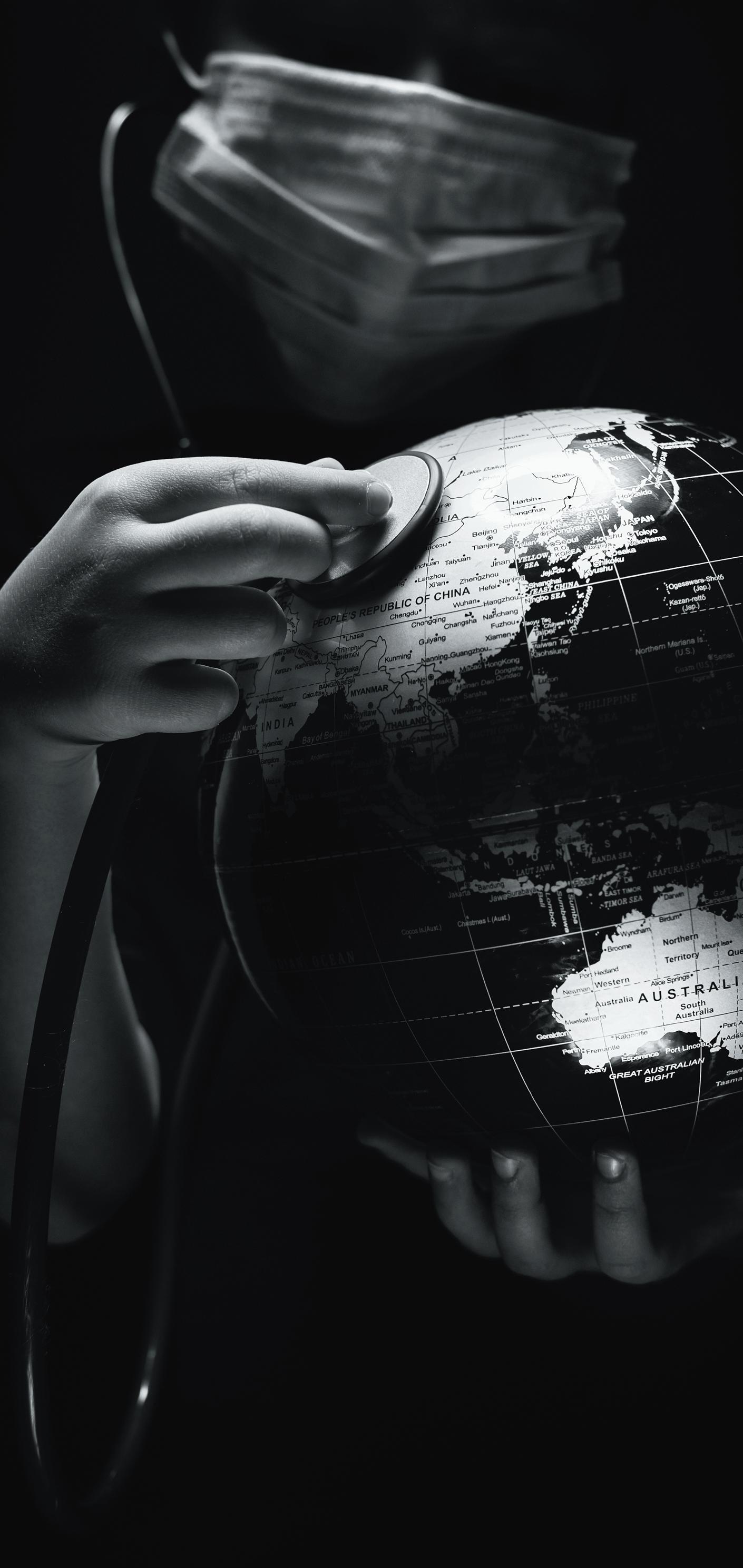
5 minute read
Agile and Flexible – A Fitness Check for the Pandemic Era
from IPI Autumn 2020
by Senglobal
The COVID-19 pandemic era is shaking up the pharma supply chain. Heavily regulated processes that used to take years are speeding up as existing drugs are repurposed as therapeutics for COVID-19 patients and new drugs and vaccines are under development. Kallik CEO Gurdip Singh provides a health check for pharma businesses who are straining every sinew to meet changing market demands.
Many global pharmaceuticals companies are struggling to meet demand, while some are experiencing dramatic drops in demand and pressure to cut operational costs. Every major manufacturer is experiencing disruption across supply chains, driven by volatility in the supply of parts and raw materials. The requirements for social distancing and employee safety measures add an additional level of pressure.
Across the globe, countries have stopped elective surgery to create capacity for treating COVID-19. Medical device suppliers supporting hospitals with procedures such as hip replacements and even elective cardiac surgery have seen a huge impact on their revenue streams. Some have diversified their product ranges to meet the demand for PPE and ventilators. As countries re-open the doors to elective surgery, there is huge pent-up demand for product. The need to able to ship different product lines rapidly has forced changes in manufacturing shift patterns and logistics.
