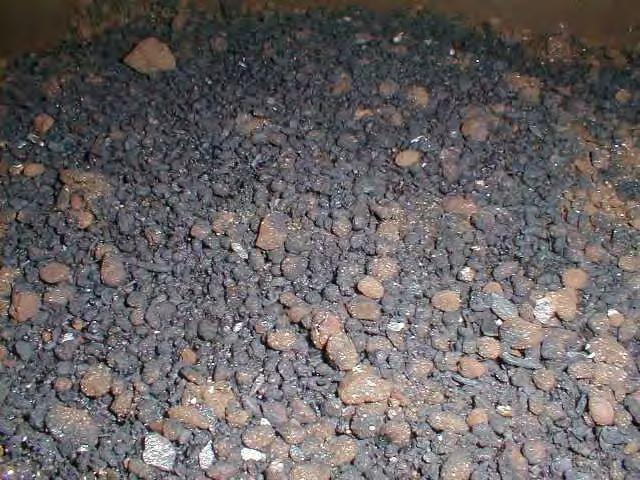
8 minute read
International Industry
Liberty Ostrava launches tender for hybrid furnace
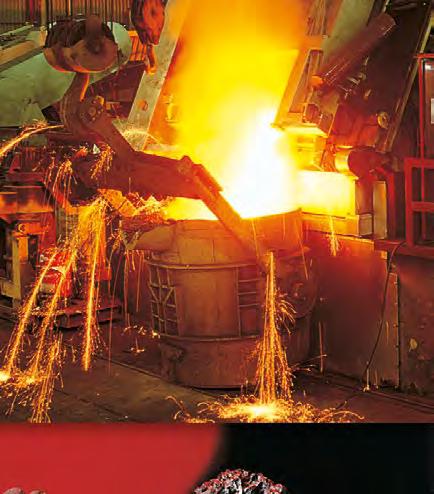
Advertisement

Liberty Ostrava has launched the public tender to procure two hybrid furnaces, Kallanish learns from the Czech steelmaker. The two hybrid furnaces will replace the plant’s existing four tandem furnaces by 2023, providing the same combined production capacity of 3.5 million tonnes/year „This is a major step in Ostrava’s journey of transformation towards new low-carbon technologies in line with the group’s overall target to become carbon neutral by 2030,“ said Sanjeev Gupta, executive chairman of Liberty Steel when announcing the tender in Ostrava on 10 November. According to Liberty, the two hybrid furnaces will be the first of their kind in Europe. The modern hybrid technology will have a significantly lower environmental footprint, reducing particulate emissions by 60% by 2023 due to a new dedusting plant. Once the 400kV electricity line is installed by 2025, carbon emissions will be reduced by 50% as the furnaces will be able to use 70% scrap. Full carbon neutrality will be achieved once the plant has transitioned to using 100% scrap or captures and recycles the CO2 from its primary units while offsetting residual carbon produced through GFG’s peat restoration project at JAHAMA Highland Estates in Scotland. Liberty plans to invest a total of €750 million in the development of its Ostrava steelworks over the course of the next ten years. In addition to the modernisation of the steel shop the transformation will also include an extensive modernisation of the steel rolling mills, which will improve the quality of steel and expand the product portfolio with high added value products.
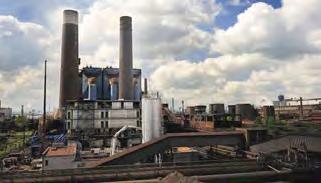
NLMK Lipetsk launches anhydrous cooling system for blast furnace slag
The system will enable it to reduce hydrogen sulfide emissions in the corresponding area by 3.5x and keep the smell from this chemical compound to a minimum, the company states. The implementation of the complex marks the full transition of the mill’s blast furnace shop No. 1 (three blast furnaces) to dry slag cooling technology. The new system completely eliminates the need to use water. Advanced excavators will be used for slag handling and loading, capable of working in high temperatures and with increased productivity. Investment in the project exceeded RUB 2 billion ($26 million).
