an opening. Check that:
• All openings are trimmed and supported correctly.
• There’s a minimum gap (usually 38mm) between roof timbers and the face of any chimney.
• Openings in roofs must not impede the ventilation airways.
Although less common, reinforced concrete decking can be used, either cast en-situ or precast. Concrete which is cast ensitu should be propped and protected until fully dried and cured. All precast concrete decking must have minimum bearing distances, so check this with the designer or structural engineer.
• Check the moisture content of concrete decks before bringing the waterproofing layer
Waterproof roofing membranes are most often used for flat roof applications but can also be used on pitched roofs. Most flat roofs are covered with a proprietary single-ply membrane, but they can still be waterproofed using modified bitumen, mastic asphalt or liquid-applied products.
• Check that the installer is a member of a suitable quality control certifier.
• The erector of the flat roof deck should survey it when complete in order to correct any depressions and to verify the falls
Access to roof voids should:
• Have a minimum opening width and length of 520mm.
• Not be located in hazardous locations, such as over stairs.
• Be served by decking, walkways or platforms (of at least 1.0 m2) to allow maintenance of the equipment.
If the roof has only a small void which doesn’t contain permanent equipment or services, access may not be required.
• Correctly sized ventilation is provided around any dormer at the sill, head and both sides.
• Breather membranes are fitted correctly around dormers.
• Dormer walls have air and vapour control layers (AVCLs).
• Dormer side walls or ‘cheeks’ should be supported by double rafters or joists.
• Prefabricated or proprietary dormers are fitted correctly.
• Integrated solar roof panels may require spaces under them for ventilation.
“Timber is not a suitable material for any element of the guarding around a roof, terrace or balcony and also should not be used as a structural support for a terrace or balcony.”
I come from a construction background and worked with large builders for many years so even though I hired a main contractor, to source subcontractors and materials, I decided to take on the role of project manager for the whole thing. It made perfect sense as I’m used to drawing up construction schedules and working to them.
Because they are at the mercy of the market, small builders have a tough time. Big contractors sway in the wind but the small ones can get knocked down. They’re at the bottom of the
pile for everything; if the big contractor needs something, the small one will have to wait.
The other thing is they can be their own worst enemy, in that they don’t plan the details very well. The big contractors have no choice but to be well prepared, otherwise you’d have mayhem.
At best, small builders will plan a month ahead. Often small contractors start out as sole traders with one construction trade, so this could explain why they tend to work out the schedule instinctively. They’re not looking at things like information programmes or decision programmes, procurement programmes or items with long lead times.
The problem with that is
Site size: 740sqm
House size: 95sqm
Bedrooms: 2
Site cost: €170k
Build cost: €340k
Heating: Air to water heat pump
Ventilation: Centralised mechanical with heat recovery
Construction: ICF
BER: A1
they have no contingency if they need their roofer on three sites at the same time, for example. Someone will just have to wait.
When we were getting within a few months of the handover date, I was getting nervous that there would be a delay on finishing. I did up a programme on MS Project and showed it to the builder. It showed a very tight run in with no contingency and by the time I issued it, there was already another few days of delay.
The contractor kept assuring me we’d be in before Christmas, and I asked him what part of the programme he would accelerate to make that happen. He said he’d just do it. As expected, this didn’t happen, but I could see it coming a few months away.
As required by the building contract, the contractor had the required insurance for the building works. Once we reached practical completion, we were required to take out our own home insurance and this proved quite a challenge as insurance companies were reluctant to quote for a house built with Insulating Concrete Formwork (ICF). ICF is viewed as relatively new, despite being around for more than a decade and there’s a very limited claims history in ICF houses. Consequently, insurance companies consider ICF to be a higher fire risk. However, most new ICF houses are now heated without fossil fuels, removing a major source of fire, and all materials are fire rated to such an extent that the fuel source is not significant. You’d think no claims, no fire source and negligible availability of combustible materials would be a positive thing but not for the insurers. In the end, I only got one quote, at €1,200 for the year, which is crazy but I had no choice but to accept it.
While the contractor could see the benefit of a detailed programme and agreed that he really needed to plan this way, he had never taken this approach even though he had run a successful building business for over 25 years.
Ideally, a project management programme should include not just the things that happen on site, but the schedule of procurement dates, the lead in times for all the critical items, an approvals schedule, a schedule of the decisions needed from the architect and the engineer and the dates the designers need
Get Louis’ construction programme here
decisions from the client.
