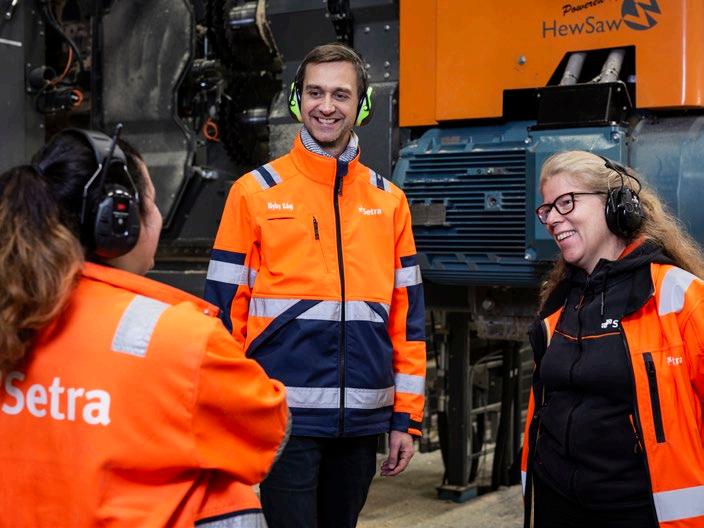
17 minute read
Culture and colleagues
We want a high performance organisation where everyone makes a contribution. Employee health and safety is our top priority.
Our opportunities and challenges
The wood industry is a future-oriented green business that is contributing to creating sustainable societies. The sustainable business model provides strong motivation for many of the people who work at Setra, and for those applying to join the company. Our vision of Grönsamhet/Green profit is founded on doing business where we, our customers, nature and society all benefit. This signals our responsibility, our commitment and our role going forward.
One of the greatest challenges entails establishing a strong and stable safety culture and bringing down the number of accidents. The wood industry is a high-risk sector from the perspective of the number of workplace accidents, and systematic, assiduous work is required to achieve results.
We are active across a large geographical area, which provides excellent opportunities to establish rewarding connections in many communities. Another effect is that we are used to meeting digitally. By working on the basis of our values, with clear leadership and a culture where everyone is involved and makes a contribution, we reinforce both well-being and commitment, which are crucial to enhancing our competitiveness at both the local and global levels.
Governance
Setra’s values and sustainability policy make clear what applies at Setra and emphasise that safety, business ethics and the working environment, including social and organisational factors, are all prioritised issues. We have a zero vision regarding workplace accidents, combined with a management system that encompasses occupational health and safety, which are examined regularly through risk analyses, safety rounds and internal audits.
Our units all comply with competition legislation, guidelines from the Swedish Anti-Corruption Institute, and international provisions regarding sanctions.
How we work
Management by objectives
In order to ensure that we are all working to achieve Setra’s overarching strategy and business plan, we apply a shared model of management by objectives. This model is based on managers and other leaders clearly communicating their expectations and setting goals in consultation with employees and work teams. The idea is to cultivate the commitment of each and every employee, and to help each individual identify his/her role in Setra’s results and development. At the same time, management by objectives assists the organisation in making full use of the skills, potential and personal drive that the employees possess.
Values-based leadership
Setra uses values-based leadership, where commitment, innovation and responsibility are key concepts. In order to develop leadership skills in line with Setra’s values, and to assure strong leadership in all areas of the company, a comprehensive initiative was launched in 2019 to work with an external partner on a new development programme for managers. The programme is mandatory for managers with subordinate employees. All managers at Setra, around 50 people, have already completed it. New managers receive continuous training, although the training programme has been put on hold during the coronavirus pandemic. The course is based on each manager being coached by his/her own manager and has consistently scored highly when assessed by the managers themselves.
The objective is for this development programme to contribute to a corporate culture where employees feel valuable, have the confidence to show initiative, know their voices are heard, and understand their own contribution to the company’s overarching goal. We also hope that the focus on leadership will have a positive influence on motivation levels, sick leave and staff turnover, which, by extension, should also have an impact on the company’s financial results.
Since 2019, all managers with HR responsibility have had access to a digital managers’ handbook to support them in their work.
Continuous improvements
We work systematically to improve the results of our operations. We are committed to enhancing safety, quality, delivery reliability and productivity. A key aspect of this work is our meeting structure, where we follow up on goals
on a daily basis, learning from any noncompliances. All production units have received training in this structure, with support from an external partner. Departments outside the area of production have also drawn inspiration from – and adopted – this way of working. The structure is based on making sure all employees are on board and making an active contribution. The daily meetings constitute a forum where the entire shift is involved in how production is running, and everyone is expected to provide input about non-compliances, as well as suggestions for improvement, on the basis of his/her professional role. The opportunity to play an active part and have an influence is a key factor in raising well-being and motivation. We have already seen several examples of how increased participation has resulted in constructive solutions.
