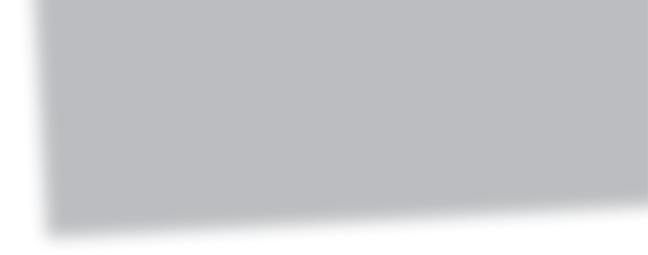
10 minute read
Engineering Matters
Including: Duplicate inspections, painting versus powder coating, AERO show musings, Kitfox fuel tanks and LAA generic maintenance schedules …
Welcome to Engineering Matters – the section of Light Aviation that is dedicated to discussing all manner of topics concerning both technical and operational aspects of the LAA fleet. If you have anything to say that you think would benefit others, then please email words and pictures to LAA Engineering at engineering@laa.uk.com
Duplicate inspections are independent inspections
Everyone involved with aircraft maintenance, be they owners or inspectors or engineers, should already be aware of the term ‘duplicate inspection’. Previously, the subject has been covered in the December 2019 edition of Light Aviation
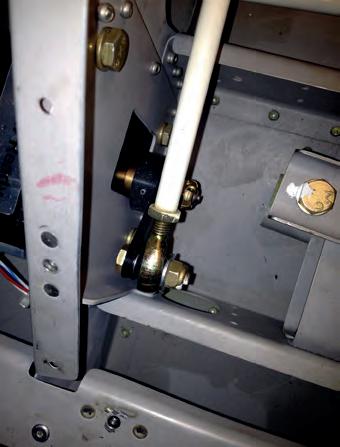
The CAA define duplicate inspections and their associated requirements as:
‘A duplicate inspection shall be carried out after any flight safety sensitive maintenance task. Maintenance tasks that involve the assembly or any disturbance of a control system that, if errors occurred, could result in a failure, malfunction, or defect endangering the safe operation of the aircraft should be considered as flight safety sensitive maintenance tasks needing a duplicate inspection.
A control system is an aircraft system by which the flight path, attitude, or propulsive force of the aircraft is changed, including the flight, engine and propeller controls, the related system controls and the associated operating mechanisms.
Duplicate inspections should be carried out by at least two persons, to ensure correct assembly, locking and sense of operation. A technical record of the inspections should contain the signatures of both persons (involved in carrying out the duplicate inspection) before the relevant Permit Maintenance Release (PMR) is issued.’
In the RAF, this form of inspection is called an ‘independent inspection’. EASA couldn’t really make up its mind whether to call it a duplicate or independent inspection and often referred to it as a
‘duplicate / independent inspection’ just to cover all bases. These days even the CAA acknowledge this variation in terms and say that the Duplicate Inspection may be referred to as an Independent Inspection.
Perhaps, ‘independent’ is indeed a better name for this inspection task, given it is a specific check that is carried out in addition to the job itself.
One might wonder as to why the name of the inspection is relevant and it comes down to understanding the purpose of the inspection and the way that it is carried out and recorded.
Owners and maintainers should remember that the duplicate / independent inspection is an entirely separate inspection to the maintenance task in question. It may well be that one or more persons involved in completing the maintenance task are also involved in carrying out the duplicate inspection but it should be treated as an independent exercise.
There are various LAA Technical Leaflets describing the procedure for duplicate inspections (as well as in the notes on the LAA Aircraft Duplicate Inspection Record) and it is imperative that the correct format is followed regarding the first and second inspections, who is authorised to sign what, and with what authorisation. For instance, if a pilot (who is also a current member of the LAA) carried out the second inspection, their pilot’s licence number is the authorisation and must be recorded against the signature and date.
Duplicate inspections are, ideally, recorded on the specific Aircraft Duplicate Inspection Record but may also be recorded (in the correct format) on a worksheet or in a log book entry.
In the litigious world that we live in, insurance companies and lawyers really do check aircraft maintenance records to ensure everything is dotted and crossed in accordance with the procedures. So, if LAA Engineering ask for an amendment to duplicate inspections to bring the record into line with LAA procedures, this is not being pedantic but potentially providing a level of protection to owners and inspectors.