At the end of the day, project management is not rocket science. It’s just a question of agreeing a reasonable duration for each task with the builder and allowing sufficient time for procurement, approvals and decisions. With this approach, very quickly you’ll see where the finish date is going to be.
We went with a strip foundation, and I had the building energy rating (BER) person involved in checking it would be built up to an A1 standard.
We went with a liquid screed and before pouring it, I asked the plumber to make sure the underfloor heating pipes were pressurised and filled with water. This meant that they could walk on the pipes to lay the screed, and the screed wouldn’t weigh down on the pipes.
Then the Insulating Concrete Formwork (ICF) walls went up. Our builder only builds with ICF and he had everything braced inside and out. Nothing moved during the pour and, as we built a bungalow, it was all done in one pour.
A benefit of going with ICF is you can order your windows early; on a block build you need to wait until the window openings are formed, to measure the as-built
dimensions, before you can place your order.
On our build we had agreed to the RAL colour and specifications of windows and doors with the architect, in the presence of the builder, and I had presumed the order would go in immediately. I decided to go with the window company that the builder had recommended, so that if there were any issues they couldn’t complain it was because we hadn’t gone with the person they were used to dealing with.
Two weeks on, when I enquired on the progress of the window order, the builder told me he was still waiting on the written instruction from the architect. That set us back two weeks, as we had to wait on the windows before the internal plastering could start.
Because lead times are long on windows, ensure you get the window choice finalised as early as you can and, crucially, keep on top of making the instruction. It is good project management practice to request a copy of all time-critical instructions from the architect and to push the builder for written confirmation that follow up action was taken on each instruction. Don’t assume the builder will take the initiative, or that he will chase up loose ends.
For the roof, the architect had originally specified a clay tile, which is what the builder’s roofers were used to working with. We had a preference for slate and from experience, I knew that it shouldn’t take more than a week to roof a house like ours with slates. However, because the roofers were more used to working with
For the suppliers list, specification, and more tips and advice, read up on the first two parts of Louis’ project here
tiles, it took them longer than the week to do it.
This highlights the fact that decisions which change the materials being used can have both a time and cost implication. Make sure you get confirmation from the builder on any such time implications as well as cost implications, as this can lead to disagreements later.
For water and wastewater we connected to the mains. We had a rainwater harvesting system for greywater, which drained the excess into a soakpit. This was sited under our planned vegetable patch. Having good soil and drainage in that area later worked very well for vegetable growing.
An aspect that’s often overlooked in house building is health and safety. It’s a legal requirement to appoint project supervisors for both the design and construction stages.
Our architect took on the role of PSDS (project supervisor design stage) and the contractor took on the role of PSCS (project supervisor construction stage), which is the normal arrangement on construction projects.
What I have noticed from several years in the industry is that small builders are not as rigorous as large contractors in their adherence to the detail of health and safety legislation. They rely much more on how safe they feel in the workplace but this sometimes means scaffolding doesn’t necessarily have the required certificate or that the correct PPE might not always be used.
That said, the builder made sure the people on site had completed Safe Pass training and was very aware that the insurance won’t pay out if there’s a problem and safety has not been properly managed.
A few things should be kept in mind at the outset, to make landscaping easier later on.
Plan the layouts of the front and rear gardens to establish the preferred locations of the soak pit, a rainwater harvesting tank (if you plan one), locations of sheds/greenhouse, etc.
Spread out the topsoil. It will eventually be needed at the front, and at the rear of the house. Consequently, the storage of topsoil from excavations should be split between front and rear, in the correct proportions.
Provide ductwork for potential electrical supplies to any part of the garden. Also decide on where you might need water outlets for external taps and lay the pipework that you will need.
Look to reuse anything you can for the garden. For example, our site had a number of sheds that were built using railway sleepers to support the walls of galvanised sheeting. We used these sleepers for flower and shrub beds.
Ensure that the levels are right. The manhole covers need to be at the level of your lawn or driveway, to avoid dips (risk of water pooling) or protrusions (tripping hazard and visually not pleasing).
In part two of his self-build diary, Patrick McMullan explains how he got on after breaking ground, with a special focus on making the home well insulated and airtight.
We started on site on the 18th July 2023. Thankfully, it was a relatively smooth process. The first reason it went well is that we had a topographical survey completed by a land surveyor prior to our planning approval. This was useful in making decisions about the house location, boundaries, and the design of the drainage system.
