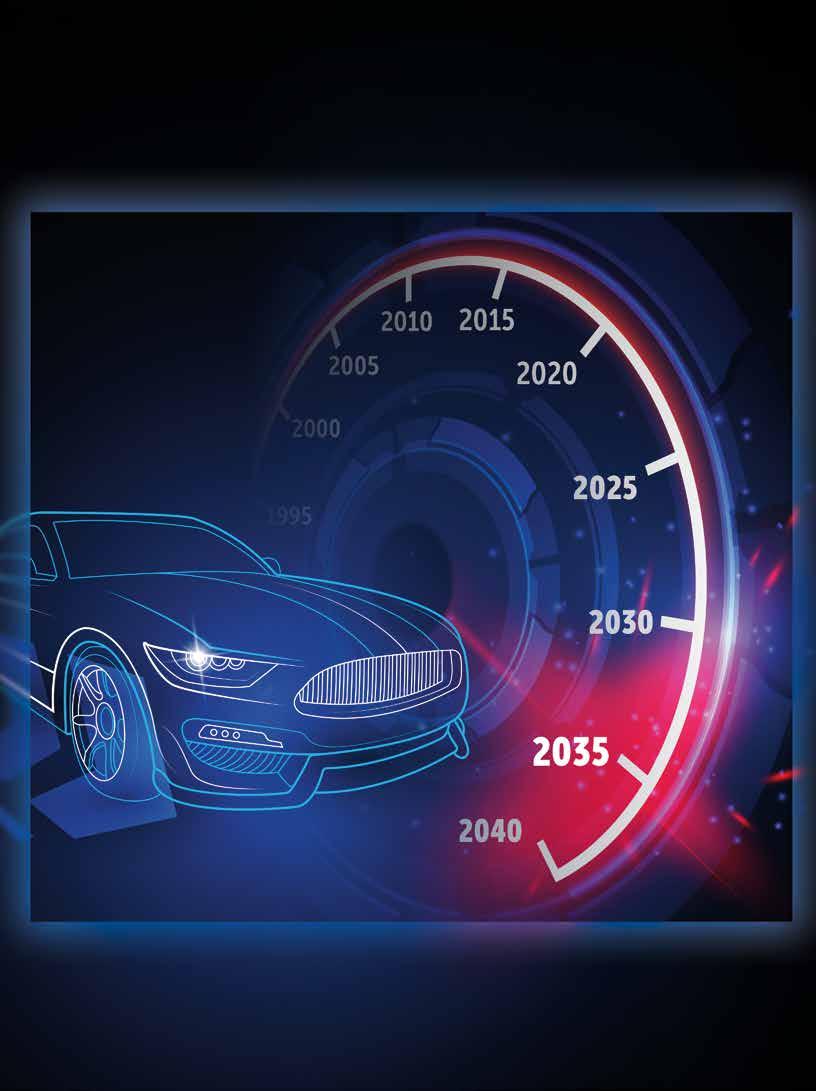
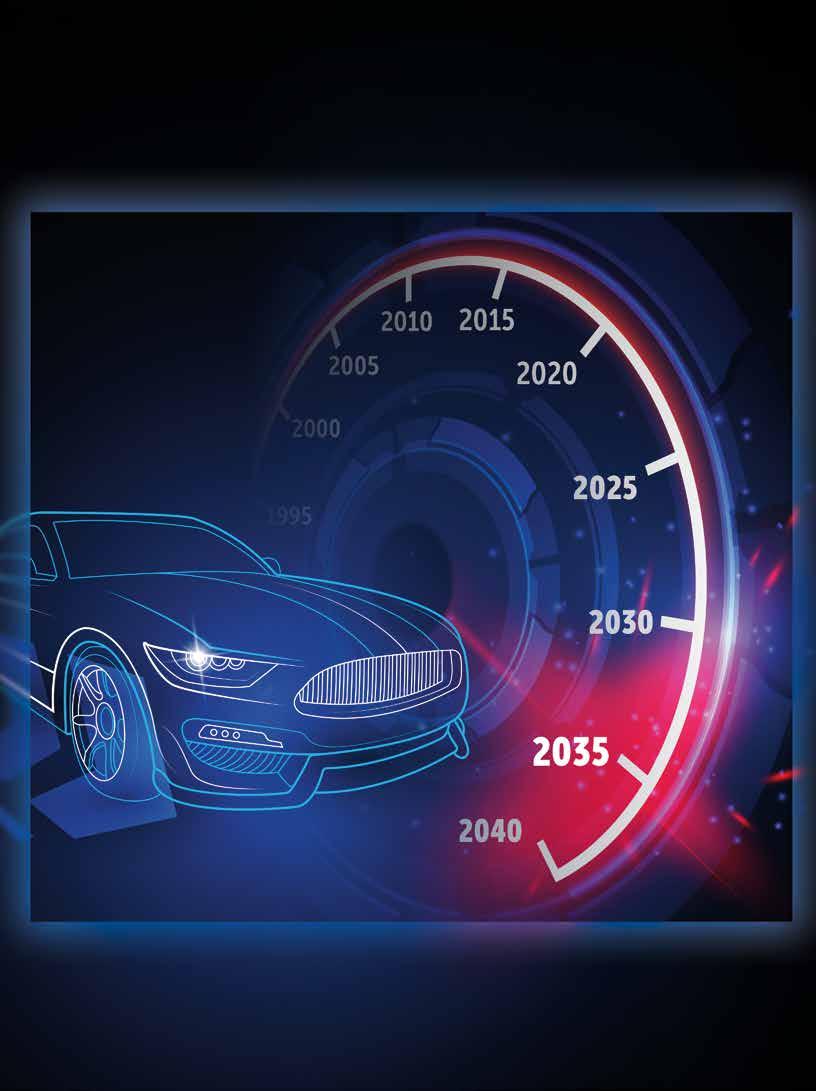
The Changing Automotive Market
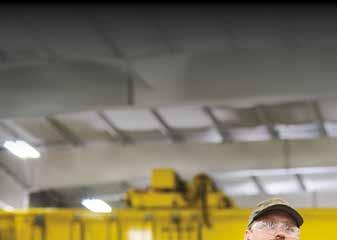

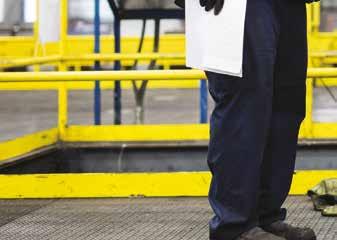
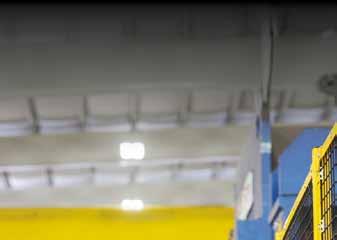
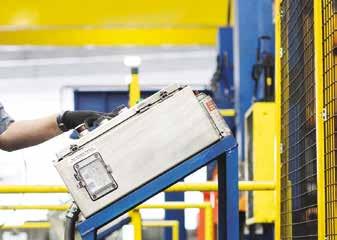
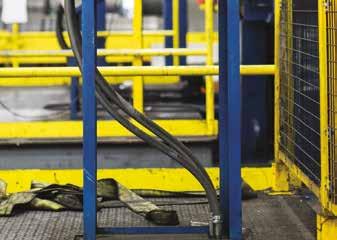

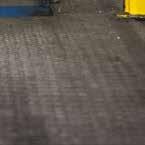
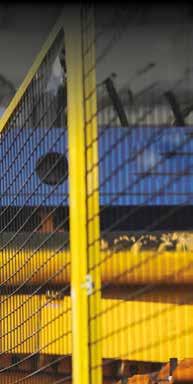
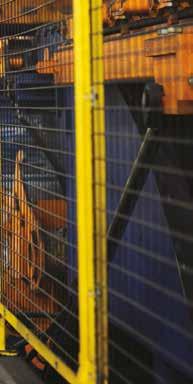
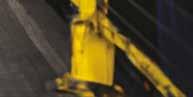
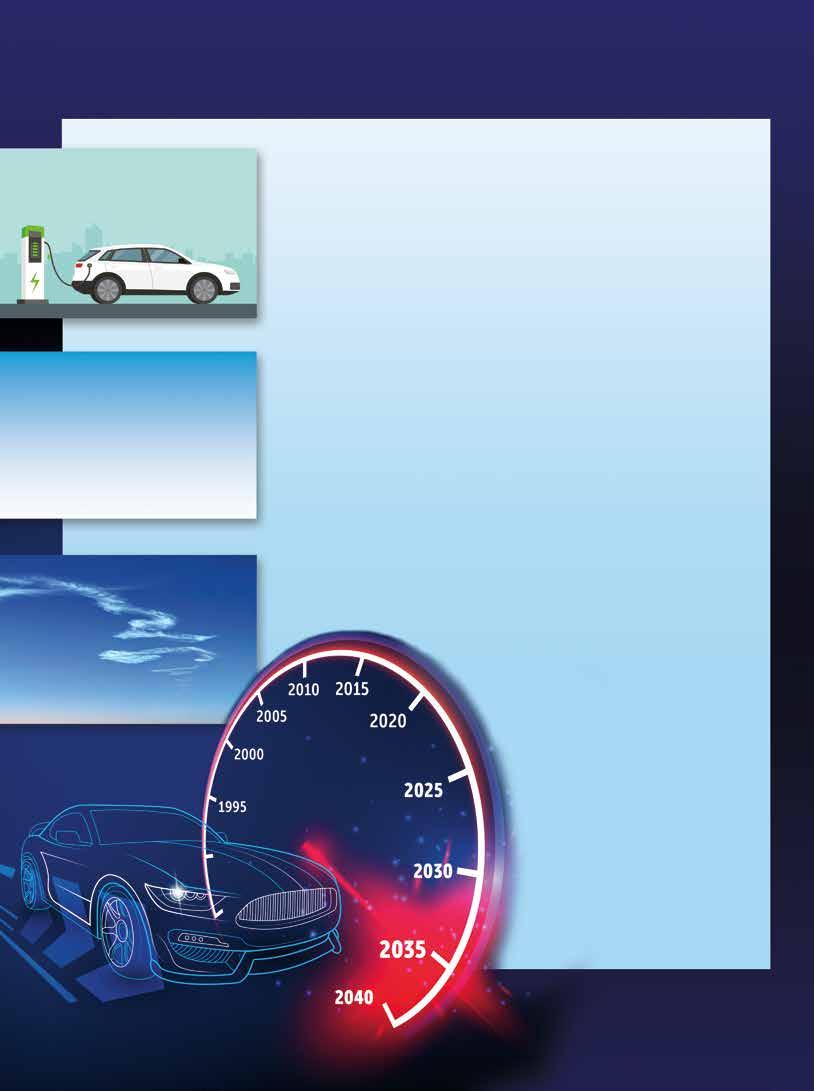

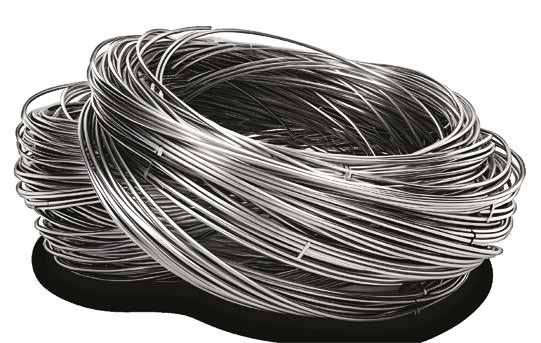
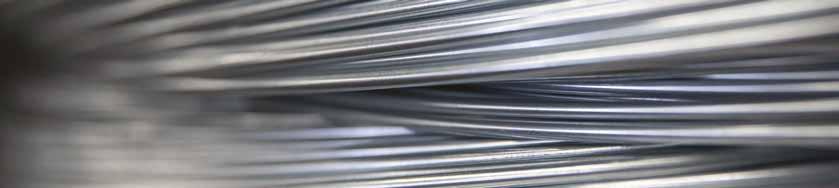
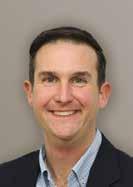
President’s Message
Looking Toward the Future
The automotive market and spring manufacturing go together like a peanut butter and banana sandwich. For some, this is an ideal pairing of sweet and salty; for others, it is something they wouldn’t touch with a ten-foot pole because of reputation, taste or unfavorable prior experience.
With over 286 million cars on the road in the U.S. alone*, there are a lot of springs, stampings and wireforms on those vehicles. Many companies in our industry have partnered and invested heavily in the automotive sector, whether that be by location, equipment or specialized manufacturing processes. Spring manufacturers are a vital part of the automotive industry.
Now, with the growth of electric vehicles, some parts that store and release energy are being phased out, and new parts like copper busbars or hairpins are becoming the conduit for energy. The commitment to electrification in North America is here, and it is only going to expand every year.
I want to take a moment and thank everyone who came to our SMI Annual Meeting in San Diego. It was a great event where we saw beautiful ocean sunsets, rocket launches, Emerging Leaders sessions, a tour of an aircraft carrier, the world-famous San Diego Zoo, phenomenal speakers, action-packed pickleball and industrywide camaraderie. I hope to see even more of you in New Orleans in 2025.
As president of SMI, my goal is to expand education. I am pleased to see that SMI is hosting 24 educational sessions at SpringWorld 2024 (www.springworld.org) Oct. 2–4. I hope that everyone can learn something new and challenge themselves to not only expand their knowledge, but also impart some of their wisdom and experience to the next generation.
“If one does not fail at times, then one has not challenged himself.”
— Ferdinand Porsche
Don Jacobson III Newcomb Spring Corp. D3@newcombspring.com
*https://www.statista.com/statistics/859950/vehicles-in-operation-by-quarter-united-states/
Update Your Records
Please be sure to update your mail and phone records with SMI’s new address and phone numbers.
Spring Manufacturers Institute Main phone z 847-450-6848 PO Box 5668 Gary McCoy z 847-450-6240 Elgin IL 60121 Gaby Carrasco z 847-857-6432
SMI Executive Committee
President: Don Jacobson III, Newcomb Spring
Vice President: David DeVoe, Plymouth Spring
Secretary/Treasurer: Dave Deerwester, The Yost Superior Co.
Past President: Gene Huber Jr., Winamac Coil Spring
At-Large: Joe Devany, Betts Company
Executive Director: Gary McCoy, SMI
SMI Board of Directors
Markus Arnold, WAFIOS I Jodi Boldenow, IDC Spring I Linda Froehlich, Ace Wire Spring & Form I Adam Jacobson, FENN/Torin I Don Lyons, JonSpring I Alex Melnikow, Midstate Spring I Tony Pesaresi, Winamac Coil Spring I Keith Porter Jr., Newcomb Spring I Monica Shafer, Novi Spring I Bernie Taylor, Hoosier Spring I Tim Zwit, Motion Dynamics Corporation
Springs Magazine Staff
Gary McCoy, Executive Director/Publisher, gary@smihq.org
Phil Sasso, Managing Editor, phil@smihq.org
Gaby Carrasco, Associate Editor, gaby@smihq.org
Lisa Plefka Haskin, Art Director, lisahaskin95@gmail.com
Communications Committee
Chair, Keith Porter Jr., Newcomb Spring I Reb Banas, Stanley Spring & Stamping I Hale Foote, Scandic Springs, Inc. I Patrick Gillum, Gilco Spring of Florida, Inc. I Adam Jacobson, FENN/Torin I Lucas Karabin, Acme Monaco I Gary McCoy, SMI I Phil Sasso, SMI I Michael Shapiro, Gibraltar Corporation I Bill Wynn, Gardner Spring, Inc.
Advertising Sales I Japan
Ken Myohdai, Sakura International Inc.
Head Office: 3F,4F, ENDO Sakaisuji Bldg., 1-7-3, Bingomachi, Chuo-Ku, Osaka 541-0051, Japan
Phone: 81-6-6624-3601 I Fax: 81-6-6624-3602
Tokyo Global Office: 5F Kamei No. 2 Bldg., 2-17-13, Kiba, Koto-Ku, Tokyo, 135-0042, Japan
Phone: 81-3-5646-1160 I Fax: 81-3-5646-1161
E-mail: info@sakurain.co.jp
Advertising Sales I Taiwan
Charlie Yu, Worldwide Services Co. Ltd. 11F-B, No 540, Sec. 1, Wen Hsin Rd. Taichung, 408 Taiwan
Phone: +886-4-2325-1784 I Fax: +886-4-2325-2967
E-mail: marketing@acw.com.tw
Springs (ISSN 0584-9667) is published quarterly by SMI Business Corp., a subsidiary of the Spring Manufacturers Institute: PO Box 5668, Elgin IL 60121 Phone: 847-450-6848; Web sitesmihq.org.
Address all correspondence and editorial materials to this address.
The editors and publishers of Springs disclaim all warranties, express or implied, with respect to advertising and editorial content, and with respect to all manufacturing errors, defects or omissions made in connection with advertising or editorial material submitted for publication.
The editors and publishers of Springs disclaim all liability for special or consequential damages resulting from errors, defects or omissions in the manufacturing of this publication, any submission of advertising, editorial or other material for publication in Springs shall constitute an agreement with and acceptance of such limited liability. The editors and publishers of Springs assume no responsibility for the opinions or facts in signed articles, except to the extent of expressing the view, by the fact of publication, that the subject treated is one which merits attention.
Do not reproduce without written permission.
Cover designed by Lisa Plefka Haskin utilizing Shutterstock imagery.
Please archive or recycle this magazine.
Join us on social media!


Don Jacobson III
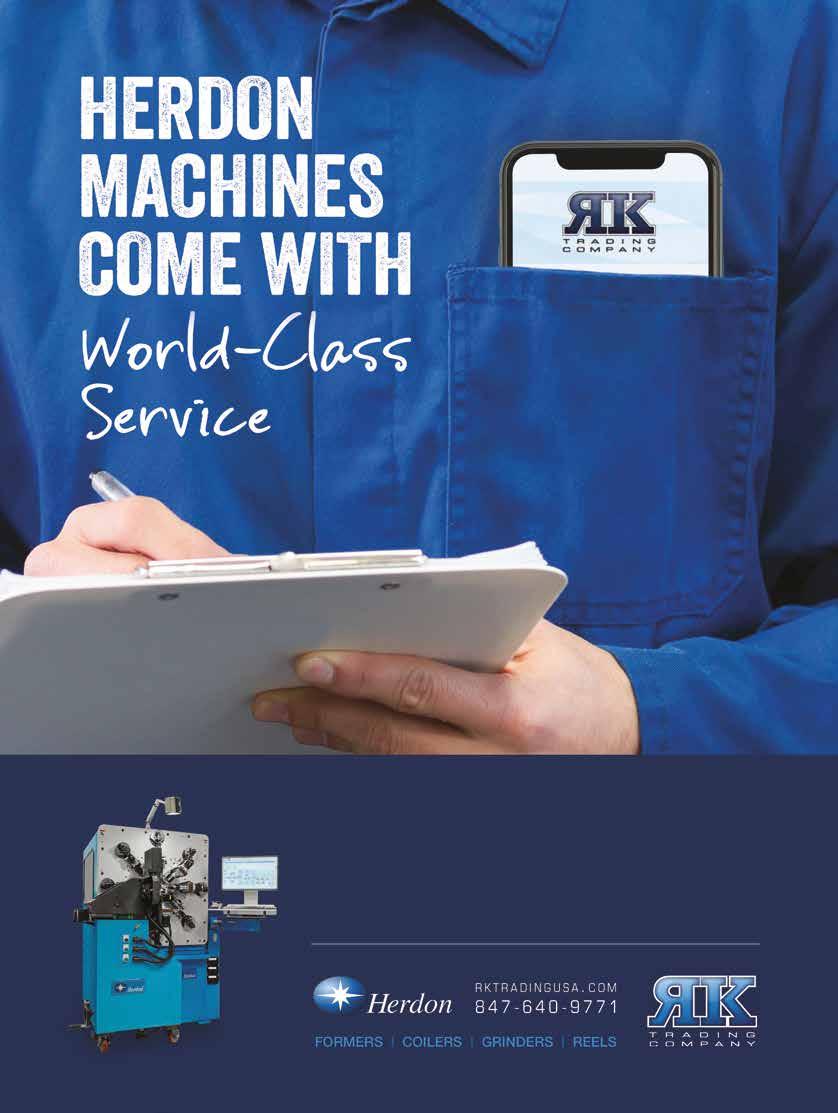
When you choose to go with RK Trading, quality service is available with one phone call. In fact, it’s part of the package—a lifetime of U.S.-based immediate service and a direct line to our Customer Service department. Don’t believe us? Give our team a call today at 847-640-9771 and ask us anything about your Herdon machine. SCAN HERE

Up to 10 % higher Production Speed
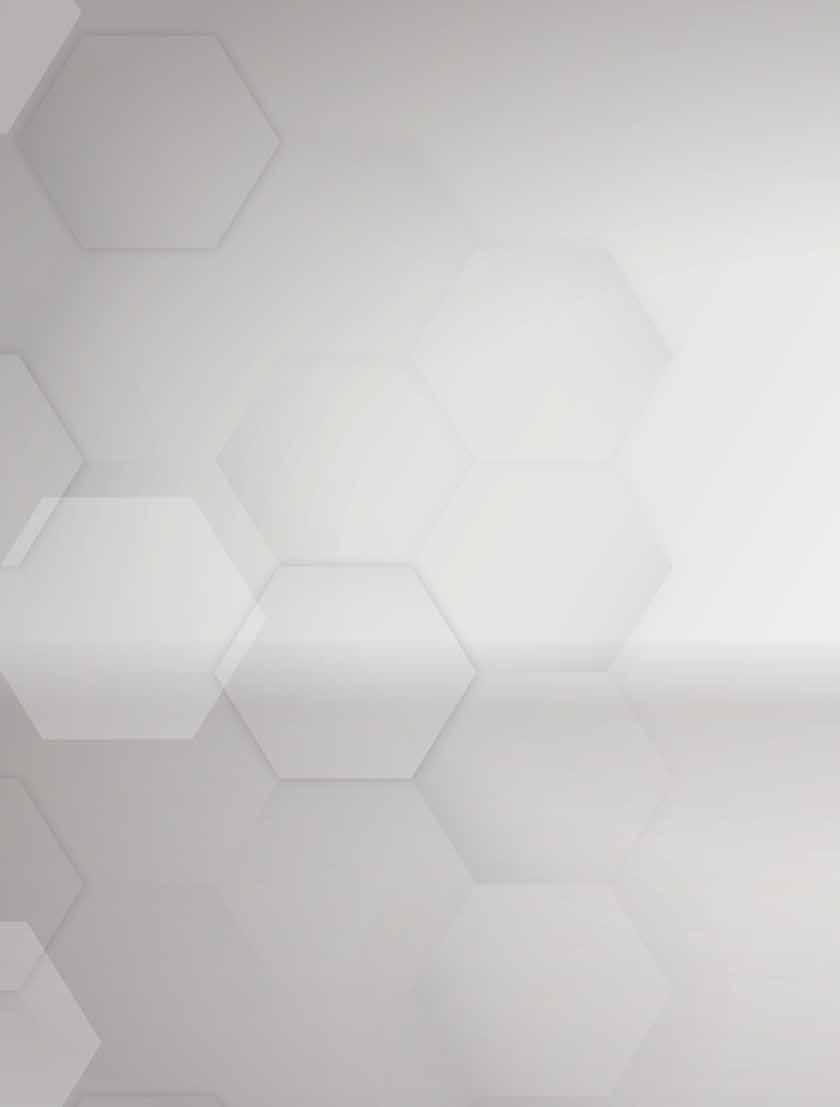
Improved geometric programming and simulation
FMU 08+ to FMU 100+
FLEXIBLE PRODUCTION OF TORSION SPRINGS
Discover the »PLUS« for your production. The new generation of FMU machines for all types of torsion springs from 0.8 to 10 mm Wiredesigned to meet the highest quality standards.
Automatic Generation of programs with iQspring+

NORTH AMERICA
The L.S. Starrett Company reached a definitive merger agreement with MiddleGround Capital, taking the company private in an allcash transaction valued at $16.19 per share. This price represents a 63% premium over Starrett’s closing stock price on March 8, 2024.
“We are pleased to reach this agreement, providing significant cash value to our shareholders,” said Douglas A. Starrett, chairman, president and CEO. “After thorough outreach, our board determined MiddleGround’s industry expertise makes them the ideal partner. As a private company, Starrett will gain financial and operational flexibility to continue delivering industry-leading service and products, while upholding our proud traditions.”
John Stewart, managing partner of MiddleGround, expressed excitement about the partnership, highlighting the company’s long admiration for Starrett. “Most of our team is familiar with Starrett products from their manufacturing careers, and we are
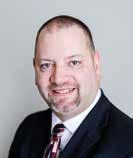
Global Highlights
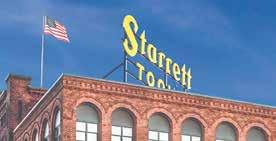
eager to advance the company’s innovation and reshoring efforts,” he said.
The transaction, approved by Starrett’s board, will be funded by MiddleGround Partners III, L.P. and committed financing without contingencies. Expected to close in mid-2024, the deal is subject to shareholder approval and other conditions. Posttransaction, Starrett will become a wholly owned subsidiary of MiddleGround, and its class A common stock will be delisted from public markets.
Winamac Coil Spring Inc., Kewanna, Indiana, announced the appointment of Andrew Pesaresi as vice president of procurement. He replaces Dan Pesaresi Jr., who officially retired in early March after 30 years of committed service to the family business.
Pesaresi has been with Winamac for 23 years. During his tenure, he has been active in quality systems, division management and, most recently, purchasing.
“I am very humbled and honored to serve in this new capacity,” Pesaresi said. “My goal is to support our WCS team using the experience and knowledge I have gained. While my focus has shifted during the years, I bring a dedicated attitude to the procurement of wire and materials striving for the right product at the right time and at the best cost. It is my desire to continue the values set by previous generations.”
Winamac Coil Spring is celebrating 76 years in business, providing expertise in spring manufacturing and wireforming to a worldwide market.
Pesaresi is a third-generation family member and grandson of Winamac Coil Spring founder Walt Pesaresi.
Bristol, Connecticut Mayor Jeff Caggiano and local officials celebrated Radcliff Wire’s 65th anniversary March 8, 2024. Mayor Caggiano presented a commemorative certificate to company president Charlie Radcliff
Radcliff and CEO Jeanne Radcliff shared the company’s history and gave a facility tour. Founded in 1959 by Don Radcliff, the company supplies unique wires for various industries, including medical, industrial and aerospace.
The tour showcased their manufacturing process, impressing visitors with an array of shapes and alloys. Radcliff Wire employs 29 people, many long-term.
Mayor Caggiano expressed hopes for another 65 successful years for Radcliff Wire.
Starrett’s headquarters in Athol, Massachusetts.
Andrew Pesaresi
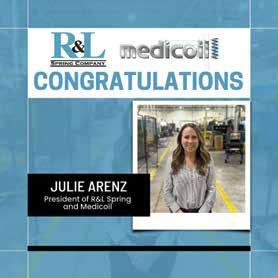
R&L Spring and Medicoil announced a leadership transition as Scott Forsythe stepped down as president after 40 years. His daughter, Julie Arenz, representing the third generation of Forsythe family leadership, has assumed the role.
Forsythe has been instrumental in the company’s growth, establishing R&L Spring and Medicoil as leaders in fabricated wire components for industrial and medical device industries.
“It has been an incredible journey leading R&L Spring and Medicoil,” Forsythe said. “I am immensely proud of our accomplishments, and I’m confident Julie is the perfect person to lead this organization into the future.”
Forsythe will serve in an advisory role, offering guidance to ensure a seamless leadership transition and the company’s continued success.
“I am honored to follow in my father’s and grandfather’s footsteps,” Arenz said. “I am grateful for the opportunity to work with our talented team and continue the legacy of excellence.”
According to the International Federation of Robotics (IFR), in 2023, U.S. manufacturing companies significantly increased automation, with industrial robot installations rising by 12% to 44,303 units. The automotive industry led the adoption, followed by the electrical and electronics sectors.
Marina Bill, IFR president, highlighted the robust demand across all major U.S. manufacturing segments. The automotive sector

saw a 1% increase in robot sales, reaching a record 14,678 units. This followed a 47% surge in 2022, positioning the automotive industry with a 33% market share of total U.S. installations. Investments are primarily driven by the electric vehicle transition and labor shortages.
The electrical and electronics industry experienced a 37% increase in robot installations, nearing pre-pandemic levels with 5,120 units and holding a 12% market share. This growth is fueled by efforts to strengthen domestic supply chains and advance clean energy projects.
Other notable sectors include metal and machinery (4,123 units, +6%) and plastic and chemical products (3,213 units, +5%), representing 9% and 7% of installations, respectively.







