
24 minute read
VERARBEITUNG
Baugruppen für Beatmungsgeräte
Advertisement
Bei Beatmungsgeräten unterscheidet man je nach Einsatzbereich verschiedene Typen. Die bekanntesten Modelle sind dabei Notfall- oder Transportrespiratoren, Heimrespiratoren und Intensivrespiratoren. Besonders den für die Langzeitbehandlung gefertigten Intensivrespiratoren kommt während der Corona-Krise eine besondere Bedeutung zu. Sie wurden entsprechend in sehr hohem Masse nachgefragt.
Die Bundesregierung erteilte verschiedenen deutschen Herstellern den Auftrag zum Bau von insgesamt 20000 Beatmungsgeräten, um eine ausreichende Versorgung aller Notfallpatienten sicherzustellen. Die hohe Stückzahl und die Dringlichkeit der Anfrage brachten dabei sowohl die Hersteller als auch die Zulieferfirmen an ihre Kapazitätsgrenzen. Um qualitativ hochwertige Bauteile zu erhalten, beauftragten die Medizingerätehersteller erfahrene deutsche Lieferanten mit deren Produktion. Auch die zur Geiger Gruppe gehörende Reiter HG Geiger Kunststofftechnik GmbH in Hilpoltstein qualifizierte sich durch 25 Jahre Erfahrung im Bereich Spritzgussteile und Systembaugruppen für Beatmungs- und Anästhesiegeräte als Systemlieferant, da sie innerhalb kürzester Zeit die geforderten Mengen produzieren konnte.
Anstieg der Nachfrage
«Mit dem Grossauftrag der Bundesregierung für die möglichst schnelle Lieferung von Intensivrespiratoren zur Bewältigung der Corona-Krise stieg auch bei uns die Nachfrage nach entsprechenden Bauteilen wie beispielsweise Adaptern zur Atemgasaufbereitung sprunghaft an», erklärt Eva Söhnlein, Geschäftsleitung der Reiter HG Geiger Kunststofftechnik GmbH. «Im Vergleich zum Vorjahr verzeichneten wir bei einzelnen Bauteilen eine Steigerung von bis zu 400 Prozent.» Die Produktionszahlen wurden innerhalb weniger Tage gesteigert, um die Nachfrage zu bewältigen. Reiter verfügt dabei über eine Expertise in verschiedenen Produktbereichen, sodass unterschiedliche Bauteile angefragt wurden. Das Portfolio des fränkischen Unternehmens reicht dabei von Temperatur-
Das Portfolio reicht von Temperaturmesstüllen und Frischgasmesstüllen, über Füll- und Anschlussadapter zur Vermeidung von Verwechslungen von Anästhesiemitteln bis hin zu komplexen Ventilbaugruppen zur Atemgassteuerung.
messtüllen und Frischgasmesstüllen, die in der Sensortechnik zur Überwachung des Patienten in der Anästhesiephase benötigt werden, über Füll- und Anschlussadapter zur Vermeidung von Verwechslungen von Anästhesiemitteln bis hin zu komplexen Ventilbaugruppen zur Atemgassteuerung. «Unsere Komponenten werden auch zur Erfassung von Messwerten sowie der Steuerung und Regelung von Atemluftströmungen eingesetzt, die speziell bei Corona-Patienten permanent überwacht werden müssen», berichtet Söhnlein. «Dank unserer langjährigen Erfahrung in diesem Bereich waren wir in der Lage, die Produktion der filigranen Bauteile in kürzester Zeit auf das notwendige Mass zu steigern, um die Herstellung von Intensivrespiratoren für Corona-Patienten durch unsere Auftraggeber so gut wie möglich zu unterstützen. Wichtig war hierbei auch eine gut funktionierende Lieferkette. Bauteile wie Dichtungen oder Federn werden von uns zugekauft. Durch die jahrelange gute Zusammenarbeit mit unseren Lieferanten war es uns schnell möglich in dieser aussergewöhnlichen Situation die Fertigungszahlen dem Bedarf anzupassen.»
Hohe Qualität auch unter Zeitdruck
Hinter der Herstellung der Baugruppen steht allerdings ein komplexer Prozess. So wird für jedes Bauteil ein eigens Spritzgiesswerkzeug benötigt und die ideale Fertigungsstrategie muss frühzeitig festgelegt werden. Hier gibt es zahlreiche Einflussfaktoren wie den Werkstoff, das Einsatzgebiet oder die notwendigen Schritte zur Weiterbearbeitung und Fertigstellung der Baugruppe. Eine besondere Herausforderung

Die Filigranität der Einzelkomponenten sowie die Komplexität der daraus gebildeten Baugruppen machen in weiten Teilen eine manuelle Endfertigung erforderlich.
stellen dabei die komplexen Geometrien und die engen Fertigungstoleranzen dar. Auch die eventuellen Fertigungstoleranzen von zugekauften Komponenten müssen im Vorfeld genau definiert und im Herstellungsprozess ausgeglichen werden. Darüber hinaus kommen bei der Produktion je nach Einsatzgebiet der Bauteile hochanspruchsvolle Kunststoffe mit bestimmten Materialeigenschaften zum Einsatz: Die Palette reicht von Hochtemperaturkunststoffen wie Polyetheretherketon (PEEK), das auch bei hohen Temperaturen bis zu 260 Grad Celsius physische Eigenschaften wie Biegefestigkeit und Zugfestigkeit aufweist, bis hin zu Polyphenylensulfid (PPS), das eine hohe chemische Beständigkeit besitzt. Weitere Werkstoffe sind Polyarylsulfone (PSU) und Polyphenylsulfon (PPSU), die über eine hohe Hydrolysestabilität verfügen und somit eine Sterilisation der Bauteile im Autoklav ermöglichen.
Automation und Handarbeit
«Trotz des enormen Drucks, der durch die hohe Nachfrage und die Knappheit an Bestandsgeräten in den Krankenhäusern ausgelöst wurde, mussten die Produkte höchsten Qualitätsanforderungen entsprechen», erklärt Söhnlein. Um ein reibungsloses Funktionieren der Komponenten sicherzustellen, gelten auch für alle nachgelagerten Verarbeitungsschritte wie Ultraschall- und Laserschweissen, sowie mechanische Bearbeitungen hohe Qualitätsstandards. Die Filigranität der Einzelkomponenten sowie die Komplexität der daraus gebildeten Baugruppen macht in weiten Teilen eine manuelle Endfertigung erforderlich. Dies betrifft sowohl die Vormontage kleiner Baugruppen als auch die Montage ganzer Systembaugruppen. Die hohen Qualitätsanforderungen an die Produkte, die auch bereits vor der CoronaKrise gültig waren, machen ausserdem eine lückenlos dokumentierte Funktionsprüfung von 100 Prozent der produzierten Komponenten mittels komplexer Prüfautomaten notwendig. Sowohl die Assemblage als auch die Qualitätskontrolle finden dabei im Sauberraum statt, um die technische Sauberkeit der Produkte nach DIN ISO 16232 sicherzustellen. «Es ist gerade in der Endmontage wichtig die richtige Balance zwischen Automatisierung und manuellen Arbeitsschritten zu finden. Wir haben Assemblage und Werkstückprüfung in einem Arbeitsschritt zusammengelegt, um zu vermeiden, dass Fertigungslose von Baugruppen bei der Endabnahme übersehen werden. Auf diese Weise können wir den hohen Qualitätsstandard unserer Produkte unter anderem für die Herstellung von Intensivrespiratoren sicherstellen», resümiert Söhnlein.
