
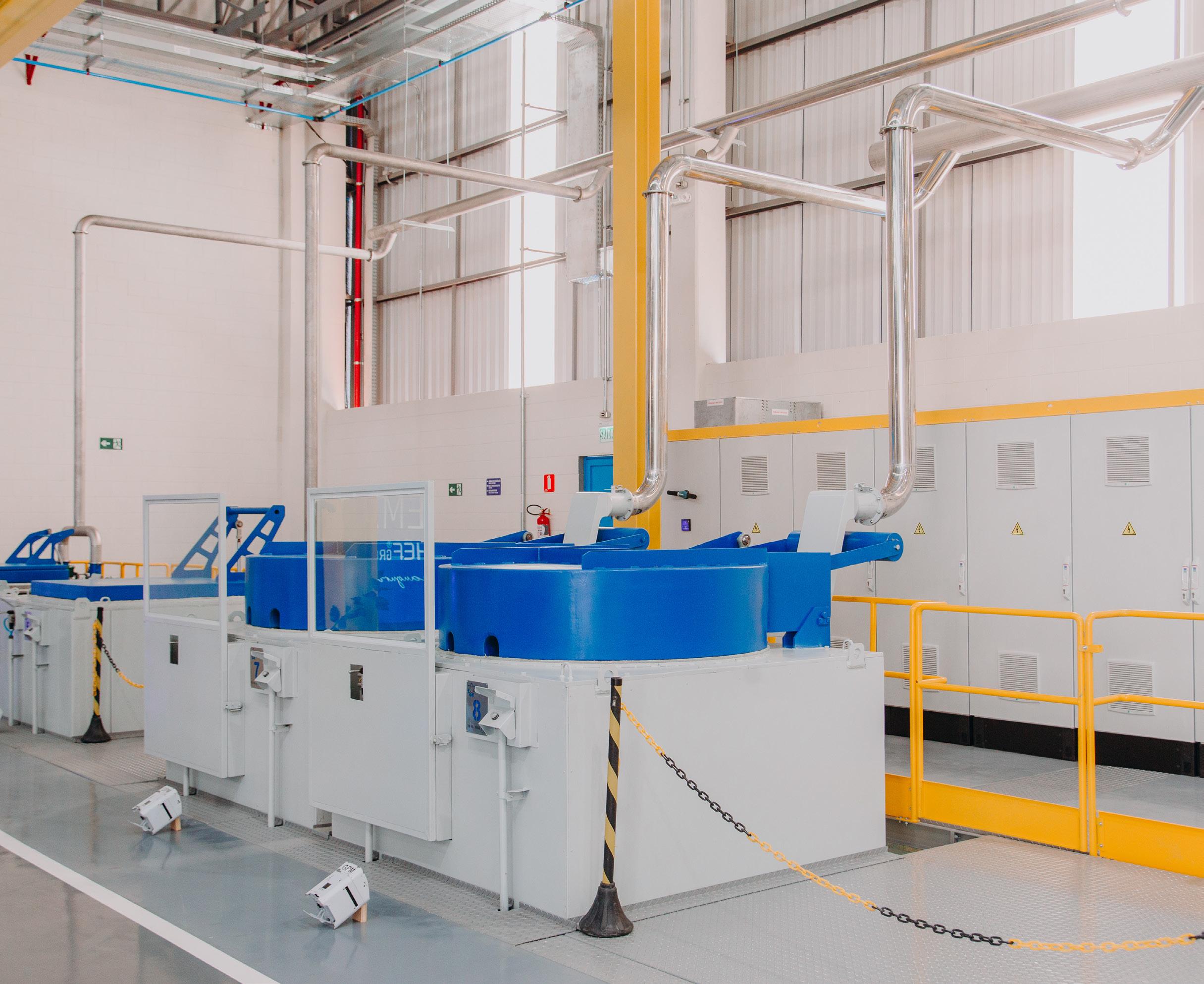
Tratamentos Termoquímicos
A ideia de tentativas e erros na vida real é do passado e não poderia ser legitimada pela gestão de hoje, tendo em conta o enorme custo e a perda de competitividade que daí resultaria. 14 22
TS Diadema: a nova unidade de nitretação do Grupo HEF. Expertise em tratamentos termoquímicos para um futuro mais verde!
No dia 22 de fevereiro de 2024 o grupo HEF Brasil concretizou um marco histórico em sua expansão: a inauguração da TS Diadema. Contando com a linha de nitretação líquida mais inovadora e sustentável da América Latina, a TS Diadema foi projetada com base em conceitos de economia circular, como otimização de recursos, eficiência energética e reciclagem de insumos; e em tecnologias digitais, como monitoramento real time controle de parâmetros do processo, otimização de ciclos e produtividade.
Controle De Processos & Instrumentação
Opções de Descarbonização para Aquecimento de Processos Industriais (Parte 2)
Arvind Thekdi
Os sistemas de aquecimento de processos industriais fornecem o calor necessário para produzir bens utilizados pelos consumidores e pelas indústrias. O calor é fornecido principalmente a partir de combustíveis, vapor e eletricidade utilizados em diversos tipos de equipamentos de aquecimento, como fornalhas, fornos, aquecedores e estufas.
Simulações
Transformação Simulada de Material: Um Estudo de Caso
Nicolas Poulain
A simulação tem aplicações quase ilimitadas e revolucionou desenvolvimentos de engenharia na manufatura.
Processos Térmicos
2º Congresso Processos Térmicos 2024
Em 19 e 20 de março de 2024 foi realizado pelo Grupo Aprenda o 2º Congresso Processos Térmicos. O evento aconteceu na área de eventos do Hotel Nacional Campinas – Trevo e contou com a participação de mais de 200 inscritos.
Processos Térmicos
Visitas Técnicas – II Congresso Processos Térmicos
Uma das atividades oferecidas aos participantes dos diversos seminários integrantes do II Congresso Processos Térmicos realizado em Campinas SP no final de Março 2024, foram as visitas técnicas a empresa da região.
Confirmação metálica
3º CCM – Congresso Conformação Metálica 2024
Em 18 e 19 de junho 2024 foi realizado pelo Grupo Aprenda o 11º Seminário de Forjamento. O evento fez parte do III CCM, Congresso de Conformação Metálica, e foi realizado nas dependências da FSA, Fundação Santo André localizado na cidade com o mesmo nome.
Revista Brasileira da Tecnologia Térmica
By
SF Editora é uma marca da Aprenda Eventos Técnicos Eireli (19) 3288-0437 - ISSN 2178-0110
Rua Ipauçu, 178 - Vila Marieta, Campinas (SP) www.sfeditora.com.br
Udo Fiorini Publisher, udo@sfeditora.com.br • (19) 99205-5789
Mariana Rodrigues Redação - Diagramação, marianar205@gmail.com • (19) 3288-0437
Jéssica Carboni Vendas, jessica@grupoaprenda.com.br • (19) 3288-0437
As opiniões expressadas em artigos, colunas ou pelos entrevistados são de responsabilidade dos autores e não refletem necessariamente a opinião dos editores.
Editorial Brasil 1a Edição da Revista
Aquecimento Industrial omo já havia anunciado em meu ultimo editorial da Revista Industrial Heating, esta revista seria substituída aqui no Brasil pela Revista Aquecimento Industrial. Uma vez que a Industrial Heating foi descontinuada a nível mundial.
Editorial Brasil 1a Edição da Revista
Aquecimento Industrial omo já havia anunciado em meu ultimo editorial da Revista Industrial Heating, esta revista seria substituída aqui no Brasil pela Revista Aquecimento Industrial. Uma vez que a Industrial Heating foi descontinuada a nível mundial.
Automóveis Sustentáveis: Deveres & Obrigações! Sustentabilidade tem sido a grande tendência atual do mundo e apostar em temas dessa área será um sucesso garantido, sejam em tecnologias de produtos, processos e novos negócios.
da. Como você pode notar nas matérias que dedicamos à sua leitura nesta edição. Além dos artigos e colunas técnicas oferecemos um panorama dos últimos e próximos eventos realizados pela Aprenda Eventos.
A Revista Aquecimento Industrial foi ori ginalmente lançada por Fernando Lummertz (ver a coluna Pioneiros da edição Jan Mar 2013 da Revista Industrial Heating Brasil no Portal Aquecimento Industrial). A revista foi publicada no Brasil de 1989 até 1993. Nossa intenção é com este primeiro número voltar a publicá-la a partir de agora, trazendo artigos técnicos, colunas e principalmente os acontecimentos em nossos eventos da área.
Também como havia comentado em meu último editorial, acabamos fechando acordo com a plataforma de notícias do setor térmico dos EUA, a Heat Treat Today. Comandada por Doug Glenn, conhecido do Brasil por chefiar no passado a revista americana Industrial Heating, seu canal de informações é neste momento o principal meio de comunicação da área térmica no continente americano. Veja por favor os comentários de Doug Glenn em sua coluna nesta edição.
Grande abraço, boa leitura!
Inscreva-se no site aquecimentoindustrial.com.br, para receber todas quartas-feiras nossa news em seu e-mail, basta colocar nome, e-mail e sua área de interesse!
DOUG GLEN Publisher/Owner
Phone: +1 724-923-8089
Os Estados Unidos continuam a ser o principal fornecedor mundial de bens manufaturados, apesar do ataque de economias manufatureiras de baixo custo em todo o mundo, como China, Índia, México e outros atores menores no corredor do Pacífico Sul, como Vietnã, Cingapura, etc. Os Estados Unidos devem grande parte da sua liderança a uma economia que tem sido historicamente livre e livre de regulamentações governamentais bem-intencionadas, mas muitas vezes prejudiciais, de um espírito de liberdade e de um individualismo robusto. Os metalúrgicos nos EUA (e no Brasil!) são pessoas trabalhadoras e engenhosas, que historicamente têm estado dispostas a trabalhar longas horas por salários modestos. O empreendedorismo prospera nos EUA porque existe uma crença fundamental de que quando uma pessoa tem sucesso num mercado livre e aberto, é porque está a fornecer um produto ou serviço que tem valor para outros. Isto é o que fez dos Estados Unidos uma grande potência metalúrgica: uma crença fundamental na liberdade individual, na engenhosidade, no trabalho árduo, na disposição para assumir riscos e uma crença fundamental de que se as pessoas forem livres para fazer o que quiserem dentro da lei, o país e o mundo serão um lugar melhor. Contudo, têm havido forças que impedem esse sucesso e quase todas essas forças provêm de políticas governamentais mal concebidas que restringem a liberdade dos indivíduos de fazerem o que sabem ser melhor para si e para os seus compatriotas. Regulamentações ambientais bem intencionadas, impostos e regulamentações financeiras excessivas, legislação sindical bemintencionada, mas prejudicial, bem como guerra
legal dirigida às indústrias nefastas de hoje (pense: Boeing, mídias sociais, IA, etc.), todos dificultam o progresso e o sucesso futuro aqui nos Estados Unidos.
A mídia, incluindo revistas técnicas de comércio industrial como a Aquecimento Industrial, é fundamental para o sucesso da indústria em geral e especialmente das indústrias de processamento térmico, forjaria, estamparia e conformação de metais. É aqui, nas páginas desta revista, que você conhecerá as mais recentes tecnologias, tendências e técnicas para ajudar você e sua empresa a serem mais lucrativos e bem-sucedidos. É também nestas páginas que as barreiras ao sucesso, como as listadas acima, podem ser discutidas e debatidas. Um indivíduo bem informado provavelmente será um indivíduo feliz e bem-sucedido.
