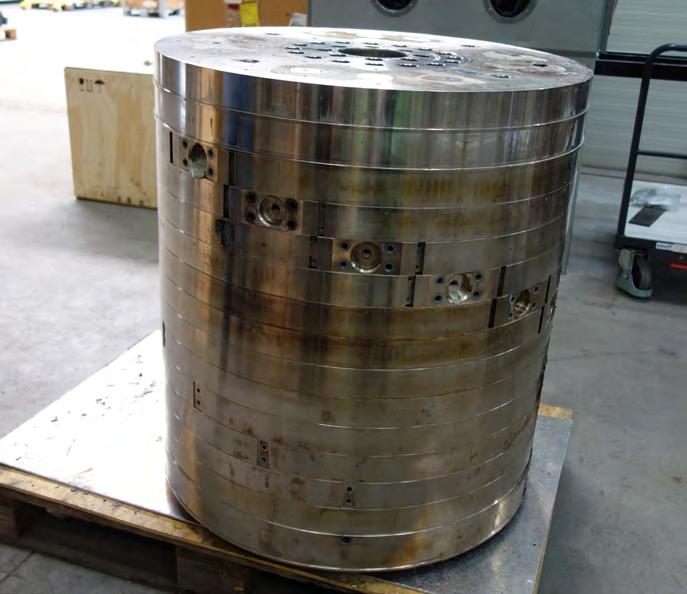
14 minute read
VERFAHRENSTECHNIK
from ChemieXtra 5/2020
by SIGWERB GmbH
Porenfreie Vernickelung
Präzise Beschichtung von Blasfolienköpfen
Advertisement
Ob Kaffeekapseln oder künstliche Wurstpellen – ihren Ursprung haben die mit Abstand meisten von ihnen auf einer Kuhne-Maschine. Schlüsselkomponenten aller Anlagen sind die Extrusionswerkzeuge, die bei Blasfolienextrusion als Blasköpfe bezeichnet werden. Bei der chemischen Vernickelung dieser hochkomplexen Bauteile vertraut Kuhne auf die Präzisionsarbeit der Pallas GmbH und Co. KG, einem ausgewiesenen Experten im Bereich anspruchsvoller Oberflächentechnik.
Die Kuhne Maschinenbau GmbH entwickelt und stellt schlüsselfertige Anlagen für die Flachfolien- und Plattenextrusion her. Neben Tiefziehartikeln wie Joghurtbechern und Kaffeekapseln werden daraus Agrar- und Baufolien hergestellt. Kernkompetenz der Kuhne Anlagenbau GmbH ist der Bau von Mehrschicht-Blasfolienanlagen für die Lebensmittel-, Medizin- und Pharmaindustrie. Auch Hersteller von Ballon- oder Batteriefolien vertrauen auf die aussergewöhnliche Leistungsfähigkeit dieser hochkomplexen Anlagen. Die für alle Anlagentypen erforderlichen Folienblasköpfe (Bild 1), Flachdüsen und Extruder fertigt die auf Zerspanen und Polierverfahren spezialisierte K-Tool GmbH. Diese ganzheitliche Aufstellung von Kuhne ist die Gewähr für hohe Qualität.
Für jede Eigenschaft eine Folienschicht Angesichts immer anspruchsvollerer Konsumentenerwartungen werden die Anforderungen der Verpackungsindustrie an Folienverpackungen kontinuierlich komplexer. Maximaler Glanz, brillante Transparenz und weiche Haptik zählen dazu ebenso wie eine Vielzahl mechanischer und funktionaler Eigenschaften. Oberste Priorität hat jedoch maximaler Schutz des Packguts bei Transport und Lagerung – verbunden mit der Forderung nach möglichst langer Haltbarkeit und multifunktionalen Barriere-Eigenschaften. Mit zuverlässiger Sperrwirkung gegenüber Sauerstoff, Feuchtigkeit oder UV-Einwirkung gewährleisten Hochbarrierefolien, dass die Produkte Farbe und Geschmack behalten und Flüssigkeiten weder nach innen noch nach aussen dringen. Ausserdem sorgen sie dafür,
Bild 1: Modell eines Blaskopfes.
