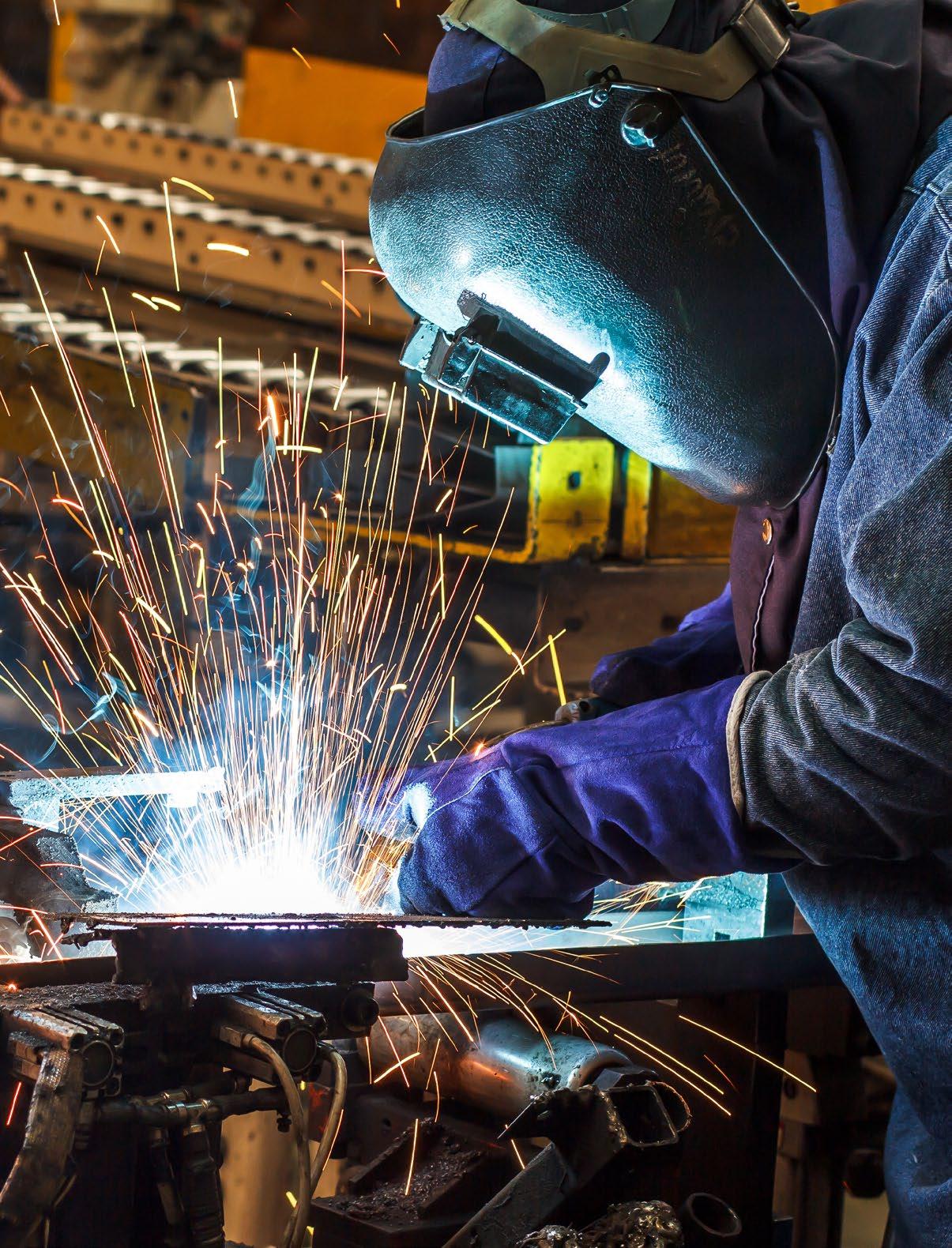


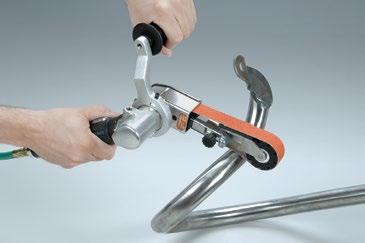
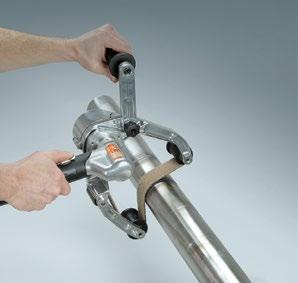


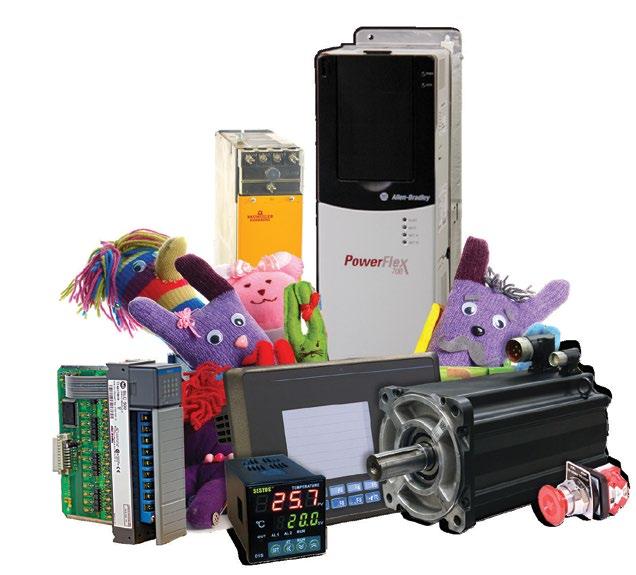

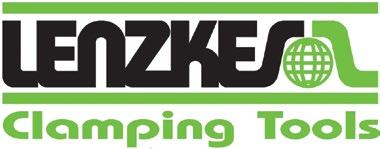











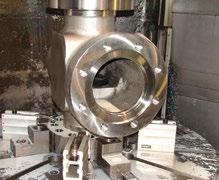

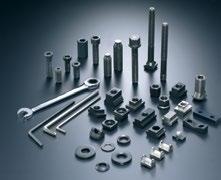

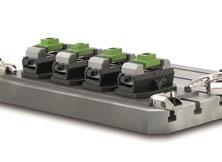
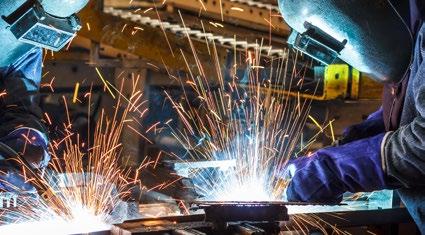
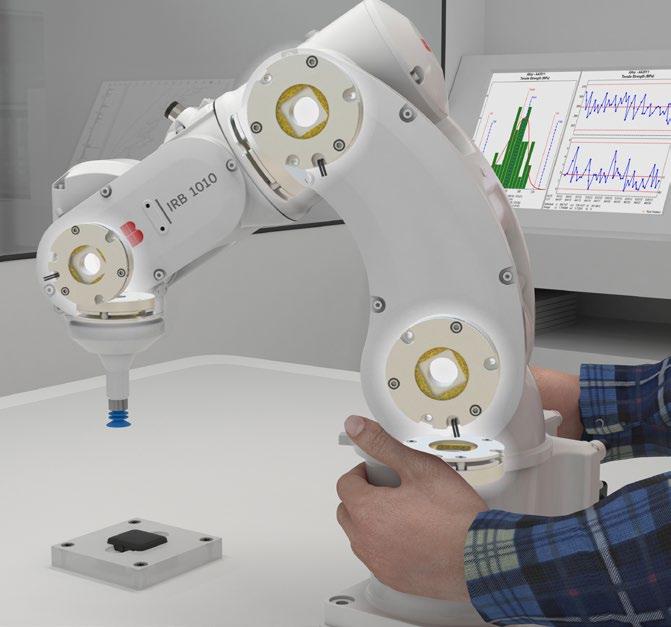
is exclusively distributed in the US and Canada by
Do you often move loads with surfaces that require protection? Then it is essential to avoid damage by lifting means at all costs. The solution: the new TXP-Texolution-Point. Its round sling reliably protects high-quality surfaces. Damaging contacts between lifting means and load surface are practically no longer an issue. And that with guaranteed total WLL. This preserves values and increases efficiency.
Hello and welcome to the November 2022 issue of Industrial machinery Digest! It’s hard to believe this year is nearly over, but here we are less than two months away from 2023. The leaves are changing, there’s a chill in the air, and organizations across all industries are entering a slow-down period as the temperatures drop and everyone prepares to close out the year. (Although we know better than most that even a “slow” time of the year still means nonstop production.)
of course, with it being November, the word “gratitude” comes to mind. And, boy, do we here at ImD have a lot to be thankful for, particularly when it comes to our readership. We’re closing out another calendar year of providing top industry-focused content like technical articles, Q&As, case studies, news releases, and more — like we have done for nearly 40 years, and we’re only getting started.
This is a special issue of the magazine, as it will be with us in Atlanta November 8-10 for FAbTeCH, North America’s largest metal forming, fabricating, welding and finishing event.
If this issue arrives in your mailbox before then and you’re planning to attend the show, then please stop by b9829 to meet our team and discuss ways we can feature your company’s story, solutions, and more in the magazine.
In this edition of ImD, you’ll find a feature on major safety issues for the metalworking and machining industry. more specifically, it will discuss the common dangers teams face on the shop floor and measures leaders can take to keep the workplace safe, starting with a robust safety culture.
You’ll also find a Q&A conversation with Dr. max Siebert, Co-Founder and Ceo of replique, which provides the first fully encrypted 3D printing platform that makes spare part management and the production of small series more sustainable. The team there offers an end-to-end solution from qualification to production and shipment by combining their digital inventory and a network of additive manufacturing professionals.
As always, happy reading, my friends! I hope you enjoy this issue and maybe even learn something new. Please do not hesitate to reach out with any comments, questions, or article ideas. I’d love to hear from you.
William C. Strickland III, Publisher william.strickland@indmacdig.com 800-366-0676 ext. 103 | Fax: 866-826-5918
Anna Claire Howard, Editor achoward@indmacdig.com 800-366-0676 ext. 104 | Fax: 866-826-5918
Shane Bell, Creative Director sbell@indmacdig.com
Lisa Hanschu, Sr. Account Executive lisa@indmacdig.com 785-965-9159 | Fax: 785-965-7199
William C. Strickland III, National Sales 205-903-9178 | fax 866-826-5918
Adrienne Gallender, Media Adviser agallender@indmacdig.com 888-407-7737
Susan Strickland, Accounting susan@indmacdig.com 205-542-1098
Fax: 866-826-5918
866-826-5918
uals.
Hardinge Inc., a multinational machine tool and accessories builder with global headquarters in Atlanta, Georgia, received the 2022 National metalworking reshoring Award in recognition of its success in bringing manufacturing back to the United States. The 2022 award was presented on Sept. 16, 2022, at ImTS – The International manufacturing Technology Show at mcCormick Place in Chicago by Harry moser, founder and president of the reshoring Initiative. The award honors companies that have effectively reshored products, parts, or tooling made primarily by metal forming, fabricating, casting, or machining, including additive manufacturing. The award is made possible by the reshoring Initiative; the Precision metalforming Association (Pm A); A mT – The Association For manufacturing Technology, which owns and produces ImTS; Sme; and the National Tooling and machining Association (NTm A).
To receive the award on the ImTS+ main Stage were Hardinge’s Jeremy michael, v ice President and General manager of Turning & milling; r yan ervin, Chief marketing o fficer and v ice President of Sales; David bassett, Senior Director Continuous Improvement, Quality, e xport Compliance; and Chandra Urs, President –Turning & milling.
