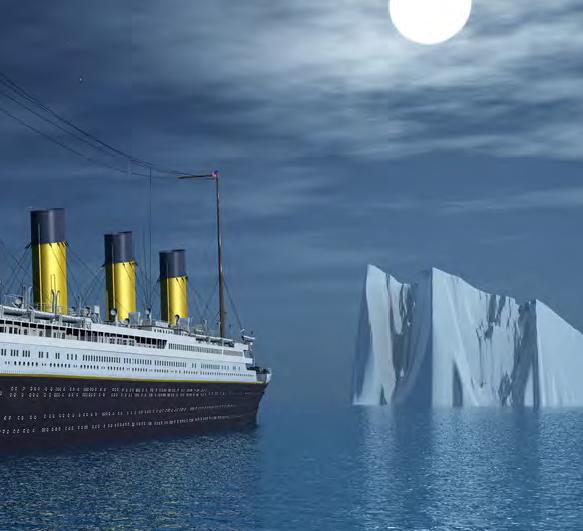
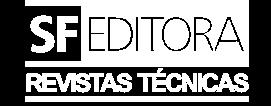
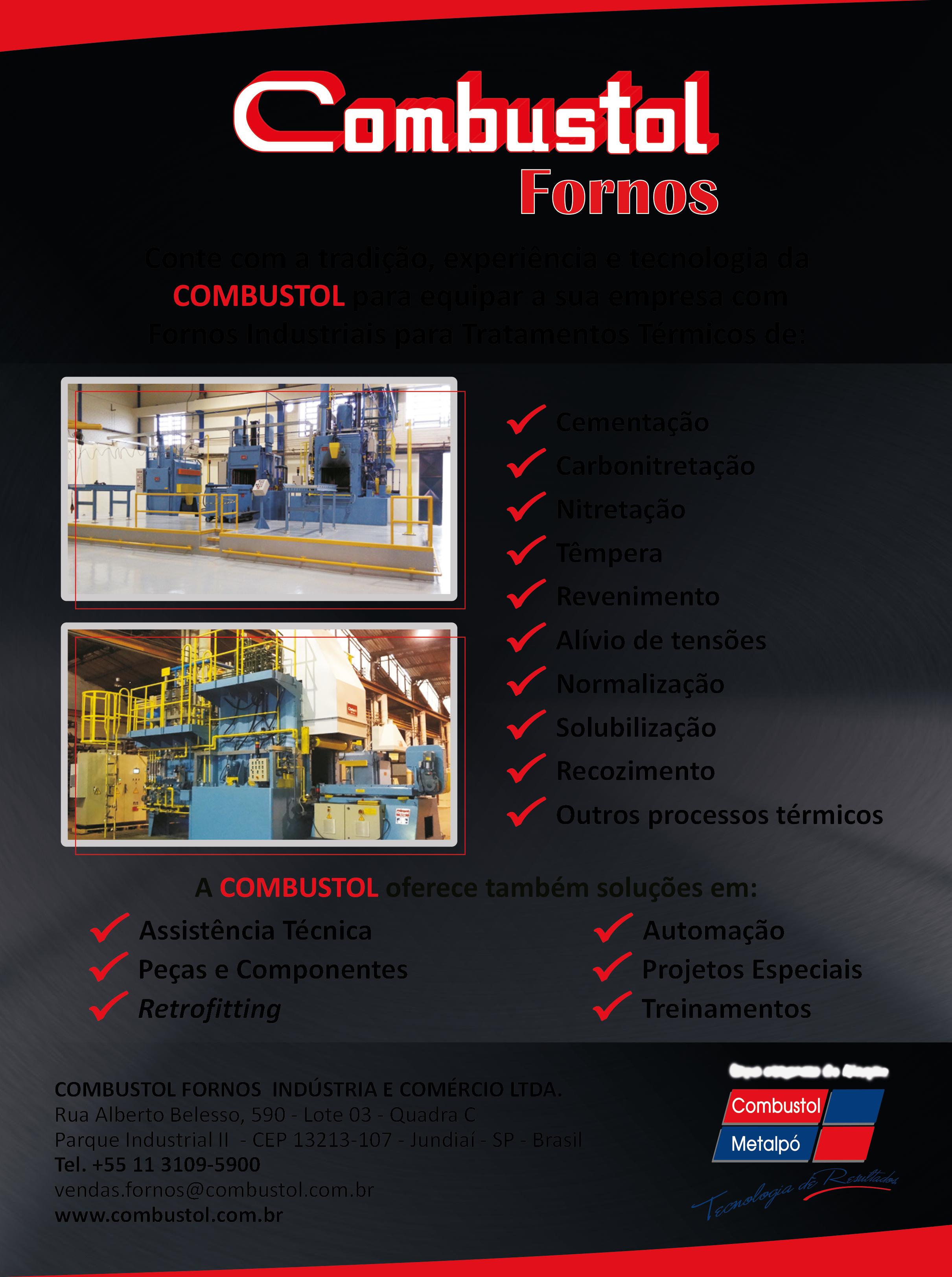
V o c ê j á c o n h e c e a s l a v a d o r a s i n d u s t r i a i s
G r e f o r t e c ? E l a s s ã o m o d e r n a s , s u s t e n t á v e i s , c o m e s t r u t u r a r o b u s t a e r e s i s t e n t e .
A s s i m c o m o t o d o s o s n o s s o s e q u i p a m e n t o s , e l a s c o n t e m p l a m a s N o r m a s Br a s i l e i r a s d e S a ú d e e S e g u r a n ç a d o T r a b a l h o , c o m N R 1 0 , N R 1 2 e N R 1 7 . A l é m d i s s o , n o s s a s l a v a d o r a s i n d u s t r i a i s c o n t a m c o m r e l a t ó r i o d e A n á l i s e P r e l i m i n a r d e R i s c o s , l a u d o s d e c e r t i f i c a ç ã o e A R T d e e f e t i v a ç ã o .
T o d a s a s n o s s a s l a v a d o r a s s ã o d e s e n v o l v i d a s a p a r t i r d e u m a m i n u c i o s a a n á l i s e d a s n e c e s s i d a d e s e p r o c e s s o f i n a l d o c l i e n t e N o s s o d e p a r t a m e n t o d e e n g e n h a r i a d e s e n v o l v e p r o j e t o s c u s t o m i z a d o s c o m o o b j et i v o d e o f e r e c e r u m a s o l u ç ã o e x c l u s i v a p a r a o s n o s s o s c l i e n t e s !
C o n h e ç a a l g u n s d o s n o s s o s p r i n c i p a i s m o d e l o s :
L a v a d o r a I n d u s t r i a l C o n t í n u a
A s l a v a d o r a s c o n t í n u a s p o d e m s e r u t i l i z a d a s p a r a r e a l i z a r a l i m p e z a a u t o m á t i c a n o s m a i s v a r i a d o s t i p o s d e p r o c e s s o s i n d u s t r i a i s , i n c l u i n d o o t r a t a m e n t o t é r m i c o . U m a d a s v a n t a g e n s d e s t e m o d e l o é o s i s t e m a d e m o v i m e n t a ç ã o p o r e s t e i r a , o u p a s s o i n t e r m i t e n t e e m q u e a p e ç a c om s u j i d a d e s e n t r a p o r u m l a d o d a l a v a d o r a e s a i j á t o t a l m e n t e h i g i e n i z a d a n o o u t r o l a d o .
L a v a d o r a I n d u s t r i a l E s t a c i o n á r i a
A s l a v a d o r a s e s t a c i o n á r i a s d a G r e f o r t e c s ã o u t i l i z a d a s n a i n d ú s t r i a m e c â n i c a p a r a o s m a i s v a r i a d o s t i p o s d e p e ç a s , c o m o p o r e x e m p l o : e i x o s , b u c h a s , c a i x a s d e c â m b i o , e n g r e n a g e n s e o u t r a s
L a v a d o r a A s l a v a d o r a s F l e x i c l e a n s ã o m á q u i n a s a u t o m á t i c a s p a r a l a v a g e m d e p e ç a s o n d e o s m a i s a l t o s n í v e i s d e p u r e z a s ã o n e c e s s á r i o s e / o u c o m p o n e n t e s g e o m e t r i c a m e n t e c o m p l e x o s d e v e m s e r l i m p o s . S e u s c o m p o n e n t e s e s s e n c i a i s i n c l u e m : u m a c â m a r a d e l i m p e z a a v á c u o , t a n q u e s i s o l a d o s p a r a a g e n t e s d e l i m p e z a ( 1 - 3 ) , b o m b a d e v á c u o , b o m b a s d e s p r a y , u m a u n i d a d e d e s e p a r a ç ã o d e ó l e o e u m s i s t e ma d e a q u e c i m e n t o .
P a r a s a b e r m a i s s o b r e a s l a v a d o r a s i n d u s t r i a i s G r e f o r t e c o u s o l i c i t a r u m o r ç a m e n t o f a l e d i r e t a m e n t e c o m n o s s o s t é c n i c o s e s p e c i a l i z a d o s , l i g u e p a r a ( 5 1 ) 3 5 6 2 - 7 0 7 1 o u e n v i e u m a m e n s a g e m n o W h a t s A p p p a r a ( 5 1 ) 9 9 3 5 4 - 3 4 5 7
G r e f o r t e c g r e f o r t e c c o m b r @ g r e f o r t e c r s
Materiais resistentes ao calor Por que afundou o Titanic? (Parte II)
David Pye – Pye Metallurgical International Consulting São apenas 110 anos desde o trágico naufrágio do navio inafundável, o RMS Titanic. A primeira parte deste artigo enfocou os rebitadores de proa e popa e o próprio processo de rebitagem. Esta segunda parte mergulha mais fundo no naufrágio do navio.
Tratamento térmico Transição de Peças da Cementação em Atmosfera para a Cementação em Baixa Pressão e os Benefícios Econômicos e Ambientais
Dennis Beauchesne, Vincent Lelong
A cementação a vácuo ou mais especificamente a cementação a vácuo de baixa pressão (LPC - Low Pressure Vacuum Carburizing) assumiu várias indústrias como a principal opção de cementação nos últimos 25 anos
Fusão
Otimize seu Forno com Base em seus Requisitos de Produção
Patrick Laskey – Onex Inc.
Se o seu forno é o gargalo em sua operação, pode ser hora de considerar a adição de um novo. Este artigo analisa os fundamentos da estrutura e estilo do forno, seleção de refratários e projeto de combustão. Conclui com um estudo de caso recente.
Processos
Sistema de Assistência para o Processo de Forjamento Baseado na Inteligência Artificial
André Rosiak; Diego Wermuth; Thomas Gomes dos Santos; Matheus Henrique Riffel; Rafael Pandolfo da Rocha e Lírio Schaeffer
Uma maneira eficaz das indústrias obterem economias significativas e melhorias de qualidade é por meio de novas estratégias de controle de processos.
Refratários/Isolamento Térmico Avanço Revolucionário em Isolamento Aumenta a Economia de Energia
Allan Davies – Unifrax; Tonawanda, N.Y., EUA
Em meados do século passado, um cientista da Carborundum Company atendeu às exigências do mercado industrializado para um material isolante de baixa massa térmica.
Processos
Por que é Importante Medir o Fluxo de Ar e Combustível em um Forno?
Manish Patel – Leomi Instruments; Gujarat, INDIA
Os fornos industriais são amplamente utilizados para fundir metais para fundição ou aquecer materiais para mudança de forma (forjamento) ou mudança de propriedades (tratamento térmico).
BRASIL
SF Editora é uma marca da Aprenda Eventos Técnicos Eireli (19) 3288-0437 - ISSN 2178-0110
Rua Ipauçu, 178 - Vila Marieta, Campinas (SP) www.sfeditora.com.br
Udo Fiorini Publisher, udo@sfeditora.com.br • (19) 99205-5789
Mariana Rodrigues Redação - Diagramação, marianar205@gmail.com • (19) 3288-0437
André Júnior Vendas, andre@grupoaprenda.com.br • (19) 3288-0437
Manor Oak One, Suite 450, 1910 Cochran Road, Pittsburgh, PA, 15220, EUA
Fone: +1 412-531-3370 • Fax: +1 412-531-3375 • www.industrialheating.com
Erik Klingerman Group Publisher, klingermane@bnpmedia.com • +1 440-292-7580
EDIÇÃO E PRODUÇÃO NOS EUA
Reed Miller Publisher Associado/Editor - M.S. Met. Eng., reed@industrialheating.com • +1 412-306-4360
Bill Mayer Editor Associado, bill@industrialheating.com • +1 412-306-4350
Brent Miller Diretor de Arte, brent@industrialheating.com • +1 412-306-4356
REPRESENTANTE DE PUBLICIDADE NOS EUA
Kathy Pisano Diretora de Publicidade, kathy@industrialheating.com +1 412-306-4357
Fax: +1 412-531-3375
DIRETORES CORPORATIVOS
Rita M. Foumia Recursos Humanos e T.I
Michael T. Powell Criação
Lisa L. Paulus Finanças
Scott Wolters Eventos
Vincent M. Miconi Produção
Beth A. Surowiec Pesquisa de Mercado
As opiniões expressadas em artigos, colunas ou pelos entrevistados são de responsabilidade dos autores e não refletem necessariamente a opinião dos editores.
EQUIPE DE EDIÇÃO BRASILEIRA
SF Editora é uma marca da Aprenda Eventos Eireli (19) 3288-0437 - ISSN 2178-0110 www.sfeditora.com.br www.aquecimentoindustrial.com.br
Udo Fiorini - Publisher, udo@sfeditora.com.br • (19) 99205-5789
Mariana Rodrigues - Diagramação, marianar205@gmail.com • (19) 3288-0437
André Júnior - Vendas, andre@grupoaprenda.com.br • (19) 3288-0437
Igor Cerqueira - Marketing, igor@grupoaprenda.com.br • (19) 3288-0437
ESCRITÓRIO CORPORATIVO NOS EUA
BNP Media • 2401 W. Big Beaver Road Suite 700, Troy, MI 48084 • www.bnpmedia.com
Erik Klingerman, Group Publisher klingermane@bnpmedia.com • +1 440-292-7580
Reed Miller, Editor nos EUA reed@FORGEmag.com • +1 412-306-4360
ESCRITÓRIO EM PITTSBURGH/EUA Manor Oak One, Suite 450 1910 Cochran Road, Pittsburgh, PA 15220 Tel: +1 412- 531-3370 • Fax: +1 412-531-3375
EDIÇÃO E PRODUÇÃO NOS EUA
Dean M. Peters, Editor dean@forgemag.com • +1 216-570-4537
Bill Mayer, Editor Associado bill@forgemag.com • +1 412-306-4350
Linda Becker, Editora Colaboradora beckerl@bnpmedia.com • +1 262-564-0074
Karen Talan, Gerente de Produção talank@bnpmedia.com • +1 248-244-6246
Brent Miller, Diretor de Arte millerb@bnpmedia.com • +1 412-306-4356
REPRESENTANTE DE PUBLICIDADE NOS EUA
Kathy Pisano, Advertising Director (412) 306-4357, Fax (412) 531-3375 kathy@FORGEmag.com
DIRETORES CORPORATIVOS NOS EUA
Edição: John R. Schrei
Estratégia Corporativa: Rita M. Foumia
Implantação de Conteúdo: Michelle Hucal
Criação: Michael T. Powell
Eventos: Scott Wolters
Finanças: Lisa L. Paulus
Tecnologia da Informação: Scott Krywko
Recursos Humanos: Marlene J. Witthoft
Produção: Vincent M. Miconi
Pesquisa Clear Seas: Beth A. Surowiec
As opiniões expressadas em artigos, colunas ou pelos entrevistados são de responsabilidade dos autores e não refletem necessariamente a opinião dos editores.
Editorial Brasil Grupo Aprenda 2023 Com a redução, tão esperada, do ímpeto da pandemia no início de 2022, tomamos a feliz decisão de voar um pouco mais alto com a nossa atividade primeira, nos últimos tempos, de realizar eventos técnicos.
Simulação Computacional Tratamento Térmico da Matéria Prima As principais fornecedoras de barras de aço como matéria prima para processos de Tratamento Térmico e Forjamento, por exemplo, têm investido esforços na melhoria da qualidade de seus produtos.
Pesquisa e Desenvolvimento Os casos do PHS para aço e estampado a quente para alumínio O universo dos materiais estampados a quente (Press Hardening Steel - PHS para os aços) ainda desperta interesse e muitos esforços das comunidades locais e internacionais.
Combustão Queimadores Infravermelhos
Dando continuidade ao tema, serão tratados agora os queimadores infravermelhos. Estes queimadores utilizam apenas gases combustíveis como gás natural, GLP e biometano pré-misturados com ar, de forma a superaquecer um elemento metálico ou cerâmico.
Editorial EUA Dando uma olhada em tecnologias novas e interessantes Normalmente, começamos o Ano Novo focando em novas tecnologias em toda a indústria de processamento térmico em nossa edição de janeiro.