In Canada, robot installations rose by 43% to 4,616 units, driven by a 99% increase in automotive sector sales. Meanwhile, Mexico’s robot installations remained steady at 5,868 units, with the automotive industry accounting for 69% of this total.
INTERNATIONAL
The 2024 wire and Tube trade fairs in Düsseldorf, Germany included 1,500 exhibitors from 60 countries at wire and 1,200 from 54 countries at Tube. The fairs covered 725,487 and 561,876 square-feet respectively, making it the largest edition in their history. A total of 2,700 exhibitors showcased innovations in energy efficiency and sustainability across 1,291,669 square-feet of net exhibit space.
“The desire for personal exchange in these challenging times was evident,” said Daniel Ryfisch, director of wire, Tube & Flow Technologies
U.S. participation was strong, with 68 exhibitors at wire and 22 at Tube, many in the
North America Pavilion organized by Messe Düsseldorf North America (MDNA)
The fairs featured a robust ancillary program with lectures, presentations and digital tours focusing on ecoMetals, hydrogen and other hot topics. Experts discussed sustainability strategies and decarbonization efforts.
According to show organizers, trade visitors from 135 countries, especially Central and North America, Turkey and Asia, praised the fairs for their comprehensive and innovative exhibits.
The next wire and Tube fairs will take place April 13-17, 2026, in Düsseldorf, Germany. For more information, contact Messe Düsseldorf North America at www.mdna.com.
The Lesjöfors Group has launched an online store offering 24/7 access to what the company describes as “the widest range of standard stock springs in the world.” Over the past decade, Lesjöfors has tripled in size to a $465 million company and is now focused on leading the online standard stock sector while aiming to become the most sustainable spring and pressing manufacturers globally.
“Over the years, our mergers and acquisitions and investment program has built a global network of Lesjöfors manufacturing, sales, and distribution sites,” said Henrik Furhoff, Lesjöfors vice president and head of standard stock. “This infrastructure now supports an online purchasing platform that
provides instant access to the widest spring product portfolio in the world.”
The e-commerce website caters to DIY enthusiasts and large companies alike, offering detailed product tolerances, fast dispatch and exceptional customer and technical support services. It acts as a warehouse, providing thousands of configurations and a gas spring builder.
CEO Ola Tengroth said, “Our new web shop is a strategic move to expand our spring and pressing supply services globally.”
“We’ve been preparing for this moment to ensure we deliver a customer service and technical support platform matching the quality of our products,” Furhoff added. The rollout began in Sweden and will expand to Europe, America and Asia. z
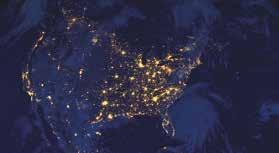
CASMI SpringWorld Right Around the Corner!
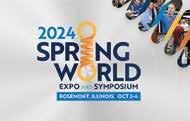
The 2024 SpringWorld expo and symposium will combine the biennial events of the Chicago Association of Spring Manufacturers, Inc. (CASMI) and SMI into one industry event. SMI will host two mornings of business and technical content on Oct. 3–4, including 24 educational sessions. The exhibit hall, hosted by CASMI, will feature OEMs, spring manufacturers, distributors, coiling, grinding, shot peening and wireforming equipment companies showcasing the newest products and latest technologies to key industry decision-makers.
For the latest updates on SpringWorld, visit the event website at www.springworld.org. The new site premieres the new event brand and provides comprehensive content on SpringWorld, including the event schedule, registration, hotel reservations, sponsorship opportunities and exhibitor information.
Upcoming CASMI Events
Aug. 29
Nov. 14
Dec. 12 Holiday Party Cooper’s Hawk, Arlington Heights, Illinois Events are subject to change. Visit casmi-springworld for the latest information.
Launched by CASMI in 1959, the show has become renowned for bringing more spring-related business people together than any other industry event. Manufacturers and attendees come from five continents to attend “The World’s Best Spring Show.” SpringWorld 2022 had more than 1,700 attendees and more than 80 exhibitors. The 2024 event is on track to exceed those numbers.
SpringWorld is conveniently located at the Donald E. Stephens Convention Center in Rosemont, Illinois, just five minutes from O’Hare International Airport, with hotel accommodations just a few steps away. The exposition is free to attend if you register in advance, otherwise the cost is $25 onsite. The symposium is $50 per person or $75 at the door. Visit www.springworld.org to register.
CASMI 2024 Scholarship Award Recipients Announced in June
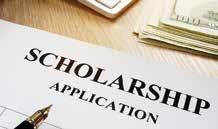
CASMI is proud to sponsor the 2024 scholarship program, which benefits dependents of member company employees. The 2024 application window closed on May 2, and announcements to award winners were scheduled to be announced in early June. We appreciate all who applied and will recognize winners in the CASMI newsletter and industry publications.
“CASMI appreciates the ability to give back to its members and the industry each year and is thankful to those who help make this happen with the support and loyalty you provide,” commented Joe Wesner, president of CASMI.
The success of SpringWorld makes it possible to fund many significant initiatives, including our scholarship program. Since the program began, CASMI and its generous donors are proud to have provided $936,250 in scholarships to undergraduate and graduate students.
WAFIOS Spring and Grinding Days Highlights
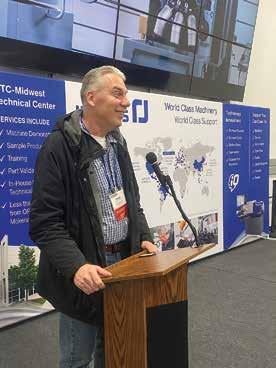
CASMI, in partnership with WAFIOS, had a great turnout at the March event. Members enjoyed an afternoon of exhibits, product demonstrations, education and networking. Exhibiting manufacturers’ representatives and a team of WAFIOS experts were on hand to demonstrate the latest technologies and make presentations, highlighting the latest developments in spring grinding and spring and wireforming technologies. Following the educational portion, CASMI hosted dinner and refreshments for all members and exhibitors.

NESMA
By Lucas Karabin, Acme Monaco, NESMA President
WAFIOS Webinar
WAFIOS held a spring and grinding webinar program, led by Markus Arnold, NESMA board member and president of WAFIOS America. Arnold and his WAFIOS team demonstrated their equipment, including high-speed coilers and state-of-the-art automated grinding systems. The attendees ranged from manufacturing participants to students in classrooms, who were reportedly excited about the technology.

Joe Wesner, president of CASMI, greets WAFIOS event attendees.
Simon Haase of WAFIOS presents at the spring and grinding webinar.
CASMI members enjoyed dinner at the educational event.
Student Outreach Programs
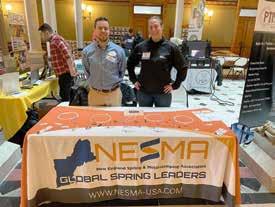
NESMA Future Leaders of Manufacturing (FLM) welcomed “Manufacturer ConneCTion Fair” attendees to the association’s booth hosted at the state capitol for the fifth time and focused on internships, apprenticeships and future college programming. The career fair’s tabletop show, free to participants, was organized by NESMA’s FLM subcommittee. The event has grown to include over 1,000 local students exploring career paths. It’s an opportunity for students to network and employers to engage the next-generation workforce.
NESMA also is sponsoring Connecticut Community College Naugatuck Valley’s summer manufacturing camp, “Introduction to Manufacturing,” which is focused on high school juniors and seniors. The event includes two separate sessions in June and July.
Technical Development
NESMA’s Technical Development Committee (TDC), led by Al Mangels of Lee Spring, is working on a pilot program allowing high school students to participate in SMI training. If a student is familiar with spring technology concepts and takes the basic course work, it could ideally lead them to an apprenticeship program.
NESMA is also partnering with local high school programs in pre-apprenticeship development and student placement. Hours from these programs can be applied towards apprenticeships in Connecticut. Mangels publishes TDC progress updates in the monthly NESMA newsletter.
Annual Golf Outing
NESMA will host our annual golf tournament again at Farmington Country Club on Aug. 26. The golf club has treated us all like members with its outstanding service and challenging course. Events committee Chair Ryan Cutter of FENN/Torin and the committee members put a lot of work into the success of our events.
To register or become a sponsor for the golf outing, scan the QR below or go to https://bit.ly/nesma-golf24.z

Legislative Watch
NESMA is a voting member of the Connecticut Manufacturers Collaborative (CMC), an alliance of industry groups working with influential state lobbyists “Statehouse Partners,” headed by Andrew Markowski and Eric Gjede. Our CMC committee, led by NESMA board member Allen Nadeau, Southington Tool and Manufacturing, tracks legislative challenges facing Connecticut springmakers. (But we’ve noticed legislation mirroring bills in neighboring states.) We are currently monitoring bills, including SB7: An Act Concerning Connecticut Paid Sick Days; SB12: An Act Modernizing the Paid Sick Days and HB5166: An Act Expanding Paid Sick Status.
Upcoming NESMA Events
Aug. 26 NESMA Golf Tournament Farmington Country Club
For an updated calendar of NESMA events, visit www.nesma-usa.com
NESMA Future Leader of Manufacturing members staff the booth at the Manufacturer ConneCTion Fair.
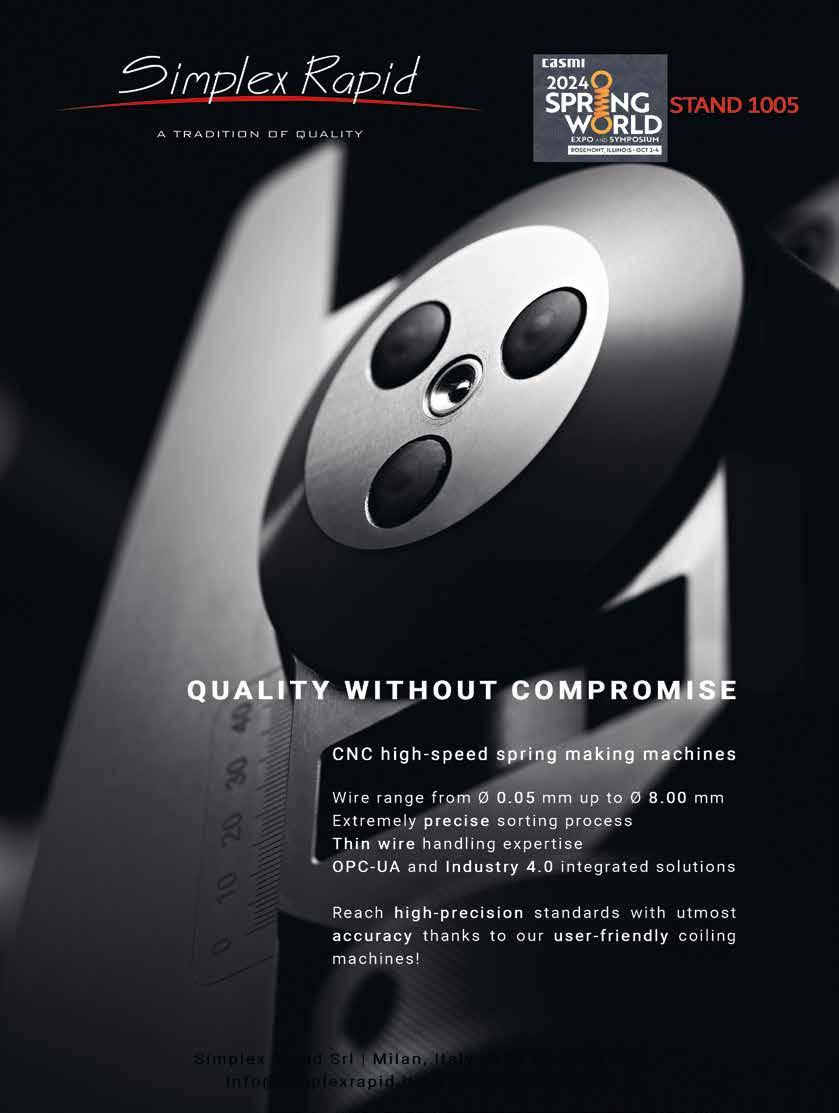

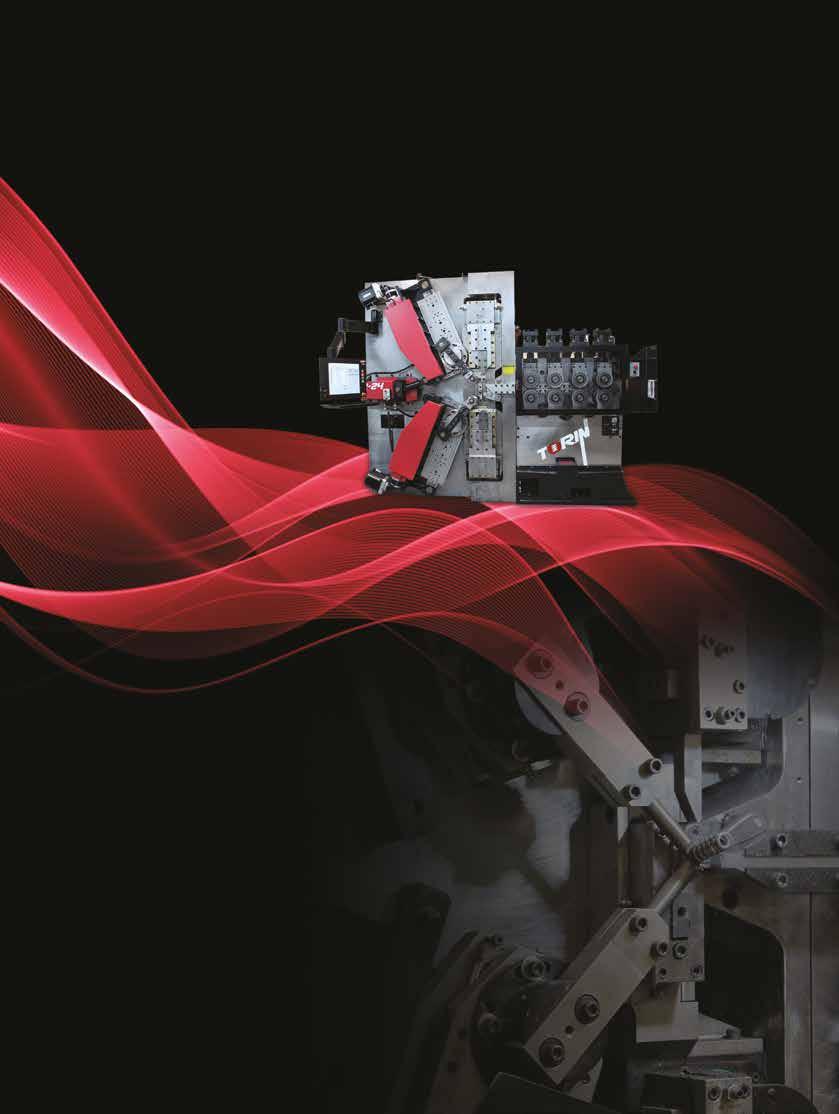

Laura Helmrich-Rhodes, CSP, Ed.D.
New OSHA Rule:
Your Safety Committee Just Got a Promotion
OSHA’s new “Walkaround Rule,” effective May 31, 2024, increases the importance of establishing employee representation in safety matters. For this reason, the role of your safety committee has become essential. When OSHA arrives, a well-trained safety committee representative must accompany the inspector on behalf of all employees. In this article, we will discuss the new rule and the role of the safety committee. The bottom line: it is time to concentrate on training your safety committee members in hazard recognition, hazard control methods, communicating employee safety concerns and how to best participate in an OSHA inspection.
The New Rule
The “Walkaround Rule,” first discussed during the Obama administration, included a public comment period but not a public hearing. As a result, many company owners are surprised to see this as an OSHA regulation, not an “OSHA standard.”1 There likely will be extensive litigation due to the haste at which it occurred and the option to invite third parties (potentially including competitors) to participate in the inspection.2
Under Section 8(e) of the OSHA Act, employees and employers have the right to have a representative accompany OSHA Compliance Officers (CSHOs) during physical worksite inspections to aid such inspections. The OSHA regulations that describe this right are under 29 CFR 1903.8. The current changes to the regulation clarify that, like employers, employees have the right to designate a nonemployee third party to be their representative.2
The Walkaround final rule clarifies that:
• The representative(s) authorized by employees may be an employee of the employer or a nonemployee third party.
• Employees’ options for third-party representation during OSHA inspections are not limited to persons with formal credentials, such as industrial hygienists or safety engineers.
• A third-party representative authorized by employees may be reasonably necessary to conduct an effective and thorough physical inspection of the workplace by virtue of their knowledge, skills or experience. This can include, for example, technical knowledge or practical experience about the processes and hazards of the type that are present in the workplace or language and communication skills that facilitate information gathering from employees.2
The Need For A Safety Committee
For many reasons (too numerous to list), I encourage all my clients to form safety committees. A few important reasons include but are not limited to: they are an excellent resource for communicating employee concerns and provide management with expertise in understanding work intricacies they otherwise would not know. Safety committees can be a value-added help in reviewing OSHA-mandated programs for appropriateness and insight as to whether the safety programs are working. The best characteristic is that it allows employees to voice their concerns (and great ideas) about environmental, health and safety issues. Learning about and reacting quickly to hazards is a valuable asset. Another reason to implement a committee is that several states grant workers’ compensation premium rebates to a certified safety committee. Check with your state to see what you save by achieving certification.
Building/Updating the Committee
Employers must exercise caution when building the safety committee to avoid violating the National Labor Relations Act (NLRA). A formal, written charter should
Be Aware
Laura Helmrich-Rhodes, CSP, Ed.D., is SMI’s regulatory compliance consultant. She is an associate professor in the Safety Sciences Department at Indiana University of Pennsylvania, teaching graduate and undergraduate classes. Contact Rhodes at SMI: 847-450-6848 laurahrhodes@gmail.com
outline the selection of representatives, terms of office and committee roles. The committee should not be directly controlled by any manager or owner. The safety committee should always act in an advisory capacity, informing management decision-makers. See the sample safety committee documents listed in the resources below. (Be sure to first check with your state to use any of their required resources for certification.) It is wise to have these documents reviewed by legal counsel to avoid violating the NLRA.
Investing in the committee’s professional development is not only a great idea and increases effectiveness, but your state may also mandate it.
Safety committee members should be trained in the characteristics of effective committees, OSHA regulations, inspection procedures, hazard identification and control measures. To be truly effective, they should be educated on how to have difficult conversations and foster leadership skills. The employees who run the committee should also be well trained in their role in the OSHA inspection process and how to be a safety champion for your organization. z
References
1. Conn, Maciel, Carey: OSHA Defense Report: Everything you need to know about the OSHA New Worker Walkaround Designation Process Rule (April 9, 2024) — https://bit.ly/SPR-3Q24-2
2. OSHA Frequently Asked Questions about the “Walk Around Rule” Worker Walk Around Final Rule - FAQ | Occupational Safety and Health Administration (osha.gov) — https://bit.ly/SPR-3Q24-1
Safety Committee Resources
TECH3 (pa.gov)
Functions and duties of the committee. This document may be helpful in the selection of members. Remember you must be careful to abide by the NLRA and your state labor laws. Note it says to stagger the terms on the committee.
https://bit.ly/SPR-3Q24-A
Sample Safety Committee Bylaws.pdf (pa.gov) This document is an example of committee bylaws. https://bit.ly/SPR-3Q24-B
LIBC-55.pdf (pa.gov)
This document has several examples and reference forms for the committee at the end. It includes the many valuable activities a committee can perform in the workplace.
https://bit.ly/SPR-3Q24-C
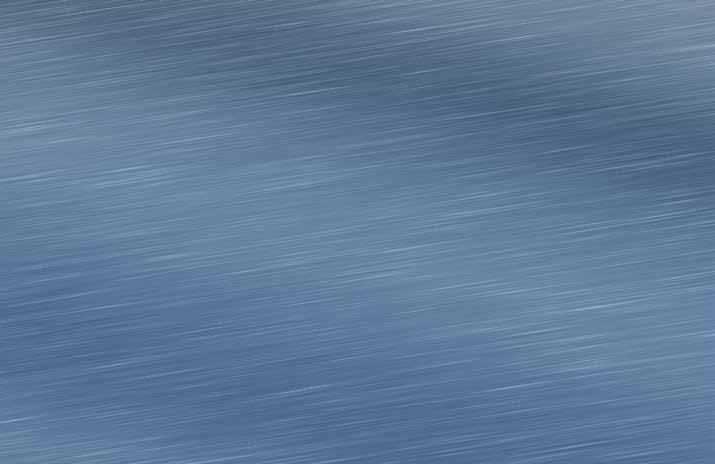
Untangle Your Spring Problem
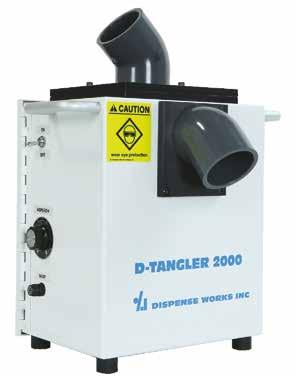


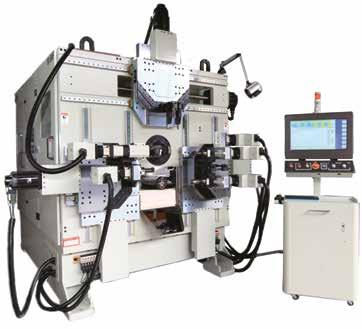
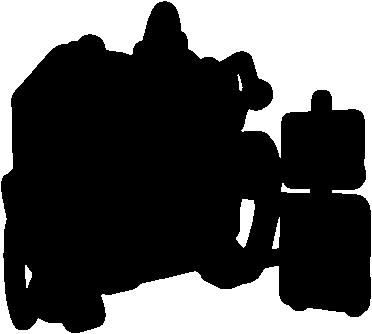
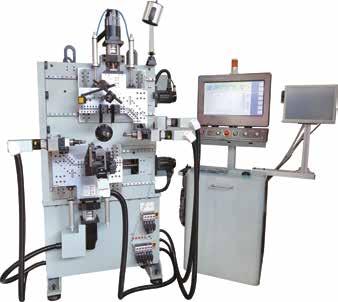
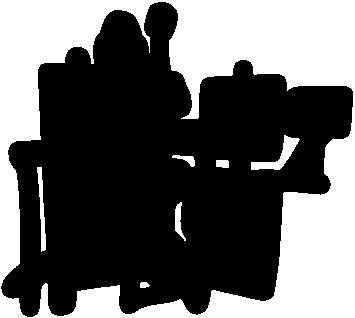
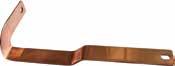

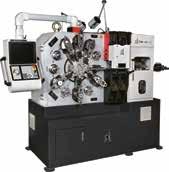
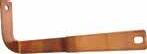
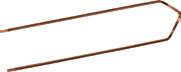
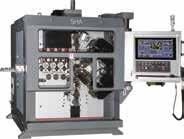
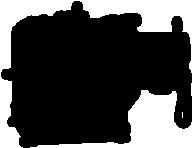
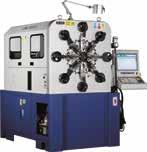

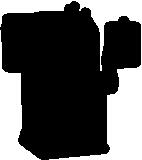
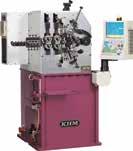