“We are very proud to be recognized by the reshoring Initiative and owe a tremendous amount of gratitude to the hundreds of Hardinge employees both in the United States and Taiwan who worked to make this initiative a success over the last two years,” says michael. “o ur teams worked late hours with their counterparts overseas to ensure that knowledge and processes were transferred to our facility in elmira, New York, and these efforts were rewarded as we
began to see machine tools rolling off the new lines and out to customers.”
Hardinge’s extensive work bringing back manufacturing production to the United States made theirs a winning case. “Hardinge shifted the manufacturing of its milling and turning machine center solutions from its Taiwan plant to its plant in elmira, New York,” moser says. “What could be more appropriate at ImTS 2022 than for the winner to be a leading A mT member and ImTS exhibitor, which has manufactured machine tools in the United States since the 1890s?”
moser believes that reshoring work done by companies like Hardinge has helped invigorate manufacturing in the United States and recognizing their accomplishments is important, saying, “The reshoring Award has helped accelerate reshoring from 6,000 manufacturing jobs per year in 2010 to 260,000 in 2021.”
Appoints Amanda Bakun as the Marketing and Communications Manager for the Americas ANCA USA, a market leading manufacturer of CNC grinding machines, has announced that Amanda bakun will take on the newly created position of marketing and Communications manager for the Americas.
Johanna boland, Group Communications and Strategy manager said, “It has been really exciting at ANCA over the past five years in the marketing communications space. We have built an
outstanding team who are leading the way in our social media, thought leadership, customer communications and even an e-commerce platform amongst other marketing activities. We have a powerful and positive brand at ANCA, and I am confident that Amanda will both nurture and grow our reputation in the Americas as well as celebrate what is key to our success – our customers.”
Since ANCA was founded in 1974, the cutting tool industry has continued to grow, in both size and application. ANCA CNC grinders are used for manufacturing precision cutting tools and components across a diverse range of competitive industries including cutting tool manufacture, automotive, aerospace, electronics and medical.
russell riddiford, Gm Americas said “I am confident that the North/South American segment of the market is going to continue to grow, and because of that we are investing in our growth strategy. We have fantastic customers and exceptional technology in a dynamic market – marketing is key to connecting these groups together.”
“ by the appointment of a local marketing and communications manager, ANCA will deliver a program of activities so that new and existing customers can remain up to date on all the latest news and innovations. This is especially important as we continue to diversify, expand, and grow our brand presence in a variety of different markets. We also pride ourselves on an aggressive product development strategy, investing more than 10% of our revenue annually into research and development - we need to ensure we are communicating these new solutions to the market,” says Johanna boland.
Although Amanda is new to ANCA, she is not new to the industry. She brings over 12 years of experience in content strategy and marketing in manufacturing. Amanda has worked for several organizations in the industry, most recently a leader in turning and grinding machines. ANCA is confident that her addition to the team will have a big impact on the region. At ANCA, Amanda will be responsible for the content marketing strategy, communications, and marketing efforts for the North and South American markets. “It is an exciting time to join the ANCA team as the company expands its product offerings in a variety of unique and diverse industries. I am honored to join the team and look forward to using my skills and experience to accelerate ANCA’s growth in the America’s,” says Amanda. Amanda has earned a bS in marketing from Grand valley State University in michigan, an mbA from Walsh College in michigan, and mS in marketing research from michigan State University.
Bernard Celebrates 75th Anniversary bernard is excited to announce that the company is celebrating its 75th anniversary. This milestone marks a history rich in welding product innovation that started with humble beginnings in a storefront on the southeast side of Chicago.
Bernard started with humble beginnings in a storefront on the southeast side of Chicago.
“ bernard was built upon a strong engineering foundation, which remains prominent in our culture today,” said Nathan miller, vP and general manager at bernard. “As the welding industry has evolved, bernard has evolved with it and continues to build upon the history of innovative solutions designed to meet the needs of the global welding industry.”
o ver the course of its 75 years in business, research and development efforts have led to multiple cutting-edge technologies, including perfecting the Dual Shield welding process in 1954 — now known as flux-cored arc welding (FCAW). During the 1960s, the company introduced its b ernard ® m IG welding gun and wire feeder, which served as the basis for continued gun and consumable innovation.
Today, bernard offers its customizable bTb semi-automatic air-cooled mIG guns and other mIG gun lines that can be configured online to meet a customer’s specific needs. bernard introduced its AccuLock™ S consumables in 2019 to address liner trim length errors and erratic wire feeding, leading to less troubleshooting, downtime and rework. This consumables system is in addition to its longstanding Centerfire™ consumables line.
bernard was family-owned and operated until 1970 when Dover Corporation purchased it. In 2001, Illinois Tool Works (ITW) purchased bernard, which is currently a division of miller electric mfg. LLC in Appleton, Wisconsin. miller is wholly owned by ITW.
Choose best-in-class cutting tools, tool holders and workholding products from bIG DAISHoWA and support your local manufacturing training programs at the same time.
From November 1 to December 30, 2022, bIG DAISHoWA will donate a tooling certificate valued at 20 percent of every order from an NTm A member company to the buyer’s school of choice.
“This is a way for us to support our partners and customers in NTm A and continue to show our commitment to workforce development,” said Jack burley, President & Coo of bIG DAISHoWA Americas. “When buyers select their favorite local school programs, they are sending resources to train their own future machinists and engineers.”
To take advantage of this promotion, the following must be met:
» A minimum order of $5,000 (earning a $1,000 tooling certificate).
» Place the order through your local distributor and request “Drop-ship from bIG DAISHoWA.”
» reference “Promo bD-SCHooLS” as a line item on your order.
“We’ve been active in NTm A for many years. o ur objective is to advise members on applying technology to reduce set ups and cycle times, improve part finishes, and lower costs through longer tool life. I hope this special promotion will be an incentive for those who have not tried our products yet,” b urley said.
b IG DAISH oWA offers 9 product lines of precision tooling, workholding, and tool management systems aimed at reducing both the overall process time and the cost per part.
Popular products include face mill holders, end mill holders, collet chucks, angle heads and tapping adaptors. The world-leading KAIS er boring system, high performance SPHINX drills and UNILo CK workholding systems are also available, as are CAT, bT, HSK and b IG CAPTo systems.
If your machine is equipped with a b IG-PLUS spindle, remember that b IG DAISH oWA is the official licensed provider of b IG-PLUS tool holders in North America. Don’t accept any substitute “dual contact” products on your valuable machines.
robert b unting follows in the footsteps of his grandfather and father with his appointment as b unting’s President and Chief e xecutive o fficer. o n o ctober 1, 2022, robert
succeeded his father, b ob b unting, in overseeing the continued growth of the global b unting group. b ob b unting assumes the position of Chairman.
b unting ® is one of the world’s leading designers and manufacturers of magnetic separators, metal detectors, materials handling, magnetic printing cylinders, magnets, magnet assemblies, and magnetizing equipment. The company, headquartered in Newton, Kansas, has multiple locations including b unting-elk Grove v illage; b untingDu b ois; b unting-b erkhamsted and b unting-redditch in the United Kingdom; and Ningbo, China.
Founded in 1959 by Walter F. b unting in Chicago, Illinois, the company has remained family-owned and family-operated ever since. Walter’s son, b ob b unting, served as president of the company since 1993 and oversaw an international expansion of the company. o ver the 29-years as president and Ceo, b ob oversaw a three-fold increase in sales. robert b unting’s appointment as president and Ceo continues the family legacy.
robert b unting joined b unting’s elk Grove v illage magnet sales team in 2007. b efore joining b unting, he had earned a degree in business management at rockhurst University in Kansas City, m issouri, and gained valuable experience during two years as an Internal Sales Coordinator at Sun Life Financial.
In 2009, robert moved into external sales covering
the Illinois and Wisconsin areas and focusing on material handling, metal detection and magnetic separation. Under his management, sales in the territory grew by 25%. This success led to robert’s appointment as the Global Product m anager for m etal Detection in 2014, where his responsibilities ranged from product development through to sales growth.
After the successful development of the metal detector product range, robert was appointed General m anager of b unting elk Grove v illage in 2016, including the online retail website b uym agnets.com. As General m anager, robert oversaw magnet inventory management, the identification and introduction of new magnetic products such as the N-40 and N-52 grades of neodymium, and the development of digital marketing strategies for online sales, including the introduction of a new website.
“ b unting’s position as a successful, well-respected global business is due to the tireless work of my grandfather and father,” explained robert. “Despite being located on different continents, the b unting Group is one company, and all our incredible employees are fundamental to our success. We have developed strategic global partnerships with suppliers and customers, which I aim to support and expand. I am both excited and honored to be entrusted with taking the company forward as president and Ceo.”
Businesses need to continually improve their products and processes to improve the efficient utilization of resources. Using fewer resources to produce the same amount of goods increases profitability, and it’s good for the environment. Improving the productivity of manufacturing facilities is one of the core tasks of the operations team.
Throughout the journey that began with steam engines, the manufacturing industry saw exponential growth in productivity. most industrial processes boast very good efficiency due to the use of modern industrial tools. This high starting point makes any productivity improvement a massive challenge. In addition to that, hurdles like lack of support, lack of training, and unrealistic expectations from management are some of the challenges plant operations teams face while trying to improve productivity.
Despite the challenges, if you want to reach your business goals, you need to improve the productivity of your facility. The following sections cover the six practices you should adopt to achieve that.
one of the biggest challenges in this aspect is the lack of direction to improve productivity. With just an overarching goal of productivity improvement, there are many avenues to achieve it. Trying to improve productivity without anything to aim at is akin to running around in the dark.
The first step in the path toward productivity improvement is to state clear, objective, and achievable goals. This is possible by identifying performance indicators for factory operations, and setting a target for the key performance indicators. Now the operations team has a clear
objective to move toward. With that, you will be able to chart the path to improve productivity.
many performance indicators can be identified for a plant operation.
You cannot use all of them to improve operations at the same time. You should definitely weigh the different indicators and pick the one that will have the most impact. The impact relevant to your plant might be different than the industry standard, and you should be choosing the performance indicator that aligns and contributes more towards improving your plant’s productivity.
Lean manufacturing is a production process ideology that emphasizes reducing wastage and improving productivity. This ideology finds its origin in Japanese manufacturing facilities and has gained acceptance across the globe. This is due to the effectiveness of implementing lean manufacturing principles to improve productivity.
The five core principles of lean manufacturing are:
1. engage only in the processes that add value to the end consumer. every other process is an excess and has to be eliminated.
2. Analyze the materials and processes involved in manufacturing a product by mapping out the value stream. This can be used to remove materials and processes that do not add value.
3. Improving lead times requires bringing down functional barriers. Create flow to carry out processes smoothly, with minimum delay and wastage.
4. manufacturing products without demand is a waste of time and resources. Create a pull system in the production process that initiates production only when there is demand.
5. embrace the philosophy of ‘Kaizen’, which means continuous improvement. You always have to find avenues to reduce wastage and improve efficiency.
Implement and completely adopt continuous improvement, and you will see gradual, yet compounding process improvements.
The lack of centralized information, and a lack of control over the information, is a challenge when the operations team wants to improve productivity. Information technology has tools to bridge this gap. It helps provide the right data at the right time — to analyze it and take appropriate actions. IT can be used for a wide range of applications in the plant, from work order management to deep supply chain integration.
A wide variety of IT tools are available for manufacturing plants. Some of the prominent tools are:
» manufacturing execution system (meS)
» Computerized maintenance management system (CmmS)
» enterprise resource planning (erP)
» Computer-aided design (CAD)
» environment, health, and safety (eHS)
» Inventory management software
Software tools help to centralize data and use actionable insights from the data to improve productivity. If you don’t have any digital tools in your facility, start your digital transformation journey immediately. Find the software tools that align with your requirements and your strategy to improve productivity.
one of the common problems that hinder productivity in manufacturing facilities are errors introduced by human employees. This significant dent in productivity can be overcome with the introduction of automated machines, which can perform operations without any human interference. The accuracy rate of automated processes is near perfect.
earlier, the cost of automation was high due to a lack of available technology. With improvements in technology, implementing automation has become affordable for most industrial facilities. Consider automating at least the complex process that come with high error rates.
