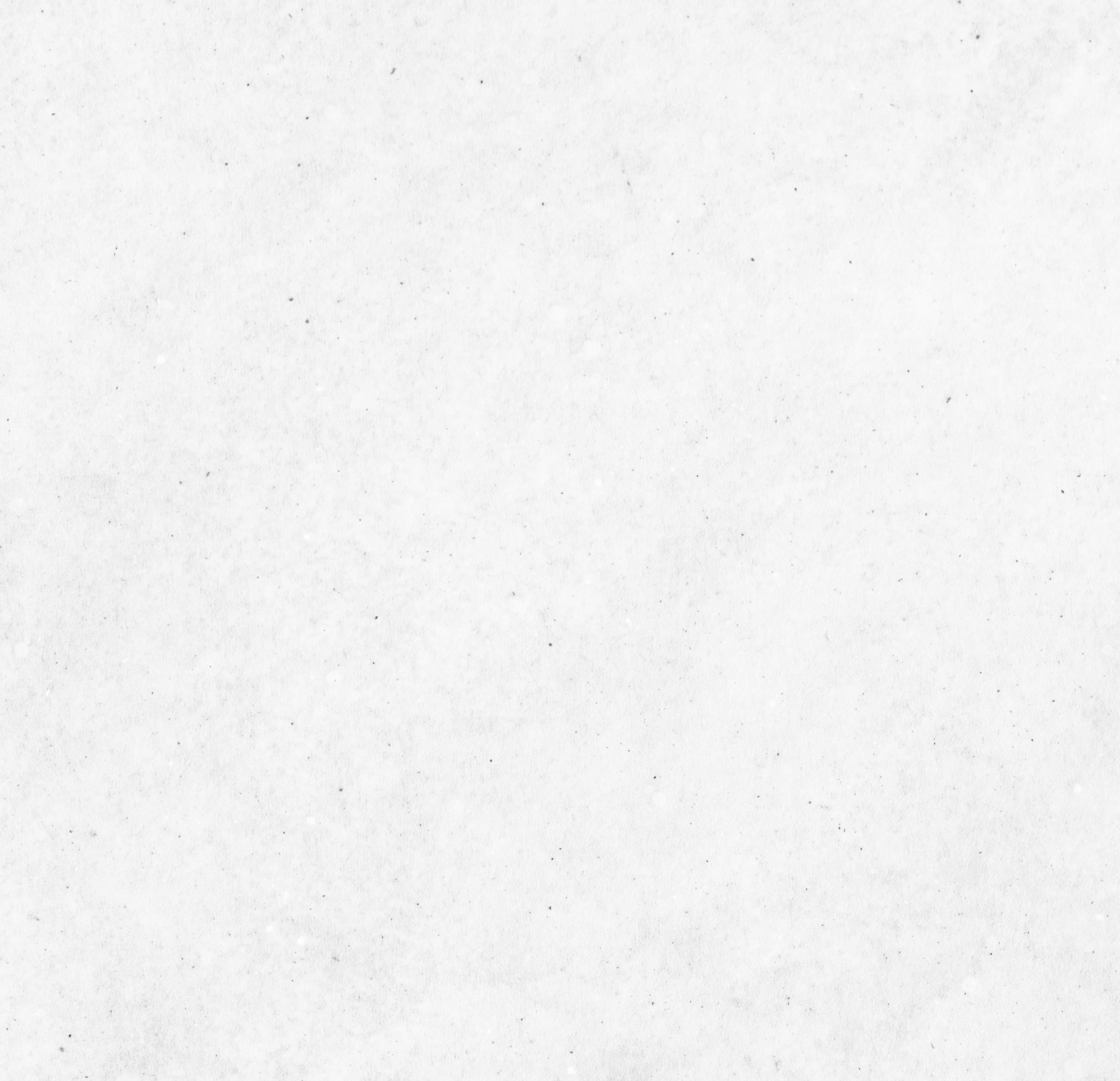
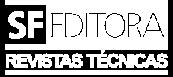
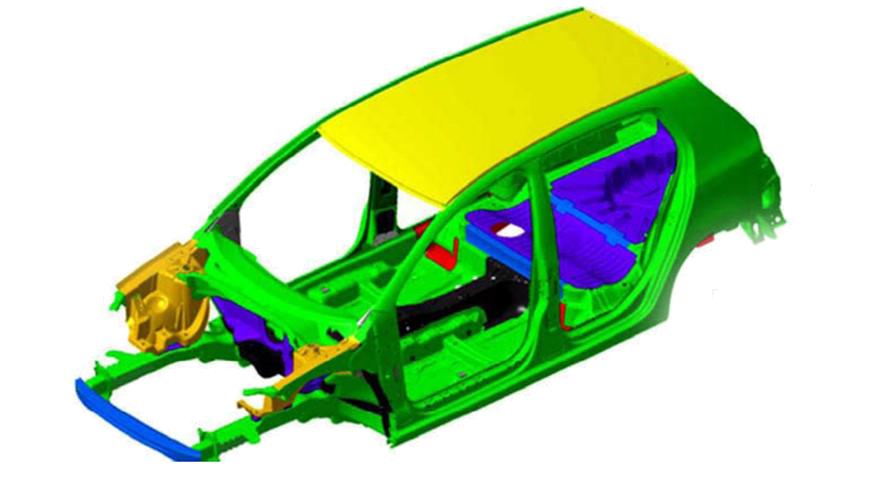
Atualmente, devido à grande competição e a constante demanda por produtos novos e de baixo custo é comum nas indústrias de transformação mecânica, principalmente no caso da indústria brasileira, encontrar metodologias de desenvolvimento baseadas na adaptação de linhas de produtos já fabricados, com modificações inspiradas muitas vezes no método da tentativa e erro.
Esta postura, principalmente quando não se tem muita experiência no processo, gera considerável desperdício de material tanto nas peças que apresentam falha, quanto no ferramental que não se adequou ao projeto.
A simulação numérica vem para ajudar os engenheiros e projetistas nessa tarefa.
e
Aços Avançados de Alta Resistência para o Setor Automotivo: Panorama e Estudo de Caso para Compensação do Retorno Elástico
Bruno Caetano dos Santos Silva; Luis Fernando Folle; Bruna Callegari; Rodrigo Santiago Coelho; Luiz Zamorano e Gilmar Ferreira Batalha
A utilização de aços de alta resistência nas carrocerias automotivas é um fator importante para a redução de peso dos veículos, com impacto direto na redução das emissões de CO2
MS.c Cristian Luiz Onzi; Eng. Josimar Santos e Dr. Ing. Lirio Schaeffer
Este artigo teve como o foco principal avaliar o retorno elástico utilizando a técnica do Processo de Dobramento em L com ressalto no punção, através de uma matriz para realizar o dobramento do aço SAE 1006.
Erlifas Moreira Rocha; Prof. Dr.-Ing. João Henrique Corrêa de Souza; Jocilei Oliveira (apoio)
As indústrias estão continuamente na busca por melhorar sua competitividade, procurando métodos eficazes para a redução de custos e do tempo dos processos de fabricação de seus produtos e processos.
Transvalor
Fundada em Genebra em 1965, a Boucledor Inc. projeta e produz fivelas e fechos para alta relojoaria e joias de luxo.
Rafael Pandolfo da Rocha; Matheus Henrique Riffel; Thomas Gomes dos Santos; André Rosiak e Lirio Schaeffer
Os esforços para construção automotiva leve aumentaram significativamente impulsionados pela atual pressão econômica e política para reduzir o consumo de combustível e as emissões de CO2
SF Editora é uma marca da Aprenda Eventos Técnicos Eireli (19) 3288-0437
Rua Ipauçu, 178 - Vila Marieta, Campinas (SP) www.sfeditora.com.br
Lirio Schaeffer Editor, schaefer@ufrgs.br • (51) 99991-7469
Udo Fiorini Publisher, udo@sfeditora.com.br • (19) 99205-5789
Mariana Rodrigues Diagramação - Revisão, marianar205@gmail.com • (19) 3288-0437
André Júnior Vendas, andre@grupoaprenda.com.br • (19) 3288-0437
As opiniões expressadas em artigos, colunas ou pelos entrevistados são de responsabilidade dos autores e não refletem necessariamente a opinião dos editores.
Empresa Pág. Contato
Imagem de Capa: Ju e Altan (2015). Veja mais na página 52.
Grupo Aprenda / CBCM 2ª Capa www.cbcm-metalforming.com AutoForm 21 www.autoform.com
Metalurgia 3ª Capa www.metalurgia.com.br
FSA Vestibular 4ª Capa www.vestibularfsa.com/ Estampagem 13 www.aquecimentoindustrial.com.br/ Technova 6 www.technnova.com.br/treinamentos
Editorial Brasil A Indústria Nacional necessita urgentemente de mais engenharia aplicada aos processos de fabricação O Brasil de um modo geral possui um grande mercado interno e sem dúvida este fato representa uma situação muito cômoda para muitas empresas nacionais.
PHS Work Force Team Clinching: Realidade na Junção de Alta Resistência Caros leitores, o grupo PHS Work Force tem mostrado continuamente seus resultados no campo de aplicações de aços avançados (ARBL) para veículos de alto desempenho e perseguindo continuamente o aumento do nível de segurança veicular em produtos brasileiros.
A Sixpro está envolvida em cinco dos projetos referentes ao programa Rota 2030, contribuindo com know-how, treinamentos, suporte técnico e softwares.
Nos dias 6 e 7 de outubro sediamos em Porto Alegre o 41° SENAFOR e 8° congresso organizado pelo BrDDRG.
OBrasil de um modo geral possui um grande mercado interno e sem dúvida este fato representa uma situação muito cômoda para muitas empresas nacionais. Entretanto, para melhorar a situação econômica do país é necessário que seja feito um maior investimento nas nossas exportações. Torna-se imprescindível que nossas empresas passam a ser também exportadoras de seus produtos. Neste cenário, principalmente na área de produtos manufaturados, o grande desafio é ganhar competitividade. Para atingir este nível é muito importante o diferencial de uma melhoria de qualidade e competência, para adequar os produtos aos padrões do mercado internacional. Por outro lado, a empresa que passa a exportar de forma sustentável, melhora sua imagem com fornecedores, bancos e clientes e este aspecto também vem a se refletir nas operações do mercado interno ( www.gov.br/siscomex).
Em muitas áreas já se observa uma supremacia brasileira em relação a muitos países no mundo. Destaca-se assim os produtos mais exportados pelo Brasil: soja, minérios de ferro, óleos brutos de Petróleo, açucares, carne bovina, farelos de soja, celulose e milho (em ordem quantitativa). Onde estão os produtos da indústria de transformação ? Por que um país que possui uma das maiores reservas de metais do mundo não consegue exportar produtos acabados? Esse fato significa, por exemplo, exportar produtos com maior valor agregado, quando comparado com a simples exportação de minérios.
O Grupo Aprenda, através de suas revistas e congressos, há muitos anos vem tentando divulgar tecnologias, inovações importantes e aspectos essenciais da engenharia que é fundamental para que os técnicos especializados nas empresas consigam otimizar seus processos a fim de atingir um melhor nível tecnológico internacional. Junto com as instituições brasileiras, que atuam na área de formação de Recursos Humanos e Desenvolvimento de Tecnologia, mostra-se assim
aos empresários brasileiros, uma rica fonte de apoio para uma melhoria de patamar em suas empresas. Não é possível apenas através dos métodos convencionais (tentativa e erro), usado ainda por muitas empresas, para melhorar a sua tecnologia. Não é suficiente importar equipamentos modernos para se ter um substancial aumento e melhoria tecnológica. É necessário o conhecimento da engenharia dos processos.
O problema no Brasil já começa com muitos fabricantes de matéria prima. Muitos Certificados de Qualidade mostram um total desconhecimento da simples diferença entre um Diagrama de Engenharia e uma Curva de Escoamento (variação da Tensão de Escoamento com a Deformação). Nas empresas a maioria de nossos técnicos especializados desconhecem os efeitos de composição química, das condições térmicas e tribológicas dos materiais, etc... No uso das simulações computacionais (a grande moda atual), quem adquire dados de materiais para os produtos fabricados no Brasil, necessários para alimentar os softwares? Como fazer engenharia com esta forma de operar?
Para contribuir com o emprego de engenharia nos processos de conformação de chapas metálicas a Revista Estampagem & Conformação procura trazer agora, em Setembro de 2022, mais uma importante edição onde os destaques são:
Aços Avançados de Alta Resistência para o Setor Automotivo: Panorama e Estudo de Caso para a Compensação do Retorno Elástico. Trabalho desenvolvido por um grupo de pesquisadores do SENAI CIMATEC (Bahia), USP (São Paulo) e FORD DO BRASIL (Bahia). O Estudo envolve análises da deformabilidade do aço TRIP 1000, que faz parte dos Aços Avançados de Alta Resistência Mecânica (AHSS) da 1ª geração. Foi mostrado como a simulação computacional do processo oferece resultados confiáveis também para aços de alta resistência.
Estratégia para a Redução do Retorno Elástico: uma nova Avaliação da Geometria no Processo de Dobramento em “L”. Este tema foi estudado pelo Grupo de Conformação Mecânica (CBCM) da UFRGS (RS). O trabalho analisou aspectos do retorno Elástico de um aço ABNT 1006, com o emprego de um ressalto no punção, no processo de Dobramento em “ L” Modelo Numérico do Processo de Hidroconformação aplicado em Carcaças de Compressores Herméticos. Este trabalho foi desenvolvido pela FURG (RS) em colaboração com a AUTOFORM DO BRASIL Ltda. Desenvolveu-se o Processo de Hidroconformação em substituição ao processo convencional de fabricação dos componentes analisados. Novamente a ferramenta básica de análise do novo processo, que culminou com excelentes resultados, foi realizado com o apoio de softwares de simulação computacional.
Desenvolvimentos na Conformação Mecânica de Chapas de Ligas de Alumínio para Indústria Automotiva. O grupo de
pesquisa CBCM, da UFRGS (Porto Alegre) inicia com o Eng Rafael Pandolfo seus primeiros projetos na área da Estampagem a Quente de Ligas de Alumínio.
Simulação de Estampagem de Componentes para Relojoaria Fina. Este estudo é apresentado por técnicos pesquisadores da empresa BOUCLEDOR Inc (Genebra) envolvendo relojoaria fina aplicada ao uso de metais preciosos. Também um estudo conjunto com a TRANSVALOR S.A. (França). Foi empregado o software COLDFORM para a otimização deste processo de mecânica de precisão na estampagem.
Uma boa leitura a todos.
Prof Lirio Schaeffer
Caros leitores, o grupo PHS Work Force tem mostrado continuamente seus resultados no campo de aplica ções de aços avançados (ARBL) para veículos de alto desempenho e perseguindo continuamente o aumento do nível de segurança veicular em produtos brasileiros. A contribuição mais recente deste grupo de professores, pesquisadores e alunos culminou na homologação da dissertação de mestrado de um dos alunos do curso de pós-graduação na área de materiais do IPEN/USP, Sr. Vanderlei M. Bastos (1), tema de nossa edição.
Sabemos que a transformação tecnológica das linhas de manu fatura para oferecer adaptabilidade é bem notada na indústria auto motiva, na indústria de linha branca, na construção leve, assim como a redução na quantidade de matérias-primas nos produtos. Por outro lado, no setor automotivo, o objetivo foca na produção de carroçarias
de veículos de construção leve, rígidas e resistentes a colisões, sem contar, às premissas de redução na pegada de carbono e do consumo de combustível. No campo de materiais para o setor automotivo, o uso dos aços avançados de alta resistência como as classes acima de 1300 MPa tem agregado uma série de benefícios nos veículos atuais e futuros, porém o aumento de resistência desses materiais tem tornado os processos industriais mais desafiadores, principalmente os de junção, também explorados por este grupo de pesquisadores.
Este amplo estudo tem correlacionado aspectos das uniões de aços de alta resistência por clinching comparativamente aos de solda a ponto por resistência elétrica, quando submetidos em regimes de tração e cisalhamento. Interessante notar que, o processo clinching, já bem conhecido para metais não ferrosos e aços de baixa e média resistência mecânica, tem sido uma opção crescente de aplicação no
lugar da solda por resistência elétrica no sentido de gerar menor mu dança microestrutural dos materiais de união, manter as proprieda des mecânicas das partes e também ter um ambiente industrial mais limpo e eficiente. Antes de trazer aos nossos leitores a importância desta tecnologia, o clinching pode ser resumido como um processo de união por conformação mecânica conforme classificado pela norma DIN 8580, a figura a seguir exemplifica este sistema de manufatura industrial segundo esta norma.
