
14 minute read
TALKING SHOP REVIEW
interested in contributing to its advance.
FEATURING:
TALKING SHOP WITH: Dave Veisz — Vice President of Engineering, MakerBot
I know that your North American operations are based in Brooklyn, New York. Give us an idea of your global footprint. Our manufacturing facility is in Asia, where we also have quality control and test labs that are an extension of our R&D and quality labs in Brooklyn. All hardware and software engineering takes place in Brooklyn, and the teams work closely with the technicians in Asia on new product introduction into manufacturing. Being part of Stratasys is a huge advantage for us, as well, since we can leverage their vast engineering expertise in our own development efforts, whether that be new printer designs or developing industrial materials beyond the eight we’re currently able to process.
While the United States is our largest market, we are active globally, in countries including Germany, China, South Korea, Africa, Australia, and Mexico. We have warehouses, reps, and stocking distributors around the world. All of our printers are stock models, with the only customization having to do with selecting the appropriate “print mode” and the desired materials to utilize.
Looking at the four different printers you offer, could you outline in what way each model excels and/or differs, and who would benefit most from its capabilities? We basically serve two primary markets: academia such as high schools, community colleges and universities, and professionals including engineers, architects, design firms, manufacturing, and industrial enterprises. With all of our printers we’ve concentrated on creating what we refer to as a “3D printing ecosystem,” where ease of use is just as important as the features the hardware and software provides.
The Replicator+ is our flagship printer for education, particularly the K-12 levels. Again, with our focus on the user experience we want the students’ introduction to 3D printing to be an accessible and welcoming experience, so we provide resources such as training, certification, and content to both the students and teachers to get the
most value and learning out of the 3D printing process. Our training not only focuses on how to use the printer and software, but also explains how to leverage 3D printing to learn design skills and problem solving. As an aside, all of our printers are meant to be connected online so that updates are made automatically to keep everyone at the leading edge of new developments, and all mobile apps and print preparation software is free. The next level is the Z18, which is primarily for higher education and professional use, with a larger build volume.
Finally, we have the Method and Method X models, which we’ve invested a lot of focus and effort in developing over the past few years, optimizing them for the professional space. These printers are ideal for manufacturing facilities, machine shops, design studios, and other professional workspaces, including higher education applications in research facilities and test labs. We have seen a great deal of early adoption and are very proud of the results.
The goal was to bring many of the capabilities found in traditional industrial 3D printers into different workspaces in a way that’s accessible and easy to understand, allowing users with direct access to create industrial-grade 3D prints at an affordable price point.
What do you see as the benefits graduates of these additive manufacturing programs will bring to the industrial workspace? They are profound. Think about what a recent graduate just entering the job market brings with them when they are equipped with these skills. Recent grads are the ones introducing 3D printing into the workplace, since they know the value from their experience in college fabrication labs, and we see that adoption throughout engineering and design offices happens quickly once they realize this value. So that’s why we’ve placed so much emphasis on accessibility, both in terms of price point as well as ease of use. The more accessible we can make this technology, the more partners we’ll find who are interested in contributing to its advance.

• NO MECHANICAL ADJUSTMENT NECESSARY
(X axis end point gets changed in the program when changing bar diameters)
• ONE TIME SETUP
• NEVER NEEDS ADJUSTMENT
•CHANGE BAR SIZE IN SECONDS (BY CHANGING “X” VALUE IN PROGRAM)
• EXTREME REPEATABILITY
RESULTS IN LESS MATERIAL WASTED PER PART
• NO GRIPPING FINGERS TO AD- JUST, LOSE OR BREAK
• EZ-PULLER WORKS ON
ROUND, HEX AND SQUARE STOCK.
