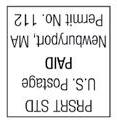
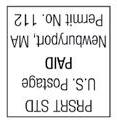
A Plan for the Future
In partnership with Fiduciary support from fiduciaryPATH 3(38)
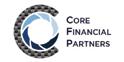
• Selects and monitors plan investments in accordance with the Investment Policy Statement (IPS)
• Provides professional asset allocation solutions that are suited to each participant’s needs
• Monitors fees to ensure they are reasonable
• Advocates for plan sponsors by negotiating below-market investment costs whenever possible
Administrative support from 3(16) plan administrator Pentegra Retirement Services

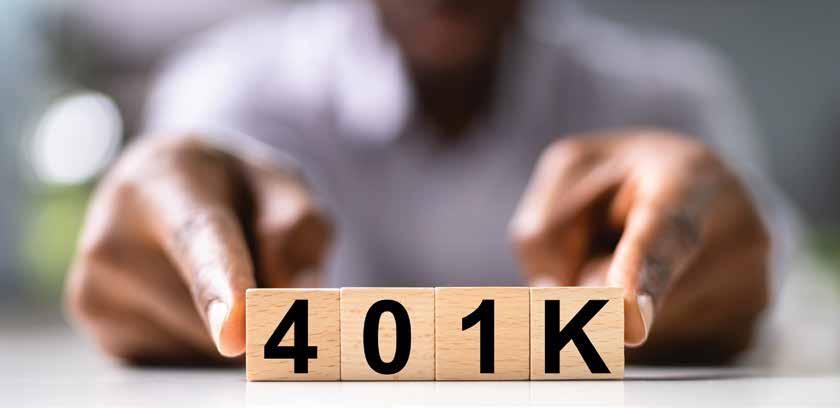
• Provides employee notices
• Interprets and enforces Plan Document
• Ensures IRS and Department of Labor compliance
• Includes an ERISA attorney as part of the compliance team
• Ensures flexibility in plan design
• Signs and files the 5500 form as the plan administrator
• Accepts nearly all responsibilities and powers of an ERISA fiduciary
Participant resources provided by Empower Retirement
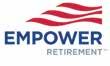
• Online tutorials
• Award-winning participant flyers
• Quarterly statements
• Electronic participant newsletters
• Online requests for loans, distributions and hardships
• Online investment fact sheets and prospectuses
• Annual fee disclosure statements
★ ★ ★ ★ ★ Thanks soooo much for all your help. I appreciate it. You’re the Best! ★ You are AMAZING!! I have known that for a long time, though. ★ Thank you, you’re a lifesaver today. ★ Thank you! You are very much appreciated! You’re the best!! The information you provide is so appreciated and always spot on. Thank you agin for your AWESOMENESS!!!!! We appreciate everything you do. It’s tough to be voted Supplier of the Year once, but to be voted Supplier of the Year two years in a row is outstanding!



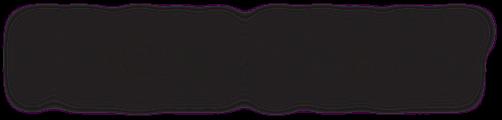
★ You’re the best! Your hard work and dedication make my job processing so much easier. Thank you and I appreciate it! I probably have worked with you more than any other vendor over the past year or so and you have always made my job very easy. You really are the best vendor I have gotten to work with in regards to being clear, concise, and timely with responses. You guys are absolutely amazing! Thank you so much!!! You are super-fast so I don’t even bother going to anyone else. You are awesome! So quick! ★ Wahoo!! SHIP IT!!!! I truly appreciate all of your hard work on this! Please let everyone involved know that I said THANK YOU! This was the best startup with a new vendor in our company’s history. ★ What a fantastic job, as always! The Gibbs Interwire team is amazing! ★ ★ ★ ★ ★
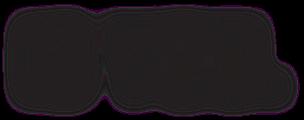
President’s Message
Managing Your Carbon Footprint
This edition of Springs focuses on “Carbon Footprint in Spring Manufacturing.” I know we have all heard the term “carbon footprint” before, but I wanted to research it before writing this message. I did this research because there seems to be a lot of discussion — if not outright debate — concerning this topic.
So first, what is your carbon footprint and how is it determined or measured? I found this answer from the Nature Conservancy: “A carbon footprint is the total amount of greenhouse gases (including carbon dioxide and methane) that are generated by our actions.”
These are facts, but what seems to be at the center of the debates and discussions is the impact of these gases and what actions we should take. While contemplating this message, I talked with one of our managers about the changes we have made at Winamac Coil Spring to save costs. For instance, we have implemented non-perishable, reusable tubs and containers in our manufacturing processes. This reduced our internal costs and minimized the production of items that needed frequent replacement. These products required electricity and natural resources to manufacture. Adopting such practices help decrease our company’s carbon footprint and cut costs. There may be some common sense in this approach, after all!
However, I am not suggesting that we can eliminate our carbon footprint. I appreciate CNC machines, automation, a good steak and air conditioning, all of which can contribute to our carbon footprint. Managing this delicate balance is what we are striving to learn about.
This edition of Springs will help us all become better informed about this topic. I am concerned not only about our company’s carbon footprint, but also the ethical and educational impact we leave for our employees, neighbors, and children to carry into the future. Once again, this is why SMI exists — to provide education and information to our industry that enables us to operate our businesses, educate our employees and positively impact our communities.
God Bless and Have a Crazy Good Day!
Gene Huber Jr.SMI Executive Committee
President: Gene Huber Jr., Winamac Coil Spring
Vice President: Don Jacobson III, Newcomb Spring
Secretary/Treasurer: David DeVoe, Plymouth Spring
Past President: Bert Goering, Precision Coil Spring
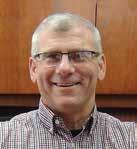
At-Large: Dave Deerwester, The Yost Superior Co.
Executive Director: Gary McCoy, SMI
SMI Board of Directors
Kelley Christy, Diamond Wire Spring • Joe Devany, Betts Company • Linda Froehlich, Ace Wire Spring & Form • Adam Jacobson, FENN/Torin • Don Lyons, JonSpring
• Alex Melnikow, Midstate Spring • Tony Pesaresi, Winamac Coil Spring • Keith Porter Jr., Newcomb Spring • Tim Zwit, Motion Dynamics Corporation
Springs Magazine Staff
Gary McCoy, Executive Director/Advertising Sales, gary@smihq.org
Phil Sasso, Managing Editor, phil.springs@sassomarketing.com
Gabriela Carrasco, Associate Editor, gaby@smihq.org
Lisa Plefka Haskin, Art Director, lisahaskin95@gmail.com
Communications Committee
Chair, Keith Porter Jr., Newcomb Spring • Reb Banas, Stanley Spring & Stamping • Hale Foote, Scandic Springs, Inc. •
Patrick Gillum, Gilco Spring of Florida, Inc. • Adam Jacobson, FENN/Torin • Lucas Karabin, Acme Monaco • Gary McCoy, SMI • Phil Sasso, SMI • Michael Shapiro, Gibraltar Corporation
• Bill Wynn, Gardner Spring, Inc.
Advertising sales - Japan
Ken Myohdai, Sakura International Inc.
Head Office: 3F,4F, ENDO Sakaisuji Bldg., 1-7-3, Bingomachi, Chuo-Ku, Osaka 541-0051, Japan
Phone: 81-6-6624-3601 • Fax: 81-6-6624-3602
Tokyo Global Office: 5F Kamei No. 2 Bldg., 2-17-13, Kiba, Koto-Ku, Tokyo, 135-0042, Japan
Phone: 81-3-5646-1160 • Fax: 81-3-5646-1161
E-mail: info@sakurain.co.jp
Advertising sales - Taiwan
Charlie Yu, Worldwide Services Co. Ltd.
11F-B, No 540, Sec. 1, Wen Hsin Rd. Taichung, 408 Taiwan
Phone: +886-4-2325-1784 • Fax: +886-4-2325-2967
E-mail: marketing@acw.com.tw

Springs (ISSN 0584-9667) is published quarterly by SMI Business Corp., a subsidiary of the Spring Manufacturers Institute: PO Box 5668, Elgin IL 60121; Phone: 847-450-6848; Web site www.smihq.org. Address all correspondence and editorial materials to this address.
The editors and publishers of Springs disclaim all warranties, express or implied, with respect to advertising and editorial content, and with respect to all manufacturing errors, defects or omissions made in connection with advertising or editorial material submitted for publication.
The editors and publishers of Springs disclaim all liability for special or consequential damages resulting from errors, defects or omissions in the manufacturing of this publication, any submission of advertising, editorial or other material for publication in Springs shall constitute an agreement with and acceptance of such limited liability.
The editors and publishers of Springs assume no responsibility for the opinions or facts in signed articles, except to the extent of expressing the view, by the fact of publication, that the subject treated is one which merits attention.
Do not reproduce without written permission.
Cover designed by Lisa Plefka Haskin utilizing Shutterstock imagery.
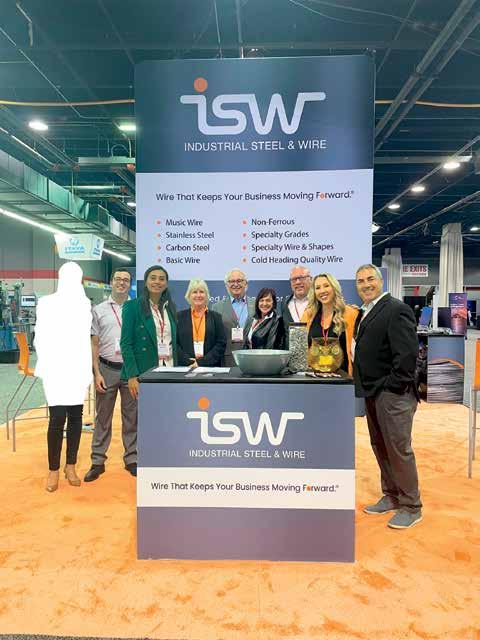
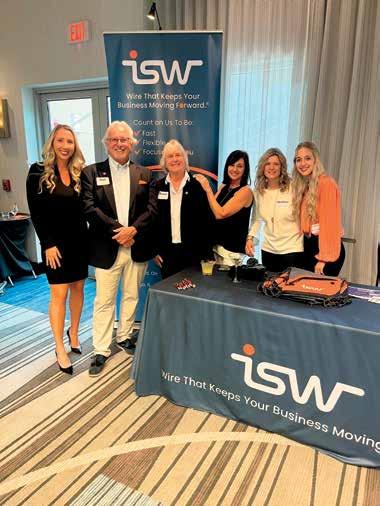
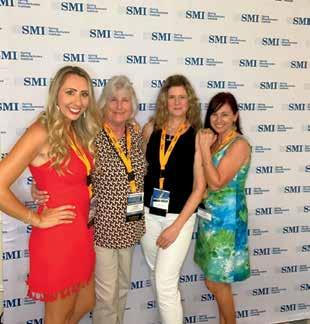
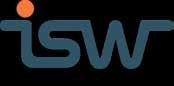
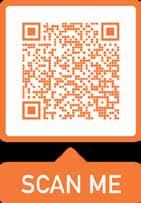
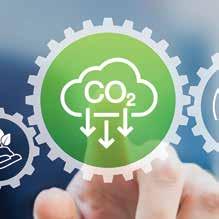
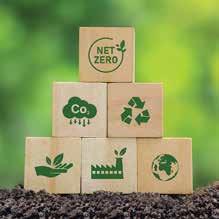
OUR CSX 20 AND HCA 30 MACHINES GIVE YOU STRENGTH IN NUMBERS—not only because of their efficient capabilities—but also for the value you can acquire at an affordable price. Herdon state-of-the-art machines accommodate your budget and a wide range of wire sizes, so you can reduce set-up time and increase your overall productivity, creating the ideal solution for your bottom line.
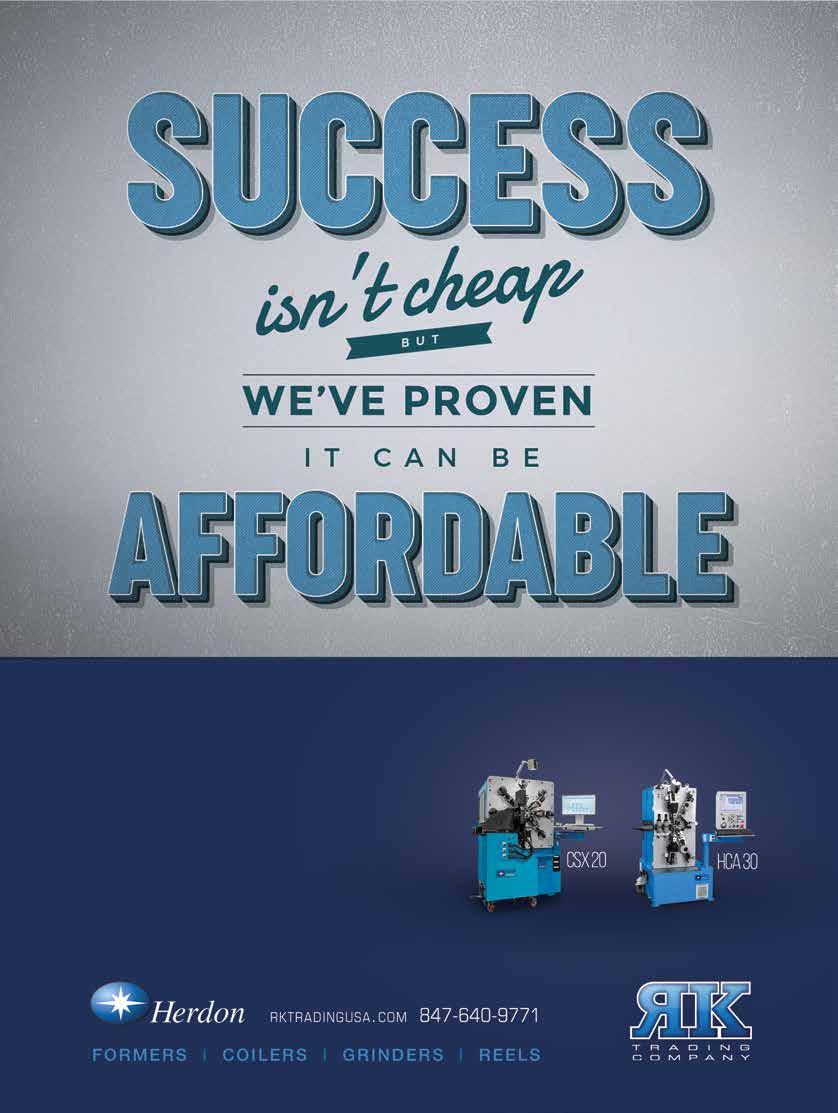
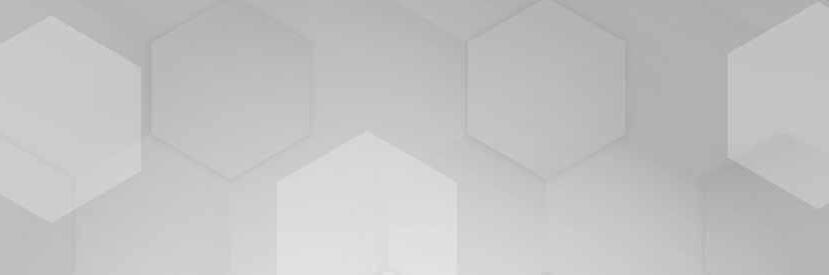
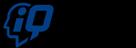




North America
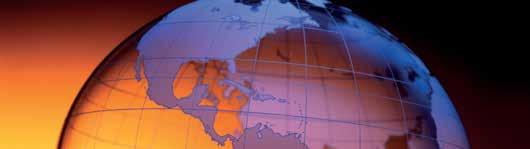
Stanley Spring and Stamping, a custom metal parts and springs supplier based in Chicago, has acquired Rich Industries and Alagor Industries in Bensenville, Illinois. The acquisition strengthens Stanley Spring and Stamping’s spring coiling and stamping capabilities by incorporating Rich Industries’ expertise.
The two companies are a strategic fit, said Reb Banas, president of Stanley Spring and Stamping, citing Rich Industries shared commitment to quality parts, customer service and timely delivery.
The L.S. Starrett Company, a leading global manufacturer of precision measuring tools, gages and metrology systems, has promoted Michael Connor to sales and marketing director for industrial products in North America.
Connor joined Starrett in March 2020, managing the company’s portfolio of strategic accounts. He previously held a sales management position with Starrett from 2002 to 2006. Connor’s extensive sales and marketing experience includes managing industrial, construction, and retail distribution channels in North America.
Before joining Starrett, he directed sales and marketing efforts at a diamond tool company and a New England supply company. Connor also spent a decade with Apex Tool Group, formerly Danaher Tool Group

Stanley Spring’s 85,000 sq. ft. facility in Chicago will take over product delivery for existing Rich Industries customers.
Rich Industries, founded in 1980, specializes in supplying automotive, electrical, HVAC and medical sectors with springs, fourslide, multislide, stampings and flat springs.
NSL Analytical Services recently announced that Dr. Edward Herderick has joined the materials and analytical testing company as vice president of science and technology development. Dr. Herderick is a leading expert in additive manufacturing, advanced ceramics, and materials characterization and will be focused on expanding NSL’s marketleading testing capabilities.
A 17-year veteran in materials evaluation and development, Dr. Herderick has extensive experience in testing and implementing complex manufacturing technology solutions for clients in the aerospace, power generation, transportation, healthcare, and other diversified industrial sectors.
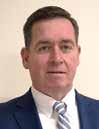
Dr. Herderick’s hiring comes as NSL, a portfolio company of May River Capital, continues to invest heavily in leadingedge materials and analytical testing capabilities. The firm recently added new LC MS-MS, stress rupture, and elevated temperature testing capabilities, with additional testing services scheduled for rollout later in 2023.
Lesjöfors, a group of almost 40 manufacturing and sales companies within multiple countries, has signed an agreement to acquire the shares in U.S. spring manufacturer Tollman Spring Company Inc. With the recent acquisitions of John Evans’ Sons and Plymouth Spring, this transaction further strengthens Lesjöfors’ presence in the U.S.
Tollman, founded in 1945 and located in Bristol, Connecticut, manufactures industrial springs with a diversified customer base of more than 500 customers in the industrial, electrical, defense and firearms, and automotive markets.
Like Lesjöfors, Tollman has longstanding customer relationships, high technical expertise, and a strong emphasis on tailored solutions. This acquisition enables other opportunities for profitable growth, such as purchasing coordination, cross-selling, as well as resource and knowledge sharing with Lesjöfors’ other U.S. companies.
After the transaction, Tollman’s current owners, Rick Zink, Tim Dudzinski and Lisa Barnes, will remain operational during a transition period. The current plant manager, Matt Zink, will be promoted to CEO and continue to develop the business. In line with Lesjöfors’ decentralized organization, the company will continue to operate under its own brand and management.
In 2022, reshoring and foreign direct investment (FDI) manufacturing jobs increased by more than 360,000 positions, a 53% increase over the 2021 record, according to a report by Reshoring
International
In collaboration with performance EV maker, Polestar, Lesjöfors, has developed suspension springs for the limited-edition Polestar 2 BST edition 270. Lesjöfors’
Initiative, a non-profit reshoring advocacy group. This growth is driven largely by concerns over supply chain resilience and the rising cost of offshoring.
The top industry sectors included electrical equipment, appliances and components, computer and electronic products, chemicals and transportation equipment, accounting for 87% of all new reshoring jobs. The five leading states for
reshoring and FDI were New York, Ohio, Georgia, Tennessee and North Carolina.
U.S. companies cited their top five reasons for reshoring and FDI as government incentives, skilled workforce availability/training, supply chain interruption, proximity to customers/market and eco-system synergies.
The full report is available for free download at bit.ly/RIData2022.

Messe Düsseldorf enters the Mexican market with the launch of the Wire Mexico pavilion at Expo Manufactura in Monterrey, Mexico, Jan. 30–Feb. 1, 2024. The pavilion is designed to meet the increasing demand for cables and wires in the Mexican automotive, electronics, and energy industries.
Founded in 1996, Expo Manufactura is the leading trade show for many Mexican manufacturing segments. In February 2023, the show attracted more than 15,500 visitors from 26 countries.
custom springs are designed to push the boundaries of electric performance.
The project involved establishing a live workshop in Lesjöfors’ factory in Sweden, where suspension spring designs were manufactured, mounted and tested on the roads surrounding the facility. The collaboration between Polestar and Lesjöfors engineers created suspension springs finely tuned to deliver the desired level of quality and performance.
Joakim Rydholm, head of chassis development at Polestar, praised
Alloy Wire International has made its seventh charitable donation through its “Wired for Good” campaign. The company, a U.K. manufacturer of round, flat and profile wire, has provided £5,000 ($6,310) to Sands, a charity committed to saving babies’ lives and supporting bereaved parents.
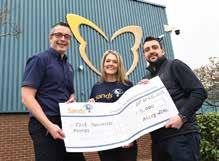
Alloy Wire International’s Wired for Good campaign aims to donate funds to local community groups and charities. This brings the company’s total donations to £35,000 ($44,175).
Several workers requested a donation to Sands. The charity will use the financial assistance to support its work, including operating costs of its free helpline, faceto-face bereavement support groups and research that will save more babies’ lives.
“There are a lot of parents at AWI, and we never want to imagine the thought
Lesjöfors’ unique service and deep understanding of spring precision. He highlighted the hand-crafted nature of the springs tailored specifically for the Polestar 2 BST edition 270. Olof Jonsson, Lesjöfors sales manager, expressed pride in delivering on the exceptional project within the given timeline.
The success of the collaboration has led to a new development, Polestar 2 owners can now order a lowering kit, complete with Lesjöfors suspension springs, for both the vehicle front and rear.
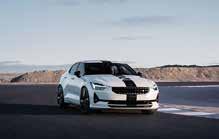
of coming to terms with losing any of our children,” said Adam Shaw, financial director of Alloy Wire International.
Sands helps anyone affected by pregnancy loss or the death of a baby, with 91,500 people helped through its bereavement support services in 2022 alone. n


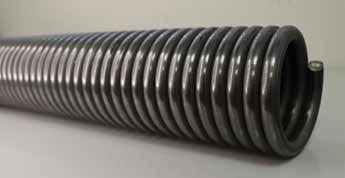
Regional Spring Association Report
CASMI Report
CASMI and SMI Host Joint SpringWorld Expo and Symposium in 2024
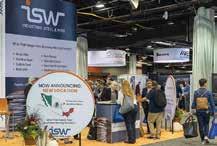
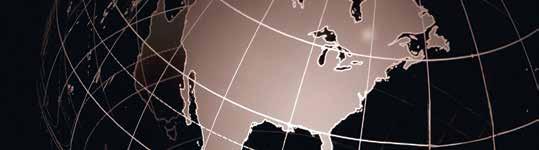
The Chicago Association of Spring Manufacturers, Inc. (CASMI) and
Spring Manufacturers Institute (SMI) have announced a combined trade show starting in 2024.
Tony Pesaresi, CASMI past president and Gene Huber Jr., SMI president, announced the new SpringWorld Expo and Symposium will be held Oct. 2-4, 2024, at the Donald E. Stephens Convention Center in Rosemont, Ill.
In addition to the joint exhibit hall, SMI will host its popular symposium featuring 24 educational sessions.
Upcoming Events
An Evening at the Ballpark
CASMI will host its 2023 installment of An Evening at the Ballpark at the home of the Chicago Dogs, Impact Field, Rosemont, Ill., Aug. 17, 2023.
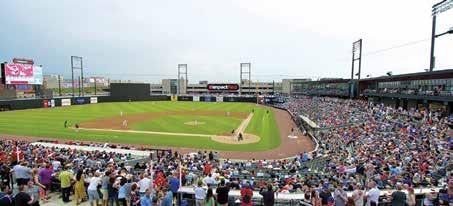
An Evening at the Ballpark, launched in 2018, provides attendees with a game ticket, food and beverage. This annual gathering is a token of appreciation from CASMI to associate members and SpringWorld exhibitors for their support.
For details and registration, visit casmi-springworld.org/event/ ballpark23.
The Chicago Dogs are a member of the American Association of Independent Professional Baseball (AAIPB), the largest and most successful independent baseball minor league in the United States.
To learn more about the Chicago Dogs and Impact Field, visit thechicagodogs.com.
SpringWorld Kickoff Dinner
CASMI members, SpringWorld exhibitors and suppliers committed to or considering exhibiting are invited to the SpringWorld Expo and Symposium
Connect With CASMI
The Chicago Association of Spring Manufacturers (CASMI) is now available on Facebook and LinkedIn. Like and follow our pages below for up-to-date information and events.
Facebook: www.facebook.com/profile. php?id=100090082190759