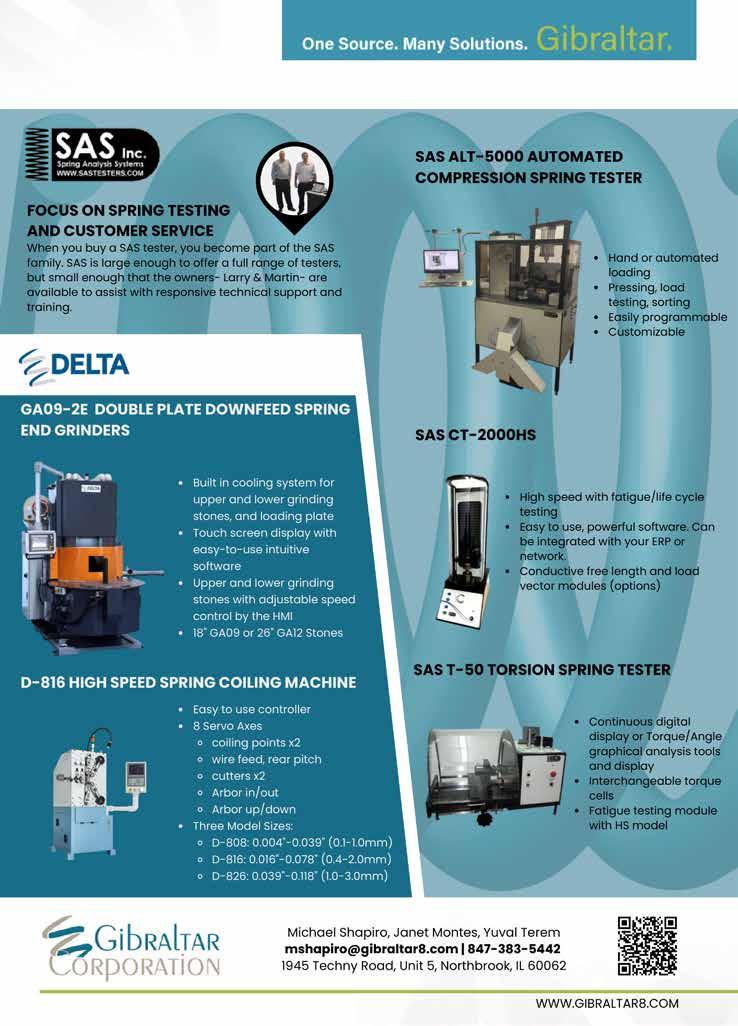
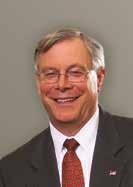
Dan Sebastian
Dean of Springs
Springs and the Automobile
The history of springs and the automobile are inalterably tied together.
Today, a significant segment of the spring industry is dedicated to automobile parts. Before the invention of the automobile, springs were largely used for carriages, rail cars, clocks, firearms and steam engines.
The incredible growth of the automobile in America was primarily driven by the quintessential American desire for individual freedom and a wanderlust to travel and explore the country. The development of the automobile created new opportunities for springmakers. Initially, it began with repurposed carriage springs and valve springs for the engine.
One of the earliest challenges springmakers faced was the life span of engine valve springs. This became a limiting factor if the automobile was to become a reliable form of transportation. Some early engines used conical springs to help with dynamic issues, but as speeds increased, inherent wire quality problems limited the reliability of valve springs.
In the late 1920s, spring engineers from Associated Spring pioneered shot peening, significantly improving durability and reliability. As wire quality increased, failures decreased. However, the automobile’s true potential to become essential in the American dream of total mobility and freedom was not yet realized.
Soon, the Great Depression slowed the auto industry’s evolution, and World War II interrupted it entirely. But the need for greater spring reliability markedly increased. The quality improvements demanded by the U.S. military were incalculable. Springmakers, like most manufacturers, introduced statistical quality systems developed by Edward Deming and Joseph Juran. This brought vehicle and motorized weapon systems to seemingly impossible levels of quality and reliability. The quality of the springs in those systems was partly why the global conflict ended.
With the war over, automotive production resumed, and the lessons learned using statistical quality control methods made springs more reliable by decreasing variations.
Postwar cars were more reliable and added creature comforts, which helped the industry grow. This put more pressure on springmakers to keep up with demand. As roads and infrastructure improved, cars symbolized the core value of freedom to all Americans.
The next step in the evolution of the automobile was speed. That produced the birth of the muscle car, pushing the demand for springs to operate at higher stress. Springmakers got help from the wire industry, which introduced surfaceprepared material. The new material had fewer surface imperfections, improving reliability and allowing springs to operate at higher stresses.
The higher stress and new environmental and safety regulations increased the operating temperature of most vehicles. Temperature increases forced springmakers to recognize that stress relaxation (load loss) needed to be considered in the spring design. The answer to this new series of challenges was new materials and the process of heat-setting springs. The continuous introduction of government regulations and customer demand for performance enhancements changed how springs were used and made.
Over the years springmakers evolved:
• Engine changes forced simple valve springs to become sophisticated dynamic components operating at elevated temperatures, and piston rings (technically springs) improved compression pressure efficiency. Fuel delivery systems changed from simple carburetors to direct injection with the help of springs.
• Transmissions evolved as engines changed. Simple hand clutches had to
Dean of Springs
change as speed and torque increased. Springs evolved with each change. The Belleville washer augmented compression. The introduction of automatic transmission inspired the slotted Belleville and various rings made with multiple geometric shapes.
• Suspension systems, which improved the ride and stability of automobiles, evolved from simple carriage leaf springs to a plethora of designs using coil springs, leaf springs, sway bars and a combination of different springs.
conditioners, assist springs in the seat belt release, push button springs around the cabin and many more.
As if those issues were not enough, current vehicles could be unsafe in an accident, and, at end-of-life, battery disposal may be a long-term environmental hazard. It will take good old American ingenuity and hard work to solve these problems. During this journey, springmakers will have the opportunity to be part of supporting many of these changes. z Dan
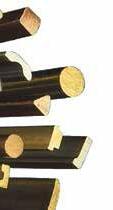
• Perhaps no area of the automobile has seen more changes and greater use of springs than the passenger compartment. The use of springs is limited only by your imagination. The seats use a wide array of springs like wireforms, cushion springs, mechanical assist and release springs. The door and trunk counterbalance come in various shapes, sizes and configurations. There are also clutch springs in air
Springs have been integral to the automobile from the beginning. Springmakers have supported all the changes, adding to automobile durability, safety and comfort. It is no exaggeration to say that there would be no automobile without springs.
The evolution of electric vehicles (EVs) will continue to include springs and wireforms. But, the EV has to overcome many obstacles, including infrastructure issues, battery range, recharging time, and reliability in harsh weather.
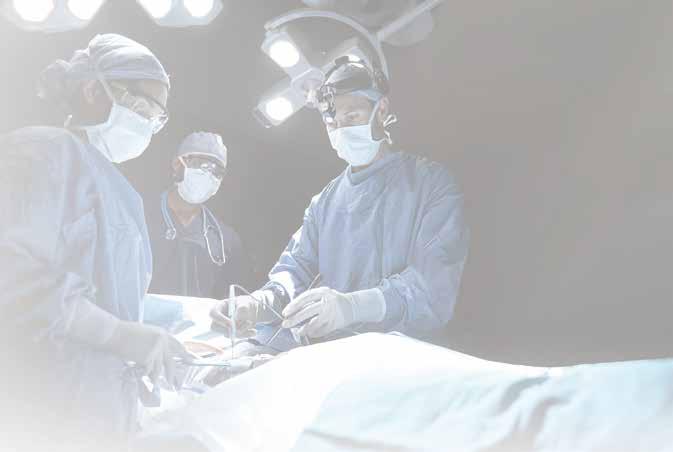

C. Richard (Rick) Gordon
Back to Basics – Extension Springs
SMI currently offers six spring design training courses, primarily as online webinars. SMI transitioned from in-person to online training during the COVID-19 pandemic, which has allowed us to cost-effectively train more students. In our 42 course offerings through May 2024, 808 students completed training sessions. We’ve received favorable student evaluations for all of our courses.
Our first three courses, 201 Compression Spring Design, 202 Extension Spring Design, and 203 Torsion Spring Design, include basic information on these spring types. We decided to feature each spring type in a series of articles in Springs. I discussed compression springs in the Winter 2024 issue1
Extension Springs
The 202 Extension Spring Design training module was first offered in 2020. Bert Goering and his team at Precision Coil Spring Company championed this module.
Extension springs exert a pulling force and store energy when extended. They are usually made of round wire and are closed wound. When we say closed wound, this means the adjacent coils in the coil body are touching. Extension springs usually have hook or looped ends. They are more complex
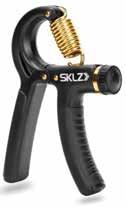
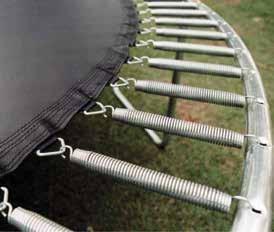
than compression springs and torsion springs in that different stresses operate in the spring body and the hooks/loops. Springs can be wound with varying amounts of initial tension. More on this later.
An extension spring is like a compression spring in that:
• Stress is torsional throughout the body, the wire in the spring body is twisted as load is applied (Figure 2)
• Equations for spring rate, torsional stress, and corrected stress are identical
• Extension springs are usually helical and can be made from round or rectangular wire
• Spring rate is constant
An extension spring is unlike a compression spring because:
• Spring rate works in reverse (i.e., a greater load/deflection means a greater length)
• Cannot buckle
• Spring diameter decreases (instead of expanding) when under load
Cylindrical helical extension spring dimensional requirements are shown in Figure 3. Free Length (Lf) of an extension spring is the distance between the inner surfaces of the ends.
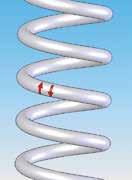
Figure 2. Schematic representation of a force applied to a helical extension spring which results in a twisting of the wire in the body of the spring generating a torsional stress (Figure courtesy of George Fournier, retired director of engineering, Acme Monaco)
Figure 1. Grip strength trainer, which uses a tapered extension spring and mechanism that allows for variable tension. Extension springs are popular on trampolines.
Mean Coil Diameter (D) is the average of the outside and inside coil diameters. It is an important parameter for many spring calculations.
Wire diameter (d) is the size of the material and is an important design parameter. Pitch (p) is the distance between the midpoint of adjacent coils.
Several parameters not shown are also important spring parameters, such as: Spring Rate (k) — The change in load per unit deflection
Initial Tension (Pi) — Amount of force needed to pull coils apart (and begin deflection)
Load (P) — The amount of (pulling) force exerted on the spring
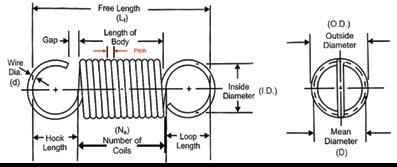
Table 1: Helical Extension Spring Nomenclature
Torsional Stress (S) — Pressure within the material caused by twisting
Modulus of Rigidity (G) — Also known as the torsion modulus or shear modulus. Property of material relating its shear stress to shear strain
Young’s modulus (E) — Also known as the modulus of elasticity or elastic modulus. This mechanical property of linear elastic solid materials defines the relationship between tensile stress (force per unit area) and tensile strain (proportional deformation)
Spring Index (C) — Ratio of a spring’s mean diameter (D) to wire diameter (d)
Density (ρ) — The degree of compactness of a substance
Table 1 of spring nomenclature is a great tool that students have found useful. Many spring companies produce springs for international clients, and the table shows the different U.S. and international spring symbols used for common parameters. U.S. and international units of measure for the parameters are also shown.
Direction of Winding
An extension spring can be left-hand wound or right-hand wound. In many cases, spring designers specify the winding direction as optional because it does not impact the performance of extension springs.
Figure 3. Dimensional requirements for a cylindrical helical extension spring (After Figure S-28 Encyclopedia of Spring Design2).
Extension Spring End Types
Figure 4 shows several cylindrical helical extension spring end types available. The end type is selected to meet specific design requirements. Hooks have gaps, while loops have little to no gaps.
Common end types include machine (aka German or full twist) or crossover center (aka English) as shown in Figure 5. Crossover ends are typically used for applications where the spring index (mean diameter/wire diameter or D/d) is greater than seven.
Threaded inserts, shown in Figure 6, are other types of ends and are some of the strongest. They are relatively heavy, expensive and convert active coils to dead coils.
What is Initial Tension?
Initial tension is the force wound into the coils of the spring during manufacture that keep the coils closed. The amount of initial tension can be varied during manufacture to achieve the design output specified on the blueprint. Initial tension is characterized as the load at no deflection. Stronger materials can withstand/support greater initial tension. An important point is that initial tension can be reduced with stress-relief heat treatment. That is why in many cases, lower temperatures and shorter times are used to stress relieve extension springs to preserve the initial tension. The “Encyclopedia of Spring Design” describes the method to measure initial tension. It is also treated in detail in SMI courses, 202 Extension Spring Design and 304 Dimensioning, Tolerancing, and Testing. Also, Gary VanBuren prepared an excellent article, “Understanding Initial Tension”, in the Spring 2021 issue of Springs magazine which is available on the SMI website3
Formulas
Formulas for stored energy, spring rate, and stress in extension springs are shown below.
Stored Energy
Energy storage capacity4 (ESC) for extension springs can be calculated using the following formula:
ESC = S2 4G
Where:
S = torsional stress
G = modulus of rigidity, shear modulus or torsion modulus
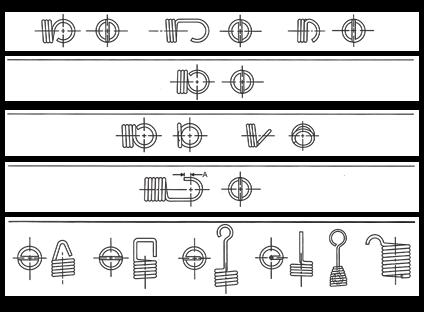
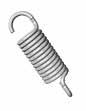
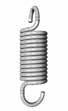
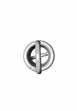
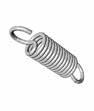


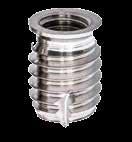
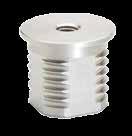
Spring Rate
For extension springs, the equation to calculate the spring rate (k) is:
k = Gd4
8N a D3
Where:
G = modulus of rigidity, shear modulus or torsion modulus
d = wire diameter
Na = number of active coils
D = mean spring diameter
Figure 4. Cylindrical helical extension spring end types (Based on Figure S-26 from the Encyclopedia of Spring Design2).
Figure 6. Threaded inserts.
Crossover Extended Machine Hook
Machine Loop
Loop
Hook
V Hook Square Hook Extended Loop Eye Swivel Loop Eye Extended Hook
Diagonal Loop
Machine Hook
Figure 5. Extension spring end comparison for machine and crossover center ends.
Machine — German — Full Twist
Crossover Center — English
Technically Speaking

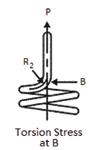
When measuring spring rate, the following equation can be used:
k = P2 – P1 f2 – f1
Where:
P1 & P2 — loads f1 & f2 — corresponding deflections
Stress
The stress in an extension spring is due to the twisting of the wire in the coil body which is a torsional stress as shown in Figure 2.
Extension springs are more complex in terms of stress because different stresses are present in the coil body and in the hooks or loops.
In the coil body, due to the curvature of the helix, the stress will distribute unevenly across the material section. This is why stress correction factors and corrected stress values are used in calculations.
S = 8PD Kw πd3
Where:
S = torsional stress
P = load
D = mean spring diameter
d = wire diameter
K w = stress correction factor
Kw = 4C – 1 + 4C – 4 0.615 C
C = spring index
C = D d
Stresses in hooks and loops can be higher than in the coil body and involve both bending stress and torsional stress. Figure 7 shows the location of the maximum bending stress (A) and torsional stress (B) in a machine hook end.
Equations for calculating the maximum bending stress (SA) at position A and torsional stress (SB) at position B are shown below.
The good news is that stress values are calculated directly in the Advanced Spring Design software5
Summary
This article presents basic information on helical extension springs to help new spring industry associates and veterans. Some helpful hints when designing extension springs for users of SMI’s Advanced Spring Design (ASD) software will be discussed in a separate Springs article.
Compression springs along with an article describing the use of ASD software were discussed in previous Springs articles1, 6 Torsion springs will be addressed in a future Springs article. z
References
1. Gordon, C.R., Back to Basics — Compression Springs, Springs, Winter 2024, p.19. https://bit.ly/SPR63-01-19
2. Encyclopedia of Spring Design, Compression, Extension, Garter and Torsion Springs, SMI 2000.
3. Van Buren, G., Understanding Initial Tension, Springs, Spring 2021, p. 21. https://bit.ly/SPR60-02-19
4. Encyclopedia of Spring Design, Fundamentals of Spring Design, SMI 2000.
5. Advanced Spring Design (ASD) software, 6. www.smihq.org, www.uts.com/Products/Asd
7. Gordon, C.R., Designing Compression Springs Using SMI’s ASD Software, Springs, Spring 2024, p19. https://bit.ly/SPR63-02-19
Want to Learn More?
For a more detailed treatment of extension springs, be sure to enroll in the next SMI 202 Extension Spring Design webinar, scheduled for Thursday, Nov. 14, 2024, 1–5 p.m. Eastern time. (www.smihq.org/page/spring-design-trainingprogram) SMI also offers on-site technical services. If you would like to have one of our experts teach a training module (or two) at your location, please contact SMI for information and pricing.
To register for this class or others, visit https://bit.ly/SMItech.
is the technical director for SMI. He is available to help SMI members and non-members with metallurgical challenges such as fatigue life, corrosion, material and processrelated problems.
Contact Gordon at 574-514-9367 or c.richard.gordon@gmail.com.
Recommended practice is to make C2 greater than four.
C. Richard (Rick) Gordon
Figure 7. Spring end maximum bending and torsion stress locations.
Bending Stress at A
Torsion Stress at B
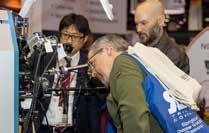
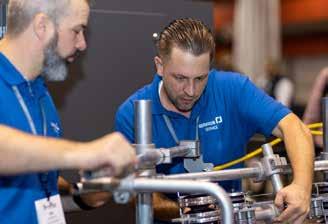
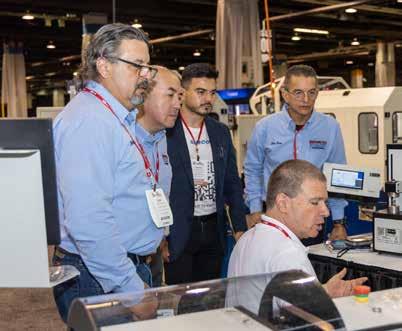
EXPO AND SYMPOSIUM
ROSEMONT, ILLINOIS • OCT 2-4
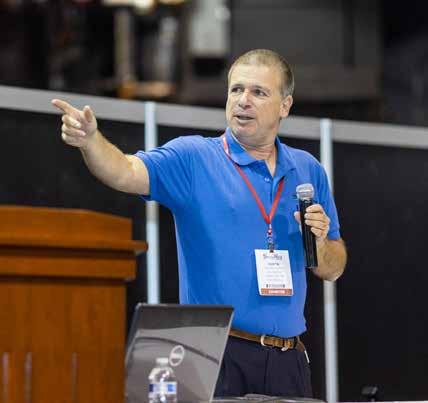
Chicago Association of Spring Manufacturers, Inc. (CASMI) and The Spring Manufacturers Institute (SMI) have partnered to combine the two organizations’ semi-annual events into one industry foremost event. The joint SpringWorld Expo and Symposium will be held October 2-4, 2024, at the Donald E. Stephens Convention Center in Rosemont, Illinois. In addition to the CASMI hosted exhibit hall, SMI will also host two mornings of business and technical content, including 24 educational sessions. Exhibit hall hours will be similar to prior years and the technical theater and receptions return! Don’t miss this comprehensive educational and networking event to learn the latest from suppliers and educators.
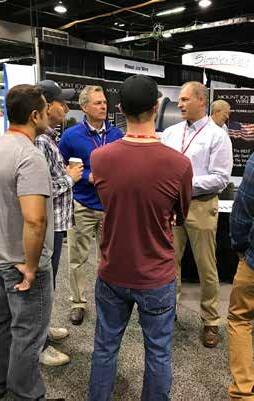
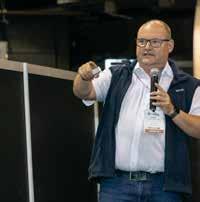
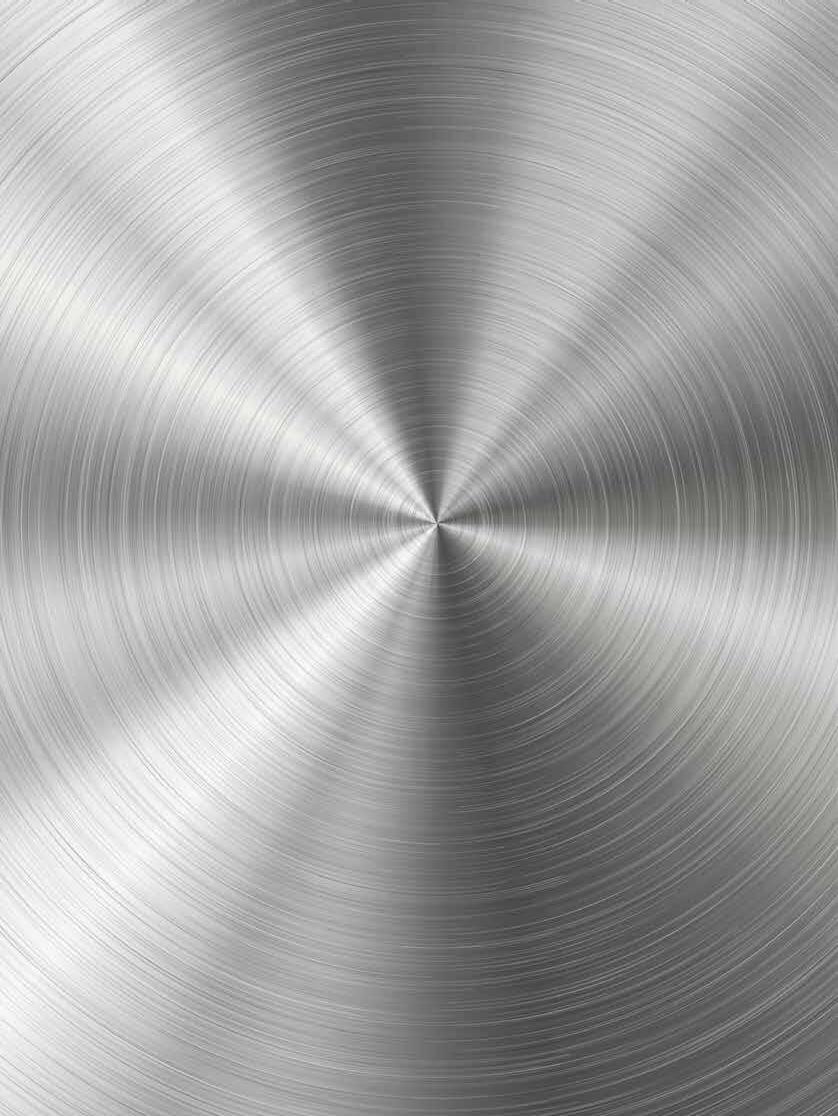
By Phil Sasso
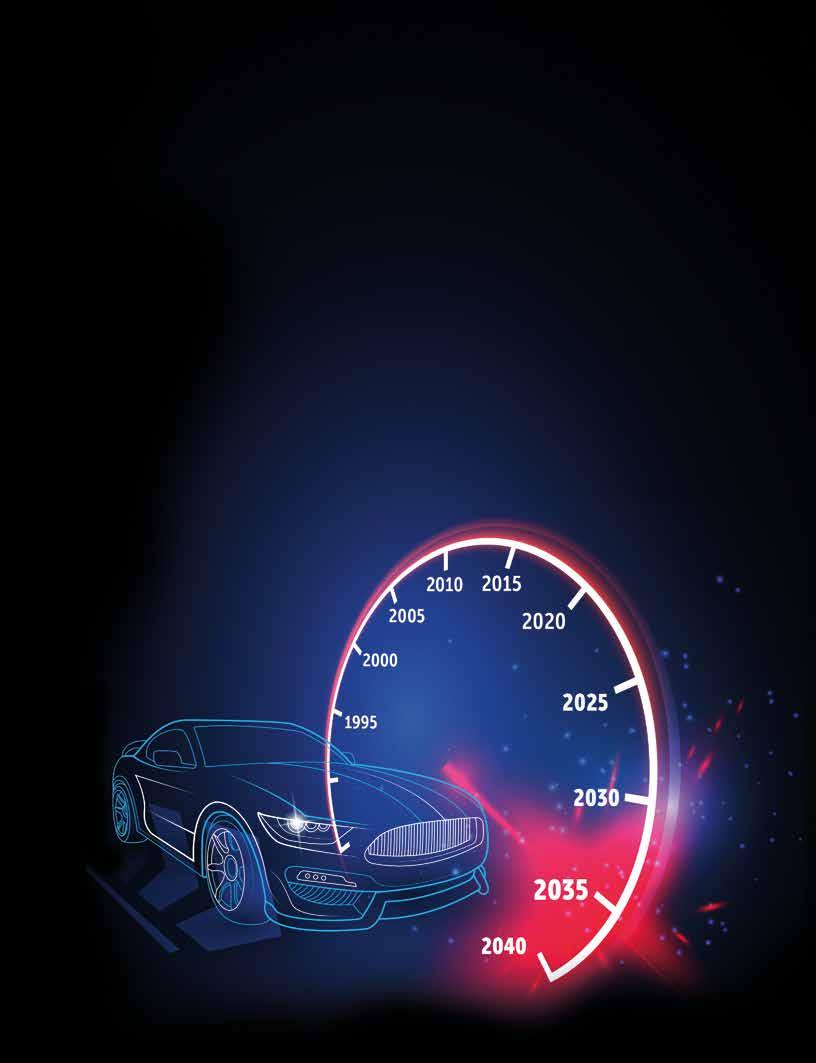
The Changing
Over the last decade, automotive technology has advanced at lightning speed. Technologies like automatic emergency braking, lane departure warnings, blind-spot monitoring, self-parking features and remote diagnostics are now commonplace. But, experts agree the trend with potentially the most dramatic impact on the spring industry is the inevitable transition to the electric vehicle (EV).
In the Rearview Mirror
Since the 1870s, the spring and automobile industries have been intertwined.
In our Flashback, “The Interrelationship of the Automobile and Spring Industries” (p. 42), we learn that car production was skyrocketing just before the U.S. entered World War II. “Spring plants multiplied and expanded to meet the demand for the 147 different springs … in the average car.”
Former SMI president and Dean of Springs, Dan Sebastian, echoes this history lesson in his column “Springs and the Automobile” (p. 19).
“The evolution of EVs will continue to include springs and wireforms,” predicts Sebastian.
“But, the EV has to overcome many obstacles, including infrastructure issues, battery range, recharging time and reliability in harsh weather.”

