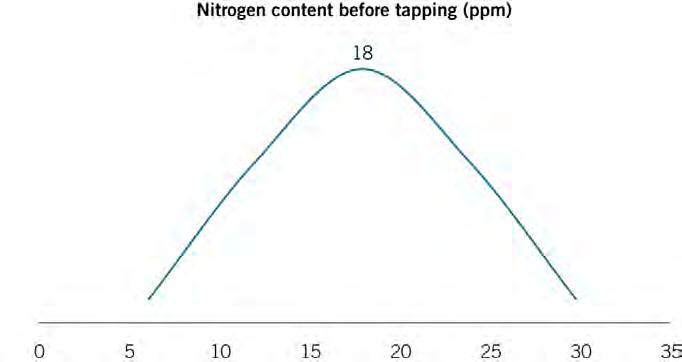
24 minute read
EAF VS. BOF
Electrical Steelmaking in place of Basic Oxygen Process – Danieli Vision from Quality Point of View
Integrated iron and steelmaking production represents the globally predominant technology. Global requirements for CO2 reduction will influence needed changes in iron and steelmaking philosophy using new technologies that generate less CO2. Based on forecasts, hydrogen application in primary steelmaking and scrap melting process will have higher shares in parts of the world where the integrated iron and steelmaking process is considered as traditional. A transition from traditional and well-established processes to the process based on DRI / HBI production, together with scrap melting in electric arc furnaces, must be followed by the means for producing high quality grades with low residual element contents. Danieli presents a way to keep capability for producing high-quality grades with low residual element contents using different charge materials.
Advertisement
AUTHORS: Bojan Vucinic, Franco Gandin, Danieli & C. Officine Meccaniche S.p.A
CONTACT: Bojan Vucinic, Senior TechTeam Manager, phone (0039) 04321955519, b.vucinic@danieli.it
Approximately 30% of the world’s crude steel production is carried out via electrical arc furnace (EAF) as the primary unit for steelmaking. The ratio between the two main primary steelmaking units, basic oxygen furnaces (BOF) versus electric arc furnaces, has changed in recent years and this trend seems to be confirmed for upcoming years due to changed conditions in raw material price and production costs, and due to strict requirements for pollution control. Making high-quality steel always has been the domain of integrated mills organized by the blast furnace-converter-secondary metallurgy-casting route. Now, numerous electric steelmaking operations around the world have successfully entered this product market. The main reason for this progress is the high flexibility in operation and raw materials options available to EAF steelmakers.
Table 1 shows allowable content of residual elements for some steel grades(1) which are mainly produced via BOF steelmaking process and must be pro-
Element, %
Cu Ni Mo Cr Sn IF steel
0,03 0,03 0,008 0,03 0,008 DDQ
0,04 0,04 0,01 0,04 0,015 Drawing
0,06 0,06 0,015 0,06 0,015 Commercial Structural
0,1 0,08 0,015 0,08 0,02 0,12 0,1 0,04 0,1 0,03 Fine wire
0,07 0,07 0,015 0,08 0,015
Table 1. Typical allowed residual elements content for most flat steel grades Rebar
0,4 0,35 0,08 0,15 0,08
duced via electric arc furnaces as well.
Nitrogen absorption during melting can be reduced by the application of controlled slag foaming, controlled carbon removal rate during process, carbon boiling control, proper EAF design, and controlled raw material application. The installation of vacuum degassers (RH or VTD) in the EAF steelmaking route improves the quality of steel products with ultra-low carbon and low-gas contents. Sulphur contents of lower than 10 ppm for certain steel grades can be produced in vacuum tank degassers (VTD.)
Integrated plant – Converter melt shops
The first step in the oxygen blow of the BOF process is silicon oxidation. The results show that no nitrogen is removed during the initial phase of the blow, when silicon oxidation is the primary reaction. The rate of nitrogen removal jumps as soon as carbon oxidation is increased. As the dissolved carbon content decreases, the decarburization rate, and therefore the CO evolution and nitrogen removal rates, also decrease. At the end of the oxygen blow process nitrogen present in the oxygen jet dissolves in the liquid bath, when the nitrogen removal efficiency of the bath is reduced due to lower CO generation rate(2). Usually, nitrogen contents before tapping from the BOF are in the range of 15 to 40 ppm, including reblown heats.
Figure 1 shows the typical nitrogen content before tapping from BOF (1.a.), and sulphur content after sulphur removal from hot metal and before tapping from BOF (1.b.)
Thanks to low nitrogen and sulphur content before tapping from the BOF, sulphur removal during secondary metallurgy and nitrogen removal during the vacuum process usually are not required for BOF based melt shops. The charge mix for the electric arc furnace process is different than for the BOF process so nitrogen content before tapping from
1.a. Nitrogen content before tapping - 2 s area | As average: 20% scrap in charge mix | Tapping temperature: 1,650-1,700°C | (12,134 heats) 1.b. Sulphur content in hot metal (12,134 heats) and in steel before tapping from BOF (12,040 heats.)