We were lucky in that breaking ground coincided with a spell of lovely summer weather, so it made it easy for the groundwork contractor to get tractors, diggers and dumpers across the dry agricultural land to begin site clearance.
The site entrance was an
existing agricultural entrance which had excellent visibility splays in both directions and it also had a partially stoned lane which helped speed up the entire process.
I had an account with a local quarry so was able to get whatever stone (4-inch crusher run) the contractor required to complete the lane.
I set up an account with the local builder’s merchant which was extremely useful to the tradesmen as they could get materials without delay. Due to the volume of materials being ordered, the builder’s merchant agreed to deliver for free.
I bought an old skip which we used to organise the waste materials, nearly all of which could be recycled. This meant we saved on landfill costs.
We then set up a temporary site office from an old container which we used mainly for storage of materials but also included A1 copies of all the architect’s working drawings which was useful for tradesmen on site. It meant that all materials and drawings were protected from the elements and could be locked securely at night.
We also installed a camera on site which helped to remotely monitor activities and provided some form of security. The mature roadside hedge and long lane meant security wasn’t a big issue.
After the plot was stripped, I had a civil engineer come out to mark out the foundations and take levels. As the site was relatively flat and the soil had a good bearing capacity we used a shallow strip foundation.
Our contractor, builder and engineer were all local and had worked together on projects before, so they were able to complete the foundations, build the footings and pour the subfloor relatively quickly.
It was a huge advantage to use local tradesmen who were familiar with each other as they worked together and were
House size: 250 sqm
Bedrooms: 4
Plot size: 2 acres
Site cost: gifted
Build cost: £250k
Construction: masonry cavity wall
Ventilation: centralised
mechanical with heat recovery
Heating system: air to water heat pump
willing to improvise to fix any small issues on site without any assistance.
At the design stage, we had initially looked at an ICF (insulating concrete formwork) building method, which had its advantages in terms of a fast build speed and giving a high performance building envelope.
However, with the high initial cost coupled with the lack of familiarity in the building trade we just didn’t feel comfortable with this method. Similarly with timber frame construction. It again would have the advantage of increased build speed with reduced labour and waste on site but personally it felt like it would require more maintenance over its lifespan and would be less stable than masonry.
We were happy to settle with the tried and tested method of masonry cavity wall construction. Primarily this was due to the familiarity within the industry, which meant we had several options in terms of the labour and materials.
We also knew there would be almost no maintenance considerations, and it would provide good structural strength and durability. The added bonus from a passive house perspective is that it would provide a good thermal mass to the building which will help moderate indoor temperatures by stabilising temperature
For detailed costs, timeline, floorplans and specifications, read up on part 1 of Patrick’s diary here
fluctuations, reducing the need for heating and cooling, and improving overall comfort.
The actual building of the blockwork was very standard practice. We went for a 200mm full fill cavity to achieve the required U-value for the walls.
A few small tweaks we made to incorporate passive principles was to use an insulated block on the inner leaf for the first course of block from the subfloor. This creates a thermal break from the foundation to the internal wall which stops the heat from inside going down into the foundation and conversely stops the cold from outside entering up through the floor.
We went for a truss roof with no chimneys and finished it with a Brazilian slate. Due to the simplicity of the house shape, we saved on both material and labour costs. As a rough estimate, I calculated we saved around £8,000 in materials alone by having no chimneys and a simple pitched roof. It meant we didn’t need any lead, flues, fascia, soffit, and there were no slates needed to be cut when being installed which was a big saving.
The two guys who slated the roof, a straight gable-to-
gable run, completed the house and garage in just two days. As well as saving on costs we found having no chimneys, rooflights or bay windows also helped with the airtightness of the building envelope, so it was a win-win scenario.
The next stage was to prepare the window openings for the window installation. Even though we went with a well renowned, high quality window installer I still felt it necessary to apply a light plaster screed around the window openings for two reasons.
Firstly, its closed off the exposed blockwork around the frame which helps with airtightness, and it meant that we would have a perfectly flat surface to apply the airtight tape to after installation.
Having spoken to numerous people in the industry over the years, almost unequivocally they say the biggest gain achievable in terms of airtightness in the home is to tape the windows and doors after installation.
Even though these window/ door reveals will be plastered afterwards, which is also an airtight coating, very often cracks or gaps will appear around the frame as the house
dries out, which can have a huge effect on how effective that airtightness barrier is.
