



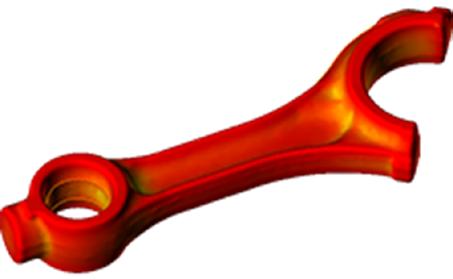
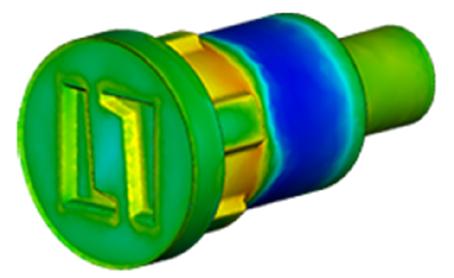
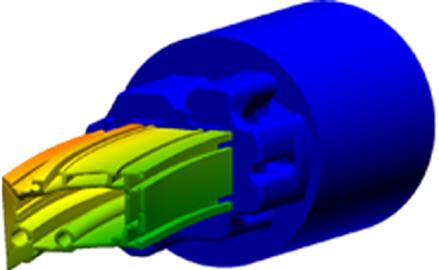
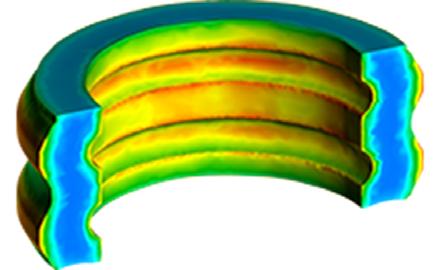
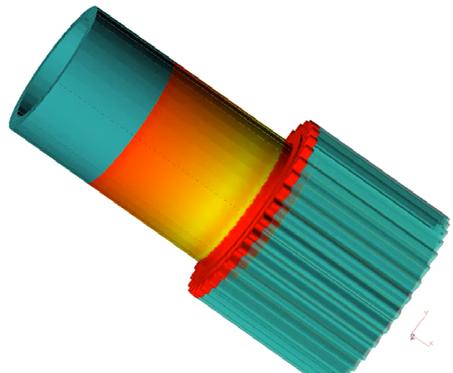


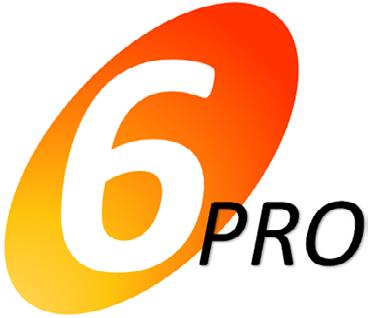
UMA CADEIA DE PRODUÇÃO RACIONAL QUE PERMITE
ECONOMIZAR AS QUANTIDADES DE MATERIAIS E REDUÇÃO DE EMISSÕES DE CO2
A solução Transvalor garante uma perfeita interoperabilidade entre todos os seus softwares com uma transferência de dados simples, rápida e segura, melhorando a precisão de seus resultados.
Comece simulando o lingotamento contínuo, continue sua análise estudando a laminação e controle a taxa de fechamento de porosidades no forjamento em matriz aberta. Simule tratamentos térmicos aplicados em suas peças e acompanhe as evoluções microestruturais em diferentes escalas macroscópica, mesoscópica e Volumes
Elementares Representativos (VER). Para garantir a qualidade das peças, efetue cálculos estruturais sob solicitações termomecânicas complexas, análise de fadiga e propagação de trincas.
Conheça Seus Durômetros para Resultados Ideais Confira na página 41
Controle de processos & Instrumentação Opções de Descarbonização para Aquecimento de Processos Industriais (Parte 1)
Arvind Thekdi
Na Capa: 33
No setor manufatureiro dos EUA, o vapor e uma grande porcentagem da eletricidade são produzidos usando combustíveis como gás natural, carvão ou outros tipos de subprodutos combustíveis.
Conversa técnica Diagnosticando a Fragilização por Hidrogênio em Peças de Aço Temperado
Debbie Aliya – Aliya Analytical Inc.
Algumas pessoas acham que podem dizer se uma peça quebrou devido à fragilização por hidrogênio olhando para ela.
Materiais / compósitos resistentes ao calor e à corrosão Molas de Compósito C/C e suas Aplicações
Hirotaka Nagao – CFC Design Inc.; Fukui, JAPAN
Compósitos C/C estão sendo usados em uma variedade de campos de tratamento térmico, enquanto espera-se que a tecnologia de molas de carbono melhore ainda mais a eficiência da produção.
41
Caracterização de materiais e testes não destrutivos
Conheça Seus Durômetros para Resultados Ideais
John Richardson – The L.S. Starrett Company; Athol, Mass. EUA Compreender os diferentes tipos e sistemas de teste de dureza pode ser útil para determinar uma solução ideal.
Fundição/Formação/Unição
Detecção de Borda Quente: o Futuro da Forja
Alaster McDonach
A detecção de borda quente (HED - Hot Edge Detection) permite a coleta de informações sobre a mudança de forma que ocorre durante o forjamento em tempo real.
SF Editora é uma marca da Aprenda Eventos Técnicos Eireli (19) 3288-0437 - ISSN 2178-0110
Rua Ipauçu, 178 - Vila Marieta, Campinas (SP) www.sfeditora.com.br
Udo Fiorini Publisher, udo@sfeditora.com.br • (19) 99205-5789
Mariana Rodrigues Redação - Diagramação, marianar205@gmail.com • (19) 3288-0437
Jéssica Carboni Vendas, jessica@grupoaprenda.com.br • (19) 3288-0437
ESCRITÓRIO CORPORATIVO NOS EUA
Manor Oak One, Suite 450, 1910 Cochran Road, Pittsburgh, PA, 15220, EUA
Fone: +1 412-531-3370 • Fax: +1 412-531-3375 • www.industrialheating.com
Erik Klingerman Group Publisher, klingermane@bnpmedia.com • +1 440-292-7580
E PRODUÇÃO NOS EUA
Reed Miller Publisher Associado/Editor - M.S. Met. Eng., reed@industrialheating.com • +1 412-306-4360
Bill Mayer Editor Associado, bill@industrialheating.com • +1 412-306-4350
Brent Miller Diretor de Arte, brent@industrialheating.com • +1 412-306-4356
REPRESENTANTE DE PUBLICIDADE NOS EUA
Kathy Pisano Diretora de Publicidade, kathy@industrialheating.com +1 412-306-4357
Fax: +1 412-531-3375
Rita M. Foumia Recursos Humanos e T.I
Michael T. Powell Criação
Lisa L. Paulus Finanças
Scott Wolters Eventos
Vincent M. Miconi Produção
Beth A. Surowiec Pesquisa de Mercado
As opiniões expressadas em artigos, colunas ou pelos entrevistados são de responsabilidade dos autores e não refletem necessariamente a opinião dos editores.
EQUIPE DE EDIÇÃO BRASILEIRA
SF Editora é uma marca da Aprenda Eventos Eireli (19) 3288-0437 - ISSN 2178-0110 www.sfeditora.com.br www.aquecimentoindustrial.com.br
Udo Fiorini - Publisher, udo@sfeditora.com.br • (19) 99205-5789
Mariana Rodrigues - Diagramação, marianar205@gmail.com • (19) 3288-0437
Jéssica Carboni- Vendas, jessica@grupoaprenda.com.br • (19) 3288-0437
Igor Cerqueira - Marketing, igor@grupoaprenda.com.br • (19) 3288-0437
ESCRITÓRIO CORPORATIVO NOS EUA
BNP Media • 2401 W. Big Beaver Road Suite 700, Troy, MI 48084 • www.bnpmedia.com
Erik Klingerman, Group Publisher klingermane@bnpmedia.com • +1 440-292-7580
Reed Miller, Editor nos EUA reed@FORGEmag.com • +1 412-306-4360
ESCRITÓRIO EM PITTSBURGH/EUA Manor Oak One, Suite 450 1910 Cochran Road, Pittsburgh, PA 15220 Tel: +1 412- 531-3370 • Fax: +1 412-531-3375
EDIÇÃO E PRODUÇÃO NOS EUA
Dean M. Peters, Editor dean@forgemag.com • +1 216-570-4537
Bill Mayer, Editor Associado bill@forgemag.com • +1 412-306-4350
Linda Becker, Editora Colaboradora beckerl@bnpmedia.com • +1 262-564-0074
Karen Talan, Gerente de Produção talank@bnpmedia.com • +1 248-244-6246
Brent Miller, Diretor de Arte millerb@bnpmedia.com • +1 412-306-4356
REPRESENTANTE DE PUBLICIDADE NOS EUA
Kathy Pisano, Advertising Director (412) 306-4357, Fax (412) 531-3375 kathy@FORGEmag.com
DIRETORES CORPORATIVOS NOS EUA
Edição: John R. Schrei
Estratégia Corporativa: Rita M. Foumia
Implantação de Conteúdo: Michelle Hucal
Criação: Michael T. Powell
Eventos: Scott Wolters
Finanças: Lisa L. Paulus
Tecnologia da Informação: Scott Krywko
Recursos Humanos: Marlene J. Witthoft
Produção: Vincent M. Miconi
Pesquisa Clear Seas: Beth A. Surowiec
As opiniões expressadas em artigos, colunas ou pelos entrevistados são de responsabilidade dos autores e não refletem necessariamente a opinião dos editores.
Editorial Brasil Lembranças Criando Futuro Neste início de 2023 tivemos a perda de dois colegas e amigos de longa data em nossa jornada no ramo de processamento térmico. Karlheinz Pohlmann e Fernando Lummertz.
Pesquisa e Desenvolvimento ELETRIFICAÇÃO & COMBUSTÃO: Qual é o futuro dos veículos Brasileiros? Importante ampliar este debate para todas as comunidades, porque a realidade da eletrificação veicular está cada vez mais próxima e a combustão cada vez mais incerta.
Simulação Computacional Estratégias de Compactação em Peças Sinterizadas A eficiência em serviço de peças fabricadas por metalurgia do pó possui influência direta das condições de processo.
Simulação Computacional Da Usina à Forjaria Como será que as características dos processos de fabricação da matéria prima em uma usina siderúrgica influenciam nas especificações finais de uma peça produzida em uma forjaria?
