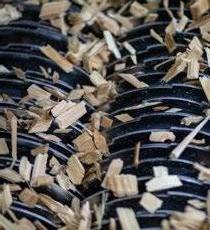
13 minute read
Resource-efficient business
We base our operations on customer requirements and focus on making optimal use of the raw material, generating efficient flows and reducing the environmental impact of Setra’s business.
Our opportunities and challenges
The principal sources of environmental impact at a sawmill are energy consumption and noise, as well as emissions into the air from internal transport vehicles such as forklifts and other machines, and from biofuel boilers. By developing our work practices and making smart investments, we can improve the efficiency of our production and reduce its environmental impact. We have also identified potential in raising the efficiency of our internal transports and increasing the share of electric vehicles in the long term.
Another benefit for Setra is that bark, woodchip and sawdust generated from the manufacturing processes can be used as biofuel in our own boilers and to benefit the local community. We have established energy partnerships in several areas, where the surplus energy from our operations is used to heat nearby premises and homes.
Governance
The environment and climate constitute an area in which Setra has the greatest influence and they are therefore clearly regulated in our sustainability policy.
Resource efficiency and energy recovery play a key role in the work to reduce our climate footprint and are therefore monitored both centrally and in each unit.
Setra’s sawmills and processing units are certified according to the ISO 14001 standard and apply systematic environmental management programmes involving precise procedures and continuous monitoring. The factory for cross-laminated timber and components will be certified according to the same standard in 2021. Our operations require an environmental permit and are subject to comprehensive environmental legislation.
How we work
Efficient production flows
Setra’s units plan their production on the basis of customer needs, so as to generate the most efficient flows possible. In this way, we can ensure that the raw material from the forest is used to manufacture the goods that are in the greatest demand and generate the highest value.
Over the past three years, we have worked intensively to introduce a process-oriented work method in all areas of our production organisation. The work method has now reached all units and departments. Every new working day/shift starts with a status update or briefing. This is used to discuss crucial factors such as safety, quality, delivery and efficiency.
It is clear that the method has generated an effect in the form of faster and clearer processing of non-compliances and improved profits. We are also seeing a tendency to be able to operate with lower stock levels which, in turn, has a positive impact on both internal transports and the volume of quality damage. When the turnover of wood products increases, the goods do not have to be moved as often. Another effect is a reduction in the risk of bluestained timber and mould developing on sawn wood that has not yet dried. Shorter lead times also mean more satisfied customers. The glulam factory in Långshyttan has made the most progress, having refined its work practices progressively over the years and repeatedly setting new internal production records.
The effects of the coronavirus pandemic
The pandemic that has dominated large parts of the world over the past year has naturally had an impact on demand for Setra’s products and caused logistical challenges. Setra’s crisis management team met every week – and sometimes several times a week – so as to respond quickly to the different situations that arose. Thanks to close cooperation between the market, supply chain, and production departments, we succeeded in continuing to manufacture without disruptions throughout the year. In the wake of an unstable spring, market conditions for wood products went sharply higher, and some products were actually in short supply during the latter half of 2020.
Operations at Setra’s sawmills and
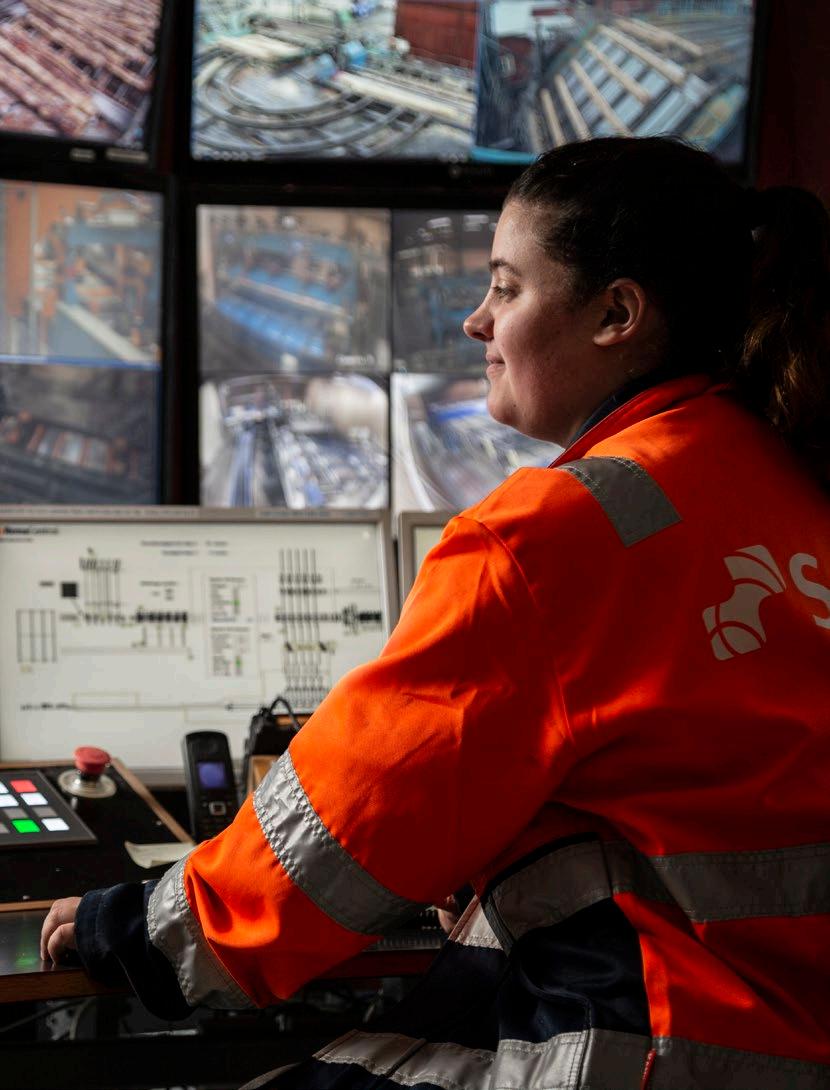