This can lead to draughts around windows/doors which will make the house uncomfortable and prone to temperature fluctuations. It’s definitely worth doing even if you are not trying to achieve the passive house standard.
We used airtightness paint on door openings that were close to the external wall prior to internal doorframes being installed, as this is another weak link. If the door frames are installed without this preparation, then the frames
would be fixed to exposed blockwork, which wouldn’t be good practice.
At this point prior to any internal plastering, we pumped in the EPS (expanded polystyrene) beads into the cavity. We went with a 200mm cavity to achieve the required U-values of 0.15W/sqmK for the passive house standard.
This pumped insulation technique was very appealing due to its speed and the size of the cavity to fill, it also meant there would be no waste and it also eliminates thermal looping
“ As a rough estimate, I calculated we saved around £8,000 in materials alone by having no chimneys and a simple pitched roof.”
which can be very common with built in cavity insulation boards.
The wall is drilled at specific points and the beads are mixed with glue and pumped in under pressure. The cavity will still be able to breathe; the bead will not absorb water and will not allow the transfer of water across the cavity to the inner leaf.
We had extra holes drilled under windows and the entire top row of blocks were drilled to ensure that the cavity would have no voids and be totally filled. We worked with a local company who has an excellent reputation in this area, and we were very pleased with the level of workmanship.
We never liked the idea of built in insulation boards for the cavity, because it is incredibly difficult to install correctly. A gap
of just 10mm has been proven to double the heat loss, which is known as thermal bypass.
We are building a two-storey home and chose hollowcore precast slabs to build the first floor, mainly for its soundproofing quality. It is very important for the airtightness of the building envelope that the ends of the slabs on the external walls are wrapped with an airtight membrane.
This means that there is no break in the airtight envelope from the ground floor to the first floor which means it follows the ‘pencil rule’ which is one of the key aspects of passive house.
If the ends of the slabs aren’t wrapped, the airtight envelope stops at the underside of the
slab on the ground floor and restarts at the top of the slab on the first floor. This means there will be movement of air at the junctions where the wall meets the slab and down the slab itself and out into the external cavity wall.
We coated the entire external
this time, so it was cheaper to go with the sand and cement render.
After the suspended metal ceiling was installed, we also insulated the ceiling void on all external walls with 100mm fiberglass insulation. This means that the ceiling void is
walls down 200mm from the precast slab with a sand and cement plaster. This means that even when the suspended metal ceiling is installed, the void between the slab and the ceiling will still be airtight and means that there is no break in the building envelope.
This could also have been done with airtight paint, which is probably more common, but we had a plasterer on site at
fully airtight with render and then insulated, which will help to retain the heat within the building envelope.
If this detail is missed, it can be extremely expensive and time consuming to retrospectively amend – especially if plasterboard or even rendered ceilings have already been completed. It’s important to have this scheduled in at the right time.
The next job to complete was the installation of the airtight membrane on the first floor ceiling. As mentioned previously our attic is a cold space so our airtight envelope stops at ceiling height.
We worked predominantly with a specific brand of airtightness products for its excellent reputation and for being readily available in local builders’ merchants. To try and achieve maximum airtightness and avoid even staple holes in the membrane, we used double sided tape on the underside of the joists and stuck the membrane up. This worked well.
It’s very important to tape any protrusions through the membrane such as electrical wires, vents, spotlights, etc. to ensure maximum airtightness is achieved. We then taped the edges of the membrane to the masonry wall to complete the airtight envelope.
This membrane will ensure that there will be no movement of air/heat through the ceiling
into the cold attic space, even if some hairline cracks appear over time in the plastered wall and ceilings.
We then moved on to insulating the upstairs ceiling with 50mm PIR board below and 150mm of fiberglass insulation above which meant we achieved the 0.15W/sqmK passive house U-value standard.
We chose to go with PIR board and plasterboard separately as opposed to insulated plasterboard for a few reasons.
The main benefit to taking this approach is that you can tape the insulation joints separately and you can also overlap the joints with each plasterboard sheet to give a more airtight finish, as opposed to butting insulated plasterboard sheets together which can leave gaps. There is also much less waste with this method and although the labour costs increase, the material cost is cheaper, so overall it is more efficient financially and performance wise
to install them separately.
We tried to use as few fixings as possible during installation as the screws penetrate the airtight membrane above, so we taped every screw head with airtight tape afterwards.
Another big aspect of getting the house airtight was both the internal and external plastering as the plastering coats themselves provide an airtight finish.