LinkedIn: www.linkedin.com/ company/90511236/admin/

2024 Kickoff Dinner at Cooper’s Hawk in Orland Park, Ill., Oct. 19, 2023. The event will feature an update on SpringWorld Expo and Symposium 2024, exhibit space registration, networking, and a dynamic speaker.
The speaker, JM Ryerson, has built and exited two successful companies that have provided him with personal and financial freedom. His “Let’s Go Win” process has allowed Ryerson to become the leader he is today, giving his companies the foundation and tools to propel them to success.
Ryerson also helps high-performing leaders define and execute their leadership styles to grow the impact and profits of their businesses. His “Show Up As You” system encourages leaders to inspire ambition and confidence in their teams, driving them to next-level success individually and collectively.
For event information, visit www.casmi-springworld.org/event/ SW2024KickoffDinner.
For more about Ryerson, visit letsgowin.com.
NESMA Report
By Lucas Karabin, Acme Monaco, NESMA PresidentNESMA entered the second quarter with much work to accomplish. We started by facilitating a listening tour with Connecticut’s Chief Manufacturing Officer, Paul Lavoie, who serves at the will of the governor. He has been visiting members focusing on manufacturers’ needs and the resources available to assist manufacturers. Connecticut has more than 4,000 manufacturing companies. Similar initiatives are taking place in surrounding states. One major initiative has focused on high school robotics programs. Another initiative, Connex Marketplace, is a domestic sourcing program where companies can identify vendors.
NESMA’s Vanguard group, led by board member Jake Youman, held a networking event on March 1. At the event, members enjoyed food, drink, and raffles sponsored by FENN/Torin, Marion Manufacturing, Acme Monaco and Plastonics. Our next event was the annual Hartford Yard Goats minor league baseball game at Dunkin Park May 17.
NESMA 2023 Scholarship Winners
NESMA and the Main Street Community Foundation have jointly established two scholarships to support education in the spring and stamping industry. The 2023 recipients are Julianne Rasten and Emily Seeds.
Rasten, a graduating senior from Southington High School, will pursue mechanical engineering.
Seeds, a sophomore at the University of Saint Joseph, is studying English and secondary education.
The Scholarship committee, led by NESMA board member Charlie Radcliff, had their work cut out for them this year with an outstanding number of applicants.
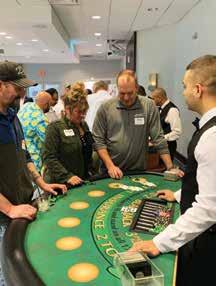

The committee was pleased with the number and quality of applicants this year. New applications increased.
Due to member generosity, NESMA increased the level of giving to $2,500 each for our two scholarships.
We value each applicant’s commitment to higher education and wish them much professional success. We want to thank Scholarship Committee Chairperson Charlie Radcliff and the scholarship committee for their continued efforts to raise awareness of our commitment.
If you have scholarship questions, please contact Samantha Rajotte at Main Street Foundation (samantha@ mainstreetfoundation.org).
In Other News
NESMA’s Technical committee has been hard at work identifying paths to bring our technical education to young people. Board member Al Mangels our technical development chairperson has taken steps to introduce students to SMI curriculum. We are seeking students for pilot runs for future SMI programs. NESMA is continuing its effort to procure floor space in Tunxis Community College’s Manufacturing Center (read more about the facility on page 51) located at 21 Spring Lane, Farmington, Connecticut. This is an existing building being retrofitted for classrooms and hands-on training on
various production equipment. It will facilitate a new pathway for job seekers in the spring industry.
The NESMA membership and board are very happy to welcome new board member Markus Arnold. Marcus will bring a high degree of industry knowledge as president of WAFIOS America. WAFIOS has a U.S. facility in Branford, Connecticut. WAFIOS has previously participated in NESMA events such as webinars for students demonstrating machine capabilities from their facilities in both the U.S. and Germany. Our organization will benefit from Markus’ wide ranging spring manufacturing expertise.
NESMA celebrated its Expo and Casino night March 23. The event drew nearly 150 participants. Key event sponsors included Amstek Metal, FENN, LLC, Gibbs Interwire, Industrial Steel and Wire, Radcliff Wire, Inc., Spring Manufacturers Supply Company, Thomaston Savings Bank and WAFIOS. The event is initially focused on tabletop expo suppliers. We then had professional card dealers bring in gambling tables and had “funny money” distributed to attendees.
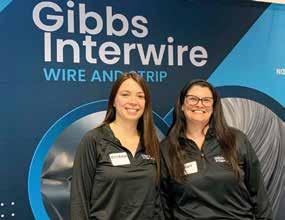
Attendees could turn in their winnings for raffle tickets. Exhibitors included Solar Atmospheres, Radcliff Wire, Gibbs Interwire, FENN, LLC, Amstek Metal, JN Machinery, Plastonics, Thomaston Savings Bank, North American Spring Tool, Ulbrich Stainless Steel, SMSC Northeast Carbide, Rolled Metal Products, Raajratna Stainless Steel, SMI, Triatic, Traver IDC,WAFIOS, ERA Wire, ISW and Architectural Building Services.
This evening was bittersweet, mixing in a retirement party for two pioneering women who have helped shape NESMA. One was Lynne Carr who recently retired as SMI executive director after 28 years. She was joined by incoming executive director Gary McCoy, along with close friends. Also retiring shortly is long-time NESMA advocate and administrative liaison Cindy Bombard from the Central Connecticut Chambers of Commerce. Lynne and Cindy were introduced by current and former board members and shared parting messages. NESMA is stronger for their commitment to our trade.
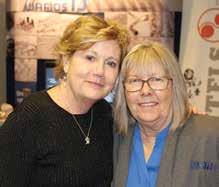
WCSMA Announces Fall Golf Outing
The West Coast Spring Manufacturers Association (WCSMA) will hold its annual Fall Golf Outing Thursday, Nov. 9, 2023, at Coyote Hills Country Club in Fullerton, California.
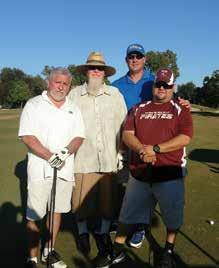
The WCSMA invites you to experience one of the premier golf facilities in greater Los Angeles for a relaxing round and to reacquaint yourself with fellow springmakers, associate members, and guests in this annual competition.
The event is open to all WCSMA members and their guests. Golfers will play a best-ball tournament, followed by a cocktail hour and dinner. There will
also be a raffle with prizes donated by WCSMA sponsors.
Registration is $245 per person for golf and dinner, $95 per person for dinner only, and $150 per person for golf only. Early bird rates end Nov. 1.
To register, contact Mark Tiedeman, WCSMA treasurer at 800-262-6266 or email mark@tru-form.com, For more information or sponsorship opportunities, contact Debra Kolodge at debra@ ftrmetalproducts.com or 562-945-7504. For more information on WCSMA, visit wcsma.website. n
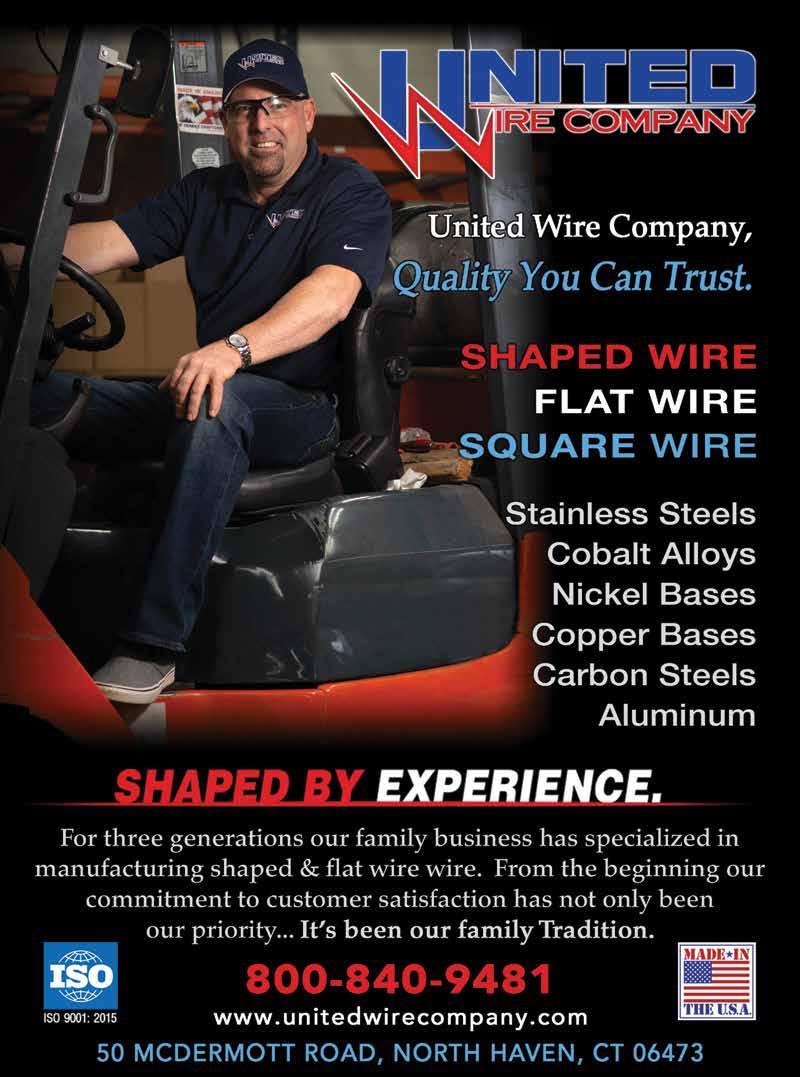

Bridging Workplace Safety and Sustainability
By Laura Helmrich-Rhodes, CSP, Ed.D.
The intersection of occupational safety and carbon footprint reduction may not be obvious to some. However, it is evident to those who have observed the transformation of employer obligations for worker and product safety into environmental obligations over the past three decades. Academic programs have evolved from “safety sciences” to encompass “environmental engineering” and “environmental, safety and health” (ESH) degrees.
In the workplace, most full-time safety professionals now have more environmental responsibilities. This intersection focuses on promoting sustainable and safe working environments, minimizing the environmental impact of work activities, and ensuring the safety and health of workers. The concept of sustainability extends beyond the actions taken to how they are carried out.
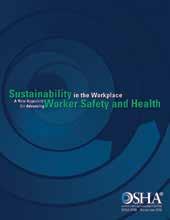
EHS professionals help reduce the carbon footprint by advocating for energy-efficient equipment, implementing recycling programs and minimizing the use of hazardous chemicals. As safety professionals become more involved in ensuring product quality and addressing environmental concerns, their additional duties positively impact worker safety and health by reducing exposure to harmful substances and minimizing the risk of accidents.
Another notable change is the increased use of the term “sustainable” in business. While it used to deal with practical issues like structural integrity or maintenance schedules, it is now featured prominently in studies, books, classes and policies. Sustainability involves not only the work being done but also how it is done, aiming to reduce environmental impact while maximizing profitability.
Two areas worth monitoring are the proposed changes to 29 CFR 1910.1200, the Occupational Safety and Health Administration (OSHA) Hazard Communication Standard, and the
Laura Helmrich-Rhodes, CSP, Ed.D., is a regulatory compliance consultant to the Spring Manufacturers Institute (SMI). A former member of PA/OSHA Consultation, she is an associate professor in the Safety Sciences Department at Indiana University of Pennsylvania where she teaches graduate and undergraduate classes on topics such as OSHA standards, safety communications, workers’ compensation and human relations. Rhodes is available for safety advice and information. Contact SMI at 847-450-6848 or laurahrhodes@gmail.com.
ongoing interest of the International Organization for Standardization (ISO) in product quality and sustainability beyond the 9000 and 14000 series. Although the topic is broad, we’ll focus on how to reduce your company’s carbon footprint from the safety professionals’ perspective.
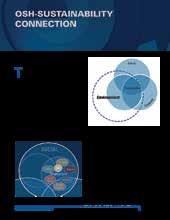
Efforts to Align Hazardous Chemicals
The recent alignment of OSHA’s Hazard Communication Standard (HCS) with the Globally Harmonized System of Classification and Labeling of Chemicals (GHS) provides a coherent approach to classifying chemicals and communicating hazard information. This update reduces trade barriers, enhances productivity for American businesses dealing with hazardous chemicals, and generates cost savings by simplifying safety data sheets and labels.
OSHA proposes further changes to the HCS to conform with the United Nations GHS (revision 7), align specific provisions with Canada and other U.S. agencies, and address emerging issues since the 2012 standard’s implementation. Readers should pay attention to proposed changes in chemical classifications, including the term “evergreen” in the standard, and revisions to information dissemination (specifically, employee training obligations). Meanwhile, it is essential to ensure compliance with the basic elements of the HCS to inform employees and avoid OSHA citations. Refer to the “Haz Com Program Checklist” at the end of this article for a quick assessment of your program’s adherence.
Sustainability in the Spotlight
Despite OSHA’s primary focus on worker protection, the agency also recognizes the importance of sustainability. Organizations
can showcase their environmental efforts on OSHA’s website, sharing informative and inspiring stories such as successful recycling initiatives. Launched in 2011, the Center for Safety & Health Sustainability, a collaboration of professional organizations in the U.S., Canada and the U.K., emphasizes that sustainable organizations must also have safe and healthy conditions for workers and contractors. The Sustainability Spotlight profiles practices, policies, research, partnerships, and case studies that demonstrate the impact of worker safety and health on sustainability strategies. Reviewing these profiles can provide insights into waste reduction and carbon footprint mitigation strategies. Check the provided link under “Helpful Resources” to access these company highlights.
ISO standards have shaped academic safety sciences programs. Since the launch of ISO 14000 (Environmental Management Systems) in 1996, safety managers have assumed greater responsibilities, in addition to previous ISO 9000 (Quality Management) responsibilities. This trend has led to job titles like EHSQ (Environmental Health, Safety and Quality), creating a demand for changes to relevant university coursework that reflect current workforce needs
Employers in the spring industry that focus on occupational safety can directly or indirectly reduce carbon emissions by creating safety and quality management policies and procedures. Safe workplaces help prevent accidents and incidents that can cause environmental damage and contribute to each company’s carbon footprint. Also, involving EHSQ professionals in decision-making enhances sustainability efforts. By managing occupational safety and reducing carbon footprint, springmakers can create healthier, safer, and more sustainable workplaces while making exceptional products. n
Helpful Resources
Key (proposed) Changes to the Hazard Communication Standard
www.osha.gov/sites/default/files/HCS%20Update_
January%202021.pdf
OSHA Sustainability in the Workplace
www.osha.gov/sustainability/sustainability-connection
Hazard Communication Standards Compliance “Check Up”
1. Current chemical inventory of hazardous chemicals
2. Safety Data Sheets (SDS) accessible to all employees (and temps) matching each chemical listed on the inventory.
3. Globally Harmonized System (GHS compliant labels on all hazardous chemicals
4. Proper containers for all hazardous chemicals
5. Segregated eating and drinking areas with handwashing away from hazardous chemicals.
6. Documented employee training completed on the standard, the hazards of the chemicals, and their rights under the Hazard Communication standard.
7. Documented agreements to assure all temporary employees and contractors have been properly trained.
Sustainability Spotlight
www.osha.gov/sustainability/spotlight
Picking the Right Quality Management System for Your Organization
www.safetyandhealthmagazine.com/articles/ 19996-picking-the-right-qms-for-your-organization
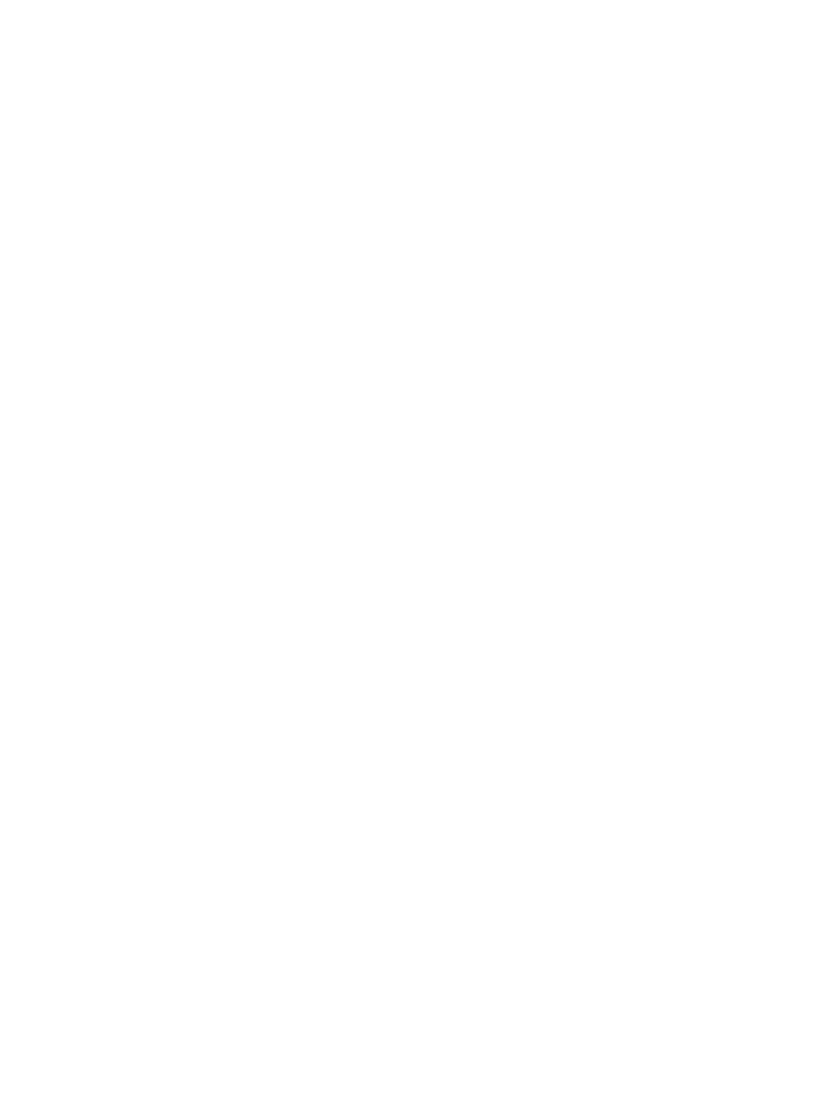
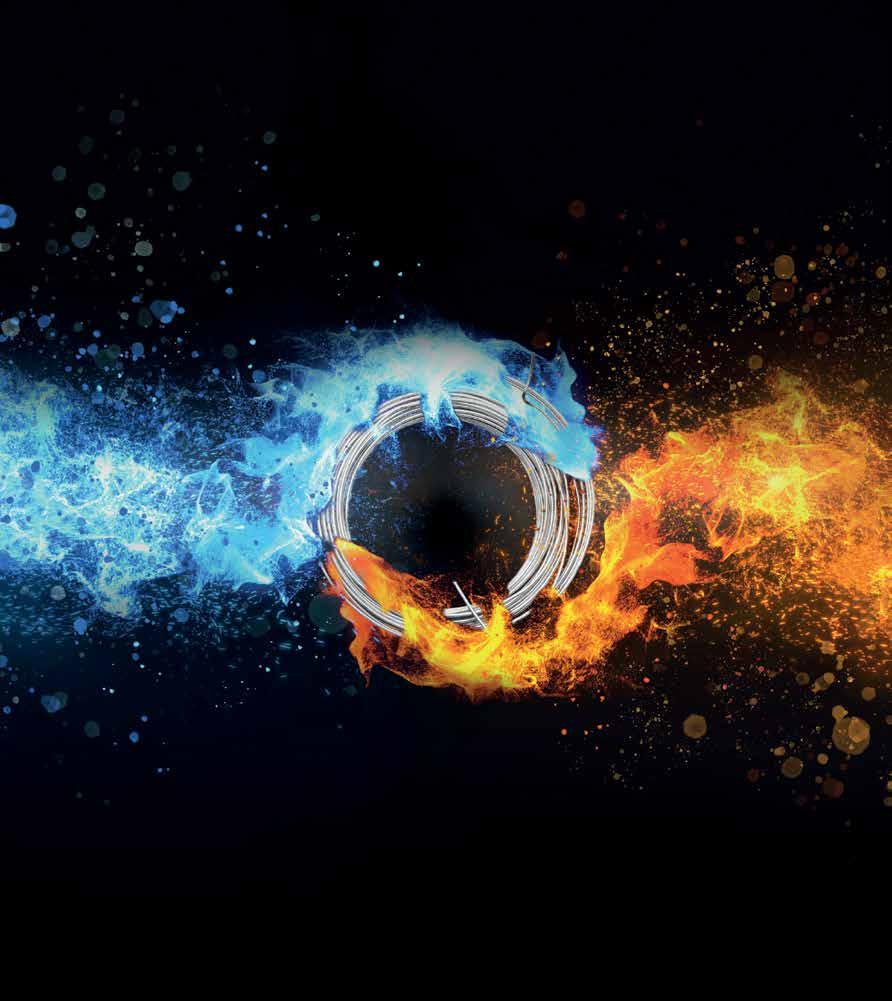
Working for Difficult People
By Dan SebastianOver my nearly 44 years in the world of springs, I had the opportunity to work for teachers, mentors and difficult people. I started at a research and development center where I encountered some of the smartest people in the spring world. I was a junior to all, but they treated me with respect and mentored me in the science of springs and the world of business; the good, the bad and the ugly. It was like being in a monastery but it would soon change.
I was sent to the Midwest to work at what appeared to be a sleepy division. What followed was a series of supervisors who did not like me because I was from the corporate office, they feared me because of my education and tried to use me for their own advancement. After a while, I learned how to get through the minefield of corporate politics but nothing prepared me for what was about to happen.
A new manager arrived who came from the high-profile automotive world. He was a yeller who “never” made a mistake. Everything that did not go as planned was someone else’s fault. He seemed to delight in displaying his frustrations by humiliating people in public settings. He had goals and always kept things moving to reach them — even at others’ expense. His biggest fault was he could not gain the respect of the workforce. Despite his irrational behavior, or perhaps because of it, I was soon put in charge of all manufacturing (the number two spot in the division).
Fortunately, when I got to the factory to oversee manufacturing, I sat the supervisory team down and explained that I came from the world of engineering and quality and would need their help if we were going to succeed. We needed to succeed, even if we did not like the guy in the corner office. I worked hard to be a member of the manufacturing team. The people in the plant seemed to speak a different language than I was used to.
After hours of hard work, I was able to find a way to become fluent in the language of the factory and learned to translate it into management objectives. The team performance was outstanding which made my work easy. I was very proud of their accomplishments.
The team's relentless pursuit of excellence allowed the harddriving, take-no-prisoners manager to get promoted back to the world of automotive. I was promoted to replace that difficult manager, but it was the team that made it possible.
In 1987, Robert M Hochheiser wrote a book titled, “How to Work for a Jerk: Your Success is the Best Revenge.” It made me appreciate all the different supervisors I had encountered and the importance of understanding all the different languages in any plant.
Summary:
There are many lessons you can learn from your supervisors. They can be teachers, mentors, confidants — or even jerks, but there is always something you can learn from them. It is essential that you “speak the same language.” You need to incorporate the good, avoid the bad, and always keep in mind that people are watching you for lessons. So do the right thing. n
Dan Sebastian is a former SMI president. He holds a degree in metallurgical engineering from Lehigh University and his industry career spans more than four decades in various technical and management roles. He may be reached by contacting SMI at 847-450-6848.
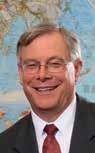
There are many lessons you can learn from your supervisors. They can be teachers, mentors, confidants — or even jerks, but there is always something you can learn from them.
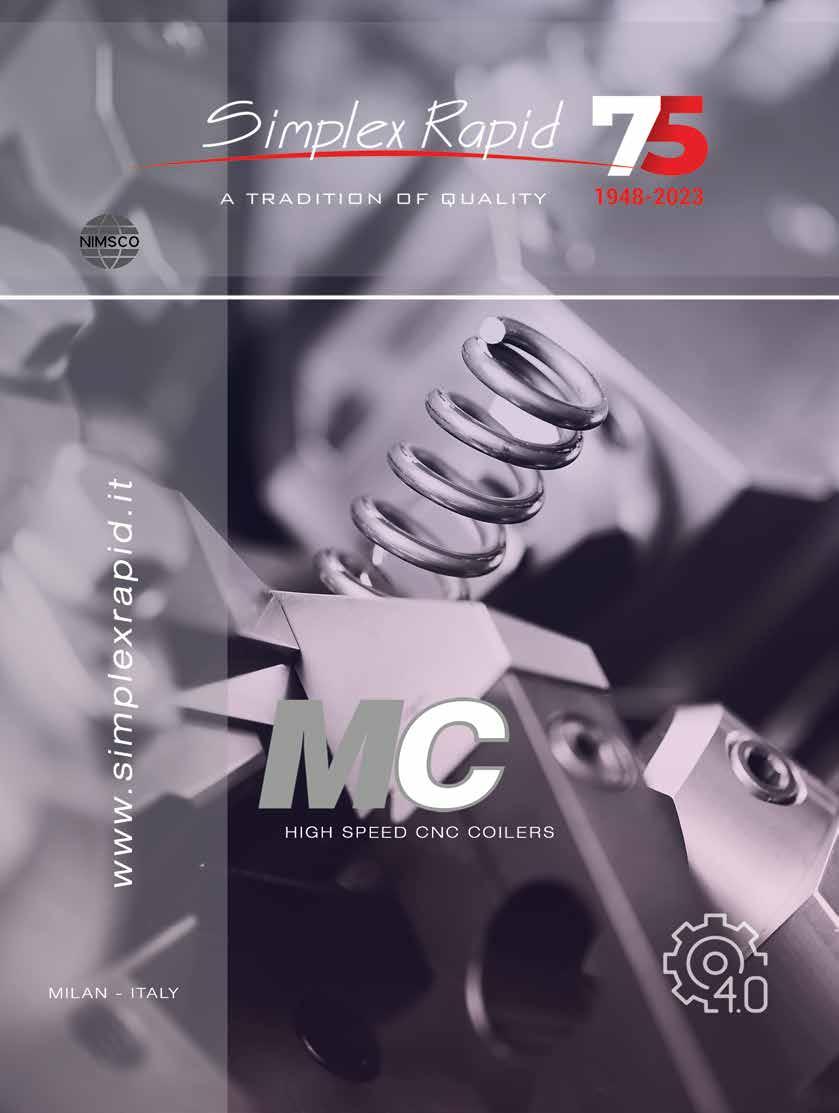
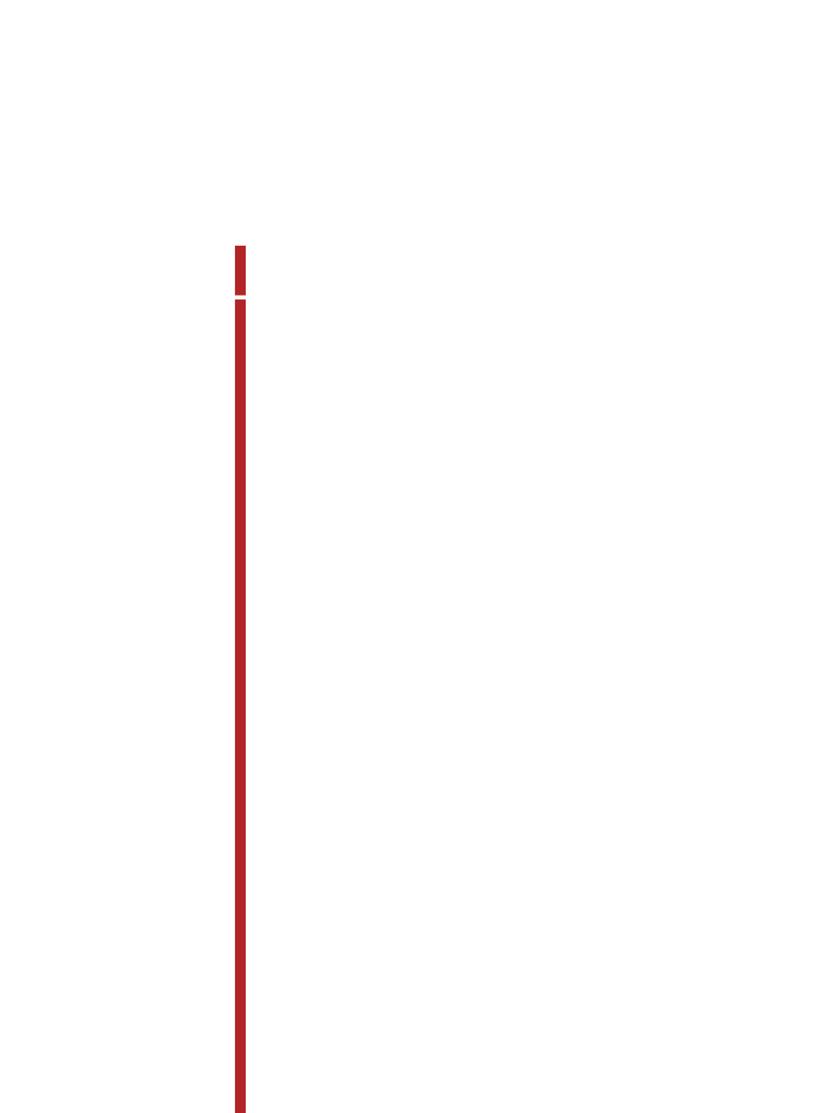
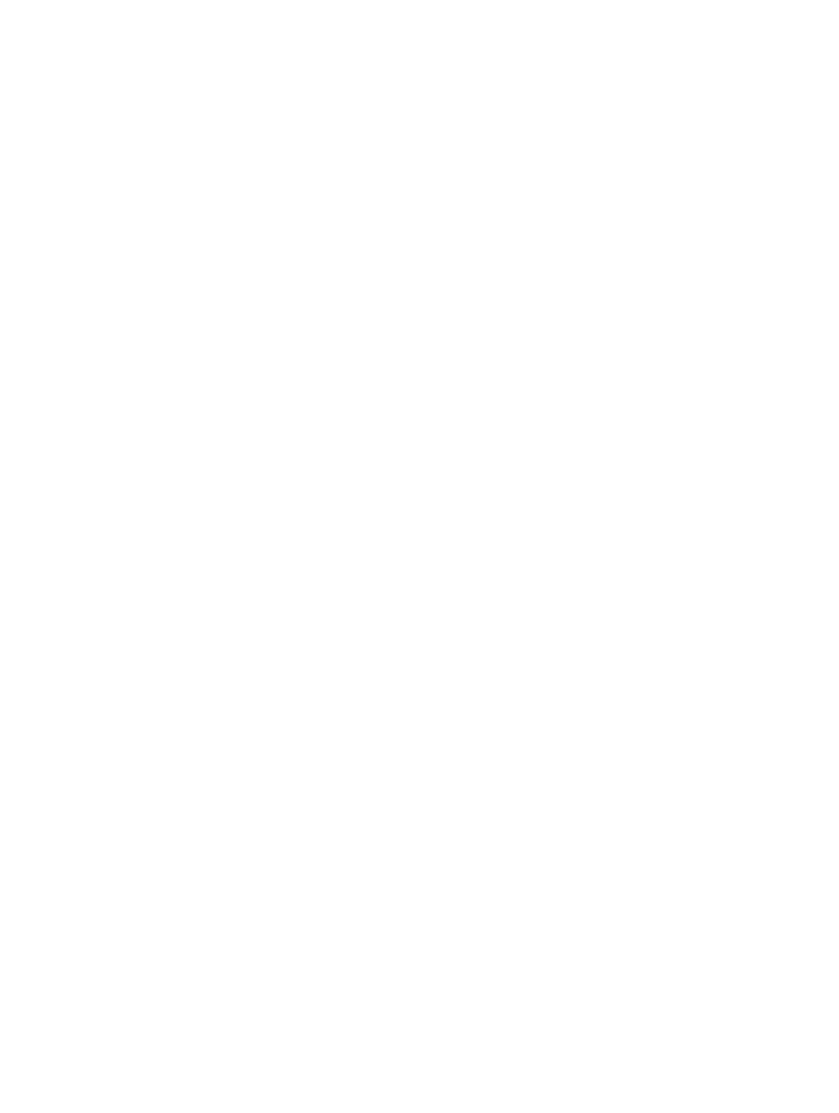
Rust and Fatigue
By C. Richard GordonSpringmakers sometimes encounter situations where springs are reported to have failed in service with multiple fractures reported in an individual spring. The objective of this article is to review some historical work suggesting rust as a possible root cause.
In the summer 2021 issue of Springs magazine1, fatigue testing of round wire was discussed as part of a series of articles regarding mechanical and technological tests for springmaking materials.
Fatigue is the fracture of a metal by cyclic stressing or straining2. A fatigue fracture generally occurs in three stages: 1) crack initiation, 2) crack propagation and 3) catastrophic fracture of the remaining cross-section. As we teach in the 301 Springs — Fatigue spring design class, a key to improving fatigue life in springs is the minimization of surface and sub-surface imperfections that can lead to crack initiation.
The rotating bending fatigue test is one of the most efficient methods used to determine the high cycle fatigue strength of wire samples. One of the two test methods discussed in the summer 2021 article was the Kenyon rotating bending fatigue test. With this test, a bending strain is imposed on a wire sample, and the sample is rotated, while remaining in the bending plane. Testing is done to establish the fatigue limit or endurance limit of materials. Fatigue testing is important to springmakers as historical work has shown that the fatigue performance of wire is well correlated with spring fatigue performance3.
John Kenyon obtained a patent (US Patent 2,170,6404) in 1939 for the rotating arc fatigue test.
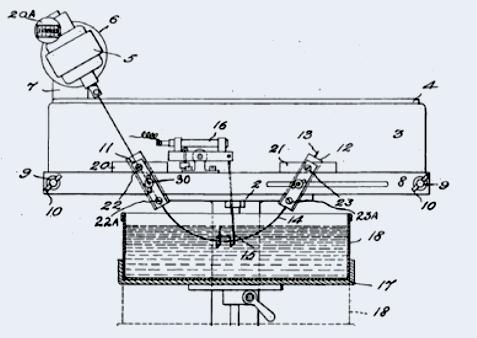
As discussed in 20211, Figure 1 is a schematic of the testing unit from the Kenyon patent. The wire is bent in an arc less than 180 degrees and fixed so one end is free to move at a tangent to the holding device. The wire sample will assume the arc of a circle. The sample is rotated using a constant rpm motor. Thus, the stress in the wire goes from compressive to tensile as the wire is rotated and the mean stress is zero, as shown in Figure 2.
Figure 3 shows wires in the test unit demonstrating a higherstressed sample and a lower-stressed sample. Approximately 15 inches of wire undergoes uniform stressing in this test, which is a relatively large sample test length. The liquid in the tank (Figure 1) is usually oil used to dampen vibration. Two test fixtures can be inserted in one tank. Different liquids can be used, for example to study corrosion fatigue.
Stress is calculated using the following equation:
S = d*E/(2R)
where:
d = wire diameter (inches)
E = modulus of elasticity (30x106 psi for steel)
R = radius of curvature (inches)
The common size range for this type of unit is 0.035 in. to 0.060 in. (0.89 to 1.5 mm) diameter.
C. Richard (Rick) Gordon is the technical director for SMI. He is available to help SMI members and non-members with metallurgical challenges such as fatigue life, corrosion, material and process-related problems. He is also available to help manage and oversee processes related to failure analysis. This includes sourcing reputable testing labs throughout North America, forwarding member requests to the appropriate lab and reporting results and recommendations. He can be reached at c.richard.gordon@gmail.com or 574-514-9367.
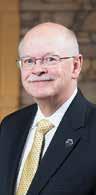
A common testing plan was cited previously1. For reference, a constant rpm motor (3600 rpm) runs 2780 minutes (46.3 hr.) to reach 10,000,000 cycles for a single wire.
Figure 4 shows example data from the Kenyon patent for four materials that show a fatigue limit: Piano wire (sample A), two samples of high carbon wire (samples B and C) and a copper-beryllium wire (sample D)1. The data shown includes the ultimate tensile strength (UTS), fatigue limit (FL) and FL/ UTS ratio for each material.