Meu amigo, colega e editor desta revista, Udo Fiorini, e eu começamos duas outras revistas de comércio industrial no final dos anos 1990 e início dos anos 2000. A Industrial Heat Brazil e a FORGE Brazil cumpriram seu propósito e podem ser consideradas antecessoras da revista que você sabe que tem em mãos. Udo e sua equipe demonstraram um compromisso vitalício em ajudar as pessoas a se manterem bem informadas e, ao fazê-lo, contribuíram para o sucesso e a lucratividade de inúmeros metalúrgicos brasileiros ao longo das décadas. Neste início da Revista Aquecimento Industrial, eu e toda a equipe da publicação de processamento térmico que publico nos EUA, Heat Treat Today, desejamos a todos os nossos irmãos e irmãs metalúrgicos brasileiros muito sucesso e prosperidade. Certamente, esta revista contribuirá ainda mais para esse sucesso.
marcocolosio@gmail.com
Diretor da Regional São Paulo da SAE BRASIL. Engenheiro Metalurgista e Doutor em Materiais pelo Instituto de Pesquisas Energéticas e Nucleares-USP, pós doutorado pela EESC-USP. Professor titular do curso de Engenharia de Materiais da Fundação Santo André e professor da pós graduação em Engenharia Automotiva do Instituto de Tecnologia Mauá. Colaborador e associado da SAE BRASIL com mais de 30 anos de experiência no setor automotivo nos campos de especificações de materiais, análise de falhas, P&D e inovações tecnológicas.
Sustentabilidade tem sido a grande tendência atual do mundo e apostar em temas dessa área será um sucesso garantido, sejam em tecnologias de produtos, processos e novos negócios. As inciativas para tornarem as metas ambientais tangíveis estão ocorrendo de forma progressiva e intensa, praticamente presencia-se ações em todos os campos; impossível ficar apático ao assunto.
O Governo tem feito sua parte e em junho de 2024 aprovou o Programa Brasileiro Mobilidade Verde (MOVER), e sua maior aposta está no final de vida dos veículos, beneficiando com renúncias fiscais as montadoras que reciclarem uma parcela considerável dos veículos produzidos anualmente e que ainda estão circulando nas ruas, Figura 1. Neste contexto, o principal dilema das montadoras está em equacionar o custo da compra do veículo e sua reciclagem em
referência aos ganhos dos incentivos fiscais; uma das iniciativas em estudo seria agregar valor na separação de materiais nobres e investigar reuso de componentes; todos esses buscando a criação de novos negócios com retorno financeiro. Prováveis parcerias com as empresas de desmanches seriam um dos caminhos, as quais somariam capacidade suficiente para destruição dos veículos em suas “sheredder”; mas, eles não teriam estrutura para agregar valor ao reciclado, isto é, executar uma separação detalhada de materiais dissimilares e desmontagem com certificação de componentes para reuso.
O final de vida do veículo tem sido um tema em discussão; porém, a escolha de materiais e as rotas de processos para construção de componentes e veículos já fazem parte das metas ambientais; por exemplo: as rotas de fabricação de materiais ferrosos são repletas
Figura 1. Programa Brasileiro Mobilidade Verde (Ref.: ABGI BRASIL, 2024)
de oportunidades e produzi-los com um caráter verde requer muito “know how” e investimento, e inevitavelmente, um custo adicional sobre o produto final; por exemplo: fala-se muito em aço verde e já existe esta designação corrente; porém, a sua viabilização é tão complexa tecnologicamente, que apostar neste caminho é uma loteria, sem contar os investimentos que impactarão o custo adicional do material acima de 20%. Por outro lado, diante de um cenário totalmente novo em nosso meio e ainda com um caráter ideológico, relato que estamos quase prontos para aceitar parte destes pênaltis em um primeiro momento; certamente, em uma pequena proporção; como diz o provérbio “no pain, no gain” parece ser a única opção. Mirando diretamente nas usinas de aço, o uso do carvão mineral (coque) é o grande vilão na emissão de CO2, e usar hidrogênio, gás natural e ou aumentar o índice de reciclados no processo têm se tornado uma grande equação para as usinas. A situação é tão desafiadora que, imagina-se um único Alto Forno, o qual produz milhões de toneladas de ferro gusa por ano, ter sua rota de produção alterada. A produção de um alto forno é tão importante ao país que poderíamos dizer que ela impacta o produto interno bruto em termos de participação. Certamente, a transição no emprego destes consumíveis (H2, gás, sucata) no processo de obtenção do ferro-gusa e do aço será gradativa e lenta.
As usinas conhecem bem a sua missão e passam a considerar esta questão como parte da estratégia; porém, “como e quando” são os grandes desafios. Temos a certeza de que todos em futuro “muito longe” atingirão a neutralidade que queremos; mas, a questão é urgente e precisa-se de tração. Por enquanto, a única solução é partir para o mercado de carbono e compra de créditos para agregar benefícios a matriz do produto; não é a rota ideal, mas o ganho ambiental é certo e aceitável.
Avançado na raiz do problema, sabe-se que os materiais e produtos sustentáveis são apenas uma parte da discussão da temática ambiental e conhecer como quantificá-los é parte importante da questão. Dentre as formas de quantificação, existe a avaliação pelo sistema Eco-audit, ferramenta que avalia a emissão de CO2 e o consumo de energia no ciclo do produto em uma forma ampla e integrada, Figura 2.
A avaliação completa do impacto ambiental para um determinado produto é composta pelas seguintes variáveis: o fator do material no componente, a manufaturabilidade, o uso em campo, as variáveis logísticas “supplier chain”, e ao final, o equacionamento e retorno por reciclabilidade no final de vida (End of life-EoL) ou o indesejado “disposal”.
Cada etapa tem um peso no resultado do impacto
Figura 2. Integração do total de emissão de CO2 e consumo de energia no ciclo de vida de um produto (https://www.ansys.com/products/materials/granta-edupack).
ambiental e conhecer os itens de maiores criticidades é fundamental para uma intervenção imediata.
Avançando no cerne da questão, entende-se que especificar um material com menor dano ambiental já é uma tarefa difícil; porém, pretende-se selecionar o fornecedor com melhor desempenho ambiental. A manufaturabilidade da peça e do veículo estão sob controles das áreas de processo e escolher caminhos mais limpos é uma tarefa contínua, sejam eles nas operações in-house, sistema de montagem, revestimentos e logísticos.
O cálculo da operação logística é simples, definir o tipo de transporte, combustível ou propulsão e as variáveis de trajetos e localidades são facilmente equacionados. Neste sentido, ter fornecedores próximos, evitar viagens longas e complexas são fatores fundamentais.
A variável uso do veículo tem um peso e importância fundamental, e é neste campo que as alternativas eletrificadas ganham de longe aos motores de combustão interna. Motorização alimentadas apenas com baterias e se possível, ainda ter uma recarga de energia por meios “limpos” são as melhores situações.
Nestas primeiras etapas, apenas avaliou-se a geração de CO2 e consumo de energia na industrialização do produto; a última etapa do Eco-audit é um contraponto ao estudo, isto é, o ciclo final de vida (EoL) envolvendo o descomissionamento, reciclagem e reuso de componentes; todos esses entrarão como créditos positivos na equação geral, e este campo será um importante requisito do MOVER. Nesta parte, conhecer materiais com melhores potenciais de reciclagem e facilidade no descomissionamento são pontos de maiores interesses. Na maioria das vezes, esta etapa não é contabilizada e nem existente e o final de vida é feito por “disposal”, gerando emissão de CO2 e consumo de energia, ou seja, trata-se de rejeitos para destruição, queima e outras etapas “sujas” ao meio.
Nota-se até aqui que, a integração individual das cinco variáveis anteriores compara o impacto ambiental de cada fase no produto e por isto, abordar diretamente o(s) item(s) com maior potencial e participação na geração de CO2 ou consumo de energia é fundamental para obter melhores resultados, sejam eles contidos no material, na manufatura, logística, no uso e “disposal” e na geração de créditos no ciclo final de vida do componente / produto.
O desenvolvimento de um novo veículo e as etapas de sua comercialização detém a maior parte das variáveis desta situação ambiental; os melhores caminhos de aplicar
materiais e processos sustentáveis a partir da escolha da especificação e a rota de produção estão na mão do engenheiro de materiais juntamente com o engenheiro de produto. Para exemplificar um caso comum de componente veicular, cito o braço de controle da suspensão (conceitos em alumínio, aço ou ferro fundido), que pode ser feito pelos processos de forjamento, fundição ou estampado-soldado. Todos anteriores já com aplicação em veículos; mas a questão remete no dilema: “qual rota escolher?”. Certamente, a decisão muitas vezes busca experiências anteriores em produtos conhecidos, tecnologias já estabelecidas e influências de fornecedores estratégicos na visão da empresa; porém, sendo pragmáticos e evoluirmos nesta discussão, pensa-se em projetos novos onde o engenheiro decidiria pela melhor rota ambiental para o produto.
A construção de uma peça fundida segue uma série de etapas, desde a compra das matérias primas, insumos, processos e equipamentos de fundição, tratamentos térmicos e usinagens; a decisão pelo maior uso de materiais reciclados ao processo está na mão dos sistemistas (tiers), em vista dos limites especificados nas normas de desenho do produto. Interessante, mas os provenientes de forjamento também têm etapas similares; porém, ainda depende da compra do aço de uma usina de produtos longos, o qual, neste caso, remete aos processos da aciaria da matéria-prima, onde a decisão do uso de reciclados está dentro da própria usina. Já na linha de estampados-soldados, as etapas são bem diferenciadas pelo caráter de uso de chapas de aço provenientes de uma rota de fabricação da usina de produtos planos, as relacionadas a metalurgia básica do Alto-Forno com emprego do carvão mineral; os processos de estampagens, tipo e equipamentos de soldagem, materiais de adição e usinagem também são etapas de interesses na avaliação ambiental.
Diante de tantas variáveis, a maioria dos engenheiros não consegue avaliar comparativamente a rota de processo mais “verde”. Certamente, esta situação é nova e desconhecida aos setores industriais e temos muito para aprender. O tema “materiais sustentáveis” é tão atual que estamos apenas iniciando um conceito pouco explorado até recentemente, que deve ser um dos “drives” de conhecimento do engenheiro do futuro. Quantificar emissão de CO2 e consumo de energia para cada componente e integrá-los em uma matriz de “business” passarão a ser atividades curriculares.
Como proposta de regulamentação a médio prazo, será exigido das usinas, produtores e sistemistas o relatório ambiental nos Escopos 1, 2 e 3 (GHG, Protocol, Greenhouse Gas Control) na contratação de um novo produto; exemplo das auditorias de empresas credenciadas, como a “Ecovadis” (https://ecovadis.com/, Figura 3), que classifica a sustentabilidade empresarial e assim, decidirmos nas melhores opções de materiais e processos para o veículo. Não será uma etapa fácil; mas, necessária para evoluirmos em busca das melhorias ambientais, apesar de que muitos fornecedores tratem o tema como confidencial por acreditarem que estes dados são fundamentais para sigilo do negócio.
Nestes últimos anos está ocorrendo uma avalanche de ideias e estratégias intensificando as tratativas de sustentabilidade, muitas delas relacionadas a eventos públicos e outras estratégicas de governo, como o recente ocorrido entre o governo Americano (World Economic Forum) e o Brasileiro com as grandes empresas do setores de aço e alumínio, onde o foco principal foi alavancar as propostas pelo fomento de recursos não reembolsáveis (First Movers Coalition, 9-11 October 2023, São Paulo, Brazil).
Concluindo, diferentemente de anos anteriores; hoje, eu já aposto que muita coisa será possível atingir em um curto espaço de tempo. Incrível, mas já está acontecendo!
Uma das atividades oferecidas aos participantes dos diversos seminários integrantes do II Congresso Processos Térmicos realizado em Campinas SP no final de Março 2024, foram as visitas técnicas a empresa da região. Realizadas no dia seguinte ao final do evento, várias vans levaram participantes para visitas a empresas como Combustol Fornos, Inductotherm, GKN, CTI Renato Archer, CNPEM
“Sirius” e Steel Tech
O grupo de participantes do congresso que visitou a Combustol Fornos situada em Jundiaí foi recepcionado pelos diretores da empresa, Aparicio Freitas e Donizetti Ribeiro. O grupo foi encaminhado à área de reuniões e eventos da empresa onde depois de um café
de boas vindas foi apresentado vídeo de sua história e linha de atuação.