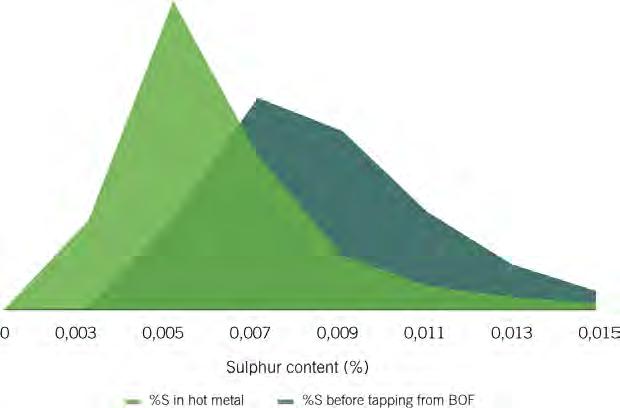
2.a 2.b
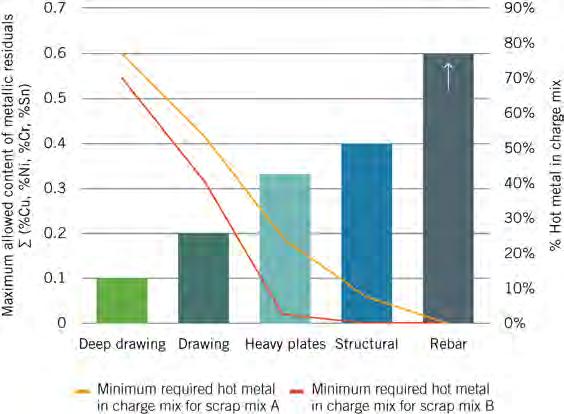
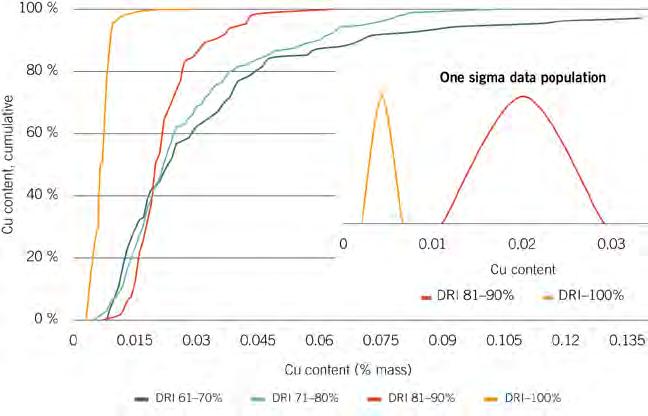
Figure 2: Content of metallic residuals for different charge mixes during EAF process 2.a: Minimum required hot metal participation in charge mix (simulation with two different assumed charge mixes) 2.b: Copper content before tapping for charge mixes with different DRI and scrap ratios (Danieli – process based on HBI, DRI and scrap)
EAF is based on carbon removal control during process, or very often the removal of nitrogen and sulphur must be considered as part of the secondary metallurgy process.
Electric Arc Furnace - Low content of metallic and non-metallic residuals
The electric arc furnace was developed mainly to recycle scrap. Application of virgin materials, such are DRI (cold and hot) / HBI / hot metal / Pig Iron, was introduced later, mainly for two reasons: operating cost control and scrap shortage. Process flexibility based on the possibility of using different raw materials, together with customized EAF design with confirmed short tap-to-tap time and less generated CO2, favours the electrical arc steelmaking process compared with the BOF process.
To lower the tramp elements in steel, different methods can be applied: • Dilution with virgin iron units • Improved scrap sorting (scrap purchasing and automatic scrap monitoring practice) • Mechanical and or chemical scrap pre-treatment In electric steelmaking, the improvement in scrap sorting and the dilution of tramp elements by mixing the contaminated scrap with virgin iron material are possible methods for reducing the concentration of tramp elements in the steel products. The direct reduced irons (DRI/HBI) or hot metal application have been used to produce several flat-product steel grades. The next two charts show hot metal participation for two different scrap mixes (scrap mix A, with higher HMS scrap, compared with scrap mix B) and copper content before tapping for charge mixes with DRI only, versus charge mix with different amount of scrap (scrap participation is reported as well.)
Improved scrap sorting could be based on automatic scrapyard control, starting from scrap monitoring (photo recognition), proper scrap sorting (dedi-
Figure 3: Impact of different scrap types on the metallic residuals content (plant A – Danieli database: rail steel application, 1,835 evaluated heats)

cated location per scrap type) and followed by mathematical modelling with continuous chemistry monitoring versus maximum allowed content of metallic residuals, versus available scrap (Q-Charge.)