Additional Kenyon Work
In one additional study5, Kenyon conducted a corrosion fatigue study using 0.037 in. diameter wire in the:

• unplated condition
• bronze (Cu-Zn by displacement) plated condition and
• Cu-Zn (hot dipped zinc + electro plated copper) condition Wires were tested in oil and distilled water. All materials were from the same coil of wire, with the plating being the only difference. All three materials showed similar fatigue curves when tested in oil, indicating no material effect due to the plating condition as shown in Figure 5. However, the distilled water tests showed entirely different behavior with respect to the protective nature of the coatings. The bronze plated material was approximately on par with the unplated wire while the copper zinc plated material was markedly better. The ductility of each wire after corrosion fatigue testing was evaluated by bending. Bending results for the unplated wire showed some ductility with an occasional break when bent around a ¼ in. diameter rod. The copper-zinc plated wire could be bent around a 1/8 in. diameter rod without breakage. The bronze-plated material broke into ½ in. lengths by finger bending.
Kenyon observed that the bronze-plated wire appeared visually bright with pin-like corrosion rust spots. Removal of the plating with ammonia revealed a mottled almost disease-like attack on the steel. The corrosion rust spots were believed to be due to the pinhole imperfections in the plating. Metallographic examination showed practically all corrosion pits had fatigue cracks in various incipient stages of development. Figure 6 shows an example of a photomicrograph through a corrosion pit that was the initiation site for a fatigue crack. Figure 7 shows an SEM micrograph of a corrosion pit on a wire surface that acted as the initiation site for a fatigue crack.
In a subsequent study, Kenyon evaluated music spring wire as received (protected) and after 30 days in an unprotected warehouse storage environment. Some pitting was observed after the 30-day unprotected storage. Fatigue results were similar to the prior study where the unprotected samples showed poorer fatigue performance. Metallography of the lightly pitted areas showed fatigue cracks in various incipient stages of development as shown in the prior work.
Figure 4. Fatigue test results presented in the Kenyon patent4Summary
The work by Kenyon shows us the detrimental impact of rust on carbon steel wires. What may appear to be minor rust spots can have an impact on fatigue performance of wires and springs. Corrosion pits, however so slight, can serve as stress concentrators leading to crack initiation. In the case of pitting, multiple cracks can form and grow. A crack that reaches the critical size results in catastrophic failure. Depending on the stress condition, multiple fractures may be observed. n
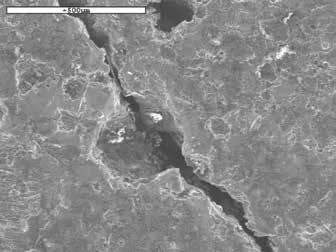
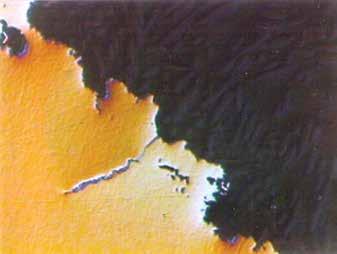
References
1. Gordon, C.R., Types of Tests Used to Characterize Springmaking Materials – Part 6: Fatigue Testing of Wire, Springs, Spring 2021, p.21.
2. Wright, R.N., Wire Technology: Process Engineering and Metallurg y, Elsevier, p150 (2016).
3. ASM Handbook, Vol. 1, Properties and Selection: Irons, Steels, and High-Performance Alloys, 10th edition, ASM International, Materials Park, OH, (1990).
4. Kenyon, J.N., “Fatigue Testing Machine,” US Patent No. 2,170640, Aug. 22, 1939.
5. Kenyon, J.N., “The Service of Plated Steel Wire as Indicated by the Corrosion-Fatigue Test,” Wire and Wire Products, 1943.
SMI has a team of experts, who speak the language of springs, ready to assist you. It could be a metallurgy question about fatigue life or corrosion, or perhaps you need help with a spring design and the use of materials when manufacturing springs. To find out how SMI Technical Services can help you, phone 847-450-6848 or visit bit.ly/springsadvice.
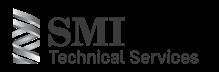
Carbon Footprint in Spring Manufacturing
By Phil SassoIn this issue of Springs , we mesh real-world business stories with technical information about measuring, managing and mitigating your carbon footprint.
There’s a lot of information here, so please consider it a buffet of information. Feel free to pick and choose what’s most interesting and relevant to you.
With the continued buzz about sustainability, customers are increasingly asking springmakers to submit carbon footprint audits.
Customers based overseas and in clean energy sectors, like electric vehicles and renewable energy, seem to be most active in CO2 reporting. Part of the reason may be regulatory and social pressure to set and reach sustainability goals — and your numbers are part of their numbers as you’ll see in our sidebar “Measuring Your Carbon Footprint: Greenhouse Gas Protocol Scopes” on page 27.
You may not be burdened with reporting your emissions yet. But many experts agree carbon reporting will someday become as commonplace as Zoom meetings.
Safety-Sustainability Crossover
In her “Be Aware” column on page 15, SMI’s Laura Helmrich-Rhodes, regulations compliance consultant, explores the connection between workplace safety and sustainability. Safety professionals today, more than ever, play a role in promoting sustainable and safe working environments, reducing environmental impact, and ensuring worker health.
“Since the launch of ISO 14000 (Environmental Management Systems) in 1996, safety managers have assumed greater responsibilities,” she says. “Involving EHSQ (Environmental Health, Safety and Quality) professionals in decision-making enhances sustainability efforts.”
Measurement: Advancing at a Crawl
In “Study: Only 10% of Companies Measure Full Carbon Footprint” on page 26 the Boston Consulting Group found that year-over-year, only 1% more businesses measured their full footprint in 2022 over 2021. And of those measuring their footprint, a significant portion felt their accounting was not entirely accurate.
With few measuring their footprint and inaccurate numbers, why bother?
The BCG article states: “About 64% of respondents who measured the full scope of their emissions and 45% who partially measured them noted a significant reduction in those emissions.” In sum, you can’t manage what you don’t measure.
In our sidebar, “Online Resources for CO2e Accounting” on page 31, you’ll find a list of four sources for carbon calculators and resources to help make recording your greenhouse gas (GHG) emissions easier. BCG notes that companies with automated emissions measurement tools are twice as likely to approach their sustainability goals.
Management: Blazing a New Path
Measuring isn’t the goal. It’s the starting line. “To know better is to do better,” to paraphrase Maya Angelou.
“They want us to be aware of it, and then they want it to be a priority to us,” says Keith Porter of Newcomb Spring in our feature story “Measuring, Managing and Mitigating Your Operation’s Carbon Footprint” on page 28. Once you have the data, you need to drill down to see how you can reduce your carbon footprint.
Likely the largest contributor to your business’ C02 footprint with all your machines, ovens and lighting is electricity. So, a primary goal is to lower your power consumption. As you’ll see, going green can save you some green, too.
Springmakers have found ways to lower power consumption by doing things like retrofitting with servos, replacing bulbs with LEDs, using tax incentives to install solar panels and more.
Speaking of solar, you’ll find “New Renewable Energy Tax Incentives” on page 34, are part of the new Inflation Reduction Act. But beware, the complicated requirements are best navigated with an experienced tax advisor as your guide.
Mitigation: Small Steps, Big Results
Beyond internal changes, there is another way to reduce your CO2 footprint, like UK-based Alloy Wire International has done in “Case Study: Carbon Neutral to Carbon Negative” on page 32. AWI purchased carbon credits to offset its footprint.
If you would like to offset your facility’s footprint, consider buying carbon credits. At the end of our feature story, Christopher Goering, son of SMI’s immediate past president Bert Goering, gives a quick primer on carbon offset, third-party verifiers and the carbon market.
Whatever your position on the controversial topic of climate change, we might all agree that the complicated subject of measuring your carbon footprint can’t be ignored. Especially if someday customers and regulatory officials may request or require this information from you. So, if you stay informed about best practices, set targets, track key metrics and monitor your progress, you’ll be well on your way to driving positive change within your organization. n
Greenhouse Gas Glossary
Here are definitions of some common phrases used in carbon footprint policy and practice.
Carbon dioxide (CO2): A colorless, odorless gas produced by breathing or burning fossil fuel.
Carbon dioxide equivalent (CO2e): A unit of measure of greenhouse gas emissions.
Carbon footprint: Total greenhouse gases released by an individual or organization.
Carbon neutral: Balance between CO2e emissions and carbon offset.
Carbon negative: Removing more carbon dioxide emissions than one produces.
Carbon offset (or carbon credit): Measured reduction in carbon dioxide to compensate for CO2e emissions.
Climate change: Variations in weather patterns attributed to GHG emissions.
Emissions: Release of greenhouse gases.
Fossil fuel: Non-renewable fuels such as coal, oil and natural gas.
Greenhouse gas (GHG): Gases that may contribute to the greenhouse effect: carbon dioxide, methane, nitrous oxide and fluorinated gases.
Greenhouse effect: Heat trapped by the atmosphere, attributed to greenhouse gases.
Mitigate (or climate mitigation): Reduce emissions, increase energy efficiency, adopt sustainable practices or acquire carbon credits to alleviate environmental impact.
Renewable energy: Power from sources such as solar, wind, water and geothermal.
Reforestation: Replanting trees or restoring forests.
Sustainability: Business policies balancing economic, social and environmental impact.
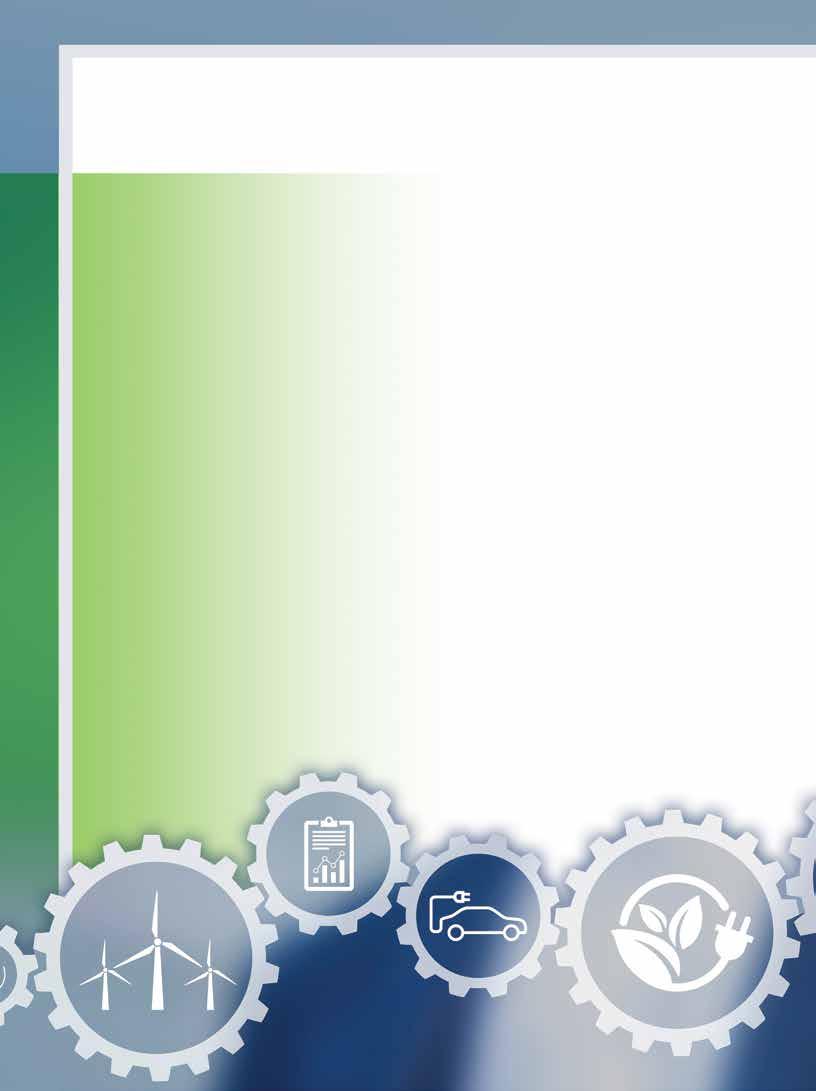
Paris Agreement (or Paris Accord): An international treaty adopted in 2015 under the United Nations Framework Convention on Climate Change (UNFCCC) to address climate change, mitigation and adaptation.
Only 10% of Companies Measure
Manufacturers worldwide are dedicating resources to reduce their carbon footprint and greenhouse gas emissions to benefit the planet and their businesses. Accurate measurement is crucial for identifying and reducing carbon footprints, according to the 2022 CO2 AI by BCG Carbon Emissions Survey. Boston Consulting Group (BCG) developed CO2 AI, an AI-powered solution that organizations from all industries can deploy to quantify current emissions and find solutions to reduce them at scale.
Measurement Adoption is Slow
Although there has been progress, only 1% more companies surveyed comprehensively measured Scope 1, 2, and 3 emissions (see sidebar) year over year — 10% in 2022 vs. 9% in 2021. In addition, respondents estimate a 25% to 30% average error rate in their emissions measurements. While 92% of all emissions are Scope 3 (external), according to the Carbon Disclosure Project (cdp.net), only 12% of organizations consider Scope 3 their top priority.
“These measurements are crucial to helping companies work towards their net-zero goals,” said Charlotte Degot, founder and global leader of CO2 AI by BCG. “And they need be supported by digital tools that help them achieve accuracy and comprehensiveness, which helps decision making for reduction.”
Their Full Carbon Footprint
Measuring Leads to Managing
The better a company measures its emissions, the more effectively it can reduce them. About 64% of respondents who measured the full scope of their emissions and 45% who partially measured them noted a significant reduction in those emissions.
Interestingly, of all sectors studied worldwide, manufacturers were at the forefront of measuring and mitigating their carbon footprint. Meanwhile, insurance, healthcare, nonprofits and the public sector were labeled as “laggards.”
Digital Solutions Create Value
Organizations with automated emissions measurement solutions are 2.2 times more likely to measure emissions comprehensively and 1.9 times more likely to reduce emissions in line with their goals. Aside from monetary savings, businesses rated improved reputation (54%) and attracting top talent (37%) as added benefits.
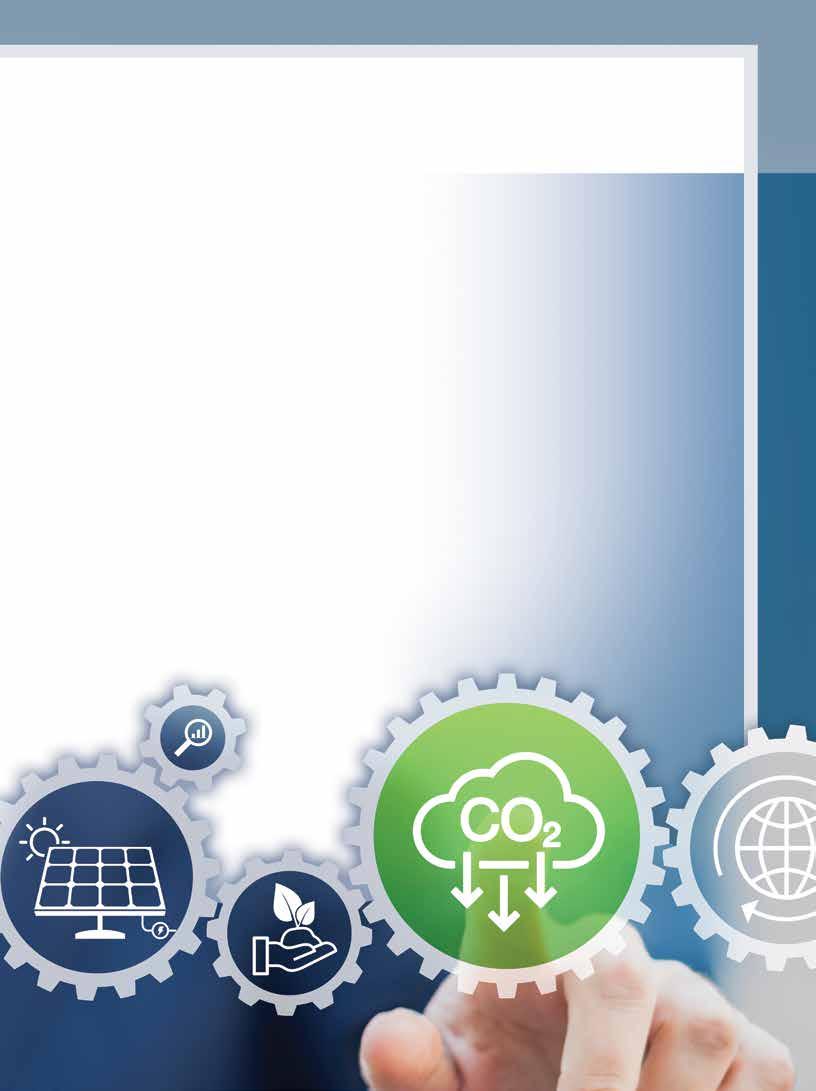
BCG’s Carbon Emissions Survey findings can be downloaded from on.bcg.com/3LAtjYc.
About BCG
Boston Consulting Group (BCG), founded in 1963, partners with leaders in business and society to tackle their most important challenges and capture their greatest opportunities. n
Measuring Your Carbon Footprint: Greenhouse Gas Protocol Scopes
These descriptions are based on GHG Protocol (ghgprotocol.org) standards, the world’s most widely used greenhouse gas accounting standards. By considering all three scopes, an organization can comprehensively understand its carbon footprint and identify opportunities to reduce emissions throughout its operations and value chain.
Scope 1:
Direct emissions from owned or controlled sources.
Examples: On-site fuel burning, company vehicles and processes
Scope 2: Indirect emissions from purchased energy. Examples: Off-site electricity/heat generation
Scope 3: Other indirect emissions in the value chain.
Examples: Purchased goods/services, employee commuting/travel and waste disposal
Measuring, Managing and Mitigating Your Operation’s Carbon Footprint
Measuring your carbon footprint is the first step to reducing it.
“It was brought to us by one of our core customers,” said Keith Porter, general manager at Newcomb Spring Corporation in North Carolina. The customer had given Newcomb several European resources for carbon footprint accounting.
Businesses in the EU are far ahead of those in the United States in measuring and managing their carbon footprint, Porter said. Many springmakers, especially those serving EU-based businesses, are being asked to record and submit quarterly greenhouse gas emissions reports.
Newcomb began measuring its carbon footprint in 2015 using a spreadsheet and formulas it developed based on its client’s input and other sources. Based on this information, they calculated the greenhouse gas (GHG) output of their nine North American facilities.
‘You don’t know what you’re not measuring,” Porter said of beginning to benchmark to understand GHG emissions. ”So, I think the first step is awareness.”
Let’s Get Technical
The Environmental Protection Agency (EPA) lists four greenhouse gas groups: carbon dioxide (CO2), methane (CH4), nitrous oxide (N2O) and fluorinated gases. But standard GHG accounting systems reduce all GHG to the environmental impact of metric tons of carbon dioxide equivalent units or CO2e.
Carbon footprint is the total emissions directly or indirectly produced by an operation. There are three scopes: Scope 1 is direct emissions, Scope 2 is indirect emissions from energy use and Scope 3 is indirect emissions from the supply chain (see “Measuring Your Carbon Footprint: Greenhouse Gas Protocol Scopes,” page 28).
Scientists believe GHG contribute significantly to climate change. At the 2015 Paris Accord, 196 parties set a goal “to limit the temperature increase to 1.5°C above pre-industrial levels.” The U.N.’s Intergovernmental Panel on Climate Change says crossing the 1.5°C (34.7°F) threshold risks severe drought, heatwaves and rainfall.
Measuring Up
Measuring Scope 1, 2 and 3 CO2e emissions requires gathering information on energy consumption, fuel use, transportation, waste generation and more. This data is used to calculate emissions for each scope. Carbon calculators can make this step easier (see “Online Resources for CO2e Accounting,” page 31).
Measuring and reporting CO2e emissions to their client was a reasonably straightforward process. “They want us to be aware of it, and then they want it to be a priority to us,” Porter said. Recently, Newcomb’s team analyzed their historic data to determine the carbon footprint trend. They found it increased due to expansion and added equipment. The team decided to make carbon footprint reduction a priority.
Reduce, Reuse, Recycle?
Initially, the team thought recycling was the answer. But they already recycled and were using recycled cardboard and metal.
“If you research it, you’ll find that 90% plus of the material springs are made of is already recycled,” Porter said.
Then, Newcomb looked at their propane, electricity and natural gas use.
“We realized right away that the best way to really make an impact was to reduce our consumption of propane, our consumption of power and our consumption of refrigerant,” said Porter. Electricity consumption is the primary source of CO2e emissions for most springmakers.
Servos to the Rescue
Newcomb realized that retrofitting its equipment with servos would reduce its carbon footprint and operating costs.
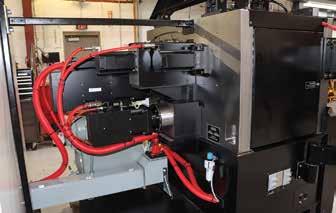
The bigger the machine, the bigger the impact retrofitting can have, Porter emphasized. This is because larger machines naturally draw more power. This means any reduction in power use is multiplied by the overall power draw.
“We all want to save the planet, but at the end of the day, money drives us, right?” said Ryan Cutter, president of FENN, LLC. “The good news is, if you’re trying to lower your carbon footprint, you’re also saving money and your profitability is going to go up.”
“Spring machines and wire formers spend a lot of energy starting and stopping,” said Cutter. “On stopping, servos use the motor as a generator, but that energy needs to be put someplace. Modern control systems use active power supplies to send that energy back to the grid instead of dumping it as heat.”
Benefiting from Retrofitting
“The benefit of a servo motor is better control, more precision and less consumption on the power pull. It’s more efficient,” said Cutter. “We can strip a machine completely down and internally load servo motors for a fraction of the cost of a new machine.
“The power consumption obviously is tremendously lower,” said Porter of retrofitting. “It’s cut by 80%, maybe 85% … and your throughput is usually slightly greater.”
“If you’re upgrading, it’s going to be more efficient. It’s going to be more precise (and) lower power consumption significantly,” Cutter added. The side benefit is the old machine sidesteps recycling. “Rather than take all that steel and iron… and throw it in the scrapyard, we’re reusing it.”
Heating Up and Cooling Down
Industrial ovens are the largest source of power consumption for most springmakers.
“At our plant in North Carolina, we run 60 ovens,” Porter said. “Those ovens, operating at 500 to 900 degrees Fahrenheit, pull a ton of power. If you look at the amperage coming off those ovens, that’s the primary power consumption within our spring manufacturing (facility).
“So, we modified our overnight shifts and added shut-off timer switches to our ovens that we didn’t have before,” he said. “When our second shift people leave, we’ll program the machine to run, let’s say four hours. And before we wired in these switches the ovens would just stay on all night.”
In addition to retrofitting machines and adding timers to ovens, Newcomb has also put economizers on all their facilities’ HVAC rooftop units (RTUs) to reduce the energy needed to heat and cool their shops.
Beyond Retrofitting
Halfway across the country, Apex Springs and Stamping in Grand Rapids, Michigan, created various initiatives to reduce the company’s carbon footprint. For example, they recycle steel and plastic, reduce water usage, use a tiny eight-cubic yard trash receptacle and only use gas for heating.
But the major carbon-reduction initiative this springmaker established was an ambitious solar panel system. CEO Dennis Bhaskaran said that Apex installed its first solar panels in 2012 with a 40-kW system on the building’s roof. The company planned another installation the following year. However, a winter storm dumped 4 feet of snow on the roof, weighing down the panels. The weight of the panels and snow was too much for the structure to handle, and the roof began to sag.
“A group of guys went up there, and we quickly shoveled all the snow off the roof,” he said. “We put a pile of
snow near where my window is. It was a huge pile, and I think that pile didn’t melt until June.”
Power Up
“We had already bought everything to do the next project,” said Bhaskaran. “We couldn’t do any more on the roof, and we (owned) the property across the street. So, we moved everything across the street that summer.”
Apex created a 125-kW, 50,000 sq. ft. solar farm which is one of Michigan’s largest. In Western Michigan, one might expect the best energy generation during the long days of the summer months. But because the system is stationary and doesn’t have articulating panels, it does not collect maximum solar energy in June, July or August. Instead, the best power-generating months tend to be March, April, September and October, Bhaskaran said.
Apex recouped its investment in the solar panel system in about five years. As a result, the system now produces about 12% of Apex’s energy needs.
Seeing the Light
As the use of renewable energy becomes increasingly popular in manufacturing, Bhaskaran believes that solar power is the wave of the future.
“I think it’s going to be the next big thing,” he said. “We’ve got to be responsible for our environment, and it’s a good business move, too. It’s not just about being responsible, but good business.