The improvement from automation is not just the elimination of errors in processes. Automation helps cut down the number of employees required to complete a process. Hiring skilled employees is quite expensive in the current labor market. Automation helps in reducing the number of employees required, and cuts down operational expenses. Considering all the cost savings and process improvement, automation initiatives can break even in very
few years despite the high initial investment required.
material and people have to move through the plant to complete various processes in creating a product. The travel between different workstations increases production time. If your facility has a process b that comes after process A, and if the workstations for these are at separate corners of your facility, it takes a long time to transport goods between the workstations. This is productivity lost due to poor production layout design.
It’s possible to improve process efficiency and production time just by adopting a production layout that cuts down the travel time between different processes. execute a detailed audit of the existing layout and modify it to cut down distances between processes. You should not be taking a siloed approach at reducing the distance between consecutive processes. Instead, take a bird’s eye view to improve your production layout.
Participation of management and employees is essential in productivity improvement efforts. Put in the effort to make all the stakeholders understand the importance of improved productivity and how it can help them individually. You can organize workshops and seminars to drive home the message.
employee empowerment is critical for the success of productivity improvement initiatives. To achieve this, provide them with training and tools to align with the initiatives. You should also delegate some decision-making abilities to employees, and thus foster a culture of taking immediate action.
Improving productivity of plant operations is at the core of the mandate for operations teams across industries. This task has its own set of challenges, ranging from apathy to a lack of expertise. Take a proactive step, and convince all stakeholders of the importance of improving productivity. each initiative might be a small step towards improvement. but these small strides compound to create radical improvement for productivity, process, people, and profits.
b ryan Christiansen is the founder and Ceo of Limble CmmS. Limble is a modern, easy-to-use mobile CmmS software that takes the stress and chaos out of maintenance by helping managers organize, automate, and streamline their maintenance operations.
Tell us a little about yourself, Dr. Siebert, and Replique.
After finalizing my PHD in material science at the max Planck Institute for Polymer research, I worked for several years at bASF as the head of the data-to-value team. In 2020, I co-founded replique, and I am currently serving as its Ceo I’m passionate about new technologies, digitalization, and digital business models, especially in the b2b sector.
replique provides the first fully encrypted 3D printing platform that makes spare part management and the production of small series more sustainable. Combining our digital inventory and a network of additive manufacturing professionals, we offer an end-to-end solution from qualification to production and shipment.
Give me some background information on Replique and how it got to where it is today.
replique is the first fully encrypted digital inventory 3D printing/additive manufacturing (Am) platform that offers oems a secure and sustainable way of providing spare parts on demand, anytime, anywhere, to their customers.
We achieve this by combining our digital inventory platform with a global decentralized 3D printing network of qualified industrial Am professionals. via this combination, we offer oems an end-to-end solution from design to manufacturing and part shipment, which can be fully integrated into b2b processes like erP systems.
I think it’s relevant to mention the importance of our partnerships in progressing us to where we are today. Partnerships create mutual benefits and synergies that improve products for end-customers. In 3D printing this has proven to be a main enabler to scale industrial production. From our own perspective, close collaborations
are essential to achieving the best solution. An ecosystem where service providers, material producers, and print farms worldwide are connected is how we build a better service.
basically, replique is an attractive solution for everybody producing small series and having to serve the aftermarket. As a consequence, our customer industries range from transportation, automotive, construction, pharma, and healthcare up to consumer goods and heavy machinery business. In fact, everybody who has a large inventory and is in need to get a reliable part supply with efficient total cost of ownership fits into our scope.
We've seen how large-scale manufacturers benefit from additive manufacturing in terms of increasing production without compromising quality or reliability of the products. But in what ways do smalland medium-scale manufacturers benefit from this technology?
Small- and medium-scale manufacturers benefit from the same things you mention, as well as both timeand cost-savings thanks to the fundamental agility and efficiency-driving capabilities of Am when compared to traditional manufacturing methods.
For Sme s, the value-proposition for A m makes perfect sense and enables the production of low-volume parts quickly and cost-effectively – particularly valuable when it comes to spare parts. This is mainly due to the fact that additional costs are eliminated. With an on-demand production model and the use of a digital inventory, you can minimize your storage and related costs. moreover, you can reduce your transport costs and avoid administrative formalities with decentralized production. In the case of spare parts, you can further reduce the
downtime costs of your customers, as parts are available on-demand in case of machine failures. o ur customers are able to scale easily across country borders and have a large capacity and the most effective solution for every part on their fingertips. They do not need to spend a lot of time in onboarding and qualification of service bureaus. As we work with the best providers out there, we can always secure capacity as we bring relevant business to the service bureaus. o ur customers profit from the expansive experience we have gathered from all industrial cases we have worked on.
I think Am will continue to establish itself as the manufacturing technology of choice for companies large and small, and – as we are already witnessing – continue to take ground from existing manufacturing technologies that are inherently less agile, slower, and more costly insofar as total cost of ownership (TCo). I think the development of certain Am technologies will further drive this change; for example SAF technology that now enables the cost-effective production of much higher volumes of parts in the tens of thousands. Further, variable costs will decrease due to greater efficiency of printers. This will make
additive manufacturing more attractive for use cases where it was previously too expensive.
And as it always has, advancements in materials development will continue to push application possibilities even further, as specific products are created to answer the ever-exacting needs of manufacturers.
The digital nature of A m makes it easy to integrate into software processes and get rid of paper heavy processes in contracting but also quality assurance processes. As A m printers are advanced IIoT devices, we for example provide a full digitalized data recording of every job executed. Data collected with IoT objects on a machine can for example
Tailor made and standard
drilling
and in the
amount of cycle time
SUHNER
be used to automatically order parts via a digital inventory platform to produce needed spare parts in case something breaks. moreover, designs could be quickly improved and printed using collected data so you iterate designs much faster in the future, resulting in better customer offerings.
We continually improve the customer experience and add new features on our platform to provide our customers with an end-to-end solution. These are mainly quality assurance features and part screening services. We also are extending continuously partner integrations, as replique is an API-first designed platform. So, anybody wishing or offering an Am solution can be integrated in the digital warehouse services and connected to the parts in there. Stay tuned for more information!
What are some of the challenges associated with 3D printing or that you've experienced yourself in the industry or with customers?
The biggest challenge is to encourage customers to get started. most of the companies see the advantages of 3D printing, but especially traditional industries are still very conservative and focus on old and existing processes. moreover, the translation from traditional into 3D printed parts can be challenging. There is not always a material that can be directly translated into 3D printing. Finding the right material and technology mix as well as redesigning a part for 3D printing can decide between a success and a failure of a 3D printing project. once customers have recognized the benefits, customers accelerate in growth very quickly.
Can you give us a case study example wherein Replique helped a customer solve a problem they were experiencing via 3D printing products and/ or services?
replique is working with Alstom, a global leader in green and smart mobility, who uses our on-demand 3D printing platform to produce customized industrial-grade serial parts. b y digitizing its supply chain, Alstom can leverage decentralized production of small batches on demand. This enables the company to respond even better to its customers' needs. replique reduces the complexity within the supply chain so that first series are not only produced faster, but also cost-competitively. The growth in parts in the inventory now happens at a very low to almost zero cost: with the digital warehouse, no ‘safe stock’ and warehousing of parts need to be done. As a consequence, further customization is easily accessible for Alstom now.
In your opinion, what makes Replique stand out in the industry from its competitors?
Coming from bASF, we combine knowhow of industrial processes with material expertise. Compared to other
service providers, we not only offer access to 3D printing partners via our platform, but access to a whole 3D printing ecosystem. This includes a digital inventory, where manufacturers can safely store, manage, and order parts, consultation services, a worldwide Am expert, and production network, as well as the possible integration of e-commerce stores and other erP systems. In the end, no customer needs to change business processes, as we integrate seamlessly. We have gathered vast experience in industrial manufacturing and speak their language. In addition, we have patented parts of the platform which secure the quality of the produced parts.
The big sectors like aerospace, automotive, and medical have been deploying Am for many years, as has the manufacturing industry itself. However, we believe that any industry can benefit from the technology if utilized correctly. The problems 3D printing solves can occur in any industry, whether it’s consumer goods, agriculture, construction, mobility, or heavy machinery.
Some skeptics believe that 3D printing will never become an effective alternative to traditional manufacturing methods and will remain, at best, just a niche technology for special applications. What would you say to people who subscribe to this belief?
even injection moulding had skeptics 70 years back. At that time, using the technology to replace materials such as steel was not highly trusted. Furthermore, materials were scarce and infrastructure was missing in the beginning. There are many parallels with Am
As always, it is not only about the technologies itself but also the right processes to utilize its strength. If you produce parts still in large batches and send them to central warehousing, you will only half way benefit from the strength of A m . Going fully decentral in production is what will make A m interesting for any parts being produced in small quantities and we are certain that this long tail has a very large volume. Combining supply chain and production in one integrated solution will make A m very attractive.
In addition, more and more parts will be designed for Am from the very beginning, making a redesign superficial. It is a little bit of a generation thing: universities start taking up Am in their curriculum, and for the actual generations of engineers, it will be another production method standing equally side-by-side with the ones we know.
Tell me about the role 3D printing plays in "bridge manufacturing" and supply chains that are susceptible to disruptions.
When supply chains are hit, people responsible for manufacturing and supply chain need a responsive and versatile solution that brings speed and adaptability so
production can ramp up and down, switch gears or even shift to new locations. This has put the spotlight on 3D printing as it is the most viable option for bridge manufacturing, especially for industrial applications. once a part is qualified and print parameters are set, there are no ramp up delays as it can simply be sent securely to a 3D print service bureau for fast, cost-effective production. And as I’ve said, that means exactly where the part is needed, when it is needed, and in the precise quantity needed –even just a lot size of one.
You can even use Am as a backup if you see a digital inventory as a kind of insurance, which enables you to switch quickly between providers in case of a supply shortage. once set up, you are able to benefit from a large network with almost unlimited capacity. Just like the cloud has changed IT, this will change manufacturing towards more flexibility.
our goal is to become the leading and well-known partner for distributed manufacturing with our platform. Within the near future we want to grow our company with the help of investors and spin-off from bASF to scale further. To realise our goal, we are continually extending our network of material and production partners, as well as adding more features to our digital platform.
As mentioned, I believe partnerships within 3D printing are paramount to provide the best possible solution. Within 3D printing, we now see the need for a more holistic collaboration. Standards have to be developed together, printer and post-processing systems should be able to work together; and collected production data could lead to improved printers and materials. only with close collaborations and permanent exchange can those in the additive manufacturing sphere offer customers the best solutions. We closely work together with material but also printer and device manufacturers for the mutual benefit to address the market and provide customers the best possible solution. our material partnership for example is a huge enabler and a real asset.
I also believe that data management and ownership will be a huge topic moving forward. This is why replique carefully selects its production partners and takes the appropriate steps to ensure design data and other intellectual property is kept in the right hands. We enforce manufacturing parameters by encrypting the data, so parts can only be produced in the requested amount and material. b y collecting manufacturing data and analysing it, mistakes can be detected quickly, improving the process and ensuring all quality requirements are met.
Noise and distractions from machines. Welding fumes and chemical emissions. Heavy materials to lift and move. The potential hazards related to the metalworking and machining industry create a long list of major safety concerns.