dass wertvolles Aroma bewahrt, störender Geruch vermieden und die Haltbarkeit maximiert wird. Jede dieser Eigenschaften bedingt zum Teil weitere Schichten in der Folienblase. Abhängig von den Kunststoffkombinationen in den einzelnen Schichten werden zusätzliche Haftvermittlerschichten benötigt. Um die Wettbewerbsfähigkeit der Verpackungskunden trotz sinkender Losgrössen zu sichern, gilt es ausserdem, durch intelligente Verfahrensoptimierungen Produktionskosten und Materialverbrauch immer weiter zu senken. Es gibt drei unterschiedliche Verfahren bei der Blasfolienproduktion: Luftgekühlte
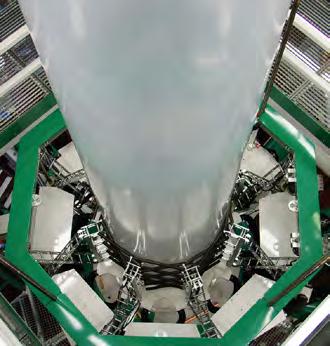
(Smart Bubble, siehe Bild 2), wassergekühlte (Cool Bubble) oder ohne Laminierund Beschichtungsprozesse in nur einem Arbeitsprozess biaxial-verstreckte Mehrschichtfolien (Triple Bubble, siehe Bilder 3 und 4). Kernkompetenz ist der Bau von Mehrschichtanlagen für bis zu 17 Schichten, die nahezu alle thermoplastischen Kunststoffe verarbeiten können. Neben dieser aussergewöhnlich hohen Anzahl an Schichtkombinationen erlauben die Anlagen auch die Produktion sehr dünner Folien – bis zu 15 μm dünn – mit entsprechend geringem Rohstoffverbrauch. Zentrale Komponente jeder Blasfolienanlage ist der Blaskopf (Bild 1), der sich aus mehreren Wendeln zusammensetzt, die in einem senkrecht stehenden Zylinder den Schmelzkanal bilden. Bei Temperaturen von bis zu 300 Grad Celsius wird flüssige Kunststoffschmelze in diese rotationssymmetrischen Bauteile – Hülsen oder Scheiben – eingespeist und mit bis zu 500 bar Druck aus ringförmigen Düsen geblasen. Dadurch entsteht ein bis 20 Meter hoher Schlauch, die sogenannte Blase, die ohne Druck durch einen Kalibrierkorb zur Flachlegung geleitet wird. Bei der Triple-Bubble-Technologie entstehen in einem Arbeitsprozess drei Folienblasen, indem die erste in der zweiten biaxial-verstreckt und die zweite in der dritten thermofixiert wird.
Auf den Mikrometer genau
Björn Greis steuert als Konstruktionsleiter Extrusion im Anlagenbau und Technischer Leiter von K-Tool unter anderem den gesamten Fertigungsprozess der Blasköpfe. Anhand der individuellen Kundenanforderungen zu Anlagentyp, Folienstruktur und -grösse sowie den Vorgaben zu Output und Masseleistung prüft er, ob für die Umsetzung bestehende Module oder Sonderkonstruktionen erforderlich sind. Neukonstruktionen von Extrusionswerkzeugen bespricht Greis anhand von Zeichnungen und CAD-Modellen zunächst mit dem K-Tool-Team, bevor entsprechende Ablaufpläne erstellt werden und die Umsetzung erfolgt. Permanente Kontrollen mit Mikro meteruhren gewährleisten schon bei der Zerspanung, dass alle Aufmasse präzise eingehalten werden. Beim Polieren ist vor allem die Erfahrung der Fachkräfte gefragt.
Bild 3 und 4: In einem Arbeitsprozess biaxial-verstreckte Mehrschichtfolien (Triple Bubble).
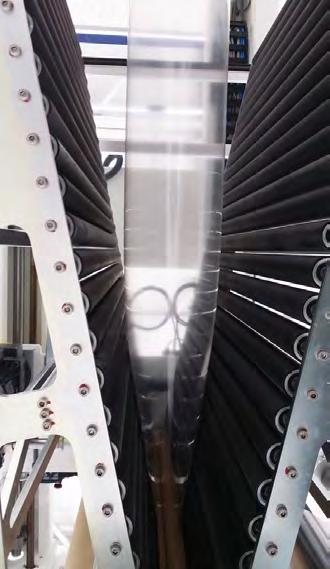

Um Fliesswiderstände der Kunststoffschmelze zu vermeiden, werden die Oberflächen von Hand spiegelblank poliert und vor dem Beschichten nochmals auf einer Koordinatenmessmaschine vermessen. Trotz der Messprotokolle lässt sich Björn Greis eine Sichtkontrolle nicht nehmen: «Jedes Kopfbauteil, das hier rein- und rausgeht, habe ich in der Hand.»