Simulação Computacional Prevendo Desgaste e Fadiga Tomando como exemplo o produto forjado mostrado na Fig. 1, fica evidenciada na Fig. 2 a possibilidade de se prever fenômenos como o desgaste na matriz responsável pela fabricação deste mesmo forjado.
Lubrificantes Lubrificante de Matriz –Grafite sintético, o mais insubstituível Como é sabido, esta coluna relata as observações, deduções, estudos e principalmente o acompanhamento ativo de testes de campo, oportunidades que são verdadeiros tesouros, agora reforçado pela parceria com meu amigo de longa data, Emerson Fabrete que também milita nessa área e com o qual tenho mantido interessantíssimo diálogos e brain stormings especializados.
19 99205-5789
udo@sfeditora.com.br
Com a redução, tão esperada, do ímpeto da pandemia no início de 2022, tomamos a feliz decisão de voar um pouco mais alto com a nossa atividade primeira, nos últimos tempos, de realizar eventos técnicos. Promover aquela enxurrada de seminários ao longo do ano, além de extremamente desgastante e cansativo, muitas vezes não atingia o objetivo do cliente interessado em conhecer mais. Ele se via forçado muitas vezes a permanecer assistindo a uma palestra sem ter a possibilidade de escolha de alternativas.
Assim, decidimos em 2022 reunir em Congressos os nossos vários Seminários que apresentavam sinergias entre si. Que possibilitassem ao participante acompanhar vários temas à sua livre escolha. Ou a grupos, como eu mesmo tive a oportunidade de presenciar, se dividirem para aproveitar melhor as inúmeras alternativas à disposição. E saírem ganhando. Em custo e em conhecimento.
Numa primeira análise, que agora percebemos foi acertada, decidimos dividir todo o acervo de seminários que até pareciam já terem sido criados com esta finalidade, em dois grandes grupos: Conformação e Processos Térmicos.
E em Junho de 2022, com o auxilio e a parceria da FSA, Centro Universitário Fundação Santo André que nos cedeu o espaço, realizamos o 1º Congresso de Conformação Metálica em suas instalações situadas na cidade de Santo André.
Problemas? Claro que houve. Mas o resultado em termos de satisfação de participantes e patrocinadores foi evidente. Graças ao espaço propício do prédio da FSA onde se situa o auditório escolhido para o evento, a lógica maior de um evento, propiciar amplo contato entre os presentes entre si e com o conhecimento foi totalmente alcançado. Integração total.
O resultado positivo animou para repetir a dose, agora completa, em 2023. E lançamos o 1º Congresso de Processos Térmicos a ser realizado em Março 14 e 15 e também o 2º Congresso
de Conformação Metálica a ser realizado em Junho 20 e 21. Ambos nas instalações da FSA em Santo André. Aliás cabe aqui um muito obrigado à FSA, em alto e bom som, em função da cessão dos seus espaços. E também agradecer aos alunos da Pós Graduação em Materiais da FSA pelo inestimável auxilio na recepção e assistência aos participantes e patrocinadores durante todo o evento.
Os dois eventos juntam números expressivos. Inúmeros Seminários. Dezenas de palestrantes. Centenas de participantes. Exige planejamento e ações controladas. Necessidade de equipe com trabalho coordenado. Tudo isso com estrutura enxuta depois de anos de redução de atividades por causa da pandemia. Esperamos que o resultado do esforço agrade ao nosso público alvo. Publicações, Revistas: com algumas pequenas correções de rota seguimos no propósito de oferecer bons artigos técnicos aos nossos leitores. A união das revistas IH (Industrial Heating) com a FORGE se mostrou acertada. Principalmente se considerarmos a redução de recursos mencionada mais acima. A revista Estampagem & Conformação deve receber mais edições em 2023, melhorando sua divulgação. Mais detalhes ao longo do ano.
A Revista Grafeno segue seu caminho de sucesso. As quatro edições publicadas em 2022 tiveram boa repercussão e excelente procura pelos leitores. Para 2023 estão previstas também 4 edições, agora focadas em quatro segmentos tecnológicos, ou seja:
1) Industrial (edição de março)
2) Mobilidade (edição de junho)
3) Biotecnologia (edição de setembro)
4) Meio ambiente (edição de dezembro)
Aproveito para desejar a todos os leitores um Feliz Ano de 2023! Que seja um período não só de aprendizado, mas também de bons resultados.
Boa leitura!
alisson@sixpro.pro
s principais fornecedoras de barras de aço como matéria prima para processos de Tratamento Térmico e Forjamento, por exemplo, têm investido esforços na melhoria da qualidade de seus produtos. Ainda que boa parte dos processos de tratamento térmico sejam considerados como bastante conhecidos pelas usinas, a simulação computacional vem sendo enxergada como uma possibilidade de melhorar ainda mais os resultados.
Tomemos um processo de laminação seguido de resfriamento controlado, como é o caso do STELMOR (Fig. 1). Após a laminação a quente, o fio máquina passa por um processo de resfriamento controlado, visando uma determinada microestrutura, como exemplificado na Fig 2.
O equipamento de resfriamento mostrado na Fig. 1 pode ser configurado para acelerar ou retardar o resfriamento do fio máquina. Com isso, as microestruturas finais poderão ser modificadas, como é apresentado esquematicamente no diagrama TRC (CCT) da Fig. 2. Logo, um mesmo aço poderá ser fornecido com propriedades mecânicas diferentes.
Dizer que o aço de uma barra ou tarugo pode possuir propriedades mecânicas distintas, significa para o profissional de forjamento que a curva de escoamento daquela matéria prima pode variar. Para ilustrar, tomemos as curvas de escoamento mostradas na Fig. 3, as quais poderiam tranquilamente ser correlacionadas com a velocidade de resfriamento no STELMOR. A barra de aço com valores de tensão efetiva mais elevados (gráfico da direita) teria
sofrido um resfriamento mais rápido e, portanto, teria uma resistência mecânica maior.
Tomando um forjamento a frio como exemplo, caso o tarugo possua um aço com tensões efetivas mais elevadas, a carga da prensa será maior, as ferramentas sofrerão maior desgaste, o projeto do ferramental poderá sofrer quebra, a qualidade superficial do produto irá variar e a dureza final do produto forjado será maior, entre outros fatores resultantes. Isso fica evidenciado no forjamento de um pino mostrado na Fig. 4, para o qual a carga da prensa foi significativamente maior para o material com tensões efetivas mais elevadas. As cargas da prensa, bem como toda a análise do ferramental, foram simuladas e posteriormente confirmadas em prática.
Toda a cadeia de produtos tratados termicamente e/ou forjados dependem do processamento da matéria prima. Assim, já estão sendo desenvolvidos trabalhos integrando forjarias, tratadores e fornecedores, buscando a obtenção de produtos finais com características dentro do especificado e com custos reduzidos.
Uma forjaria gostaria de ter o seu produto final com uma dureza dentro do especificado, por exemplo, reduzindo os esforços de forjamento, facilitando o refino de grão, eliminando quebras de ferramentas, entre vários outros resultados possíveis. Vamos juntos!?
MARCO ANTONIO COLOSIO
marcocolosio@gmail.com
Diretor da Regional São Paulo da SAE BRASIL. Engenheiro Metalurgista e Doutor em Materiais pelo Instituto de Pesquisas Energéticas e Nucleares-USP, pós doutorado pela EESC-USP. Professor titular do curso de Engenharia de Materiais da Fundação Santo André e professor da pós graduação em Engenharia Automotiva do Instituto de Tecnologia Mauá. Colaborador e associado da SAE BRASIL com mais de 30 anos de experiência no setor automotivo nos campos de especificações de materiais, análise de falhas, P&D e inovações tecnológicas.
Ouniverso dos materiais estampados a quente ( Press Hardening Steel - PHS para os aços) ainda desperta interesse e muitos esforços das comunidades locais e internacionais. Quando pensamos que o tema está esgotado tecnicamente, percebemos que ainda tem muita água para rolar. Aparentemente, o termo PHS usado exclusivamente para os aços está associado ao fato de obter um endurecimento microestrutural durante a estampagem a quente, efeito este causado pelo rápido e controlado perfil de resfriamento na ferramenta de estampagem; no caso do alumínio, não caberia adotar o termo PHS, mas sim seria aceitável empregar hot stamping (estampagem a quente). O efeito obtido estrutural em um alumínio é a mesma linha de motivação no emprego do aço, ou seja, melhora a estampabilidade e aumenta as propriedades mecânicas na aplicação no veículo; porém, conceitualmente é diferente entre ambos, isto é, as chapas de alumínio que estão sendo desenvolvidas para este processo estão, principalmente, dentro da classe AA 7000, portanto, durante a estampagem a quente, pode-se esperar um mecanismo de solubilização dos elementos de liga através da ação de um resfriamento rápido suficiente do material e posteriormente realizar um envelhecimento artificial para endurecimento da liga. Neste ponto existe uma grande dificuldade na definição tempo-temperatura de precipitação; normalmente a melhor condição de valores
tempo-temperatura vai para temperaturas baixas e tempos longos; a etapa da pintura do veículo pode agregar parte deste benefício e propiciar uma melhora dos valores propriedades mecânicas provenientes do mecanismo de envelhecimento artificial, mas não atingirá as melhores condições finais, que requerem tempos longos em fornos externos ao processo de produção.
Na visão do setor automotivo da eletrificação está claro que, a aplicação do alumínio em componentes estruturais e no BIW ( Body in White ) também segue em crescimento, a qual é uma das consequências da necessidade de redução de massa das carrocerias, permitindo maior eficiência das baterias elétricas e ainda somados a necessidade do aumento de tenacidade provenientes destes materiais não ferrosos na proteção dos ocupantes do veículo. Uma enorme parcela de estudos globais foca os alumínios estampados a quente dentro desta linha de interesse; porém ainda tem uma parcela ainda maior desse público que tem os aços como propulsor de avanços tecnológicos e é neste ponto que darei uma contribuição aos caros leitores.
Tenho debatido as estratégias de aços estampados a quente em nossa comunidade local bem antes de seu início formal nos veículos, participei de inúmeros debates e trabalhos acadêmicos e estive na frente de alguns dos principais avanços físicos em veículos locais, sempre certificando a vantagem de sua aplicação nas avaliações de segurança veicular do
automóvel. Nestes últimos três anos, o setor automotivo tem focado na homologação e emprego do PHS 2000; mas uma questão que está sempre impactando a viabilização de grande parte de propostas locais ainda é o custo do produto, seja o ferramental ou da matéria prima, que geralmente são aços com um revestimento de Al-Si e ferramental importado. Propostas variadas focaram e vem estudando revestimentos alternativos como Zn-Ni, Zn puro, Zn-Fe e MG zinc; todas elas têm sido motivações de vários estudos acadêmicos; porém, alego como uma constatação pessoal, “entendo que dificilmente todas estas últimas tirarão a hegemonia do Al-Si.” Por outro lado, o ferramental envolvido ainda está bem acima dos custos comparados aos do processo de estampagem a frio, por serem dispositivos de alto valor agregado e aperfeiçoados com tecnologias de resfriamento controlado por regiões distintas e contendo complexos sistemas de refrigeração de água, todas estas tecnologias tornam nossos ferramentais locais ainda embrionários, direcionando as grandes empresas aplicadoras a comprarem essas ferramentas normalmente do México ou de alguns poucos países da Europa. Por outro lado, o emprego de aços sem revestimento também tem sido usado, porém com um processo posterior de jateamento para limpeza superficial, obrigatório nestes casos; todavia, não se obtém o custo desejado, porque estes processos de limpeza tornam o produto mais custoso. Uma linha seguida localmente e explorada por um único sistemista brasileiro foi a aplicação de aquecimento rápido do blank por conceitos físicos de aquecimento por efeito Joule, que de certa forma poderia atenuar a agressão do calor a superfície do aço, mas não foram suficientes para remoção definitiva dos revestimentos, e neste caso teve o Zn-Fe como mais indicado para este processo.
Nesta questão anterior, torna-se claro que os aços usados são caros quando aplicados os revestimentos tradicionais e as ferramentas são extremamente custosas e ainda importadas na maioria das vezes. O ponto que os engenheiros estão focando para viabilizar esta tecnologia é atenuar o custo destes processos e material no contexto de aplicação no BIW, ou seja, projetar uma estrutura BIW mais
otimizada e menos custosa a partir de aplicações de algumas peças de PHS no conjunto de componentes que garantem o desempenho e rigidez do produto final; trata-se de uma tarefa difícil e complexa e exige-se muito de uma engenharia local que em via de regra no Brasil é muito otimizada para este desafio. Já nas usinas tradicionais, foca-se muito no aumento dos graus de resistência destes aços, como por exemplo: o atual PHS 2000, porque, a partir do aumento destes graus será possível os engenheiros automotivos atingirem melhores resultados estruturais das mesmas BIW(s) e ao final ter um conjunto com menor custo e com similar ou melhor desempenho. No campo dos ferramentais, o Rota 2030 tem mostrado uma força muito grande no fomento de projetos de viabilização da tecnologia de construção de ferramentais localmente, e nota-se uma enxurrada de projetos submetidos nas PPP (programa de projetos prioritários) e muitos já aprovados; certamente teremos boas novidades em breve no setor; todavia, os grandes sistemistas terão que se convencer e aceitar estrategicamente que fazer uma ferramenta no Brasil poderá ter ganhos indiretos sem contar com provável custo inferior.
O alumínio estampado a quente da série 7000 não tem a desvantagem da obrigatoriedade em ter um revestimento na chapa anterior a estampagem e por isto soma-se uma vantagem de não agregar o custo deste revestimento, mas o material não ferroso ainda é um desafio no custo, em processos de resfriamento e na tecnologia de junção no BIW, mas certamente, são desafios superáveis e ainda mais para o caso de um ambiente atual e futuro de eletrificação automotiva.
Estudar novos revestimentos, promover aquecimentos mais rápidos da chapa ou ter aços ferrosos mais resistentes às oxidações durante o aquecimento e estampagem à quente são uma opção futura de projetos, e por isso, os estudos neste campo ainda continuarão sendo executados e consequente assistiremos o caso PHS mantendo-se a “menina dos olhos” dos componentes estampados, e em paralelo e de grande importância, o alumínio estampado a quente buscando um lugar ao “sol”.
Muito obrigado e até a próxima edição da IH.
Dando continuidade ao tema, serão tratados agora os queimadores infravermelhos. Estes queimadores utilizam apenas gases combustíveis como gás natural, GLP e biometano prémisturados com ar, de forma a superaquecer um elemento metálico ou cerâmico, de forma a transferir de calor para superfícies principalmente por radiação na faixa do infravermelho.
fcorner@uol.com.br
A potência da radiação infravermelha que incide numa superfície é inversamente proporcional ao quadrado da distância entre a fonte radiante e o corpo receptor. Assim, quando se requer um aquecimento uniforme a partir de queimadores infravermelhos é necessário que as superfícies mantenham distâncias iguais entre a superfície radiante e o corpo receptor em aquecimento. A Figura 1 mostra a transferência de calor entre superfícies planas e a Figura 2 entre superfícies cilíndricas.
A grande vantagem dos queimadores infravermelhos é a possibilidade de proporcionar um aquecimento superficial uniforme até em grandes áreas. Inúmeras aplicações industriais são realizadas, desde esterilização térmica de superfícies, secagem de tintas e vernizes, cura de entretelas e tecidos engomados, fixação de filmes multicamadas, tratamento térmico de placas de vidro plano, aquecimento de ambientes externos, climatização de aviários e muitas outras.
Os materiais utilizados como superfície radiante após aquecimento podem ser desde telas metálicas de aço inoxidável, como as utilizadas nas tradicionais assadeiras de frangos, placas cerâmicas microperfuradas e malhas metálicas em liga de ferrocromo-alumínio, estas últimas superando temperaturas de 900°C com maior durabilidade que as tradicionais ligas de níquel-cromo.
Muito embora projetados para uso no modo radiativo, estes queimadores podem também trabalhar no modo convectivo, onde a faixa de potências operacionais se amplia. As densidades de potência no modo radiativo são da ordem de 50 W/cm² ou 43 kcal/h/cm². Quando produtos de diferentes dimensões são tratados por queimadores infravermelhos, estes devem ser instalados em módulos com controles independentes, de forma a adequar a área da superfície radiante a cada produto evitando desperdício de gás combustível, reduzindo assim a emissão de gases do efeito estufa.
Concluindo, os queimadores infravermelhos destinam-se a aplicações específicas, podendo em muitos casos substituir resistências elétricas, principalmente nas situações em que a demanda de eletricidade esteja sendo continuamente complementada por termelétricas. A geração termelétrica apresenta baixas eficiências, portanto emitindo significativamente mais carbono do que a queima de gases combustíveis na aplicação direta na maioria nos processos térmicos.
Normalmente, começamos o Ano Novo focando em novas tecnologias em toda a indústria de processamento térmico em nossa edição de janeiro. Com isso em mente, vamos começar 2023 analisando alguns desenvolvimentos tecnológicos interessantes que chegaram à minha caixa de entrada nos últimos nove meses.