SafeStart has been serving clients with solutions to increase personal safety awareness and skills for 25 years. According to the company, every employee’s reaction in any situation is primarily dependent on the adequacy of their training, company culture, their state of mind, and the safety of the working environment. They say that a company that is not investing in removing or mitigating existing hazards or providing protection against hazards that cannot be removed is failing its workforce.
According to optimum Safety management, a company that partners with clients to achieve best practices
in workplace safety management, those who manage metal fabrication facilities or other similar manufacturing facilities must have a thorough understanding of the unique industrial safety risks and how to combat them. It’s not optional since workers’ lives and well-being are at stake.
However, with the metalworking and machining industry, it’s difficult to develop elevated standards of safety because the work occurring on the floor is very high-risk. It’s important to know what the major safety issues of the industry are and best practices for dealing with them.
According to Thomas, a Xometry Company, a data, platform, and technology company that has become a leading resource for the industrial marketplace, material handling is a frequent cause of injury in the workplace. With
Sustained
occur.
posture, and
guarding mechanisms are important in preventing a worker's fingers from entering the metal trapping space of a cutting guillotine. If these safety guards are improperly installed, there is an increased chance of hand injury or finger loss.
metal pieces can lead to minor and major cuts or scrapes, and flying shards or sparks
also lead to impairments.
also be hazardous. In welding
of
workers may face
other emissions
chemicals, which can pose a risk particularly in spaces with
exhaust or poor ventilation.
employee
to unguarded or inadequately guarded
is prevalent in many workplaces, according to the occupational Safety and Health Administration (oSHA). because of this, workers who operate and maintain machinery suffer approximately 18,000 amputations, lacerations, crushing injuries, and abrasions per year; and there are more than 800 deaths each year related to inadequately guarded machines.
Thomas says that access to many areas and equipment should be prohibited in a metal fabrication shop and other types of machining facilities. Guardrails or other barriers should be used to prevent accidental entry. but poorly maintained or non-existent guards are among the most common causes of barrier-related injuries. For example,
According to optimum Safety management, most violations involve the requirements for design and construction. Lockout/Tagout violations are also common, as well as safety violations related to machinery. Some of the most dangerous machinery includes mechanical power presses, mechanical power-transmission apparatus, abrasive wheel machinery, woodworking machinery, and hand and portable power tools and equipment.
Personal protective equipment (PPe) is another important area to consider, and employers should determine what exactly is needed so that each individual employee can safely carry out each task required of them. In the metal fabrication industry, for example, common risks that can be mitigated by protective equipment include metal fume inhalation, airborne silica, molten metals, chemicals, heat, and falling hazards. These hazards may require equipment for respiratory protection, eye and face protection, hand protection, foot protection, and more.
Ultimately, SafeStart says that the working environment must be as free from hazards as possible, and all required guards should be installed and functioning. Guards and PPe should be inspected and checked regularly.
Thomas says that one reason why metal fabrication can be so hazardous is that there is the potential for inattentiveness due to noise or other distractions. This can result in a loss of concentration, leading to accidents.
Additionally, when employees feel rushed, frustrated, or fatigued, or if they’ve gotten used to taking shortcuts with their work, their chances of sustaining an injury increase substantially, according to SafeStart. The problem often surrounds the fact that a lot of the materials in the metal fabrication industry require manual handling, and the work conditions can be demanding. but when employees exhibit personal awareness of their physical surroundings and they are in a good state of mind, they are less likely to be injured on the job.
Safety training should start at the beginning of each employee’s time with the company, and they should immediately see a commitment to regular training updates, according to SafeStart. No subject is too small to discuss, but it’s difficult to implement a safety program without having buy-in from everyone at the organization, from those working on the floor to upper management. managers must lead the way by always following safety protocols and attending all safety training sessions. A successful program should instill a sense of accountability in workers and allow for a judgment-free way of addressing employee concerns. The goal is for everyone to understand, accept, and believe in the value of safety practices and standards.
Keeping Your Metalworking or Machining Shop Safe optimum says that the most effective method of keeping your metal fabrication shop safe is three-pronged:
1. Identification – To make your shop a safe workplace, conduct a thorough safety assessment to identify risks that need prevention. These risks are unique to your shop.
2. Prevention – once you’ve completed your safety assessment, come up with a prevention plan and implement the preventative measures for the risks that need to be addressed. This may work well using procedural steps within each risk area.
3. Safety culture – A transformative safety culture is needed to continually and successfully keep your employees healthy and safe.
Thomas offers additional best practices for the prevention of injuries, including the advice to always adhere to strict safety protocols. managers should also consider the following for workplace safety in metalworking and machining shops:
» If appropriate, install adjustable workstations that can accommodate different tasks and employees
» Limit or control exposure to harmful materials
» ensure that workspaces are uncluttered with a smart layout that reduces contact with dangerous areas or equipment
» Pay special attention to personal surroundings and physical exertions required by employees
» ensure the proper use of forklifts or cranes to unload heavy raw materials
» Have appropriate training regarding effective lifting methods
» Use trolleys to transport materials between stages of the fabrication process
» make sure ventilation systems work properly and provide PPe as needed
» regularly inspect any potentially hazardous piece of machinery to ensure necessary safety measures are in place
» Select hand tools based on the suitability of their design
» maintain a brightly lit workplace and avoid extreme temperatures in the shop
While the inherent dangers related to the metalworking and machining industry cannot be removed completely, focusing on safety from the shop floor all the way up to management is the best way to prevent injuries, protect workers’ health and safety, and keep your shop running as smoothly and efficiently as possible.
SOURCES:
https://www.optimumsafetymanagement.com/blog/metalfabrication-safety-how-to-keep-the-shop-safe/
https://safestart.com/news/4-major-safety-issues-metalfabrication-industry/
https://www.thomasnet.com/articles/custom-manufacturingfabricating/metal-fabrication-injuries/
https://www.osha.gov/etools/machine-guarding
Abb has launched its smallest ever industrial robot, offering new possibilities for faster, more flexible and high-quality production of wearable smart devices. With its compact size, class-leading payload and unrivaled accuracy, the new Irb 1010 offers electronics manufacturers the opportunity to increase their production of devices including smart watches, earphones, sensors, and health trackers through automation.
“The market for wearable smart devices is accelerating rapidly, with projections estimating double digit growth between 2022 and 2028,” said rui Liang, managing Director of Abb robotics’ electronics business line. “To meet this growth, companies are demanding compact robotic solutions that are suited to narrow production spaces in electronics manufacturing lines and that can accurately handle the small components used in wearable devices. As the most accurate robot in its class for 1.5kg payloads, our Irb 1010 meets these demands, enabling companies to maximize output and productivity while maintaining the highest levels of product quality.”
» New Irb 1010 designed to meet growing consumer demand for wearable smart devices
» most accurate robot in class for 1.5 kg payloads for highest manufacturing quality, 50 percent higher payload than comparable robots on the market,
» Consumes 20 percent less energy using omniCore e10 controller enabling manufacturers to improve energy efficiency, reduce costs
The Irb 1010 is designed to suit the narrow spaces and special purpose machines typical of electronics production environments. With a reach of 370mm and a footprint of 135mm by 250mm, the Irb 1010 is 30 percent smaller than Abb’s current smallest robot, the Irb 120. These compact dimensions increase the number of cells that can be fit into production spaces, enabling manufacturers to boost output through higher density factory layouts.
Capable of handling loads up to 1.5kg, the Irb 1010 has the highest payload in its class, with the ability to lift up to three times more weight than comparable robots. This increased payload capacity – coupled with a larger diameter air hose that provides added power for vacuum
suction – enables simultaneous handling of multiple objects, allowing more objects to be processed per hour. It also opens opportunities for new applications including film peeling, material handling, assembly, gluing and inspection.
Productivity is further enhanced by the inclusion of six braking systems, which allow the robot arm to remain in its position even when stopped. by eliminating the time needed for the robot to recover its position after a stop or pause, production can be resumed more quickly, enabling the Irb 1010 to do more in less time than other robots in its class.
Key to the Irb 1010’s high accuracy is Abb’s omniCore™ e10 controller, which offers class-leading position and path repeatability of 0.01mm. With its slimline design, the controller is well suited to small part assembly in applications where production cell sizes need to be minimized. The controller offers the flexibility to meet
changing requirements, with built-in digital connectivity and over 1000 additional functions enabling easy scalability.
Consuming up to 20 percent less energy compared to Abb’s previous IrC5C controllers, the omniCore e10 also enables manufacturers to cut their energy costs and improve energy efficiency.
Robot Control Mate makes programming simple
Programming the Irb 1010 is made simple with Abb’s robot Control mate. Available as an add-in to Abb’s robotStudio® programming software, robot Control mate enables users to move, teach and calibrate the Irb 1010 from their computer or mobile tablets without the need for programming skills.
This simple programming, together with the small size of the Irb 1010, also opens new possibilities for educational applications. The Irb 1010’s compact design makes it suitable for installation on classroom desktops, while its ease-of-use enables both teachers and students to quickly master the skills needed for programming and operation.
The addition of the Irb 1010 complements Abb’s comprehensive range of articulated industrial robots, with includes a full range of small, medium, and large options, including a growing family of collaborative robots that can be safely deployed alongside workers.
For more information, visit www.abb.com/robotics.
Abb robotics & Discrete Automation is a pioneer in robotics, machine automation and digital services, providing innovative solutions for a diverse range of industries, from automotive to electronics to logistics. As one of the world’s leading robotics and machine automation suppliers, we have shipped more than 500,000 robot solutions. We help our customers of all sizes to
increase productivity, flexibility and simplicity and to improve output quality. We support their transition towards the connected and collaborative factory of the future. Abb robotics & Discrete Automation employs more than 11,000 people at over 100 locations in more than 53 countries. go.abb/robotics
May
The
• Can be modified or made to
allows
Cosen Saws is one of the world’s leading band saw manufacturers with a diverse product line and a sales and service network covering all of North America. Cosen’s band saws deliver exceptional quality at a competitive price. They offer solutions for cutting applications, whether you are looking for an everyday, saw that can help automate your workflow or just a small band saw to keep in the shop for one-off cuts. Cosen Saws offers over 140+ reliable and dependable sawing options that are all configurable to help provide the best cutting solutions possible.
Cosen Saws will be exhibiting at booth b8629. During FAbTeCH, Cosen Saws will feature a variety of different band saw models including manual, vertical, and automatic saws. Cosen Saws experts will also be available for live cutting demonstrations and to answer any questions you may have in finding the perfect cutting solution for your shop.
The following metalworking saws will be featured during the event:
V-2026NC –Semi-Automatic Tilt-Frame Band Saw Capacity: 20" x 26"
Cosen's v-2026NC is a vertical tilt-frame saw built with the capability of cutting angles of up to 60°. The v-2026NC comes standard with an automatic angle adjust built into the HmI to help make the cutting process simpler. It is an excellent option for any fabrication production shop looking to transition into the vertical saw market.
G320 – Fully Automatic Horizontal Dual Column Band Saw
Capacity: 12.8" x 15"
Considered the premier saw of Cosen, the G320 is a combination of rigidity, state of the art software, technology, and affordability. The saw utilizes a true stainless steel dual column design and is perfect for cutting in high production settings. Paired with Cosen’s v_Drive technology, the G320 can easily improve operator efficiency and cut results, as well as help reducing cost per cut.
C-260NC – Fully Automatic, Horizontal Scissor Style Band Saw Capacity: 10.2" x 11.8"
The C-260NC provides every automatic feature needed in a scissor style band saw. It is very suitable for high production settings just like other Cosen automatic machines. The control system allows you to store 100 jobs and index up to 999". The C-260NC can help maximize your workflow efficiency due to its advanced capabilities and reliability.
SH-500M –Semi-Automatic Horizontal Scissor Style, Mitering Band Saw Capacity: 11" x 19.7"
The SH-500m is the most popular semi-automatic machine offered by Cosen. This machine can miter cut up to 60°. Whether cutting single or multiple pieces, this saw is able to meet the diverse needs of any job shop with its relatively small footprint. It has a large capacity and is easy to use making it perfect for a variety of materials and any operator.