Konturtreue Beschichtung Entsprechend kritisch war er auch bei der Auswahl eines neuen Beschichters für die chemische Vernickelung der Blasköpfe. Mehrere schlechte Erfahrungen mit fehlerhaften Oberflächen hatten ihn grundsätzlich misstrauisch gegenüber dieser Technik für Extrusionswerkzeuge gemacht. Angesichts der Komplexität der Geometrie und extremen Beanspruchung der Einzelkomponenten durch Verschleiss und Korrosion ist jedoch eine Beschichtung mit Chemisch Nickel allen anderen galvanischen Verfahren deutlich überlegen. Exzellente Korrosionsbeständigkeit und eine mit Hartchrom vergleichbare Härte kennzeichnen die in diesem chemischen, autokatalytischen Prozess erzeugten Schichten. Im wässrigen Elektrolyten scheidet sich die Schicht ab, die überall dort, wo das Bauteil mit der Lösung in Berührung kommt, eine absolut gleichmässige Nickel-Phosphor-Legierung darstellt. Diese aussenstromlos abgeschiedene Schicht veredelt konturtreu und mikrometergenau auch sehr komplexe Geometrien mit vielen Passungen, Kanten und Gewinden. Durch abschliessendes Tempern erhält die Schicht eine Härte von bis zu 950 HV. Anders als bei Hartverchromungen entfällt bei einer chemischen Vernickelung jede Nachbearbeitung. Entscheidend für die Qualität dieser Beschichtung ist jedoch eine perfekte Beherrschung dieses ausgesprochen sensiblen Verfah rens. In Pallas fand Björn Greis vor rund eineinhalb Jahren einen ausgewiesenen Experten, der zudem das von Kuhne geforderte hochwertige High-Phos-Verfahren anwendet. Diese Badchemie erzeugt eine Nickelschicht mit über zehnprozentigem Phosphorgehalt. Dadurch sind die so veredelten Oberflächen chemisch sehr beständig und bieten einen hohen Korrosionsschutz.
Behandlung wie ein rohes Ei
Diese Beschichtung wird besonders oft für Extrusionswerkzeuge der Triple-Bubble-Anlagen angewendet. Deren hochglanzpolierte Blasköpfe – je nach Anwendung
in Hülsen- oder Scheibenbauform – vernickelt Pallas komplett. Bei einem ElfSchicht-Kopf umfasst der Auftrag elf Wendel sowie je eine Boden- und Abschlussplatte mit unzähligen feinen Bohrungen, Kanten und Gewinden. «So eine Bohrung hat nur einen Durchmesser von acht Millimetern und 65 Millimeter Länge», erläutert Björn Greis. «Je nach Anwendung brauchen wir eine porenfreie Schicht von 10 bis 50μ. Da ist absolute Präzision und Sauberkeit erforderlich!» Die damit verbundenen Anforderungen sind schon wegen der Dimension der Bauteile beachtlich: Mit 800 Millimetern Aussendurchmesser und 160 Kilogramm Gewicht pro Wendel – die Bodenplatte bringt sogar 300 Kilogramm auf die Waage – verlangen die hochglanzpolierten Komponenten eine entsprechend leistungsfähig ausgelegte Infrastruktur und gleichzeitig eine Behandlung wie ein rohes Ei. Den Beginn markiert ein mehrstufiger Reinigungsprozess, der entscheidenden Einfluss auf die spätere Haftfestigkeit und Optik der Beschichtung hat. Sämtliche Fett- und Oxidschichten sowie andere Verunreinigungen wie Abrieb müssen rückstandslos entfernt werden. Nacheinander durchlaufen die Bauteile dafür eine alkalische und elektrolytische Entfettung sowie eine saure Beize. Zwi schen jedem Behandlungsschritt erfolgen zudem aufwendige Spülgänge. Danach werden alle Gewinde und Bohrungen, die nicht vernickelt werden sollen, sorgfältig per Hand abgedeckt. Die Bearbeitungsdauer von rund 14 Tagen für die Beschichtung eines Blaskopfes ist für Björn Greis eine lange Zeit, denn die Nachfrage nach Blasköpfen von Kuhne sei gross.
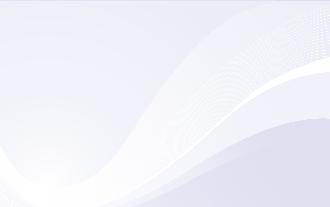
Kontakt Pallas GmbH &Co. KG Adenauerstrasse 17 D-52146 Würselen +49 2405 4625 0 info@pallaskg.de www.pallaskg.de
Labor-Kühlwasser-Verteiler in Edelstahl für Vorlauf und Rücklauf.