Automotive Market
Navigating Transition
SMI member Agustín Estalayo from RPK Mexico explores EV’s bumpy road to the future in “eMobility and the U.S. Automotive Market” (p. 30). “A battery electric vehicle (BEV) with current lithium battery technology could mean the end of the most profitable springs in the internal combustion engine (ICE) engine,” says Estalayo. But he concludes, “The ICE in the U.S. is nowhere near dead yet, making the demand for ICE springs likely to remain strong for years or decades to come.”
Many springmakers are transitioning to produce new spring and wireform products to circumvent a decline in ICE springs. An example of this can be found in “Innovations in Stator Windings” (p. 32) by Simon Haase, applications engineer for WAFIOS. Haase provides technical insights into improved production techniques for EV stator motor windings.
Powering the Future
The spring industry and the automotive market will likely take a few detours until government zero-emission vehicle (ZEV) mandates and consumer buying patterns converge.
By 2050, about half the vehicles on the road will still have ICE, projects automotive industry expert and futurist Derek Kaufman in “2035: An EV Odyssey?” (p. 30). In the same article, automotive technology expert, speaker and trainer Bill Peek says, “EV technology is here. The infrastructure just needs to catch up.
“Right now, plugging in your EV is like running 48 refrigerators in your garage,” Peek concludes. That’s a lot of power draw — much more than the current electric grid can produce as we strive to build an all-EV world.
Working together, the spring industry will find new markets, perhaps in EV components, charging stations, and power production and distribution. However, history shows us whatever obstacles are found in the road ahead, springmakers always find their way through. z
A to Z EV Glossary
Some words in this special section may read like alphabet soup. Here are definitions of several acronyms and phrases:
ACT (Advanced Clean Truck): standards requiring all medium- and HD vehicles produced to be ZEVs by 2045.
BEV (Battery Electric Vehicle): A fully electric car powered by a battery and electric motor with no gasoline engine.
CARB (California Air Resources Board): Part of the California Environmental Protection Agency established in 1967. It sets emissions standards for vehicles and fuels that 17 states have adopted.
Charging Methods: Level 1 is the slowest method, typically used for overnight charging at home. Level 2 is faster than Level 1 and is often found at public charging stations and workplaces. DC charging, the quickest method, uses direct current.
EV (Electric Vehicle): A general term for a vehicle that uses electricity as its primary power source, including BEVs, PHEVs, and HEVs.
HEV (Hybrid Electric Vehicle): A car with an electric motor and gasoline engine. HEVs do not plug in. The gas engine or regenerative braking charges the battery.
kW (Kilowatt): The power unit used to measure charging speed.
ICE (Internal Combustion Engine): An engine that burns fuel to generate mechanical energy, commonly used with gasoline, diesel or natural gas.
LEV (Low-Emission Vehicle): A car or truck with lower-than-average nitrogen oxide, carbon monoxide and hydrocarbon emissions.
PHEV (Plug-in Hybrid Electric Vehicle): A car with an electric motor and a gasoline engine that can be plugged in to charge but also runs on gasoline.
Range: The maximum distance an EV can travel on a single full charge. Fear of running out of battery power far from a charging station is called “range anxiety.”
Regenerative Braking: A system that captures energy from braking and uses it to recharge the battery, extending the EV’s range.
ZEV (Zero-Emission Vehicle): A vehicle that produces no tailpipe emissions, including EVs and hydrogen fuel cell vehicles.
By Phil Sasso
2035: An EV Odyssey?
The transition to electric vehicles (EVs) will impact springmakers who currently produce components for engines, brakes, transmissions and other systems for internal combustion engines (ICE). Those not presently involved in the automotive or heavy-duty industries may want to reconsider because of new opportunities to produce springs and wireforms for various components required by EVs.
The EV movement is being driven by the California Air Resources Board (CARB). The objective of the agency’s zero-emission vehicle (ZEV) program is to reduce emissions by phasing out the sales of consumer, light-duty and off-road internal combustion engines (ICE) by 2035 and by eliminating new medium- and heavy-duty diesel ICE trucks by 2045.
The impact of CARB is significant because 17 states and the District of Columbia, representing 39% of the U.S. population, have adopted the agency’s ZEV standards.
To EV or Not to EV?
While EVs are the anticipated ZEV of choice, hybrids and alternative fuels also have a significant role to play, said Derek Kaufman, a transportation industry expert and managing partner at Schwartz Advisors.
“There are several solutions that are very low carbon or near zero emission, including biodiesel, hydrogen-infused diesel, and synthetic fuels,” Kaufman said. “These alternatives can keep internal combustion engines operational with minimal environmental impact, offering a bridge during the transition to fully electric vehicles.”
“CNG (compressed natural gas) and propane offer another option while the infrastructure is built out, especially for fleets,” said Bill Peek, automotive and heavy-duty vehicle curriculum developer, trainer and president of MPC Publishing. “EV technology is here. The infrastructure just needs to catch up.
“Right now, plugging in your EV is like running 48 refrigerators in your garage,” Peek explained. That’s a lot of power draw — much more than the current electric grid can supply if EV sales increase in step with government mandates.
Cautious Consumers
ABI Research projects global EV sales growth will slow to 21% in 2024 and 19% in 2025. This represents a significant dip from growth rates of 31% in 2023 and 60% in 2022.
Excess EV inventory at U.S. dealerships also suggests the initial surge in demand has tapered off.
“The reality of some of the limitations of EVs, such as range and cold weather performance, has begun to set in,” Kaufman said. In cold climates, EVs can lose a significant portion of their range overnight due to the energy required to keep the batteries warm.
“A friend of mine parked his Ford F-150 Lightning with 300 miles of range overnight in Iowa, and by morning, it had only 200 miles of range left,” Kaufman added anecdotally. “It hadn’t moved an inch, but the system’s work to keep the battery warm in the cold weather drained the battery significantly.”
The price point of an EV is about double an ICE vehicle. This is also a deterrent for many buyers.
Battery Blues
A few other battery technology issues may hobble the adoption of EVs.
Several minerals required in EV batteries, including lithium and cobalt, are mined overseas, making the U.S. EV market dependent on foreign sources.
“There’s lithium in America, but nobody wants to mine it because of environmental hazards,” said Peek. Additionally, the safety of EVs in collisions is still being determined, as battery fires are common.
While Peek acknowledges ongoing research into new battery technology could change the landscape, he admits there's no guarantee of a breakthrough that would significantly improve range or reduce charging times.
Lagging Infrastructure
EV range anxiety, fear of a lack of battery power or charging stations to reach the final destination, is also impacting EV sales. Earlier this year Google Maps launched a feature that can flag EV chargers along a route.
In an AAA survey, 56% of U.S. consumers said a lack of public charging stations is why they chose not to buy an EV. A significant build-out of public charging stations may be needed for consumer EV demand to meet government mandates.
The U.S. Department of Energy website shows 176,586 public EV charging ports across the U.S. as of June 7, 2024. Three-quarters of those ports are Level 1 or 2 AC slow chargers best suited for locations where drivers will park for an hour or more. The remaining one-quarter are DC fast-charger ports are best suited for highway waysides. By comparison, there are 4 million electric vehicles (EVs) on the road in 2024, representing about 1% of all vehicles, according to the DOE.
“Congress has committed $7.5 billion toward adding 500,000 EV chargers,” Kaufman said. “In almost two years since that's been allocated, there have been eight chargers installed by the federal government.
“The Empire State Building was built in 410 days, and it's taken us two years to put in eight chargers,” Kaufman quipped.
Charging at Home
“All the people who originally bought Tesla’s were mostly high-income people who own homes and charge them in their garage,” Kaufman said. “As you come up Moore's curve past initial innovators and early adopters, you get to the early majority. That’s when things get more complicated. These people may not own houses, they may live in apartments or condos. Now, there aren’t enough chargers in their parking lot, or they have street parking.” This may be further challenged by the issues of outdoor parking at low temperatures.
“It’s a complicated thing that we should allow consumer demand to define, but [CARB] and the federal government are trying to force-fit it,” Kaufman said.
“The only thing pushing EVs is politics right now,” Peek said. This pressure on manufacturers and dealerships might not be sustainable in the long run, especially if political winds change, explained Peek.
Long-Haul Hurdles
Twelve of the 17 states that follow CARB’s ZEV program have also adopted Advanced Clean Truck (ACT) standards requiring all medium- and heavy-duty vehicles sold be ZEV by 2045.
Heavy-duty “combination trucks” produce about 20% of U.S. vehicle emissions while accounting for only 1% of vehicles according to a video on the Tesla website.
But there are significant hurdles for long-haul trucks to switch to ZEV, Peek said.
For example, the Tesla Semi, a battery-electric Class 8 heavy-duty truck, began limited production in late 2022. PepsiCo has received many of the deliveries to date.
“With less than 2 kWh per mile of energy consumption, Semi can travel up to 500 miles on a single charge,” reads the Tesla website. By using Tesla’s specially designed Semi chargers, it can recover up to 70 percent of its range in 30 minutes.
However, the lack of a public HD charging infrastructure remains a major obstacle. Peek emphasized that while EVs may eventually be able to replace school buses and garbage trucks, long-distance trucking with the current technology and infrastructure is not yet practical.
Spring Industry Implications
A shift to EVs will impact the spring manufacturing industry. Phasing out ICE vehicles means declining demand for springs used in internal combustion engines, such as valve springs.
“The valve train is going away, and that’s a loss for the industry,” Kaufman admitted.
“We think the undercar suspension situation is actually very favorable,’ Kaufman said. “Because of the weight of batteries and the torque. Electric motors can produce very high torque.” The weight and torque put a lot of strain on the suspension and may require more frequent replacement.
Also, EVs require unique springs and wireforms in various components, creating new opportunities for springmakers.
Down the Road
Despite challenges, the transition to EVs is inevitable, albeit likely at a slower pace than some policymakers envision.
Infrastructure development, battery technology advancements and economic considerations will all determine the ultimate trajectory of EVs, Peek said.
“We project that about 50% of vehicles on U.S. roads in 2050 will still be ICE, while the other half will be battery electric,” Kauffman stated. This scenario reflects a more pragmatic approach to a complex and multifaceted transition to zero emissions.
“While the regulatory landscape is driving significant changes, the industry’s ability to innovate and adapt will be crucial in navigating the future of automotive technology,” Kaufman concluded.
The spring manufacturing industry can adapt by innovating and diversifying its offerings to meet the new production needs of EVs and ICE vehicles. z
Additional sources: www.afdc.energy.gov/laws/california-standards www.business.ca.gov/industries/zero-emission-vehicles/zev-timeline/ www. afdc.energy.gov/stations/states
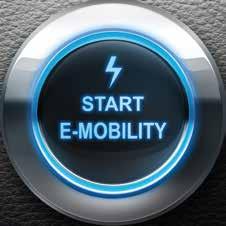
By Agustín Estalayo
eMobility and the eMobility and the
The trend toward electromobility (eMobility) in the automotive market is an unstoppable pattern. eMobility refers to the use of electrified vehicles for transportation purposes.
The timing of its adoption is not clear yet in the U.S., as automotive technology continues to evolve toward eMobility as electric vehicles (EVs) become a larger part of the market. As a result, the demand for springs in internal combustion engines (ICE) and transmissions could decline dramatically.
U.S. Demand for EVs Has Hit a Wall
While U.S. and international automotive OEMs have been actively changing manufacturing platforms from ICE to EV, the demand for EVs in the U.S. has not kept pace. We are not seeing the market share for pure battery electric vehicles (BEVs) escalate at initially forecasted levels.
(See Chart 1.)

According to many sources, this is an unexpected outcome. Consumers are willing to buy EVs if their expectations are met. But can OEMs catch the next wave of EV adopters? According to Boston Consulting Group (BCG) up to 70% of U.S. consumers are considering an EV.1
“A narrative has emerged lately that U.S. demand for EVs has hit a wall,” says BCG. “Inventory piled up and a ‘price war’ ensued that dominated headlines. OEMs have since slashed production targets and delayed product launches. To add to the general sense of pessimism, customers continue to express concerns over high costs, unpredictable residual values, frustrating charging experiences and poor range in colder weather.”2
Misunderstanding the U.S. Customer Journey Life Cycle
The EV may be a perfect solution for moving around big cities (like in China or Europe). However, the EV battery functionality is reduced dramatically over long distances and on highways. In city driving, where aerodynamics don’t matter as much, the brakes are constantly being applied and energy is being recovered and converted back to electricity.
Considering the customer journey life cycle (See Chart 2), the EV market share is not growing as projected because it is not meeting the needs of many customers. In the digital world we live in, the number of buyers sharing their problems with EVs on social media has reinforced the impression that EVs are not for everyone.
The mass-produced car was developed in the U.S. at the turn of the 20th century. It helped people move from point A to point B. Soon, people could drive long distances, which created a
Chart 1: S&P study shows meager BEV sales growth since Jan. 2022.
U.S. Automotive Market U.S. Automotive Market
sense of freedom. Autonomy and the automobile became part of the American DNA.
The U.S. infrastructure was based on cars. Public transportation was not a part of urban planning, as it was in China or Europe. There, the BEV is an extension of public transit. In many places in the U.S., you can only get from point A to B by car.
Current BEVs work best for people who travel short distances or inside city limits, where charging is not an issue.
When traveling longer distances in a pure BEV, you need to plan carefully for the temperature, speed, distance and availability of public charging stations. Unlike gas or diesel, charging takes time. So, on a holiday road trip, you’d also need to consider the charging needs of other travelers in BEVs.
Conclusion
The last word has not been written on the transformation of the automotive market from ICE to EVs. For most U.S. consumers (even those concerned about climate change) hybrid electric vehicles (HEVs) offer the best solution. In the U.S. the automobile symbolizes a sense of freedom. For that reason, hybrid electric vehicles (HEVs) may be the eMobility trend for the foreseeable future.
HEVs maintain the same level of springs as a current car by using both ICE and EV technologies.
A BEV with current lithium battery technology could mean the end of the most profitable springs in the ICE engine.
Also, the current lithium-ion battery BEV, makes the whole supply chain heavily dependent on China. That is why the Inflation Reduction Act (IRA) of 2022 established provisions to explore various different energy sources and to maintain a sustainable supply chain within the eMobility automaker industry in North America.

Perhaps changes in current ICE technology, such as using hydrogen, could be part of the future of the eMobility model. The ICE in the U.S. is nowhere near dead yet, making the demand for ICE springs likely to remain strong for years or decades to come. z
References
1. BCG Adoption Survey (January 2024)
2. Can OEMs Catch the Next Wave of EV Adopters? (BCG, March 20, 2024)
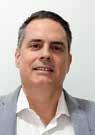
Agustín Estalayo is CEO of RPK Mexico. He has more than 20 years of strategic and daily operations experience and oversees the company’s NAFTA operations. He is a prior member of the SMI board of directors and currently serves on the association’s communications committee. Estalayo holds a BBA from Deusto Business School in Spain, a global executive MBA from Instituto Tecnologico Autonomo de Mexico and a global business MBA from Tulane University.
Chart 2: BCG survey indicates 70% of consumers considered an EV, but 57% do not plan to
one as their next vehicle.
By Simon Haase Applications Engineer WAFIOS
Editor’s note: As consumer and heavy-duty electric vehicle (EV) sales continue to grow, springmakers are getting more orders for new spring and wireform products. One of those items is stator windings. This article explores techniques to improve the power density of stator windings.
IN STATOR WINDINGS
There are many innovations in stator winding technology, including axial flux, raxial flux and toroidal flux. However, the more conventional hairpin design is still prevalent and definitely not at the end of its advanced possibilities. Refined motor designs can improve performance and efficiency. One key to increased power density is the copper fill factor, which requires suitable material and production techniques.
Copper conductors for EV applications are rectangular to increase the fill factor, in contrast to round wire, which is used in common motor windings. Rectangular wire geometries (such as those for hairpins) bring some challenges. When bending hairpins over the shorter edge, it is especially important to ensure the parallelism of the legs, the correct shoulder width and the accurate position and rotation of adjacent wire lengths.
Traditional bending uses a bending pin and bending mandrel, which doesn’t give enough
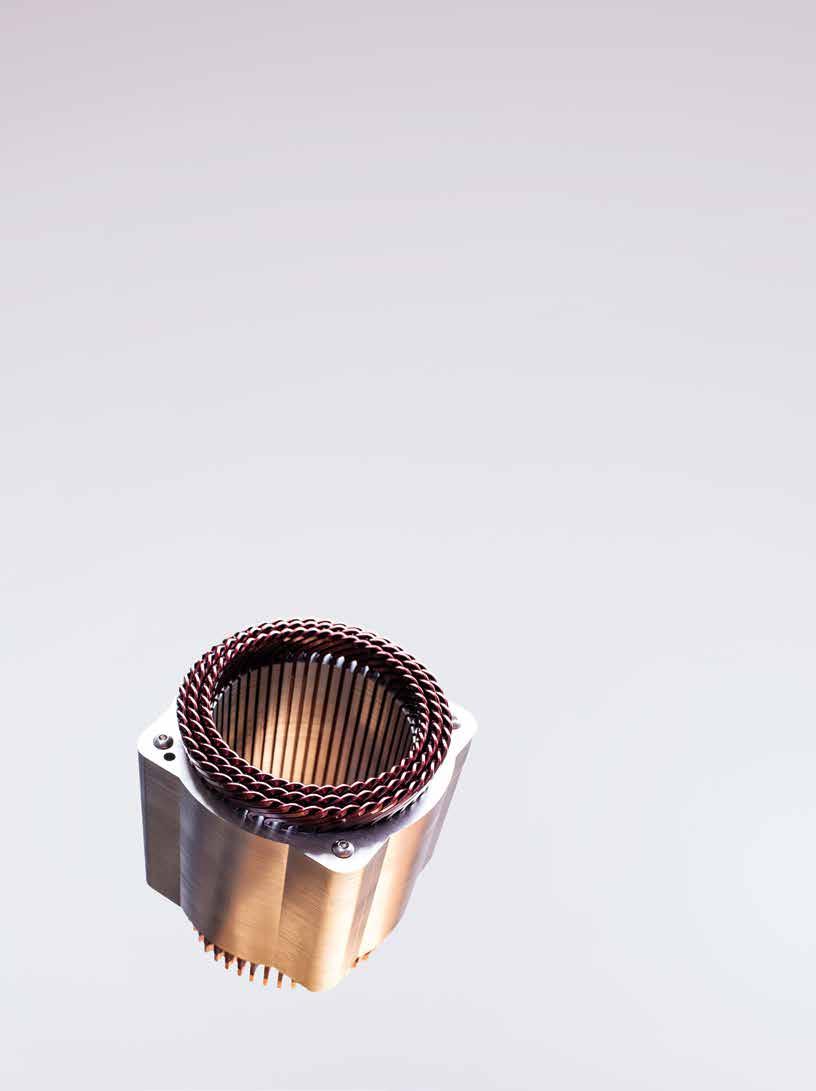
guidance and control over the geometry, especially for larger bending angles. A long-proven method of bending delicate tubes, called rotary draw bending, can be applied to this situation. The free end of the wire is clamped, and as the mandrel turns the material is fed into the bending area to ensure the material is not stretched. For tubes, this provides a consistent inner cross section even in the bend. This also works for rectangular copper wire, which has the added challenge of delicate insulation that can be damaged if over-stretched or relative tooling movement occurs. Also, the clamping can keep previous bent parts stable while executing “compound bends,” where bends over the long and short edges are right on top or very close to each other.
Edgewise Bending Reduces Thickness
Rotary draw bending is a good solution for hairpins but is unsuitable for producing axial flux coils and their variations without another development step. Executing a rotary draw bend still allows for a slight thickening of the material on the inner radius of the material so that it is trapezoidal to some degree. While this is not critical for hairpins, it reduces the fill factor when several bends like this are stacked on top of each other, like in an axial flux coil. The thicker part of the material lies on top of each other, keeping the single coils further apart. This thickness can be increased between 15-20%.
Applying a tool to the side of the bend material minimizes the forming of this trapezoidal cross section in the wire. The advancement with this “edgewise bending” technology reduces the thickening to 1-2%. The material is clamped vertically and horizontally before executing the rotary draw bend described above, ensuring equal material flow and a result with higher power density. This technique can also be utilized with “bending after the cut” technology to produce two neighboring axial flux coils. This effectively reduces weld points and potential component failure points.
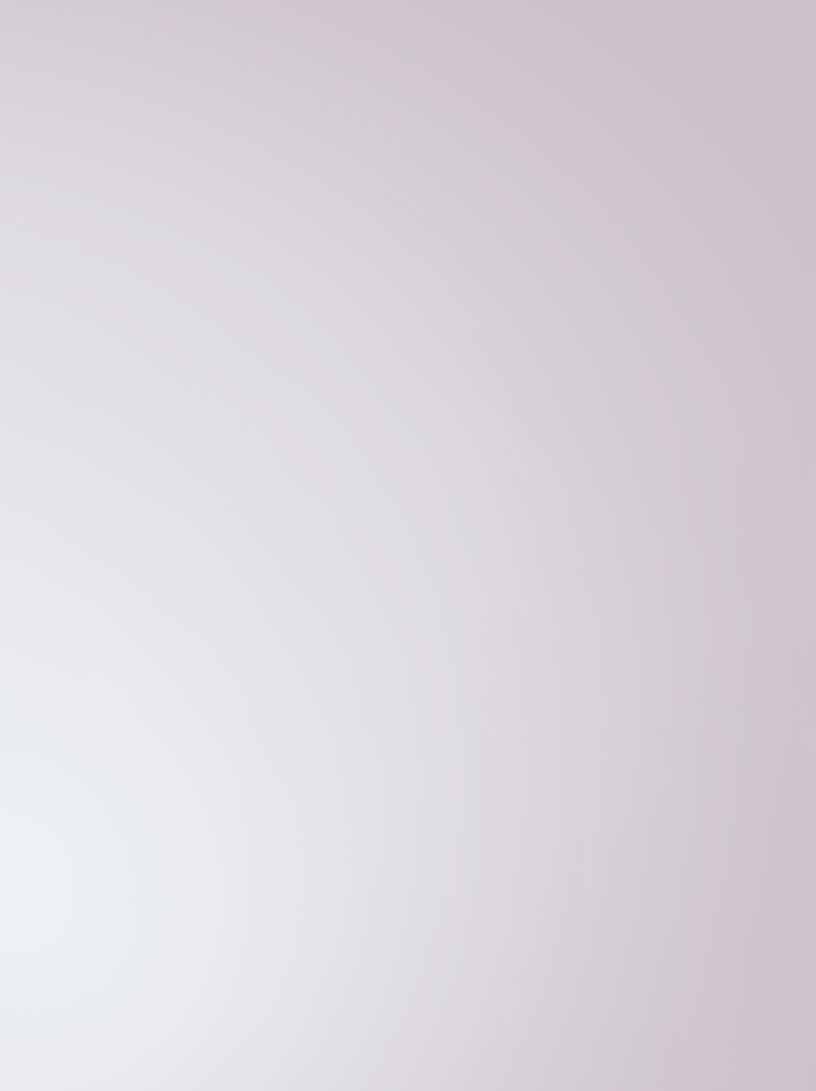
HQ Bending Utilizes Unique
Tooling Concept
HQ bending stands for “High-Quality bending” and advances the technology further. A more compact crown geometry (known as “winding head”) is favorable for building smaller and lighter motors. To achieve this, the “edge-wise bending” technology can be applied to the hairpin bending process. A more compact crown geometry can be achieved by changing the sequence of the process steps. Specialized tooling and tool positioning are necessary to realize this sequence.
This allows making the flat bends in the crown utilizing the edge-wise bending technique and executing the bends for the offset in the middle of the crown (known as “S-bend”) afterward. “HQ bending,” realizes very high fill factors in the stator and compact crown geometries that are even more compact than can be achieved with hairpins produced by die-forming.
This process retains flexibility and can speed up workpiece adjustments and changeovers. Additionally, the flexibility of the described CNC equipment and technology makes it possible to manufacture complete parts on one machine without additional process steps. Combined with other optional equipment, laser edging or milling can remove the insulation on the ends of the hairpins, coils or busbars.
Flexible machine solutions can produce variations of a part by program changes, reducing the time to market, shortening setup times and reducing costs. Customers in this fastmoving market often request extreme flexibility for their development and production. In contrast to bending technologies with dies, 3D bending technology can perform when extreme demands for flexibility and accuracy are needed. z
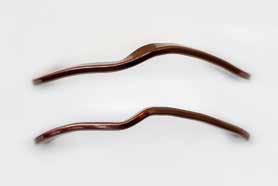
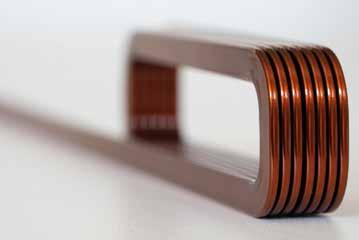
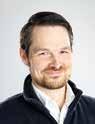
Simon Haase is an applications engineer for WAFIOS in Mokena, Illinois. He specializes in the EV industry, providing technical consultation and sample production for parts like hairpins, axial flux coils and busbars. Before moving to the U.S. in 2023, he worked six years for WAFIOS Reutlingen, Germany. Haase studied mechanical engineering in Dresden, Germany.
WAFIOS has been involved in wire bending for 130 years. The company entered the EV market in 2014, developing solutions for bending hairpins, axial flux coils and busbars. WAFIOS supports customers from prototyping, tool design and engineering to sample, small series and mass production.
Crown geometry produced with minimal thickening using “HQ bending” technology.
Compact, stacked windings of an axial flux coil with minimal thickening.

