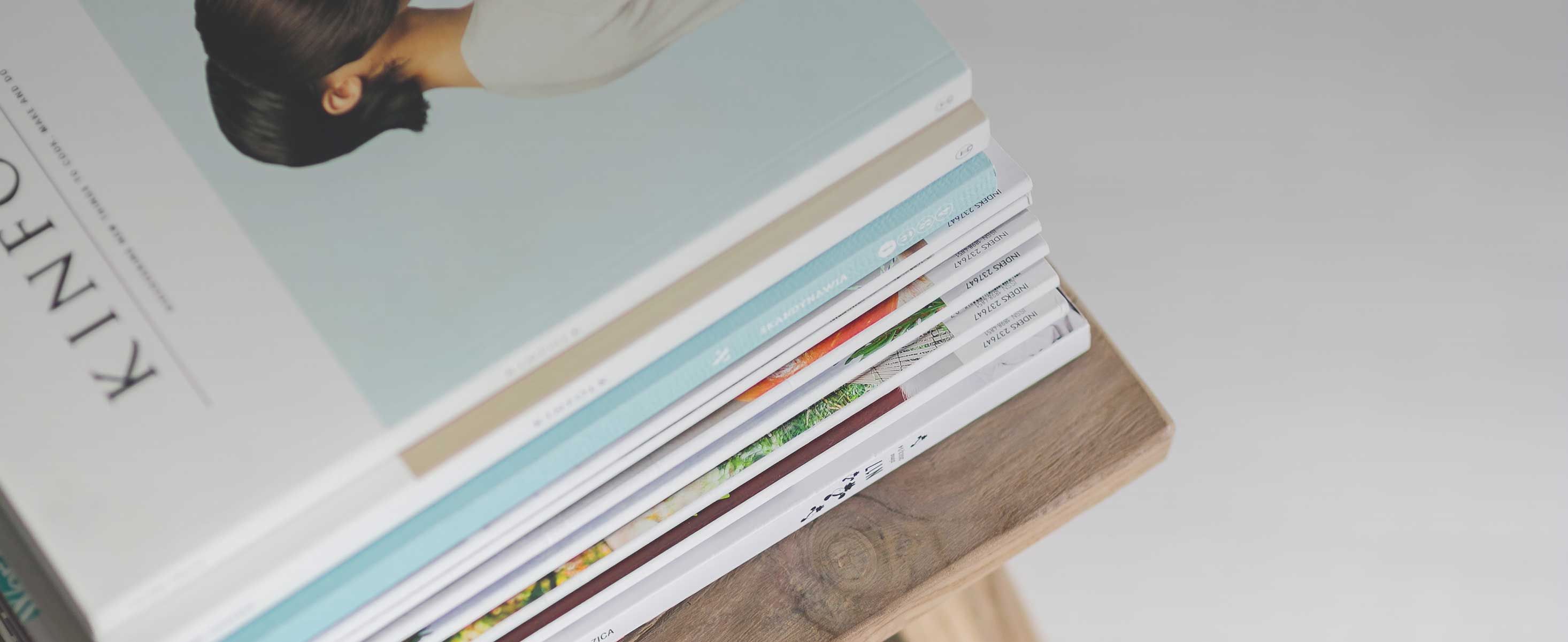
3 minute read
4 CHAPTER TECHNICAL
Drawings
4.1 DESIGN
Advertisement
4.2 BUILDING WEEK
Every design can look great on paper or in renders, but it is also important that it works and can be built. To achieve this, technical plans are necessary, as they are the means by which the constructor can make the design a reality.
In this case, two types of plans were made: the design technical plans of the complete object and the technical plans for the prototype construction that would be built in the following weeks. The difference mainly lies in the materials that are detailed and the scale used.
4.1 DESIGN TECHNICAL DRAWINGS
Thousands of hand drawings were made in the design process of OSTRA, but also work technical plans accompanied this stage, which helped to give scale to the ideas. After the design was completed, the final technical plans were made and are shown below.
The technical file consists of general top views, a section of specific parts, and a top view with sections of the most important elements.
1. General Top Plan (open stage):
In this plan the main general dimensions are shown, as the distance from the center to the farthest points. Also, every fin lenght is detailed, for this reason the open stage of the object was considered appropriate. Finally, the materials and thickness of the most important elements which can be seen are shown; some of them appear in a dotted lines as projections.
GENERAL TOP VIEW PLAN
OPEN STAGE
ESC.: 1/25
To give more information, color was included to the plan. The gradient color gives depht to the drawing, which can help to understand which fin are aboved and at the bottom.
All the fins are shown one on top of the other. Also, the bollard can be seen in the background.
General Topview Plan
CLOSE STAGE
ESC.: 1/50
Distance from the ground to the lowest and heighest fin are shown, as the handle’s height.
The top part of the object is where almost all of the mechanism for movement for the happen.
5, 6. Joint plans (type 1):
One of the biggest challenges in the design was the joint between the pole and the fin, which also needed to move. For that purpose ball bearings were used to make the rotation possible.
The design have two kind of joints. The first is attached to the gear, the second type are above and repeats eleven times.
7. Joint plan (type 2):
The design contemplates a casting fabrication for this piece. For that matter, in this plan all the dimensions to make the mold for the joint are shown.
Plans
JOINT PIECE - TYPE 1
ESC.: 1/5
JOINT PIECE - TYPE 2
ESC.: 1/5
8. Detail Section 1: A close view in section of the joint showing the dimension and also how the stopper would work.
9. Detail Section 2: Other section of the joint showing the longest part which will be in contact with the fin.
4.2 BUILDING WEEKS TECHNICAL DRAWINGS
For the materialization of one of the models that were done, plans were also needed. The following ones correspond to a ball bearing production, part of the rotational system. One section and several plans of two levels and the middle ring were drawn These drawings were done after studying the material that would be used and the available tools. During the construction, changes were also made.
1. Thrust ball bearing:
Left: Ball bearing plan view. Bottom: Ball bearing section. Right: Middle ring plan view.
2. Groove ball bearing:
Top: Ball bearing plan.
Middle: Ball bearing section.
Bottom: Section showing the parts which conform the channel for the ball bearing.
BALL BEARING FOR JOINT TYPE 1
ESC.: 1/5
BALL BEARING FOR JOINT TYPE 2
ESC.: 1/5
BALL BEARING FOR JOINT TYPE 2
ESC.: 1/2
3. Section for 1/1 Model:
The prototype of the mechanism was tried to be represented, before the actual building weeks, in a section with all its components. Some of the materials for the elements where not decided yet.
1. 1 Hollow Pole (material unknown) - metal or PVC. D=30cm. H=40cm.
2. 1 Hollow Pole (material unknown) - metal or PVC. D=15cm. H=20cm.
3. 1 First Joint (Detailed below)
4. 2 Second Joints (Detailed below)
5. 1 Rod (material unknown) connection between worm gear and spur gear - metal or PVC. D=1cm. H=40cm.
6. 1 Rod (material unknown) for the handlemetal, wood or PVC. D=4cm. H=7.5cm.
7. 1 Worm Gear System. 3D printed. (Detailed below) H=29cm.
8. 1 Rod (material unknown) connection between handle and worm gear - metal, wood or PVC. D=1cm. H=5cm.
9. 1 Spur Gear (upper part). 3D printed(?). (Detailed below).
10. 6 Support Triangles. (material unknown)metal or wood. W=1.5cm. H=2cm. Thickness: as thick as possible.
11. 3 Separation Rings. (material unknown)metal or wood. IR=15cm. ER=18cm.