Posteriormente o grupo percorreu as instalações da empresa, visitando tanto a área administrativa, com destaque para a engenharia, como a área fabril. Iniciando pela área de montagem elétrica de painéis e de fabricação de resistências. Na sequencia foram visitadas a área de usinagem de partes e peças de fornos e da área de pintura (foto).
A Combustol Fornos começou como Engefor em 1986 na Vila dos Remédios, na cidade de São Paulo/ SP. Depois de 20 anos de existência, em 2008 mudouse para as instalações atuais em Jundiaí, prédio próprio.
Em Abril de 2013 a Engefor foi adquirida integralmente pelo grupo Seco Warwick da Polonia e passou a se chamar Seco Warwick do Brasil. Desde 2016, o Grupo Combustol & Metalpó incorporou as operações nacionais da SECO/WARWICK e conta com parceria tecnológica e de negócios firmada com a multinacional, que também é referência mundial no mercado de fornos industriais, ampliando ainda mais a gama de produtos e de serviços.
A incorporação da Seco Warwick do Brasil/Engefor a Combustol Fornos continua trazendo frutos com a fabricação local de equipamentos na área de brasagem bem como na área de tratamento sob vácuo com diversas instalações e fabricação local além de pleno atendimento de assistência técnica e suporte local aos clientes nacionais.
Nestes últimos 7 anos de período pós incorporação houve significativos fornecimentos em diversos segmentos do mercado industrial de tratamento térmico e aquecimento industrial impulsionando a atividade da empresa, aumentando seu número de colaboradores, criando talentos. Além de consolidar conhecimento e experiencia acumulada em mais de 60 anos de atividade no mercado nacional e sul-americano com recentes exportações para Argentina, Chile, Peru entre outros. Mesmo em períodos de Covid houve solidez financeira da empresa que soube administrar as encomendas em fabricação na época e superar, com facilidade, aquele período.
Voltando à visita técnica, após percorrerem os diversos setores de fabricação os visitantes chegaram à área de montagem de fornos. Abaixo foto de recente degreaser contínuo fornecido em conjunto com Afterburner para processamento conforme regulamentos ambientais. Segue a respectiva curva de processo
A respectiva curva de processo
A Inductotherm Group Brasil agradece sua visita! Foram três dias de evento e superaram as expectativas. Apresentando os mais novos Sistemas de Indução de alto desempenho e fontes de alimentação em ação, elevando o padrão de produtividade e qualidade. Explore nosso compromisso com a sustentabilidade por meio de nossas soluções de aquecimento verdes. Experimente como estamos reduzindo o consumo de energia, minimizando o desperdício e aumentando a eficiência para diminuir o impacto ambiental.
TS Diadema: a nova unidade de nitretação do Grupo HEF. Expertise em tratamentos termoquímicos para um futuro mais verde!
No dia 22 de fevereiro de 2024 o grupo HEF Brasil concretizou um marco histórico em sua expansão: a inauguração da TS Diadema. Contando com a linha de nitretação líquida mais inovadora e sustentável da América Latina, a TS Diadema foi projetada com base em conceitos de economia circular, como otimização de recursos, eficiência energética e reciclagem de insumos; e em tecnologias digitais, como monitoramento real time controle de parâmetros do processo, otimização de ciclos e produtividade.
A HEF investiu mais de R$ 15 milhões na construção da linha da TS Diadema, instalada em um galpão de 1250 m² e tendo 40 metros de comprimento. Ela conta com um sistema computadorizado in cloud de supervisão para monitoramento, controle e registro de todos os parâmetros de processo (temperaturas, tempo de permanência em cada estação, etc.) real time. Também serão instalados sistemas eficientes de exaustão, modernos equipamentos de resfriamento e um sistema de gerenciamento de águas que vai viabilizar a reciclagem dos sais, que serão reutilizados na própria linha.
Atualmente, a nova planta conta com dois fornos de nitretação, tendo previsão de ampliação em mais um forno. Cada um tem capacidade para tratamento de 250 toneladas de peças/mês, totalizando uma capacidade anual para tratamento de 9.000 toneladas. O espaço também conta com salas dedicadas a tratamentos pós-nitretação, como polimentos e tribo-acabamentos, que adequam as superfícies dos componentes aos padrões tribológicos especificados, de acordo com o propósito de cada aplicação.
“É uma linha de nitretação líquida (em banhos de sais) completamente diferente do que temos visto no Brasil já há alguns anos”, diz Danilo Assad Ludewigs, diretor geral da HEF Durferrit do Brasil. De acordo com o executivo, já faz algum tempo que a nitretação líquida tem sido injustamente taxada como uma tecnologia poluente e, por isso, tenderia a deixar de existir no futuro. “Porém, a realidade global é outra. Principalmente na Europa, na Ásia e na América do Norte, esta é uma tecnologia em grande expansão, pois além de suas já consagradas vantagens técnicas e de custo, estes locais contam com linhas de nitretação modernas, controladas por computador, com sistemas rastreáveis, utilização de matérias primas isentas de substâncias CMR, NOx e VOCs, e reciclagem de sais, muito mais sustentáveis e ecológicas até mesmo do que outros processos apontados como mais limpos, como o de nitretação gasosa, por exemplo. A linha da TS Diadema vai ser montada dentro deste conceito moderno e sustentável”, detalha Ludewigs.
“Vamos em breve agregar também a esta linha outras tecnologias digitais e de dados que já estão sendo testadas na matriz na França há algum tempo, inserindo-nos definitivamente na era da indústria
4.0. Todas essas inovações deverão muito em breve configurar o novo padrão brasileiro de tecnologias de banhos de sais. Com certeza, nós vamos revolucionar o mercado de nitretação nacional e beneficiar diversos setores da indústria”, afirma Ludewigs.
Veja em primeira mão, como foi nosso evento:
Ao longo do evento, diversos parceiros de negócios prestaram depoimento a respeito da tecnologia de nitretação CLIN:
“A CIP busca soluções para resolver problemas de desgaste e atrito de seus parceiros industriais, sendo a sustentabilidade requisito essencial para nossos fornecedores. A TS Diadema tem o nível de excelência ambiental requerido para desenvolvimentos de superfície com a CIP.”
Vitor Facciolla – diretor administrativo-financeiro da CIP
“A tecnologia CLIN de nitretação da HEF é candidata a minimizar desgaste, aumentar resistência à fadiga, garantindo durabilidade e eficiência a sistemas de valvetrain/powertrain. A CUMMINS busca emissão zero em toda a sua cadeia produtiva e a TS Diadema se enquadra nesse conceito.”
Renan Barro – gerente de engenharia da CUMMINS
“A ENGRECON tem uma série de componentes de transmissão que solicitam nitretação com requisitos metalográficos bem rígidos. A tecnologia CLIN atende com excelência tais especificações, além de possibilitar uma cadeia de serviços sustentável. Sustentabilidade não é modismo, é uma necessidade.”
Arivaldo Cardoso – gerente industrial da ENGRECON
“Tratamento térmico é um processo extremamente técnico. Porém, além da excelência é necessário garantir um processo ecológico e competitivo aos clientes. A TS Diadema, com a sua tecnologia CLIN de nitretação é capaz de garantir qualidade, excelência e sustentabilidade a seus parceiros de negócios, se tornando uma empresa única e de grande destaque no mercado nacional”
Emerson Bertaglia de Paula – engenheiro de materiais da MAGNETI MARELLI
“O setor automotivo necessita de novas tecnologias e a TS Diadema se enquadra como uma oportunidade tecnológica (digitalização e controle das variáveis do processo), ecológica (conceitos de economia circular com reutilização e redução de consumíveis, reciclagem e descarbonização) e de excelência para satisfazer os requisitos mecânicos da mobilidade nacional.”
Marco A. Colosio – gerente de engenharia e diretor regional SAE Brasil
“O Sindipeças é um difusor de conhecimento do mercado de mobilidade nacional. A TS Diadema, associada do Sindipeças, com sua expertise em tratamentos de superfície, promove a difusão de conceitos de economia circular e digitalização de seu processo de nitretação CLIN. É gratificante alinhar conhecimentos de mercado e técnicos para contribuir com o desenvolvimento da indústria automotiva.”
Francisco A. Marianno – chefe de marketing do SINDIPEÇAS
“A Tramontina preza pela excelência em seus produtos. A TS Diadema, com seu time de especialistas em tratamentos termoquímicos, é capaz de prover todo o suporte técnico e comercial para desenvolvimentos de tecnologias de superfície em bens de consumo. A sustentabilidade é mandatória para o fortalecimento da parceria entre Tramontina e TS.”
Samyr Ismail – supervisor metalúrgico da TRAMONTINA
“O desenvolvimento de um processo de superfície sustentável é mandatório para o presente/futuro dos componentes da Parker. A TS Diadema, por apresentar uma linha tão sustentável e digitalizada, oferece ao mercado hidráulico uma alternativa ao cromo duro: a tecnologia CLIN de nitretação. Parceria que está revolucionando conceitos de superfície para um futuro mais verde.”
Denis Sarmento – gerente de engenharia da PARKER HANNIFIN
“A TS Diadema revoluciona o mercado de tratamentos térmicos/termoquímicos nacional, apresentando conceitos inovadores, como a digitalização de todas as etapas do processo de nitretação, a redução/reutilização de consumíveis, a eficiência energética e a reciclagem de matéria prima. Essas características fazem com que a TS seja pioneira nesse mercado com a diretriz de Waste To Zero Generation.”
Udo Fiorini – CEO do Grupo Aprenda
Venha conhecer a TS Diadema! Expertise em tribologia e engenharia de superfície para um futuro mais verde.
O evento de inauguração da TS Diadema foi um marco para o mercado de tratamentos térmicos/ termoquímicos nacional. O grupo HEF expressa sua extrema gratificação a todas as empresas, imprensa e órgãos renomados participantes, dentre os quais ABM; BSB ROLAMENTOS; BTM BRASAGEM; CBMM; CIP; CONSULAT G. FRANCE À SP; CUMMINS; ENGEMET; ENGRECON; GM; GRUPO APRENDA; IPEN; KNORRBREMSE; MAGNETTI MARELLI – SUSPENSÕES; SCHAEFFLER; SINDIPEÇAS; STABILUS; TENNECO; TRAMONTINA; USP.
Horário: 8h às 17h
30 e 31 de Outubro de 2024
31 de Outubro de 2024 - Visita a Villares Metals
Incluso: - Brunchs - Coffee Breaks
- Visita Técnica a Villares Metals * Uso obrigatório de sapatos de segurança Mídia Oficial: Patrocínio Ouro: Realização:
Arvind Thekdi
Obs: Este artigo foi originalmente publicado em 4 partes na edição americana da revista Industrial Heating durante o ano de 2023. A primeira parte, traduzida, foi publicada no Brasil na edição de Junho 2023 da revista Industrial Heating Brasil. Esta revista foi descontinuada nos EUA e também no Brasil, sendo substituída pela presente Revista Aquecimento Industrial onde passaremos a publicar as partes faltantes.
Os sistemas de aquecimento de processos industriais fornecem o calor necessário para produzir bens utilizados pelos consumidores e pelas indústrias. O calor é fornecido principalmente a partir de combustíveis, vapor e eletricidade utilizados em diversos tipos de equipamentos de aquecimento, como fornalhas, fornos, aquecedores e estufas.
Este artigo – parte 2 de uma série de 4, descreve os diferentes tipos de sistemas de aquecimento de processo utilizados pelas indústrias, as emissões de CO2 destes sistemas e possíveis caminhos para alcançar emissões líquidas de carbono zero, com citação de alguns exemplos.