Kontakt Reiter HG Geiger Kunststofftechnik GmbH An der Autobahn L5 D-91161 Hilpoltstein +49 9174 971080 kontakt@geiger-gruppe.de www.geiger-gruppe.de n
In der Tri-Extrusion fertigt SLS innovative Kunststoffprofile aus drei Komponenten
Nahtloser Verbund mit Umweltvorteil
Mit der Tri-Extrusion bietet SLS einen erweiterten Spielraum für die Realisierung ressourcenschonender und hochfunktioneller Profilsysteme aus Kunststoff. Diese Variante der Extrusionstechnik führt stets drei Komponenten mit unterschiedlichen Eigenschaften nahtlos zu einer Verbundlösung zusammen.
Manfred Stiller ¹
Mit der Tri- oder Dreifach-Extrusion nutzt der Kunststoffverarbeiter SLS eine der Königsdisziplinen für die Herstellung sowohl nachhaltiger als auch intelligenter Profilsysteme. Seinen Kunden ebnet das Dahner Unternehmen damit unter anderem den Weg zur Realisierung von Verbundlösungen mit einer erhöhten Funktionalität, mit einer verbesserten Ökobilanz, mit attraktiven Farbwechseln und mit unterschiedlichen Oberflächenstrukturen. Spezialisiert hat sich SLS dabei insbesondere auf die Tri-Extrusion verschiedener PVC-Sorten. «Von der Mono- und Co-Extrusion bis hin zur PostCo- und Tri-Extrusion nutzen wir in unserem Werk aktuell mehrere TechnologieVarianten. Werkstofftechnisch richten wir in der Tri-Extrusion den Fokus auf die Verarbeitung von Hart- und Weich-PVC sowie PVC-Blends und -Regenerat. Hier sehen wir das grösste Potenzial für die Serienfertigung innovativer und ressourcenschonender Profilprodukte», erläutert SLS-Geschäftsführer Jan Leibrock.
Viele Eigenschaften kombinierbar
Durch den Einsatz der verschiedenen PVCSorten kann SLS in der Tri-Extrusion hohe technische Anforderungen umsetzen und anspruchsvolle Kundenwünsche erfüllen. So lassen sich in diesem Verfahren nicht nur langlebige Kunststoffprofile realisieren, bei denen matte und glänzende sowie transparente und verschiedenfarbige Oberflächenbereiche nebeneinander liegen, sondern auch hochfunktionelle Verbundlösungen, bei denen sich harte und
¹ Manfred Stiller, Freier Fachjournalist, Darmstadt
Bilder: SLS Kunststoffverarbeitung Multifunktionalität aus einem Stück: Tri-Extrudiertes Kunststoffprofil mit grauem Innenkern, weisser Deckschicht und Dichtlippe.

weiche Bereiche abwechseln. Von grosser Bedeutung für die ökologische Optimierung der Profile ist zudem die Möglichkeit, in erheblichem Umfang rezykliertes und regeneriertes Kunststoffgranulat einzusetzen. Leibrock erklärt dazu: «Unter dem Gesichtspunkt der Nachhaltigkeit lohnt sich der Einsatz von Regenerat vor allem bei Profilen mit grossen Querschnitten. In der Tri-Extrusion können wir hier den gesamten Innenkern aus Regenerat fertigen, während neues Granulat den Deckschichten vorbehalten bleibt. Im gleichen Prozess erhalten die Profile dann oft noch weiche Dichtlippen.» Anspruchsvolles Verfahren Optisch zeichnen sich tri-extrudierte Profile dadurch aus, dass sie keine Nahtstellen oder Verbindungsgrate aufweisen. Abgesehen von den funktionellen oder umweltschonenden Aspekten erfüllen sie also immer auch hohe Ansprüche an das Design der Oberflächen. Aufgrund der technologischen Komplexität versteht sich allerdings nicht jeder Kunststoffverarbeiter auf diese Variante der Extrusionstechnik. Charakteristisch für das Verfahren ist bei-
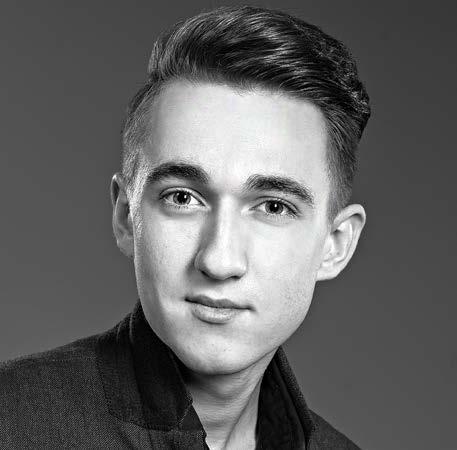
spielsweise der Einsatz von drei einzelnen
SLS-Geschäftsführer Jan Leibrock: «Hinsichtlich der Nachhaltigkeit lohnt sich die Tri-Extrusion vor allem für Profile mit grossen Querschnitten. Denn hier lässt sich der gesamte Innenkern aus Regenerat fertigen, während neues Granulat den Deckschichten vorbehalten bleibt.»

Einwandfreie und konstante Dosierungen
Die Tri-Extrusion stellt sowohl erhöhte Anforderungen an den Werkzeugbau als auch an die Komplexität der Produktionstechnik. Das Bild zeigt einen Beispritz-Extruder mit Befülltrichter.
Extrudern, in denen die drei Komponenten vor ihrer Zusammenführung im Werkzeug getrennt voneinander mit hoher Genauigkeit temperiert werden. Viel Know-how erfordert zudem die Auslegung der Extrusionswerkzeuge, die eine gleiche und homogene Austrittsgeschwindigkeit der verschiedenen Materialien gewährleisten müssen. Nicht zuletzt ist darauf zu achten, dass sich die drei Komponenten optimal miteinander zu einer werkstofftechnischen Einheit verbinden. Das Ganze ist also eine Sache für echte Spezialisten. «In der Tri-Extrusion profitieren wir inzwischen von etlichen Jahren praktischer Erfahrung und unserem über die Jahrzehnte gewachsenen Know-how aus der Co- und Post-CoExtrusion», betont Leibrock.
Material-Alternativen möglich
SLS legt den Schwerpunkt bei der Tri-Extrusion zwar auf die Verarbeitung von PVC-Sorten, da dieser Werkstoff aufgrund seiner Belastbarkeit, Formstabilität und Lebensdauer für viele Profile eine ideale Lösung darstellt. Das Unternehmen ist aber jederzeit in der Lage, auch auf andere technische Kunststoffe umzusteigen. Insgesamt verarbeitet SLS derzeit auf 30 Extrusionslinien neben H-PVC, W-PVC beispielsweise ASA, PE, PP, PS, POM, SB und ABS sowie eine Reihe verschiedener Blends und Schäume. Übrigens: Ab einer bestimmten Losgrösse kann sich die Tri-Extrusion gerade für die Fertigung grosser Kunststoffprofile mit voluminösen Innenräumen als überraschend wirtschaftlich erweisen. Denn hierbei wirkt sich der hohe Anteil an einsetzbarem Regenerat als kostensenkendes Momentum besonders stark aus.