19 99205-5789
udo@sfeditora.com.br
Neste início de 2023 tivemos a perda de dois colegas e amigos de longa data em nossa jornada no ramo de processamento térmico. Karlheinz Pohlmann e Fernando Lummertz. O primeiro, tive como chefe direto em um dos momentos na Brasimet, quando esta empresa em que servi por 13 anos decidiu entrar no comércio internacional ao criar seu departamento de vendas internacionais. Que tive o orgulho de chefiar. Pohlmann foi presidente da Brasimet em todo o período em que lá trabalhei. Quando abri meu próprio negócio no ramo editorial, tive o imenso prazer de poder entrevistá-lo e publicar sua mini biografia na série Pioneiros que criei na revista Industrial Heating nos idos de 2011. Estamos reprisando esta página em memória de Karlheinz Pohlmann nesta edição. Segue ao lado deste editorial. O Sr. Pohlmann faleceu em 1 de março de 2023.
O amigo Fernando Lummertz conheci quando, ao procurar um nome para a revista que estava começando a criar em 2007, resolvi encontrar o dono da marca Revista Aquecimento Industrial. Que ele havia criado na década de 1970. Já no primeiro encontro o tempo parou. Ficamos horas conversando, o que se tornaria de certa forma rotina a partir de então. E, já no primeiro momento, ele me cedeu os direitos de utilização da marca Aquecimento Industrial. Registrada, esta marca só não foi utilizada no primeiro instante porque acabei fechando com uma editora americana a utilização da marca Industrial Heating. Que, como se verá no final deste editorial, também está chegando ao final de seu ciclo de vida...
Mas voltando a Fernando Lummertz, também o retratei em uma das páginas
dos Pioneiros. Veja por favor a reedição desta entrevista nas duas paginas seguintes a este editorial. Ele faleceu em 3 de fevereiro de 2023 e eu gostaria, ao reeditar “In Memoriam” estas páginas, dele e de Karlheinz Pohlmann, prestar homenagem a dois ilustres nomes dos “Pioneiros” do setor de Processamento Térmico deste país. Sem desmerecer ou esquecer os muitos outros eméritos que também foram retratados em nossas edições da Industrial Heating.
Outro assunto que temos tristeza ao informar é o desaparecimento da marca Industrial Heating Magazine. Sim, não estou errado ou mentindo ao afirmar isto. A BNP Media, editora norte americana que tem os direitos sobre as publicações FORGE, Industrial Heating, Process Heating, entre outras, decidiu descontinuar a publicação destas revistas a nível mundial. A partir de 1º de setembro próximo.
Lamentável e triste notícia, afinal no caso da IH trata-se de uma revista centenária. Recebemos a informação esta semana, mas não nos pega desprevenidos. Como comentei acima, já há anos temos registrado no INPI a marca Revista Aquecimento Industrial. E também já estamos em negociação com outro parceiro na área de publicações do setor de processamento térmico, para recebimento de material técnico e substituir o nome da IH Brasil. Em breve traremos mais notícias sobre esta novidade. Positivas!
Obs: Não deixe de ler sobre o 10º Seminário de Forjamento nesta edição. Boa leitura!
MARCO ANTONIO COLOSIO
marcocolosio@gmail.com
Diretor da Regional São Paulo da SAE BRASIL. Engenheiro Metalurgista e Doutor em Materiais pelo Instituto de Pesquisas Energéticas e Nucleares-USP, pós doutorado pela EESC-USP. Professor titular do curso de Engenharia de Materiais da Fundação Santo André e professor da pós graduação em Engenharia Automotiva do Instituto de Tecnologia Mauá. Colaborador e associado da SAE BRASIL com mais de 30 anos de experiência no setor automotivo nos campos de especificações de materiais, análise de falhas, P&D e inovações tecnológicas.
Importante ampliar este debate para todas as comunidades, porque a realidade da eletrificação veicular está cada vez mais próxima e a combustão cada vez mais incerta.
No meu ponto de vista, a questão é clara e o equacionamento é empírico. Por exemplo: quantos países parceiros globais estarão conosco na continuidade do veículo a combustão ou quantas empresas produzirão os veículos a combustão globalmente no futuro? Se conseguirmos prever estes cenários, podemos acreditar na continuidade ou não da estratégia de manter o veículo a combustão, principalmente na matriz do etanol. Olhando por outro ponto de vista, atualmente uma boa parte dos componentes para os veículos OTTO (combustão) são importados, normalmente os de maiores valores agregados e isto não deve mudar; porém, também existem empresas brasileiras que exportam componentes automotivos de alto valor agregado. Para ambos os casos anteriores, a continuidade da produção de componentes locais ou estrangeira precisa atingir uma quantidade ou volume mínimo de peças para viabilizar economicamente o “business” e manter-se firme no negócio e assim, tornar o veículo a combustão longínquo. Mas, qual é este mínimo?
Se estamos tratando de alinhamento estratégicos na eventual continuidade de veículos a combustão, nos parece que a questão está mais voltada na política internacional e menos na local, isto é, quantos países estarão se juntando conosco neste cenário. Veja a criticidade desta situação: o mundo já se aproximou dos 100 milhões de veículos a
combustão produzidos em 2017 e nosso país atualmente orbita em torno dos 2 milhões. Se juntarmos países que poderiam pensar no etanol em sua matriz veicular, como exemplos: Índia, Indonésia e Tailândia e eventualmente alguns outros, o volume de produção na melhor das situações não passaria dos 10 milhões. Certamente, nesta conta, ainda será fortemente subtraído os eletrificados que entrarão em boa parte da demanda futura global. Será que nosso país e alguns poucos outros estarão dispostos a apostar fortemente no etanol? Esta será a grande questão.
Enquanto os eletrificados avançam rapidamente, continuaremos a assistir personalidades discutindo o futuro por aqui e também associá-lo a um problema da falta de política pública, porém acredito ser mais importante focar na política e diplomacia internacional.
O debate da produção global de componentes para veículos a combustão e sua influência futura no mercado brasileiro no emprego do etanol e ainda, por certo tempo os combustíveis de origens fósseis, devem ganhar força nestes próximos anos, porém a continuidade da matriz energética focando no etanol é de nosso maior interesse pelo caráter verde e tecnologia “abrasileirada” e neste momento, assistiremos, muito em breve, o aumento de incentivos em P&D&I para melhoria da eficiência energética dos mesmos, para que na ótica ambiental, os de combustão desperte ainda interesses e possam voltar ao páreo e contrapor com os eletrificados. Estejam preparados!
Inevitavelmente, as movimentações globais já estão acontecendo, e baseado em fatos recentes percebidos no setor automo -
tivo que estão ocorrendo silenciosamente e escondidos da ótica da nossa comunidade que discute a “propulsão veicular”; situações estas os quais poderão impactar os veículos brasileiros a combustão ou nosso business local. Relato que se nota uma situação fora da média temporal, onde fornecedores e sistemistas têm declinados da produção e fornecimento de componentes para o nosso mercado; claro que estes fatos podem ser coincidências ou meramente uma pontinha de um grande iceberg; porém, os mesmos podem se intensificar e começar a desenhar uma tendência para os próximos anos. Este é um importante ponto que faz sentido nesta discussão, ou seja, grandes empresas sistemistas globais também devem alinhar suas estratégias conforme as tendências e precisam tomar decisões focando o mercado futuro dos componentes automotivos, ou seja: veículos a combustão ou veículos eletrificados. Estas decisões referenciam o tipo e a escala de produção, rotas de manufaturas e/ou otimização de linhas globais para linhas únicas e específicas em países de interesses e por fim, se concentrar em apenas linhas específicas de produto. Sejam quaisquer os motivos, raramente serão expostos ao público; mas se
fossem, poderiam ser uma grande ferramenta de orientação das nossas discussões e estratégias.
Somando estas opiniões e diante de uma ótica de uma eventual situação futura desfavorável de longo prazo, nos parece que os veículos a combustão possivelmente serão mais caros que os veículos eletrificados, seja pela redução de custo que deve acontecer continuamente nos eletrificados e somadas a um provável aumento de custo “forçado” dos componentes utilizados nos de combustão diante da redução na demanda global e local. Neste cenário, ainda terá a influência do aspecto ambiental, o qual deve acrescentar uma parcela, principalmente na política pública local na decisão de curto-médio prazo, focando em subsídios, incentivos e legislações ambientais.
Finalizado, fica claro que o cenário futuro é uma “equação empírica” e a previsibilidade dos números indicarão quem fica e quem sai. Em todo caso, a política e diplomacia internacional precisam estar presentes nisso e trabalhar ao nosso favor, caso realmente desejarmos a longevidade ao veicular a etanol e certamente, mantendo o veículo de combustão por mais tempo.
Muito obrigado e até a próxima edição da IH.
alisson@sixpro.pro
eficiência em serviço de peças fabricadas por metalurgia do pó possui influência direta das condições de processo. Isso acontece porque é possível que regiões críticas da peça durante a sua aplicação, ou seja, regiões que sofrem tensões elevadas, podem ter uma resistência mecânica reduzida. Para exemplificar, observa-se na Fig. 1 a falha de uma peça fabricada por metalurgia do pó na fase de desenvolvimento do produto.
de Materiais da UFMG. Possui Pós-Doutorado em Metalurgia da Transformação
Durante a etapa de compactação do pó metálico é possível que algumas regiões da peça não atinjam uma densidade apropriada. Essa possibilidade se torna crítica, uma vez que características do material como a resistência mecânica, a resistência ao impacto ou a vida em fadiga são influenciadas pela densidade do material da peça. Logo, caso regiões de reduzida densidade coincidam com regiões que sofrem esforços ou tensões relativamente elevadas em serviço, a falha é uma consequência.
EDUARDO NUNES
edunu@alumni.usp.br
Eduardo Nunes, Engenheiro de materiais na General Motors. Doutor em Engenharia de Materiais pela Escola Politecnica, USP. BEng em Engenharia Metalúrgica, forte conhecimento em investigação de falhas. Design para Six Sigma, Master Black Belt. Especialista em encontrar a melhor rota de fabricação de peças metálicas considerando critérios técnicos e comerciais.
Foi realizada uma simulação da compactação relativa à peça abordada na Fig. 1 via QForm
UK., a qual está mostrada na Fig. 2. Observou-se que, da maneira que a peça foi compactada, haveria uma região de baixa densidade (em azul), a qual coincide com a região de maior esforço em serviço e, portanto, contribuiria para a quebra por fadiga exatamente naquela região.
Nesse caso, testou-se de uma estratégia de compactação na qual foi feita uma alteração de produto que priorizaria o ganho de densidade na região crítica, sem investimentos adicionais, ou seja, somente modificando o design do topo do punção. Observa-se então, na Fig. 3, que esta estratégia foi implementada no produto em estudo, o que aumentou em 10x a sua vida em fadiga, devido a aumento de densidade na região crítica em termos de tensão.
Portanto, a estratégia de compactação pode e dever ser investigada, preferencialmente utilizando simulação. Assim, diferentes possibilidades podem ser testadas e otimizadas com foco na maximização da resistência mecânica final da peça.