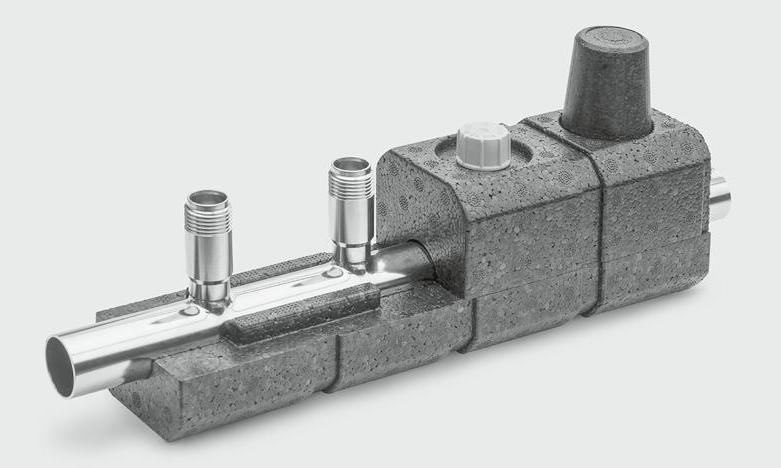
Kühlwasser-Hauptverteiler im Labor 4-fach Verteiler komplett in Edelstahl Ein- und Ausgang ø 28 mm Pressrohr 2 oder 4 Stück OR G1/2“ Auslauftüllen Ausströmsicherungen in Edelstahl Isolation: EPP Halbschalen
VariflexLaborerschliessung
Wir bringen Energie auf den Punkt.
H. Lüdi +Co. AG, Moosäckerstrasse 86, CH-8105 Regensdorf ZH Telefon +41 44 843 30 50, sales@hlag.ch, www.hlag.ch
Durchflussmessung 4.0
Normierte Kommunikationsschnittstelle
Werden leitfähige Medien wie beispielsweise Kühlwasser einem Prozess hinzugegeben, sind in der Regel magnetisch-induktive Durchflussmesser zur Überwachung installiert. Besonders im Rahmen der Dosierungsüberwachung müssen die Messgeräte über präzise Ansprechzeiten und eine hohe Kalibrierfreiheit verfügen, da sonst eine falsche Dosierung oder unzureichende Wiederholgenauigkeit auftritt. Eine vielversprechende Kommunikationstechnologie kann hierbei weiterhelfen.
«Magnetisch-induktive Messgeräte kommen ohne bewegliche Teile wie Flügelräder aus, weshalb sie kaum Verschleisserscheinungen zeigen. Deshalb haben sich diese Geräte für die Durchflussbestimmung leitfähiger Medien bewährt – ob Wasser, Breie und Pasten, Säfte oder Emulsionen», erklärt Raza Ali Agha, Ver triebsleiter bei der Kobold Messring GmbH. «Dieses breite Einsatzspektrum führt aber auch zu sehr unterschiedlichen Einbausituationen, da die Messgeräte in verschiedenen Industrien und Prozessen eingesetzt werden.» Die Nennweite der angeschlossenen Rohre, die mögliche Ausrichtung beim Einbau und die Einbindung in bestimmte Prozessketten, wie die Dosierung beim Einfärben von Tabletten oder der Kühlmittelzufuhr, beeinflussen die Wahl eines passenden Gerätes. Insbesondere im Rahmen von Dosiervorgängen müssen die Messinstrumente die Möglichkeit zur Programmierung von Zwischenwerten bieten, um die Mengen zu dokumentieren und eine ungenaue Dosierung zu vermeiden. Zudem sollte die Anzeige mehrzeilig und gut sichtbar sein, damit das Anlagenpersonal rechtzeitig vor der Überschreitung eines Grenzwertes gewarnt wird. Häufig erfüllen Durchflussmesser jedoch nur einen Teil dieser Anforderungen etwa auf Kosten der Bedienbarkeit. Deshalb hat das Unternehmen universale Durchflussströmungsmesser mit IO-Link entwickelt, welches die Kommunikation zwischen dem Gerät und Automatisierungssystem ermöglicht. Diese normierte Kommunikationsschnittstelle (DIN EN 61131) ist für nahezu jede Messsituation geeignet und neben guten Ansprechzeiten von teilweise unter 100 Millisekunden ist eine hohe Programmierfreiheit gewährleisten. Dafür sor
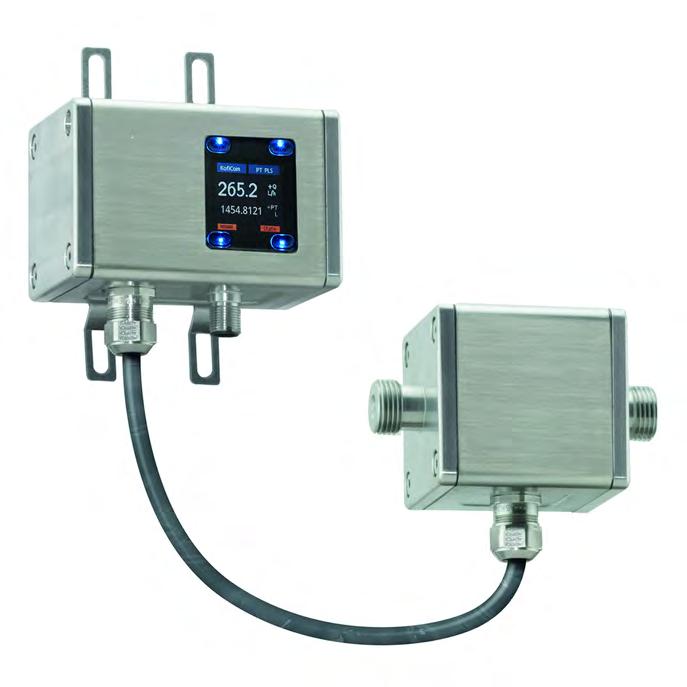
Bei der getrennten Ausführung des Durchflussmessgerätes enthält die medienberührende Einheit lediglich den Sensor. Die gesamte Elektronik sowie die Steuerung und Anzeige sind separat untergebracht und über ein Kabel in sicherem Abstand zur Sensoreinheit am Rohr verbunden.