Tratamento Térmico Permite que Metais Impressos em 3D Resistam a Condições Extremas
Um novo tratamento térmico desenvolvido pelo Massachusetts Institute of Technology (MIT) transforma a estrutura microscópica de metais impressos em 3D, tornando-os mais fortes e resistentes em ambientes térmicos extremos. A técnica pode possibilitar a impressão 3D de pás e palhetas de alto desempenho para turbinas a gás e motores a jato geradores de energia. Isso pode levar
a novos projetos com melhor consumo de combustível e eficiência energética.
Os cientistas do MIT descobriram uma maneira de melhorar a estrutura das ligas impressas em 3D adicionando uma etapa adicional de tratamento térmico, que transforma os grãos finos do material impresso em grãos “colunares” muito maiores. O novo método da equipe é uma forma de recristalização direcional – um tratamento térmico que passa um material por uma zona quente a uma velocidade controlada com precisão para fundir os muitos grãos microscópicos de um material em cristais maiores, mais resistentes e uniformes.
Em um estudo, a equipe do MIT adaptou a recristalização direcional para superligas à base de níquel impressas em 3D, metais que normalmente são fundidos e usados em turbinas a gás. Você pode aprender mais sobre o processo aqui
Uma nova tecnologia de laser de feixe dinâmico (DBL - Dynamic Beam Laser) permitirá a soldagem a laser de passagem única de metais de 25 a 50 mm de espessura. As frequências de nível megahertz do DBL, que expõem um conjunto mais amplo de parâmetros para controle aprimorado dos processos de soldagem a laser usando modelagem de feixe ilimitada e até 20 mm de posição de foco, influenciam quanto controle os soldadores a laser têm sobre a dinâmica do buraco da chave e da poça de fusão.
Civan Lasers e AMET colaboraram para desenvolver o sistema de soldagem a laser. “Os DBLs são semelhantes à tecnologia de feixe de elétrons em sua capacidade de oscilar o feixe em regimes de megahertz. No entanto, os DBLs podem fazer isso sem exigir um ambiente de vácuo”, disse o Dr. Eyal Shekel, CEO da Civan.
Os recursos exclusivos do DBL permitem a soldagem a laser de metais espessos pela primeira vez, de acordo com as empresas colaboradoras. As vantagens da tecnologia DBL incluem a eliminação da necessidade de chanfro e redução de HAZ e distorção, juntamente com velocidades de soldagem mais altas. As empresas
Bill Mayer, Editor nos EUAapresentarão o primeiro sistema, que está sendo produzido na fábrica da AMET em Idaho, EUA, em fevereiro de 2023.
A Primetals Technologies e a RHI Magnesita estão trabalhando juntas para desenvolver uma nova tecnologia de aço verde para substituir as usinas de alto-forno. O Smelter é um forno movido a energia elétrica e utilizado para fusão e redução final de ferro reduzido direto (DRI - Direct Reduced Iron). Operado em conjunto com uma planta de redução direta e um conversor LD (BOF), o Smelter produz metal quente para produção de aço e escória líquida que pode ser utilizada na indústria de cimento. A rota convencional do conversor BF-LD resulta em quase 2 toneladas de CO2 por tonelada de aço líquido. Segundo a Primetals Technologies, a nova tecnologia reduzirá as emissões de CO2 em um fator de seis, para 0,33 toneladas de CO2 por tonelada de aço líquido.
O material refratário protege o invólucro do forno contendo metal quente a temperaturas de pelo menos 1500°C. Composto por tijolos, ele se expande quando aquecido e suporta temperaturas
foram realizadas. A Primetals Technologies e a RHI Magnesita dizem que o Smelter está pronto para o mercado.
A Coolbrook, uma empresa de tecnologia de engenharia com sede na Finlândia, está trabalhando em uma tecnologia que pode produzir o calor extremo necessário para processos industriais a partir de fontes renováveis de eletricidade. A empresa diz ter encontrado uma maneira de atingir temperaturas de até 1700°C por meio de uma nova forma de eletrificação.
De acordo com a Coolbrook, seu RotoDynamic Heater (RDH) é a única tecnologia de aquecimento de processo elétrico capaz de atingir 1700°C sem queimar combustíveis fósseis. No RDH, o ar, o nitrogênio e os gases do processo são aquecidos a altas temperaturas, e o gás aquecido é usado fora do aquecedor para substituir a queima de combustíveis fósseis no aquecimento do processo. A empresa diz que a tecnologia pode substituir fornos e estufas movidos a combustíveis fósseis por aquecimento elétrico em processos industriais.
extremamente altas. O desempenho do material refratário é determinado por vários fatores, como tamanho, qualidade, projeto mecânico do forno e soluções de resfriamento.
A colaboração já existe há algum tempo e várias simulações
RDH reúne ciência espacial, turbomáquinas e engenharia química. Com ação aerodinâmica obtida por meio de um fluxo de lâmina rotativa, o RDH pode substituir fornos convencionais e fornos movidos a combustíveis fósseis em processos de aquecimento industrial, transmitindo diretamente a energia mecânica do eixo ao gás aquecido para fornecer calor de processo para a produção de aço, cimento e outros produtos químicos. Um motor elétrico aciona os rotores e o ar, o nitrogênio ou os gases do processo são aquecidos a temperaturas extremamente altas.
Coolbrook diz que a tecnologia pode ser adaptada às fábricas de produção existentes e estará pronta para uso em larga escala em 2024. Leia sobre isso aqui
Avanço com Soldagem por Feixe de Elétrons em Materiais de Seção Espessa A Sheffield Forgemasters anunciou um avanço na industrialização da soldagem por feixe de elétrons (EBW - ElectronBeam Welding) para materiais de seção espessa. Usando EBW, a empresa soldou duas seções de vasos forjados de aço nuclear de 200 mm de espessura (8 polegadas de espessura) e 3 metros de diâmetro (9 pés de diâmetro). A solda, equivalente a aproximadamente
10 metros (32 pés) de comprimento, foi concluída em uma única passagem e em um prazo drasticamente curto. A solda foi concluída em 140 minutos sem nenhum defeito reportável mostrado em testes preliminares não destrutivos (NDT). Uma solda desse tipo normalmente levaria meses e incluiria vários estágios de NDT e tratamento térmico, de acordo com a Sheffield Forgemasters, baseada no Reino Unido.
A Sheffield Forgemasters visa incorporar técnicas avançadas de fabricação, que proporcionarão economias significativas em tempo de processamento e custo por meio do potencial de EBW em relação ao método mais tradicional de soldagem de gás inerte de tungstênio para vasos de pressão de seção espessa. O processo EBW usa vácuo local e um canhão de elétrons de
alta potência, que penetra no material do vaso com um feixe de elétrons, para derreter e fundir os dois componentes em uma única passagem, em vez de construir várias camadas de arame de solda.
Bill Mayer EditorTelefone: +1 248-833-7388
E-mail: bill@industrialheating.com
Tomando como exemplo o produto forjado mostrado na Fig. 1, fica evidenciada na Fig. 2 a possibilidade de se prever fenômenos como o desgaste na matriz responsável pela fabricação deste mesmo forjado. Logo, o intuito aqui é falar um pouquinho sobre análises de matrizes e sobre os seus ganhos para a forjaria.
A partir de várias razões possíveis, um desgaste acentuado tende a evoluir para uma fratura da matriz, caso os esforços e as temperaturas não sejam reduzidas naquela região. A matriz mostrada na Fig. 2 sofreu fratura por fadiga. Uma fotografia desta fadiga e a respectiva previsão por simulação estão mostradas na Fig. 3. As possibilidades de previsão do desgaste e, inclusive, do número de ciclos para fadigar são análises preciosas que ajudam na definição de soluções e, consequentemente, na redução dos custos de forjamento.
Diversos fatores econômicos podem ser considerados na definição da redução de custos e no ganho de oportunidade quando se é implementada a simulação do processo de forjamento. Embora o conjunto de fatores econômicos possa variar e até mesmo apresentar elevada complexidade, boa parte desses está apresentada na Fig. 4.
O uso de um software de simulação normalmente não deve ser compreendido como um custo, mas como um verdadeiro investimento. Com o uso da simulação, torna-se viável o desenvolvimento de novos processos, a otimização de processos correntes e a redução de custos.
Em especial, para quem trabalha diretamente na produção, poder quantificar o número de peças que um ferramental pode produzir é de extrema importância para a eficiência de cada linha de produção. Tanto a produção quanto a ferramentaria alcançam ganhos. No caso das ferramentarias, por exemplo, o retrabalho se torna reduzido e outras despesas como mão de obra, insumos, eletrodos, ferramentas de usinagem etc. são minimizados.
Alisson Duarte é Consultor Técnico da SIXPRO Virtual&Practical Process e também Professor do Dept. de Eng. de Materiais da UFMG. Possui Pós-Doutorado em Metalurgia da Transformação. Ele pode ser contatado em alisson@sixpro.pro.
“O uso de um software de simulação normalmente não deve ser compreendido como um custo, mas como um verdadeiro investimento.”Figura 1. Produto forjado (a) via simulação no QForm UK e (b) na prática [Santos et al. Est. Desgaste e Fadiga Matr. Forj. Quente. 41º SENAFOR, 2022].
Como é sabido, esta coluna relata as observações, deduções, estudos e principalmente o acompanhamento ativo de testes de campo, oportunidades que são verdadeiros tesouros, agora reforçado pela parceria com meu amigo de longa data, Emerson Fabrete que também milita nessa área e com o qual tenho mantido interessantíssimo diálogos interessantíssimos e brain stormings especializados.
Em coluna anterior a intenção era mostrar a insubstitutibilidade do grafite em relação ao uso dos chamados lubrificantes sintéticos, sais, polímeros e os assim chamados NPFL (non pigmented forging lubricants) e comentei que a lubrificação de matrizes de alguns processos só os viabiliza com a utilização do grafite e que as tentativas de substituição do grafite por um lubrificante sem grafite são difíceis e até impossíveis. Agora afirmo que também não é qualquer grafite que é adequado para determinados processos de forjamento cada vez mais rápidos e automatizados, onde uma capacidade de formação de camada a alta temperatura e com muita rapidez são requeridas.
É que nos últimos anos houve significativas melhorias no processo de redução de tamanho de partícula que beneficiou tanto os grafites sintéticos como os naturais. Outras propriedades, até então pouco conhecidas vieram a baila, como a cristalinidade e tipos de ligações dentro dos cristais de grafite que passaram a ser utilizados de maneira muito inteligente pelos micronizadores.
E mostramos que um grafite bem selecionado e bem aplicado possibilita os melhores resultados em termos de vida de matriz, preenchimento da gravura, redução de força de forjamento, qualidade do forjado, redução de sucata e a redução de consumo de lubrificante.
O interessante é que às vezes existem benefícios que são mais importantes, por exemplo, processo de forjamento transfer a morno a vida de matriz é extremamente sensível ao tipo de grafite e ao seu processo de redução de tamanho de partículas. Num processo de forjamento a martelo ou prensa de altíssima capacidade o que interessa é a elevada temperatura de molhamento e velocidade de formação de camada.
Outra coisa que nos ficou bastante clara na tentativa
de passagem de um tipo de grafite para outro. Explico, numa tentativa de troca de um grafite premium para um lubrificante polimérico, o resultado “menos pior” foi obtido ajustando as condições de aplicação a partir da estaca zero. Num caso onde foi feita a tentativa de substituir o grafite premium por um grafite natural de granulometria 3 a 4 vezes maior, para se conseguir uma vida de matriz equivalente houve a necessidade de se concentrar o teor de sólidos 3 vezes mais. A consequência foi um excesso enorme que causou um build up enorme.
Tentativas de substituição de produtos de grafites naturais com granulometrias de 4 a 10µm para grafites sintéticos de 1 a 3µm mantendo os parâmetros de lubrificação, vazões, pressões, trajetos, tempos e até tipos de bicos em geral não produzem um bom resultado. Haverá que se partir da estaca zero e usar os parâmetros corretos para aquele tipo de grafite.
E é aí que surge a grande pergunta: quais são os parâmetros para cada tipo de grafite? Ou a pergunta mais básica e profunda seria: qual é a quantidade certa de grafite para proporcionar os benefícios de um bom forjamento, vida de matriz e qualidade de peça forjada.
O Toyota Paper, que também já foi analisado aqui e que merece até uma revisão face aos novos reconhecimentos nos dá uma boa pista para os parâmetros de um grafite premium, gotas do pulverizado as menores que possíveis, para isso precisamos de bicos adequados com pressão de ar e pressão/vazão de lubrificante ajustáveis.
E é aí que entra a temperatura da superfície de trabalho.
Lubrificante de Matriz – Grafite sintético, o mais insubstituível
“Nos últimos anos houve significativas
melhorias no processo de redução de tamanho de partícula que beneficiou tanto os grafites sintéticos como os naturais.”
Até então, se trabalhou com uma janela de trabalho do lubrificante que começava em 100ºC, temperatura de evaporação da água até uma temperatura máxima chamada de molhamento, que é a temperatura máxima na qual o lubrificante consegue “molhar”, aderir à superfície quente para formar camada. No entanto, ficou provado que, se os 100ºC são suficientes para secar a totalidade da água veículo do grafite não haverá calor suficiente para a mecânica de adesão do grafite à superfície quente. Isso ocorre quando a substância orgânica que acompanha o grafite o “assa” à superfície quente. Deduz-se que a camada de grafite é constituída de uma boa camada de aderência formada até no mínimo 200ºC, e quando a temperatura abaixa de 200ºC forma-se uma camada de acumulação, mas como ela não está bem aderida não consegue contribuir com a eficiência de lubrificação da camada.
Também a expressão da janela de temperatura de trabalho que começa em 100ºC, por si, já se revelou um
engano já que na realidade o trabalho do lubrificante começa a alta temperatura da superfície das matrizes e é ele que vai abaixando a temperatura pela evaporação da água e “assamento” do grafite à superfície quente.
Portanto passamos a considerar a temperatura mínima do final da janela de funcionamento do lubrificante como sendo 200ºC e na temperatura máxima e inicial é que se encontram as diferenças. Pelas minhas observações, os grafites naturais, mesmo com granulometria muito fina tem uma capacidade de formação de camada cerca de 300ºC enquanto que os grafites sintéticos conseguem formá-la a quase 400ºC. Esses 100ºC a mais são muito importantes pois representam mais uma oportunidade de formação de camada do grafite. Além do mais, o grafite sintético apresenta o que chamo de “efeito oportunista” de formação de camada. Pulverizado sobre uma superfície com temperatura acima de 400ºC, há uma refrigeração acompanhado de uma iniciante formação de camada,
isto é, o grafite sintético não só forma uma camada a temperatura elevada, mas ele começa a formar camada mesmo acima de 400ºC.
Isso quer dizer que não haverá necessidade de um processo de refrigeração das superfícies quentes para só depois ocorrer a formação da camada lubrificante, evitando assim a fadiga térmica que nucleia as micro-trincas superficiais e principalmente ganhando tempo de ciclo.
No gráfico 1, a temperatura de molhamento do lubrificante de matriz é de cerca de 400ºC. A espessura de camada é de mais de 20 µm e começa a se formar em menos de 1 segundo após início da pulverização.
No gráfico 2, a temperatura de molhamento do lubrificante de matriz é de cerca de 300ºC. A espessura de camada é de um pouco mais de 15 µm e começa a se formar em cerca de 2 segundo após início da pulverização.
Conclusão: O grafite sintético começa a formar camada a
cerca de 400ºC enquanto que o melhor grafite natural começa a formar camada a cerca de 300ºC. Isso faz com que o grafite sintético comece a formar camada de adesão mais rapidamente. Característica essa que vem de encontro com os modernos processos de forjamento automático onde o tempo para a lubrificação de matrizes é escondido atrás do tempo de manipulação das peças forjadas.
Henri Strasser é engenheiro e sócio-diretor na Strasser Consultoria de Projetos Ltda, , consultor especializado em Metalforming para a Henkel e representante da AED Automation. Ele pode ser contatado em: henristrasser@uol.com.br.
Apoios:
Organização:
David Pye – Pye Metallurgical International Consulting
São apenas 110 anos desde o trágico naufrágio do navio inafundável, o RMS Titanic. A primeira parte deste artigo enfocou os rebitadores de proa e popa e o próprio processo de rebitagem. Esta segunda parte mergulha mais fundo no naufrágio do navio.
Oninho de corvo no alto do navio observou o iceberg a uma distância de aproximadamente 1,25 milhas (aprox. 2 km) à frente da embarcação usando a visão visual. Em outras palavras, eles não receberam binóculos. Eles fizeram suas observações enquanto o navio flutuava / movia-se rapidamente em direção ao iceberg. É um fato conhecido que aproximadamente 1/10 do iceberg é observado na água com cerca de 7/10 a 9/10 abaixo do nível da água.