Como será que as características dos processos de fabricação da matéria prima em uma usina siderúrgica influenciam nas especificações finais de uma peça produzida em uma forjaria? Com o advento do uso de simuladores por elementos finitos por parte das usinas que produzem barras para forjamento, recentes trabalhos integrados com as forjarias já começam a ajudar a responder a essa questão.
Barras e arames para o forjamento a frio, por exemplo, utilizados na fabricação de diversas peças para o setor automotivo, ou para fixadores em geral, ou para várias outras aplicações, comumente passam por etapas de processos térmicos e de conformação, como a laminação e a trefilação. Portanto, será que os processos de laminação a quente influenciam nas propriedades mecânicas lá no final da cadeia de produção, considerando a indústria como um todo? E os processos de trefilação? E os tratamentos térmicos intermediários? Mas acima de tudo, como eles influenciam e qual a relevância deles na qualidade final?
Se considerarmos uma barra trefilada, é possível verificar que a sua dureza não é pontual. A partir da simulação da trefilação de
um Fio Máquina (barra laminada a quente ou a frio), cortou-se um tarugo para ser recalcado (ou ensaiado por compressão), como pode ser visto na Fig. 1 (a). Logo, observa-se que o encruamento ao longo do diâmetro não é uniforme, uma vez que a deformação plástica na região próxima à superfície é maior do que na região central. Sendo assim, como fica a curva de escoamento para o tarugo a ser forjado? A curva de escoamento definida para o
“Barras e arames para o forjamento a frio, por exemplo, utilizados na fabricação de diversas peças para o setor automotivo, ou para fixadores em geral, ou para várias outras aplicações, comumente passam por etapas de processos térmicos e de conformação, como a laminação e a trefilação.”Figura 1. (a) Barra trefilada cortada e (b) ensaiada por compressão via simulação no QForm UK.
Fio Máquina pode ser considerada na previsão do processo de forjamento? E quanto à previsão da dureza final do forjado, ela deve considerar a distribuição de dureza do trefilado?
Ao menos para a distribuição final da deformação plástica encontrada na Fig. 1 (b), é possível determinar diferenças em relação a um caso para o qual se considera uma deformação plástica uniforme no tarugo inicial. Logo, há de se investigar se o mesmo acontece para o forjamento de uma peça comercial.
Não menos importantes, muitas outras questões também podem ser esclarecidas para produtos forjados a quente. Por exemplo, a peça mostrada na Fig. 2 sofre aquecimento parcial antes de ser prensada. Assim, como a laminação a quente prévia pode influenciar em eventuais defeitos formados no forjamento, ou até mesmo nas propriedades mecânicas das regiões não aquecidas? Isso tudo sem considerar operações posteriores ao forjamento,
A revista Industrial Heating é disponibilizada gratuitamente na área de PUBLICAÇÕES no site Portal Aquecimento Industrial, junto dos Artigos e Colunas mais relevantes sobre a indústria no Brasil e no mundo.
OGrupo Aprenda realizou em 20 e 21 de junho o 10º Seminário de Forjamento, que comemorou assim 10 anos ininterruptos de sua realização. O evento fez parte do II Congresso de Conformação Metálica, e foi realizado nas dependências da FSA, Fundação Santo André localizado na cidade com o mesmo nome.
Além do 10º Seminário de Forjamento, o II Congresso de Conformação Metálica, também sediou os eventos: 5º Seminário Tecnologia de Estampagem, sob a coordenação técnica de João Henrique Correa de Souza; o 2º Seminário de Soldagem com a coordenação técnica de José Castillo Lara e o 2º Encontro Especialistas de Elementos de Fixação (Fastening) sob a coordenação técnica de Roberto Garcia.
O Seminário Forjamento foi criado em 2013 ano em
que foi realizado no Hotel Plaza Vinhedo, localizado em Vinhedo, interior de São Paulo. E foi realizado nestes 10 anos em diferentes localidades e instalações, como fábricas, caso da Eaton Valinhos e Prensas Schuler; instituições de ensino como FEI e agora na FSA; instituições de pesquisa, caso do IPT; e também on-line durante os anos de pandemia.
Como já vem acontecendo há alguns anos, o evento teve a coordenação técnica do Prof. Dr. Mauro Moraes de Souza do Centro Universitário FEI. Mauro Moraes, como um dos Key Speakers do Congresso, apresentou na abertura do evento a palestra: Alinhamento de Expectativas para o Congresso, Reflexões Sobre o Setor Produtivo e os Caminhos para Sustentabilidade na Conformação Metálica.
Após a sequencia de palestras da abertura, já na sala específica do Seminário do Forjamento, foram apresentadas nos dois dias do evento as seguintes palestras:
Alisson Duarte, 6Pro Virtual And Practical Process - Como o QForm UK Contribui para a Eficiência da Indústria do Forjamento
Tiago Chalinski, Viemar Indústria AutomotivaForjamento a Frio em Aços Tratados Térmicamente
Jose Santaella Redorat Jr., Santec Tecnologia em Soldagem - Aumento de Vida de Matrizes com Soldagem
Ana Paola Villalva Braga, IPT - R$ 15 Milhões para Pesquisa em Matrizes de Forjamento – Conheça o Novo Edital da Linha IV do Rota 2030
Leandro Pasti, Rodolfo Fonseca, Inductotherm Group Brasil - Flexibilidade em Sistemas de Aquecimento por Indução para Conformação de Metais
Guilherme Goulart, MAXIFORJA - Estratégias para Parametrização de Processo de Forjamento Completo em Simulação Numérica - Caso Prático
Oswaldo Ravanini, Transvalor Americas - O Uso da Otimização Automática na Simulação de Conformação com o FORGE NxT 4.0
André Rosiak, UFRGS - Conformação 4.0: A Revolução da Indústria Metalmecânica Através da Inteligência Artificial
Felipe Oliveira, Huender Trajano, Metalúrgica Onix - Aumento da Vida Útil de Matrizes de Forjamento a Quente com o Auxílio do QForm UK
Mário Teixeira Neto, EATON Valinhos
- Manutenção Centrada em Confiabilidade (RCM) em Forjaria
Jaderson Melo, EATON ValinhosTecnologias Disruptivas em Ambiente de Forjaria
Alliston Oliveira Souza, Matheus
Alencar Benevides – CIE Forjas
Minas - A Importância da Análise de Elementos Finitos como Ferramenta no Desenvolvimento de Novos Produtos
Durante a realização do seminário, a Diretora Geral e filha do Presidente
Fundador da VIEMAR Indústria
Automotiva, Juliana Toniolo Vieira
Salis entregou ao palestrante Tiago
Nunes Chalinski, Coordenador da Engenharia de Corte e Conformação da empresa, uma placa de homenagem por representar a empresa no evento.
A empresa Metaltork, uma das patrocinadoras Ouro do Congresso e participante com palestras Key Speaker e no Seminário Fastening, ofereceu a inscritos no evento a possibilidade de visita técnica às suas instalações. A visita foi realizada no dia 22 de junho, portanto no dia posterior ao final do Congresso. A Metaltork, fabricante de elementos de fixação, possibilitou visita aos seus departamentos de conformação, tratamento térmico, usinagem, entre outros setores.
Finalizando o Congresso, Mauro Moraes apresentou a palestra Reflexões Finais sobre o 2º Congresso de Conformação Metálica - Aprendizados, Highlights, Contribuições para o Ambiente Brasileiro de Conformação.
O próximo Congresso de Conformação Metálica, que passa a se chamar 3º CCM – Congresso de Conformação Metálica, está previsto para acontecer em 18 e 19 de Junho de 2024 em local a ser divulgado nos próximos meses.
e
No setor manufatureiro dos EUA, o vapor e uma grande porcentagem da eletricidade são produzidos usando combustíveis como gás natural, carvão ou outros tipos de subprodutos combustíveis. Em última análise, a principal fonte de calor para o aquecimento do processo são os combustíveis com uma quantidade variável de teor de carbono, com exceção de uma pequena porcentagem de eletricidade gerada pelo uso de fontes renováveis e usinas nucleares. O carbono dessas fontes de combustível acaba na atmosfera como dióxido de carbono (CO2), que é reconhecido como um dos principais gases de efeito estufa (GEE).
Conforme relatado na literatura e na mídia, um esforço conjunto está sendo feito para reduzir as
emissões de carbono (CO2, CH4, hidrocarbonetos, etc.) para limitar o aumento da temperatura global em 2°C acima dos níveis pré-industriais. No entanto, a eliminação ou grande redução das emissões de CO2 é uma tarefa muito desafiadora para as operações de manufatura estabelecidas devido aos seus efeitos nos parâmetros econômicos e financeiros. Muitas corporações estão assumindo cada vez mais compromissos para reduzir as emissões de carbono como passos progressivos em direção à sustentabilidade corporativa e conformidade com quaisquer regulamentos que possam estar por vir. Considerando a escala de fabricação nos Estados Unidos, alcançar emissões líquidas zero de gases do efeito estufa enquanto mantém a competitividade é um grande desafio.
Metais fabricados
Alumina e Alumínio
Vidro e produtos de vidro Cimento
Alimentos e bebidas
Ferro e aço
Produtos Florestais
Produtos químicos
Refinamento de petróleo
Uso de Energia de Aquecimento de Processo (TBtu / Ano)
Por tipo de energia utilizada - dados MECS 2018
Este artigo – parte 1 de uma série que será apresentada nas próximas edições – descreve os diferentes tipos de sistemas de aquecimento de processo usados pelas indústrias, as emissões de CO2 desses sistemas e possíveis caminhos para atingir emissões líquidas de carbono zero com a citação de alguns exemplos.
Em 2018, os processos térmicos, incluindo combustíveis, geração de vapor on-site e sistemas de cogeração que fornecem vapor e eletricidade representaram 67% do uso total de energia de manufatura nos EUA. O calor usado para todos os processos térmicos é fornecido por combustível e vapor ou eletricidade. Na maioria dos processos de aquecimento individuais, no entanto, é fornecido por uma única fonte. Em apenas alguns casos, o sistema de aquecimento pode usar duas ou mais fontes de calor ao mesmo tempo.
É útil entender os padrões de uso de energia e
os detalhes do sistema de aquecimento do processo antes de discutir as opções de descarbonização. O uso total de energia para o aquecimento do processo varia consideravelmente de indústria para indústria. Cinco indústrias respondem por mais de 80% de todo o consumo de energia da manufatura dos EUA: refino de petróleo, produtos químicos, produtos florestais, incluindo papel e celulose, ferro e aço, e alimentos e bebidas. Cerca de 36% da energia de aquecimento do processo fornecida aos fornos, estufas e outros equipamentos de processamento térmico é perdida como calor residual. Parte dessas perdas pode ser recuperada e pode resultar em economia de energia e redução de emissões de GEE.