Kontakt SLS Kunststoffverarbeitungs GmbH & Co. KG Industriestrasse 11 D-66994 Dahn +49 6391 92 43-0 info@sls-kunststoffprofile.de www.sls-kunststoffprofile.de

SPECTROPLUS
SPECTROPLUS – ein Dosiersystem für sämtliche Extrusions- und Compoundieraufgaben
Egal ob Granulat, Mahlgut, Pulver, Flüssigkeiten oder Flakes – motan-colortronic stellt auf der diesjährigen K-Messe ein neues Dosier- und Mischgerät vor, das sich an die unterschiedlichsten Dosieranforderungen anpassen lässt. Speziell entwickelt für den Extrusionund Compoundingbereich gewährleistet das SPECTROPLUS einwandfreie und konstante Dosierungen für kontinuierliche Prozesse.
motan-colortronic ag info@motan-colortronic.ch - Tel. +41 62 889 29 29
www.motan-colortronic.com
Die Blende wird zum Human Machine Interface
Kunststoffbauteile für Designblenden im Automobilbau oder bei Haushaltsgeräten sind bereits seit mehreren Jahren weit verbreitet. Allerdings reicht heutzutage eine Auslegung der Bauteile unter optischen und haptischen Aspekten häufig nicht aus, um für die Kunden überzeugende Lösungen präsentieren zu können. Mit der zunehmenden Digitalisierung steigen die Anforderungen in Bezug auf Funktionsintegration vor allem im Bereich der Elektronik. Die Blende wird zum Human Machine Interface (HMI).
Curdin Wick ¹
Bei solchen Blenden findet aktuell eine Verschmelzung von Bedienfläche, Designfläche und Funktionsfläche statt. Das heisst, es resultieren Bedienblenden mit einer glatten hochwertigen Oberfläche ohne Unterbrüche, die sich im ausgeschalteten Zustand möglichst unauffällig, z. B. als einheitliche schwarze Oberfläche, präsentieren (Deadfront-Effekt). Solche Produkte kommen heutzutage grösstenteils aus Asien, wo sie in Handarbeit montiert werden. Die Schwierigkeit für die Unternehmen in Europa besteht darin, die stetig zunehmenden Anforderungen mit wirtschaftlich konkurrenzfähigen Produkten abdecken zu können. Das Hinterspritzen von funktionalisierten Kunststofffolien kann hier eine Lösung bringen.
Einsatz der Technologie am Standort Schweiz
Die Umsetzung einer solchen Technologie für den Standort Schweiz wurde mit vier Industriepartnern unter Mitfinanzierung der Innosuisse, der Schweizerischen Agentur für Innovationsförderung, untersucht. Am Standort Schweiz ist es wichtig, nicht nur den Standardfertigungsprozess zu beherrschen, sondern auch die Herstellung anspruchsvoller Bauteile in Sonderverfahren. Der Spritzgiessverarbeiter A. & J. Stöckli AG, welcher heute bereits erfolgreich Produkte mit IMD-Technologie umsetzt, ist neben zwei weiteren Schweizer Firmen Hauptumsetzungspartner im Pro-
¹ Curdin Wick, Fachbereichsleiter Spritzgiessen, IWK der Ostschweizer Fachhochschule Bild 1: Rückseite von Versuchsblenden mit unterschiedlicher Dekoration und Sensorfoliengrössen (kleine Sensorfolie mit verstecktem Tail (grün))
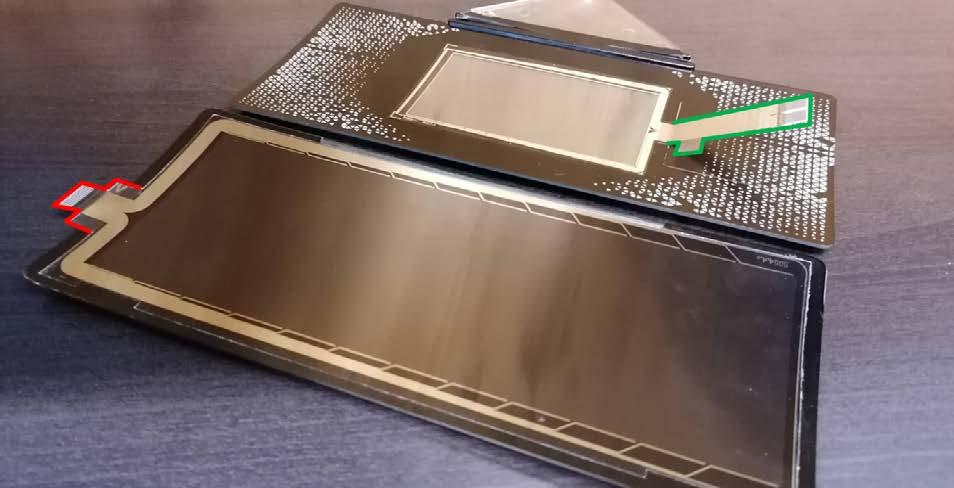
jekt. Dabei wird auf Folien und bestehendes Know-how des Projektpartners Kurz Prägefolien AG zurückgegriffen. Bei dieser Technologie werden ein IMD- und ein IML-Prozess kombiniert, was bei der Firma Stöckli in der speziell dafür ausgelegten Fertigungszelle einwandfrei umgesetzt wurde. Die Dekoration der Blende erfolgt durch die sogenannte IMD-Technologie (In-Mold Decoration). Dabei wird während des Spritzgiessprozesses ein mehrschichtiges Lackpaket im kundenspezifischen Design auf das Kunststoffbauteil übertragen. Die dazu notwendige IMDFolie der Firma Kurz wird über ein Folienvorschubgerät auf der beweglichen Werkzeugseite nachgeführt. Das jeweilige Einzelbilddekor wird mit einem Klemmrahmen fixiert und anschliessend die Luft zwischen Folie und Kavität evakuiert. Gleichzeitig wird auf der festen Werkzeugseite eine Sensorfolie, sprich eine mit Leiterbahnen bedruckte IML-Folie, ins Werkzeug eingelegt (In-Mold Labeling). Diese Sensorfolien werden durch die Firma PolyIC, ein Tochterunternehmen der Firma Kurz, hergestellt. Anschliessend erfolgt das Einspritzen des Kunststoffs zwischen die beiden Folien, wodurch ein funktionalisiertes Bauteil in nur einem Prozessschritt hergestellt werden kann.