Powder coating or painting
Many manufacturers and aircraft builders choose to powder coat metal components such as undercarriage legs and engine mounts because of the coating’s hard-wearing properties.

There is no disputing that this is a plus point of powder coating, but proceed with caution. Because of the thickness of the coating and its ‘flexibility’, it can hide defects (cracks) and corrosion issues in the metal component it is protecting. It is actually a much better practice to use ordinary paint on aircraft components and contrary to the industry norm, use a light colour. Cracks tend to be black so do not show up well on items that are painted black.
Recently cracks were found in the upper section of a Pioneer 300 nose undercarriage leg during routine undercarriage functional (retraction) tests. This is not known to be a common problem with the Pioneer and may be a one-off occurrence.
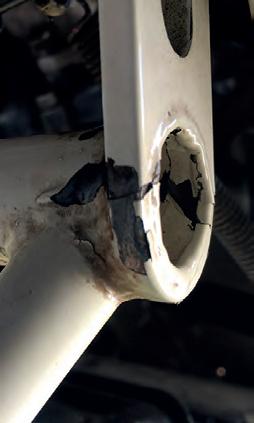
Incidentally, the importance and value of undercarriage retraction tests should not be underestimated. While it can be a bit of a pain to carry out, as it requires the safe jacking of the aircraft, it is really the only way to ascertain that the system is functioning correctly and to be able to test any emergency extension systems.
Retractable undercarriages are inherently more complicated than fixed gear, simply by the fact they have more moving parts, which can make them heavier and less accepting of abuse, such as heavy landings and operations from rough strips. Lubrication and correct adjustment are paramount in maintaining retractable undercarriage in an airworthy condition.
Ben and Jerry’s AERO 2022 trip
With the advent into the UK of factory built sub-600kg microlights, Ben Syson and Jerry Parr were sent on their travels to represent the LAA at the AERO 2022 show at Friedrichshafen, Germany.
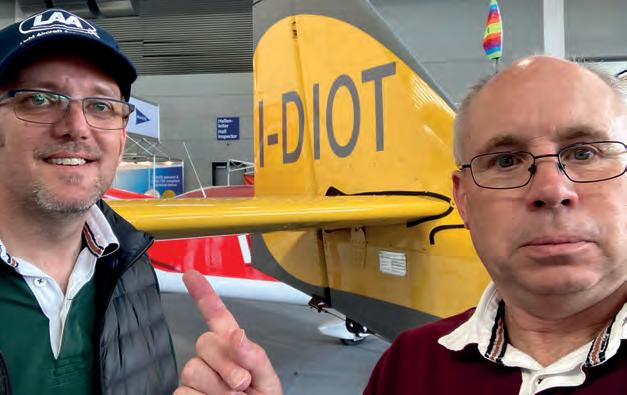
The primary mission was to visit all the manufacturers which are interested in importing factory built sub-600kg microlights into the UK, and that were exhibiting at AERO.
Due to the availability of flights, we planned on being there for just one day and found that there was sufficient time to get around all of the exhibition halls and promote the LAA’s services to the various manufacturers. There will now be follow up communication with the various manufacturers, offering LAA Engineering support (and eventually, oversight and administration of their products) as and when required.
In addition to the 600kg manufacturers, we also spoke to various propeller and engine manufacturers and other exhibitors. Everyone
Open worksheet entry
When carrying out maintenance tasks on an aircraft, worksheets should be raised listing the individual maintenance tasks to be carried out. These are called ‘open’ entries, as the ‘work required’ is called up but the work has yet to be carried out.
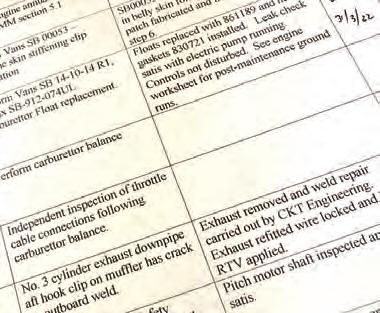
Once the task has been completed, this should also be recorded and signed for as required by the maintainer and inspector (if outside what is allowed under the terms of ‘pilot authorised maintenance’ – see LAA Technical Leaflet TL 2.05).
If a maintenance task is started but not completed, then an open entry should be made, so it is obvious that that task has not been completed. This is very important when maintenance is not going to be, for example, completed in one day, and so acts as an aide-mémoire. It’s easy to be distracted from the job in hand, and a task left incomplete. An example would be the disconnection of a flying control pushrod to allow for an adjustment to be made. The worksheet may call up ‘elevator range of movement to be adjusted’ in the ‘work to be required’ column.
