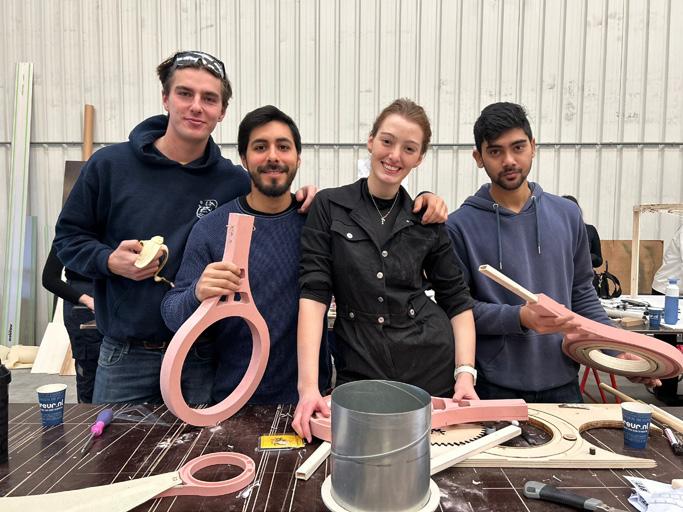
10 minute read
5CHAPTER BUILDING
Weeks
5.1 TARGETS
Advertisement
5.2 BUILDING WEEK PROGRESS
5.3 GANT CHART
5.4 PHOTOS
5.1 TARGETS: 1:1, 1:2, 1:10
To give a good impression of how the OSTRA project looks and works, several scales of the project were built. Target beforehand were three different scales:
1:1 model, this scale is all about the rotational mechanism. How does is it open and close and what happens inside of the structure?
1:2 model, the 1:2 model is proposed to show of the fin structure and the attachment details of fabric to the fin and fin to the joint.
1:10 model, this scale will show the whole structure and give an impression of how the project will turn out to be.
5.2 BUILDING PROCESS WEEK 1
The first day was the introduction day, where several experienced people showed the powertools to the students and how to handle them with care.
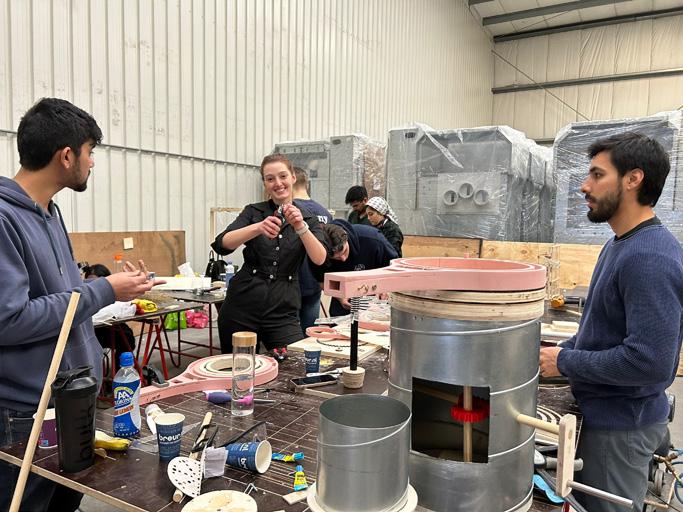
On tuesday the group was excited to start and knew it had a big task to get all of the ball bearings and joints finished on time. After some quick discussion and question with and to Marcel, the router was taken and a lot of circles for the ball bearings were made. The 1:1 model required one thrust ball bearing and two groove ball bearings. The thrust ball bearing consisted of two separate rings and the groove ball bearings of four rings each.
So, a lot of circles in not so much time had to be delivered. In turns the group took up the router so the process did not stop, the bit was rotating in overtime and got so hot it burnt some of the circles and the bit had to be thrown away, unfortunately... While this process was going on drawings were made for the 1:2 joint, which was going to be made by using the Shaper tools. Wednesday arrived and the group needed the whole day to finish the circles for the ball bearings. While two people were working on the rings, the other two finished the 1:2 joint.
After two very productive days, thursday was a day off; the group was a bit lost and did not really know what to do. Drawings for the shaper took a lot of time and besides getting the lasercuts for the 1:10 not a lot of progress was made unfortunately. At the end of the day a plan was made so the group would not get stuck again.