Grundlagenuntersuchungen zur Prozesstechnik
Im Rahmen dieses Projektes wurden die Möglichkeiten dieser Technologie aufgezeigt, aber auch die Grenzen hinsichtlich
Bild 2: Versuchsblende an Vitrine montiert in ein- und ausgeschaltetem Zustand
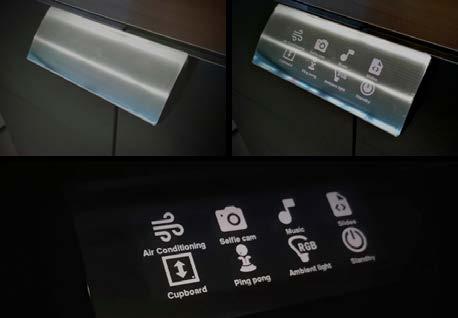
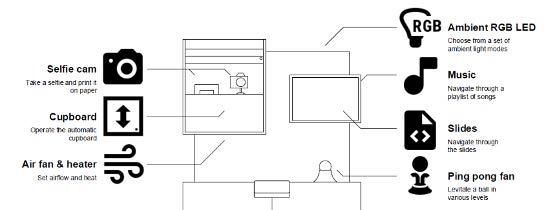
Bild 3: Vitrine mit Features, welche alle über die mittig platzierte Versuchsblende (auf dem Bild ausgeschaltet) bedient werden können.
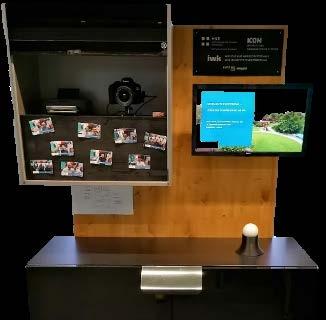
der Gestaltungsmöglichkeiten der Blenden untersucht. Für erste Grundlagenversuche zur Erarbeitung des Prozess-Know-hows wurde ein Werkzeug zur Herstellung einer einfachen Versuchsblende (Bild 1) gebaut. Damit konnten unterschiedlich aufgebaute Transferveredelungsfolien mit verschiedenen Kunststoffmaterialien hinterspritzt und gemäss den Kundenanforderungen getestet werden. Mit dem Spritzgiesswerkzeug für diese Versuchsblende kann die Sensorfolie ins Werkzeug eingelegt und festgehalten werden. Die Konnektierung dieser Folie erfolgt über einen sogenannten Tail. Dieser kann durch eine im Rahmen dieses Projektes entwickelte Technologie im Werkzeug «versteckt» werden und muss nicht mehr wie bis anhin seitlich über das Bauteil und die Werkzeugtrennung ragen.
Entwicklung einer Demonstratorblende
In einem zweiten Schritt wurde eine neue Blende für einen Demonstrator von Grund auf entwickelt. Die sogenannte Demonstratorblende weist eine grössere und stärker verformte Oberfläche auf und soll die Grenzen hinsichtlich der Gestaltungsfreiheit und zulässigen Umformgraden für die Transferveredelungsfolien aufzeigen.
Projektteam IWK der Ostschweizer Fachhochschule ICOM der Ostschweizer Fachhochschule A. & J. Stöckli AG Kurz Prägefolien AG Zusätzlich wurden die verschiedenen Anforderungen der Projektpartner berücksichtigt. So sollen unter anderem multifunktionelle Touchdisplays, möglichst hohe Verformungsgrade von IMD und IML sowie ein Deadfront-Effekt bei ausgeschaltetem Display ermöglicht werden. Die bei der Versuchsblende gewonnenen Erkenntnisse flossen direkt in die Entwicklung der Demonstratorblende ein. In der Demonstratorblende sind diverse Slider, Tasten, hinterleuchtete Dekorationselemente mit Deadfront-Optik und ein Sichtfenster für ein Display integriert. Die Toucherkennung für die verschiedenen Elemente erfolgt über eine einzelne Sensorfolie, weshalb das Display keine zusätzliche Touch-Funktion benötigt. Die Demonstratorblende ist leicht grösser als die Versuchsblende. Die Sensorfolie wird wie bei der Versuchsblende 2D verformt. Das Dekor wird allerdings auf die 3D verformte Bauteilpartie aufgebracht. Die Demonstratorblende wurde abschliessend zu einem funktionalen Demonstrator verbaut, um potenziellen Kunden live zeigen zu können, was für Designideen umsetzbar sind.
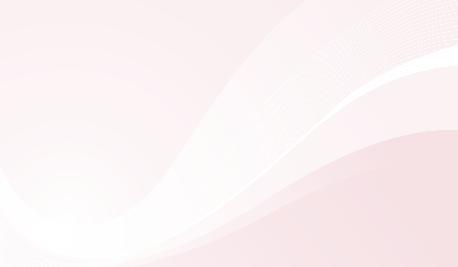
Möglichkeiten für neue Produkte
Mit der Kombination dieser beiden Prozesse ist es möglich, verformte Blenden herzustellen. Das IMD-Verfahren ist für verformte Blenden geeigneter als z.B. Heissprägen. Es resultiert ein wirtschaftlicher, hochautomatisierter Prozess, der für eine Vielzahl verschiedener Anwendungen geeignet ist: – Grossflächige Abdeckungen mit Touchbedienung Dekorelemente durch Hinterleuchten der Transferveredelung Verschiedene Produktelinien (Preisklassen) mit dem gleichen Werkzeug herstellbar. Touchfunktionen können beliebig auf der gesamten Sensorfolie programmiert werden und bei tieferen Preisklassen können die zusätzlichen Funktionen ausgeblendet werden. Ersatz für aktuell verwendete teure Touch-Displays Human Machine Interface allgemein
Vitrine zur Darstellung der Funktionalität
Neben der Umsetzung der Erkenntnisse in einem Demonstrator wurde am IWK zusätzlich eine Vitrine aufgebaut, um das Potenzial der gedruckten Elektronik aufzuzeigen. Zur Veranschaulichung können vielfältige Funktionen über die Versuchsblende angesteuert werden. Der Controller für das Auslesen der Sensorfolie sowie für die Ansteuerung der Funktionen ist komplett vom Institut für Kommunikationssysteme ICOM entwickelt worden. Verbaut ist die Versuchsblende mit einer verspiegelten Transferveredelung inkl. DeadfrontOptik (Bild 2). Zwecks Flexibilität werden alle Symbole hinter der Blende auf einem preiswerten Bildschirm dargestellt. Die gesamte Benutzeroberfläche kann also jederzeit frei angepasst werden.
Kontakt Curdin Wick IWK Institut für Werkstofftechnik und Kunststoffverarbeitung OST Ostschweizer Fachhochschule curdin.wick@ost.ch www.iwk.hsr.ch
Maskenproduktion: Anspruchsvoll, aber nicht neu
Warum LSR die bessere Wahl ist
Das Thema Masken ist in aller Munde. Durch die weltweite Verbreitung des Corona-Virus sind sie ins Rampenlicht gerückt. Doch schon lange davor waren Schutzmasken, Atemmasken, Schlafmasken oder auch Tauchmasken unersetzlich. Warum dabei Flüssig-Silikon eine wichtige Rolle spielt, beschreibt die Rico Group in diesem Artikel.