Gases de Efeito Estufa (GEE)
Uma grande percentagem das emissões de CO2 nas operações de produção provém diretamente da combustão
de combustíveis utilizados em equipamentos de aquecimento de processos ou indiretamente da geração de vapor e eletricidade. A Tabela 3 apresenta uma lista de emissões de CO2 provenientes da combustão de combustíveis em fornos e caldeiras.
A emissão de CO2 gerada pela combustão depende do teor de carbono do combustível e da quantidade de oxidante, geralmente ar ambiente ou oxigênio, utilizado para a combustão. Qualquer quantidade de ar de combustão igual ou superior ao ar estequiométrico (excesso de ar) resultaria em uma quantidade fixa de CO2 expressa em libras de CO2 por MM BTU de calor liberado durante o processo de combustão. Os métodos de poupança de energia normalmente recomendados – como a redução ou o controle do excesso de ar, a utilização do pré-aquecimento do ar de combustão, o enriquecimento do ar de combustão com
oxigénio ou a utilização da combustão de oxicombustível –não têm um efeito direto no CO2 gerado pela combustão. Contudo, a utilização de qualquer uma destas etapas resultaria em economias de energia e redução do uso de combustível por unidade de produção, resultando numa redução nas emissões de CO2 por unidade de produção do equipamento de aquecimento de processo. Portanto, qualquer uma destas ações ou outras medidas de poupança de energia normalmente recomendadas poderiam resultar na redução das emissões totais de GEE de uma instalação.
Processos que utilizam vapor e eletricidade como fonte de calor não possuem emissão direta de CO2 no local onde o equipamento de aquecimento é utilizado. Contudo, a produção de vapor e de eletricidade gerada em centrais alimentadas a combustíveis fósseis emite CO2
no local de produção. A contabilização da descarga de CO2 de sistemas aquecidos a vapor requer consideração do conteúdo total de calor do vapor utilizado, do tipo de combustível utilizado nas caldeiras e da eficiência do sistema de geração de vapor.
Por exemplo, a emissão de CO2 de um sistema aquecido a vapor que fornece 1 MM de calor de BTU a um processo e é derivado de uma caldeira a gás natural com eficiência de 85% teria 135 libras de emissão de CO2 por MM de calor de BTU fornecido pelo vapor. Também é necessário considerar as perdas de calor provenientes da distribuição de vapor, do retorno de condensado e do equipamento de aquecimento do processo quando se considera a emissão de CO2 associada ao equipamento de aquecimento.
Os cálculos da emissão de CO2 de um sistema aquecido eletricamente podem ser um pouco mais complicados porque é necessário considerar a fonte de eletricidade. De acordo com a Agência de Informação de Energia dos EUA (EIA - Energy Information Agency), a emissão média de CO2 em 2020 foi de cerca de 0,85 libras por kWh para todo o país. Isto representa a produção de eletricidade de todas as fontes mencionadas neste artigo. A emissão real de CO2 de um processo de aquecimento depende da eficiência do uso da eletricidade.
Por exemplo, um sistema de indução que utilize 10.000 kWh de energia elétrica para fundir ferro ou alumínio com 70% de eficiência térmica global teria 12.140 libras de emissões de CO2 por hora. Em muitos casos, as emissões de CO2 por kWh para a produção de eletricidade no local que utiliza calor e eletricidade combinados (CHP - Combined Heat and Power) ou cogeração podem ser substancialmente inferiores ao valor médio nacional.
A maioria dos sistemas de aquecimento nos EUA
utiliza gás natural, que apresenta as taxas de emissão de CO2 mais baixas, como combustível. As emissões de CO2 de um sistema movido a combustível não são afetadas pela quantidade de excesso de ar utilizado ou pela temperatura dos gases de escape. No entanto, a utilização de medidas de conservação de energia – tais como a redução do excesso de ar, a utilização de sistemas de recuperação de calor residual e o funcionamento eficiente através de melhores controles – reduz o consumo de energia por unidade de produção e, correspondentemente, reduz as emissões de CO2. Se a combustão for subestequiométrica (queima rica), as emissões de CO2 serão menores. No entanto, os produtos de combustão contêm CO, H2, etc.
As emissões de dióxido de carbono são geradas a partir de vários sistemas utilizados nas fábricas. A Figura 2 mostra as principais áreas de uso de energia na fabricação e as emissões de CO2 dessas áreas, que incluem geração local de vapor e eletricidade, uso de energia de processo e uso de energia não processual. Uma análise mais detalhada dessas
Emissões de Combustíveis e GEE (CO2e) – 2018 (MM Toneladas)
Todos os setores industriais
três áreas principais e das emissões de CO2 das fábricas dos EUA em 2018 também é mostrada na Figura 2.
O vapor e a eletricidade gerados no local podem ser usados para aquecimento de processos em sistemas aquecidos eletricamente, sistemas aquecidos a vapor ou outros sistemas. A eletricidade e o vapor adquiridos no exterior (mostrados fora da linha limite da fábrica) não estão incluídos nesta discussão, mas contribuem indiretamente para as emissões de CO2 associadas às operações de fabrico. Estas emissões adicionais de CO2 são de 385 milhões de toneladas e quase 50% das emissões geradas no local.
Além do fornecimento de energia ou das emissões de GEE relacionadas com a combustão, alguns processos térmicos produzem emissões de GEE que resultam de reações químicas ou da decomposição de produtos como o carbonato de cálcio (calcário) na produção de cal. Isto é relatado como parte das emissões de CO2 provenientes do uso de energia de processo. O processo de descarbonização requer abordagens diferentes para cada categoria.
Sistemas Geradores de CO2
De acordo com a Agência de Informação de Energia (EIA) do Departamento de Energia (DOE - Department
of Energy), o total de emissões de CO2 das operações de fabricação (1.165 toneladas/ano) foi de cerca de 20% do total de emissões dos EUA (5.742 toneladas/ano) em 2018. As emissões totais de CO2 dos processos de fabricação são mostradas em 3. Observe que as emissões de CO2 resultantes de sistemas de combustão utilizados para aquecimento de processo representam 38% do total de emissões de CO2, enquanto o CO2 gerado pelo processo que se origina dos materiais processados dentro do equipamento de aquecimento representa 23% do total. Portanto, 61% do total de emissões são provenientes de equipamentos de aquecimento de processo utilizados nas fábricas. Exemplos de CO2 gerado por processos incluem a calcinação de calcário na indústria de cimento e reformadores utilizados em operações de refinação de petróleo. Eles não podem ser eliminados apenas pela substituição de combustíveis. Eles precisam de tecnologias como captura, armazenamento ou transformação de carbono ou substituição das matérias-primas do processo e mudanças nas rotas do processo.
As emissões de CO2 relatadas na Figura 3 provêm de centenas de sistemas de aquecimento – pequenos e grandes – cada um com requisitos de processo, projeto do
Categoria 1
Sistema de aquecimento com emissão de GEE gerada pela combustão
Exemplos: Fornos a combustível que utilizam queimadores acionados diretamente ou em tubos radiantes para aquecimento de metais/ não metálicos, fusão de metais ou vidros, caldeiras de vapor ou água quente, aquecedores a queimador, estufas, fornos de cimento, etc.
equipamento e procedimentos operacionais únicos. Embora a maior parte das emissões sejam provenientes de sistemas alimentados a gás natural, incluem combustíveis como combustíveis gasosos manufaturados (gás de coqueria, gás de alto-forno, gases de refinaria), combustíveis líquidos, carvão e outros combustíveis sólidos. É um enorme desafio analisar e desenvolver sistemas de controlo de emissões de CO2 para cada tipo de processo ou equipamento de aquecimento. Contudo, quando consideramos a origem das emissões de CO2 e as opções para as reduzir ou eliminar, é possível agrupá-las em quatro categorias – cada uma com um padrão semelhante de produção de CO2.
Dependendo da fonte de geração de CO2, do tipo de sistema de aquecimento utilizado e dos requisitos específicos do processo, os sistemas geradores de CO2 podem ser classificados em quatro categorias.
Categoria 1: Sistema de Aquecimento Apenas com Emissões de GEE Geradas por Combustão Neste tipo de sistema (Fig. 4), o calor é fornecido por um queimador convencional a combustível localizado em um forno ou indiretamente por um tubo radiante ou mufla, que é aquecido por um queimador a combustível.
Esses combustíveis contêm carbono e hidrogênio, e sua combustão ou reação de oxidação produz calor e produtos de combustão que contêm principalmente CO2, H2O, N2
e O2 com vestígios de combustíveis e SO2 se o combustível contiver enxofre. Os gases de combustão quentes produzidos pela combustão estequiométrica ou por excesso de ar são descarregados diretamente de um forno ou após tratamento dos gases de combustão, resultando na emissão de CO2 na atmosfera.
A transferência de calor dos produtos de combustão ocorre principalmente por convecção com alguma radiação da chama ou produtos de combustão que contêm CO2 e H2O. Para fornos de alta temperatura (>760°C), a radiação térmica dos produtos de combustão pode ser responsável por uma parte significativa do calor total transferido para o material que está sendo aquecido. As considerações de transferência de calor desempenham um papel muito importante no caso de métodos alternativos de fornecimento de calor, como o aquecimento eléctrico, quando pode ser utilizado para eliminar o CO2 gerado pela combustão. A grande maioria dos processos de aquecimento industrial enquadra-se nesta categoria.
Categoria 2: Sistemas de Aquecimento Reativos que Utilizam Material Carbonáceo como Fonte de Calor
Neste tipo de sistema (Fig. 5), combustíveis como carvão ou coque metalúrgico ou de petróleo são misturados ou reagem com uma fonte de oxigênio (ar ou oxigênio
Categoria 2
Sistema de aquecimento reativo usando material carbonáceo para calor e reações
Exemplos: Alto-forno, forno de cúpula ou forno de sinterização utilizando carbono misto para reação e geração de calor.
puro) para produzir calor por combustão completa ou, mais frequentemente, parcial. Os produtos de reação, como CO e H2, são usados como agentes redutores ou reagentes para as reações químicas necessárias. O calor gerado pela combustão é usado para aumentar e manter a temperatura de reação necessária do material que está sendo processado.
Um bom exemplo disso é a fusão de ferro em cúpulas ou a redução de minério de ferro em altos-fornos. Neste caso, a utilização de combustível não carbonáceo ou de um sistema de aquecimento alternativo (tal como um dos métodos de aquecimento elétrico) ainda requer a utilização de um agente redutor ou de cementação alternativo para o processo. O fluxo de gases de escape contém uma mistura de gases contendo CO2, CO, H2, N2 e gases combustíveis que são usados como combustíveis de baixo valor calorífico em processos posteriores. Esses processos são utilizados na indústria química, nas refinarias de petróleo e na indústria de papel e celulose. Os gases com componentes combustíveis (como H2, CO ou outros hidrocarbonetos) são utilizados como combustível em outros sistemas de aquecimento, como fornos, geradores de vapor, turbinas a gás, ou simplesmente incinerados resultando na descarga de CO2 na atmosfera.
Categoria 3: Sistemas de Aquecimento que Utilizam Combustíveis e Matérias-Primas
Carbonáceas
Neste tipo de sistema (Fig. 6), a combustão de combustíveis carbonáceos é utilizada para elevar a temperatura dos materiais que estão sendo processados. A uma determinada temperatura o material “se decompõe” e libera CO2. Um bom exemplo disso é a produção de cal em forno. Neste caso, o calcário (CaCO3) é aquecido a 1.450°C usando o calor da combustão do combustível quando o CO2 é liberado da calcinação do calcário. Este CO2 é misturado com produtos de combustão e outros gases e sai do sistema de aquecimento (forno, neste caso) como gás de exaustão. O CO2 gerado pela combustão pode ser reduzido ou eliminado usando combustíveis com baixo teor de carbono ou não, mas o CO2 produzido a partir do processo de calcinação não pode ser eliminado. Neste tipo de processo, o CO2 tem de ser capturado e convertido ou armazenado mesmo quando o calor é fornecido por uma fonte alternativa que não produz CO2.