Employeeship and dialogue
Our employees are our most important resource. It is their knowledge, drive and commitment that power Setra forwards. For this reason, employees and managers share responsibility for reinforcing and improving our working environment. One fundamental component in this work is the performance review, which focuses on the working environment, development and job satisfaction. The reviews are held once a year between each employee and their manager.
SetraRingen, the annual employee survey, is another tool we use to improve our working environment. The findings from the survey indicate changes in attitude over time and highlight the issues that require focus and attention. The 2020 survey was held at the beginning of the year and shows that the EMI (Employee Motivation Index) has risen from 71 to 72. The result is stable and in line with comparable industries. The objective is for the index to continue to rise, reaching 75 in 2025.
Setra’s focus on developing leader-
Key figures, employees
Number of employees Proportion of women
2020 779 18%
2019 767 17%
2018 861 17%
2017 849 14%
2016 855 14%
44
The average age of Setra’s employees.
Total sick leave
(percent, Setra in Sweden)
5,3 5,1
4,5 5,2 6,3
2016 2017 2018 2019 2020
Sick leave in 2020 was higher than in normal years on account of the coronavirus pandemic. Short-term absence due to illness increased by around 1.5 percentage points. Setra is working in several ways to improve employee health, and our goal is for a healthy presence figure of at least 95 percent.
Employee motivation index,
EMI (Setra in Sweden)
70 71 70 71 72
2016 2017 2018 2019 2020
The SetraRingen employee survey is held every year. EMI is an overarching measure of how motivated our employees are in their work. Setra’s result is stable and in line with comparable industries. ship and the work with the daily status updates may go some way to explaining why motivation is on the rise within the company.
Skills development and recruitment
As Setra develops as a company, our skills requirements are naturally changing and the company requires more and more technical competence. Prior to staffing the new planing mill in Hasselfors, we mapped skills to identify any training requirements. In 2021, we will be starting work on reviewing skills throughout the Setra organisation, using the new HR system, Setra People, that we introduced in 2020. The system will make it easier to follow up on personal development, certifications, permits and skills, and to compile HR statistics. Setra People also meets GDPR requirements better than our previous solution.
Around ten new jobs were created in 2020, primarily at the wood industry centre in Långshyttan and in Pyrocell, our jointly owned subsidiary based in Gävle. The recruitment situation is favourable, and we are noting that sustainable construction involving wood is an area that is attracting applications from both white and blue collar workers.
The wood industry remains a heavily male-dominated sector, and we have much to gain, especially from a purely business perspective, by improving our work with equality. Setra often recruits via staffing companies and always highlights equality as a key aspect of the assignment. This has proved to be a successful approach to attracting more applications from women. After an introductory period, Setra has the opportunity to take over the employment.
Preventative safety work
Setra has a stated zero vision: no-one is to come to harm through his/her work. For 2020, we had a sub-goal of fewer than 1.0 accidents resulting in sick leave per 100 employees – a goal we unfortunately failed to achieve. There were 26 accidents resulting in sick leave during the year, corresponding to a figure of 3.6. This is the same as in 2019 but represents a rise since 2018.
Setra uses SIA, the sawmill industry’s shared system for reporting work injuries and for processing near misses and accidents. Two years ago, we adopted the LTA (Lost Time Accident) Frequency Rate for measuring accident frequency. This measurement presents the number of accidents resulting in sick leave of more than one day per million hours worked. Our new subgoal is that the accident frequency rate shall not exceed 10 by 2025. The result for 2020 was an accident frequency rate of 21 (22.5). The goal for the year was 16, which corresponds to a maximum of 20 accidents within the business. The most common incidents are slips, crushing and cutting injuries. The accidents often happen when work is being done to deal with a disruption to operations.
For the past two years, the strategy for reducing accidents has entailed focusing on reporting near misses and risk observations. According to Heinrich’s triangle theory – also know as “the iceberg principle” – every serious accident is preceded by a large number of smaller accidents and near misses. It should therefore be possible to prevent serious accidents by learning from earlier non-compliances.