Uma revisão dos tipos de energia usados na manufatura (Fig. 1) mostra que os combustíveis fornecem 64%, o vapor fornece 29% e a eletricidade fornece 7% da energia total usada para aquecimento de processos e processos eletroquímicos. O vapor é usado principalmente em produtos florestais, produtos químicos e refino de petróleo, enquanto a eletricidade é usada principalmente para metais (ferro e aço). Observe
Tabela 1. Tipos de processos térmicos usados para oito indústrias consumidoras de energia. As cores indicam as faixas de temperatura. Azul = baixa temperatura (<430°C); amarelo = temperatura média (430-760°C); vermelho = alta temperatura (>760°C).
Processos térmicos
Calcinação
União, Cura e Conformação
Secagem
Aquecimento de Fluídos
Tratamento Térmico (Metais e Ametais)
Reaquecimento de Metais e Não Metais
Fusão de Metais e Não Metais
Outros Processos de Aquecimento
Processos Térmicos Reativos
Fusão, Aglomeração
Geração de Vapor
que cada BTU de vapor requer um uso de combustível 20-40% maior em equipamentos de geração de vapor (caldeiras) e um uso de combustível 30-50% maior para geração de eletricidade, seja no local ou fora do local, exceto por uma pequena fração da eletricidade comprada gerada de fontes renováveis. Isso indica que a combustão de combustível é o principal método de fornecimento de calor e é a principal fonte de geração de CO2 do equipamento de aquecimento de processo.
As emissões de CO2 são geralmente relatadas como gases GEE equivalentes a CO2 (CO2e). Para sistemas de aquecimento de processo, eles são principalmente provenientes da combustão de combustíveis carbonosos usados direta ou indiretamente pelas indústrias de manufatura. Além do aquecimento do processo, o resfriamento do processo e outros processos podem usar vapor e eletricidade gerados pelo uso de combustíveis e contribuir para as emissões de CO2.
A energia térmica, seja gerada pela combustão de combustível ou vapor ou eletricidade, é usada para uma variedade de processos em cada indústria. Por exemplo, a indústria siderúrgica usa combustível e outros tipos de energia para aquecimento de minério de ferro, fabricação de ferro em altos-fornos, fabricação de aço em BOFs e
EAFs, reaquecimento de placas ou lingotes, recozimento ou endurecimento de chapas ou fios laminados, conformação e forjamento de peças de aço, tratamento térmico de peças acabadas, etc
As emissões de CO2 são geralmente relatadas como gases GEE equivalentes a CO2 (CO2e). Para sistemas de aquecimento de processo, eles são principalmente provenientes da combustão de combustíveis carbonosos usados direta ou indiretamente pelas indústrias de manufatura. Além do aquecimento do processo, o resfriamento do processo e outros processos podem usar vapor e eletricidade gerados pelo uso de combustíveis e contribuir para as emissões de CO2.
A energia térmica, seja gerada pela combustão de combustível ou vapor ou eletricidade, é usada para uma variedade de processos em cada indústria. Por exemplo, a indústria siderúrgica usa combustível e outros tipos de energia para aquecimento de minério de ferro, produção de ferro em altos-fornos, produção de aço em BOFs e EAFs, reaquecimento de placas ou lingotes, recozimento ou endurecimento de chapas ou fios laminados, conformação e forjamento de peças de aço, tratamento térmico de peças acabadas, etc
Muitos desses processos têm características comuns
e podem ser divididos em algumas categorias amplas. Essas categorias de processo, listadas em ordem alfabética com faixa de temperatura e as indústrias onde são usadas, são mostradas na Tabela 1. Essa categorização ajuda a entender os requisitos importantes do processo e as abordagens que podem ser adotadas para reduzir as emissões de GEE.
Aqui está uma descrição muito breve e generalizada de cada um dos processos térmicos listados na Tabela 1.
Este é um processo de aquecimento para materiais como carbonato de cálcio (calcário) ou certos processos de reforma onde o material de alimentação se decompõe quando aquecido, liberando CO2 ou outros gases devido à decomposição química do material de base.
Tabela
Processos Térmicos
Calcinação Produção de Cal
Esses processos de aquecimento usam principalmente queimadores de queima direta para fornecer o calor, e os produtos da combustão são misturados com CO2 ou outros gases antes de serem descarregados na atmosfera. Em um caso específico da indústria de cimento, uma série de etapas de recuperação de calor (incluindo a secagem da “farinha” crua carregada no forno usado para produção de clínquer) são usadas antes que os gases sejam descarregados, muitas vezes com teor de umidade muito alto. Um sistema semelhante é usado para a produção de cal.
O calor é fornecido para unir, endurecer ou curar materiais (como tintas ou revestimentos, plásticos e borracha) quando eles são aquecidos dentro de uma
Processos Usados na Produção de Fero e Aço
União, Cura e Conformação Secagem e Cura de Tintas e outros Revestimentos
Secagem Secagem de Minério de Ferro, Panela/Distribuidor, Sucata
Aquecimento de Fluídos
Aquecer Alto Forno, Limpeza de Metais, Tanques
Tratamento Térmico (Metais e Ametais) Têmpera de Aço, Fornos Câmara e Contínuos de Recozimento
Reaquecimento de Metais e Não Metais Reaquecimento de Aço para Laminação, Forja, Trabalhos a Quente de Peças Acabadas
Fusão de Metais e Não Metais Fornos Elétricos a Arco (EAF)
Outros Processos de Aquecimento Aquecimento de Panelas e Distribuidores, Aquecimento de Moldes, Oxidadores Térmicos, HVAC
Processos Térmicos Reativos Sinterização de Minério de Ferro, Fundição, Altos-Fornos, Fornos de coque, Produção de Ferro por Redução Direta (DRI). Panelas de Refino, Geradores de Atmosfera
Geração de Vapor
Caldeiras a Vapor, Caldeiras de Recuperação de Calor Residual, Caldeiras de Água Quente
determinada faixa de temperatura. O processo é realizado a uma temperatura relativamente baixa na faixa de 150-300°C. O processo pode liberar vapores de materiais orgânicos ou inorgânicos, que podem precisar de tratamento adicional para atender aos requisitos de regulamentação de emissões existentes. Esses sistemas geralmente usam aquecimento por convecção forçada, onde queimadores de queima direta fornecem o calor do processo e os produtos da combustão são misturados com um grande volume de gases recirculantes. Uma grande quantidade de ar de diluição ou gases inertes é usada para evitar a formação de mistura de gás inflamável dentro do sistema de aquecimento. Os gases de escape contêm alto teor de oxigênio, variando de 14 a 18%, com possibilidade de vapores orgânicos que precisam ser tratados. Eles são incinerados em oxidadores térmicos ou outros sistemas antes de serem descarregados na atmosfera
Secagem
Este é um processo onde a água ou outro líquido do material úmido é evaporado pelo aumento da temperatura do material. Também inclui processos de separação onde líquidos de diferentes pontos de ebulição são separados por destilação seletiva. Exemplos incluem secagem de grãos, papel, minérios metálicos e têxteis, e destilação de materiais orgânicos, petróleo bruto e produtos químicos. Uma variedade de equipamentos é usada para secar os materiais. Os secadores usam gases recirculados, como ar ou uma mistura de ar e produtos de combustão, para fornecer calor ao material. O ar recirculado é aquecido misturando-se diretamente com os produtos de combustão de queimadores a combustível (geralmente gás natural) ou em um trocador de calor onde vapor ou produtos quentes de combustão são usados como fonte de calor ou fornecendo calor de elementos de aquecimento elétrico. Os gases de exaustão do secador contêm produtos de combustão e parte do ar recirculado para manter a umidade necessária ou o nível de pressão de vapor no secador. Além dos sistemas movidos a combustível, alguns sistemas de secagem especializados usam tecnologias eletroeletrônicas, como secagem ultrassônica, radiofrequência (RF) ou secagem por micro-ondas. Nos sistemas de separação térmica,
os vapores de uma mistura de líquidos são separados seletivamente (destilação fracionada) usando vapor ou calor de outras fontes. Um processo de secagem é usado em todas as indústrias de uma forma ou de outra.
O aquecimento de um fluido (líquido e gás) para aumentar sua temperatura sem mudança de fase ou quebra do material de base é um dos requisitos mais comuns em muitas indústrias. Gases como o ar são aquecidos por mistura direta com produtos de combustão ou em um trocador de calor, onde gás quente ou vapor são usados como fonte de calor. Outros tipos de líquidos são aquecidos em um aquecedor acionado ou em uma caldeira de líquido, onde o calor é fornecido por queimadores acionados. Em alguns casos, vapor ou eletricidade são usados para aquecer líquidos especializados. O aquecimento de fluidos é realizado em uma ampla faixa de temperatura de menos de 100°C a até 400°C em equipamentos como aquecedores de ar, aquecedores de óleo cru e caldeiras de água quente. Os gases de exaustão desses sistemas de aquecimento incluem produtos de combustão limpos e raramente precisam de qualquer tipo de tratamento de gases de combustão.
Tratamento Térmico de Metais, Ametais Este processo aquece um material ferroso ou não ferroso a uma temperatura em que sua estrutura ou composição de grão muda, resultando em mudanças em suas propriedades físicas. Exemplos incluem cementação (endurecimento) ou recozimento (amolecimento) de peças de aço e recozimento e têmpera de vidro. Os fornos de tratamento térmico de metais podem ser aquecidos diretamente (revenimento do aço) ou aquecidos indiretamente usando tubos radiantes ou muflas. Os processos mais utilizados requerem uma atmosfera protetora, que é gerada em um gerador de atmosfera usando gás natural ou amônia como material de base. O tratamento térmico a vácuo de metais usa eletricidade para fornecer o calor. O tratamento térmico de não-metal inclui recozimento e têmpera do vidro, onde o vidro é aquecido a uma certa temperatura e resfriado a uma taxa de resfriamento controlada para
atingir as propriedades físicas desejadas. Esses fornos são aquecidos diretamente com combustível ou usam eletricidade para fornecer o calor.
Este processo aquece um material (metal ou não-metal) para aumentar sua temperatura sem que ele derreta, quebre ou altere suas propriedades metalúrgicas. Exemplos incluem o reaquecimento de lingotes, tarugos ou placas de aço ou alumínio. Os equipamentos usados para reaquecimento de metais variam de pequenos fornos de forjamento a fornos de reaquecimento de aço muito grandes. Os fornos de aquecimento de metal usam queimadores de queima direta e os gases de exaustão são descarregados diretamente na atmosfera. O aquecimento de não metais é usado em muitas indústrias para processos como aquecimento de vidro para vidraria decorativa, cerâmica e tijolos. Esses fornos também usam queimadores de queima direta ou calor elétrico. Na maioria dos casos, eles não requerem tratamento de gases de combustão antes de serem descarregados na atmosfera.