“Our people love to hear that we’re producing power,” said Bhaskaran. “We’ve got a solar farm website that we can pull up, and they can see what we produced during that day.”
Apex also did an energy audit and replaced all the existing fixtures with LED panels. But instead of using the opportunity to reduce their carbon footprint and electricity usage, Bhaskaran elected to improve the overall lighting. As a result, employees enjoy a brighter workplace.
Meanwhile
on the West Coast
Scandic Springs in San Leandro, California, has taken significant steps to reduce its carbon footprint over the years. It started with small changes like better lighting and upgrading the heating system, said Hale Foote, CEO and co-owner of Scandic, along with his daughter, Andrea.
He said the catalyst for their carbon footprint reduction initiative was climate change concerns. They started with minor changes.
“It’s the small little things that count. If you can start small, it’s the right way to go. You can get some wins under your belt and then go bigger,” Foote said.
Other changes, like setting flexible start hours to help production workers avoid traffic and using a closed-loop water system for their water jet, helped create a culture of environmentalism. These changes gained momentum and enabled them to take on more significant projects like solar panels.
Solar in Sunny California
Initially, solar panels were not part of Scandic’s plan. They were too expensive. But in 2013, when approached by a contractor that informed them of a 30% federal and 20% state tax credit for solar panels, Foote began to consider the project.
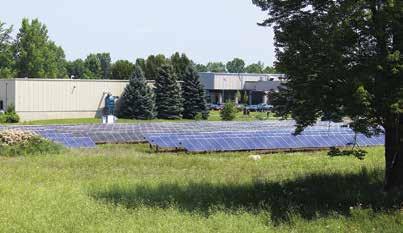
“That made it a lot more attractive,” said Foote. “So, we did it … we put solar panels on the roof as big as the city would let us and used the taxpayers’ dollars. Thank you.”
The pay-off for the 398 solar panels on his 35,000 sq. ft. facility was faster than expected. It took only five instead of the predicted seven years to pay off the system. The life span of Scandic’s solar panels is 25 years. Since the five-year payoff ended, the panels operate basically for free.
On the Bright Side
Aside from the direct financial benefit of solar panels, Scandic Springs enjoys several other benefits. One is that the new roof on the southwest side of the building will last virtually forever, as the solar panels cover and protect it. Another benefit is that the building is cooler in the summer, since there is far less sunlight hitting the roof, the heat transfer is minimized.
Scandic has also received positive customer reactions — especially in the electric vehicle world.
“Those companies look at us as being an early adopter and say it’s kind of cool. That gives us a little bit of (credibility) with the EV world who are very clean and very clean conscious,” Foote said.
“I’ve also had employees say, ‘I like working for a company that does that kind of stuff.’ It’s a slight morale boost to some employees,” Foote said. He emphasized that being a green company provides Scandic with a good employee retention and recruiting tool.
Foote’s advice for other springmakers who want to reduce their carbon footprint is to start with small changes, such as changing light bulbs to LED, which is a low-hanging fruit that can quickly lead to momentum.
In Debt to Carbon Credits
Every springmaker will have a carbon footprint. A manufacturer cannot entirely eliminate their emissions, but there are ways to reach zero or even net negative emissions (See “Case Study: Carbon Neutral to Carbon Negative”).
An organization can buy carbon credits, also called carbon offsets, to compensate for their GHG emissions. Some regulators require that certain businesses purchase carbon credits to offset their environmental impact. Currently, the U.S. federal government does not require carbon offset, but some state and regional authorities may, depending on the business sector.
“Carbon credits are units of emission reduction, measured in metric tons of carbon dioxide equivalent (CO2e),” said Christopher Goering, operations director at ECOLIFE Conservation (ecolifeconservation. org) and son of SMI immediate past president Bert Goering, president of Precision Coil Spring.
The younger Goering develops programs that generate carbon credits for sale.
“Buying carbon credits can help a business meet their carbon reduction goals,” Goering said.
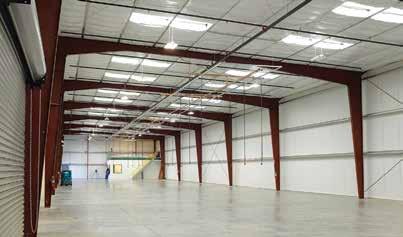
Some organizations develop projects that remove or reduce GHG emissions and create carbon credits. Enterprises that remove emissions would include reforestation and agricultural projects. Other organizations reduce existing emissions. For example, ECOLIFE’s Patsari Improved Cookstove program uses 60% less wood to reduce carbon emissions and minimize the demand for firewood among the native people of Michoacán, Mexico.
Take Credit Where Credit is Due
Verified carbon credits are audited, using internationally established standards, by third-party verifiers such as American Carbon Registry (americancarbonregistry.org), Gold Standard (goldstandard.org) and Verra (verra.org). Regulators require carbon credits to be verified.
“These carbon credits are acquired on carbon markets, trading systems in which carbon credits are sold and bought,” said Goering.
There are two types of markets, compliance and voluntary. Compliance markets trade in carbon credits to serve national, regional or international policy or regulatory requirements. Voluntary markets are generally used by corporations with sustainability targets.
Due to the complexity of the carbon credit market, you may want to work with a consultant to acquire credits if you choose to offset your footprint.
Reducing Your Footprint Starts with One Step
Measuring, managing, and mitigating your carbon footprint is an ongoing process. It requires continuous monitoring and adaptation. But, by taking steps to reduce emissions, springmakers can contribute to a more sustainable future while also reaping the benefits of cost savings, enhanced reputation and employee satisfaction. n
Online Resources for CO2e Accounting
Here are a few organizations with online carbon footprint calculation tools and resources for businesses:
• Environmental Protection Agency (EPA) (epa.gov)
The EPA website has tools and resources to help businesses measure and track their carbon footprint. The EPA’s “Sustainable Materials Management (SMM) Program” tool is specifically designed to estimate and track organizations’ emissions. They also have an SMM Web Academy (bit.ly/eps-smm).
• World Resources Institute (wri.org)
Washington, D.C.-based WRI’s “GHG Protocol,” is the most widely used international accounting tool for measuring and managing greenhouse gas emissions. Founded in 1982, WRI provides comprehensive resources, standards, and tools for businesses to calculate their carbon footprint.
• Carbon Trust (carbontrust.com)
The Carbon Trust is a UK-based not-for-profit with offices worldwide including in the United States and Mexico. It has a range of services and tools to help businesses reduce their carbon emissions and improve sustainability. They provide carbon footprint calculators and guidance on measuring and managing carbon emissions.
• CDP (cdp.net)
CDP, formerly known as the Carbon Disclosure Project, is a global nonprofit that encourages businesses to measure, disclose and manage their environmental impact. While CDP primarily focuses on reporting and disclosure, they also provide business resources to calculate and reduce carbon footprint.
In addition, carbon accounting software providers such as Greenhouse Gas Management Institute (GHGMI), thinkstep, and Ecochain offer proprietary applications and platforms for calculating and managing carbon footprints. BCG markets an AI application for larger companies (see “Study: Only 10% of Companies Measure Full Carbon Footprint”).
While these websites provide valuable resources, a consultant may help you more accurately measure and manage your business’s footprint. There are also consultants that specialize in mitigating your emissions and acquiring carbon offset units.
Scandic Springs added motion-sensor LED lighting and skylights to reduce their energy use and emissions.CASE STUDY
By Tom ManderCarbon Offset Initiatives Take SMI Member from Carbon Neutral to Carbon Negative Status
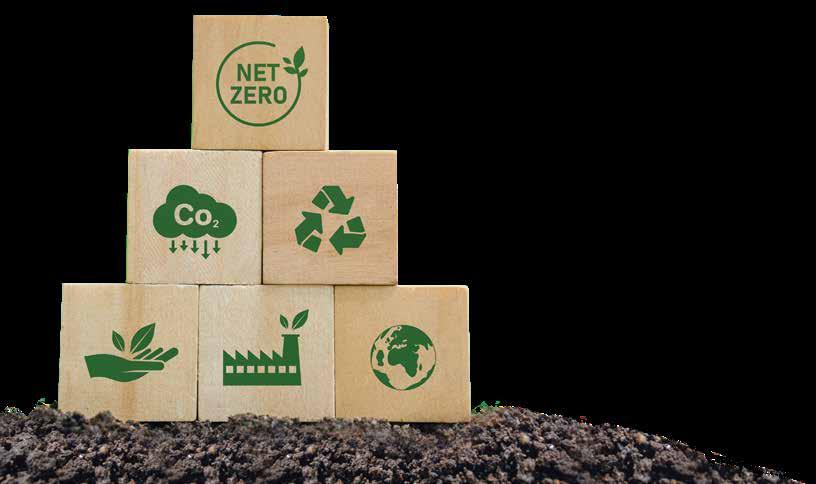
When you process more than 200 tons of alloy a year, working to become a carbon-neutral manufacturer may seem daunting. However, for us at Alloy Wire International (AWI), producers of round, flat and profile wire, it was a business decision we felt we had to take. It wasn’t just because people were talking about carbon footprint — or that it would look good on a website and in marketing materials — it was a conscious decision to become forerunners in sustainability in an industry sector that has sometimes been behind the curve.
Founded in 1946 by John Stockdale in an old ambulance station in West Midlands, England, AWI’s client base stretches across more than 60 global locations. For our management team, becoming a greener manufacturer was all part of living up to our business philosophy of “manufacturing quality, delivering reliability.” While becoming “carbon neutral’ was the original target, the end goal quickly accelerated.
1What made Alloy Wire International go down the carbon-neutral route?
As a management team, we are always trying to look ahead and see what the next big industry trends are. “Digital manufacturing” and “servitization” (strategic shift from product to value-added, product-service offerings) have become big buzzwords. The other major talking point has been the move to a “net zero”, or first, to a “net neutral” carbon footprint.
The U.K. is driving the adoption of this target, especially in many industries we supply, including aerospace, automotive, defense, nuclear and oil and gas manufacturing. However, with so much noise coming from the top, we knew “intention” would soon become “directive,” so we decided to become one of the first in our sector to go down the carbon neutral route.
This decision was made roughly the same time as our 75th anniversary in 2021. So, we felt the best way to show we were committed to a further 75 years in business was to look at our commitment to sustaining ourselves and the environment around us.
As a manufacturer, there will always be a ceiling to how environmentally friendly we can be, but we want to show that we are doing our best in this arena.
2 Why wasn’t carbon neutral good enough for the business?
Being carbon neutral means we offset all the carbon we generate as a business. This spans our production, transportation, supply chain and even our staff’s work commute.
This was a big task and required knowledge that we didn’t have within the business, leading us to partner with Carbon Neutral Britain, a specialist in this field.
They worked with us to analyze our carbon usage throughout the year, which accounted for 450 tons of CO2. Once we had this figure, we could look at various initiatives to offset the total, including planting trees and supporting eco-projects that provide agricultural education and sustainable incomes to local communities.
The process was relatively straightforward once we had our head around what was required and the staff was brought on board. This encouraged us not to stop there; instead, we turned our attention to the coveted carbon negative status.
3
What measures did you initiate to reach being carbon negative?
At the start, everything seemed quite daunting. We had to analyze many areas of the business to determine how much carbon dioxide an activity produced.
Getting an expert was the best thing we did. Carbon Neutral Britain had everything mapped out. They applied a tried-and-tested process to quickly measure our Scope 1, 2 and 3 emissions and to offset that total to go further and become carbon negative.
There are a myriad of carbon offset projects specifically set up to reduce carbon emissions, ranging from reforestations and solar farms to improving inefficient energy usage.
4
How did you get the staff to buy in?
The good news for other wire manufacturers and springmakers looking to do this is that your staff doesn’t have to do much. It all tends to be done for them by whoever is championing the project in the business.
All of our 33 employees were on board with this project. It is important for us as a company to leave a positive legacy in the communities in which we operate. Sustainability and protecting the planet are the biggest positive actions we can take.
5
What challenges did you face and how did you overcome them?
Did you need external help?
As mentioned previously, we partnered with Carbon Neutral Britain, who have significant experience achieving this accreditation with many other UK companies.
I can’t stress how good this decision was. We run a company that supplies over 6,000 customers every year, and we don’t have much time to focus on non-core activities. So having an external expert guide us through the journey was something we required.
Carbon Neutral Britain helped evaluate the carbon emissions and then acted on our behalf as a broker to purchase carbon credits to offset our usage.
6
What does being carbon negative mean? What benefits does it provide for the business?
Carbon negative means we are offsetting more carbon emissions than we produce as a business.
Consumers and businesses are paying more attention to how companies act regarding their environmental
credentials and sustainability policy. We didn’t want to wait to be scrutinized, instead preferring to get ahead of the trend and acknowledge that we see this as an important issue.
It’s difficult to attribute any tangible financial benefits so far. But I’m sure being “a socially-green business” can only help when attracting future staff members and when tendering for future work.
7 Has it helped you win any new business?
Hand on heart, I can’t say we’ve had a customer say we are choosing you because you are carbon negative. However, it is still in its early days, and I’m sure this will change with the movement toward more sustainable manufacturing.
We have enjoyed very positive public relations around securing this status, and we have had clients and even competitors get in touch to ask us how we achieved it so quickly.
8
Do you have future plans to build on carbon-negative status? Is there anywhere else to go?
We are very passionate about continuous improvement and fully intend to explore additional ways to build on our carbon-negative accreditation.
For example, we have already digitalized some processes internally as we work toward becoming a completely paperless business, while future investment is planned to fit solar panels to our factory in the West Midlands.
Maximizing the spirit of collaboration, we have partnered with JUST ONE Tree (justonetree.life), which plants a tree for every 100 kg of wire we sell.
Based on the volumes we have sold since the relationship started, we have donated 2,000 trees, each of which will support reforestation projects in countries such as Mozambique, Haiti, Kenya and Madagascar. n
Tom Mander, managing director of Alloy Wire International (AWI), joined the company in 2005. Within a decade, he led the sales team to triple revenues with international orders accounting for 60% of total sales. Mander was also integral to the recent management buyout. Outside work, he enjoys soccer, going to the gym and spending time with his wife and two children. For more information, email tommander@alloywire.com or call 01384 262022.
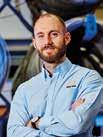
Renewable Energy Tax Incentives Require Expert Guidance
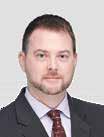
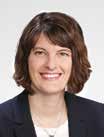
Renewable energy adopters can get up to 50% or more in tax credits under the new Inflation Reduction Act (IRA). This has significantly increased investments in energy credit projects according to our research.
The investment tax credit (ITC) provides a base credit of up to 30% if the renewable energy project meets specific requirements related to wages and apprenticeships.
The IRA also offers bonus credits for projects in certain geographies that use domestically sourced materials.
Claiming a 10% domestic sourcing bonus may require detailed manufacturing and supply chain documentation from suppliers and contractors. This documentation should be specified as mandatory in all agreements with contractors. Domestic sourcing could also increase project costs, reducing the tax incentive value.
To qualify for the domestic content bonus credit, either all steel and iron components must be made in the U.S. and 40% of the total costs (including components) for all manufactured products must be mined, produced, or manufactured in the U.S. (20% for offshore wind facilities). These percentages are scheduled to increase for projects launched after 2026.
According to IRS guidelines, refurbishing projects may qualify for domestic bonus credits if the fair market value of the new property constitutes at least 80% of the total value and the sourcing rules are satisfied.
The IRA and ITC are complicated programs, so be sure to consult with a tax advisor. n
Ellen Martin is the national leader of Grant Thornton LLP’s Strategic Federal Tax Services business line and is located in the metro Washington D.C. area. Martin has over 20 years of public accounting and tax experience. In her current role, Martin provides a broad range of tax consulting and planning services for business tax issues. For more information, email Ellen.Martin@us.gt.com.
Dustin Stamper is a managing director in Grant Thornton LLP’s Washington National Tax Office in Washington, D.C. Stamper leads the tax legislative affairs practice, where he is responsible for monitoring tax legislative and regulatory activity for the firm. For more information, email Dustin.Stamper@us.gt.com.
Predicting Deflection Angles
on Torsion Spring Arms During Stress Relieving
By Thomas Grenier-DesbiensAn extensive heat-treating study was conducted to determine the stress-relieving parameters required to control the deflection angles on torsion springs. The objective of this work was to identify the optimum temperature and time in order to optimize deflection control. As a result of this work, it was possible to specify the time at temperature to achieve any deflection angle with a +/- 1 degree tolerance.
This represents a significant improvement for all springmakers since they may spend much time on trial and error. Some have tolerances of +/-20 degrees deflection and most springmakers who contact us need +/-3 degrees deflection angles, with this study we achieved +/- 0.5 degrees.
Objective
In this work, an experiment was performed using a heat-treating furnace produced by Pyromaitre Inc., model PYRO-128E. Sets of torsion springs were treated to determine the effect of temperature and time on torsion-end deflection. The objective of this work was to define the optimum conditions (thermal effect) for control of torsion spring end deflection.
In order to come up with an appropriate expression for the thermal effect it is necessary to categorize time into two components.
i) The time taken by the spring to reach a particular temperature (t1)
ii) The time for which a spring is held at a particular temperature (or) the soak time (t2) The experiment was designed in such a way as to determine the significance of soak time in producing a thermal effect on a spring.
Initial Experiment Conditions
Springs
For each test spring, the angle between arms on the as-received springs was measured.
Springs were instrumented with a thermocouple and time and temperature were recorded during each experiment were recorded using a data-logger model.
Furnace
The input temperature of the oven was set to 400°C (752°F).
Test #1: The oven was cold started with a minimum efficiency such that the spring reached the required temperature very slowly (60 minutes). The spring was taken out of the oven as soon it reached the required temperature and air-cooled. The deflection of the spring arms from its initial dimension was measured and recorded.
Test #2: Following the cold-start the temperature cycle was set so that the spring would reach 400°C (752°F) in 30 minutes. The spring was held at temperature (soak) for 30 minutes before it was taken out of the furnace and air-cooled. The deflection of the spring arms from its initial dimension was measured and recorded.
Test #3: Following the cold start, the temperature cycle was set so that the spring would reach 400°C (752°F) in 10 minutes. The spring was held at temperature (soak) for 50 minutes before it was taken out of the furnace and air-cooled. The deflection of the spring arms from its initial dimension was measured and recorded.
Test results for the initial experiment are shown in Table 1.
Discussion
The data suggests that the soak time plays a significant role in producing a thermal effect on a spring apart from the temperature and the time taken by the spring to reach a particular temperature. The data in Table 1 suggests a greater thermal effect is produced on a spring with an increasing soak time. The data is not a linear function. It is possible that an additional effect due to soak starts to decrease with time. It is also observed from the graph in Figure 1 that the curve flattens out at large values of t2.
Design of Experiments
Design of Experiments (DOE) is an effective way to understand and make inferences about a process or a system. In this method, a test plan is developed which can be analyzed statistically where a limited number of experiments (fraction factorial) can yield the same inferences