RANGE:
.093″ – 1.750″ ROUND STOCK .125″ – 1.375″ HEX STOCK .125″ – 1.000″ SQUARE STOCK
Fastest, Most Accurate Bar Puller On The Market
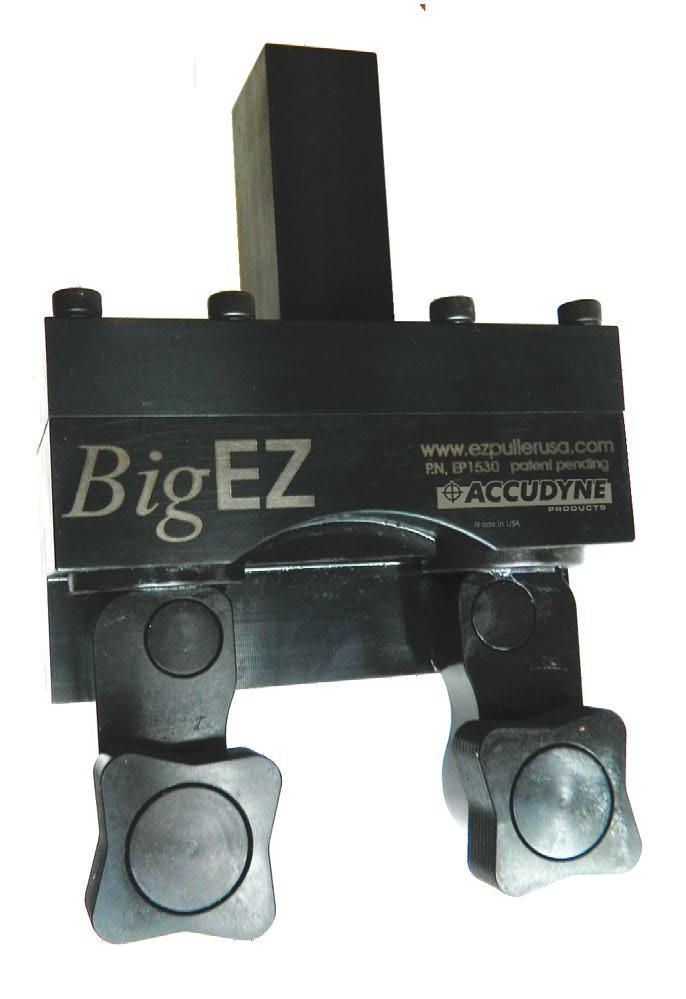


Watch the video now at: ezpullerusa.com
by

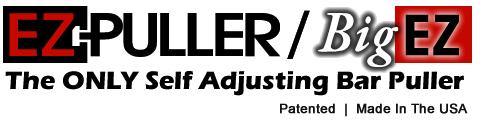
60 Day Money Back Guarantee - 2 Year Warranty! “Absolutly, no time. Zero time adjusting the tool.” - Randy, CNC Lathe Programmer
effective solutions.
FEATURING:
TALKING SHOP WITH: Steven Holmes — CNC Education Manager, Siemens
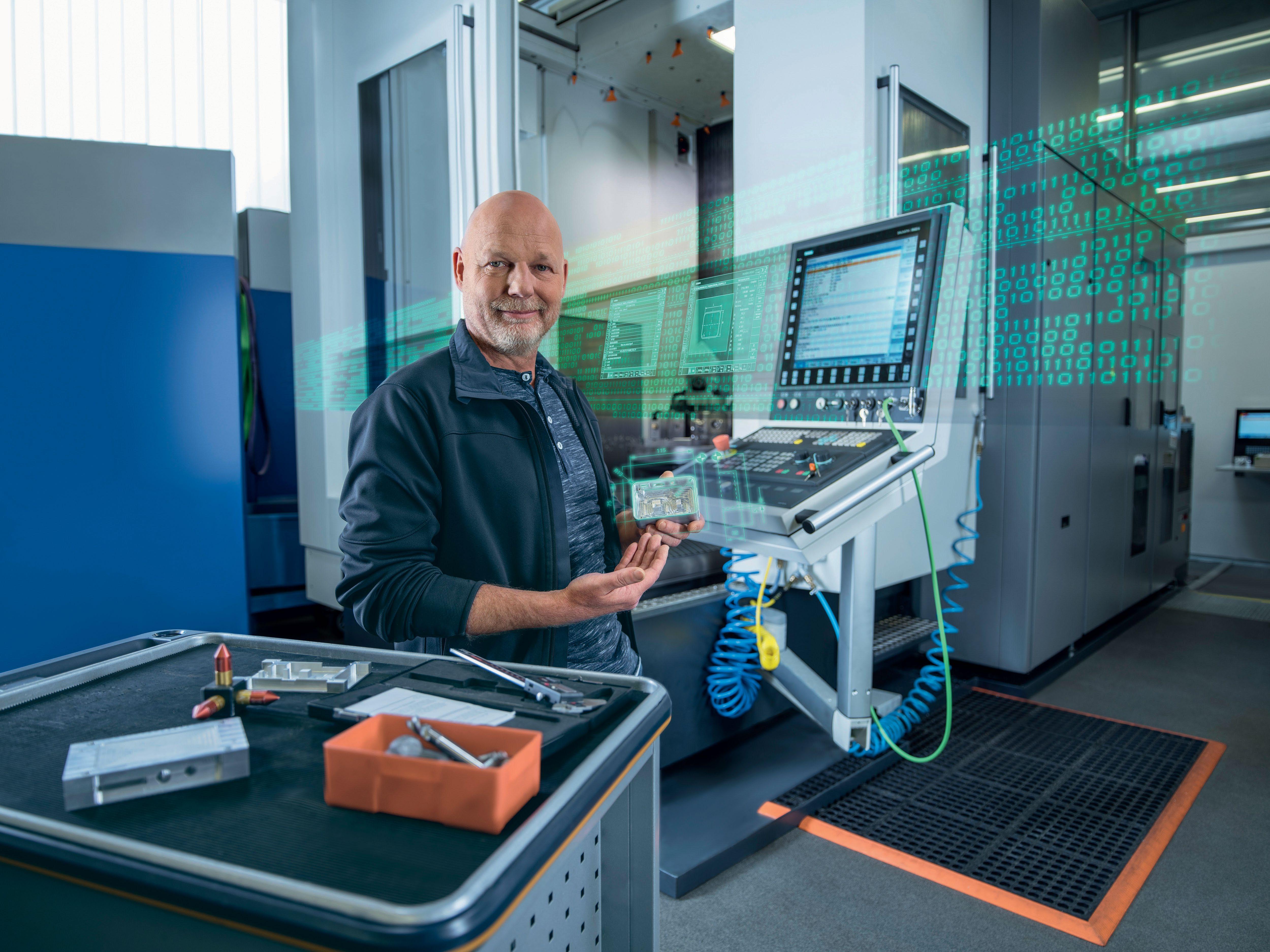
Be smarter and more flexible— see how. What was the impetus behind the launch of the LEAP initiative in 2017? The Lifelong Educational Advantage Program, or LEAP, was launched as an offshoot of Siemens Cooperation with Education, which was already in place at the time. SCE was active at our locations throughout Europe and the USA, so we were able to use that experience as a model for a similar initiative here in the States. Siemens has some 350,000 employees worldwide, and approximately 65,000 in the U.S., so we had thousands of people with a lot of experience to draw from in offering training opportunities to students in high schools and secondary institutions such as technical programs, community colleges and universities. How did you go about approaching high schools and technical programs about enrolling in LEAP? How do they get started, and what costs do they incur? We already had longtime relationships with about 500 U.S. academic institutions at the time, so we were able to use that as a starting point as we began reaching out to other potential enrollees. The schools that apply and are approved receive a 90 percent discount on the Sinutrain training system they receive, which turns any PC screen into an almost exact representation of the Sinumerik 828D and 840D sl controls on the machine. As for the training, we train and certify the instructors, who then train the students who are working toward their own certifications. The schools pay no extra cost beyond their initial software investment.