O processo de união por conformação mecânica é muito depen dente dos mecanismos de deformações elásticas e plásticas dos mate riais envolvidos e são estas propriedades que ditam o grau de ancora gem da junta ou também conhecido como embricamento mecânico. Portanto, foi neste ponto que a pesquisa teve um grande êxito, ou seja, pouco se sabia do emprego desse processo para aços de resistên cias acima dos 1300 MPa, parte devido à falsa idéia da necessidade de ductilidade dos materiais como um fator determinante de fixação, e por outro lado, situações de fragilização associadas ao elevado grau de dureza do aço. Mas o estudo mostrou que o resultado positivo de junção destas partes aumenta consideravelmente nestes aços devido à origem de um alto grau residual de energia plástica proveniente da deformação do material, somado a uma condição geométrica de ancoramento com elevada energia de deformação elástica estocada, que é grande responsável pela estabilidade da fixação e integridade do produto em uso sem adicionar tensão, lembrando que a energia elástica é responsável em manter a junta rígida mesmo em situações de carregamentos cíclicos. Para tornar mais claro o mecanismo e ancoramento, a figura a seguir exemplifica uma junta composta de
As contribuições deste trabalho abrem diversas oportunidades no setor automotivo, onde a possibilidade contínua de criação de pro jetos de carroçarias mais rígidas e eficientes com emprego dos aços de alta resistência de segunda e terceira geração e adicionalmente, evitando a conhecida presença de danos de soldagem por resistência elétrica, nas temperaturas elevadas que reduzem localmente as pro priedades destes aços e também exigem fatores elevados de segurança adotados perante conhecidas falhas de fusão na região de junção. No entanto, o clinching preserva as propriedades mecânicas dos aços, é mais robusto e previsível, tem baixa possibilidade de falhas pontuais na união, fatos estes que ajudarão os engenheiros a buscarem novos caminhos na virtualização das juntas em projetos e certamente, a otimização no número de pontos de ancoragem nestes sistemas de fixação metálica em veículos. Obrigado e até a próxima coluna da revista Estampagem.
Grupo formado dentro do IPEN no inicio de 2010 e intitulado como PHS Work Force Team em 2015, sem fins lucrativos, formado por pesquisadores e especialistas internos e externos na área de aços de alto desempenho, com foco em impulsionar o setor da mobilidade e solucionar problemas que habitam esta comunidade.
Sixpro está envolvida em cinco dos projetos referentes ao programa Rota 2030, con tribuindo com know-how, treinamentos, suporte técnico e softwares.
Dentre estes projetos, destaca-se o DEMESTAA (Demonstrador do Processo de Estampagem de Superfí cies Classe A), que tem o objetivo de construir um ferramental para a estam pagem de uma porta externa. E, nesse contexto, criou-se o ambiente perfeito para a realização de um trabalho muito produtivo em conjunto com a Gaspec –vencedora da licitação para construção do ferramental –, envolvendo o software OmniCAD.
A Gaspec é uma ferramentaria de grande porte, com estrutura para desenvolvimento de processo e produ ção de ferramentais de pequeno, médio e grande porte. É também uma das poucas ferramentarias no Brasil com capacidade e expertise para a produção de ferramental para peças de pele.
Como contrapartida ao DEMES TAA, a Sixpro disponibilizou o softwa re OmniCAD para a Gaspec e, durante uma semana, deu treinamentos e fez de monstrações em casos reais da empresa. Assim, ao final foi possível apresentar diversos estudos de caso, nos quais ob servou-se uma significativa redução do tempo de engenharia e um grande po tencial na redução das horas de try-out. Os estudos também mostraram a ótima qualidade das superfícies compensadas e/ou modificadas no OmniCAD.
Após a semana de treinamento, foi concedido um período de licença para a Gaspec para que os trabalhos relativos ao DEMESTAA pudessem ser reali zados, além de outros testes internos de interesse da empresa. Um dos testes realizados consistiu na compensação do springback de um assoalho de grandes dimensões (aproximadamente 1,8m x 1,5m), que pode ser visto na figura 1.
Este trabalho se destacou justamente pelo grau de dificuldade imposto pelas dimensões e pela sua complexidade.
O assoalho em questão já havia sido compensado previamente com base em simulações. Porém, no try-out, apresentou áreas com desvios dimen sionais acima da tolerância permitida, conforme pode-se verificar na figura 2, demandando uma re-compensação para
melhorar o resultado dimensional.
Para avaliar a qualidade dimensio nal, foi realizado o escaneamento do produto estampado, obtendo-se a malha no formato “stl”. Então, decidiu-se recompensar a ferramenta de repuxo utilizando o OmniCAD.
Para isso, primeiramente são impor tadas a malha do produto (no formato “stl”, obtida através do escaneamento), as superfícies nominais do produto (forma to “igs”) e as superfícies da ferramenta conforme foi copiada inicialmente. Através de um comando simples, o Om niCAD então faz a medição dos desvios entre a geometria nominal e a malha do produto escaneado, projeta automatica mente essas distâncias na superfície da ferramenta e realiza uma nova compen sação. Neste procedimento é possível escolher o nível de alisamento a ser aplicado na superfície a ser gerada. O OmniCAD permite escolher entre cinco níveis de alisamento, em que o mais alto prioriza a preservação da curvatura da superfície original, garantindo a melhor qualidade possível. Geralmente, para painéis internos, é aplicado um nível de alisamento médio e, para peças classe A, o nível mais alto.
Outro parâmetro a ser escolhido pelo usuário é o fator de compensação. Neste trabalho foi aplicado o fator 1, ou seja, o valor do desvio medido foi aplicado in tegralmente na compensação, respeitan do-se o alisamento escolhido. À medida em que o usuário do OmniCAD ganha experiência na compensação de dife rentes produtos, é possível estabelecer qual é o melhor fator a ser aplicado em função do material, tipo de produto etc.
A compensação foi aplicada somente na região indicada pela linha ponti lhada na figura 3, mantendo as demais áreas conforme a que havia sido copiada previamente.
Após a compensação, a região alterada foi mesclada com a região não alterada, utilizando a função Free Transformer, mantendo-se uma faixa de transição suave.
Todo o procedimento foi realizado em aproximadamente 3 horas de traba lho, exportando, ao final, a superfície da ferramenta recompensada para a cópia.
A ferramenta de repuxo foi então recopiada e reajustada em try-out, estampando uma nova amostra. Foi realizado o escaneamento e uma nova análise dimensional. O resultado pode ser verificado na figura 4
Conforme pode ser observado nas figuras, houve uma redução considerável na amplitude dos desvios e na área fora da tolerância após a recompensação no OmniCAD. Possivelmente, com um fator de compensação maior do que 1, o resultado seria ainda melhor.
Com este desafiador estudo de caso
foi possível comprovar a eficácia do OmniCAD quando aplicado diretamen te no try-out para solucionar problemas de springback, reduzindo horas de try-out e de engenharia e aumentando a qualidade final do produto.
Ricardo A. Micheletti Viana, Engenheiro Mecâ nico, graduado pela UFMG com 15 anos de expe riência no processo de conformação de chapas, simulação e acompanhamento de try-out. É autor de patente, livro, artigos e colunas diversas. Ge rente técnico e sócio na empresa “SIXPRO Virtual and Practical Process”. ricardo@sixpro.pro
Patrícia Marques, Tecnóloga em engenharia mecânica, com 16 anos de experiência no ramo automotivo, sendo 4 anos na Gaspec Ferra mentaria, atuando em simulações e compensa ções, projetos de ferramentas e tratamento de superfícies. Sócia proprietária na empresa “SM Engenharia Ltda”. smengenharia.pm@gmail.com
Nos dias 6 e 7 de outubro sediamos em Porto Alegre o 41° SENAFOR e 8° congresso organizado pelo BrDDRG. Foram dois dias de intenso aprendizado, reencontros e novos contatos. Falamos sobre materiais, tribologia, ferramental, manufatura digital e hot stamping, entre outros.
Entre as participações nacionais e internacionais que se destacaram podemos mencionar:
Professor Mathias Liewald do IFU Stuttgart, Gianfranco Ruggiero e Todd McClanahan da AutoForm, Marco Antonio Wolff da Usiminas, Jessica Santana da Benteler, Vagner Braga da Bruning, Gustavo Hendos da CBA, Professor Gilmar Batalha da Poli-USP, entre outros.
Conseguimos juntar sob o mesmo teto ICTs, universidades, indústrias e estudantes. Em nome da comissão técnica do BrDDRG nosso muito obrigado a todos os presentes, especialmente palestrantes e patrocinadores.
Ano que vem tem mais!
Dr.-Ing. João Henrique Corrêa de Souza é s ecretário n acional da BrDDRG, professor visitante na FURG - Universidade Federal de Rio Grande. Technnova Consultoria em Engenharia e Inovação. Para saber mais acesse o site: www. technnova.com.br ou o perfil no Linkedin www. linkedin.com/in/joaohcdesouzametalforming.
A utilização de aços de alta resistência nas carrocerias automotivas é um fator importante para a redução de peso dos veículos, com impacto direto na redução das emissões de CO2. Essa necessidade contribuiu para o desenvolvimento constante de aços avançados que visam ao atendimento de requisitos cada vez mais arrojados de resistência mecânica e ductilidade. Por outro lado, maiores níveis de resistência estão associados a efeitos mais expressivos de retorno elástico (springback), um problema de processo que provoca distorções na peça conformada, principalmente em chapas metálicas estampadas. O objetivo desse trabalho consistiu em avaliar a confiabilidade do modelamento numérico para previsão do efeito de retorno elástico em um aço com efeito TRIP. Constatou-se que o aço TRIP1000 apresentou um comportamento de retorno elástico voltado para o encruamento isotrópico. O estudo evidenciou que a simulação numérica pode proporcionar resultados confiáveis quando apoiada por dados obtidos de maneira assertiva. Ensaios complementares podem apoiar no aprimoramento do modelo numérico, de modo a permitir um aproveitamento ainda maior das potencialidades do software.
Palavras-chave — estampagem a quente, 22MnB5, força de estampagem, retorno elástico.
om as exigências das montadoras por automóveis com desempenho cada vez melhor em testes de im pacto de carrocerias automotivas (crash tests) aliado à redução de peso da estrutura, para diminuição do consumo de combustível, houve avanços significativos no desenvolvimento de aços avançados de alta resistência (advanced high strength steels – AHSS) para aplicações automotivas. Alguns desses aços possuem maior resistência combinada com elevada ductilidade, permitindo sua conformação para transformação em componen
tes com geometrias relativamente complexas. Porém, maiores níveis de resistência tendem a promover efeitos mais intensos de retorno elástico, um problema de processo que causa distor ções na peça conformada, principalmente em chapas metálicas estampadas. O efeito Bauschinger, pouco conhecido antes do surgimento dos aços avançados de alta resistência, consiste na diminuição da resistência do material quando submetido a um carregamento reverso, o que pode intensificar o retorno elástico. Um dos desafios associados a esse efeito é dificuldade de quan tificá-lo em chapas metálicas, uma vez que, ao ser carregada
AÇOS AVANÇADOS DE ALTA RESISTÊNCIA PARA O SETOR AUTOMOTIVO: PANORAMA E ESTUDO DE CASO PARA COMPENSAÇÃO DO RETORNO ELÁSTICO
Figura 1. Diagrama de desempenho dos aços avançados de alta resistência. Os desempenhos de ligas leves de aplicação automotiva – Alumínio e Magnésio também são apresentados para comparação. Adaptada de: [14]–[16].
sob compressão, a chapa pode flambar em um ensaio de tração seguido de compressão. Por isso, diversos esforços vêm sendo realizados para resolver esse problema [1]–[4].
Os estudos que tratam desse assunto nomeiam o compor tamento do material como sendo de endurecimento (encrua mento) cinemático e, através de modelos matemáticos, buscam descrever tal comportamento. O modelo de Yoshida–Uemori, explorado no trabalho de Chang et al. [5], e o modelo de Chaboche [6], [7], usado no trabalho de Peč, Šebek e Petruška [8], são exemplos de abordagens. Também, existem trabalhos que utilizam as curvas geradas em ensaios de tração/compressão diretamente em softwares de simulação, como feito no trabalho de Ma et al. [9]. Com o material caracterizado pelos modelos de endurecimento cinemático, vários estudos foram conduzidos para se verificar o quanto esses modelos podem melhorar a capacidade de softwares de simulação para predição do compor tamento do material (e.g. [2], [3], [9], [10]). Existem esforços, ainda, no sentido de avaliar como o retorno elástico pode ser minimizado, tanto com testes físicos quanto através de simula ções (e.g. [4], [11], [12]).
Assim, pode-se dizer que o efeito de retorno elástico em peças estampadas de aços de alta resistência constitui um dos principais problemas tecnológicos enfrentados pelo setor auto motivo. O melhor entendimento desse fenômeno e a aplicação de medidas de mitigação são de grande relevância para a apli
cação industrial desses materiais. Motivado por essa questão, o presente artigo apresenta um estudo focado na análise do retor no elástico (springback) em um aço com efeito TRIP (Trans formation Induced Plasticity) de terceira geração por meio de simulações numéricas em software de elementos finitos, com posterior validação através de ensaios físicos, além de trazer um cenário geral sobre o desenvolvimento de aços AHSS aplicados na indústria automotiva.
Como mencionado, aços avançados de alta resistência vieram como resposta às demandas da indústria automobilística por materiais com baixo peso e espessuras reduzidas, porém com boas combinações de resistência e conformabilidade, para reduzir os impactos ambientais, melhorar eficiência energética e, ao mesmo tempo, conferir a proteção necessária aos tripulan tes do veículo [13]. Esta família de aços possui microestruturas cuidadosamente projetadas, resultantes de processos complexos de deformação e transformação de fases para atingir combi nações de resistência e ductilidade muito superiores às vistas em aços convencionais utilizando técnicas de processamento já existentes [14]. Aos aços com resistência superior 780 MPa, dá-se, também, o nome de aços de ultra-alta resistência (ultra
Figura 2. Metodologia utilizada no desenvolvimento do estudo.
-high strength steels – UHSS). O diagrama da Figura 1 mostra os desempenhos dos diversos aços avançados das três gerações, comparando-os, inclusive, com aços tradicionais e ligas leves de aplicação automotiva (alumínio e magnésio). O aumento da ductilidade confere maior conformabilidade ao aço, enquanto o aumento da resistência permite a redução de peso dos compo nentes; o efeito adverso da elevada resistência, porém, é a maior suscetibilidade ao efeito de retorno elástico.
Os aços AHSS são divididos em três gerações. A primeira geração inclui classes de aços já bem desenvolvidas e com am plas aplicações na indústria automobilística, com microestrutura majoritariamente martensítica, a qual confere elevada resistência mecânica ao material, podendo conter, também, outros micro constituintes, como ferrita, bainita e austenita retida. Este grupo é composto pelos aços de fases complexas (complex phase – CP), aços bifásicos (dual-phase – DP), aços com efeito de plasticidade induzida por transformação (transformation-induced plasticity –TRIP), e aços martensíticos, inclusive estampados a quente – con formação com têmpera simultânea - CTS (hot-formed – HF – ou press-hardened – PHS). A segunda geração é composta por aços com maior teor de austenita retida, para melhoria da ductilidade, como aços inoxidáveis austeníticos e aços com efeito de plasticidade induzida por maclação (twinning-induced plasticity – TWIP).
Já a terceira geração foi motivada pelo objetivo de criar ligas com níveis de resistência e ductilidade semelhantes ou superiores aos encontrados nas gerações anteriores, sem perder o foco na redução de custos [13], [17], [18]. São, em sua maioria, baseados no efeito TRIP conferido pela presença de austenita retida na microestru
tura, a qual se transforma em martensita mediante a aplicação de tensão ao material. Na terceira geração, além do desenvolvimento de novos conceitos de design microestrutural, como é o caso de aços de baixa densidade, aços quenching & partitioning (Q&P), aços TRIP com bainita ferrítica livre de carbonetos (TRIP-assis ted ferritic bainite – TFB), e aços trifásicos com nano-precipitados (triple-phase with nano-precipitation – TPN), estão incluídos, também, aços cujas classificações se encaixam nas gerações an teriores, mas que foram desenvolvidos mais recentemente com o objetivo de melhoria dos limites de propriedades de resistência e/ ou ductilidade em relação aos aços já tradicionalmente existentes dentro dos respectivos grupos. Abaixo, são descritos alguns aços desenvolvidos na terceira geração.
• Aços de baixa densidade: aços Fe-Mn-Al-C, nos quais a adição de alumínio leva a uma considerável redução de densi dade e, consequentemente, de peso, além de melhorar a resis tência à corrosão e oxidação. Podem ser puramente ferríticos, puramente austeníticos, ou possuir uma microestrutura du plex com diferentes relações ferrita/austenita, dependendo da composição. Aços de base austenítica possuem níveis de resis tência e ductilidade consideravelmente maiores que os de base ferrítica. Os aços ferríticos, devido às propriedades mecânicas limitadas, em combinação com a conformabilidade limitada, não são atraentes para aplicações automotivas. Por outro lado, os austeníticos, apesar de apresentarem desempenho superior, possuem conformabilidade ainda limitada quando compara dos a outros aços avançados, como aços TWIP e DP, o que constitui uma desvantagem para emprego em componentes
automotivos com geometrias complexas [19].
• Aços Q&P: aços com níveis de resistência de até 1100 MPa, cuja rota de tratamento térmico envolve uma etapa de auste nitização seguida por têmpera até uma temperatura dentro do campo de transformação martensítica, retendo certa quan tidade de austenita, seguida por uma etapa de tratamento isotérmico nessa temperatura, para estabilização da austenita retida pela difusão de carbono da martensita formada [20]. Tais aços possuem composições semelhantes às de aços TRIP, mas apresentam resistência superior. São estampáveis a frio, sendo aplicáveis em peças críticas de segurança no automóvel com geometrias complexas [14].