as a full factorial design. Technically we can define DOE as a test or series of tests in which purposeful changes are made to the input variables of a process or a system to identify the reasons for changes that may be found in the output response. The objectives of DOE are
• Determining the variables for the experiment that affect the output of a response
• Determining the set of values for the variables so that the output is near the nominal value.
• Select the variables’ values so that the process’s variability are minimized.
• Determine the values for the variables such that the effects of nuisance factors are diminished.
For this experiment, furnace temperature, ramp-up rate and soak time were selected as the three variables that affect the stress-relieving response of torsion springs. In order to understand how these variables affect the process, a fractional factorial design was done with these three variables as the factors and with two levels hence making it a 23 design.
Design
In general, fractional factorial designs are one of the most efficient methods to do an experiment on a process. Factorial design means taking into consideration all the combinations of the levels and factors that are being investigated. In our experiment, we have three factors and two levels.
Analysis
The data above was analyzed using analysis of variance (ANOVA) and a regression analysis of the data resulted in the equation shown below for predicting torsion angle deflection.
For this study:
Torsion spring arm deflection = -34.18750 + (0.12188 * Furnace Temperature) – (0.031250 * Ramp-up Rate)(0.077083 * Soak Time) + (3.12500E-004
* Furnace Temperature * Ramp-up Rate) + 7.29167E-004 * (Furnace Temperature
* Soak Time) - 2.08333E-004 * (Ramp-up Rate * Soak Time)
The predicted R2 value was 0.998. A full step-by-step statistical analysis of the data is beyond the scope of this article. For those interested, please contact the author.
Conclusions
As a result of the heat-treating studies conducted in this work, stress-relieving parameters required to control on the deflection angles on torsion springs were determined. A regression analysis equation was developed to predict the stressrelieving temperature and time needed to optimize torsion spring arm deflection control. As a result of this work, it was possible to specify the time at temperature to achieve torsion spring deflection angles with a tolerance of +/- 1 degree. This represents a significant improvement for all spring makers since they may currently spend much time on trial and error. n
Thomas GrenierDesbiens is a partner in Pyromaitre Inc. Quebec, Canada. Thomas has more than 10 years of experience conducting and performing stressrelieving and tempering process improvements for manufacturers supplying mostly to the automotive market. He can be reached at tgrenier@pyromaitre.com.
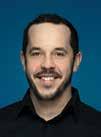
SMI’s Annual Meeting
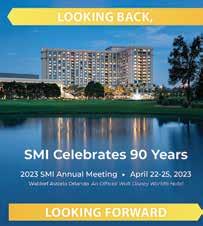
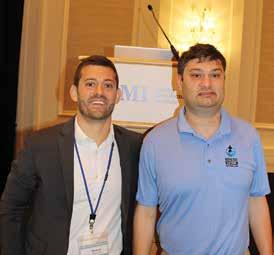
The 2023 SMI Annual Meeting, April 22-25, at the Waldorf Astoria Orlando was an enjoyable and productive experience in the heart of the Magic Kingdom. While networking and education were the event’s focus, there was occasional downtime to visit the shops and restaurants at Disney Springs or magical moments with family and friends at the “Mouse House.”
The Opening Reception was a great time to reconnect with old colleagues and meet new ones. Members and guests also met new Springs managing editor Phil Sasso and new SMI Communications and Administrative Coordinator Gabriela “Gaby” Carrasco. There was a lot of energy and vision at the committee and board of directors meetings. And the inaugural Avant-Garde Social was a great time for younger members to relax and connect.
Social entrepreneur and author of “The Power of Potential” (see Book Corner page 59) Thomas D’Eri told how he and his father re-engineered a struggling car wash to employ an 80% autistic and 20% non-autistic workforce, inspired by his autistic brother Andrew. Today, Rising Tide employs 100 people at three car washes in southern Florida.
(Andrew also attended the session.)

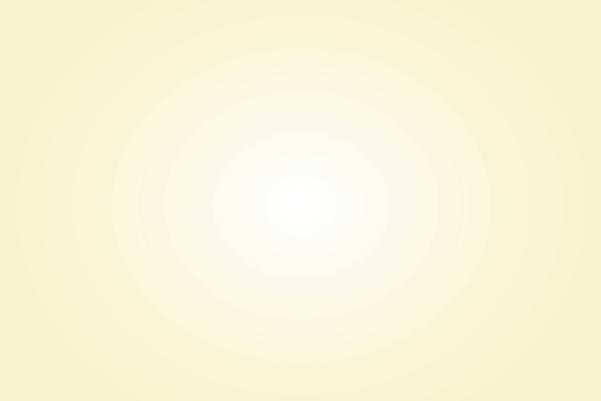
But D’Eri’s overarching message was that many workers that might otherwise be dismissed could be productive employees with a shift in how a business interviews, trains, manages and motivates their team.

The Power of Potential
Thomas D’Eri Co-Founder and COO, Rising Tide Car Wash
“Looking Back, Looking Forward” Informs and Inspires
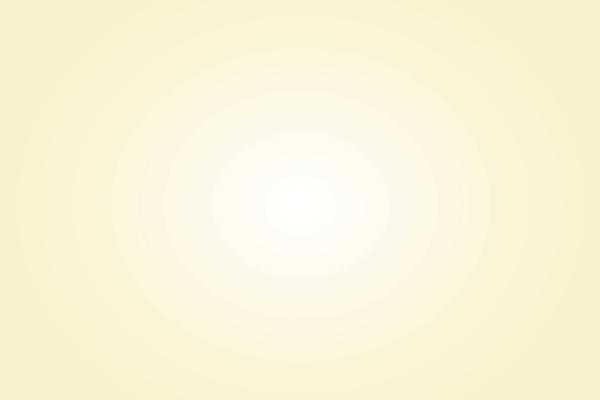
The challenge in writing a synopsis of Story Musgrave’s presentation is insufficient space. He has accomplished more in his 80-some years than the average person might in 10 lifetimes.





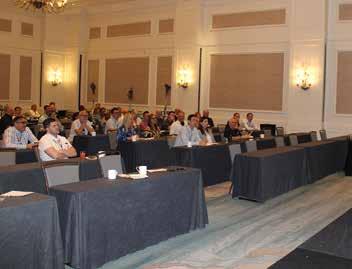

It’s hard not to feel inadequate when you hear how this father of seven, a trauma surgeon and astronaut, earned six advanced and 21 honorary degrees, made over 800 freefalls, and walked in space along with dozens of other remarkable accomplishments.
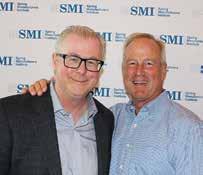
But Musgrave’s goal was to motivate. Fittingly he ended his presentation by encouraging attendees to “Seize every opportunity that comes your way!”
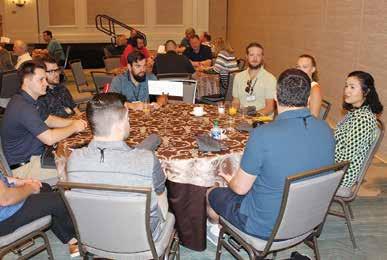
Farm Kid to Trauma Surgeon to Astronaut and Way Beyond!


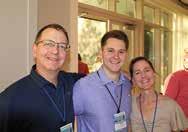
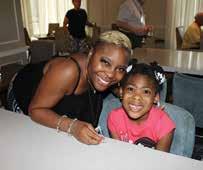
Story Musgrave, M.D. Physician and Retired NASA Astronaut
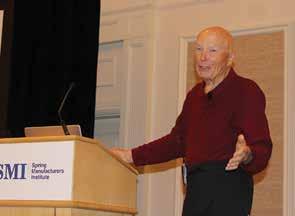
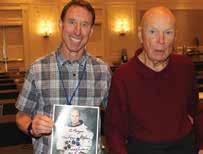
A first-ever for SMI was a cornhole/bags tournament, aptly dubbed the SMI Cornament, was held on the Waldorf Astoria lawn. The winners of the double-elimination tournament emerged from the youngest team, “Hubeer,” comprised of Quinn Huber, son of SMI president Gene Huber Jr. and his nephew, Cade Beer. Second place belonged to the father-son duo of David and Joe DeVoe of Plymouth Spring aka “Fenway” and third place honors went to college friends
Don Jacobson III, SMI first vice president and speaker Charles Gaudet II. Members of the three highest-ranked teams each received an SMI-branded cornhole set.
GENERAL SESSIONS
Charles Gaudet shared his secrets to success as an entrepreneur and proclaimed, “There’s no such thing as a good economy or a bad economy, only different economies.”
Gaudet said businesses that adapt are the ones that thrive. He provided strategies to overcome three common business challenges. The first challenge involves more demanding buyers, explaining that the solution is targeting the most discerning buyers. The second challenge is that a buyer’s journey is not linear, which can be overcome by focusing on demand creation. Finally, he said every company must get beyond word-of-mouth and referrals by adding more spokes to their marketing wheel.
Everyone who attended the presentation received a free copy of Gaudet’s book “The Predictable Profits Playbook.”
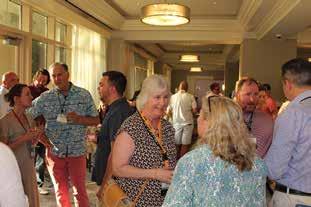
Growth Today and Tomorrow
How to Create Sustainable Growth in the New Economy
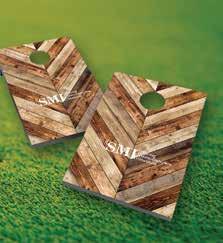
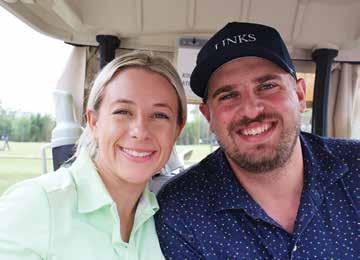


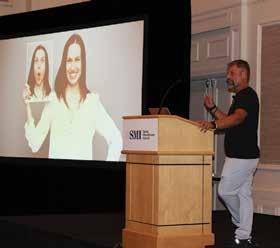
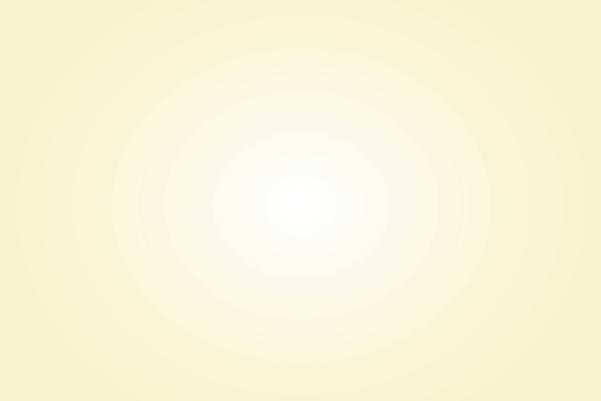
The Closing Reception and Dinner was a send-off for retired SMI Executive Director Lynne Carr. The evening included a fun and touching 22-minute video tribute to Carr featuring family, friends and SMI members.

There were many tears shed and a standing ovation, as SMI members thanked Carr for her 28 years of service to SMI (read more about Carr’s retirement on page 42).
LOOKING AHEAD
SMI’s 2024 Annual Meeting will be held April 6-9, at Loews Coronado Bay Resort in Coronado, California. An induction ceremony for its new president will cap off networking events and stimulating speaker sessions as SMI welcomes the entire 2024-2026 executive committee.
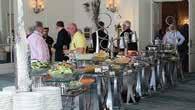
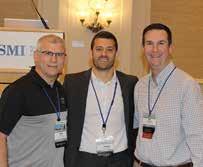
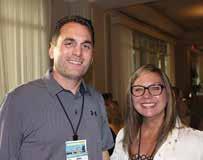
Laura Helmrich-Rhodes, reviewed OSHA’s priorities which includes a focus on heat prevention. She also reviewed OSHA’s “National Emphasis Program” (NEP) which includes areas of concern for the spring and wire products industries. This includes: combustible dust, amputation prevention, outdoor and indoor heat-related hazards, hexavalent chromium, lead, primary metal industries, process safety management (PSM) and respirable silica. Finally, she reviewed the OSHA unified agenda and looked at the top 10 current OSHA citations impacting the spring and metal forming industry.
Her goal during the presentation was to help SMI members begin to measure the maturity of safety efforts at their facilities.
Rhodes will hold webinars throughout the year to inform and educate SMI members. A complete list of times and dates can be found on page 64.
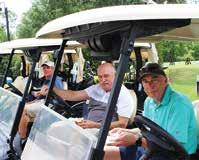

Predictable Citations: An OSHA Update



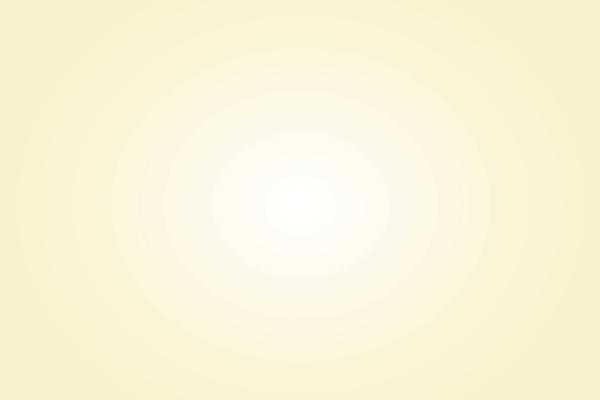



Laura Helmrich-Rhodes, SMI Regulatatory Compliance Consultant
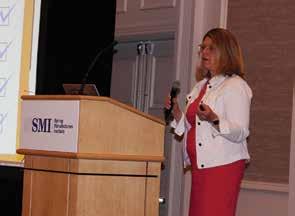
SMI Says Goodbye and Thanks
By Gary McCoy, Executive Director



A lot of tears, hugs and words of gratitude were expressed at the 2023 SMI Annual Meeting in Orlando for outgoing SMI Executive Director Lynne Carr. That’s because the Florida gathering marked the last event for Carr in a remarkable 28-year career with the association. It was at the 2022 SMI Annual Meeting in Scottsdale, Arizona, that Carr had tearfully announced that she would retire a year later from an industry that she had poured her heart and soul into for nearly three decades.
Carr’s SMI journey started in 1995 when she was a stayat-home mom looking for part-time work while her three children were in school. She answered an ad for a part-time administrative position with SMI, and the rest is history.
“My youngest child had just turned five, and I didn’t know what to do with myself,” Carr recalled in a 2016 Springs article to celebrate her 20 year anniversary with SMI. “I started looking for a job. I never envisioned being the executive director here. That was really not a goal at the time.”
Remarkably she started out as advertising manager for Springs and never relinquished that title. Carr was named SMI’s executive director in 2013 and is known in the spring industry for her knowledge, diligence and deep relationships with a wide variety of people.
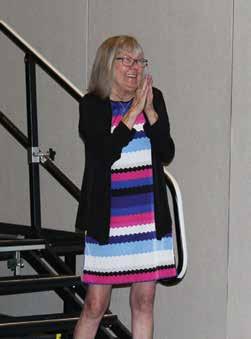

to Lynne Carr




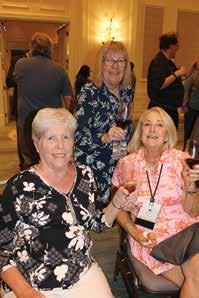
A Moving Tribute
28 Years of Hard Work and Dedication
Carr was honored for her SMI service during the closing dinner at the 2023 meeting with her three children in attendance, which included her daughter, Alyson Lundby, son, Mark Carr, daughter, Tracy Carr, son-in-law, Nathan Lundby and grandsons, Donovan and Graham Lundby. Of course, her extended SMI family was there to provide well wishes and thanks. The evening started with a 22-minute video tribute to Carr that included messages from family, friends, co-workers and SMI leaders. The video was a surprise to Carr, who kept saying, “Oh my gosh,” and wiping tears from her eyes. Having worked with Carr for 15 years I know full well how hard it is to keep anything secret from her, but the mission was accomplished! You can read some of the expressions of gratitude from the video later in this article.
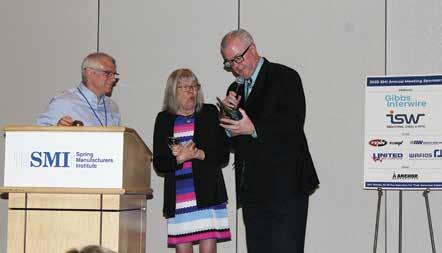
SMI president Gene Huber Jr. presided as master of ceremonies. He announced that SMI had established the Lynne Carr Scholarship in her honor. The $2,000 scholarship will begin in 2024. Huber mentioned how the scholarship was appropriate because Carr had been instrumental in starting the scholarship program in 2010. He also announced that Carr had been named as a prestigious SMI Honorary Member. She becomes the first female recipient. A hand-crafted art glass award was presented to her that read: “Lynne Carr, 1995 to 2023, In Appreciation for Outstanding Dedication and Leadership.”
Other parting gifts included a new suitcase for Carr to use while traveling to see family in California and personalized Disney luggage tags.
Tributes from family and
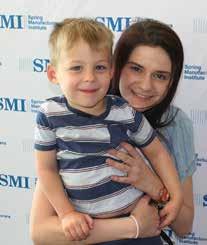
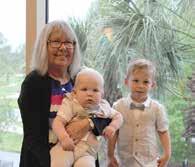
Heartfelt Thanks Expressed




After watching the video and receiving the awards, Carr stood at the podium flanked by her children and joked, “I need a stunt double with no emotional attachment to any of you to get through this speech.”
She started out with a question, “How many people in this room get a new boss every two years?” After a long silence, she said, “Yeah, I didn’t think so. I have had many going back to 1995.”
She listed all 15 SMI presidents that she had served under during that time, starting with Pete Peterson and ending with Huber.
“When I started at SMI part-time, I was put in charge of securing ads for Springs magazine which I still do today,” she remarked. “I didn’t want to give it up because I came to know the associate members very well, even better than I knew the springmakers. We developed relationships that I will never forget.”
She said the advertising role with the magazine “will always hold a special place in my heart.”
Carr related how things started moving forward in her career, and she was finally allowed to go to SMI conventions. “My very first was in Albuquerque, New Mexico. And here we are for my final one in Orlando.”