“With Siemens,
I control my future.“
10 | IMD | Q1 2020 As a machine shop owner, I want to be smarter and more flexible in my manufacturing; I want to be more competitive. So when I invested in my CNC machine, I insisted on the control system that delivers the greatest returns.
When the program mentions “hands-on” training, does this describe onscreen exercises or actual exposure to a machine tool? The training modules vary, depending on what the student is drawn toward. If it’s turning, there are two levels, with the first being conversational — mostly onscreen work — and the second focusing on writing G-Code. If it’s milling they choose, there is a third level for 5-axis machining. They have a wealth of resources on our Siemens CNC4you web site, including webinars and live machining demos. As for the hands-on portion, once they’re ready the students are required to develop their part programs which are verified with 3D graphics, paying special attention to any potential collision scenarios, and then to have their instructor sign off on the results before they load it into an actual machine at their facility. They must prove to the instructor that they can run the part they’ve designed before they’re eligible for certification. When they have that in hand, they are very desirable as a candidate once they enter the job market.
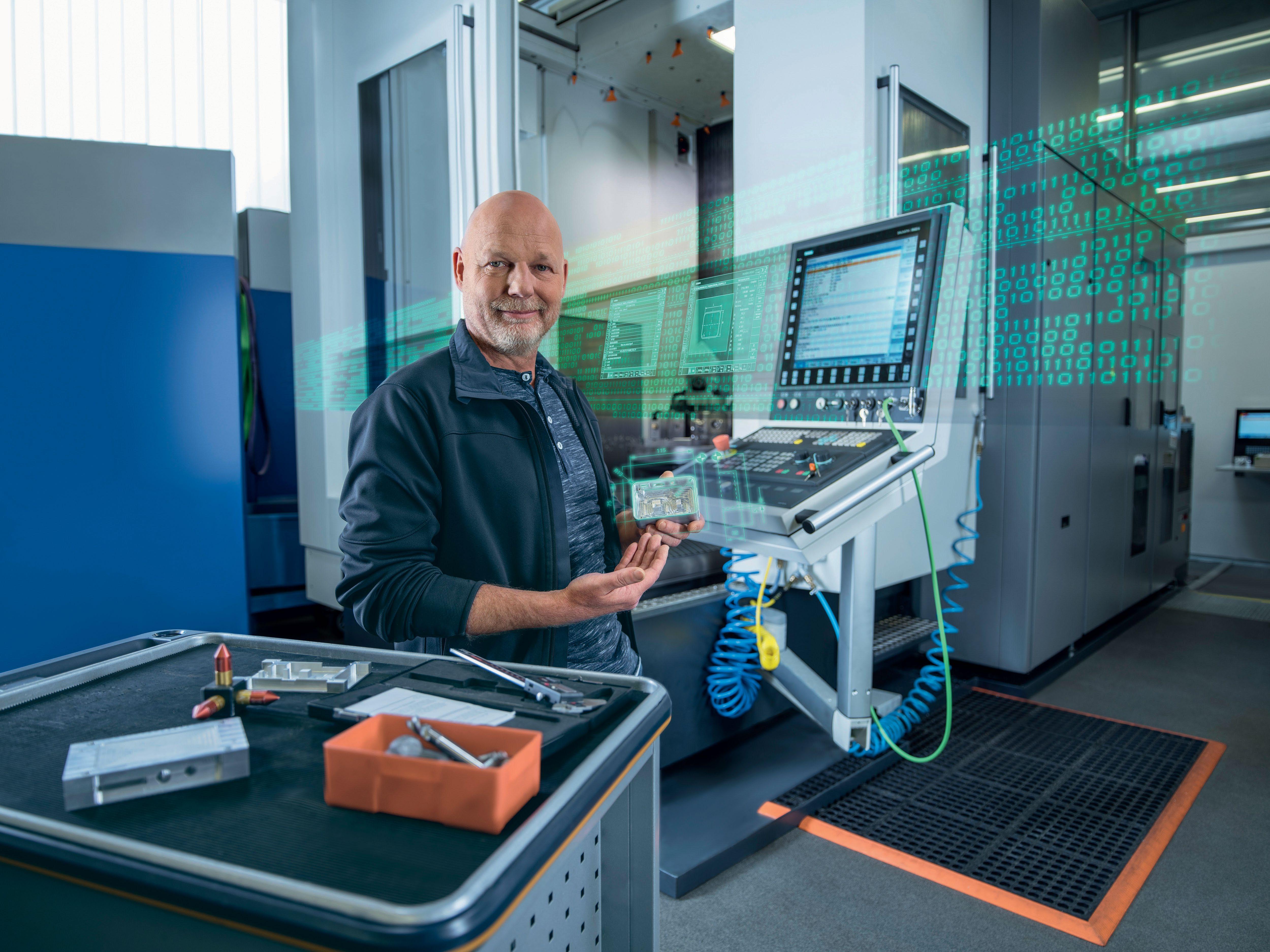
In the two years that this initiative has been in place, can you speak to growth in terms of enrollees and/or industry partner OEMs? In 2017, starting with six or seven schools that had been approved for entry into the program, since then we’ve seen that number double every year, with more than 50 academic institutions now enrolled, and we’re issuing hundreds of student certifications every year. So we’re quite pleased with the progress we’ve made, and we expect this upward trend to continue. And the list of OEM partners is thriving as well, with companies such as DMG Mori, ROMI, Emco and Levil, among many others, onboard as industry supporters.