• Aços TBF: também denominados CBF (carbide-free bainitic), possuem efeito TRIP com microestrutura com posta por grãos ferríticos e bainita entremeada com auste nita retida, a qual é obtida por um tratamento que envolve recozimento intecrítico seguido por resfriamento rápido até uma temperatura de tratamento isotérmico dentro do campo de transformação bainítica, acima da temperatura de início de transformação martensítica. Tal fenômeno é possibilitado pela adição de silício em concentrações de aproximadamente 2%, que retarda a precipitação de cementita [21]. A austenita retida se apresenta mais refinada, em contraste com os grãos relativamente grosseiros da fase observados em aços TRIP de primeira geração [22]. A substituição de um aço TRIP convencional com nível de resistência de 980 MPa por um aço TBF com resistência equivalente permite uma redução de 20% na espessura de um componente automotivo, devido à ductilidade e conformabilidade superiores [23].
• Aços TPN: aços constituídos por grãos de ferrita, bainita e filmes de austenita retida, contendo, ainda, nano-precipitados que conferem elevada resistência, aliada à conformabili dade promovida pela austenita retida. Atingindo níveis de resistência de até 900 MPa, são adequados para aplicação em estruturas como coluna B, membros transversais e longitudi nais e como reforço do painel lateral [14]. Foram desenvolvi dos pela Thyssen-Krupp Steel Europe em cooperação com a japonesa JFE [24].
• Aços TRIP com teor médio de Mn: enquanto aços TRIP da primeira geração raramente contêm mais que 2% de Mn em peso e aços TWIP de segunda geração contêm cerca de 20% de Mn, os aços com teor médio do elemento o pos suem em concentrações entre 3 e 12%. O ciclo térmico não difere muito do aplicado a aços Q&P, com a diferença de que o Mn aumenta a estabilidade da austenita, diminuindo a temperatura de fim da transformação martensítica abaixo da
Figura 3. Curvas tensão-deformação verdadeiras do aço TRIP nas três direções principais em relação a direção de laminação
temperatura ambiente, resultando em maiores quantidades de austenita retida. Assim, o aço apresenta níveis semelhantes de resistência, mas com ductilidade superior à dos aços Q&P [25]. Tais aços, porém, ainda não possuem comercialização expressiva [22].
• Aços PHS: são aços tipicamente ligados ao manganês e boro conformados a quente, em um processo que permite sua estampagem em geometrias complexas na condição austeníti ca. Mediante taxas relativamente elevadas de resfriamento na matriz arrefecida a água, uma microestrutura 100% mar tensítica pode ser obtida. Desenvolvido na primeira geração, o exemplar mais conhecido da classe é o aço 22MnB5, que contém cerca de 0,2% C e apresenta resistência de 1500 MPa na condição martensítica pós-estampagem. Na segunda geração, com o advento dos revestimentos à base de Al-Si, a resistência à corrosão e oxidação foi melhorada [26]. Atu almente, aços com maiores teores de carbono (0,30-0,38%) que atingem níveis de resistência de 1700-2000 MPa já estão consolidados, sendo aplicados em componentes críticos de
1. Valores obtidos para os coeficientes de resistência (K) e de encruamento (n) da equação de Hollomon.
Figura 4. Curvas sobrepostas dos ensaios de tração monotônica e cíclica (a), e curva de decaimento exponencial do modulo de elasticidade, obtida através do ensaio de tração cíclica (b). São mostradas as curvas de decaimento experimental e ajustada de acordo com a Equação 1.
segurança automobilística, como a coluna B. Já foi demons trado que o uso de um aço PHS com resistência de 1900 MPa na fabricação da coluna B pode contribuir para uma econo mia de peso de 22% em comparação ao uso de um aço DP (dual phase) com limite de resistência de 600 MPa, custan do, ainda, 9% menos que o aço DP, e que a substituição do tradicional 22MnB5 pelo mesmo aço permite uma redução de 15% no peso do automóvel [18]. Além disso, a volta ao uso de aços não revestidos, para redução de custos, está em voga; neste sentido, o desenvolvimento de composições com elevada resistência à corrosão e oxidação é de extrema relevância. Na seção seguinte, será discutido o modelamento do efeito de retorno elástico em um aço com efeito TRIP pertencente à ter ceira geração, com ênfase no efeito dos modelos utilizados e em sua respectiva adequação à predição do fenômeno, com validação através de testes físicos.
Para o desenvolvimento deste estudo, foram realizados ensaios físicos e simulações numéricas com o intuito de investigar o com portamento de retorno elástico de chapas de um aço TRIP1000 de terceira geração, em condições de estampagem a frio. As chapas possuíam espessura de 1,5 mm. A metodologia do estudo desenvolvido foi dividida em três etapas:
• Etapa 1 de caracterização mecânica: envolveu os ensaios realizados para a obtenção de coeficientes do material a serem utilizados como dados de entrada para a simulação numérica, visando obter uma resposta numérica mais assertiva na previ são de comportamentos associados à deformação do material.
• Etapa 2 de simulação numérica: correspondeu à execução da simulação numérica propriamente dita do retorno elástico utilizando elementos finitos.
Tabela 2. Valores obtidos do ensaio de tração cíclica para o decaimento do módulo de Young
Módulo de Young inicial ou isotrópico (E) 90o 204,86 GPa
Fator de redução do módulo de Young (γ) 0,4
Taxa de redução do módulo de Young (χ) 20
• Etapa 3 de validação: consistiu na execução de ensaios físicos de dobramento para avaliação do retorno elástico, com posterior comparação dos resultados obtidos com aqueles previstos pela simulação, de modo a avaliar a adequação da simulação e dos modelos utilizados na predição da ocorrência do fenômeno de retorno elástico no aço em questão.
O fluxograma da Figura 2 ilustra a metodologia utilizada, incluindo os dados de entrada da simulação obtidos através de cada ensaio e os dados de saída, ou seja, os resultados obtidos pela simulação.
Figura 5. Comportamento do material segundo os modelos isotrópico (a) e cinemático (b). A linha azul corresponde ao modelo de equação de Hollomon com os coeficientes medidos. A linha verde corresponde ao espelhamento dessa equação na região de compressão. A linha laranja corresponde ao modelo cinemático ou isotrópico adotado.
Nessa etapa, foram realizados ensaios de tração monotônica, anisotropia e tração cíclica, além de ensaios tribológicos. Os procedimentos dos ensaios de tração e anisotropia são descritos a seguir. Os ensaios tribológicos são detalhados e discutidos em outro trabalho publicado pelos autores.
Foram executados ensaios de tração em triplicata nas três dire ções principais (0°, 45°, 90°) em relação à direção de laminação da chapa. As curvas tensão-deformação obtidas são mostradas na Figura 3, enquanto a Tabela 1 evidencia os coeficientes de encruamento e de resistência da equação de Hollomon (σ = K.εn), a qual é mais usual para aços ao carbono.
Os ensaios de anisotropia seguiram as mesmas condições dos ensaios de tração, utilizando geometrias idênticas de corpo de prova. O procedimento consistiu em submeter o material a uma deformação pré-determinada de 6%, interromper o ensaio, e realizar medições da largura do corpo de prova utilizando um pa químetro calibrado. As medidas de comprimento foram obtidas por meio de extensômetro acoplado ao corpo de prova.
Figura 6. Geometria utilizada nas simulações numéricas e nos ensaios físicos de retorno elástico.
Durante a conformação de uma chapa metálica em um raio da matriz ou através de um quebra-rugas, o material é submetido a um dobramento, subsequente desdobramento e dobramento novamente. Para uma simulação precisa de tal processo, é neces sário um modelo constitutivo adequado, que possa considerar os fenômenos que ocorrem durante o carregamento cíclico, como o efeito Bauschinger, o comportamento transiente, o amolecimen to permanente e a estagnação do encruamento [8]. Todos esses efeitos podem ser descritos pela chamada “lei de encruamento cinemático”. Os ensaios realizados tiveram como objetivo o levantamento dessas informações.
Figura 7. Níveis de retorno elástico obtidos na simulação da peça com efeitos isotrópicos (a) e cinemáticos (b) no material.
Figura 8. Diferença entre as distorções da peça simulada sem retorno elástico, com retorno elástico considerando efeitos isotrópicos, e com retorno elástico considerando efeitos cinemáticos no material.
O primeiro ensaio que gera informações sobre o encruamento cinemático é o ensaio de tração cíclica, onde o corpo de prova é submetido a um ciclo de carga e descarga até a ruptura. Mais uma vez, o corpo de prova utilizado foi o mesmo do ensaio de tração. A deformação adotada para esse ciclo foi de 2%. Os resul tados são mostrados na Figura 4a.
Em aços de alta resistência, o módulo de elasticidade apre senta um decaimento exponencial que pode ser descrito através da Equação 1. Os valores constantes dessa equação são mostrados na Tabela 2. Com essas informações, é possível plotar uma curva de ajuste que descreve esse fenômeno, mostrada graficamente na
4b.
-
A simulação numérica pelo método de elementos finitos (MEF) foi conduzida no software AutoForm. Para a simulação, foram considerados dos modelos de encruamento: o modelo isotrópico e o modelo cinemático. A Figura 5 mostra os comportamentos ob tidos para o material em cada uma das duas condições avaliadas.
Para ambos os modelos (encruamento isotrópico e encruamento cinemático), a deformação de reversão (reversal strain) foi definida como 0,2. No modelo isotrópico, a taxa de amolecimento transiente (tran sient softening rate) e a razão de estagnação (stagnation ratio) foram definidas como nulas. Já no modelo cinemático, os valores atribuídos aos parâmetros foram de 0,1 e 1, respectivamente. Isso significa, basicamen te, que efeito Bauschinger é muito pronunciado no modelo cinemático e praticamente nulo no modelo isotrópico. O Efeito Bauschinger é uma diminuição do limite de escoamento quando há uma mudança de direção da deformação plástica, no caso de tração para compressão. Em outras palavras, ao deformar um metal em uma direção até que seja ultrapassado o limite de escoamento, e deformando-o após na direção contrária, seu limite de proporcionalidade nesta última direção é menor. Isso faz com que as tensões que iriam estabilizar a geometria da peça apresentem maior desbalanceamento, promovendo um maior retorno elástico.
Para as simulações, foi considerada uma geometria de chapéu idên tica à utilizada nos testes físicos, mostrada na Figura 6. Os resultados da simulação mostraram que o modelo utilizado exerce efeito significativo
na predição do retorno elástico. A Figura 7 mostra, em perspectiva, o formato final simulado de cada peça após a abertura das matrizes. A Figura 8 mostra uma vista lateral de meia geometria comparando os resultados desconsiderando a ocorrência de retorno elástico e consideran do-o com encruamento isotrópico e com encruamento cinemático. Esse efeito é esperado, visto que, quando o material sofre uma deformação de compressão após a tração, há uma suavização das tensões residuais na pa rede lateral da peça, o que promove um aumento dos efeitos das tensões residuais do outro lado da espessura da chapa, fazendo com que ela seja “torcida” com maior intensidade naquela região.
Para validação dos resultados da simulação, foram realizados testes físicos utilizando a geometria mostrada na Figura 6 para quantificação do retorno elástico real sofrido pelo componente durante o processo. A Figura 9 mostra as peças estampadas em três condições – sem lubrificação, com lubrificante de baixa vis cosidade e com lubrificante de alta viscosidade – sendo os ensaios
também conduzidos em triplicata. Como esperado, a lubrificação não possui influência sobre o retorno elástico. Tal comportamen to foi observado já nos ensaios tribológicos, por meio dos quais constatou-se que a lubrificação não gera impactos significativos no atrito entre a chapa e a matriz.
Comparando-se os resultados do material ensaiado fisica mente com os das simulações (Figura 10), foi observado que o aço estudado apresenta comportamento de encruamento isotrópico, ou seja, com efeito Bauschinger pouco pronunciado. Na figura 10, é mostrado o resultado do ensaio sem lubrificante, pois, como constatado, os testes com lubrificante resultaram em pouca variação. É possível observar a clara coincidência entre os formatos finais simulado com encruamento isotrópico e obtido experimentalmente.
Esse estudo teve como objetivo avaliar a confiabilidade do modelamento numérico para previsão do efeito de retorno elástico em um aço com efeito TRIP, de modo a validar a simulação numérica por elementos finitos como um método confiável para prever o comportamento do material mediante processamento por estampagem a frio. Os resultados mostram que a simu lação numérica é efetiva e confiável para tal predição, quando embasado em dados obtidos de maneira assertiva através de uma metodologia robusta de ensaios mecânicos. Assim, pode-se dizer que a simulação constitui uma ferramenta com elevado potencial para otimização do projeto de peças estampadas de aços avançados de alta resistência. O material em questão apresentou um comportamento de retorno elástico voltado para o encruamento isotrópico. Entretanto, vale ressaltar que a simulação, apesar de conseguir prever corretamente o comportamento do material no estado atual, ainda carece de um modelo mais preciso do material, para que o software possa ser aproveitado com todo seu potencial.
Os autores agradecem à empresa Usiminas pelo fornecimento do aço TRIP1000.
[1] J. Cao, W. Lee, H. S. Cheng, M. Seniw, H. P. Wang, and K. Chung, “Expe rimental and numerical investigation of combined isotropic-kinematic hardening behavior of sheet metals,” Int. J. Plast., vol. 25, pp. 942–972, 2009, doi: 10.1016/j. ijplas.2008.04.007.
[2] P. A. Eggertsen and K. Mattiasson, “On the identification of kinematic hardening material parameters for accurate springback predictions,” Int. J. Mater. Form., vol. 4,
pp. 103–120, 2011, doi: 10.1007/s12289-010-1014-7.
[3] B. Chongthairungruang, V. Uthaisangsuk, S. Suranuntchai, and S. Jirathearanat, “Springback prediction in sheet metal forming of high strength steels,” Mater. Des., vol. 50, pp. 253–266, 2013, doi: 10.1016/j.matdes.2013.02.060.
[4] R. Radonjic and M. Liewald, “New process design for reduction of springback by forming with alternating blank draw-in,” Procedia Manuf., vol. 29, pp. 217–224, 2019, doi: 10.1016/j.promfg.2019.02.129.
[5] C. Y. Chang, M. H. Ho, and P. C. Shen, “Yoshida-Uemori material models in cyclic tension-compression tests and shear tests,” Proc. Inst. Mech. Eng. Part B J. Eng. Manuf., vol. 228, no. 2, pp. 245–254, 2014, doi: 10.1177/0954405413499011.
[6] J. L. Chaboche, “Time-independent constitutive theories for cyclic plasticity,” Int. J. Plast., vol. 2, no. 2, pp. 149–188, 1986, doi: 10.1016/0749-6419(86)90010-0.
[7] J. L. Chaboche, “Constitutive equations for cyclic plasticity and cyclic viscoplastici ty,” Int. J. Plast., vol. 5, no. 3, pp. 247–302, 1989, doi: 10.1016/0749-6419(89)90015-6.
[8] M. Peč, F. Šebek, and J. Petruška, “Basic kinematic hardening rules applied to 304 stainless steel and the advantage of parameters evolution,” Mech. Solids, vol. 54, no. 1, pp. 122–129, 2019, doi: 10.3103/S0025654419010102.
[9] W. Ma, J. Yang, X. Zheng, B. Wang, C. Li, and Y. Zhang, “The effect of Baus chinger related parameters on material property of Dh780 and springback behavior of longitudinal beam,” IOP Conference Series: Materials Science and Engineering, vol. 472. p. 012045, 2019, doi: 10.1088/1757-899X/472/1/012045.
[10] J. Min et al., “Effect of tension-compression testing strategy on kinematic model calibration and springback simulation of advanced high strength steels,” Int. J. Mater. Form., vol. 14, pp. 435–448, 2021, doi: 10.1007/s12289-020-01583-8.
[11] E. M. Lee, D. S. Shim, J. Y. Son, G. Y. Baek, H. S. Yoon, and K. B. Ro, “Study on design of progressive dies for manufacture of automobile structural member using DP980 advanced high strength steel,” J. Mech. Sci. Technol., vol. 30, no. 2, pp. 853–864, 2016, doi: 10.1007/s12206-016-0140-7.
[12] A. Mousavi and A. Brosius, “Improving the springback behavior of deep drawn parts by macro-structured tools,” IOP Conference Series: Materials Science and Engi neering, vol. 418. p. 012105, 2018, doi: 10.1088/1757-899X/418/1/012105.
[13] M. Y. Demeri, Advanced high-strength steels: Science, technology and applica tions. ASM International, 2013.
[14] S. Keeler, M. Kimchi, and P. J. Mooney, “Advanced high-strength steels applica tion guidelines version 6.0.” WorldAutoSteel, p. 314, 2017.
[15] M. Soleimani, A. Kalhor, and H. Mirzadeh, “Transformation-induced plasticity (TRIP) in advanced steels: A review,” Mater. Sci. Eng. A, vol. 795, p. 140023, 2020, doi: 10.1016/j.msea.2020.140023.
[16] R. Rana and S. B. Singh, Eds., Automotive steels: Design, metallurgy, processing and applications. Woodhead Publishing, 2017.
[17] D. K. Matlock and J. G. Speer, “Third generation of AHSS: Microstructure de sign concepts,” in Microstructure and texture in steels and other materials, A. Haldar, S. Suwas, and D. Bhattacharjee, Eds. Springer-Verlag London, 2009, pp. 185–204.