Blaulichtorganisationen, Krankenhäuser und Forschungseinrichtungen setzen schon lange Schutzmasken ein. Auch in der Privattherapie, etwa bei der Behandlung von Schlafapnoe, gewinnen sie immer mehr an Bedeutung. Oftmals wird dafür ein weiches Flüssig-Silikon (LSR-liquid silicone rubber) eingesetzt, da es für ein besonders angenehmes Tragefühl sorgt. Aber auch die Kombination mit anderen Materialien ist üblich: Das Gehäuse aus Thermoplast, der Mund- und Nasenbereich aus Silikon, mit wechselbaren oder einsetzbaren Filtersystemen, um nur ein paar Beispiele zu nennen. Die Anwendungsgebiete sind vielfältig, die Umsetzungsmöglichkeiten ebenso. Das Material ist ein echter Allrounder und verbindet Biokompatibilität, Allergenfreiheit, Geruchs- und Geschmacksneutralität sowie eine gute Temperaturbeständigkeit (-50 bis +250 Grad Celsius) mit hoher Design-Freiheit und der Realisierbarkeit von komplexen Geometrien und Materialkombinationen.
MehrkomponentenSpritzguss
Flüssig-Silikon kann im 2K- oder Mehrkomponenten-Spritzguss verarbeitet werden. Materialpaarungen, wie z.B. LSR mit LSR (in unterschiedlichen Shore-Härten) oder LSR mit Thermoplasten sind abbildbar. Insbesondere mit High Performance und Engineering Plastics wie PEEK, PPS, PSU, PBT, PA, PMMA, PET und PC gibt es bei Masken gute Erfahrungen, aber auch der Verbund mit Glas, Glasfaser oder Metall ist grundsätzlich möglich. Die hohe Weiterreissfestigkeit, der geringe Druckverformungsrest, das gute Rückstellvermögen, die Möglichkeit das Material beliebig einzufärben oder zu beleuchten
Bild: Rico Group

Der Produktionsprozess für 2K-Masken ist herausfordernd.
wird nur der Vollständigkeit halber erwähnt.
Hauchzarte Gesichtsauflage
Durch spezielle Anforderungen an das Maskendesign und die Funktionalität, ergeben sich immer wieder neue Herausforderungen für den Formenbau und in der Verarbeitung. Der Tragekomfort und die unterschiedlichen Gesichtsformen müssen dabei gleichermassen berücksichtigt werden. Das resultiert im Mund- und Nasenbereich in 3D-Freiformen, die im Werkzeug abgebildet werden. Bei einer reinen Silikon-Maske (1K) gibt es oftmals starke Wandstärkenunterschiede. Sie ist z.B. dick im Funktionsbereich aber zart und weich an den Berührungspunkten im Gesicht. Das ergibt sehr dünne, membranartige Bereiche an der Maske. Auch Texturunterschiede an den Masken machen die Fertigung komplex. Vor allem Materialien mit niedriger Viskosität, wie ein 5-Shore-Material, ist besonders anspruchsvoll im Werkzeugbau und der Produktion. Hier muss insbesondere auf die Wiederholgenauigkeit, einen stabilen Prozess und höchste Qualitätsanforderungen geachtet werden.
Produktionsprozess herausfordernd
Die Produktion von Masken reizt die Grenzen des Planbaren nahezu aus. Bei 3DFreiformen kann der Zusammenfluss des Materials nur schwer berechnet werden. Obwohl die Formgebung und die Entformung durch Simulationen abgedeckt werden, sind es die erfahrenen Anwendungstechniker/innen der Rico Group, die die letzten Meter am Weg zum perfekten Produkt bestimmen. Werden die Teile vollautomatisch produziert, brauchen sie Platz. Nicht nur im Handling bei der Entformung und der Ablage auf dem Förderband, sondern auch im Temperofen und der anschliessenden Verpackung. Die Materialversorgung während der mannlosen Fertigung bei Nacht muss gewährleistet sein. Die Corona-Krise hat gezeigt, dass Masken, die sehr schnell benötigt werden, selten aus Silikon gefertigt sind. Die Herstellung hochwertiger LSR-Masken weist eine längere Entwicklungszeit als bei anderen Materialien auf und die Anforderungen an sauber durchdachte Konzepte sind besonders hoch. Ausschuss muss aufgrund hoher Materialkosten vermieden werden.
Kontakt Rico Elastomere Projecting GmbH Am Thalbach 8 A-4600 Thalheim bei Wels +43 7242 76 460 office@rico.at www.rico.at
Kompakt, flexibel, wirtschaftlich
Anlässlich der virtuellen Messe live e-xperience präsentierte Engel im Oktober die neue Generation seiner vollelektrischen e-mac Spritzgiessmaschinenbaureihe. Bei maximaler Flexibilität für individuelle Kundenwünsche ist die e-mac jetzt noch kompakter.
Die Qualität von Pipettenspitzen hängt massgeblich von der Präzision des Einspritzvorgangs ab. Zugleich erfordern die langen Kerne im Werkzeug absolut präzise Bewegungen der Werkzeugaufspannplatten beim Öffnen und Schliessen. Vollelektrische Spritzgiessmaschinen finden in diesem Anwendungssegment deshalb bevorzugt Einsatz, wobei die Wirtschaftlichkeit bei der Maschinenwahl entscheidend ist. Mit der e-mac hat Engel eine vollelektrische Spritzgiessmaschine im Programm, die eine hohe Leistung und Energieeffizienz mit einem äusserst kompakten Maschinendesign kombiniert und damit auch in regulierter Reinraumumgebung niedrigste Stückkosten sichert. Engel hat jetzt den Stellflächenbedarf der e-mac Maschinen noch weiter reduziert. Durch eine optimierte Kniehebelgeometrie baut die zur Markteinführung präsentierte e-mac 265/180 um 450 mm kürzer als die bisherige 180-Tonnen-Ausführung, ohne dass der Öffnungshub verkleinert wurde. Unter den vollelektrischen Maschinen am Markt sind die e-mac Maschinen der neuen Generation über die gesamte Baureihe in ihrem jeweiligen Leistungssegment eigenen Angaben gemäss die weltweit kompaktesten.
Spritzaggregat neu entwickelt
Sämtliche Bewegungen der e-mac – auch die Düsenbewegung und das Auswerfen – werden von servoelektrischen Antrieben ausgeführt. Damit erreicht die Maschine einen sehr hohen Gesamtwirkungsgrad. Bei Bedarf lässt sich ein Servohydraulikaggregat ohne zusätzlichen Platzbedarf in den Maschinenrahmen integrieren. Das Spritzaggregat der e-mac wurde mit Fokus auf eine noch höhere Dynamik von Grund auf neu entwickelt. Es steht in drei
Bild: Engel Die jetzt noch kompakteren vollelektrischen Engel e-mac Maschinen sind für einen optimalen Gesamtwirkungsgrad ausschliesslich mit besonders leistungsstarken Servomotoren ausgerüstet.

