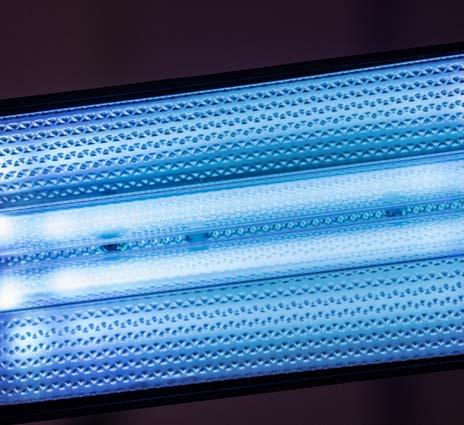
6 minute read
MESSEN/PRÜFEN/QS
UV-C-Technik
Kunststoffmaterialien unter der Lupe
Advertisement
UL, ein führendes Unternehmen im Bereich der Sicherheitswissenschaften, gibt bekannt, dass das UL Labor in Carugate, Italien, jetzt Kunststoffmaterialien auf ihre Eignung im Zusammenhang mit UV-C-Licht testen und verifizieren kann.
Das UL-Labor in Carugate ist seit kurzem gemäss der internationalen Norm IEC 60335-1 Anhang T zertifiziert. Die Fachleute von UL können nun auch an diesem Standort Alterungstests an ausgewählten Kunststoffmaterialien durchführen, um jede Veränderung der Materialeigenschaften durch die Einwirkung von UV-C-Strahlung zu überprüfen. Auf diese Weise wird verifiziert, ob durch die Einwirkung von UVC-Licht die elektrischen oder mechanischen Eigenschaften des Materials sich nicht verändern und dieses sicher verwendet werden kann.
UV-C im Kampf gegen Covid-19
Aufgrund der desinfizierenden Eigenschaften von UV-C-Strahlung setzen immer mehr Unternehmen und Einrichtungen UV-C gegen Coronaviren ein. Mehrere auf der UV-C-Technologie basierende Systeme wurden bereits zur Desinfektion von Oberflächen und Umgebungen in Krankenhäusern und an öffentlichen Plätzen eingesetzt. Nun, da die Desinfektionswirkung gegen Coronaviren wie SARS-CoV-2 durch mehrere Forschungsstudien nachgewiesen
Bild: UL International Germany GmbH
Unter Einfluss von UV-C-Strahlung können sich die mechanischen Eigenschaften von Kunststoffprodukten verändern.
wurde, hat die Zahl der Produkte, die UVC-Licht verwenden, stark zugenommen. Das sind zum Beispiel: UV-Desinfektionsroboter, tragbare oder stationäre Luftfiltergeräte, Wasseraufbereitungsgeräte, tragbare UV-Sterilisatoren und UV-C-Leuchten. Auch wenn UV-C-Licht zur Bekämpfung von Coronaviren beitragen kann, stellt es bei unsachgemässer Verwendung auch Gesundheitsrisiken dar. Eine Person kann Schäden an Augen, Haut und sogar an der Lunge erleiden. Ähnlich wie die schädliche Wirkung von UV-C auf den Menschen, wirkt sich UV-C auch auf Kunststoffe aus. Unter Einfluss von UV-C-Strahlung können Kunststoffprodukte eine sichtbare Farbveränderung auf der Oberfläche zeigen oder das Material kann verspröden. Technisch gesehen, verursacht UV-Strahlung einen photooxidativen Abbau, der zu einem Bruch der Polymerketten und einer Verschlechterung der mechanischen Eigenschaften führt. Darüber hinaus kann Kunststoff, der durch UV-C geschädigt wurde, schnell seine elektrischen und mechanischen Eigenschaften verlieren. Bei einigen Kunststoffen kann eine UV-C- Schädigung zum vollständigen Versagen der Komponenten führen. Davide Atzeni, Operations Manager von UL, betont: «Es gibt zwar Beweise dafür, dass UV-C-Licht zur Bekämpfung von Coronaviren beitragen kann, aber es ist auch wichtig, die langfristige Sicherheit von Produkten zu berücksichtigen, die kontinuierlich UV-CStrahlung ausgesetzt sind.
Kontakt UL GmbH in Switzerland https://switzerland.ul.com
Machen Sie den richtigen Zug!