[18] E. Billur, Ed., Hot stamping of ultra-high strength steels. Springer Nature Switzerland, 2019.
[19] R. Rana, Ed., High-performance ferrous alloys. Springer Nature Switzerland,
2021.
[20] J. Speer, D. K. Matlock, B. C. De Cooman, and J. G. Schroth, “Carbon partitioning into austenite after martensite transformation,” Acta Mater., vol. 51, pp. 2611–2622, 2003, doi: 10.1016/S1359-6454(03)00059-4.
[21] F. G. Caballero, M. J. Santofimia, C. Capdevila, and C. García-Mateo, “Design of advanced bainitic steels by optimisation of TTT diagrams and T0 curves,” ISIJ Int., vol. 46, no. 10, pp. 1479–1488, 2006, doi: 10.2355/isijinternational.46.1479.
[22] “3rd Generation Steels.” .
[23] E. O. Arman and T. Hebesberger, “Development of a TBF980 MPa class steel to meet challenges of weight reduction & stampability,” 2017.
[24] B. Hammer, R. Laurenz, and S. Woestmann, “TPN®-W 780: Three-phase-steel with nano-precipitation.” 2014.
[25] J. Speer, R. Rana, D. Matlock, A. Glover, G. Thomas, and E. De Moor, “Proces sing variants in medium-Mn steels,” Metals (Basel)., vol. 9, p. 771, 2019, doi: 10.3390/ met9070771.
[26] T. Taylor and A. Clough, “Critical review of automotive hot-stamped sheet steel from an industrial perspective,” Mater. Sci. Technol., vol. 34, no. 7, pp. 809–861, 2018, doi: 10.1080/02670836.2018.1425239.
Bruno Caetano dos Santos Silva, SENAI CIMATEC – Instituto SENAI de Inovação em Conformação e União de Materiais, Salvador-BA, Brasil; Universidade de São Paulo – Escola Politécnica, São Paulo - SP, Brasil | (bruno.silva@fieb.org.br);
Luis Fernando Folle, SENAI CIMATEC – Instituto SENAI de Inovação em Conformação e União de Materiais, Salvador-BA, Brasil | (luis.folle@fbter. org.br);
Bruna Callegari, SENAI CIMATEC – Instituto SENAI de Inovação em Conformação e União de Materiais, Salvador-BA, Brasil | (bruna.callegari@ fbter.org.br);
Rodrigo Santiago Coelho, SENAI CIMATEC – Instituto SENAI de Inovação em Conformação e União de Materiais, Salvador-BA, Brasil | (rodrigo.coelho@ fieb.org.br);
Luiz Zamorano, Ford do Brasil, Salvador-BA, Brasil | (lzamoran@ford.com);
Gilmar Ferreira Batalha, Universidade de São Paulo – Escola Politécnica, São Paulo - SP, Brasil | (gfbatalh@usp.br)
Este artigo teve como o foco principal avaliar o retorno elástico utilizando a técnica do Processo de Dobramento em L com ressalto no punção, através de uma matriz para realizar o dobramento do aço SAE 1006. Nos ensaios de dobramento foram possíveis identificar as deformações do lado externo das fibras dos corpos de prova com 1,5 mm de espessura, tal como o retorno elástico nos sentidos de laminação de 0° e 90°. No processo de dobramento foram utilizados dois modelos de punção, sem e com ressalto de 0,25 mm de altura e 1,2 mm de largura, para averiguar o fator do retorno elástico (K), as deformações verdadeiras (φext) e relativas (ε) que ocorreram no lado externo das fibras, para realizar uma avaliação comparativa dos valores teóricos. Os resultados experimentais das deformações verdadeiras (φext)/relativas (ε) com o punção sem ressalto foram 0,18[-]/20% para o sentido da laminação 0° e 0,26[-]/30% para o sentido da laminação 90°, já para o punção com ressalto foram 0,34[-]/40% para laminação a 0° e 0,38[-]/45% para laminação a 90°. O valor teórico da defor mação relativa (ε) resultou em uma variação máxima de 9% e a deformação verdadeira (φ) em 0,7 [-] quando comparados aos resultados experimentais. Através dos dados obtidos, comprovou-se que a Linha Neutra (LN) da dobra da chapa gerou uma deformação assimétrica e constatou-se que as maiores deformações ocorreram no sentido de laminação a 90°. Os resultados obtidos experimentalmente do fator do retorno elástico (K) mostraram compatibilidade com os dados obtidos teoricamente, evidenciando que ao utilizar o método do punção com ressalto diminui o retorno elástico, demostrando que o maior valor do fator de retorno elástico ocorre no sentido de laminação a 90°.
Oprocesso de conformação de chapas caracteriza-se na transformação de uma chapa metálica para adquirir uma nova geometria, através da utilização de uma prensa e um ferramental, no qual é constituía por uma matriz, prensa chapas e um punção. A combinação destes elementos gera uma deformação plástica na chapa metálica [1]. No processo de
dobramento, o metal sofre uma inflexão ao longo de seu eixo neutro, gerando uma deformação por flexão. O dobramento é obtido por matrizes com segmentos curvos para deixar as chapas com o formato desejado, para o tal processo, ocorrem tensões combinadas quando o metal escoa, gerando forças primárias tra tivas na posição chapa em contato com a matriz e forças compres sivas indiretas na chapa com o contato do punção. O dobramento
MS.c Cristian Luiz Onzi; Eng. Josimar Santos e Dr. Ing. Lirio SchaefferPalavras-chave — Dobramento em L, Retorno elástico, Conformação a frio do aço SAE 1006, deformação verdadeira
ESTRATÉGIA PARA REDUÇÃO DO RETORNO ELÁSTICO: UMA NOVA AVALIAÇÃO DA GEOMETRIA NO PROCESSO DE DOBRAMENTO EM L
gera momentos fletores na chapa e devido a elasticidade do material, é comum que haja retorno elástico [2], [3], [4].
O retorno elástico tem sido muito explorado em diversas técnicas de dobramento como: em V estudadas pelo autor Park [5], Huang e Leu [6], Tekaslan [7] e Wang [8], dobramento em L por Kazan [9], Phanitwong e Thipprakmas [10], Ling [11] e Jamli [12] e para dobramento em U por Lee [13] e Dongjuan [14]. Os estudos desenvolveram métodos de cálculos e conceitos para auxiliar na fabricação de ferramentais. Porém, muitas técni cas utilizadas para restringir o retorno elástico nos processos de dobramento nas indústrias são poucas divulgadas, que é um parâ metro importante no projeto de ferramentais. Tal como, o estudo realizado por Ling [11] que avaliou o processo de dobramento em L utilizando um ressalto no punção de dobra ocasionado uma conformação direta na chapa, que posteriormente foi estudado por Jafari [15], reforçando que aplicação desta técnica reduz o retorno elástico.
O propósito desde artigo é avaliar o retorno elástico do processo de dobramento com dois modelos de punção, sem e com ressalto para largura e altura determinada em projeto, conside rando os sentidos de laminação de 0° e 90° no aço SAE 1006 de espessura de 1,5 mm. Contudo, os resultados obtidos foram a partir de ensaios mecânicos que são confrontados por equações extraídas da literatura, para fins de avaliação de conceitos teóri cos com práticos. Através deste estudo almeja-se contribuir com um novo conceito para readaptação no processo de dobramento na avaliação do retorno elástico.
O processo de dobramento L ou pelos termos em inglês L-ben ding é utilizado principalmente em etapas de dobramento em matrizes progressivas, o tal efeito trata-se quando uma das abas da chapa é fixada por um prensa chapas ao passo que a outra extremidade sofre o dobramento de 90° pela ação do punção [9], [16]. Já o método de dobramento em L com ressalto possui si milaridade com o processo de dobramento em L convencional, a diferença característica está presente no punção inferior conforme visto na Figura 1. Neste local, há um ressalto com altura e largu ra determinada que no processo de dobramento executa também uma conformação direta no lado interno da dobra [11], [15], [17].
Quando a chapa é dobrada dá origem a uma dupla tensão, no lado externo ocorre tensões trativas e lado interno compressivas. A intensidade de ambas tensões decrescem nas fibras externas ao
Figura 1. Geometria característica do processo de dobramento em L com ressalto. Adaptado de [15].
Figura 2. Representação das variáveis na geometria do dobramento de chapas. Fonte: Adaptado de [22].
centro da peça, chegando ao ponto aonde as tensões se anulam, surgindo a linha neutra, considerada como a linha de passagem entre as tensões de compressão e tração [18].
O dobramento na zona elástica apresenta certas variáveis explanados na Figura 2, que possibilita realizar o cálculo para determinação do comprimento do arco dobrado (lca) e a própria deformação relativa (ε) [19], [20]. A Figura 2 mostra a simetria nas tensões de compressão presentes com maior intensidade no raio interno r i e tração no lado do raio externo (re) no momento do dobramento, neste sentido a linha neutra se encontra na me tade da espessura do material, no qual estão posicionados a linha
(lca) e o raio médio (r m) [21].
Através da variação relativa dos arcos dobrados lca e l 2 encon tra-se a deformação relativa (ε) pela equação 1 [18]. A equação 1 pode ser utilizada em casos quando não há simetria entre a região comprimida e tracionada da chapa:
No dobramento plástico parte-se do pressuposto que há uma simetria entre a região tracionada e a região comprimida, e que a relação
é sabida como dado inicial do produto a ser submeti do ao dobramento. Sendo que, qualquer seção haverá a máxima deformação relativa (ε max) que ocorre nas fibras externas (tensões de tração) distantes da linha neutra [18]. Neste sentido é possível calcular a máxima deformação relativa pela equação 2, onde s 0 é a espessura inicial da chapa e r refere-se à relação r = r m + y confor me indicado na Figura 2.
L adotando o cálculo da equação 5 [16]. Em que, b é o compri mento de dobra, s 0 a espessura da chapa, r p o raio do punção, j a folga entre o punção e a matriz, r ma o raio da matriz, R m tensão máxima e Ks um fator de correção que abrange 1.5 a 2.
No processo de dobramento o fator do retorno elástico (K ) pode ser verificado através da equação 6, sendo a razão entre os ângu los de dobramento [3].
Quando não é conhecido os ângulos de dobramento pode ser calculado o retorno elástico pela equação 7 [20]. Onde, M é o momento de dobramento da chapa, s 0 espessura da chapa, b a largura da chapa a ser dobrada, E o módulo de elasticidade, por fim, r p no qual se refere ao raio do punção.
A deformação no processo em estudo é inevitável, os ma teriais em geral possuem uma capacidade de estiramento que resultaram na deformação da superfície externa quando o dobra mento ocorre [23]. No processo do dobramento as fibras externas aumentam de tamanho [1], a partir disto, é possível também mensurar as deformações verdadeiras de tração (φ) pela equação 3 conforme a posição da linha neutra (LN):
No estudo de [23], sobre avaliação de processo de dobra mento, considerou que a posição y sendo deformação nas fibras externas, partindo da premissa que há simetria nas deformações de tração e compressão:
O momento de dobramento pode ser calculado com a equa ção 8, onde w é a distância de apoio de dobramento e F_d a força de dobramento.
É possível estimar o valor da força máxima do dobramento em
Foi realizado o ensaio de tração com o foco de investigar as pro priedades mecânicas do aço SAE 1006 com 1,5 mm de espessura (s 0), tais como, a tensão máxima (R m), tensão de escoamento (σesc) e o alongamento absoluto (∆l ). Foram utilizados 5 corpos de prova nos sentidos de laminação 0º, 45° e 90° totalizando 15 copos cor tados com o processo a laser seguindo os procedimentos da norma NBR 6892-1 (2013). Os ensaios foram conduzidos na máquina universal de ensaios mecânicos do fabricante EMIC modelo DL-20000 com a utilização do extensômetro com velocidades
de ensaio baseada na taxa de tensão de 10 MPa s-1, dentro dos parâmetros estabelecidos de 6 a 60 Mpa s-1 para materiais com o módulo de elasticidade (E) igual e maior a 150.000 MPa [24].
Para avaliar o dobramento em L nos sentidos de laminação de 0° e 90° foram fabricados 5 corpos de prova que possuem 2 abas para serem dobradas, como pode ser visto na Figura 3a. Neste intuito, foi confeccionado uma ferramenta que permite realizar o dobramento das duas abas em um único golpe (Figura 3b). Para o processo de dobramento foram utilizados dois punções, o modelo de punção com a face lisa e punção com ressalto de 1,2 mm de largura e 0,25 mm de altura. Em ambos punções foram fabrica dos com um raio de 0,5 mm.
2.3. Determinação das deformações no dobramento em L Para averiguar a deformação externa no processo de dobramento os corpos de prova, foram gravados uma malha circular em sua superfície através de processo eletrolítico, cada círculo possui um diâmetro inicial de 2,5 mm. A deformação verdadeira (φ) pode ser mensurada com a medição da variação dimensional das grades impressas em um componente, como por exemplo a gravação
circular dado que, após receber ação do dobramento trona-se uma elipse [1]. Portanto, foi utilizado uma régua flexível impressa em escala correspondente a gravação realizada nos CP’s, a mesma possibilita coletar dados da deformação relativa (ε) em porcen tagem (%) e o próprio valor da deformação verdadeira (φ) sendo radial ou tangencial. Portanto, a régua possibilitou a medição dos CP’s na fibra externa da dobra tracionada.
Para avaliar a microestrutura dos corpos de prova após o processo de dobramento utilizou método da norma ABNT NBR 13284 (1995) [25]. O processo iniciou com o corte dos corpos de prova através da eletroerosão a fio. A Tabela 1 exibe a divisão dos cortes após o processo de dobramento. A separação foi feita em 4 grupos, cada grupo corresponde ao método de dobramento e o sentido de laminação. Em seguida foi realizado os processos de embutimento, lixamento, polimento e o ataque químico com 2% de Nital por um período de 25 segundo por imersão. O ataque proporcionou a revelação da microestrutura dos grãos com predo minância da fase de ferrita típica do aço SAE 1006 [26], [27] que foram avaliadas através do microscópio ótico.
Logo depois do procedimento de metalografia e coleta das
de grupos para metalografia
imagens de cada processo de dobramento, permitiu-se fazer a medição da linha neutra através do software CAD SolidWorks®. As imagens foram inseridas através do comando inserir imagem, em seguida foi ajustado a mesma para a escala real usando a medida conhecida da espessura da chapa e conferido a referência de escala indicativa que o microscópio sobrescreve na imagem fotografada. Desta maneira, foi criado esboço gerando as circun ferências a partir da imagem, o que permitiu coletar a distância y, sendo a amplitude do raio linha neutra (LN) até o raio externo (re) da dobra da chapa.
Deformações plásticas em chapa geram um comportamento de deformação assimétrico, onde o movimento da linha neutra depende das taxas de compressão e tração, normalmente a LN move-se para direção interna, mas em alguns casos em que as condições das deformações efetivas não são iguais ocasiona o movimento da LN para o lado externo da superfície da chapa [22]. Os resultados encontrados nas medições da linha neutra pelas avaliações das deformações dos grãos estão sendo ilustrados na Figura 4.
As informações exibidas na Tabela 2 relaciona-se as propriedades mecânicas extraídas através da curva de engenharia (
) pelo ensaio de tração. A tabela informa os valores médios da tensão máxima (R m), alongamento máximo (δ) e tensão de escoamento (σ esc) para cada sentido de laminação dos 5 CP’s ensaiados. Ade mais fazendo um comparativo entre os dados do sentido de lami nação 0° e 90° percebe-se que o valores de tensão máxima (R m) ficam próximos, com apenas uma diferença de 0,5 MPa sendo menor no sentido de laminação de 90° [28]. Entretanto a tensão de escoamento resultou em 11,8 MPa superior no sentido de 90°. Além disso, como pode ser observado no sentido de laminação a 0° possui uma maior porcentagem de deformação pelo fato de as ibras estarem no mesmo sentido da força aplicada.
A Tabela 3 está apresentado o comparativo dos valores encontrados da deformação relativa (ε), sendo os valores experimentais obtidos
pela medição, dados calculados pela equação 1 e pela equação 2, em que r = r m + y uma vez que considera simetria na deforma ção dado que y = s 0/2. Ao analisar o comparativo da deformação relativa (ε) presente na Tabela 3 nota-se que, a equação 2 se mantém constante de 37,5%, pelo fato de a mesma considerar que há simetria das fibras entre as regiões tracionadas e comprimida no processo de dobramento. Ao comparar este valor com o experi mental, nota-se a variação da deformação relativa (ε) para cada grupo ensaio. Dessa forma, é visto que nos ensaios apresentaram dissimetria nas regiões de tração e compressão no dobramento, que ao utilizar a equação 1. [18], [29] os valores da deformação verdadeira se aproximam havendo uma variação mínima de 3% e máxima a 9%.
Análise comparativa da deformação verdadeira do lado externo (φext) dos dados experimentais e teóricos calculados através das equações 3 e 4 estão sendo apresentados na Tabela 4. Avaliando os resultados calculados teoricamente pela equação 4 [23], nota-se que os resultados das deformações verdadeiras (φext) apresentaram valores fixos de 0,47[-]. Já para a determinação do valor teórico utilizando a equação 3 [18], apresentou variação mínima de 0,01[-] e máxima de 0,7[-] para cada grupo de ensaio
conforme a medição da linha neutra assemelhando com os valores experimentais, que ocasionou um efeito do comportamento de deformação assimétrico [22] em vista da linha neutra se deslocar para o lado externo da superfície da chapa.