On friday the first joint for the 1:1 model was made as well as the base for the 1:10, after an intense first week it was time for the weekend.
Most of the products were finished starting the first week, this week would be finishing up and assembling the products in order to be finished on Wednesday.
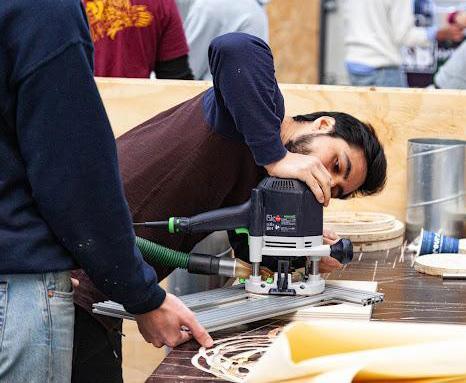

On Monday two shapers were used all day in order to finish the joints for the 1:1 model. Taking turns the team managed to get them right, a few mistakes were made because of the repetitive cutting of the joints. These mistakes were small and the team was able to get them right afterward by using sandpaper. In the evening the gears were printed so we could assemble the gear system on Tuesday. To get this system working the team had to improvise a bit, the main issue was the round pole where the gears had to be attached to. After some trial and error with the different types of gear, the team managed to get them tight and working. Until this point, the product was never assembled