Este processo aquece um material ou uma mistura de materiais a uma temperatura alta o suficiente para derretê-los e produzir material fundido que é moldado no produto final. Exemplos incluem fusão para produzir vidro, produção de ferro em altos-fornos, fusão de sucata em fornos de arco elétrico (EAFs Electric Arc Furnaces) ou simplesmente fusão de lingotes de metal/não-metal ou outras formas para produzir fundidos ou outros produtos. Cada um desses processos usa um método diferente para fornecer calor. Fornos de fusão de vidro usam queimadores de queima direta e eletricidade em alguns casos. A produção de ferro requer o uso de coque para redução do minério de ferro em um alto-forno e para fornecer o calor necessário. A fusão de ferro ou aço pode ser realizada em um forno de indução ou em um EAF, que usa eletricidade e alguns combustíveis fósseis. A fusão de não-metais usa uma variedade de métodos de aquecimento usando combustíveis fósseis e eletricidade. A temperatura e a natureza dos gases de exaustão descarregados de cada um desses processos
variam consideravelmente e precisam de algum tipo de tratamento de gases de combustão antes que os gases sejam descarregados na atmosfera.
Outros
Isso inclui processos de aquecimento não incluídos na lista da Tabela 1. Alguns exemplos que podem se enquadrar nessa categoria incluem aquecimento de refratários, aquecimento de panela e distribuidor e soldagem de materiais. A maioria deles usa queimadores a combustível (gás natural) e descarrega os gases de exaustão diretamente na atmosfera.
Este processo aquece materiais, geralmente uma mistura de mais de um material, para promover uma reação química com ou sem a presença de um catalisador ou outro método de afetar (acelerar) uma reação química. Esses processos são utilizados em indústrias como química, refino de petróleo, siderurgia e alumínio e produtos florestais. O método de aquecimento para este tipo de processo depende das características do processo, capacidade de produção e tipo de materiais produzidos. Por exemplo, reformadores de gás natural usam aquecimento indireto de queimadores a combustível, enquanto processos de redução de minério de metal usam suprimento de ar ou oxigênio e materiais carbonáceos para produzir calor dentro do reator. Os gases de exaustão desses sistemas podem ser produtos de combustão limpa para sistemas de aquecimento indireto ou uma mistura de gases combustíveis e não combustíveis junto com partículas que podem ser usadas como combustível em outros processos e, em última análise, precisam ser tratadas antes de serem lançadas na atmosfera.
Este processo aquece a água em alta pressão para produzir vapor em uma caldeira. O termo caldeira é usado como um sistema de aquecimento genérico utilizado para aquecer ou vaporizar uma variedade de líquidos. O vapor é necessário em quase todas as indústrias e usado como fonte de calor para produção
de energia mecânica ou elétrica ou como matéria-prima em muitos processos químicos. Em alguns casos, outros líquidos são aquecidos para produzir vapores líquidos usados em processos. A capacidade da caldeira é relatada como libras de vapor produzidas por hora ou potência da caldeira (BHP - Boiler Horse Power), o que representa 20.000 libras/hora de capacidade de produção de vapor por BHP. Quase todas as caldeiras são alimentadas a combustível e podem usar biocombustíveis, carvão e subprodutos. A composição dos gases de escape de uma caldeira depende do tipo de combustível utilizado e pode necessitar de tratamento adicional se contiverem poluentes como SO2, fuligem, cinzas ou outro tipo de partículas.
Essas categorias de processo abrangem quase todos os processos térmicos usados nas fábricas. Deve-se notar que essas categorias não são compartimentadas. Em alguns casos, eles se sobrepõem. Por exemplo, a redução de minério de ferro para produzir ferro líquido inclui aquecimento, reações térmicas e fusão. Certos
processos químicos e de refino de petróleo podem incluir aquecimento de fluidos, reações químicas térmicas e até fusão. Essa classificação de processos térmicos é muito útil na identificação e implantação de uma ou mais estratégias de descarbonetação. Nem todos os processos são usados em cada fábrica. Algumas indústrias podem usar apenas processos de secagem, fusão e recozimento, enquanto uma siderúrgica integrada pode usar quase todos os processos listados na Tabela 1. A Tabela 2 fornece uma lista de processos térmicos em cada categoria aplicável para a indústria siderúrgica.
Este artigo terá sequencia com a Parte II na próxima edição desta revista Industrial Heating Brasil
PARA MAIS INFORMAÇÕES: Arvind Thekdi é presidente da E3M Inc., que fundou há 22 anos, em Gaithersburg, Md. EUA. Ele tem mais de 55 anos de experiência em combustão, melhorias de eficiência energética, redução de emissões e recuperação de calor residual em sistemas de aquecimento industrial. Ele pode ser contatado em arvindthekdi@gmail.com.
Conheça o Portal Aquecimento Industrial, Notícias, Artigos, Colunas junto com informações relevantes sobre a Indústria Metalmecânica no Brasil e do mundo.
Algumas pessoas acham que podem dizer se uma peça quebrou devido à fragilização por hidrogênio olhando para ela. Isso não está correto. O momento da trinca é apenas um dos principais fatores que precisam ser documentados se houver suspeita de fragilização por hidrogênio. Mais quatro estão listados na barra lateral.
Embora seja possível que a fragilização por hidrogênio possa estar associada à fratura imediata na instalação, seria surpreendente se não houvesse fatores adicionais que facilitassem um evento de dano assistido por hidrogênio tão rápido. Talvez uma trinca de têmpera ou uma descontinuidade de formação ou fundição concentrou as tensões além do plano de projeto. A suspeita é justificada ao revisar relatórios que diagnosticam hidrogênio sem relatar o momento do(s) evento(s) de trinca.
Todos os cinco parâmetros listados devem ser documentados para um diagnóstico confiável de fragilização por hidrogênio em componentes de aço endurecido. Observe que existem outras fontes de hidrogênio além da decapagem e do revestimento. Também é importante perceber que as trincas intergranulares podem parecer muito diferentes em componentes que sofreram trabalho pesado a frio sem exposição adicional a altas temperaturas.
Historicamente, pensava-se que a fragilização por hidrogênio estava confinada a partes acima de 39 Rockwell C. Em minha experiência, pequenas peças galvanizadas acima de 43 Rockwell C parecem preencher as fileiras de trincas relacionadas à fragilização por hidrogênio a uma taxa significativamente maior do que aquelas entre 39 e 42.
Esta é uma afirmação problemática, uma vez que a precisão do método de teste Rockwell C é geralmente considerada mais ou menos 2. Esta é a minha experiência, por isso estou relatando-a.
Aqui está a razão pela qual decidi que seria útil revisar a questão da fragilização por hidrogênio. Chegou ao meu conhecimento que algumas empresas estão permitindo que galvanizadores de aço endurecido esperem até quatro horas, ou até mais, antes de fazer um cozimento de prevenção de fragilização por hidrogênio. Isto é um erro. “Antigamente”, a fragilização por hidrogênio era um problema tão grande que o governo federal americano estava considerando a prisão de técnicos que cometessem erros ao testar fixadores de Grau 8 usados para aplicações militares! (Na época, meu técnico no laboratório independente me fez prometer que levaria ensopado de mariscos, não creme de tomate, se fosse esse o lote dele.)
A ameaça de prisão foi resultado de numerosos problemas de fragilização por hidrogênio em equipamentos militares e reatores nucleares. Para piorar a situação, descobriu-se que os parafusos SAE J429 Grau 8.8 foram marcados incorretamente como parafusos Grau 8. Os parafusos de grau 8.8 não resistem a condições de temperatura elevada, assim como os parafusos de grau 8, que devem ser temperados a uma temperatura mais alta, e os parafusos de grau 8.8 podem ter tensões residuais mais altas mesmo antes de serem colocados em serviço. Isso prepara o terreno para que as rachaduras de hidrogênio nucleassem imediatamente após a galvanoplastia.
Uma consequência adicional do “escândalo de parafusos falsificados” foi que a maioria das pessoas na indústria
Diagnosticando a Fragilização por Hidrogênio em Peças de Aço
aprendeu que a desidrogenização tinha que ser efetuada dentro de uma hora após as peças saírem do banho de galvanização. A indústria convenceu o Congresso de que se autorregularia. Problemas de fragilização por hidrogênio pareciam ser poucos e distantes por alguns anos depois disso. Agora eles parecem ser mais frequentes. Pelo menos eu ouço pessoas alegando ter problemas de fragilização por hidrogênio com mais frequência. Eles podem não ter estudado a lista de 5 passos na barra lateral.
5 características principais que permitem o diagnóstico adequado da fragilização clássica por hidrogênio em aço endurecido:
1. Trincamento retardado sob uma tensão sustentada
2. Características de trincas em microescala intergranular (Fig. 1)
3. Uma fonte conhecida de hidrogênio (geralmente galvanoplastia ou decapagem)
4. Um componente suscetível (geralmente onde a resistência ao escoamento se aproxima da resistência à tração)
5. Isenção documentada de outros problemas conhecidos por promover fratura intergranular (como temperatura de revenimento imprópria ou resfriamento lento de componentes muito grandes devido ao processamento a quente), especialmente na presença de carga de impacto (Fig. 2).
Mesmo que algumas empresas tenham permitido que o ciclo de desidrogenização seja adiado além de uma hora após o revestimento, é altamente preferível tratar as peças o mais rápido possível e o mais próximo possível após a saída do banho de revestimento. Uma hora é preferível como o tempo máximo decorrido antes de iniciar o ciclo.
Isso é especialmente importante para peças críticas que têm implicações de segurança ou para peças pequenas que vão para montagens caras. Considere o custo para colocar as peças no forno em tempo hábil em comparação com o custo para consertar um número indeterminado de peças quebradas em uma montagem complexa. Fabricantes de peças pequenas fariam bem em considerar isso ao cotar peças pequenas endurecidas e revestidas.
Minimizar o atraso pós-galvanoplastia antes do cozimento também é extremamente importante para peças tratadas termicamente cuja dureza especificada está acima de 40 Rockwell C e para peças pesadamente trabalhadas a frio, qualquer que seja seu valor de dureza.
PARA MAIS INFORMAÇÕES: Debbie Aliya é proprietária e presidente da Aliya Analytical, Inc. em Grand Rapids, Michigan, e é especializada em análise e prevenção de falhas.
Compósitos C/C estão sendo usados em uma variedade de campos de tratamento térmico, enquanto espera-se que a tecnologia de molas de carbono melhore ainda mais a eficiência da produção. Os materiais compósitos de carbono reforçados com fibra de carbono (C/C) têm várias vezes a resistência e o módulo de elasticidade dos materiais convencionais de carbono e grafite e oferecem excelente resistência ao calor, resistência à abrasão e tenacidade. Os compósitos C/C têm sido amplamente utilizados em tampas de nariz e bordos de ataque de asas de naves espaciais, peças resistentes ao calor de motores a jato e turbinas a gás e materiais de freio de aeronaves.