PASSING THE GAVEL
By Phil Sasso
The palm trees and bay views from San Diego’s Coronado Island provided a breathtaking backdrop for SMI’s 2024 annual meeting, “A Roadmap For The Future,” at Loews Coronado Bay Resort, April 6–9.
Leadership Transition
Every two years, SMI welcomes a new president and executive committee members at its annual meeting. This year, Don Jacobson III, vice president of business development of Newcomb Spring Corp., was installed as SMI’s new president, and Gene Huber Jr., executive vice president of Winamac Coil Spring, Inc., ended his two-year tenure. Huber will now serve as the immediate past president.
The remainder of the executive committee includes vice president David DeVoe, president of Plymouth Spring in Bristol, Connecticut; secretary/ treasurer Dave Deerwester, president of The Yost Superior Company, Springfield, Ohio; and at-large representative Joe Devany vice president of manufacturing, Betts Company, Fresno, California.
Jacobson Accepts the Gavel Jacobson is the third generation in his family to serve as SMI president.
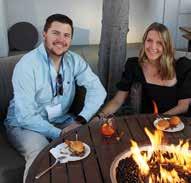
Jacobson follows in the footsteps of his grandfather, G. Donald Jacobson Sr., who served as SMI president from 1960-1962 and his dad, G. Donald Jacobson Jr., who served as president from 1995-1997. Jacobson has been a long-time SMI volunteer and a member of the SMI executive committee since 2017. He is active on the SMI technical committee and helped launch the SMI 201 Compression Spring design class.
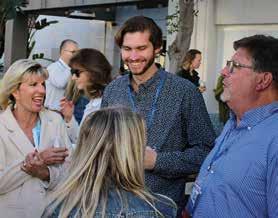
At the closing reception and dinner, Huber passed a handcrafted gavel to Jacobson, symbolizing the transition of leadership. Jacobson sincerely thanked Huber and his wife, Sherrie, for their service and presented them with flowers, a personal gift and a birthday cake to celebrate Huber’s birthday. In addition, a charitable donation was made to the local chapter of LifeWise in honor of the Hubers.
In his inaugural speech, Jacobson outlined his vision for SMI, encouraging members to focus on volunteerism, collaboration and education.
“Volunteerism and cooperation are at the core of our organization,” Jacobson said. “As an organization, springmakers and associates, I’m asking you to embrace volunteerism and cooperation as its core. It’s the embodiment of selflessness and compassion.”
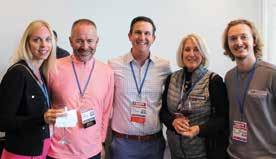
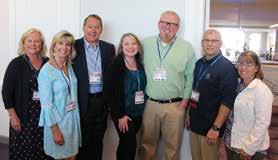
Above and right: Members enjoy an al fresco opening reception on an outdoor patio at the Loews Coronado Bay Resort.
“Green Dot” newcomers pose with former SMI presidents and spouses.
First-time annual meeting attendees mingle with veteran attendees at the newcomers reception.
“It’s the act of giving one’s time, talent or treasure without expecting anything in return,” he continued. “It’s about reaching out a helping hand to those in need, lifting them up, standing beside them in solidarity. Volunteerism is about fostering a sense of community and cooperation. It is the art of working together toward a common goal.”
“We can learn from each other. Our Avant-Garde group (now Emerging Leaders) met this week and had some great conversations,” Jacobson said. (see Emerging Leaders p. 38) “One of the topics that was shared with me was to lean into change, empower yourself and others to make mistakes and learn. Growth doesn’t come from staying in your comfort zone.”
“What’s important to me is education,” he said at a separate time. “It’s getting the next generation involved, and it’s also about keeping your employees engaged. Education is a top goal that I will focus on during my time as SMI president.”
Educating and Encouraging
Informative and inspiring speakers and networking were focal points of the 2024 meeting. The following speakers engaged members on Monday and Tuesday mornings.
Service as An Attitude
Bianca Lager, keynote speaker and virtual trainer, Fundamentals at Work, discussed servant leadership that can foster trust, collaboration and community within organizations.
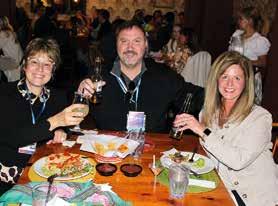

“Leadership is a choice,” said Lager. “Of course, it doesn’t matter what your job title is. I mean it does to some degree, but you are a leader if you choose to be.”
She highlighted the pillars of servant leadership should include listening, empathy, awareness and innovation. Lager stressed building a community among employees, customers and partners.
While acknowledging challenges in implementing servant leadership, she emphasized its adaptability and positive impact on job satisfaction, performance, customer service and employee retention.
Lager shared personal anecdotes and provided tangible tips for fostering a servant leadership culture, such as rewarding contributions to others, normalizing asking for help, allowing space for mistakes and sacrificing comfort for honest feedback.
Overall, reflecting on her father’s legacy and her own journey, Lager underscored the importance of leading collaboratively and empathetically.
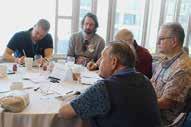
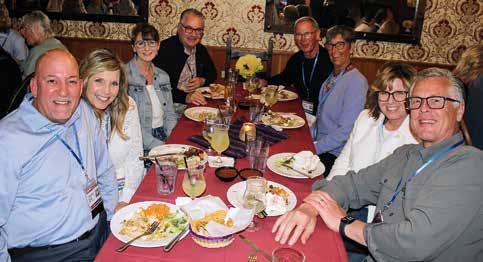
Breakfast and committee meetings were well attended including the safety committee (above) and the associates committee (right).
SMI members enjoyed a reception and dinner at the Barra Barra Saloon in the Fiesta de Reyes area of San Diego’s historic Old Town.
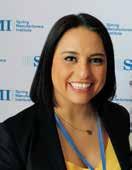

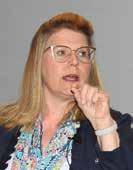
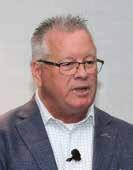
Seeing The Invisible and Doing the Impossible
Inspirational speaker Eric LeMarque shared a message of perseverance, survival and redemption. He emphasized the importance of resilience and determination in the face of adversity.
A former NHL hockey player and avid snowboarder, he recounted his harrowing ordeal of being stranded in the snowy wilderness of a mountainside for eight days, battling freezing temperatures, hunger and the constant threat of death.
“That’s strength under control,” LeMarque said. “It’s like taking a horse and breaking it. It’s still
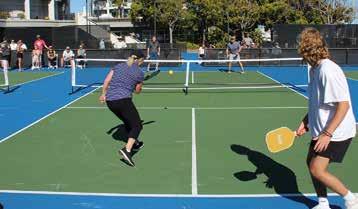

the same horse, but now it has power under control, strength under control.”
Despite facing overwhelming odds, he refused to give up, relying on his survival instincts and sheer willpower to endure until a National Guard helicopter rescued him.
LeMarque lost both his legs to frostbite.
He reflected on his past struggles with meth addiction acknowledging his mistakes and lessons learned. As his story unfolded, he encouraged SMI members to overcome their own challenges.
LeMarque’s story inspired the 2017 movie “Six Below” starring Josh Hartnett as LeMarque (available streaming).
OSHA Safety Update
SMI regulatory compliance consultant Laura Helmrich-Rhodes covered recent changes in OSHA regulations, emphasizing the importance of electronic record-keeping, timely reporting of severe injuries and adherence to safety protocols.
Rhodes reviewed current OSHA statistics on workplace injuries and stressed the need for proactive safety measures, particularly regarding lockout/tagout procedures and heat-related
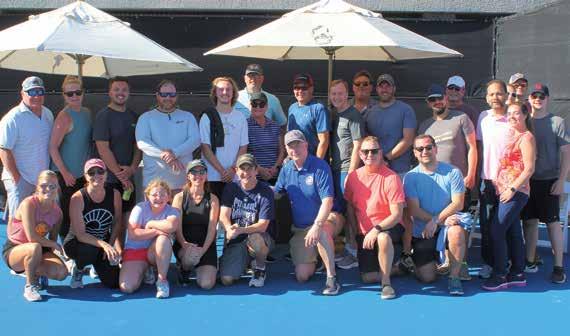
Bianca Lager Eric LeMarque
Laura Rhodes Bill Coughlin
Pickleball Tournament (clockwise from top): Final match, participant and spectator group photo and spectators smiling on sidelines.
illnesses. She discussed the significance of rapid response investigations and a safety committee’s role in promoting a safety culture.
She highlighted upcoming regulatory changes including OSHA’s unified agenda and national emphasis programs. Rhodes also addressed legal considerations, urging companies to retain knowledgeable legal counsel for OSHA compliance issues.
“So if OSHA shows up, call me,” Rhodes said. “But you need to connect with me before they show up. … [As an SMI member] you have free access to me.”
Her overall message was to stay informed, maintain robust safety protocols and know your rights during OSHA inspections.
Leadership and Culture Development Partnership
Bill Coughlin, a member of the executive team at Lippert Components Inc. shared his company’s journey to foster a healthy, productive corporate culture.
Prior to joining Lippert’s executive team more than 10 years ago, the company’s turnover rate was 131%. It now hovers around 20%.
“Think about that, all of these people would come in this door and go back out that door,” said Coughlin. “And on my first day there, I almost did the same thing. That’s how bad it was.”
He advocated for a clear mission statement and core values to guide organizational behavior and decision-making. Underlying this, his team has found that a positive attitude is foundational to personal and organizational success.
He emphasized that helping team members navigate the “Five Storms of Life” (money, marriage, job, family and health) impacts morale and performance.
Coughlin challenged attendees to build a positive corporate culture regardless of position or company size. Everyone has the potential to make an impact through positive influence.
Learn more about Lippert Leadership Academy at: www.corporate.lippert.com
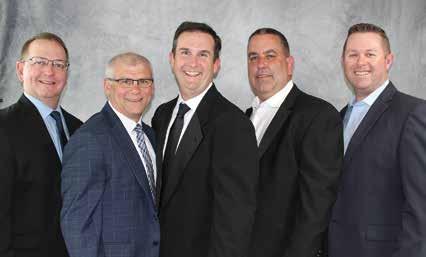
Springmakers In a Pickle
Pickleball was a fun diversion and team-building activity on the final afternoon of this year’s annual meeting. A full roster of 32 players participated in the second-ever SMI Pickleball Tournament. On the sidelines, dozens of spectators rooted for their favorites.
This year’s winners were Steve Kempf, Lee Spring and Ryan Cei, Radcliff Wire.
Thanks to SMI Meeting Sponsors
Throughout the meeting, Jacobson expressed appreciate to all the sponsors who supported SMI’s annual meeting, saying, “We want to thank each sponsor for their support.”
The 2024 supporters were Platinum sponsors Gibbs Interwire and Industrial Steel & Wire; Gold sponsors FENN/Torin and WAFIOS; and Silver sponsors Core Financial Partners and Global Specialty Steel. z
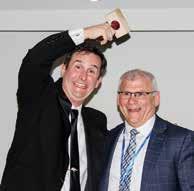

Join Us Next Year!
Mark your calendar for the 2025 SMI Annual Meeting to be held at the Kimpton Hotel Fontenot, New Orleans, March 29–April 1, 2025.
The 2024-26 SMI executive committee (l to r): Dave Deerwester, Gene Huber Jr., Don Jacobson III, David DeVoe and Joe Devany.
SMI Annual Meeting closing dinner: incoming president, Don Jacobson III (l) clowns around with a handcrafted gavel presented to him by outgoing president, Gene Huber Jr (r). Executive Director, Gary McCoy, speaks to attendees.
By Gaby Carrasco
SUCCESSFUL INAUGURAL Emerging Leaders Conference

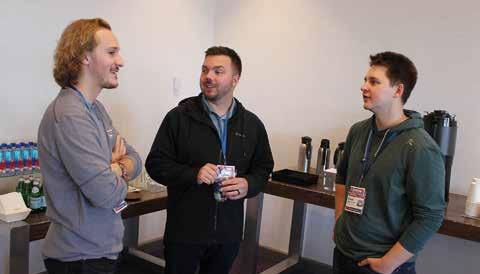
This year’s overwhelming success will keep the momentum going.
The 2024 SMI Annual Meeting introduced the inaugural “Avant-Garde Leadership Conference” on April 6–7, 2024, in Coronado, California. The conference, hosted by the SMI Emerging Leaders group and spearheaded by SMI members Alex Melnikow of Midstate Spring and Adam Jacobson of FENN/ Torin, was attended by 13 SMI members. Emerging Leaders, formerly Avant-Garde, is a group of SMI members bringing innovative and experimental ideas to shape the future of SMI and the springmaking industry.
Attendees mingle during a 10-minute recess. Pictured (l-to-r): RJ Froehlich (Ace Wire), Cullen Olson (IDC Spring) and Caleb Deerwester (The Yost Superior Co.).
2024 Emerging Leaders Conference attendees.
Designed to focus on industry-specific content and opportunities for peer connection, the “conference within a conference” was a strategic move to minimize cost and time away from work. It was tailored to the needs of critical non-owner employees, as well as emerging, future and next-generation leaders within the spring industry, equipping them with practical knowledge and connections.
“We were able to provide roughly six additional hours of content and activities,” said Jacobson. “Our main focus was getting to know one another in a constructive way that allowed us to be more comfortable not only in our own companies but also in the spring community as a whole. There is always room for improvement, but this year’s overwhelming success will keep the momentum going for New Orleans and beyond.”
Day one included a teambuilding exercise, followed by a roundtable discussion where participants shared tips they believed would be helpful to their peers. It also included a presentation by SMI’s regulatory compliance consultant, Dr. Laura HelmrichRhodes, who gave a brief overview of safety resources available to SMI members and a presentation on “What Do You Do When OSHA Shows Up at Your Door.”
Day two included a presentation on SMI technical services by the association’s Technical Director, C. Richard “Rick” Gordon. There was also a panel discussion on business succession planning with Don Jacobson III, incoming SMI president and vice president of business development at Newcomb Spring; Alex Melnikow, President and CFO at Midstate Spring, Inc., and David DeVoe, SMI board member and president/ CEO of Plymouth Spring.
The conference concluded with much positive feedback.
“Unsurprisingly, this group is filled with great people who showed up ready to participate,” Melnikow said. “Many were strangers
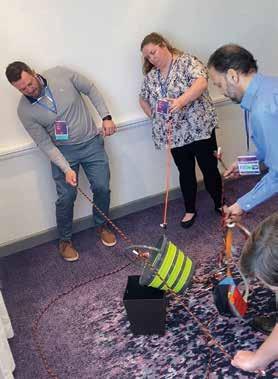
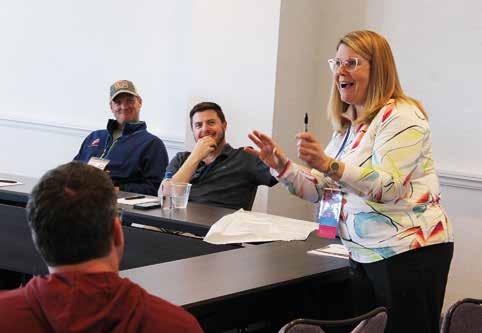
to me at the start of the conference, but by the end, we walked away with a deep understanding of each other’s businesses and, most importantly, our values. I look forward to future interactions with this group!”
The next “Emerging Leadership Conference” will be held at the 2025 SMI Annual Meeting in New Orleans, Mar. 29–Apr. 1, 2025. Details to come at: www.smihq.org z
Attendees participated in a team-building activity led by Katherine Dalton of Gardner Spring.
Laura Helmrich-Rhodes discusses “What Do You Do When OSHA Shows Up at Your Door?”
By Gaby Carrasco
Eleven Students Receive $25,000
Receiving this scholarship is truly a financial blessing to my family and me. Beyond finances, your generosity will go towards supporting my passion for teaching…
Ellie Kiscellus Granger, Indiana
I appreciate the recognition and I am glad that there is an institution willing to help students in some way related to the spring industry.
Joshua McManus Grand Haven, Michigan
This scholarship will immensely help my family and I afford the cost of my bachelor’s degree at a time when my parents are working to pay for two children in college. When I graduate in the spring of next year, I will be the first in my family to earn a college degree.
Nicholas J. Yax Logansport, Indiana
One of many SMI membership benefits is access to the association’s scholarship program. Each year, all SMI member companies’ employees and their dependents are encouraged to apply for the many available scholarships. This year, $25,000 in financial aid was distributed to 11 students throughout the U.S. This marks the first year that the Lynne Carr Scholarship was awarded in honor of former SMI executive director and honorary member, Lynne Carr.
“At SMI, we believe in the transformative power of education,” said SMI president, Don Jacobson III. “Our scholarship program encompasses this belief, providing deserving students with the financial support they need to pursue their academic and career aspirations. By investing in their futures, we not only empower individuals but also strengthen our community and industry as a whole.”
Since the SMI scholarship fund started in 2011, 178 students have received a total of $382,500 in financial assistance.
To be eligible for an SMI scholarship, award winners must be full-time employees or the dependent child of a full-time employee who works for an SMI member company.
In 2024, SMI awarded five regional scholarships for $2,000 each. In addition, six at-large scholarships were selected: Ronald and Adrienne Banas Scholarship • $5,000
International Spring Scholarship • $4,000 awarded to two students for $2,000 each
Callaghan-Hart Scholarship • $2,000
The Gibraltar Company Scholarship • $2,000
Lynne Carr Scholarship • $2,000
The SMI scholarship program is administered by Scholarship America, the nation’s largest designer and manager of scholarship, tuition assistance and other educational support programs for corporations, foundations, associations and individuals. Awards are granted without regard to race, color, creed, religion, sexual orientation, gender, disability or national origin.
SMI member companies will receive information for the 2025 scholarship program in the fall via email and on SMI’s website, www.smihq.org. z
I am honored and humbled to have received this award. The money will go towards my education at Dordt University.
Tara Schmitz
Cedar Grove, Wisconsin
Through SMI Scholarship Program
2024 Regional Scholarships
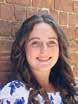
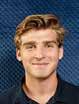

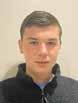
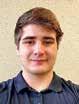
Kara Baker
Hometown: Grafton, Wisconsin
SMI Member Parent: Ryan Baker, Matthew Warren Spring
Attending: Purdue University
Major: Animal Science/Pre-Vet
Joshua McManus
Hometown: Grand Haven, Michigan
SMI Member Parent: John McManus, Motion Dynamics Corporation
Attending: Rose Hulman
Institute of Technology
Major: Mechanical Engineering
Kyla O’Guin
Hometown: Centerville, Tennessee
SMI Member Parent: Jason O’Guin, Sumiden Wire Products Corporation
Attending: University of North Alabama
Major: Biology
Dominick Seymour
Hometown: Wilbraham, Massachusetts
SMI Member Parent: Jeremy Seymour, Jonspring Company, Inc.
Attending: Rochester Institute of Technology
Major: Chemical Engineering
Logan Woodard
Hometown: Waukesha, Wisconsin
SMI Member Parent: Logan Woodard, WCS Industries
Attending: University of Wisconsin –Milwaukee
Major: Mechanical Engineering
This award will help me in my pursuits, as well as give me the ability to enrich my educational pursuits through devotion to service and extracurricular activities.
Kyla O’Guin
Centerville, Tennessee
2024 At-Large Scholarships
Goldberg Family Foundation Scholarship
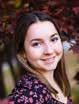
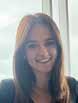
Sara Deerwester
Hometown: Springfield, Ohio
SMI Member Parent: David and Sharon Deerwester, The Yost Superior Co.
Attending: The Ohio State University: Columbus Campus
Major: Mechanical Engineering
Haley Densow
Hometown: West Bend, Wisconsin
SMI Member Parent: Scott Densow, Exacto Spring
Attending: University of Wisconsin –Stevens Point
Major: Marketing
Callaghan-Hart Scholarship
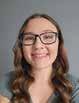
Ellie Kiscellus
Hometown: Granger, Indiana
SMI Member Parent: Paul Kiscellus, Hoosier Spring
Attending: Bethel University
Major: Elementary Education
Lynne Carr Scholarship
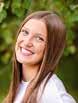
Tara Schmitz
Hometown: Cedar Grove, Wisconsin
SMI Member Parent: James Schmitz, Exacto Spring Corporation
Attending: Dordt University
Major: Elementary Education
Gibraltar Corp. Scholarship
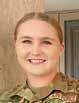
Lora Wargo
Hometown: Carrollton, Texas
SMI Member Parent: Jason Wargo, Newcomb Spring
Attending: Trinity University
Major: Computer Science
Ronald and Adrienne Banas Scholarship
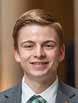
Nicholas Yax
Hometown: Logansport, Indiana
SMI Member Parent: Ryan Yax, Myers Spring
Attending: Purdue University
Major: General Management
I was very excited when I read the email and had to call my parents immediately to tell them! It means so much to me to have SMI’s support for my college education.
Growing up around Yost and going to SMI meetings are what led me to decide to major in mechanical engineering and minor in business.
Sara Deerwester Springfield, Ohio

Flashback
The Interrelationship of the Automobile and Spring Industries
Editor’s Note:
In this condensed article from The Mainspring published in Oct. 1954, we follow the parallel history of automakers and springmakers. It’s a fun lookback. As an aside, electric vehicles have intrigued us from inventions in the 1870s to predictions in the 1950s to our roads in the 2020s.
Little did Dr. J.W. Carnhart know when he mounted a steam boiler to a wagon in 1871, that the automobile would create great prosperity and impact U.S. springmaking. In 1877, Selden built an internal combustion engine car. Others built various steam, gasoline and electrically propelled vehicles. In 1892, Duryea made the first marketable car in Springfield, Massachusetts. King manufactured the first car in Detroit in 1896. Olds followed in 1897, and the automotive market grew. From 1890 until 1954, about 2,200 different makes of automobiles were produced in the U.S.
When Ford built his Model T in 1908, small springmakers were scattered nationwide. Many springmakers had secret methods and inconsistent results. Motorists had to be mechanics as well as drivers. In a hundred miles of driving, replacing a few valve springs was common. Cars came with tool kits with extra valve springs, bearings, breaker points and more. Engines were built so repairs could be made on the roadside. Springmakers were challenged to make more springs for more cars. Gasoline motors with numerous springs became popular. By 1909, steam cars were nearly extinct.
During World War I, spring manufacturers struggled to produce automotive parts in volume. Most springs were made of harddrawn wire or annealed material that was hardened and tempered after forming. But automobile production grew, and the demand for better parts performance grew with it. This meant spring failure studies to correct issues.
Between 1920 and 1930, car builders added safety features, including four-wheel brakes by Rickenbacker Motor Company. During
this time, the spring industry set its house in order. Engineering and research developed answers.
Top speeds reached about the same as cars today. But faster engines made springs do funny things. Vibrations made them destroy themselves. Springs were redesigned to suppress vibrations. The spring industry developed better materials, like Swedish steel, with fewer surface imperfections. Manufacturing began with continuous tempering of wire before coiling springs. The 25,000-mile car became commonplace. By the 1930s, automobiles reached 80 HP and added tempered glass.
By the 1940s, the spring industry added shot-peening (initiated by the Associated Spring Corporation in 1929). This increased the power and life of springs by as much as 40%. With few or no repairs, the expected car life reached 50,000 miles.
Car production grew each year. Spring plants multiplied and expanded to meet demand for the about 147 different springs … in the average car. Springmaking became a science, and information was freely shared. Broken springs became uncommon.
As the U.S. entered World War II, the auto industry made munitions and vehicles. Just in time, the U.S. spring industry and steel companies developed American-made spring materials, as Swedish imports were shut off. Demand grew for springs in tanks, planes and guns under terrifically high loads and often under intense heat. Many new spring alloys with special uses were born of the war effort.
Meanwhile, wire drawing experts developed new methods. Using tungsten carbide dies and cooling them, the wire produced
had a much better surface. Its performance could be accurately predicted, and it was consistently uniform. This impacted both the spring and automotive industries.
Automobiles again increased horsepower. Engines were made more prominent, and the performance demands on springs were increased. Spring manufacturers produced more energy in less space. As engine power increased, the accident rate decreased. Twenty years ago, one person was killed for every 6.4 million vehicle miles in the U.S. In 1954, with around twice the horsepower, it is now 13.2 million miles per death. We are twice as safe with nearly twice as many cars on the road. Also, as power increased, so did the life of the engine. The 100,000-mile vehicle had arrived.
What does the future hold for automakers and springmakers? What is the automobile of the future? Based on airplanes, we can visualize piston engines being replaced with a different power plant. Perhaps a gas turbine? What about atomic power? If the submarine Nautilus can be driven atomically, the car of the future certainly can. What about a steam or perhaps an electric motor? Future safety features might prevent passengers from being thrown from a car or cut by flying glass in an accident.
Can springmakers create springs three or four times the strength of today’s steel? Plotting music wire on a strength curve shows strength increases as wire size decreases. If we mathematically project this curve to a wire diameter of one iron molecule, we get a tensile strength of 30 million pounds per square inch, or about 100 times what we now have. Springmakers have room to grow in the automotive industry! z
Originally published in The Mainspring, October 1954 and is used by permission from Associated Spring US, LLC.
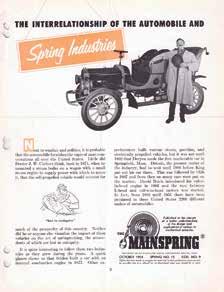
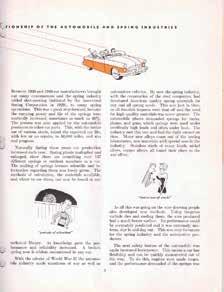

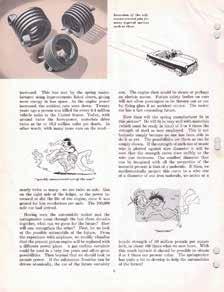
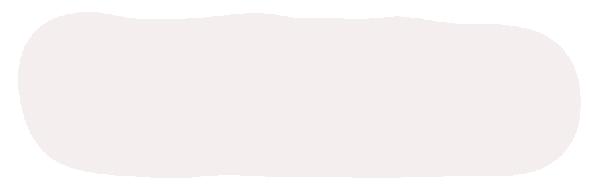
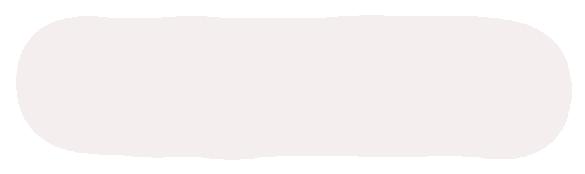