and the team did not know yet if the model was going to work. The process in which the product had to be assembled could only start when every individual product was done. On the final day, all of the products were done and the different models had to be finalized. Most important was the 1:1 model, the assembly of the model went quite well. The main problem was that the ball bearings had some imperfections which led to crooked angles and therefore the angle of the joint was crooked as well. The team took 5 mm of tolerance between the joints but this was not enough in the actual model.
The different joints stacked on top of each other were touching and this led to resistance between them. When rotating the lowest joint the joint on top of that one started to move because of this. To solve this issue a few marbles were put inside of the H-section of the joints in order to give some extra tolerance between them. This solved the issue of the resistance but was of course not the perfect solution. The team had no time to solve this in another way so this solution was chosen. In the end the 1:1 model rotated as envisioned, the 1:2 gave a great representation of the fin structure and the 1:10 model looked very cool. Satisfied the OSTRA team enjoyed some nice snacks and beers with the rest of the Bucky Lab colleagues.
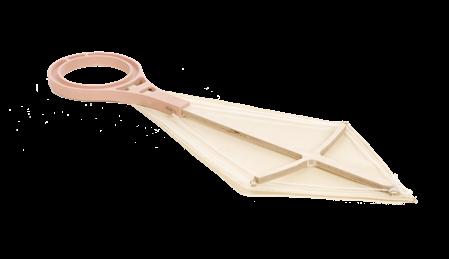


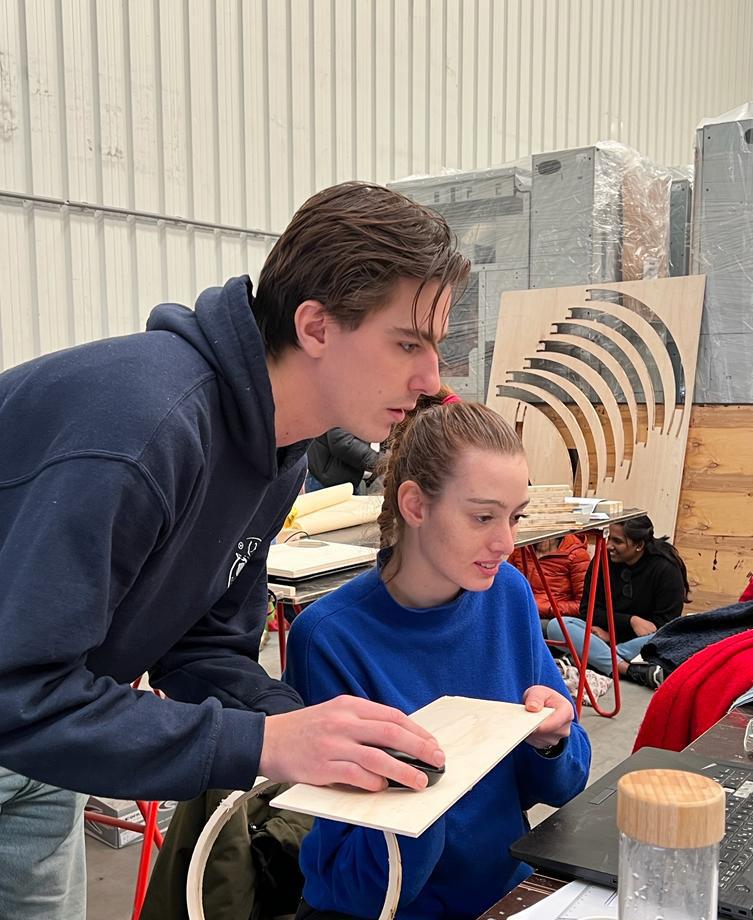
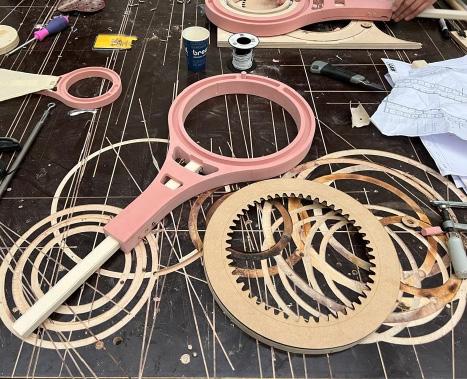
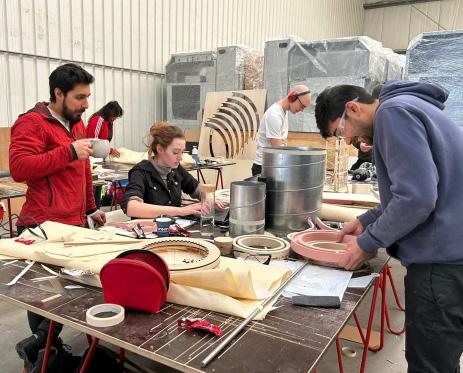
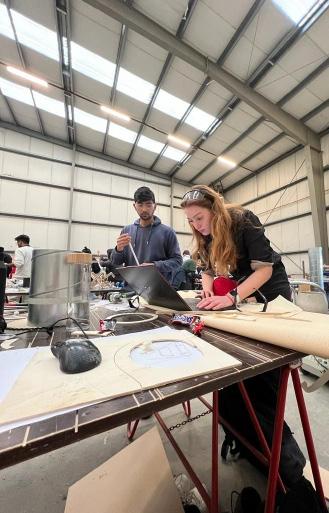
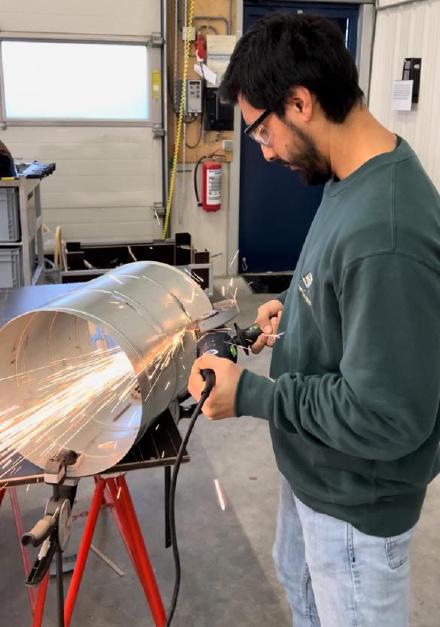


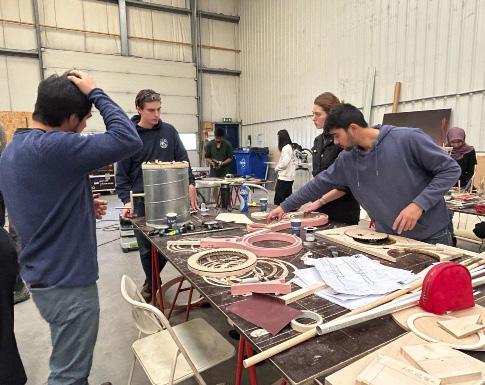

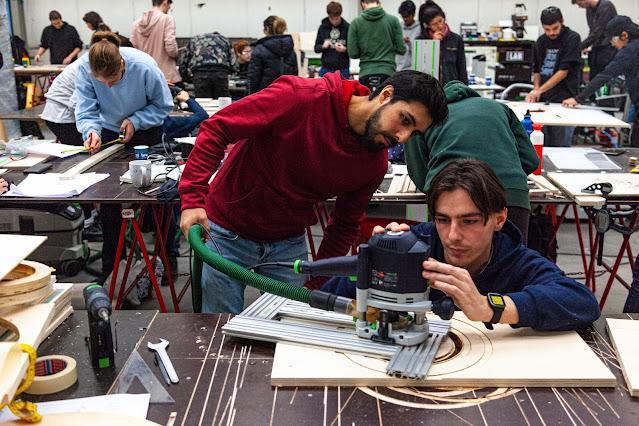

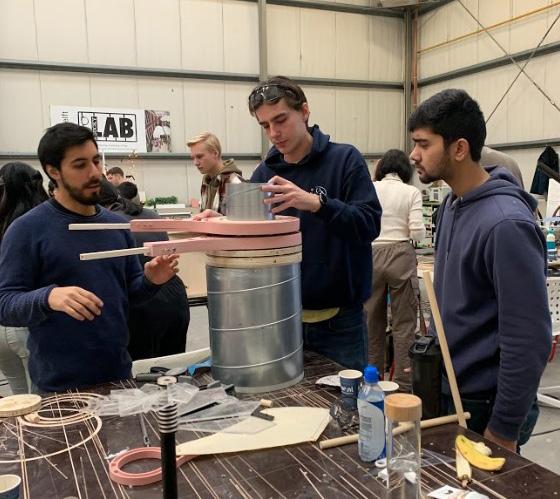
Chapter Final Product
6.1 RENDER
6.2 SOUTH ELEVATION
6.3 AXONOMETRIC VIEW
6.4 PHASES
6.5 ASSEMBLY DETAIL
6.6 EXPLODED DETAILVIEW
The render shows how the project is envisioned by the team in front of the Delft Central station. It provides shade throughout the day and it can be operated by individuals belonging to all age-groups.
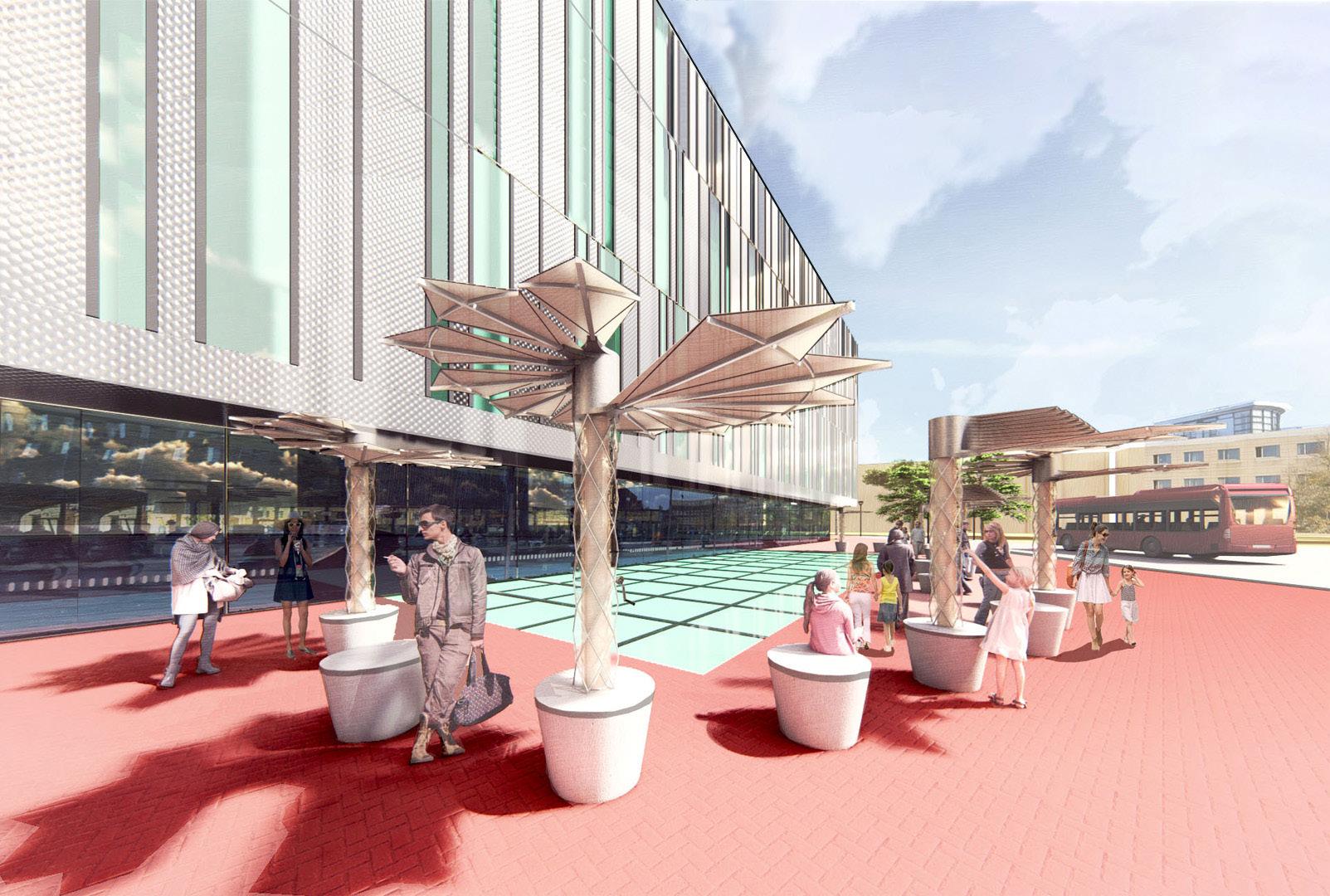