Categoria 4: Sistemas de aquecimento onde combustíveis à base de carbono são usados como matéria-prima para produzir um reagente alternativo ou outro tipo de mercadoria
Alguns exemplos desse tipo de sistema (Fig. 7)
Categoria 3
Sistema de aquecimento utilizando combustíveis e matérias-primas carbonáceas
Exemplos: Fornos de produção de clínquer na indústria de cimento, fornos de cal, vasos de reação, certos reformadores, etc.
incluem a produção de coque metalúrgico e de petróleo, ânodos e cátodos de carbono usados na indústria de alumínio e eletrodos de grafite usados em EAFs. Esses sistemas produzem CO2 a partir de duas fontes: do sistema de combustão utilizado para fornecer o calor do processo para aumentar a temperatura do produto e dos gases voláteis liberados do material que está sendo aquecido ou processado.
A eliminação do CO2 gerado pela combustão requer o uso de combustíveis não carbonáceos. Neste caso, a utilização de aquecimento eléctrico, particularmente aquecimento por resistência ou indução, não é prática devido ao ambiente de trabalho, que contém vapores condensáveis e inflamáveis e pode encurtar a vida útil dos componentes do sistema de aquecimento. A emissão do material volátil e dos gases libertados pelo material a ser aquecido não pode ser evitada. Esses gases de exaustão do lado do processo podem ser usados como matéria-prima na produção de produtos químicos ou como combustível em outros processos. Neste último caso, o processo de combustão produzirá CO2, que deve ser tratado para evitar emissões de CO2.
Em alguns casos, os voláteis liberados do produto reagem com o ar pré-aquecido dentro do forno ou reator, resultando na combustão parcial de voláteis e calor que pode atender às necessidades de calor do processo.
Neste caso, deve ser utilizado algum método de captura de CO2 para evitar emissões de CO2. É necessário ter um sistema de aquecimento externo para aumentar a temperatura do material na condição de inicialização, e as emissões de CO2 durante a inicialização precisam ser capturadas.
Categoria 4: Sistemas de Aquecimento onde Combustíveis à Base de Carbono são Usados como Matéria-Prima para Produzir um Reagente Alternativo ou Outro Tipo de Mercadoria
Alguns exemplos desse tipo de sistema (Fig. 7) incluem a produção de coque metalúrgico e de petróleo, ânodos e cátodos de carbono usados na indústria de alumínio e eletrodos de grafite usados em fornos elétricos a arco (EAFs - Electric Arc Furnaces). Esses sistemas produzem CO2 a partir de duas fontes: do sistema de combustão utilizado para fornecer o calor do processo para aumentar a temperatura do produto e dos gases voláteis liberados do material que está sendo aquecido ou processado.
A eliminação do CO2 gerado pela combustão requer o uso de combustíveis não carbonáceos. Neste caso, a utilização de aquecimento elétrico, particularmente aquecimento por resistência ou indução, não é prática
Categoria 4
Sistema de aquecimento onde combustíveis à base de carbono (carvão, hidrocarbonetos, etc.) são usados como matéria-prima
Exemplos: Pirólise de carvão/coque para produzir produtos químicos, produtos industriais de carbono (ou seja, carvão ativado), etc., usados por metais, produtos químicos e outras indústrias
devido ao ambiente de trabalho, que contém vapores condensáveis e inflamáveis e pode encurtar a vida útil dos componentes do sistema de aquecimento. A emissão do material volátil e dos gases libertados pelo material a ser aquecido não pode ser evitada. Esses gases de exaustão do lado do processo podem ser usados como matéria-prima na produção de produtos químicos ou como combustível em outros processos. Neste último caso, o processo de combustão produzirá CO2, que deve ser tratado para evitar emissões de CO2.
Em alguns casos, os voláteis liberados do produto reagem com o ar pré-aquecido dentro do forno ou reator, resultando na combustão parcial de voláteis e calor que pode atender às necessidades de calor do processo. Neste caso, deve ser utilizado algum método de captura de CO2 para evitar emissões de CO2. É necessário ter um sistema de aquecimento externo para aumentar a temperatura do material na condição de inicialização, e as emissões de CO2 durante a inicialização precisam ser capturadas.
Desde 1944, a Villares Metals reafirma seu papel como referência global em soluções de aços e ligas especiais, unindo tradição, inovação e uma cultura de parceria e colaboração que agrega valor aos clientes, aos parceiros e à sociedade. Com visão atualizada e voltada ao futuro, impulsionamos a transformação industrial nacional e global, promovendo sustentabilidade e avanço constante do país.
Para entregar qualidade aliada com responsabilidade ambiental e social, investimos em tecnologia de ponta e práticas sustentáveis
Comprometidos com a excelência operacional, nossos processos são certificados por rigorosas normas internacionais.
Priorizamos segurança e desenvolvimento tecnológico, reduzindo perdas e acelerando ganhos com digitalização de processos e automação industrial.
/company/villares-metals
Quase todos os processos térmicos utilizados na indústria podem ser classificados em uma dessas quatro categorias. A Tabela 4 mostra exemplos de onde alguns dos processos térmicos comumente usados se enquadram nessas quatro categorias. Os processos mencionados aqui são apenas alguns exemplos de muitos processos utilizados na fabricação, e cada um deles deve ser avaliado considerando os requisitos do processo, os sistemas de aquecimento atualmente utilizados e outras características do processo, conforme descrito em uma das quatro categorias. Os métodos de descarbonização para cada processo devem ser selecionados com base nas considerações discutidas na terceira parte desta série.
Este artigo terá sequencia com a Parte III na próxima edição desta Revista Aquecimento Industrial Para mais informações: Arvind Thekdi é presidente da E3M Inc., que fundou há 22 anos, em Gaithersburg, Md. EUA. Ele tem mais de 55 anos de experiência em combustão, melhorias de eficiência energética, redução de emissões e recuperação de calor residual em sistemas de aquecimento industrial. Ele pode ser contatado em arvindthekdi@gmail.com
Hoje, celebramos com nosso legado e nos preparamos para mais décadas de sucesso, em que atuaremos com dedicação e paixão para seguirmos forjando o presente e transformando o futuro
Vinhedo Plaza Hotel
Vinhedo / SP / Brasil
Av. Independência n º 4111 - Pinheirinho
Em 2025 o Grupo Aprenda continuará reunindo seus seminários em Congressos, como já iniciado no ano de 2022. Assim estará realizando de 24 e 25 de Junho de 2025 o 4º Congresso de Conformação Metálica em auditório e salas
Seminários presenciais incluídos no programa apresentados simultaneamente em salas distintas:
Asimulação tem aplicações quase ilimitadas e revolucionou desenvolvimentos de engenharia na manufatura.
A ideia de tentativas e erros na vida real é do passado e não poderia ser legitimada pela gestão de hoje, tendo em conta o enorme custo e a perda de competitividade que daí resultaria. No entanto, a simulação, que permite aos engenheiros experimentar uma variedade de cenários num ambiente computacional simulado, tem aplicações quase ilimitadas e revolucionou os desenvolvimentos de engenharia na produção em todos os setores. A simulação ocorre em diversas etapas do processo de fabricação, desde a mineração até a linha de montagem.
Os engenheiros devem aprender com a experiência, que geralmente é adquirida no trabalho. No entanto, com a força de trabalho a enfrentar enormes perturbações devido às aposentadorias dos engenheiros mais experientes, a questão é: como é que as empresas conseguem que os novos engenheiros
se desenvolvam rapidamente e, ao mesmo tempo, lhes permitem adquirir a experiência necessária para realizarem o seu trabalho de forma eficiente? A resposta é simulação.
O software de simulação oferece o melhor compromisso entre aprendizado rápido e eficiência de custos. Os engenheiros podem testar ideias quase sem nenhum custo (além do tempo e do custo da licença), criar seu próprio banco de dados de casos para referência posterior e ganhar experiência e confiança em seu julgamento. Esperançosamente, alguma sobreposição com engenheiros experientes será garantida antes da aposentadoria, para que eles possam aprender com décadas de experiência no campo.
Este artigo propõe um estudo de caso para transformação de lingotes de grande porte utilizando um conjunto de softwares da Transvalor: THERCAST para simulação de fundição de lingotes e FORGE para transformação de metais sólidos.
O Estudo de Caso
Este estudo de caso foi desenvolvido em nosso laboratório. Embora os projetos e os parâmetros sejam semelhantes aos padrões da indústria, os dados não provêm de um caso industrial. Sugerimos investigar dois métodos de transformação de lingotes e analisar a qualidade do semiproduto após a transformação para cada método.
Após o enchimento e solidificação inicial do lingote, o lingote é reaquecido em um forno e submetido ao processo de cogging. O processo de cogging é um conjunto de manipuladores (segurando o lingote) e duas ferramentas que aplicam a deformação ao lingote. O objetivo desta transformação é geralmente obter um semiproduto para ser enviado a um cliente para futuras transformações, como forjamento em matriz fechada. O processo de cogging pode também ser usado para produtos acabados de grande porte, como grandes eixos de turbinas.
Este estudo se concentra na forma das ferramentas de cogging. O objetivo aqui é transformar um lingote em um produto redondo. Exploramos um conjunto de ferramentas em forma de V e em formato de superfície plana. Usando a mesma quantidade de deformação para cada projeto de ferramenta, queremos descobrir qual formato oferece a melhor qualidade de produto. A qualidade do produto neste caso é a redução da porosidade na linha central do lingote,
que é o típico defeito de fundição que os engenheiros tentam minimizar durante esta operação.
Outra análise na qual engenheiros e metalurgistas estão interessados é o crescimento e tamanho do grão após a transformação. Embora esta análise esteja disponível na suite de softwares da Transvalor, não nos concentraremos nesta análise neste artigo.
Descrição do Projeto
O primeiro passo é o enchimento e solidificação do lingote. O lingote escolhido pesa 1,6 toneladas e o material utilizado é 40CMD8. A Figura 1 mostra a configuração com todas as partes envolvidas na fundição: riser, molde, hot top, refratário e pó exotérmico.
Uma vez solidificado o lingote, ele é reaquecido em forno a gás antes de ser conduzido por um manipulador para a operação de cogging. As Figuras 2 e 3 mostram a descrição das ferramentas em formato V e formato plano utilizados neste estudo.
Vários golpes ocorrem durante o processo de cogging. Um golpe é o ciclo completo da ferramenta superior descendo para atingir uma altura especificada e voltando à sua posição original. Para transformar um lingote cônico de formato hexagonal em uma barra de seção redonda, uma série de rotações e deslocamentos devem ocorrer durante
Figura 4. Para o estudo, sensores de rastreamento de pontos foram colocados nas áreas de interesse, ou seja, na linha central. Esta figura mostra a posição do grupo de sensores.
todo o processo. O cogging também é descrito por uma série de passes. Neste estudo, passe é a operação completa para ir de uma extremidade à outra do lingote. Ambas as configurações foram criadas para serem comparáveis. Os parâmetros utilizados em ambos os casos são descritos abaixo:
· Número de golpes (oito para uma rotação completa)
· Ângulos de rotação (22,5 graus) e direção
· Quantidade de deformação
· Deslocamento entre golpes
· Número de passes
· Materiais
· Atrito (sem lubrificação)
· Temperatura inicial definida para 1250°C.
Executamos dois passes para este estudo de caso, indo e voltando. Além disso, colocamos alguns sensores (rastreamento de pontos) nas áreas de interesse, isto é, a linha central. A Figura 4 mostra a posição do grupo de sensores. Os sensores acompanharão a deformação do material e registrarão todos os resultados fornecidos pela simulação, permitindo uma análise minuciosa do processo.