MH-300DM – Manual Horizontal Scissor Style Band Saw Capacity: 9" x 11.6"
The mH-300Dm is a great smaller sized machine capable of cutting square, round, and rectangular solids, as well as tubing material. The saw comes equipped with a manual vise and adjustable hydraulic down feed. Perfect for the small to medium machine shop, maintenance shop, metal fabricating shop, school, or just for limited run production work. Its heavy duty construction ensures years of reliability and accuracy at a high level of performance.
x 22"
In an ever changing and growing fabrication
the need for cost effective cutting
different capacities and
points is evident. With the growing popularity of vertical saw design, Cosen’s v-1822 takes the renown tilt frame-design and applies to a reliably constructed yet small footprint. The manual
control the cutting angle
13" x 20"
The C-510mNC is a high production, fully programmable, automatic miter cutting band saw. It is a heavy duty machine that fits the needs of any
to 60°
manufacturing environment with its diverse capabilities and user friendly controls. make cuts of up to 60° and program up to 100 different jobs with the C-510mNC.
Since its establishment in 1976, Cosen Saws has grown into one of the world’s largest professional band saw manufacturers. Today's Cosen manufactures over 100 models including manual, semi-automatic, fully automatic, and NC band saws that are capable of cutting anywhere from 200mm (8") to 2000mm (78") in capacity. Cosen aims to go above and beyond in terms of customer service before, after, and during your purchase and they are always here to support you. With a record of more than 82,000 band saws sold within five continents, Cosen Saws markets expand internationally to over 80 countries through authorized distributors for the metal cutting industry with help from offices in Taiwan and europe.
When it comes to training, many manufacturers start off strong. employers implement a formal onboarding program to immerse new employees in company culture, teaching them the skills and knowledge they need before setting out on their own.
but that’s where training falters. From there, employees are often left to navigate a web of informal learning and development tactics, in the form of job shadowing and tribal knowledge sharing.
In fact, according to Tooling U-Sme’s mission Critical: Workforce 2021 report, three out of four manufacturers (75 percent) say their company doesn’t offer a structured training program on manufacturing skills.
The consequences are varied and disastrous: high turnover, low morale, safety concerns, reduced productivity, and sluggish growth.
In contrast, high-impact learning organizations (HILos) understand that successful learning programs are continual, moving from day one through all talent management processes. They reap the benefits and tend to significantly outperform their peers in productivity, customer satisfaction, quality and other metrics.
It’s important to remember that training is not just building a worker’s performance level — it’s also ensuring the employee stays at the desired performance level. Continuous education and performance support need to be part of every learning and development strategy to build company productivity and profitability. If that isn’t incentive enough, take a look at the five reasons training must go beyond onboarding.
A study at the University of Warwick found that happiness led to a nearly 12 percent increase in productivity. How can you cultivate a positive vibe? Start by building a learning culture.
A strong training program assures employees that a company is investing time and money in their development, which boosts morale and productivity. This, in turn, helps improve retention.
In fact, people often cite lack of professional development as a reason for leaving their jobs. A survey by Paychex showed nearly one in three people (29 percent) left their previous job due to lack of skills development. 1
Investing in your employees by providing formal programs with defined job roles, clear career pathways, and a competency-based training curriculum can ensure you retain a long-term, productive team.
A direct benefit? In addition to avoiding the financial and cultural costs associated with departing employees, reducing turnover can positively impact customer satisfaction. That means your happy workers can develop happy customers, growing your company in the process.
Without ongoing training, employees suffer a decline in skills. Worker competence and performance diminish over time.
To counter this, a continuous education or performance support initiative must be built into a learning and development strategy. For instance, to validate a worker’s continued ability to meet organizational performance requirements, a requalification strategy may be necessary.
michael munday, Ceo of Arwood machine Corp., in Newburyport, massachusetts, explains it this way: “Someone may claim to have 20 years of experience, but it could be one year repeated 20 times. If there is no training, they haven’t learned anything new.”
munday should know. After losing a long-time customer because the company was unable to hire enough skilled workers to fill a large order,
munday worked with Tooling U-Sme to create a training program that would develop new employees and sharpen the skills of incumbent workers. This was a critical part of the company’s growth plan. Within a short time, the company saw a 10 percent upward trend in productivity. In addition, scrap cost as a percentage of sales was at a lower level, and defects were down. on the other hand, morale was up.
The pace of technology has never moved faster, and it will continue to accelerate. In fact, it inspired futurist and author ray Kurzweil to develop a theory called The Law of Accelerating returns. As tools improve and become faster, the subsequent generation of tools becomes that much faster and better. Growth becomes exponential.
manufacturers need to anticipate and plan for this change — and train their employees to embrace it as an opportunity.
In a recent op-ed in The Wall Street Journal, authors michael milken and Igor Tulchinsky write about how digital innovation and robots are opening new possibilities for workers across the U.S. economy: “enlightened manufacturers are minimizing layoffs by preparing assembly-line workers for higher-level duties, while relegating routine tasks to robots and AI programs.”
Change is inevitable, and it’s the obligation of manufacturers to invest in their employees through continuing education that will prepare companies — and their employees — for success into the next decade and beyond.
As munday of Arwood said, “Technology is advancing dramatically, and to keep moving forward, the key is continuous improvement around equipment, processes and employees.”
more than ever, customers expect their business partners to at least keep up with them in terms of manufacturing advancements and solutions — if not to lead the way. A well-trained team with a continuous improvement mindset is inherently going to provide the innovation and forward thinking that customers need and demand.
by fully understanding equipment and available technology, team members connect dots and come up with more efficient approaches, new product ideas and more. Cross-training employees for a variety of jobs through
a blended learning program enhances productivity and efficiency. It also helps employees approach problemsolving from multiple angles, leading to fresh thinking.
Take lean manufacturing, an overarching business philosophy that drives sustainable improvements and results within an organization. This continuous improvement approach is often overlooked when it comes to learning and development. Yet, as training supports the overall business goals of an organization, it is a natural and needed extension.
For instance, KYoCer A SGS Precision Tools, Inc. (KSPT) is a lean manufacturing organization that supports continuous training and development improvement by mandating an ambitious 50 hours of training per associate per year.
As Gary miller, director of training and occupational development, said, “our training philosophy is to train as much as you possibly can and use a blended approach, including computer-based instruction and on-the-job training.”
even after more than six decades in business, KSPT continues to grow, recently adding a new manufacturing facility. For continued growth and innovation, building a well-trained team of high performers remains a business priority for KSPT, whose employees have an average tenure of 14 years.
baby boomers are retiring at a pace that outruns hiring. In fact, 14 percent of respondents in Tooling U-Sme’s Workforce 2021 Assessment said they will lose a full quarter (25 percent) or more of their workforce to retirements in the next five years.
The predicted “silver tsunami” is here, and there is no time to lose when it comes to transferring knowledge from seasoned workers to younger members of the workforce.
Desperate to ensure that these newer workforce members will be able to perform the work of experienced employees, maintain production and understand customers, many companies are looking at formalized plans that include an internal mentoring and training program.
This changing of the guard presents the perfect opportunity to reflect on existing learning and development programs and revamp them to attract, develop and retain millennials and the upcoming generations.
It is true that millennials bring unique differences to the workforce. After all, they are shaped by their
Companies that take a fresh look at their training and development approaches, creating structured and measurable programs, can ultimately elevate the performance of everyone in an organization — not just millennials — leading to loyal employees and stronger business results.
A strong onboarding program creates a solid bond with employees from day one. but training and development can’t stop there. As world-class manufacturers know, an ongoing standardized learning and development program that is methodical, visible and tied to the bottom line will provide manufacturers with a competitive advantage for years to come.
1. “ employee retention: What makes employees Stay or Leave?,” Paychex Wor X, Aug. 2016.
free, expert, no obligation, online technical resources are now available to answer questions prior to project bidding or purchasing new equipment.
Machine shops that have historically lacked unbiased, expert guidance on selecting better tooling for their specific applications now have online access to comprehensive resources that cover the breadth of the marketplace with no strings attached.
In the industry, smaller machine shops face challenges not only in the wide range of applications and materials they encounter but also in selecting the tooling that will best accommodate it.
“I’ve seen many machine shops essentially over-spec the tools they need for a new project, and it is costing them a lot of money,” said Lermit Diaz, founder and Ceo of SCTools, a michigan-based national distributor to machine shops. “It can work the other way too, where the machine shop ends up not getting the best tool for the job, costing them time and material to make it work.”
Unlike an oem, which may dedicate a machine to a single material or to one operation, smaller CNC machine shops survive by being able to machine a variety of materials for customers across diverse sectors such as aerospace, medical, semiconductors, electronics, automotive and general parts.
“A machine shop may be cutting stainless steel one day, forged steel the next, and then have an order for aluminum parts,” said Diaz. “Flexibility is important, but it is very difficult for a smaller shop to stay current with the latest information on all materials and all styles of machining. They don’t have the margins the large oems have to hire a
mechanical engineer or purchase separate tooling for every material machined.”
The idea to develop free online resources to assist small and medium-sized CNC machine shops came from the questions that Diaz would get from customers. “ every time I visited customers, they asked a lot of questions. They might not know how to do a specific job, or they wanted to know how to do it better. That sparked the idea to provide free online machining resources for the industry.”
Diaz wanted to fill an education gap that he saw when looking at the traditional relationship between a shop and their distributor.
“So many shops go to a distributor website and order several different tools, cutters, or inserts and still don’t achieve the desired [machining] result. They may also run the tool on the machine incorrectly. That means they are spending money hand-over-fist because they are purchasing tools they don’t need, and instead of getting five to ten parts per cutter, they might get one.”
To empower smaller CNC machine shops to make the right decisions on their machining orders, Diaz created TechTips, a free online resource where questions can
be answered before they bid on projects and purchase new equipment. The website page was created solely for educational purposes to assist small and medium-sized CNC machine shops, with no obligations to purchase from the distributor that hosts the content, SCTools. For those that simply want to call in and get questions answered, the support staff at SCTools has extensive knowledge and often hands-on machining background that includes operating equipment and programming.
The online resource is a significant database of technical knowledge. Since launching the TechTips database, it has grown to over 1,500 electronic pages of resources for the machining industry with plans to expand it to 2,000 pages by the end of the year. The database continues to increase its glossary to facilitate topic searches. Content areas include turning, milling, drilling, tapping, metals, calculation & programming, and grinding. To give an example of just how detailed this resource is, a section on how to machine the most common materials in the market is over 700 pages.
For those interested in new developments in the industry, a weekly e-newsletter called TechTalk from SCTools also provides content on a wide range of topics including machining, grinding, cutting tools, metals, and coatings.
When founding SCTools, Diaz wanted to challenge the traditional role of a distributor.
“Traditionally distributors will serve you if you have a part number,” said Diaz. “Instead, the focus should be on the customer’s application to identify just the tools they need. There are many distributors that CNC machine shops can go to if they just want to order a part and have the order filled. Instead, we are trying to be more of a resource for the smaller machine shops, a partner to go to for advice and help.”
According to Jason Huo, m anager at Cold Forging, Dyna-m ig, a division of F&P mfg., Inc: “In choosing tooling options for the development of a new model, we have definitely benefited from relying on expert guidance rather than resorting to lengthy, more costly trials.”
o nline resources that make a wide span of technical machining knowledge available to small and medium sized machine shops are enabling them to make better decisions as they take on new projects. In the process, the traditional relationship between machine shop and distributor is evolving to be more of a partnership.
For more information on the free online machining resources, visit the TechTips page at https://sctools.online/pages/ machining-techtips.
Del Williams is a technical writer based in Torrance, California.