Analisando atentamente a Figura 5 e Figura 6, percebe -se que a deformação verdadeira (φext) e relativa (ε) nos corpos de prova são sempre maiores no sentido da laminação de 90°. Ademais, é possível observar que o grupo de ensaio 3 e 4 que foram submetidos ao processo de dobramento para o punção com ressalto, sofrem um tracionamento maior na parte externa por estarem submetidas a um processo de conformação executada pelo ressalto.
O ângulo final (α 1) foi medido após o ensaio dos 5 CP’s através do projetor de perfil, a Tabela 5 dispões a média final e o resul tado do fator de retorno elástico (K) determinado pela equação
6. Os dados para os cálculos são as médias dos valores coletados do ângulo final (α 1) e para o ângulo inicial (α 0) foram medidos durante os ensaios antes da remoção da carga, onde o valor pre dominou a 90°, esta condição é validada em função do projeto do
ferramental estar com o punção alinhado com o prensa chapas e não haver a folga do dobrador lateral perante a chapa.
O sentido de orientação da laminação de chapas possui influ ência no processo de dobramento, quando executado o mesmo no sentido de laminação a 0° o alinhamento da dobra estará perpendi cular as fibras, com isto haverá maior resistência no dobramento e maior retorno elástico. No entanto, para a orientação de laminação 90° ocorre o efeito contrário, pois o dobramento está paralelo as fi
bras [28]. Ademais, nos resultados encontrados é possível constatar que com a utilização do punção com ressalto evidência um fator K maior que a utilização do punção reto, que resulta em um menor retorno elástico no dobramento [11], [15], [17].
Na Tabela 6 está apresentado o valor teórico do retorno elás tico determinado pela equação 7. Para a determinação do mesmo, foi adotado o módulo de elasticidade do aço baixo carbono de E = 210GPa [30], a utilização da equação 8 para o cálculo do
momento e a equação 7 para encontrar a força de dobramento considerando o fator K s = 1,5 [16], demais parâmetros dos resulta dos encontrados estão sendo apresentados na Tabela 7.
Por meio da Tabela 8 e Figura 7, pode-se visualizar um com parativo dos resultados do fator K experimental obtido pela equa ção 6 e pelos resultados teóricos, através da equação 7 utilizando o dado de entrada da força pela equação 5 [16]. Observa-se que, os valores experimentais ficaram próximos aos valores teóricos calculados, surgindo um erro relativo de 0,2% a 0,7%.
Ao avaliar a deformação relativa (ε) no lado da fibra externa do dobra mento, conclui-se que os valores medidos no ensaio quando comparados com os dados teóricos obtidos pela equação 1 apresentam uma variação máxima de 9%, em contrapartida a equação 2 obteve 17,5 % quando com parados com valores medidos no ensaio. Já para avaliação da deformação verdadeira (φ), o valor experimental ficou muito próximo da equação 3, sendo a variação máxima de 0,7[-] um valor menor quando analisado os re sultados obtidos pela equação 4, sendo 0,47. Dessa forma, pela aproxima ção dos resultados experimentais nas equações 1 e 3, compreende-se que o processo de dobramento gerou um comportando de deformação assimétri ca, pelo fato das equações consideram a variação da posição da linha neutra (LN). Além disso, averiguou-se que tanto no processo de dobramento com punção sem e com ressalto a deformação sempre gerou um valor maior no sentido de laminação 90°, devido a este sentido possuir menor resistência ao dobramento e maior deformabilidade.
Diante do exposto, na avaliação experimental compreendeu duas situações, no processo de dobramento o retorno elástico se torna menor sempre no sentido da laminação de 90° e a utilização do processo de dobramento em L com ressalto no punção restringe o efeito do retorno
elástico devido a redução da região deformada plasticamente localizada na dobra da chapa.
Com a utilização do dado de entrada da força pela equação 5, entende-se que é adequada no processo de dobramento em L, pelo fato dos resultados obtidos do fator K gerado pela equação 7, que quando comparados com dados coletados experimentalmente apresentaram um erro relativo menor de no máximo 0,7%.
Contudo foi possível comprovar pelos métodos analíticos e expe rimentais o processo de dobramento com o ressalto presente no punção reduz o retorno elástico, sendo um método que possa ser adotado em projetos para restringir o retorno elástico.
[1] L. Schaeffer, R. M. Nunes, and A. M. BRITO, Tecnologia da estampa gem de chapas metálicas, 1st ed. Porto Alegre: Impressa Livre, 2017.
[2] B. K. dos SANTOS and M. L. de QUADROS, Processo de conforma ção. Porto Alegre: SAGAH, 2018.
[3] G. E. Dieter, Metalurgia Mecânica, 2nd ed. Rio de Janeiro: Ganabara Koogan S.A., 1981.
[4] C. S. KIMINAMI, W. B. DE CASTRO, and M. F. DE OLIVEIRA, Introdução aos processos de fabricação de produtos metálicos. São Paulo: Blucher, 2013.
[5] H. Park, S. J. Kim, J. Lee, J. H. Kim, and D. Kim, “Delamination beha vior analysis of steel/polymer/steel high-strength laminated sheets in a V-die bending test,” Int. J. Mech. Sci., vol. 173, p. 105430, 2020, doi: 10.1016/j. ijmecsci.2020.105430.
[6] Y. M. Huang and D. K. Leu, “Effects of process variables on V-die bending process of steel sheet,” Int. J. Mech. Sci., vol. 40, no. 7, pp. 631–650, 1998, doi: 10.1016/S0020-7403(97)00083-0.
[7] Ö. Tekaslan, U. Şeker, and A. Özdemir, “Determining springback amount of steel sheet metal has 0.5 mm thickness in bending dies,” Mater. Des., vol. 27, no. 3, pp. 251–258, 2006, doi: 10.1016/j.matdes.2004.10.006.
[8] L. Wang, G. Huang, H. Zhang, Y. Wang, and L. Yin, “Evolution of springback and neutral layer of AZ31B magnesium alloy V-bending under warm forming conditions,” J. Mater. Process. Technol., vol. 213, no. 6, pp. 844–850, 2013, doi: 10.1016/j.jmatprotec.2013.01.005.
[9] R. Kazan, M. Firat, and A. E. Tiryaki, “Prediction of springback in wipe-bending process of sheet metal using neural network,” Mater. Des., vol. 30, no. 2, pp. 418–423, 2009, doi: 10.1016/j.matdes.2008.05.033.
[10] W. Phanitwong and S. Thipprakmas, “Development of anew sprin g-back factor for a wiping die bending process,” Mater. Des., vol. 89, pp. 749–758, 2016, doi: 10.1016/j.matdes.2015.10.031.
[11] Y. E. Ling, H. P. Lee, and B. T. Cheok, “Finite element analysis of springback in L-bending of sheet metal,” J. Mater. Process. Technol., vol. 168, no. 2, pp. 296–302, 2005, doi: 10.1016/j.jmatprotec.2005.02.236.
[12] M. R. Jamli, A. K. Ariffin, and D. A. Wahab, “Incorporating feedforward neural network within finite element analysis for L-bending springback prediction,” Expert Syst. Appl., vol. 42, no. 5, pp. 2604–2614, 2015, doi: 10.1016/j.eswa.2014.11.005.
[13] J. Y. Lee, F. Barlat, and M. G. Lee, “Constitutive and friction modeling for accurate springback analysis of advanced high strength steel sheets,” Int. J. Plast., vol. 71, pp. 113–135, 2015, doi: 10.1016/j.ijplas.2015.04.005.
[14] D. Zhang, Z. Cui, X. Ruan, and Y. Li, “An analytical model for predicting springback and side wall curl of sheet after U-bending,” Comput. Mater. Sci., vol. 38, no. 4, pp. 707–715, 2007, doi: 10.1016/j.commats ci.2006.05.001.
[15] M. Jafari, M. Lotfi, P. Ghaseminejad, M. Roodi, and R. Teimou ria, “Numerical control and optimization of springback in L-bending of magnesium alloy through FE analysis and artificial intelligence,” Trans. Indian Inst. Met., vol. 68, no. 5, pp. 969–979, 2015, doi: 10.1007/s12666015-0535-7.
[16] J. RODRIGUES and P. MARTINS, Tecnologia Mecânica: Tecnologia da deformação plástica - aplicações industriais, vol. 2. Lisboa: Escolar, 2005.
[17] C. C. Kuo and B. T. Lin, “Optimization of springback for AZ31 magnesium alloy sheets in the L-bending process based on the Taguchi method,” Int. J. Adv. Manuf. Technol., vol. 58, no. 1, pp. 161–173, 2012, doi: 10.1007/s00170-011-3373-8.
[18] L. Schaeffer, Manufatura por conformação mecânica, 1st ed. Porto Alegre: Impressa Livre, 2016.
[19] G. M. Barbosa, “Processo de dobramento de chapas metálicas,” Exacta, vol. 7, no. 1, pp. 109–120, 2009.
[20] K. GRÜNING, Umformtechnik, 4th ed. Braunschweig: Springer-Ver lag, 2013.
[21] K. LANGE, Umformtechnik: Handbuch für Industrie und Wissens chaft, 3rd ed., vol. 3. Berlin: Springer-Verlag, 1990.
[22] K. Ahn, “Plastic bending of sheet metal with tension/compression asymmetry,” Int. J. Solids Struct., vol. 204–205, pp. 65–80, 2020, doi: 10.1016/j.ijsolstr.2020.05.022.
[23] M. valentim da silva Fress, “Avaliações sobre o processo de dobramento do aço NBR 6656 LNE 380,” Dissertação (Mestrado em Engenharia de Minas, Metalúrgica e de Materiais) - Universidade Federal do Rio Grande do Sul, Porto Alegre, 2017.
[24] ASSOCIAÇÃO BRASILEIRA DE NORMAS TÉCNICAS, “ABNT NBR 6892-1: Materiais metálicos - Ensaio de Tração Part1: Méto do de Ensaio a Temperatua Ambiente,” ABNT, Rio de Janeiro, 2013.
[25] Associação Brasileira de Normas Técnicas, “ABNT NBR 13284: Meta lográfica Procedimento Preparação de corpos de prova para análise,” ABNT, Rio de Janeiro, 1995.
[26] T. D. S. Cavalcante, P. P. Rebouças Fillho, V. H. C. Albuquerque, and J. M. R. S. Tavares, “Aplicação de Técnicas de Processamento e Análise de Imagem na Análise Automática da Quantidade e do Tamanho do Grão em Imagens Metalográficas,” Congreso de Métodos Numéricos en Ingenieria. Congreso de Métodos Numéricos en Ingenieria, Barcelona, pp. 1–9, 2009.
[27] V. L. De Araújo Freitas, V. H. C. d. Albuquerque, E. de M. Silva, A. A. Silva, and J. M. R. S. Tavares, “Nondestructive characterization of microstructures and determination of elastic properties in plain carbon steel using ultrasonic measurements,” Mater. Sci. Eng. A, vol. 527, no. 16–17, pp. 4431–4437, 2010, doi: 10.1016/j.msea.2010.03.090.
[28] D. K. Leu, “A simplified approach for evaluating bendability and springback in plastic bending of anisotropic sheet metals,” J. Mater. Process. Technol., vol. 66, no. 1–3, pp. 9–17, 1997, doi: 10.1016/S09240136(96)02453-3.
[29] Z. Marciniak, J. Duncan, and J. Hu, Mechanics of sheet metal forming, 2nd ed. London: Elsevier, 2002.
[30] W. D. Callister and D. G. Rethwisch, Ciência e engenharia de mate riais: uma introdução, 8th ed. Rio de Janeiro: LTC, 2012.
[31] Folle, L.F.; Caetano dos Santos Silva, B.; Sousa de Carvalho, M.; Zamorano, L.G.S.; Coelho, R.S. Evaluation of the Friction Coefficient for TRIP1000 Steel under Different Conditions of Lubrication, Contact Pressure, Sliding Speed and Working Temperature. Metals 2022, 12, 1299. https://doi.org/10.3390/met12081299
MS.c Cristian Luiz Onzi, Federal University of Rio Grande do Sul, Brazil, onzi.engenharia@gmail.com
Mechanical Engineer Josimar Santos, Federal University of Rio Grande do Sul, Brazil
Prof. Dr. Ing. Lirio Schaeffer, Federal University of Rio Grande do Sul, Brazil
Erlifas Moreira Rocha; Prof. Dr.-Ing. João Henrique Corrêa de Souza; Jocilei Oliveira (apoio)
As indústrias estão continuamente na busca por melhorar sua competitividade, procurando métodos eficazes para a redução de custos e do tempo dos processos de fabricação de seus produtos e processos. Um dos métodos de inovação de processo das empresas é a troca de um processo convencional de produção por um método não convencional mais competitivo. Nesse contexto, com o apoio das Empresas Tecumseh do Brasil, AutoForm e TechnNOVA, neste trabalho busca-se iniciar um estudo da viabilidade de aplicação do processo de hidroconformação de chapas em substituição ao processo convencional de estampagem, para aplicações em carcaças de compressores herméticos, com o auxílio de simulações numéricas. A hidroconformação é considerada um processo de conformação não convencional. O processo tem sido utilizado por muitas empresas, em nichos específicos, devido a determinadas características que podem trazer benefícios ao processo, como por exemplo: melhor aproveitamento da conformabilidade do material, excelente qualidade superficial da peça, ótima precisão dimensional, redução do retorno elástico e tensões internas no material, redução do custo de ferramentas através da redução do número de estágios do processo. Os resultados obtidos ao longo desse projeto, demonstraram algumas vantagens da utilização da tecnologia, principalmente para baixos e médios volumes de produção.
Palavras-chave — Embutimento hidromecânico; Hidroconformação de chapas; Estampagem; Simulação; Com pressores herméticos; Conformabilidade;
MODELO NUMÉRICO DE PROCESSO DE HIDROCONFORMAÇÃO APLICADO EM CARCAÇAS DE COMPRESSORES HERMÉTICOS
As indústrias de transformação têm por rotina a pro cura por métodos eficazes para a redução de custos e do tempo dos processos de fabricação, desde a fase do projeto inicial ou no contexto de protótipos de pesquisas e desenvolvimento com intuito de avaliar uma possível inovação. Atividades de pesquisa e desenvolvimento em nível de processo são cada vez mais rotineiras, visando manter um ótimo nível de competitividade da empresa. As concorrentes de qualquer ramo industrial não podem contar com inovação somente através de projetos de longa duração, desperdiçando tempo valioso. Inovações precisam ser realizadas constantemente dentro da linha durante sua operação, e uma linha que não passa por transformações internamente acaba correndo o risco de ser des qualificada perdendo sua competitividade. Em geral algumas alternativas são:
• Redução do número de componentes de um determinado produto.
• Substituição do processo de fabricação com o objetivo de redução do número de etapas e aumento da robustez do processo.
A hidroconformação é considerada um processo de con formação não convencional. O processo têm sido utilizado em determinadas aplicações por oferecer algumas vantagens em
relação à estampagem convencional, como por exemplo: melhor aproveitamento da conformabilidade do material, excelente qualidade superficial da peça em relação ao processo convencio nal, ótima precisão dimensional, redução do retorno elástico do material, redução do custo de ferramentas (redução do número de estágios do processo, como foi dito anteriormente) e entre outros aspectos positivos que podem ser alcançados. Porém, assim como todo o processo, este possui limitações. Entre as maiores limitações do processo estão maior força de prensa necessária, menor produtividade em relação ao processo de estampagem convencional e gestão do fluido hidráulico utili zado (água com aditivos). Do ponto de vista industrial as duas grandes possibilidades que os processos de hidroconformação oferecem são:
• Redução do número de componentes de um sistema (uma peça mais complexa ao invés de várias peças simples) e con sequentemente redução do número de operações de união.
• Redução do número de etapas de fabricação e do investi mento em ferramental.
O objetivo deste trabalho foi avaliar a viabilidade da subs tituição do processo atual de estampagem convencional por hidroconformação, mais exatamente embutimento hidromecâ nico, na fabricação de carcaças de compressores herméticos da empresa Tecumseh do Brasil. O trabalho contou com o apoio
das empresas Autoform do Brasil com o sistema CAE, Techn NOVA PD&I no apoio para o desenvolvimento do modelo e da própria Tecumseh que disponibilizou os componentes reais e dados do processo.
Subsidiária da Tecumseh Products Company (EUA), a Tecum seh do Brasil (TdB) foi fundada em novembro de 1972 e iniciou suas atividades produtivas em 1973. Está localizada em São Carlos, na região mais próspera do Estado de São Paulo (Bra sil). A cidade é conhecida nacionalmente pelos seus importantes polos industriais, científico e tecnológico. Possui um moderno parque industrial com 803 mil m² de área total e 145 mil m² de área construída. Suas duas plantas estão integradas na produ ção de compressores herméticos para refrigeração doméstica, comercial e condicionadores de ar; produção de componentes elétricos e eletrônicos; produtos fundidos. Os produtos Tecum seh são projetados para promover o bem-estar dos usuários e são encontrados em produtos como refrigeradores, congeladores, expositores comerciais, bebedouros, condicionadores de ar, segmento automotivo entre outros (conforme a Figura 1).