Como esperado, os resultados da fundição mostram porosidades na linha central. As porosidades neste estudo de caso são detectadas utilizando o critério de Niyama, que é um critério muito comum utilizado na indústria. Como a parte superior e inferior do lingote são descartadas para o produto final, concentramos nosso estudo na linha central para garantir que aplicamos deformação suficiente no centro para reduzir a quantidade de porosidade.
A Figura 6 mostra a fração líquida ao final do enchimento. O azul escuro representa o metal solidificado, a cor vermelha é o líquido e quaisquer outras cores são a zona pastosa. A zona pastosa é uma mistura de sólido e líquido, começando com a formação da primeira dendrita e terminando com a zona totalmente solidificada. Demonstra que a solidificação começa bem antes do final do enchimento e que a fase de solidificação é de fato uma continuidade da fase de enchimento. A solidificação é um processo contínuo que começa assim que o líquido é despejado no molde. É essencial que o software de simulação considere isso para evitar discrepância entre a simulação e a realidade.
Figura 5. Aqui são mostradas as configurações iniciais com formato em V à esquerda e formato plano à direita.
Figura 6. Os resultados da fundição mostram porosidades na linha central. Esta figura mostra a fração líquida no final da fase de enchimento.
Resultados em Forma de V
O método em forma de V mostra uma boa quantidade de deformação no centro e uma superfície lisa no diâmetro externo. A Figura 8 mostra uma seção transversal longitudinal do lingote após dois passes com a distribuição de deformações. O azul escuro representa pouca ou nenhuma deformação, e a cor vermelha mostra a maior quantidade de deformação. A Figura 9 fornece informações sobre o nível de deformação e evolução ao longo do tempo para cada sensor posicionado na linha central do lingote. O formato em V apresenta resultados de boa qualidade em relação ao objetivo do nosso estudo, que é diminuir o nível de porosidade na linha central. O nível de porosidade é avaliado por um modelo considerando a porosidade existente e o nível de deformação recebido durante o processo de transformação do cogging. A Figura 10 mostra a avaliação da porosidade após dois passes na seção transversal longitudinal.
Resultados de Formato Plano
O método de formato plano mostra uma quantidade de deformação um pouco mais localizada na superfície do lingote transformado. A superfície também é lisa no diâmetro externo. A Figura 11 mostra uma seção transversal longitudinal do lingote após dois passes com a distribuição de deformações. O azul escuro representa um valor de deformação 0 (nenhuma deformação ocorreu nessas áreas), e a cor vermelha mostra valores de deformação em torno de 10. A Figura 12 é um gráfico da evolução da deformação ao longo do tempo na linha central onde nossos sensores foram originalmente posicionados.
O ferramental de formato plano parece sugerir que menos deformação é aplicada ao centro do lingote. Como o objetivo deste processo é reduzir a quantidade de porosidade no centro do lingote transformado, parece que o ferramental de formato plano não é o ideal. A Figura 13 fornece mais informações sobre este assunto com a informação direta
Figura 7. As porosidades neste estudo de caso são detectadas utilizando o critério de Niyama, um critério muito comum utilizado na indústria. Aqui são mostradas as análises de porosidades para este estudo.
Figura 8. O método em forma de V mostra uma boa quantidade de deformação no centro e uma superfície lisa no diâmetro externo. Esta figura mostra uma seção transversal longitudinal do lingote após duas passagens com a distribuição de deformação.
do nível de redução da porosidade. O azul escuro (0) não apresenta porosidade detectada nessas áreas, enquanto a cor vermelha (1) apresenta porosidade não reduzida, detectada inicialmente após a fundição. Qualquer cor entre o azul e o vermelho sugere algum nível de redução.
Comparação
Depois de avaliar cada método individualmente, é hora de fazer uma comparação lado a lado dos resultados e decidir qual deles atingiria melhor nosso objetivo. Como é complicado comparar todos os resultados dos sensores de uma só vez no mesmo gráfico, extraímos um sensor localizado no meio da linha central e plotamos os dois sensores no mesmo gráfico. A comparação mostra que o sensor em formato V (curva azul claro) proporciona uma melhor redução de porosidade do que o ferramental em formato plano (curva laranja).
O ferramental em formato V conseguiu uma melhor movimentação do material (deformação) na linha central do lingote. Isto é importante porque é o principal objetivo da redução da porosidade. As Figuras 10 e 13 mostram
que isso se traduz em uma melhor redução de porosidade para o ferramental em formato de V. Embora a forma plana possa certamente atingir o mesmo nível de redução que a forma em V, provavelmente exigirá mais passes do que a forma em V para obter os mesmos resultados. A adição de mais passes tem um custo significativo para a empresa – como um ciclo de forjamento mais longo para atingir o mesmo resultado, maior consumo de energia e desgaste adicional do ferramental. Isto se traduz em substituição mais frequente do ferramental, o que, em última análise, aumenta o custo geral de transformação do mesmo lingote.
A análise mostra que o formato em V se ajusta melhor. No entanto, deve-se considerar que uma ferramenta em formato de V pode exigir que uma empresa solicite um novo conjunto de ferramentas, enquanto ferramentas em formato plano podem estar disponíveis. Considerando todas essas informações, a empresa pode decidir que o custo envolvido no corte de novas ferramentas não vale a pena para um trabalho específico. Se a empresa estiver procurando uma estratégia de investimento de longo prazo com mútiplos pedidos de clientes, entretanto, uma
ferramenta em formato V faz mais sentido porque será mais econômica no longo prazo.
Conclusão
O objetivo deste artigo foi demonstrar o benefício do uso da simulação no departamento de engenharia. O caso aqui utilizado é voltado para a tomada de decisão para desenvolvimento e investimento de processos, mas essa análise pode ser feita em múltiplos níveis. A maioria das empresas utiliza a simulação para responder aos pedidos de cotação e garantir que a sua proposta é a melhor possível tendo em conta as capacidades e recursos da empresa. O tempo de desenvolvimento foi drasticamente reduzido desde a introdução do software de simulação, e quaisquer empresas que ainda não estejam equipadas com simulação estão a perder propostas para projetos, colocando os seus negócios em perigo.
Este artigo fornece um instantâneo do potencial
da simulação. O tamanho do grão e a análise da ferramenta, como tensões e temperatura, são outros resultados importantes a serem considerados e estão disponíveis por meio de simulação. Tal análise seria quase impossível de ser feita através de experimentos devido ao custo e à praticidade de tal investigação.
Softwares de simulação devem ser prioridade para as empresas. O software deve ser calibrado para os processos da empresa, mas vir com parâmetros prontos para uso imediato. As empresas ainda não equipadas devem investigar urgentemente qual software de simulação funcionaria melhor para elas e certificar-se de fornecer treinamento suficiente aos seus funcionários para que possam usar a simulação nas melhores condições e obter o máximo valor.
Para mais informações: Nicolas Poulain é CEO da Transvalor Americas Corp. (www.transvalorusa.com). Ele pode ser contatado pelo telefone +1312-219-6029 ou nicolas.poulain@transvalor.com
+55 (19) 97828-8511 vendas@sulvybrasil.com.br @sulvybrasilcoatings
www.sulvybrasil.com.br
Especialistas em soluções de alta tecnologia para revestimentos industriais em peças metal-mecânicas, que trabalham em ambientes corrosivos ou que precisam de características superficiais tais como:
Resistência Térmica
Química
à Abrasão
10º Seminário de Processos de Tratamentos Térmicos,
9º Seminário Manutenção e Segurança de Fornos Industriais,
3º Seminário Aquecimento por Indução
2º Seminário de Tecnologia da Metalurgia do Pó
2º Seminário Fusão por Indução
2º Seminário Recobrimento Industrial e Decorativo
Em 19 e 20 de março de 2024 foi realizado pelo Grupo Aprenda o 2º Congresso Processos Térmicos. O evento aconteceu na área de eventos do Hotel Nacional Campinas – Trevo e contou com a participação de mais de 200 inscritos. O Congresso teve como coordenadores técnicos em cada Seminário, realizado em salas distintas: 10º Seminário de Processos de Tratamentos Térmicos: Carlos Humberto Sartori, Gerente Técnico – Engenharia de Aplicação e Assessoria Técnica da empresa Villares Metals; 9º Seminário Manutenção e Segurança de Fornos Industriais: Ralph Trigueros sócio diretor da empresa Sulvy Coatings; 2º Seminário Metalurgia do Pó: Eduardo Nunes, Especialista em Sinterizados Aplicados na Indústria Automotiva; 3º Seminário Aquecimento por Indução e 2º Seminário Fusão por Indução: a empresa Inductotherm Group Brasil coordenou os
trabalhos; 2º Seminário Recobrimento Industrial e Decorativo teve a coordenação técnica de Udo Fiorini, Grupo Aprenda.
Key Speakers
Após a recepção e abertura com as boas vindas aos participantes do evento no auditório foi iniciada a sessão Key Speakers sendo apresentadas as seguintes palestras:
• Fabio Sant’Ana - Farcco Tecnologia - O Brasil e a Manufatura Aditiva de Metais: As Indústrias, Os Materiais e As Oportunidades
• Danilo Assad Ludewigs - HEF Durferrit - TS Diadema - Tecnologia de Nitretação Liquida Inovadora e Sustentável para a Indústria Verde do Futuro
• Giovani Verdi Cappucio – Villares Metals - Mercado Atual de Tratamentos Térmicos: a Prestação de Serviços, Perfil e Tendencias
Após a sequencia de palestras da abertura, já na sala específica do Seminário de Processos de TT, o Auditório do Hotel Nacional Inn, foram apresentadas nos dois dias do evento as seguintes palestras, sob a coordenação técnica de Carlos Sartori:
Luigi Mazzuco – SCIENCA Suporte Metalúrgico Cuidados com os Fluidos para Têmpera: Longevidade do Banho e Estabilidade de Processos
Lukasz Chwialkowski - Seco Warwick, Polonia - Heat Treatment Tools and Dies, Brings Benefits in Various Industries. Austenitizing Process According to Various Standards of NADCA, GM, FORD - “Tratamento Térmico de Ferramentas e Matrizes traz Benefícios em Diversos Setores. Processo de Austenitização de Acordo com Vários Padrões da NADCA, GM, FORD”
Carlos Sartori - Villares Metals - Explorando Casos de Falhas no Tratamento Térmico de Ferramentas
Antônio Gremes Pereira, Alexandre Trindade – GREFORTECDescarbonização no Tratamento Térmico – ESG
Lauralice Canale - USP São Carlos (Convidada SCIENCA) - Temperabilidade como um dos Fatores na Seleção do Meio de Resfriamento
Roberto Tiburcio – Villares Metals - Tratamentos Térmicos Virtuais: Estudos de Casos com Simulações Numéricas de Tratamentos Térmicos
Felipe Moreno Siqueira Borges de Carvalho – IPT - Ajustes no Tratamento Térmico de Esferoidização para Melhoria do Forjamento a Frio
Felipe Moreno Siqueira Borges de Carvalho – IPT - Desenvolvimento do Ciclo de Tratamento Térmico de um Aço Bainítico Fundido
Fernando Vieira, Inductotherm Group Brasil - FMEA de Tratamento Térmico por Indução e Aplicações
Cláudio Leitão – SUPERTRAT - Cementação e Carbonitretação - Parâmetros Teóricos e Práticos (Inclui: Microestruturas e Propriedades)
Alisson Duarte - 6Pro Virtual And Practical Process - Uso da Simulação na Análise do Tratamento Térmico dos Aços
Alexander Varhoshkov – Ionitech, Bulgária - Application and Effect of Ion (Plasma) Nitriding on Different Types of Steel Grades - “Aplicação e Efeito da Nitretação de Íons (Plasma) em Diferentes Tipos de Aços”
Lukasz Chwialkowski - Seco Warwick, Polonia - Low Pressure Carbonitriding – Heat Treatment Suited for a Sustainable Future - “Carbonitretação de Baixa Pressão –Tratamento Térmico Adequado para um Futuro Sustentável”
Oliver Bockemühl - Stange Elektronik, Alemanha - Integration of HT Process Control Data in ERP (Enterprise Resource Management) Systems for Improved Quality and Productivity - “Integração de Dados de Controladores de Processos do TT em Sistemas ERP para Melhorar a Produtividade e a Qualidade”
Bruno Nunes da Silva – UNITRAT - A Influência da Têmpera e Austempera em Itens de Segurança Automotivos
Dennis Beauchesne – ECM USA - Different Applications of Vacuum Furnaces / Processes in Modern Industry and in Scientific and Academic Development“Diferentes Aplicações de Fornos/Processos a Vácuo na Indústria Moderna e no Desenvolvimento Científico e Acadêmico
Na sala específica do Seminário de Manutenção e Segurança de Fornos Industriais, foram apresentadas nos dois dias do evento as seguintes palestras sob a coordenação técnica de Ralph Trigueros:
Márcio Boragini - UPC / Nitrex - Atmosferas Para Tratamento Térmico: Como Escolher, Controlar e Manter
Roberta Gomes - MG Instalação e Mecânica Industrial - Manutenção Preventiva em Fornos a Vácuo
Ivan Siqueira - PhoenixTM Brasil - Sistemas PhoenixTM para TUS / SAT / Perfil de Temperatura
Rodrigo Peres Granja – GREFORTEC - Como Prolongar a Vida Útil do seu Forno
Silvio de Campos Junior - Combustol Fornos - Manutenção Segura em Fornos de Atmosfera Ativa
José Benedito Pinto – TTTermicos - Pirometria e Procedimentos para TUS/SAT Conforme CQI-9
Manuel Schepp - Medenus Gas-Druckregeltechnik, Alemanha - Valves for Natural Gas with Integrated Safety Lock and Preparations for Operation and for Gas Easels - “Válvulas para Gás Natural com Trava de Segurança Integrada e Preparações para Operação e para Cavaletes de Gás”
Einar Cristofani - CONAI (Convidado Combustol Fornos) - Sistemas de Combustão a Gás – Segurança, Manutenção e Ajustes
Ademir Figueiredo - Inductotherm Group Brasil - Rotinas de Manutenção para Fornos a Indução
Este seminário teve a organização técnica efetuada por um Grupo de Trabalho composto por: Cristiano Binder, UFSC; Daniel Bayerlein, Metalpó; Daniel Rodrigues, BRATS; Eduardo Galvani, Hoganas; Eduardo Nunes, Especialista MP; Ana Luiza Queiroz, Hoganas; Antonio Carlos, FACENS; Henrique Rodrigues Oliveira, ISI/SC; Ronaldo Pegorer, Consultor PM / Eltro; Udo Fiorini, Grupo Aprenda.