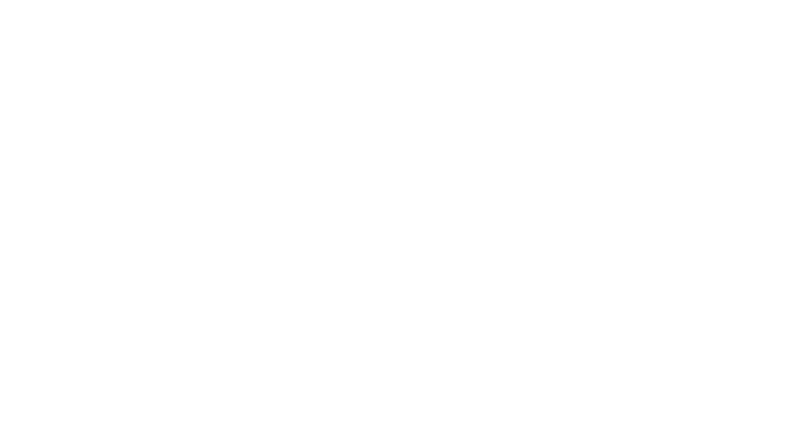
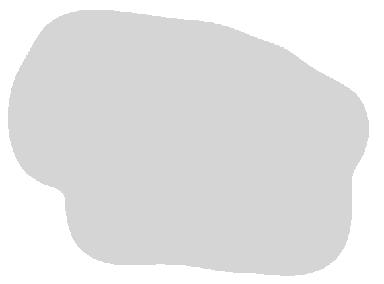
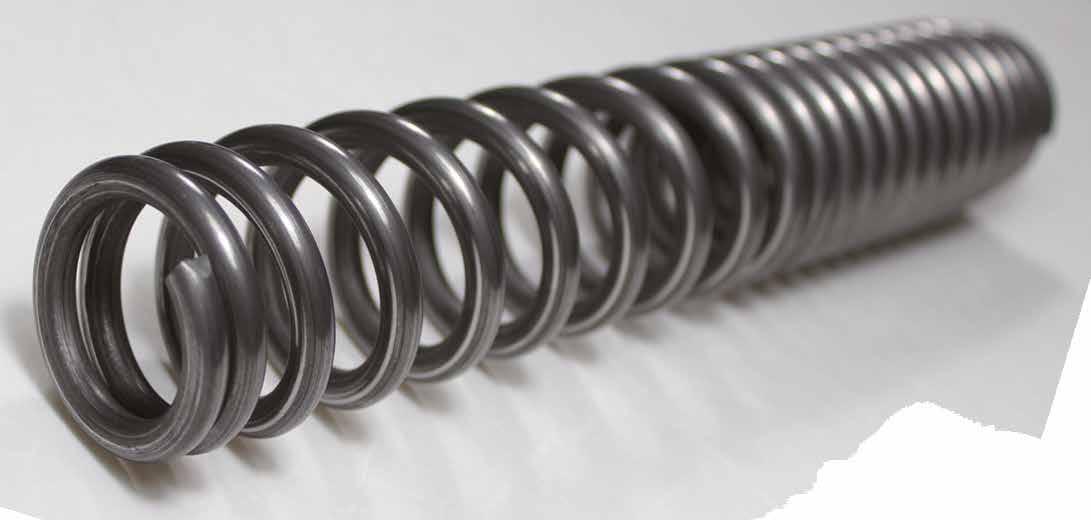
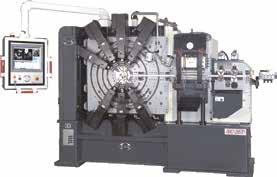

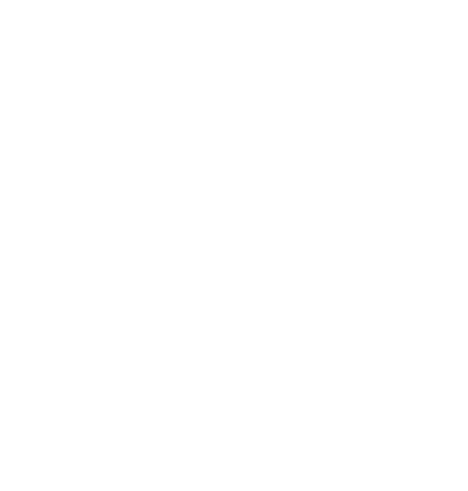
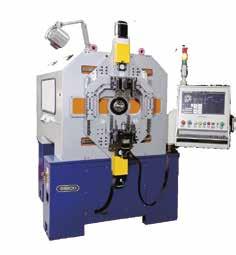
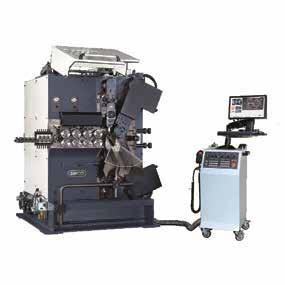


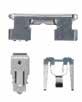
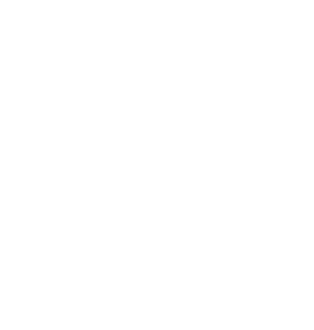
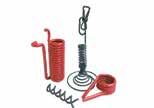

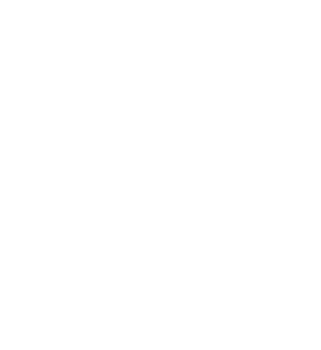
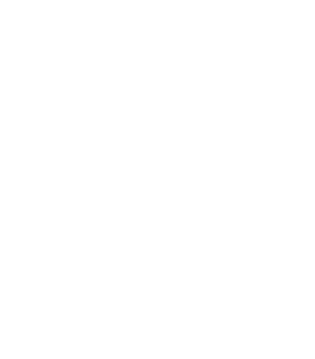
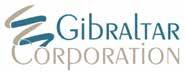
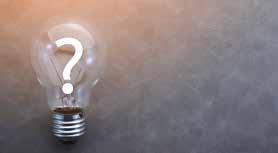
Five Questions
Five Questions allows SMI associate members to tell the spring industry about their products and services. In this edition, we talk with David Janowski from
A&D Trading
1
Tell us your company history and products you offer spring manufacturers.
A&D Trading LLC was founded by David and Amanda Janowski in 2003 to fill an industry need. A&D represents some of the finest spring coiling and grinding, wire bending and forming equipment from Taiwan, Japan, Italy and China. We offer cost-effective, quality-oriented machinery that will perform for years to come with service to match.
2 What trends are impacting your industry, and how do they affect springmakers?
One trend that directly affects us is the value of the U.S. dollar. Since most of our products are imported, we see the dollar not going as far as it did in the past. This ultimately means that the products cost more as we experience inflation. Another trend is rising interest rates and the potential phase out of IRS section 179 in the tax code. It’s harder to sell a $100,000.00 machine when it costs 9% to finance, and you can’t fully depreciate the asset the year it was purchased.
3 What products and services do you offer springmakers?
We offer CNC compression coiling machinery from KHM and SHA featuring 2-axis to 10-axis equipment with a full range from .1mm (.004) to 25mm (.985) and CNC grinding machinery from SHA to match the coiling side.
We provide wireforming / versatile springforming equipment from CSM and Plus Machinery from 3-axis to 16-axis capability, and wire ranges from .25mm (.010) to 8mm (.314).
We carry CNC multi-slide hard-tooled machinery from TCIM. This is a modern,
more versatile version of a fourslide or vertislide machine with CNC programming and easily replaceable individual tools.
4 What role does logistics play in serving spring manufacturers?
Logistics has proven to be a challenge, especially in recent years. We have noticed rapidly increasing shipping rates, including fuel surcharges, both on the sea and ground. Port congestion always seems to be an issue along with random Homeland Security inspections, but overall, our clientele is understanding and knows what they receive is well worth the wait.
5 Can you tell us about a recent challenge you solved for a customer?
Recently, we had a customer who was making an unusually shaped, close-wound spring from a very small initial diameter to a much larger final diameter. The client set up the machine using a double-cut feature, so they had no “hook in” on the large diameter. The client said it worked well, but the “trims” tended to fly off randomly. This risked potentially jamming a slide or hitting an employee and causing injury.
Because the client had a SHA 10-axis machine with a fully programmable arbor and home position, we made the spring as a “mirror image” itself on one cycle, meaning we coiled one “forward,” moved the arbor “up,” and cut, then coiled one “backward,” moved the arbor “down” and cut. This fully eliminated the “trim” and made two springs per cycle. The overall output rate was increased over the original set-up, and there was substantially less “mess.”
The result was a very satisfied customer! z

David Janowski
A&D Trading LLC PO Box 60
3435 South Main Street Rock Creek Ohio 44084 Phone: 440-563-5227
djanowski@adtradingllc.com www.adtradingllc.com
Follow SMI on social media for bonus content on David Janowski and A&D Trading, LLC.
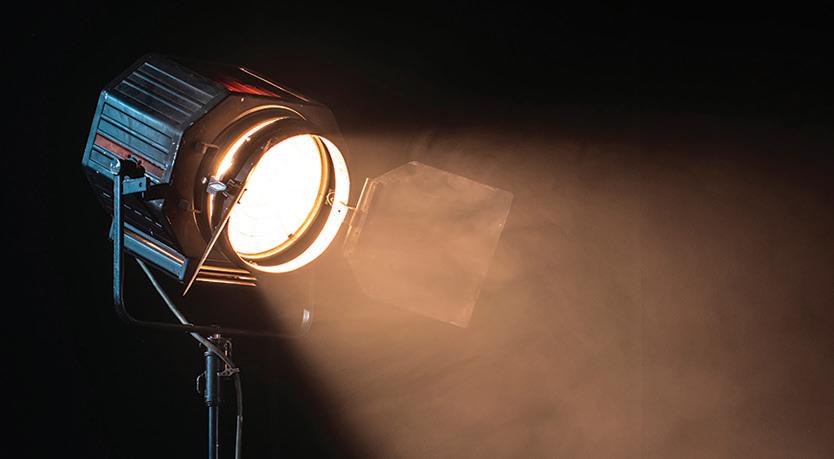
By Gary McCoy, Executive Director
Good Bones
Springmaker Spotlight
A Profile of Alex Altstatt and Western Spring Manufacturing
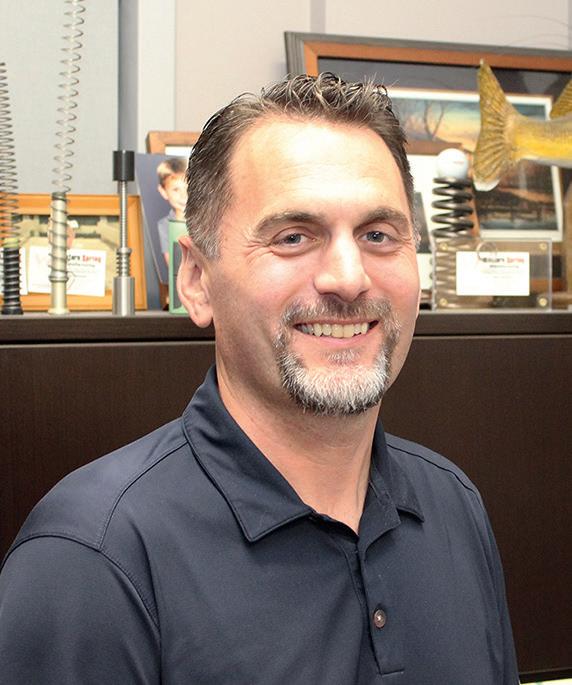
For Western Spring Manufacturing, it all started at 443 Wall Street, a 6,000 square-foot building in St. Paul, Minnesota, nearly 100 years ago.
As described on the Western Spring website, the company was “established in 1909 as the Robert Goss Company, the business served as a blacksmith and machine shop. Charles Altstatt was employed as a foreman and, in 1932, became the owner. He pioneered the legacy of Altstatt family ownership with his strong German work ethic. Requests for coil springs and his insightful craftsmanship to produce them led to the specialty that nurtured the current Western Spring Manufacturing.”
It is important to note that in the 1940s and 50s, Western Spring used coal boilers for heat to bend wire on lathes driven by overhead line shafts.
Alex Altstatt, a fourth-generation company owner, explained that the St. Paul building is well over a hundred years old with exposed timbers and brick. “It was built very well and has good bones to it. I could see it someday becoming a brewery or something, but for now, it continues to be a company asset.”
The original St. Paul building plays an important role in Western Spring’s legacy.
As times changed and to accommodate growth, the company relocated in 2005 to a 16,000 square-foot building in a suburban industrial park in Hugo, a city 18 miles north of downtown St. Paul.
Like many spring companies, they outgrew the original Hugo facility and, in 2017, erected a new, purposely designed 40,000 squarefoot structure located next door.
“It has all the modern features such as well-lit LED lights, occupancy sensors, automated access control doors, air conditioning/ heating and security cameras throughout,” explained Altstatt. The company owns an additional 5 acres of land should it ever need or desire to expand.
The company’s “good bones” goes back to second-generation leaders Ray Altstatt and his son, Joe, Alex’s dad, who took over leading the company in 1980. Joe was the leader who transitioned the company to focus exclusively on springmaking. While still an owner of the company, Joe is no longer involved in the day-to-day operations.
Alex Altstatt graduated with a degree in manufacturing management from Bemidji State University in 2005. After a short internship with an automation distributor, he came to work full-time at Western Spring later that year. He serves as the company’s business development and project manager and is a self-described “visionary” who is not afraid
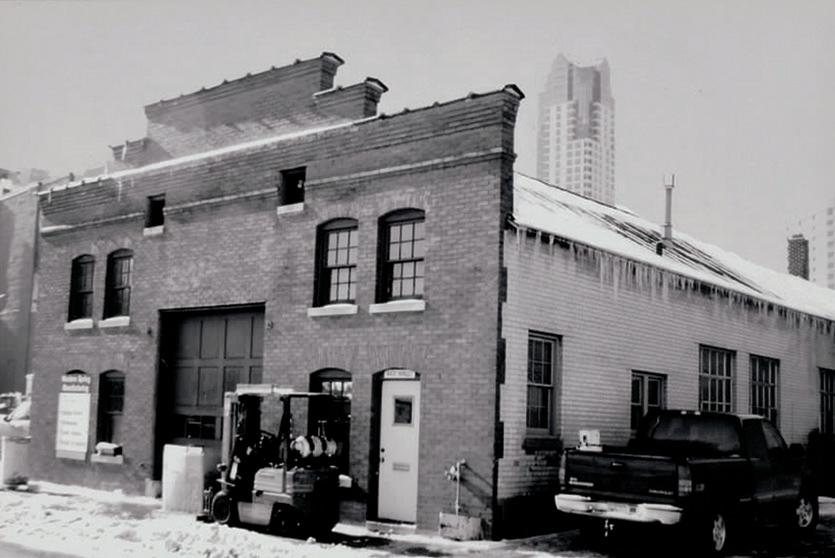
Alex Altstatt
The original location for Western Spring at 443 Wall Street in St. Paul, Minnesota.
to try new things. He’s involved in ownership with his dad and is working toward becoming a majority owner.
Alex’s brother, Ben, is also a part of the fourth generation and has been with the company since 2000. He is the company’s production manager and spends most of his time on the shop floor.
Alex and Ben have a sister, Adrienne, who does not work in the business. But like every child of a spring manufacturer, she once did a stint working at the company.
Growth and Diversification
It’s interesting to note that when Charles Altstatt started Western Spring, he had a couple of workers to help him. When the company moved to Hugo in 2005, its employee population was four. Now, the company employs 25 workers.
Like every spring company, they are always looking to hire the “right people.” At the time of my visit in May, they were looking to hire a quality manager.
With its roots in working with large wire, the company has transitioned and added fine wire to its repertoire, enabling it to work in industries like medical. “We go down to .003 and all the way up to a diameter of .625. So, I often joke that the big wire is small money, so there’s a lot of risk,” said Altstatt.
“There are few springmakers that have the range that we do,” said Altstatt, “which allows us to be a one-stop shop for our customers.”
Altstatt points out that their largest customers float around 10% of their business.
“Like a good investment manager will tell you, ‘diversification’ is the key,” explained Altstatt. “If somebody takes a hike as a customer, we can say it was, ‘Nice working with you,’ and it doesn’t adversely affect our business.”
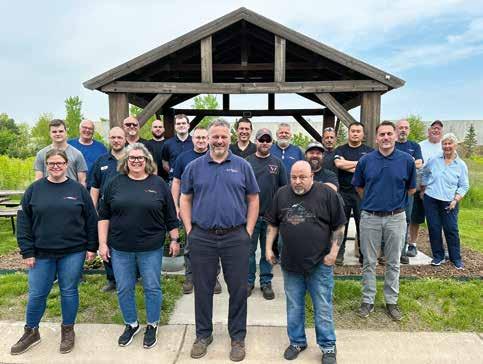
In addition to medical, Western Spring’s diverse customer base includes many industries, including aerospace, agriculture, automotive, defense, industrial, maintenance and repair, along with short-run prototyping. Their portfolio of products includes compression, extension, torsion and flat springs, along with wireforms.
A self-described lover of automation, Altstatt believes it is the key to success in U.S. manufacturing. “Without it (automation), we wouldn’t be the same. We’ve got a couple of collaborative robots (cobots), vision systems, bowl feeders, grippers and other systems to help us. Automation is part of the answer to the workforce crisis.”
There are few springmakers that have the range that we do, which allows us to be a one-stop shop for our customers.
A recent team photo of Western Spring employees at an employee appreciation food truck event.
At the time of my visit, Western Spring leaders, especially Matt Haberman, engineering manager and Zach Hawley, technical sales manager, were working to implement a new enterprise resource planning (ERP) system. Altstatt says they’ve faced adversity in getting the ERP system up and running. He’s excited about the capabilities of the new software system to help Western Spring’s business, especially the promise of supporting the company’s automation within the ERP system and to better plan its production schedule and raw material needs.
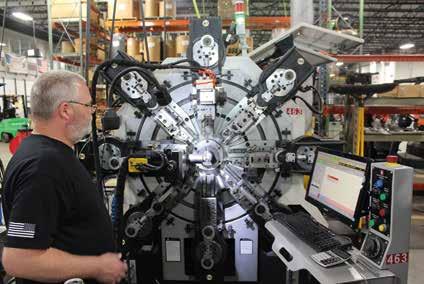
Shop Floor Training
Alex Altstatt has a unique “side hustle” that is a separate LLC from Western Spring. It is something he has been able to do with the blessing of his father, Joe.
In this role, he helps train operators of import machinery for a particular brand from China. He’s trained people in the U.S., Canada, Mexico and even once in Japan.
“When I went to Japan, they started the day reading an excerpt out of the quality manual and would clean their calipers at the same time,” said Altstatt. “And all our shoes were off. It was fun.”
Getting inside the walls of more than 20 or so different spring companies, Altstatt says he’s met some very talented individuals in the spring manufacturing industry.
“I’m not just talking about the frontend C-suite people,” explained Altstatt. He’s most comfortable when he can roll up his sleeves and get down in the “trenches” on the shop floor. His LLC does not sell equipment.
I had the privilege of walking the floor at Western Spring with Altstatt, where I saw a great mixture of machinery from the U.S., Germany, Austria, Taiwan, China and Japan.
Altstatt says the company’s machinery is all over the map. “It’s all about having the right machine that runs each particular part in the most efficient and effective way.”
A Gemba Walk
With his degree in manufacturing management, Altstatt is well-steeped in the language of process improvement, including Lean and Six Sigma. Leaders at Toyota developed what they call a “Gemba Walk.” Translated, it means “the real place” and “the place where value is created.”
Altstatt attempts to get out of his office and walk the floor every morning. It’s all about taking the time to watch how a process is done and talking to the workers on the shop floor who are making the company’s springs and wireforms.
He asks questions such as: “How are you doing?” or “What’s this program running?”
The goal is to bridge the gap between what is assumed to be happening and what actually is happening.
When I toured Western Spring, I saw Altstatt’s friendly banter with his employees. He asked several of them, “What have you
In what he calls “Productivity Consulting,” he offers advice if people ask his opinion on things such as, “What’s the best machine for this part?”
Often, he says he will respond with a question, such as, “Do you want to spend a half million dollars or $150,000?” “What is your production rate target?” or “What are your technicians' skillsets?”
Altstatt is always thinking of new ideas and said he could envision leasing out cobots to other spring manufacturers.
“If I see an application when I’m out there in the wild, where they have labor doing this part. I’ve often asked myself, ‘What if I purchased a cobot, set it up on their machine, made it run and charged them per hour or on a lease?’” He said he could remotely monitor the cobot with a camera.
The inspiration for the idea came from reading a trade journal article from the sheet metal industry.
For Altstatt, the wheels are always turning, and he believes, “You’ve always got to be a couple of steps ahead.”
The production floor at Western Spring is always a busy place.
learned from decades working in the spring industry? Is it more art or science?”
Most said it was definitely more of an art form, due to the constant challenges of manufacturing parts that will work for the customer.
Altstatt is all about feedback, whether on the shop floor or elsewhere. “My door is always open,” he said.
Company Outreach
The company launched a new website a few years ago and has become more active on social media. One of its recent LinkedIn postings was published in a trade magazine.
The new website has produced one game changer with customers: the ability to book a virtual consultation with Western Spring subject matter experts (SME).
“Everybody keeps their calendar within Outlook. Customers can go to our website and choose a time that works best for them by looking at the calendar and seeing what’s open,” said Altstatt. “It has eliminated the inefficient back and forth that used to take place with emails.”
Altstatt says with their cameras on, they can share screens with customers. Often, they will pull up SMI’s Advanced Spring Design (ASD) program to assist customers with designs.
“We don’t technically design springs, but we can be a subject matter expert to help the customer,” said Altstatt.
In addition to its social media and web presence, the company is active at a few trade shows each year, but that has diminished over the years.
Being on the smaller side, the company takes advantage of many different outside resources, especially the ones SMI offers in technical consultation and failure analysis.
Away from the Shop
Though Altstatt prides himself on being a professional resource for his customers, he is also a loving husband to his wife, Nicole, and father to Ava, 7 and Oliver, 5.
“My daughter always asks me, ‘What is the secret to making springs?’ I often say, ‘Someday when you’re older, you can learn.’”
With a laugh, Altstatt says Ava thinks there’s a secret, and we both know, ‘The secret is there’s no secret to springmaking.’”
In his leisure time, Altstatt can usually be found in the summer crewing on 7-man scow boats (which he loves for the teamwork involved) or fishing for bass in a league. In
the winter, Alex loves to go out and participate in outdoor activities with friends, such as ice fishing, snowmobiling and playing hockey in a men’s league.
Alex and Nicole live on a hobby farm with chickens and enough land to provide maintenance all year round.
If there is a secret to Western Spring's success, it is most likely revealed in Altstatt’s 2023 Snapshot profile in Springs (https://bit.ly/SPR62-4-p78). When asked about his most outstanding qualities, he said, “Persistence. Us Altstatt’s keep showing up to work. That is likely a key to our success.”
It all goes back to good bones. z

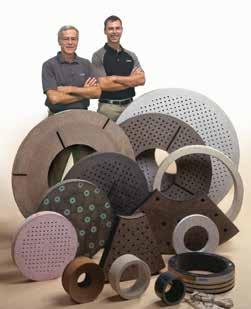
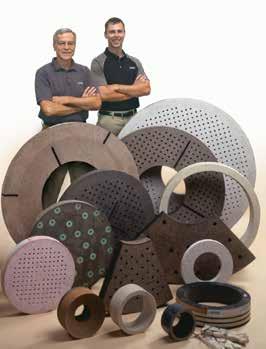
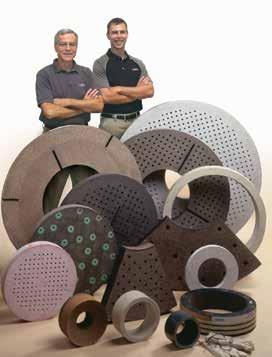
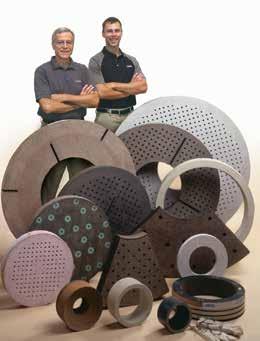
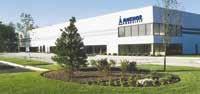
At Anchor Abrasives we specialize in the design and manufacture of resin, epoxy and oxychloride bonded nut inserted discs and cylinders...plus centerless and rollwheels.
At Anchor Abrasives we specialize in the design and manufacture of resin, epoxy and
At Anchor Abrasives we specialize in the design and manufacture of resin, epoxy and oxychloride bonded nut inserted discs and cylinders...plus centerless and rollwheels. Today, in our modern manufacturing facility, we are ready to continue our tradition of innovative quality products and unmatched customer service. For more information contact Anchor Abrasives Company, 7651 West 185th Street, Tinley Park, IL 60477 U.S.A. Phone: 708-444-4300; Fax: 708-444-1300.
nut
discs and cylinders...plus centerless and rollwheels. Today, in our modern manufacturing facility, we are ready to continue our tradition of innovative quality products and unmatched customer service. For more information contact Anchor Abrasives Company, 7651 West 185th Street, Tinley Park, IL 60477 U.S.A. Phone: 708-444-4300; Fax: 708-444-1300.
Today, in our modern manufacturing facility, we are ready to continue our tradition of innovative quality products and unmatched customer service. For more information contact Anchor Abrasives Company, 7651 West 185th Street, Tinley Park, IL 60477 U.S.A. Phone: 708-444-4300; Fax: 708-444-1300. www.anchorabrasives.com
continuing the tradition at Anchor Abrasives.
Jack and Jeff Shoemaker, second and third generations continuing the tradition at Anchor Abrasives.
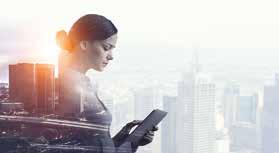
By Sara Scullin
Women in Springs
A New Day, a New Ride
Leeco Spring International’s Tamara Couey Reminds Us to View the Business with New Eyes, Whether You’ve Been There Three Years or 37.
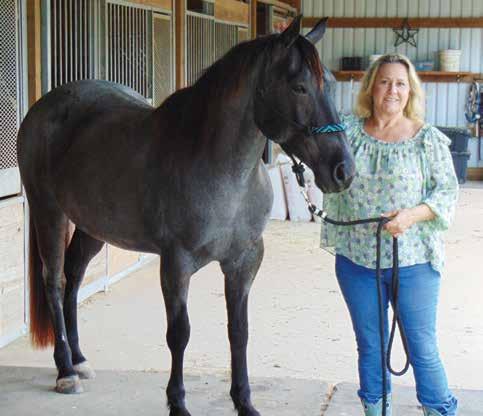
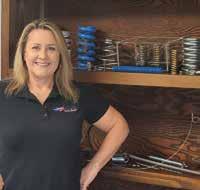
Tamara “Tami” Couey, co-owner of Leeco Spring International, climbs into the saddle each day after her 50-mile drive home from work. Horses are her first love, and springs are maybe a close second.
Couey has been with Houston-based Leeco since 1987. It was run by partners Phil Lee (the founder’s son) and Ed Eckert at that time. The dynamic company remains a family business. Couey runs it with her business partner, James Moody, who manages the shop, and her two sons (Blake and Matt), who work in the office with her.
Leeco is now in its 65th year. Couey’s long career with the business has been a series of stepping stones. She’s always maintained a growth mindset, which has undoubtedly contributed to her success and that of the company.
“At the start of my career, I knew zero about springs. I was just in the market for a new job,” she recalls. “I answered an ad in the local paper and interviewed with the son of the founder. He hired me on the spot.”
It wasn’t long before Couey became adept at order processing and office operations.
“I’d never wound a spring in my life,” she says, “But I’d go out to the shop. I watched and asked questions. I went from processing orders to shipping orders and then later quoting. I’d just say to the boss, ‘I’ll do that, too.’ I wanted them to know I was all about being an asset to the business.”
“I worked my way up. That’s my nature,” Couey says. “Don’t stop me here … I want to learn everything.”
Phil Lee passed away in 2001, and Tami and James bought the business from Eckert in 2011. Today, Leeco’s small, strategic team delivers compression, extension and custom springs to its customers.
Tami with her granddaughter’s barrel-racing mare, Sage.
Tami Couey
They specialize in applications for the food and beverage industry, medical, agriculture, electronics, oil and gas … even go-carts.
Sometimes the right springs for an application start as an idea.
“We have customers who walk in the door and want to invent a product that then comes to fruition,” says Couey. “We manufacture springs for those clients.”
Along with diving into new industries and novel ideas, comes knowing when to let go in the interest of moving forward.
Until recently, Couey says they worked alongside NASA and the aerospace community but ultimately excused themselves from that business due to the red tape involved.
Couey’s no stranger to change. She was there at the dawn of the Internet. She helped to migrate inventory and information onto computers. After acquiring the company, she and James continued upgrading old software and dot matrix printers.
Timely technology and machining updates have kept this nimble outfit operating at peak performance. Leeco is 11 people strong: three work in the office and eight in the shop.
Couey aims to keep the business small and efficient.
“A little growth is great,” she says. “But here in the city, we can’t grow our plant more.”
What they have done is enhanced the manufacturing area and the machinery.
“We’ve improved the value of what we can offer customers, too.” she says, adding, “We have a fabulous on-time record.”
Couey says the trade is a bit like blacksmithing in how specialized it is. Leeco’s shop crew are all cross-trained.
On the design side, her main engineer, son Matt, enjoys designing a spring (or a better