gen zum einen die zahlreichen Funktionen wie die Temperaturmessung oder die Dosierung, welche sich in nur wenigen Schritten im Menü auf Schnellwahltasten legen lassen. Zum anderen ermöglicht die robuste und flexible Bauweise einen einfachen und übersichtlichen Einbau auch in eng ausgelegten Rohrsystemen.
Einsatz unter extremen Bedingungen
Die Durchflussströmungsmesser sind komplett in widerstandsfähigem Material ausgeführt. Ein Modell der zwei entwickelten Modelle (der MIM) ist sogar in Edelstahl gekleidet. Neben der Funktion zur
Temperaturmessung, die nur der MIM aufweist, unterscheiden sich die Geräte vor allem in Bezug auf die Rohrgrössen, bei denen sie zum Einsatz kommen. Während das andere entwickelte Modell (MIS) für die Nennweiten DN 80 und DN 100 bzw. 3“ und 4“ geeignet ist, kann der MIM auch bei sehr kleinen Rohrnennweiten eingesetzt werden und deckt je nach Nennweite einen Messbereich ab 30 ml/min aufwärts ab. «Die Durchflussmesser verfügen über zwei individuell konfigurierbare Ausgänge, die je nach Einstellung beispielsweise als Puls-, Alarm- oder Analogausgang fungieren können», erklärt Agha. «Dadurch lassen sie sich leichter in ver schiedene Prozesse oder Hilfskreisläufe einbinden.» Das Farb-Multi-Display lässt sich zudem digital in 90-Grad-Schritten drehen, so dass bei einem Standortwechsel kein anderes Modell benötigt wird und die Anzeige unabhängig von der Position der Anschlüsse ist. Damit das Gerät auch beim Dosieren von Kleinstmengen genutzt werden kann, wurde die Ansprechzeit verbessert. Ausserdem lassen sich über das Menü verschiedene Teilmengen programmieren. Um nicht bei jeder Neueinstellung umständlich durch das Menü navigieren zu müssen, wurde die Anzeige um sogenannte Hotkeys erweitert. Auf diese Weise lässt sich die gewünschte Dosierung bequem durch die Schnellwahltasten auf dem Startbildschirm auswählen. Über einen externen Steuereingang lässt sich der gewünschte Dosiervorgang starten und stoppen. Dabei kann vor Ort über den MIM oder MIS die Menge jederzeit angepasst werden. «Insbesondere bei sensiblen Prozessen wie der Tablettenbeschichtung sind präzise gemessene Teilmengen und eine sehr gute Ansprechzeit unabdingbar», bestätigt Agha. Damit diese Möglichkeit auch bei heissen Medien und in stark temperierten Umgebungen wie bei Kühlwasserkreisläufen gegeben ist, ist der MIM in einer getrennten Ausführung entwickelt worden: Anders als bei sonst üblichen Geräten enthält die medienberührende Einheit lediglich den Sensor. Die gesamte Elektronik sowie die Steuerung und Anzeige sind separat untergebracht und über ein Kabel in sicherem Abstand zur Sensoreinheit am Rohr verbunden. Dadurch sind auch Temperaturen bis +140 °C kein Problem und das Gerät kann störungsfrei arbeiten, da die Elektronik geschützt bleibt.