Leistungsklassen zur Verfügung. Damit lässt sich die Maschine exakt an die Anforderungen anpassen, um für die unterschiedlichsten Anwendungen jeweils die höchste Gesamteffizienz zu erzielen. Für Präzisionsanwendungen mit Zykluszeiten oberhalb von vier Sekunden stellt die e-mac im Bereich der vollelektrischen Spritzgiessmaschinen oft die wirtschaftlichste Lösung dar. Ausser in der Medizintechnik findet die Maschine in den Bereichen Verpackung, Teletronics und Technischer Spritzguss Einsatz. Die Automatisierung leistet einen zusätzlichen Beitrag zum sehr kleinen Footprint der präsentierten Fertigungszelle. Sie umschliesst alle Automatisierungskomponenten und Downstream-Prozesseinheiten, wie die Qualitätskontrolle, Trayserver oder Boxenwechsler, und ist dabei deutlich schmaler als eine übliche Schutzumwehrung. Ihr standardisierter Aufbau ermöglicht bei einem Produktwechsel ein schnelles Umrüsten der Anlage. Auf Kundenwunsch liefert Engel auf die Anwendung exakt zugeschnittene Produktionszellen, die neben der Spritzgiessmaschine und Automatisierung zum Beispiel auch Lösungen für die Digitalisierung und Vernetzung umfassen. Während z.B. iQ weight control für jeden einzelnen Schuss das Schmelzevolumen nachjustiert und damit für eine konstant hohe Qualität der Spritzgiessprodukte sorgt, regelt iQ flow control Temperaturdifferenzen im Kühlwasserverteilerkreis automatisch aus. Dafür nutzt die Software die von den elektronischen Temperierwasserverteilern e-flomo ermittelten Messwerte. Das Ergebnis sind konstante Temperierverhältnisse und eine deutlich bessere Energieeffizienz, denn auch die Drehzahl der Pumpen in den Engel e-temp Temperiergeräten wird automatisch bedarfsgerecht geregelt.
Kontakt Engel (Schweiz) AG Hungerbüelstrasse 17 CH-8500 Frauenfeld +41 52 725 07 57 Info.ch@engel.at www.engelglobal.com
Qualitätssicherung in der Kunststoffindustrie
Schnelle Füllstoffbestimmung
Durch die Zugabe von Fasern lassen sich bei Kunststoffen die mechanischen und mechanisch-thermischen Eigenschaften verbessern. Zur Bestimmung des Füllstoffgehalts in Kunststoffen braucht es spezielle Verfahren, damit die Prozesskontrolle zeitnah erfolgen kann.
Die Fasern im Compoundierverfahren direkt in die Schmelze zugeben, ist bei vielen Herstellern im grossen Umfang üblich. Viele technische Kunststoffe sind ohne Fasern nicht mehr denkbar. Häufig werden Kurzglasfasern verwendet, deren Faserlänge im Granulat bei 300 µm liegt. Vereinzelt werden auch Langfaserprodukte verwendet, deren Faserlänge bis zu dreimal grösser ist. Zu jedem Herstellungsprozess und jeder Eingangskontrolle gehört daher die Messung des Glasfaser-Füllstoffgehalts. Zudem werden immer häufiger Kohlefaser, Carbon Nanotubes etc. in das Compound eingearbeitet. Im Zeichen zertifizierter Qualitätssicherungssysteme nach DIN ISO 9000ff, die heute von den meisten Produktionsbetrieben eingerichtet sind, soll die Überprüfung der Produktqualität in kurzen Abständen erfolgen und Konsequenzen ermöglichen: ein rasches Eingreifen und Anpassen des Fertigungsprozesses ist nötig.
Die Prozesskontrolle
Dieser Forderung steht eine Veraschungszeit von mehreren Stunden im konventionellen Muffelofen gegenüber, viel zu lange, um aufgrund der Messergebnisse noch wirksam in die Produktion eingreifen zu können oder bei der Warenanlieferung die Abladung zu beeinflussen. Auch in Forschung und Entwicklung, z. B. von Recycling-Verfahren, wird eine schnelle, flexible Versuchsdurchführung immer wichtiger. Hier gewährleisten die schnellen Phönix Black Muffelöfen eine deutliche Zeitverkürzung bei gleichbleibender analytischer Qualität und stellen somit Alternativen zu etablierten konventionellen Techniken dar. Reglementiert wird die Bestimmung des Aschegehaltes durch die ISO 3451 Teil 1–5, worin die Trockenveraschung und
Bilder: CEM
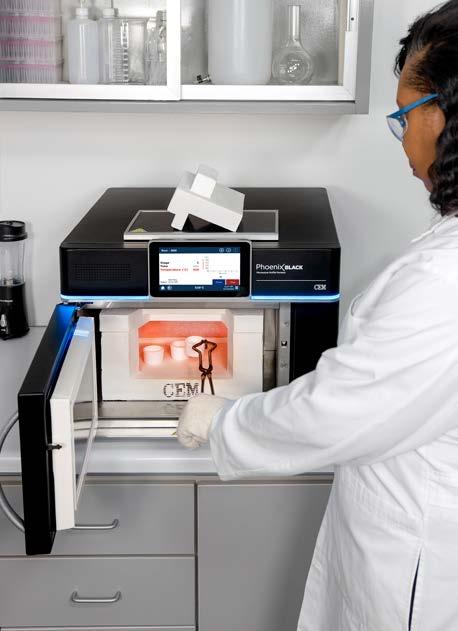
Der Muffelofen Phoenix bietet eine schnelle Veraschung zur Bestimmung von Füllstoffgehalten.
Sulfatveraschung beschrieben sind. Hier wird ein Mikrowellen-Muffelofen mit zu regelnden Veraschungstemperaturen von 600 + 25 °C, 750 + 50 °C, 850 + 50 °C und 950 + 50 °C genannt. Die High-TechMuffelöfen der Phönix Black-Familie von CEM erfüllen diese Regularien auf den Punkt genau.
Wie Phönix aus der Asche
Moderne Produktionsverfahren sind zunehmend gekennzeichnet durch das Erzielen höherer Umsatzraten und schnellerer Produktion, kontinuierlicher Verfahrensabläufe, Automatisierung sowie standardisierte Produktqualität. Dieses stellt an die begleitende und überwachende Analytik neue Anforderungen, wie z. B. hinsichtlich der Schnelligkeit, Verlagerung der Messung vom analytischen Labor hin zum Produktionsort, robuste Apparaturen («Handschuhtauglichkeit») sowie einfache Handhabung durch teilweise nur angelerntes Personal. Je nach Branche und Verfahrensablauf eröffnet der Einsatz eines Schnellanalysen-Systems eine Reihe von Einsparungsmöglichkeiten z. B. in der kunststofferzeugenden und kunststoffverarbeitenden Industrie bzw. in der Recyclingbranche: 1. Bessere und gleichmässigere Qualität der Ausbeute durch exakte Messung der Glasfaser-Füllstoffgehalte in engen
Toleranzen 2. Verkürzung des Prozesses durch kürzere Wartezeiten 3. Schutz vor Ausschuss durch schnelle
Kontrollen = Erhöhung der Ausbeute
Analyse in wenigen Minuten
Mit dem Schnell-Muffelofen Phönix Black werden die Glasfaser-Kunststoffe innerhalb von wenigen Minuten analysiert, d. h. die Probe wird verascht – die Glasfaser bleibt zurück. Die Analyse funktioniert so: Unter Veraschungen versteht man die thermische Zersetzung kohlenwasserstoffhaltiger Produkte, wobei die anorganischen Bestandteile zurückbleiben. So werden konventionelle Muffelöfen schon seit langer Zeit für die verschiedensten Veraschungen eingesetzt. Dabei wird eine
Innerhalb weniger Minuten wird die Probe verascht – die Glasfaserstruktur bleibt zurück.