There are several ways that nitrogen can be controlled during the EAF steelmaking process. Figure 4 is a pictorial representation of key drives needed to minimize nitrogen content at the end of EAF process.
Nitrogen content at the end of EAF process can range from 20 ppm to 110 ppm. The wide range of nitrogen contents at the end of the primary steelmaking process is driven by the type and quality of raw material applied during the process, equipment design and level of process control. Thanks to confirmed know-how with numerous different EAF designs for different applications (from extremely highly productive low-medium quality steel meltshops up to the melt-shops with demanding steel quality and low-medium-high
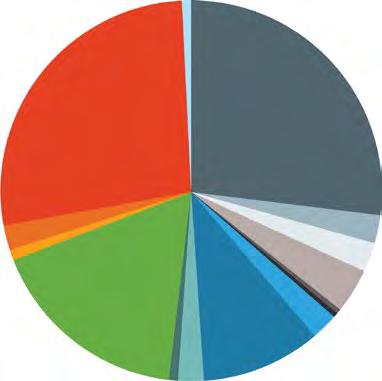
Figure 4: Strategies for minimizing nitrogen content at the end of EAF steelmaking process

productivity) Danieli is able to confirm application of EAF instead of BOF for high-quality grades, including steel with low nitrogen contents.
A study conducted by Pilliod has demostrated the change in nitrogen content in the steel bath during the melting and refining period of EAF process (see figure 6)(3). During the first melting period in region B, where a small molten steel pool forms, nitrogen increases significantly. In the second melting period the nitrogen is diluted thanks to minimized nitrogen pickup into the bath (due to more molten slag-covered electric arc) and increased liquid steel mass due to new solid scrap melting. As the final charge is melted and a foamed slag layer is formed, nitrogen pick-up is inhibited. When region E is reached, significant boiling and foaming of the slag occurs, which drives the nitrogen out of steel and significantly lowers the partial pressure of N2, resulting in significantly lower nitrogen. It is important to highlight that during tapping the nitrogen pickup is considerable and tapping procedure must be developed to minimize this phenomenon (automatic tapping control inlcuding monitoring of caryover slag and fast back tilting).
The results of a study by Pilliod gives us the main process and equipment design guidline needed to reduce nitrogen content before tapping: • Boring period reduction Vs. flat bath condition application: • 100% continuous - endless scrap charging (flat bath condition) • CO boiling: • Virgin material application with high carbon content (this is the best
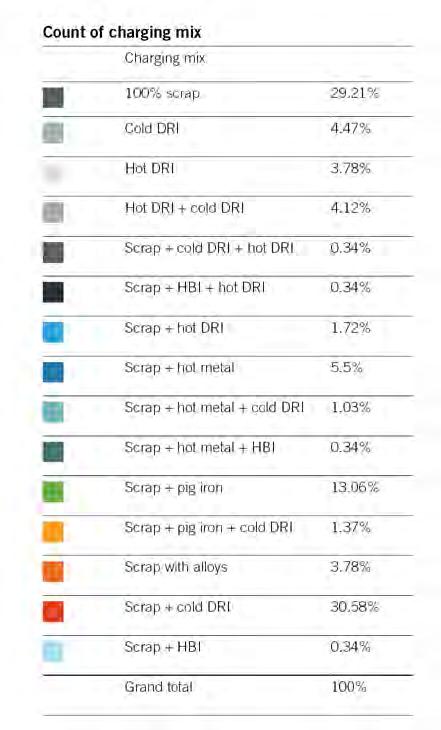
Figure 6: Nitrogen content of the steel during the operating practice of the EAF
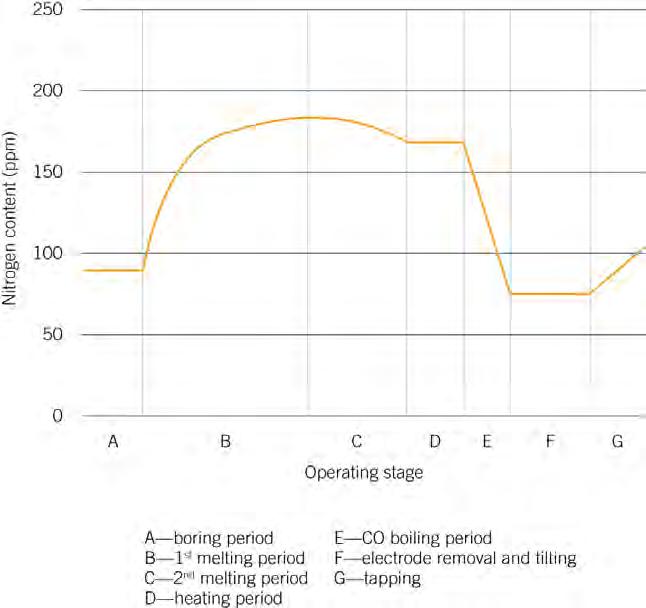
and more efficient way to introduce carbon into the molten bath) • Carbon addition (in form of raw material) per different process step: always keeping a higher level of carbon in the system in order to maintain a high rate of nitrogen removal. • Slag coverage index: • Electric Arc Stability and Coverage and radiation index control • Slag viscostity and MgO saturation control (advanced process, level 2 cotrol using continious process control loop) • Closed process loop: electrical (electrode stability) vs. chemical (oxygen supply vs. carbon injection is slag) Nitrogen pick-up reduction during the first stage of the EAF steelmaking operation is possible with a high hot heel and flat bath EAF concept. Compared with a standard bucket process, endless scrap charging and scrap melting during the entire process (EAF ECS) has less nitrogen content before tapping. The main reasons for lower nitrogen content before tapping are shorter duration of the boring stage, slag generation in early stage of process, and better arc coverage index starting from early stage of melting process. Figure 7 displays the applied power and arc coverage index for a process with bucket charging (first bucket) and in a case of continuous scrap charging. Compared with the EAF bucket process (100% scrap-based process), during endless scrap charging (EAF ECS), scrap is melted by heat convection and conduction, and not by arc radiation, as it is in a case of bucket process. During the continuous scrap feeding operations, the arc is kept covered by foamy slag and scrap falls into the hot heel.
Figure 8 shows the reduction of nitrogen content before tapping for two different scrap-charging practices, with the same scrap type per both analyzed pro-
Figure 7: Nitrogen pick-up during boring and first melting operating stage versus power stability and arc coverage index for bucket process (first bucket) and for EAF ECS (endless scrap charging with scrap preheating.) Left to right: Nitrogen pick-up (see Fig. 6); Bucket process applied power and arc stability; Endless scrap charging (EAF ECS) applied power and arc stability
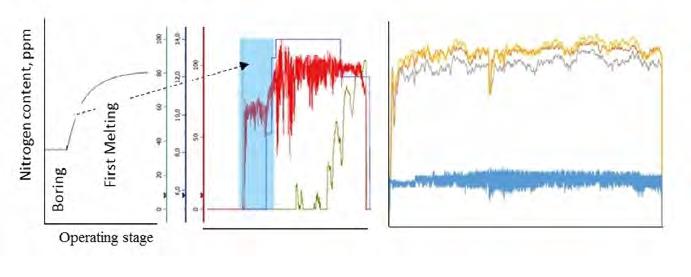
cess: fully continuous scrap charging with scrap prehetating process, versus scrap charging with a single bucket (3040% from total required scrap amount) and continuous scrap charging. Thanks to scrap charging via bucket with a high hot-heel and due to low amount of added scrap in this way, the difference in nitrogen content is in the range of 5 ppm, which means that nitrogen content at the end of the continuous scrap-charging process is less by approximatelly 10-15 ppm, compared with a standard two-bucket process with stand-
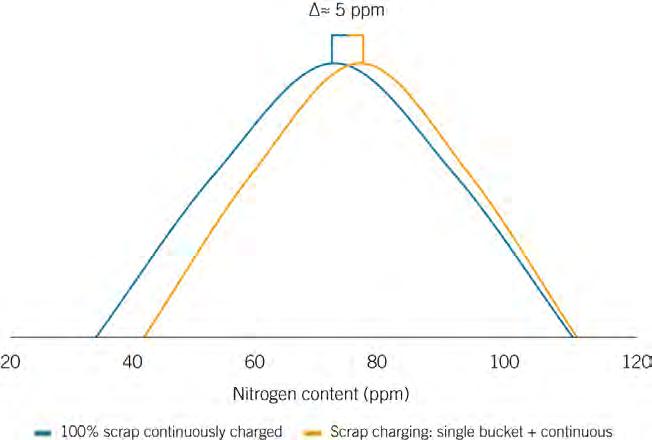
Figure 8: Nitrogen content: fully continuous scrap charging versus combined scrap charging practice: single bucket (30-40% from total scrap amount) together with continious scrap charging (high hot heel practice.) (Plant B: Danieli database – 591 evaluated heats.)
ard hot heel in the range of 15-20% from tapped heat size.
Apart from reduced nitrogen content at the end of the process, scrap preheating can reduce the power consumption of EAFs by using the waste heat in the furnace off-gas to preheat the scrap. Thanks to a dynamically optimized boring phase and stable covered arc, without peaks of current absorption, from early the operating stage electrode consumption is less compared with bucket process. Both savings make a significant contribution to a reduced CO2 footprint.