production units have been adapted to prevent the spread of infection, not only to protect our employees, but also to safeguard our delivery reliability. A ban on visits, digital or physically distanced meetings for the unit management and careful planning to prevent the mixing of employees from different shifts are some examples of new procedures that we have introduced. See page 40 for additional information about what we are doing to protect our employees.
Fewer interruptions to production
Maximising availability – i.e. the time our sawmills and processing units run without interruption – is clearly linked to efficiency. Fewer stoppages translates into increased accessibility and higher production, which means lower energy consumption per volume produced. It also means that employees need to devote less time to operational disruptions and acute maintenance – tasks that can also be associated with elevated risk.
In order to understand what causes stoppages in production, we break down non-compliances into their root causes and then work on solutions designed to prevent recurrence of the problems. The starting point is to ensure that all tasks are performed in the best way possible before we start replacing equipment. In 2020, new software for measuring downtime was introduced in all units and we are working to prepare a shared method for using it. We also focus on cutting downtime in connection with retooling and on improving maintenance efficiency by involving operators in the care of the equipment. One good example is the Skinnskatteberg sawmill, where a systematic approach having operators do some of the maintenance resulted in an increase in productivity. Downtime is reduced by separating activities that can be dealt with in advance or in parallel, and defining standardised work procedures for resetting the machines.
The whole log is used
It is important to make use of the entire log, from the perspectives of profitability and sustainability alike. We strive to achieve a high saw yield, i.e. a high volume of sawn product in relation to the volume of incoming raw timber material. The saw yield is defined by the log dimensions, sawing technique and how it is decided to saw the log into boards and planks on the basis of the financial value of the end products. In 2020, saw yield amounted to 49.2 percent, which is slightly lower than in 2019 (49.5), largely on account of working with slightly smaller logs. As a result, around half of each log becomes bioproducts such as cellulose chip and
biofuel. The quality of the bioproducts is important; they constitute a valuable raw material or fuel in customers’ processes.
The yield is naturally important for processing as well. For example, we manufacture CLT in flexible widths, which means that we can adapt the size of the solid panels to match each project. As a result, our production is highly resource-efficient and generates minimum waste.
Goals for reducing energy consumption
Several aspects of sawmill and wood processing procedures demand a great deal of energy, so we accord high priority to reducing consumption. Setra’s overarching goal was to cut electricity consumption by 20 percent and fuel consumption by 15 percent per cubic metre of sawn wood between 2010 and 2020.
Electricity consumption has been reduced by 9.6 percent since 2010. We are implementing energy-saving measures and working to increase accessibility and, consequently, productivity. This should lead to a reduction in specific emissions, since we report our electricity consumption in relation to the volume of cubic metres produced. It has not proved sufficient for us to achieve our goal, however, which was based on the general objective of the Swedish Forest Industries Federation for the sector. We can now see that more aggressive measures would have been required to make more progress in this area. Certain initiatives, including improving the efficiency of the kiln drying process, have been underway for several years, but are only now beginning to generate results. In summary, it is our view that our sawmills and production units still contain appreciable potential for improvement, and that increased accessibility in the production process is a key issue.