Outras preocupações incluíam:
• A temperatura da água do mar estava em aproximadamente -3°C, o que significa aproximadamente 3°C abaixo da temperatura de congelamento da água. Isso, é claro, se devia à salinidade da água do mar naquele ponto. A quantidade de sal presente na água do mar determinaria a temperatura em tempo real. No entanto, o ponto de congelamento da água do mar estava bem abaixo da temperatura de congelamento da água doce.
• Devido aos elementos de contaminação no ferro forjado, as propriedades mecânicas não eram completamente conhecidas. No entanto, as propriedades mecânicas do ferro forjado provocaram sérias alterações nas propriedades esperadas
• O iceberg era aparentemente um volume grande e considerável (Fig. 6). Observe que o iceberg foi fotografado durante o dia e não à noite quando ocorreu a colisão.
Houve também um diferencial de temperatura entre as placas
externas que estavam em contato direto com a água do mar e em temperatura ambiente no interior da embarcação. Este diferencial de temperatura também seria responsável por qualquer precipitação concomitante dentro do rebite de ferro forjado.
Dentro da própria embarcação, havia enormes portas de segurança nas salas das caldeiras para reduzir o risco de flutuar quando a porta fosse fechada. No entanto, essas portas de segurança estavam sendo abertas e fechadas para acesso a outros compartimentos do casco. Isso permitiu que grandes quantidades de água do mar entrassem nas salas das caldeiras e das máquinas, contribuindo assim para o aumento do peso da água adicionado a uma taxa muito rápida.
As fraturas do casco e da placa da quilha foram enterradas no fundo do oceano quando a embarcação começou a se quebrar. Isso significa que nenhum dos rebites do arco foi recuperado. No rompimento secundário do vaso, no entanto, as fraturas pareciam começar atrás da chaminé número três. Estes eram os rebites de liga de aço.
Além disso, quando a parte da popa do navio começou a se romper, isso ocorreu devido à ocorrência de condições de compressão e tração.
Os rebites que estavam no fundo da quilha começaram a experimentar uma condição de compressão, enquanto os rebites acima do nível da quilha começaram a sofrer tensões de tração com o carregamento mecânico sendo tal que a seção da popa (logo atrás da chaminé número três) começou a falhar. Pode-se notar como um ponto de falha potencial que as fraturas dos rebites de popa ocorreram na seção de popa devido à transição dos rebites de liga de aço, que eram usados na seção central da embarcação, e os rebites de popa (os rebites de ferro forjado).
Outra contribuição do rebite para a falha do casco seria o fluxo de grãos como visto na Fig. 8. A placa indica um fluxo de grãos vertical, e o rebite exibe um fluxo de grãos horizontal em ângulos retos ao fluxo direcional de grãos da placa. Foi ainda notado que apareceram fissuras microscópicas na placa perfurada no ponto de perfuração da placa.
Conclusões
Na opinião deste escritor, vários itens parecem ter sido negligenciados na construção do Titanic e em seu eventual naufrágio.
• Era óbvio a partir de observações microscópicas (e confirmadas com testes mecânicos) que os rebites de ferro forjado estavam muito contaminados com corpos estranhos.
• A operação de aquecimento do rebite no conjunto do casco foi deixada para a “visão do olho” pessoal.
• Não houve medição ou controle de temperatura na câmara do forno. Coube aos rebitadores adivinhar qual seria a temperatura perfeita.
• Não havia controle real sobre quantos minutos os rebites de ferro forjado estavam na temperatura apropriada, nem havia controle sobre o tempo no forno.
7. A embarcação atingiu o iceberg a estibordo da embarcação. Todos os rebites na proa foram fabricados com ferro forjado contaminado e não aço. O impacto do iceberg estava abaixo da linha d'água do navio
iceberg.
• O escritor acredita que a Harland and Wolff não inspecionou a qualidade do rebite quanto à composição e propriedades mecânicas no recebimento de seu fornecedor.
• O navio estava viajando a aproximadamente 21 nós através de um campo de gelo. Do ponto de observação do iceberg, não houve tempo de evitar a colisão.
Tenho uma crença muito simples de que o tratamento térmico pode literalmente fazer ou quebrar o produto que está sendo tratado. Muitos produtos produzidos hoje podem ser considerados vitais para a vida e para a integridade física de indústrias como aeroespacial e automotiva. Eu sempre disse: “Faça certo da primeira vez, porque a segunda vez provavelmente lhe custará dinheiro”. Em relação ao RMS Titanic, o construtor naval Harland & Wolff é um excelente exemplo dessa filosofia simples.
• Havia pouco ou nenhum controle sobre a qualidade de entrada do ferro forjado selecionado para juntas de placas.
• O bom treinamento foi claramente omitido. Os rebitadores confiaram apenas na experiência pessoal e nas críticas dos membros da equipe de rebites.
• Não houve premeditação dada ao efeito de contaminantes materiais que seriam propagados pelo nível de salinidade da água do mar e pela temperatura no ponto de colisão com o
Este artigo teve início na edição anterior.
David Pye - Pye Consultoria Metalúrgica Internacional David Pye é um escritor contribuinte. Ele pode ser contatado pelo telefone +1 757-968-1007, pye_d@ymail.com ou https://www.pyemallurgical.com. Todas as figuras/gráficos fornecidos pelo autor, exceto onde indicado.
A cementação a vácuo ou mais especificamente a cementação a vácuo de baixa pressão (LPC - Low Pressure Vacuum Carburizing) assumiu várias indústrias como a principal opção de cementação nos últimos 25 anos. Este artigo revisará as particularidades do processo Infracarb® patenteado pela ECM para atingir os requisitos metalúrgicos na fase de desenvolvimento do tratamento térmico. Analisaremos em quais parâmetros os clientes precisam se concentrar em relação aos do tratamento da atmosfera. As vantagens da instalação de cementação a vácuo em relação à microestrutura, uniformidade da cementação, a maior temperatura de tratamento disponível e o controle do processo da carga para carregar durante a produção. Exemplos de tempo de ciclo e resultados em aços cementados clássicos serão mostrados em relação à têmpera de óleo e gás, controle de distorção e análise de custos.
Introdução
Fornos a vácuo e processos de cementação a vácuo estão no mercado desde os anos sessenta com sucesso em aplicações e experimentos específicos. Durante os últimos 25 anos, esta tecnologia foi introduzida no mercado da indústria automotiva como um dos processos de tratamento térmico preferidos para substituir os fornos de atmosfera em novas aplicações. Aceito pelos principais fabricantes de automóveis e indústrias aeroespaciais, cada vez mais tratamentos térmicos são alterados para LPC (Low Pressure Vacuum Carburizing - Cementação a Vácuo de Baixa Pressão). O crescimento das instalações em
todo o mundo é exponencial com a comprovada flexibilidade, repetibilidade e desempenho alcançados em materiais de cementação padrão e materiais especiais. A capacidade da mais recente tecnologia de resfriamento a gás usando gases com pressão de 20 bar para têmpera tem sido uma grande influência, aumentando as possibilidades do processo. Agora, LPC e têmpera de gás de alta pressão (HPGQ - High Pressure Gas Quenching) são quase sinônimos. A alta velocidade e as rápidas taxas de resfriamento agora atingíveis na têmpera a gás permitiram que muitos materiais adicionais fossem resfriados a gás. Embora o óleo ainda seja uma necessidade em peças de grandes seções transversais, o HPGQ substituiu uma alta
Transição de Peças da Cementação em Atmosfera para a Cementação em Baixa
porcentagem de instalações como o meio de têmpera preferido. O controle de distorção também é um recurso central do HPGQ que tem sido preferido pelos clientes.
A cementação a vácuo a baixa pressão com o processo da ECM Technologies consiste em craquear o acetileno somente quando a carga atingir uniformemente a temperatura desejada de cementação sob um vácuo constante de baixa pressão entre 7 e 13 mbars. O processo Infracarb® é descrito pela alternância de boosts de um gás de processo e boosts de nitrogênio
durante a fase de difusão (ver Tabela 1). A duração e a quantidade de reforços estão relacionadas com o teor de carbono original do aço, a temperatura de tratamento, o carbono final desejado na superfície e a profundidade de revestimento necessária. Usar acetileno como o único gás de processo para o carreador de carbono e usar nitrogênio durante os tempos de aquecimento e difusão sob vácuo oferece a vantagem de um único gás e uma mistura de vários gases. Isso reduz qualquer influência do oxigênio no processo. Esta redução e eliminação de oxigênio é a principal razão pela qual não há oxidação intergranular devido ao tratamento térmico em comparação com a cementação atmosférica. O processo LPC é desenvolvido com o software ECM CBPWin® durante a fase de desenvolvimento do tratamento para atingir as especificações metalúrgicas na temperatura que melhor se adequa ao volume de produção e tempo de ciclo. (Ver Tabela 1 e 2) Devido ao vácuo, a temperatura de tratamento pode ser aumentada desde os fornos de atmosfera clássicos de 930°C - 950°C a 980°C até 1050°C sem crescimento significativo de grãos durante o tratamento e aumentos produtividade reduzindo o tempo de ciclo. Graças aos fornecedores de aço, os aços padrão da indústria, como 5120, 8620 ou 4320, foram modificados para se adequar a essas temperaturas, aumentando o teor de liga e adicionando microligas. Essas melhorias nos aços resultaram em melhor temperabilidade, bem como na melhoria constante da célula de têmpera a gás, dada a vantagem de mudar da têmpera a óleo para a têmpera a gás com resultados metalúrgicos comparáveis. Eles também mostram um ambiente de trabalho significativamente mais limpo com redução ou eliminação de limpeza e/ou usinagem dura após o tratamento térmico e permite que o forno LPC seja reconhecido como uma máquina-ferramenta na linha de produção (consulte a figura 1). O tratamento térmico não é mais uma parte perigosa e assustadora da fabricação colocada atrás de uma parede à prova de fogo.
O forno a vácuo, com múltiplas configurações, permite um ambiente de parede fria sem cortinas cortafogo. Esses sistemas de fornos são muito bem-vindos nas células de usinagem das fábricas. Paredes cortafogo de tijolos não são mais necessárias para separar esta parte importante da fabricação.
A repetibilidade do processo LPC da carga carregar é controlada em cada etapa do aquecimento, cementação e têmpera por sensores e análise de computador entre os parâmetros da receita e o próprio forno. Esses sensores estão principalmente no monitoramento de pressão de gás, fluxo e temperatura, pois não há sensores ou sondas in-situ no forno durante o processo. O ciclo de aquecimento da receita é desenvolvido para o tamanho da carga e o desenho da peça. Quando os resultados da receita são validados, toda carga que é executada com a receita deve respeitar os diferentes parâmetros da mesma. Para o processo de qualidade, cada vez mais dados são registrados. Durante o ciclo de aquecimento, as temperaturas e os tempos são verificados para seguir a receita específica o mais próximo possível da classe do forno. O processo Infracarb® de cementação e boosts de difusão são controlados pelo tempo do boost e pela vazão dos gases de processo e nitrogênio.
Para a têmpera, em função do desenho da célula e da escolha do meio gás ou óleo, são verificados o tempo, a pressão, o sentido do fluxo e a velocidade do gás para seguir a receita. Além disso, durante uma têmpera de óleo, a temperatura do óleo é verificada e resfriada para respeitar as tolerâncias da receita ao longo do ciclo. Todos esses parâmetros são registrados e formatados para um relatório de cada carga, mostrando as curvas de temperatura, consumo de energia e duração dos diferentes eventos do ciclo de tratamento térmico. No caso de variação da receita, alarmes serão exibidos e o cliente terá a possibilidade de identificar a origem do problema. Esses dados são relativos à própria receita. Existem também vários outros parâmetros sobre como o forno deve funcionar que executam relatórios para informar ao cliente sobre transferências de carga ou eventos durante o processo.
As informações a seguir explicam as vantagens do LPC em diferentes temperaturas de cementação em relação aos tempos de ciclo, aumento de produtividade e economia de custos. Este estudo é baseado em um aço carbono 0,2% e uma carga de 500 Kg. As temperaturas escolhidas são 930°C, 960°C, 1000°C e 1030°C; o tempo de aquecimento antes da cementação foi fixado em 90 minutos para as duas temperaturas mais baixas e 120 minutos para as duas temperaturas mais altas. Uma temperatura de austenitização de 900°C foi adicionada ao ciclo para preocupações com distorção; Foram adicionados 50 minutos para as duas temperaturas mais baixas e 75 minutos para as duas mais altas. Além disso, foram estudadas quatro profundidades de camada diferentes: 0,5, 1, 1,5 e 2 milímetros (ver Tabela 1). Para a profundidade efetiva da camada menor (ECD - Effective Case Depth), apenas 930°C e 960°C foram estudados neste caso, mas isso não significa que a cementação para 0,5 mm não possa ser realizada em temperatura mais alta.
Este estudo mostra as vantagens de se utilizar temperaturas de cementação mais altas. Por exemplo, um aumento de temperatura de 30°C de 930°C dá uma
redução do tempo de cementação de 40 a 55% em função da profundidade de camada desejada. Executar o processo de cementação a 1000°C versus 930°C proporcionará uma
redução de tempo de 70 a 75%. A cementação a 1030°C trará essa redução para 80-85%. No caso de ECD a 2 milímetros entre a temperatura clássica de 930°C e 1030°C economizará mais de 13,5 horas ou 68% do tempo de ciclo. Esta é uma grande economia de tempo e custos, especialmente no trabalho de engrenagens grandes e camadas profundas.
Para um forno modular padrão de 8 células de aquecimento, um aumento de produção de 15 a 55% pode ser feito para as 2 peças de camada menor se a temperatura for aumentada para 960°C; para as peças com camadas mais profundas, a produtividade sobe para 70%. Executar a produção a 1000°C para profundidades de camada entre 1 e 2 mm resultará em um ganho de 55 a 155%. Fazer 1030°C aumentará a produção de 70 para 215% para as mesmas profundidades de camada.
Com base nos tempos de ciclo e no uso de gás de processo em um sistema LPC de produção de 8 células executando ECD de 1 mm a 1.030°C versus 930°C, economizará até 20% por carga. A quantidade de economia irá até 35% para 1,5 mm e até 50% para uma profundidade de camada de 2 mm. Por exemplo, uma carga de 68 dólares a 930°C custará 36 dólares a 1030°C para ECD de 2 mm com resfriamento de nitrogênio de 20 bar. A repartição do custo de uma carga geralmente pode ser dividida em 90% para a eletricidade, 7% para o gás de processo e 3% para o nitrogênio, incluindo a têmpera sob nitrogênio.
Como temos falado muito sobre o método de cementação e as temperaturas que estão sendo usadas para esse método, também devemos nos concentrar no método otimizado de têmpera. A têmpera é o processo mais importante para reter a microestrutura no formato necessário para fornecer a estrutura dos materiais no formato mais benéfico para oferecer resistência e durabilidade. Este processo para a maioria das aplicações sob atmosfera está sendo feito usando óleo, embora outros processos como sal e água também estejam disponíveis e sejam usados em quantidades reduzidas. Como o processo LPC foi escolhido pelos benefícios para as peças no fato de a camada de cementação ser muito uniforme e o processo ser feito em equipamentos muito limpos, também é desejável ter um método de têmpera que também possa operar em um ambiente limpo. Com a
têmpera a gás, isso é possível. (veja a Figura 4).
Como em qualquer processo de têmpera, a quantidade de meios de resfriamento que se movem pela superfície das peças processadas e é essencial a manutenção da eficiente remoção de calor do meio de têmpera. Isso não é diferente na têmpera a gás. Com movimento de gás mais uniforme e melhor remoção de calor, isso aumentará a eficiência
da têmpera de gás. Essas capacidades de uniformidade e transferência de calor aumentaram ao longo dos anos com melhores avanços no movimento de gás, tecnologia de trocador de calor e também movimento de gás através da carga para também melhorar o controle de distorção. Vemos isso porque as atualizações estão acontecendo em equipamentos mais antigos usando os mesmos
processos de peças, permitindo pressões de têmpera muito mais baixas para alcançar os mesmos resultados metalúrgicos. Porém, proporcionando menor distorção nas peças devido à menor pressão utilizada. (Ver Figura 3)
Razões adicionais para usar a têmpera a gás, como dissemos, é o processo limpo, além de fornecer peças limpas saindo do sistema do forno. Isso significa uma enorme economia no tratamento da água de lavagem para remover óleos e também economia na reposição de óleos que foram removidos por arraste na têmpera de óleo. No geral, com a melhoria dos materiais de liga usados para produção de peças, métodos de transferência de calor aprimorados e otimização da célula de têmpera a gás, a têmpera a gás está encontrando seu caminho em mais e mais aplicações. Essas aplicações adicionais incluem peças com seções transversais maiores e cargas mais pesadas.