Have you seen a shift in recent years within manufacturing, from mere awareness of the shortage of STEM-trained graduates to actually tackling the problem, as Siemens is doing? Yes, without a doubt. We’ve reached a tipping point where the skills gap is now a mainstream news topic that everyone is aware of, and industry and academia have joined forces to develop effective solutions. We need to convey to students that today’s manufacturing jobs pay $85,000 a year on average and often involve carrying an iPad, not a toolbox. Work/life balance is taken into consideration, and manufacturers are beginning to reestablish apprenticeship programs based on the German model. We want these young people to understand that a four-year college experience might not be for everybody, and that there’s a way to start your life and career after school without being buried under a mountain of debt.
To learn more go to www.siemens.com and search using “CNC4you” for video and other LEAP-related resources.


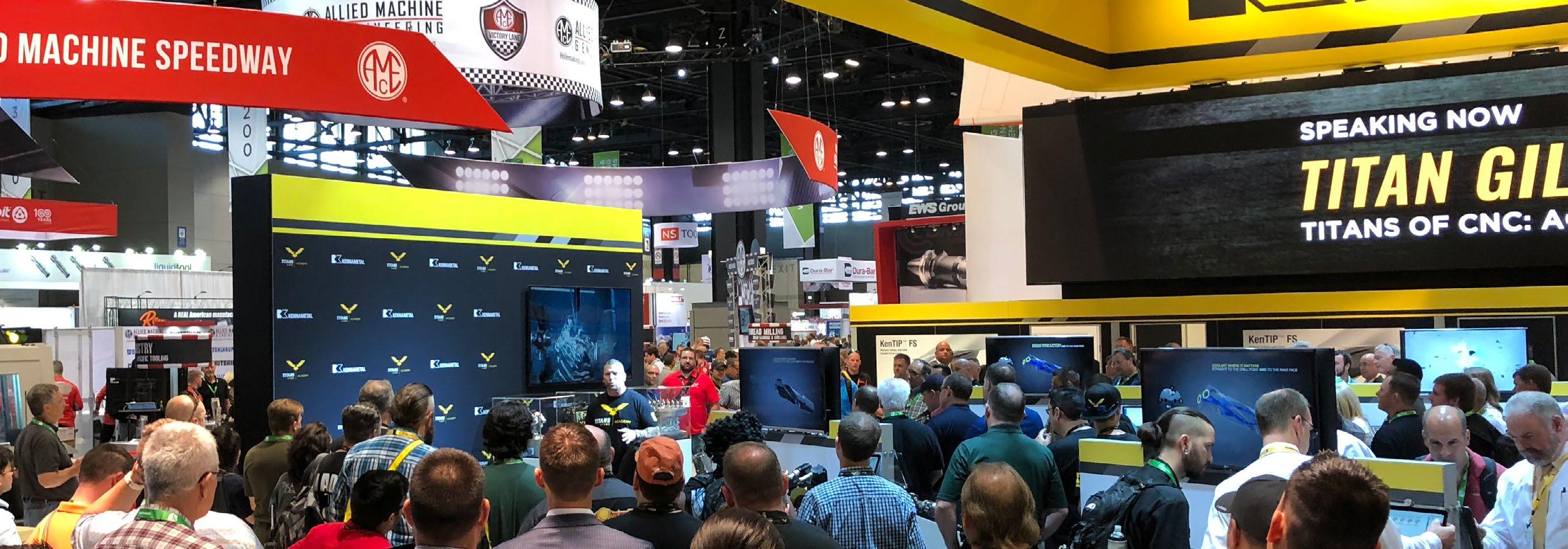
FEATURING:
Titan Gilroy — Founder, CEO and President, TITANS of CNC: Academy
Can you give us a quick tour of how this whole adventure began? Sure. I started working for different machine shops in Northern California in 1996, and then I decided to go out on my own in 2005. I only had a couple of guys helping me, and I basically worked 24 hours a day, grabbing a few hours of sleep on a couch in the office when I could. Within three years we were pulling in a million dollars a month. Then the recession hit and I almost lost the company. But we outworked the competition and started pursuing precision machining for the top aerospace companies. Seeing what manufacturing was going through made me start thinking about where the industry had gone wrong. We’d stopped reaching out to kids and teaching them