We have succeeded in cutting fuel consumption by 11 percent since 2010, which indicates that our initiatives to improve the efficiency of internal transports are paying dividends – but they can be developed even further.
Setra’s total energy consumption amounted to 624 GWh in 2020. Thermal energy accounted for 78 percent of this figure, electrical energy a little under 18 percent, and fuel consumption slightly more than 4 percent.
Going forward, we will be working
Energy consumption, 2020
Setra consumed a total of 624,362 MWh
481,710 MWh
Bioenergy district heating or own boiler
9,194 MWh
Internal transport (biodiesel)
111,796 MWh
Renewable electrical energy
17,263 MWh
Internal transport (diesel)
4,399 MWh
Heating oil district heating or own boiler
Electricity consumption, 2010–2020
(kWh/m3 sawn timber)*
75
70
71.1
65
63.1 62.4 63.7 64.3
60
55
50
2010 2017 2018 2019 2020 Targets 2020
56.9 kWh/m3 (-20% compared to 2010)
Setra has cut electricity consumption by 9.6 percent since 2010, but we unfortunately failed to reach our goal of lowering consumption by 20 percent. Consumption per m3 sawn timber has increased slightly over the past two years. A few units have had problems achieving the productivity as planned, partly on account of our having started up new production. Since 2018, Setra purchases electricity exclusively from renewable sources.
Diesel consumption, 2010–2020
(kWh/m3 sawn timber)*
20
15
17.6
15.1 16.0 15.7
10
5
15.7
Targets 2020
15.0 kWh/m3 (-15% compared to 2010)
0
2010 2017 2018 2019
2020
We have cut diesel consumption by 11 percent since 2010. The improvement is attributable to more efficient driving and we have identified potential for even greater efficiency. The share of biodiesel is shown in green. * Calculated for units with year-round production
towards the overarching goal of making our company climate neutral (excluding foreign transports) by 2030. Continuing to reduce energy consumption plays a key role in this work, and we will be following up on this goal by continuing to measure the consumption of electricity and diesel as a KPI. In addition to the Group-wide measures, each unit is responsible for identifying and implementing those measures that are expected to generate the greatest impact locally. For additional details of the Climate report, see page 28.
Energy survey highlights opportunities
Setra is working systematically to map our energy consumption and identify potential savings. We are subject to the Swedish Act on Energy Audits in Large Enterprises (EKL), and we have been surveying consumption at all our production units since 2016. The findings indicate those measures that are most profitable from the perspective of energy savings and are reported to the Swedish Energy Agency.
Our conclusion is that the greatest potential is to be found in improving the efficiency of the wood drying process, which accounts for 50 percent of the company’s electricity consumption and 95 percent of the thermal energy consumption.
In 2019, we prepared a report setting out methods for drying significantly more wood using the same or a lower volume of energy and maintaining the current quality. In 2020, the conclusions from this report were implemented at four units, and the work will continue in 2021. One good example comes from the sawmill in Heby, which appreciably shortened the change-over time between drying programmes and achieved significant benefits in efficiency.
Other savings could potentially be made by investing in new, energy-efficient equipment and developing new work practices and procedures. In 2020, Setra invested in a new trimming and planing line, as well as a new dryer in Hasselfors. We have fitted our sawmill
in Nyby with a new saw line, which can produce higher volumes and provide a better saw yield.
We are continuing to replace all light sources with LED lighting, while systems powered by hydraulic oil are progressively being replaced with electric systems. Other ongoing projects include fitting presence sensors to lights, checking the maintenance temperature in our premises and expanding eco-driving training.
Renewable energy and energy partnerships
More than 99 percent of Setra’s thermal energy stems from renewable fuels. Bark and sawdust from our own production is incinerated in boilers and the heat is then used in drying kilns. During the past year, we replaced an old oil boiler at our CLT plant in Långshyttan with a new bio-boiler.
In several locations, we have also set up energy partnerships with the local community. Malå, Gävle and Skinnskatteberg all use biofuel from Setra in their district heating boilers, with some of the energy generated being returned to our industrial plants.
In Nyby, we also use our own boiler to generate district heating for the nearby town of Björklinge.
Since 2018, Setra only buys ecolabelled electricity, from suppliers of hydropower, wind power and bioenergy.
Reduced emissions from internal transports
Setra’s forklifts are powered by diesel with up to 42 percent renewable additives. Our unit in Färila is an exception, as we use almost 100 percent HVO there. In Nyby and Kastet, the internal transport of timber is handled by the contractor Pålgårds, which uses 35 percent bio-additive.