The elevation shows how OSTRA reacts to its context. As it has minimum 2.4 meters clear height, it allows people to stand next to it as well as sit on the bollard. OSTRA makes the bollards outside Delft Central station more usable as people can now wait for their bus in the shade, The pole also give back rest for people sitting thus making it more ergonomical.
OSTRAs are placed on alternate bollards. This scheme was conclusively chosen after running real-time sun solar simulations. With this arrangement, there are always pockets of shaded areas either close to the bollard or onto the next bollard. Alternate OSTRAs also make the place look less clustered from eye-level thus not making it overwhelming for people using it.

Fin
Cast Aluminium Joint
Inner column 150mm Dia.
Exoskeleton 300mm Dia.
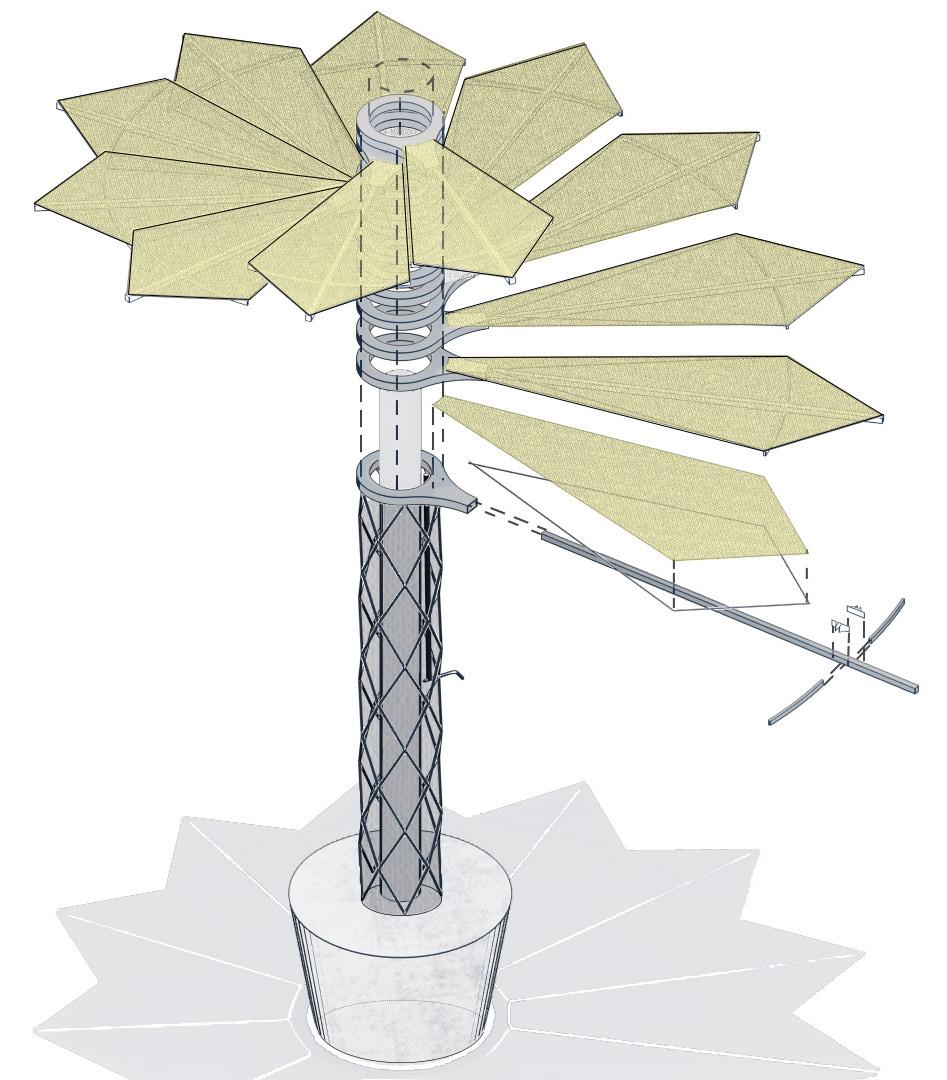
Handle for Gear system
Existing Concrete bollard
Ball bearings 200mm(outer dia.) 150 mm(inner dia.)
AL Stopper
Cast Aluminium joint
5X5 mm channel section
Rail channel
25mmX15mm
