
7 minute read
RECICLAJE DE NEUMÁTICOS
rCB en NBR – 5 % rCB en NBR – 10 % rCB en NBR – 25 %
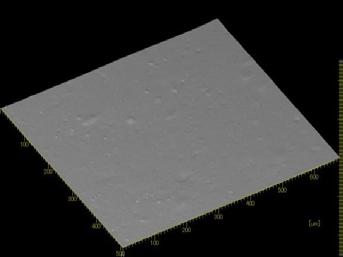

En la próxima entrega de RevistaSLTCaucho, presentaremos la segunda parte de esta investigación, retomando los resultados obtenidos y la conclusión. ■
Referencias
1. C. Norris, S. Renegar: The Influence of Pyrolysis Residues on the Properties of Recovered Carbon Black, IRC 2019, Londres 05/09/2019.
2. C. Norris. How to Maximize the Performance of rCB, SMG 2020, Londres05/02/2020.
3. M. White. Carbon Black Regulatory Overview SMG 2020, Londres 05/02/2020.
4. C. Norris, M. Hale, and M. Bennett, “Pyrolytic carbon: factors controlling in-rubber performance” Plast. Rubber Compos., vol. 43, no. 8, pp. 245–256, 2014.
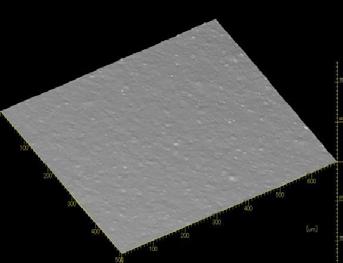
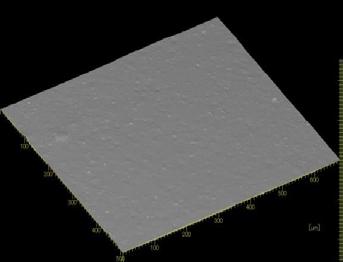
5. AA. Quek and R. Balasubramanian, “Liquefaction of waste tires by pyrolysis for oil and chemicals - A review,” J. Anal. Appl. Pyrolysis, vol. 101, pp. 1–16, 2013.
6. Nocolaus Probst, Progress on recovered Carbon Black from Waste Tire Pyrolysis, KGK rubberpoint, 1 2021, pag35-40.
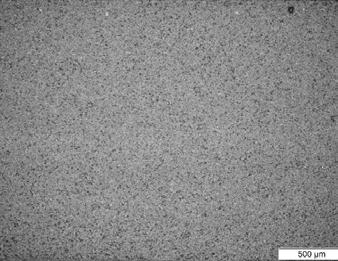
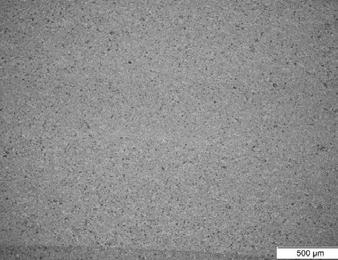
7. C. Norris, S. Renegar: The Influence of Pyrolysis Residues on the Properties of Recovered Carbon Black, IRC 2019, Londres 05/09/2019.
8. L. Moulin, S. Da Silva, A. Bounaceur, M. Herblot, and Y. Soudais, “Assessment of Recovered Carbon Black Obtained by Waste Tires Steam Water Thermolysis: An Industrial Application” Waste and Biomass Valorization, vol. 8, no. 8, pp. 2757–2770, 2017.
Acuerdo con Revista Caucho del Consorcio Nacional de Industriales del Caucho (España) para el intercambio de artículos de interés entre ambas publicaciones | www.consorciocaucho.es
La hoja de ruta general de la Industria 4.0, en la que se enmarca el proyecto Moldcaucho, es avanzar hacia la digitalización de los procesos de moldeo de caucho, para hacerlos más eficientes, competitivos y respetuosos con el medio ambiente
Esta herramienta sirve para la optimización del diseño de moldes y del proceso de fabricación de piezas de caucho.
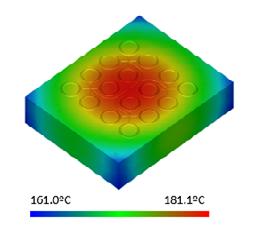

Problem Tica Abordada En La Industria Transformadora De Caucho
El foco principal del proyecto es aumentar la productividad y calidad de los componentes fabricados en moldes multi-cavidad, en los que posibles gradientes de temperatura dentro del molde pueden provocar diferencias de temperatura entre las diferentes cavidades, lo que repercute en una mayor variabilidad en las piezas producidas.
Para ello, Moldcaucho tiene como objetivo el desarrollo de una herramienta, basada en simulación, para apoyar el diseño de molde y la selección de parámetros de proceso óptimos en la fabricación de piezas de caucho mediante moldeo por inyección.