Os compósitos C/C já haviam aparecido no mundo na década de 1960 e começaram a encontrar uso prático
nas aplicações mencionadas anteriormente na década de 1980. Apesar disso, eles não têm sido amplamente utilizados em aplicações industriais em geral. No entanto, a faixa de preço atual está totalmente dentro do escopo de uso em aplicações industriais gerais. Como material substituto para grafite e aço resistente ao calor, o uso de compósitos C/C está se expandindo no campo de tratamento térmico globalmente.
As molas helicoidais são usadas como elementos mecânicos em várias máquinas, dispositivos ou mecanismos e tornaram-se peças indispensáveis e importantes em utensílios domésticos diários, produtos industriais e outros campos. As molas helicoidais convencionais são geralmente feitas de metal, mas as molas helicoidais de metal têm baixa resistência ao calor e são difíceis de usar em altas temperaturas.
Por exemplo, uma chamada liga resistente ao calor tem uma temperatura máxima de 400°C. Além disso, mesmo ligas super resistentes ao calor, como Inconel e Hastelloy, perdem força e se deformam significativamente em temperaturas acima de 700°C, impossibilitando seu uso como molas em tais ambientes. Além disso, como alguns tipos de molas helicoidais de metal são facilmente magnetizáveis, elas não podem ser usadas em um ambiente afetado pelo magnetismo.
Por outro lado, as molas helicoidais de cerâmica, como nitreto de silício e zircônia, têm resistência ao calor e à corrosão superiores quando comparadas às molas helicoidais de metal, mas são vulneráveis a choque térmico e quebram quando usadas repetidamente em temperaturas superiores a 1000°C. As molas helicoidais de cerâmica também têm a desvantagem de serem frágeis e difíceis de manusear devido à falta de resistência.
Nos últimos anos, automóveis e aeronaves foram reduzidos em peso para melhorar a eficiência de combustível. Várias máquinas industriais também requerem materiais de mola leves para substituir os metais para diversos fins.
Uma solução para esses problemas é o uso de molas em compósito C/C. Existem molas helicoidais de compósito C/C que são feitas cortando blocos de compósito C/C reforçados com fibra longa reforçados bidimensionalmente. No entanto, houve uma desvantagem. A fibra foi
segmentada durante o processamento e não foi possível apresentar resistência suficiente. Isso significava que a constante da mola provavelmente diminuiria no uso repetido em condições quentes.
Para compensar estes inconvenientes, foi proposta uma mola de compósito C/C de um tipo em que as longas fibras de carbono são espiraladas contínuas numa direção e não segmentadas. Uma vez que as fibras desta mola são contínuas e podem demonstrar plenamente o seu papel como fibra de reforço, é um produto que mantém uma constante de mola estável … mesmo após uso repetido em condições quentes.
As vantagens de usar um dispositivo de brasagem equipado com mola compósito C/C são as seguintes:
• Redução de peso total e maior produtividade: Isso elimina a necessidade de pesos mortos e melhora a eficiência térmica, levando à economia de energia.
• Eficiência operacional aprimorada: O uso de molas helicoidais C/C leves em vez de pesos mortos pesados não apenas economiza energia, mas também melhora o ambiente de trabalho e o desempenho dos operadores de fabricação.
• Redução da taxa de defeitos: O calor radiante não é mais bloqueado por um grande peso, levando a uma redução na taxa de defeitos.
• Maior vida útil: Como não há deformação térmica do próprio peso do metal, não há preocupação com cargas desbalanceadas, levando a uma vida útil mais longa.
• Aumento do volume total de produção: É possível aumentar a carga total das peças processadas reduzindo consideravelmente o peso do dispositivo.
As molas helicoidais compósitas C/C contínuas de fibras longas descritas têm a desvantagem de serem difíceis de organizar ordenadamente as fibras longas em forma de espiral, tornando-as inadequadas para produção em massa.
Como o tamanho da mola depende do tamanho do molde, tem sido difícil produzir uma variedade de tamanhos e resistências de mola.
Para compensar essas desvantagens, foi desenvolvida uma mola com um alto módulo de cisalhamento que pode suportar uma grande carga com um processo de fabricação mais simples e produção em massa. Em vez de uma mola helicoidal, uma mola em forma de placa foi fabricada em zigue-zague usando um compósito C/C.
Em vez de um material compósito C/C reforçado unidirecional, no qual as fibras de carbono são alinhadas em uma direção no plano da placa, fibras curtas de carbono foram usadas como material de reforço e orientadas aleatoriamente no plano em camadas. Verificou-se que o módulo de cisalhamento no plano de um compósito C/C bidimensional orientado aleatoriamente foi drasticamente melhorado, de modo que esta orientação de fibra pode ser aplicada como um material para uma mola de placa usinada em forma de Z.
Como resultado da configuração descrita, a mola Z pode ser usada repetidamente mesmo em ambientes de alta temperatura acima de 1000°C. Tornou-se possível produzir uma mola com um alto módulo elástico de cisalhamento capaz de suportar uma grande carga.
A Figura 3 mostra um exemplo representativo de uma mola em forma de placa com uma estrutura em forma de Z. Esta figura mostra uma mola de placa de compósito C/C usinada em forma de Z por corte a jato de água a partir de uma placa laminada de compósito C/C na qual as fibras
de carbono de fibra curta são orientadas aleatoriamente de maneira bidimensional.
Na Fig. 3, a direção do eixo Z indica a direção na qual os materiais intercamadas semelhantes a folhas e as fibras de carbono são orientados aleatoriamente
bidimensionalmente e laminados. No laminado moldado de compósito C/C, as fibras de carbono fibrosas curtas são orientadas aleatoriamente bidimensionalmente no plano XY, mas as fibras de carbono fibrosas curtas não são dispostas na direção do eixo Z.
Portanto, dando direcionalidade conforme mostrado na Fig. 3, uma mola em forma de placa usinada em forma de serpentina no plano do eixo XY e tendo uma largura predeterminada na direção do eixo Z pode ser obtida. Uma vez que tal método de processamento pode ser adotado, se um laminado feito de compósito C/C com um tamanho predeterminado for fabricado, tornou-se possível produzir em massa molas em forma de placa usinadas em forma de zig-zag por usinagem.
Quando tal mola plana usinada em forma de Z é usada como uma mola de compressão ou uma mola de tensão, as características de carga-deflexão da mola plana são determinadas pela rigidez à flexão (a rigidez à flexão é determinada pelo módulo de tração de cada placa de material) e a rigidez ao cisalhamento. Em ambos os casos, conseguimos obter uma alta carga e uma grande margem de deflexão que não poderiam ser alcançadas com molas de compósitos C/C em forma de espiral.
A Figura 5 mostra a curva de carga/deslocamento da mola de compósito C/C tipo Z. A partir desta figura, são exibidas características satisfatórias da mola, mesmo em testes de carga repetidos.
Depois de aquecer a mola de compósito C/C tipo Z em um estado comprimido usando parafusos e porcas a 1250°C por 30 minutos em uma atmosfera de nitrogênio (Fig. 6), as características da mola foram medidas à temperatura ambiente e um teste de aquecimento repetido foi realizada.
A Figura 7 mostra a mudança no comprimento natural. Uma diminuição de cerca de 1% no comprimento natural foi observada apenas durante a primeira fase de aquecimento. No entanto, o comprimento natural não mudou, mesmo que o aquecimento fosse repetido depois, e descobriu-se que não havia ajuste algum.
Em comparação com as molas de compósitos C/C em forma de espiral, as molas de compósitos C/C feitas de
materiais com reforço de fibra curta são caracterizadas por muito poucas restrições de forma e várias configurações possíveis.
Exemplos de Aplicação de Molas de Compósito C/C Feitas de Reforço de Fibra Curta
A mola tipo Z de compósito C/C descrita até agora exigia várias outras peças e componentes para fixação na peça de trabalho, conforme mostrado nas figuras anteriores. O clipe C/C foi desenvolvido para evitar essa complexidade.
Pressionando as extremidades opostas da abertura, o clipe C/C abre conforme mostrado na Fig. 8. Ensanduichando as peças nesta porção conforme mostrado na Fig. 9, é possível aplicar uma carga nas peças sem preparar um dispositivo de fixação com uma estrutura complicada.
Foi desenvolvido um produto que combina as características da mola Z de compósito C/C e as funções do parafuso de compósito C/C. O forno, que realiza tratamento térmico em temperaturas próximas a 2.000°C, possui eletrodos e elementos de aquecimento feitos de grafite. À medida que o tamanho deste forno de aquecimento aumenta e o tamanho dos elementos de grafite aumenta, a deformação devido ao próprio peso do elemento de aquecimento aumenta e a deformação permanece após aquecimento e resfriamento repetidos.
Como método para reduzir esta deflexão, é possível fazer os elementos de aquecimento de compósito C/C. Mesmo que seja o mesmo material de carbono, no entanto, o grafite e o compósito C/C aquecem até quatro vezes mais. A diferença no coeficiente de expansão e o estresse térmico causado por essa diferença não podem ser suportados, resultando muitas vezes em falha da junta. Ao usar um parafuso com função de absorção de expansão térmica, conforme mostrado na Fig. 10, a parte entalhada do parafuso C/C atua como uma mola, absorvendo mudanças dimensionais devido à expansão térmica e evitando danos.
Como mencionado anteriormente, as molas convencionais de compósito C/C em forma de espiral eram limitadas em tamanho devido a limitações de moldagem. Vários tamanhos de mola de compósito C/C podem ser fabricados a partir de materiais reforçados com fibras, desde que a placa de material seja preparada e esteja dentro do tamanho da placa.
A Figura 11 é um exemplo de uma mola em Z com um grande formato em serpentina que não poderia ser realizado com uma mola em forma de espiral, enquanto a Fig. 12 mostra a curva de carga/deslocamento desta
Compreender os diferentes tipos e sistemas de teste de dureza pode ser útil para determinar uma solução ideal. A funcionalidade de teste de dureza evoluiu e agora os usuários podem discar para instrumentação de calibre de classe mundial que se alinha mais de perto com seus aplicativos disponíveis.
Um dos testes de dureza de indentação mais comuns usados atualmente é o teste de dureza Rockwell. Embora menos difundidos, os testes de dureza Brinell e Vickers também são utilizados. A maioria dos testes de dureza de indentação mede a deformação que ocorre quando o material sendo testado é penetrado com um indentador. Dois níveis de força são aplicados ao penetrador em taxas e tempos de permanência especificados ao realizar um teste de dureza Rockwell. Isso é diferente dos testes Brinell e
Vickers, onde o tamanho da indentação é medido após o processo de indentação. A dureza Rockwell do material é baseada na diferença na profundidade do penetrador em dois momentos específicos durante o ciclo de teste. O valor da dureza é calculado usando uma fórmula que foi derivada para produzir um número dentro de uma faixa de números arbitrariamente definida, conhecida como escala de dureza Rockwell.