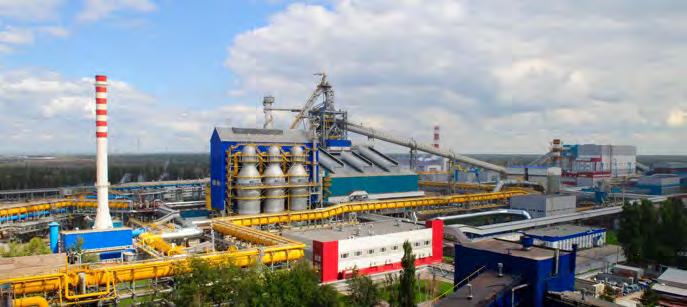
Americas
USA
Andritz Herr-Voss Stamco, a member of international technology group Andritz, has commissioned a new cut-
to-length line delivered to Rolled
Alloys for their facility in Fairfield, OH, USA. The new line processes 0.125’ x 48’ wide stainless steel and nickel alloys and has an incoming coil capacity of 20,000 lbs. Its “backbone”, Andritz says, is a precision roller-leveler technology. According to this, the line includes two precision levelers, both with the manufacturer’s “Punch-N-Go” leveler control system. The line also comprises a precision roll feed system coupled with a high-speed shear that can cut both long and short blanks.
AIC supplied and commissioned the process automation solution for the rolling mill of CHS Chicago Heights Steel in Chicago heights, IL, USA. The project included the automation system and equipment for the revamping of the rolling mill, starting rougher group and going through the takeout of the bar on the cooling beds. AIC was also involved in installation supervision and commissioning phases within the project schedule, which took place in October 2020.
Asia
CHINA
Baowu Steel Group (former Baosteel) and Shanghai Court Roll Surface Treatment entrusted the machine builder Heinrich Georg with the en-
gineering and realisation of five
roll-grinding machines of the manufacturer’s ultragrind type. Background was the planned plant expansion of the Zhanjiang site in Guangdong province with the target to build the world’s most modern CRM roll shop. For both Baowu Steel and Shanghai Court the de-
Georg’s “Smart Control”-technology in operation cisive criteria for placing the order was Georg’s latest technology “Georg Smart Control”. It is based on the machine control system “Sinumeric One” by Siemens and integrates a digital twin in the company’s roll grinding machines.
Europe
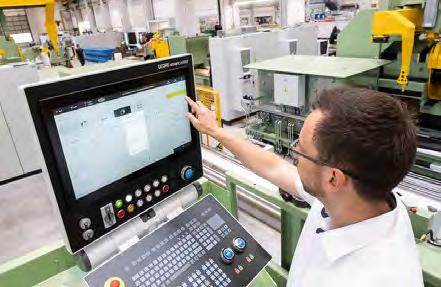
AUSTRIA
The Steel Division of Voestalpine awarded Primetals Technologies an order to modernise the basis auto-
mation systems of the continuous annealing live 1 (KGL1) in the Linz
plant in Austria. The replacement of the now obsolete systems will improve the operational safety and availability of the annealing plant as well as in-
Continuous annealing line 1 (KGL1) at Voestalpine in Linz
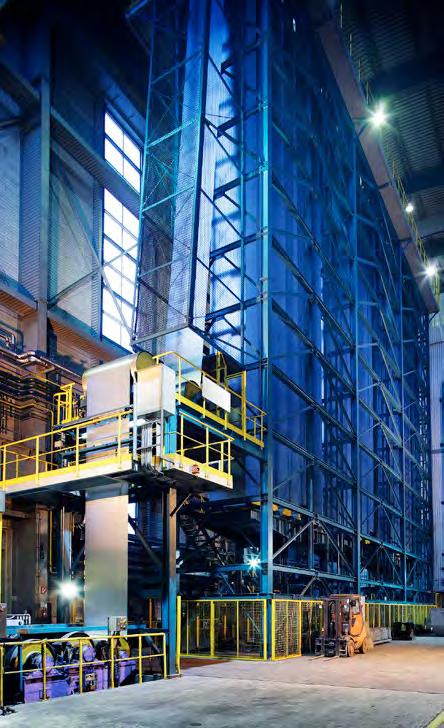
crease personal safety. All the sequence controllers will be modernised, and the KGL1 safety concept will be implemented. Amongst others, the signals will be interconnected via decentralised I/O systems which are linked to the automation system by a fieldbus. The existing sensors and actuators will be linked into the newly supplied control cabinets. Also some of the local control desks will be modernised and the central I/O modules of the automation system will be replaced by new decentralised hardware. The project processing is especially challenging, Primetals says, because work can only be executed during ten- to twelve-day plant shutdowns which only take place about every six months. (17. November 2020)