spring) for customers using SMI’s ASD7 software. Her son Blake takes care of shipping, receiving and inventory.
Finally, Couey notes it’s important to “mind the marketing.” The team’s marketing consultant reports on website performance and email blasts, and Leeco’s doors are always open to customers who pop in with questions or to find catalog items stocked in-house. (The comprehensive online catalog features 8,500 stock springs.)
Off the clock, Couey cares for her three horses and has started taking barrel racing lessons.
“Retirement’s not real close,” she laughs. “At 60, I realize how short life is, and that I’ve got a lot of things on my bucket list to cram in.”
If you haven’t caught on yet, when this career springmaker says, “don’t stop me here,” she means it. z
At the start of my career, I knew zero about springs. … I watched and asked questions. … I wanted them to know I was all about being an asset to the business.
Each Leeco employee brings unique talents and experience to the table. Pictured (l-to-r): Tami’s sons Blake and Matt, Tami, her partner James Moody, and his brother, John.
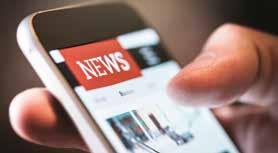
By Phil Sasso
CTE News Sparking Interest in Springmaking
For many teenagers, the path to a future career seems distant and daunting. However, MiCareerQuest in Grand Rapids, Michigan, introduces young students to exciting career opportunities, piquing their interest at a young age.
“We all know the changing demographics in our country are not in our favor as employers,” says Jay Dunwell, president of Wolverine Coil Spring Co., an SMI member company, who has been involved with the program since its inception in 2015. “We’re looking to get students excited about manufacturing careers, and the sooner, the better.”
SMI Members Lead the Way Central to MiCareerQuest’s success is its partnerships with regional businesses and organizations. Dunwell highlights Wolverine’s collaboration with SMI member
We’re looking to get students excited about manufacturing careers, and the sooner, the better.
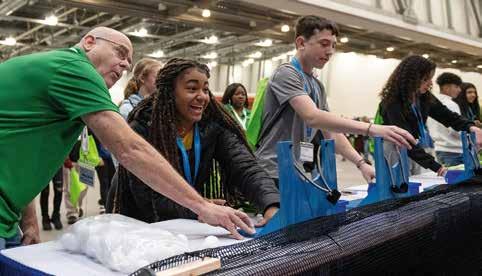
springmaker Scherdel Sales and Technology and SMI associate member A.I. Technology, the North American distributor for Itaya spring machines.
Held at DeVos Place in Grand Rapids, Michigan, March 27, 2024, the event “allowed more than 8,000 West Michigan middle and high school students to engage with over 300 high-demand careers ... students got their hands on 121 interactive exhibits from 111 employers representing 301 professions from across five high-demand industries,” including the new agribusiness sector, Malinda Powers of West Michigan Works! wrote in an email.
The advanced manufacturing sector of MiCareerQuest covered 29,600 square-feet. with 31 exhibitors presenting 75 manufacturing-related professions. The second-largest booth at the event was the springmakers showcase, a 160 square-foot exhibit featuring a hands-on computer numerically controlled (CNC) springmaking system and a “springshot” game. Two teenage participants, children of springmakers, taught attendees how to use a CNC spring machine to create one of several wireforms. Attendees took home their creations.
Not a Recruiting Event
“MiCareerQuest is not your average career fair. In fact, it’s not a career fair at all. It’s a career exploration experience,” touts the organization’s website (www.micareerquest.org).
“Students rotate through sectors highlighting six high-demand industries: agribusiness, construction, health sciences, hospitality, information technology and advanced manufacturing. Students engage with professionals and participate in activities that showcase various high-growth occupations, opening their eyes to opportunities for great careers in West Michigan.”
Students learn about stored energy by playing with a “springshot” at the spring manufacturing booth at MiCareerQuest.
“It’s kind of a fun adventure,” Dunwell says. Students wear colored lanyards and follow leaders to one of the six career sectors. Upbeat music about every 25 minutes signals it’s time to change up.
Beyond the Cliché
Exhibitors at MiCareerQuest’s advanced manufacturing sector tackled another crucial challenge: combating outdated stereotypes about manufacturing careers. The students quickly learned that modern manufacturing facilities are high-tech, with a growing emphasis on automation, robotics, CNC and computer-aided design (CAD). Gone are the days of dark, dingy factories that their parents may recall.
“We hope to show the kids the types of technologies we are working with,” Dunwell says. “It’s high-tech, cool, sophisticated and precise.”
This event showcases innovative technologies and has the students’ peers demonstrate their use. It shatters the perception that manufacturing is about dirty, boring jobs. Students see firsthand the creativity, problem-solving and technical expertise of modern manufacturing processes.
Building a Pipeline
MiCareerQuest recognizes that addressing the skills gap requires a long-term approach. By planting the seeds of interest early on, the program fosters a future generation of skilled workers prepared to fill critical manufacturing roles.
By nurturing local talent, MiCareerQuest helps bridge the skills gap and ensures a sustainable workforce for the manufacturing sector. This not only benefits individual companies but also contributes to the overall economic health of the region.
“We’re saying, ‘What can we do with the students in our communities?’” Dunwell emphasizes. While some companies might be concerned about promoting themselves to such a young audience, Dunwell sees the bigger picture.
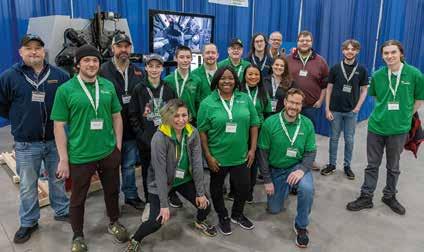
“We’re not promoting Wolverine or Scherdel as specific spring companies,” he clarifies. “We’re trying to say, ‘ This is what springmaking is like.’”
The goal is to spark an interest in manufacturing as a whole, planting a seed that may blossom years down the road. The program engages young people. Students leave wanting more, and employers enjoy the opportunity to showcase their industries.
“Our staff truly appreciate the excitement they see in the kids’ eyes, ” says Dunwell.
A Blueprint to Follow
The success of MiCareerQuest has garnered national attention, serving as a model for other states looking to clone its approach. The program’s collaborative nature, where multiple industries work together, shows the power of a unified effort to tackle workforce shortages. z
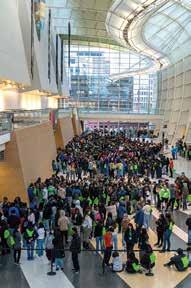
Over 8,000 West Michigan middle and high school students attended the career exploration event.
MiCareerQuest is not your average career fair. In fact, it’s not a career fair at all. It’s a career exploration experience.
Employees and family members of Wolverine Coil Spring, Scherdel Sales and Technology and A.I. Technology engaged students at the spring manufacturing booth.
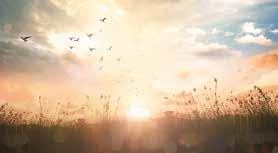
By Phil Sasso
Difference Makers
The Yost Superior Co. Cultivates Well-being
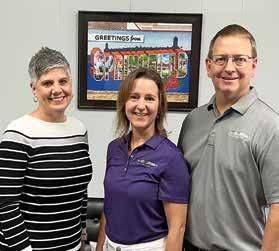
At the core of most successful companies is a commitment to both their products and people. This is true at The Yost Superior Co., an SMI charter member company in Springfield, Ohio. They recently embraced a novel approach to employee wellness: workplace access to monthly face-to-face life coaching sessions.
The idea took root in 2021 when Yost director Sharon Deerwester and her husband, Yost president Dave Deerwester, were inspired to help their employees.
Sharon heard a local human resources group presenter speak about providing meaningful employee benefits and emphasizing mental wellness. “In essence, the meeting discussed investing in mental health as a proactive way to support employees and, in turn, the business,” Sharon explained.
Statistics show that when employees come to work thinking and feeling better, they are more likely to perform better, with 25% fewer days missed, a 24% increase in productivity and 43% less likely to leave the company.1
Shortly after the HR meeting, Sharon had a newer employee come to her office with thoughts of suicide. Instead of contemplating
if they should try to find ways to help their employees with their mental well-being, Sharon and Dave’s question turned to how. Sharon began looking into various organizations and services that were available to them. The hope was that someone could come to Yost and meet one-on-one confidentially with their team members.
“I had heard of someone who had gone through the certification process to become a professional life coach, and I messaged her on LinkedIn,” Sharon explained. Life coach Carisa Peters reached back, and what began as a simple inquiry grew into an innovative partnership.
Peters had never coached in a corporate setting before but saw no difference between them and her other clients. Most of Peters’ clients from across the country interact
What began as a simple inquiry grew into an innovative partnership.
Yost Superior life coach Clarisa Peters (left) with Sharon and Dave Deerwester.
with her via Zoom, so regular face-to-face meetings at the workplace seemed a natural extension.
The program was launched at a monthly Yost company luncheon in March 2022, where Peters introduced herself to employees and outlined her new role as the company’s life coach.
“She explained coaching would be provided to Yost employees individually in an office in our building,” Sharon says. The free program is an entirely confidential employee benefit. Yost maintains discretion, aiming to de-stigmatize mental health.
“We have no idea what the conversations are about,” Dave emphasizes. “It’s a private one-on-one session with the life coach. We’re not aware of what they’re working on or what they’re talking about. We don’t know if it’s personal or work-related.”
Employees can schedule a session with Peters any time during the two half days a month she is at Yost’s facilities. Since its inception, about half of the company’s 50 employees have participated in at least one life coaching session. On average, about a quarter of Yost’s employees attend a 20-minute personal life coaching “power session” with Peters on any given month.
“All they need to do is send me a text or an email, and then I just forward that to Carisa, and she takes the scheduling from there,” says Sharon. “It is open to everyone.” Participants in varied roles, from management to team members working in the factory.
Peters’ approach involves more than individual 20-minute sessions. She sends follow-up emails, sometimes including resources and links to further information.
Dave and Sharon reached out and asked several employees if they would share what
they have found helpful regarding Peters’ life coaching (identities have been kept confidential):
“Carissa has helped me deal with difficult customers. The coaching model helps breakdown my thinking and why I am reacting in a certain way. It provides an alternative route instead of having the same unhelpful thoughts. I’ve also found it a helpful source of unbiased advice for both personal and work matters.”
About half of the company’s 50 employees have participated in at least one life coaching session.
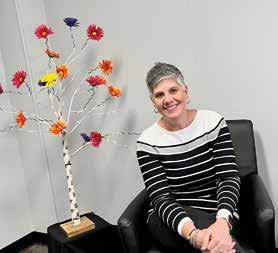
Life coach, Carisa Peters, helps employees “clarify their goals, overcome obstacles and create actionable plans.”
Difference Makers
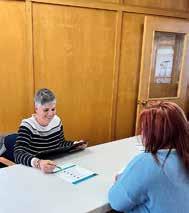
“While we are always growing and changing, Carisa’s life coaching has helped me to be more focused on my thoughts, more aware when I feel overwhelmed or anxious, and how to divert my thoughts to more productive feelings and actions. I can understand what I feel, why I feel that way, accept it and find my anchor thoughts that bring me back to a less chaotic place.”
“I’ve watched a few employees start out their career doing great and being very productive. But then they experienced some life struggles that took a toll on them personally and in their job. While I strive my best to help any of my peers, I don’t have the tools to help them all navigate the life challenges they have been facing. Once our company started offering life coaching to our employees, I noticed how much it had helped people with these issues.”
A Life Coach on Life Coaching
We asked Yost Superior’s life coach, Carisa Peters, to discuss her profession and its benefits in a business setting.
How did you become a life coach?
My parents started a printing company when I was a year old. I grew up in the business and would end up owning/operating the business for the last 15 years. Our business was impacted when COVID hit, forcing me to assess my life. I realized I wasn’t happy or living my life in a healthy manner. I stumbled upon life coaching through a podcast recommended by my doctor. It was action-oriented and helped me make positive life changes. I underwent a transformation and eventually sold our family business to pursue life coaching full-time in 2022.
In a nutshell, what is life coaching?
Life coaching is about helping individuals clarify their goals, overcome obstacles and create actionable plans for personal and professional growth. It’s different from therapy in that it’s not focused on diagnosing or treating mental illness but rather on empowering individuals to reach their full potential.
You’ve said life coaching is for people who want a better life. Could you elaborate?
Life coaching is for individuals who are functional in their daily lives but feel something is missing or not quite right. They may be successful in their careers or relationships but still struggle with happiness or fulfillment. Life coaching helps them identify areas for improvement and provides tools and support to make positive changes.
After more than two years, the life coach initiative has become ingrained in Yost’s culture, fostering personal growth and overall morale among its workforce. “It’s about attitude and action,” says Dave, indicating the practical tools Peters shares. “Things are going to happen in our lives. Life coaching gives us tools, so we have the right attitude and right action.” z
1. Bondar J, Babich Morrow C, Gueorguieva R, et al. Clinical and Financial Outcomes Associated With a Workplace Mental Health Program Before and During the COVID-19 Pandemic. JAMA Netw Open. 2022;5(6):e2216349. doi:10.1001/ jamanetworkopen.2022.16349
Know a difference maker?
Email your suggestion to Phil Sasso at phil@smihq.org
What credentials should someone look for when choosing a life coach?
While life coaching isn’t regulated, look for coaches who have undergone reputable training programs or certifications. Referrals and testimonials from previous clients can also help assess a coach’s effectiveness and suitability for your needs.
How have you incorporated life coaching into the business setting, and what tips do you have for other business owners considering it?
Incorporating life coaching into the workplace can improve employee well-being, productivity and overall company culture. Offering coaching as part of employee benefits demonstrates a commitment to support their holistic development. Businesses can introduce coaching through companywide announcements, informational sessions and providing dedicated time and space for coaching sessions. Regular communication and feedback between coaches and employers can ensure the program’s success and address challenges.
Anything else you’d like to add?
Life coaching is a forward-thinking approach to employee development and well-being. By investing in life coaching, businesses can foster a positive work environment, improve employee satisfaction, increase retention and ultimately drive better business outcomes. It’s a valuable investment in both individual and organizational growth.
For more than two years, Peters has held confidential 20-minute monthly coaching sessions with Yost employees.
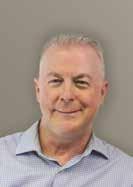
Gary McCoy
Lessons about Ants and AI
My granddaughter just turned three. With her curly hair, sweet smile and bright personality, she’s curious about many things. Currently, she’s fascinated with insects, and specifically, with ants.
When I asked my son about a present for her birthday, he said, “How about an ant farm?” The present arrived this week, and we’ll see how long the fascination lasts. Stay tuned.
We recently concluded our annual meeting in San Diego, and we asked attendees in our post-event evaluation about future speaker topics. The top two subject matters listed were the economy and artificial intelligence (AI).
I’m curious like my granddaughter and have experimented with ChatGPT before, which is basically an AI chatbot. ChatGPT can respond to questions and compose various written content, including articles, social media posts, essays, code and emails. In light of my granddaughter’s interest, I decided to ask ChatGPT: “How are ants and humans similar?” Here’s the answer:
Ants and humans, despite their vast differences in size and complexity, share several surprising similarities. Both species are social creatures, relying on intricate communication systems to organize their societies and coordinate tasks. They exhibit complex behaviors such as cooperation, division of labor and collective problemsolving. Just as humans build cities, ants construct elaborate colonies with chambers for various functions like nurseries, food storage and waste disposal.
Additionally, both ants and humans demonstrate remarkable adaptability to diverse environments, allowing them to thrive in a wide range of habitats worldwide. They both possess highly developed senses that aid in navigation, communication and resource acquisition. Moreover, both species exhibit forms of altruism, with individuals sacrificing personal gain for the benefit of the group, whether it’s ants defending their
colony or humans engaging in acts of kindness and cooperation.
Furthermore, ants and humans share similarities in their ecological impacts, shaping and influencing their respective environments through their activities.
Despite the vast biological and behavioral disparities, exploring these parallels illuminates the fascinating interconnectedness of life on Earth, showcasing the diverse strategies organisms employ to navigate the challenges of survival and success.
Amazing that this 200-word answer was composed in seconds (I got a similar quick response when I asked about differences). While I could philosophize about ants and their productivity or adaptability, I think it is more interesting to consider the ways that AI can help or hurt your business.
Like any new technology, there are going to be early adopters and skeptics. I believe AI is a tool that can help improve productivity, if used right. Here’s what Forbes Advisor said in a recent article:
“While concerns exist, such as technology dependence and potential workforce reduction, most business owners foresee a positive impact from AI implementation. The anticipated benefits of ChatGPT, such as generating content quickly, personalizing customer experiences and streamlining job processes, demonstrate the transformative potential of AI in various aspects of business.”1
I look at AI as similar to automation, because automation has helped many manufacturers take away manual, repetitive jobs and give workers more meaningful and productive duties.
Is AI a threat? Possibly. We intend to explore the topic in more depth in Springs and at our next annual meeting. In the meantime, I don’t anticipate any more articles on ants!
Gary McCoy Executive Director
1. “How Businesses Are Using Artificial Intelligence In 2024,” by Katherine Haan, Forbes Advisor, April 24, 2023 (www.forbes.com/advisor/business/software/ai-in-business)
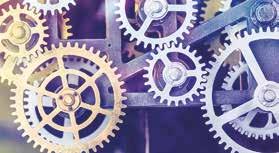
Inside SMI
SpringWorld 2024 Symposium

Be sure to join your spring industry colleagues in Rosemont, Illinois, for the 2024 edition of SpringWorld, presented by the Chicago Association of Spring Manufacturers, Inc. (CASMI) and the newly added Symposium, presented by SMI. This year’s event will take place Oct. 2–4, 2024, at the Donald E. Stephens Convention Center.
Education in the Spotlight
In addition to the CASMI-hosted exhibit hall, SMI will host two mornings of business and technical content, Oct. 3–4, including 24 educational sessions.
The educational symposium will include speakers on workforce development, technical topics such as spring equipment, new developments in spring and wire technologies and other manufacturing–related topics.
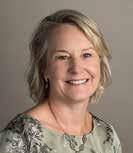
Among the featured speakers is Micki Vandeloo, president of Lakeview Consulting, a team of five experienced grant professionals who have collectively obtained over $150 million in grant funding for clients in the manufacturing and trade association communities. She will discuss opportunities for springmakers to obtain manufacturing grants and funding for apprenticeship programs and other leadership training opportunities.
The Lakeview team provides research, writing and consulting services to help their clients fund their success. Vandeloo has
more than 15 years’ experience performing grant consulting services for clients in the manufacturing community, including forprofit companies, manufacturers and trade associations. Her engineering and business degrees, as well as over 25 years’ experience in manufacturing, provide a sound technical foundation for her grant writing services.
Vandeloo published the book, “THE ForProfit Grant Writing Guide,” in 2014 and has been honored by the Grant Professionals Association and the St. Louis Small Business Journal for her work.
Daniel B. Pickard, based in Washington, D.C., is a lawyer with Buchanan Ingersoll & Rooney. He has more than 20 years of experience representing clients in international trade and national security-related matters.
Pickard will present two sessions during the symposium related to his work representing clients in all aspects of international trade law, including trade remedy matters such as anti-dumping (AD), countervailing duty (CVD), and safeguard investigations. Specifically, Pickard helps U.S. manufacturing companies who are losing market share or suffering from decreased profits to obtain relief against unfairly priced imports. He is rated among the nation’s leading international trade lawyers and is a frequent presenter and commentator on U.S. trade policy.
Pickard currently serves on Buchanan, Ingersoll & Rooney’s board of directors. Daniel B. Pickard
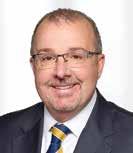
Micki Vandeloo
Three Days of Exhibits and More
The SpringWorld show includes three days of exhibit hall hours. Below is a tentative agenda, which is subject to change.
Wednesday, Oct. 2, 2024
8 a.m.–6 p.m. Registration
9 a.m.–5 p.m. Exhibit Hall Hours
1–3 p.m. CASMI Technical Theater
5–6 p.m. Taste of Chicago Reception
6 p.m. Exhibit Hall Closes
Thursday, Oct. 3, 2024
8 a.m.–6 p.m. Registration
8–8:50 a.m. SMI Educational Symposium, Day 1, Session 1
8:50-9 a.m. Break
9–9:50 a.m. SMI Educational Symposium, Day 1, Session 2
10 a.m.–5 p.m. Exhibit Hall Hours
1–3 p.m. CASMI Technical Theater
5–6 p.m. Oktoberfest Reception
6 p.m. Exhibit Hall Closes
Friday, Oct. 4, 2024
8 a.m.–6 p.m. Registration
8–8:50 a.m. SMI Educational Symposium, Day 2, Session 1
8:50–9 a.m. Break
9–9:50 a.m. SMI Educational Symposium, Day 2, Session 2
10 a.m.–1 p.m. Exhibit Hall Hours
1 p.m. Exhibit Hall Closes
1–5 p.m. Exhibit Teardown
Registration for the Exhibit Hall is free or $25 on-site. To attend the Symposium it is $50 per person or $75 on-site. For the latest details and to register for SpringWorld, visit www.springworld.org.
Sponsors Help the Cause
SMI is grateful for the support of its sponsors in helping make the educational symposium a success. Gibbs Interwire is a Platinum Room sponsor and WAFIOS is a Ruby Room sponsor.

SMI is also grateful to associate member, Industrial Steel & Wire (ISW), for being the SpringWorld visionary sponsor.
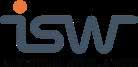
Spots are still available for one more Platinum and Ruby sponsors and two Diamond room sponsorships. For more information on sponsorship, visit https://bit.ly/SW-sponsor or contact Gary McCoy at gary@smihq.org or 847–450–6240.
2024 Spring Design Training Schedule
Class
301 Springs — Fatigue
In-Person at SpringWorld
201 Compression Spring Design
202 Extension Spring Design
203 Torsion Spring Design
Webinars are offered from 1–5 p.m. EDT/EST
*Dates are subject to change.
Aug. 15, 2024
Oct. 1, 2024
Oct. 17, 2024
Nov. 14, 2024
Dec. 19, 2024
Springs Are Everywhere Podcast
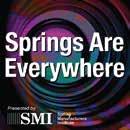
The “Springs Are Everywhere” podcast provides educational information on manufacturing issues. The program, currently offered on a quarterly basis, provides SMI with another venue to share information, inspire action and educate people about the spring industry with leading experts.
Hosted by SMI executive director, Gary McCoy, the podcast is on Spotify and SMI’s YouTube channel. Be sure to like, review and subscribe to the program, which is available on all major podcast platforms.
The “Springs Are Everywhere” podcast is produced with the help of Platinum Sponsor, Gibbs Interwire and Silver Sponsor, Automated Industrial Motion.