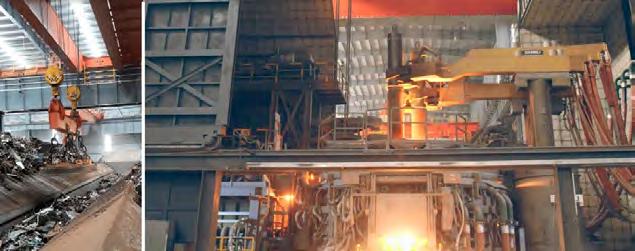

Figure 9 shows a chemical package layout for an EAF process with endless scrap preheating and charging, a project commisioned in 2019 (plant C) together with equipment described in table 2.
Standard practice for reducing nitrogen content at the end of the EAF process is to promote CO boil. This involves a vigorous reaction between carbon and oxygen deep in the bath. Generated bubbles of CO absorb nitrogen as they ascend to the surface, releasing both gases to the atmosphere. At the same time CO
Type of EAF AC EAF ECS
Tap-To-Tap time Tap weight Hot heel Total steel capacity
Lower shell diameter Panel inner diameter 40 minutes 150 t 80 t 230
7000 mm 7100mm Material addition Scrap Raw material
Electrode diameter Argon stirring Sampling Auxiliary Systems
Chemical package Continuous Continuous feeding -> 5th hole
710 mm Three plugs Automatic (during process) Q-Reg (electrode regulation system / arc stability evaluation) 1 Supersonic Oxy-Carbon Movable lance (O2-C) 3 M-ONE – fixed wall injectors
Table 2: EAF ECS (Endless Scrap Charging and heating) equipment description
10.a 10.b
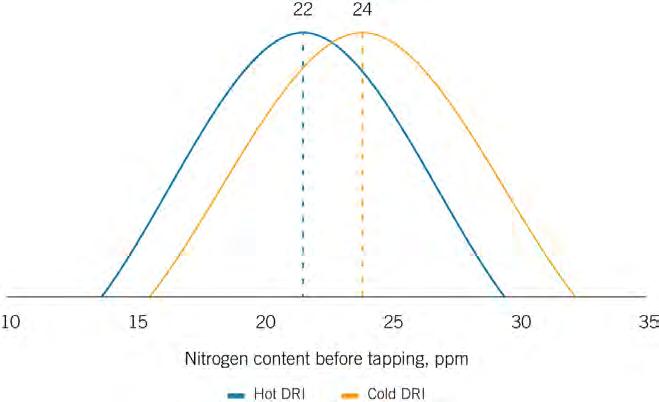
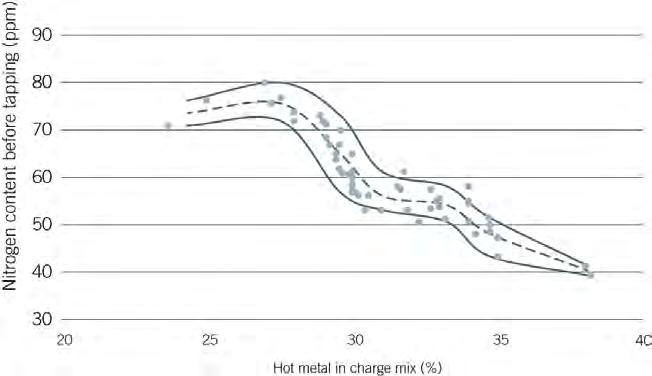
Figure 10: Nitrogen content with a process based on DRI (hot and cold) and based on hot metal. 10.a Nitrogen content before tapping for process with 100% cold DRI and 100% hot DRI – 1 s data population (plant D) 10.b Nitrogen content before tapping for process with different hot metal vs. scrap ratio (plant E)
from the liuqid steel together with CO generated by reduction of FeO with injected powdered carbon generates a foamy slag. The purpose of foamy slag is to shield the steel from the atmosphere and to cover the arc, which minimizes the dissociation of nitrogen molecules and nitrogen content pick-up in steel.
Raw material with high carbon content needed to promote CO boil are cold and hot DRI, HBI and hot metal. Figure 10 shows nitrogen content before tapping from the EAF for two processes: Figure 10.a shows 100% hot DRI and 100% cold DRI, and on figure 10.b shows the process with hot metal. Pig iron usually is applied as the raw material, to dilute content of nitrogen and metallic residuals.