Die Anwenderfreundlichkeit steht im Mittelpunkt Die Flexibilität der Gerätefamilie zeigt sich auch in der Nutzerführung und dem Funktionsumfang. Nahezu alle Einstellungen lassen sich bequem über vier optische Tasten vor Ort auf dem Display einstellen. Funktionen wie Teilmengenanzeige, Tem peraturmessung oder Maximaldurchfluss lassen sich auch auf die genannten Hotkeys legen, so dass nicht ständig über mehrere Steuerungsebenen im Menü navigiert werden muss. Dies lässt sich auch mit Handschuh durchführen, da die Tasten über verschiedene Empfindlichkeitsstufen verfügen. Die mehrzeilige Anzeige bietet einen besseren Überblick als vergleichbare Kompaktgeräte und kann auch neben dem Messwert die entsprechende Einheit oder andere Zusatzinformationen abbilden. Diese Übersichtlichkeit wird nochmals durch die Mehrfarbigkeit des Displays verstärkt: Beispielsweise ändert sich die Farbe, wenn eine bestimmte Durchflussmenge erreicht worden ist. Dadurch sieht der Anwender auch aus der Distanz, wenn etwa eine bestimmte Menge dosiert oder ein Grenzwert überschritten wurde. «Während der Konzeptionsphase haben wir Erfahrungsberichte unserer Kunden aus den verschiedenen Branchen zu Grunde gelegt, um ein sehr flexibles und zuverlässiges Universalgerät entwickeln zu können. Mit dem MIM und MIS gibt es nun die Würfel für fast jedes Messvorhaben», resümiert Agha.
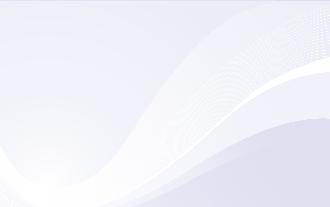
Kontakt Kobold Messring GmbH Nordring 22–24 D-65719 Hofheim/Taunus +49 6192 299 0 info.de@kobold.com www.kobold.com
APOVAC UND COMBIVAC VON BUSCH
Nach der Übernahme von NSB durch Busch Vacuum Solutions sind APOVAC und COMBIVAC Systeme nach einer kompletten Überarbeitung durch Busch lieferbar. Individuell auf chemische und pharmazeutische Anwendungen und Prozesse abgestimmt, bieten wir Ihnen die richtige Vakuumlösung.
www.buschvacuum.com
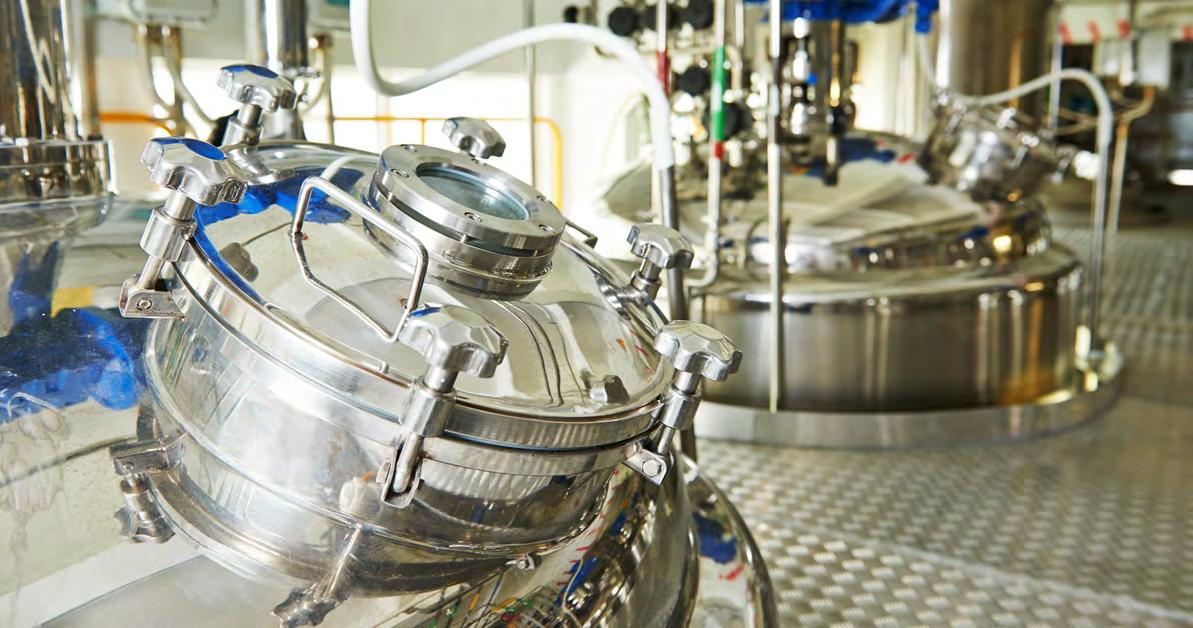
Die Produktion von Milchpulver für Säuglinge und Kälber verläuft in vergleichbaren Prozessschritten. Die Nahrungsmittelproduktion für Säuglinge unterliegt jedoch viel strengeren hygienischen Auflagen, denen die verwendeten Explosionsschutztechnologien gerecht werden müssen.
