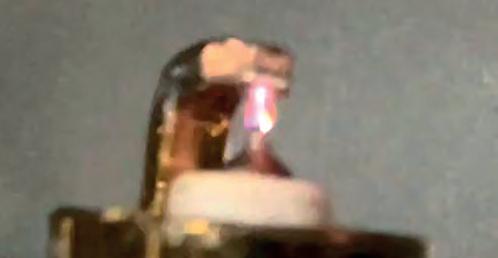
11 minute read
Electronic Ignition
Is electronic ignition
Advertisements and anecdotal accounts are tantalising builders with wondrous gains to be had by replacing that dinosaur of aviation, the magneto. What is aircraft electronic ignition about and what is its potential?
While some Rotax and VW based engines already enjoy dual electronic ignition as standard and aftermarket solutions are beginning to appear, most of our engines including the majority of Lycoming and Continental are still ignited by old style magnetos. Electronic ignition is a common subject on several of the aviation forums these days with debate revolving around the benefits it might afford. Typically, aftermarket electronic ignitions cost upwards of £1,500 per bank of plugs and some, but not all, are quite simple to install.
A new traditional magneto is more expensive, a refurbished one less. This leads to temptation to replace ageing magnetos with modern technology with the additional hope of some performance benefits.
The perceived bête noir of classic magnetos is starting the engine. To be self-contained they generate their own electricity, whose strength is a function of engine speed (rpm). At low rpm they don’t generate much, so the resultant spark is not strong and sometimes fails to overcome all of the many challenges that starting can present. Once running, the spark is normally adequate although, in the quest for simplicity, their fixed timing is sometimes less than optimum.
While simple, they do depend on old electrical technology which is stuck in the dark ages and can be short-lived and unreliable.
Electronic ignition differs in several ways from a traditional (points and coil) magneto ignition. It has far fewer moving parts and its electronics offer a consistent stronger spark (Picture 1) using the battery as its electricity source.
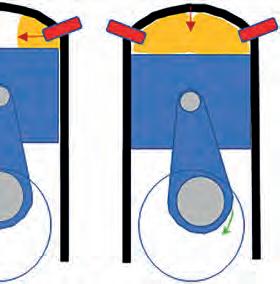

It is not just an electronic implementation of the old magneto, it is a fundamental change to the way your engine operates. The key difference is, it adds automatically varied ignition timing.
Left, no spark. Middle, coil and points generated spark. Right, a capacitive discharge (electronic) spark.
Why is ignition timing important?
A magneto on most aircraft engines has only one timing setting, fixed somewhere between 20-25° before the crank’s top dead centre position (TDC). Other than for starting, this doesn’t vary. It is a long-established compromise between performance (which requires more complexity) and reliability (where simple is best). It works because, unlike cars, once flying, the engine speed remains in a relatively narrow and efficient band, even more so with a constant speed prop. Once you move outside that band, it is less efficient.
When an engine is running normally, two synchronised sparks initiate burning of the compressed fuel air mixture. (Picture 2) The resultant fire progressively fills the cylinder with hot gas. This results in pressure of up to 2,000 psi, ideally peaking at a sweet spot 16° after top dead centre (ATDC). This sweet spot provides maximum torque and hence economy and efficiency. The high pressure pushes the piston down to turn the crank.
Simple, but best power, economy and engine life depend on the engine being operated around that torque sweet spot under all conditions. Variable timing sets out to broaden the efficient operational envelope by adjusting the spark timing to reflect the differing rpm of the engine and speeds the fuel / air mixture burns in the cylinder. As an illustration, at sea level and set to 2,400 rpm (a typical Lycoming cruise setting) the crank rotates 40 times a second or once every 25 milliseconds (ms). Once ignited, the fuel flame front expands at about one inch per ms, so for a Lycoming’s five-inch diameter piston (Picture 3) the flame has to travel 2.5in from each spark plug to complete the burn and build up maximum pressure. To match this to the torque sweet spot, the burn should start 2.5ms before the engine reaches that point. At 2,400 rpm in 2.5ms the crank will have turned 36°, so for optimum timing the ignition should fire 20° (36 minus 16) before TDC.