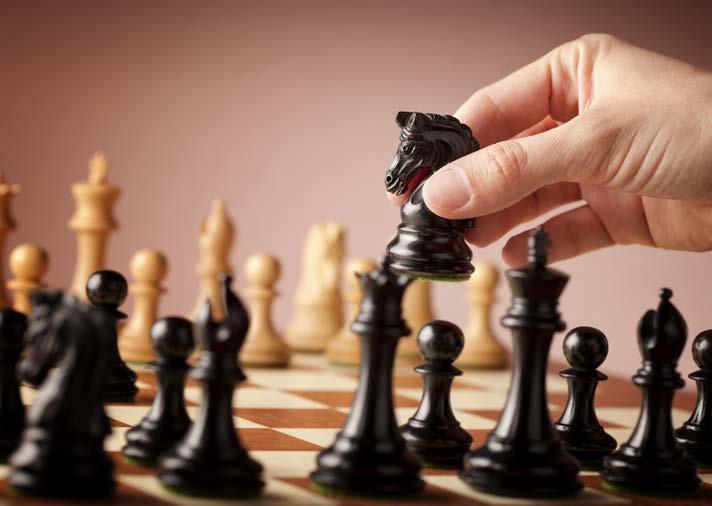
Erfolgreich werben mit der KunststoffXtra.

KUNSTSTOFF XTRA
+41 (0)56 619 52 52 · info@sigimedia.ch
„SCHLIESSKRAFTERFASSUNG PER SENSORMATE APP IM BLICK HOLMDEHNUNGSMESSUNG MIT QE1008-W“
EASY SETUP MOBILE FIRST ACCURATE SYSTEM
Tel: +41 (0) 52 523 25 00 info@sensormate.ch www.sensormate.ch
Lebensdauer von Kunststoffen vorhersagen
Kunststoffe haben Stress mit ihrer Umwelt: Wechselnde Temperaturen, Sonnenstrahlung, Feuchte, chemische Substanzen und mechanische Belastungen setzen ihnen zu und verändern die Materialeigenschaften.
Um die Risiken beim Einsatz neuer Materialien oder bei geänderten Betriebsbedingungen zu minimieren, sind belastbare Aussagen zur Lebensdauer erforderlich. Voraussetzung hierfür sind neben Prüfmethoden, die Schädigungen frühzeitig zu erkennen, geeignete Alterungs- und Versagensmodelle sowie anwendungsrelevante Schadenskriterien. Um die Material- und Bauteilentwicklung zu beschleunigen, ist es zudem von Vorteil, die Dauer der Prüfzyklen, der Klimalagerung oder der Laborbewitterung zu verkürzen. Forscherteams aus dem Bereich Kunststoffe des Fraunhofer-Instituts für Betriebsfestigkeit und Systemzuverlässigkeit LBF entwickeln massgeschneiderte Prüfmethoden und koppeln diese mit Modellierungssoftware zur Lebensdauervorhersage für komplexe Einsatzszenarien. Das Resultat sind kürzere Entwicklungszeiten und ein verringertes Ausfallrisiko im späteren Einsatz. Um die Betriebssicherheit von Kunststoffbauteilen zu garantieren, sind belastbare Aussagen zur Lebensdauer erforderlich, die den konkreten Anwendungsfall so gut wie möglich widerspiegeln müssen. Beispiele sind Kunststoffe und polymerbasierte Beschichtungsmaterialien im Aussenbereich, Bauteile unter stark wechselnden thermischen und mechanischen Lasten oder Druckbehälter für organische Flüssigkeiten bei hohen Temperaturen. Besonders wichtig ist eine zuverlässige Lebensdauervorhersage für sicherheitsrelevante Kunststoffanwendungen wie Gefahrstoffbehälter, tragende Bauteile oder Injektionsdübel für lasttragende Befestigungen.