Hemp fabric 5mm
Cast Aluminium joint
5X5 mm channel section
Mortise and tennon AL joint
20mmX15mm
Fin primary spine
Carbon fiber 25mmX40mm
Thrust ball bearing
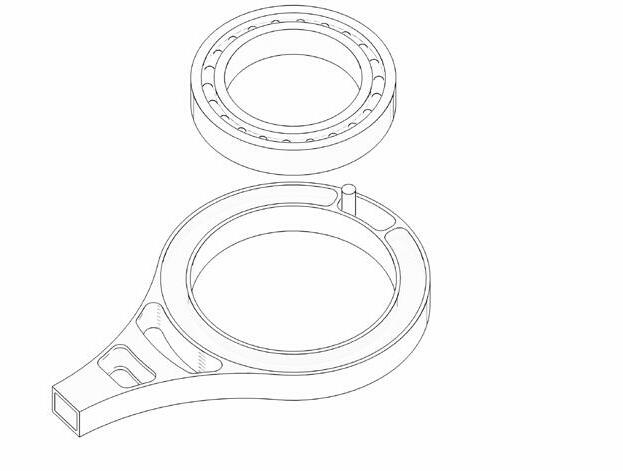
300mm(outer dia)
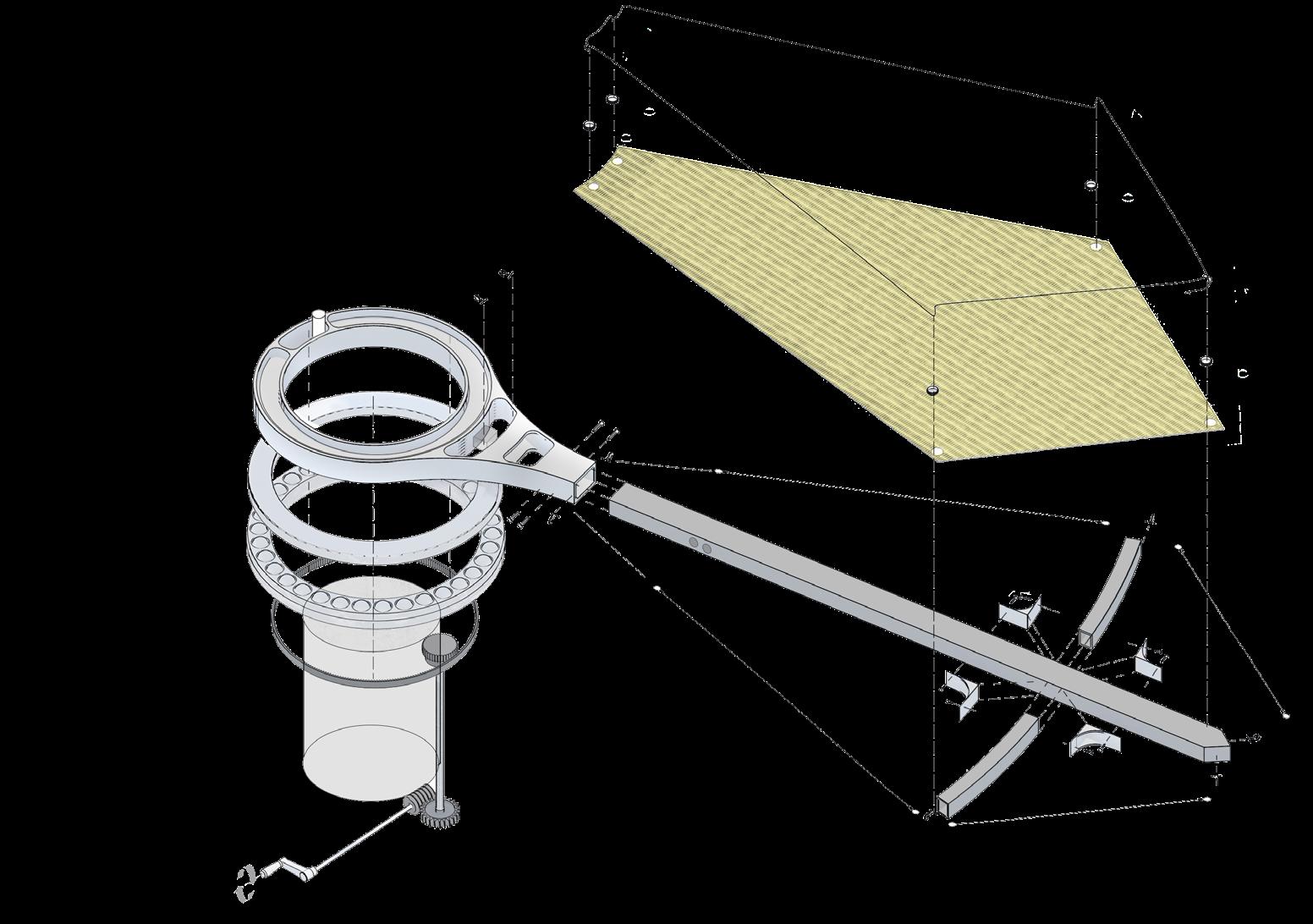
240mm(inner dia)
Spur gear 40mm Dia.
10 mm Rod
Worm gear
Inner pole
150mm(outer dia)
Handle
Steel cables 3mm
Eyelets 3mm
Steel cables 3mm
Steel hooks
Spilcing plates 3mm
Screws 5 mm
Chapter Reflection
7.1 GROUP REFLECTION
7.2 FUTURE CONSIDERATIONS
7.3 INDIVIDUAL REFLECTION
Who are we?
We, the group of “OSTRA”, are MSc. Building Technology students of TU Delft, coming from three different continents around the world.

During the initial phase of Bucky Lab, we all shared similar ideas on a sunshade which was designing a manually operated sunshade supported by a pole, addressing issues of high temperatures and the urban heat island effect. We came together and chose a design that had a strong starting point, a great location in Delft, in the Netherlands, and then started brainstorming to improve it. Having that purpose as a team, our journey as OSTRA had begun!
Our diverse backgrounds enabled us to come up with unique concepts, references, and ideas that would not come to others’ minds. We always enjoyed our company, and learned from each other, not just academic stuff but also about our cultures. Eloy made us familiar with the local Dutch culture and became the tourist point whenever we needed him; Daniel made us familiar with the amazing natural habitats and places of Peru; Shashvat taught us all the colorful and joyful Indian Festivals and his rockstar talents; and Ece made us familiar with the delicious Turkish cuisine and increased our curiosity of Istanbul to see both continents at once!
Throughout the Bucky Lab, we tried to keep our meetings 1-2 times a week and 1 time during the Bucky Lab studio. During each meeting, we never forget to enjoy our coffee sponsored by the person who came latest to the group meeting! We even learned who we liked and what type of coffee, haha!