Internally all walls were masonry built, so we used a sand and cement base coat and finished it with a gypsum plaster. This is standard practice in most masonry builds so there are good labour and material options available.
We let this plaster cure slowly to avoid shrinkage cracks and made sure the house was well ventilated to allow the moisture to escape as the porous plaster can absorb moisture from the air which can lead to mould growth. The ceilings were bonded and finished with a gypsum plater which again is standard practice.
Externally we were keen to get render on the house to keep it air and watertight. We had looked at lots of options but eventually settled for a sand and cement scratch coat with
Thermal looping: Constant air movement within the cavity wall due to warm air rising at one end and cool air descending at the other end, which negates the performance of the insulation.
Thermal bypass: Heat loss from a break (gap) in the insulation.
U-value: Measure by which the energy efficiency of a building element (thermal resistance) is measured; the lower the value the better.
PIR: Polyisocyanurate is a plastic insulation material that comes in board form; it’s the most common board material used in Ireland today as it strikes a balance between cost and efficiency.
EPS: Expanded Polystyrene is a plastic insulation material that comes in board form, most commonly used for floors, and in beads for cavity walls. It’s a less effective insulant (you need a thicker EPS board to achieve the same thermal resistance as a thinner PIR board) than PIR but more cost effective overall.
a rubbed-up sand and cement finish.
The house will eventually be painted but this external render leaves us with a blank canvas as we take time to decide what colours will work best.
The most important thing is that we have an excellent airtight coating on the external surface of the house as at this point in the build it was coming into autumn/winter. This render coating allows us to carry out our airtight testing, as it means all exposed leaky blockwork has
been covered.
We then moved on to insulating the floor. On the ground floor we went with a build-up of 50mm liquid insulated screed to cover all pipework, and then 150mm PIR board split between separate 50mm and 100mm sheets which got us the required U-value for passive house standard.
Like the ceilings, we split the PIR sheets so that we could overlap the joints. No matter how tightly fitted, a single 150mm
sheet would have air gaps when butted together.
We also went with a 50mm PIR board upstand on all external walls to create a thermal break on the floor to wall junction. Our engineers report detailed that a 25mm upstand was sufficient but with such little difference in the price of 25mm and 50mm PIR board, around £2 per sheet, we felt it best to go with the 50mm.
We took a three-pronged approach to airtightness: airtight paint, airtight tape and sand and cement render. A key consideration is to ensure that there is no exposed blockwork as it has very poor airtightness due to it being an extremely porous material.
The benefit of using the insulated liquid screed for the first 50mm is that it covered all pipework and left a perfectly level floor, so there is no cutting or levelling required on the PIR boards which improves their performance, reduces waste and speeds up installation. We taped all joints on each layer of PIR board to leave a well-sealed uniform surface.
Upstairs we went with 50mm PIR board with a 50mm upstand on the floor to wall junction. We then taped all joints with aluminium foil to make sure there was no air gaps.
If I was to do this again, I would have gone with insulated liquid screed upstairs as there were pipes to cut around which was time consuming, and reduced the performance of the PIR board. The hollowcore slabs can also be uneven when laid, so some of the floor had to be levelled with sand to prevent them from see-sawing.
We used airtight paint on the floor to wall junction as well as in all the external wall chasings (tracking). The airtight paint is useful for difficult to reach areas or uneven surfaces.
Generally, the wall chasing will have conduit installed and then a plaster coat over the surface, but this still leaves a lot of exposed blockwork in the back of the track. This allows
unwanted airflow.
It may not seem significant but if you add up the total number of metres in the entire home then it is. This can be felt very clearly in some homes where you can feel a draught around switches and plugs.
Even after the electrical wires have been installed it’s a good idea to close the end of the conduit with a silicone-based sealer as air could still flow in the conduit if it was running to an area outside the airtight envelope.
Another detail we completed was to fill all ducting voids for the MVHR with insulated beads. This is because our MVHR unit is in the attic which is outside the heated building envelope so it’s important to try and keep this as well insulated and airtight as possible. We also used airtight tape to tape the pipes to the membrane where they protrude in the attic.
Patrick McMullan chose to install solar panels on his house. Here Peter McCarty of First Class Solar walks us through the system.
Patrick McMullen’s installation features a 14-panel photovoltaic (PV) system paired with a hybrid inverter. This setup allows him to use solar power efficiently while preparing for future battery storage upgrades.
The all-black panels were carefully positioned to maximise sun exposure and seamlessly blend with the home’s modern design.