A Tecumseh tem investido em laboratórios de engenharia, pesquisa e desenvolvimento na América do Norte, Europa, América do Sul e Índia, além de parcerias com centros de pesquisa e desenvolvimento em universidades de todo o mundo. Estes centros não são apenas responsáveis em aplicar soluções de produto, as universidades parceiras também fazem pesquisa de ciências biológicas sobre como seus produtos se relacionam
com o ser humano e com o meio ambiente.
Atualmente oferece uma linha completa de compressores herméticos para condicionamento de ar residencial e especia lizado, refrigeradores e congeladores residenciais e refrigera ção comercial. Mas a sua especialidade não se resume a isso; também oferece uma linha completa de unidades condensadoras para uso interno ou externo, evaporadores, bombas de calor, sistemas completos de refrigeração e serviço autorizado de com ponentes de reposição.
2.1 Conformação de chapas metálicas De acordo com Souza [15], os processos elementares de confor mação de chapas são: embutimento, estiramento, dobra e corte. Essa classificação se baseia no mecanismo que gera a deforma ção plástica na materia-prima, ou seja tração-compressão (no plano), traçã-tração (no plano), tração-compressão (na espessu ra) e cisalhamento, respectivamente.
As tecnologias envolvidas no desenvolvimento de proces sos de conformação de chapas abrangem diferentes campos do conhecimento, razão pela qual o domínio desta arte exige sempre uma abordagem multidisciplinar. As mais importantes áreas de conhecimento que compõe o universo dos processos de conformação de chapas podem ser verificadas na Figura 2.
Em relação a Figura 2, podemos destacar fortemente os termos “Mecânica dos meios contínuos” e “Mecânica compu tacional”. Na mecânica dos meios contínuos, destaca-se não somente a teoria da plasticidade dos materiais, mas principal
mente a definições de conformabilidade da chapa. Já a mecânica computacional se tornou um elemento vital nas últimas décadas, não sendo mais possível desenvolver produtos estampados com a velocidade, qualidade e custo necessário no mercado hoje sem o uso de sistemas CAE. No contexto brasileiro, onde o custo da matéria-prima determina uma fração bastante elevada do custo total da peça, isso se justifica mais ainda.
Finalmente, podemos destacar como pontos positivos da atual tecnologia de conformação de chapas baseada em sistemas CAE para simulação e gêmeos digitais aplicados à manufatura:
• Excelente resistência dinâmica.
• Possibilidade de fabricar formas relativamente complexas.
• Altas taxas de produção.
• Alto rendimento da matéria-prima.
• Alta qualidade superficial e dimensional e de forma do componente final.
• Aumento da resistência do material devido à conformação.
• Materiais metálicos são totalmente recicláveis.
O processo de hidroconformação teve seus primeiros desen volvimentos em meados de 1940, praticamente no início da Segunda Guerra Mundial. Suas aplicações eram praticamente destinadas somente à indústria aeronáutica alemã e alguns cam pos de aplicação, tornando, de certa forma, restritas a alguns
campos específicos devido a direitos particulares de desenvolvi mento tecnológico.
Segundo Ramalheira [10], uma das primeiras patentes desenvolvidas do processo, realizada por Parker, em 1903, passa a descrever um protótipo para conformar elementos com geometrias ocas em serpentina para equipamentos de caldeiras a vapor. Nesta patente poderia ser identificada os elementos de destaque da hidroconformação de tubos: um metal maleável com determinadas conformações, aplicado na cavidade inferior da matriz. A patente demonstrava as vantagens do processo: mão de obra aplicada, materiais que eram desperdiçados de uma forma reduzida e melhoria da uniformidade das dimensões. Com o passar dos anos, novas patentes foram aparecendo: uma delas foi a de Gray (de 1940), onde ele descreve um protótipo para a fabricação de acessórios em “tê” de material forjado. A diferença é que, nessa patente, os detalhes eram evidentes, além da matriz e do fluído na conformação, a alimentação axial das extremidades do material (o que permitia fabricar produtos com ramificações) a baixa pressão e o aumento da pressão até um valor máximo para se obter a conformação.
Recentemente, em torno de 1990, a hidroconformação passou a ganhar espaço em muitas áreas de aplicações indus triais, e chamou bastante a atenção de grandes montadoras automobilísticas. Nos processos de aplicações industriais de hoje, as empresas automotivas, bem como diversas indústrias que produzem máquinas e equipamentos de aplicações diversas,
buscavam processos inovadores para redução de peso e aumento da resistência mecânica de estruturas. Com o desenvolvimento de aços avançados de alta resistência processos de hidroconfor mação renasceram como possíveis alternativas para a fabricação de peças com geometrias complexas e alta precisão dimensional.
A hidroconformação é um processo de conformação mecânica, plástica, de um material com caráter dúctil (normalmente cha pas ou tubos) através de uma aplicação de pressão hidrostática que é exercida na parte interior de uma determinada peça. Essa pressão hidrostática é exercida por um fluído que passa a ser injetado no interior da peça, isso causa uma expansão do mate rial da peça em função dos limites dimensionais que a matriz de conformação passa a conceder no processo.
Desta maneira, há a possibilidade de se obter peças com a maior variedade possível em questões de geometrias. Uma peça pode haver zonas de geometrias bastante variadas, portanto a uma ocorrência de seções com variações. De acordo com Zhang [21], a hidroconformação é dividida em dois processos distintos, e podem ser divididos (Figura 3) de acordo com:
• Hidroconformação de tubos;
• Hidroconformação de chapas planas;
Em ambos os processos, o equipamento é composto por uma ferramenta ou matriz de conformação, uma prensa hidráulica, e um sistema de intensificação de pressão no fluído de trabalho, sendo que na hidroconformação de chapas é possível eliminar o sistema de intensificação de pressão, substituindo-o pelo próprio efeito do martelo da prensa sobre o fluido. A pressão hidrostática é o suficiente para realizar deformação plástica na peça e para fazer com que ela adquira forma da cavidade da matriz. O processo pode ser concebido de forma a realizar ainda a perfuração de ranhuras e de furos, enquanto ele ainda se encontra a elevadas pressões.
Uma vantagem da hidroconformação é que permite fazer numa só operação em uma peça inteira, a qual, em outros pro cessos como a estampagem convencional, seria obtida a partir de várias operações de conformação de subcomponentes. É o caso de algumas peças de carroçaria e de chassis de veículos. A redução do número de processos de produção que a hidrocon formação traz como inovador, torna os custos de produção mais viável, o que é um grande aspecto decisivo nas indústrias que implementam tal processo. Além disso, as peças são mais leves, pois podem ser fabricadas com materiais de menor espessura, e possuem maior integridade estrutural, pois não há descon tinuidades ou regiões de sobreposição/ união de componentes para a ligação. As peças são assim produzidas com economia de mão-de-obra, de matéria-prima e com uma melhor relação resistência mecânica/peso.
Em geral, o processo de hidroconformação de chapas pode ser dividido em dois grandes grupos, sendo eles:
• Hidroconformação de chapas com membrana de borracha (processo que separando o fluido do “blank”).
• Hidroconformação de chapas sem membrana de borracha (realizado com a ação direta do fluido contra o “blank”) –sendo o exemplo mais importante o muitas vezes citado em bibliografias como “Embutimento Hidromecânico”.
Processos de hidroconformação de chapa permitem atingir uma maior relação de embutimento, representado comumente na literatura alemã como β, e calculado como o diâmetro máximo do blank, DBmax dividido pelo diâmetro do punção Dp. Na estam pagem convencional o βmax fica em torno de 2,1 para condições controladas. Com o embutimento hidromecânico é possível alcançar βmax de até 2,5. Isso se reflete em um aumento signifi cativo na profundidade de estampagem (até 1,5 vezes mais).
Nesse processo utiliza-se uma câmara com o fluído de traba lho (água). A câmara (ou tanque) é selada por um diafragma elástico (elastômero), sendo esse o principal componente que terá o contato direto entre a chapa, conforme a Figura 4. O grande desafio desse processo está diretamente relaciona do com o fato de que a membrana de borracha resiste a um número limitado de operações. De acordo com Zhang [21], essa tecnologia tem sido aplicada com bastante frequência em peças automotivas para produção protótipos e pequenas séries. Torna-se especialmente adequada para a conformação de peças que são fabricadas a partir de chapas metálicas nem etapas de desenvolvimento de protótipos ou peças de pequena escala de produção.
Nesta variante do processo de hidroconformação de chapas, a membrana de borracha é dispensada. De acordo com Zhang [21], a pressão da água passa a tocar diretamente no “blank”, sendo o fluido contido através de uma vedação instalada no anel da matriz. O processo se dá da seguinte maneira: Quando o punção começa a realizar o seu ciclo, o volume da câmara onde contém o fluído começa a diminuir e, consequentemente, cargas de caráter compressivo geradas através do fluido come çam a conformar a superfície do material, o mesmo começa a copiar a geometria do punção e passa a adquirir o seu formato (Figura 5).
Interessante no embutimento hidromecânico é o fato de não ser necessária a instalação de um intensificador de pressão na câmara do fluido. A pressão pode simplesmente ser controlada por uma válvula proporcional ou mesmo uma válvula limitadora a de pressão, já que o movimento do punção ao pressionar o fluido gera um aumento natural da pressão do fluido.
Em relação ao aumento da conformabilidade representado pela maior relação de embutimento, esta se dá graças ao maior atrito entre punção e chapa, já que a pressão do fluido está constantemente empurrando a última contra o punção, fazen do com que exista maior área de apoio para puxar o material através da matriz. Adicionalmente, o fluido comprimindo a chapa evita a formação de rugas e retarda o início de instabi lidades plásticas, possibilitando a fabricação de peças cônicas impossíveis de serem fabricadas com estampagem convencio nal em uma única etapa. Este é também o motivo pelo qual se necessita da geometria da peça somente no lado do punção. Isso significa uma economia em termos de tempo de usina gem. Por outro lado, pressão excessiva pode causar problemas durante o processo, conforme ilustrado na Figura 6.
Além do ilustrado na Figura 6, deve-se destacar também a relação entre força do prensa chapas e a pressão do fluido. Da mesma forma que um processo de estampagem convencional, a força do prensa-chapas controla o fluxo de material durante o processo. No embutimento hidromecânico o prensa chapas tem a responsabilidade de manter o fluido contido no reci piente de pressão. Uma queda na força pode gerar vazamento de pressão e rompimento da peça, o que pode ser verificado na Figura 7.
Para direcionar o estudo do presente trabalho, foi estabeleci do um diagrama geral da metodologia aplicada, ele pode ser verificado na Figura 8, onde, através dele, foi estabelecido os critérios de análises.
Em primeiro lugar, foi estabelecido duas linhas de meto dologias, sendo elas:
1) Metodologia laboratorial;
2) Metodologia de simulações numéricas;
O objetivo da divisão mencionada foi devido os seguintes fatos: Antes de realizar as simulações dos processos de fabricação, foi necessário ter o conhecimento do processo de estampagem atual das carcaças dos compressores; após a análise de todo o processo, foi coletada a carcaça da etapa em que seria realizada a simulação e, com isso, foi caracterizado o material para a valida ção do afinamento. Com a análise comparativa entre a simulação convencional e a prática, poderíamos então validar o processo de hidroconformação e analisar a viabilidade de um processo em relação ao outro.
Após o recolhimento da carcaça do compressor da etapa de es tampagem em que seria simulada posteriormente, para a análise laboratorial, foi preparado um diagrama (Figura 9). O objetivo dessa etapa foi a análise da espessura ao longo da carcaça (visando o percentual de afinamento das regiões).
Figura
Figura
Antes da caracterização do material da carcaça, foi analisado o processo convencional de estampagem. Por questões de sigilo interno, não serão divulgados os estágios de estampagem. A es tampagem das carcaças dependerá do planejamento do projetista em relação ao punção ou matriz do processo; algumas empresas conseguem cortar o blank e iniciar o primeiro repuxo em uma única etapa, o que passa a reduzir um gasto adicional de maqui nário e diversos outros fatores envolvidos.
Para validar a simulação convencional de estampagem, a carcaça do compressor foi cortada para a análise da variação do afina mento desde a tampa até regiões mais críticas. Foram separadas 2 amostras por carcaça, sendo elas:
1) Corte da carcaça para análise da espessura da tampa até a região do ressalto do compressor;
2) Corte da carcaça para análise da espessura da tampa até a região central do compressor (passando pelos pés);
Os locais de corte na carcaça podem ser verificados na Figura 10.
As amostras cortadas para a verificação foram separadas e podem ser analisadas de acordo com a Figura 11.
Após os cortes realizados na carcaça, as amostras foram
separadas em 11 regiões (Figura 12a), onde cada região foi realizada 3 medições em sua espessura; após as medições, foram coletados as médias e o desvio padrão; o objetivo seria a análise do comportamento/ variação da espessura em regiões mais espessas e em regiões consideradas “críticas” na simulação.
As imagens foram retiradas de uma lupa da marca OLYM PUS SZ – ET JAPAN em um aumento de 6,7x, após isso foi utilizado o software Digimet Plus 5G para a calibração e medição das espessuras. Na Figura 12 (b) pode ser analisada as 11 regiões de uma amostra.
Neste tópico será abordada a metodologia referente as simu lações numéricas realizadas. Toda a geometria estampada foi importada no software Autoform R10. Serão apresentadas todas as particularidades das análises, bem como as imagens obtidas em relação aos parâmetros aplicados. As análises finais de cada processo (afinamento, curvas CLCs etc.), serão demonstra dos nos resultados e discussões. Esse projeto possui um termo de sigilo com a empresa Tecumseh do Brasil, devido a isso, o estudo realizado do processo de estampagem convencional e hidroconformação apresentado aqui foi referente apenas a
carcaça representada na Figura 10. Assim como foi realizado na metodologia experimental, esse processo metodológico para o início da simulação precisou ser realizado um diagrama para a estruturação do projeto. O diagrama geral utilizado nesta etapa, pode ser confirmando através da Figura 13.
Em relação ao diagrama demonstrado na Figura 13, o pro cesso de simulação consistiu em 3 análises distintas, sendo elas:
1) Processo convencional de estampagem: utilizado hoje na produção.
2) Processo convencional de estampagem alternativo: consiste na mesma geometria utilizada na hidroconforma ção, porém simulada de forma convencional para fins de comparação.
3) Processo de hidroconformação por embutimento hidromecânico: geometria consiste em etapa preliminar à calibração da geometria final, eliminando-se, porém, uma das etapas de fabricação através do processo convencional.
Para a construção dos modelos de simulação do processo convencional foi importado ao software a geometria final da carcaça do compressor hermético, cujos complexos detalhes geométricos tornam impossível a conformação em uma única etapa de estampagem (ver Figura 14).
Para a simulação, são informados dados relevantes como a geometria da peça e dados do material como resistên cia mecânica, anisotropia e coeficiente de encruamento. O
material utilizado não será divulgado devido as questões de sigilo. Foi utilizado o modelos de curva de escoamento de Swift e envelope de escoamento anisotrópico de Banabic 2005. Com estes dados o software realiza o cálculo da conformação, apresentando resultados como regiões críticas de conforma ção, variação na espessura, retorno elástico, curva limite de conformação etc.
Utilizando os procedimentos do software Autoform, foram definidas as geometrias das ferramentas, e sua cinemática. Foi utilizada a geometria do blank conhecida previamente. As configurações de matriz, prensa-chapas e punção para a etapa intermediária de conformação podem ser visualizadas na Figura 15.
Para a realização da simulação do processo convencional alternativo, o procedimento inicial foi adotado de acordo com o processo convencional, ou seja, o material e a geometria importada foram os mesmos. A diferença foi uma alteração
realizada no raio da tampa da carcaça do punção e da matriz. Esta se fez necessária devido a prováveis problemas de vedação que iriam ocorrer no processo de hidroconformação, na fase final de fechamento da ferramenta, já que o raio da matriz era excessivamente grande. A modificação pode ser vista na Figura 15.
Para a modelagem numérica do processo de hidroconforma ção, o material da carcaça e a geometria importada foram iguais aos processos anteriores. A particularidade desse pro cesso está relacionada com o procedimento do embutimento; uma vez que o embutimento hidromecânico não necessita de uma matriz definida, esse processo pode ser apenas um tanque com um fluído de trabalho (nesse caso a água); na modelagem realizada, foi realizado um “tanque” com a geometria final da peça apenas para o reaproveitamento das ferramentas anterio res. Podemos ressaltar que não há a necessidade da modelagem da matriz.
O processo convencional alternativo apresentado anterior mente, foi fundamental para a modelagem do processo de hi droconformação. Uma vez obtido resultados satisfatórios com o reajuste do raio da geometria, conseguimos aprimorar essas condições para a modelagem desse processo não convencional.
No processo de hidroconformação de chapas, caso a geometria do punção e da matriz fossem de acordo com o pro cesso convencional (demonstrado na Figuras 15), o processo ocorreria problemas de vedação e, consequentemente, parte do fluído no tanque seria perdido e, também, acarretaria em uma perda de pressão interna (caso o processo fosse com fluído ativo); essa consequência foi demonstrada na Figura 7.
