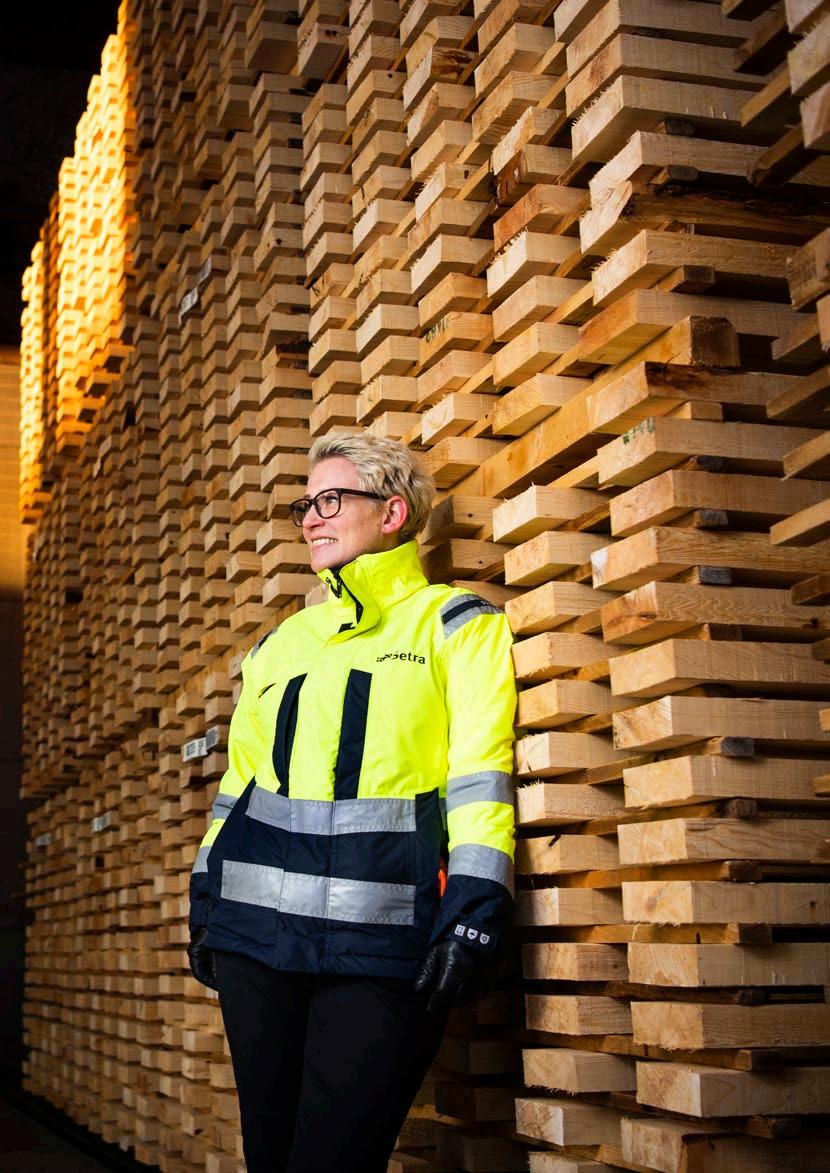
11 minute read
Managing Setra’s sustainability work
Setra’s aim is for the perspective of sustainability to be an integral part of everything we do. Our core values of commitment, innovation and responsibility are to serve as our guiding lights in making sustainable decisions and acting ethically in our everyday work.
Materiality analysis – prioritised sustainability areas
In order to identify our key sustainability areas, we have completed a materiality analysis, taking as our starting point both the impact our business generates in every link of the value chain, and the demands and expectations placed on us by the outside world. The materiality analysis is checked and updated regularly in step with the development of our business, changes in the world around us and the progression of our stakeholders’ expectations on us.
We have packaged the findings from the materiality analysis into five key issues: Our portfolio, Resource-efficient business, Culture and colleagues, Climate-smart raw material and Sustainable transport. What we consider important in each area, how we work, goals and follow-up are all set out in this sustainability report.
Stakeholder dialogue
Setra’s prioritised stakeholders are customers, employees, owners and suppliers. We maintain an ongoing dialogue with our stakeholders to identify areas for improvements, pick up on ideas for stimulating working relationships, and remain up-to-date with the latest requirements and expectations.
Over the course of 2020, climate issues have been highlighted even more clearly as being important to the stakeholders with whom we work actively. We have noted this primarily among our existing and potential customers, who are increasingly asking questions about the climate performance of our products and how we are working to reduce emissions from our business.
Another area that is gaining an increasingly prominent position in the public debate, in the media and among our owners involves issues relating to sustainable forestry and biological diversity. This is a key issue for us, and one on which we are working constantly in partnership with the industry, our owners and our suppliers.
The coronavirus pandemic has had an impact on us all in 2020. Initially, the pandemic affected demand for our products, but the market has actually remained strong during the year. We have worked hard to keep production running at our units and to establish a good working environment that minimises the risk of infection.