Once the pushrod has been disconnected, an open entry should then be made in the ‘work required’ column specifically stating exactly what needs to be carried out to complete the task, i.e. ‘elevator pushrod to be reconnected at elevator bellcrank’ Ideally, there would also then be an open entry made on the worksheet for: ‘duplicate inspection to be carried out on elevator pushrod at the bellcrank’.
Open entries may be made for any required maintenance task, not just those involving flying control or engine control connections.
seemed very upbeat about life in general in General Aviation. It was certainly good to see various UK dealers and importers at the show, many of them working on the stands of products they represent.
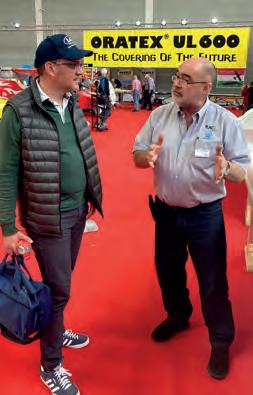
Kiev propeller hub crack
Propellers operate under immense loading and stress when operating and so it should not be a surprise that issues and defects occur. Many of these have been reported in previous Engineering Matters articles, and concern propellers from just about every manufacturer and involve certified and non-certified propellers.
Recently, a problem was highlighted on a BMAA-administered EV-97 Eurostar with a Kiev propeller where the hub has cracked. The propeller type is also found on a number of LAA-administered aircraft. At the current time, it isn’t known what caused this failure but it is imperative to thoroughly inspect propeller assemblies during routine maintenance (including removing the spinner), or at any time there is a strange vibration or other anomaly found with the propeller.
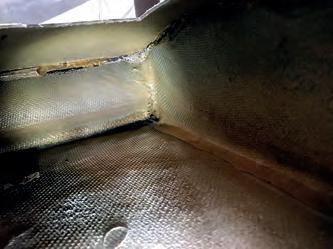
Problems may be caused by propeller strikes (even when the propeller is stationary), incorrect torquing of propeller hub bolts, blade pitch out of alignment on ground adjustable propellers and lack of lubrication on variable pitch propellers.

Propeller spinners and spinner attachment plates are also operating under high loads, so include them in the maintenance checks.
Andair gascolator filter element
The builder of a Europa recently highlighted an issue he found with an Andair gascolator fuel filter he had received. Initially, it was thought to be a scratch on one of the filter elements but on closer inspection, it was found to be a cut or split right through the filter element.



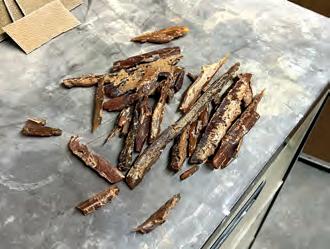
Andair replaced the filter immediately and this is most likely to be an isolated case, but it is still worth checking next time you have the gascolator bowl off.
LAA Inspector Dave Bland has previously reported issues with Kitfox fuel tanks and has now sent an update on his investigations into what he has found with one pair of tanks after cutting access holes. This particular tank rattled when moved about as something was loose inside. It goes without saying that having loose articles inside a fuel tank is not a good idea as they will normally manage to make their way to the fuel tank outlet and cause a blockage.
Dave reports, “The construction method seems to be that the baffle rib was bonded to the lower main moulding and then the top surface was bonded on. Obviously, the excess resin from the bonding joint area could be cleaned off externally but remained on the inside. I suspect that the excess resin at the joints did not like fuel vapour and this may possibly be exacerbated if the tank has contained mogas. The sloshing compound looked pretty nonexistent and what was there, appeared to be peeling and flaking. The excess resin broke away easily and some of it was found loose in the tank – hence the rattling noise.”
Dave is currently working on a repair scheme for the fuel tanks.
LAA generic maintenance schedules
The LAA-issued Generic Maintenance Schedules have been revised and are available for download (in MS Word format) from the LAA website in the ‘Aircraft Maintenance’ part of the LAA Engineering ‘Operating and Maintaining’ section.
The Generic Maintenance Schedules include a Check A, 50 hour / six month inspection, 150 hour / 12 month inspection and 500 hour / 36 month inspection.