Capability of nitrogen removal during EAF process is influenced: a. By raw material composition (carbon content) and temperature There are two reasons for nitrogen reduction with higher carbon content in raw material: higher amount of CO bubbles generated during process, and less power-on applied (less electrical energy consumption.) The impact of carbon content in DRI on nitrogen content before tapping is confirmed by many authors (4). Figure 11 shows the carbon removal rate with different hot metal consumptions for fixed tap-to-tap times, steel temperature and chemistry, and with different bottom sheel diameters (Danieli simulation.) In order to keep the same production rate (same tap-to-tap time) for full range of hot metal in the charge mix, the shell diamater has to be increased with increasing hot metal share. b. By content of non-metallic part in
DRI: the higher the gangue content, the higher the Electrical Energy Consumption and hence the related nitrogen pickup due to longer power-on time; c. By equipment design (EAF design) • For example, in order to boost carbon removal rates in case of high hot-metal consumption, the available surface area has to be enough in order to keep violent reaction under control and to avoid steel and slag splashing out of the EAF. Violent reaction control is linked with the carbon-removal rate per surface area (figure 11.) • Slag door: It has to be in the closed position during the entire process in order to reduce nitrogen absorption into the liquid steel from the air (appliction of advanced Danieli slag door). The impact of above-explained carbon content (from raw material) on nitrogen
Figure 11: Carbon removal rate with different total charged carbon (different specific hot metal consumptions) - Danieli simulation

Figure 12. Nitrogen content, specific electrical energy and oxygen consumption for three different charge mixes with same scrap consumption (plant D – charge mix with scrap and DRI and plant F – charge mix with scrap / HBI / DRI) 12.a: Nitrogen content before tapping (avg/StDev) 12.b: Electrical energy consumption
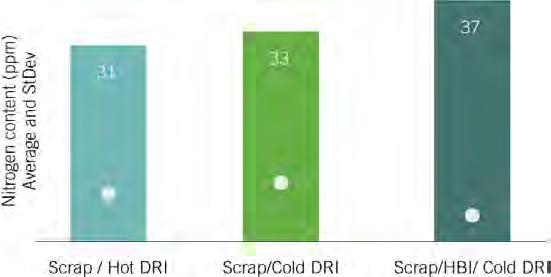

levels in steel at the end of the EAF process is reported in Figure 12. Typical carbon content in HBI is in a range of 1.5%, which generates less volume of CO and due to less generated chemical energy caused by carbon oxidation requires higher electrical-energy consumption.
Higher nitrogen content before tapping for a charge mix with cold DRI can be explained with higher electrical energy consumption. The highest nitrogen content (average) is for a charge mix of cold DRI with HBI and scrap. The reasons for this are: less carbon content with raw material and higher electrical energy consumption. Different raw material densities have a strong impact on electric arc stability as well, and therefore on nitrogen content before tapping.
Phosphorous content before tapping from the EAF is driven by phosphorous content in the raw material, and process parameters such as: FeO content in slag, temperature and slag basicity. It is important that the gangue (non-metallic) material content should be as low as possible, to avoid either using excessive amount of slag builders or (very often) to reduce final slag basicity due to compromise between slag viscosity (impact on slag foaming index) and slag weight.
Sulphur content before tapping from the electric arc furnace depends on sulphur content in the raw material. Compared with BOF process, wherein hot metal is pre-treated and charged sulphur content with hot metal could be up to 0.003%, in the case of EAF process sulphur content depends on the quality of raw material. Needs to pay strong attention on raw material purity from sulphur content point of view is driven by: 1. Capability of secondary metallurgy process to removal sulphur 2. Type of product mix For example, in the case of interstitial free grades with process route tappingLF-VD(RH)-casting destination, sulphur content must be controlled during the EAF process having clean material.
Conclusion
According to the International Energy Agency (IEA), the iron and steel industry accounts for approximately four to five percent of total world CO2 emissions.(5) Internationally, the steelmaking process has been optimised with respect to energy intensity over time. Currently, the process operates close to the thermodynamic limits, so further significant reductions in CO2 emissions for conventional technologies will be difficult. This suggests that only fundamentally new processes or “breakthrough” technologies will make a significant, further reduction in emissions. The key ‘breakthrough’ directions being investigated by the World Steel Association include: a. Replacement of some of the carbon-based fuels in the steelmaking process with hydrogen; a. Use of biomass, such as char, to replace coal in the iron and steelmaking processes; a. Carbon capture and storage (CCS) technology. According to forecasts, integrated iron and steelmaking processes will remain dominant with regard to crude iron and steel productivity. The Eleectric Arc Furnace process is part of the “breakthrough” technology mainly thanks to low CO2 footprint, and the flexibility to use different raw materials with high productivity per hour, supported by strong and continuous improvement in metallurgical process control.
Based on strong and accumulated experience by Danieli with the EAF process for high-quality grades, it is clear that the EAF can be implemented for most high-quality grades, together with modern secondary metallurgy stations provided with state-of-the-art, adaptive self-learning technology and models. Apart from the primary steelmaking unit, secondary metallurgy applied for BOF or for EAF-based melt shops is different mainly due to different output from EAF, and this is why secondary metallurgy performances must be excellent and reliable.