Na sala específica do Seminário da Metalurgia do Pó, foram apresentadas nos dois dias do evento as seguintes palestras sob a coordenação técnica de Eduardo Nunes sendo a programação dividida em Macro Temas e Painéis Técnicos:
Macro Tema: Aplicadores da Manufatura Aditiva
Moderadores: Daniel Bayerlein / Henrique Rodrigues Oliveira
Piter Gargarella – UFSCAR - A Manufatura Aditiva de Biomateriais Metálicos no Brasil
Lucas Salomão Peres – CBA - Explorando o Potencial do Alumínio na Manufatura Aditiva
Cristiane Gonçalves – Villares Metals - Aplicações da Manufatura Aditiva na Indústria de Ferramentais
Macro Tema: Produtor de Pós Metálicos
Moderadores: Eduardo Galvani / Ana Luiza Queiroz
Alaércio Vieira – MEXTRA - Ferro Titânio para Soldagem, Catálise e Metalurgia do Pó
Luis Simões / Ana Queiroz – Hoganas - Pós Metálicos: Processos Produtivos Versus Aplicação
Jörg Fischer-Bühner - Blue Power / Indutherm (Alemanha) - Tecnologia de Produção de Pó Metálico para Manufatura Aditiva
Mario Boccalini – IPT - Núcleo de Pesquisa em Manufatura Aditiva de Metais MAM
Painel: Manufatura Aditiva Metálica no Brasil
Moderadores: Daniel Bayerlein, Henrique Rodrigues Oliveira
Fabio Sant´Ana, Mario Boccalini, Cristiane Gonçalves, Ana Queiroz - Manufatura Aditiva Metálica no Brasil, Como Aumentar o Mercado Existente e Aproveitar os Potenciais Nacionais em Relação ao Mercado Global?
Macro Tema: Materiais Magnéticos
Moderador: Daniel Rodrigues
Daniel Rodrigues – BRATS - Materiais Magnéticos e Metalurgia do Pó: Competitividade ou Desempenho?
Fernando Landgraf – USP - Desafios para Implantar uma Cadeia Produtiva de Ímãs de Terras Raras no Brasil
Leandro Lima – UFSC - Estratégias de Processamento de Soft Magnetic Composites para Otimização de Aplicações Magnéticas
Marco Pallini – GKN - Potencial de Uso de Materiais SMC em Motores Elétricos e Exemplos de Aplicação
Macro Tema: Materiais Tribológicos
Moderador: Cristiano Binder
José Daniel Biasoli de Mello – UFU/UFSC - Tribologia em Materiais Sinterizados
Márcio Silvério – Embraco / Nidec - Efeito da Porosidade e Ferro-Oxidação nas Propriedades Mecânicas de Componentes Sinterizados
Domingos Theodoro - BS Powder Metallurgy - Mancais Autolubrificantes Sinterizados: Aspectos Importantes sobre Óleos de Impregnação e Estrutura Metalográfica
Macro Tema: MIM
Moderador: Cristiano Binder
Helder Barbosa da Silva – Orthometric - Powder Injection Molding (PIM)Tecnologia para Fabricação de Componentes de Alta Complexidade e Valor Agregado
Macro Tema: Processos Convencionais
Moderador: Ronaldo Pegorer
Alisson Duarte - 6Pro Virtual And Practical Process - Simulação da Compactação com Foco no Produto: Distribuição de Densidade e Propriedades Mecânicas
Maria do Carmo Amorim – Marelli - P/M Wish List
Eduardo Puerta – Metalpó - Conversão de Processos de Forjamento, Estampagem, Fundição e Injeção para Metalurgia do Pó
Ronaldo Pegorer - Consultor PM / Eltro - Zoneamento em Fornos Continuos de Esteiras para Sinterização e Aspectos em Tratamento Térmicos Posteriores
Painel: As Oportunidades da Eletrificação Veicular para a Cadeia da Metalurgia do Pó
Moderador: Antonio Carlos Gomes Jr
Edison Serbino, VW; Roberto Piovatto, GM; Pedro Mazza , Hoganas; Fernando Landgraf, USP; José Daniel Biasoli Mello, UFF; Marco Pallini , GKN
Coordenados por Inductotherm Group Brasil com as seguintes palestras apresentadas por técnicos da empresa:
Anderson Caproni - Soluções Simples para os Típicos Desafios de Aquecimento por Indução: Lições Aprendidas
Fernando Vieira - Impacto da Eletrificação em Sistemas de Aquecimento por Indução
Anderson Caproni - Impacto da Eletrificação em Sistemas de Aquecimento por Indução
Leandro Pasti - Tudo o que Você Sempre Quis Saber Sobre Tratamento Térmico por Indução Mas não Tinha Oportunidade de Perguntar
Fabio Cardoso - Sistemas de Proteção Inductotherm para Fornos de Fusão e Gerenciamento iSense
Fabio Cardoso - Confiabilidade nos Sistemas de Fusão para o Aumento de Taxa de Utilização
Seminário apresentado no auditório sob a coordenação de Udo Fiorini com as seguintes palestras:
Ralph Trigueros - Sulvy Brasil CoatingsRevestimentos Industriais para Proteção de Superfícies Metalmecânicas com Exemplos de Aplicações
Stefan Haas – RÜBIG (Áustria) - Rübig Duplex
DLC and PVD Sputter Coatings - “Revestimentos por Pulverização Catódica Rübig Duplex DLC e PVD”
Paulo Vencovsky - HEF Groupe - TS DiademaRevestimentos DLC em Componentes Seriados: uma Solução
Tecnológica Competitiva para Redução de Desgaste e Atrito
Após o evento, no dia 21 de março foi oferecido aos participantes do congresso a possibilidade de participar de um amplo programa de visitas técnicas a empresas
e laboratórios próximos à região de Campinas. Foram visitados: Combustol Fornos, Inductotherm, GKN, CTI, CNPEM Sirius e Steel Tech
O 2º Congresso Processos Térmicos contou com o o Patrocinio Ouro das empresas: Combustol Fornos, Industrial Heating Fornos, Inductotherm Group Brasil, First Fornos, GREFORTEC, TecProPro. E o Patrocinio Prata das seguintes empresas: BRATS Filtros Sinterizados, SCIENCA Suporte Metalúrgico, Sulvy Brasil Coatings, Villares Metals
O próximo Congresso de Processos Térmicos, em sua 3ª edição, terá como Chairperson Antonio Carlos Gomes Jr e está previsto para acontecer em 08 e 09 de Abril de 2025 no mesmo local, Hotel Nacional Inn Campinas - Trevo. Até lá!
11º Seminário do Forjamento,
6º Seminário da Estampagem,
3º Encontro Especialistas de Elementos de Fixação (Fastening)
Em 18 e 19 de junho 2024 foi realizado pelo Grupo Aprenda o 11º Seminário de Forjamento. O evento fez parte do III CCM, Congresso de Conformação Metálica, e foi realizado nas dependências da FSA, Fundação Santo André localizado na cidade com o mesmo nome. O Congresso contou como Chairperson o Prof. Dr. Mauro Moraes de Souza, Professor e Coordenador de Educação Continuada do Centro Universitário FEI.
Além do 11º Seminário de Forjamento, também coordenado tecnicamente por Mauro de Souza, o III CCM - Congresso de Conformação Metálica também sediou o 6º Seminário Tecnologia de Estampagem, sob a coordenação técnica de Prof. Dr. Gilmar Batalha, Professor Associado na Universidade de São Paulo e o 3º Encontro Especialistas de Elementos de Fixação (Fastening) que contou com a coordenação técnica de Dr. Roberto Garcia, Consultor Especializado em Elementos de Fixação e Corrosão.
Key Speakers
Mauro Moraes, como um dos Key Speakers do Congresso, após a recepção e abertura com as boas vindas aos participantes do evento apresentou a palestra:
Oportunidades de Crescimento Tecnológico: Panorama Brasileiro Atual de Fomento em PD&I. A inda na programação dedicada à Key Speakers, foram apresentadas as seguintes palestras:
André Rosiak (coautor Lírio Schaeffer) - UFRGS - Processos de Manufatura por Conformação Mecânica no Contexto Brasileiro Neste Mundo de Transformação Digital
Marco Colosio - Diretor Regional SP - SAE BRASIL - Os Desafios do Setor Automotivo em Vista das Novas Tendências e Tecnologias em Materiais e Processos.
Silvia Ribeiro de Aquino - Metalúrgica Onix / SINDIFORJA - Aspectos Gerais da Produção de Forjados no Brasil.
Robinson Bittencourt Lara - Dörken Coatings - Revestimentos Anticorrosivos – Tipos, Desafios e Tendências.
Roberto Garcia – Consultor da Area de Elementos de Fixação - Os Elementos de Fixação no Nosso Cotidiano, Muita Ciências dos Materiais e, Deveras Desprezados.