Vacuum pump failures
Following the piece in last month’s Engineering Matters concerning a failed vacuum pump drive shaft that happened to be installed on the engine of a Bulldog, Mark Miller (Chief Engineer of de Havilland Support Ltd) has kindly highlighted the existence of DHSL Service Bulletin BDG/100/180.
This Bulldog-specific Service Bulletin is titled Vacuum System Components – Approval of Replacement Parts and Their Recommended Maintenance and Lifting Requirements
LAA Engineering housekeeping
Permit to Fly Revalidation paperwork: Fairly frequently, we receive emails with a scanned copy of the Permit to Fly revalidation documentation attached. The current procedures require LAA Engineering to only accept the original ‘hard’ copies of the revalidation application. Due to the number of Permit to Fly revalidations received, the applications that are emailed to LAA Engineering will not be reviewed until the hard copy is received.
Check your ‘junk’ folders: It would appear that some LAA emails end up in people’s Junk folders. Please check your Junk folder if you are expecting an email from LAA Engineering, including the Permit to Fly Certificate of Validity.
LAA Engineering charges
LAA Project Registration
Kit Built Aircraft £300
Plans Built Aircraft £50
Initial Permit issue
Up to 450kg £450
451-999kg £550
1,000kg and above £650
Permit Revalidation
(can now be paid online via LAA Shop)
Up to 450kg £170
451-999kg £220
1,000kg and above £260
Factory-built gyroplanes* (all weights) £275
*Gyros note: if the last Renewal wasn’t administered by the LAA, an extra fee of £125 applies
Modification application
Prototype modification minimum £60
Repeat modification minimum £30
All of the LAA Generic Maintenance Schedules are intended to be amended by the owner as required, to suit the maintenance requirements of that specific aircraft.
It is highly recommended that owners and maintainers of LAA-administered aircraft use a bespoke maintenance schedule for their aircraft to accurately track and record all scheduled maintenance tasks.
Cessna 120/140 seat belt bracket
As anticipated, the problem with Cessna 120 / 140 seat belt attachment brackets (as discussed in the April 2022 Engineering Matters) is now an FAA Airworthiness Directive. The FAA has issued FAA AD 2022-08-03. Reference to this FAA AD will be added to the TADS for the Cessna 120 in due course and compliance with the AD is mandatory for LAA-administered examples.
Postage: Please ensure the correct postage is paid for when sending documents to LAA Engineering. Items with incorrect postage often get delayed by one to two weeks in the Royal Mail system. It is advisable to keep copies of documents sent to LAA Engineering, just in case the items do get lost en route.
Change of ownership: When an aircraft is bought or sold, please inform LAA Engineering, preferably using the form in LAA Technical Leaflet 2.18. This includes when a group member sells their share or buys into a group-owned aircraft. The CAA does not always inform the LAA when there are changes to aircraft ownership details. ■
LAA Fleet Summary
New Projects Registered in 2022: 18
Transfer
(from C of A to Permit or CAA Permit to LAA Permit)
Up to 450kg £150
451 to 999kg £250
1,000kg and above £350
Four-seat aircraft
Manufacturer’s/agent’s type acceptance fee £2,000
Project registration royalty £50
Category change
Group A to microlight £150
Microlight to Group A £150
Change of G-Registration fee
Issue of Permit documents following G-Reg change £55
Replacement Documents
Lost, stolen etc (fee is per document)£20
PLEASE NOTE: When you’re submitting documents using an A4-sized envelope, a first-class stamp is insufficient postage.
Permit to Fly First Issues in 2022: 16
Permit to Fly Revalidations - 2022: 594
Recent Alerts & AILs (check the LAA website for further details)
Zivko Aeronautics Inc. Edge 360, Edge 540 and
Laser Z200: Aileron Centre Hinge Attachment
CAA MPD: 2022-001
LAA Alert: A-001-2022
MT-03, MTOsport, MTOsport 2017, Calidus and Cavalon: Rotor Blade Inspection/Replacement/
Life-Limitation
CAA MPD: 2002-002
LAA Alert: A-002-2022
TLAC Escapade and Sherwood Scout: Seat locking and Secondary Seat Restraint
CAA MPD: 2022-004-E
LAA TSB: TSB-001-2022
Europa: Door Latch System Stop
CAA MPD: 2022-003
LAA AIL: MOD/247/012
LAA Alert: LAA/AWA/21/08
Adjustable Seats in General Aviation Aircraft
CAA Safety Notice SN-2022/001: Security and locking of adjustable seats