Predictive and periodically scheduled maintenance can extend the life of valuable equipment. This month, iMD highlights the strategies to determine when it’s best to rebuild, retrofit with new technology, or replace outdated machinery.
By: Chris Williams is Sr. Manager, Customer Care at Yaskawa America, Inc. – Motoman Robotics DivisionAdvanced technologies, including high-performance robots, continue to build automation confidence and positively impact operational efficiency across the industrial landscape. To sustain a high level of productivity and associated cost savings, company leaders are implementing proactive measures to maximize robot reliability and safety – as fixing a critical asset once it breaks or addressing safety concerns after an unfortunate incident, is not a plan. Key steps manufacturers are taking include:
While today’s robots are extremely reliable and comply with stringent safety standards, each should have a well-maintained life cycle. Whether for installation, upkeep, continuous improvement, or retrofitting or redeployment, manufacturers should follow strict guidelines and maintenance schedules to facilitate peak performance. To better maintain the needed robot functionality, company leaders are placing greater focus on continuous improvement via data collection, and many are turning to factory automation monitoring systems that can instantly track, accumulate and visually deliver data throughout networked production environments.
Leading asset management platforms enable data-driven optimized planning for preventative and predictive maintenance, enabling proactive decisionmaking for more productive factories. From knowing when to order parts for future maintenance or when to change consumables for a weld process, to tracking the velocity of product movement for optimal bin assignment during a pick and pack process, these integrated solutions provide a wide range of alarms and prompts to keep operations running smoothly. Proven edge server platforms that use a leading oPC-UA interface, such as Yaskawa Cockpit™, support multiple brand devices, including robots and their peripherals, and collect information in real time to achieve this.
A robot provides the greatest reliability when it is well-maintained. That said, most Tier 1 suppliers work diligently to keep their robot performance near a 99% efficiency rate, creating and executing a stringent
maintenance strategy that seeks to eliminate breakdowns before they happen. While a one-size-fits-all approach to robot maintenance does not exist, completing preventative maintenance checks at regular intervals can help optimize robot performance for the utmost safety.
To minimize the deterioration of the asset and maximize robot uptime, measuring a combination of robot levels is suggested. From overall performance (where items such as path accuracy and part quality are tracked) to internal functionality (where things like grease levels, torque and cabling are monitored), there are multiple factors to consider. Attention should also be given to robot controller performance.
often a marker for when upkeep is required, checking the condition of the gear reducers is a frequent maintenance test manufacturers use. This process typically includes:
» Grease Analysis – A routine grease analysis for each axis serves to keep iron levels in range, as a spike could be indicative of a damaged drive. The type of grease to be used should always be referenced in the robot manual.
» Manual Test – This test entails jogging the robot to reveal problem areas such as vibration and gear noise. As with other tests, this test may be helpful in determining whether a reducer is failing or has completely malfunctioned.
» Torque Analysis – Typically performed by the robot brand manufacturer, this test measures the torque of the motors, looking for indicators that might show inconsistencies in the robot motion. A spike in the data generated during this procedure will typically reveal any inconsistencies.
» Backlash Test – Also commonly performed by the robot brand manufacturer, this procedure uses a dial indicator to determine the amount of backlash in the gear reducer. For accurate readings, the robot and dial indicator are placed in a specific location.
While these checks do not need to happen as a collective, each should be utilized, as needed, to determine robot function. Keep in mind, maintenance intervals are based on servo hours (tracked in the robot), and it is typically performed every 6,000 servo hours. As always, individuals should reference the robot manual for guidelines specific to the model in use.
Whether a manufacturer assumes full responsibility for any of these tests or relies on scheduled visits from the robot manufacturer, there should be a clear plan in place that designates leadership, best practices, inventory strategies and action steps for reaching specific goals. If external technicians or contractors are required to complete specific tasks, scheduling should be accomplished at least six months in advance to accommodate busy schedules.
especially helpful for 24/7 operations that may not be able to completely close for a scheduled shutdown, a growing number of manufacturers are stocking spare parts on-site to avoid long lead times for parts delivery. In this instance, historical data is often relied upon to know what parts may be necessary in the future. Commonly stocked items (with average replacement intervals) include:
» Controller CPU battery – replace every three years
» Controller air filter – replace annually
» Controller fan unit – replace every three years
» Gaskets / Gasket covers – replace every three years
» Connectors – replace, as needed
» Seals – replace, as needed
» Cables – check frequently and replace, as needed
» Teach pendants – test frequently and replace, as needed
» Gear oil – replace every other year
» Grease for bearings and pertinent parts – monitor often and re-grease, as needed
Part of a smart inventory strategy is to hold an annual planning session with a customer service representative from the robot brand manufacturer. This will serve to answer any questions and address other areas of maintenance that may have been overlooked.
While all manufacturers should take proper precautions for robot operation and maintenance, companies that take a DIY approach should be especially careful. In fact, it is critical for robot programmers and maintenance staff to have the proper training to do the job correctly. Courses taught at an International Accreditors for Continuing education
and Training (IACeT) accredited facility, such as Yaskawa Academy, are ideal. These locations provide hands-on instruction in application-specific classrooms with leading technologies, ensuring robot uptime and worker safety for a better return on investment (roI). Supplemental training and support for robot maintenance, troubleshooting and repair can also be gained through user-friendly, yet comprehensive, web-based solutions, like robotPro®
The uncertainty to retrofit a robotic system is common. From downtime to cost, there is a lot to unpack. While concerns about low quality parts have been valid in the past, decision makers can gain confidence in the fact that technological advancements and safety standards have greatly improved part quality in recent years.
When smaller components, such as a power source or weld torch fail to deliver the desired quality, or something becomes a potential safety risk, the decision to retrofit is easier. When faced with the choice to add a robot to a current workcell or upgrade all together to meet throughput demands, things can get complicated. regardless, an appropriate option can usually be agreed upon over the phone with the robot supplier or integrator.
In some cases, a representative from the appropriate vendor may need to make a site visit to determine the best retooling and equipment options to meet application requirements. Likewise, if a retrofit is being considered for a safety issue or a process change, a risk assessment may be required – as the American National Standards Institute (ANSI) safety standards must be followed and should be paramount when making any retrofitting decision.
When mulling over the decision to retrofit versus a complete upgrade, manufacturers should also consider the concept of using certified pre-owned robots. A growing trend, this option is often more affordable for small job shops and medium-size companies.
Planning for repairs and retrofits is crucial to achieving long-term corporate goals, especially for suppliers with lights-out operations. From creating a monetary budget to applying the lessons learned from prior projects, a comprehensive plan with full directives should be followed. While doing this may seem excessive or unrealistic to some manufacturers, maintaining equipment and applying new technologies, when needed, can prevent costly breakdowns and unnecessary downtime.
A large part of executing a solid life cycle management program with preventative maintenance is having access to diverse support services. Whether 24/7 technical support is needed to diagnose a problem remotely, a field service technician is needed for rapid on-site support, or an emergency part is needed in the middle of the night, a committed robot supplier or integrator with skilled technicians goes a long way to maintaining safe operations and meeting production goals for maximum roI.
According to the definition given by the U.S. environmental Protection Agency (ePA), sustainable manufacturing is “the creation of manufactured products through economically-sound processes that minimize negative environmental impacts while conserving energy and natural resources.” It also enhances employee, community, and product safety. The ePA says that an increasing number of manufacturers are realizing substantial financial and environmental benefits from sustainable business practices.
but how sustainable is it really, why is it necessary, and how practical is it for small-to-medium size manufacturers?
When we talk about environmental impacts, we are referring to several resources, such as energy, material, solids, air, and water. According to the U.S. energy Information Administration’s International energy outlook 2019, the manufacturing sector consumes around 40% of global
energy. This is more than 80% of the world’s industrial energy use, making it the largest energy consumer within the sector. more specifically, machining processes such as turning, grinding, milling, and reaming contribute to a significant fraction of this energy use. machining has a large environmental footprint due to energy and resource use since it involves the process of removing or cutting away material. Turning, the removal process of material from a rotating/cylindrical workpiece is the most prevalently used and significant machining technique. It uses a considerably larger amount of energy than other machining operations.
According to Nabil Nasr, associate provost and director of the Golisano Institute for Sustainability at rochester Institute of Technology and Ceo of the remade Institute, experts say that if we continue along the path we’re on, greenhouse gas emission will likely increase by 43% by 2060. but by implementing effective sustainability measures across the globe, we could reduce greenhouse gas emissions by a significant percentage, possibly as much as 90%.
While it may have started with big business, sustainable manufacturing has evolved to include benefits for newer manufacturers, start-ups, and other small-to-medium size companies. These often have more flexible business models and they may rely less on long-established methods or ways of doing things. This allows for opportunities to innovate and change quickly when it comes to sustainable practices.
In fact, a growing number of companies are treating sustainability as an important objective in their strategy and operations to increase growth and global competitiveness, according to the ePA. Companies engaged in sustainability efforts include those of all sizes, ages, and sectors. In many cases, their efforts are having significant results, and they are seeing key benefits such as:
» Increasing operational efficiency by reducing costs and waste
» responding to or reaching new customers and increasing competitive advantage
» Protecting and strengthening sales as well as brand and reputation
» building public trust
» building long-term business viability and success
» responding to regulatory constraints and opportunities
» Lowering resource and production costs
» Lowering regulatory compliance costs
» Increasing access to financing and capital
» Finding it easier to hire and retain employees
one of the biggest considerations that can be difficult, especially for small-to-medium size manufacturers, is the transition to achieve more sustainability. While it should ultimately save the business money, it can cost a significant amount in the short term. The transition typically requires not only the implementation of new manufacturing processes, but also the ability to design and build the technology and machinery needed to support the new sustainable practices. However, in some areas, there may be tax benefits available that can help offset the costs of the transition.
The switch to sustainability can also lead to higher costs in the production process or elsewhere in the facility. A manufacturer who changes suppliers to buy only sustainably made products will likely have to pay a premium price. The higher costs must be passed on to customers or it will mean a smaller profit margin for the manufacturier.
The ePA says there are several ways in which companies can progress further on the path to sustainability:
» Address sustainability in a coordinated, integrated and formal manner, rather than in an ad hoc, unconnected, and informal manner
» Focus on increased competitiveness and revenues rather than primarily focusing on cost-cutting, risk reduction, and improved efficiency
» Use innovation, scenario planning, and strategic analysis to go beyond compliance
» Integrate sustainability across business functions
» Focus more on the long term
» Work collaboratively with external stakeholders
While Nasr has seen instances where the indicators were there and businesses identified approaches to increase sustainability, manufacturers don’t always follow through with the plans. but because there’s been so much progress in learning about the right path forward, he continues to be optimistic about moving in the right direction for sustainability.
SOURCES:
» https://www.epa.gov/sustainability/sustainable-manufacturing
» https://www.eia.gov/outlooks/ieo/pdf/ieo2019.pdf
» https://theconversation.com/how-sustainablemanufacturing-could-help-reduce-the-environmentalimpact-of-industry-185672
» https://www.oecd.org/innovation/green/toolkit/ aboutsustainablemanufacturingandthetoolkit.htm
» https://smallbusiness.chron.com/advantages-disadvantagesgreen-manufacturing-businesses-22312.html
and dual frequency AC coils can be rotated to locate connectors to your need. DIN, Deutsch Flying Leads and Wire Box Connection are available as standard Manual Override. Full line of Sandwich Controls.
FIVE SERIES OF VALVES RATE TO 5000 PSI: RPE3-04, providing 8.0 GPM; RPE3-06, providing 21.0 GPM; RPE4-10, providing 37.0 GPM; RPE4-16, providing 80.0 GPM; RPE4-25, providing 160.0 GPM
GEAR PUMPS: Argo-Hytos gear pumps provide high reliability, high volumetric efficiency, and low noise levels over the entire operating range.