A Figura 16 (a) se refere ao processo com a geometria sem alteração, nota – se que o fluído tenderá a sair do tanque na mesma pressão devido a abertura excessiva da geometria. Na Figura 16 (b), o processo com o raio ajustado permite uma vedação mais segura.
4.1.1 Análise da redução de espessura ao longo da carcaça Como foi abordado na metodologia, foram cortadas 2 amos tras na carcaça para a análise da variação da espessura ao longo de regiões de acordo com:
a) Região da tampa do compressor até a região central basal (passando pelo ressalto do compressor);
b) Região da tampa do compressor até a região central basal (passando pelo pé do compressor);
Após o corte, foram selecionadas 11 regiões de cada amostra, onde em cada região foram efetuadas 3 medições. Após a realização das 3 medições em cada região, foi realizado uma média e verificado o afinamento médio de cada região em relação a espessura nominal da chapa. Na Figura 17 é possível verificar os resultados obtidos.
Em relação à região que inicia a partir da tampa do
compressor e chega na região dos pés (Figura 17 - esquerda), podemos verificar um afinamento real de até 40,79% em relação a espessura nominal da chapa. Já na região do ressalto do compressor (Figura 17 - direita) o afinamento máximo encontrado é de apenas 25,73%.
4.2.1 Curvas Limite de Conformação (CLC) e redução de espessuraProcessos convencional e convencional alternativo
As simulações dos processos de embutimento convencional demonstraram regiões com alta criticidade e, que poderiam ser um problema futuramente. Essas regiões se encontravam principalmente nos pés do compressor. O processo convencio nal alternativo (processo com ajuste no raio da geometria da carcaça) demonstrou melhor aproveitamento da conformabili dade do material em relação ao processo convencional, apesar do raio reduzido. Isso demonstrou que o atrito na região do raio provavelmente era muito elevado. As CLCs do processo convencional pode ser vista na Figura 18a, e do processo con vencional alternativo na Figura 18b.
As espessuras nas regiões de alta criticidade do processo convencional ficaram na faixa de 30% a 40% menores em relação a espessura nominal, nesse caso, nas regiões dos pés (Figura 19a). Já no processo convencional alternativo, os valo res na região dos pés ficam na faixa de 20% a 33% em relação a espessura nominal (Figura 19 b), o que demonstra uma melhoria do processo.
No embutimento hidromecânico é necessário determinar uma pressão máxima durante o processo. Algumas simulações foram realizadas com objetivo de encontrar o valor ideal de pressão de trabalho. Um resumo dos resultados pode ser visto na Figura 20, que representa as CLCs correspondentes a qua tro valores de pressões.
O melhor resultado foi obtido para 10 bar (Figura 20a), pois representa uma condição mais segura de conformação. Na Figura 20d é reproduzido o caso extremo de explosão da chapa devido à alta pressão na câmara.
Posteriormente foram avaliados os valores de afinamento das regiões ao longo da carcaça. A Figura 21 representa os valores de espessura para diferentes pressões. Percebe-se um melhor resultado a 10 bar. Neste caso os valores na região dos pés da carcaça tiveram redução na faixa de 20% a 25% em relação a espessura nominal, o que representa um avanço em relação ao processo convencional. Os valores de espessura vão reduzindo gradativamente com o aumento da pressão. A Figura 21d ilustra o momento em que a chapa colapsa sob a excessiva pressão.
Como foi mencionado na revisão, o processo de embutimento hidromecânico, possui suas limitações em relação à pressão de trabalho. Quando o blank é submetido a altas pressões, a pressurização excessiva na câmara pode vir a elevar o material contra a direção de embutimento, isso provocará uma restrição do material e impedirá o fluxo de material para a conformação da geometria desejada (vide Figura 6 da revisão). Esse fenô meno característico do processo foi verificado no estudo. Na Figura 22, vistas laterais do processo ilustram a sua formação em função da pressão de trabalho.
No resultado apresentado na Figura 22d a geometria que está submetida a 50 bar gerou colapso da chapa após a elevação excessiva do material. Isso demonstra a necessidade de con trolar tanto o valor máximo com o valor mínimo da pressão durante o processo.
Os resultados obtidos durante a investigação demonstraram as seguintes afirmações e conclusões:
• O uso do processo processo de hidroconformação permi te usar melhor a conformabilidade do material. Isso ficou demonstrado através dos menores valores de afinamento em relação ao processo convencional.
• O processo proposto permitiu ainda eliminar uma etapa de fabricação durante a estampagem da carcaça do compressor.
• Melhores resultados foram obtidos com uma pressão de 10 bar (com regiões críticas demonstrando um afinamento de apenas 20%).
• Com o processo de hidroconformação foram obtidos valores de redução de espessura de apenas 20% nas regiões críticas, contra 40% no processo convencional, podendo ser uma alter nativa para a Tecumseh usufruir da tecnologia futuramente.
• O uso do Autoform como ferramenta de análise permitiu uma análise detalhada e abrangente dos prós e contras do processo proposto.
Em especial, os autores desse trabalho agradecem a empresa Tecumseh do Brasil – Setor de P&D, por todos os recursos ofertados e disponibilidade de informações para o trabalho. Os autores agradecem também, a empresa Autoform do Brasil pelo apoio na operação de simulação e à empresa TechnNOVA PD&I pela orientação quanto à implementação do modelo de simulação para hidroconformação.
Figura 17. À esquerda, valores de afinamento obtidos na seção Tampa-Pés. À direita, valores obtidos na seção Tampa-Ressalto.
[1] American Society for Testing and Materials. Standard Test Method for Tension Testing of Metallic Materials [Metric], ASTM E 8M-04, U. S. A., 2004.
[2] AUTOFORM (FORMING REALITY). Formação de chapas metálicas. Disponível em: https://www.autoform.com/en/ glossary/sheet-metal-forming/. Acesso em: 11 dez. 2021.
[3] FARIA, Alfredo R. de; REGO, Ronnie. Introdução a mate riais e processos de fabricação: escoamento plástico. São José dos Campos: Instituto Tecnológico de Aeronáutica (ITA), s.d. 47 slides, color.
[4] FARIA, Alfredo R. de; REGO, Ronnie. Introdução a materiais e processos de fabricação: conformação de chapas. São José dos Cam pos: Instituto Tecnológico de Aeronáutica (ITA), s.d. 104 slides, color.
[5] HENKLEIN, Pedro. ANÁLISE DE ENSAIOS DE DESEM PENHO DE COMPRESSORES HERMÉTICOS DURANTE O TRANSITÓRIO. 2006. 136 f. Dissertação (Mestrado) - Curso de Pós-Graduação em Metrologia Científica e Industrial, Programa de Pós-Graduação em Metrologia Científica e Industrial, Universidade Federal de Santa Catarina, Florianópolis, 2006.
[6] LAJARIN, Sérgio Fernando. INFLUÊNCIA DA VARIAÇÃO
DO MÓDULO DE ELASTICIDADE NA PREVISÃO COM PUTACIONAL DO RETORNO ELÁSTICO EM AÇOS DE ALTA RESISTÊNCIA. 2012. 197 f. Tese (Doutorado) - Curso de Engenharia Mecânica, Departamento de Engenharia Mecânica, Universidade Federal do Paraná, Curitiba, 2012.
[7] LANGE, K. Umformtechnik – Band 3 – Blechbarbeitung. Springer – Verlag. Heidelberg, Alemanha, 1990.
[8] PORTELLA, Silvane Antonio. PROJETO E CONSTRUÇÃO DE UM SISTEMA PARA TESTES DE HIDROCONFORMA ÇÃO DE CHAPAS. 2012. 114 f. TCC (Graduação) - Curso de Engenharia Mecânica, Departamento de Engenharia Mecânica, Universidade Regional do Noroeste do Estado do Rio Grande do Sul - Unijuí, Panambi, 2012.
[9] R., Rodrigo A. Pizarro. INFLUÊNCIA DO ÓLEO LUBRI FICANTE NA TRANSFERÊNCIA DE CALOR EM UM COMPRESSOR HERMÉTICO ALTERNATIVO. 2007. 161 f. Dissertação (Mestrado) - Curso de Engenharia Mecânica, Depar tamento de Engenharia Mecânica, Universidade Federal de Santa Catarina, Florianópolis, 2007.
[10] RAMALHEIRA, Jorge Manuel Lopes. Comportamento Me cânico de Peças Hidroformadas. 2008. 125 f. Dissertação (Mestra do) - Curso de Engenharia Mecânica, Departamento de Engenharia Mecânica, Universidade do Porto, Portugal, 2008.
[11] SCHAEFFER Lirio, Conformação de Chapas Metálicas, Edi tora Imprensa Livre, Porto Alegre, 2004.
[12] SCHULER, GmbH. Metal Forming Handbook /Schuler. Berlin, Heidelberg: Springer Verlag, 1998.
[13] SOTOMAYOR, Paul Ortega. Caracterização e Simulação de Compressores Alternativos Utilizando Fluidos com Baixo Potencial de Aquecimento Global. 2013. 331 f. Tese (Doutorado) - Curso de Engenharia Mecânica, Departamento de Engenharia Mecânica, Universidade Católica do Rio de Janeiro, Rio de Janeiro, 2013.
[14] SOUZA, João Henrique Corrêa de. Processos de conformação: conformabilidade. Rio Grande: Universidade Federal do Rio Gran de (FURG), 2020. 82 slides, color.
[15] SOUZA, João Henrique Corrêa de. Processos de conformação: estampagem 1. Rio Grande: Universidade Federal do Rio Grande (FURG), 2020. 162 slides, color.
[16] SOUZA, João Henrique Corrêa de. Processos de Conformação: hidroconformação. Panambi (Rs): Unijuí, 2013. 90 slides, color. Notas de aula do curso de Engenharia Mecânica.
[17] TECUMSEH PRODUCTS COMPANY. Products. Disponí vel em: https://www.tecumseh.com/pt/sa/products/. Acesso em: 7 dez. 2021.
[18] THÖN, Ivan Lairton. DESENVOLVIMENTO DE UM SIS TEMA DE HIDROCONFORMAÇÃO EM TUBOS DE AÇO.
[19] VIEGAS, Mário João Pereira. Identificação da anisotropia de chapas metálicas com recurso a ensaios mecânicos simples. 2017. 59 f. Tese (Doutorado) - Curso de Engenharia Mecânica, Departamen to de Engenharia Mecânica, Universidade de Coimbra, Coimbra, 2017.
[20] VIEIRA, Diana. Estudo de Ferramentas FEA Comerciais na Simulação Numérica de Processos de Conformação de Chapas Metálicas. Aplicação à Indústria Automóvel. 2015. 153 f. Disserta ção (Mestrado) - Curso de Engenharia Mecânica, Departamento de Engenharia Mecânica, Instituto Superior de Engenharia do Porto, Portugal, 2015.
[21] Zhang, S. H. Developments in Hydroforming. Journal of Ma terials Processing Technology. vol. 91, pp. 236-244, 1999
[22] Quintus Technologies. Disponível em: https://quintustechno logies.com/
Erlifas Moreira Rocha, Universidade Federal do Rio Grande (FURG), e-mail: erlifas.m.rocha@hotmail.com;
Prof. Dr.-Ing. João Henrique Corrêa de Souza, FURG, TechnNOVA PD&I Ltda., e-mail: joaoh_cs@hotmail.com;
Jocilei Oliveira (apoio), Autoform do Brasil Ltda.e-mail: jocilei.oliveira@ autoform.com.br
Fundada em Genebra em 1965, a Boucledor Inc. projeta e produz fivelas e fechos para alta relojoaria e joias de luxo. Apoiada no amplo conhecimento e experiência adquiridos ao longo dos últimos 50 anos, a Boucledor desenvolve produtos de alta qualidade e atende com sucesso às demandas mais exigentes de seus clientes.
Os fabricantes de Boucledor estampam peças em pequenas e médias produções. O setor de Relojoaria Fina deve enfrentar desafios específicos envolvendo o uso
de metais preciosos. Por isso é essencial controlar o peso do flanco em gramas.
Os desafios de software são bastante numerosos:
• Dominar o projeto de ferramental (projeto direto do ferramental de préforma)
• Definição do flanco (pré-forma inicial)
sem testes físicos empíricos (otimização do material utilizado como liga e tempo de fabricação do ferramental)
• Otimização da sequência de estampagem (melhoria da estampagem ao longo do tempo)
• Custo de otimização do ferramental
• Controlar a dureza HV das peças no caso de peças “elásticas”
• Dominar a robustez do ferramental
(possibilidade de fazer manutenção preventiva)
• Engenharia reversa (no caso de ferramental antigo).
“A implementação do software
COLDFORM® nos ajudou a reduzir nossos custos de projeto e fabricação de matrizes de estampagem, reduzindo a quantidade de ferramentas em nosso processo de estampagem.
Graças à análise e simulação a montante do software, o fabricante de estampos agora pode comparar diretamente a teoria com a prática durante o projeto da cadeia de
Figura 23. Cálculo de restrições em estampos e previsão da força de ataque
estampagem, o que torna possível evitar qualquer desvio do nosso processo e se traduz em grandes economias de tempo.
Também conseguimos prolongar a vida útil de nossas ferramentas de estampagem (punções, machos, matrizes, etc.) reduzindo a quantidade de quebras, distribuindo melhor as tensões em nossas ferramentas.” Benoit Pes, chefe de Estampagem e Mecânica; e André Chaves, expert Stamp Maker BSA.
Otimiza a sequência de estampagem operacional
Todo o modelo CAD (peças e ferramental) bem como os dados técnicos internos (registro de material, condições de lubrificação) são importados para o programa COLDFORM® para simular a sequência operacional projetada.
A função «encadeamento automático» («automatic chaining») calcula a sequência na sua totalidade desde a 1ª estação até ao final sem necessidade de intervenção do utilizador. Isso produz uma economia de tempo considerável.
A simulação pode facilmente chamar a atenção para as áreas subpreenchidas.
A forma do flanco e seu corte interior podem, portanto, ser otimizados para garantir o preenchimento completo sem gerar excesso de material.
Além disso, estar ciente dos fenômenos elásticos é essencial. O cálculo com matriz deformável permite quantificar a deformação elástica do ferramental e consequentemente controlar melhor as geometrias finais. Isso garante tolerâncias estritas e limita a repetição da produção da peça final.
Controle a estampagem e gerencie os custos a longo prazo
- Simulação completa da operação de estampagem «cadeia»
- Validação numérica da taxa de preenchimento
- Validação numérica de tonelagem
- Validação numérica de ferramental
- Validação numérica da sequência final (incluindo as operações de recozimento e lubrificação)
- Validação do estresse mecânico do ferramental
- Planos de manutenção preventiva
O software COLDFORM® agora contribui para a validação dos procedimentos de fabricação na Boucledor.
Os esforços para construção automotiva leve aumentaram significativamente impulsionados pela atual pressão econômi ca e política para reduzir o consumo de combustível e as emissões de CO2. Nesse contexto, o interesse por soluções que envolvem o uso de ligas de alumínio tem crescido substancialmente. Diante da importância tecnológica do processamento destes materiais, este trabalho apresenta uma revisão das principais características técnicas e propriedades das ligas de alumínio. Ademais, as especificidades da produção de componentes automotivos por conformação mecânica com ênfase no processo de estampagem a quente são discutidas.
Os desenvolvimentos da indús tria da mobilidade objeti vando soluções inovadoras e econômicas para ampliar a eficiência energética dos veículos têm crescido continuadamente. Paralelamente, as exigências relacionadas a requisitos de impacto também estão sendo cada vez mais maximizados. Consequentemente, os carros estão mais seguros do que nun ca e materiais leves e de alta resistência, perfeitamente adaptados, tem dado uma importante contribuição para isso.
As ligas de aço ainda dominam o mercado automotivo devido à sua adequada relação custo/desempenho. No entanto, as ligas de alumínio surgem como uma alternativa para substituir os
Figura 1. Aplicações de ligas de alumínio nos componentes automotivos de um carro de passeio típico [5].
materiais convencionais e desempenham um papel importante para aplicações leves. Estas ligas apresentam resistên
cia, absorção de energia muito boa, excelente conformabilidade e reciclabi lidade. Além disso, as ligas de alumínio
Rafael Pandolfo da Rocha; Matheus Henrique Riffel; Thomas Gomes dos Santos; André Rosiak e Lirio SchaefferDESENVOLVIMENTOS NA CONFORMAÇÃO MECÂNICA DE CHAPAS DE LIGAS DE ALUMÍNIO PARA INDÚSTRIA AUTOMOTIVA
apresentam boa resistência a corrosão e baixo peso. Em comparação com o aço o uso do alumínio pode gerar uma redução de peso de até 50% [1].
Diante da relevância do processa mento das ligas de alumínio, este artigo se propõe a expor os principais aspectos da conformação destes materiais quando dispostos na forma de chapas, bem como suas características metalúrgicas e tecnológicas.