El fin último y el beneficio para la empresa es poder tener disponible una herramienta con una doble función:
En fase de diseño de molde: la simulación permitirá conocer la distribución óptima de temperaturas en el molde, como ayuda a la ubicación de sensores y la detección de zonas con necesidad de implementar zonas locales calefactadas.
En fase de puesta en marcha de proceso y posteriormente en producción: la herramienta predecirá de forma rápida las características de la pieza que se esté fabricando y contribuirá a la elección de los parámetros de proceso para conseguir una fabricación óptima (vulcanización, tiempo de ciclo, etc.).
PROYECTO DESARROLLADO DENTRO DEL MARCO DE LA AEI
El proyecto ha sido subvencionado por el Ministerio de Industria, Comercio y Turismo de España, en su programa de apoyo a Agrupaciones Empresariales Innovadoras (AEI). Este tiene como fin mejorar la competitividad de las pequeñas y medianas empresas del país, en el marco del Plan de Recuperación, Transformación y Resiliencia.
El Consorcio Nacional del Caucho, como AEI, ha coordinado el proyecto, en el cual han participado ITAINNOVA, como organismo público de investigación, y dos PYMES: MIJU, especializada en la fabricación de piezas de caucho por compresión, transferencia e inyección, y MOLWELD, empresa de desarrollo, fabricación y reparación de moldes.
Caso De Uso En El Sector Del Autom Vil
Para el desarrollo del proyecto, MIJU seleccionó el caso de uso de un componente para el sector automoción, con requerimientos funcionales específicos. Se requirió comenzar el trabajo con el desarrollo de una mezcla de caucho específica para esta aplicación. El conjunto, perteneciente al sistema de refrigeración, debía deslizar con mínima fricción, pero garantizando el sellado, lo que obligaba a unas tolerancias dimensionales muy estrechas.
La compatibilidad química con el líquido refrigerante, el rango de temperaturas de operación de -35 ºC a 110 ºC (con picos de 130 ºC) y las características funcionales requeridas (se requería una dureza 85 Shore A) llevaron a MIJU al desarrollo de una mezcla EPDM con sistema de curado en base peróxido. Dicha mezcla resultaba en una viscosidad muy elevada, por lo que su inyección podría ser dificultosa.
Por ello, MIJU, junto al MOLWELD, siguieron un proceso de desarrollo del molde en dos etapas. En primer lugar, trabajando sobre un molde prototipo, se realizaron pruebas básicas de inyección y se investigó la contracción del componente. Dicha información fue la base del diseño del molde multicavidad, soportado por simulaciones de inyección básicas
El material final desarrollado fue analizado de forma completa para validar los requerimientos funcionales y de procesabilidad. En particular, se determinaron las características de material necesarias para la simulación detallada del proceso de inyección.
HERRAMIENTA PARA LA PUESTA A PUNTO DEL PROCESO
ITAINNOVA ha creado un gemelo digital basado en la física del problema para este caso demostrador. Para su desarrollo, el primer paso ha sido la creación un modelo de detalle del molde multicavidad para simulación de la inyección, incorporando los modelos de material ajustados con la caracterización realizada, elementos calefactores y sensores virtuales.
Dicho modelo incorpora la base física de los fenómenos físico-químicos que suceden durante el procesado. Básicamente, se trataba de simular un flujo transitorio no isotermo de un fluido viscoso no newtoniano en el que entran en juego distintos mecanismos físicos, tanto de transmisión de calor por conducción (calor transmitido del molde al flujo con el que está en contacto), convección (calor perdido a través de las paredes del molde con el exterior) y por resistencias térmicas de contacto, además de la propia cinética de la reacción de vulcanización, que entre otros efectos, cambios de volumen en las cavidades (relación pvTC).
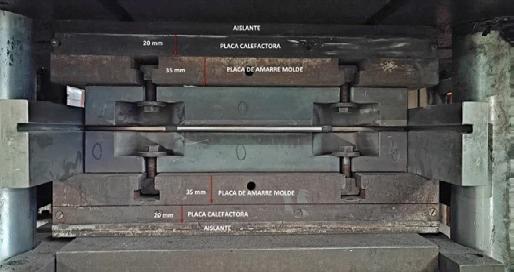
De los numerosos resultados que la simulación ofrece, se han seleccionado aquellos de mayor interés para el inyector. Por una parte, aquellos relativos a los límites del proceso, como la máxima presión alcanzada o la fuerza de cierre necesaria. Por otra, los relativos a las características de las piezas obtenidas de las diferentes cavidades, como las diferencias de temperatura y grado de curado en cada cavidad y entre cavidades, además de las características dimensionales de las juntas (diámetros).