Independentemente da escala Rockwell ou penetrador sendo usado, o procedimento geral do teste Rockwell é o mesmo. O penetrador é colocado em contato com o material a ser testado e uma força preliminar (também
conhecida como carga menor) é aplicada ao penetrador. A força preliminar geralmente é mantida constante por um período definido (tempo de permanência), após o qual a profundidade da indentação é medida. Depois que a medição é feita, uma quantidade adicional de força é aplicada a uma taxa definida para aumentar a força aplicada ao nível de força total (também conhecida como carga principal). A força total é mantida constante por um tempo definido, após o qual a força adicional é removida, retornando ao nível de força preliminar. Depois de manter a constante de força preliminar por um tempo definido, a profundidade da indentação é medida uma segunda vez, seguida pela remoção do indentador do material de teste. Para calcular o número de dureza Rockwell, é usada a diferença medida entre a primeira e a segunda medições de profundidade de indentação, h.
Se estiver usando um durômetro Rockwell mais antigo, o operador pode ter que controlar manualmente algumas
ou todas as etapas do procedimento de teste. A maioria das máquinas mais novas de hoje executa automaticamente todo o teste. Quando deixar uma marca ou entalhe não é uma opção, a tecnologia ultrassônica não destrutiva pode ser usada.
Ao testar a dureza de aço carbono, liga de aço, ferro fundido, metais não ferrosos e plásticos de engenharia, os durômetros digitais de bancada Rockwell podem ser usados para medir diretamente as escalas de dureza Rockwell regulares mais populares. Eles também podem converter rapidamente esse valor de dureza em HB, HV, HK e muitas outras escalas. Os recursos desejáveis do durômetro incluem a capacidade de obter resultados ultraprecisos, uma ampla faixa de medição e recursos selecionáveis de força de teste de escala. Além disso, o carregamento/ descarregamento forçado de teste principal automático, um display digital de alta resolução e armazenamento de dados USB são todos vantajosos.
Uma interface de tela sensível ao toque amigável pode acelerar as operações, e a capacidade de usar a saída USB para uma unidade flash é excelente para mobilidade de dados. Existem opções para aplicar a carga de peso, como em sistemas digitais que usam pesos para aplicar a carga ou usam uma célula de carga de malha fechada para aplicar a carga de peso. Este último proporciona maior precisão e repetibilidade. Com um sistema de peso carregado, o nível da máquina é de grande importância para que os pesos caiam corretamente. Esta é uma questão menos crítica ao usar um sistema de células de carga.
Em conformidade com os padrões ASTM E-18
Superficial Rockwell Hardness, os durômetros nesta categoria oferecem excelente repetibilidade em todas as escalas de dureza Rockwell superficial. O teste superficial de dureza Rockwell é projetado para peças de trabalho muito finas e macias. Os sistemas são ideais para uma ampla variedade de ambientes, incluindo
laboratórios de inspeção, instalações de tratamento térmico, ferramentarias, oficinas e laboratórios. Para maior versatilidade, os durômetros duplos são capazes de testar em todas as escalas de dureza Rockwell regulares e superficiais.
Os sistemas Dolphin-nose permitem o teste de dureza de diâmetros internos e externos. Os sistemas são geralmente maiores em tamanho do que outros sistemas Rockwell de bancada, oferecendo maiores alturas e profundidades de teste. Os modelos Dolphin-nose oferecem uma alça manual que ativa o sistema de pré-carga ou um sistema avançado de pré-carga de eixo z automático. Usando o sistema de pré-carga automática do eixo z, após colocar a peça de trabalho na posição de teste, o operador só precisa pressionar o botão de partida para que a máquina conclua o processo de teste.
O teste de dureza Brinell é comumente usado para testes grandes e porosos de metais menos duros, como peças fundidas. Sistemas de bancada modernos podem lidar com as aplicações de dureza Brinell mais populares e incorporar a mais recente tecnologia de circuito fechado. Uma carga de teste é aplicada por meio de uma unidade de controle de circuito fechado com uma célula de carga (para aplicar cargas de peso de até 3.000 kg), um motor de corrente contínua e uma unidade eletrônica de medição e controle. O resultado são medições de dureza Brinell altamente precisas em todas as cargas de teste de até 0,5%. Uma carga comum over shoot ou under shoot, também conhecida como peso morto tradicional (loop aberto), é eliminada. A ausência de pesos mecânicos não só elimina problemas de atrito como também torna o equipamento menos sensível a desalinhamentos causados por vibrações. Os sistemas são ideais para laboratórios, oficinas, salas de ferramentas e laboratórios de inspeção.
Os sistemas ópticos digitais acionados por software oferecem vantagens sobre os microscópios manuais que são fornecidos com várias máquinas de teste de dureza. Conectado a um PC, laptop ou tablet, o operador pode apertar um único botão para fazer medições automáticas e instantâneas. Todos os gráficos podem ser salvos junto com os resultados do teste em formatos Word ou Excel.
Os durômetros de bancada Micro Vickers/Knoop são opções econômicas em aplicações de dureza Vickers. Estes são ideais para aqueles que não realizam testes de alto volume todos os dias. O teste é realizado em peças de trabalho extremamente finas/pequenas e geralmente é usado para verificar a dureza de camadas, recobrimentos e revestimentos em peças pequenas em um ambiente de laboratório. Um alto nível de preparação é necessário para tais testes, incluindo, mas não se limitando a, um alto grau de polimento.
Existem três tipos de controle de torre, incluindo uma torre manual básica para mudar de óptica para indentação e de volta para óptica para medição. Um segundo tipo incorpora uma torre automática, dando aos operadores maior liberdade para alterar a posição da torre por meio de um botão no teclado do testador. Os testadores de dureza Vickers/Knoop mais populares
têm uma opção de controle de torre que usa software para controlar todo o teste com um processo de um clique usando detecção automática de borda calibrada. O software de vídeo e medição de precisão também permite clicar nas bordas da indentação no software e, em seguida, derivar uma leitura de dureza na tela.
Projetado para medições precisas de dureza de pequenas peças de precisão, materiais finos, camadas endurecidas e todos os tipos de componentes de aço, os testadores de dureza macro Vickers utilizam cargas de peso maiores de até 50 kg. Este tipo de teste preenche a lacuna entre as máquinas superficiais Rockwell e micro Vickers. Estes sistemas têm uma torre manual.
Os durômetros portáteis Shore são usados para testar materiais como borracha, plásticos macios e couro. Versões também estão disponíveis para testar plásticos duros, como bolas de boliche e capacetes. Os durômetros eletrônicos para medir os valores Shore A e Shore D são projetados para caber confortavelmente e firmemente na mão do usuário. Um grande visor de LED e um controle simples de três botões tornam este dispositivo fácil de usar.
Existem dois métodos digitais populares de teste portátil de dureza. O primeiro é o impacto dinâmico, baseado no princípio Leeb de dureza desenvolvido por Dietmar Leeb na década de 1970. Um corpo de impacto carregado por mola é empurrado para a superfície de teste, afetando o rebote. O impulso inicial e a velocidade de rebote são medidos em um modo sem contato e são calculados como um valor de dureza Leeb.
Eles são então automaticamente convertidos em valores Rockwell C, B, Brinell, Vickers e Shore. O benefício da portabilidade também significa que o testador pode ser levado até a peça de trabalho, o que é especialmente útil ao testar peças grandes e/ou pesadas. Este método resultou em resultados de testes de dureza portáteis eficientes, rápidos e precisos.
Quando uma marca ou entalhe na peça de trabalho deve ser evitada, no entanto, o teste ultrassônico é uma ótima solução. Testadores de dureza portáteis não
destrutivos avançados utilizam tecnologia ultrassônica com impedância de contato ultrassônica (UCIUltrasonic Ccontact Impedance), permitindo que um durômetro portátil teste superfícies especiais em peças pequenas e finas sem marcar a superfície. Essas unidades podem testar metais tão finos quanto 2 mm em todas as escalas - duros ou macios. A tecnologia UCI está disponível em sistemas manuais e motorizados. Os sistemas de sonda motorizada são usados para testar recobrimentos e revestimentos muito finos ou superfícies com acabamento de alto polimento.
O UCI é baseado em um diamante de 136 graus na extremidade de uma haste vibratória sendo pressionada na superfície de teste com uma carga fixa. A diferença na frequência de vibração ultrassônica é então calculada em um valor de dureza. O procedimento de teste UCI é mais lento do que o estilo de impacto dinâmico. No entanto, o método UCI tem as vantagens de ser não destrutivo e capaz de testar peças finas e pequenas.
Anteriormente, indentações destrutivas feitas em tais peças de amostra significavam a pilha de lixo para aqueles testados. Usando ultrassom, esse não é mais o resultado. Esses sistemas possuem arquitetura aberta e podem ser calibrados para leitura de qualquer metal, em qualquer escala de dureza, com amostras de referência para realizar a calibração inicial. O teste ultrassônico portátil é ideal para aplicações como rolamentos, pistões e válvulas, entre muitos outros. As indústrias para este tipo de teste incluem a indústria aeroespacial, automotiva, de peças médicas e fabricação de facas, para citar apenas algumas.
PARA MAIS INFORMAÇÕES: John Richardson é coordenador de produtos da The L.S. Starrett Company em Athol, Massachusetts, EUA. Ele pode ser contatado em jrichardson@starrett.com ou em +1 978-249-3557, ext. 519. Para obter informações adicionais, visite www.starrett.com.
Alaster McDonach - Centro de Pesquisa de Conformação Avançada da Universidade de Strathclyde (AFRC - Advanced Forming Research Centre) dentro do Grupo do Instituto Nacional de Manufatura da Escócia (NMIS - National Manufacturing Institute Scotland); ESCÓCIA Anastasia Khatuntseva – Fábrica Digital NMIS; ESCÓCIA Constantinos Vassiades –Doutorando patrocinado por membros do núcleo do AFRC; ESCÓCIA
Adetecção de borda quente (HED - Hot Edge Detection) permite a coleta de informações sobre a mudança de forma que ocorre durante o forjamento em tempo real. A integração do HED fornecerá uma medição de geometria confiável e automática, que fornece uma melhor compreensão da evolução microestrutural que ocorre durante o forjamento.
Apesar de ser um dos métodos de fabricação mais antigos, ainda há muito a ser entendido sobre a complexidade do processo de forjamento. No entanto, a forja de metais certamente percorreu um longo caminho desde que ganhou destaque no século 13 e evoluiu além do reconhecimento nos últimos 800 anos.