The work method involving the daily briefings ensures that the working environment and safety issues are always at the top of the agenda. A briefing is held every Monday, where Setra’s mill managers share information about the latest non-compliances and approve actions for the coming week. The number of near miss reports and risk observations has risen sharply in recent years, but as the number of serious accidents has not decreased, two new preventative tools were brought into play in 2020. One involves all managers in production writing a safety promise, in which they specify what safety means to them in their role, and how they are to work with the issue. The promise is then shared with the employees. In addition, a quick, deeper root cause analysis is performed on all accidents resulting in sick leave. Measures required to eliminate the risks are mapped on the basis of a “measure staircase” and then communicated to the organisation. We have also introduced a checklist for new or high-risk work tasks to ensure that the work is performed safely.
Two key factors in reducing accidents at Setra are to establish a behaviour where safety always takes priority, and to cut the number of stoppages in our production. We know that disruptions to operations lead to more high-risk situations than when the equipment is running as planned.
Training in working safely is a key component in the preventative work. Setra uses SSG’s safety training course, which is an established concept in Swedish industry. The course is mandatory for all new employees and is renewed every five years. Corresponding requirements are made on contractors who perform work at our units.
Perimeter protection and protective equipment
Setra has invested heavily in perimeter protection over the years. All saw lines and trim saws are fitted with barriers and safety guards that disconnect the power if anyone comes too close to the machinery. Additional protective barrier measures such as fences and gates are required to create a safer environment at our units. Over the course of 2020, we have improved the external perimeter protection at two further units, so now only Hasselfors remains, and the protective coverings there will be upgraded over the coming year.
New, more stringent requirements on work clothes and protective equipment were introduced over the past year. For example, the requirement for hi-viz clothing has been changed such that a warning vest must now be worn as a minimum in all areas.
Working environment
Being a Setra employee entails participating in occupational health and safety work and making an active contribution to the working environment. Each production unit has its own safety committee tasked with following up and taking decisions on issues relating to the working environment.
Managers, leaders and safety officers all take the common training course entitled BAM – Bättre arbetsmiljö (Better Working Environment). The objective is to lay the foundations for systematic work to improve the physical, organisational and social working environments at the respective workplaces. The training course is held every year to include all new managers, leaders and safety officers. On account of the coronavirus pandemic, it was not possible to hold the course as planned this year, so all managers and safety officers have been encouraged to complete their working environment training remotely. We hope to be able to recommence the in-person training courses in 2021.
Employee distribution 2020
76%
Proportion blue collar
93%
Proportion of employees in Sweden
24%
Proportion white collar
7%
Proportion of employees in other countries
Workplace accidents
5
4
3
2
1
2.9
2 2.5 3.6 3.6
25
20
15
10
5
0
10
2016 2017 2018 2019 2020
0
Workplace accidents with sick leave per 100 employees per year (left axis) Lost Time Accident (LTA) Frequency Rate: number of accidents resulting in sick leave of more than one day, calculated per million hours worked (right axis) Target for LTA Frequency Rate in 2025
Safety always comes first at Setra, and our vision is that no-one should come to harm at work. In 2020, we adopted a number of new measures intended to reduce the number of accidents. Our new sub-goal is that the accident frequency rate shall not exceed 10 by 2025. This KPI encompasses everyone who works at our facilities, including temporary staff and long-term contractors.

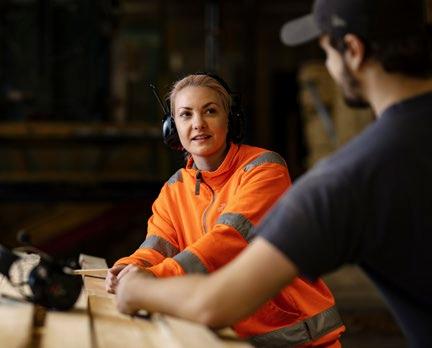
In the most recent employee survey, three percent of respondents stated that they have been subjected to some kind of discrimination. The proportion is slightly lower than the average for the industry but may indicate the existence of unrecorded cases. Setra has a system for reporting, processing and following up on discrimination, and is working tirelessly with the issue. Aspects such as workplace culture and discrimination feature in both the BAM training course and the leader development programme.
Random drug and alcohol tests have been carried out at all parts of Setra since 2019. On account of the pandemic, these tests were paused at the offices in Solna and Gävle, where almost all the staff worked from home.
Preventative measures against COVID-19
A number of measures have been adopted to prevent the spread of infection among employees. The company’s precautionary regulations during the coronavirus pandemic have been communicated centrally via the intranet and screens and through the management structure.