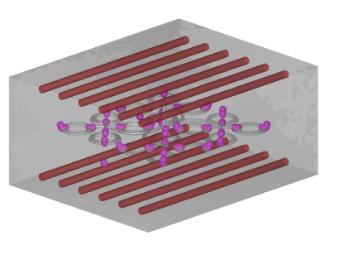
Para extraer el máximo conocimiento de modelos de simulación, se ha realizado un diseño de experimentos (DOE) en el cual se variaban los parámetros de proceso en rangos amplios. De dichas simulaciones se extraen los resultados claves definidos. Dicha información, consistente en las combinaciones de parámetros de entrada junto a la lista de resultados obtenidos, es utilizada para generar unos modelos de orden reducido (MOR) que encapsulan el conocimiento generado en expresiones matemáticas para cada resultado, evaluables en tiempo real
Para que el usuario pueda utilizar estos modelos de forma interactiva, se hacen operativos (imagen 1-a) a través de la interfaz de usuario mostrada en la siguiente figura:
La funcionalidad de esta herramienta permite evaluar cualquier combinación de parámetros de proceso en los rangos definidos (imagen 1-b) y obtener de forma instantánea, no solo el valor predicho de cualquier variable (imagen 1-c y 1-d) en esa combinación, sino también cómo cada parámetro afecta a cada resultado (imagen 1-e). También permite al usuario definir límites y tolerancias para cada resultado.
Dicha herramienta da soporte a la toma de decisiones sobre los parámetros de proceso, proporcionando un conocimiento por anticipado de la sensibilidad de los parámetros de proceso; y puede usarse en tiempo real para guiar las pruebas de inyección en la puesta en marcha del proceso. Por ejemplo, se puede elegir un curado mínimo objetivo y con ella buscar, en la cavidad más desfavorable, cuál es el tiempo de vulcanizado mínimo necesario.
Prospectiva Para Mejorar La Uniformidad T Rmica Del Proceso
El estándar de producción basado en utilizar moldes en una prensa de platos calientes ofrece limitadas posibilidades para mejorar grado de uniformidad térmica en el molde, dado que la regulación térmica de los platos forma parte del control de la prensa y ésta habitualmente no permite acceder a ese control más allá de seleccionar la temperatura objetivo.
1. Herramienta de ajuste de parámetros de proceso.
La parte final del proyecto Moldcaucho ha tratado de investigar cual serían los potenciales beneficios de poder actuar sobre el control térmico de los platos de la prensa y, adicionalmente, proveer al molde de un sistema de calefacción accesorio Para ello, se ha completado el modelo de simulación de la inyección con la posibilidad de modificar el reparto de potencia entre las resistencias ubicadas en diferentes zonas, a las que además se han añadido unos cinturones calefactados periféricos en el molde.
La comparativa de escenarios realizada permite estimar la potencial mejora en uniformidad térmica entre cavidades del molde, que ha permitido pasar de aproximadamente 8 ºC de diferencia máxima a una diferencia de estimada de 1 ºC. Esta mayor uniformidad térmica hace que el vulcanizado de las piezas progrese más uniformemente. Evaluado en un punto de vulcanizado intermedio, las mayores diferencias en curado pasan del 28 % al 10 %.
El modelo se ha explotado de la misma forma descrita anteriormente, es decir, a través de un DOE de simulaciones, encapsulación de resultados en modelos de orden reducido y su importación en una interfaz de usuario para su análisis.
Mediante el uso de la aplicación, se han realizado optimizaciones de distribución de potencia en varios escenarios. Como referencia se ha utilizado el control actual, que aporta una potencia distribuida uniformemente entre las resistencias de los platos. El segundo escenario optimiza las potencias suministradas a las resistencias de cartucho de los platos. Por último, el tercer escenario incluye también en la optimización las potencias de los cinturones laterales.
Conclusiones
Como conclusión de esta segunda parte del proyecto, un control térmico por zonas independientes permitiría conseguir reducir aún más los gradientes térmicos en comparación al control estándar, lo que repercutiría directamente en mejora de calidad de la pieza y ajuste del tiempo de ciclo. En una futura implementación, los modelos de orden reducido basados en simulación, desarrollados en el marco del presente proyecto, podrían utilizarse como predictores en los algoritmos de control térmico de los platos y el molde.
El proyecto MOLDCAUCHO ha sido subvencionado por el Ministerio de Industria, Comercio y Turismo, en su programa de apoyo a Agrupaciones Empresariales Innovadoras (AEI).■
Autor: Manuel Laspalas, Materiales y Componentes.
Acuerdo con Revista Caucho del Consorcio Nacional de Industriales del Caucho (España) para el intercambio de artículos de interés entre ambas publicaciones | www.consorciocaucho.es