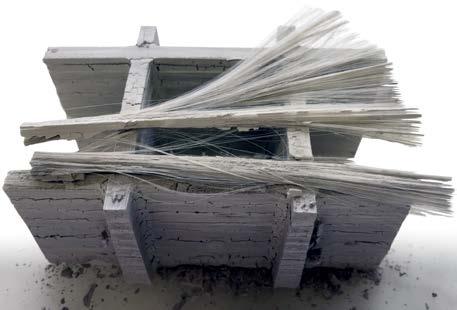
Probe in einen Tiegel eingewogen, welcher vorher getrocknet bzw. ausgeglüht wurde. Anschliessend wird das Probengut in einen konvektiv beheizten Muffelofen gegeben, wo es in der Regel etliche Stunden bis zur Gewichtskonstanz verbleibt. Danach wird der Tiegel aus dem Ofen entnommen und zum Abkühlen für gut eine Stunde in einen Exsikkator gegeben, ehe eine Rückwiegung erfolgen kann. Dieser relativ einfache Prozess ist äusserst arbeits- und zeitintensiv, welches vor allem in der Produktions- und Qualitätskontrolle ein grosses Problem darstellt und ein schnelles Zugreifen in laufende Produktionen verhindert. Abhilfe schaffen hier die Phönix Black Muffelöfen von CEM. Für die Trockenveraschung setzt man das Muffelofensystem Phönix Black ein, während für Nassveraschungen mit Schwefelsäurezusatz (Sulfataschen) das Phönix Black SAS eingesetzt wird. Die Vorteile dieser Technik sind eine drastische Zeitreduktion und ein «sauberes» Arbeiten. Was mit der konventionellen Technik früher Stunden benötigte, wird mit der Phönix-Technik nun in Minuten erreicht.
Die Funktionsweise des Phönix
Die schnellen Veraschungen basieren auf der «Ofen-im-Ofen-Technik». Dabei wird um den heissen inneren Ofenteil mit den Proben ein optimierter Luftstrom herumgeführt. Dabei bleibt die heisse Muffel von aussen kalt und es können keine Unfälle in Form von Verbrennungen an den Fingern erfolgen. Durch die poröse Muffel dringt diffusiv die Luft zum schnellen Veraschen/Oxidieren ins Innere vor. Dort werden die Kunststoffproben mit einem Überschutz an Luft schnell verascht. Als Veraschungstiegel kommen spezielle Quarzfasertiegel zum Einsatz, in denen dann bei Veraschungstemperaturen von bis zu 1200 °C die Probe behandelt wird. Zur Kennzeichnung können die Tiegel mit einem Hochtemperatur-Markierungsstift beschriftet werden. Zudem bieten diese Tiegel den Vorteil, dass sie innerhalb von wenigen Sekunden nach der Entnahme aus dem Ofen abkühlen, ohne dabei Feuchtigkeit aufzunehmen. Somit wird ein Überführen in den Exsikkator hinfällig und beschleunigt das Handling des Rückwiegens enorm. Ein Abluftrohr wird direkt am Gerät angeschlossen, das damit selbst, wie auch seine Umgebung frei von Ablagerungen bleibt. Die Raumluft und somit auch der Anwender werden nicht belastet (Arbeitsschutz) und die Installation braucht unter keinem Abzug zu erfolgen.
Kohlenstoff- und CarbonFüllstoffe
Die enorme Schnelligkeit der gesamten Veraschung zur Füllstoffbestimmung wird
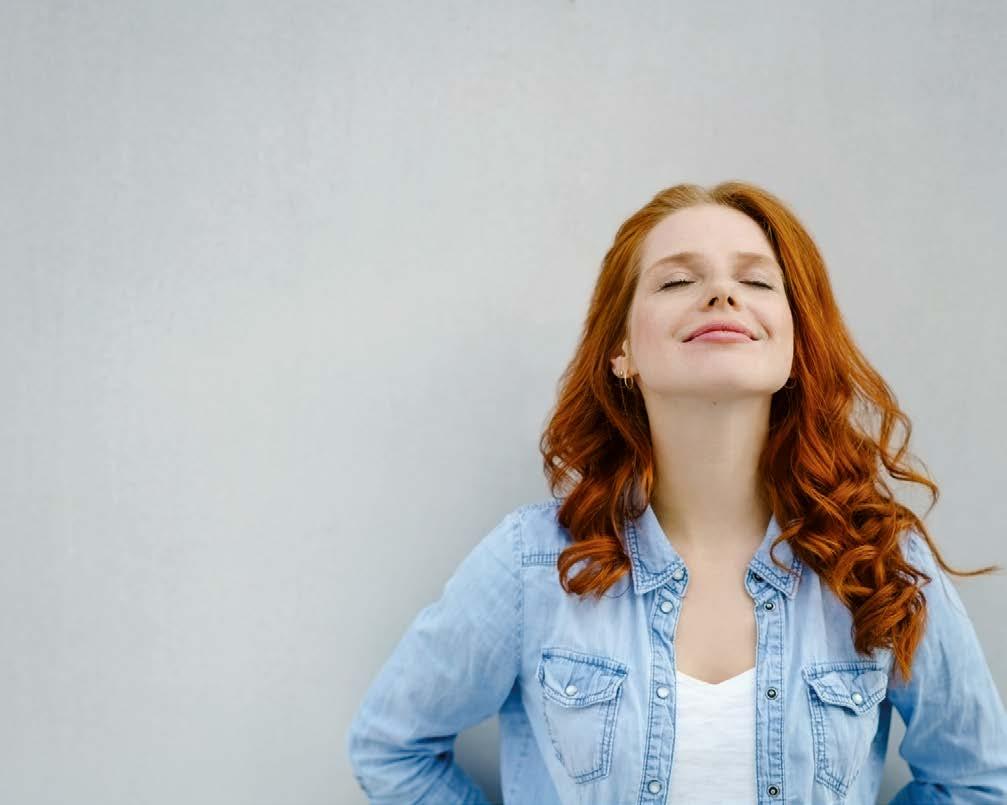
TEMPRO plus Temperiergeräte
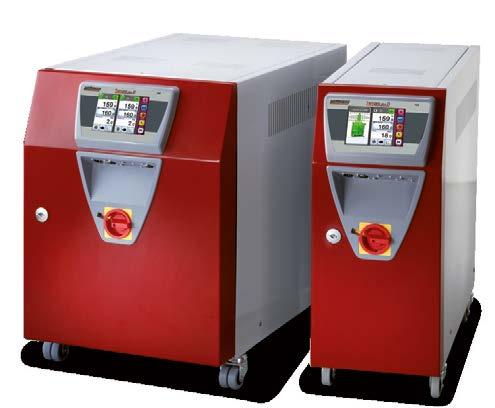
beispielhaft in der Tabelle gezeigt. Neben den aufgeführten Materialien können auch alle anderen Kunststoffe, Polymere, Gummiarten etc. im Phönix Black Muffelofen verascht werden. Somit werden die Füllstoffstrukturen wie Glaskugeln, Glasfasern, Glaswaben etc. schonend freigelegt. Neben anorganischen Füllstoffen wie Glasfaser oder Glaskugeln werden auch organische Füllstoffe wie Holzmehl, Kohlefaser, Russ, Carbon Nanotubes etc eingesetzt. Da sich diese organischen Füllstoffe zu einer anderen Zeit mir dem Sauerstoff um-

setzen, als das Polymer, wird im Phönix Black MIV unter Inertgas-Atmosphäre gearbeitet. Damit wird das Polymer verascht und die freigelegten Kohlenstoff-Füllstoffe bleiben unversehrt zurück.