In normal operation the Lycoming’s rpm can vary between 1,800 and 2,700 and the speed of the flame front in the fuel / air mixture between 0.5in a second to 1.5in per millisecond. The flame front speed is very sensitive to the fuel / air mixture and density (and to a lesser extent several other parameters). The lower the density, the slower the flame front. Reducing the throttle limits the amount of mixture that can get into the cylinder lowering the density, slowing the flame and vice versa.
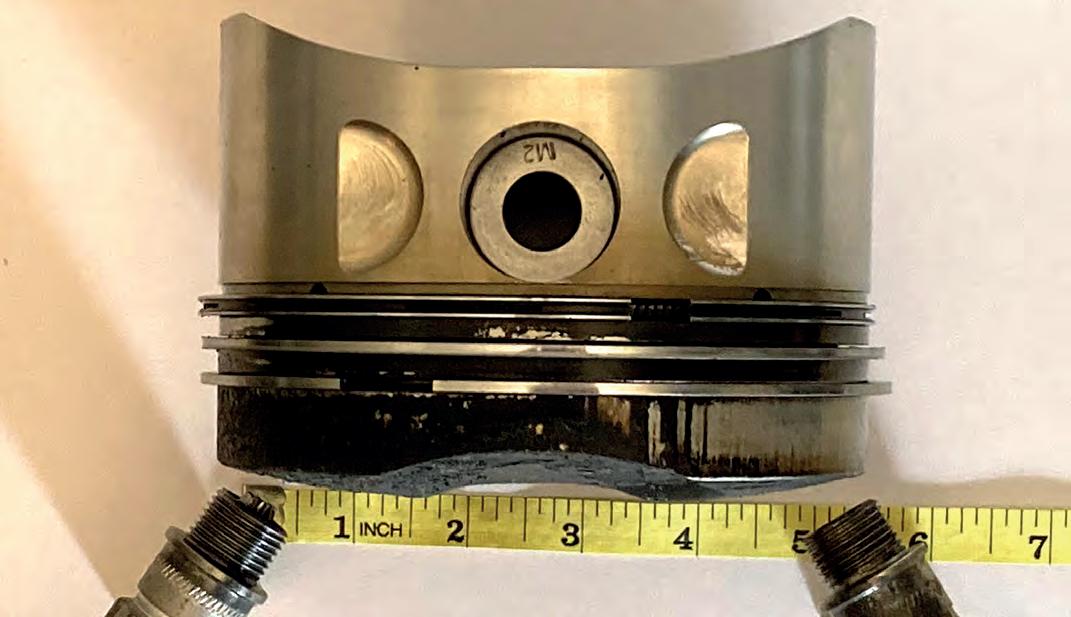
Flying higher also reduces the air density available to the engine and reduces the fuel / air mix density. While the sweet spot remains unchanged at 16°, the required spark timing to achieve it can vary by as much as 40°.
Cars of the 1950s-1960s introduced mechanical devices (centrifugal and vacuum ‘advance’ mechanisms) to adjust ignition timing to compensate for these variables. Because of the fairly narrow range of operation for an aircraft engine and the low price of fuel in the USA, the benefits of variable timing over the fixed system did not justify the complexity and the car technology was not taken up. In the late 1960s, electronic ignition was developed by Delco (Chrysler) and by the 1980s sophisticated versions were commonplace in most cars contributing to the increased efficiency required by evolving emissions legislation.

But by that time the aviation product liability die was set, paranoia took over and this technology never transferred over to the aviation dinosaurs. Even today the big guns in piston aviation engines are only just beginning to look at variable ignition timing.
In literature on the subject, it is suggested that in some circumstances even well set up and operated classic aircraft engines with fixed timing, may be performing at only 80% of their potential efficiency.
By making the timing controllable through electronic ignition systems, some of that efficiency loss may be recovered. But you can’t just bolt on a 20% improvement. What you can gain depends on how you operate your aircraft.

Electronic ignition
Creating the spark. Capacitive discharge ignition (Picture 4) creates a bigger spark by firstly generating a bigger voltage (250v or more) within the ignition (from the battery which has a lot more power available than a mag’s generator) which it stores in a capacitor. When needed, it is discharged through a coil to the plugs to create a spark. This spark voltage is normally greater than 20,000v regardless of rpm (a mag produces 6,000-10,000v) and has no problem igniting fuel in most conditions.