Sichere Schüttgutindustrie
Fünf zentrale Faktoren für den Ex-Schutz
In der Schüttgutbranche gehört die Arbeit mit explosionsfähigen Stäuben zum Alltag. Entsprechend wichtig ist es, die mehr als 60000 Beschäftigten allein im deutschsprachigen Raum zu schützen. Konstruktive Explosionsschutzsysteme bieten eine effektive Lösung, sofern die durchgehende Funktionalität der Komponenten im Zusammenspiel gewährleistet wird. Fünf Kriterien sind hierbei von besonderer Bedeutung.
Damit Sicherheitskonzepte in der Praxis halten, was sich die Anwender von ihnen versprechen, sind sorgfältige Abstimmungsmassnahmen unverzichtbar. Vor allem gilt es, die individuelle Sicherheitsphilosophie des jeweiligen Unternehmens auf die objektiven Anforderungen und Gegebenheiten im Praxiseinsatz vor Ort abzustimmen. Dabei sind folgende Faktoren zentral:
Produkt, das verarbeitet wird Für die Auswahl des richtigen Explosionsschutzkonzepts sind die produktspezifischen Eigenschaften des Schüttguts massgebend. Bei explosionsfähigen Schüttgütern wie Holz und Getreide eignet sich einerseits ein Schutzkonzept sowohl aus aktiven Explosionsschutzsystemen, die mittels dynamischer Druckdetektion bei Bedarf die Ausschüttung eines Löschmittels im Inneren des Prozesses aktivieren, als auch aus passiven Systemen wie Berstscheiben oder Ventilen zur flammenlosen Druckentlastung. Bei chemischen Substanzen ist manchmal jedoch Vorsicht geboten: Enthalten diese toxische Stoffe, dürfen Explosionen nicht nach aussen in die Umgebung abgeleitet werden, wie es bei passiven Lösungen der Fall ist. Für diesen Fall sind ausschliesslich aktive Explosionsschutzsysteme geboten.
Verwendungszweck des Produkts Ausser den produktspezifischen Eigenschaften ist der jeweilige Verwendungszweck des Schüttguts entscheidend. Ein Beispiel: Die Produktion von Milchpulver für Säuglinge und Kälber verläuft in vergleichbaren Prozessschritten. Die Nahrungsmittelproduktion für Säuglinge unterliegt jedoch viel strengeren hygienischen Auflagen, denen die verwendeten Explosionsschutztechnologien gerecht werden müssen. Hier eignen sich spezielle Ventile zur flammenlosen Druckentlastung, die aufgrund ihrer eigens dafür konzipierten Sitzkonstruktion nicht mehr mit dem Produkt im Prozess in Berührung kommen. Auf diese Weise erfüllen sie die hohen Anforderungen an hygienische Prozesse in der Lebensmittelindustrie.
Produktionsumgebung
schutzkonzepts unbedingt zu beachten: Wenn beispielsweise Berstscheiben zur Druckentlastung eingesetzt werden, muss die Explosion ausserhalb von Gebäuden an einer gefahrlosen Stelle abgeleitet werden. Befindet sich der zu schützende Behälter innerhalb eines Gebäudes, erfolgt die Entlastung über Kanäle, die nach draussen führen. Falls die räumlichen Gegebenheiten eine Entlastung ins Freie jedoch nicht zulassen, müssen Ventile zur flammenlosen Druckentlastung verwendet werden, denn Berstscheiben stellen in Innenräumen eine Gefahr für Mitarbeiter und Anlagen dar.