THREE SERIES: GP1-P, maximum pressures from 2300-4350 flows 1.0 gpm; GP1-T, maximum pressures from 1700-4200, flows 1.0 to 17.0 gpm; GP1-Q, maximum pressures from 2900-4500, flows 7.1 to 42.8 gpm.
FAbTeCH provides a convenient ‘one-stop shop’ venue where you can meet with world-class suppliers, see the latest industry products and developments, and find the tools to improve productivity, increase profits and discover new solutions to all of your metal forming, fabricating, welding and finishing needs.
www.fabtechexpo.com
Cosen Saws can help find the right cutting solutions for your application at FABTECH 2022. Cosen Saws is one of the world’s leading band saw manufacturers with a diverse product line and a sales and service network covering all of North America. Cosen’s band saws deliver exceptional quality at a competitive price. Whether you are looking for an everyday saw that can help automate your workflow or just a small band saw to keep in the shop for one off cuts, with Cosen Saws 140+ reliable and dependable options are all configurable to help provide the best cutting solutions possible. Cosen Saws will be exhibiting at booth b8629. During FAbTeCH, Cosen Saws will have a variety of different band saws including manual, vertical, and automatic saws on display. Cosen Saws experts will provide live demonstration on the machines and available to answer any questions you might have on finding your ideal cutting solution no matter the industry.
Leading machine tool manufacturer to unveil the industry’s newest cobotic welding technology at the show.
We’re living in a digital world, and CINCINNATI® Incorporated (CI) puts digital innovation on full display at FAbTeCH 2022 (November 8-10, Atlanta, GA). Attendees can visit CI in booth b7909 in Hall b of the Georgia World Congress Center, to explore some of the latest metal
fabricating equipment and software solutions – including the industry’s newest cobotic welding technology. Additionally, CI service representatives will be available to discuss the company’s aftermarket options including training, machine upgrades, and more.
marketing manager, Nikki Stenzel explained that the event offers a unique opportunity to witness CI’s integrated design to part manufacturing environment.
“With its extensive collection of fabricators, machinery, software, and service providers, FAbTeCH is North America’s premier metal fabrication event. And we’re excited to show the industry what CINCINNATI is all about,” said Stenzel. “Attendees will have an opportunity to see our encompass by CI software suite followed by bending and welding demonstrations as we take a part from 3D design through all phases of manufacturing. Needless to
industrial Machinery Digest's on exhibit features the latest news and press releases from companies exhibiting at the leading trade shows across north america.
say, anyone looking to enhance shop floor efficiency through automation should make it a point to see what CINCINNATI has to offer.”
CINCINNATI’s encompass software is dedicated to helping operators tackle projects with greater speed and quality. And today, using digital twins, one moves from the digital part to the physical part accurately and efficiently. The encompass by CINCINNATI suite includes:
» Design: From 3D models, accurately import geometry and identify the correct flat blank.
» Nest: Amplify your ability to nest your laser parts with software automation and create optimized machine code to make your Cincinnati laser (and most other lasers) operate at top performance.
» bend: Supercharge your offline press brake programming with advanced software automation.
» Schedule: Take the stress out of scheduling by automatically scheduling multiple jobs across multiple shifts and multiple CI lasers.
» Automate: Advanced software for
robot-tended press brake bending cells. Feature-rich simulation capability ensures collision-free solutions and the generation of efficient programs for both the robot and the press brake.
» Analyze: Get real-time and historical insight into the productivity of all your CI machines anywhere, from any device with CIberDash.
Nobody does press brakes like CINCINNATI, and our Autoform line combines precision forming with leading-edge features and control technology. The 60-ton Autoform+ with 6-Axis backgage provides all the benefits of a hydraulic press brake in a smaller footprint and will be our featured press brake at the show.
FAbTeCH attendees will be among the first to experience the industry’s newest cobotic welding technology.
A cobot, or collaborative robot, is a robot intended for direct human-robot interaction within a shared space. Simple to use and easy to program, the CINCINNATI Cobotic Welding cell is the first of its kind for TIG welding. With a
working range of 2400 mm x 1200 mm (approx. 4’ x 8’) the automated system is suitable for large or small production batches. The cell is compact, easily repositioned, and contains advanced adjustable safety devices including the continuous robot elbow monitoring.
Dynabrade is proud to introduce a new line of 1.3 HP Air tools. These new high quality air tools are available as a rightAngle Disc Sander and a right-Angle Depressed Center Wheel Grinder.
Available in 4”, 4-1/2” and 5” diameters, the tools are excellent for fast stock removal, metal clean up prior to welding, removal of weld beads and various material removal applications. The Depressed Center Wheel Grinder is available in either 12,000 or 13,500 rPm . The grinder is ideal for use with Type 27 Grinding Wheels. The 1.3 Hp Disc Sander, available in 12,000 rPm is for use with a wide variety of coated abrasives.
The tools feature a governor assembly for maintaining rPm under load. Also included is a safety-lock throttle to prevent accidental start-up and a Spindle Lock for fast, easy abrasive/wheel change. A Two-Position Side Handle for left or right-hand use is included. This vibration-dampening handle also reduces vibration to the operator’s hand. This line of air tools was also designed with a Wick Lubrication System, which extends gear life when the tool is properly lubricated with gear oil. Also included is a 360° rotational exhaust for directing the exhaust away from the operator. The Depressed Center Wheel Grinder also includes a safety guard and wheel flange kit. 3/8”-24 and 5/8”-11 spindle models are offered. made in the U.S.A.
eSAb Corporation announced today the launch of InduSuite (InduSuite.
ESAB Launches InduSuite: A Brand-Agnostic Workflow Software Portfolio Solution for Robotic, Welding, and Cutting OperationsNew Line of 1.3 Hp Air Tools from Dynabrade Feature Right Angle Grinders and Sanders
com), a brand-agnostic portfolio of software applications that revolutionizes workflow, quality, and business performance, to help fabricators and manufacturers improve operational efficiency. InduSuite offers three key benefits for mixed fleet customers: simplicity for accessing data and documents with an easy-to-use interface; real-time insight into performance, traceability and workforce accountability; and an unprecedented level of control over metal fabrication operations.
“The InduSuite portfolio helps our customers improve efficiency and quality at every step of the fabrication process, from plate to finished product,” says Jon Hofmann, Director Product Development, InduSuite. “For example, one of our customers, an Italian manufacturer of agricultural equipment gained 6,000 more hours of welding time, a Finnish manufacturer of mining equipment increased arc-on to 20 percent (about double the industry average), and a brazilian petrochemical giant saved thousands of hours of engineering time while improving weld quality and reducing risk.”
Cloud-based InduSuite solutions include WeldCloud Productivity, WeldCloud Fleet, WeldCloud Notes, and CutCloud for cutting data analytics. Installed InduSuite software applications include CoLUmbUS CAD/CAm nesting software for automated cutting and oCToPUZ for offline robot programming. These apps enable users to improve operational efficiency through:
» ensuring compliance by developing welding and cutting procedures in accordance with standards and regulations.
» Improving productivity with offline programming of robot, welding, and cutting.
» Tracking and analyzing welding and cutting productivity, quality, and consumables usage.
» maintaining fleet equipment in optimal working conditions.
» Accountability and oversight of all key welding and cutting activities.
The cloud-based applications feature an intuitive interface that enables users to be up and running after an hour of training without IT expertise. The applications function on a common platform built with state-of-the-art microsoft Azure, which is among the most secure and reliable cloud architectures.
InduSuite offers solutions suited for operations of all sizes, from small fabrication customers to large companies with fleets of equipment spanning multiple countries. This collection of cloud-based and installed software applications connects equipment and data across all brand platforms so companies can take total control of their operations.
Flextur announces the launch of its robotic and cobot workstations to help manufacturers achieve maximum efficiency. The workstations are available as a standard solution or custom engineered solution.
robots and cobots are becoming more and more popular in manufacturing facilities as companies adopt automation and Industry 4.0 technologies. robotic/Cobot technology integration alleviates challenges such as labor and skill shortages and replaces humans in mundane or repetitive tasks allowing them to be available for highervalues activities. Additionally, robots and cobots perform tasks faster and with greater strength, accuracy, and data capabilities.
To keep up with the increased production, organizations must utilize lean methodologies to create greater efficiencies and ensure consistent throughput when working with robots and cobots. This is especially important with cobots. Workstations should be set up with all of the proper tools and materials within reach to maintain efficiency and keep up with the cobot’s output.
“This new launch adds to the versatility of Flextur workstations. our tables and carts are durable and stable enough to hold any robotic arm while also providing the opportunity to create a lean/5S workstation. Flextur is here to help our customers achieve maximum efficiency, greater production and throughput, and solve labor and skill shortages,” says Pioneer Corp Ceo Daniel Wengerd.
Flextur partners with robotic and cobot manufacturers to develop workstations with existing robot systems and to create cobot stations with a Flextur table or cart to anchor the cobot arm. Some of Flextur’s current automation partners are Yaskawa, oTC, KC robotics, as well as many others.
Hypertherm Associates heads to FABTECH 2022 with all new Hypertherm plasma, OMAX waterjet, and software products Hypertherm Associates, a U.S. based manufacturer of industrial cutting products and software, is preparing for FAbTeCH 2022, North America’s largest fabricating, welding,
and finishing exhibition. The company’s Hypertherm and omAX technology brands will welcome show visitors from two halls at Atlanta’s Georgia World Congress Center on November 8, 9, and 10.
The Hypertherm and omAX technology brands will exhibit from one combined booth to offer show visitors a comprehensive array of plasma and waterjet products. visitors to booth b8309 will have an opportunity to see the world’s only X-Definition plasma and a new HPr cartridge for HPr XD plasma systems. In addition, they can see the optimAX, considered the world's most accurate waterjet, along with the ProtomAX, a compact, self-contained cutting system perfect for prototyping and low volume cutting. Hypertherm Associates will also feature its ProNest CAD/ CAm nesting software, providing show visitors with live demonstrations of its recently released ProNest 2023.
Powermax air plasma products, including the innovative Powermax SYNC plasma with built-in intelligence and a single-piece consumable cartridge, will be available in booth C11237. Attendees will have the opportunity to try the Powermax SYNC and its SmartSYNC torch. They can also meet metal Artist, T v Personality, and Author rae ripple who plans to unveil her newest creation, an intricately cut vintage car hood that she made with her Powermax65 SYNC.
Finally, Hypertherm Associates will exhibit its robotmaster offline programming software for robots from booth C10827. The robotmaster team will demonstrate new software that bridges the gap between CAD/CAm and robotics by enabling seamless integration between a user’s chosen CAD/CAm software and robotmaster.
“We are excited to return to Atlanta for FAbTeCH 2022,” said Kristy Gerwig who is managing this year’s show for
Hypertherm Associates. “We can’t wait to see our partners and loyal customers in person and meet new customers to discuss how our plasma, waterjet, and software products can support their business goals.”
KYZEN to Exhibit METALNOX Alkaline Cleaners with Corrosion Inhibitors at FABTECH 2022 KYZeN, the global leader in innovative environmentally friendly cleaning chemistries, will exhibit at FAbTeCH 2022, scheduled to take place November 8-10 at the Georgia World Congress Center in Atlanta. The KYZeN Clean team will highlight me TALNoX m6314CP and me TALNoX m6324CP in booth #b5017.
Cleaning and then protecting metal parts is traditionally done in two stages with two different chemistries; however, there are products with the corrosion inhibitor built in to simplify the process while providing pristine parts. visit KYZeN at FAbTeCH to learn how its product offerings for clean, rust-free parts can save both time and money.
me TALNoX m6314CP is an aluminum-safe alkaline parts cleaner formulated to remove numerous manufacturing oils used in a range of machining, stamping and deep draw operations. m6314CP is built with effective steel corrosion inhibitors to provide long-term protection for both mild and cast steel. With its advanced formula, this product successfully prevents flash rusting common in aqueous processing of ferrous metals. me TALNoX m6314CP also is suitable for use on non-ferrous metals, stainless steel, chrome steel, aluminum, magnesium, and HSS-parts.