As a component of SMI’s Advanced Spring Design (ASD) computer software, SMI offers spring design training programs to help industry newcomers and veterans increase their knowledge. Training is available to both members and nonmembers.
Our upcoming training schedule for the rest of 2024 is shown below. An in-person class at the 2024 SpringWorld Expo and Symposium, sponsored by CASMI and SMI, will be offered. More details to come. For more information and to register for classes, visit https://bit.ly/SMItech or contact Gaby Carrasco at gaby@smihq.org.
Calendar z Key Events for the Global Spring Industry
2024
Oct. 2–4
SpringWorld Expo and Symposium
Donald E. Stephens Convention Center Rosemont, Illinois springworld.org
Sept. 13
ISO/TC227 Meeting Milan, Italy
2025
March 29–April 1
SMI Annual Meeting
Kimpton Hotel Fontenot New Orleans www.smihq.org
Send Us Your News
SMI members receive priority placement for their product, company, personnel and events announcements in the magazine. Your news releases should be roughly 50 to 100 words and may be accompanied by color photos (high-resolution .JPEG photos at 300 dpi preferred). Send to gaby@smihq.org.
We’d love to hear from you!
Springs welcomes your notes and comments on the contents of our publication. Please email Phil Sasso, Managing Editor, at phil@smihq.org.
SMI Mourns Passing of Members
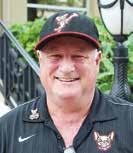
Keats Manufacturing recently announced the sudden passing of Matt Keats, 66, May 10, 2024 due to complications from surgery. Keats was a former member of the SMI board of directors.
Keats leaves a legacy in El Paso, Texas, that started in 1994 with the founding of Keats Southwest. He served numerous roles at the Keats companies becoming an owner and president of the El Paso operations, most recently, serving as co–chairman with his brother, Wade Keats. He was involved in the El Paso Chamber of Commerce, Hospice El Paso and Sunrise Rotary.
Keats grew up in Winnetka, Illinois and played hockey for New Trier High School’s first hockey team that won the state tournament in 1973. He was the only freshman on the team. Keats continued playing hockey during his college years at Curry College in Milton, Massachusetts, where he majored in psychology. Post–college, Keats stayed in the Boston area to work at the Joslin Diabetes Center as a phlebotomist until he moved back to the Chicago area to join the family business, Keats Manufacturing Co.
Keats was predeceased by his parents Bert and Barbara and is survived by his sons Dean and Brian, brother Wade (Christine), sister Paula (Steve Horwath), nephews Brad, Todd, Jack, and niece, Jessica.
The company asked that donations be made to Hospice El Paso (https://bit.ly/keats24-2) and the Sunrise Rotary of El Paso (https://bit.ly/keats24-1).
A celebration of life event for Keats was held May 31 at Southwest University Park (Chihuahua Stadium) in El Paso, Texas. Another celebration of life is scheduled to be held in the Chicago area at a future date.
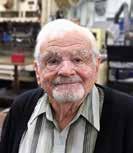
Kenneth John “Kenny” McLaren, 68, March 11, 2024. McLaren was a member of the CASMI board of directors. McLaren is survived by his wife, Fiona, four children and two grandchildren.
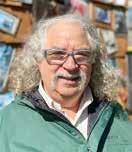
CASMI said in an announcement about McLaren’s passing, “Kenny was a compassionate, kind and caring man with a wonderful sense of humor. He touched the hearts of all who knew him. He was a great addition to our board, adding bright new ideas at every meeting, but most importantly he was our friend. His career spanned decades in our industry.”
Over the course of his life, McLaren mastered a foundation of manufacturing skills as he grew from an apprentice tool and die maker, to ultimately becoming the vice president of operations at Perfection Spring and Stamping. His career spanned three countries and five decades.
Services for McLaren were held March 19, 2024. Memorial donations may be made in McLaren’s name to the Itasca Lions Club Itasca Lions Club https://bit.ly/mclaren24.
Louis S. Kahn, 97, the founder of Perfection Spring and Stamping Corp. Following his honorable discharge from the U.S. Navy in 1946, after serving during World War ll, Kahn attended trade school to become a tool and die maker.
In 1955, with $5,000 in capital, he purchased a single coiling machine and a “very used” fourslide machine and founded Perfection Spring. His wife, Barbara, would assist by running the machine during the day, and Kahn would go on the road by day to drum up business, working on new tooling and setting up new jobs at night, after dinner.
Kahn always said, “Back then, business was done with a handshake, based upon trust and integrity…Just the way I like it.”
Kahn retired full-time from the company in 1991, handing the reins to his two sons, David and Joshua. Perfection Spring and Stamping, now in its 69th year of business, continues Kahn’s legacy.
Matt Keats
Louis S. Kahn
Kenneth John McLaren
SMI Survey Schedule: Benchmark with Your Peers
SMI regularly surveys its members to help them understand how they are doing relative to others in the industry. Confidentiality is important when surveys are conducted, which means no company data is ever shared with SMI members or SMI itself.
Here’s the schedule of surveys for 2024 and into 2025.
Key Business Trends (regular and associate members)
Second Quarter 2024
Third Quarter 2024
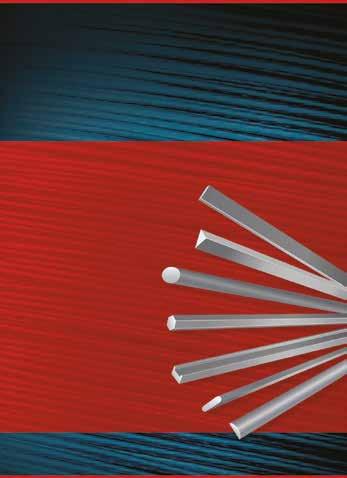
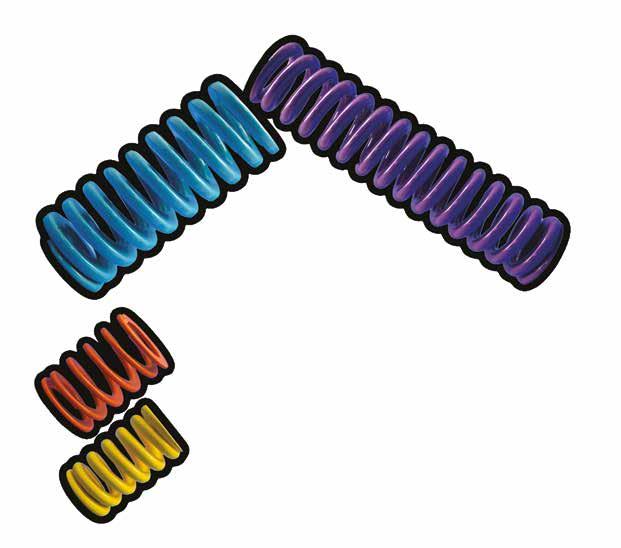
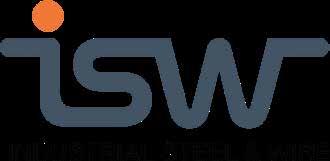
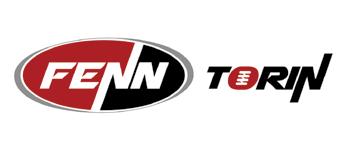

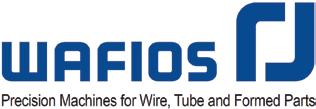
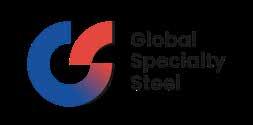
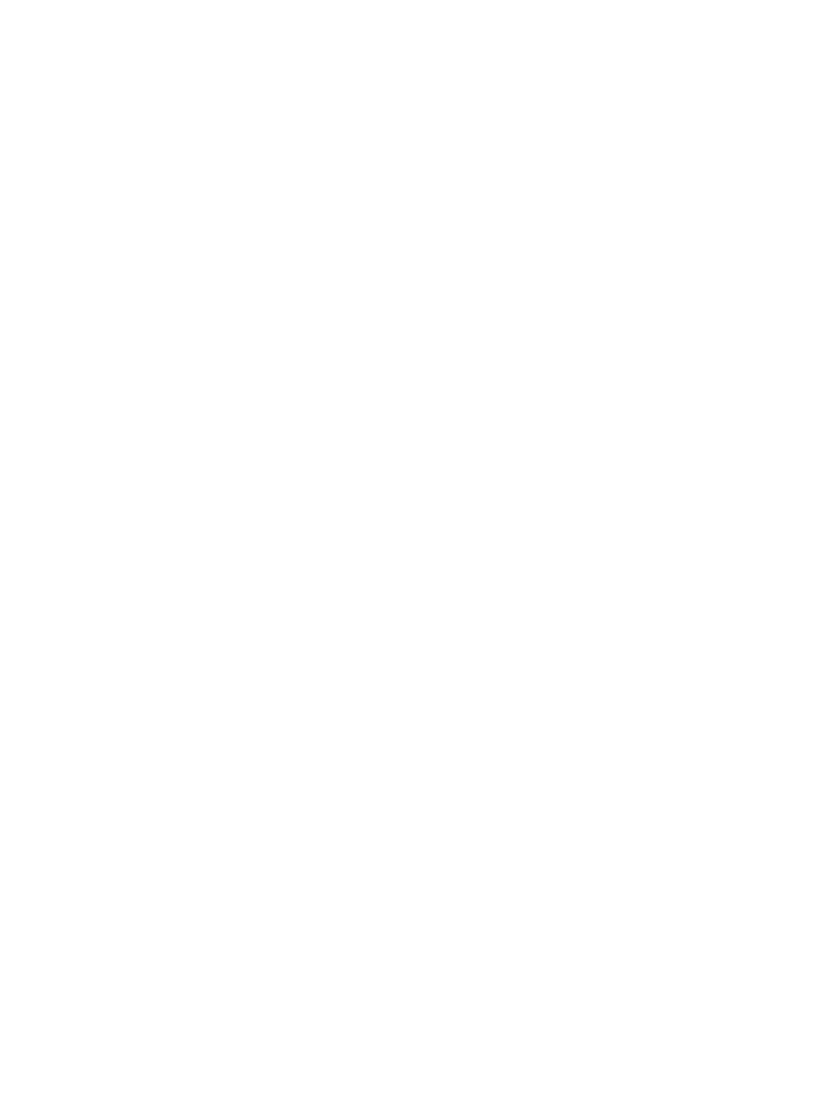

Gaby Carrasco
Podcast Picks
Managing Priorities
The How of Business | Henry Lopez
E522 | May 27, 2024 | 46 min.
I often wish for more hours in the day. Between work, caring for a toddler, household chores and my pregnancy, prioritizing tasks is challenging. This podcast review focuses on managing priorities, a topic I and many others struggle with.
Henry Lopez, a serial entrepreneur and small business coach, hosts the podcast aimed at helping business owners start, run and grow their small businesses. His guest, Harry Max, is an executive coach, consultant and hands-on product design and development leader. Max is a managing partner at Peak Priorities and the author of “Managing Priorities — How to Create Better Plans and Make Smarter Decisions.”
Max wrote the book to meet a demand for resources on prioritization, especially among newly promoted managers, people with increased responsibilities and business owners. After speaking on a different topic, he was surprised by a flood of questions on prioritization. After some research, Max found no books exclusively about the topic.
He emphasizes that rather than work more hours, small business owners should learn to prioritize tasks effectively. Max says decision-making involves choosing and implementing an option, while prioritization involves identifying and ranking options in order of importance. Prioritization requires identifying options and determining the criteria for ranking them.
Max’s book is as much for a team or organization as it is for personal use.
“There are a very, very small number of incredibly powerful approaches if it’s just you by yourself, on your own, or if you’re a member or leading a team, or if you’re part of a larger organization.”
For example, the “speedboat” visual framework helps teams prioritize by identifying anchors (things that slow you down), rocks (things to avoid) and propellers (things that speed you up).
Max’s DEGAP method of prioritization has five steps:
1. Decide whether you have the time to commit to the process.
2. Engage in the process and identify who needs to be involved.
3. Gather all relevant information.
4. Arrange the information using a suitable framework.
5. Prioritize the options based on the gathered information.
These steps can help identify tasks we avoid, Max says. We often avoid tasks that cause us stress.
“In my research, I’ve learned it’s not really a procrastination problem — it’s an emotional regulation problem,” Max says. “It is kind of overwhelming to think about these things.”
While I can’t add more hours to my day, I can implement these skills to prioritize my hectic life better. z
Want to share a business development podcast for me to review? Please send your suggestions to gaby@smihq.org.

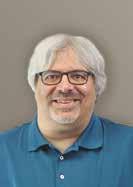
Reviewed by Phil Sasso
Book Corner
Manufacturing Engagement 98 Proven Strategies to Attract and Retain Your Industry’s Top Talent
In “Manufacturing Engagement,” author Lisa Ryan provides a guide to building a corporate culture that engages employees and reduces attrition. She distills her insights into 98 actionable strategies, making the book a practical resource for manufacturing leaders.
Rather than a sit-thru read, I suggest you keep a copy on your desk or laptop and read it in bite-size pieces for daily inspiration to improve your business and culture.
The book’s overall focus is on building a positive workplace. Ryan’s strategies are particularly relevant for spring manufacturing, where retaining skilled labor is an ongoing challenge. The first part of her book emphasizes the importance of building trust and open communication.
“When your colleagues and workers know that you will stand behind them, they are more likely to make better decisions, try new things and take calculated risks than if they don’t feel that you will support them,” she writes.
Ryan stresses two-way employee interaction, proposing an “open mind” policy to encourage employees to grow in independence and problem-solving skills.
“Have an ‘open mind’ versus an ‘open door’ policy,” writes Ryan. “An ‘open mind’’ policy shows that you are open to frank discussion and you will set appropriate boundaries that work for you and your team.”
She also discusses her hallmark strategy: employee recognition and appreciation.
Ryan is the founder of Grategy, a professional training and coaching firm that works with individuals and organizations to use the power of gratitude in business and in life. In the book, she highlights the impact of gratitude and employee recognition to increase morale and reduce turnover.

“Be the first to acknowledge and celebrate the good work of your workforce,” states Ryan. She quotes Dale Carnegie, “Be lavish in your praise.”
In manufacturing, recognizing and rewarding employees’ contributions can foster a sense of ownership and pride in their work to enhance overall production quality.
Ryan suggests flattening the organizational chart to facilitate better communication and decision-making. She believes this approach produces more innovative solutions and improves worker responsibility.
Finally, she encourages leaders to understand and serve employees. By regularly engaging with staff, managers build mutual respect and stronger relationships.
Ryan’s practical strategies provide a blueprint for building a more engaged and productive workforce, leading to meaningful culture and better retention.
Book Corner
Ryan is a past SMI annual meeting speaker, Springs contributor and a guest on the inaugural episode of the “Springs Are Everywhere” podcast (https://bit.ly/SAE-S1E1).
I emailed Ryan to ask for her insights on the book and its relevance to springmakers. Here’s my question and her response.
If you had to pick one strategy, which would you say is the most relevant or impactful to spring manufacturers?
I’d suggest Chapter 6, “Building a Culture of Appreciation,” would be the most relevant and impactful for spring manufacturers. This chapter explores the importance of employee engagement and how a culture of appreciation can positively affect many aspects of your business.
Employee Motivation: Expressing gratitude boosts morale and productivity, which is essential in the demanding environment of spring manufacturing.
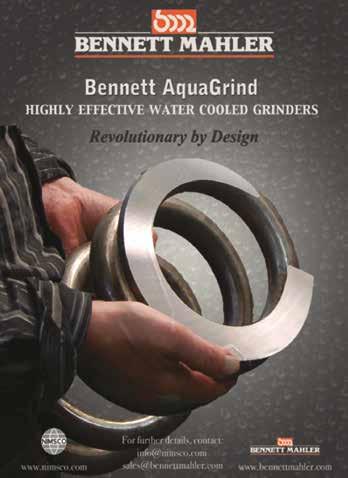
Retention Strategies: The methods covered help reduce turnover by making employees feel valued and connected to the organization’s success.
Customer Satisfaction: An engaged and grateful workforce positively impacts the customer experience, which is crucial for business growth in manufacturing.
This chapter can provide valuable insights to your readers, offering actionable strategies that could have a meaningful impact on their businesses. z
Ryan has agreed to give Springs readers the “Manufacturing Engagement” e-book.
Download your free copy at: http://bit.ly/mfgengage
Have a favorite business book you would like me to review? Email your suggestion to phil@smihq.org.

North American Spring Tool (NAST) has merged with Spring Manufacturers Supply Company (SMSC), to create a new company, Spring Tool Solutions (STS).
Providing a complete line of carbide and steel tooling for spring coiling machines:
Fenn (TORIN) | Itaya | MEC | Samuel | Sleeper & Hartley and more... (see website for complete list)
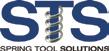
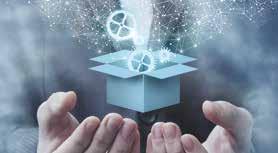
New Products
Cooling and Parts Collecting Systems Streamline Production
HSI and Forming Systems, Inc. have introduced various combinations of cooling and parts-collecting systems in response to changing demands.
HSI cooling systems include flat or elevating conveyors with speed-variable cooling fans (optional), which cool the parts while moving them from the oven to the collection system.
Forming Systems can provide a variety of parts collecting systems for diverse
demands. Parts can be counted by number of pieces, time or weight and collected with HSI standard bins (PC-30, PC-100 etc.) or your regular part container/carton for ease of handling (PCR-50 and PCS-5).
For additional information, including option details and pricing, please contact Forming Systems, Inc. at info@formingsystemsinc.com or 269-679-3557. z





















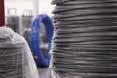
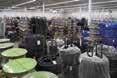
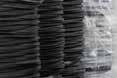
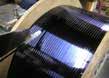
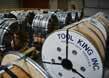
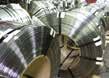
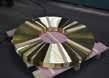
Send us Your News
SMI members get priority placement of their product news. News releases should be roughly 50 to 100 words and may be accompanied by color photos (HiRes .JPEG at 300 dpi preferred). Send to gaby@smihq.org.
Your source for the best in close tolerance strip and edged
strip: cold rolled high carbon/pre-tempered spring steels, coated, low carbon stainless, copper based alloys and aluminum ultra-narrow width, close-tolerance slitting edging: round, square, semi-round, deburred, custom, etc oscillate (traverse) and ribbon wound coils ISO 9001: 2015 certified 43 years servicing the industry
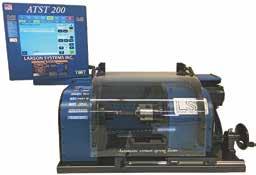
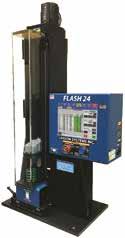
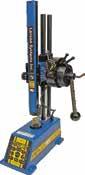








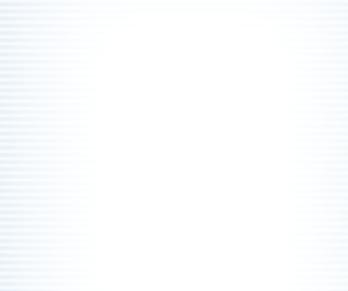

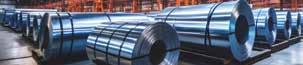
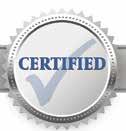
Don’t Settle For Seconds
At Admiral Steel, we understand that your product is your reputation. That’s why we take pride in specializing in premium quality high carbon steel that meets specs such as AMS, QQS, and ASTM certified. Our commitment to providing certified material means that you can trust that you are receiving the highest quality steel available. Don’t settle for seconds and rejects. Choose Admiral Steel for the assurance of premium quality steel products. Call
SUPERIOR QUALITY SPRING WIRE

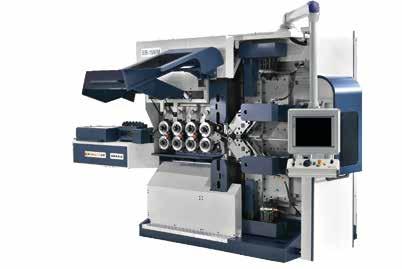





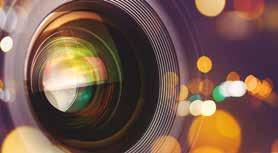
y Gardner Spring, Inc.
Bill Wynn
Name: Bill Wynn
Snapshot
Company name and city:
Gardner Spring, Inc., Tulsa, Oklahoma.
A brief history of your company: Founded in Chicago in 1907, Gardner moved to Tulsa in the 1960s, and has been a woman-owned business since 1978.
Job title: Vice President of Operations. What I like most about being a springmaker: Solving problems. It’s particularly rewarding to see a finished product where a spring we helped design plays a key role.
Spring industry affiliations: SMI, National Association of Manufacturers (NAM) –Trade Policy Committee
Birthplace: Little Rock, Arkansas.
Current home: Tulsa, Oklahoma.
Family (spouse, children, pets, etc.): I have a daughter (Yuchen) in college and a cat and dog at home.
Favorite food: Anything with a spicy kick.
Favorite books/authors: Kurt Vonnegut, Christopher Moore and David Sedaris.
Favorite song/musician: I have lots of favorites, including The Beatles, The Rolling Stones, The Who, Richard Thompson and Harry Nilsson.
Hobbies: Travel, music and watching baseball and soccer games.
Favorite places: So far include the Pacific Northwest, Thailand and the French Riviera.
What is on your bucket list: There are four continents and countless countries that I’ve yet to visit. I’d also like to get to the stacks and stacks of books I bought but haven’t yet read.
Aside from necessities, what is one thing you could not go without: Music and friendships.
Best times of my life: High school, oddly enough.
A really great evening for me is: Cooking a nice meal with friends.
The one thing I can’t stand is: Hypocrisy.
My most outstanding qualities are: Loyalty and being a good listener.
People who knew me in school thought I was: A bit weird.
I knew I was an “adult” when: I had to start paying off my student loans and pay for my own insurance.
If I weren’t working at my company, I would like to: Be writing somewhere by a beach or in the mountains.
The most difficult business decision I ever had to make was: Letting people go is never easy.
Role models: My grandfather, who was a truly decent and patient man.
I would like to be remembered in the spring industry for: My commitment to quality and customer service.
But people will probably remember me for: Observations probably best kept to myself.
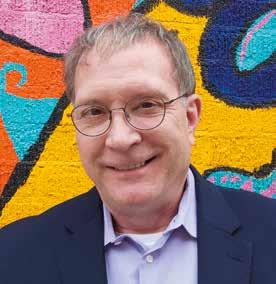
Bill Wynn
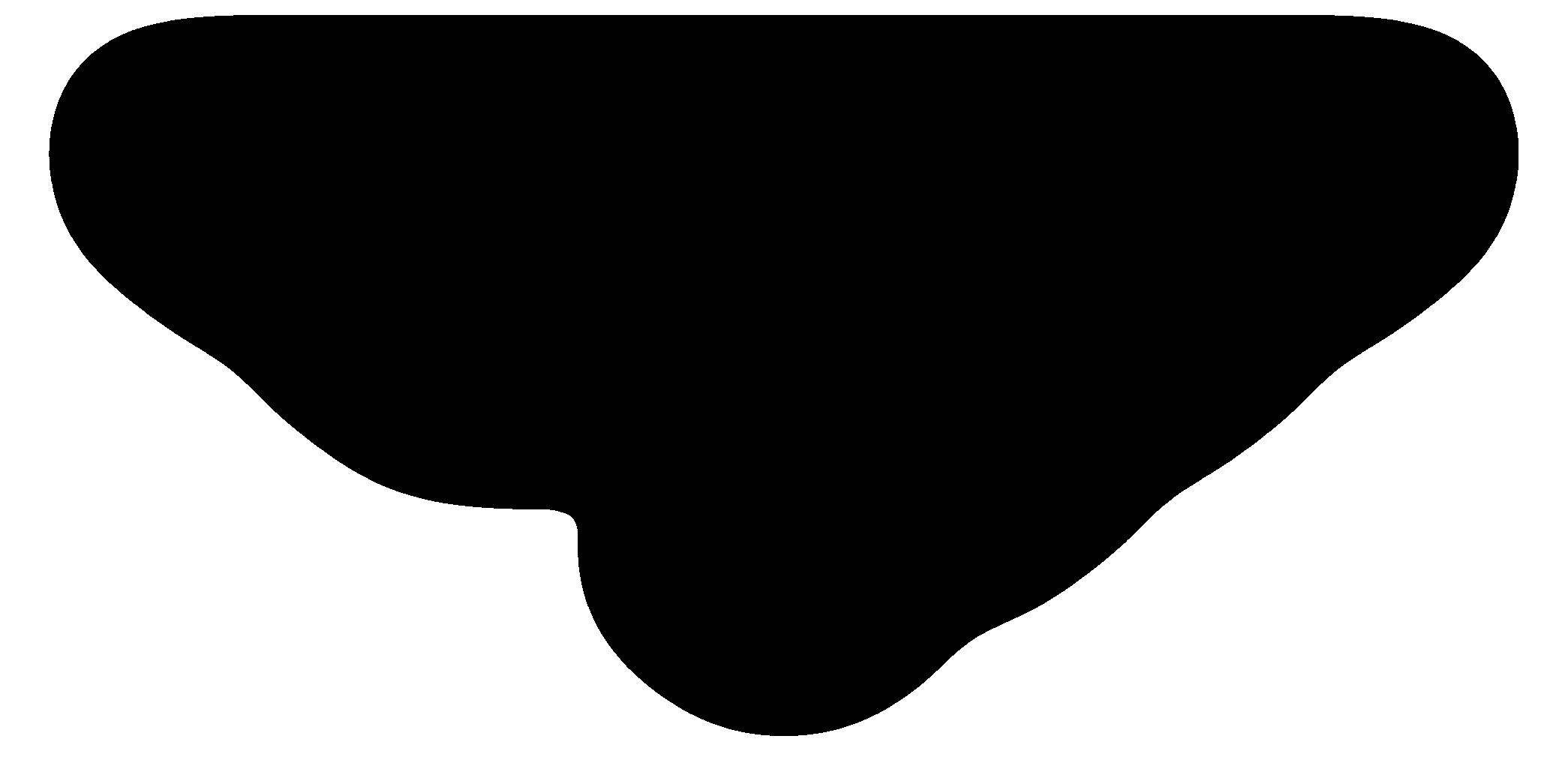
Introducing our new logos:

Change Service Requested
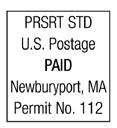
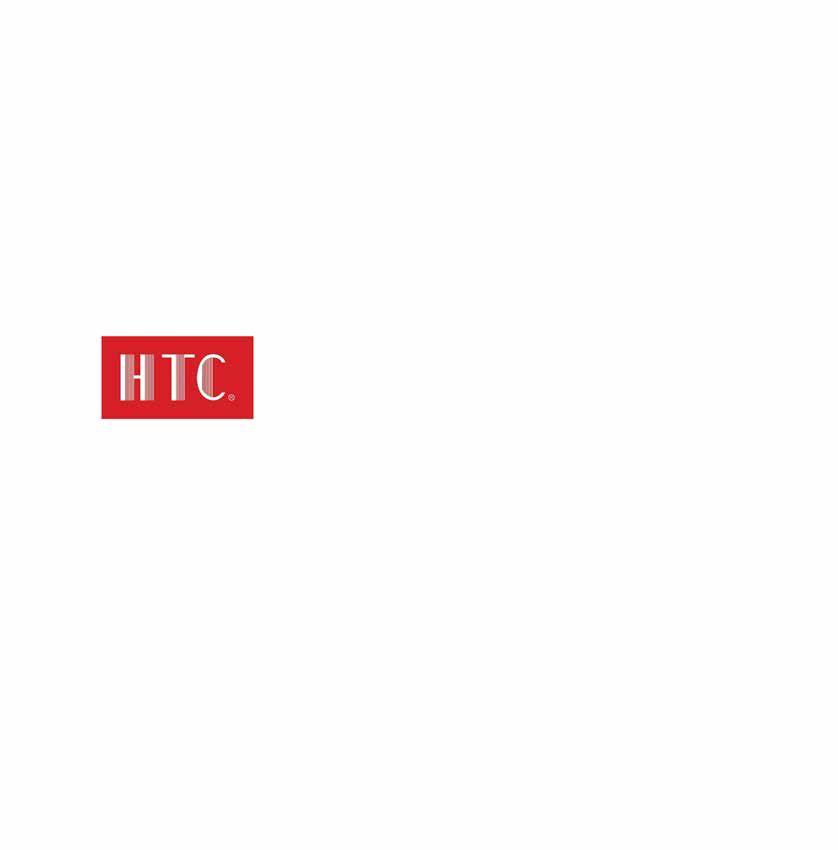
Central Slide