Após a sequencia de palestras da abertura, já na sala específica do Seminário do Forjamento, o Auditório FAECO da FSA, Fundação Santo André, foram apresentadas nos dois dias do evento as seguintes palestras, sob a coordenação técnica de Mauro Moraes: André Rosiak, UFRGS - Machine Learning Aplicada na Previsão da Curva de Escoamento de Aços Deformados a Quente
Gustavo Estrela, Jefferson Santos, UNIFORJA - Inovações em Simulação: Dinâmica de Forjamento, Otimização de Tratamento Térmico e Análise de Falha
Rafael Coutinho Pinto, EMGEPRON - Fábrica de Munição da MarinhaSimulação de Forjamento a Quente Aplicada a Fabricação de Projéteis
Jose Santaella Redorat Jr., Santec Tecnologia em Soldagem - Solda de Manutenção em Forjarias
Anderson Dascenzio, EATON Valinhos - Conversão de Forjamento a Quente para Forjamento a Morno em Matriz Fechada
Márcio Boragini, UPC Marathon - Benefícios da Nitretação Gasosa Controlada para Matrizes de Forjamento
Luigi Mazzucco, ALL Lubrificantes - Desmoldantes Atuais e Novas Tendências de Tecnologia para Forjamento
Carlos Sartori, Villares Metals - Estudo de Caso: Erros Conceituais na Seleção de Aços Ferramenta para Forjamento
Nicolas Soares Machado, CISER - Previsão de Quebra por Fadiga em Ferramenta de Forjamento a Frio
Alisson Duarte, 6Pro Virtual And Practical Process - Seminário QForm UK Brasil 2024 e Cases de Forjamento
Joel Renato da Silva , Villares Metals - Rastreabilidade Digital de Lingotes e Tarugos em Fornos de Aquecimento para Forjamento de Produtos Não Seriados
Rodolfo Fonseca, Inductotherm Group Brasil - Flexibilidade em Sistemas de Aquecimento por Indução para Conformação de Metais
Vitaliy Belugin, QForm UK Group - Metal Flow Optimization and Defects Analysis in QForm UK - “Otimização de Fluxo de Metal e Análise de Defeitos no QForm UK”
Oswaldo Ravanini, Transvalor Americas - Simulação de Dano Dútil e Propagação de Trincas em Conformação a Frio
Já na sala específica do Seminário do Estampagem, foram apresentadas nos dois dias do evento as seguintes palestras sob a coordenação técnica de Gilmar Batalha: Rafael Coutinho Pinto, EMGEPRON - Fábrica de Munição da Marinha - Análise da Deformação Plástica do Latão na Fabricação de Estojo Vitaliy Belugin, QForm UK Group - Sheet Forming Simulations in QForm UK - “Simulações de Conformação de Chapas no QForm UK”
Flavio Pessutte de Castro, Volkswagen - Otimização Topológica em Fundidos de Ferramentais
Oswaldo Ravanini, Transvalor Americas - Simulação de Fine-Blanking com o COLDFORM NxT 4.0 – Estudo de Casos
Fernando Henrique Grandizoli , AutoForm do Brasil - Solução Virtual Para União de Componentes Metálicos Estampados, Gerando Resultados Através dos Gêmeos Digitais
Beatriz Beloti, Laminação São Joaquim - Estudo de Inibição da Descarbonetação no Processo de Reaquecimento de Tarugos na Laminação a Quente
Gilmar Ferreira Batalha / Bruno Caetano Silva , EPUSP / SENAI CimatecEstampagem a Quente Com Tempera Simultanea - Manufatura Aditiva de Ferramental com Canais Conformais
Paula Fernanda Farina , UNICAMP FEM - Desafios e Oportunidades na Fabricação de Matrizes para Estampagem a Quente
Luigi Mazzucco, ALL Lubrificantes - Desmoldantes Atuais e Novas Tendências de Tecnologia para Estampagem
Adilson Calmona, AutoForm do Brasil - Aprovação de PPAP Virtual
Ricardo Viana, SIXPRO Virtual&Practical Process - Gestão Eficiente Integrando os Sistemas CAD/MES/ERP com o Cover4PM
Ricardo Viana, SIXPRO Virtual&Practical Process - Técnicas de Compensação de Springback no Processo de Estampagem
Carlos Eduardo Ciardi Barbosa , Politécnica USP - Desenvolvimento do Processo FSSW (Friction Stir Spot Welding) na Indústria Automotiva
Felipe Ribeiro Toloczko, USP / FATEC SP - Superplasticidade: Conceitos
Fundamentais e Aplicações Industriais
Na sala específica do Encontro Especialistas de Elementos de Fixação (Fastening), foram apresentadas nos dois dias do evento as seguintes palestras sob a coordenação técnica de Roberto Garcia:
Cássio Aurélio Suski , IFSC Campus Itajaí - Influência da Temperatura de Austenitização na Microestrutura de Parafusos de Aços 15BCr30 E PL22
Rubens Cioto, CTF Centro Tecnológico de Fixação - Entendendo o Comportamento de uma Junta Submetida a Vibração Transversal
Marcos Souza, CTF Centro Tecnológico de Fixação / UFRG (RS) - Análise
Experimental da Influência do Comprimento Carregado em Juntas Aparafusadas
Submetidas a Vibração Transversal
Alisson Duarte, 6Pro Virtual And Practical Process - Projetando o Forjamento de Elementos de Fixação com o Auxílio da Simulação
Douglas Mesquita, Mesquita Consultoria e Assessoria Empresarial - O Custo da Qualificação da Mão-de-Obra não é Despesa, é Investimento com Retorno Garantido
Fabio Fernandes / Edvaldo Rocha , DS4 Innovation / JVS - Braço de Reação
Inteligente: Ajuste Dinâmico e Prevenção de Falhas Integrados à Indústria 4.0
João Marcelo Marçal Bocca , Gerdau - Avanços na Produção de Parafusos: Tecnologia de Laminação, Tratamentos Térmicos de Aços Especiais
Udo Fiorini - Grupo Aprenda, Gustavo Pires, Cesar Zeferino, Augusto Camilo e Fernando Forato - thyssenkrupp
Wanilto Santos / Rebeca Ramos , METALTORK / UNESP AraraquaraTécnicas Eletroquímicas para Detectar Cobertura de Revestimento em Parafusos
Lidio Andrade Jr, Systek - Juntas Aparafusadas - Meios de Controle no Processo de Montagem Dessas Juntas e sua Relação com Falhas em Veículos, Motores, Máquinas
Oswaldo Ravanini, Transvalor Americas - Simulação de Laminação de Roscas com o COLDFORM NxT 4.0
Robinson Bittencourt Lara , Dörken Coatings - Coeficiente de Atrito - Desafios e Causas de Falhas
Stephany Kamarowski, Vinicius A. Voiciekouski , CISER - Qual o Efeito dos Coeficientes de Atrito, sobre Diversos Revestimentos, Aplicados em Parafusos de Classe de Resistência 10.9, Analisados em Apertos nos Regimes Elástico e Elastoplástico
José Carlos D´Amaro, ALPHAGALVANO - “PLATING” Aspectos Físico Quimicos e Propriedades Tribológicas
Leonardo Fassio, QUIMIDREAM - A Importância da Desfosfatização como Pré Tratamento ao Tratamento Térmico em Fixadores e o Enegrecimento como Possível Pós Tratamento
Vitaliy Belugin, QForm UK Group - Cold Forming Simulations and Tool Life Analysis in QForm UK - “Simulações de Conformação a Frio e Análise de Vida Útil da Ferramenta no QForm UK”
Finalizando o Congresso, Mauro Moraes apresentou a palestra Reflexões Finais sobre o 3º Congresso de Conformação Metálica - Aprendizados, Highlights, Contribuições para o Ambiente Brasileiro de Conformação.
O III CCM contou com o apoio da Revista do Parafuso e o Patrocinio Ouro das empresas: 6Pro Virtual And Practical Process, CISER, Metaltork, Transvalor Americas. E o Patrocinio Prata das seguintes empresas: ALL Lubrificantes, Dörken Coatings, Inductotherm Group Brasil, MARAJÁ Autopeças, Santec Tecnologia em Soldagem, Villares Metals.
A Revista do Parafuso (The Fastener Brazil Magazine), através de seu editor Sergio Milatias foi a mídia apoiadora do 3º CCM
O próximo Congresso de Conformação Metálica, 4º CCM, também contará com Mauro Moraes de Souza como Chairperson e está previsto para acontecer em 24 e 25 de Junho de 2025 no Hotel Plaza Vinhedo, localizado na cidade de Vinhedo, interior de SP. Nos vemos lá!
Grefortec:
Grefortec:
+ de 30 Anos de Excelência em Equipamentos para Tratamento Térmico e Serviços Industriais
+ de 30 Anos de Excelência em Equipamentos para Tratamento Térmico e Serviços Industriais
Ao longo de mais de três décadas, a Grefortec consolidou-se como uma referência no mercado de equipamentos para tratamento térmico e serviços. A empresa ganhou a confiança de importantes nomes da indústria, graças aos seus resultados consistentes, atendimento excepcional ao cliente e compromisso com a excelência.
Como licenciados exclusivos da Aichelin Group, líder mundial em equipamentos e para tratamentos térmicos e termoquímicos, a Grefortec garante aos clientes produtos da mais alta qualidade, sendo a fabricante oficial em toda a América do Sul.
seguem acontecendo dentro da empresa e se estendem para o mercado com a implantação de cursos específicos, voltados para a área de tratamento térmico, e a partir deste ano, abrangendo também a área de operação de fornos.
Portfólio de Serviços Especializados em Tratamento Térmico e Produção de Equipamentos Personalizados
Com processos de têmpera, revenimento, carbonitretação e nitretação, oferecemos soluções que aprimoram a resistência mecânica do metal, garantindo durabilidade e eficácia às peças de nossos clientes.
Desenvolver e industrializar soluções térmicas personalizadas que agreguem valor aos clientes, acionistas, colaboradores, fornecedores e sociedade.
Missão Visão
Ser referência em soluções tecnológicas em aquecimento para a indústria.
Valores
Desafios industriais e tecnológicos, cooperação constante, adaptabilidade em projetos, respeito e ética nas relações, responsabilidade e segurança em nossas atividades, comprometimento com os clientes internos e externos, confiabilidade nas soluções apresentadas e serviços prestados, e qualidade em produtos e processos.
Inovação e Crescimento Contínuo
Com o passar dos anos, o nome Grefortec se tornou associado à excelência em tratamento térmico e serviços industriais (fabricação, manutenção e reposição de peças), adotando tecnologias de ponta e aprimorando constantemente seus processos. O crescimento e a inovação
Contate a Grefortec
Além dos processos de tratamento térmico, oferecemos uma ampla gama de produtos para atender às diversas necessidades, desde fornos câmara e contínuos até assistência técnica especializada e peças de reposição de alta qualidade. Ainda, prestamos serviços de manutenção, reposição de peças, monitoria, auditoria e assessoria, tanto de produtos como de serviços prestados.
Compromisso com a Sustentabilidade e Inovação
Na Grefortec, o compromisso com a sustentabilidade está no centro de tudo que fazemos. Desde a destinação adequada de resíduos até a implementação de práticas inspiradas no programa 5S, estamos empenhados em minimizar nosso impacto ambiental e contribuir para um futuro mais sustentável.
É importante destacar que há 15 anos a empresa iniciou o trabalho de redução na emissão de CO2, desenvolvendo um sistema tecnológico de composição de gases industriais formadores de atmosferas para processos de tratamento térmico de peças e componentes ferrosos e ligas metálicas.
Esta iniciativa foi patenteada pela Grefortec, tornando-a uma das poucas metalúrgicas de Tratamento Térmico Verde do Brasil.
Para mais informações, visite nosso site em www.grefortec.com.br e descubra as possibilidades que sua empresa pode ter acesso quando qualidade e inovação se unem em prol do sucesso industrial.
Equipamentos Assistência Técnica Tratamento Térmico
R. Estrada Estância Velha, 1134, Bairro Portão