Sustainability policy
Setra’s sustainability policy is our overarching governing document for our work with sustainability. The policy highlights the focus areas of business ethics, employees, occupational health and safety, the climate and the environment, and is published online at setragroup.com
Organisation and responsibility
The work forms an integral part of our processes and common way of working. All managers and employees are responsible for making a contribution within the framework of their respective areas of responsibility and roles.
Setra operates a sustainability function that encompasses the environment and communication departments. The sustainability function is the responsibility of the company’s sustainability manager and is tasked with developing the work, providing expertise and supporting the business operations. The HR unit also has an important role to play in our sustainability work. Responsibility for risk management is delegated from the CEO to the SVP for Enterprise Risk. The operative work with environmental, ethical, OHAS and staff issues takes place at the respective workplaces.
A reorganisation has been planned for 2021, whereby responsibility for sustainability issues will be distributed more clearly within the organisation and at the different units. The cohesive responsibility for sustainability within the organisation is placed with the EVP for Production and Sustainability, and a new Sustainability Manager will be recruited in 2021.
Certified management systems and shared goals
Setra’s Swedish operations are certified in accordance with the ISO 14001 environmental management standard. Setra’s management system also includes health and safety and fire safety, which it is checked regularly through internal audits and insurance inspections. These elements have not been externally certified.
Setra’s sawmills and processing units are certified in accordance with FSC and PEFC Chain-of-Custody standards and the FSC standard for Controlled Wood. The certification demonstrates that the company has a system in place for tracking the raw wood material and ensuring that it originates from a responsibly managed forest.
The company has four overarching sustainability goals: one each for climate performance, energy utilisation, work safety (accidents) and sick leave. The majority of the goals applied up until 2020. Over the past year, a new sub-goal for work safety has been adopted. The number of workplace accidents resulting in sick leave per million hours worked (known as the LTA Frequency Rate) shall not exceed 10 by 2025. Setra has also decided to
strive for a healthy presence level of 95 percent.
In 2019, Setra adopted a new, overarching climate goal: to become climate neutral by 2030. In addition to this, local sustainability goals have been set for each unit.
Good result from external audit
In autumn 2020, an external audit was performed of the environmental management system for the Hasselfors, Skinnskatteberg, Långshyttan and Heby units, as well as for the Head Office in Solna. On account of the pandemic, the audits were performed in digital format.
The audit report states that Setra meets the requirements defined in the standards and contains several positive comments on our work. Neatness and tidiness, a well-functioning system for handling chemicals, and methodical work to improve energy efficiency are some of the aspects highlighted. Areas in need of improvement include updating documentation and environmental delegation when managers are replaced.
Our management systems for FSC and PEFC were also audited in the autumn. This audit revealed that the traceability requirement is well integrated into our everyday operations, and that Setra staff are knowledgeable. Some non-compliances and suggested improvements were noted in the audit, too, and these will be rectified/implemented. The certificate has been renewed.
Permit obligation under the Environmental Code
All of Setra’s production units are subject to permit requirements or reporting requirements under the Environmental Code. The principal sources of environmental impact from our production are energy utilisation and noise.
Several of Setra’s production units have historically worked with wood impregnation and/or used various wood protection agents that may have resulted in pollution of the soil. Some other processes and activities may also have contributed to pollution. In addition, there are around 15 currently identified sites where the group has carried out operations in the past. The environmental authorities have requested an investigation and, in some cases, subsequent treatment at a number of these sites. Other requirements may be made going forward, therefore Setra has established reserves to cover possible future treatment measures.
Sustainability requirements on suppliers
Setra’s Code of Conduct for Suppliers is based on the principles in the UN Global Compact and relevant international conventions. It is intended for suppliers of goods and services and for partners, both in Sweden and abroad. Setra’s largest and most important purchasing category is timber; other significant purchase areas include transport, plastic wrap, stickers and contracting services. As from 2020, Setra only purchases wood raw material from suppliers who are certified in accordance with FSC or PEFC standards. The work on the Code of Conduct for Suppliers was started in 2017. Over the past two years, we have concentrated on communicating it and having it signed by our suppliers. In order to identify the suppliers that constitute the highest risk from a sustainability viewpoint, we have analysed all parties who sell products or services to Setra for at least SEK 1 million per year. The analysis was based on country, sector, product and supplier. The risk analysis affects our way of working with certain types of suppliers. For the largest purchase categories: timber and transport, and those considered to entail certain risks, we work continuously on specifying requirements and following up; see the sections about Climate-smart raw material (page 18) and Sustainable transport (page 32).
For new suppliers, we conduct a sustainability investigation if the business or the product is considered to entail risk. In 2020, we completed a comprehensive sustainability investigation of a potential supplier.