Ao comparar a cementação em atmosfera com a cementação em baixa pressão, parece que as tecnologias a vácuo permitem uma economia significativa de energia. O desenvolvimento de fornos elétricos com tecnologias a vácuo agregam valor aos tratamentos térmicos tornando-os seguros, eficientes, altamente integrados e de melhor qualidade metalúrgica com uma relação custo/ desempenho otimizada. Os ganhos no consumo de gás estão diretamente ligados ao uso do vácuo e ao fato desses
fornos serem aquecidos eletricamente. De fato, o processo não requer nenhuma atmosfera carbonatada, mas apenas C2H2 e N2 que são injetados alternadamente durante o processo, liberando átomos de carbono que se difundirão na superfície das peças como discutimos anteriormente. Essa tecnologia elimina o gás necessário para aquecer o forno, bem como o fluxo permanente de gás usado para a cementação.
Após o resfriamento a gás, a lavagem não é mais necessária. Este processo de pós-lavagem foi levado em consideração nos cálculos de energia para têmpera em óleo porque é essencial. Gastos de energia adicionais, como aumento do esforço de retífica devido à camada de oxidação, aumento da distorção (permissão de retífica) e descarte de óleo usado, não estão incluídos. Mas mesmo sem os parâmetros adicionais, uma imagem clara da
economia de energia pode ser vista - Pro Tecnologia LPC. Além disso, uma tendência clara pode ser observada: quanto mais profundo o EHT (EHT - Effective Hardness Testing – Teste de Dureza Efetiva), mais econômico é o processo LPC.
Conclusões
O LPC tem o potencial de reduzir custos de tratamento térmico pela possibilidade de processos de maior temperatura com grande repetibilidade e qualidade da metalurgia carga a carga. Os clientes têm a chance de integrar o LPC diretamente em sua linha de produção, especialmente usando resfriamento a gás para fornecer um ambiente de trabalho mais limpo por dentro e por fora. A combinação de LPC, HPGQ e economia de energia, tempo de produção e redução da geração de carbono do processo de tratamento térmico torna esse processo uma necessidade de revisão para cada aplicação de cementação.
PARA MAIS INFORMAÇÕES: Dennis Beauchesne, gerente geral da ECM-USA, Inc. ECM-USA, Inc., Pleasant Prairie, WI, EUA. Email: Dennisbeauchesne@ecm-usa.com, Vincent Lelong, Gerente do Centro de Sinergia/Sr. Metalúrgico na ECM-USA, Inc. ECM-USA, Inc., Pleasant Prairie, WI, EUA. Email: vincentlelong@ecm-usa.com, 262-925-6320
Se o seu forno é o gargalo em sua operação, pode ser hora de considerar a adição de um novo. Este artigo analisa os fundamentos da estrutura e estilo do forno, seleção de refratários e projeto de combustão. Conclui com um estudo de caso recente.
Não é segredo que os fabricantes estão tendo dificuldade em acompanhar a demanda. Isso é especialmente verdadeiro para forjadores de aço, que estão enfrentando atrasos de até 18 meses. Mas existem alguns segredos para aumentar a potência do seu processo por meio de um projeto de forno inteligente, seja adaptando um forno antigo ou construindo um novo. Esses segredos estão em seu projeto de combustão, posicionamento do queimador, cálculos de BTU e especificações de revestimento refratário.
As forjas americanas estão se adaptando a um novo normal com reformas em massa, escassez de material, avanços intermináveis em tecnologia e novas regras e regulamentos para segurança operacional. Nunca foi tão importante para o seu forno industrial operar com a maior eficiência possível para acompanhar o aumento da demanda e atender às necessidades de cada um de seus clientes. Isso significa que a configuração de seu forno precisa ser otimizada com base em seus requisitos de produção. Otimize seu forno com base em seus requisitos de produção
Se o seu forno for o gargalo da sua operação, talvez seja hora de considerar a adição de um novo forno especificamente projetado para maximizar o rendimento da sua linha de produtos. Há uma tonelada de considerações a serem consideradas quando você embarca na construção de um novo forno, por isso é importante ter uma visão de 360 graus de seus requisitos e restrições. Um forno projetado de forma inteligente pode aumentar sua lucratividade e, ao mesmo tempo, ajudar a reduzir os acúmulos de produção.
Ao projetar um novo forno, comece observando sua operação atual e suas metas de produção de longo prazo. Quanto mais detalhado você conseguir, melhor. Defina o número de peças que deseja processar em quanto tempo, o tipo de material que está aquecendo, a forma e o peso de suas peças maiores e mais pesadas e a temperatura mais alta que precisa atingir. Responder a essas perguntas com antecedência ajudará a determinar a melhor opção para aquecer suas peças de maneira rápida e uniforme.
Depois de revisar suas metas de produção, você pode começar a avaliar diferentes métodos para abrir e fechar o forno. Faz sentido um forno basculante, onde as dobradiças do teto se abrem (Fig. 1), ou um tipo sino, que requer um guindaste para pegar a parte superior do forno e colocá-lo de lado para colocar o aço e tirá-lo de volta? Seria melhor um forno estilo câmara com uma porta tradicional?
Determine as dimensões internas e externas do forno. É importante saber quanto espaço você tem para trabalhar, sua proximidade com outros equipamentos e a configuração do seu fluxo de produção.
Tudo o que vai para o forno também precisa ser pensado com cuidado, como o carro que transporta as peças e o dispositivo usado para carregálo e descarregá-lo. Esses sistemas precisam ser cuidadosamente projetados para garantir que possam suportar o calor e lidar com o peso das peças que você está processando além da própria estrutura do forno.
A vida útil geral de um forno é amplamente determinada pela capacidade do revestimento refratário de suportar seu ambiente operacional hostil. As altas temperaturas dentro do forno e a variação de temperatura quando ele abre e fecha podem causar estragos no revestimento refratário. O mesmo acontece com as exposições químicas da escória e, às vezes, até mesmo da abrasão mecânica, dependendo da finalidade do forno. Infelizmente, é quase impossível encontrar uma única composição refratária capaz de suportar todas essas variáveis a um preço razoável. É possível substituir o revestimento refratário, mas você quer adiar essa despesa o máximo possível.
Um refratário de alta resistência (Fig. 2) com resistência à abrasão é mais propenso a rachar sob variações extremas de temperatura devido ao choque térmico. No entanto, o material refratário que não racha sob choque térmico ainda pode corroer devido à exposição a produtos químicos. Freqüentemente, você precisa equilibrar as propriedades do material para diferentes zonas para garantir a vida útil mais longa do refratário. O refratário usado próximo à
porta, onde ocorrem variações drásticas de temperatura, será diferente do tipo usado no teto e nas paredes laterais. Encontrar a combinação certa pelo preço certo pode ser muito complicado.
Agora que você conhece o tamanho, a forma e o estilo do forno – além de seus parâmetros de produção – você pode calcular o tamanho, número e posicionamento de seus queimadores para que o forno aqueça as peças na temperatura certa sem danificá-las.
A perda de calor é outro fator crucial. Calcule quanto calor você está perdendo quando a porta abre e fecha ou que escapa pelas paredes laterais ou pela chaminé, para que você possa chegar a um número de BTU e dividir pelo número de queimadores. Quanto mais largo o forno, maiores os queimadores (normalmente), de modo que eles empurram o calor com mais força para alcançar o outro lado do forno mais rapidamente.
Outras considerações incluem o nível de controle que
você deseja sobre o que está acontecendo dentro do forno, quais problemas potenciais podem surgir e as necessidades de manutenção que você pode ter no futuro. É possível projetar o forno de forma a tornar qualquer problema muito mais rápido, barato e fácil de resolver. Por exemplo, você pode dividir os queimadores em diferentes zonas, cada uma com seu próprio termopar, o que também permite maior ajuste e estabilidade.
Fornos especializados requerem conhecimento técnico e engenharia para obter os melhores resultados. Assim como há uma ampla gama de variáveis no processo de produção do aço, há ainda mais variáveis envolvidas no projeto de um forno. Desde o sistema de combustão até o carro que transporta o aço, existem centenas de considerações se você deseja um sistema que aumente a lucratividade. Além disso, o sistema deve ser projetado e construído para durar décadas, com manutenção mínima, permitindo atender às demandas de uma crescente base de clientes.
Um novo forno (ou até mesmo um retrofit) é uma grande despesa de capital, então escolha um fornecedor que entenda o seu negócio, tenha o conhecimento técnico necessário para atender às suas necessidades de equipamento e produção e possa garantir o máximo retorno do seu investimento.
Projeto de Forno para Processamento de Chapa de Aço Pesada
Uma planta de processamento de aço no Centro-Oeste americano confiou na nossa empresa Onex para projetar e construir um novo forno para expandir sua capacidade de produção. Eles precisavam adicionar um novo forno que aqueceria os lingotes de aço a uma temperatura interna de 1230°C. Os lingotes então vão para um laminador para processamento. Seu único forno existente pode levar até 16 horas para aquecer oito lingotes.
Durante nossa consulta inicial, descobrimos que este forno alimenta uma usina que ainda terá capacidade disponível mesmo após a adição do segundo forno. Esse fato
trouxe à equipe de projetos da Onex que, se conseguíssemos encontrar uma maneira de reduzir o tempo de aquecimento dos quatro lingotes adicionais, isso aumentaria o rendimento do cliente ainda mais do que o planejado. Considerando que eles têm apenas um forno para alimentar a fábrica agora, essa era uma perspectiva empolgante.
A Onex revisou vários projetos diferentes e, por fim, propôs um forno basculante. A seção superior da carcaça se dobra ao longo da borda traseira e se abre, permitindo que o carro que carrega os lingotes de aço quente entre e saia.
A chave para aquecer esses lingotes mais rapidamente é aquecê-los de cima para baixo, o que cria um calor mais uniforme. Ao apoiar os lingotes em pilares feitos de material refratário especializado, o fundo aquece na mesma proporção que o topo, criando uma distribuição de temperatura uniforme. A fim de evitar o impacto das chamas, a Onex acrescentou pequenos queimadores que disparavam em um caminho de chama estratégico abaixo das peças entre os pilares, com queimadores maiores queimando acima das peças. Este projeto de queimador auxilia no fluxo de ar e facilita uma melhor uniformidade de temperatura da peça.
O forno desta planta de processamento de aço (Fig. 4) foi
projetado para ter quatro zonas de controle – essencialmente uma para cada lingote – que oferecem um maior nível de regulação térmica à medida que os lingotes são adicionados e removidos do forno. Isso requer que o refratário resista ao choque térmico, além do calor ultra-alto. Projetamos um sistema refratário composto por formas projetadas, incluindo o deck de carros pré-moldados e pilares, juntamente com módulos de combinação de fibra cerâmica para o teto com face quente policristalina de grau refratário. A pré-moldagem das formas permite uma instalação mais rápida no local e fornece melhores propriedades mecânicas.
Nossos cálculos estimam que este novo forno (Fig. 5) será mais eficiente do que o forno existente e requer apenas manutenção de rotina. Novos motores e ventiladores a cada duas décadas podem ser planejados como uma despesa de capital. O novo forno ocupará cerca de metade do espaço do forno existente e operará quase a mesma quantidade de aço, aumentando o rendimento geral do cliente.
Durante nossa consulta inicial, descobrimos que este forno alimenta uma usina que ainda terá capacidade disponível mesmo após a adição do segundo forno. Esse fato trouxe à equipe de projetos da Onex que, se conseguíssemos
caminho de chama estratégico abaixo das peças entre os pilares, com queimadores maiores queimando acima das peças. Este projeto de queimador auxilia no fluxo de ar e facilita uma melhor uniformidade de temperatura da peça.
O forno desta planta de processamento de aço (Fig. 4) foi projetado para ter quatro zonas de controle – essencialmente uma para cada lingote – que oferecem um maior nível de regulação térmica à medida que os lingotes são adicionados e removidos do forno. Isso requer que o refratário resista ao choque térmico, além do calor ultra-alto. Projetamos um sistema refratário composto por formas projetadas, incluindo o deck de carros pré-moldados e pilares, juntamente com módulos de combinação de fibra cerâmica para o teto com face quente policristalina de grau refratário. A pré-moldagem das formas permite uma instalação mais rápida no local e fornece melhores propriedades mecânicas.
Nossos cálculos estimam que este novo forno (Fig. 5) será mais eficiente do que o forno existente e requer apenas manutenção de rotina. Novos motores e ventiladores a cada duas décadas podem ser planejados como uma despesa de capital. O novo forno ocupará cerca de metade do espaço do forno existente e operará quase a mesma quantidade de aço, aumentando o rendimento geral do cliente.
PARA MAIS INFORMAÇÕES: Patrick Laskey é Gerente de Desenvolvimento de Negócios da Onex Inc. Ele pode ser contatado em patrick.laskey@onexinc.com ou +1 814-440-1494. Para obter informações adicionais, visite https://onexinc.com. Todas as imagens são cortesia de Onex Inc.
Inscreva-se no site aquecimentoindustrial.com.br, para receber todas quartas-feiras nossa news em seu e-mail, basta colocar nome, e-mail e sua área de interesse!
Resumo
Uma maneira eficaz das indústrias obterem economias significativas e melhorias de qualidade é por meio de novas estratégias de controle de processos. A aplicação de princípios de otimização e controle inteligente de processos dinâmicos, possibilita reduções no número total de operações, do consumo de material e energia, além de minimizar o desgaste de equipamentos e ferramentas. Neste artigo, é apresentado um sistema de assistência para o processo de forjamento baseado na Inteligência Artificial desenvolvido no Centro Brasileiro de Inovação em Conformação Mecânica (CBCM). Paralelamente, uapresenta-se uma revisão aprofundada sobre as tecnologias que compõe sistemas avançados de digitalização nos processos de fabricação.
A indústria de manufatura está passando por uma transformação significativa na direção da digitalização, conectividade e maior flexibilidade dos processos. Esta rápida mudança é impulsionada pela chamada Indústria 4.0, tendência atual que propõe otimizar os processos de fabricação através da automação e análise de dados. Isso é possível através de sistemas ciber-físicos, da Internet
das Coisas (Internet of Things - IoT ) e da computação cognitiva e em nuvem, criando uma fábrica inteligente [1].
Na indústria de forjados, a demanda por alta qualidade e produção econômica está em constante crescimento ampliando o interesse em adotar a Indústria 4.0 em suas práticas. Existem várias incertezas no processo de forjamento que afetam a robustez e confiabilidade da produção. As propriedades do material de trabalho, a temperatura e o atrito são exemplos de variáveis que afetam significativamente a qualidade do produto final. Flutuações destes parâmetros podem aumentar a taxa de refugo, o retrabalho e, consequentemente, os custos de produção.
Para controlar estes parâmetros e tornar os processos mais eficientes e robustos, sistemas de controle complexos estão sendo desenvolvidos. Neste contexto, o Centro Brasileiro de Inovação em Conformação Mecânica (CBCM), em cooperação com as universidades UFSC, SATC, IFC e IFSul, está desenvolvendo um sistema avançado de assistência à produção baseado na integração da Inteligência Artificial (IA) nos processos de conformação mecânica.
Este artigo apresenta a proposta de assistência técnica a produção em desenvolvimento no CBCM e uma extensa revisão da literatura referente à digitalização do processo de forjamento.
O desenvolvimento atual das empresas de manufatura é impulsionado pela fusão do mundo do processo físico com os dados do processo digital. Com base nisso, é proposto o modelo de infraestrutura de produção integrada mostrado na Figura 1.
O objetivo da infraestrutura mostrada na Figura 1 é criar um processo de conformação autônomo com máxima eficiência e taxa mínima de refugo. Para tanto, sensores monitoraram continuamente as variações dos principais parâmetros do processo. Os dados captados, em conjunto com informações oriundas de réplicas
virtuais do processo e modelos analíticos, dão origem a um valioso banco de dados em constante expansão. Métodos de aprendizagem de máquina analisam estes dados e imagens digitais da produção, as mais completas possíveis, são disponibilizadas o tempo todo na linha de produção e remotamente.
Os enormes volumes de dados de produção tornam o modelo de IA suficientemente treinado e permitem que um processo de conformação autônomo seja desenvolvido. Assim, com a incorporação da Internet e da Inteligência Artificial, a fábrica é capaz de tomar decisões ágeis e bem fundamentadas.
KLOCKE et al. (2017) definiram quatro níveis diferentes de digitalização de processos de manufatura representados, esquematicamente, na Figura 2. Um sistema de primeiro nível apenas sinaliza os estados atuais do processo sem fazer uma avaliação. O operador da máquina interpreta esse estado e, a seguir, age com base em seu conhecimento e experiência.
O segundo nível de assistência monitora continuamente o processo e dispara rapidamente uma mensagem, no caso de o processo desviar dos limites especificados. Depois de perceber a mensagem, o operador da máquina age com base em seu conhecimento. O controle estatístico do processo é um exemplo desse sistema de assistência.
No terceiro nível de assistência, os dados diretos e indiretos do processo são registrados continuamente. A partir desses dados, o sistema modela as relações de causa e efeito entre os processos diretos e indiretos. O operador da máquina analisa e interpreta as informações de forma independente com base em seu conhecimento.