She went on to say, “This has been a great ride and a fantastic job, one that I have enjoyed immensely. No one misses the work part, but you always miss the people. You have always treated me like family and never like a staff member. SMI will always be in my heart, as will all of you.”
Carr attended the NESMA Casino Night in March in Bristol, Connecticut, where NESMA president Lucas Karabin and SMI treasurer and NESMA board member David DeVoe gave moving tributes to Carr and presented her with a necklace. In her speech she said, “I was completely surprised how they made this happen without me knowing about it since I sat on their board.”
She saved her last thanks for her family, who “are all here to enjoy this with me. It was a sacrifice for them, as well, that Mom was at work or out of town for certain events. Not to mention they flew across the country to celebrate with me here.”
She closed her speech by returning to her NESMA send-off in March. “I would like to quote the words of a former NESMA President (Michael Brault) from a song by The Eagles called Hotel California. ‘You can check out, but you can never leave.’ And none of you will ever leave my heart.”
Her last line was greeted by a thundering standing ovation as many in the room wiped tears from their eyes.
Goodbye and farewell, Lynne Carr. You will be missed, but always remembered.
Video Tributes
Here are edited versions of the many thanks extended to Carr during the video presentation. To watch the video, visit the SMI YouTube page: youtu.be/dZbKM9-RqNM.
Scan to watch the Lynne Carr tribute video.
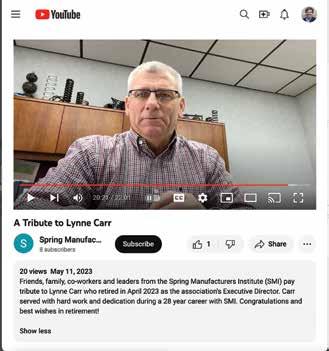
“Hey, Mom, I wanted to wish you a happy retirement. I wanted to tell you that I love you and I’m so proud of everything that you’ve done throughout your life, not just with your work, but in raising us and implanting into us love and empathy and intelligence and just being decent human beings.”
—Mark Carr, Son“You’ve been such a great role model for all three of your children and now for your grandchildren, and you’ve always been a great role model for me too. Just the way you’ve used your humility and your sense of humor and your incredible work ethic. You bring the same even-keeled spirit every day to handle whatever life throws at you and it’s really been an inspiration for me. We’re excited to have more time at home with Grandma.
Congratulations on your retirement.”
—Nathan Lundby, Son-in-Law“SMI has been such a huge part of our family’s life for decades now, and I honestly can’t even believe it’s coming to an end. I’m just in awe of everything that you’ve done with your career, and I wore my Wonder Woman shirt so you can know that you’re truly my Wonder Woman and our family’s Wonder Woman. We love you so much and we can’t wait to see what’s to come.”
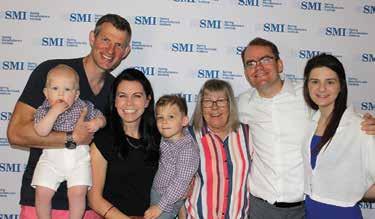
“Happy birthday and congratulations on your retirement! I know you’re concerned about being bored, but between your trips to California, Indiana, and all your dream destinations, you’ll be too busy racking up the airline miles to be bored. Enjoy your kids, grandkids, rest and relaxation, and I’ll see you when you have a spare moment. Love ya!”
—Dina Travis Sanchez, Former Administrative Coordinator, SMI“I want to wish you the best retirement ever. We spent about 20 years together. We had some good times and some bad times, but for me, you always made the bad times a little bit better.”
—Jim Wood, Retired Regulatory Compliance Consultant, SMI

“I met you in April 2008 and 15 years later it’s hard to believe you are retiring and I’m stepping into your shoes as executive director of SMI. You’ve left a big hole in the organization, and it will be hard to fill your shoes, but you put together a solid foundation that I plan to build upon. You always treated me with kindness, respect, and as a staff member even though technically I was a contractor. Happy retirement.”
—Gary McCoy, Former Managing Editor, Springs and Current Executive Director, SMI“Lynne’s my favorite and she got me through a lot of challenges, and she dedicated everything she had to making the organization better. We will sorely her, but I couldn’t be happier for someone who’s done such a tremendous job. Cheers to you! We love you dearly. Congratulations.”
—Reb Banas, Past President, Stanley Spring and Stamping
“Over the years, we’ve become great friends and I look forward to continuing our friendship in your retirement years. I wish you all the best for good health, happiness and travel. Enjoy yourself, stay healthy and stay in touch. All the best.”
—Linda Froehlich, SMI Board Member, Ace Wire Spring & Form Co.


“What a celebration for all your years of service; you have been amazing. Your commitment to the industry, to all the members to make the industry the very best it can be. We so appreciate and thank you so much for everything.”
—Mike Betts, Past President, Betts Company“I started working with you on regulatory compliance and then you helped me through my term as SMI president. I appreciate everything you’ve done through the years; how you’ve helped me to grow and help the organization to grow, and I wish you so much fun and success in your retirement.”
—Scott Rankin, Past President, Vulcan Spring“Congratulations, Lynne. You really have been the heart and soul of the organization for as long as I can remember. It’s special for me because you came on board when my dad was president of SMI 28 years ago, and here I am on the board now. It’s kind of a fitting bookend. You’re awesome and we’re going to miss you.”
—Don Jacobson III, SMI First Vice President, Newcomb Spring“Lynne, 28 years at SMI with so many presidents. You have the patience of an angel and especially tolerating me as your pandemic president. It was a great ride. We wish you all the best for an excellent retirement. Love you.”
—BertImmediateGoering,Past President, Precision Coil Spring“Congratulations on your well-deserved retirement after 28, amazing years of commitment and dedication to SMI and its members. There are a few people I know who have demonstrated the level of passion and the level of work ethic in your commitment to serving all of us. Your compassion for SMI and the membership was evident in all that you did. Sandy, and I’d like to take this moment to congratulate you on this well-deserved retirement. We pray for God’s blessing on your life as you begin to enjoy the fruits of retirement that you’re well due.”
—Steve Moreland, Past President, Automatic Spring Products Corporation“I’d like to say congratulations and remind you that during my two-year presidency from 2014 to 2016, we did big things for SMI, including the hiring of Laura Rhodes as our safety consultant, and especially the planning, the execution, and putting on of the first-ever SMI Metal Engineering eXpo in Charlotte, North Carolina at the NASCAR Hall of Fame. Congratulations.”
—Hap Porter, Past President, SEI MetalTek“I want to thank you for all the things that you’ve done for me personally. The relationships that you helped me build. We’re going to miss you completely. I hope your retirement is just as happy as the way you made everybody else feel through the 28 years that you worked at SMI. Happy retirement.”
David DeVoe, SMI Treasurer, Plymouth Spring“Sharon and I wish you the very best in your retirement. You have a special gift of hospitality and always went out of your way to make us feel welcome at SMI events, starting with our first visit to Disney when the kids were little. You have been a great blessing to so many across our industry, and we hope that your retirement is full of great times and new memories with family and friends. We pray that you would have good health and much love, joy and peace each day.”
—Dave Deerwester, At-Large Representative, Executive Committee, The Yost Superior Company
“A big thank you and congratulations for all you did for SMI. You always made the associate members feel very welcome. I also want to thank you for all the help you gave Lori and me with our dietary restrictions. You always made sure that there was something we could eat and there wasn’t a medical emergency at any convention. You’re a special person and I know that many of us feel that way. I wish you the best of luck.”
—Bill Torres, Former Board Member, Gibbs Interwire“Your passion for and commitment to SMI is unsurpassed. You shepherded me through my time on the executive committee and as president working hard behind the scenes to ensure that I look more competent than reality. What stands out for me, more than your tireless efforts on behalf of SMI, is what a wonderful person you are and what a great friend you’ve become. Thank you for all that you’ve done for SMI and for me personally.”
—Steve Kempf, Past President, Lee Spring“Congratulations on your retirement. We’re so glad for your future that you get to go do what you want to do. When I think of SMI, I remember Lynne Carr; your stable, calm, and very fiscally responsible leadership that has led us to where we are today. You’ve been through many presidents, many past presidents, and herded us cats along the way. You helped the Metal Engineering eXpo flourish and led us through a pandemic. We thank you for all those efforts and for being our friend. God bless you; we’re going to miss you.”
—Gene Huber Jr., SMI President, Winamac Coil SpringOiling The Money Machine
(Editor’s note: This condensed version of “Oiling the Money Machine” by Cecil J. McFadden, first appeared in the April 1968 issue of Springs. It discusses various business financing options, many of which are still relevant today. In 1968, the United States faced raging inflation due, in part, to the Vietnam War. Today’s post-pandemic economic challenges are also impacting interest rates and financing decisions.)
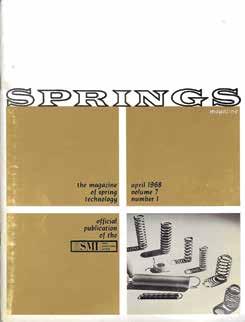
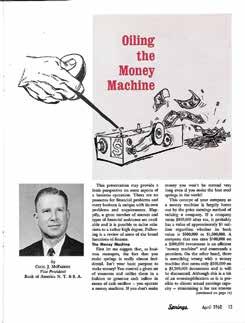
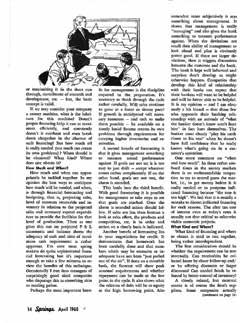
The Money Machine
First let me suggest that, as business managers, the fact that you make springs is really almost incidental. Isn’t your basic purpose to make money? If you don’t make money you won’t be around very long even if you make the best steel springs in the world!
Your company is a money machine. A company that earns $100,000 on a $500,000 investment is an efficient money machine. On the other hand, there is something wrong with a money machine that earns only $100,000 on a $1,500,000 investment. This is a bit of an oversimplification — but, the basic concept is valid.
What is the lubricant for this machine? Proper financing. This helps it run at maximum efficiency. But how much oil is really needed (too much can create its own problems)?
How Much and When?
I’m sure most springmakers do quite sophisticated financial forecasting but it’s important enough to take a few minutes to review the benefits. Perhaps the most important benefit for management is the discipline required in the preparation. It’s necessary to think through the cycle rather carefully.
A forecast gives management something to measure performance against. If goals are not set, it is too easy to just drift. It can also help in negotiating credit. If done on a monthly basis, the forecast will show peak seasonal requirements and whether repayment can be made at the low point in the cycle. It also shows the relation of debt to equity at the high point.
What Kind and Where?
The first consideration should be whether the requirement can be met internally.
• Can receivables be collected faster by closer follow-up?
• Can you offer discounts or increase discounts?
• Can the needed funds be released by better control of inventory?
A closely related, but external source is the firm’s suppliers. Some companies actually make payments faster than the terms willingly provided by suppliers.
These are the least expensive sources but the quantity of funds available is limited. For larger amounts, it is necessary to turn to conventional means.
Equity Sources
If a decision is made that funds are needed on a permanent basis, then financing should be done by the equity routes. What are the alternative sources and types?
Owner – The present owners may be in a position to enlarge their investment preferring not to let outsiders in.
Personal Relationships – Owners may wish to be selective and permit relatives and friends to invest.
Business Relationships – Ownership may ask suppliers or customers to participate in equity. There may be benefits to tying in suppliers and customers but there are also hazards.
SBIC – Another possible source of equity is from a small business investment company. Although the SBA administers this program, it is privately managed and operated to the largest extent with private money. SBIC can make straight loans but usually wants equity. The SBIC may buy common stock, but more frequently purchases debentures with warrants attached which would enable the SBIC to purchase common stock in the future at an agreed-upon price. This is not a “government trough” — investments must measure up economically.
Private Equity – There are also a number of other private organizations that buy stock of certain selected small corporations. Investment bankers are the classic source of assistance in equity financing. More tailoring is possible than may first come to mind. Of course, there is the “garden variety” common stock but preferred stock with a fixed dividend and restricted voting power may be a better fit.
Or another step can be taken up the equity ladder to pseudo equity, such as convertible debentures. By this mechanism, one may be able to sell the stock today at tomorrow’s higher prices and in the interim enjoy the benefit of paying interest with before-tax dollars compared with paying dividends with aftertax dollars.
This does not exhaust the list of potential types of equity instruments, but it does give some indication of the tailoring possibilities.
Credit
If the decision is made that there is adequate equity and that financing requirements are of a temporary nature, then management will want to borrow the money.
Sources of Borrowing
Many equity sources are also sources of credit: owners, friends, relatives and suppliers. We are seeing increasing use of ledger balance financing by which a few suppliers provide, in effect, term credit out to 3, 4, or 5 years.
Other sources include leasing companies, commercial finance companies, life insurance companies and pension funds. But the commercial bank is still the department store of credit with a broad variety on its shelves.
Short Term
The most common type is the short-term commercial note. An example is the merchant who borrows in October to buy Christmas merchandise and then repays from proceeds from Christmas sales. If the need is recurring, then a line of credit
is established under which the borrower can borrow and repay with no need to negotiate for each borrowing.
Long Term
Frequently, requirements for capital equipment, plant expansion, and similar activities require funds paid back out of cash generated over a period of years. This is a term loan. The banker’s primary concern here is historical cash flow, but will also allow for contributions from new assets acquired, changes in operation or a reasonable expectation of better than historical performance.
Term loans usually are unsecured and subject to a loan agreement. It is important that the credit agreement be a bilateral arrangement so that each side knows the rules of the game going in.
Accounts Receivable – AR financing is one of the most frequently used types of secured financing. The most common and most simplified is where all receivables are pledged and the borrower can borrow any amount he requires at any given time up to a given percentage — frequently 80% — of eligible receivables.
Factoring is similar to AR financing. But here the “borrower” is not a borrower at all. He sells receivables to the bank. The benefits include: the bank assuming collections, bookkeeping, and correspondence regarding the receivable. There is no borrowing to show on your balance sheet.
Inventory Lien Financing supplements accounts receivable financing very nicely. The bank files a financing statement on the inventory based on the marketability of the inventory. The advantages are similar to those attributed to accounts receivable financing.
Warehouse Receipts Financing is another type of financing secured by inventory except that the bank has control of the security that it normally does not have under inventory lien financing.
Equipment Lease Financing is something relatively new to banks. A bank can only lease personal property — it cannot own and lease real estate, but personal property covers a broad spectrum. Our leasing division has leased everything from computers to airliners. The advantages include the possible favorable appearance of the balance sheet, the tax benefits of depreciation and investment tax credit.
Real Estate Loans provide secured term financing. It is possible to arrange interim financing for construction, but only if an insurance company or other institutional lender agrees to take over the long-term mortgage financing once the structure is completed.
SBA Loans are an option where other sources of financing are not available. One advantage is longer than normal bank terms can sometimes be arranged, but it won’t turn unacceptable bank risks into bank loans.
Conclusion
Tailor your financing carefully to your situation, keeping in mind always the next step as well as the immediate requirement. The more perfectly selected and blended and the more timely applied, the better your money machine will operate. n
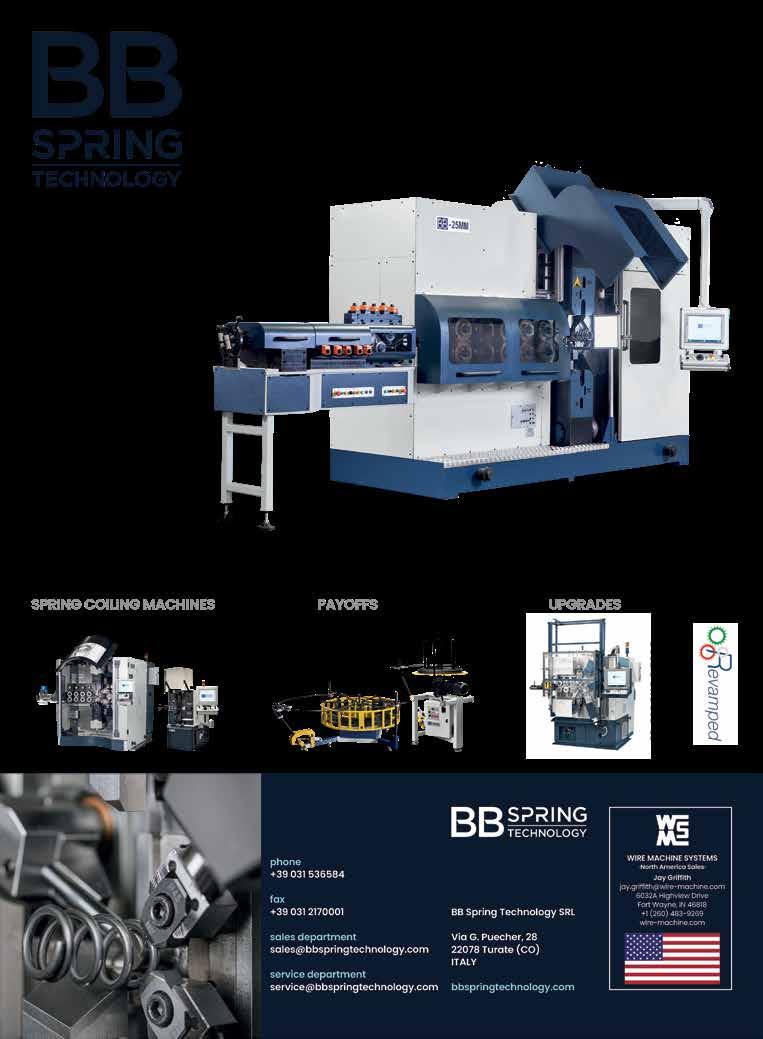
Amstek Metal
Five Questions provides an opportunity for SMI associate members to tell the spring industry about the products and services they offer. In this edition, we talk with Thomas Hunt, Vice President of Sales & Marketing at Amstek Metal.
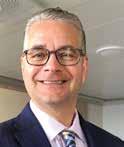
1
Can you tell us about the history of Amstek Metal and the products it offers to spring manufacturers?
Amstek Metal is owned by the Charles G.Stevens Company. Founded in 1898, four generations of Stevens family members have been engaged in the specialty stainless and carbon steel processing and distribution business.
Established in 1987, Amstek Metal is a multi-location service center supplying high-quality engineered strip and wire products to precision springmakers, specialty metal stampers and fabricators.
The most important service we provide our customers is our Amstel Metal team members. We are all committed to providing the best products and services in a timely and professional manner to achieve 100% customer satisfaction.
What role does logistics play in serving spring manufacturers?
4
110
thunt@amstekmetal.com
2
What are the latest trends impacting wire distributors, and what effect is it having on spring manufacturers?
We foresee continuing pressure on both inventories and logistics, which requires additional lead times and supply chain visibility regarding raw material requirements.
3
What types of services do you offer to springmakers?
As a wire and precision slit strip supplier, we work closely with our accredited mills to provide engineered products to precision springmakers and specialty metal stampers that require high-quality, tighttolerance materials to reduce production variations. With our years of experience and internal capabilities, we design specific programs to offer the highest quality processing, dedicated inventories, JIT deliveries, and custom packaging to optimize product flow and efficiencies for our customers.
Successful product development, supply and order fulfillment rely on understanding market logistics. Therefore, we strive to obtain accurate information about material flow from the steel mill to Amstek Metal to the springmaker or specialty metal stamper and, ultimately, to the end-user.
5
Can you tell us about a recent challenge that you were able to solve for a customer?
During the past several years, Amstek Metal has faced many challenges impacting traditional business models. From raw material shortages, escalating commodity prices, logistical bottlenecks, and global political policies, it has been an unprecedented time to supply steel products to our customers. Our best success stories in resolving customer challenges have all had three recognizable elements: open communications, accurate forecasting and detailed, up-to-date supply chain planning. With these tools, Amstek Metal has assisted several customers in accelerating speed-to-market programs critical in obtaining contract parts, assemblies, and essential business. n

Thank You!
SMI is grateful to the sponsors who supported this year’s annual meeting.
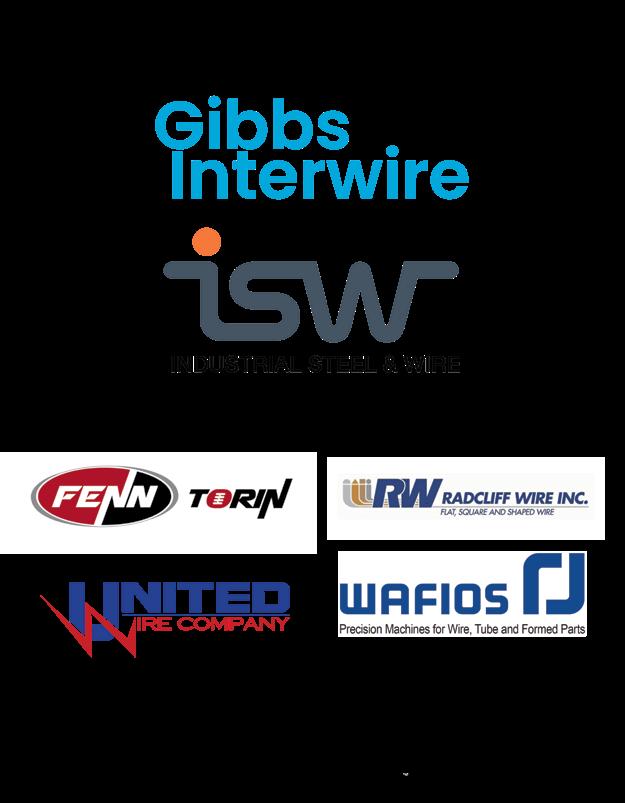
Nepotism Runs Deep: A Profile
of Rick and Randy Richter and R-R Spring
By Gary McCoy, Executive Director
Ronald “Rick” and Randall “Randy” Richter are the proud owners and operators of R-R Spring Corp. in the western Chicago suburb of Addison. With 35 employees and one location, Rick jokes that “nepotism runs deep, as it does at most family companies.”
Rick’s wife Wendy works at the company, along with his son, Ron, Ron’s wife, Krystle and Randy’s wife, Bette, and son, Jake.
The company was started in 1970 by their father, Ron, but the truth is the Richter’s have been in the spring business since 1928. “My great aunts and uncles worked for Illinois Coil Springs Co. at the time,” explained Rick.
“I remember my Uncle Max telling us stories about playing softball in the parking lot. And how the owner of Illinois Coil would come out and say, ‘Today you and you are working.’ This was during the height of the Great Depression.”