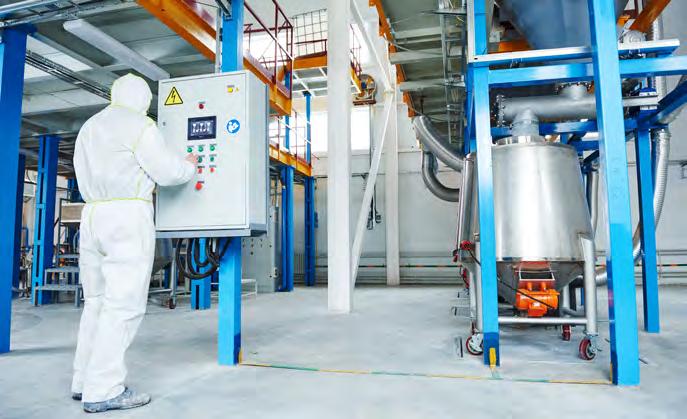
Änderungen an Bestandsanlagen Jeder Betreiber einer explosionsgefährdeten Anlage ist vor der Inbetriebnahme gemäss den Atex-Richtlinien dazu verpflichtet, ein Explosionsschutzdokument zu erstellen. Werden Modifizierungen an der Anlage sowie Änderungen an Arbeitsmitteln und -abläufen vorgenommen, betrifft dies auch das Explosionsschutzdokument – es muss entsprechend angepasst werden. Das Dokument erfasst unter anderem die Beurteilung der Explosionsrisiken sowie die getroffenen Schutzmassnahmen, durch die das Risiko minimiert wird. Doch aufgepasst: Sobald eine neue Anlage gebaut, eine existierende Anlage ausser Betrieb genommen oder zwei Anlagen miteinander verbunden werden, muss eine erneute Risikobeurteilung erfolgen. Dies hat zur Folge, dass das Explosionsschutzdokument aktualisiert und somit auch das
Nicht nur die Produkteigenschaften, sondern auch die Gegebenheiten vor Ort müssen genaustens bekannt sein. Das gehört zum Schutzkonzept dazu.
Explosionsschutzkonzept angepasst werden müssen, um weiterhin das Maximum an Sicherheit zu gewährleisten.
Klare und vertrauensvolle Kommunikation «Neben den produktspezifischen Eigenschaften – allen voran den Explosionskenndaten und den technischen Faktoren – spielt im Explosionsschutz die Kommu nikation zwischen dem Anlagenbetreiber, dem Anlagenbauer sowie dem Explosionsschutzanbieter eine zentrale Rolle», erklärt Markus Häseli, Director of Sales Europe bei IEP Technologies. «Es muss klar sein, welche Produkte in den einzelnen Anlagenabschnitten verarbeitet werden und welche Produktcharakteristika wie bei spielsweise Korngrösse und Feuchtigkeitsgrad jeweils vorliegen. Bei gegebenen verfahrenstechnischen Abläufen gilt es, die Detailkonfiguration der Anlage optimal mit dem angedachten Schutzkonzept abzustimmen und somit ein massgeschneidertes Konzept umzusetzen, das optimale Sicherheit gewährleistet.»
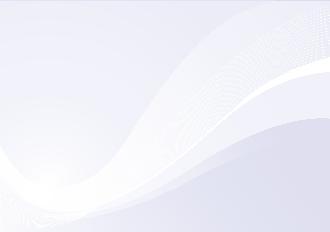
Kontakt Markus Häseli IEP Technologies Kaiserswerther Strasse 85c D-40878 Ratingen +49 2102 5889 221 markus.haeseli@hoerbiger.com www.ieptechnologies.com
7. und 8. Oktober 2020 | Expo Beaulieu Lausanne | ilmac.ch
Plateforme pour la chimie, la pharmacie et la biotechnologie
Für die französischsprachige Schweiz
Partner
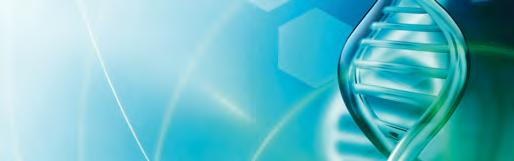
Teilnahme sichern: ilmac.ch/anmelden
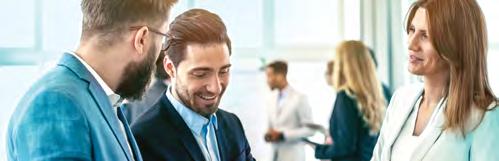