A magneto routes the spark voltage pulse through a moving arm that ‘distributes’ it to the appropriate plug lead. Most electronic ignition systems eliminate the ‘distributor’ by the ‘wasted spark’ system. Instead of the distributor, each spark plug has an individual coil (Picture 5). They are fired as two pairs, one pair around TDC and the other 180° later. No need to worry where the engine is in the four-stroke cycle, just crank position will do. One plug will fire as the piston approaches the top of the compression stroke creating the bang and the other at the top of the exhaust stroke where there is nothing to ignite, the so-called ‘wasted spark’. One revolution later they swap. Although it does nothing for performance it is much cheaper to make and eliminates another less reliable moving part.
Timing the spark. Typically, a magnet and sensor are placed on the crank (Picture 6), flywheel or old mag housing for position and rpm calculation.
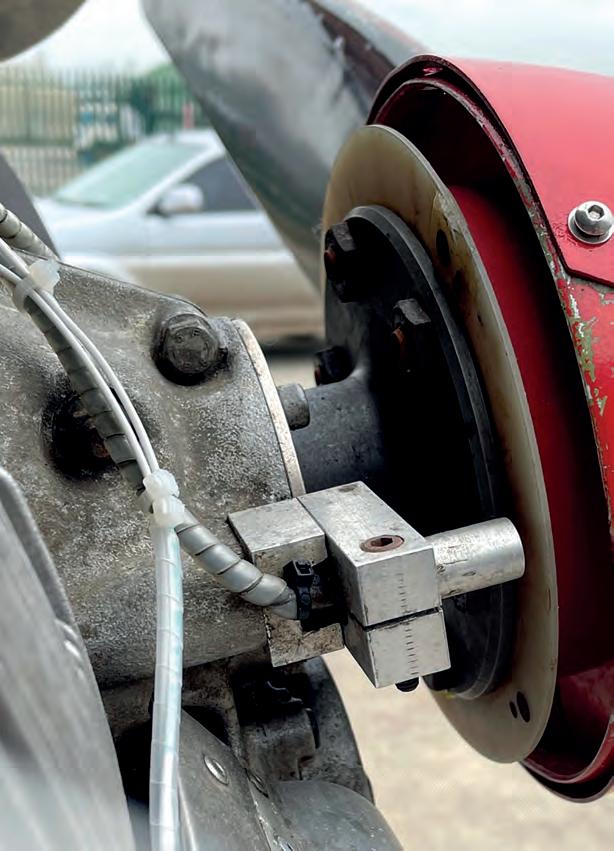
Manifold pressure (MaP) used by some ignitions relates to fuel / air density and is measured via a digital pressure sensor connected to a small port on one inlet manifold.
This data all goes to an ignition controller which uses a digital ‘map’ of timing settings to determine the optimum point to set off the spark (similar in function to that in a modern car engine ‘chip’). Thus, for a chosen fuel type, the best spark timing can be determined for any rpm, throttle setting or altitude (but note, not mixture!).
Electronic ignition drawbacks
It is important to be aware that although electronic ignition eliminates a lot of the mechanical and electrical weaknesses of the mag system, it comes with its own baggage. The bigger spark normally needs a different spark plug (temperature range). The wrong plug will negate many of the benefits sought and may even damage the engine.
Electronics are also a lot more sensitive to heat than a magneto. Effective cooling or a cool location (Picture 4) is absolutely essential to achieve the promised reliability improvements of an electronic ignition.
A note of caution. There is a limit to spark timing variation beyond which it is counterproductive and even risks damaging the engine. Too early (advanced) a spark, as well as being very inefficient (working against crank rotation), can cause a phenomenon called detonation. This can seriously damage your pistons and valves.
On a silenced car engine this can sometimes be heard as a knocking or pinging sound (called pinking). In most aircraft this will go undetected mainly due to the competing noises and noise reducing headsets. As well as being affected by mixture density the optimum timing advance required for an aircraft engine is impacted by fuel type and mixture. Lower octane fuels and weaker mixtures counter-intuitively burn faster. An engine ignition optimised (mapped) for 100LL will in some circumstances be firing up to 40° BTDC, which could be much too far advanced for unleaded fuels (mogas or UL91), risking detonation. Similarly, a leaned mixture is more prone to detonation and, in combination with variable ignition timing advance, a potential risk.