“After working there for many years, they decided to start their own spring company along with my grandfather in 1945,” added Rick.
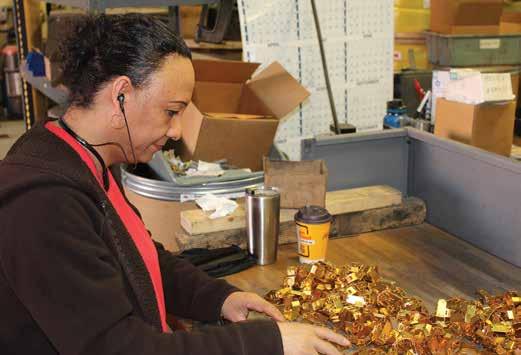
The driving force behind Richter Spring was “Uncle Max” (as everyone knew him) Richter. He ran the company which made springs for automobiles,
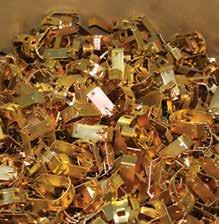
industrial machinery and appliances, until the family decided to sell it due to union issues in 1969. After the older Richter’s sold Richter Spring, it went out of business in 1977.
Their dad, Ron Richter, left Richter Spring shortly before it was sold and started R-R Spring in 1970 with his brother-in-law, John Legrady.
The Origin of the Company Name
An often-asked question, according to Rick and Randy, is the origin of the company’s name. Especially because the brothers’ first names start with R, along with their dad, Ron, and their mother, Ruth.
“That’s kind of a funny story, because my dad incorporated under Richter Industries,” said Rick. “Uncle Max came to visit with a folder marked ‘R-R Spring,’ because my dad was going to lease equipment from him.”
Rick explained that when Uncle Max sold Richter Spring he founded J. M. Engineering, a leasing company specializing in springs, and he leased equipment to many of his former competitors.

“With Uncle Max holding the folder R-R Spring, my dad just went with it as the company name and it stuck right away,” explained Rick.
Uncle Max was a colorful character and a legend in the spring business, according to Rick and Randy. Uncle Max died in 1997 and it is safe to say an entire article could be published about his exploits. “He was so dependable,” said his wife, Jeanette in a Chicago Tribune obituary. “He was a friend, adviser and confidant to so many in the business world.”
The Early Years
Two former employees of Richter Spring joined Rick and Randy’s dad and uncle to help start R-R Spring in a 6,500-squarefoot building in Franklin Park, Illinois. After early success, the company took over the building next door that occupied 8,100 square feet.
Rick and Randy fondly recall going into the factory when they were young. “They had two automatics running, but no wire reels,” explained Rick. “They would lay the wire out in long, straight lengths. When the weather was nice, the wire went out the door and right into the machine.”
In 2001, Ron passed ownership of the company to Rick, who serves as president and Randy, who holds the title of vice president. Ron Richter died in 2007. Their mom, Ruth, worked at the company for nearly 30 years, helping in the office with accounting and bookkeeping. She died recently in 2022.
R-R Spring moved to its current 25,000-square-foot location in Addison in 2006. “We were busting out of the walls in Franklin Park,” explained Rick. “We were here in Addison for about a year before everything tanked because of the Great Recession.”
Despite the challenges, the company survived and both brothers were thankful that their dad had died before the troubles hit.
As the company’s founder, Ron established a culture of excellence and innovation that has driven its success over the years.
“Our dad was very humble,” said Randy. “He learned so much on the technical side from Uncle Max, but he also had a degree in finance from DePaul University in Chicago and was a CPA.”
The combination of technical and accounting skills helped the company thrive.
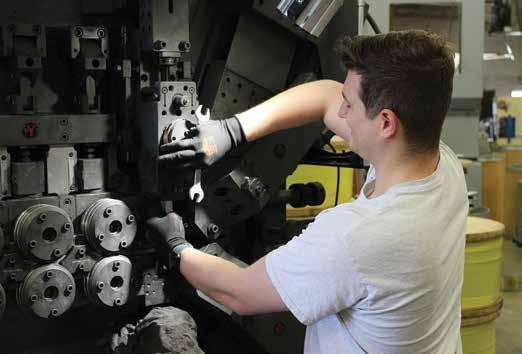
Randy remembers his dad attending an engineering meeting where he was able to display his prowess in the spring business. “They put a problem on the board,” said Randy. “Before the presenter could explain the formulas he had used to solve the problem, my dad had already calculated the answer in his head.”
Where They Thrive
Like other manufacturers in the industry, R-R Spring specializes in compression, extension, torsion, double torsion, spiral torsion, and flat springs. They also produce wireforms and flat forms, utilizing a variety of equipment including fourslide machines. The Richter brothers said they never intended to get into fourslide work, but a customer steered them in that direction, and they have excelled at it ever since.
The roles that the Richter brothers play in the business just happened naturally they say. “But Dad may have pushed us in those directions,” admitted
As the company’s founder, Ron established a culture of excellence and innovation that has driven its success over the years.
A Musher at Heart
Rick Richter is one who loves the outdoors. He’s involved heavily in winter sports such as downhill skiing and he is also involved in dog-powered sports which are affectionately known as “mushing.”
For those not familiar with mushing it is a sport or transport method powered by dogs to pull a sled either on snow or dry land. For Richter it involves skijoring, dog carts, bikejoring and dog sleds.
“I have had a couple of Siberian huskies,” explained Richter. “I am down to one right now, but hoping for more.”
Richter is one of the founders of the Windy City Mushers. “We run our dogs
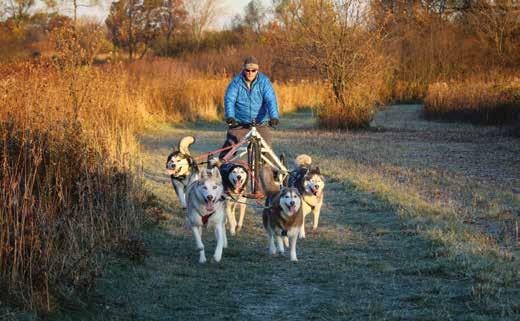
in the local forest preserves and race in a few events around the Midwest every year.”
While the club has about 900 members worldwide, Richter says there’s a core group of about 30 who show up with dogs, some with multiple dogs, at suburban Chicago-area forest preserves.
“Within our group we have members that actually run the dogs,” explained Richter. “A lot of people want to exercise their dogs, but they don’t want to or are unable to run the dogs themselves.”
Richter is not a professional musher. As an amateur musher he has raced
with members of the Windy City Mushers in a number of charity races around the Midwest.
The Iditarod, an annual longdistance sled dog race in Alaska, is something that Richter has never experienced. “It’s an amazing race that I would love to see some day.”
Richter has skied downhill his whole life and enjoys going to Colorado, where he has a house in Fraser. “I am in the process of trying to pass the ski bug to my 5-year-old granddaughter,” said Richter.
When the weather turns warm, Richter says he heads into the mountains where it is cooler to hike.
The one thing Richter doesn’t do is ride a motorcycle. He leaves that up to his brother Randy, who owns a Harley.
Randy used to ski more until his wife suffered a knee injury. Like Rick, Randy enjoys backpacking and hiking in the mountains and riding his electric bike. Randy has a lot in North Carolina that he and Bette hope to build upon someday.
The Windy City Mushers were featured in a 2021 article by Elisa Shoenberger. (bit.ly/mush9-21)
An episode of a podcast called “It’s All Good — A Block Club Chicago Podcast” featured an interview with Shoenberger that includes comments from Rick Richter. (bit.ly/mush11-21)
“What I have learned over the past 45 years is that business is in constant change, and you need to keep up.”
Rick with a laugh, “and we just never realized it.”
While Randy is more involved with what goes on the shop floor and knows the machines better, Rick is more involved in the finances and operations of the company.
“We talk to each other all the time about what goes on here,” said Rick.
“I’ll be talking to a sales rep, and they’ll say, ‘Will you tell Rick about this,’” said Randy. “I usually tell them: ‘Rick already knows.’”
Rick says, “We’ve kind of taken different roles in the business, but we sit in our conference room almost every day and have lunch with everybody. As you can imagine, we start kicking ideas off each other all the time.”
Industry Involvement and Family
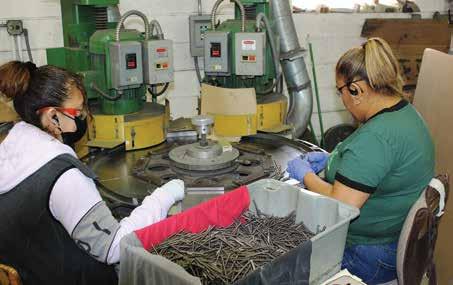
Rick is a former SMI board member and CASMI president. Randy had the desire to serve, but family obligations made it difficult to volunteer time outside the business.
As mentioned earlier, Rick is married to Wendy who works at R-R Spring with their son, Ron, and his wife Krystle. Rick and Wendy have a son Matt, who earned a master’s degree in music and owns a music school in Denver. Their youngest daughter, Jessica, lives in the Chicago area. She has a degree in English and works in the marketing department of a well-known company.
Randy and his wife, Bette, who works off-site in accounting for R-R Spring, have three children. As mentioned previously, Jake works in the business on special projects. “He loves to learn new
things,” said Randy. Jake and another employee at R-R Spring are currently taking classes to become black belts in lean manufacturing.
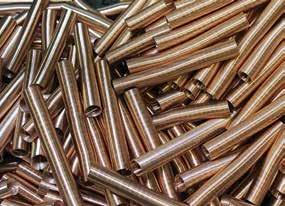
Their middle son, Eric, is a chef. He has taken an acre of land at the farm where Randy and Bette live in Maple Park, Illinois, and dedicated it to no-till organic farming. Their oldest son, Randy, works as a CPA for Moderna in Maryland after a stint at PwC.
Between next-generation family members Ron and Jake Richter, right now Ron seems to be the heir apparent to run the company someday. “Time will tell,” says both Rick and Randy.
An Evolving Industry
The spring industry has been good for the Richter family. “What I have learned over the past 45 years is that business is in constant change, and you need to keep up,” admitted Rick. “I look back on how
“We always say we are extremely flexible, and we can be accommodating where a lot of larger companies can’t be. So that’s an advantage we have.”Working at the grinder is Celia Ramos (left) and Judith Magana.
Rick said it was common to once say that springs were 90% physics and 10% black art. “I think that has changed with the advancement in spring programs to 95% physics and 5% black art. So, we seem to be going in the right direction.”
For Rick, it all comes down to, “Never stop learning.”
Both Rick and Randy are optimistic about the future of the industry. Rick admits that he is an optimistic person by nature, and he believes the future of manufacturing is bright in the U.S. “I think we’ll be here for a while. I see things continuing to improve as far as technology, especially as AI (artificial intelligence) becomes more prevalent.”
They both marvel that they now have a collaborative robot (cobot) on the factory floor fitted with an arm that takes stuff off a coiling machine and packs it into a box.
Rick and Randy both believe that in the future, the industry will see less and less family-owned businesses. They see being family-owned as an advantage, says Rick. “We always say we are extremely flexible, and we can be accommodating where a lot of larger companies can’t be. So that’s an advantage we have.”
Disc
58 | SPRINGS | Summer 2023
Certified
to
At Anchor Abrasives we specialize in the design and manufacture of resin, epoxy and oxychloride bonded nut inserted discs and cylinders...plus centerless and rollwheels.
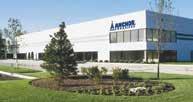

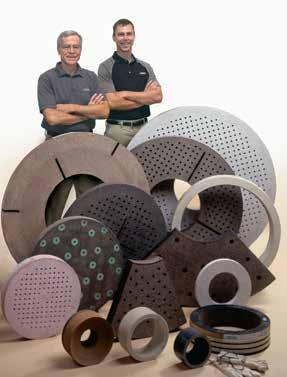
The Power of Potential
Reviewed by Phil SassoIn 2009, Andrew D’Eri graduated high school. It was a time of sunshine and rainbows for his classmates — the future was limitless. But Andrew’s father, John D’Eri, saw a cloudy and perhaps even dreary life for his son. That is because Andrew had autism.
John decided to find a way to build a business to provide a future for Andrew and others like him. So, in 2012, he and his younger son, Thomas D’Eri, bought a struggling carwash and built Rising Tide, a for-profit company that employs a team of 80 percent people with autism and 20 percent nonautistic workers.
In his book “The Power of Potential: How a Non-Traditional Workforce Can Lead You to Run Your Business Better,” author and social entrepreneur Thomas D’Eri shares the journey he and his father traveled to build Rising Tide.
The book encourages readers to rethink how they interview, train and build their business in a way that opens doors for a broader spectrum of people. He also challenges business leaders to seek excellence. “Most businesses don’t struggle because they suck,” he writes. “They struggle because they’re average, and average isn’t good enough.”
Attendees at the April SMI 2023 Annual Meeting in Orlando had the privilege of meeting Thomas and his brother Andrew. As the opening speaker, he shared his “The Power of Potential” presentation with an engaged audience.
After the presentation, I shook their hands, took photos and thanked them for making a difference.
“While Andrew was among the 31 percent of children with autism who have intellectual disabilities, employment prospects for anyone with autism are not very good,” writes Thomas.
“Every time I came home from college, I felt a lump rise in my throat when Andrew and I hugged,” Thomas writes. “I became interested in business and, specifically, social enterprise, but I had no plans to dedicate my career to empowering adults with autism.”
Then, one day John made his pitch to Thomas. Together they would build a business around employing people with autism. It might be a carwash or perhaps another business.
“Worst case scenario, the business fails,” said John, who was willing to put up to a million dollars behind his conviction. “Best case scenario, Andrew has a future, we have a great business, and you’ll be invited to teach MBAs instead of wanting to get one yourself.”
No one had done what they proposed. There was no roadmap.
The book chronicles the steps and missteps John and Thomas took to build their prosperous carwash business by employing “a very specific talent pool that most people overlooked.”
In the book’s opening, Thomas tells his family’s personal story. Then, he relates the advantages of hiring individuals on the spectrum with the unique skills and perspectives they bring to the workplace. He also debunks misconceptions of low productivity and reliability.
After the opening, the book breaks into two parts: The Four Problems and The Four Wins.
In The Four Problems, Thomas discussed the practical aspects of a nontraditional workforce. He provides unique strategies for recruiting and training a neurodiverse crew. He also explains how he has created a culture that values diversity and promotes personal growth.
In The Four Wins, he concentrates on the benefits of a nontraditional
workforce. Social enterprises focused on diversity and inclusion, like Rising Tide, positively impact their local economy and community while increasing awareness of issues like neurodiversity.
In 2012, that struggling car wash the D’Eris’ bought served only 35,000 vehicles. By 2021 it was profitable, washing more than 170,000 cars a year. Today, Rising Tide employs over 100 people at three locations in the greater Miami area.
“The Power of Potential” is worth reading. It is relevant to springmakers or any business considering the benefits of building the diversity, equity and inclusion aspect of their workforce.
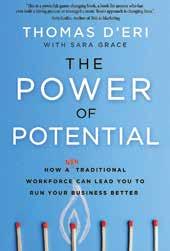
“We didn’t succeed despite our nontraditional workforce — we succeeded because of it,” Thomas writes. “Today, I’m convinced what we learned in the process can help any business escape average.” n
Have a favorite business book you would like to tell us about or review? Send your suggestions to Springs magazine editor Phil Sasso at phil.springs@sasssomarketing.com.

A THREE YEAR WARRANTY = OUTSTANDING QUALITY!
A&D Trading LLC now offers a THREE year warranty for all mechanical parts and machinery controller, all servo components have a TWO year warranty! Our product lines are second to none world wide!
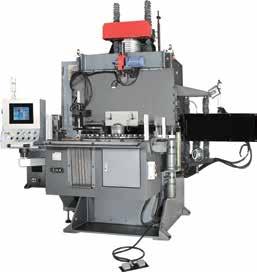
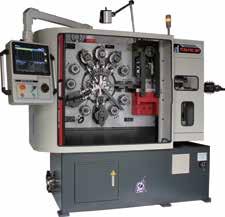
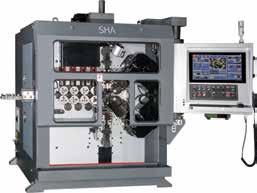

(Wire range 0.5-20.0mm)
(Wire range 0.12-6.0mm) Max Axis: 16
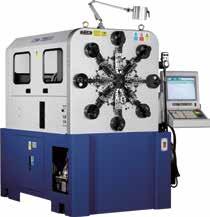
(Wire range 1.0-30.0mm)
Max Axis: 10
(Wire range 0.1-3.2mm)
(Wire 0.2-5.0mm, strip 2.0 thickness x 50mm width)

Progress Continues on Connecticut Manufacturing Center
By Gary McCoy, Executive DirectorAnew manufacturing center is under construction on the Tunxis Community College campus near Bristol and the epicenter of Connecticut spring manufacturing. Appropriately, the facility is located on Spring Lane in Farmington, Connecticut.
Along with Lucas Karabin of Acme Monaco and Al Mangels of Lee Spring, I had a chance to tour the facility in March with Rich DuPont, the interim associate dean of advanced manufacturing for the northwest region in Connecticut. DuPont is part of the team at Tunxis Community College working on the buildout and development of the facility. DuPont has been working closely with Karabin and Mangels to include a section of the facility to teach spring coiling. He also hopes to add classes on wireforming and stamping. DuPont meets regularly with the NESMA committee responsible for workforce development.
The facility is one of 10 programs in Connecticut, and the 40,000 sq. ft. building makes it among the five largest in the state. The facility will initially utilize 15,000 sq. ft. of space dedicated to a hands-on, state-of-the-art manufacturing lab with classrooms and training areas for manual machining, CNC machines (both mills and lathes), surface grinding, wet jet cutting and mechatronics. In the future, they hope to add areas for automation and robotics (cobots and industrial robots).
“With its central location, the stateof-the-art facility on Spring Lane will not only support traditional manufacturing and aerospace, but it also establishes a unique identity to serve spring manufacturers,” explained DuPont. He says the
spring manufacturing emphasis makes this facility stand out from the rest of the centers scattered throughout the state.
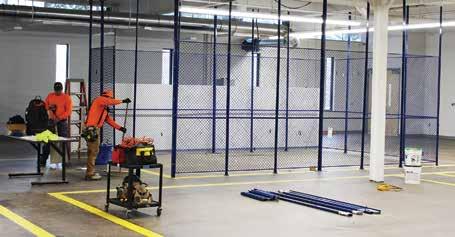
A Sustainable Path to Employment

DuPont says the program is designed to offer multiple pathways to employment. “With the demand so high for these skillsets for manufacturing in Connecticut, this program is a priority,” said DuPont. “For those interested, we offer a sustainable path to be prepared as possible for gainful, sustainable employment opportunities in manufacturing”
The program focuses on a 10-month, two-semester manufacturing certificate program based on hands-on training. The program does not include any humanities or electives. Classes include credit and non-credit classes in math, blueprint reading, CAD, introduction to machining, manual machining, CNC machining, safety and quality — all directly related to manufacturing.
DuPont says this is an ideal program for those who want or need to quickly
get to work in manufacturing and also opens up opportunities for continuing education.
“A person who completes the program can earn up to 33 credits, which is basically half of what that same student would need for an associate degree in either advanced manufacturing machine technology or advanced engineering technology offered via our College of Technology.”
DuPont says those credits would transfer seamlessly to a bachelor’s degree program in those same two disciplines.
“The program helps those who are looking for a better place in life, respective to their career path,” says DuPont. “They are choosing a certificate program so they can get to work and continue improving.”
Once a graduate secures employment in manufacturing, DuPont says many will return for additional training to further develop their skills.
“These programs are also designed to support a high school pathway,”
explained DuPont, “that starts during a student’s junior year when they dual enroll. By the time they graduate as a senior, they can earn up to 17 credits or up to half of the certificate program. Post graduation, one semester later, they could potentially complete the certificate.”
DuPont says those who complete half the program in high school “are much more job-ready than they would be otherwise. For those who grow up in underserved communities, oftentimes this is a need, a reality, that this program becomes the path for them to take part in and does, in fact, change lives.”
Others Who Can Benefit
The program also targets adult learners, some of whom are looking to reposition their careers. “Especially someone who has lost a job in another career and sees the opportunities available in manufacturing.”
For instance, DuPont says they had a Wall Street investor who simply burned
out. So he wanted to try manufacturing as an alternative career. He completed the program successfully and has done very well in his new career in manufacturing.
He says they also work with those who are seeking a second chance and women in manufacturing, “which is a big push for us right now. Women are really good at critical thinking, which is important in manufacturing.”
DuPont says all their programs are driven by industry. “We have industry advisers who meet with us regularly to provide input on what they need,” said DuPont.
He says that’s why he works closely with organizations like NESMA to make
sure the program is meeting the real needs of manufacturers. “I very much enjoy this because they are a group that is on top of what is needed for curriculum.’
DuPont and the team at Tunxis are working toward finishing the Spring Lane facility in Farmington, with an opening
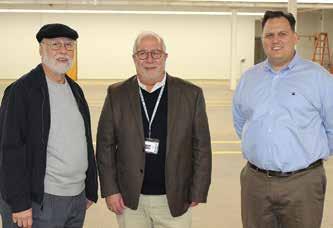
Machines
• Fenn (TORIN)
• Itaya
• MEC
• Samuel
• Sleeper & Hartley
• Additional Machines
– A.I.M.
– ASAHI
– Bamatec (Schenker)
– Baird
– Bobbio
– E.N. Machine (Ming)
– Simplex
– Wafios
Line of carbide and steel tooling include…

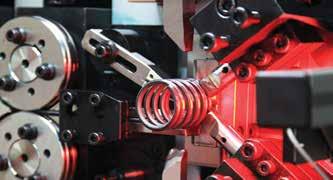
• Arbors/Mandrels
• Block Guides
• Body Tools
• Caps
• Coiling Tools
• Cutting Tools
• Feed Rolls
• Guides/Liners
• Pencil Arbors
• Pitch Tools
• Quills
Magazine Committee Changes Name, Broadens Mission
Keith Porter Jr., chair of the SMI magazine committee, announced at the SMI Annual Meeting in April that the group has transformed into the communications committee. The name change, unanimously adopted by the SMI board of directors, reflects the expanded focus by the committee to utilize various channels, from the print and online magazine to modern social media platforms, email blasts, a website, and even a new soon-to-be-launched podcast.
“When SMI started Springs in 1962 that was the primary vehicle for communicating information to members and the spring industry,” said Porter. “The name change
better aligns with the way members now engage with information and the committee’s mission to provide a comprehensive range of resources for SMI members and springmakers. In addition, by embracing multiple communication avenues, SMI aims to cater to its members’ diverse preferences and needs, ensuring they receive valuable information in the format they prefer.”
The revamped communications committee will continue to provide input to SMI staff so the spring manufacturing community receives industry insights, best practices and technical information. The spring industry will continue to access in-depth articles, expert interviews