References
Alvarez, I.: HBI/DRI value economics of HBI/DRI use in the EAF. ISS Short Course: Direct Reduction. 27th April 2003. Hydrogen and Nitrogen Control in Steelmaking at U. S. Steel; Siddhartha Mishra, Yun Li and Sohn; AIST November 2009. Pilliod, C F, Variables Affecting the Nitrogen Content of Carbon and Low Alloy Acid Electric Arc Furnace Steels, 46th Electric Furnace Conference Proceedings, Pittsburgh (USA), 6-9 December 1988, The Iron and Steel Society, pp. 107-110 The production of Steel Applying 100% DRI for Nitrogen Removal, The Experience of Arcelor Mittal Lazaro Cardenas Flat Carbon; R. Lule, F. Lopez, J. Espinoza, R. Torres and R.D. Morales; AISTech 2009. Assessment of Opportunities for CO2 Capture at Iron and Steel Mills: An Australian Perspective; Dianne E. Wiley, Minh T. Ho, Andrea Bustamante; Science Direct, 2011.
Danieli: Upbeat on Business with Emerging Markets and Green Steel
In the near future, Italian plantbuilder company expects a change on the European market focusing on green investments and fully automated, increasingly intelligent plants,. The new trend will be the driving force that will motivates mill operators to invest.
And this will not only be true for Europe, CEO Giacomo Mareschi Danieli believes. „It’s almost certain that the world will follow the European trend,“ he said in an online conference on the company’s performance in the fiscal year 2019/20 and its plans for the near future. On the coporate culture, he noted that stakeholders „are rewarding excellence and proactiveness while discouraging superficiality and lack of discipline.“ The company has been restructuring divisions that do not bring sufficient value to the group and customers.
„Our target is not to have a cash cow but to continue growing“
On measures taken, he reiterated that some product lines have been restructured and downsized. But, „if results are positive, they can expand again. It was decided not to yield ground on any technology considering that our complete product portfolio is one of the company’s strengths,“ Mareschi Danieli said. „Metaphorically speaking, we must not invest in areas we are unfamiliar with because we are no longer able to get satisfaction from the current ones.“ Hence, Danieli will be continuing to innovate to come up with tomorrow’s solutions, concentrating on green aspects, he empasised.
Danieli’s main achievements in 2019/20
„The Danieli Digital Melter, which replaces the traditional EAF (electric arc furnace), has overcome the initial inertia typical of all innovative technologies and is increasingly appreciated by the market. We can therefore expect its success to grow, in both new and existing electric meltshops.“
„The MI.DA. (Danieli Minimill) has consolidated its success as confirmed by a contract for a Hybrid MI.DA. (H MI.DA) in the USA. Thanks to the Danieli Digital Melter, this plant will be the first to operate with alternative renewable energies (solar panels, wind, own energy production with gas, water, etc.).“
„The Digi&Met project, which aims to achieve full automation and digitalization of meltshop processes and logistics, is advancing as foreseen.“
From left to right: Camilla Benedetti, Giacomo Mareschi Benedetti, Gianpietro Benedetti, Allessandro Brussi, Rolando Paolone, Carla de Colle, Antonello Nordegaglia, Anna Mareschi Danieli, Stefano Scolari

He highlighted that the group in its research centre has more than 100 currently ongoing projects, and is testing more than ten prototypes industrially all over the world. – Including projects like the MIDA mill, Q One, a thin slab caster to produce exposed auto parts, and a high speed caster for long products running at speeds higher than 10 m/min.
More human capital overseas
Internationally, new service centres have been opened in the USA, Mexico and Vietnam while others have been enlarged – in the UK, Russia and Brazil. „The Covid-19 issues made these decisions even more strategic, our continuous local presence helped to keep sales, manufactring and customer service going,“ said Camilla Benedetti, Danieli ASIA and Ethics Audit.
She highlighted growth ambitions in Asia by investing in local teams and proposing new products and services. One example the new joint venture in robotics and digital solutions with China’s Jianlong Steel, alomng with miscellaneous enhancements of acivities in Thailand, India and Vietnam.
Finances
The last fiscal year ended with an EBITDA not significantly affected by the impact of the Covid-19 pandemic, reaching €188 million, on a revenue of €2.8 billion. The essential plantbuilding activities accounted for €2.14 billion, and saw an increase of 5% in the reporting period. The group’s net profit came to €62 million.