An approval for your engine to use unleaded fuel may not be valid with electronic ignition. In some of those 1960s cars, when faced with unleaded fuels, ‘vacuum advance’ devices often had to be disconnected to avoid over-advance to protect the engine from detonation. Modern car electronic ignitions have a detonation (knock) sensor which can detect the detonation effects of lower octane fuel and are able self-adjust to compensate. There are technical reasons why electronic identification of ‘knock’ is challenging in some aircraft engines. To date, no aviation aftermarket ignitions have this feature. To be safe, ensure that your automatic timing is correct for your leaning policy and all fuels it will face now and, in the future (100LL will die sooner rather than later).

Left Electronic ignition monitor and in-flight programmer. This one, the EI Commander fits a 2-1/4in hole and is aimed at the popular E-MAG range of ignitions. It is indicating an ignition advance of 32.2 BTDC being applied but a deviation of 5.8° between the two ignitions. They are supposed to be the same, so that’s an engine problem that needs addressing. Useful device.
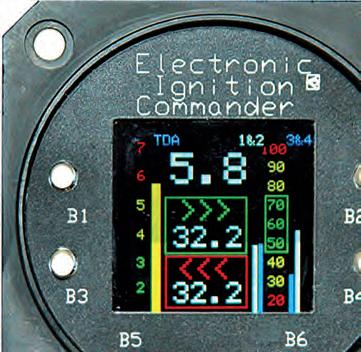
Below The popular E MAG. It packages all its bits into a casing that replaces the departing mag. It also includes a built-in generator to address the LAA’s fail-safe concerns and is easy to install.
Installation. Aftermarket electronic ignitions all have slightly different subset of the various features of electronic ignition and typically come in one of two physical packages. One is built into a mag-like body which just bolts in place (Picture 8) of the old one requiring just a few minor electrical changes. The other, a modular system (Pictures 4,5 & 6) comprises a box of electronics, separate coils and a crank position sensor which can be installed around or outside the engine compartment as appropriate, requiring a little more wire and mechanical work. Functionally they do much the same task although any performance benefits are down to the suitability of their built in ‘timing map’. Some products offer computer access to the timing map to customise the timing variation, even in the air! (Picture 7) LAA requirements for installation of electronic ignition. There is very little mention of electronic ignition in the LAA’s technical data library save for TL 3.15 (applicable to modifying Lycoming engines). Any modification to an engine including addition of electronic ignition generally renders it non-standard. Unless Electronic Ignition is listed as a ‘standard option’ in the TADS for that engine type, such a change must be the subject of a formal modification proposal, initially through form MOD 2 (or, if identically repeating an existing mod on the same airframe, engine and prop, a repeat mod application can be made using MOD11 – TL 3.01 and 3.07 refer). Using TL 3.15 as indicative of the LAA’s general position raises two points, metal props and fail-safe. The former reflects the view of some of the principal propeller manufacturers on potentially destructive resonances aggravated by different ignition characteristics. We already see this phenomenon reflected in the rpm band limitation imposed on some of our aircraft with metal blade props. In order to consider an electronic ignition proposal for a metal prop, the LAA expects you to demonstrate that your prop manufacturer is happy with your proposal (a ‘nonobjection’), or that a certified version of your proposed engine / prop / ignition combination already exists.
The LAA will also be expecting you to propose a fail-safe solution whereby a single failure (such as a common power source) does not stop the engine. This often involves self-powered ignitions (Picture 8) or an independent battery backup. One of the ‘acceptable’ approaches to achieve a fail-safe solution is to replace just one mag but, before you plan a single electronic ignition, consider what it is actually doing and if the benefit of that one device is worth the investment or effort. With that approach, you will have one spark being generated consistently at 20° BTDC and another firing anywhere between TDC and 40° BTDC depending on your environment. In an engine designed to have both sparks firing together the resultant timing and benefits will certainly not be the same as for a dual system and its effect needs to be carefully considered.