With rising energy costs, this system is projected to produce 5,128kWh per year, saving the homeowner approximately £923 annually.
The system’s total cost was £4,800, which gives them a return on investment of just over five years.
It’s also expected to reduce the property’s carbon footprint by over 1.3 tonnes of carbon dioxide each year, offering both financial and environmental benefits.
For this project, battery storage wasn’t initially installed, but the system is batteryready. Batteries can enhance energy independence by storing excess power for night time use.
While upfront costs will be higher, they’re a valuable investment for those aiming to maximise self-consumption and protect against future energy price hikes.
We often get customers charging their batteries overnight on the cheaper Economy 7 or EV tariff, meaning they wake up through the winter months with batteries full of generally half price electricity.
This installation was on a concrete tile roof, a common choice for self-builds. Each roof type, whether slate, tile, or metal, presents unique challenges and opportunities.
Our team ensures that every system is custom-designed for optimal performance, regardless of roof type.
Slate is typically the most expensive
For a free no obligation quote, contact info@firstclasssolar.co.uk, tel. 028 96 005042, firstclasssolar.co.uk
roof to install on, with tile and slate coming in several hundred pounds cheaper due to both a quicker installation and cheaper roof mounting systems.
Regardless of the roof covering, all solar installations, when done correctly, will be 100 per cent waterproof and won’t be affected by strong winds.
For Brian’s full DIY paint guide, go to the Selfbuild+ Resource Bank here
Impossible to answer accurately since every situation is different. In my experience a small room will need 2.5 to 3 litres of paint; a large room at least 5 litres and an average hall, stairs and landing in the region of 5 to 7 litres.
If you’re not sure, err on the higher side. And remember... if you’re using a paint colour which is not off-the shelf and has to be mixed, buying a 10 litre bucket may work out cheaper and be more consistent in colour than buying 5+5 or even 5+3.
Should I use a brush or a roller to emulsion my
These days a roller is almost always used; a brush is simply too time consuming and tiring. However, there are certain ceilings e.g. those in Victorian properties which may be damaged extensively if you use a standard 9” roller - the suction is too great and will pull off the existing paint.
In that case you have two alternatives: use a mini-roller carefully or use a wide brush.
Personally I do ceilings first, then walls, then woodwork. I would also break down the area into the three distinct sections so you’re not all over the place, particularly when tackling a large room.
If you’re unsure about being able to “cut in” accurately you may find it better to paint the
woodwork first, wait for it to dry completely, then apply masking tape to the edges you’ve just painted and proceed to paint the walls. The downside of this approach is it takes much longer because you have to wait for the paint on the woodwork to dry. The paint will remain soft for a time until it cures completely. Apply ordinary masking tape too soon and you risk pulling off the paint you have just applied. Safe-release masking tape can potentially get around this but it
is more expensive and may still not be foolproof.
To ‘cut in’ means painting at the dividing line between two surfaces – usually the ceiling and walls. The aim is to get a razor sharp line between the wall and ceiling.
A 9” or 18” roller will not be able to cover right into the edge between the ceiling and the wall so switch to the miniroller if the distance between
the ceiling and wall is an inch or more. Very carefully roll out the paint as close to the ceiling as you can get without getting paint on it.
You have two choices here. Either use a 2” synthetic noloss brush or, if you are not so confident, a 15mm sash brush. The synthetic brush holds plenty of paint and lays it down over a broader area than the sash brush but being larger you may find it a little more difficult to work with.
A sash brush is an oval brush which not only holds lots of paint but spreads out to form a consistent line of paint without stray bristles sticking out.
Standard, non-synthetic, flat bristle brushes are not suitable for cutting-in since they do not hold enough paint and tend to have stray bristles which can put coloured paint onto a nice white ceiling.
Belfast
247 Castlereagh Road
Belfast BT5 5FL
T: 028 9045 0103
E: info@agabelfast.com
Open 9am – 5pm weekdays
Saturdays 10am – 2pm
Bangor / Newtownards Greenway Conlig Co. Down BT23 7SU
T: 028 9122 5432
E: conlig@agabelfast.com
ü Woodburners
ü Multi-Fuel Stoves
ü Electric Fires
ü Gas Fires
ü Free Survey
ü Installation
ü Free Advice
Open 9am – 5pm weekdays Saturdays by appointment agabelfast.com
110+ EXHIBITORS SHOWCASING 50+ ADVICE TALKS