During the past year, a new leasing agreement came into effect, whereby the forklifts are progressively replaced with newer models with more eco-friendly engines. Setra is closely monitoring developments in drive lines in the forklift market, and will likely switch to purely electric forklifts in the future. At our new CLT factory in Långshyttan, we are already using electrically powered forklifts indoors.
We are also checking the traffic routes at all our units. At Kastet, the old saw intake was demolished during the year to shorten the distance between the timber store and the table where the timber is loaded.
Noise
Disruptive noise is always a highpriority issue when making new investments and operational changes. Noise calculations make it possible to determine how any new operations will affect local residents, and how the unit can be designed to prevent unnecessary disruption.
97%
How much of the energy we use is renewable
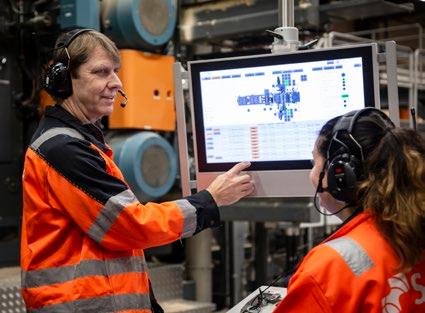
Smart choices in the component factory
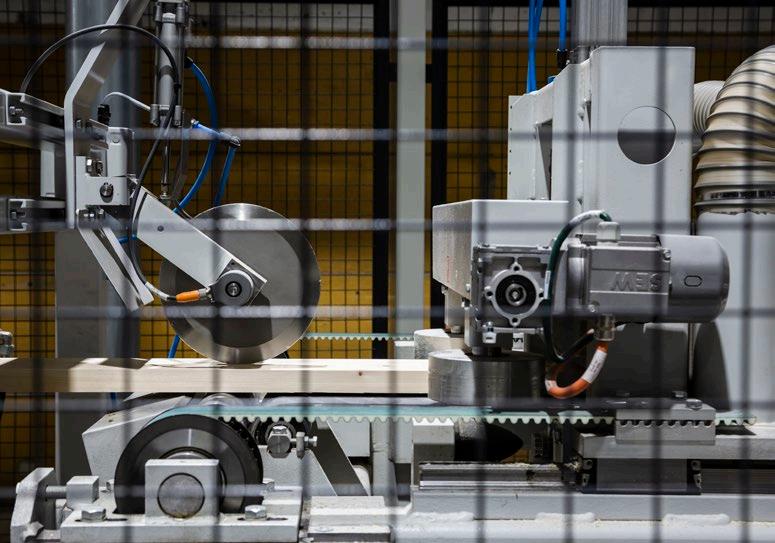
Setra’s newly opened factory for door and window components has completed an impressive journey of improvement. In just a short time, we have almost tripled the pace. We will shortly be making another new investment that should make the business even more resource-efficient.
What is the background for the improvement work?
Initially, we were a little too quick to step on the accelerator, which is an easy mistake to make when you are eager to move ahead. For example, we needed better basic knowledge about the machines and to come up with procedures for our work.
How did you go about it?
Switching from a two-shift system to daytime enabled us to consolidate the core of the group and create a really strong team that works well together. We pooled our resources and focused on reviewing our procedures together. We “put out the fires” systematically rather than trying to work on all fronts at the same time. A lot of people in Långshyttan have been involved in the process, working hard to achieve a solid result.
What’s the biggest difference in production compared to previously?
We know more about the machines today and we have procedures that hit all the right notes. This has resulted in us feeling much more confident when we start the line in the morning. Everything is finely tuned now, and we usually run without any problems all day long. We’ve increased production from 29,000 running metres in the two-shift setup to 44,000 running metres in our daytime system. The efficiency we have achieved means that we can choose the most profitable deals. What is more, the number of complaints is effectively zero – which proves we’re doing things right.
A new investment is now being planned for the factory; what does that entail?
We’ll be able to make even better use of the raw material and we’re adding another product to our range. We’ll be using some of what previously went to waste to make construction joists. It naturally feels great to be able to make long-life products from material that would otherwise be used as biofuel.
What’s your biggest take-away from your journey of improvement?
Improvement work is an ongoing process that requires you to maintain full control of what you are doing. All employees need to pull in the same direction; they have to know what needs doing and what is expected of them. Only then can you achieve the production targets and find ways to improve the efficiency of the business.
Fredrik Eriksson, Shift manager and foreman on the component line, Setra Långshyttan