In the current fiscal year, 2020/21 – the group banks on a revenue of €2.9 to 3.1 billion, with sales rising in both segements, plantbuilding and steelmaking (ABS), says group CFO Group CFO Alessandro Brussi. The EBITDA is forecast to reach
US steelmaker CMC orders its third MI.DA ECR Minimill from Danieli. Hybrid-ready,featuring the Q-One Digimelter
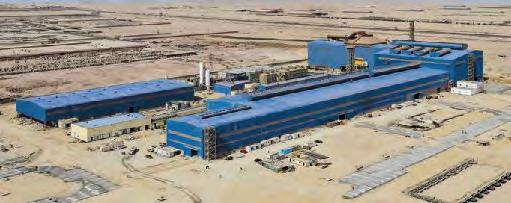
€210-220 million, and he also expects to see „ a good net profit.“ And, when looking further ahead, Brussi forecasts an again higher pre-tax profit in the fiscal year 2021/22, in both the group’s activity segments.
Danieli makes more steel, too
A Danieli feature not known to everyone internationally is that it also operates as a steelmaker with its subsidiary ABS, which is about to boost ist capacity with an all- new mill
The year that ended 30 June was a „special“ year for ABS. „This is not quite unusual in an industry subject to fluctuations but it leads to decidedly different scenarios where structual market changes can be seen on the horizon,“ said ABS vice chairwoman Anna Mareschi Danieli at the conference. The year 2019 brought a revenue of €661 million, with 1m tonnes of product shipped, which includes a production stoppage from March to April.
ABS is in the process of building a new quality wire rod mill - project QWR4.0 – that was due to be started up in recent weeks. This meant an investment of €190 m for 500,000 t/y of wire rod. According to ABS’ CEO Stefano Scolari, it will be the only in Europe to provide products from 5 to 500mm. ABS is also ramping up the Sisak facilty in Croatia to maximum ca-
Russia’s OMK has contracted a new DRI plant, to be installed at Vyksa Steel Works, as part of the new complex for the production of slabs, seamless pipe and rail wheels pacity with the target of producing 350,000t per year as soon as 2021, to bring it up to 450,000t in the years to follow.
Group chairman Gianpietro Benedetti gave a summary of Danieli’s vision of the past five years, which points very much towards Green Steel. „We are proud to have received two important orders that put an exclamation mark on the investment in research, made in the last two years. Basically, he referred to the order from CMC in the USA for its third MI.DA mill, which will be the first to produce sections in endless mode, even in hybrid mode, and will allow to use renewable energy sources such as solar and wind.
The other main contract was concluded in September 2020 with OMK (Russia) for a direct reduction plant equipped with an endless charging system directly feeding the EAF, with 64% lower emissions than the best integrated complexes. It will be the first “green steel” plant in Russia and the European region, Danieli claims. „ It’s more or less what has been dicussed for years in relation to the Taranto works in Italy,“ Benedetti noted. And he added that „In the next few years in Europe, the USA and I’d say significantly also in China, the theme of green steel production is progressively becoming paramount.“
In his closing remarks, Benedetti said that the company keeps trying to maintain „management developed in-house that can share the company’s spirit and character, which must certainly evolve while maintaining its supportive pillars.“

Since more than 50 years!
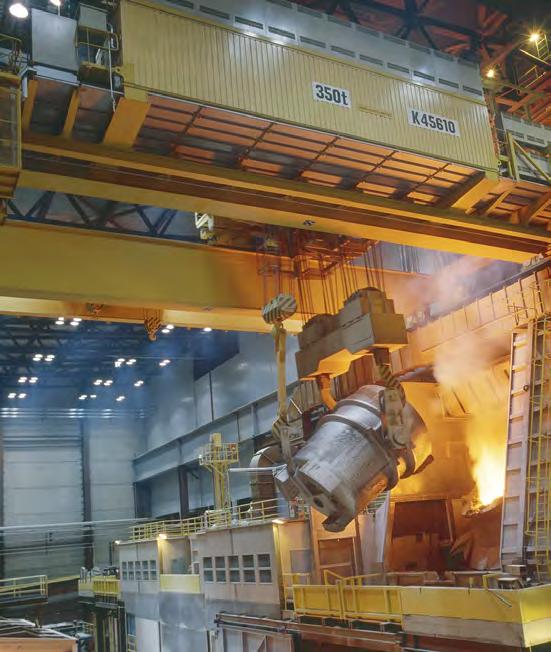
The market for steelmaking plants
Demand is maintaining appreciable growth in the BRIC and North African countries for new generation integrated large plants whereas in the USA and EU for mid-sized flexible plants and modernisation of existing plants to enable environmental-friendly, higher quality production with high finishes used in mechanical engineering, car making and infrastructure. The anti-dumping policies now activated by all major steel producing countries have stimulated demand for new plants that must also guarantee low emissions for sustainable production in line with the trend of CO2 reduction required today by every production chain and which will lead to many investments in innovative plants already during 2020 and in the following years. CRANEFRIGOR™ – AC-unit for severe duty conditions works.


FrigorTec GmbH • info@frigortec.de • www.frigortec.com