GERMANY
Tenova has received a major order from Thyssenkrupp Steel Europe for the supply of a walking beam furnace, designed for the heating of slabs, which will be located at the Thyssenkrupp Beeckerwerth plant, Duisburg. The plant will be build in Hot
Walking beam furncace designed by Tenova

Strip Mill 2, “meeting the strictest requirements for the production of premium sheets to be used in the automotive industry”, Tenova says. The scope of the contract includes engineering and the largely turnkey delivery of all equipment as well as the erection and commissioning including training. The plant replaces an old reheating furnace and will be installed directly next to an existing Tenova walking beam furnace.
ITALY
AIC completed the second phase of the revamping project at Ecoacciai in Pontedera, Italy. The full scope of the project included the replacement of
the scrapping mill automation
Scrapping mill at Ecoacciai in Pontedera, Italy.
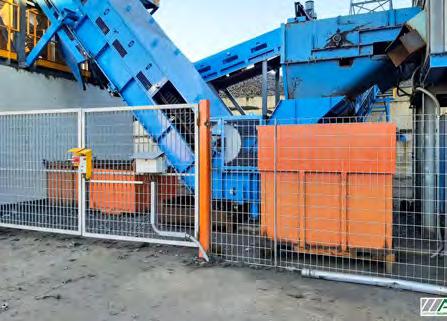
part, the hardware integration, the software security and safety systems installation. More specifically, this stage of the modernisation consisted of the installation of the safety access with electronic doors and coded key system to access the area as well as the activation
of the entire security system. AIC also provided access control to production areas for maintenance and operation activities due to the full controlled safety system. (27. Oktober 2020)
Acciaierie di Sicilia chose to ATS Mechatronics to supply and integrate two tying machines (TMB 400) and AIC to upgrade the electrical and
automation system of the cooling bed exit and bundle forming areas
of the rolling mill in Catania, Italy. These were follow-up measures to the installation of six new roughing stands and the renovation of the automation system in 2019. The upgrade aims to increase performance and improve troubleshooting by replacing obsolete equipment and upgrading the automation system. All tying machines of ATS Mechatronics were tested in its workshop prior to shipment to the site, reducing start up time and costs, AIC says. According to the project schedule, AIC was also involved in installation supervision and commissioning phases.
NETHERLANDS
Laura Staalcenter Maastricht has purchased a new levelling machine from the German manufacturer Kohler, which is represented in the Netherlands and Belgium by the company Hevami Surface Technology. With the machine, type PeakPerformer 100P.2500-RB-C, Laura Staalcenter can level sheets up to 2500 mm width, whereby in practice a maximum of 2100 mm will be processed as this is the maximum width of the decoil lines. The new Kohler levelling machine has a width to make optimal use of the existing crowned roll system which has been purchased to remove wavy edges and centre buckles from the sheet. Depending on the yield strength of the steel, sheets of 2000 mm wide can be processed up to a thickness of 12 mm. It is scheduled to be operational by mid2021.