Is electronic ignition worth it? While the spark strength benefits for starting are without question, the spark alone does little for power or efficiency. From a timing point of view, the way most of us fly in the UK the aircraft is close enough to the sweet spot for the fixed ignition timing much of the time. Measurable efficiency benefits from variable timing will only really come if it is operated for a significant time outside of the sweet spot envelope, e.g., if it does a lot of long-distance high-altitude work or perhaps lots of low throttle work. Of course, if you have to change a mag then it’s a serious contender even if you have to fix its timing to that of the old mag. The feedback from my investigation and on the forums tends to back this conclusion, with few reports of tangible performance gains, although lots of praise for starting improvements.
Below A fine wire (iridium) plug, beside a traditional massive electrode plug. The massive electrode, while lasting well, masks the spark from much of the fuel resulting in much less reliable ignition. A fine wire plug produces a much larger spark from the same voltage and much less masking results in better ignition. The catch is, the exotic materials needed to avoid wearing out too quickly. My, are they expensive!
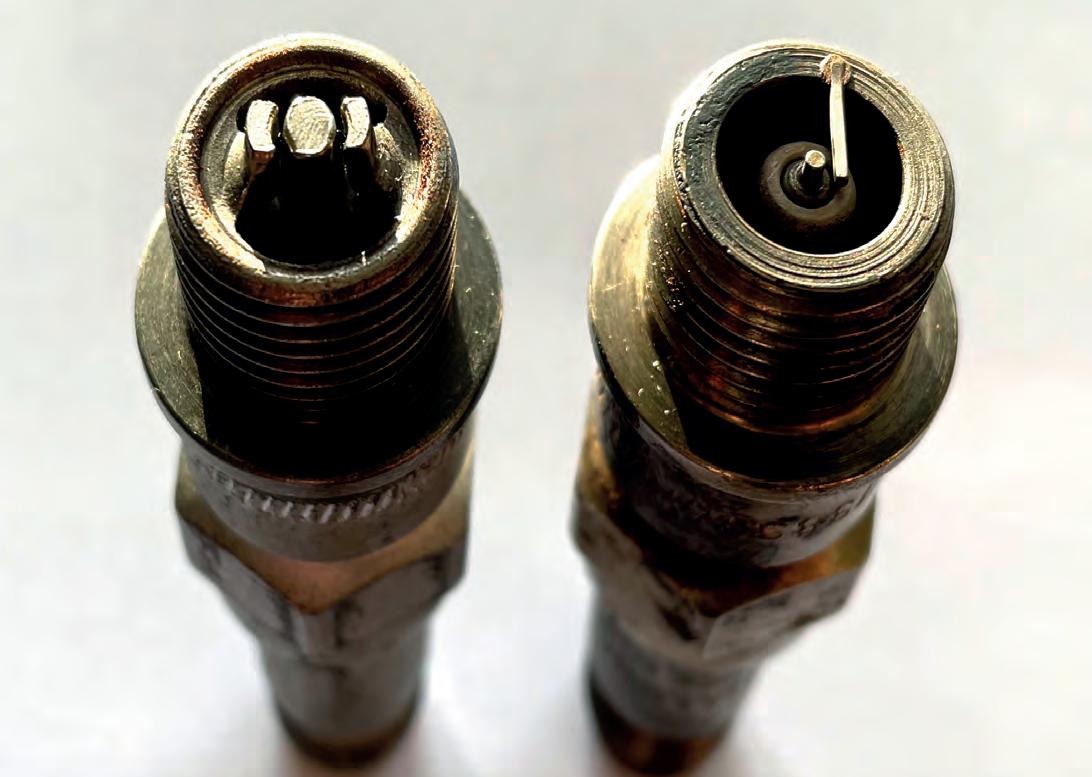
I looked carefully at electronic ignition for my RV-6 (Lycoming O-320 & metal fixed prop) and, notwithstanding the metal prop issue, concluded that a single electronic ignition for my normal use would not provide any quantifiable efficiency or performance benefits. A dual system might show some efficiency improvement long-term and, of course, would be kinder to the environment, but costs twice as much.
Also, I use fine wire plugs (Picture 9) with a less shielded spark area and narrower electrode producing a much better spark from my standard magnetos, so I would gain little from the bigger spark. But, if I could put it in, would I? Yes, if I could install a dual system. But then again, that is me and I like playing with technology… ■