Für die Material- und Produktentwicklung sowie zur Verringerung der Versagenswahrscheinlichkeit im Einsatz sind zeit-

Lebensdauervorhersage für vorgegebene Lastszenarien durch Kopplung von Experiment und Modellierung.
und kostenaufwändige Tests erforderlich. Der Beschleunigung solcher Versuche durch erhöhte Temperaturen, Umgebungsfeuchte, Bestrahlungsstärke oder kürzere Prüfzyklen sind Grenzen gesetzt. Noch schwieriger ist es, Alterung und Versagen für neue Betriebszyklen oder für den Einsatz unter veränderten Umgebungsbedingungen vorherzusagen. Im Bereich Kunststoffe des Fraunhofer LBF arbeiten interdisziplinäre Teams eng zusammen. Ziel sind optimierte Prüfverfahren und Software-Tools zur Lebensdauervorhersage für komplexe Einsatzszenarien. Indem sie Alterungsexperimente und Modellierung koppeln, können die Wissenschaftlerinnen und Wissenschaftler des Fraunhofer LBF Lebensdauer und Versagensrisiko für vorgegebene Einsatzfälle besser abschätzen. Durch Superposition von aufeinanderfolgenden Temperatur-, Feuchte-, Bestrahlungs- und mechanischen Lasten können sie nahezu beliebige Szenarien nachstellen. Als Eingangsgrössen dienen dabei zeitaufgelöste Messdaten für verschiedene Betriebszustände, Wetterdaten oder hypothetische Einsatzszenarien. Kürzere Entwicklungszeiten und verringertes Ausfallrisiko
Am Fraunhofer LBF steht hierfür eine Toolbox bestehend aus Klimalagerung und Bewitterung, vielfältigen Mess- und Prüfmethoden, einer breit gefächerten chemischen Analytik und anpassbaren Alterungs- und Lebensdauermodellen zur Verfügung. Die Vorgehensweise lässt sich direkt mit der Bauteilauslegung mit FEMethoden koppeln. Gemeinsam mit Industriepartnern passen die Darmstädter Forschenden diese an die jeweilige Fragestellung an und begleiten die Überführung in bestehende Abläufe und vorhandene Infrastruktur. Das Resultat sind anwendungsbezogene Prüfvorschriften, kürzere Entwicklungszeiten und ein verringertes Ausfallrisiko im späteren Einsatz.
Kontakt Fraunhofer-Institut für Betriebsfestigkeit und Systemzuverlässigkeit LBF Schlossgartenstrasse 6 D-64289 Darmstadt +49 6151 705-0 info(@lbf.fraunhofer.de www.lbf.fraunhofer.de n
Forscherteam entwickelt mathematisches Modell
Ermüdungsverhalten von Faserverbunden
Faserverbundmaterialien werden aufgrund ihres Gewichtsvorteils in immer mehr Branchen eingesetzt, etwa in der Automobilfertigung. Bislang gibt es aber noch keine zuverlässigen Prognoseverfahren für die Lebensdauer solcher Bauteile, so dass diese aus Sicherheitsgründen oftmals überdimensioniert werden. In einem Forschungsprojekt haben die TH Köln und die Structural Engineering GmbH & Co. KG jetzt ein allgemeingültiges Berechnungsmodell entwickelt.
«Faserverbundbauteile kommen häufig an Stellen zum Einsatz, an denen sie zyklischen Belastungen ausgesetzt sind. Es gibt zwar bereits einfache Richtlinien, die eine konservative Abschätzung derartiger Bauteile ermöglichen, eine umfassende Lebensdauervorhersage, die für jede Art der Faserverbundarchitektur Gültigkeit hat, ist jedoch heute noch nicht möglich», erläutert Projektleiter Prof. Dr. Jochen Blaurock vom Institut für Fahrzeugtechnik der TH Köln. Die bislang verwendeten Richtlinien beruhen beispielsweise auf der maximal zulässigen Dehnung des Materials oder auf Ermüdungsdauermodellen von metallischen Werkstoffen. Dies wird aber den spezifischen Eigenarten von und den komplexen mechanischen Vorgängen in Faserverbunden häufig nicht gerecht. Deshalb kann deren Lebensdauer nur durch experimentelle Untersuchungen ermittelt werden, die dann auch nur für das spezifische Bauteil Gültigkeit besitzen.