what manufacturing was really about. The top companies from around the industry were locked behind closed doors, unwilling to share their knowledge and experience with the next generation. This really created a skills gap, or awareness gap, for the trade. It was left to the previous generation to figure out how to stay competitive, which has led to the major problems we’re still fighting today. Once the economy improved, unemployment numbers dropped, but many of those jobs were low-income and didn’t provide enough money for workers to get ahead. I also met employers at smaller shops who wanted to train their employees but didn’t know how. So I started wondering, “How could I make a difference in my trade? How could I find a way to bridge all these different needs in a way that made sense and actually worked?” Department of Corrections, who oversaw San Quentin State Prison, called and said “look, we have 35 prisons, most of them with machine shops, can you help me out?” I thought “I used to be in that situation and have been in prison, so I can definitely understand.” So we built our own curriculum, which we fine-tuned and then helped to develop a similar program with Dan Frank at Rocklin High School, which is nearby. We worked with our amazing partners like Kennametal, who donated tools, and once we’d run the whole program through quality control, we put it all online for free, for anyone willing to put in the time. It markets itself, because it provides high-level training where nothing else like it exists. Suddenly we had kids all over the world making parts and posting them on Instagram and YouTube; it just went crazy. Students and their parents began realizing that manufacturing didn’t have to be a dirty, old-school environment anymore, but a modern facility using the latest technology to compete on a global scale. We found that employers were relieved to find out they didn’t have to develop a training