SMI Hosts 2023 ISO/TC 227 Springs Meetings in Las Vegas
Under the auspices of SMI, the U.S. will host the 2023 ISO/TC 227 Springs meetings at the South Point Hotel, Casino and Spa, Las Vegas, Sept. 14 -15, 2023. The resort is just minutes away from the famous Las Vegas Strip in the heart of the premier southwest Las Vegas valley.
The SMI executive and board of directors will meet a day prior on Wednesday, Sept. 13.
SMI also will host a special event at The Mob Museum, officially the National Museum of Organized Crime and Law Enforcement, Thursday, Sept. 14. The history museum, established in 2012 near the famous Fremont District, features artifacts, stories, and history of organized crime and the actions and initiatives by U.S. law enforcement to prevent these crimes.
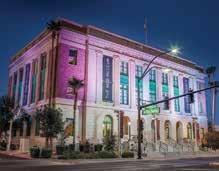
In 2022, more than 28 people from 10 contributing participating-member countries (China, Germany, Italy, France, United Kingdom, United States, Japan, Malaysia, Thailand, and India) participated in the virtual meeting. The 2023 event will mark the first time ISO/ TC227 has been held in person since the COVID-19 outbreak in 2020.
and informative features through Springs magazine, but SMI will now utilize the power of social media platforms to engage a broader audience and foster meaningful discussions within the industry.
A notable addition to the committee’s repertoire is the coming launch in the fall of the “Springs Are Everywhere” podcast hosted by SMI Executive Director Gary McCoy. The podcast will be a dynamic platform for industry professionals to share their expertise, success stories, and innovative ideas. Those who engage with the podcast will gain valuable insights to expand their knowledge and stay connected with the community.
SMI serves as the technical advisory group to the American National Standards Institute (ANSI) for ISO/TC227. The role of the U.S. delegation is essential to ensure that the interests of American springmanufacturers,designersandconsumers are represented in international standards development.
The U.S. delegation is led by Tom Armstrong, retired chairman of Duer/ Carolina Coil, and Rick Gordon, SMI’s technical director.
Workinggroup4(WG4)isscheduled to meet Thursday, Sept. 14, followed by a plenary session on Friday, Sept. 15. SMItechnicalexpertsbringmanyyears ofmanufacturingexperiencetotheISO/ TC227workinggroup4thatisdeveloping new standards.
Anyone interested in participating in the ISO standards process should contact Rick Gordon at c.richard.gordon@gmail.com.
Tentative List of Safety Webinars 2023
Join us as Dr. Laura Helmrich-Rhodes, SMI’s regulations compliance consultant, explores important safety topics of interest to all spring manufacturers. These webinars are free for SMI members, the
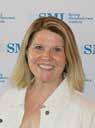
non-member fee is $149. To register contact Gaby Carrasco at gaby@smihq.org or phone 847-857-6432
Presenter: Dr. Rhodes conducts safety audits and provides employee training to member companies as a part-time consultant. She is a full-time tenured Associate Professor at Indiana University of Pennsylvania Safety Sciences Department where her teaching assignments currently focus on OSHA compliance, adult education/training, and oversight of internship/cooperative education experiences. Dr. Rhodes’ work experience includes three global commercial insurance companies, PA/ OSHA Consultation, and private practice. Her doctoral dissertation focused on surveys of human resource (HR) professionals about their safety obligations. She is a board certified safety professional in Comprehensive Practice by exam with over thirty years of industrial safety experience.
Completion certificates are available upon request (often these are used for safety committee state-required training or documenting professional development)
Thursday, July 6, 2023, 1 p.m. EST
OSHA Inspection-Are You Ready?
Audience: Owners, HR managers, safety professionals and department managers (only)
Thiswebinarwillreviewthestep-by-step processofaninspectionandreviewyour rightsasanemployerintheprocess(this is not the “OSHA Top Ten Most FrequentlyCited”webinar).Thediscussion
will focus on Federal inspections. Some of the information is similar to staterun OSHA programs. Materials you can implement will be provided.
Friday, August 18, 2023, 1 p.m. EST
Basic Accident Investigation — Not Just A Reporting Process
Audience: Owners, HR managers, safety professionals and department managers (only).
Even some seasoned company owners, HR, and safety professionals are surprised to find that accident investigation and accident reporting are NOT the same! Most are simply reporting accidents. Also, many company owners do not realize that strong, accident investigation processes (by trained supervisors) can reduce the potential for workers’ compensation fraud significantly. Learn how to get to the root causes of property damage, employee injuries and even near misses. The presentation also covers identifying causes and implementing strategies to prevent event reoccurrences.
Tuesday, September 12, 2023, 1 p.m. EST Safety Lessons for the Human Resources Professional — The Research and Practical Impacts Audience: Anyone involved with hiring, interviewing, developing, and leading the workforce.
This webinar is designed for the person handling HR in your facility. This will be geared toward both the seasoned HR professional with a Society of Human Resource Managers (SHRM) designation to the newly assigned HR person looking to expand their understanding of the HR function. This webinar is based on experience as well as research data. Key crossover safety topics and areas where HR pros have identified where they fall short will be emphasized as well as resources to support their job task. On-going mentoring for new HR and safety professionals is anticipated.
Springs Launches “Podcast Picks”
We’re unveiling a new “Podcast Picks” section in this issue of Springs (page 67). This new content shares interesting business podcasts that provide valuable insights, strategies, and inspiration for springmaking leaders.
As podcasts grow and become a deeper part of the fiber of our culture, we want to help readers select from the myriad of choices available. In each issue of Springs, a staff member will review a specific business podcast episode.
Statistics reveal that there are 464.7 million podcast listeners globally as of 2023. It is predicted that this number will reach 504.9 million by the end of 2024. Overall, the podcast industry market size is 23.56 billion.
For our premiere edition, Gabriela “Gaby” Carrasco, assistant editor and SMI communications and administrative coordinator, reviews a podcast by SMI 2023 Annual Meeting speaker Charles E.Gaudet II. In the episode reviewed, Gaudet talks with Aaron Bare, a serial entrepreneur and author of “Exponential Theory: The Power of Thinking Big” about the impact of purpose.
Calendar of Key Events for the Global Spring Industry
2023
Sept. 14-15
ISO/TC 227 Springs Meetings
South Point Hotel, Casino and Spa
Las Vegas, Nevada
2024
April 6-9
SMI Annual Meeting
Loews Coronado Bay Resort
Coronado, California smihq.org
April 15-19
wire and Tube
Düsseldorf, Germany wire-tradefair.com tube-tradefair.com
Oct. 2-4
SpringWorld Expo and Symposium
Donald E. Stephens Convention Center Rosemont, Illinois casmi-springworld.org smihq.org
2023 Spring Design Training Schedule
Send Us Your News
SMI members receive priority placement for their product, company, personnel and events announcements in the magazine. Your news releases should be roughly 50 to 100 words and may be accompanied by color photos (high-resolution .JPEG photos at 300 dpi preferred). Send to gaby@smihq.org.
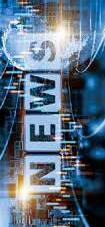
Your source for the best in close tolerance strip and edged products

strip: cold rolled high carbon/pre-tempered spring steels, coated, low carbon stainless, copper based alloys and aluminum ultra-narrow width, close-tolerance slitting edging: round, square, semi-round, deburred, custom, etc
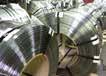
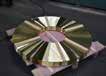
oscillate (traverse) and ribbon wound coils
ISO 9001: 2015 certified 43 years servicing the industry

tel. 847.537.2881 toolkinginc.com

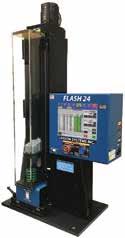
Wheeling (Chicago), Illinois 60090 USA
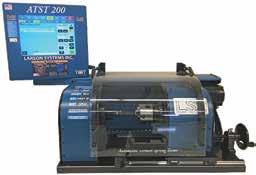
SMI Survey Schedule: An Opportunity to Benchmark with Your Peers



SMI regularly surveys its members to help them understand how they are doing relative to others in the industry.
is important when SMI conducts each survey. No company data is ever shared with SMI members or SMI itself. n
Here’s the schedule of surveys for 2023 and into 2024.
MAPES FINE MUSIC WIRE




Call for special wire needs and solutions, including restricted tensiles and size tolerances.














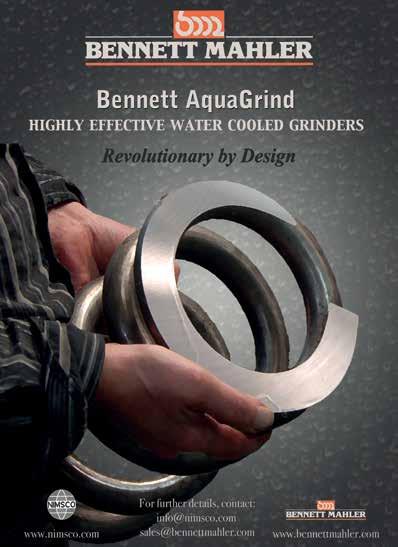
Wire diameter .063" – .006" / 1.6 mm – .15 mm


Coatings Phosphate, Tin Zinc, Tin
JISG 3521 SWA, SWB JISG 3522 SWPA, SWPB Military specifications Others, inquire
MAPES PIANO STRING COMPANY P.O. BOX 700, ELIZABETHTON, TENNESSEE 37644
9001: 2015



QMS


Mapes: quality that’s never out of tune.
Podcast | Beyond 7 Figures: Build, Scale, Profit
Episode | Exponential Theory: Embracing Failure, Learning and Thinking Big in Entrepreneurship
Length | 28 minutes
Ioften reflect on the lack of time to focus on personal growth. With work, family, friends and life in general, spending time reflecting on personal and business goals is difficult. Podcasts allow you to learn something new, often while you’re doing something else. All you need is a phone, computer or smart speaker and some great recommendations. This is one recommendation.
In this episode, Gaudet and Bare discuss how exponential theory helps entrepreneurs make decisions that lead to more than just a “seven-figure income.” One takeaway is that you only fail when you do not learn from the outcome. It is easy to be discouraged or give up when faced with challenges, but approaching problems with a positive mindset can turn boulders into pebbles.

Editor’s Note: Welcome to “Podcast Picks,” a new section in Springs that explores podcast episodes featuring interviews, discussions and presentations on business topics of interest to springmakers.


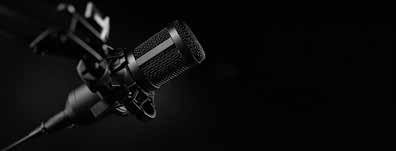
Our mission: curate and review podcast episodes that inform, educate and empower.
You might recognize Charles Gaudet, CEO of Predictable Profits and host of the podcast “Beyond 7 Figures: Build, Scale, Profit” as a speaker at the 2023 SMI Annual Meeting. In each podcast episode, Gaudet interviews executives and entrepreneurs who share insights on business models that go beyond seven figures.
This episode features Aaron Bare, author of “Exponential Theory: The Power of Thinking Big,” a book about exponential leadership and problem-solving.
Gaudet and Bare agree exponential leaders focus on greater purpose versus seeking short-term financial gain. By making decisions based on a longterm purpose, they achieve exponential success. Exponential leaders also invest emotionally in their business mission, values and vision. This sets them apart from any other managers.
Whether you are commuting to work or on an evening walk, this episode provides a brief introduction to exponential theory and challenges listeners to view obstacles as opportunities for learning and growth. n
In the hands of skilled craftsmen, our steel becomes the parts, components and products that make the world turn. For over 65 years, fabricators and manufacturers big and small have trusted Admiral Steel to help them leave their mark on the world. For any size order from 10 lbs. to 10,000, you get first-class quality, on-time delivery, and personalized service from Admiral. Contact us for a quote today!
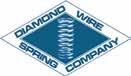
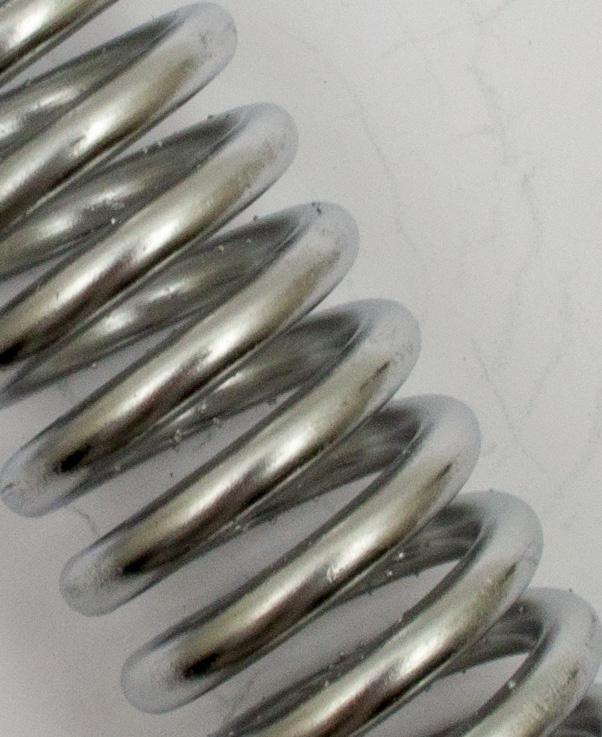
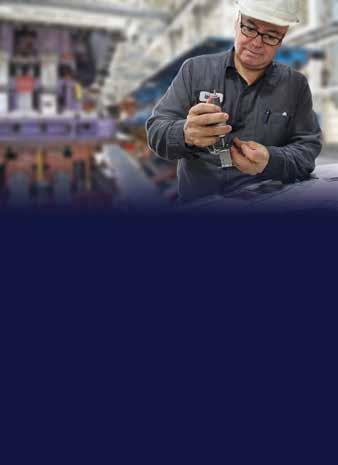
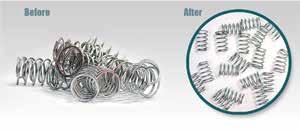
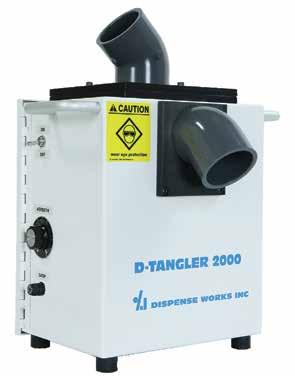

Konica Minolta Introduces CoboVox
Konica Minolta Business Solutions
Europe GmbH’s innovation team has globally launched CoboVox, a voiceenabled programming and control application for robots. This platform, certified by Universal Robots and compatible with most end effectors, allows operators to effortlessly control collaborative robots using natural voice commands and
simple language instructions. CoboVox is accent-agnostic and even recognizes synonyms of common terms.
Unlike alternative methods such as 3D vision systems, simulation-based offline programming, and machine learning, CoboVox eliminates the complexity and costs of programming robots. It can be installed and voice-activated
New HTC28CP Six Axes CNC Spring Coiler
HST and Forming Systems, Inc. have launched the new HTC28CP, six axes CNC spring coiler with a wire range of 0.8mm – 3.0mm (.031” - .118”).
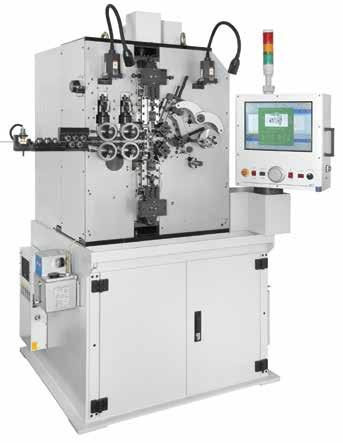
The HTC28CP includes a programmable servo central slide that moves into position automatically according to the program when the O.D. is changed during production. This provides setup flexibility and strengthens the cutter structure.
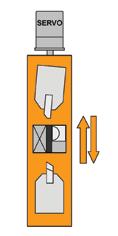
Optimized auto lubrication and pretension devices are available options along with SDR/SDL. The coiler is ready for Industrial 4.0 (optional WF3).
For more information, visit formingsystems.com.
New Products
By Gabriela Carrascowithin minutes, enabling staff of all skill levels to operate without extensive robot programming experience. Recent tests with Universal Robots show CoboVox can reduce programming time up to 43%.
CoboVox offers manufacturers significant efficiency and cost savings, particularly in labor-constrained markets. For more information, visit www. cobovox.com.

Kassow Launches KR1805 Cobot With Seven Axes

Kassow Robots has introduced the KR1805 industrial cobot to North America. Designed for precise and repetitive tasks like machine tending, assembly, quality assurance and pick-and-place operations. It features seven axes, a 5 kg payload and an 1800 mm reach.
The KR1805 boasts the largest reach among their high-performance cobots, making it suitable for various industrial applications, said Dieter Pletscher, global sales manager at Kassow Robots.
The unique seventh axis enables continuous dispensing, welding and material removal at various angles without
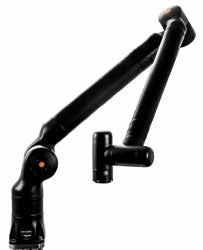
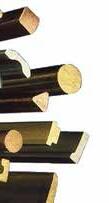
reorientation. This additional axis also provides a compact footprint (160 x 160 mm), enhancing maneuverability and expanding the range of motion for tasks such as bin picking and labeling.
The KR1805 safely collaborates with humans after a site-specific safety assessment. Weighing just 38 kg, it is portable for flexible deployment within a facility. Kassow Robots’ intuitive graphical user interface, similar to a smartphone, enables operators of all technical skill levels to program the cobot efficiently.
For more information, visit www. kassowrobots.com. n
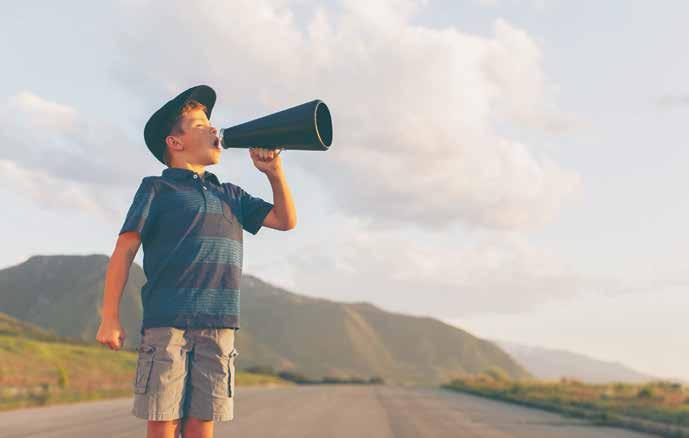
Joseph DeVoe • Plymouth Spring
Name: Joseph DeVoe.
Nickname (if any): Joey, Coach Joe.
Company name and city: Plymouth Spring, Bristol, Connecticut.

Brief history of your company: Plymouth Spring has been in the business of manufacturing compression springs, wireforms and metal stampings since 1959.
Job title: Vice President of Manufacturing. Spring industry affiliations (Names of organizations you’re active in and title of elected position, if any): Member of the SMI Avant-Garde group.
Birthplace: Bristol, Connecticut.
Current home: Wolcott, Connecticut.
Family (spouse, children, pets, etc.): My wife, Jessica, and I have three energetic boys, Cayden (9), Mason (7), and Logan (4).
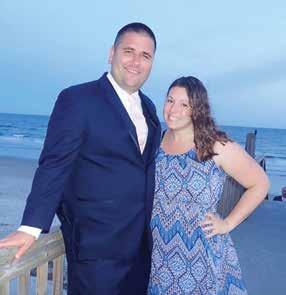
Favorite food: Seafood and chicken wings (not together).
Favorite song/musician: Aaron Lewis.
Hobbies: I like to take my boys fishing and do other outdoor activities with them. I am the president of our town’s baseball association and coach at least 2-3 teams a year.
Favorite places: By the water, whether it’s a pool, beach or lake
Best times of my life: The little moments in life that don’t mean much, sharing those moments with family and friends and enjoying the memories that come out of them.
A really great evening to me is: A movie night with the family with pizza and ice cream.
The one thing I can’t stand is: People who think Coke and Pepsi are the same thing.
My most outstanding qualities are: I’m always willing to help, whether it’s at work, with family or with sports. I would rather be part of the solution than the problem.
I knew I was an “adult” when: I got my first heating bill for my first apartment. If I weren’t working at (Plymouth Spring), I would like to: Own a bar and restaurant.
I wonder what would have happened if: I didn’t come to work at Plymouth 10 years ago.
Role models: David DeVoe.
I would like to be remembered in the spring industry for: Providing a stable working environment for our staff to excel in life. The people are the ones who make our business successful.
But people will probably remember me for: Being Dave’s son.
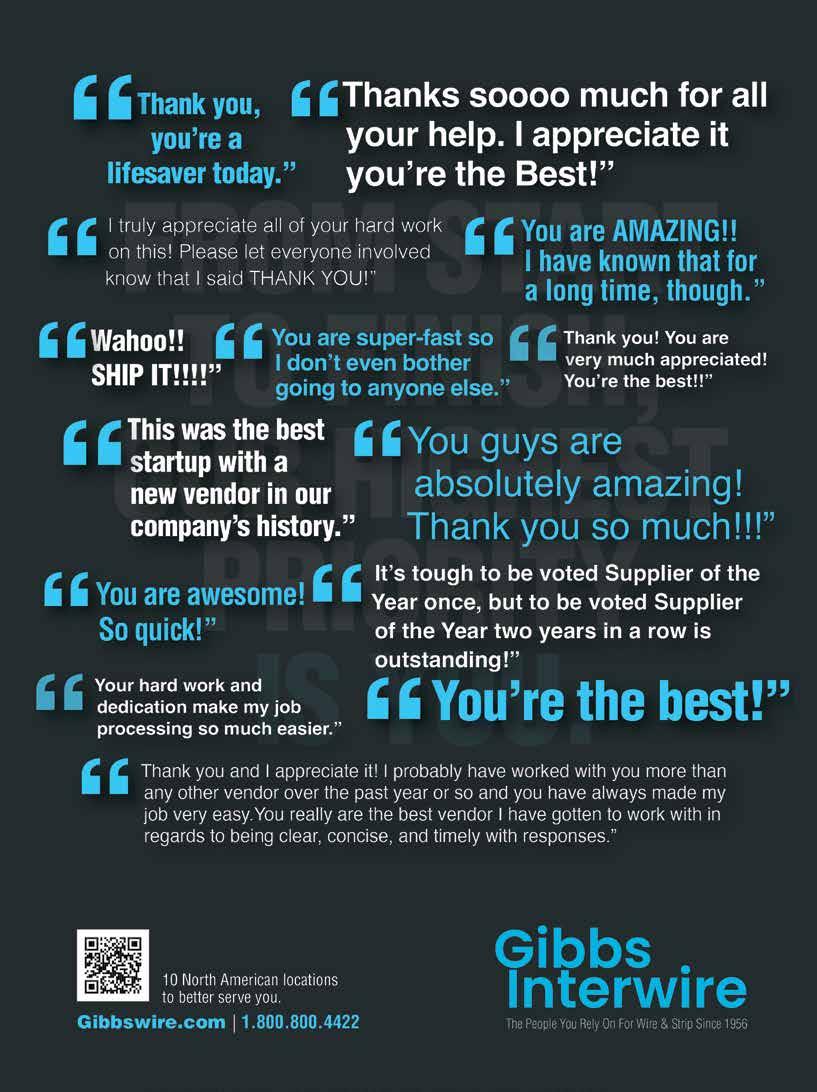