All travel and visits that are not directly mission-critical have been cancelled, and staff at the offices in Solna, Gävle and at at our overseas offices have worked from home. The production units have been cleaned more often than previously. Workstations, machine interfaces and forklifts have been disinfected at every staffing rotation. Hand sanitizer is always available, as are face masks that are to be used for work tasks where it is not possible to maintain a safe distance. The mill managers have worked together to share experience and solutions in a shared best practice set-up, and meetings have been held digitally or outdoors as far as possible. All in all, Setra has succeeded in continuing to operate without interruption even though some employees have become infected and sick leave, including precautionary time off and usual winter colds, has been high at times at certain units.
Employees in risk groups who need to be particularly careful have found solutions in consultation with their managers
Physical and mental health
Sick leave increased over the past year, totalling 6.3 (5.2) percent, including both long- and short-term sick leave. Short-term sick leave was approximately 1.5 percentage points higher than in a normal year, which was only to be expected given that society adopted more stringent regulations during the coronavirus pandemic, and that everyone showing symptoms of a cold had to stay at home. A couple of Setra units also experienced redundancy notices and lay-offs, which may well have affected our employees during the year.
Our objective is to achieve a healthy presence rate of at least 95 percent. We are well aware that numerous factors affect how often we are off sick, and for how long, and we are working on the issue in several ways. Examples include our focus on leadership development, performance reviews and a meeting structure where everyone has the opportunity to take part and give their opinion.
Setra has an agreement with a company that is helping us with the issue of concealed mental health issues stemming from stress or problems with drugs and alcohol. The agreement also gives all employees the chance to ask questions anonymously about mental health issues – both work-related and private. All Setra managers with subordinate employees are trained in spotting the signs of concealed mental health issues. In 2020, we introduced an updated digital training course for managers in dependency and substance abuse issues.
Business ethics
Business ethics plays a key role in value-based leadership. Setra strives to maintain high ethics in all our business relations and to demonstrate responsibility and integrity in all interactions with our customers, suppliers and partners. Setra’s business ethics guidelines encompass compliance with competition legislation, gifts and representation and our Code of Conduct for Suppliers.
A new digital training course in business ethics was introduced in 2019. The course is intended for all white collar workers, agents who work on behalf of Setra, and production staff who have contact with customers, suppliers and/ or partners. Fully 94 (40) percent of the target group had completed the course by the end of the year.
Setra also has a white paper based on actual cases from a survey of the company’s business risks. The purpose of the white paper is to provide additional guidance in business ethics dilemmas. Over the past year, the company prepared to procure an external whistleblower service, which is to be introduced in 2021 to make it possible to report irregularities within the business anonymously. Setra already operates an internal anonymous whistleblower function.
Generating a winning corporate culture

Over the past two years, the Setra glulam factory in Långshyttan has been joined by two new, strategic factories – one for wood components and one for CLT. In just a short space of time, the number of employees has almost doubled, from 60 to 110. Factory Manager Kjell Lilletjernbakken is in charge of the work to shape a rapidly developing production organisation that is to be characterised by participation and a “we” spirit.
The glulam factory enjoys a reputation as a high-performance organisation, with short decision-making paths and consistently high scores in employee surveys. What have you done to transfer this culture to two new factories?
Early in the process, we recruited key staff from the glulam factory to work at the component factory. We then did the same thing with the CLT factory. In addition, many of our new employees started off by working six months or more at the glulam factory. Our guiding principle is to create safe and secure workplaces where everyone is involved and can contribute his/her skills. Key aspects are neatness and tidiness, clear structures and roles, good communication and a good helping of responsibility and co-determination.
What was the main challenge?
Building up a new organisation in the middle of a construction site at the same time as commissioning and calibrating new machines is never easy. But generally speaking, everything ran smoothly. We have celebrated our mini-victories along the way and eaten a fair amount of cake. Maintaining an open working atmosphere is an ongoing assignment. Against a background of safe conditions, there has to be space for innovation and problem-solving in an everyday context, at the same time as we have to take care to report all non-compliances. It is when we bring mistakes out into the light that we have the chance to improve.
You’ve spent your entire professional life in the wood industry in Långshyttan, holding several management positions. How would you characterise your leadership?
Långshyttan is an old factory site, and back then the steel industry featured a clear distinction between blue and white collar workers: “us” and “them”. I grew up in a worker’s home and I’m fully familiar with “mill mentality”. A winning corporate culture looks very different today. It has to be founded on team spirit, involvement and the capacity to see the big picture and the end product of what we are doing. Setra does not make planks and boards; rather, we make components for deluxe homes in Japan, as well as walls and floors for modern apartment blocks in Scandinavia. Today, it is all about “we”.
Kjell Lilletjernbakken, Factory Manager Business Area Building Solutions & Components