Also on display, me TALNoX m6324CP is formulated to remove chlorinated, paraffinic oils used in a various machining, stamping and deep draw operations. It is built with effective steel corrosion inhibitors to provide long-term protection from rust. m6324CP can be added to both the wash and rinse stages of multi-stage cleaning systems, and is excellent at removing difficult soils including carbon smut and chlorinated oils. Low foaming with a very low vo C, m6324CP is easy to use and environmentally friendly. The solution provides effective steel corrosion protection for up to 90-days of indoor protection and has an oil splitting formula to allow efficient oil removal.
Leading laser manufacturer Luxinar is focusing on innovations for the manufacturing industry with its oem and Sr series of sealed Co2 laser sources on booth b9653 at FAbTeCH,
taking place November 8-10, 2022 at the Georgia World Congress Center in Atlanta, GA.
Luxinar specialises in the manufacture of laser sources for industries throughout the world including automotive, electronics, packaging and textiles. Its Co2 lasers are available at three wavelengths, 10.6, 10.25 and 9.3 microns, and are widely employed for cutting, perforating, marking and scribing of a variety of materials such as plastics, metals, wood, paper and glass.
The oem series of Co2 lasers with a power range up to 1000W represents a compact solution that can be easily integrated into industrial processing production lines both with and without covers. The range includes an integrated rF power supply, enabling the laser to produce short optical pulses with high peak power or quasi-CW output and it can operate safely over a wide range of pulse widths and frequencies including through the acoustic regions and a broad range of coolant temperatures. There is also the option for an absorbing thin film reflector (ATFr) to prevent back reflection.
The Sr series of sealed Co2 laser sources have a power range up to 250W and a rating of IP66; this means they are ideal for the harshest of industrial environments to ensure a high level of protection against water and dust ingress. The product range is constructed for ease of installation, use and maintenance in laser-based processing machines. each unit has a compact and lightweight mechanical design with
a straightforward DC power supply connection, easy-tounderstand control interface and digital diagnostics with enhanced LeD. The same output beam position allows for power upgrades with minimal design changes and an integrated rF power supply that is replaceable in the field ensures that production downtime is minimal.
“We are looking forward to showcasing our range of laser sources at FAbTeCH,” said John Podwojski, regional General manager of Luxinar’s USA office. “This allows us to present our Co2 lasers and the benefits of working with a company that has nearly 25 years of experience in laser technology.”
Dynabrade, Inc., the leading industrial abrasive power tool manufacturer announced that the Company has earned ISo 9001:2015 certification for its quality management system.
ISo 9001:2015 is a globally recognized quality management standard developed and published by the International organization for Standardization (ISo). The certification provides a model for companies of all types and sizes to use in creating an effective quality management system. The standard is based on quality management principles, including having a strong customer focus and having a thorough processbased approach to procedures with ongoing improvement.
Dynabrade's ISo 9001:2015 certificate (# QSr-1915) was issued by Quality System registrars, the first US-accredited registrar of ISo certifications. Dynabrade's certification is for providing quality abrasive power tools and process solutions
in all industry markets that require material removal and surface finishing. Activities at Dynabrade's corporate headquarters (8989 Sheridan Drive, Clarence, NY, USA) are included in the scope of certification.
"Dynabrade tools are designed, engineered, and built right at our manufacturing headquarters in Western New York," said Dynabrade President and Ceo michael buffamonti. "our ISo 9001:2015 certification is confirmation of our ongoing commitment to the high-quality standards our end users expect in every Dynabrade product."
Since 1969, Dynabrade has earned a reputation for quality and excellence in the innovative design and manufacture of unique portable pneumatic abrasive power tools, related accessories, and clean air solutions. Dynabrade products are sold in over 90 countries through a worldwide network of professional distributors.
visit www.Dynabrade.com
New TurboBlast Safety Air Gun for Heavy Duty Jobs Requiring Powerful Blowoff e XAIr’s new Turboblast® Safety Air Gun is the latest addition to the e XAIr line of Safety Air Guns. This dynamic air gun is capable of producing up to 23 pounds of force with a simple press of a button trigger and is the ideal solution for blowoff applications requiring maximum force such as removing stubborn or heavy debris like slag and flash, part drying or cooling from a distance, as well as heavy duty cleanup in busy facilities.
The Turboblast features a cast aluminum handle with a rugged elastomer grip that’s not only comfortable, but Uv resistant, chemical resistant and insulated from heat or cold. The light touch activation trigger creates a powerful blast of air and also includes a “Dead man’s” grip that turns air off if the air gun is dropped. All models include an integrated nozzle guard for safety. models are available with an adjustable gate valve to control blowing force on the fly, or without the gate valve.
The Turboblast is available in multiple different flow rates and extensions up to 6 feet long to provide ease of reaching into difficult to reach areas. The Turboblast Guns are the most powerful air guns from eXAIr and complement our variblast Precision, variblast Compact, Soft Grip and Heavy Duty Safety Air Guns. All eXAIr Safety Air Guns are Ce compliant and meet oSHA standards. Price starts at $800.00.
visit: www.exair.co/153-turbo
As Helios Gear Products continues to grow and expand their gear cutting tool offerings, their unparalleled application engineering support and competitive lead times are helping manufacturers deliver during supply chain instability. With globally competitive pricing and
expert Helios team, custom cutting tools are being delivered in weeks, not months, keeping job shops and high-production manufacturers competitive. From hobbing to shaping, power skiving, worm milling, and more, Helios is supporting manufacturing with tool design and delivery needs, production estimates, reverse engineering, process optimization, and fixture design expertise.
“We were able to get the tools and create the parts, and finish them, in a very short timeframe that nobody else would've been able to do… so without Helios’ help we wouldn't have been able to produce those parts in the 8-10 weeks that they required, which usually would’ve
said Pete Dimascio at Delta research. With applications engineers on-call for custom gear-cutting tool design, gear manufacturers can receive dedicated domestic support for engineered solutions right when they need it. reflecting on a recent delivery, Jared Lyford from Forest City Gear says, "these are solid carbide tools with custom proportions, so these are special tools. The performance has been nothing but stellar. I would
incumbent." Helios welcomes new gear-cutting tool design challenges and is excited to continue to support North American manufacturers with unrivaled gear-cutting tool solutions.
visit: www.heliosgearproducts.com
Hypertherm Associates introduces new single-piece cartridge consumable for HPRXD plasma systems
Hypertherm Associates, a U.S. based manufacturer of industrial cutting products and software, today announced the release of a single-piece consumable cartridge and cutting torch for Hypertherm HPr XD® plasma systems.
The new HPr® cartridge is designed for use with current HPr XD systems, and aside from the new torch, requires no changes to the system or system settings. operators can replace both in seconds without the use of tools.
The cartridge replaces the traditional 5-piece consumable stackup with a perfectly aligned part that lasts longer and delivers extended high-definition cut quality. It makes consumable management and assembly much easier, and eliminates errors caused by incorrect handling or installation.
“We are very excited to bring this new cartridge to market since it offers so many benefits to our loyal HPr customers,” said Kristopher rich, the marketing director for HPr XD products. “It simplifies plasma cutting and training for fabricators, job shops, and manufacturers struggling to fill open positions. At the same time, it makes cutting with one of our best-selling systems more efficient by nearly eliminating the high cost of downtime from consumable selection errors and reducing time spent on consumable management and changeouts.”
The HPr cartridge and torch are now available from authorized partners of Hypertherm technology brand products. The cartridge comes in three amperages—80, 130, and 260 amps—for mild steel cutting.
Hypertherm Associates is a U.S. based manufacturer of industrial cutting products and software. Its products, including Hypertherm plasma and omAX waterjet systems, are used by companies around the world to build ships, airplanes, and railcars; construct steel buildings, fabricate heavy equipment, erect wind turbines, and more. In addition to cutting systems, the company creates CNCs and software trusted for performance and reliability that result in increased productivity and profitability for hundreds of thousands of businesses. Founded in 1968, Hypertherm Associates is a 100 percent Associate-owned company, employing approximately 2,000 Associates, with operations and partner representation worldwide. visit: www.HyperthermAssociates.com
Jergens introduces its newest cast iron tooling columns that offer maximum rigidity. The key to this performance is single piece cast iron construction. These columns are made in the U.S.A., increase horizontal machining potential, and provide a solid basis for custom workholding to suit specific customer needs.
Several mounting options are possible including direct, with center pin locating or edge locating, and also quickchange applications via ZPS with K20 pull studs and 4 module subplate. New column styles include square, cross, and rectangular. The square and cross styles are well suited for high density multi-part fixtures or incorporating multiple operations into a single column. The cross style allows the added benefit of increased spindle access near the column, eliminating the need for extra-long tools. The larger upright faces of the rectangular columns are ideal for applications involving larger workpieces.
Column construction uses stress relieved, class 40 cast iron, with the base and sides milled flat, perpendicular, and parallel within .001"/ft. providing an accurate foundation on which to setup workholding devices or quick-change systems. What does this spec translate to for customer use? other features include a center locating bore, inch, and metric hole patterns, m12 lifting holes for secure hoist ring attachment.
With technical staff support, Jergens tooling columns are customizable as well as easily integrated into full custom design and build projects. Popular patterns and methods include tapped grid, bushed, and tapped grid for modular fixturing applications, or for quick-change, add either ball Lock® receiver bushings or ZPS modules.
Actek manufacturing and engineering Inc. — www.actekmfg.com
Air-vac Systems — www.air-vacsystems.com
ATTCo, Inc. DbA Syclone ATTCo Service — www.skyhookmfr.com
behringer Saws, Inc. — www.behringersaws.com
betenbender manufacturing, Inc — www.betenbender.com
Carell Corporation — www.carellcorp.com
23 Clamprite — www.clamprite.com
Combilift, USA — www.combilift.com
CoXreeLS — www.CoXreeLS.com
Denver breaker & Supply — www.denverbreaker.com
Design-2-Part Shows — www.d2p.com
Dynabrade, Inc. — www.dynabrade.com
eagle bending machines — www.eaglebendingmachines.com
23 eNm Co — www.enmco.com
essex Structural Steel Co. — www.essexstructuralsteel.com
Formdrill USA Inc. — www.formdrill-usa.com 27
Fortville Feeders, Inc. — www.fortvillefeeders.com 48 H&K equipment, Inc. — www.hkequipment.com
HmI div of betenbender manufacturing — www.betenbender.com 30
HYDmeCH — www.hydmech.com 7 ImDauctions.com — www.imdauctions.com 49 Industrial magnetics, Inc. — www.magnetics.com
Kanetec USA Corp — www.kanetec.com 47 KHK Gears — www.khkgears.us
Lenzkes Clamping Tools, Inc. — www.lenzkesusa.com
L&L Special Furnace Co., Inc. — www.llfurnace.com
macmillin Hydraulic engineering Corporation — www.macmhydraulic.com
morgan manufacturing, Inc. — www.morganmfg.com
Pro-Line — www.1proline.com
radwell International, Inc. — www.radwell.com
royal Products — www.mistcollectors.com
Schweiss Doors — www.schweissdoors.com
Scotchman Industries, Inc. — www.scotchman.com
Sprinter marking, Inc. — www.sprintermarking.com
Standard Direct — www.Standard-Direct.com
Stor-Loc — www.storloc.com
Suhner Industrial Products — www.suhner-machining.com
The Caldwell Group, Inc — www.caldwellinc.com
Tormach — www.tormach.com
Trim-Lok
www.trimlok.com
We have launched our online, searchable directory with over 400 categories specifically designed for the industrial machinery industry.