À medida que a tecnologia se desenvolve, também aumenta nossa capacidade de forjar uma gama cada vez maior de peças de alta integridade. Até hoje, o forjamento continua sendo um processo crucial na cadeia de suprimentos de manufatura. É o método de fabricação escolhido para setores como petróleo e gás, ferroviário, nuclear e aeroespacial, onde resistência, durabilidade e segurança são as principais prioridades.
Mas a forja tem sido historicamente resistente à Indústria 4.0, ou a quarta revolução industrial, e não conseguiu acompanhar outros processos de fabricação. A
adoção lenta resultou em um processo antigo existente em um mundo moderno, onde a maioria dos equipamentos de forjamento industrial oferece recursos limitados de coleta de dados, com armazenamento restrito ou nenhum armazenamento de dados. Isso significa que devemos confiar fortemente em operadores qualificados e conhecimento tácito.
Em comparação com suas contrapartes mais elegantes, como usinagem e metrologia, a indústria de forjamento carece de uma abordagem transformadora orientada por dados e dos vastos benefícios de eficiência que a acompanham.
O atraso nos dados não se deve à falta de interesse no processo, mas sim a um reflexo das duras condições ambientais associadas ao forjamento, o que o torna geralmente menos receptivo à adoção da Indústria 4.0. Se pudermos ir além disso e usar dados para entender verdadeiramente o comportamento de um material durante o processo de forjamento, podemos ajustar nossos métodos para produzir melhores resultados. As melhorias de qualidade podem ser alcançadas pela digitalização dos principais parâmetros do processo, resultando em reduções de custo e energia, menos desperdício de material e peças de maior integridade.
Adicionando Dados a um Processo Histórico em Questão de Segundos Juntos, a Fábrica Digital do Instituto Nacional de Manufatura da Escócia (NMIS) e o Centro de Pesquisa de Conformação Avançada estão buscando maneiras inovadoras de incorporar a digitalização no núcleo do processo de forjamento. Os operadores só podem acessar um determinado nível de dados dentro da cadeia de fornecimento de forjamento, e essas informações não estão disponíveis. Não é uma tarefa pequena, mas esse processo de “arte negra” será verdadeiramente revolucionado quando pudermos acessar os dados de forjamento em tempo real, permitindo finalmente entender o que realmente se passa dentro da prensa e como isso afeta a peça forjada.
Na primeira etapa da transformação digital, instalamos um sistema de aquisição de dados baseado em PLC chamado Data Hub, que permite a integração de vários sistemas e fluxos de dados. Isso permitiu a aquisição direta não invasiva de dados da prensa hidráulica de 500 toneladas, demonstrando que a digitalização nem sempre requer atualizações caras de hardware e que mesmo as máquinas herdadas são capazes de se comunicar com sistemas externos.
Dentro do mesmo Data Hub, também integramos dados do forno e alguns sensores externos para entender melhor o processo de forjamento. A integração de sistemas é importante para análises futuras porque permite o controle total dos fluxos de dados. Mais importante, todos os fluxos de dados tornam-se sincronizados, o que significa que há um único carimbo de data/hora em todos os sistemas.
A segunda etapa da transformação digital é focada em uma peça forjada em si. Temos trabalhado em uma solução abrangente de visão de máquina, integrada no mesmo Data Hub. Essa solução de visão de máquina foi chamada de detecção de borda quente (Hot Edge Detection - HED). Ele pode detectar o tamanho de um tarugo durante o processo de forjamento.
Como melhorar a conectividade é fundamental para obter aquisição de imagens e transmissão de dados em alta velocidade, uma câmera habilitada para
GigE Vision foi integrada ao sistema para detecção, medições e análises de formas ao vivo. O algoritmo desenvolvido fornece o perfil e o tamanho de uma peça forjada a quente em 10-30 milissegundos.
Um formato de exibição útil para suporte ao operador também é crucial para monitoramento e controle de processo ao vivo. Foi desenvolvida uma Interface em tempo real Homem-Máquina (Human-Machine Interface - HMI), permitindo ao usuário interagir com o sistema de visão de máquina durante o forjamento. Essencialmente, a HMI permite ao usuário definir uma região de interesse para auxiliar o HED caso necessário.
Além disso, a exposição da câmera pode ser alterada rapidamente para compensar os efeitos de resfriamento durante a fabricação. Para maior flexibilidade, o perfil do componente pode ser extraído em um formato de arquivo que permite análise pós-processamento.
Como parte dessa pesquisa, estamos usando o HED para obter a avaliação da superfície de um tarugo durante o forjamento para determinar a forma e a microestrutura de uma peça, o que fornece uma janela para a transformação termomecânica durante o processo como nunca antes.
Mais sobre Detecção de Borda Quente (HED) HED é um processo automático que permite a coleta de informações sobre a mudança de forma que ocorre durante o forjamento. A conversão de um lingote fundido em tarugo requer muitos golpes de forjamento combinados com etapas de reaquecimento, o que torna muito difícil entender as mudanças exatas na estrutura que ocorrem durante o processo.
Em muitos casos, verificar o tamanho e a forma final de um componente forjado ainda envolve algum tipo de verificação manual – uma abordagem testada e comprovada que carece de um método de validação matemático e baseado em dados. Da mesma forma, o processo requer calor extremo, o que significa que os fabricantes devem validar o processo à distância. No entanto, o HED está mudando isso e transformando a confiança em habilidades e conhecimentos em um sistema numérico baseado em dados, permitindo a validação em um ambiente seguro.
O HED usa um sistema inovador de câmeras, que podem identificar a radiação de comprimento de onda emitida por objetos quentes em milissegundos e, portanto, identificar as bordas de um determinado objeto com segurança e distância. Crucialmente, uma vez que as arestas de um objeto tenham sido detectadas,
o sistema pode fornecer essas informações a um computador, que então mede a evolução da geometria das peças forjadas a quente durante o processo de forjamento.
Os lingotes fundidos usados no forjamento são tipicamente caros, e o processo em si é intensivo em energia e oferece margens mínimas de erro. No entanto, a incapacidade de recuperar dados em tempo real significa que não podemos alterar o processo e podem ocorrer erros, resultando em atrasos significativos, desperdício de energia e aumento de custos.
Através do HED podemos executar o processo de forjamento e depois examinar o tarugo em tempo real, o que nos permite revisar a mudança de forma e alterar nossa abordagem enquanto o processo ainda está em andamento.
O uso de um sistema seguro, confiável e automático para medir peças forjadas a quente também pode permitir que os especialistas desenvolvam uma melhor compreensão do processo de fabricação e da resposta do material. Ao integrar esse sistema de monitoramento ao processo industrial, os fabricantes podem aprender como implementar e desenvolver um sistema de modelagem mais preciso que tornará o processo de forjamento mais eficiente no futuro.
A integração do HED fornecerá uma medição de geometria confiável e automática, o que representa uma grande oportunidade para entender melhor a evolução microestrutural que ocorre durante o forjamento. Podemos então prever melhor as propriedades finais de um determinado objeto. Pense nos benefícios que podem ser desenvolvidos por meio desse sistema –não menos importante, a capacidade de coletar dados automaticamente para implementação futura.
Os elementos digitais do processo de forjamento se desenvolverão com o tempo, assim como nossa compreensão do método de fabricação. A integração da Indústria 4.0 dentro de um método tradicional de fabricação não vem sem desafios. Ele abre, no entanto, uma oferta única para a indústria de forjamento em escala global e o HED faz parte dessa jornada para um melhor entendimento.
Claramente, contaremos com o processo de forjamento nos próximos anos. Para garantir que este método de fabricação estabelecido esteja à altura do desafio de se destacar no futuro, é crucial agirmos agora e transformálo em um processo que possa acompanhar as demandas de um mundo digital.
O NMIS é um grupo de instalações de pesquisa e desenvolvimento de manufatura lideradas pela indústria, onde a indústria, a academia e o setor público trabalham juntos em pesquisas de manufatura inovadoras para transformar os níveis de produtividade, tornar as empresas mais competitivas e aumentar as habilidades de nossa força de trabalho atual e futura.
É operado pela Universidade de Strathclyde e apoiado pelo governo escocês, Scottish Enterprise (Agência Nacional de Desenvolvimento Econômico da Escócia), Highlands and Islands Enterprise (Agência de Desenvolvimento Econômico e Comunitário para o Norte e Oeste da Escócia), High Value Manufacturing Catapult, Skills Development Scotland, Scottish Funding Council e Renfrewshire Council.
A nova instalação NMIS, juntamente com os centros de tecnologia especializada NMIS (Lightweight Manufacturing Center e Strathclyde’s Advanced Forming Research Centre) e o centro High Value Manufacturing Catapult na Escócia são instalações-chave no Advanced Manufacturing Innovation District Scotland sendo desenvolvido pelo Renfrewshire Council em parceria com Governo escocês e Scottish Enterprise.
O NMIS irá:
• Aumentar a produtividade reduzindo as barreiras à inovação
• Estimular o investimento e aumentar a competitividade da manufatura
• Catalisar a criação de empregos e fortalecer os elos da cadeia de suprimentos
• Inspirar e atrair talentos e equipar a força de trabalho atual e futura com as habilidades que eles e as empresas precisam
• Fornecer liderança, construir colaborações e aprimorar capacidades para influenciar a adaptação e explorar oportunidades de fabricação para impulsionar a transição da Escócia para uma economia de emissões líquidas zero até 2045
• Trabalhar com empresas de manufatura de todos os tamanhos e vários setores, oferecendo benefícios em toda a Escócia Para mais informações: O autor principal Alaster McDonach (à esquerda)
é Engenheiro de Manufatura Sênior no Centro de Pesquisa de Conformação Avançada da Universidade de Strathclyde (AFRC), um centro dentro do Grupo do Instituto Nacional de Manufatura da Escócia (NMIS). A coautora Anastasia Khatuntseva (ao centro) é líder do tema Conectividade Digital no NMIS Digital Factory. O coautor Constantinos Vassiades (à direita) é um estudante de doutorado patrocinado por membros centrais do AFRC.
PARA MAIS INFORMAÇÕES: Entre em contato com Hayley Blackwood em Hayley.blackwood@ bigpartnership.co.uk ou nmis@bigpartnership. co.uk para obter informações adicionais. Para saber mais sobre HED e como estamos incorporando a Indústria 4.0 no processo de forjamento, visite www.nmis.scot e entre em contato com a equipe da NMIS para se envolver.
Confira as mais recentes notícias do Portal Aquecimento Industrial e tenha informações sobre a indústria metalmecânica no brasil e do mundo.
Site: aquecimentoindustrial.com.br
Oferecendo qualidade e confiabilidade superiores ano após ano, otimizando o desempenho e a eficiência de custos e garantindo um ótimo retorno sobre o investimento.
HVF Series (Horizontal)
Quantum QuenchTM (Resfriamento Direcional) 3QTM Series (Resfriamento Rápido)
VVF Series (Vertical)
SAR (Revestimento Vapor Phase Aluminide)