Um sistema de quarto nível trabalha com total transparência de informações e pode acessar todos os dados diretos e indiretos do processo, bem como todas as informações da empresa. Com a ajuda de dados históricos, as relações de causa e efeito são mapeadas com alta precisão. Usando algoritmos adequados e dados em tempo real, o comportamento do processo pode ser previsto com alto grau de assertividade e recomendações podem ser formuladas para o operador da máquina [2].
Os sistemas de digitalização de terceiro e quarto nível praticamente não foram introduzidos na prática até hoje,
especialmente na indústria brasileira. A razão para isso é que esses sistemas requerem extensos modelos cognitivos nos quais as habilidades cognitivas humanas também são mapeadas. A fim de acelerar o desenvolvimento deste grupo de sistemas de assistência, diferentes disciplinas especializadas devem trabalhar juntas.
O desenvolvimento proposto pelos pesquisadores do CBCM (Figura 1) compreende um sistema de assistência de quarto nível. Em um sistema avançado como este, as tarefas humanas devem ser simuladas. Como mostra a Figura 3, três etapas são necessárias para realizar esta tarefa: a aquisição de dados, o processamento de dados e a utilização de dados. As próximas seções apresentam em detalhes cada uma destas etapas.
A aquisição de dados é realizada através de sensores, criando um banco de dados para a tomada de decisão. O sensoriamento é uma das tecnologias-chave de tendências atuais das indústrias manufatureiras como IoT (Internet of Things) ou Industria 4.0 [3]. Atualmente, sistemas de monitoramento e coleta de dados são parte integrante de muitas operações de conformação mecânica e representam uma ferramenta indispensável para garantir a eficiência da produção. Sensores instalados em cada estágio de processamento e nas estruturas das máquinas detectam falhas de transferência e alimentação, quebras de ferramentas, sobrecargas, etc [4].
Vários sensores e dispositivos de monitoramento foram desenvolvidos para medir força [5], vibração [6], emissão acústica [7], temperatura [8], deslocamento [9]
e condições de atrito [10]. Os sinais obtidos por estes instrumentos são alterados se alguma anormalidade ocorre durante o processo.
O princípio básico do monitoramento consiste no uso de sensores adequados que “observam” o processo e “aprendem” o perfil correto dos sinais. Este perfil corresponde ao comportamento ideal e é conhecido como a assinatura do processo. A partir de áreas inteiras ou pré-selecionadas da assinatura, limites de controle superior e inferior são definidos para verificar a qualidade de cada peça produzida. Ou seja, em cada operação é verificado se os sinais obtidos estão dentro dos limites de controle aceitáveis. Sinais fora dos limites indicam a ocorrência de problemas no processo. Neste caso, ações são tomadas pelo sistema, como a exibição de mensagens de alerta para o operador ou o desligamento automático da máquina. Em alguns sistemas, as mensagens de alerta podem informar exatamente qual erro foi detectado, facilitando a tomada de ação corretiva.
A força é uma variável dependente cuja magnitude é
derivada das variáveis independentes do processo de forjamento. Dessa forma, o perfil dos sinais de força obtidos no processo reflete o comportamento de todas estas variáveis. Consequentemente, alterações desses sinais refletem variações no processo devido instabilidades. Quaisquer alterações geométricas nas ferramentas devido ao desgaste progressivo são evidenciadas nas forças requeridas no processo. Alterações na peça de trabalho, tanto na superfície quanto na dimensão, podem ser observadas como uma indicação de variações na força gerada. As condições de lubrificação contribuem significativamente para o sinal de força e para o desgaste da ferramenta, que por sua vez, também influencia os sinais de força nos ciclos seguintes [11]. A Figura 4 apresenta o comportamento da evolução da força de forjamento em função do deslocamento da prensa para três falhas comuns do processo de forjamento [4].
Strain gages são tradicionalmente usados como transdutores de força em sistemas de monitoramento de carga. Quatro ou oito sensores, geralmente em ponte, são montados em um ponto adequado na estrutura da prensa ou da ferramenta. Nos últimos anos, a utilização
piezoelétricos nos sistemas de monitoramento de força tem crescido, não apenas para o registro de carga dinâmica, mas também para medições quase estáticas [12].
A qualidade das informações adquiridas e a eficácia do monitoramento na detecção de desvios dependem da localização do sensor e da resposta de interesse. É desejável montar o sensor em um local facilmente acessível onde não seja propenso a danos. No entanto, esses locais geralmente são distantes da interface ferramenta-peça e, consequentemente, os sinais de força adquiridos incluem efeitos dinâmicos da máquina, além de informações sobre a deformação da peça. Os padrões de força são mais precisos se os sensores estiverem mais próximos da superfície da matriz e da peça [7].
Nos processos de conformação mecânica, o deslocamento das ferramentas é comumente controlado através do uso de transdutores de deslocamento linear (linear variable differential transformer - LVDT ). Por se tratar de um método preciso e confiável para medir distâncias lineares, estes sensores encontram usos também em máquinasferramenta modernas, robótica, aviônicos e fabricação computadorizada.
O deslocamento da ferramenta durante o processo de forjamento também pode ser registrado através da utilização de câmeras de alta velocidade, codificadores magnéticos, sensores a laser e acelerômetros.
Atualmente, as câmeras de alta velocidade são capazes de filmar uma cena com altíssima resolução (variando de cerca de 60×10 pixels a 2000×2000 pixels) com frequência de aquisição muito alta (variando de 24 fotos/s a 650000 fotos/s), e com memória interna suficiente para gravar todos os dados. Para medir o deslocamento de uma máquina de forjamento durante um golpe, o critério mais importante a ser configurado é a frequência de aquisição, pois ela deve ser suficientemente alta em relação à velocidade máxima da máquina [13].
A temperatura é um dos parâmetros mais importantes dos processos de conformação. Com base em medições de temperatura, os fenômenos que ocorrem ao longo do processo podem ser identificados e analisados. O monitoramento do processo de aquecimento fornece uma variedade de detalhes sobre a transferência de calor desenvolvida durante o processo, ampliando a compreensão dos fenômenos desenvolvidos [14].
No forjamento em matriz fechada a quente, a distribuição da temperatura e o histórico térmico são de imensa relevância, por exemplo, para a análise da vida útil das ferramentas. Além disso, as distribuições de temperatura nas ferramentas e na geratriz constituem dados de limite e de entrada para modelagens analíticas e numéricas.
A medição de temperatura em processos industriais
está entre os procedimentos mais complexos da engenharia térmica, uma vez que se trabalha sempre com medidas indiretas. Características de corpos termométricos diretamente dependentes da temperatura são utilizadas na medição. Volume de fluido e gás, comprimento de corpos sólidos, resistência, tensão elétrica na interface de dois metais e radiação térmica emitida são as características comumente utilizadas nestas práticas [11].
A medição por contato, utilizando termopares, é a forma de medição mais confiável e precisa devido ao contato direto com o corpo analisado. Contudo, a necessidade de contato é impossível para objetos sob tensão elétrica, em movimento ou distantes. Além disso, há a necessidade de proteger o sensor contra a radiação do entorno que não corresponde a do corpo de interesse. No forjamento, a impossibilidade de instalação do ponto sensível do termopar diretamente na superfície examinada é a principal desvantagem deste método. Nas ferramentas, a junta de medição do termopar fica abaixo da superfície, o que provoca grande incerteza [15].
Medições de temperatura sem contato, com o uso de câmeras termovisuais e pirômetros, são cada vez mais comuns na prática industrial devido ao progresso técnico no campo da eletrônica e à introdução da tecnologia digital. Estes dispositivos possuem uso extremamente fácil e funções de visualização contínua dos resultados, contudo, limitam-se a medidas de temperatura da superfície dos corpos. Tal medição é muitas vezes imprecisa devido à emissividade variável dos objetos analisados [11]. A Figura 5 (a) mostra um exemplo de análise termográfica da temperatura máxima na
superfície das ferramentas no processo de forjamento. Estas análises podem ser complementadas através da modelagem numérica, permitindo a determinação da distribuição de temperatura na camada logo abaixo da superfície da ferramenta ou após a conformação (Figura 5 (b)).
Uma das maiores dificuldades na medição de temperatura óptica em processos de forjamento é oxidação da superfície (formação de carepa). A emissividade, ou seja, a capacidade do material de emitir radiação, muda drasticamente com a formação superficial de óxidos. Por exemplo, em uma temperatura real da geratriz de 1200°C, o valor medido pode variar com uma mudança na emissividade em torno de 130°C. Para minimizar as influências da superfície, recomendase o uso de modernos pirômetros de quociente que medem a radiação em dois comprimentos de onda e determinam a temperatura a partir da razão das duas intensidades de radiação [16].
A técnica de emissão acústica (EA) é uma das mais importantes e avançadas ferramentas de avaliação não destrutiva de monitoramento de processos em tempo real. Um transdutor ou sensor acoplado a um corpo que sofre alterações dinâmicas detecta a energia elástica emitida pela amostra e fornece informações sobre as alterações dinâmicas que ocorrem neste corpo [17]. Assim, fenômenos como fratura, deformação, movimento de discordâncias e transformações de fase podem ser identificados. Esta técnica tem sido
amplamente utilizada para estudar vários processos de conformação e soldagem em diferentes materiais [18,19].
MULLINS et al., (1997) utilizaram a emissão acústica no monitoramento do processo de forjamento. Nesta investigação, modelos físicos de monitoramento foram desenvolvidos para prever a atividade da taxa de eventos de emissão acústica a partir de parâmetros como tensão, deformação e velocidade de deformação. Os modelos foram incorporados em um programa de simulação de elementos finitos e os sinais de emissão acústica gerados durante as operações de forjamento foram previstos [20].
A análise dos sinais de EA mostra que o processo de forjamento é caracterizado por três etapas: um rápido aumento inicial na atividade de EA, seguido de uma diminuição no EA e, por fim, novamente um aumento significativo no EA (Figura 6). A maior emissão acústica no início do processo tem sido atribuída à geração e movimentação de discordâncias no material da peça. Este fenômeno é seguido do encruamento no material devido ao aumento da densidade de discordâncias, gerando redução do EA. O novo aumento significativo do EA tem sido atribuído ao preenchimento da matriz que promove o aumento do atrito entre a matriz e o material da peça [41].
Estudos demonstram que a análise de sinais de emissão acústica também pode ser aplicada para o controle do atrito [17,20], para a detecção do preenchimento da matriz [21] e para determinar o desgaste de ferramentas de forjamento [11].
A introdução de novas tecnologias no ambiente fabril torna fundamental a construção de pontes entre os mundos virtual e físico. Isso é realizado através dos denominados Gêmeos Digitais (Digital Twin - DT ). DTs são réplicas virtuais do produto, processo ou serviço em que todas as operações devem ser analisadas, previstas e otimizadas antes da implementação no mundo real [22].
Os Gêmeos Digitais espelham características estruturais e comportamentais relevantes dos Gêmeos Reais (Real Twins - RT ). O acúmulo de conhecimento gerado pelos DTs introduz novas oportunidades de melhoria contínua para maximizar a eficiência e o valor agregado das empresas [23].
A maioria dos gêmeos digitais hoje é baseada em um conceito simples: coletar dados reais e usá-los no sistema virtual para modelar o comportamento esperado do sistema real. O objetivo é determinar os resultados do sistema sem acesso direto ao sistema real ou partes dele, evitando o método de “tentativa e erro”. Aplicando gêmeos digitais no processo de forjamento podemos simular cenários hipotéticos para, por exemplo, entender se a alteração de uma operação de conformação melhoraria a fabricação aliviando as forças requeridas, aumentando a produção, reduzindo defeitos e custos de fabricação.
Esta solução promissora maximiza a eficiência industrial através do mapeamento bidirecional entre o espaço físico e o espaço virtual seguindo um circuito fechado. Dados de simulação alimentam o sistema físico para calibrar as operações e aprimorar o desempenho do sistema. [44]. Assim é possível antecipar possíveis estados futuros e aprimorar o gerenciamento dos recursos ao longo do ciclo de produção.
A Figura 7 apresenta uma possível estrutura de gêmeos digitais representando a ligação entre um mundo físico e um mundo digital. O mundo físico inclui dispositivos associados a vários sensores e aquisição de dados. Os dados adquiridos são enviados para o espaço virtual onde são analisados para monitorar o processo. Várias tarefas de processamento de sinal, algoritmos de aprendizado de máquina e simulações são utilizadas para fazer previsões úteis sobre o processo e, assim, transmitir essas informações ao mundo físico para controle em tempo real. O retorno ou resposta do mundo digital pode ser previsões de parâmetros úteis para julgar o processo, estado e vida útil das ferramentas e da máquina, sugestões ao usuário sobre
como garantir um modo de operação seguro, etc.
Apesar da implementação de DTs ter o potencial de contribuir notadamente para indústria, sua engenharia ainda é um campo de pesquisa emergente [24]. Segundo GRIEVES et al. (2017), no futuro, acredita-se que esta tecnologia evoluirá possibilitando maior autonomia e reduzindo a complexidade operacional [26]. Os DTs terão autonomia para identificar e gerenciar informações de diferentes fontes, detectando e mitigando desvios no processo. Modelos e controles adaptativos serão utilizados para gerar o auto-ajuste do processo de forma ágil [27].
Durante as operações industriais, os DTs são executados em sincronia com as contrapartes físicas, com o objetivo principal de rastrear inconsistências de dados entre o espaço físico e virtual. Inconsistências entre os dois espaços exigem a adoção de melhores estratégias de calibração e teste que envolvam modelos de DT e contrapartes físicas para sustentar estimativas, otimizações e previsões mais precisas dos processos industriais [28].
O sucesso do emprego de DTs depende fundamentalmente da consistência dos dados que relacionam o espaço físico contínuo e o espaço virtual discreto. Os dados inseridos nas DTs são de importância crítica, pois são responsáveis pela tomada de decisões racionais e pela execução precisa, ajudando a eliminar interrupções operacionais e incertezas [22].
Os processos de aquisição, processamento e utilização de dados devem ter um banco de dados comum em uma nuvem. A nuvem pode ser entendida como um repositório centralizado para grandes quantidades de dados brutos (ou minimamente processados) de várias fontes [53]. As tecnologias de nuvem permitem armazenar grandes quantidades de dados em máquinas virtuais que não precisam estar alocadas em espaços físicos dentro da empresa. A ferramenta é capaz de agregar dados de diferentes fontes e a expansibilidade dos bancos de dados. Isso permite o desenvolvimento de efeitos de rede positivos, que aumentam os benefícios do sistema de assistência a cada novo conjunto de dados [29]. Neste contexto, a infraestrutura de TI deve garantir uma conexão sem problemas com a nuvem e aspectos de segurança de dados devem evitar vulnerabilidades, pois os dados transitam entre servidores externos.
Com a ajuda da arquitetura de dados, os sistemas de assistência técnica à produção podem cumprir três tarefas essenciais relacionadas a uma máquina ou processo [2]:
• Reconhecer/agrupar estados: respondendo perguntas como: “Quais fatores têm influência no desgaste da ferramenta?”;
• Prever estados: respondendo perguntas como: “Qual é o valor de desgaste da ferramenta amanhã, depois de amanhã ou em uma semana e qual a probabilidade desse valor de desgaste ser verdadeiro?”;
• Decidir com base nos estados: respondendo perguntas como: “A ferramenta precisa ser trocada no turno da noite ou a troca da ferramenta pode ser adiada para o primeiro turno sem prejudicar a qualidade dos componentes?”.
A tarefa de reconhecer/agrupar estados pode ser realizada com algoritmos de agrupamento (clustering). Algoritmos de agrupamento são processos de aprendizado não supervisionados. Com esses métodos, as conexões entre as variáveis de processo e resultado podem ser identificadas exploratoriamente.
Um algoritmo de agrupamento bem conhecido é o “ k-means”. Este algoritmo divide iterativamente um conjunto de dados em metades e calcula um data center (“média”) para ambas as metades. O método é repetido até que a distância entre os pontos de uma metade e o data center tenha sido minimizada. K-means é um dos processos de clustering de particionamento. Para questões mais
complicadas, procedimentos mais complexos podem ser usados [30].
A previsão de uma determinada variável de estado relacionada à produção pode ser realizada com o uso de algoritmos de regressão. Os algoritmos de regressão mapeiam uma dependência entre as variáveis de entrada e a variável de saída usando modelos matemáticos. O desafio aqui é encontrar correlações estatísticas que podem ser descritas por uma relação de causa e efeito. A forma mais simples de regressão é a modelagem linear entre as variáveis de entrada e saída. Este algoritmo é particularmente adequado para prever tendências lineares e mudanças sistemáticas em um conjunto de dados dependente do tempo [2]. De um ponto de vista estatístico, entretanto, os cenários mais realistas são caracterizados por interações não lineares. Para ser capaz de representar essas relações, existem abordagens matemáticas, por exemplo, equações de regressão exponencial ou polinomial e métodos de aprendizado de máquina [31].