SWEDEN
SSAB has chosen Paul Wurth to carry out a revamp of parts of its coke battery at Luleå steel works in northern Sweden, which focuses on battery life extension and emissions reduction. The replacement works were planned in two steps including preparation activities to remove existing constraints in summer 2020 and the main intervention for replacing the raw gas
Coke oven at SSAB’s Luleå steel works
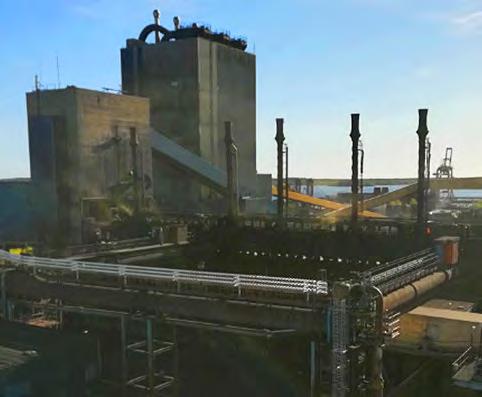
system and the oven refractory roof in summer 2021. In September, during a planned blast furnace shutdown, a project team already replaced the old gate valves on the off-takes. In addition, without proceeding with hot tapping activities, a new coke oven gas (COG) feeding line could be connected to the suction main, thus creating a long bypass on the exhauster system.
SWITZERLAND
ABB has been selected to supply its Flow Control Mold (FC Mold) electromagnetic stirring and braking solution for one of the world’s widest thick slab continuous casters at the new Nu-
cor Corporation steel plate mill at
Brandenburg, Kentucky, USA. With capacity for slabs of up to 305 mm thick by 3,150 mm wide, the caster is “the widest ever to be equipped with FC Mold”, ABB says. The order, placed by caster supplier SMS Group, will be operational by 2022. In continuous slab casting, conditions in the meniscus area of
Within ABB’s FC Mold three independent magnetic fields generate simultaneous stirring and braking in the mold from one fixed position.
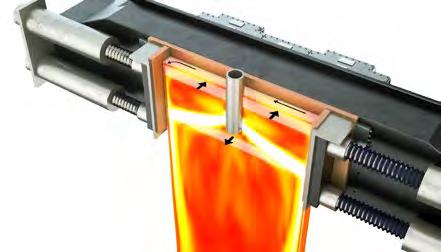
the solidifying steel are crucial to determining end product quality and have a major impact on productivity and overall operating costs. Integrated with the caster, FC Mold uses electromagnetic fields to control meniscus flow speed and fluctuations, while helping prevent gas bubbles and impurities from becoming trapped in the solidifying steel.
More Precision
Advanced thickness profile measurement
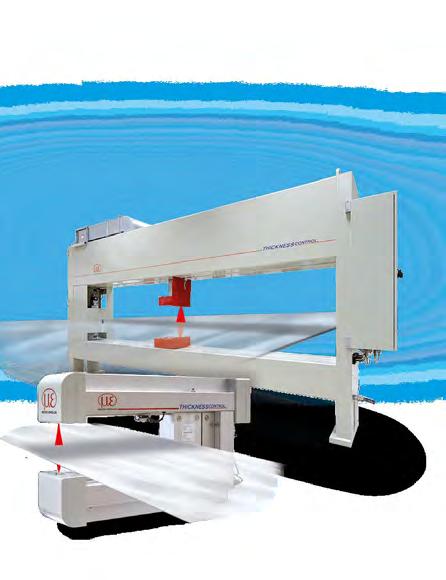
C-Frame / O-Frame based measurement systems for cold and hot rolling mills Laser line measurement ensures maximum precision, even for tilted strip No isotopes or X-rays Measurement independent from strip movement, tilt, surface type and alloys
Watch video
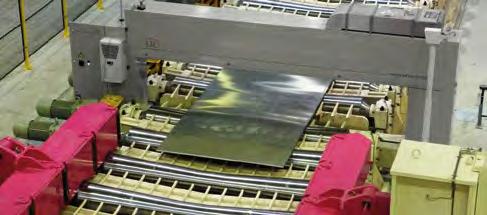