All of those made our design process more stronger and fun. We always had a healthy discussion, where we were able to discuss our ideas freely, and respectfully and come up with decisions altogether. We have understood the importance of having constructive feedback from each other, which we believe made us great groupmates and made our design stronger.
Throughout the process, all of us put in our effort equally, always asking “how can I help?
That’s us! But, you might still wonder where our unique group name “OSTRA” is coming from. So, there it is
*A small note: Shashvat wanted to say “Rule” but as the others, we wanted to keep it low-key! Haha
Design Week Process:
During the design processes, we have focused more on how to operate our system and the shape of our design to optimize the shade as much as possible. Learning about different gear systems and ball bearings became the most interesting part for us, which we ended up even constructing! We made several working models, using different materials depending on the objective of each one. Despite the good communication we had between us, we started with a fine model of our joint, it cost a lot but was not entirely necessary to make it so perfect. We learned from our mistakes and in the end, everything turned right.
On the other side, there were some challenges we wish we should have tackled during the design process.
One of them is the wind load. Even though the weight on the center creates a balance for the cantilever units, taking a closer look at the wind load and the deflection of the individual units would have made our design more realistic.
The attachment to the bollard was not fully resolved. In the last design week we tried to get into more detail in the connection between the metal pole and the concrete bollard. We made some sketches and got a couple of options but we were not entirely sure about them. A few more days would have been enough to completely solve it
Building Weeks:
One of the most fun and educational parts of the whole studio was the Building Weeks. At first, we had all our drawings ready but we did not have a proper schedule and did not know which tools and techniques are the best fit for us; which made us end up losing a little bit of time in the beginning. Luckily, with the help of Marcel, Nadia, and George we managed it quickly and adapted to tools and materials. Furthermore, we had to revise all the drawings to make them fit the available materials we have, especially the pole we collected (which used to be an air duct).
It was very effective and joyful to use all these power tools and be the engineers behind our design. We mainly used the router and a shaper, which gave our design its unique pinkish appearance. We all were quite excited to see how the mechanism operates so we couldn’t wait but assembled the parts we constructed before taking a photo.
Is it a good idea? Yes!
We believe that our design is proposing a sunshade that can be operated by people of ages and can be located not just in Delft but anywhere having a concrete base, especially on the bollards. It is a good improvement for urban furniture, making security elements feel safer and more useful for the pedestrians and the city by giving an aesthetic look in contrast to the securi bollards. Even legos can get benefit from OSTRA, if they need shade!
Can it be improved? More yes!
Our end product needs more improvement in terms of material selection, bulkiness, number of components, and some further load analysis.
Currently, we have lots of components and materials that can be considered expensive. Our first idea would be to replace the carbon fiber with a more budget-friendly alternative but maintaining the properties of stiffness and lightness needed for that element. Secondly, we would change the material of the joints. It was designed as an aluminum cast element, but after we learned from one of our peers during the final presentations, it would be a better option with magnesium cast. Thus, our design could be stiffer, stronger, and more inexpensive compared to the options we have now.
In the end, it was a special Bucky Lab journey. We enjoyed collaborating with each other as a team at the OSTRA. We not only learn from each other but also from our professors, our colleagues, and everyone else who was there with us. It was great to see so many cool projects being realized.
A very special thanks to Marcel and Nadia who guided us endlessly throughout the process and encouraged us to strive for the better and giving the opportunity of a hands-on project and experiment for turning our sketches into real working models. Also, thank you for reminding us the process is our real journey, mistakes are a key to success, and most importantly to having fun during this very special Bucky Lab journey!
We also had a great group dynamic during these weeks, always asking each other “what can I do further?” or “do you need any help”. We guess we enjoyed our company quite a lot so that we were even spending our lunch times together!
We finalized our modeling weeks by having three different scale models: 1:1 showing the mechanism of the design, 1:2 showing our shading unit, and 1:10 our overall design. The highlight of the process was seeing the smile on our pink dust-covered (thanks to our fins)
Also, we were not quite happy with having a bulky appearance on an already bulky concrete. To overcome this, we already came up with a more aesthetic and lighter idea with the use of uniquely designed diamond framing around a glass pole. However, we could not evaluate the design yet if it would support the structure in terms of strength. Another reflection on our design, which we received from our peers and tutors during the presentation was the various sizes of the shading elements we had, which was not making the individual units modular.