A decisão com base nos estados e na distribuição de probabilidades requer a combinação de algoritmos de regressão e classificação. Os algoritmos de classificação podem ser usados com base nas análises de agrupamento ou regressão realizadas previamente para atribuir o status atual ou futuro a uma categoria e fornecer-lhe uma probabilidade
de correlação [2].
As Redes Neurais Artificiais (RNAs) podem resolver problemas complexos e não lineares, com a capacidade de usar dados atuais e históricos [32]. As RNAs são capazes de executar funções complexas, como adaptação, generalização e aprendizado. As redes neurais artificiais em particular têm o potencial de reproduzir relações complexas de causa e efeito e tomar decisões confiáveis [2].
As RNAs baseadas no princípio do processo do cérebro humano, tem sido utilizadas para prever as condições do ferramental e monitorar o processo de forjamento [5]. A aplicação de redes neurais artificiais na conformação mecânica também pode ser vista no planejamento do processo, para determinar métodos de conformação adequados a partir da geometria do produto e para a previsão do número de estágios de conformação necessários. OSAKADA E YANG (1991) previram a localização das fraturas da matriz e defeitos de superfície no produto final usando RNAs. As RNAs também foram acopladas ao método dos elementos finitos para prever forças e tamanhos iniciais das geratrizes, projetar a geometria da ferramenta e prever as forças do processo.
KONG e NAHAVANDI (2002) desenvolveram um sistema on-line de monitoramento e controle das condições da ferramenta para um processo de forjamento
usando RNA e metodologia de fusão de dados (Figura 8). Com base em informações incrementais adquiridas usando um sistema específico de aquisição de dados, um sistema de gerenciamento foi desenvolvido para pré-processar os dados, compará-los com a vida útil projetada e o histórico real da ferramenta, prever a vida útil restante e fornecer um cronograma ideal de manutenção. Um modelo teórico que correlaciona as propriedades do material e as condições de produção com a vida útil da ferramenta foi desenvolvido considerando o histórico de processamento e a qualidade dos produtos. Os autores destacam que as condições da ferramenta são influenciadas, não apenas pelas condições atuais de processamento, mas também pelo seu histórico [5].
Após as etapas de aquisição, armazenamento e processamento de dados, um aplicativo deve implementar a etapa de utilização de dados por meio de uma interface homem-máquina ou máquina-máquina.
Atualmente, os sistemas disponíveis comercialmente contêm um gerenciamento de alertas adequado focado na redução dos tempos de parada. Através de configurações definíveis, as medições e os parâmetros podem ser monitorados proativamente. Os operadores podem ser
notificados em tempo real, no local de trabalho, no escritório, na diretoria, por e-mail, SMS ou outros serviços de mensagem quando qualquer desvio no processo for detectado. Os alertas devem ser apresentados de tal forma que facilite a identificação do problema mais importante em meio a todas informações disponíveis pelo sistema. Todos os alertas iniciados, assim como os tempos de reação correspondentes, são documentados automaticamente.
A partir da interface homem-máquina todos os ajustes, incluindo limites de capacidade da máquina, alarmes de proteção de ferramentas e contadores de peças podem ser feitos. Estes dados podem, por exemplo, ser transferidos para uma série de monitores na linha de produção por Bluetooth.
No caso de interface máquina-máquina, o sistema de assistência tem acesso a atuadores e age de forma automática. A Figura 9 mostra um exemplo de atuação do sistema. Durante a transferência pelas estações de processamento a temperatura da geratriz é constantemente medida. Se o valor sair da tolerância predefinida para o trabalho, a partida da prensa é impedida para evitar a sobrecarga na máquina. Uma vez que as condições de alarme sejam corrigidas, o relé é reiniciado automaticamente, permitindo que a máquina faça o ciclo. Este recurso não permitirá nenhum erro do operador que possa causar danos dispendiosos às ferramentas ou à
máquina. Paralelamente, modelos de Inteligência Artificial - treinados a partir de dados analíticos, simulações numéricas e de históricos - definem a ação necessária para corrigir o desvio no processo. A operação de aquecimento é, então, automaticamente corrigida, impedindo que a próxima peça seja produzida de forma inadequada.
Este artigo se propôs a apresentar uma extensa revisão sobre as tecnologias que constituem a digitalização do processo de forjamento a partir da proposta de sistema avançado de assistência à produção em desenvolvimento no Centro Brasileiro de Inovação em Conformação Mecânica (CBCM). As tecnologias apresentadas têm potencial para tornar o setor de forjamento mais competitivo. A implementação de um sistema de assistência a produção baseado em dados torna possível a tomada de decisão de forma ágil, com decisões bem fundamentadas e a auto-otimização e controle das operações. Dessa forma, apostando em estratégias relacionadas à Indústria 4.0 e na modernização das operações, é possível ampliar a capacidade de competição da indústria nacional frente aos produtos importados.
Agradecemos as entidades de pesquisa CNPq e Capes pelo fomento à pesquisa brasileira. Este estudo está sendo financiado, em parte, pelo Conselho Nacional de Desenvolvimento Científico e Tecnológico - CNPq –Chamada CNPq/MCTI/FNDCT Nº 18/2021 - Faixa
B - Grupos Consolidados (Código de financiamento: 404196/2021-7). Este estudo teve aporte por Bolsa de Produtividade em Pesquisa – PQ 1 (Chamada CNPq Nº 4/2021), Bolsa PDJ (Chamada CNPq 25/2021 - PósDoutorado Júnior - PDJ 2021), Bolsa de Doutorado (Programa CAPES/PROEX - IES) e Bolsa de Doutorado – GD (CNPq - Cotas do Programa de Pós-Graduação).
[1] KIM H., Industry 4.0 and AHSS Applications, World Auto Steel, 2021.
[2] KLOCKE, F., KAMPS, S., MATTFELD, P., SHIROBOKOV, A., STAUDER, J., TRAUTH, D., Assistenzsysteme in der Produktionstechnik, Virtuelle Instrumente in der Praxis VIP, 2017.
[3] KAGERMANN H., WAHLSTER W., HELBIG J., Final report of the Industrie 4.0 working group, ACATECH, 2013.
[4] KIM S.Y., EBINA A., SANO A., KUBOTA S., Monitoring of process and tool status in forging process by using bolt type piezo-sensor, Procedia Manufacturing 15, 2018.
[5] KONG L.X., NAHAVANDI S., On-line tool condition monitoring and control system in forging processes, Journal of Materials Processing Technology, Volumes 125–126, 2002.
[6] GE M., ZHANG G.C., DU R., XU Y., Feature extraction from energy distribution of stamping processes using wavelet transform, J Vib Control 8:1023–1032, 2002.
[7] JAYAKUMAR T., MUKHOPADHYAY C.K., VENUGOPAL S., MANNAN S.L., RAJ B. A review of the application of acoustic emission techniques for monitoring forming and grinding processes. J. Mater Process Technol 159:48–61, 2005.
[8] NG Y-M.H., DU R., Reconstruction of 3D thermal distribution from infrared images. In: Proceeding of the first international symposium on mechatronics, pp 379–383, 2004.
[9] LI X., BASSIUNY A.M., Transient dynamical analysis of strain signals in sheet metal stamping processes. Int J Mach Tools Manuf 48:576–588, 2008.
[10] KIM H., SUNG J.H., SIVAKUMAR R., ALTAN T., Evaluation of stamping lubricants using the deep drawing test. Int J Mach Tools Manuf 47:2120–2132, 2007.
[11] HAWRYLUK M., ZIEMBA J., Possibilities of application measurement techniques in hot die forging Processes, Measurement, 2017.
[12] INTERNATIONAL COLD FORGING GROUP, document No.18/07, 40 Years History Document, 2007.
[13] DURAND C., FREUND L., BAUDOUIN C., BIGOT R., GUÉRIN J., Comparison of different sensor technologies to monitor a forging process, 24th International Conference on Material Forming, 2021.
[14] POLOZINE A., LIMA D.R.S., SCHAEFFER L., Desenvolvimento de Novo Método de Medição de Temperaturas em Forjamento, FORGE, 2010.
[15] POLOZINE, A. Desenvolvimento da técnica analítica para determinar a resistência térmica de contato “material forjado - ferramenta” para o processo de forjamento, Tese de Doutorado em Engenharia, Escola de Engenharia, Universidade Federal do Rio Grande do Sul, 2009.
[16] BOOK A., Steigerung der Effizienz des Schmiedeprozesses durch moderne Messtechnik, Massivumformung, 2019.
[17] JAYAKUMAR T., MUKHOPADHYAYS C.K., VENUGOPAL S., MANNANBALDEVRAJ S.L., A review of the application of acoustic emission techniques for monitoring forming and grinding processes, Journal of Materials Processing Technology, 2005.
[18] RAJ B., JAYAKUMAR T., Acoustic emission during tensile deformation and fracture in austenitic alloys, in: Acoustic Emission: Current Practices and Future Directions, ASTM STP 1077, American Society for Testing and Materials, 1990.
[19] RAJ B., VENKATRAMAN B., MUKHOPADHYAY C.K., JAYAKUMAR T., LAKSHMINARAYANA A., SARATCHANDRAN N., KUMAR A., Intelligent welding using NDE sensors, in: Proceedings of the Seventh European Conference on NDT, 1998.
[20] MULLINS W.M., IRWIN R.D., MALAS J.C., VENUGOPAL S., Examination on the use of acoustic emission for monitoring metal forging process: a study using simulation technique, Scripta Mater, 1997.
[21] MUKHOPADHYAY C.K., VENUGOPAL S., JAYAKUMAR T., MANNAN S.L., RAJ B., CHATTERJEE B., SRINIVASAN R., GOPALAKRISHNAN V., MADHUSUDAN G., TRIPATHI R.S., Optimisation of the positioning of acoustic emission sensor for monitoring of hot forging process, Materials and Manufacturing Processes, 2005.
[22] SUHAIL S., HUSSAIN R., KHAN A., HONG C.S., Orchestrating product provenance story: When IOTA ecosystem meets the electronics supply chain space, Computers in Industry, vol. 123, p. 103334, 2020.
[23] SARACCO R., Digital twins: Bridging physical space and cyberspace, Computer, vol. 52, no. 12, pp. 58–64, 2019.
[24] JONES D., SNIDER C., NASSEHI A., YON J., HICKS B., Characterising the digital twin: A systematic literature review,” CIRP Journal of Manufacturing Science and Technology, vol. 29, pp. 36–52, 2020.
[25] GRIEVES M., VICKERS J., Digital Twin: Mitigating Unpredictable, Undesirable Emergent Behavior in Complex Systems. Springer, 2017.
[26] RIVERA L.F., JIMENEZ M., VILLEGAS N.M., TAMURA G., MULLER H.A., The Forging of Autonomic and Cooperating Digital Twins, IEEE Internet, 2021.
[27] RIVERA L.F., MULLER H.A., VILLEGAS N.M., TAMURA G., JIMENEZ M., “On the engineering of IOT-intensive digital twin software systems,” in Proceedings of the 42nd IEEE/ACM International Conference on Software Engineering Workshops (ICSEW). ACM, 2020.
[28] TAO F., CHENG J., QI Q., ZHANG M., ZHANG H., SUI F., Digital twindriven product design, manufacturing and service with big data, The International Journal of Advanced Manufacturing Technology, vol. 94, no. 9-12, pp. 3563–3576, 2018.
[29] PETERS R., Internet-Ökonomie, Springer Verlag, Heidelberg, 2010.
[30] WUEST T., WEIMER D., IRGENS C., THOBEN K.D., Machine learning in manufacturing. Advantages, challenges, and applications. In: Production & Manufacturing Research, 2016.
[31] PHAM D.T., AFIFY A.A., Machine-learning techniques and their applications in manufacturing. In: Journal of Engineering Manufacture. 219, 2005.
[32] WADI, I., BALENDRA R., Using neural networks to model the blanking process, J. Mater. Process. Technol., 1999.
[33] OSAKADA K., YANG G., Application of neural networks to an expert system in cold forging, Int. J. Mach. Tools Manuf., 1991.
Em meados do século passado, um cientista da Carborundum Company atendeu às exigências do mercado industrializado para um material isolante de baixa massa térmica. Charles T. McMullen inventou a fibra cerâmica, um isolamento de silicato de alumina com propriedades de isolamento térmico superiores, especialmente quando comparado à gama de materiais refratários convencionais usados na época para diversos setores industriais.
Esta descoberta inovadora permaneceu adormecida por mais de 10 anos. Na década de 1950, a fibra cerâmica tornou-se um substituto popular para o refratário duro devido à sua resistência ao choque, baixo armazenamento de calor, peso mais leve, facilidade de instalação e menor condutividade térmica. Vários tipos de produtos de fibra cerâmica foram desenvolvidos ao longo dos últimos 70 anos para atender às demandas de uma ampla gama de setores industriais e suas demandas de isolamento térmico de alta temperatura.
A gama de produtos de fibra cerâmica aumentou constantemente para incluir 70 ou mais formas de produtos diversos. As indústrias atendidas por esses produtos incluem cerâmica, vidro, petroquímica, geração de energia, siderurgia e alumínio.
Os efeitos mais amplos da pandemia global em 2020 reduziram a demanda por um grande número
de produtos industriais, equipamentos e serviços. A severidade econômica durante esse período afetou uma ampla variedade de empresas de manufatura e engenharia. Esse efeito foi sentido fortemente pelos produtores de metais ferrosos e não ferrosos, bem como pelas empresas envolvidas nos processos térmicos pósfabricação desses metais.
Os sinais de recuperação à medida que avançamos no tempo pós pandemia foram encorajadores. No entanto, qualquer otimismo foi atenuado pelo rápido e enorme
aumento do custo da energia, em particular do gás natural. À medida que a confiança retorna, o mesmo acontece com a demanda por esses bens específicos.
À medida que as empresas aumentam a produção de acordo com a demanda, haverá ainda mais requisitos para que operem da maneira mais eficiente possível, ao mesmo tempo em que diminuem os custos de produção sempre que possível. As empresas que aproveitarem a oportunidade para adotar uma postura diferente e proativa se posicionarão para serem enxutas e competitivas.
As empresas procurarão ter sucesso em mercados que se tornaram mais competitivos. Eles estarão buscando novas oportunidades de negócios com maior crescimento de mercado para garantir a segurança futura sem se chocar com as metas de emissão de carbono cada vez mais rígidas.
Os principais setores industriais têm se beneficiado da utilização de soluções de isolamento térmico para
altas temperaturas. No entanto, os produtores de metal aproveitaram os sistemas de revestimento leves e termicamente eficientes para fornos usados com sucesso na produção de aço por muitos anos. Isso também é verdade para uma variedade de setores de fabricação onde fornos e estufas são necessários para combinar eficiência térmica, produtividade máxima e baixa manutenção.
Processo de Fabricação de Fibra Cerâmica
É importante entender como a fibra cerâmica é produzida para avaliar como melhorias em sua fabricação podem melhorar diretamente seu desempenho térmico. O processo começa pesando em batelada os dois componentes principais, alumina e óxidos de sílica, em uma proporção pré-determinada. Para um produto com temperatura de classificação de 1260°C, a proporção é Al2O3 47-52% e SiO2 48-53%. Esta mistura de óxidos é transferida
para o forno de eletrodo submerso (SEF - Submerged Electrode Furnace). Os três eletrodos localizados dentro do SEF geram um arco elétrico e temperaturas em torno de 1800°C, que estão acima do ponto de fusão dos óxidos combinados com fibras cerâmicas.
Uma poça de fusão se forma na base central do forno cilíndrico e flui através de um orifício especialmente desenvolvido para formar o fluxo de fusão que cai devido à gravidade. A próxima etapa é a desfibração. Isso envolve direcionar um jato de ar comprimido para o fluxo de fusão (conhecido como método de sopragem de fibragem). Isso faz com que o único fluxo de fusão mude de direção e se quebre em várias fibras de pequeno diâmetro que são transferidas para a câmara coletora.
A fibra inicia como uma bola de fibra cerâmica derretida, que é transformada em um longo fio pelo processo de desfibração. Nesta fase, a fibra a granel (como é comumente conhecida) pode ser transferida ao longo
de um sistema de dutos e embalada. Outro método de desfibração é o processo de fiação. Isso envolve o fluxo de fusão atingindo uma série de rodas metálicas de alta velocidade. Isto tem o mesmo efeito. No entanto, as fibras produzidas normalmente têm um diâmetro médio maior e são mais compridas.
A fibra a granel pode ser processada posteriormente com o uso de um sistema transportador (e um vácuo) para assentar uma manta espessa de baixa densidade. Este tapete é comprimido para uma espessura uniforme e as fibras são entrelaçadas usando um sistema de agulhamento. Para a produção de mantas, uma pequena quantidade de lubrificante é adicionada para auxiliar o processo de agulhamento. A manta passa por um forno alimentado por esteira e qualquer lubrificante é queimado. O cobertor agora é inorgânico. Ele sai do forno e é cortado on-line na largura e comprimento corretos do rolo antes da embalagem. A maioria das
mantas produzidas hoje, como Durablanket® HP-S, utiliza o processo de fiação giratório.