program for their employees themselves, we were doing it all for them, and it was free. Fast-food workers saw there was a way they could make a decent living and support their families, and inmates were able to develop skills prior to their release that would allow them to find a job and build a life for themselves. We now have approximately 80,000 people enrolled in our Academy in 170 countries around the world, and we’re partnering with about 2,500
Sounds overwhelming. What was the first step you took in addressing the situation? This was before social media had come on strong, so we decided to start filming a show for cable TV that showed clean shops and innovators with amazing machines. We wanted to erase the image of manufacturing as a sweatshop in students’ minds, and we wanted fast-food workers to realize there was a way they could make a good wage for their efforts. Then, during the second season, the vice principal of Career & Technical Education for The California
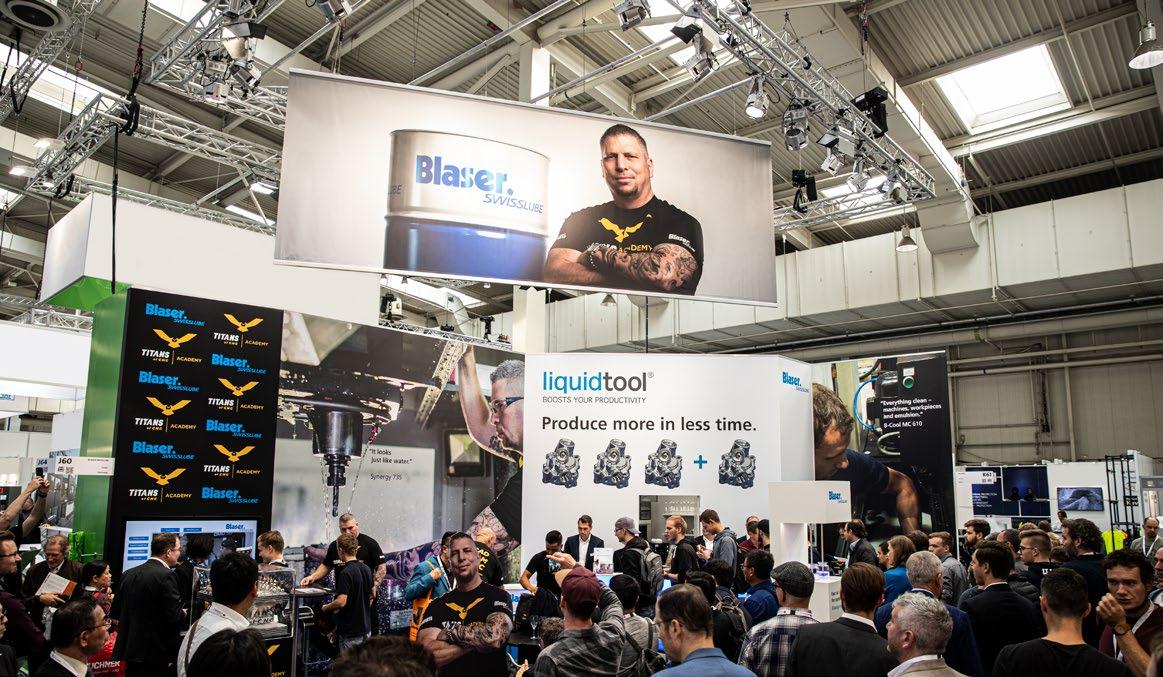
educational institutions. Our industry partners include companies like Kennametal, Mastercam, Makino, DMG Mori, Blaser Swisslube, Schunk, and many more. And now we get about 100 calls a day from industry giants who need qualified workers, seeking out our students. It’s just incredible. And on top of that we have a link on our website called “small groups” where you can punch in your zip code and it will give you a list of local companies that offer three-hour training sessions on Saturday mornings to people who want to attend. We also have a list of over 1,000 industry endorsements for companies that have validated our approach to teaching CAD, CAM, and CNC. Top manufacturers around the world are seeing the value and importance of high-level training for the next generation of employees. These are just a few examples of how we are doing our best to continually increase awareness that really shows results.