In the pharmaceutical sector, many players have pivoted their operations to join in the race to develop a vaccine or repurpose existing drugs to treat COVID-19. The need to repurpose patient information labelling rapidly to meet regulatory requirements is an immediate challenge.
Normal has fundamentally shifted. Leaders in pharmaceuticals, medical devices, chemicals and cosmetics who understand and act on this new normal will have ample opportunities for growth. The possibility of future pandemics is very real. From now on, suppliers must be mindful that they may have to diversify from mainstay revenue streams at short notice. The dynamic of the supply chain has changed. Traditional, smooth processes will need to adapt to peaks and troughs.
Diversification is key to responding to changes in buyer behaviour and the macro economic environment – and avoiding massive dips in conventional revenue streams. A centralised view of data and insights across the whole manufacturing operation will become a standard component of running a manufacturing organisation.
Diversify to Survive For the survival of many organisations, it is vital to accelerate diversification and boost speed to market. Data analytics, harnessing the power of data that companies already have, can help organisations understand their customers’ fast-changing needs at a granular level. Getting information about the product to the right stakeholders so they can use it safely and effectively is key. Patient information need no longer be produced only in the form of a label or a leaflet. Consider what is the most effective means for people to consume that information – an online video may be a useful supplement to traditional paper information.
If patient information data is stored at component level, separated into symbol, text, or phrase, right through to adaptations for different languages, it will enable faster change. That way, when a company has to diversify rapidly, it is easy to reuse existing data to create new labelling using confirmed branding, logos and phrases. A medical device company that produces predominantly orthopaedic surgical devices might be able to produce ventilators. Reusing existing data, it can get a new product line labelled and out very rapidly. Anyone selling a drug that can be used to treat COVID-19 can repackage and deliver it within a matter of days.
Addressing Staffing Issues Social distancing measures have had a huge impact on staffing. Many organisations have been forced to put in place remote working access for office staff – that meets regulatory requirements – at short notice. Manufacturers may lose up to 50% of their on-site personnel1. To address this, some manufacturers have adjusted shift patterns to reduce the number of staff on site at any one time. Longer term, increasing process automation is more effective.
In the scramble to pivot business models to address fast-changing supply challenges, it is difficult to look ahead to the likely long-term changes to the sector. Some things won’t change. We don’t need a pandemic for organisations to know they need to focus on driving efficiency. That is something that is always at the heart of business. Automation, supported by the Internet of Things (IoT), is increasingly looking like a sensible way of achieving greater and sustainable efficiency.
Analyst firm McKinsey highlights how the manufacturing sector, where physical distancing can be challenging, is tapping into the IoT: “In the recent past, there was some scepticism about applying the Internet of Things (IoT) to industry. Now, many industrial companies have embraced IoT to devise safety strategies, improve collaboration with suppliers, manage inventory, optimise procurement, and maintain equipment. This virtual shift will help digitise and scale much-needed expertise across the organisation to enable the extended and often virtual workforce to become more focused, effective, and more productive.”2
Remote Management and Reducing Costs Significantly accelerated deployment of industrial IoT is already contributing more data visualisation and insights across operations. Remotely managed virtual solutions can help companies adjust to a very different future by reducing costs, enabling physical distancing, and creating more flexible operations. Increased automation of all processes can support business resilience across pharmaceutical businesses. Automation underpins business agility, making it easier and quicker to gain business insights and respond by changing processes more quickly than was previously possible.
Pharma businesses looking to evaluate supply chain robustness and build resilience for the future have a number of urgent considerations. These include, how ready is your business to work with a reduced or variable supply chain headcount? How are your product information, labelling and work processes affected by employees working from home or reduced headcount? It might well be possible to address some issues with better labelling automation.
Are you prepared in case of another lockdown? Local lockdowns are already beginning to happen and it is important to consider how this scenario would impact staffing, manufacturing and the supply chain. Critically, can you still get product out the door as easily and profitably as before and can you easily offer new essential product lines? It is vital to identify and address all the bottlenecks. In the new reality of the Covid-19 pandemic, pharmaceutical leaders must be ready at all times to diversify product lines and update product information to meet regulatory requirements as quickly as possible.
REFERENCES
1. https://www.industryweek.com/technologyand-iiot/article/21129334/what-will-manufacturings-new-normal-be-after-covid19 2. https://www.mckinsey.com/industries/ healthcare-systems-and-services/ourinsights/beyond-coronavirus-the-path-tothe-next-normal
Gurdip Singh
Gurdip Singh is CEO of Kallik, the marketleading enterprise labelling company, and a deeply experienced practitioner and leader in life sciences industry transformation. He previously held senior life sciences industry leadership roles at CSC, then DXC Technology. He is passionate about the user experience. Over his career he has also worked extensively in the healthcare, life sciences and banking industry, giving him an insight into transferable/crossindustry best practice.
Email: gurdip.singh@kallik.com