Nassveraschung zur Sulfatasche-Bestimmung
Neben den bisher aufgelisteten Beispielen zur Trockenveraschung gibt es für Nassveraschungen weitere Vorschriften zur Bestimmung des Glührückstandes nach Schwefelsäure-Behandlung der Probe (Sulfatasche). Neben der bereits erwähnten ISO 3451, die auch die Sulfatveraschung von Kunststoffen beschreibt, ist für die Prüfung von Kautschuk, Elastomeren und Kunststoffen die Sulfatasche gemäss DIN 53568, Teil 2 sowie ISO 247 (Rubber – Determination of ash) vorgeschrieben. In der PVC-Industrie wird der Kreideanteil von PVC-Formteilen als Sulfatrückstand nach vorheriger Nassveraschung bestimmt. Diese Sulfatasche-Bestimmung gemäss der vorgenannten Vorschriften ist bedingt durch die einzelnen Arbeitsschritte ein mühseliger und langwieriger Prozess und zudem für den Bediener äusserst unangenehm. Das Probengut wird dabei in einem Porzellan- oder Platintiegel mit Schwefelsäure versetzt, danach auf offener Flamme vorverascht und anschliessend im konventionellen Muffelofen bei ca. 600 °C bzw. 950 °C (je nach Vorschrift) verascht. Neben den aufwändigen Arbeits-
Vergleich der Veraschungszeiten mit einem konventionellen Muffelofen und dem Phönix.
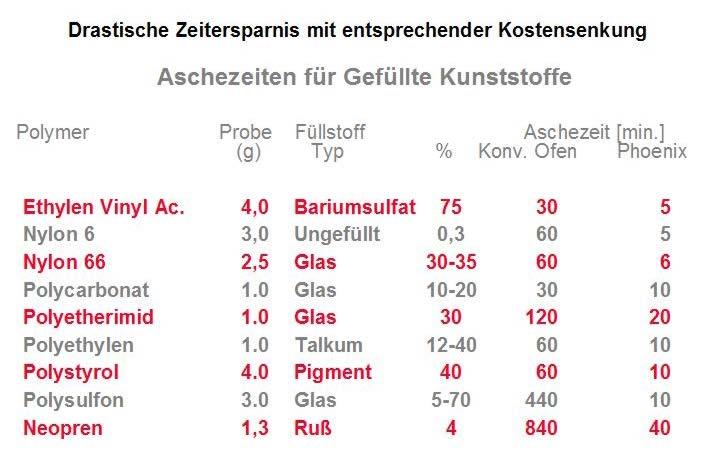
schritten (dauert bis zu 12 h) ist das Handling mit der abrauchenden Schwefelsäure äusserst umständlich und gesundheitsbeeinträchtigend. Nach der Beendigung des Schwefelsäureabrauchens sind vielfach aufwändige Reinigungsarbeiten am Abzug vorzunehmen. Eine Alternative bezüglich der Schnelligkeit, des Arbeitsschutzes und des Bedienerkomforts stellt auch hier ein PhönixSystem dar. Die komplette Veraschung inklusive Vorveraschung wird im Phönix Black SAS durchgeführt, wo mit einer Vakuumabsaugung aus dem Veraschungseinsatz eine doppelte Absaugung der sauren und teilweise toxischen Verbrennungsprodukte gewährleistet wird. Dabei führt aus dem Veraschungseinsatz mit den zu bearbeitenden Proben ein Quarzrohr zu einer Abscheide- und Neutralisationseinrichtung, bestehend aus Waschflaschen und Aktivkohlefilter. Die Veraschungsdauer verkürzt sich deutlich auf ca. 60 Minuten bei gleichzeitiger Veraschung von bis zu 15 Proben.
Kontakt CEM GmbH Carl-Friedrich-Gauss-Str. 9 D-47475 Kamp-Lintfort +49 2842 9644-0 Ulf.Sengutta@cem.com www.fuellstoff-bestimmung.de
Machen Sie den richtigen Zug!
Erfolgreich werben mit der KunststoffXtra.
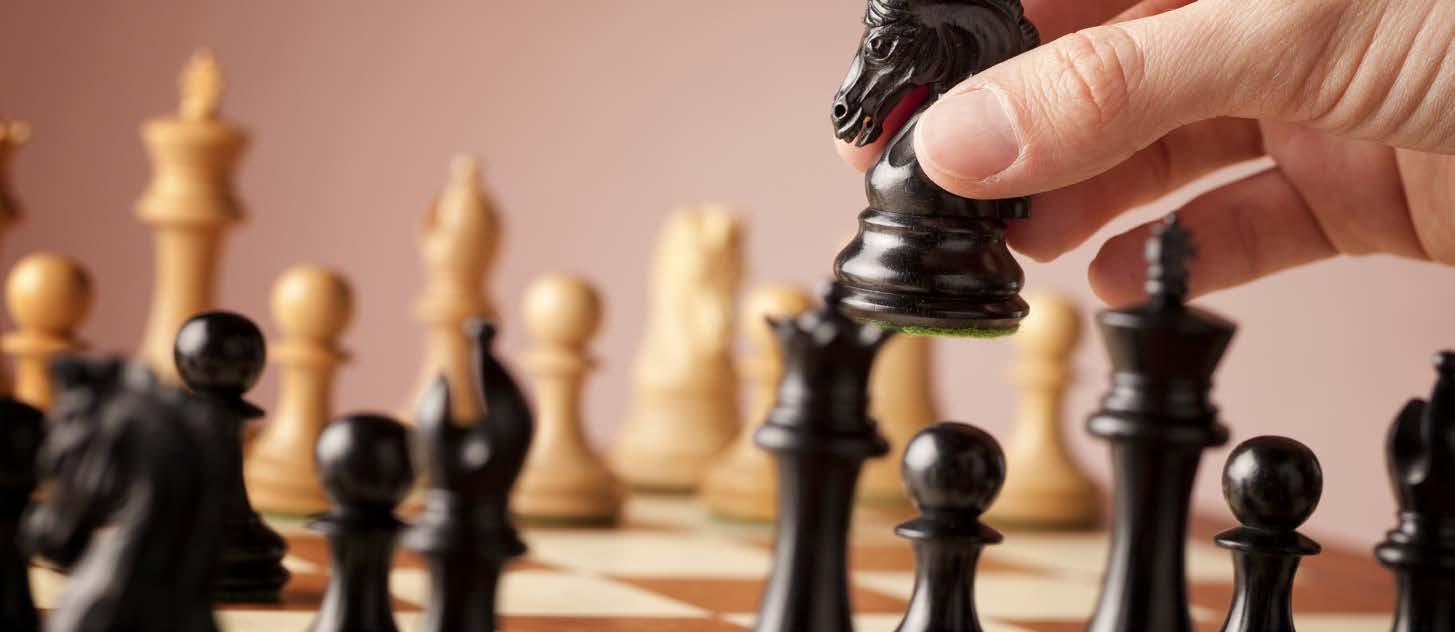