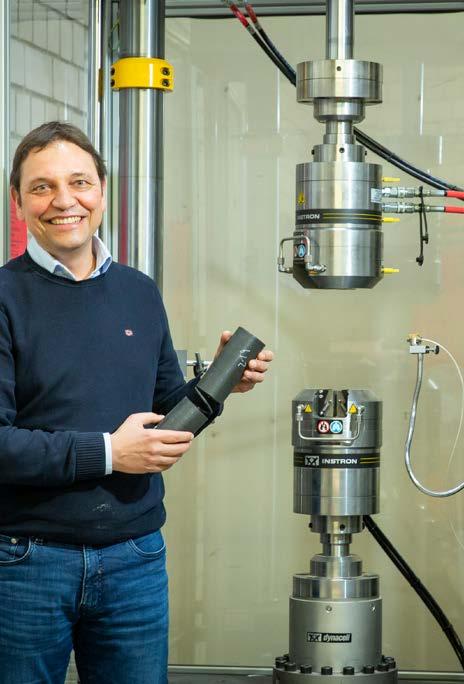
Kritische Zwischenfaserbrüche
Im vorliegenden Forschungsprojekt hat Marc Möller im Rahmen seiner Promotion ein mathematisches Verfahren entwickelt, das auf Grundlage einiger weniger Versuche eine Lebensdauerberechnung für beliebig konstruierte Faserverbundbauteile
Bild: TH Köln die Wirkung auf den Gesamtverbund. Diese Rechnung wird für mehrere Millionen Lastzyklen wiederholt und der dabei entstehende Schadensfortschritt in jeder Schicht und im Bauteil insgesamt errechnet», so Blaurock. Auf diese Weise werden insbesondere die kritischen Zwischenfaserbrüche prognostiziert, die schnell zum Versagen des gesamten Bauteils führen können.
Prof. Dr. Jochen Blaurock vor dem Hydropulser
ermöglicht. «Grundlage hierzu ist die sogenannte restfestigkeitsbasierte Ermüdungsbruchkurve für mehrachsige und nichtproportionale Beanspruchungen, welche auf Materialkennwerten basiert, die in den Einzelschichten ermittelt werden», erläutert Möller. «Das Modell ermittelt den Schaden, der durch eine einmalige Belastung – einen sogenannten Lastzyklus – in jeder einzelnen Schicht entsteht und darüber hinaus Das Modell weiterentwickeln
Das berechnete Versagensverhalten stellte Möller anschliessend im Labor auf die Probe. Die Gelenkwelle eines Sportwagens wurde in einem Hydropulser zeitgleich Zug-, Druck- und Torsionsbelastungen ausgesetzt und dabei bis zu 40 Mal pro Sekunde zehn Tonnen Gewicht ausgesetzt. «Das Experiment und die anschliessende Untersuchung des zerstörten Bauteils haben gezeigt, dass die mathematische Vorhersage mit dem eintretenden Schaden gut übereinstimmte», so Blaurock. In einem Folgeprojekt soll jetzt das erarbeitete Modell für stochastische Beanspruchungen weiterentwickelt werden.
Kontakt Technische Hochschule Köln Claudiusstrasse 1, D-50678 Köln +49 221-8275-0, www.th-koeln.de n
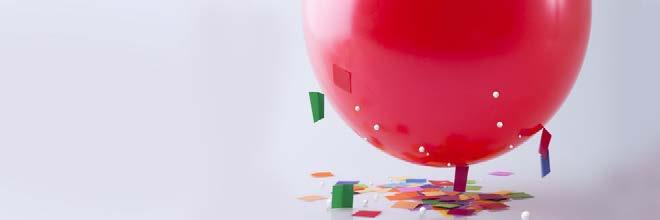
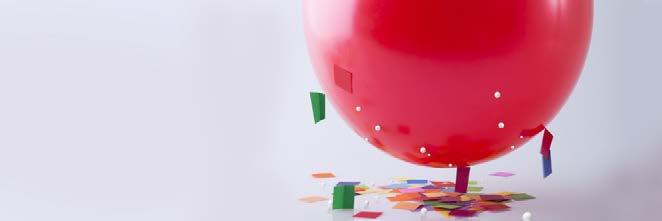

HAUG BIEL AG
Johann-Renfer-Str. 60
Postfach CH-2500 Biel/Bienne 6 Tel.: +41 (0) 32 344 96 96 Fax: +41 (0) 32 344 96 97 info@haug.swiss www.haug.swiss