A indústria de alumínio tem desenvol vido inúmeras soluções inovadoras e leves baseadas em ligas já estabelecidas e em soluções aprimoradas [2-3] para um projeto otimizado de veículos orientados para o alumínio. Uma das principais van tagens destas ligas é a disponibilidade em uma grande variedade de formas semi-a cabadas, todas adequadas para produção
em massa e soluções inovadoras. As peças finais atendem às altas demandas de alto desempenho, qualidade e capacidade de fabricação econômica [4].Além disso, foi realizada uma revisão dos trabalhos acadêmicos para obtenção das proprieda des físicas e mecânicas do aço inoxidável austenítico AISI 304 (tabela 01), visando instruir corretamente esse software e, posteriormente, a execução dos cálculos analíticos.
A aplicação de ligas de alumínio na indústria automotiva cresceu mais de 80% na última década e, com base nos novos conceitos de projeto, o progresso continuará seguindo esta tendência nos próximos anos. Em 1996, 110 kg de ligas de alumínio eram utilizados em um veículo e a expectativa é que esta quan tidade aumente para 250 ou 340 kg [5].
A Figura 1 mostra algumas aplicações de ligas de alumínio nos componentes auto motivos de um carro de passeio típico.
O conceito Super Light Car mostrado na Figura 2 propõe a utilização de diver sos materiais na construção do veículo.
Essa solução permite uma redução de massa de 95 kg (34%), com custos adi cionais de peças de 5 € /kg. O alumínio, que compõe 53% do veículo, é usado nos painéis, trilhos dianteiros, para-choques e em elementos de colisão.
Em particular, as ligas de alumínio da série 7xxx oferecem grandes vantagens em comparação com os aços endurecidos por prensagem (Press Hardened Steel - PHS) se as resistências específicas dos materiais correspondentes forem comparadas entre si (Figura 3) [7]. Esse potencial ser utilizado para reduzir o consumo de energia durante a vida útil de um veículo [8].
Os fabricantes de automóveis que ten dem a optar por ligas de alumínio uma vez que, além de reduzir o peso dos veículos, estes materiais apresentam menor custo
que outros materiais leves, como compósi tos e ligas de magnésio. A aplicação destes materiais concentra-se predominantemente na fabricação de carros de corrida, carros esportivos e supercarros de luxo [7].
Um exemplo atual da aplicação das ligas de alumínio da indústria da mobili dade é o uso da liga AMAG TopForm® UHS para fabricação de estrutura com impacto lateral no BMW i8 (Figura 4).
A AMAG TopForm® UHS é uma liga AA7075 (AlZn5.5MgCu) otimizada para conformação a quente na condição T6 [9].
Outro exemplo é a carroceria do Ford F150 em que o aço foi substituído por liga de alumínio para economizar peso [10].
A conformação mecânica de ligas de alumínio concentra-se, especialmente, nas classes endurecíveis, tratáveis termica mente e endurecíeis por envelhecimento, como 2xxx, 6xxx e 7xxx.
As ligas 6xxx atualmente usadas em carroceria são A6016 (Europa), A6111 (América) e A6181A, que foram adicio nadas mais recentemente devido a aspec tos de reciclagem. Nos EUA, o A6111 é frequentemente usado para painéis externos em espessuras de 0,9 a 1,0 mm, o que combina alta resistência com boa
conformabilidade. Na Europa, a EN6016 é preferida e aplicada em espessuras de 1 a 1,2 mm. Esta liga apresenta uma conformabilidade superior permitindo a obtenção de peças mesmo em chapas com pré-deformação local. No entanto, a resistência endurecida por recozimento do 6016 é significativamente menor do que a do A-6111 [11].
Os componentes de ligas de alu mínio endurecidas por envelhecimento (6xxx) são normalmente conformados na condição T4, seguido de envelhecimento artificial para aumentar a resistência, ou na condição T6 [12]. Mesmo na condi ção T4, a baixa conformabilidade é uma questão crítica do processamento de chapas de alumínio. Outro aspecto críti co é o retorno elástico associado a baixos valores de módulo de Young.
A Figura 5 mostra a evidente dife rença na precisão dimensional de peças após a conformação a frio e a quente (na temperatura de solubilização). As peças conformadas a quente indicam quase nenhum retorno elástico, enquanto a precisão das peças conformadas a frio é muito baixa. O retorno elástico da liga AA7075 é claramente maior em compa ração com a AA6082 após a conforma ção a frio devido a maior resistência ao escoamento [12].
Figura 5 - Comparação entre o retorno elástico de ligas de alumínio submetidas a conformação a frio e a quente [12].
Esses problemas são geralmente compensados através da conformação a temperaturas elevadas [13,14].
À medida que a temperatura aumenta, a ductilidade e a conformabilidade das ligas de alumínio aumentam significati vamente. Contudo, a conformação a quente ou a morno resulta em muitos desafios: aquecimento e controle da temperatura, lubrificação, seleção da prensa de conformação, tempo de ciclo e aumento de custo [12].
Os processos envolvem o aquecimento da chapa antes e/ ou concomitantemente com uma etapa de conformação. Em algumas aplicações a liga é aquecida a uma temperatura es pecificada na faixa de 125-425°C a uma taxa de aquecimento especificada na faixa de cerca de 3-200°C/s. Tal combinação da temperatura e taxa de aquecimento pode resultar em uma combinação vantajosa de propriedades.
Na conformação isotérmica, o aquecimento das matrizes requer estratégias complexas, com alto custo de ferramental e tempo de ciclo relativamente alto. Também é muito difícil alcançar condições de temperatura uniformes e manter uma temperatura constante da matriz. [11]. Na estampagem a morno, a chapa é aquecida entre 240 e 260°C e então confor mada em uma prensa hidráulica convencional em temperatura ambiente [14,11]. A Figura 6 demonstra uma rota de processo típica do processo de conformação a morno para ligas de alu mínio de alta resistência.
Figura 6 - Rota típica de processamento a morno de cha pas de ligas de alumínio [11].
Na estampagem a morno, as chapas geralmente são aqueci das em poucos segundos por meio de contato direto em uma estação de aquecimento, depois transferidas para a prensa. Ao contrário das linhas de endurecimento do setor siderúrgico, não existem grandes fornos com altas exigências de energia e longos tempos de aquecimento. Outra vantagem é que as chapas podem ser cortadas usando métodos convencionais, portanto, não há necessidade de corte a laser [15].
KUMAR, et al (2017) investigaram a estampabilidade a morno da liga AW-7020-T6. A Figura 7 revela que a 200°C a chapa é conformada sem a obtenção de fratura, contudo à temperatura ambiente a fratura é inevitável. Os autores verificaram que a profundidade máxima de estiramento obtida aumenta significativamente com o acréscimo da temperatura entre 150°C a 200°C.
A estampagem a temperaturas em torno de 200°C. Por defini ção, a conformação semi-quente difere da conformação a quente, pois a temperatura de recristalização é significativamente menor.
As ligas da série 7xxx com tratamento T6 não possuem conformabilidade para serem conformadas à temperatura am biente. Tanto a conformação a morno, com temperatura abaixo de 250°C, quanto a conformação a quente, a cerca de 475°C, podem ser utilizadas [11].
A conformação a quente com a têmpera na matriz foi de senvolvida para superar os problemas de conformabilidade e retorno elástico das ligas de alumínio. Neste processo, a deformação plástica e a têmpera são combinadas em um único estágio. A estampagem a quente pode ser usada para formar componentes de formato complexo e alta resistência em uma única operação [17,18].
No processo de estampagem a quente de ligas de alumínio (Figura 8), a chapa é aquecida à temperatura de solubilização e mantida nesta temperatura por um período especificado para dissolver todos os precipitados na matriz primária da fase α [17]. A chapa totalmente solubilizada é então transferida para uma prensa e conformada e dentro de matrizes frias. A têmpera rápida evita a formação de precipitados grosseiros da fase , principalmente nos contornos de grão. Após a deforma ção, a peça é mantida entre as matrizes, o que evita a distorção
térmica. A peça é posteriormente envelhecida para permitir que precipitados sejam formados de forma controlada [19,20].
A primeira etapa desta tecnologia é aquecer a chapa até a temperatura de tratamento térmico solubilização e perma necer por algum tempo para obter uma solução sólida mo nofásica da fase α. No entanto, geralmente leva muito tempo para completar a solubilização: 500°C por 2h para AA6061 [22], 535°C por 2h para AA6061 [23], 570°C por 20min para AA6061 [24], 480°C por 1h para 7075 [25,26] e assim por diante. A longa duração do tratamento térmico tem limitado a industrialização da estampagem a quente de ligas de alumínio e também aumenta o custo de produção [21].
HIRSCH (2014) avaliou o efeito da temperatura de solu bilização nas propriedades mecânicas de peças estampadas a quente nas ligas AA7075 e AA6082. A liga AA7075 apre senta um aumento da resistência mecânica com a temperatura de conformação, mesmo em níveis acima do recomendado na literatura (465-480°C) [28]. Já a liga AA6082 apresenta aumento significativo das propriedades mecânicas apenas quando a temperatura é elevada dentro da faixa recomendada para a solubilização do material, entre 525 e 540 °C [28]. Aci ma destas temperaturas não é encontrado nenhum aumento nas propriedades mecânicas com a elevação da temperatura. Ambos os materiais, apresentaram comportamento semelhante quando foram utilizadas temperaturas abaixo da faixa reco mendada para a solubilização. Nesta condição, observou-se uma diminuição dramática na resistência.
ZHOU et al. (2014) investigou a estampagem de chapas da liga de alumínio AA6111 para a produção de uma viga de impacto lateral. A Figura 9 mostra que a conformação à tem peratura ambiente resultou na fratura do material, enquanto a conformação a quente com a têmpera nas ferramentas aumen tou a conformabilidade permitindo a obtenção de uma peça livre de defeitos [20].
Um exemplo da aplicação desta tecnologia na indústria au tomotiva é a fabricação da parte interna de porta de um Lotus mostrado na Figura 10. O componente é produzido através da conformação em uma única etapa de uma liga de alumínio de alta resistência [20,26].
Devido, especialmente, à sua baixa densidade e resistência à corrosão as ligas de alumínio vem ganhando espaço em muitas aplicações automotivas, como chassis, carrocerias e componen tes estruturais. Este artigo demonstrou que o pleno conheci
mento sobre os fenômenos mecânicos e metalúrgicos envol vidos no processamento destes materiais permite a fabricação de produtos otimizados para as altas demandas em aplicações automotivas. Além disso, exemplos de implementações industriais bem-sucedidas das tecnologias de conformação foram expostas, comprovando o grande avanço nas aplicações automotivas do alumínio nos últimos anos.
[1]
AUMÜLLER M., Sicherheit und Leichtbau mit AMAG Aluminium, AluReport, AMAG TopForm UHS: Durchbruch im Karosserieleitbau. pp. 14 a 15. 2014.
[2] BRÜNGER, E., ENGLER, O., HIRSCH, J. Al−Mg−Si Sheet for Autobody Application. Virtual Fabrication of Alumi nium Products. Chapter 1−6. Weinheim: Wiley-VCH Verlag, 2006: 51−61.
[3] LAHAYE, C., et al. Contribution of Aluminium to the Multi-Material Light-Weight BIW Design of SuperLight-Car (SLC). Aluminium International Today. V. 21 No. 5. 2009.
[4] HIRSCH, J., et al. Hot Forming of Aluminium for Ligh t-Weight Car Design. Aluminium International Today. Aachen, Germany. pp. 2388 a 2393. 2008.
[5] AKKIREDDY, L. A., et al. Formability Studies of Au tomotive Aluminium Alloy Sheet series: A Review, E3S Web of Conferences. Vol. 184. 2020.
[6] JU, L., ALTAN, T., Forming Al Alloys at Elevated Tem peratures, Part I - Stamping Journal. 2015.
[7] SCHLOSSER J., et al. Materials and Simulation Mo delling of a Crash-Beam Performance – a Comparison Study Showing the Potential for weight Saving Using Warm-For med Ultra-High Strength Aluminium Alloys. 36th IDDRG Conference – Materials Modelling and Testing for Sheet Metal Forming. 2017.
[8]
OSTERMANN, F., Anwendungstechnologie Aluminium, Heidelberg: Springer Verlag, Book, 2007.
[9]
AUMÜLLER M., Sicherheit und Leichtbau mit AMAG Aluminium, AluReport, AMAG TopForm UHS: Durchbruch im Karosserieleitbau. pp. 14 a 15. 2014.
[10] KELSCH, R., Company-Internal Document. Schwäbisch Gmünd. Voestalpine Polynorm, 2011.
[11] EAA BROCHURE, Aluminium in Cars. Ducker Report. 2012.
[12] SCHARIF, I. E., KNOTH, R., WEIDIG, U., Thermo -Mechanical Forming Procedure of High Strength Aluminum Sheet With Improved Mechanical Properties and Process Effi
ciency, Procedia Manufacturing Volume 29. pp. 481 – 489. 2019.
[13] TAKATA, K. Warm Forming of Aluminum Alloys. Ni ppon Steel Technical Report No. 103 pp. 104 a 109. 2013.
[14] HARRISON, N. et al. Optimization of High-Volume Warm Forming for Lightweight Sheet. SAE Technical Paper. pp. 11.2013.
[15] MOHAMED M. S., et al. Hybrid Forming Processes for Production of Lightweight High Strength Automotive Panel Parts. International Heat Treatment and Surface Engineering, Vol.4, No.4, pp.160-165, 2010.
[16] KUMAR V., et al. Materials Science and Engineering: A 679, 2017
[17] BRÜNGER, E., ENGLER, O., HIRSCH, J. Al−Mg−Si Sheet for Autobody Application. Virtual Fabrication of Alumi nium Products. Chapter 1−6. Weinheim: Wiley-VCH Verlag. pp. 51−61. 2006
[18] BURGER, G. B., et al. Microstructural Control of Aluminium Sheet Used in Automotive Applications. Materials Characterization. Vol.35. pp 23 – 39. 1994.
[19] MOHAMED, M. S., FOSTER, A. D., LIN, J. Solution Heat Treatment in HFQ Process. Journal Steel Research Interna tional. Vol. 79. pp. 160−167. 2008.
[20] ZHOU, J. et al. Forming Defects in Aluminum Alloy Hot Stamping of Side-Door Impact Beam, Transactions of Nonfer rous Metals Society of China, Volume 24, Issue 11, 2014.
[21] WAGNER, P., et al. Proc New Developments in Sheet Metal Forming. DGM. 2008.
[22] HIRSCH J, BRÜNGER E, KELER S, KIPRY K. Hot forming of aluminium for light-weight car design [C]//HIRSCH J, SKROTZKI B, GOTTSTEIN G. Aluminium Alloys; Their Physical and Mechanical Properties. Proceedings ICAA-11. Aachen, Germany: Whiley-VCH, 2008: 2388−2393.
[23] MASSARDIER. V., EPICIER, T., MERLE, P. Correla tion Between The Microstructural Evolution of a 6061 Alumi nium Alloy and the Evolution of its Thermoelectric Power. Acta Materials. Vol. 48. Pp. 2911 – 2994. 2000.
[24] POGATSCHER, et al. Mechanisms Controlling the Ar tificial Aging of Al-Mg-Si Alloys, Acta Materials. Vol. 59. Pp. 3352 – 3363. 2011.
[25] ROJAS, J. I., CRESPO, D. Dynamic Microstructural Evolution of an Al-Zn-Mg-Cu Alloy (7075) During Continuous Heating and the Influence on the Viscoelastic Response. Mate rials Characterization. Vol. 134. pp. 319 a 328. 2017.
[26] IBRAHIM, M. F., et al. novel solution heat treatment of 7075-type Alloy, in: B.A. Light Metals. pp. 383 a 390. 2013.
[27] HIRSCH J., Recent Development in Aluminium for Auto
motive Applications. Transactions of Nonferrous Metals Society of China. Vol. 24. pp. 1995 – 2002. 2014.
[28] MOHAMED, M.S., et al. Investigation of Deformation and Failure Features in Hot Stamping of AA6082: Experimenta tion and Modelling. International Journal of Machine Tools and Manufacture. Vol. 53.pp. 27–38. 2012.
Rafael Pandolfo da Rocha, Engenheiro Mecânico, Mestrando do Programa de Pós-Graduação em Engenharia de Minas, Metalúrgica e Materiais (PPGE3M), na Universidade Federal do Rio Grande do Sul – E-mail: rafael. pandolfo@ufrgs.br
Matheus Henrique Riffel, Engenheiro Mecânico, Mestrando do Programa de Pós-Graduação em Engenharia de Minas, Metalúrgica e Materiais (PPGE3M), na Universidade zzzFederal do Rio Grande do Sul) – E-mail: matheus.riffel@ufrgs.br
Thomas Gomesdos Santos, Engenheiro Metalúrgico, Doutorando do Programa de Pós-Graduação em Engenharia de Minas, Metalúrgica e Materiais (PPGE3M), na Universidade Federal do Rio Grande do Sul –E-mail: thomas.santos@ufrgs.br
André Rosiak, Engenheiro Metalúrgico, Doutorando do Programa de PósGraduação em Engenharia de Minas, Metalúrgica e Materiais (PPGE3M), na Universidade Federal do Rio Grande do Sul – E-mail: andre.rosiak@ufrgs.br
Lirio Schaeffer, Engenheiro Mecânico, Prof. Dr. Ing. do Programa de PósGraduação em Engenharia de Minas, Metalúrgica e Materiais (PPGE3M), na Universidade Federal do Rio Grande do Sul – E-mail: schaefer@ufrgs.br