What do you have on the horizon that you’d like to share with our readers? We’re always working on new projects, but there are a few in particular that will launch soon that we feel really good about. One is the Titans of CNC: Aerospace Academy. This platform, launching in April 2020, is designed specifically to teach CNC machining at the highest level. Because of our experience as aerospace machinists, we are qualified to help others achieve the same level of skills to get to that level. This will allow shops to grow and extend their clientele, while working on projects that will support the next generation of space travel and beyond. Our next project in progress is our certification platform,
DRILL. TAP. REPEAT. Engineered Tough for Year After Year Reliability
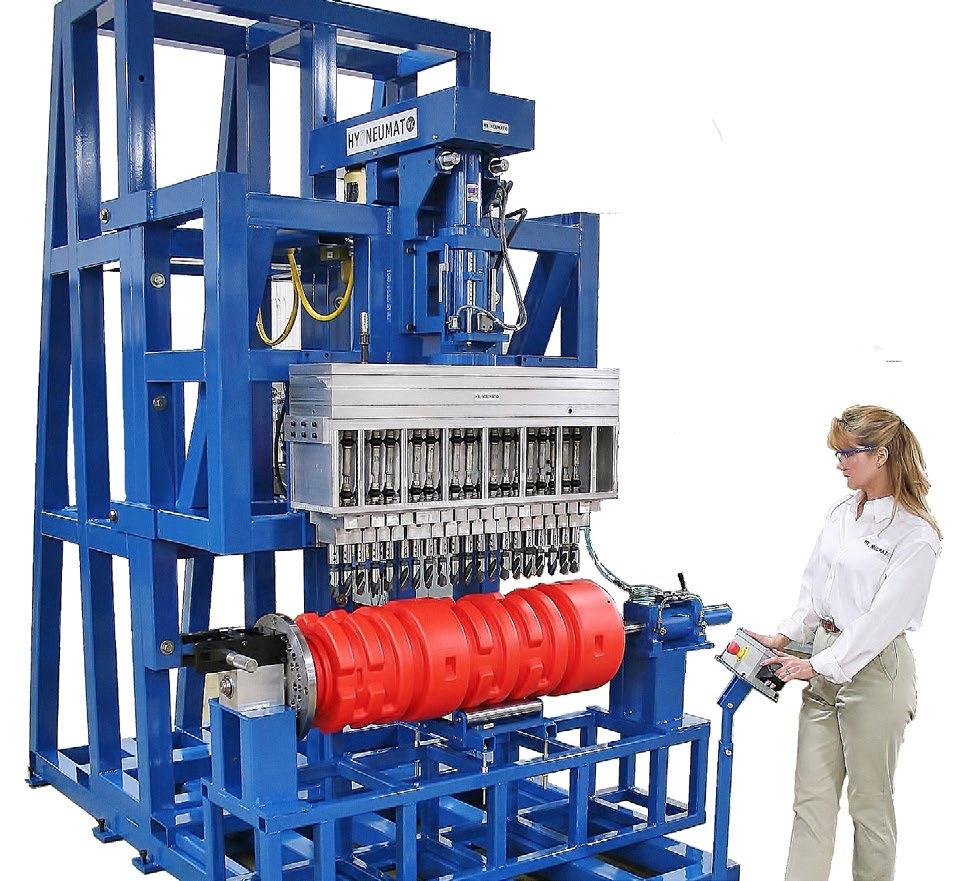
Experts in Automatic Drilling & Tapping Units and Multiple Spindle Heads CNC Expert. This platform will provide an opportunity for users to be validated on their hard work and skill producing Titans of CNC parts. We are developing our own list of skills and standards, validated by industry, that will ensure that each certification has real-life value to individuals looking for opportunities in the trade. All of this is based on a graduate actually being able to make a part according to a print. It’s a real-world approach to training and certification.
Why do you do this, Titan? Is it even possible to sum it all up? I never knew my father growing up, or anything about my family. Years later I met my dad, and I found out that both of my grandfathers were machinists, one in Detroit and the other in Seattle. That was pretty mind-blowing, to find out that I come from good people and have a lineage of great machinists in my family. I just walked into the trade and it clicked for me, but now I know it wasn’t an accident. The same opportunity is out there for others. A great career with great opportunities to make a difference. At this point in my life, that is what I am focused on; helping others reach their potential and bringing awareness to a trade that has made such a huge difference in my life. The older I get, the more I realize that what’s most important in life is to serve others. I have five great kids and a beautiful wife now. I want to help others find their way to a better place, as well.
To learn more please visit academy.titansofcnc.com.