Risk management and sustainability risks
Since 2018, Setra has implemented a company-wide process for risk management (Enterprise Risk Management, ERM). The objective is to work more efficiently to prevent and deal with risks identified in the business for the company’s stakeholders. Responsibility for risk management is ultimately placed with the company’s SVP for Enterprise Risk, who is also a member of the Group Management.
The following section presents a summary of the company’s risks related to sustainability. These are primarily operative risks within a timeframe of 1–3 years. Financial risks and market risks are dealt with in the overarching company risk process and are not reported here.

Sustainability risks ■ Potentially high risk ■ Medium risk ■ Low risk
Description of risk Risk assessment 2020 Risk management
Fire We work systematically with fire safety, but we operate in an industry with an elevated fire risk. Setra works systematically and preventatively with fire safety measures. This work includes: • Training • Installations to limit spread and damage – alarms and sprinklers, for example. • Risk inspections and action plans • Reporting risk observations and near misses with an emphasis on fire
OHAS-related health risks on account of COVID-19
Workplace accidents The pandemic has involved a work environmentrelated health risk for our employees, especially those who work in production or are unable to work remotely for other reasons.
Our business operations have a high-risk working environment where failure to comply with procedures can result in injury and material damage. Setra’s Group management and Head of Communications constitute the crisis management group. In the early stages of the pandemic, the crisis management group met digitally several times a week. Since the summer, the group has held weekly meetings. Risk analyses and action plans have been prepared at the company level, per workplace and per workstation. Information and guidelines are communicated via the intranet. The following overarching guidelines are in place to reduce the risk of infection: • Office staff work from home; advance notice must be issued of all visits to the office • Staff at the industrial facilities must comply with strict procedures for distancing and hygiene • The units only receive mission-critical visits • Only mission-critical business travel is permitted
Setra works systematically with occupational health and safety issues and applies a documented health and safety management system. Work and measures to ensure a safe working environment include: • Safety committee meetings and safety rounds • Risk analyses for the introduction of new machinery and other changes • Reporting of risks, accidents and near misses, daily management and reporting of non-compliances. • Perimeter protection such as barriers and safety guards • Training in occupational health and safety issues for all managers and employees
Bribery and corruption This risk primarily applies in the context of relations with customers and suppliers. Setra has relations all over the world, which makes this risk difficult to check and monitor. Setra takes a zero tolerance approach to bribery and corruption. The preventative work in this area includes: • Guidelines for compliance with competition legislation, as well as regarding gifts, benefits and third party hospitality. • A control function on the signing of significant contracts • Training and dilemma exercises for staff who have working relationships with customers/ suppliers. • The Code of Conduct for Suppliers includes requirements to combat corruption • Simpler whistleblower function (to be developed in 2021)
Regulation of and limitations on biofuel A major debate is underway in the EU regarding the use of wood as a raw material for energy. There is a risk that new regulations will limit the opportunity for using residual products from production as biofuel. Ongoing and active dialogue with industry organisations, owners and suppliers. Keeping track of research and development of knowledge in the sector to make the best use of the wood raw material.
Quality shortfalls in responsible forestry
Natural disasters, impacts of climate change
Breaches of environmental legislation
Unplanned emissions into the soil, air and/ or water
Soil pollution
Breaches of human rights The risk of non-compliance with legislation and requirements in forestry.
Increased risk of storms, forest fires and insect attacks that may affect the reliability of timber deliveries to our units and require us to be prepared to take care of damaged wood.
We have a systematic approach, but there is always a risk of incidents.
Setra runs operations in Sweden and the UK; our biggest suppliers are Swedish, and Sweden has strict legislation. Human rights risks are primarily to be found in the supply chain, more specifically within certain sectors. As of 2020, Setra only purchases raw material from suppliers who are FCS- or PEFC-certified. All the timber we purchase is traceable and fulfils our requirements for checked raw material. We maintain a continuous dialogue with owners and suppliers.
Examples of activities include: • Working with raw material suppliers to minimise the consequences of climate-related damage to forests. • Planning and contingency measures to deal with storm-felled, fire damaged and insect damaged wood – through increased opportunities to water timber stocks, for example. • Consideration for location, flood risk and soil conditions when setting up new operations.
Setra works systematically to improve and secure its operations, supported by our ISO 14001-certified management system. Examples of activities include: • Establishing and following up on environmental targets • Procedures/instructions • Internal and external audits • Monitoring legislation and implementing new legislation • Maintenance of plants • Dialogue with public authorities
Setra has clear policies and guidelines concerning equality and non-discrimination, equal rights, recruitment and pay. Corresponding requirements are applied to suppliers through the Setra Code of Conduct. Separate requirements on risk reporting apply in the UK. The Modern Slavery Act came into effect in 2015, requiring all companies with operations in the UK to report risks and risk management measures with regard to forced labour and trafficking in the supply chain. Examples of measures to protect human rights include: • Requirement for FSC- and PEFC-certification on purchased wood • Supplier evaluation and requirements specified for suppliers • Dialogue with employees – via employee surveys, for example