Isolamento térmico de alta temperatura tem sido usado com sucesso por muitos anos em equipamentos de processamento térmico, principalmente fornos, estufas e aquecedores. O isolamento térmico atua para restringir o fluxo de energia da fonte de calor de alta temperatura, como o interior de um forno ou estufa, para o invólucro externo e dissipador de calor de baixa temperatura, como o ar ambiente onde o forno está localizado. Quanto maior for a restrição do fluxo de energia, mais fria será a superfície do invólucro e a subsequente perda de calor (energia) será reduzida. O isolamento térmico de alta temperatura deve fornecer uma barreira eficaz na restrição do fluxo de energia combinado com baixo encolhimento e durabilidade física em serviço.
A condutividade térmica é uma medida da capacidade de um material de transferir energia térmica através de sua massa. É medido em W/mK. Uma baixa condutividade térmica é necessária para que um material seja um bom isolante. É útil considerar os mecanismos de transferência de calor e o papel da condutividade térmica do isolamento de fibra cerâmica na redução das perdas de calor e do consumo de energia.
A transferência de calor tem três modos principais: condução, convecção e radiação.
A condução de calor ocorre quando átomos ou moléculas vibrantes colidem e interagem com partículas adjacentes.
A condução ocorre no espaço de ar entre as fibras, bem como através da fibra e das próprias partículas de granalha. Como o isolamento de fibra cerâmica é uma dispersão de fibras descontínuas, a transferência de calor por condução não pode ocorrer facilmente. A transferência de calor por condução é o principal mecanismo de transferência de calor em temperaturas abaixo de 538°C.
A transferência de calor por convecção precisa de um meio, como líquido ou gás, para transportar calor de superfícies quentes para superfícies frias. O tamanho do poro é pequeno em produtos de fibra cerâmica. Portanto, os bolsões de ar individuais são menores do que o normalmente necessário para que a transferência de calor por convecção seja aparente.
A radiação térmica é a radiação eletromagnética (uma forma de energia que viaja pelo espaço exibindo comportamento semelhante a uma onda) gerada pelo movimento térmico de partículas carregadas. Este é o principal modo de transferência de calor em altas temperaturas, normalmente acima de 538°C. A radiação tem um grande impacto em altas temperaturas porque é proporcional à quarta potência do diferencial de temperatura entre as superfícies envolvidas. O isolamento de fibra cerâmica faz um trabalho adequado de bloquear a transferência de calor por radiação porque a grande dispersão de fibras fornece um caminho traiçoeiro para a passagem das ondas de calor.
Efeito do Shot (Material não Fibrado) na Condutividade Térmica
Ambos os processos de desfibração são incapazes de converter totalmente todas as matérias-primas em fibras. Cada processo irá gerar uma certa quantidade de particulado que não completou o fibramento, ou Shot, como é conhecido. O número real de partículas de “shot” é pequeno em comparação com o número de fibras, mas a quantidade de shot e fibra são quase iguais em termos de massa.
Uma das propriedades físicas comumente publicadas para fibra cerâmica refratária é o índice de fibra. Esta é a proporção em peso da fibra expressa em porcentagem (Índice de Fibra % = 100 - teor de shot %). Um produto com alto índice de fibra tem muito pouco shot com base no peso. Como o shot reduz a quantidade de fibra cerâmica dentro de um determinado volume, ela diminui o desempenho térmico. A fibra tradicional fabricada por sopro ou fiação normalmente tem um índice de fibra de 45-55%.
O shot é um subproduto do processo de fabricação da fibra. Shot é o termo comum para o particulado que não completou o fibramento e que também é produzido. Shot não é um bloqueador eficiente de radiação térmica.
Shot são grãos globulares de fibra cerâmica que não foram convertidos em fibra durante o processo de fabricação. A fibra começa como uma bola de fibra cerâmica fundida e é estendida em um longo fio durante o processo de desfibração (normalmente fiação para manta). Essa bola derretida geralmente congela antes de ser completamente transformada em uma fibra.
Ao contrário da fibra, o shot não é um bloqueador eficiente da radiação térmica. Isso se deve à sua baixa área superficial específica quando comparada à fibra dentro da mesma matriz de fibra do produto.
A reinvenção de qualquer coisa é sempre extraordinária. Desde a década de 1960, os produtos de isolamento de silicato de alumina são conhecidos e confiáveis por seu desempenho, versatilidade e manuseio, formando a base de sistemas de revestimento energeticamente eficientes
para fornos de tratamento térmico onde aplicações de alta temperatura impõem demandas extraordinárias aos componentes isolantes. Com a redução do uso de combustível – combinada com a vida útil prolongada do revestimento do forno – os usuários finais se beneficiaram de custos operacionais e de produtos mais baixos, bem como melhor produção e melhor qualidade do metal. Usando os avanços na inovação de fabricação, a Unifrax lançou um novo produto, Durablanket LT e LT Z, em 2020. Ele representou um produto inovador de RCF (Refractory Ceramic Fiber - fibra cerâmica refratária) que oferece uma melhoria radical no desempenho térmico para temperaturas de até 1340°C versus manta convencional de alumina-silicato (Fig. 2).
Ter condutividade térmica 20% menor em comparação com o próximo melhor material de manta RCF disponível significa economia de energia tangível em todas as aplicações nas indústrias de metais ferrosos e não ferrosos e períodos de retorno em apenas alguns meses de serviço (Fig. 3).
Em vez de aproveitar apenas a economia de energia,
o desempenho de baixa condutividade térmica do Durablanket LT pode ser aproveitado por meio de uma redução no peso e/ou espessura da manta, criando mais espaço disponível em fornos e estufas. Por exemplo, com 96 kg/m3, Durablanket LT oferece o mesmo desempenho de isolamento que um produto de manta padrão de 128 kg/m3, o que pode resultar em economia de peso de até 25%.
Um dos principais desafios enfrentados pelos clientes é o aumento dos preços da energia em todo o mundo. Em setores de todos os tipos, os clientes procuram
reduzir o consumo de energia o máximo possível. Além disso, as demandas dessas mesmas indústrias para reduzir as emissões de acordo com os regulamentos locais e acordos internacionais tornam Durablanket LT e LT Z uma escolha natural quando se trata de aumentar a eficiência térmica, reduzir custos e honrar os compromissos de CSR (Corporate Social Responsibility - responsabilidade social corporativa) para alcançar sustentabilidade. Durablanket LT e LT Z podem reduzir os custos de energia em 15-20% em média (Fig. 4).
Durablanket LT tem um índice de fibra mais alto do que a manta RCF padrão. Ao contrário da fibra, o shot (parte do material que não completou o fibramento), um subproduto do processo de fabricação da fibra, não é um bloqueador eficiente da radiação térmica. As propriedades da fibra do Durablanket LT foram otimizadas para minimizar o conteúdo do shot e reduzir o tamanho do mesmo. O resultado é um desempenho térmico superior. Isso é aprimorado ao produzir uma manta com um toque mais macio e melhor manuseio (Fig. 5).
Aproximadamente 30% a mais de fibra por unidade de massa e menos partículas de shot grandes permitem que o shot pequeno restante seja “travado” da superfície, o que resulta em um mínimo de partículas livres na matriz da fibra. Simplificando, as mantas Fiberfrax Durablanket LT e LT Z proporcionam uma vida útil mais longa em ambientes de alta vibração e alta temperatura.
Esta nova tecnologia de produção também significa que Durablanket LT e LT Z oferecem melhor manuseio para uma instalação mais segura, rápida e fácil. Além disso, maior durabilidade e resistência à tração permitem que ele funcione por mais tempo, mesmo nos ambientes operacionais mais extremos.
Como resultado, é ideal para uma variedade de aplicações, incluindo:
• Fornos de reaquecimento de tarugos/placas
• Revestimentos de fornos de tratamento térmico
• Revestimentos e vedações de portas de fornos
• Isolamento da caldeira
• Isolamento de tubos e dutos
• Aquecedores de processo químico
• Vedações e juntas de alta temperatura
• Fornos de alta temperatura e revestimentos de fornos
O processo de fabricação proprietário oferece um produto de manta com mais fibras entrelaçadas e menos conteúdo de shot, tornando-o mais fácil de moldar e manusear. Sua alta resistência à tração – 11,6 PSI (80 kPa) – significa que o Durablanket LT é mais difícil de separar, tornando-o mais robusto durante a instalação e mais resistente ao estresse devido à expansão de carcaças e componentes sob calor extremo (Fig. 6).
Durablanket LT e LT Z estão disponíveis como um produto de manta agulhada ou como módulos de fibra cerâmica. Os produtos do módulo de fibra cerâmica são projetados para atender a uma ampla gama de requisitos de aplicação em uma variedade de fornos de processamento térmico, estufas e aquecedores. Esses módulos de isolamento combinam uma instalação rápida com uma solução de revestimento termicamente eficiente. É fácil trabalhar com qualquer formato. Há pouca poeira gerada durante a instalação e há menos probabilidade de irritação da pele devido à sua superfície mais lisa e macia (Fig. 7).
Usados com sucesso por décadas, os produtos de fibra cerâmica têm sido utilizados em aplicações para metais ferrosos e não ferrosos, geração de energia e indústrias cerâmicas em todo o mundo. Agora Durablanket LT e LT Z oferecem desempenho térmico ainda melhor e uma vida útil ainda mais longa.
PARA MAIS INFORMAÇÕES: Allan Davies é gerente de produto da Unifrax / UK. Ele pode ser contatado em allan.davies@unifrax.com. Para obter mais informações sobre Unifrax, visite www.unifrax.com. Todos os gráficos fornecidos pela Unifrax
Os fornos industriais são amplamente utilizados para fundir metais para fundição ou aquecer materiais para mudança de forma (forjamento) ou mudança de propriedades (tratamento térmico).
Basicamente, os fornos industriais podem ser de dois tipos com base no método de aquecimento: combustão (usando combustíveis) e elétrico. Os fornos de combustão são usados para aplicações como aço, cerâmica, vidro e muito mais. Funcionam em função do tipo de combustão: a óleo, a carvão ou a gás.
O processo de combustão realiza a ignição com a ajuda de ar (21% de oxigênio) e combustíveis. Idealmente, o ar e o combustível devem ser bem misturados para uma combustão adequada. Existe uma relação ar-combustível definida (conhecida como relação estequiométrica) levada em consideração pelo projetista do forno industrial. Pode variar dependendo da aplicação e do padrão de carga.
Muitos operadores de fornos, no entanto, são incapazes de monitorar o processo. Eles estão perdendo quantidades significativas de energia devido ao excesso de ar que entra no forno, o que resulta em perda de calor pelos gases de combustão. O excesso de ar resulta em oxigênio que não é consumido durante a combustão, e esse oxigênio absorve o calor utilizável e o transporta para fora da chaminé.
A quantidade quimicamente ideal de ar que entra em um forno é apenas o suficiente para que todo o oxigênio do ar seja consumido. No entanto, esta mistura ideal é difícil de alcançar porque o combustível e o ar não se misturam completamente. Portanto,
uma certa quantidade de excesso de ar sempre será necessária para a combustão completa. Na verdade, muito pouco ar em excesso resulta em queima ineficiente de combustível, acúmulo de fuligem e emissões desnecessárias de gases de efeito estufa.
O nível ideal de excesso de ar varia de acordo com o forno e suas aplicações. Geralmente, um excesso de ar de 10-15% é recomendado para manter a temperatura de entrada atual ou o nível de saída de produção, o que for desejado.
Nos processos de combustão, a relação ar/combustível é normalmente expressa em massa. Obtemos o máximo de calor útil se fornecermos ar à zona de combustão a uma taxa de fluxo de massa (por exemplo, libra/minuto, kg/ hora) que corresponda adequadamente à taxa de fluxo de massa de combustível para o queimador.
Considere a equação 1 para a química da combustão do combustível.
O ar é composto principalmente de oxigênio (21%) e nitrogênio (79%). O oxigênio no ar se combina com o carbono no combustível a uma temperatura elevada na câmara de combustão. Ao queimar hidrocarbonetos, a natureza prefere fortemente as ligações duplas de carbono-oxigênio do dióxido de carbono e produzirá energia térmica significativa em uma reação exotérmica para atingir essa forma de CO2.
Assim, o dióxido de carbono é o gás de efeito estufa comum produzido a partir da combustão completa de combustível de hidrocarbonetos. O vapor de água (H2O) também é um produto normal da combustão de hidrocarbonetos.
CO2 = dióxido de carbono
CO = monóxido de carbono
H 2 O = água
Ar = 21% de oxigênio (O2) e 79% de nitrogênio (N2)
Combustível = hidrocarboneto, como gás natural ou óleo combustível líquido.
Se a relação ar/combustível for menor, não há oxigênio suficiente disponível. Isso levará a uma combustão incompleta com maior quantidade de combustível/ carbono não queimado, o que significa desperdício
ÁREA DE MÁXIMA EFICIÊNCIA DE COMBUSTÃO
MAGRA (EXCESSO DE AR)
PONTO ESTEQUIOMÉTRICO
direto de combustível. À medida que a disponibilidade de oxigênio diminui, gases de exaustão, incluindo monóxido de carbono, se formarão. À medida que a relação ar/combustível diminui ainda mais, o combustível parcialmente queimado e não queimado começa a ser emitido pela chaminé de exaustão como fumaça e fuligem, o que cria poluição do ar.
Mais Ar Perde Combustível e Energia Térmica
Se a relação ar/combustível for maior, muito ar é alimentado na câmara de combustão. Isso completará a combustão e o excesso de ar presente, contendo nitrogênio
e oxigênio indesejado, absorve a energia térmica. Isso faz com que a temperatura operacional na câmara caia, e o substrato de aquecimento é incapaz de extrair energia térmica. Além disso, o excesso de ar quente gerado escapará da chaminé, resultando em perdas de energia térmica.
Ar Teórico (Estequiométrico)
A relação ar-combustível teórica é definida como a quantidade mínima de ar e combustível necessária para converter combustível de hidrocarboneto em dióxido de carbono e vapor de água. Mesmo mantendo um ar teórico na combustão real devido ao menor tempo de
SENSOR DE O2
contato na câmara de combustão, a mistura ar-combustível é inadequada, o que acaba resultando em combustão incompleta; daí a perda de energia e aumento dos níveis de poluição. Com a ajuda do monitoramento on-line de ar e combustível, no entanto, podemos obter uma relação que funcione com a menor perda de calor.
CORRETA DE AR/COMBUSTÍVEL EM UM FORNO
Os principais benefícios do controle da relação ar/ combustível são:
• Melhora a combustão e otimiza a eficiência térmica
• Economiza custos ao reduzir o consumo de combustível
• Melhora a qualidade do produto por um perfil de temperatura uniforme
• Ajuda a aumentar a produtividade
• Reduz poluentes/emissões
Para obter essas vantagens, a medição do fluxo de ar e combustível é de vital importância. O controle da relação ar-combustível desempenha um papel fundamental na operação eficiente e segura dos fornos a lenha. Isso ocorre porque a relação ar-combustível na zona de combustão desses processos afeta diretamente a eficiência da combustão de combustível e as emissões ambientais. A quantidade de ar em excesso dentro do sistema pode ser determinada analisando a quantidade de oxigênio no
gás de combustão. Quando a relação ar/combustível é otimizada, a economia de energia resultante geralmente varia de 5% a 25%.
Fatores importantes ao selecionar o melhor sensor de fluxo para aplicações em fornos incluem:
• Sensor inteligente com design robusto
• Versátil em uso para todas as aplicações de forno a gás
• Queda de pressão mínima
• Maior sensibilidade e resolução
• Maior precisão e repetibilidade
• Sem manutenção
• Limpeza fácil, se necessário.
A medição de vazão convencional usa um medidor de vazão de orifício ou um medidor de vazão de turbina, que tem limitações como menor precisão, menor taxa de abertura e alta queda de pressão. Considerando as limitações das antigas técnicas de fluxo em aplicações de fornos, uma nova técnica calorimétrica (dispersão térmica) está ganhando terreno para a medição de fluxo de fornos industriais. Possui uma medição simples de temperatura diferencial baseada no princípio de anemometria de temperatura constante. Ele evoluiu nos últimos 20 anos e se tornou altamente sensível, ajustável e versátil para uso com ar e gás combustível.
Além da medição de fluxo, outros parâmetros aconselháveis para medir incluem:
• Temperatura dos gases de exaustão na saída do forno
• Porcentagem de oxigênio nos gases de combustão
• Monóxido de carbono
Para atingir a eficiência térmica ou de combustão ideal, o controle da relação ar-combustível é de vital importância. Por esse motivo, o excesso de ar (O2%) nos gases de exaustão do forno (gases de combustão) deve fazer parte da lógica de controle necessária.
PARA MAIS INFORMAÇÕES: Manish Patel é diretor da Leomi Instruments Pvt. Ltd. Ele pode ser contatado em leomi.instruments@gmail.com.